TRUMP’S TRADE TARIFFS AND EUROPE: A TRANSATLANTIC TIFF WITH A SIDE OF CHAOS

THE FUTURE OF EUROPE'S AUTOMOTIVE INDUSTRY, ROADS AND TRANSPORT FACILITIES
THE FUTURE OF EUROPE'S AUTOMOTIVE INDUSTRY, ROADS AND TRANSPORT FACILITIES
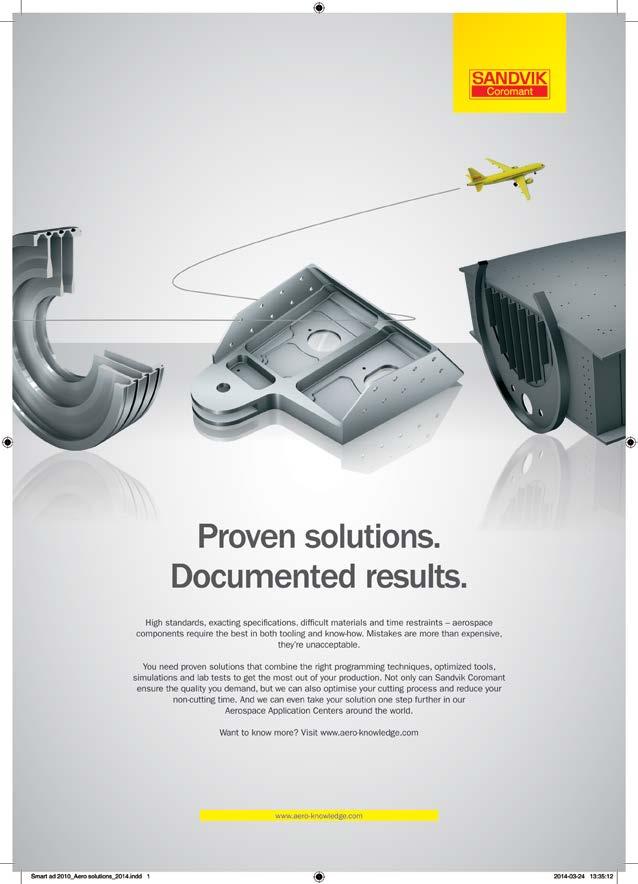
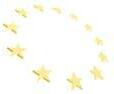
TRUMP’S TRADE TARIFFS AND EUROPE: A TRANSATLANTIC TIFF WITH A SIDE OF CHAOS
THE FUTURE OF EUROPE'S AUTOMOTIVE INDUSTRY, ROADS AND TRANSPORT FACILITIES
THE FUTURE OF EUROPE'S AUTOMOTIVE INDUSTRY, ROADS AND TRANSPORT FACILITIES
Ah, trade tariffs. They’re like that one friend who insists on bringing their own rules to game night, ruining the flow of a perfectly good Monopoly session. Back in 2018, former U.S. President Donald Trump decided the global economy needed a shake-up (because why not?), slapping tariffs on steel and aluminum imports. Europe, naturally, was not amused. What followed was a transatlantic economic spat that had all the drama of a Shakespearean play—if Shakespeare wrote about WTO disputes and the price of cheddar cheese.
In true Trumpian fashion, the tariffs arrived with all the subtlety of a bull in a china shop.
The U.S. imposed a 25% tariff on steel and a 10% tariff on aluminum, citing national security concerns. Because nothing screams "national security" like European aluminum used in soda cans. The European Union, being the sophisticated and principled entity that it is, responded with a mix of outrage, retaliatory tariffs, and the kind of passive-aggressive diplomacy usually reserved for family reunions.
The EU’s response was as stylish as a Milan Fashion Week runway but packed with economic firepower. Tariffs were imposed on iconic American products, including HarleyDavidsons, bourbon, and—wait for it—peanut butter. That’s right. Europe took a strategic shot at America’s beloved PB&J. If you wanted to watch an economic soap opera unfold, this was premium entertainment.
Harley-Davidson, caught in the crossfire, quickly decided to shift some production out of the U.S. to avoid the tariffs. Trump was not pleased, unleashing a Twitter storm that could power a small nation. Meanwhile, bourbon lovers in France had to pay more for their Ken-
tucky whiskey, and suddenly, everyone had a vested interest in transatlantic trade policies.
While Europe and the U.S. were busy playing tariff chess, businesses across the continent were left scrambling. European car manufacturers, for instance, were on high alert. Trump had hinted that cars could be his next target, and German automakers like BMW and Mercedes-Benz had heart rates higher than a contestant on a reality TV elimination round.
Trump’s trade tariffs reminded Europe—and the world—of a few key lessons. First, economic policies have consequences beyond political soundbites. Second, peanut butter is a surprisingly effective weapon in trade disputes. And finally, if you mess with the price of whiskey and cheese, be prepared for some very disgruntled Europeans.
Additionally, European farmers who exported to the U.S. found themselves caught in the fray. The cheese industry, which relies on transatlantic trade, faced uncertainty. Imagine a world where brie and camembert were harder to find in American supermarkets. A true catastrophe for brunch enthusiasts.
The tariffs didn’t just spark a U.S.-EU spat. They also threw a wrench into global supply chains. As steel prices rose, industries from construction to canning were forced to make adjustments. European manufacturers who
relied on American materials suddenly had to rethink their entire strategy. Meanwhile, China—never one to miss a good economic opportunity—started cozying up to Europe, offering trade deals and whispering sweet nothings about free markets.
As with all good dramas, the Trump-era tariff war didn’t end in a tidy resolution. Over time, negotiations took place, some tariffs were lifted, others remained, and everyone involved looked at each other like two kids caught fighting over the last piece of cake.
When President Joe Biden took office, he approached the issue with a little more diplomacy. Some tariffs were eased, and discussions reopened, but the scars remained. The EU and U.S. realized that while they may have their differences, economically, they were kind of stuck with each other—like an old married couple that bickers but ultimately stays together because the alternative is just too complicated.
Trump’s trade tariffs reminded Europe—and the world—of a few key lessons. First, economic policies have consequences beyond political soundbites. Second, peanut butter is a surprisingly effective weapon in trade disputes. And finally, if you mess with the price of whiskey and cheese, be prepared for some very disgruntled Europeans.
In the end, the tariffs were a rollercoaster ride with more twists than a season finale of Game of Thrones, minus the dragons (though some might argue Trump’s Twitter feed came close). The world learned that trade wars are easy to start, messy to manage, and often come with unintended consequences—like making Europeans genuinely angry about peanut butter for the first time in history. n
Editorial Director
Roger Sullivan
Profile Writers
Romana Moares
Dariusz Balcerzyk
Emma-Jane Batey
Director of Sale & Business Development
Katarzyna Pozoga
Art & Design studio@industryeurope.net
Editorial Office editor@industryeurope.net
Accounts accounts@industryeurope.net
Industry Europe
110 Boundary Road, Norwich NR6 5JE, United Kingdom
Tel: +44 1133 281 173
Email: studio@industryeurope.net
Web: www.industryeurope.com
LinkedIn: www.linkedin.com/company/industry-europe
©
As Europe moves toward a more sustainable and technologically advanced transport system, the future of its automotive transport facilities and road infrastructure is set to undergo significant transformation. Driven by policies focused on reducing carbon emissions, enhancing connectivity, and incorporating smart technologies, the next decades will see a shift toward more efficient and eco-friendly road networks.
One of the key developments in Europe’s future transport facilities is the integration of smart road infrastructure. Smart highways, equipped with IoT sensors, AI-driven traffic management systems, and real-time data analytics, will play a crucial role in reducing congestion and improving safety. Countries like the Netherlands and Germany are already testing adaptive roadways that can change speed limits dynamically based on traffic conditions and weather.
Additionally, road surfaces may incorporate self-healing materials, reducing maintenance costs and increasing durability. Photovoltaic roads, capable of generating solar energy, are also being explored as a means to power streetlights and even electric vehicle (EV) charging stations.
The shift toward electric mobility necessitates a robust charging infrastructure across Europe. The European Union (EU) has set ambitious targets to phase out internal combustion engine (ICE)
vehicles by 2035, which means significant investment in public and private EV charging stations. Ultra-fast chargers, capable of replenishing battery power within minutes, will become more widespread, with highway corridors equipped to support longdistance travel for EV users.
Wireless charging technology is another area of development, with dynamic charging roads that can wirelessly charge electric vehicles while in motion being tested in countries such as Sweden and Italy. These advancements will help alleviate range anxiety and promote EV adoption on a mass scale.
Autonomous vehicles (AVs) and connected cars are expected to reshape European roads. With companies such as Tesla, Volkswagen, and BMW investing heavily in self-driving technology, the future road network will need to accommodate these vehicles through enhanced digital infrastructure. This includes vehicle-to-
everything (V2X) communication, enabling vehicles to interact with traffic signals, pedestrians, and other cars to improve road safety and efficiency.
Autonomous trucking is another area poised for growth, with trials already underway in several European countries. Self-driving trucks could revolutionize freight transport by reducing costs, optimizing fuel consumption, and improving delivery efficiency through platooning technology, where multiple trucks travel in close formation to reduce air resistance.
To support Europe’s commitment to sustainability, future roads will incorporate eco-friendly materials. Recycled plastics, rubber, and bio-asphalt are being researched as alternatives to traditional asphalt and concrete. These materials not only reduce environmental impact but also enhance road durability.
Green corridors and nature-integrated roadways will become more common, with tree-lined highways acting as natural carbon sinks and noise reducers. Additionally, urban road design will prioritize pedestrian-friendly layouts, cycling lanes, and dedicated lanes for electric and shared mobility options.
As urbanization increases and demand for efficient intercity travel grows, Europe is expected to invest in high-speed road networks. The development of smart motorways and express lanes will facilitate seamless transportation, reducing travel time between major cities. The expansion of cross-border road networks, supported by EU funding, will enhance connectivity within the region, supporting economic growth and regional integration.
Hyperloop-inspired transport systems, which involve highspeed pods traveling in low-pressure tubes, may also become a reality for ultra-fast road-based travel, complementing traditional automotive transport.
European cities are increasingly adopting smart traffic management systems to address congestion and pollution. AI-powered traffic lights, predictive analytics, and digital twins (virtual replicas of real-world road networks) will optimize traffic flow, reducing delays and emissions.
Many cities are also implementing congestion pricing and lowemission zones (LEZ) to limit the number of polluting vehicles on the roads. Car-free city centers, such as those in Oslo and Madrid, serve as models for future urban transport planning, encouraging the use of public transport, cycling, and walking over private car ownership.
While Europe’s future road infrastructure holds immense promise, several challenges must be addressed. The transition to EVs and AVs requires substantial investment in digital connectivity, road adaptations, and public acceptance. Cybersecurity concerns associated with connected vehicles need to be managed to prevent hacking risks.
Moreover, equitable access to EV charging stations and smart road infrastructure must be ensured, particularly in rural and less developed areas. Policymakers will need to balance innovation with affordability, ensuring that technological advancements benefit all citizens.
Europe’s future automotive transport facilities and roads will be defined by sustainability, innovation, and digital transformation. Smart highways, extensive EV charging networks, autonomous vehicles, and environmentally friendly road materials will shape the next era of transportation. While challenges remain, the vision for a cleaner, more efficient, and interconnected transport network is steadily becoming a reality. Through continued investment and collaboration, Europe is set to lead the way in revolutionizing automotive transport for future generations. n
Swift Engineering, a leader in advanced solutions for unmanned and manned aviation as well as a range of other critical applications, has been honored as Innovator in Aerospace by the Internet Marketing Association (IMA).
Swift Engineering provides a full-service resource that encompasses R&D, product development, engineering and manufacturing, from prototype to complete vehicle architecture and packaging. These capabilities support programs for an array of components, systems and vehicles in both aviation and aerospace, notably in the area of unmanned platforms.
"We are very pleased to receive this important recognition from a professional organization like of expertise," said Dr. Hamed Khalkhali, President of Swift Engineering. "Our goal is to deliver transformational solutions that impact peoples lives through advancements in technology."
Most recently, the company achieved a major milestone for its SULE (Swift Ultra Long Endurance, a HAPS platform) aircraft in a flight
that reached 55,904 ft. MSL (Mean Sea Level).
The groundbreaking, 24-hour flight opened up new possibilities for scientific research and environmental monitoring as well as defense and aerospace applications.
The IMA IMPACT Award is one of the most respected honors in the professional business world, recognizing organizations that demonstrate excellence in innovation, leadership and global influence.
IMA (www.imanetwork.org) is one of the fastest growing and largest Internet marketing groups in the world, with professional members in fields including sales, marketing, business ownership, programming and creative development. It provides a platform where proven Internet marketing strategies are demonstrated and shared to increase members value to their organizations.
Thales Alenia Space signs contract with ESA to develop the Argonaut Lunar
ThalesAlenia Space, joint venture between Thales (67%) and Leonardo (33%), has signed a contract with the European Space Agency (ESA), worth € 862 Million, related to the design, the development and the delivery of the Lunar Descent Element (LDE) for ESA’s Argonaut Mission, including responsibility for mission design and integration.
Planned to be launched from the 2030s, Argonaut will deliver cargo, infrastructure and scientific instruments to the Moon’s surface.
The first mission is envisioned to deal with delivery of dedicated navigation and telecommunication payloads as well as energy generation and storage system, as European enterprises to explore the Lunar southern area.
The Argonaut spacecraft consists of three main elements: the lunar descent element (LDE) for flying to the Moon and landing on the target, the cargo platform one, which is the interface between the lander and its payload, and finally, the element that the mission designers want to send to the Moon.
Adaptability is a key element of Argonaut's design, which is why the cargo platform is designed to accept any mission profile: cargo for astronauts near the landing site, a rover, technology demonstration packages, production facilities using lunar resources, a lunar telescope or even a power station. The project will strengthen Thales Alenia Space’s skills in several technological areas essential to space exploration beyond the Moon.
The future space ecosystem requires new solutions dedicated to the transport and return of cargo from low Earth orbit and lunar orbit, as well as crew transport to low Earth orbit. Thales Alenia Space is ready to put in place what is needed to prepare for humanity’s future life and presence in Space, laying the foundations for the post-ISS era and meeting new economic needs for research and science.
Thales Alenia Space is the prime contractor for the development of the Lunar Descent Element. The overall mission responsibility, ie the use of the LDE and integration with payload, will be the subject of a separate procurement in the future. The Lunar Descent Element is an independent architecture block of the international lunar exploration activities, namely a versatile system to support a variety of missions.
As prime contractor and system integrator of the Lunar Descent Element, Thales Alenia Space in Italy will lead the industrial consortium that will be responsible for the system, the entry descent and landing aspects, as well as the general and specific architectures of the thermomechanical, avionics and software chains. Thales Alenia Space in France and in the UK will respectively focus on data handling systems and propulsion. OHB System AG as
additional core team member of the Thales Alenia Space consortium will be responsible for guidance, navigation and control (GNC), electrical power systems (EPS) and telecommunications (TT&C) aspects.
Drawing on over 40 years of experience and a unique combination of skills, expertise and cultures, Thales Alenia Space delivers costeffective solutions for telecommunications, navigation, Earth observation, environmental management, exploration, science and orbital infrastructures. Governments and private industry alike count on Thales Alenia Space to design satellite-based systems that provide anytime, anywhere connections and positioning, monitor our planet, enhance management of its resources and explore our Solar System and beyond. Thales Alenia Space sees space as a new horizon, helping to build a better, more sustainable life on Earth. A joint venture between Thales (67%) and Leonardo (33%), Thales Alenia Space also teams up with Telespazio to form the parent companies’ Space Alliance, which offers a complete range of services. Thales Alenia Space posted consolidated revenues of approximately €2.2 billion in 2023 and has around 8,600 employees in 8 countries, with 16 sites in Europe.
The23 EU nations that are also NATO members are expected to agree on increasing the defense spending target beyond the current 2% of national output at the alliance’s June summit, where a new level will be set, European Council President Antonio Costa said.
U.S. President Donald Trump has been urging NATO allies to raise defense spending to 5% of gross domestic product (GDP)—a goal that none of the 32 NATO members, including the United States, currently meets. Costa has scheduled an informal meeting of European Union leaders next Monday to discuss defense and security investment, he said in an interview with Portuguese public broadcaster RTP late on Wednesday.
NATO Secretary-General Mark Rutte and British Prime Minister Keir Starmer will also attend the meeting, he added.
According to Costa, the collective defense spending of the 23 EU nations within NATO already meets the 2% target, following a 30% increase since Russia’s invasion of Ukraine in February 2022. "There is a very reasonable consensus among member states to continue on this path," he added.
"I would anticipate that, surely, at the next NATO summit in June, a target higher than 2% will be set," Costa said. "Whether it's 5%, whether it's 3%, I don't know, it's a decision that member states will make within NATO."
The European Council, led by Costa, represents the national governments of the EU’s 27 member states. Analysts and officials have told Reuters that spending 5% of GDP on defense would be politically and economically unfeasible for most NATO members, as it would require billions of dollars in
additional funding. However, they believe allies are likely to agree to exceed the current 2% target at the June summit.
Costa, a former Portuguese prime minister, identified Russia as NATO’s primary threat and emphasized the need for countries to focus on strengthening air defense, anti-missile, and electronic warfare systems. He noted that investing in defense technology and industry would also enhance the EU economy’s competitiveness and suggested that, eventually, there would need to be a discussion on "common funding" for collective defense.
France and the Baltic states are advocating for joint European Union borrowing to finance defense spending. The outcome of that debate may hinge on next month’s national election in Germany, which has so far opposed the idea.
BAE Systems has been awarded a £285m contract by the Ministry of Defence to support the Royal Navy’s Shared Infrastructure, Combat Management Systems (CMS) and warship networks
RECODE is an eight-year programme ensuring the Navy’s fleet is armed and ready for evolving military challenges. It is tailored to meet the Royal Navy’s future operational needs and will deliver a modernisation programme at pace to enable the agile deployment of capabilities.
The contract award builds on 13 years of collaboration with the Royal Navy in which the BAE Systems’ CMS is used across a wide range of naval assets.
The core elements of RECODE include:
• Maintaining high levels of safety, security and availability of combat systems across 20 Royal Navy ships. Architectural and capability changes delivered directly to the fleet to keep pace with the operational tempo.
• Delivering BAE Systems’ CMS on the Queen Elizabeth Class aircraft carriers, Type 45 destroyers and Type 26 frigates. The whole RECODE enterprise will adopt the engineering principles of DevSecOps1, with security integrated at every phase of the software development and operational lifecycle. This agile methodology will deliver the best CMS capability in the shortest amount of time.
• A new collaborative working philosophy with DE&S Maritime Combat Systems and Navy Command which will mean closer working, joint decision-making and increased communication and collaboration between both parties.
RECODE will support more than 200 highly-skilled jobs at BAE Systems’ Naval Ships business across the Company’s sites in Filton, Dorchester, New Malden, Frimley and Portsmouth. It will also create additional investment in UK SME and high-tech suppliers across the UK.
Steve Carter, Naval Ships Combat Systems Director, BAE Systems, said:
“RECODE represents a huge stride forward in our partnership with the Royal Navy
and will help to realise warfare capability of the future. The global threat picture, advances in commercial technology and the immense volume of data available to crews means we need to become even more ambitious and far-reaching in our services and support. We are excited and privileged to secure this programme that will sit at the heart of the Navy’s ambition to be a protean force.”
Commodore Phil Game, Interim Director of Sense, Decide and Communicate, DE&S, said:
"This is an essential programme that will sustain current combat management systems on board in-service Royal Navy vessels, to enhance their capability and make them fit for the future. This new programme will ensure that at their core, the systems are evergreen, robust and flexible.
“Through our close collaborative work with industry colleagues, this contract will also help to upskill the programme's workforce and sustain UK jobs. The improvements made will be instrumental in making the UK Royal Navy more agile and more capable in our rapidly changing global Defence environment."
Captain Kevin Miller, Combat Systems Design Authority and Surface Ships Combat Systems Group Team Leader, Royal Navy, said:
“We have a long and successful history with Naval Ships Combat Systems and RECODE represents an important next phase of our collaboration. Today’s challenging landscape means we must adapt and evolve at pace. Agility is at the heart of the programme in three ways – equipment to maintain our capability, process so we can adapt that capability at the pace of relevance and a mindset to ensure we deliver. Those are the key facets that will enable the military advantage our crews are relying on.”
The BASF Group’s sales for the full year 2024 are expected to be €65.3 billion (2023: €68.9 billion). This is in line with the figure estimated by analysts on average according to Vara. While volumes slightly increased, sales prices declined but showed a steady price recovery throughout 2024 compared with the respective quarter of the previous year. Currency effects negatively impacted the sales development.
Income from operations before depreciation, amortization and special items (EBITDA before special items) for 2024 is expected to be €7.9 billion, which is at the level of the average analysts’ estimates for 2024 (Vara: €7.9 billion) and slightly below the range forecast by BASF in February 2024 of €8.0 billion to €8.6 billion. The most recent earnings expectation was at the low end of this range. In 2023, EBITDA before special items was €7.7 billion. The increase compared with the previous year was due to higher earnings in the core businesses, primarily driven by increased volumes. In the fourth quarter of 2024, however, the earnings momentum particularly in the Chemicals segment declined considerably; this segment only
slightly exceeded the low EBITDA before special items of the fourth quarter of 2023. The Agricultural Solutions segment considerably increased its contribution to EBITDA before special items in the final quarter compared with the same period of the previous year.
Cash flows from operating activities are in the range indicated by BASF and are expected to reach €6.9 billion in 2024 (2023: €8.1 billion). Free cash flow is expected to be €0.7 billion in 2024, considerably exceeding the average analysts’ estimates (Vara: €0.4 billion) and exceeding the forecast range of €0.1 billion to €0.6 billion. Payments made for property, plant and equipment and intangible assets rose consider-
ably but were lower than expected. In 2023, free cash flow amounted to €2.7 billion.
EBIT of the BASF Group for 2024 is expected to be €2.0 billion, which is below the analyst consensus for 2024 (Vara: €3.2 billion) and below the previous year’s figure (2023: €2.2 billion). The main reasons for the deviation from the analyst consensus are non-cash-effective impairments, primarily on battery materials in the Surface Technologies segment, as well as restructuring costs in all segments. BASF is making good progress with the announced restructuring measures; they account for a significant portion of the special items. In total, special items in EBIT are expected to amount to minus €1.9 billion in 2024.
Net income of the BASF Group is also affected by these special charges. Currently, BASF cannot provide a figure for net income, as the contributions from a significant nonintegral at-equity participation have not yet been received. BASF expects that the analyst consensus of €2.2 billion will not be achieved. However, the net income of €225 million for 2023 will be significantly exceeded.
VACUUM has developed a new series of magnetically levitated turbomolecular pumps that can withstand the demands of both challenging industrial environments and research processes. The oil-free nEXT2807M and nEXT3207M Maglev pumps are specially designed for areas where a contamination-free vacuum is required for high process quality. The virtually maintenance-free models (up to 80,000 hours) are among the lightest and most space-saving turbopumps in their class.
The oil-free nEXT2807M and nEXT3207M Maglev pumps are specially designed for areas where a contamination free vacuum is required for high process quality.
The pumps are designed to achieve consistently good results even in the most adverse environments and harsh industrial processes. Their robustness makes them best suited for a wide range of applications for the use in the R&D and industrial markets; including various coating applications, vacuum ovens, thermal vacuum chambers for space applications, and high energy physics applications.
In actual use, the nEXT M pumps offer their users a whole range of advantages,“ explains the Product Manager at EDWARDS VACUUM, Jinane
Haddad. „Besides their low vibrations, which is crucial in many environments, the pumps also feature hydrocarbon-free performance, durability, and versatility, with efficient water cooling. This results in an overall extension of the operating and maintenance intervals and ultimately a higher pumping capacity of the nEXT M series,“ product manager Jinane Haddad emphasises.
As the process reliability directly impacts overall productivity and profitability, maintaining a consistent level of performance is essential,“ says Product Manager Jinane Haddad. The design and functional features of the new EDWARDS series contribute to this in equal measure: with a bespoke rotor design, the nEXT M series have anexcellent pumping speed – up to 3,200 l/s for the larger nEXT3207M. The smaller nEXT2807M version has a pumping speed of up to 2,500 l/s (nitrogen). A reduced weight of the rotors decreases power consumption, especially in the start-stop phases. nEXT M pumps are the ideal solution for industrial and R&D processes that require minimal vibrations and no hydrocarbons. The bottom line is that with this innovative turbomolecular pump technology, we ensure that sensitive processes in particular are not negatively affected by external interference,“ concludes Product Manager Jinane Haddad.
Atinfinitas in Gachenbach, Bavaria, premium vehicle modification is top of the agenda. Exclusively refined vehicles from BMW and MercedesBenz roll off the yard for demanding customers around the world. LIQUI MOLY is also to be found in the vehicles ranging up to 1,000 hp and containing systems that have already set speed records. Passion and motivation, experience and competence, quality and performance: This unites the tuner infinitas and the engine oil manufacturer LIQUI MOLY. Ideal conditions for successful collaboration: Since this year, infinitas has exclusively used the engine and gear oils, brake fluids and additives from LIQUI MOLY. The highend customizer also uses extensive workshop equipment and devices from the full-range
supplier. For example, infinitas uses the fully automatic ATF oil service device Gear Tronic III from LIQUI MOLY and thus offers its customers the automatic transmission oil service.
“It is most gratifying that infinitas relies on LIQUI MOLY for its high-quality assemblies. We are convinced that our products can play out their strengths in these premium vehicles where extraordinary performance and protection are required,” says David Kaiser, Head of Research and Development at LIQUI MOLY.
infinitas Managing Director Nicolai Stöber emphasizes: “My customers expect everything to run smoothly. That’s why I need reliable partners.” And such a partner was found with LIQUI MOLY: “What distinguishes LIQUI MOLY apart from the good engine oils is the super service. Never before have I experienced such dedicated support from any other company, and I really appreciate that. I have a reliable contact person who always responds quickly to inquiries and the products are delivered to me quickly. The service is just right.”
If required, LIQUI MOLY can use the workshop and the modern single-roller dynamometer, which the tuning smithy has at
its disposal for performance measurements and diagnostic work and which can measure up to 3,000 hp. This is of particular benefit to the Research and Development Department.
David Kaiser continues: “The partnership is a win-win situation for both sides. It gives us the opportunity to perform product tests under a variety of simulated conditions. Here, we can test our proven products as well as new developments in a practical environment.”
An important role in the cooperation is played by the attention of the tuning customers; the visibility of the partnership and the recommendation of the products. LIQUI MOLY branding can be found in the workshop and on the performance test bench, while the customer vehicles and the delivered compressor kits are provided with recommendation stickers. This is complemented by special service offers: The LIQUI MOLY oil guide is integrated on the infinitas website, so that every tuning enthusiast can find the right oil for their vehicle with just a few clicks.
“Our modified engines deliver top performance, even at very high revs. Here, absolute top performance is also important in engine oil, and LIQUI MOLY delivers this,” Nicolai Stöber is convinced.
The companies are in constant dialog about what further opportunities for cooperation may arise to benefit both parties over the long term.
Cambridge-based Intellegens today announced a new product suite that represents a step-change in ease-of-implementation and use for machine learning to accelerate R&D. Alchemite™ Suite draws on the power of the Alchemite™ method, a machine learning algorithm that has unique capabilities for working quickly and flexibly with real experimental and process data. The Suite delivers a new set of software apps targeted on key tasks for development teams in chemicals, materials, foods and FMCG, life sciences, and manufacturing. The apps are interoperable, making it straightforward to share results and insights across inter-disciplinary teams.
Alchemite™ Suite will be applied in areas including:
• Design of Experiments (DOE), where its machine learning-led approach has been
shown to achieve targets with 50-80% fewer experiments than conventional DOE;
• Formulation development, where the Alchemite™ technology has helped to cut months from development timescales while finding innovative new solutions;
• Generating deep insights from R&D data by finding and enabling the exploration of previously hidden relationships in datasets.
Each Alchemite™ Suite app focuses machine learning (ML) on a different R&D challenge. Alchemite™ Designer, for example, enables fast setup of DOE projects, with no need for coding or advanced statistics. Alchemite™ Explorer lets scientists quickly generate ML models and use them to test hypotheses. Individuals can pick the right Alchemite app for their R&D challenge. R&D organisations can match the right app to the right team member, then share projects to enable collaboration across their teams.
“Recent UK Government announcements on AI investment highlight the strategic importance of applying this technology in industry,” comments Intellegens CEO, Ben Pellegrini. “Our focus is on enabling machine learning to become a standard productivity tool in chemical, materials, and related R&D. Over the past year, we’ve distilled years of experience working in this area into designing and building this new generation of Alchemite™ apps. We’re looking forward to measuring the impact in increased adoption and improved R&D outcomes.”
“A key focus is ease-of-use,” says Alchemite™ Product Manager, Rachael Clarke. “We’ve concentrated on delivering an intuitive user experience, based on input from our customers, that means important tasks can be completed quickly. Our users are running advanced machine learning methods but, in most cases, won’t need to be experts in the AI, or require training on the apps. They will apply Alchemite™ as an essential R&D productivity tool.”
In an industry operating on fine margins, unplanned downtime can be the death of profitability. Poor maintenance of plant and machinery can produce sub-par parts or goods that fail quality inspections and even expensive breakdowns.
This is where preventative maintenance comes into its own, as any operations director or production manager understands, preventative maintenance is vital to avoid these costly issues. However, we can all fall into the trap of repeating tried and tested methods that might now be outdated. Everyone with responsibility for maintenance, repair and overhaul (MRO) should regularly ask themselves: Are our MRO procedures robust enough? and Are we making the best use of the latest MRO products and services?
Manufacturing and engineering companies are well-versed in adopting best practice for production – but are you doing the same for plant maintenance? By taking a more proactive approach to MRO, your business can protect your profitability and deliver great return on investment (ROI).
Keeping an industrial facility up and running requires a vast array of products and services, spanning multiple categories. There are several specific areas we would recommend for focus and prioritisation.
If you are going to make truly informed decisions, you need accurate information – and a good place to start is a comprehensive assets survey. This process should include defining how critical each asset is to your operations. From here, you can create a detailed inventory of the spare parts held in stock to keep each asset working. This will also identify any areas where your business is lacking spare parts to support a critical asset.
Leading on from this, online condition monitoring platforms represent one of the most significant developments in maintenance management. By using a combination of AI and sensors on your machinery, they can continuously monitor your assets and help to identify issues before they cause costly failures. These intelligent platforms evaluate historical data
trends, enabling them to identify anomalies that might otherwise go undetected.
Taking proactive maintenance to a new level enables you to understand and deal with minor issues before they can cause serious disruptions to the production lines. While preventing downtime represents a major cost saving, these platforms can also optimise machinery maintenance schedules, ensuring that parts are serviced or replaced at the most cost-effective times.
AI can deal with huge volumes of data, in real time, in a way that humans simply cannot replicate. Self-learning capabilities mean that the longer the platform is in place, the more it improves its own issues detection expertise. Fundamentally, you can deploy this self-learning AI to undertake root cause analysis and set its own parameters to detect anomalies in machinery.
There is also no need for major investment as sensors can be applied to your existing machinery and components to give you and your employees access to a condition monitoring solution. These solutions should integrate seamlessly into existing plant management software, making it quick and easy to access insights and alerts. Alternatively, you can outsource the entire process to a third party remotely monitoring the data, such as Rubix, providing you with a 24/7 early warning system.
While Big Data, sensors and AI-powered technology can assist engineers in optimising their proactive maintenance processes, other more hands-on approaches can still positively impact your MRO.
By understanding when components or lubricants are deteriorating, you can schedule preventative maintenance to avoid expensive emergency repairs.
There are several strands to these solutions, each addressing an important facet of condition monitoring:
1. Vibration analysis enables early detection of wear and fatigue in rotating machinery, helping to prevent failure. By accurately measuring absolute and relative vibration on critical assets, experienced engineers can even provide you with a predicted time to failure, ensuring you schedule proactive maintenance before you reach failure.
A good provider will create reports on their findings for each asset, comparing current vibrations to historical baseline data. They will also provide photography and a list of recommended remedial actions.
Machinery such as motors, gearboxes, pump fans and compressors are often vital to the production lines. Early detection of vibration issues can prevent prolonged periods of unplanned production pauses, contaminated goods, or even injury to workers.
2. Thermographic surveys use a thermal imaging camera to identify faults or potential problems in your assets. These infrared cameras can capture differences in temperature on machinery surfaces. This enables experts to identify heat anomalies such as a machine overheating due to component fatigue or failure, or even electrical overloads.
One of the key advantages of thermography is that it is non-intrusive testing, which does not interfere with your operations – meaning there is no need for downtime while the engineers gather the necessary data.
When using this service, make sure that the provider carries out the survey in line with industry best practices. Parameters measured should include emissivity – the level of thermal energy emitted from a surface – as well as ambient and reflective temperatures, distance and humidity.
3. Air leakage surveys employ leading-edge technology to identify leaks in compressed air systems. By locating and identifying air leaks - and then fixing them - facilities can not only reduce energy consumption but also lower
operational costs. In addition, they can extend equipment life by reducing unnecessary demand on their compressors.
In our experience, air leaks are one of manufacturing facilities' biggest drains on energy efficiency. In a typical factory, compressors account for approximately 30 percent of the site’s total energy bill. And up to 30 percent of compressed air is lost to leakage, meaning that a significant portion of that energy is wasted.
4. Oil and lubrication sampling assesses the condition of machinery lubricants to ensure they are still doing their job properly. A good test will look for contaminants, signs of machinery wear and chemical breakdown. If left untreated, these issues can reduce the lifespan of critical assets and cause breakdowns, with all the related costs from repair and downtime.
Ultimately, protecting your assets protects your profit margins. Therefore, thinking smarter about proactive maintenance can deliver
savings on secondary damage, lost production and unplanned maintenance.
Asset tracking and condition monitoring provide your maintenance teams with detailed information about the health and performance of your plant machinery. A proactive and upto-date strategy can prevent revenue losses and enhance ROI.
However, it can become challenging to manage if dealing with a large number of product and service suppliers. Dealing with so many suppliers can be a drain on time, effort and money for manufacturing businesses. Working with a single source provider ensures that your company gains all the benefits with none of the downsides.
Industry understands economies of scale better than any other sector – so apply it to your MRO partners. That should mean a supplier with a local footprint, or even potentially installing a branch of their business in your premises. Additionally, it should equate to a provider offering a wide variety of products
As a safety professional, selecting flame detectors that align with your facility’s requirements is essential. Discover the key factors to consider when choosing a flame detection system. As a safety professional, you want to purchase flame detectors that meet your facility’s needs. Learn what to consider when choosing a flame detection system.
From traditional industrial environments to today’s increasingly complex hazardous processes, the risk of explosion and/or fire remains a critical concern. However, basic process controls typically do not warn of conditions outside normal system limits. Since industry vapors and gases (hydrocarbons) burn with very high flame temperatures, an external fire detection system that can rapidly sound an alarm in the event of a fire is essential to protect human lives and valuable equipment.
As a safety professional, you want to purchase flame detectors that best meet your facility’s particular needs. Here are a few things to consider when researching a fire and gas detection system.
For a comprehensive overview of flame detectors, such as operating principles and
coverage best practices, download our Flame Detection Handbook.
The most popular systems use optical methods to detect flames; that is, they detect the absorption of light at specific wavelengths. Two common optical flame detector types are (1) combination ultraviolet/infrared (UV/IR) and (2) multi-spectrum infrared (MSIR). Unlike simple UV or IR detectors, UV/IR and MSIR devices are sensitive to more than one band on the energy spectrum and therefore are less likely to produce a false alarm. Both technologies function well either indoors or outdoors and provide a reasonably fast response time.
Should you choose UV/IR or MSIR detectors? That depends on several factors.
What kind of fuels does your facility employ? Alcohols? Gasoline? LNG/LPG? Solvents? Something else? Understanding your fuel’s flammable properties will help you determine the optical flame-detecting technology you need.
Do other types of radiant energy exist in your facility, such as arc welding, hot objects, or direct sunlight? Your flame detectors should
and services to fulfil your MRO requirements. Larger scale ensures improved product availability along with the most competitive prices and terms from suppliers, which also translates to enhanced support for special projects.
The right partner can provide the proper blend for your site, whether that is online condition monitoring technology or boots on the ground, or both, to conduct routine onsite maintenance checks. In this way, businesses can transition from reactive maintenance towards truly predictive and proactive models. The impact on the bottom line can be impressive: reducing the risk of catastrophic failures, cutting maintenance costs and ensuring continuous, efficient operations.
Rubix is the largest supplier of industrial MRO products and services in Europe. It supports clients in a wide range of sectors including manufacturing, automotive, food and beverage, and energy.
To discover more about how Rubix can support your business, visit: www.rubix.com.
be able to distinguish between these non-fire energy sources and real flames. Typically, MSIR detectors provide the best immunity to these types of false alarms.
How high is the risk of air-borne particulates should a fire occur? Smoke, oil, grease, and some chemical vapors can reduce a UV/IR unit’s detection range, so if, for example, heavy smoke is a concern, you should consider MSIR technology.
Can the detector be placed near the potential ignition source or must it be located relatively far away? How wide an area should the device monitor? Different UV/IR and MSIR units offer varying detection ranges and fields of view (FOV). Match your environment with the corresponding device specifications for the best coverage.
This post has covered key factors to consider when choosing the right flame detection system for your needs. For further insights on these topics, including false alarm immunity and self-test diagnostics, download our Flame Detection Handbook
BASF has signed a binding agreement to sell its Food and Health Performance Ingredients business, including the production site in Illertissen, Germany, to Louis Dreyfus Company (LDC), a leading global merchant and processor of agricultural goods including high-quality, plant-based ingredients. BASF’s Food and Health Performance Ingredients portfolio plays a vital role in addressing growing trends in human nutrition. However, the business has limited synergies and integration into BASF and is no longer a strategic focus area.
Luftbild des BASF-Standorts Illertissen (Deutschland) Foto: BASF SE Aerial view of BASF-site Illertissen (Germany) Photo: BASF SE
As part of the agreement, approximately 300 employees are expected to transfer from BASF to LDC as of the closing of the transaction. Both parties have agreed not to disclose financial details of the transaction. Continuous and reliable supplies and business relationships will not be impacted by this transaction.
“Building on our teams’ success to develop this business very well over the last years, LDC as a future-oriented company can offer our employees and the portfolio a promising perspective,” says Michael Heinz, Member of the Board of Executive Directors of BASF SE and responsible for the Nutrition & Health division. “The divestment of this business to LDC supports our strategic portfolio optimization and will allow us to focus on our core businesses in Nutrition & Health. We remain committed to leveraging our core product platforms and expanding our business in key areas such as vitamins, carotenoids and feed enzymes.”
agreement is an opportunity to accelerate LDC’s participation in the rapidly growing plant-based ingredients market,” says Michael Gelchie, LDC’s Chief Executive Officer. “We are excited about the prospect of this transaction, as LDC’s first investment in dedicated facilities to produce food and health performance ingredients at scale.”
The food and health performance ingredients business includes food performance ingredients such as aeration and whipping agents, food emulsifiers and fat powder grades; health ingredients such as plant sterols esters, conjugated linoleic acid (CLA), omega-3 oils for human nutrition and some smaller product lines.
The transaction is subject to customary closing conditions, including approval from relevant regulatory bodies.
a century at the forefront of cosmetic packaging and applicators
GEKA, a global leader in high-precision beauty application solutions and part of medmix, is thrilled to celebrate 100 years of excellence and innovation. Across a century of success, the company has grown from crafting brushes to becoming a pioneer in brushes, applicators, packaging solutions and beauty tools.
GEKA’s story began in 1925, when the company was founded by Georg Karl senior in Waizendorf, Germany. At the time, the business was a simple brush factory, but as the years passed it began to grow in terms of both scale and scope.
In the 1950s, Georg Karl junior, inspired by a visit to the USA and a meeting with cosmetics icon Helena Rubinstein, launched the company into the beauty sector with the production of twisted wire brushes. This forward-thinking leap laid the groundwork for GEKA’s future in high-precision beauty applications.
Through the 1960s and 70s GEKA’s advancements mirrored the evolution of the cosmetics industry: The opening of a plastic molding facility in 1964 and the addition of a new production site in Waizendorf in 1974 marked GEKA’s entry into the burgeoning world of plastic packaging and applicators. During this time, the company also expanded internationally, establishing a UK subsidiary and acquiring complementary businesses to broaden its expertise.
Across the 1980s and 90s, GEKA became synonymous with innovation, introducing modular systems for over-the-counter products and pioneering synthetic fiber technology for cosmetic brushes. In 1996, GEKA entered a strategic partnership with Toly USA, cementing its status as a global player.
The turn of the millennium saw a defining moment in 2005 when GEKA unveiled its groundbreaking molded mascara brushes in New York, showcasing 1K and 2K molding PRESS RELEASE December 2025 GEKA CELEBRATES A CENTURY Page 2 of 3 medmix CONFIDENTIAL technology. This set a new standard for precision and performance in mascara applications. Over the next decade, the company expanded into Brazil and Asia-Pacific, furthering its global reach.
In recent years, GEKA has embraced sustainability and digital innovation while working alongside Sulzer and later medmix. In 2019, it launched the world’s first online configurator for cosmetics packaging, offering unprecedented flexibility and personalization to customers.
GEKA’s story is far from over, however. As the company looks back on its achievements, it also looks to the future. With sustainability at the heart of its operations, the company continues to innovate in ways that reduce environmental impact and align with evolving consumer values. Investments in advanced manufacturing, such as expanded facilities in Germany, the USA, and Brazil, position GEKA to maintain its leadership in the beauty industry for decades to come. "Our 100-year anniversary is more than a milestone—it’s a testament to the spirit of innovation and quality that has defined GEKA since it was a simple brush factory,” said Oliver Vogel, GEKA CEO. “By celebrating a century of progress we honor the generations of employees, partners, and customers who have shaped our legacy. At the same time, we look forward to a future of sustainability, cutting-edge technology, and ongoing growth in the beauty sector."
Warehouseautomation and software specialist Dematic has recently signed a contract with Globalpesca – a leading Italian provider of frozen foods and food services to the hotel, restaurant, and catering industries – to ensure operational efficiencies at a new low-temperature warehouse for frozen goods.
“Important factors in our decision process included knowing that Dematic has many years of experience developing automation solutions for the hospitality and catering industry and it has deep experience in the storage of food items at low temperatures,” explains Andrea Ruffoni, the supply chain director at Globalpesca, adding, “And when it comes to stacker cranes for pallets, we were confident that Dematic was the right company to partner with.”
Dematic was commissioned by Globalpesca to automate a new deep-freeze warehouse
Headquartered northwest of Milan in Gravellona Toce, Italy’s Piedmont region, Globalpesca S.p.A. is a family-owned business whose roots date back nearly 125 years.
Due to rapid growth in the hospitality and catering industry in Italy, food service companies must
prepared to continuously improve service levels. Globalpesca recognised that automation would support its operations by bringing improvements in two key areas: better planning and managing of its inbound product process and better handling in storage and restocking of its picking areas.
The Dematic solution is going to be installed in a new warehouse facility adjacent to Globalpesca's distribution centre in Gravellona Toce. The solution calls for a self-supporting structure designed to meet the load and temperature requirements of the warehouse, the second temperature-controlled warehouse adjacent to the distribution centre.
The 24-metre high new warehouse covers approximately 1,400 square metres. The
Dematic solution includes two RapidStore® UL1200 stacker cranes with an option of an additional one for future expansion plans, a pallet transport system using BK25 conveyors, and two Ergopal picking workstations with an option for a third workstation. Installation and commissioning are scheduled to be completed by early 2026.
The Italian frozen foods specialist aims to automate its operations and improve the efficiency of its processes with more precise inventory tracking and improving ergonomics for its operators by no longer needing them to access the facility’s −25°C areas and having them work at better designed workstations for preparing pallets.
During the project’s conception phase, an Italian team from Dematic together with a customer project team led by Ruffoni, worked closely to review various possible scenarios for Globalpesca to determine the best fit with future scalability as one of the priorities.
According to Mauro Corona, the sales director for Dematic Italy, the project is a great example of a strong collaboration. “The extensive automation expertise of Dematic and Globalpesca’s deep experience in their industries came together in a strong cooperative partnering for an efficient solution that will provide a strategic lever for Globalpesca in a demanding business environment.”
Medmix, a global leader in high-precision delivery devices, is pleased to announce that Nande van Aken has been appointed as Head of Global Operations Beauty
With more than 15 years of experience in driving operational excellence and organizational transformation, Nande brings a wealth of expertise to her new role. Her extensive career spans a wide range of industries and various management roles in manufacturing, supply chain and R&D, equipping her with the diverse skill set to further enhance GEKA’s capabilities and performance.
At medmix Beauty, Nande will be part of the management team, where she will oversee the company’s global manufacturing operations. Her focus will be on building a sustainable strategy and robust operations, optimizing functionality, quality, and profitability across the business, and strengthen GEKA’s ability to support customer, end-user and industry needs.
With a proven track record of implementing change and improvement, fostering cultural change, and navigating complex challenges, Nande is poised to bolster GEKA’s position as a global innovator in beauty application solutions.
On joining GEKA, Nande said: "I am excited to be part of an organization with such a rich legacy of innovation and excellence. I look forward
to working with the team to further boost efficiency and drive sustainable growth in line with GEKA’s vision."
GEKA’s latest strategic appointment reinforces its commitment to delivering high-quality, cutting-edge beauty application solutions to customers worldwide.
Technology group Wärtsilä will supply its EnergoFlow solution and Fixed Pitch Propellers (FPP) for three Pure Car/Truck Carrier (PCTC) vessels owned by Sallaum Lines – an international RoRo cargo operator. The combination of these upgrade solutions will notably improve the propulsion efficiency of these existing vessels, in turn reducing fuel consumption and CO2 emissions. The order was booked by Wärtsilä in Q4 2024.
Sallaum Lines has selected Wärtsilä’s EnergoFlow solution and Fixed Pitch Propellers for three PCTC vessels, following a thorough and rigorous analysis and modelling exercise carried out as part of Wärtsilä’s unique Decarbonisation Programme.
To meet the industry’s 2050 net-zero goals, shipping must embrace a change in how ships operate. This includes implementing a wide range of carbon-reducing practices and technologies for existing ships, such as these PCTC vessels, which have been operating for 15 years. With a focus on limiting its environmental impact across its fleet, Sallaum Lines selected the Wärtsilä solutions following a thorough and rigorous analysis and modelling exercise carried out as part of Wärtsilä’s unique Decarbonisation
Programme. The programme was tailored to these specific vessels so that the right solutions could be selected for optimal sustainability.
“Wärtsilä’s Decarbonisation Programme has greatly helped us as we strive to minimise the environmental impact of our operations. By adding the Wärtsilä innovations to these three vessels, we are taking an important step forward towards meeting our sustainability goals,” says Puneet Arora, Head of Technical – Sallaum Lines.
Wärtsilä FPPs are designed to deliver optimal performance and efficiency, while at the same time minimise noise and vibration levels. Designed for
the existing fleet market, Wärtsilä EnergoFlow is an innovative pre-swirl stator that creates an optimal inflow for the propeller, reducing fuel consumption and emissions in all operating conditions.
The three vessels to be fitted with these solutions are the ‘Silver Queen’, the ‘Silver Moon’ and the ‘Silver Sky’. All are 183-metre long PCTCs capable of carrying 4,900 cars. By optimising the propulsion efficiency of these ships with these solutions will cut their emissions, whilst also reduce operating costs.
“Our Decarbonisation Programme is designed to support owners and operators invest in the most appropriate solutions for their particular vessels,” comments Rajan Khanna, Head of Sales for Middle East – Wärtsilä Marine. “With increasing pressure within the industry to decarbonise, we applaud Sallaum Lines for taking action to proactively implement solutions which will help them to maximise operational efficiency and minimise environmental impact of their vessels.”
Wärtsilä supports its customers in the Middle East region with more than 300 employees and a workshop in the United Arab Emirates.
Energia Italia supports the launch of the first Renewable Energy Community
“The energy community in the Staffora Valley represents a cutting-edge project with a high innovative value. We are proud that MET Energia Italia has promoted and overseen its implementation,” said Vito Carriero, CEO of MET Italia Energy Solutions. MET Italia's energy services company deals with energy efficiency, supporting firms and energy communities.
Energia Italia, subsidiary of Swiss-based MET Group, has launched the first Renewable Energy Community in Lombardy. The community is open to all citizens, companies and local authorities in the area, and uses renewable energy to generate energy savings.
The Renewable Energy Community’s photovoltaic plant is located on the roofs of a disused company centre in the village of Cegni. The installed panels can produce up to 200 KW (kilowatts) of energy, with the possibility of increasing up to 400 KW if demand grows. So far the community, called Staffora 1, has collected 100 signatures, i.e. contact points, and the energy produced is sufficient to supply 200 households.
MET Energia Italia was responsible for developing the project, building the plant and – in cooperation with local authorities – oversaw the authorization process.
The CEO added: “Our goal is to help improve energy efficiency and reduce environmental impact in industrial and commercial sectors. Whilst Staffora 1 is a significant achievement, we are already working on financing other photovoltaic systems on the roofs of our industrial partners, throughout Italy. This will also benefit citizens who decide to join the energy communities we promote.”
MET Group is an integrated European energy company, headquartered in Switzerland, with activities and assets in natural gas and power markets. MET is present in 15 countries through subsidiaries, 30 national gas markets, and 39 international trading hubs. The company's 1,000+ employees represent close to 60 nationalities. MET has extensive experience operating green (renewable) and flexible (conventional) energy assets, thus providing the widest possible support to energy transition. In 2023, MET Group’s consolidated sales revenue amounted to EUR 24.5 billion, with a total traded volume of natural gas amounting to 88 BCM and total traded electricity of 68 TWh.
IMIis set to provide a PEM electrolyser for a new hydrogen refuelling station at the Port of Klaipėda in Lithuania, to be developed by EPC contractor MT Group. This groundbreaking project will position the Port of Klaipėda as the first in the Baltic region to produce green hydrogen on-site.
MT Group is a leading EPC contractor in critical energy and industrial infrastructure projects across Europe. The company's expertise extends to the development, engineering, and construction of renewable energy, hydrogen, and carbon capture facilities, positioning MT Group at the forefront of sustainable engineering. The company is also a founding partner in one of the largest renewable energy undertakings in the world – Green Energy Park Global, which will produce some of the most cost competitive Green Hydrogen at the gigawatts scale, servicing the decarbonization needs of the hard to abate sectors, including transport and power across Europe and elsewhere around the world.
The IMI VIVO electrolyser will enable the port, which is the second largest EU port by tonnage in the Baltic[1], to produce 500kg of green hydrogen on-site per day. This is equivalent to 127 tons per year while using an electrical input of 3 MW, drawn from sustainable sources. On-site production helps to reduce the need for transportation and storage of hydrogen, while also reducing associated emissions.
With the European Green Deal requiring ports to achieve a 90% reduction in transport emissions by 2050[2], operators are under pressure to make advances towards greener solutions. The hydrogen produced by the electrolyser will be used to fuel vessels as well as shore-side equipment.
IMI’s VIVO Electrolyser offers full customisation in size, capacity, and configuration, ranging from 100kW to 5MW, with potential for further expansion to 20MW through a modular configuration. As a result, the solution specified by IMI was able to meet the exact requirements of the brief set out for this project. The customisation offerings were attractive to both the Lithuanian EPC contractor MT Group and the Klaipėda State Seaport Authority, which selected IMI as the preferred choice for this project partly due to the flexible nature of the product.
Mauro Natalini, Sales & Business Development Manager at IMI, said: “Electrolysers can provide huge benefits to the marine sector, and help to meet the stringent targets set out by the EU as part of the European Green Deal.
“We’ve been working closely with both MT Group and the Seaport Authority throughout this process, with some of their technicians recently visiting our manufacturing site in Sardinia to see the electrolyser production process in person. This cements our strong bond, as we both strive to help accelerate the use of green hydrogen in the Baltic region. It also reflects our commitment to working with our clients to help deliver solutions that enable emissions reductions in key industries.”
Mindaugas Zakaras, CEO of MT Group, said: “As part of our vision to encourage sustainability, we are committed to making the new hydrogen refuelling station in Klaipda a benchmark for the entire industry. This will be achieved by using the most innovative technology to maximise capacity while meeting the highest quality and safety standards.
“IMI was able to provide us with a prompt response and technical expertise alongside their customisable solution. This was exactly why we chose to partner with them on this exciting project.”
has installed and commissioned the world’s first 8DAB 24, the groundbreaking blue GIS medium-voltage system, in the Alpine town of Davos, Switzerland for its customer EWD Elektrizitätswerk Davos AG. The switchgear system, which uses Clean Air as insulating gas instead of sulfur hexafluoride (SF6), is deployed in the Dorf substation in Davos, securing reliable power supply for up to 40,000 people. The installation of this 24kV circuit-breaker switchgear is an important step towards a climate-friendly and smart power distribution in Davos. The Fluor-gas-free blue GIS-portfolio was launched by Siemens ahead of EU regulations, serving as another proof point of the company’s focus on sustainability across its portfolio. Siemens introduced the first SF6-free solution around seven years ago, since then installed many more successfully and this being the latest addition.
“If we want to achieve our net-zero targets, we need to make power grids future ready with innovative, eco-friendly technology,” said Matthias Rebellius, Member of the Managing Board of Siemens AG and CEO of Siemens Smart Infra-
structure. “Therefore, it is essential to invest in the continued expansion of power grids. I am pleased that our long-standing customer EWD is using our pioneering switchgear technology that paves the way for climate-neutral and smart power distribution in Davos.”
“SF6 was never ideal for the environment,” said Andy Kollegger, CEO of EWD. “There was no doubt in our minds: If there is an alternative on the market that has the same functionality but without this disadvantage, we will switch to it.”
With over 1.3 million overnight guests in 2023, Davos is one of Switzerland’s biggest tourist destinations. It is also the venue for the World Economic Forum (WEF) that sees almost 3,000 guests flocking to the town each year. While close to 12,000 residents live in the highest town in the Alps year-round, Davos accommodates over 40,000 people during high season. EWD Elektrizitätswerk Davos AG operates three substations, 168 transformer stations, 154 kilometers of medium-voltage grid and 300 kilometers of low-voltage grid in the Davos grid area.
Reliable power supply is essential to a well-functioning infrastructure. At the heart of sustainable power distribution is switchgear. Its applications include substations where it connects power generators and large power consumers, such as industrial plants or data centers, to the power grid. Another important role of switchgear is monitoring and protecting power grids, for example against short circuits. The Clean Air used as an insulating medium in the blue GIS portfolio consists of natural components of ambient air, making it climate-friendly, extremely stable, non-toxic, non-flammable, and suitable for all operating temperatures.
In addition, the blue GIS switchgear is equipped with smart sensors and standardized interfaces for Electrification X. Part of Siemens Xcelerator, Electrification X is a comprehensive IoT suite that provides solutions to challenges faced by public and private power grid operators. It improves energy efficiency and enables a seamless digital and sustainable transformation.
Finland has specific expertise and experience in the cleanroom sector, and some of the leading Finnish businesses in this sector have formed a working partnership to offer complete solutions in international cleanroom markets, with particular emphasis on sustainability.
The new partnership has been created within the ASC alliance (Alliance for Sustainable Cleanrooms), which was established to meet the internationalization objectives of cleanroom industry participants, building on the success of previous collaborative projects. "Clients ordering cleanroom solutions often seek turnkey solutions, so with this new cooperation, it is more than achievable," says Jukka Vasara, vice president at Granlund, who initiated the alliance.
The ASC members believe that cleanroom clients typically have two main priorities: fast project completion on schedule, and quality as a top priority. This is because errors can disrupt production, which can be very costly.
“The strength of the alliance,” Vasara explains, “lies in decades of expertise in design, project management, and system capabilities, alongside technological excellence.”
Cleanrooms are essential for many crucial processes, so demand is high, particularly for
sustainable, turnkey solutions, and this is one of the major justifications for the ASC Alliance. For example, laboratories and production facilities require strictly regulated environments in electronics, pharmaceuticals, biotechnology, food, and semiconductor industries, as well as in hospital pharmacies, operating rooms, and the optical industry.
Cleanrooms are classified according to ISO into classes 1–9, and according GMP into classes A to D. Each class defines how clean the air must be, specifying how many particles are allowed per cubic meter of air. The standard's requirements must be meticulously followed, and thoroughly documented. In pharmaceutical cleanrooms, microbiological contamination must also be measured and controlled.
In practice, clean air is typically achieved through effective ventilation and filtration. Consequently, cleanrooms consume high levels of energy, and therefore possess a large carbon footprint. To enhance energy efficiency, the sizing and regulation of cleanroom ventilation systems need to be demand-driven, with accurate monitoring and control systems that are reliable in the long-term. The sustainability of cleanrooms can be further enhanced through initiatives such as the reduction of chemical usage, and better waste management.
The ASC combines the specialized expertise of its member companies in cleanroom technology, enabling them to provide comprehensive solutions for customers in international markets. The ASC has recently benefited from ‘Group Explorer’ funding from Business Finland, which will enable the alliance to explore new global opportunities, expanding market access and building a stronger international presence.
Members of the alliance include:
• Vaisala - monitoring and measurement solutions
• Granlund - cleanroom design
• Halton - ventilation solutions
• Cleamix - decontamination solutions
• LED Tailor - blue light solutions
• Hermetel - cleanroom elements
• Zeus Tech - validation, measurement, and testing solutions
• Kavika HealthCare - furniture solutions
Visit ASCG.fi to request information on turnkey cleanroom solutions or for the contact details of ASC members.
On January 29, 2025, Health Secretary
Wes Streeting addressed the issue of NHS overspending, emphasizing the need for the health service to "learn to live within its means." He declared that the "culture of routine overspending without consequences is over" and acknowledged that this shift would necessitate "tough decisions" at the local level, empowering systems to make necessary adjustments.
This statement aligns with recent findings from the Public Accounts Committee (PAC), which criticized NHS leaders for "glacially slow progress" in transforming the health service. The PAC report highlighted a lack of fresh ideas and drive among senior health officials, as well as a disregard for financial planning principles, noting that budgets were often not approved until after the financial year had started. The report also pointed out issues such as an excessive reliance on outdated technologies
like fax machines and paper records, with funds intended for digitalization being redirected to cover other deficits. The NHS recently overspent its £171 billion budget by £1.4 billion and is currently less productive than before the pandemic.
In response to these challenges, Streeting has announced plans to streamline NHS operations by scrapping approximately half of its current targets to focus on reducing waiting lists. This decision comes in the wake of a winter crisis that led to numerous deaths and aims to address long waits in A&E and for non-urgent treatments. The new approach seeks to cut long waits and reduce micromanagement of health chiefs, offering them greater freedom while demanding tangible results. Some targets in areas like women's health and learning disabilities will be dropped, while core goals in A&E and cancer treatment will be maintained or strengthened.
Despite resistance from campaign groups, the government argues that focusing on fewer, more critical outcomes will better serve patients.
Streeting's stance reflects a broader governmental push to reform the NHS and address its financial challenges. He has previously emphasized the importance of reforming the NHS rather than continually increasing its budget without addressing inefficiencies. The British Social Attitudes survey for 2023 revealed that only 24% of the public are satisfied with the NHS, the lowest since 1983. Amanda Pritchard, CEO of NHS England, admitted that hospital productivity has declined, further exacerbated by long waiting lists and pandemic-related setbacks. Despite an increased hospital workforce, productivity remains low.
Continue reading at: www.industryeurope.net
Thenew Trane® City™ RTSF HT high-temperature heat pump delivers up to 110°C hot water with proprietary screw compressor technology and advanced controls. Thanks to industrial-scale manufacturing and Trane’s extensive sales and service network, the portfolio expansion is poised to accelerate the decarbonisation of industrial heating processes.
Trane®, a leading global provider of indoor climate control solutions and a brand of Trane Technologies, has introduced the RTSF HT, a hightemperature water-to-water heat pump capable of delivering hot water up to 110°C. The RTSF HT expands the Trane CITY™ portfolio of compact water-to-water heat-pumps and chillers. Designed to meet the demands of industrial and commercial applications, the RTSF HT marks a significant step forward in decarbonising high-temperature process heating, which still heavily relies on fossil fuel boiler technology.
The introduction of the RTSF HT positions Trane as the first global thermal systems provider to offer high-temperature heat pump technology up to 110°C with standardised technologies, industrial-scale manufacturing, and a comprehensive sales and service network across Europe, the Middle East, Africa (EMEA), Australia, and New Zealand. To ensure reliability and performance, the unit is rigorously tested in Trane’s state-of-the-art laboratory in Epinal, France.
“The new CITY™ RTSF HT units extend our decarbonisation efforts into industrial process heating, complementing our portfolio of solutions for space and comfort heating,” said Erik van Oossanen, product management leader for Trane in Europe, Middle East and Africa. “Many industries heat and cool within the same process, often simultaneously. This practice causes large thermal inefficiencies. By electrifying process heating and enabling the repurposing of
wasted thermal energy, we are helping industries transition away from fossil fuels and achieve ambitious sustainability targets.”
The RTSF HT is powered by Trane’s proprietary screw compressor technology and features ultra-low global warming potential (GWP) R1233zd(E) refrigerant. This combination ensures outstanding performance, achieving a coefficient of performance (COP) of up to 4.6 under typical operating conditions. The unit's compact footprint, just 930 mm wide, makes it ideal for applications requiring high capacity (up to 380 kW) while optimising space efficiency and reducing installation costs.
Equipped with the Trane Tracer Symbio™800 controller, the RTSF HT ensures smooth, reliable operation and connectivity through advanced algorithms, delivering operational efficiency with a low cost of ownership.
The RTSF HT is suited for a variety of applications, including industrial processes in food and beverage, pharmaceutical, and chemical sectors, as well as district heating and cooling and advanced cascade heating systems. The system’s ability to recover industrial waste heat enables customers to optimise energy use and reduce the carbon footprint of the industrial thermal system, contributing to the sustainability of their operations.
The RTSF HT product introduction aligns with Trane Technologies' commitment to sustainable innovation. Providing sustainable cooling and heating solutions is part of Trane Technologies’ overall approach to reducing carbon emissions in the industries and markets they serve. It helps advance the 2030 Sustainability Commitments, including the Gigaton Challenge to reduce customer greenhouse gas emissions by 1 billion metric tons.
Merck, a leading science and technology company, and Opentrons Labworks, Inc., a leader in lab automation and accessible robotics, announced a multi-year agreement to automate assay kits on a custom Opentrons Flex® workstation.
Scientists and engineers will collaborate to develop and verify platform workflows utilizing Merck’s broad offering of automation-enabled assays. Together, the custom workstation and automation-enabled assays will deliver increased consistency and higher throughput by reducing manual processing and repetitive tasks with a userfriendly robotic system.
“Our customers are prioritizing tools and technologies that improve reproducibility and productivity, allowing them to focus on more complex tasks that take their science further, faster,” said Jean-Charles Wirth, Head of Science & Lab Solutions for the Life Science
business of Merck. “Our partnership with Opentrons reinforces our focus to automate and digitalize the lab - supporting scientists at all stages with tools that can increase efficiency, safety, and success rates of delivering new potential therapeutics.”
Customers can place orders for workstations and assay kits from Merck starting mid-2025. Applications will include broad workflows across protein sample preparation, molecular, cell, and other biochemical and chemistry workflows launching throughout the length of the agreement.
“Part of our commitment to making lab automation as accessible as possible is finding partners who share a similar vision,” said Jonathan Brennan-Badal, CEO of Opentrons. “Merck Life Science is a proven leader in terms of the breadth and quality of products they offer for pharmaceutical development and manufacturing, and we’re excited to
combine that with our ability to provide worldclass automation, service and support.”
By combining the automation expertise and service excellence of Opentrons with the powerful R&D, supply chain, and quality systems of Merck we will deliver reliable products streamlining research from sample prep to analysis for immunodetection, protein research, enzyme technology, genome editing, omics research, pharmaceutical development, service and testing and cell culture.
This adds to Merck’s existing Biology innovations to increase Life Science lab productivity, like the Millicell® DCI Digital Cell Imager that allows for accelerated cell culture analysis with an intuitive interface while also adding to the company’s commitment to provide next-generation biology solutions such as their recent acquisition of HUB Organoids Holding B.V.
Goldhandel reflects on an exceptionally successful financial year in 2024, driven by significant growth across all six newly redefined business segments (purchase and sale of investment products, scrap gold purchase, gold savings plans, valuables storage, and safe deposit box services). Notably, the gold savings
plan, introduced in partnership with Deutsche Bank and available for less than six months, made an extraordinarily large contribution to the company’s success.
Popular with investors with a long-term strategy for asset accumulation: the 1 kg gold bar from Degussa. / More information via ots and www.presseportal.de/en/nr/105154 / The use of this image for editorial purposes is permitted and free of charge provided that all conditions of use are complied with. Publication must include image credits.
While Degussa – like most market participants – achieved gains in the acquisition of precious metals, the company also exceeded its sales targets, defying broader market trends. These achievements were largely driven by stra-
sive digital transformation. Additionally, a new and innovative brand identity fuelled substantial growth in both retail and online sales channels.
"We are extremely pleased with the results of the 2024 financial year and will continue to pursue the realignment of our strategy with determination in the year ahead," stated Degussa CEO Christian Rauch.
Building on this momentum, Degussa aims to further accelerate its progress in 2025. Key priorities include the ongoing expansion of its digital transformation efforts, attracting new customer segments, introducing innovative products, and advancing its international footprint.
CFO Mark Sommer added: “Our investments in digital transformation and the expansion of our international operations have set us on a highly
Century Lithium Corp. (TSXV: LCE) (OTCQX: CYDVF) (Frankfurt: C1Z) (Century Lithium) is pleased to announce it signed a non-binding memorandum of understanding (MOU) with Orica Specialty Mining Chemicals (Orica) on January 16, 2025. The non-binding MOU outlines the intent of Century Lithium and Orica to formalize a multiyear offtake agreement for Orica to purchase sodium hydroxide (NaOH) from Century Lithium's wholly owned Angel Island project near Silver Peak, Nevada. Orica is one of the world's leading mining and infrastructure solutions providers, and a major US manufacturer and supplier of specialty mining chemicals to Nevada's mining industry.
"The non-binding MOU with Orica marks a key milestone for Angel Island," said Century Lithium President and CEO, Bill Willoughby. "The MOU outlines the first expected agreement of its kind for the project and involves a large portion of the surplus sodium hydroxide anticipated during the early years of operation. We are excited to work with Orica and have their support at this stage of development at Angel Island."
Orica President Specialty Mining Chemicals Andrew Stewart said: "This collaboration
signifies our commitment to strengthening and unlocking Nevada's manufacturing and mining sectors. By securing a reliable source of sodium hydroxide from Angel Island, we strengthen the local supply chain and reinforce our dedication to innovative US manufacturing solutions for our customers in North America."
Century Lithium patent-pending process for extracting lithium from the claystone at Angel Island combines chloride leaching with direct lithium extraction and uses salt, in the form of solid sodium chloride or saline brine, to make the reagents for leaching and pH control. In addition to lithium, the process produces surplus sodium hydroxide, the sales of which are antici-
pated to underpin low operating costs for Angel Island's primary product, lithium carbonate.
• Century Lithium to intends to provide Orica membrane-grade sodium hydroxide (NaOH)
• Initial 5-year term, right of first offer for an additional 5 years
• Pricing to be determined by definitive agreement
• Orica – Century Lithium relationship will strengthen the U.S. supply chain, reducing reliance on imports of NaOH to the western U.S. and supporting Nevada's mining industry
Metso is advancing the education of future mining professionals in the Middle East through a training agreement with Saudi Mining Polytechnic
Metso and Saudi Mining Polytechnic (SMP) institute have signed a training agreement to support mining career development and address the mining labor shortage. Metso will select young Saudi graduates to undergo training services at SMP as per the agreement. This includes training trainees for the Associate Diploma in the specified programs at SMP over one year, with an additional three months of onthe-job training at the customer site.
“A training agreement is an important way to develop the local capabilities and offer opportunities for skill enhancement and career growth for students to meet the growing need for mining professionals in the area. This initiative is a concrete example of Metso’s commitment to community development in Saudi Arabia. Our target is to make the mining industry more appealing to potential new Metso employees by helping to attract and also retain talent,” says Rajneesh Mishra, Vice President, Sales and Service, Middle East area.
SMP is semi-governmental, and the degree is accredited by the Ministry of Education and the Technical and Vocational Training Corporation (TVTC).
“We are dedicated to training Saudi youth to achieve the highest level of Saudization and job localization in the mining industry. The training agreement with Metso is a significant addition to our partner network. We recognize the labor market
needs in the mining industry and are committed to nationalizing jobs in this growing industry,” says Abdullah Amer Alotaibi, Managing Director, Saudi Mining Polytechnic.
Metso has signed several major mining capital projects and life cycle service agreements in the Middle East area over the years. Local workforce capability development and training has become a crucial part of the life cycle service contracts.
Metso offers training to bridge the knowledge gap between customer personnel, equipment, and operational goals. Through its Metso Academy, led by global experts with decades of experience, Metso provides comprehensive and tailored training programs designed to enhance technical knowledge, safety, reliability, and operational performance.
LBMA(London Bullion Market Association) is delighted to announce the launch of its Gold Bar Integrity (GBI) Database powered by aXedras, marking a significant milestone in enhancing trust and transparency within the global precious metals market. The database went live this January, offering participants the opportunity to onboard and leverage this transformative digital platform. By end of 2025, we expect all 100+ Good Delivery refiners to be onboarded by aXedras, enabling enhanced reporting.
The GBI Database represents a major step forward in modernising data collection and management processes across the precious metals value chain. It centralises and safeguards key data points, such as Responsible Sourcing deliverables and Country of Origin information whilst enabling refiners, custodians, and other stakeholders to seamlessly share this data with LBMA.
“The GBI Database will initially focus on two crucial datasets: Refiner Data and London Vault Data. This means faster, more secure data collection and processing. Beyond this, the platform’s ability to automate risk identification and flag potential issues quickly will play a vital role in enhancing confidence across the market,” said Ruth Crowell (CEO, LBMA).
Urs Röösli (CEO, aXedras) comments: “Over the years, we have worked alongside key players and LBMA to develop a solution that would further their commitment to enhancing trust across the industry. By leveraging our common team know-how and technology such as Distributed Ledger Technology (DLT), we have created the Gold Bar Integrity (GBI) Database that serves as a stepping-stone towards greater digitalisation.”
Many refiners have already been onboarded and are in a position to submit their data and assurance deliverables to the platform this year, reflecting the strong industry commitment to this initiative.
The GBI Database is part of LBMA’s broader Gold Bar Integrity Ecosystem, which integrates advanced technologies to strengthen the integrity and efficiency of the market while enabling a collaborative approach to future challenges.
If you have any questions or would like further information, please visit our dedicated GBI webpage or contact us at gbi@lbma.org.uk.
release of a pivotal policy paper calling for an urgent investment commitment under the European Union’s upcoming Framework Programme 10 (FP10) to strengthen Europe’s supply chain resilience for critical and strategic raw materials (CRMs and SRMs).
Bernd Schäfer, CEO, Managing Director, EIT RawMaterials highlighted the urgency of the paper’s recommendations: “The crucial role of raw materials in Europe’s future has never been more apparent. The Draghi Report on European Competitiveness, which will form the foundation for the new European Commission’s flagship Competitiveness Compass, ranks raw materials as the second most critical issue for Europe, closely following energy security. This policy paper outlines a pathway to build a resilient and sustainable raw materials supply chain — essential for Europe’s competitiveness and industrial future. Framework Programme 10 presents a unique opportunity to unlock large-scale private sector investment, accelerating innovation and industrialisation.”
Schäfer added: “It is vital to build upon the investments made under the Horizon and Horizon Europe programmes over the past decade and the strong foundation of the raw materials knowledge and innovation community established as part of the EIT ecosystem.”
With global demand for raw materials accelerating, particularly those critical to the energy transition, the European Union faces a pressing need to diversify supply sources, enhance sustainable recycling and circularity, and reduce reliance on single-country suppliers to achieve its climate and digital goals.
In response to these challenges, the European Union adopted the Critical Raw Materials Act (CRMA), setting ambitious targets including:
• Expanding Europe’s domestic raw materials production to 10%,
• Increasing processing capacity to 40%, and
• Recycling rates to 25% by 2030.
The CRMA underscores the critical importance of a robust European raw materials sector, stating: “Critical raw materials are indispensable for the EU economy and necessary for a wide range of technologies in strategic sectors such as renewable energy, digital, aerospace, and defence.”
However, Europe’s raw materials sector faces complex challenges, primarily due to its heavy reliance on imports from international suppliers, which produce over 70% of raw materials for batteries and clean technologies. As global demand rises, ensuring sustainable and reliable supplies has become crucial to Europe's strategic autonomy and industrial competitiveness.
Amid these challenges lies a transformative opportunity: a recent European Commission report highlights the potential for the raw materials sector to generate over €2 trillion in value and support 32 million jobs by 2030, underscoring the immense economic potential from strategic investment in this field.
Recognising both the challenges and opportunities, EIT RawMaterials is calling for a commitment of €4 billion under Framework Programme 10 to deliver targeted, high-impact investments in research, innovation, and education across the raw materials value chain. This funding is essential to address Europe’s urgent priorities and strengthen its raw materials ecosystem.
EIT RawMaterials’ proposed investment aligns directly with the objectives of the CRMA by advancing sustainable mining, driving research into advanced materials, and promoting circular economy practices. These efforts will enable Europe to establish a secure, self-sustaining supply chain for critical raw materials, positioning the continent as a global leader in the green and digital transitions, fostering economic growth, and ensuring Europe’s industrial resilience.
To achieve these goals, EIT RawMaterials will collaborate closely with its partners — the largest and most active Knowledge and Innovation Community in the raw materials sector, European and Member State institutions, stakeholders, investors, researchers, and academic institutions. Together, these efforts will attract significant private investment, develop breakthrough technologies, and cultivate the skilled workforce needed to secure Europe’s raw materials future.
EIT RawMaterials is supported by the European Institute of Innovation & Technology (EIT). EIT Knowledge and Innovation Communities have built Europe’s largest innovation network, bringing together more than 2,400 key organisations in business, education, and research with activities in each EU Member State, strategic partner nations and beyond. The EIT ecosystem has achieved strong performance on key indicators, training over 800,000 direct learners, and powering more than 10,000 start-ups collectively valued at approximately €72 billion at the end of 2023. EIT-supported ventures have attracted investments of over €9.2 billion.
£1.5 million+ on offer to UK construction via The Pallet LOOP
Companies across UK construction can claim a share of more than £1.5 million(1) (GBP) by returning bright green LOOP pallets for reuse according to new figures released today by The Pallet LOOP – the circular economy pallet reuse scheme for the construction sector that’s part of BSW Group.
In its first six months, The Pallet LOOP has issued more than 450,000(2) of its distinctive green, reusable pallets to British Gypsum to transport its bagged plaster and plasterboard products. With a financial incentive of up to £4(3) available on each of these pallets, when companies return them to The Pallet LOOP, there is now a huge pot of money available for businesses throughout the building materials supply chain that sign up for LOOP collections.
A growing number of companies are already using The Pallet LOOP’s collection service and reaping the rewards. To date, The Pallet LOOP has paid out around £150k(4) to users of the scheme including builder’s merchants, principal contractors and housebuilding companies – and the number of pallets being returned is growing month on month. In October, the number of green pallets that
IThe Pallet LOOP collected was around 30% of the number it issued that month(5). This figure already exceeds previous benchmarks for standard pallet return rates in the construction sector, which have historically hovered around the 10% mark(6).
In addition to claiming up to £4 back for every green LOOP pallet returned, companies using The Pallet LOOP could be saving vast amounts of money on waste costs, while also cutting their carbon footprint and helping to reduce the unnecessary waste of a precious natural resource. So far, The Pallet LOOP estimates it has saved companies returning pallets up to £800k on skip costs(7). The Pallet LOOP has calculated that putting pallets in wood skips can cost up to £8 per pallet(8). Put that money together with the LOOP PayBack, and companies using The Pallet LOOP could be up to £12 better off for every green LOOP pallet that gets recovered for reuse – further increasing the financial incentive.
Explaining more, Paul Lewis, Founder of The Pallet LOOP, said: “Getting a financial reward for returning pallets, and saving on waste costs is good news for merchants, principal contractors and housebuilding companies up and down the country
as they face fresh operational headwinds and get to grips with changes coming into force as part of the recent budget. From the start, our model was designed to be financially equitable for everyone in the building materials supply chain, as well as better for the environment. What we’ve achieved in the first six months shows our vision is now a reality. Companies returning green LOOP pallets are getting a real boost to their bottom line. They can also access sustainability data relating to the number of pallets they have returned via our Power Bi platform. We are delighted with the progress made to date. But this is just the start – with more LOOP pallets set to hit the sector in the year ahead.”
“From December, Isover will start moving its insulation materials on our circular economy pallets. We’re also in advanced discussions with other building material manufacturers that want to follow Saint Gobain’s sustainable leadership and switch to using LOOP. By the end of 2025, we estimate we will have issued more than 2.5 million LOOP pallets – creating a PayBack pot of up to £10 million. If you are a company in construction, and you haven’t done so already, now is the time to get in the LOOP and start sending back green pallets.”
Continue reading at: www.industryeurope.net
Trump’s New Immigration Policy: Strict Enforcement, Mass Deportations, and a Merit-Based Future
n January 2025, President Donald Trump enacted a series of stringent immigration policies aimed at overhauling the U.S. immigration system. These measures have sparked significant debate, with supporters lauding the emphasis on national security and critics expressing concerns over potential humanitarian impacts.
One of the administration's first legislative actions was the signing of the Laken Riley Act. This law mandates the detention and potential deportation of individuals in the U.S. illegally who are accused of theft and violent crimes, even before conviction. Named after Laken Riley, a victim of a crime committed by an undocumented immigrant, the act allows state attorneys general to influence federal immigration policies. While it passed swiftly through the Republican-controlled Congress with some Democratic support, it has faced criticism from immigrants' rights advocates
who argue it could lead to mass roundups and is seen as punitive and discriminatory.
The administration has intensified immigration enforcement through nationwide raids conducted by Immigration and Customs Enforcement (ICE). In the first week alone, over 7,300 individuals were detained. The deployment of 1,500 troops to the southern border, with plans for up to 10,000 more, underscores the administration's commitment to securing the border. These actions have led to a significant decrease in illegal border crossings, dropping from thousands to less than 600 per day.
The aggressive enforcement measures have instilled fear within immigrant communities. Highprofile raids and the rollback of protections for sensitive locations such as schools and churches have heightened anxiety among undocumented
individuals. Critics argue that these actions could lead to widespread unrest rather than the order the administration anticipates.
The crackdown on immigration is expected to have ripple effects beyond border security. Immigrant workers play a crucial role in disaster recovery efforts, providing skilled labor for rebuilding communities affected by natural disasters. Mass deportations could disrupt these efforts, leading to labor shortages and delayed reconstruction, particularly in states vulnerable to climate-related events.
Internationally, the administration's policies have led to tensions, notably with Colombia. A dispute over the treatment of deported migrants resulted in threats of trade tariffs, highlighting the broader geopolitical implications of the U.S.'s stringent immigration stance.
Continue reading at: www.industryeurope.net
ItohDenki’s stand (no. 1K25 in Hall 1) will display number of novel systems, all based on acclaimed MDR technology, which bring greater control and modularity to a broad spectrum of material handling processes in both the warehouse and the factory.
Optimising both throughput and performance, Itoh Denki’s modular systems allow for unrivalled flexibility to meet changing operational demands.
Taking centre stage will be FNR, an MDRpowered conveyor platform which safely and efficiently transfers light loads of all shapes and sizes via a patented bed system comprising robust plastic wheels.
FNR can undertake any task handled by belt conveyors, while delivering additional benefits in the form of near-silent operation and colleague safety.
Requiring minimal set-up and ongoing maintenance, FNR has been designed specifically for applications involving small and medium-sized items and is particularly suited to singulation and accumulation tasks for order preparation. In these applications, thanks to its short, independently controlled zones, FNR can rapidly and efficiently singulate or accumulate items even in very short distances.
As an entirely modular system, FNR is easily integrated into systems already in place – and has the scope to be reconfigured whenever necessary as requirements evolve.
FNR will be joined by Itoh Denki’s family of diverter units which can between them cater for a vast array of application requirements.
The Multi-Angle Ball Sorter (MABS) harnesses patented rotating ball transfer technology to enable diversion to exits at 30°, 45° or 90° angles on both sides. Capable of handling up to 4,300 units per hour, MABS can be integrated into any type of conveyor system.
Where it can handle loads up to 30kg of varying shapes and sizes. Available in five sizes and easily reconfigurable to meet changing requirements, up to eight units can be combined as necessary to create larger transfer zones.
MABS will be demonstrated in combination with Itoh Denki’s acclaimed F-RAT NX compact 90° diverter and sorter module for smaller loads up to 50kg, and M-RAT module for larger loads up to 250kg.
Italy, part of AMETEK Inc., proudly announces the opening of its new Customer Solutions Center in Milan. This state-of-the-art facility is designed to enhance customer experience with its testing capabilities, product demonstrations, and a collaborative approach to innovating across a wide range of applications.
Image shows left to right:Keith Kowalski – Vice President & General Management AMETEK Advanced Motion SolutionsAlessandro Fossati –AMETEK Country Manager Italy, Spain & BrazilStefano Milani – Division Vice President AMETEK Europe & Brazil
The new Customer Solutions Center features solutions from several AMETEK businesses including Creaform, Dunkermotoren, LAND, Haydon Kerk Pittman, MAE, MAGNETROL, MOCON, ORTEC, Powervar, SPECTRO, Taylor Hobson, TMC and Zygo.
“We are proud to launch the new facility which represents our commitment to solving complex challenges through our innovative capabilities and expertise,” said Alessandro Fossati, AMETEK Country Manager Italy, Spain & Brazil. “This facility allows us to bring our innovations even closer to customers, while empowering them to leverage the full potential of AMETEK’s technologies.”
Offering a customized approach to product development and technical consulting, the Customer Solutions Center is designed to drive continuous
F-RAT NX and M-RAT are the only diverters of their type to transfer products at 90° on either side of the conveyor line without needing to lift the product between the entry and the exit, enabling smoother transfers and simpler conveyor design.
MABS, M-RAT and F-RAT are all powered by 24V DC power, enabling designers and specifiers to move away from pneumatically powered systems with all their associated challenges when it comes to commissioning, maintenance and safety.
Tatsuya Akashi, President of Itoh Denki Europe, explained: “As the leading international trade show for intralogistics solutions and process management, LogiMAT once again offers the opportunity for system designer sand specifiers from across the world to see for themselves the gains in productivity and flexibility they can enjoy by choosing systems from Itoh Denki.
“MDR-based systems continue to become the preferred choice for a vast range of applications where performance cannot be compromised, while bringing advantages in terms of enhanced safety - for both colleagues and products –energy efficiency, minimal maintenance, and ease of setup and reconfiguration.
“We anticipate strong interest in all of the technologies we will have on show at LogiMAT.”
innovation across several markets including medical, automation, power, automotive, research, defense, commercial aerospace, metals, oil & gas, semiconductors, food & beverage, and more.
The facility recently held a grand opening event to provide customers, distributors, and partners with a tour of the site’s capabilities and an overview of AMETEK’s offerings.
The new center joins a global network of over 10 AMETEK Customer Solution Centers that expands its ability to serve customers all over the world, while providing localized expertise to help solve their most complex challenges.
Funded by ASI – the Italian Space Agency, the two-year GLAMS Project (Geopolymers for Additive Manufacturing and Lunar Monitoring) aims to create structural elements for the construction of lunar bases through a 3D printing approach that uses cement binders extracted from lunar soils (regolith).
By exploiting locally available raw materials, the concept of the project is to minimize the costs and environmental impact due to the transport of raw materials from Earth to the Moon.
Coordinated by the Center for Space Studies and Activities "Giuseppe Colombo" (CISAS) of the University of Padua, the GLAMS Project holds a partnership with the Institute of Condensed Matter Chemistry and Energy Technologies of the CNR (ICMATE) based in Genoa and WASP, the Italian leader of 3D printing. The project includes Professor Luca Valentini of the Department of Geosciences as scientific manager and Prof Carlo Bettanini and Dr. Giorgia Franchin of the Department of Industrial Engineering who will lead specific work packages.
The research team intends to optimize the lunar cement formulated from regolith soils found on the Moon. The base must consider environmental conditions, including high temperature ranges, reduced gravity, atmospheric pressure, and possible impact of micrometeorites.
During the first phase of the project, Luca Valentini and Giorgia Franchin guided the research unit of the University of Padua for the formulation of the 'geo polymer binders' obtained from the chemical activation of lunar regolith. From here, the Institute of Condensed Matter Chemistry
and Energy Technologies of the CNR of Genoa selected suitable foaming agents that ensure a macro-porous structure affixed to the hardened geopolymeric binder.
Subsequently, WASP implemented the formulations undertaken during the previous phases of the project, to create a prototype of the structural element of a medium-scale macro-porous structure fabricated through 3D printing. Finally, a group coordinated by Carlo Bettanini will provide sensors for the structural elements, integrating appropriate sensor networks, aimed at the continuous monitoring of micro-meteoritic impacts.
The hope is that the GLAMS Project will help meet the needs of space agencies by creating semi-permanent human settlements on the Moon within the next decade.
The project was presented at the 75th International Astronautical Congress (IAC) in Milano, as one of the projects of the IAF SPACE EXPLORATION SYMPOSIUM, for the Session: Moon Exploration. During the event, the research team presented the project and showcased one of the first 3D-printed geopolymer samples, produced using the WASP 40100 LDM equipped with the Manual Feeding System Extruder.
Fiveinternational shipping companies have committed to deploying Orca AI’s cuttingedge automated situational-awareness platform on selected vessels. This milestone follows a strategic partnership forged earlier this year with NorthStandard, one of the world’s largest P&I clubs.
The collaboration between Orca AI and NorthStandard aims to enhance safety and operational efficiency, highlighting the shared dedication of both Orca AI and NorthStandard to innovative solutions that reduce navigational risks and safeguard vessels, crew, and cargo.
US-based Liberty Maritime and Curtin Maritime, Greece-based SeaTraders along with Singapore’s Eastern Pacific Shipping and MMSL, are the first NorthStandard members to adopt the technology. Their decision facilitates broader uptake across the maritime sector and reinforces Orca AI’s and NorthStandard’s mis-
sion to protect members’ assets and ensure the well-being of seafarers.
By implementing Orca AI’s advanced platform — which includes the SeaPod computer-vision lookout unit and the FleetView application for shore offices — these companies are poised to improve navigational safety and enhance their claims records.
“We're thrilled to welcome these established shipping companies as the latest adopters of our technology,” said Yarden Gross, CEO and Co-founder of Orca AI. “Their commitment to safety, efficiency, and reliability not only strengthens their individual operations through proactive risk management but also sets a benchmark for the broader maritime community. As the shipping industry undergoes transformational change, advanced technology is unlocking new opportunities for collaboration that benefit all stakeholders and wider society.”
digital watchkeeper to maximize voyage safety and operational efficiency for ships and fleets.
Powered by maritime purpose-built machine learning and computer vision technologies, the Orca AI platform empowers crew to make data-driven decisions in congested waters and in low visibility conditions. Additionally, it allows fleet managers and operators to have a better understanding of their fleets’ performance and identify unsafe or risky and inefficient behaviours easily.
In 2022, Orca AI empowered the world's first commercial autonomous voyage in partnership with Designing the Future of Full Autonomous Ships (DFFAS) and The Nippon Foundation.
Orca AI’s solution is already utilized by leading shipping companies worldwide, including Maran Tankers, MSC, SeaSpan and NYK.
CMA CGM to reduce methane emissions with newly released EnviroPac feature for Wärtsilä 34DF engine
Technology group Wärtsilä has introduced its new EnviroPac feature for the Wärtsilä 34DF constant speed engine. The feature is designed to significantly reduce methane emissions while maintaining the engine’s high-power output and compliance with IMO Tier 3 NOx requirements. The first order for engines with this new feature has been placed by the French shipping company CMA CGM. The engines will be installed in eight new LNG-operated container vessels being built at the Shanghai Waigaoqiao Shipbuilding (SWS) yard in China. The engine order for the first two vessels was booked by Wärtsilä’s joint venture company, CWEC (Shanghai) Co., Ltd., (‘CWEC’) in Q4 2024.
As ship operators and owners strive for more sustainable operations, LNG plays a key role as a transition fuel, bridging the gap between conventional diesel fuels and future carbon-neutral or carbon-free alternatives. However, the main component of LNG is methane and when burned as a fuel, a very small amount may not combust
properly, leading to methane escaping into the atmosphere. Across the shipping industry, cutting methane emissions is one of the most effective ways to decrease overall GHG emissions from engines over the next 10 years, complementing other efforts to reduce CO2 emissions.
When operating with LNG fuel, the EnviroPac feature cuts methane emissions in half, compared to the standard Wärtsilä 34DF engine. This is without altering the existing power output of 520 kW per cylinder. In addition to the environmental benefit, the reduction in emissions has an impact on costs when operating in EU waters since it results in lesser penalties under both the EU’s Emissions Trading System (ETS) and FuelEU Maritime (FEUM). The EnviroPac feature is available for both new and latest versions of existing Wärtsilä 34DF constant speed engines.
“This is a very important development that will have a major beneficial impact on our operations,” says Xavier Leclercq, Vice President, Newbuilding, CMA CGM. “We are working hard to minimise the
Serlands, proudly announces the launch of the portable InTankFITT® Container, a containerized version of its revolutionary filterless Ballast Water Treatment System (BWTS), InTank®.
Designed to address the growing regulatory and operational challenges in ballast water management, this solution represents a major advancement in maritime technology.
Compact and Portable Design: The containerized system is preassembled and housed within a shipping container, enabling one treatment system to be shared between two or more project vessels or barges that do not require regular ballast water treatment.
environmental footprint throughout our fleet, and this latest technology from Wärtsilä provides strong support to these efforts.”
The eight 9200TEU LNG-powered vessels will each operate with two 6-cylinder Wärtsilä 34DF and two 9-cylinder Wärtsilä 34DF EnviroPac engines, as well as the selective catalytic reduction (SCR) systems. The Wärtsilä equipment is scheduled for delivery to the yard commencing in early 2026.
“We are proud to launch this new EnviroPac feature for our already efficient Wärtsilä 34DF engine. Our long-standing relationship with CMA CGM is once again enhanced with this order, and we complement them on their vision for actively achieving sustainability throughout their fleet,” comments Stefan Nysjö, Vice President of Power Supply, Wärtsilä Marine.
Regulatory Compliance: InTank’s automated treatment provides assured compliance – treatment is checked twice and the TRO is recorded before discharge with automated, easy-to-read treatment reports available to the crew, port authorities, and customers before discharge.
Operational Efficiency: The filterless design eliminates the need for a complex and lengthy filtration process, reducing operational downtime and maintenance requirements. Fitted to a port-based ballast water reception barge, InTank’s non-filter and in-tank treatment makes receiving water from a discharging vessel very simple.
Scalable and Flexible: ideal for retrofits and temporary applications, the container design can be mounted on the deck or placed on a temporary platform for operation. The system's compact design allows it to be housed in a standard 20-foot container, facilitating worldwide shipping. InTank water treatment is not linked to ballast operations, removing stress during intake and discharge.
‘The application for the SciencoFAST InTank Container is for up to 50,000 DWT (or system can treat 500-5,000 m3 of ballast water, up to 12 tanks (upgradeable) and all water types), which is a significant portion of the market. UniBallast offers this as both a product and a service, and this new capability not only simplifies ballast water management but empowers ship-owners and operators to achieve compliance with confidence and ease’ said Rudy Mes, Sr. Vice President.
The InTank Container is for hire or purchase and is available for ordering starting 2025. Demonstrations are available in Rotterdam and additional product information is available at info@uniballast.nl or intank@sciencofast.com
Donut Lab presents further advanced technology for electric vehicle development in partnership with software company Qt
Donut Lab, a pioneer in electric transport solutions, unveils at CES its plan to enhance the Donut platform with new technology solutions and artificial intelligence features. This update will not only simplify and expedite vehicle development but also mark the beginning of a strategic partnership with software company Qt, whose innovative service will be seamlessly integrated into the Donut platform.
In November, Donut Lab introduced its modular technology platform, offering a library of compatible components, such as an electric motor, battery pack, and on-board vehicle computer. These components have been designed to operate together without any manual integration work, which significantly accelerates and simplifies the development of electric vehicles.
Now, at the CES trade show, the company is revealing more about the features of the upcoming software layer of the Donut platform. The Donut platform aims to speed up the development of vehicle software by 10-fold while increasing vehicle safety and testing through new technologies. Donut Lab says it is developing the world's first no-code environment for vehicles, which means that, in the future, all software logic for cars and drones can be done with a graphical user interface
instead of traditional programming-based code. This significantly reduces the number of errors, increases vehicle safety and accelerates development work.
“Although the physical components of the Donut platform, such as the motor and battery pack, are already revolutionizing the automotive industry, a completely new software layer has also been part of the plan from the very beginning. With the help of an intelligent software layer, we can automatically integrate physical components, but in addition to this, we are now developing future software development solutions that will make vehicle development significantly more efficient and agile. At the core of all of this is advanced artificial intelligence, and in the future, the artificial intelligence features of the Donut platform will improve vehicle design, development, testing and validation in unimaginable ways,” says Marko Lehtimäki from Donut Lab.
Unique collaboration automates the development of HMI interfaces for vehicles
Donut Lab's vision for the Donut platform is to create a dynamic ecosystem of technology partners that fosters continuous innovation and enhances vehicle development methods. The platform's scalability and seamless integration of third-party technologies, both software and hardware, are designed to bring this vision to life.
Donut Lab's strategic collaboration with the international software company Qt is a significant step towards its vision. At the CES trade show, Qt introduced its new Qt Accelerate solution, a game-changer that will automate and streamline the development of HMI (HumanMachine Interface) user interfaces for electric vehicles. This innovative solution will soon be integrated into the Donut platform, further enhancing its capabilities.
“With the help of Qt Accelerate, the development of HMI interfaces will become automated and significantly more efficient. The technology to be integrated into the Donut platform will recognize the vehicle configuration and will be able to create an HMI that matches the vehicle's actual features. This takes place completely automatically and therefore requires no manual work,” says Petteri Holländer, Senior Vice President, Ventures, Qt Group.
"Qt Accelerate offers an extremely fast and efficient way to create HMIs fully automatically without programming and is designed specifically for the needs of the automotive industry. Our collaboration provides significant advantages to the development of vehicles, and it is also the first step in building a broader ecosystem for the Donut platform," Lehtimäki continues.
Wärtsilä Gas Solutions, part of technology group Wärtsilä, will supply the cargo handling systems for three new 93,000 m3 capacity Very Large Ammonia Carriers (VLACs). The ships are being built at the Korean shipyard Hanwha Ocean Co, formerly known as DSME. Two vessels are for a Greek ship owner and one for a Japanese owner. These two orders, both booked by Wärtsilä in Q4 2024, further strengthen Wärtsilä’s position as a market-leading supplier of cargo handling systems.
The Wärtsilä scope for the complete Cargo Handling System encompasses the engineering scope, the material scope, and the supervision, commissioning, and gas trial scope. This comprehensive system is designed to ensure optimal performance and safety in cargo handling operations.
“We are happy to have Wärtsilä as a project partner for these ships. We have earlier worked with them and have complete trust in the efficiency and reliability of their products,” says Mr. Lee, Leader of Basic Design Team, Hanwha Ocean Co.
VLACs are essentially Very Large Gas Carriers but designed to carry full cargoes of ammonia. Since ammonia has a high specific gravity, VLAC cargo tanks and hulls need to be reinforced, and the vessels will have a deeper draught when fully loaded.
cargo handling systems for vessels in this segment,” comments Patrick Ha, Sales Manager, Wärtsilä Gas Solutions. “We have enjoyed a long and successful relationship with Hanwha and look forward to building an even stronger relationship with ship owners through this project. We are very pleased to continue this relationship with both companies, and fully committed to providing our full support throughout this latest project.”
The Wärtsilä equipment is scheduled for delivery to the yard commencing in Q2 2025.
SUUS expands cooperation with Hisense by opening a dedicated warehouse in Warsaw
The new development of nearly 50,000 m² is a state-of-the-art logistics warehouse designed to handle Hisense products, as well as Gorenje and ASKO, which are part of the Hisense Group. The facility offers block and rack storage, including bonded and recognised storage. It consolidates processes previously carried out in four different locations, making them more efficient and reducing costs. This is the next stage in SUUS' more than five-year collaboration with this rapidly growing manufacturer of white goods and consumer electronics. Currently, in the supply chain of the Hisense brand, the operator provides: warehousing, order picking, import and export customs handling, domestic distribution, as well as full-vehicle road transport to foreign markets, including Ukraine, Moldova or the Baltic States. There are plans to develop further destinations.
Krzysztof Rzeźniczek, director of the Rohlig SUUS Logistics branch in Warsaw, says: "For us, the cooperation with Hisense is a strategic project that shows how, through joint action and mutual trust, we can grow together. When we started our cooperation in 2019 at the customer's warehouse in Ożarów Mazowiecki, we were managing an area
of 10,000 m². Five years on, we are opening a dedicated location with five times as much space, where we can handle 100 cars on a single day. We are also consolidating existing processes from other locations there. One logistics centre means less reloading, which means a more efficient and costreducing distribution process". He adds:. "The challenge in launching the warehouse was to efficiently relocate 800 semi-trailers with goods from the previous locations, while accepting a similar number of new products from the factories and maintaining the continuity of the customers' logistic processes. We coped with this"..
Arkadiusz Olszewski, Regional Logistics Director, Hisense Polska, says: -"The consolidation of the warehouses is a milestone in our logistics strategy, bringing a number of tangible benefits for both the company and our customers. Thanks to close and long-term cooperation with a proven partner such as Rohlig SUUS Logistics, we have managed to optimise our warehouse processes, which will translate into faster order fulfilment and optimised operating costs. This project will also allow us to increase the efficiency of stock management, which will result in greater flexibility in responding to market needs. We are convinced that the launch
of this dedicated and state-of-the-art warehouse will have a positive impact on the quality of service provided to our customers and the further dynamic development of our company".
Rohlig SUUS Logistics' new logistics centre has been located in Park P3 Warsaw I. It is located south of Warsaw just 13 km from its ring road and 8 km from the S8 expressway. The logistics park comprises 3 buildings with a target area of 115,365 m2.
Zbigniew Smyczyński, Head of Development P3 Logistic Parks in Poland, says: "Warsaw and its surroundings are one of the most dynamically developing logistics regions in Central and Eastern Europe. Thanks to its excellent connections to the main traffic arteries and proximity to the international airport, P3 Warsaw I can become a key hub for both national and international distribution. Our park offers state-of-the-art technological and environmental solutions, making it an attractive choice for companies concerned about sustainable development. The lease of such a large space in P3 Warsaw I by Rohlig SUUS Logistics is proof that our park meets the highest standards and expectations of our customers".
Continue reading at: www.industryeurope.net
AutoFlight, a leading innovator in electric vertical take-off and landing (eVTOL) technology, has marked a significant milestone with its first successful flight in Japan. On November 29, the company’s two-ton eVTOL aircraft completed its inaugural demonstration flight in Okayama Prefecture.
The historic eVTOL flight was conducted in collaboration with MASC, a Japanese nonprofit organization dedicated to aerospace industry advancement. With full approval from the Japan Civil Aviation Bureau (JCAB), this achievement represents a crucial step forward in MASC’s “Setouchi Community AAM Infrastructure 2028 Project” (SCAI28).
The successful demonstration paves the way for future test flights across multiple Japanese cities, accelerating the path toward commercial Advanced Air Mobility (AAM)
operations in Japan. This initiative aligns with the country’s vision for next-generation urban air transportation.
The Setouchi region, a vital coastal area along Japan’s Inland Sea, connects three of the country’s main islands: Honshu, Shikoku, and Kyushu. The region currently faces significant challenges, including aging infrastructure in coastal areas and limited transportation options between the mainland and remote islands. Through the SCAI28 project, MASC aims to address these challenges by implementing innovative air mobility solutions while fostering local industrial development.
AutoFlight’s state-of-the-art eVTOL aircraft features a Lift and Cruise configuration and all-electric propulsion system. Its vertical take-off and landing capabilities eliminate the need for traditional runways, while its efficient
transition to horizontal cruise flight enables extended range operations. This innovative design achieves an optimal balance of range and efficiency, offering a safe, reliable, and environmentally conscious transportation solution. This eVTOL model along with the future new model are poised to serve multiple roles in the Setouchi region, from cargo transport to future passenger transport as well as medical assistance and tourism services.
As countries worldwide race to implement Advanced Air Mobility (AAM) solutions, eVTOL technology has emerged as a key enabler. The industry is advancing through demonstration flights in diverse scenarios, while simultaneously developing essential infrastructure including vertiports, digital management platforms, and regulatory frameworks. Continue reading at: www.industryeurope.net