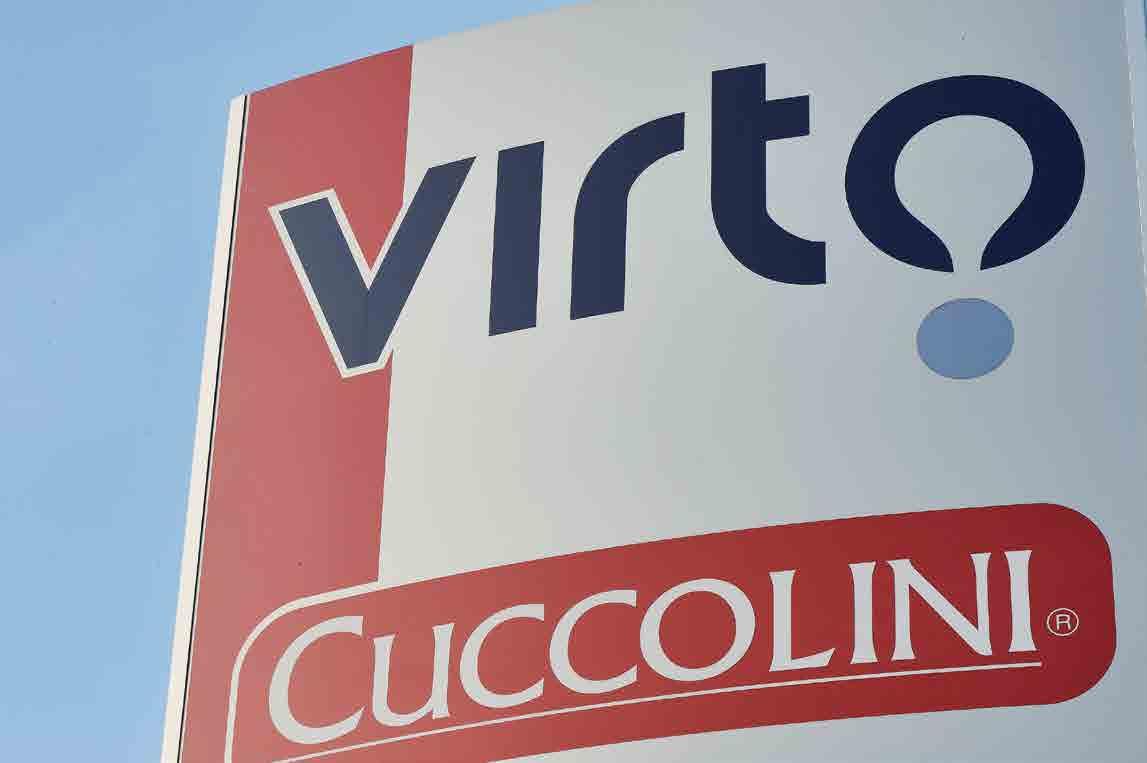
5 minute read
Redefining screening technology Virto Group
REDEFINING SCREENING TECHNOLOGY
The Virto Group is a global leader in the design and manufacture of screening and separation equipment. During the past few years the company has begun to revolutionise the industry with its patented multifrequency vibrating sieve technology called ‘ScreenX’. Philip Yorke talked to Mark Peatey, the company’s CEO, about its unique screening products and its move into new markets.

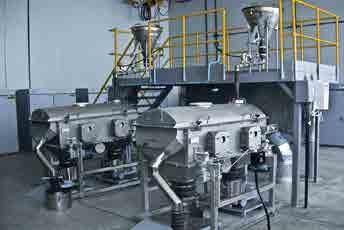
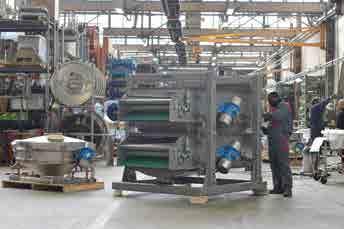
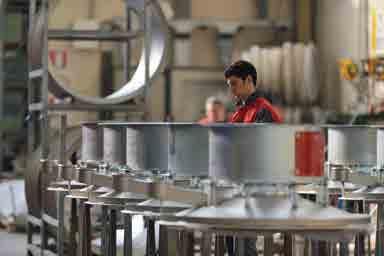
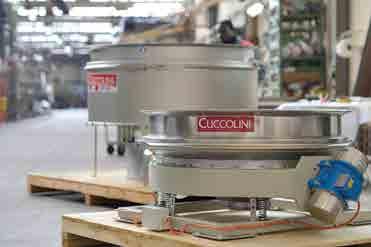


The Virto Group traces its origins back to 1946 when the Cuccolini screen maker was founded near Bologna in Italy. By 2008, when the Virto Group acquired the business, Cuccolini had become one of the biggest manufacturers of vibrating sieves in the world. By acquiring the Cuccolini product range and combining it with its patented and revolutionary multi-frequency vibrating (MFV) ‘ScreenX’ line, the Virto Group is rapidly becoming one of the most successful and diversified screening equipment businesses in the world.
Today the Virto Group is a global leader in the design and manufacture of screening solutions with a unique manufacturing heritage in the production of screening equipment that goes back almost 70 years. It has provided advanced vibrating sieves and separation tools for thousands of customers operating across more than 50 different industries worldwide. These range from fine food powders to heavy aggregate and mining materials. With its extensive production facilities located near Bologna in Italy, its R&D labs in multiple locations and worldwide network of agents, Virto is a truly global operation. Its diverse range of screeners are FDA and ATEX compliant and are presented across its two distinct product lines: Cuccolini and ScreenX. Revolutionary technology
Virto’s diverse product portfolio of screeners offers highly efficient and large capacity screening solutions for diverse particle separation requirements, in particular for difficult-to-sieve materials that may be wet, sticky, agglomerative or aggressive. Whilst the company’s Cuccolino brand is well known for its high quality, cost-effective and traditional industrial sieves, Virto’s ScreenX brand is unique and utilises the company’s patented and cutting edge ‘MFV’ technology. This is a revolutionary process that is unrivalled in its ability to not only significantly increase capacity, but also to process problematic materials that are abrasive, sticky or very fine. The company’s ScreenX line of vibrating sieves utilises its patent protected multifrequency technology to convert single-frequency oscillations into multi-frequency movement. As a result, the acceleration transmitted to the screen mesh reaches 500G as opposed to just 5G delivered by traditional screening equipment.
This new screening technology has been developed over a 20-year period by Virto through a robust, in-house R&D programme. These cutting-edge industrial sieves consistently outperform other screening brands in terms of their throughput for the classification,
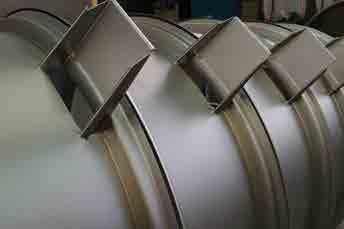
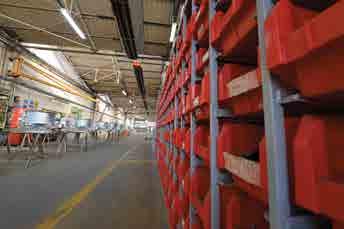
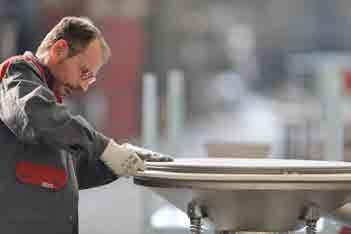
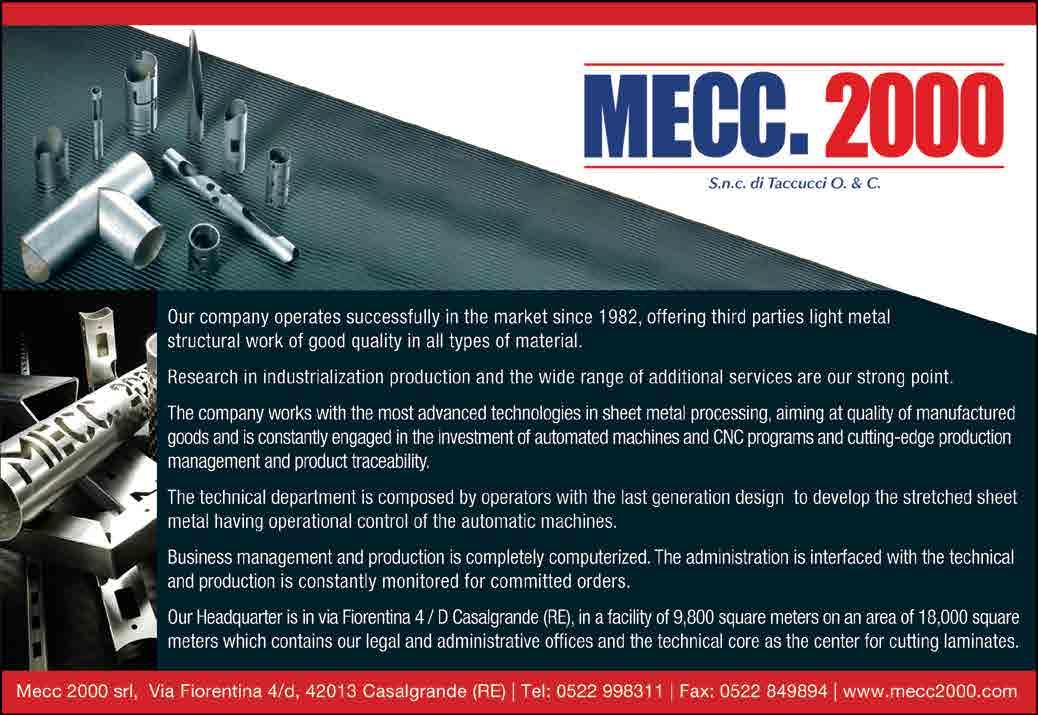

screening and de-dusting of coarse materials but also with highly efficient fine particle separation going down to 6 micron. It is able to do this because it overcomes mesh blinding and material agglomeration due to the power of the 500G of acceleration imparted in to the screening mesh which is transferred in to the material that requires particle size separation.
Peatey said, “As a privately owned company we are able to offer not only our unique cutting-edge technology but also a more flexible and dedicated service to our customers. During the last five years we have revolutionised screening processes for many industries and made what was previously impossible, possible. Our multi-frequency industrial sieves can cover an infinite range of materials with a particle size ranging from 20 mm to 6 micron. Today around 80 - 85 per cent of traditional separation needs can be met with traditional screeners such as Virto’s Cuccolini line. However, the remaining 15 - 20 per cent is a very different market because that material is typically “unscreenable” for standard technology because it is wet, sticky, agglomerative or too fine. This is where ScreenX comes into its own. For example, until now many types of metal powders could not be “economically” separated below 30 micron but now they can to as small as 6 microns. Our laboratories are also our shop windows and a place where we can demonstrate and test any screening challenge that a customer might have.
“In fact, we recently created the ‘Virto Challenge’ where we invite prospective customers to send us difficult samples for free testing and we ask them for the toughest that they have, in order to prove that we have a screening solution for what was not previously possible.”
Peatey added, “We are extending our global reach and have recently established a new facility in Latrobe near Pittsburgh, Pennsylvania and will shortly be opening another in South Africa. In addition we have an extensive network of agents, distributors and re-sellers (ADRs) that we are looking to continuously grow. We offer equipment that ranges from standard, cost-effective and highly reliable to cutting edge, high quality and tailored machines specifically designed to meet the exacting standards of our clients, including the de-dusting and control screening for the packaging industry. We serve many of the biggest names in foods, pharmaceuticals, chemicals, metallurgy and mining and petroleum.”

New technology driving sales
The Virto Group continues to see strong growth and has set itself the target of becoming the world’s number one screening and separation technology company in the world. It is already one of the world’s largest manufacturers of screening equipment producing more than 2500 machines a year sold in more than 75 countries.
With its patented MFV technology that allows Virto equipment to achieve previously unobtainable particle size separation results for difficult materials across multiple industries, it is well placed to achieve its objective. n
For further details of the Virto Group’s revolutionary screening products visit: www.virtogroup.com
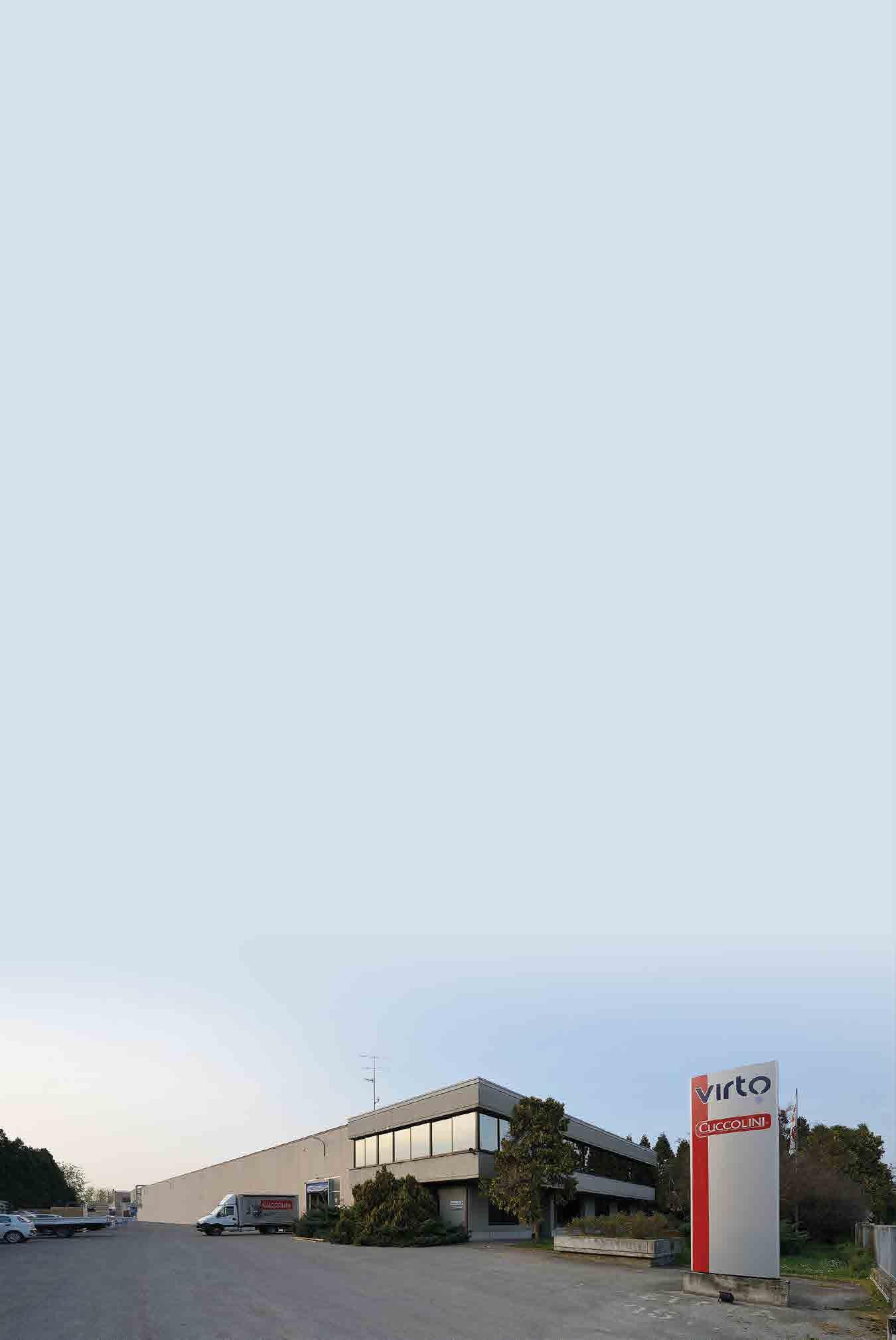