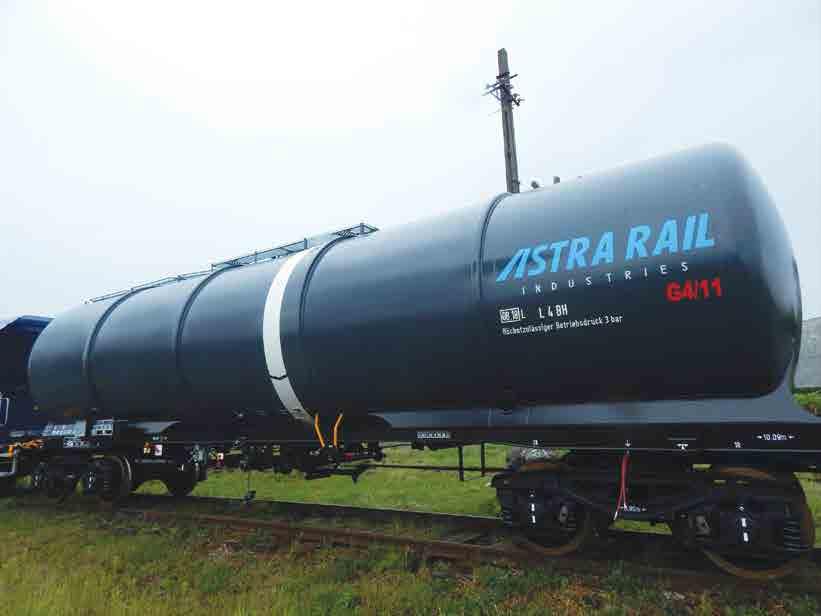
9 minute read
On a roll Astra Rail
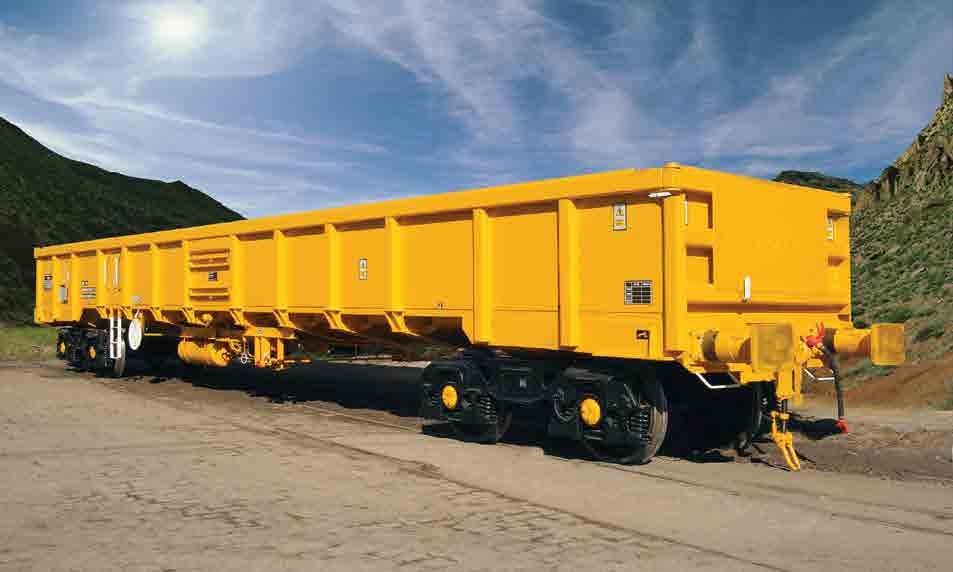

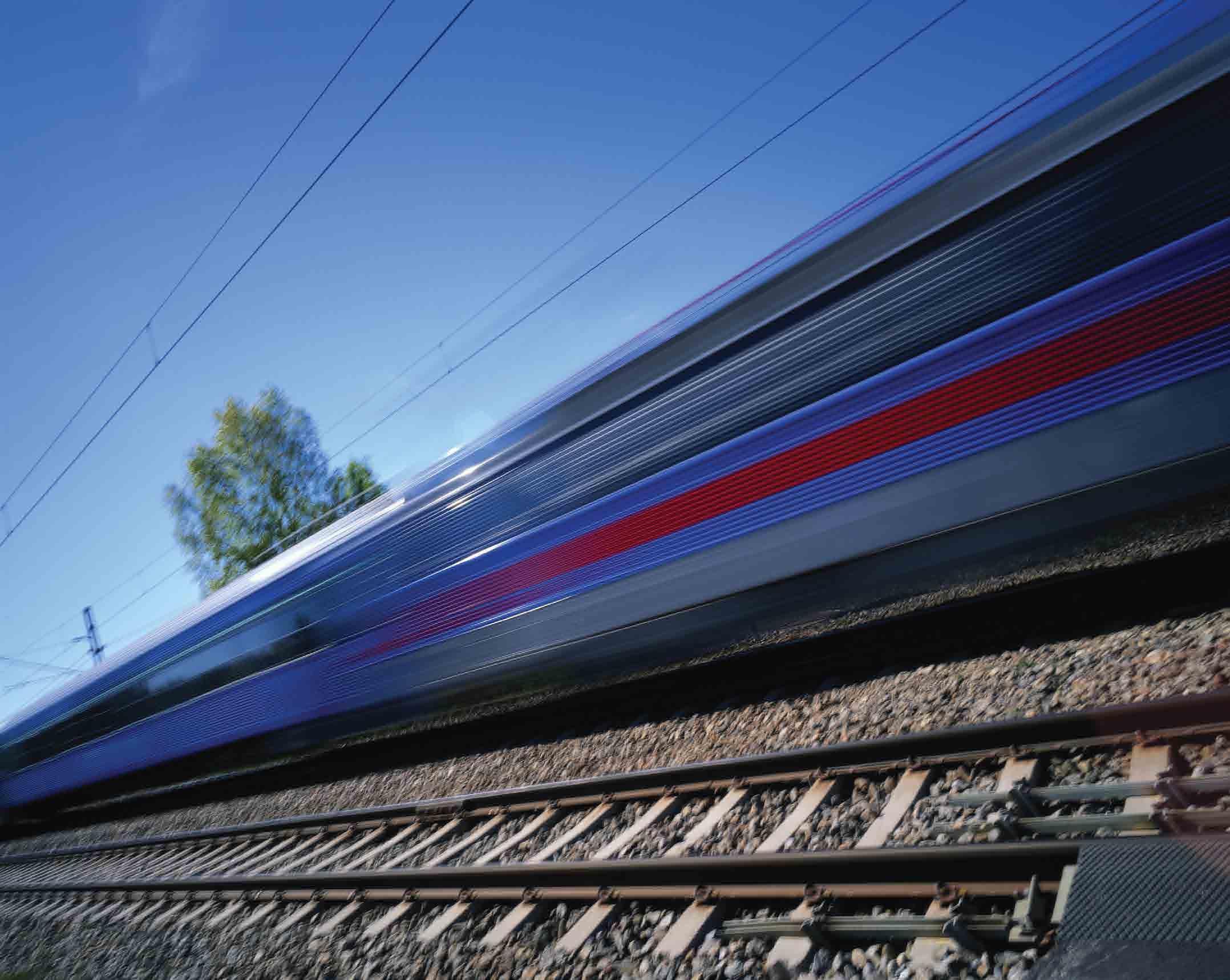
ON A ROLL
Optimising Europe’s rolling stock is the sole focus of Astra Rail Industries, which is a leading developer and producer of modern freight wagons, bogies and rail cars. Philip Yorke spoke to John Brown, the company’s sales and marketing director, about its continuing investment in new technology and move into new markets.
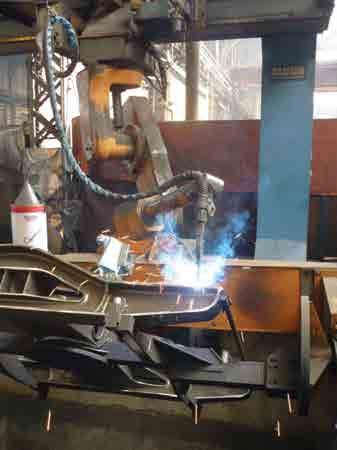
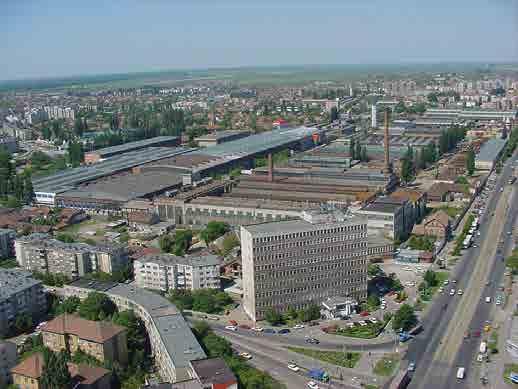
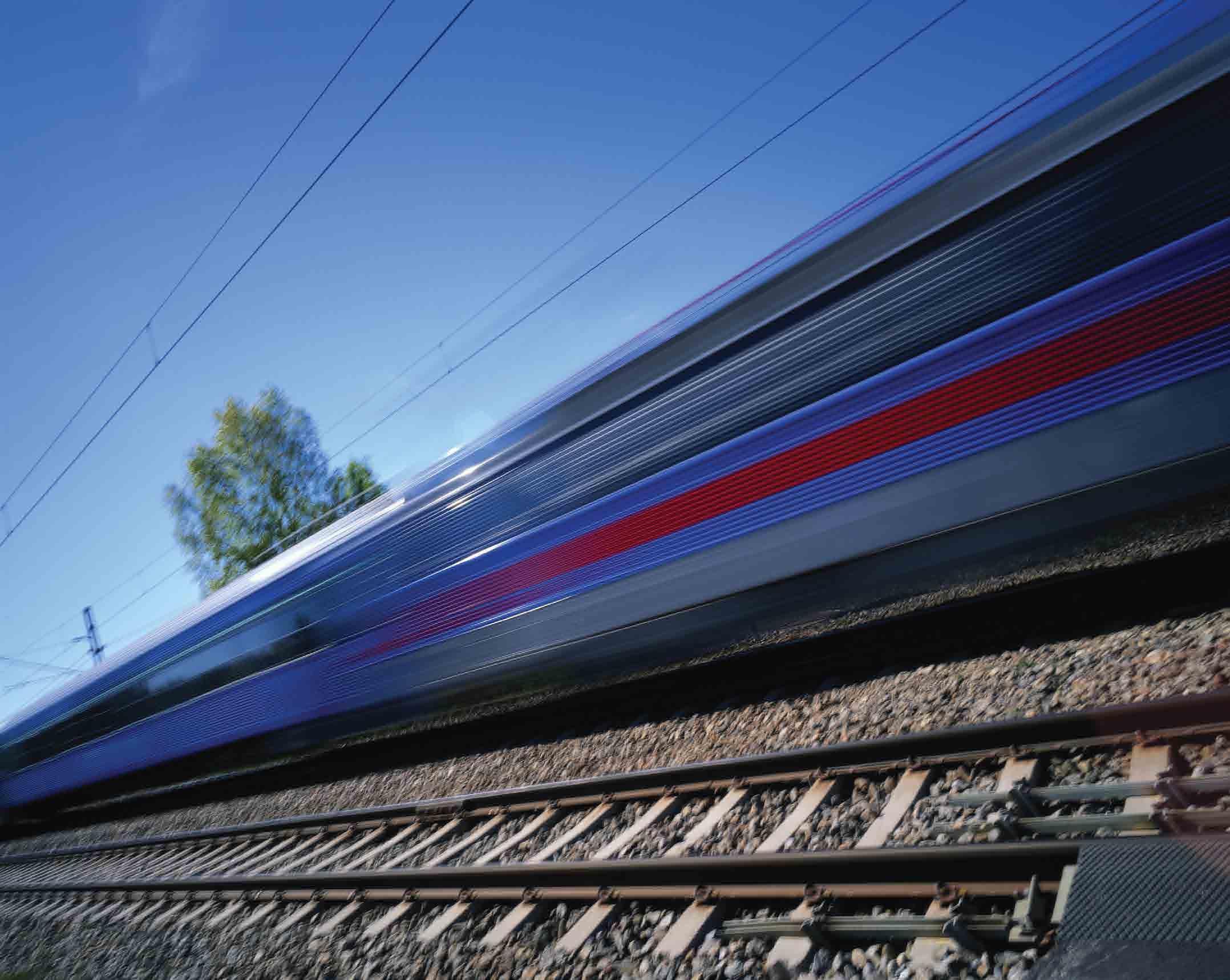
Astra Rail Industries was founded in Romania in 1882 and has since produced over one million freight wagons. The company operates three modern manufacturing facilities in Romania, in Arad, Turnu-Severin and Caracal. Operated and driven by a German management team with unrivalled experience since 2012, the company subscribes to the highest standards of European freight wagon engineering. Astra Rail Industries SRL has the largest freight wagon manufacturing capacity in Europe, with covered working areas exceeding 350,000 square metres. This enables Astra Rail to produce more than 5000 freight wagons per year in a wide variety of designs and with many innovative tailor-made features.
In addition to freight wagon production, Astra also provides servicing, maintenance and repair facilities, as well as offering special services for the development and inspection of railcars. Today the company is able to draw upon the expertise of two of its subsidiaries for special projects: ICPV, with its prestigious engineering offices
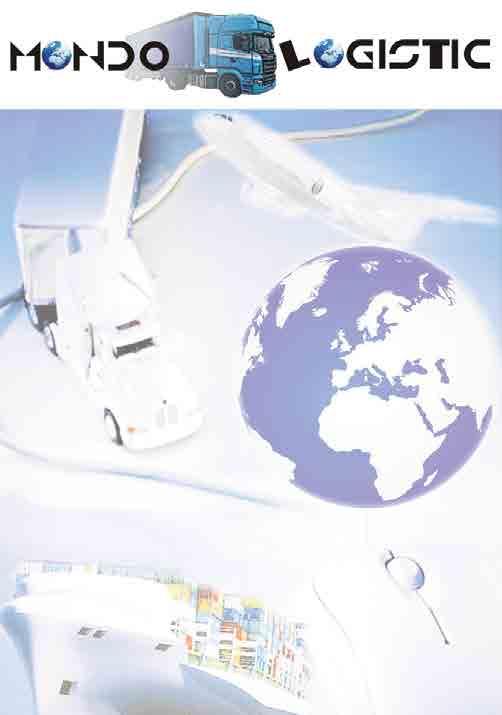
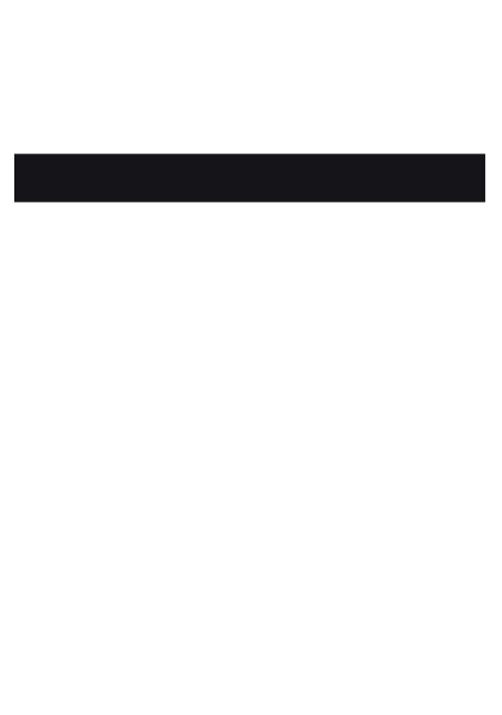

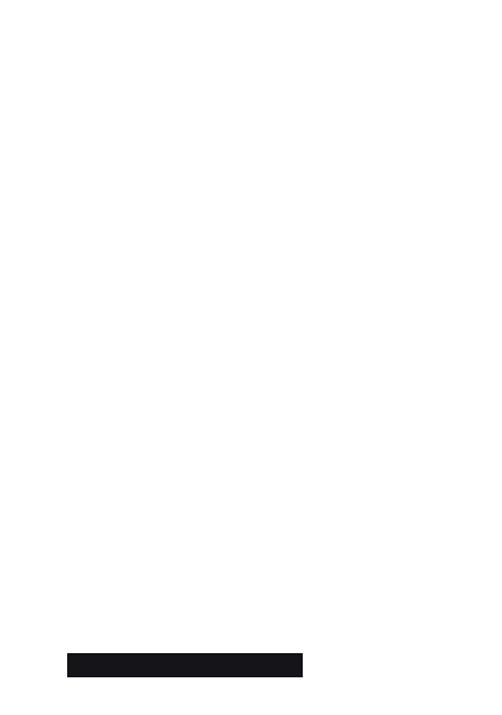

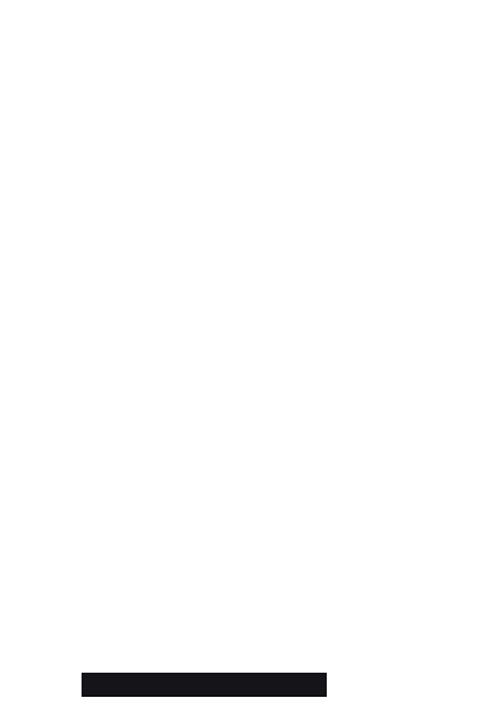
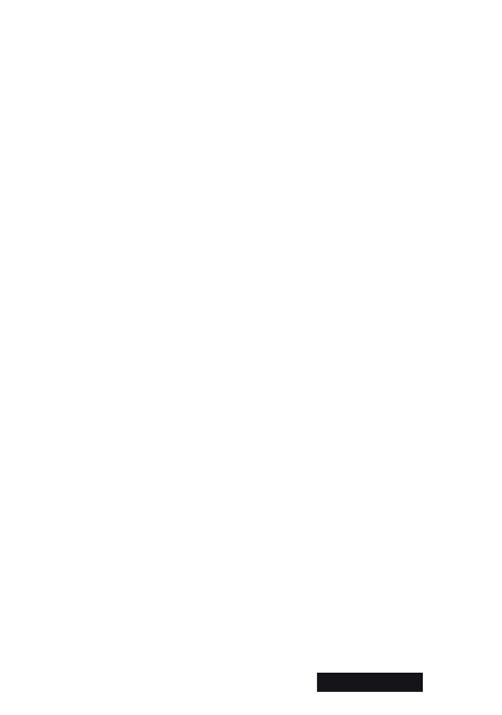
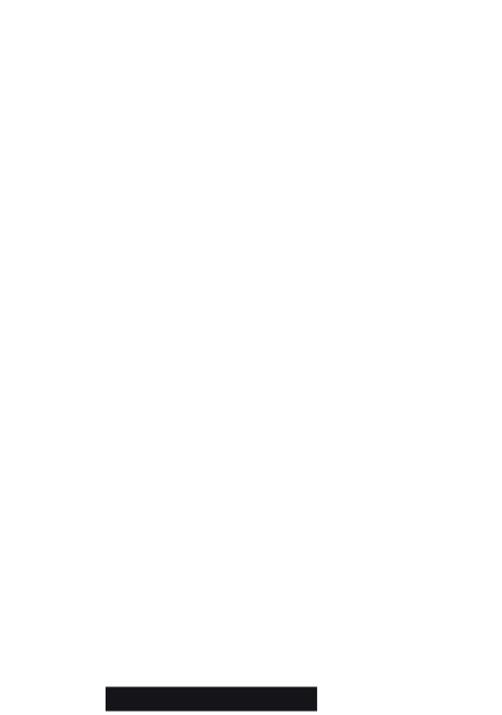
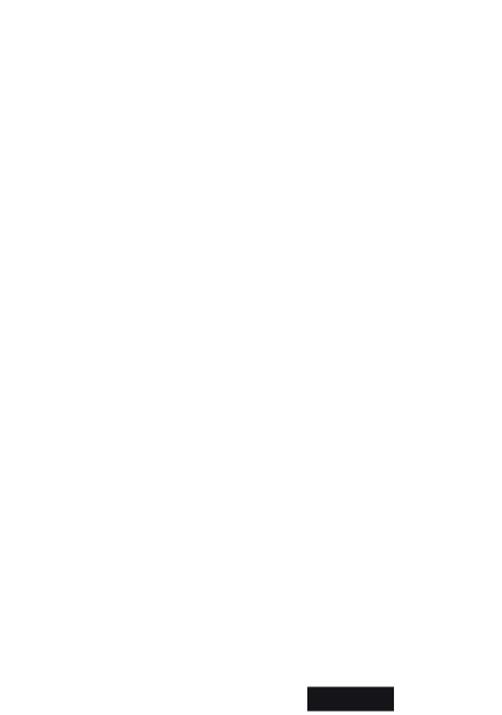
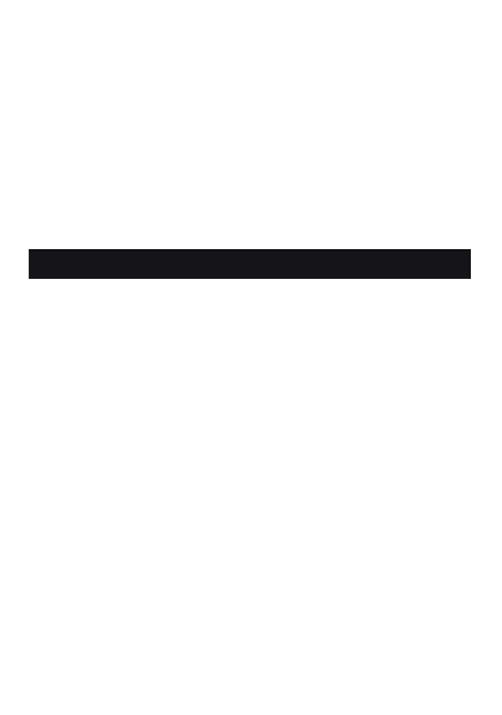
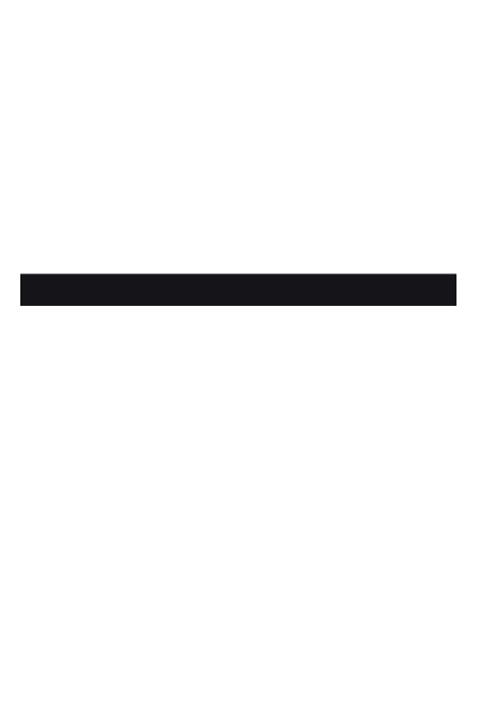
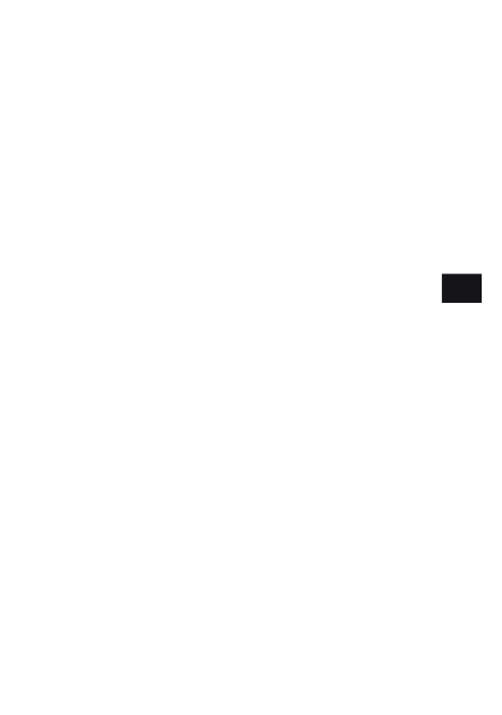

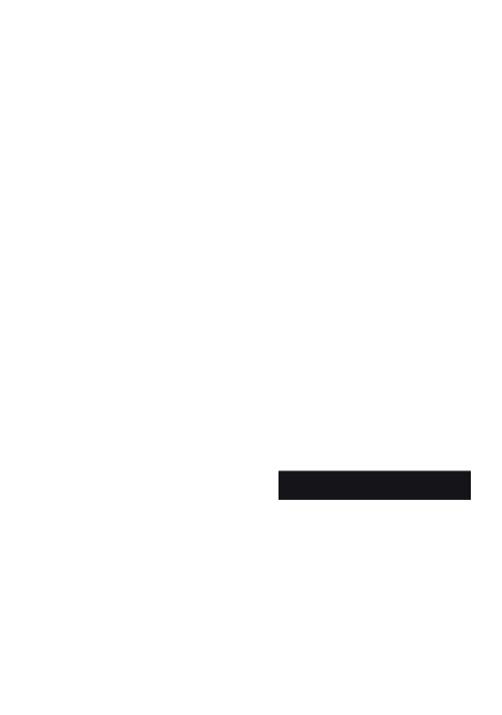

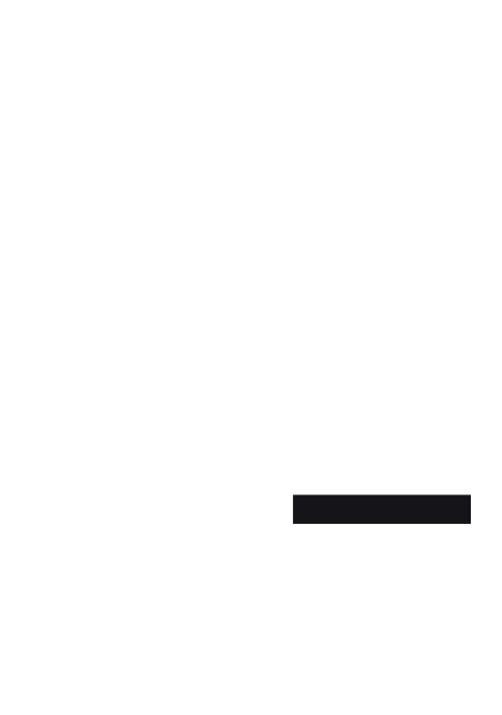

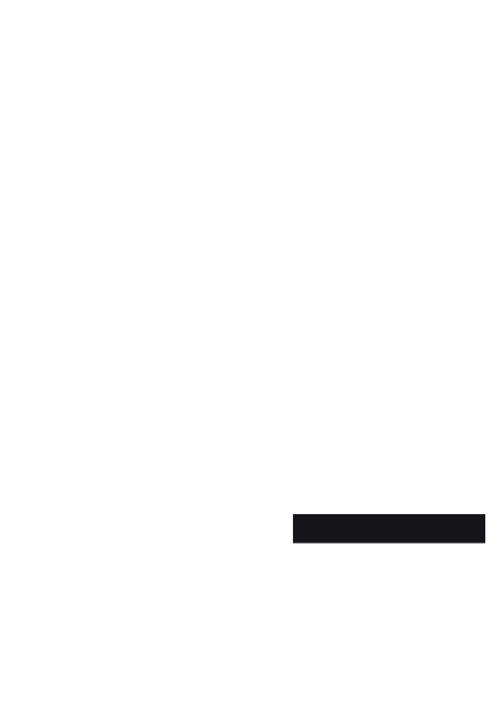
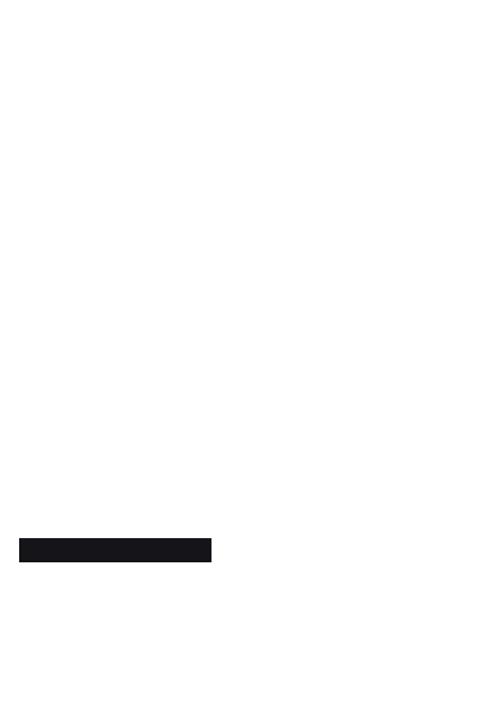
AIL NNOVATION Compact Brake IBB10
Lightest brake application on the railway market designed for UIC freight wagon Allows easy assembly and disassembly of the Compact Brake and all single components Maintenance and overhauling by ECM workshops
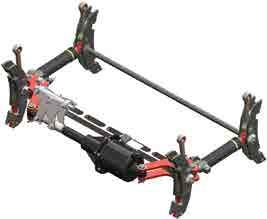
Wabtec Europe GmbH Austria Tel: +43 1 890 49 87-0 wabteceurope@wabtec.com www.wabtec.com
Wabtec Corporation (Westinghouse Air Brake Technologies) is a global provider of value-added, technology-based products and services for railways, transit, freight and other industrial markets. The company has facilities located throughout the world.
Reliable. Sustainable. Secure.
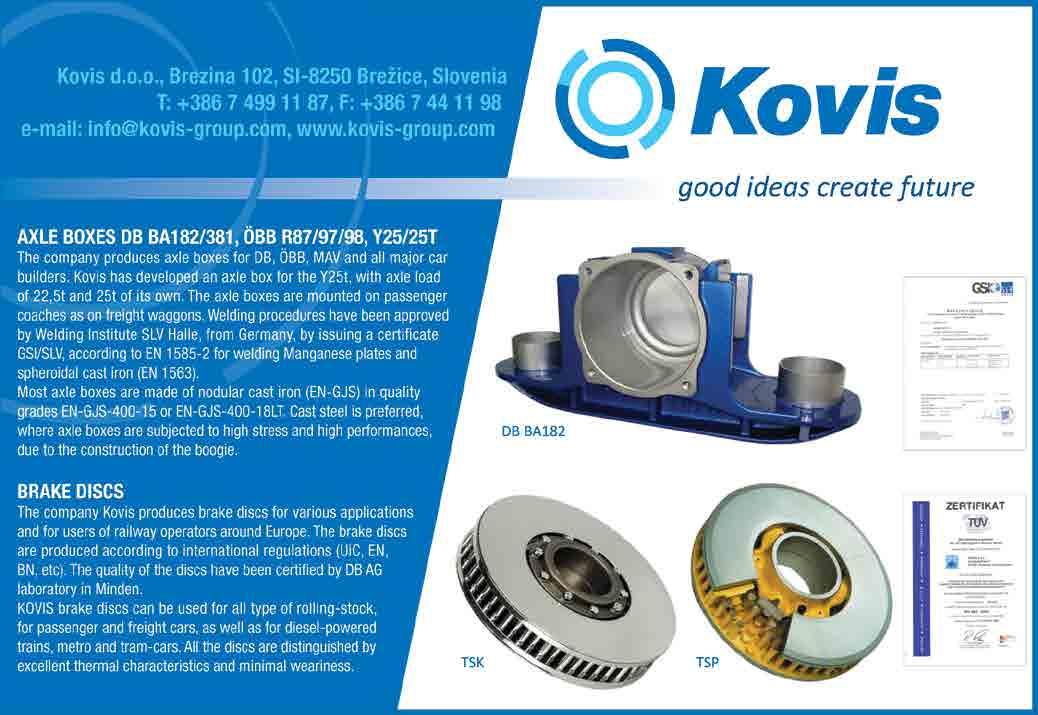
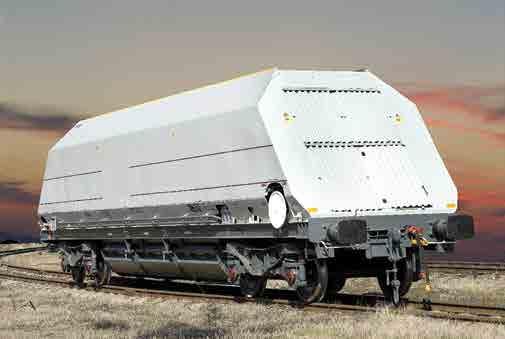
in Arad; and Astra Project, a company based in Proprad in Slovakia. Today the management of Astra is clearly focused on promoting the sustainable and long-term development of the Astra Rail Group, in its evolution into a strong financial entity and a clear market leader in its sector. At Astra Rail, therefore, long-term thinking takes precedence over short-term, profit-driven considerations.
Innovation and service driving sales
Today Astra’s key sales markets are mainly the countries of the European Union. However, since 2012 the company has been extending its geographic reach and now exports its products to Russia and the Middle East. Brown said, “As a privately owned company based
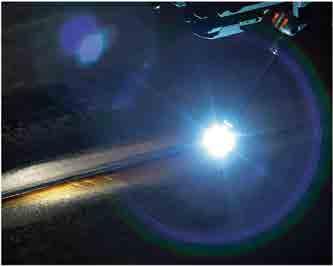
Certified to DIN ISO 9001:2008 · DIN EN ISO 3834-2:2006 DIN EN 1090-1/-2 Level EXC3 DIN EN 15085-2:2008-01 Level CL1 Connecting what belongs together
Research, development and innovation – a triad that is both maxim and aspiration for Ferro Umformtechnik.
Cutting technology • Laser technology Working range 5,200 x 31,000 mm
Material thickness up to t = 20/25 mm
• Fine plasma cutting technology Working range 6,000 x 27,000 mm
Material thickness up to t = 40 mm Bending technology Work length up to 28,500 mm
Press power up to 4,400 t
Laser welding technology Working range for sheet metals 6,000 x 25,500 mm Working range for profiles 13,000 mm
Welding technology • Component and assembly manufacturing
Construction Laser-welded side wall Length 18 m
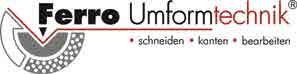
Ferro Umformtechnik
GmbH & Co. KG 48703 Stadtlohn, Germany Phone: +49 2563 - 93 37 - 0 Fax: +49 2563 - 93 37 - 999 info@ferro-umformtechnik.de www.ferro-umformtechnik.de
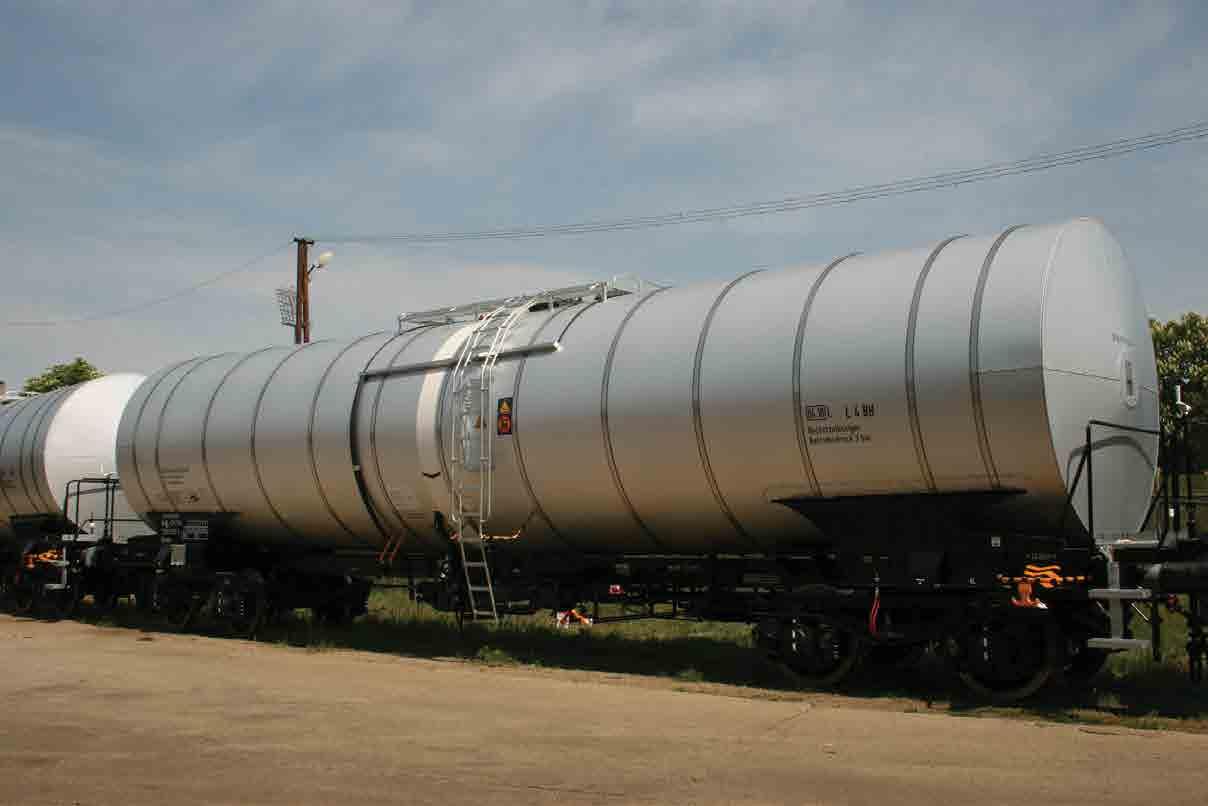
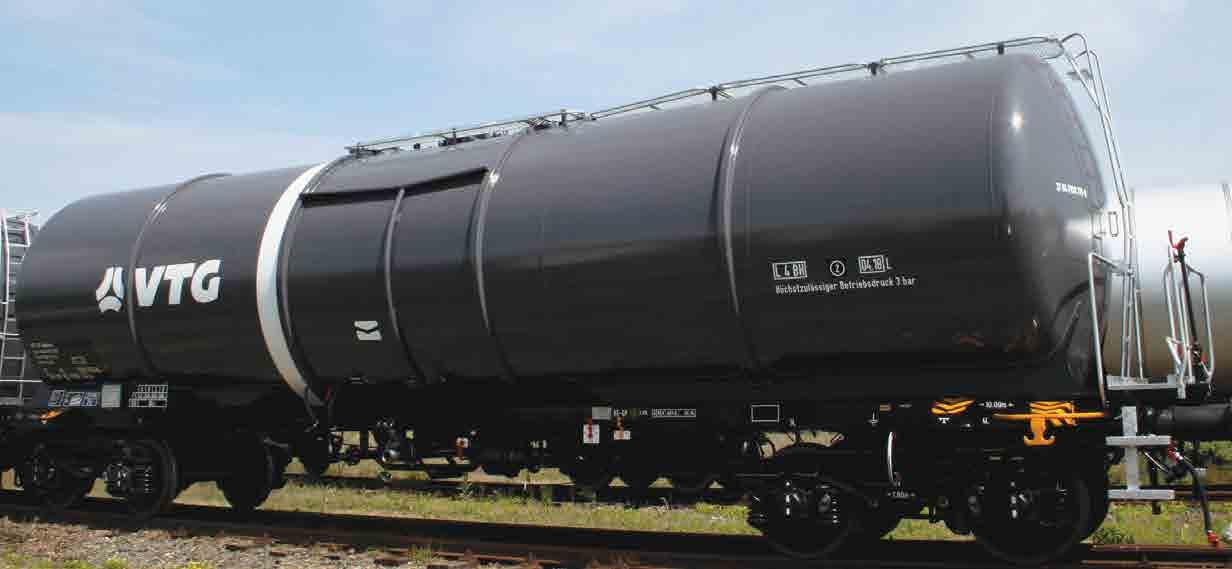
in the Netherlands, we are well placed to offer the highest quality, reliability and flexibility. In addition to our three modern factories we also manage a network of maintenance shops throughout Europe and are able to conduct all our testing programmes in-house. Our customer base is comprised of leading rail operating companies and we have more than 60 highly qualified and dedicated design engineers serving them, as well as our own state-of-the-art testing facility located in-house.
“We are a very lean, efficient and reliable company and pride ourselves on the service we offer our customers, as well as in the high standards of our products. We are getting more and more involved in the design and manufacture of highly complex special projects and introducing new technologies in the development of multi-functional freight wagons. Our main European markets are Germany, France, England, Switzerland and France. However, we’re seeing consistent growth in new markets such as the United Arab Emirates, Russia and the USA.
“We continue to invest heavily in new technology and now have the latest laser-cutting machines and employ robotics for many stages of our manufacturing processes. We always like to look at things in the


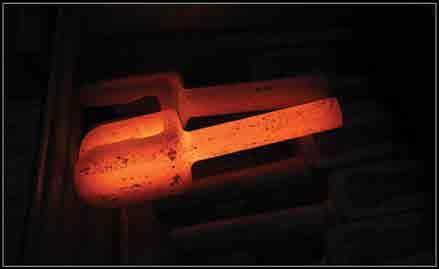

MSV Metal Studénka, a.s. is a leading modern forging shop and the largest European supplier of forgings and rolling stock subassemblies for railways, which annually exports 80% of its production to roughly 22 countries across Europe, Africa and Asia.
A er two years of heavy investment we recognized a signi cant improvement in our production process, thanks to which we maintain our leading position in the production of bu ers, screw couplers, draw hooks, draw gears and most of the spare parts for railway wagons and bogies. We deliver the forgings and stampings heat-treated, painted and we are increasingly focusing on their machining. Customer interest is growing mainly for the supply of an innovative mass-produced bu er and draw gear. We are continuously expanding our product portfolio with the objective to provide comprehensive supplies to all sectors – key manufacturers as well as railway wagon repair shops. Over the last two years we have invested EUR 5.2 million in new technologies, which has enabled us to reduce the energy demands of production, increase the productivity of the workplaces and raise the quality of our products. We are going to continue our investments in future – our investment plan for the next two years shall reach the amount of EUR 4.6 million.
All of our key products undergo a series of qualitative and supplier audits each year, and some of these products have been upgraded this year by obtaining the certi cation by Noti ed Body, which moves us another step ahead of our competition. MSV Metal Studénka, a.s. R. Tomáška 859 742 13 Studénka Czech Republic +420 556 472 202 obchod@msvmetal.eu www.msvmetal.eu
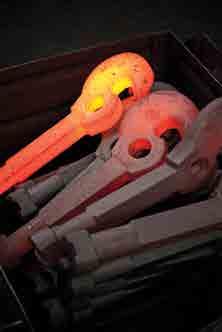
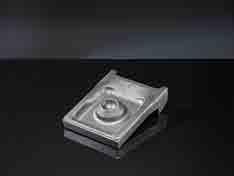
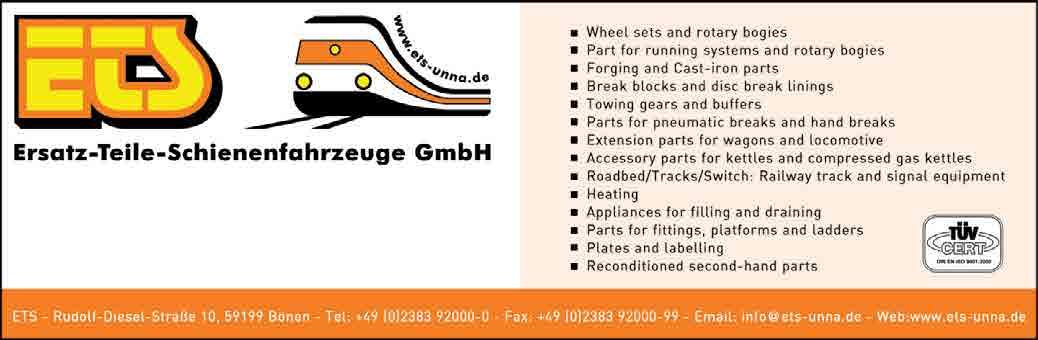
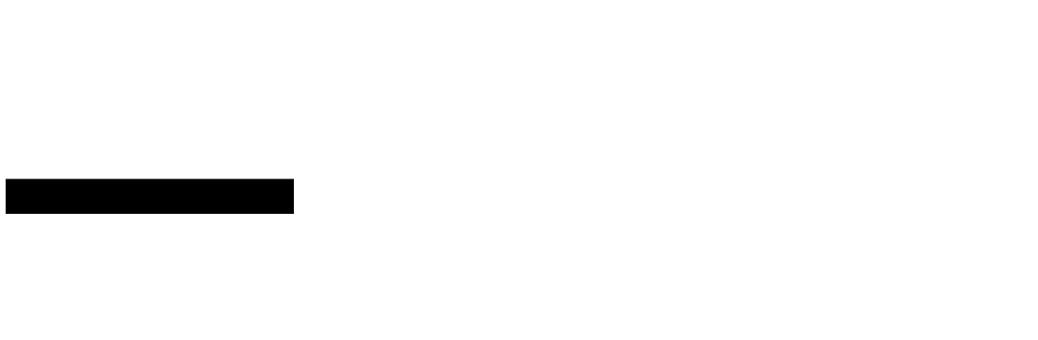

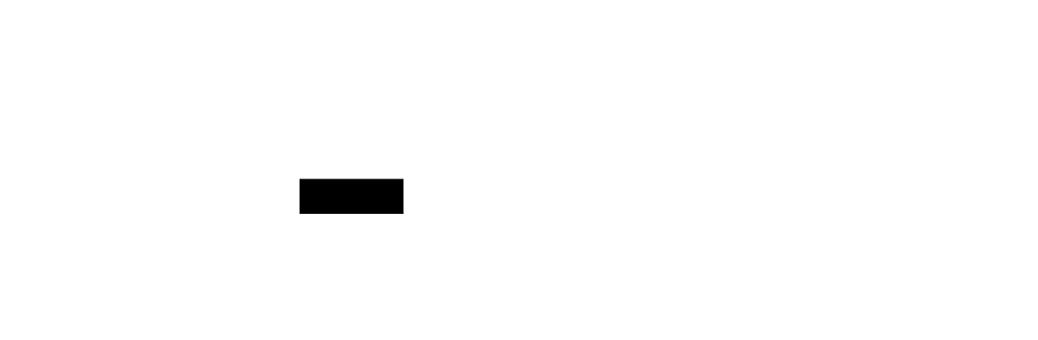
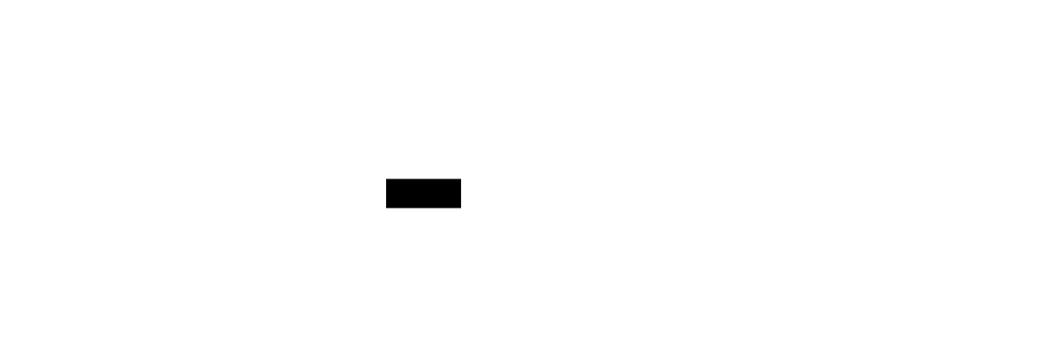
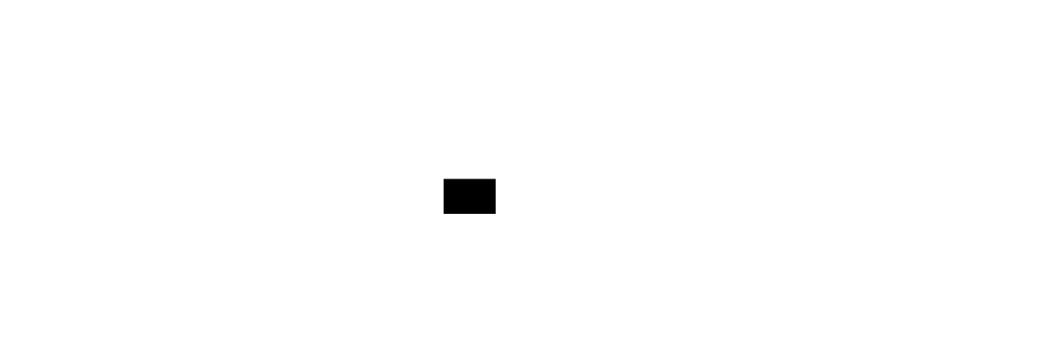
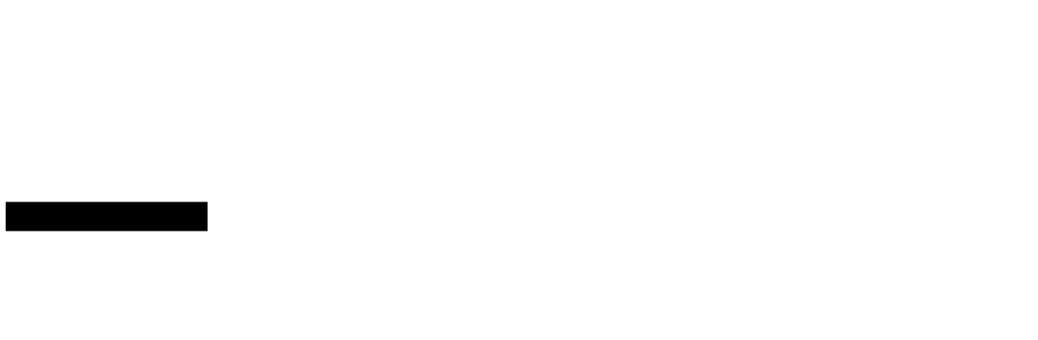

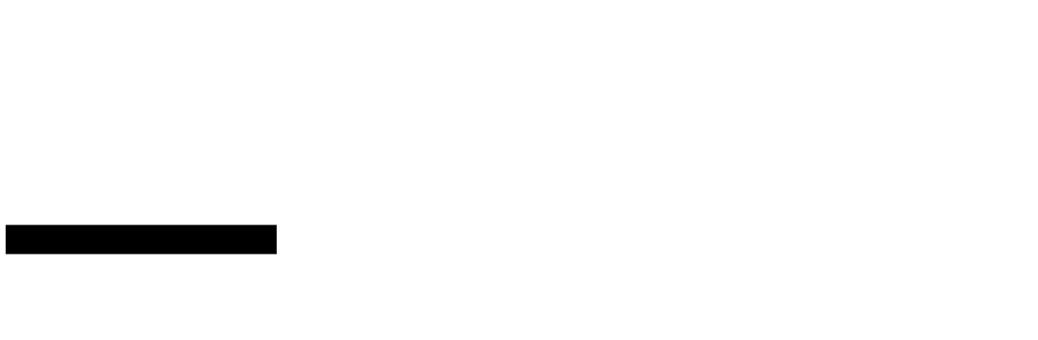
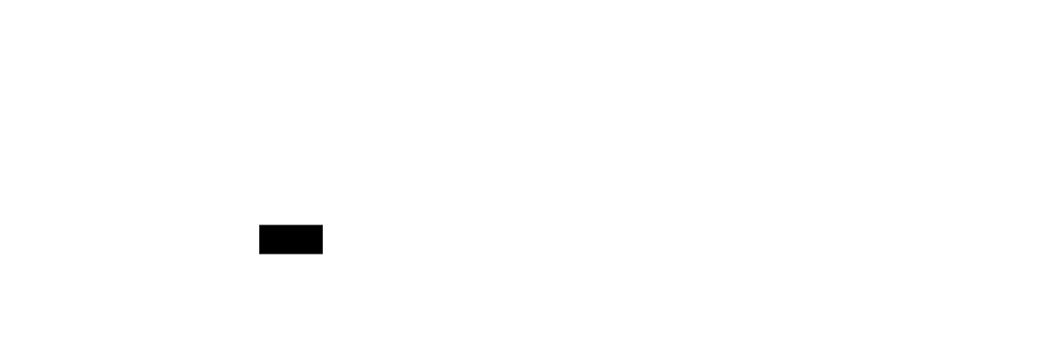
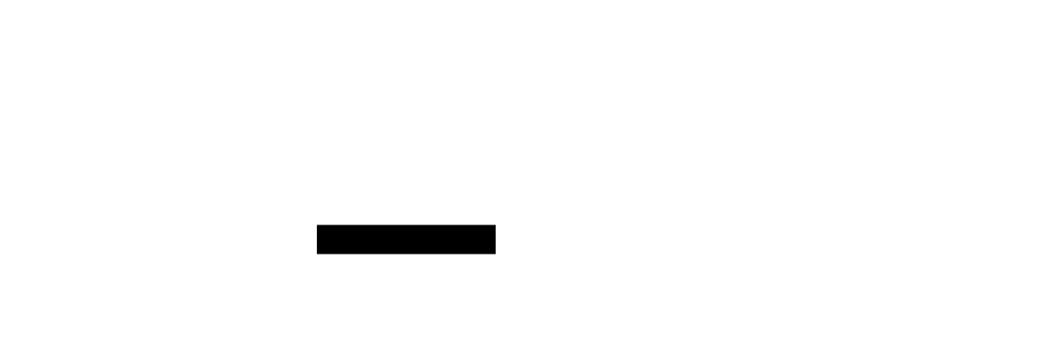
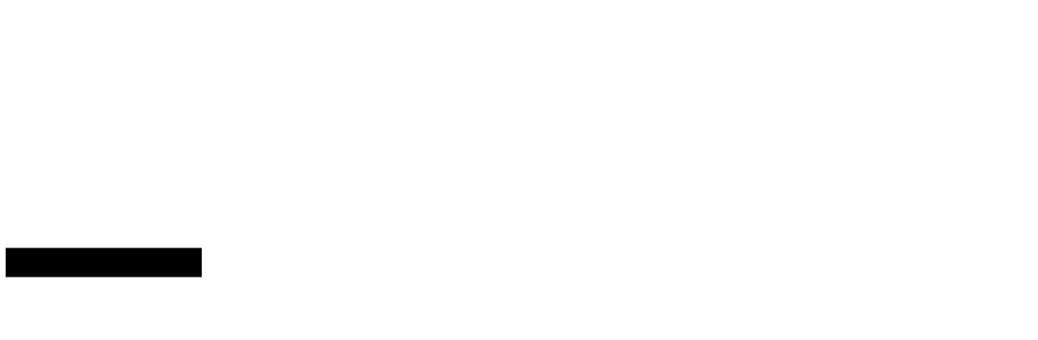
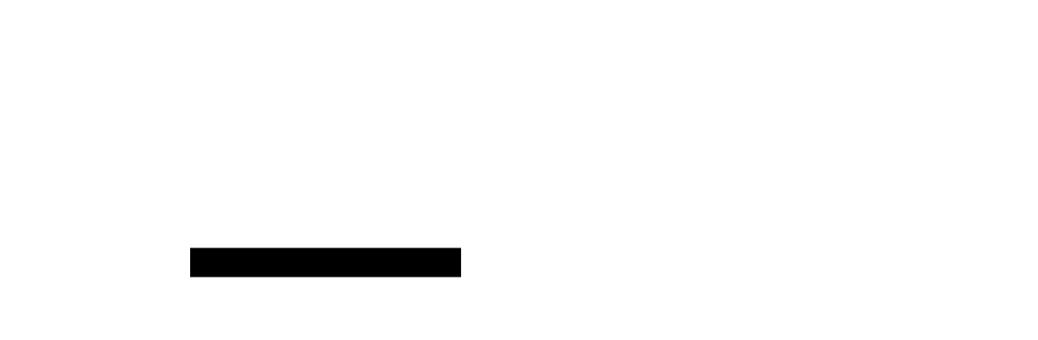
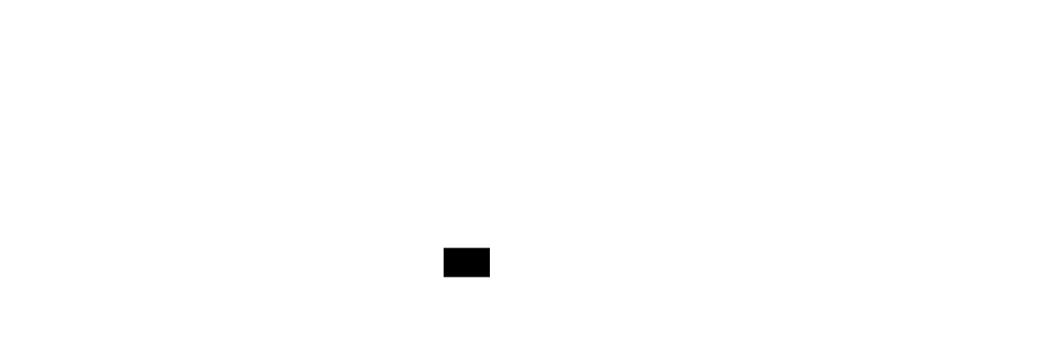


long-term and develop mutually beneficial relations with our clients. In fact, many of our rail operator customers have been with us for many, many years.”
Increasing demand for special freight wagons
The demand for individual high-spec rail cars and freight wagons has kept the company’s two specialist subsidiaries very busy. ICPV and Astra Rail Project operate as Astra’s construction and development teams as well as operating its in-house, independent testing laboratories. These two engineering offices develop railcars and bogies for in-house production and are commissioned by external companies to carry out advanced development contracts. The whole value chain is encompassed by their services, from technical analysis, consultancy and execution, through to technical acceptance that includes final testing and approval.
A good example of recent developments in special contracts can be seen in the company’s latest ‘Super Self Discharging Train’. This vehicle is 600 metres long and consists of permanently coupled rakes, each with either six or four wagons, with an incorporated conveyer discharging system. This train is suitable for the effective transportation of gravel, ballast, sand and mixed materials. In addition, each rake consists of a power unit fitted with a diesel engine, which powers the hydraulic, electric and pneumatic systems.
Continuously enhancing quality
One of Astra Rail’s most important strategic goals is to continuously enhance the quality of its products and services. The company aims to satisfy and exceed the high expectations of its international customers on a long-term basis and to maintain its position as one of the world’s foremost manufacturers of advanced rail cars and wagons. To this end, more than 50 employees are dedicated exclusively to providing quality assurance services at all levels.
The Astra Rail management system has been certified in accordance with ISO 9001:2008, EN 14025, EN ISO 3834-2 and EN15085. This is a field where Astra Rail works together with TUV (German Technical Inspectorate) and Astra Rail has also been certified under the Deutsche Bahn’s HPQ and VPI. n For further details of Astra Rail’s latest innovative rolling stock products and services visit: www.astrarail.com
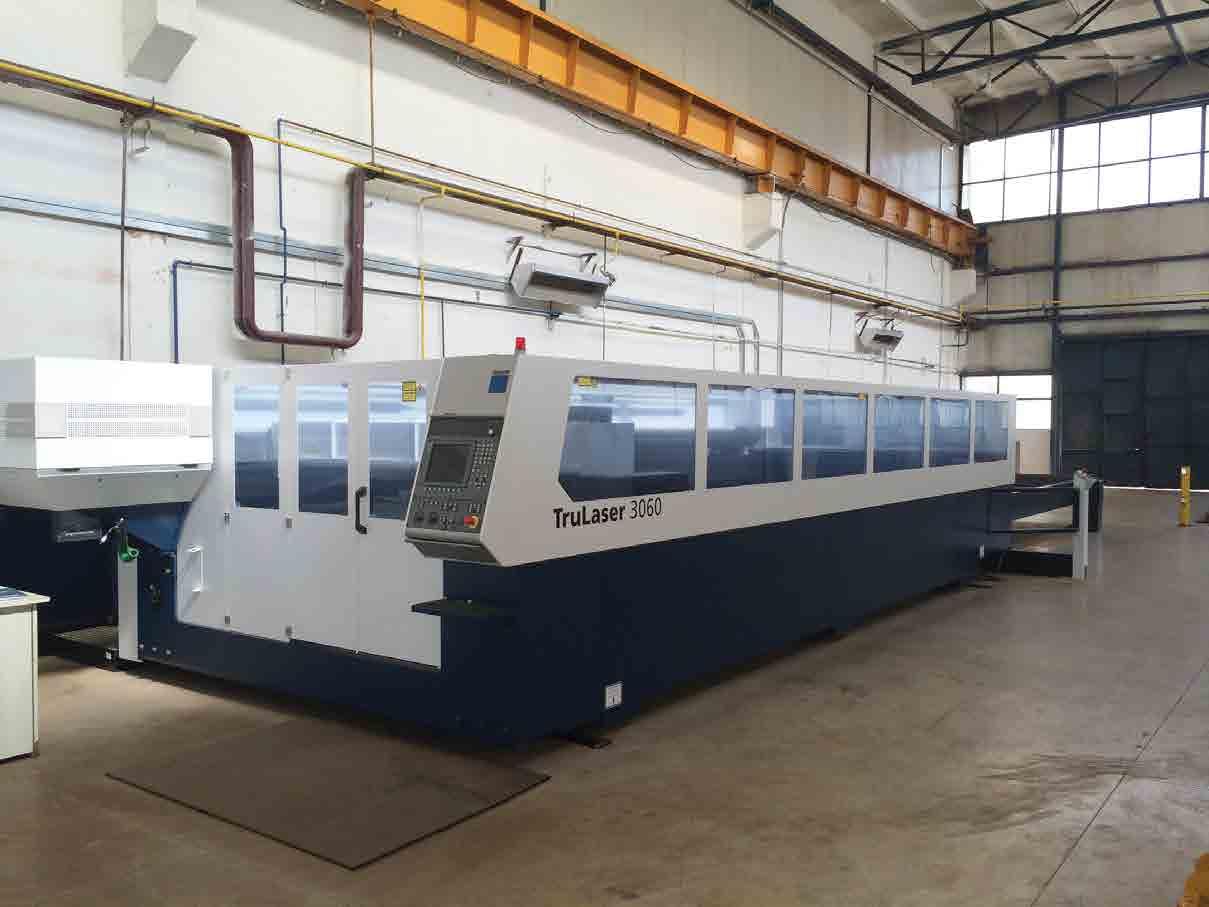