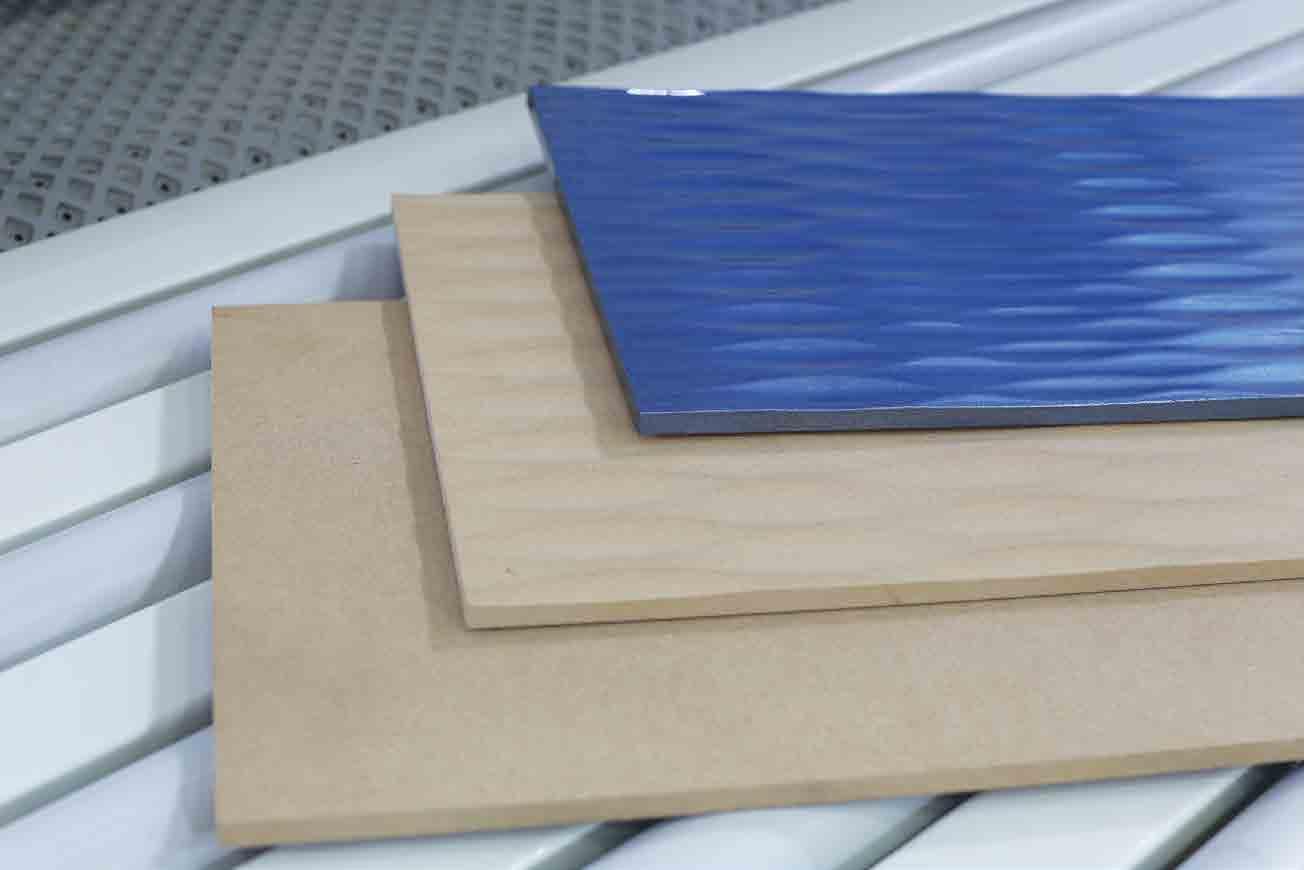
6 minute read
Wood industry specialist SCM Group
WOOD INDUSTRY SPECIALIST

The SCM Group is a leading producer of woodworking machinery, industrial components and iron castings. Laura Travierso talks to technical director Federico Ratti to find out more about its global presence and state-of-the-art solutions.


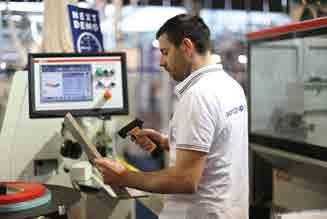

Based in Italy, for over 60 years SCM Group has designed and produced a wide range of woodworking machinery, industrial components and iron castings for various applications including furniture, door and window frames or for the nautical, aeronautical and automotive sectors.
“The company’s core business, as one can imagine, is represented by woodworking (69 per cent of sales), followed by machinery for other materials (22 per cent of sales) and industrial components (9 per cents),” begins Federico Ratti. “The Group realises 90 per cent of its turnover through exports, divided into the following areas: 47 per cent western Europe; 25 per cent America; 15 per cent eastern Europe; 9 per cent Asia and 4 per cent to the rest of the world.”
With 20 subsidiaries worldwide and over 350 selected dealers, SCM can produce the widest range of machinery for wood processing. It clients range from large industrial companies to the smallest craftsman, all supplied from its three main production sites in Italy (Rimini, Vicenza and Bergamo) and plants in China and Brazil.
Research and development
“Our R&D division has a great deal of experience which always allows us to offer the best solution for any application,” says Mr Ratti. “Our aim is to constantly develop our technology and knowhow to supply customers with high performance solutions that set the technological benchmark for the industry. The use of an advanced PLM (Product LifeCycle Management) system allows for the rationalisation of design through a rigorous process of product development and the identification of shared functional platforms and modules.”
The company has developed three dedicated centres of expertise, which are: The Csr research consortium, dedicated to studies and tests relating to vibration, acoustic optimisation, safety and operator-machine interaction, energy efficiency, dust reduction and fluid dynamics; the Dmc hi-tech research laboratory, whose goal is to design and create innovative solutions for the use of machines with flexible abrasives; and the Crif research centre for the casting industry.
Software means evolution
“Software is the most important development for this business. We are developing the software of the future, which means smart and user friendly. This means opening up new frontiers and making new projects effectively possible,” says Mr Ratti. “All those involved in the production process no longer need to be familiar with sophisticated technology programming, because the entire process know-how is contained in the software. How can we shift to this tech approach? With an advanced software dedicated to all the different machining technologies for a fully integrated software experience. In this way software is the king, and we work to make it easy to use.”
From the very beginning, SCM Group has been working with artisans, firms and large industries with the aim of developing everyday design solutions for wood products, marble, plastic,
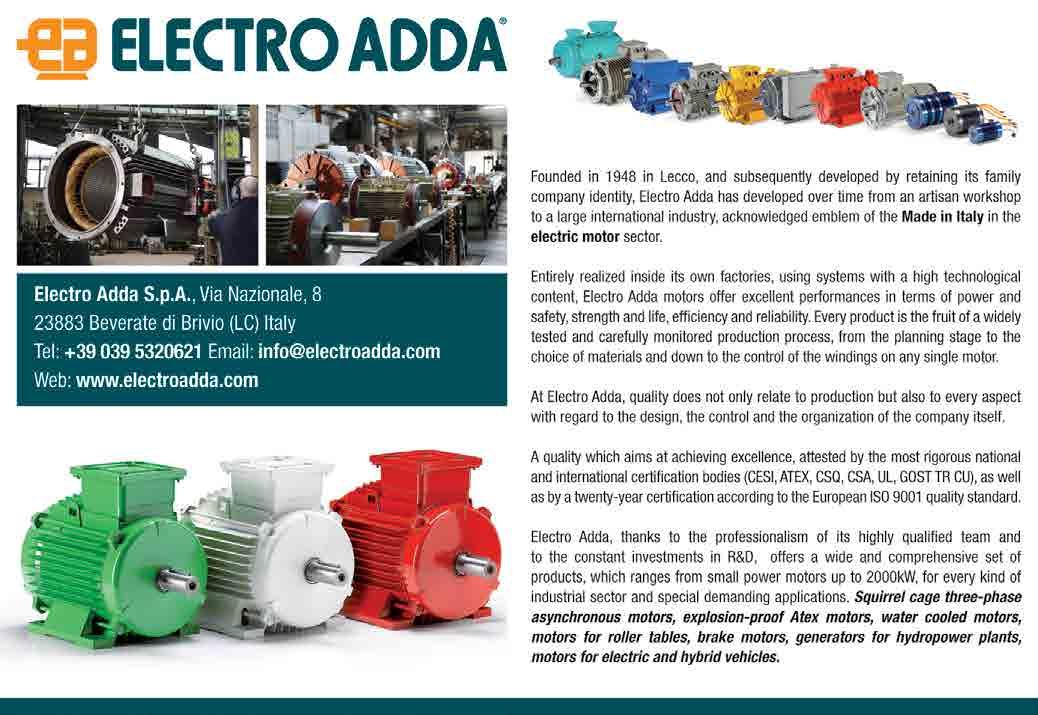
Electro Adda
Electro Adda is the reference technological partner for highly specialized companies in different sectors. The ability to produce custom-made and high quality motors is highlighted in the cooperation that Electro Adda can assure to SCM GROUP.
SCM and Electro Adda have started their relationship since 1950 and they well represent the rising family companies which were destined to grow over time until today. At first, SCM work in the field of machines for woodworking starting from the “Invincibile”, a classic machine in short widespread all over the world and Electro Adda in the field of the electric motors. The relationship of mutual esteem between the founders of these two companies brought Electro Adda to develop electric motors suitable for the field of machines for woodworking and to have SCM not only as a customer but also as a Partner with whom to share their experiences.
This relationship of mutual esteem is not failed over time, in spite of the different ways and size of rise, the different type of products and manufacturing technologies.
Electro Adda still provide to SCM Group trusted and efficient electric motors that meet specific requirements, such as standard machines, working centres, plants for panel processing, systems for window and door frames, technologies for the plastic working, glass, marble and composite materials.
A relationship between SCM and Electro Adda which from the founders has come until today thanks to a collaboration that has never been stopped which continues successfully for more than 60 years.
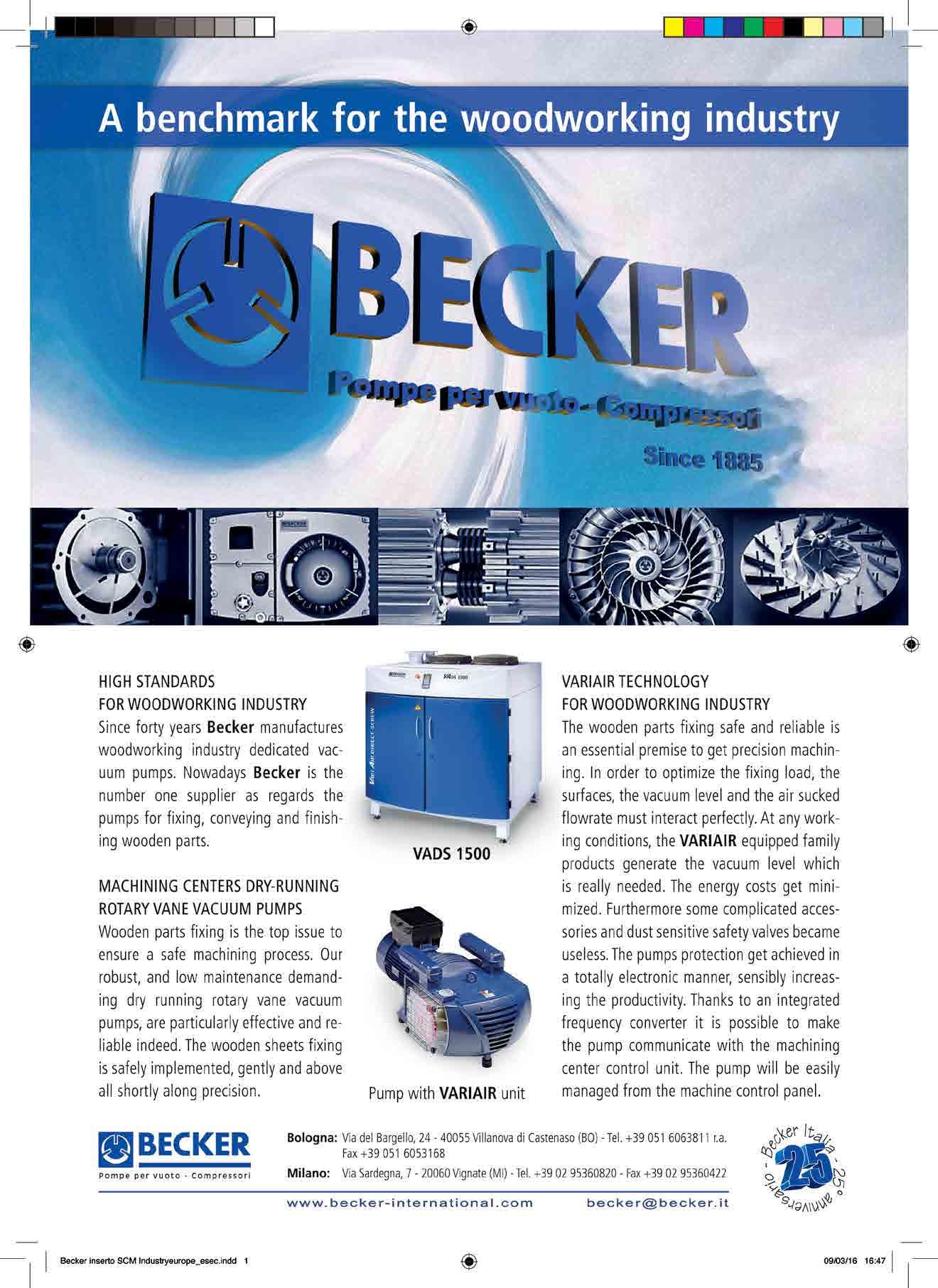
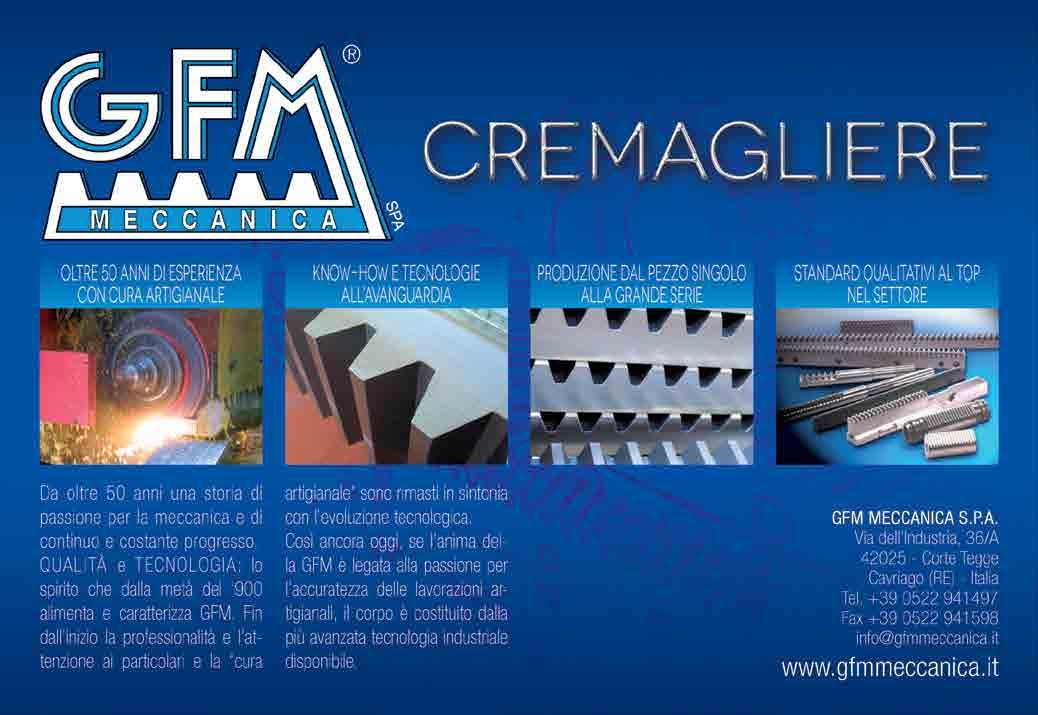
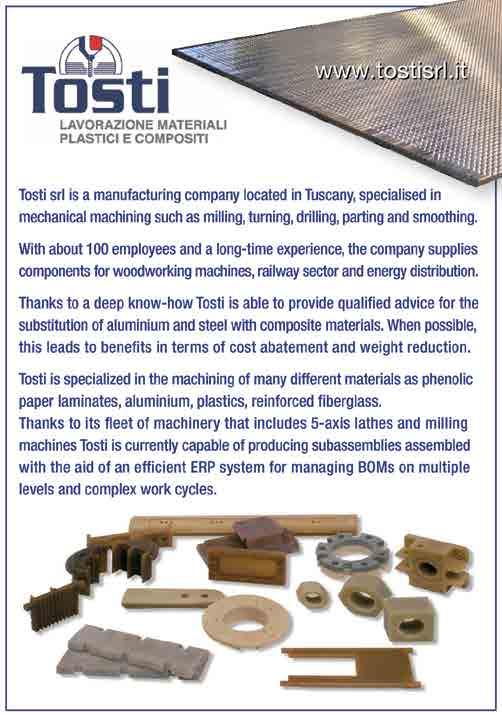
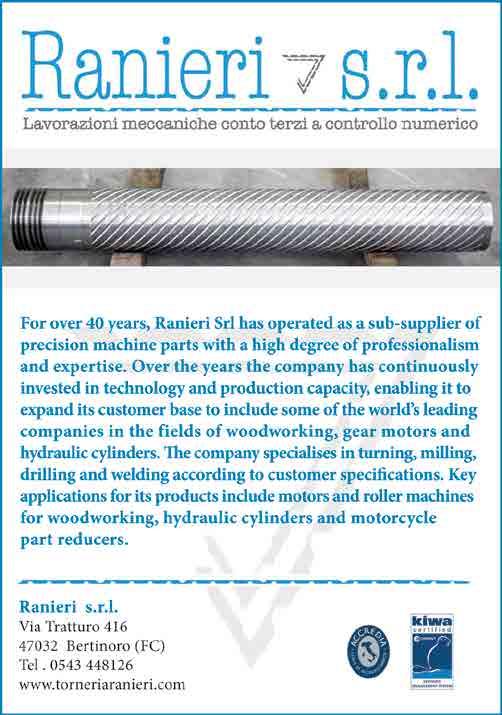
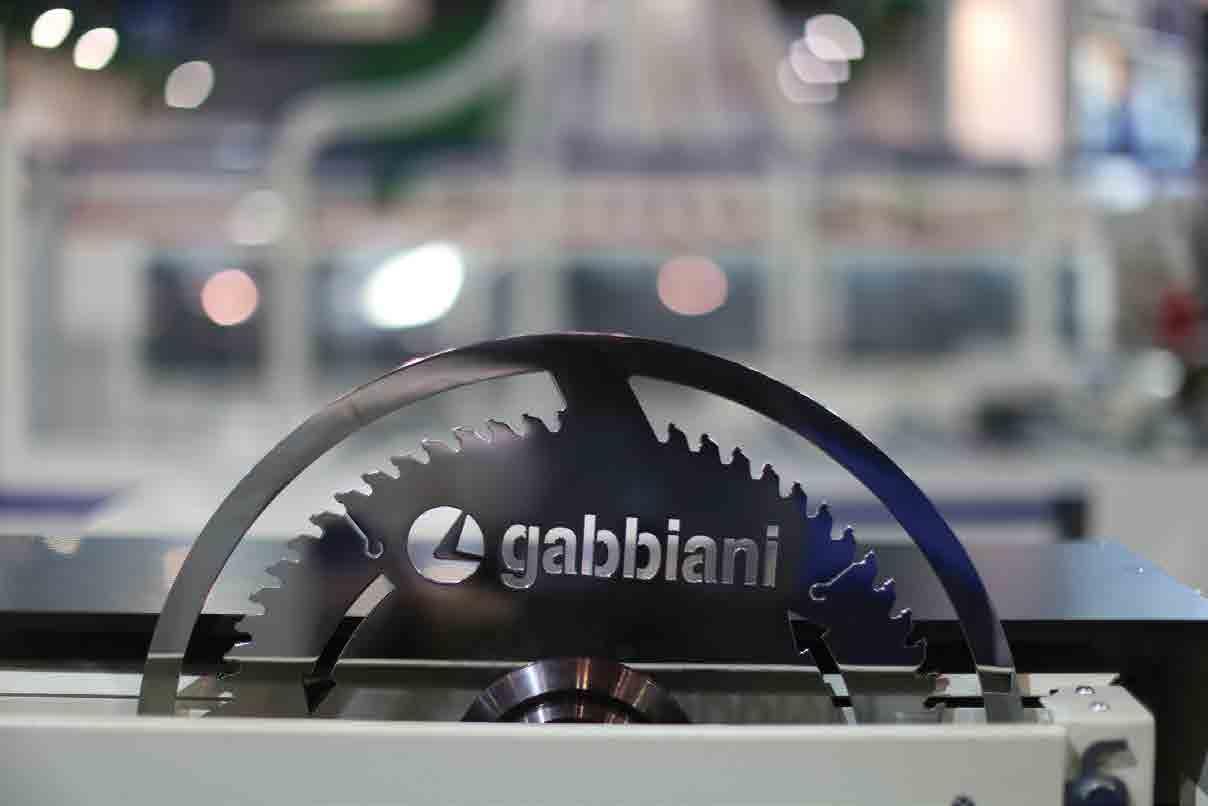
composite materials and glass. “SCM Group is now able to offer complete support in the development phase of a new project,” adds Mr Ratti, “from the research to design optimisation. We are able to follow every single phase, from the very beginning to post sale. Our partners will never be alone.”
Breaking news: Powerflex boring machine
This new automatic boring machine for furniture making is developed for large volume production in small batches. With a high quality output and absolute precision, the sturdy single-body mechanical structure ensures the absence of vibrations and can be configured with up to 26 machining heads and 660 independent spindles. All this is combined with extremely high productivity with programme changes in just a few seconds and 80m/min. axis positioning speed, thanks to the high performance of the operating units.
A new challenge: Close to the Customer
Close to the Customer is a pilot project developed in cooperation with the European Union. In essence, the concept is a local, flexible manufacturing facility for green personalised furniture (literally) Close To the Customer in terms of time, space and cost. The project will involve the construction of a working centre, equipped with an anthropomorphic robot working as a loading/ unloading system, able to automatically manage the panels stock and the feeding panels to the machine. The ultimate implementation envisions a ‘green factory behind a glass pane’ directly in the shopping mall, where the customer witnesses the manufacturing of its personalised furniture. The working area has been designed in order to support, completely automatically, all the operations such as cutting, boring, routing and tooling of wood panels in a complete range of dimensions and shapes. The system can be used by a single worker empowered by advanced HMI control and automatic machine set-up for different production batches, and will then run in a continuous flow. n

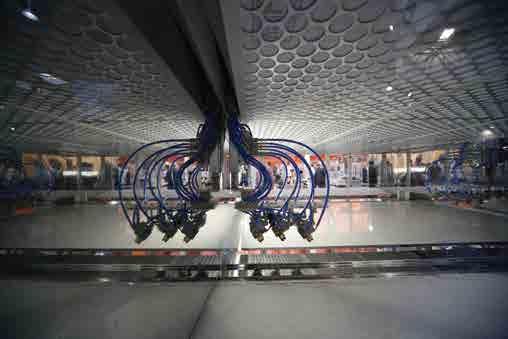
