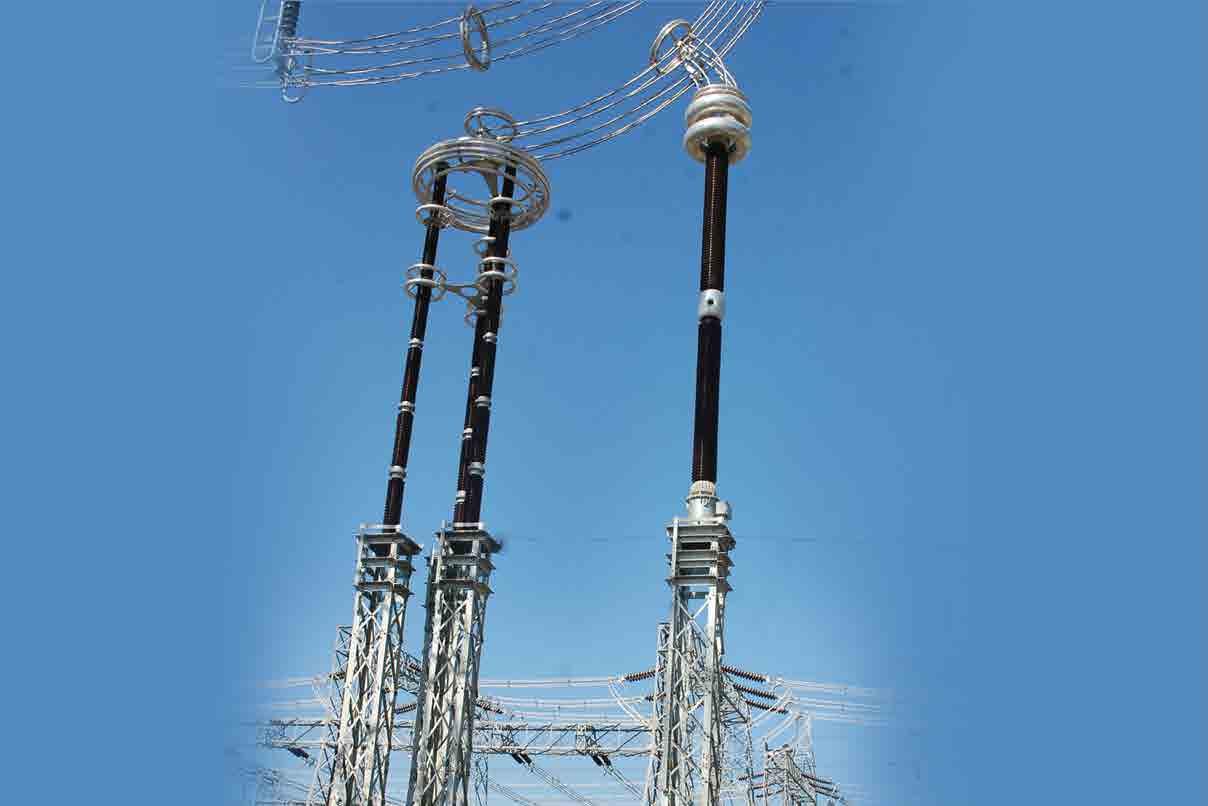
6 minute read
Global leaders in insulators Aditya Birla
1200kV Solidcore and Hollow insulators
GLOBAL LEADER IN INSULATORS
Aditya Birla Insulators, part of the €38 billion multinational Aditya Birla Group, is headquartered in the state of Gujarat, in western India. Industry Europe spoke with Vikas Khosla, president of Aditya Birla Insulators, a unit of Aditya Birla Nuvo Ltd and a leading company within the group.
Globally, Aditya Birla Insulators is the fourth-largest manufacturer of high voltage porcelain insulators. The company was founded in 1967 in Rishra near Kolkata (West Bengal) in the eastern part of India. Subsequently, a second production facility was put in place in 1982 at Halol (Gujarat) near Vadodara in the western part of India. A third facility for composite insulators was also established at Halol in 2009.
The company’s product range includes hollow & solid core insulators for the substation segment and disc, pin & post insulators in the transmission segment. Additionally, the company manufactures composite long rod insulators for special application requirements. Insulators manufactured by Aditya Birla Insulators have been installed successfully in over 58 countries worldwide.
Both plants are ISO 9001, 14001 and OHSAS 18001 accredited. The Rishra plant is also certified for SA 8000. High voltage porcelain insulators
The company specialises in the production of high strength porcelain insulators for use in circuit breakers, instrument transformers, condenser bushings, disconnector switches & railway traction systems as well as transmission line insulators for voltage applications up to 1200 kV.
Vikas Khosla: “The current combined production capacity of both facilities is in excess of 62,000 MT p.a. for the porcelain segment, of which only 45,000 MT is currently under utilisation owing to significant imports from China. The Indian government has launched a programme called ‘Make in India’ to bolster the domestic industry and make our country a global manufacturing hub in the years to come. This will boost demand and we are waiting for the programme to kick in. The current Chinese imports have impacted the domestic industry significantly with domestic capacity utilisation hovering at around 60–80 per cent. The
prices of Chinese products are artificially pegged and I am convinced these are not sustainable in the long run. Additionally, the quality of Indian products is good and, when it comes to the life cycle cost, we have an advantage. We do believe that finally the quest for quality with economic product value will prevail.”
Each stage in the manufacturing of porcelain insulators, from the wet grinding of raw materials to vacuum extrusion to provide plastic clay right through to the final assembly of the insulators requires rigorous testing, both mechanical and electrical. The production cycle is supported by a comprehensive system of process and quality control. These control systems are fully documented, being a vital part of production at both the units.
Vikas Khosla continues: “We are the only insulator manufacturer in the world using barcode for product traceability during the production process. This is a very important quality aspect: it shows how much we trust our products, and how much we value our customers. These barcodes enable every product to be tracked in the entire manufacturing cycle. We can even track specific machines and the supervisor responsible for the production shift. This helps us to continuously ensure high standards.”
Aditya Birla Insulators employs 3600 blue-collar workers and 400 white-collar managerial staff. These 4000 employees generated a turnover of €84 million in the last fiscal year, up 8 per cent from the previous year. It looks as though the turnover for the current fiscal year will be between 94 and 95 million euros. The company expects to achieve a turnover of 140 to 150 million euros by 2020 by expanding its global reach.
“As a subsidiary of Aditya Birla Nuvo which is part of Aditya Birla Group, a global conglomerate, we benefit in many ways. We share the same values, and since the commercial activities of the group and its different subsidiaries are highly diversified, we all share the best business practices of the group. By keeping a close eye on what each unit of the group does to improve business performance, customer satisfaction & employee happiness, we continue to learn and to raise the bar.”
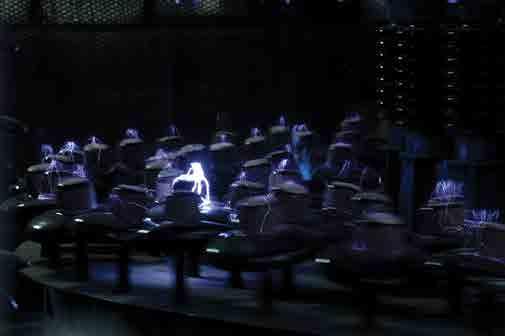
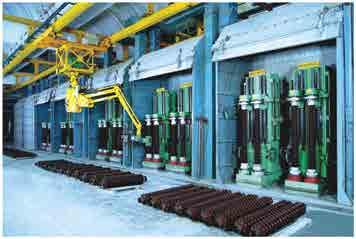
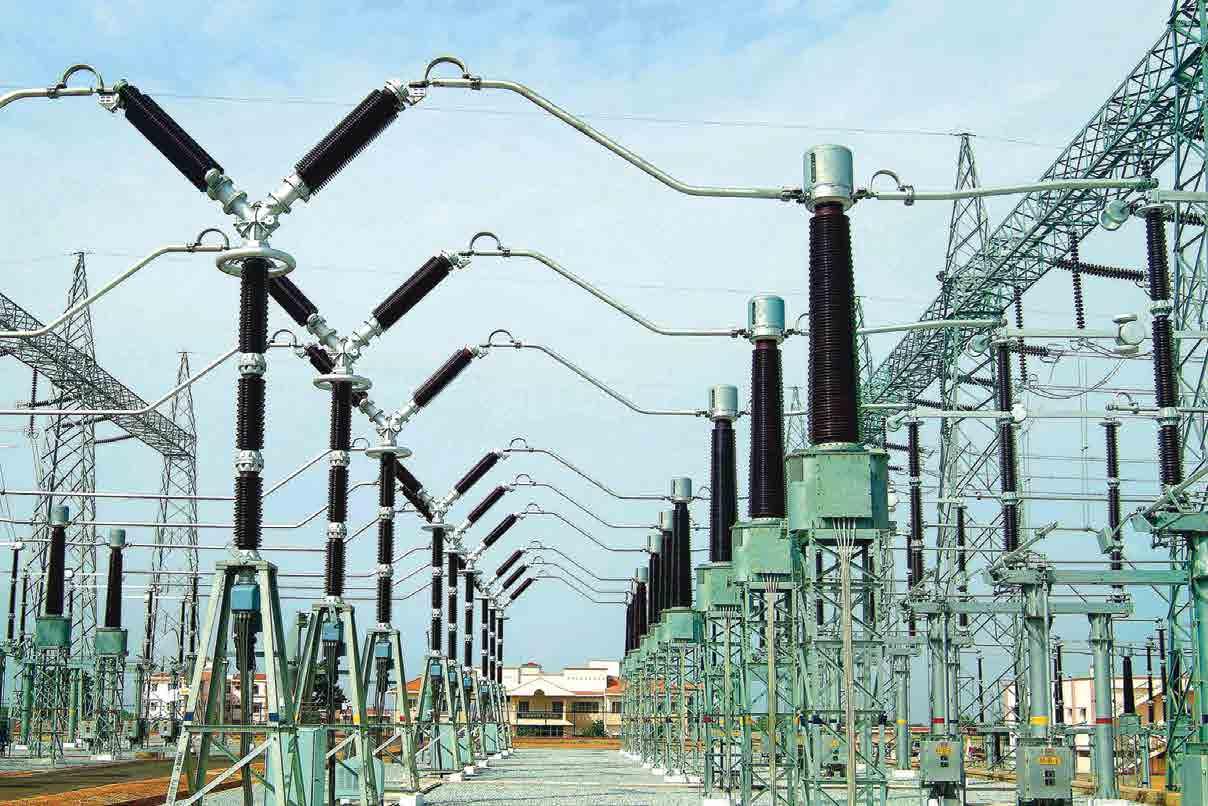
Economic developments
Aditya Birla Insulators has customers all over the world including Siemens, Alstom, ABB, Crompton Greaves and EPCs like KEC International, Larsen & Toubro, Tata Projects, Kalpatru and so on. In addition to being the dominant player in the Indian market, Europe and the US are important overseas markets for the company. The current government’s focus on ‘Power for all’ by 2019 will stimulate demand. The ‘Make in India’ campaign aims to promote national buying and counter the tendency towards buying cheaper goods from China.
Vikas Khosla adds: “The Ministry of Power (Government of India) contacted the domestic industry in 2006 with the request that we increase our manufacturing capacity. To accommodate the country’s future demand, we increased our investment budget in the following years and up-scaled our capacities in line with their projections, but as of today the domestic industry is operating at sub-economic production levels. This means that we can supply the overseas markets rapidly as our production infrastructure and capacity is readily available. Customers won’t have to wait for the construction of a new production site – they can be serviced for their requirements now. We believe India could be a major supply hub for insulators to global customers in the next three to four years.”

Pollution resistant insulation
With the continuing global trend towards urban development resulting in the necessity of inter-regional transmission and system strengthening, Aditya Birla Insulators’ competitive positioning looks good with strong potential for network expansion. In addition to this, its commitment and continuous efforts to act upon customers’ changing needs means the company has the strength to grow and deliver.
Vikas Khosla concludes: “Our company is focusing on R&D activities in line with ever-changing customer needs. The engineers at our R&D department are in regular collaboration with renowned power & technical institutes such as CPRI, and are currently focusing on the development of high pollution resistant insulators that can take up to 160kg particles per cubic metre. The pollution handling capacity of insulators manufactured today is up to 56kg of particles per cubic metre for the ceramic insulators.
“We have also teamed up with a global market leader in RTV coating solutions to provide Si coated solutions for ceramic insulators which will combine the positive attributes of both porcelain & composite insulators.
“Furthermore, our company collaborates with customers on various initiatives relating to product development and design & cost optimisation. This helps to enhance the customers’ competitiveness and provides them with products in line with their own customers’ requirement and expectations. As an organization, we are aligned to create sustainable value for our customers and that builds brand ‘ABI’.” n
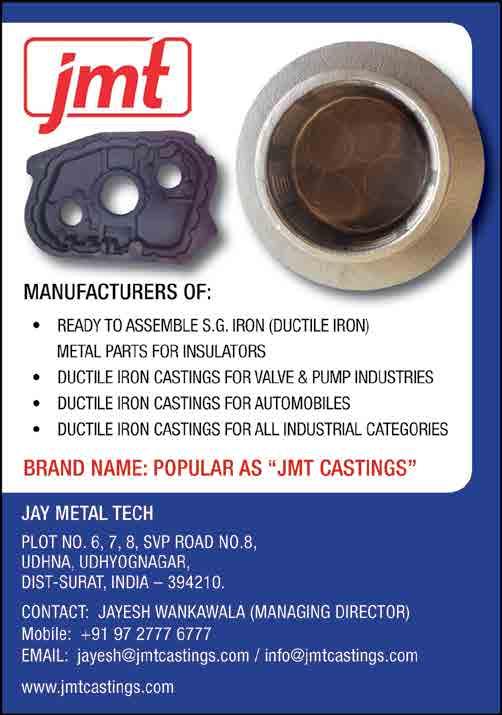


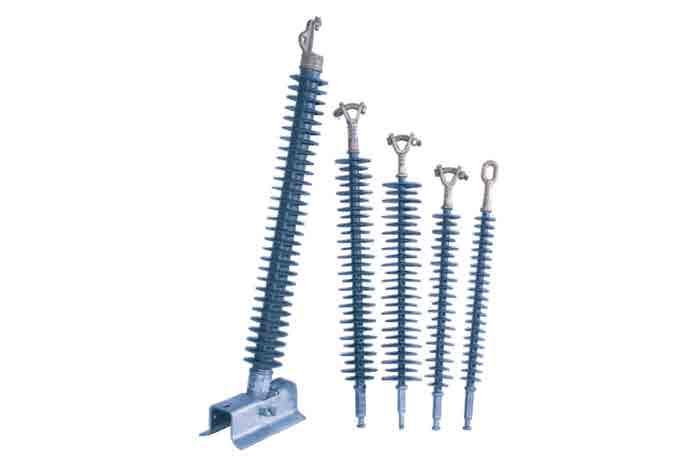