
12 minute read
Universities, Research & Collaboration
Pioneering collaboration between Rockwell Automation and University of Melbourne to help decarbonise Australia
Rockwell Automation and the University of Melbourne signed a Memorandum of Understanding (MoU) on Wednesday for advancing digital innovation to help decarbonise manufacturing and resource industries.
Advertisement
This union of an eminent Australian university and the world’s largest company dedicated to industrial automation and digital transformation is a major step forward that ultimately will help Australian businesses achieve environmental objectives increasingly demanded by consumers.
Rockwell Automation and the University of Melbourne will collaborate on research activities, jointly develop training and work together to help solve real-world challenges presented by industry.
Rockwell Automation will contribute engineering resources and product training to the project. The university will bring academic and research expertise, and world class innovation infrastructure.
Anthony Wong, regional director, South Pacific, Rockwell Automation, said the MoU marks an important new phase that will benefit industry.
“Decarbonisation is now front of mind for Australian industrial companies,” Mr Wong said. “They know they must act to remain attractive to consumers and meet compliance targets, but they often don’t know how to start or where to focus their energies for the greatest returns.”
“Rockwell Automation and the University of Melbourne are coming together to share our expertise and explore practical solutions to this challenge.”
University of Melbourne will provide research expertise, academic and physical resources, and use the collaboration to give its students real-world training, preparing them to tackle tomorrow’s engineering challenges – including using digital innovation – to accelerate decarbonisation and become future leaders in their field.
Faculty of engineering and information technology dean, University of Melbourne Professor Mark Cassidy, said the MoU would allow the two organisations to collectively deliver outcomes that could not be achieved independently.
“Our engineering and information technology talent and resources, and Rockwell’s capital and expertise are perfectly placed to achieve the digital transformation of Australian industrial manufacturing that is needed. We see this collaboration as a key opportunity to demonstrate the university’s research capabilities, while providing opportunities to enrich our students’ learning experience through industry-led challenges and access to state-of-the-art technology,” Professor Cassidy said.
Industry backs collaboration
The collaboration officially commenced at an MoU signing event at Melbourne Connect on Wednesday July 27. Guests from the manufacturing, resources, food and beverage, and agricultural processing industries heard from a panel of experts discussing the role of industry-university collaboration in solving digital innovation challenges. Speaking ahead of the event, the panellists expressed their support for the concept saying:
“Bega Cheese have seen the advantages of partnering with the University of Melbourne. The value of bringing together a leading, global technology provider in Rockwell Automation, with the University and industry will be of great benefit to all parties.” - Anthony Bourke, General Manager, Operations, Bega Foods
“Developing strong tripartite relationships between industry, solution providers and universities, is fundamentally important to accelerating development and solving important strategic problems in vital industries.” - Michelle Ash, Technology Executive, Oz Minerals
“Learnings from the pandemic are still emerging, but I hope we are appreciating the value of a competitive and sustainable local manufacturing industry. Striving for cost competitiveness and improved sustainability should not be seen as opposing business goals. We can achieve both – reducing waste lowers costs and improves sustainability, and likewise, integrated digital solutions can enhance market responsiveness and encourage circularity.” Associate Professor Jo Staines, Enterprise Fellow, University of Melbourne.
Industry Update applauds this ground breaking venture between two giants – Rockwell Automation and the University of Melbourne.
Rockwell Automation
rockwellautomation.com/en-au
University of Melbourne
unimelb.edu.au
Industry Update promotes collaboration with new university section
Continued from front page
investment to boost the Australian economy by promoting collaboration between universities and industry.
While the plan was announced by the previous government, we see no good reason why it would be cut by the new executive. It’s an eminently sensible scheme, relevant to the goals of both major parties.
If Albanese is to deliver on his commitment to ensure Australia is “a country that makes things”, this is just the sort of program he should maintain. Indeed he should expand it.
Thanks to the visionary commercialisation action plan, never before has there been a better time for universities and business to collaborate. And never before have Australia’s researchers and universities been presented with such strong incentives.
Most of the funds ($1.6 billion) from the $2.2 billion plan are being directed towards a program called Australia’s Economic Accelerator. The AEA aims to overcome the so-called ‘valley of death’ between promising early-stage research and commercialisation.
Plenty of good Aussie ideas struggle to make the latter stages of development because of commercial risk and uncertainty. The AEA will help bridge this gap.
It has just commenced providing grants to universities to support projects aligned with the six National Manufacturing Priorities: • space • medical products • resources technology and critical minerals processing • food and beverage • defence • recycling and clean energy
The AEA is a fast-fail model designed to attract projects at a proof-of-concept or proof-of-scale level of commercial readiness.
To incentivise performance, the funding increases as projects mature towards at-scale commercialisation.
Examples of industry involvement in AEA include embedded industry experts, memoranda of understanding, in-kind support, formal partnerships and co-investment.
Under AEA, $150 million is slated to expand CSIRO’s Main Sequence Ventures to harness venture capital investment.
The commercialisation action plan also includes $242.7 million in competitively allocated ‘trailblazer’ funding for a select group of universities with projects that are aggressively pushing the envelope on industry partnership and commercialisation.
Trailblazer objectives are to promote open and collaborative IP agreements, incentivise researcher engagement with industry, and achieve co-funding and genuine collaboration from business.
Moreover, the government is fostering workforce mobility between academia and business with $296 million for 1,800 ‘National Industry’ PhDs over 10 years.
These consist of two sorts of doctoral programs: ‘University-led Industry PhDs’ undertaking research projects in collaboration with industry, and ‘Industry-driven Researchers PhDs’ that go to industry professionals supported by their employers to undertake PhD projects in partnership with a university. These will help build interlocking relationships between the sectors.
Crucially, the government is transforming the university IP framework to facilitate greater collaboration by universities and improve attractiveness for Australian business.
To achieve the aim of bridging the cultural divide between universities and business, the commercialisation action plan will shift the dial on research funding incentives from blue sky ideas, targeted at publication in prestigious international journals, to more concrete real-world research orientated towards solving practical problems in the context of commercial realities.
Whether the plan fully delivers on this lofty ideal remains to be seen, but it’s a necessary step in the right direction.
And Industry Update will be there to support it every step of the way, as part of our ongoing commitment to Australian manufacturing. We are excited to launch Universities, research and collaboration.

CSIRO Robot Olympics prize money to train next generation of Aussie scientists
The CSIRO is providing $1.2 million to support eight robotics scholarships at Queensland University of Technology, targeting high-performing students in groups underrepresented in the industry.
The funds were sourced from the CSIRO’s winnings in its historic podium finish at the 2021 DARPA Subterranean (“SubT”) Challenge. The “SubT” Challenge is a competition organised by the Defense Advanced Research Projects Agency under the US Department of Defence. It aims to explore new approaches to rapidly map, navigate, and search underground environments.
A world-class robotics research and education institution, QUT has a track record of educating some of the best and brightest minds in the robotics industry.
Professor Elanor Huntington, CSIRO Executive Director of Digital, National Facilities and Collections said the scholarship fund was an investment in the future of Australian robotics and would spread the benefit of the win across the entire community.
“In 2021, a group of robotics experts from Queensland took on the world’s best in a competition dubbed ‘the robot Olympics’ and came second in a photo finish,” Professor Huntington said.
“Using that prize money to educate a diverse cohort of robotics experts – who might be a 2031 DARPA Challenge team - will help Australia seize the AU $22.17 trillion global AI opportunity.
“We know that diversity is the engine room of innovation, and we hope to inspire and support a dynamic new generation of robotics talent,” she said.
Diversity in the Australian
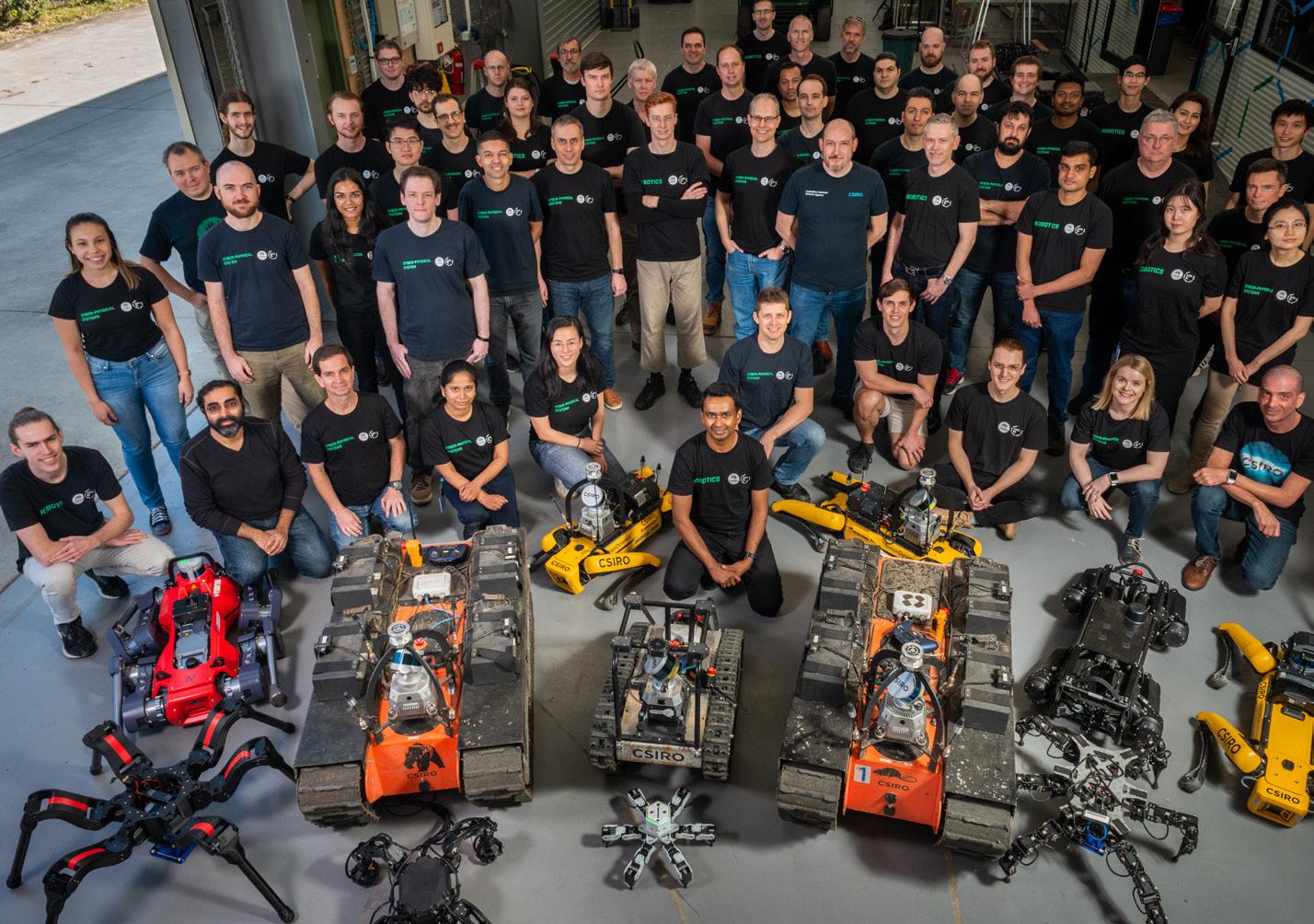
CSIRO’s Robotics and Autonomous Systems Group
robotics industry is one of the key obstacles to its growth according to Robotics Australia Group’s A Robotics Roadmap for Australia 2022 report released late last year. The government’s 2021 STEM Equity Monitor reported men accounted for 87 percent of 2020s national STEMqualified occupations.
CSIRO and QUT will jointly oversee applicant selection, course design, education, and mentorship. Applications will open in September 2022 and close in 2027.
CSIRO puts the smart into smart manufacturing
Australia needs to develop its innovation eco-systems. Collaboration – between technologists, researchers, innovators, commercialisers, investors and customers – is critical. Where can businesses look for guidance? Industry peak body groups are a starting place. The CSIRO, Australia’s National Science Agency is another. CSIRO’s R&D Labs, SME Connect, and Kickstart programs are designed to support collaboration between likeminded change-makers.
CSIRO draws ideas from international innovation initiatives such as Plattform Industrie4.0 in Germany, the CESMIS Smart Manufacturing institute in the USA, and Catapult UK model. Each of these have industry sectoral or technology specific foci, open standards and reference architectures, specifically funded technology deliverables, innovation processes, and their network of networks.
But what aspects are best suited to Australian requirements and industry scale? This requires judicious collection and analysis of data and information. Valuable work here includes CSIRO’s Advanced Manufacturing Roadmap, AMGC’s Sector Competitiveness Plan and the CSIRO’s National Hydrogen Roadmap.
Every business and industry sector has unique challenges, so organisational strategy development is a complex sectoral or organisational task. Strategies were once considered limited to lowest cost economy of scale, differentiation and niche positioning. But now we might consider cost leadership, value-chain leadership, design leadership, syndicate leader, and more. Diverse frameworks can be valuable.
Advances in product design creates competitive advantage. CSIRO looks to integrate advances in artificial intelligence and computational modelling to optimise product performance. Can AI make ‘left field’ suggestions that create step changes in performance? To test this hypothesis CSIRO is working on AI based design methods for catalysts and static mixers in flow chemistry, and in robotic soft gripper design.
More intelligent products that are cloud integrated can offer the opportunity for hardware as a service (HaaS), also known as servitisation. Moving costs from capital expense to operational expenses can be attractive to both supplier and client. CSIRO is exploring how to make battery management systems more intelligent, integrating battery chemistry with cloud data to optimise lifecycle and performance. CSIRO is working on numerous direct to market technology solutions, including secure and intelligent IoT wireless mesh networks featuring sensor integration featuring and integrated business rules engine. Another solution in the works is robotic additive manufacturing for metal component repair and maintenance featuring self-calibrating computer vision and real-time sensor fusion.
CSIRO is also working on foundation platforms to facilitate fast and robust solution development. For example, artificial intelligence augmented design tools incorporating experimental and computational methods (aka AI4Design).
Under development are novel approaches to integrate multiple computer vision sensors at multiple scales for real-time closed loop process control at the micro-scale such as in robotic additive manufacturing, and end-of-arm collision avoidance at a larger scale.
The above emerging technologies are variously involved in a range of CSIRO collaborations. This includes, for example, developing intelligent secure by design wireless mesh networks for complex assembly in aerospace structures, ship building, industrial and building construction. It also includes supporting a shift from batch to flow chemistry, suited to Australian scale of niche, high value bespoke chemical synthesis.
Additive manufacturing has had decades of
development, but CSIRO is still leading internationally in many areas. CSIRO’s Clayton based Lab22 facility has pioneered the reliable use of several exotic materials for medical implants. More recently, advances in cold spray, laser and wire arc, have progressed from simple 3D metal printing to complex six degree of freedom robotic metal deposition. In conjunction with real-time laser scanning, robotic factory floor or in-the-field repair or modification of metal structures such as defence equipment or foundry castings is feasible and cost effective. Advanced sensor systems and algorithms to compare scanned point-clouds against CAD specifications to determine defects, or to place new enhanced features, will soon be available as part of the robotic additive manufacturing toolkit. Innovation today requires a change of thinking at all levels. Essential skills include the ability to create, recognise, and cultivate innovation opportunities. We need to foster these at a national level. One approach might be with innovation micro-credentials, such as in global IP scanning, innovation pipeline development, discovery sprints, investment proposal writing, fail fast to innovate philosophy, and more. We need to get better at “delivery science”. Many of our corporate leaders typically come from finance, law and risk. We must build capacity in science, technology, change and innovation. Another more bold approach may be a national open innovation platform including standards, guidelines, case studies, a grant/investment concierge, and eco-system collaboration tools (i.e. at the national, state, regional, sector specific, and technology specific levels). CSIRO’s new Future Digital Manufacturing initiative brings together our domain experts and world leading innovations across physical and information sciences to underpin business aspirations. If you are an ambitious SME, or you deliver high value manufactured solutions, or seek to target emerging future industries, then CSIRO is positioned to be a solution partner. Christian Ruberg, Future Digital Manufacturing Lead, CSIRO Manufacturing and acknowledging the collaboration with my team colleagues Dr Simon Dunstall & Dr Melanie Ayre. Free education, guidance and leadership for Australian manufacturers seeking advancement, competitiveness and growth. 9 learning modules 20 real stories of Australian success 4+ hours of content manufacturingacademy.org.au SCAN TO FIND OUT MORE
Christian Ruberg, Future Digital Manufacturing Lead, CSIRO Manufacturing. Australia languishes at 91 of 133 countries on the Harvard Economic Complexity Index. The index captures an economy’s sophistication and diversity – and is linked to growth prospects. Christian Ruberg, Future Digital Manufacturing Lead, CSIRO explores how collaboration and organisational strategy can help up Australia’s game. MARKET REACH WORKFORCE RESILIENCE THE STATE OF MANUFACTURING COMPETITIVENESS PRODUCT VALUE INDUSTRY 4.0 MANUFACTURING WITH ROSIE THE CIRCULAR ECONOMY
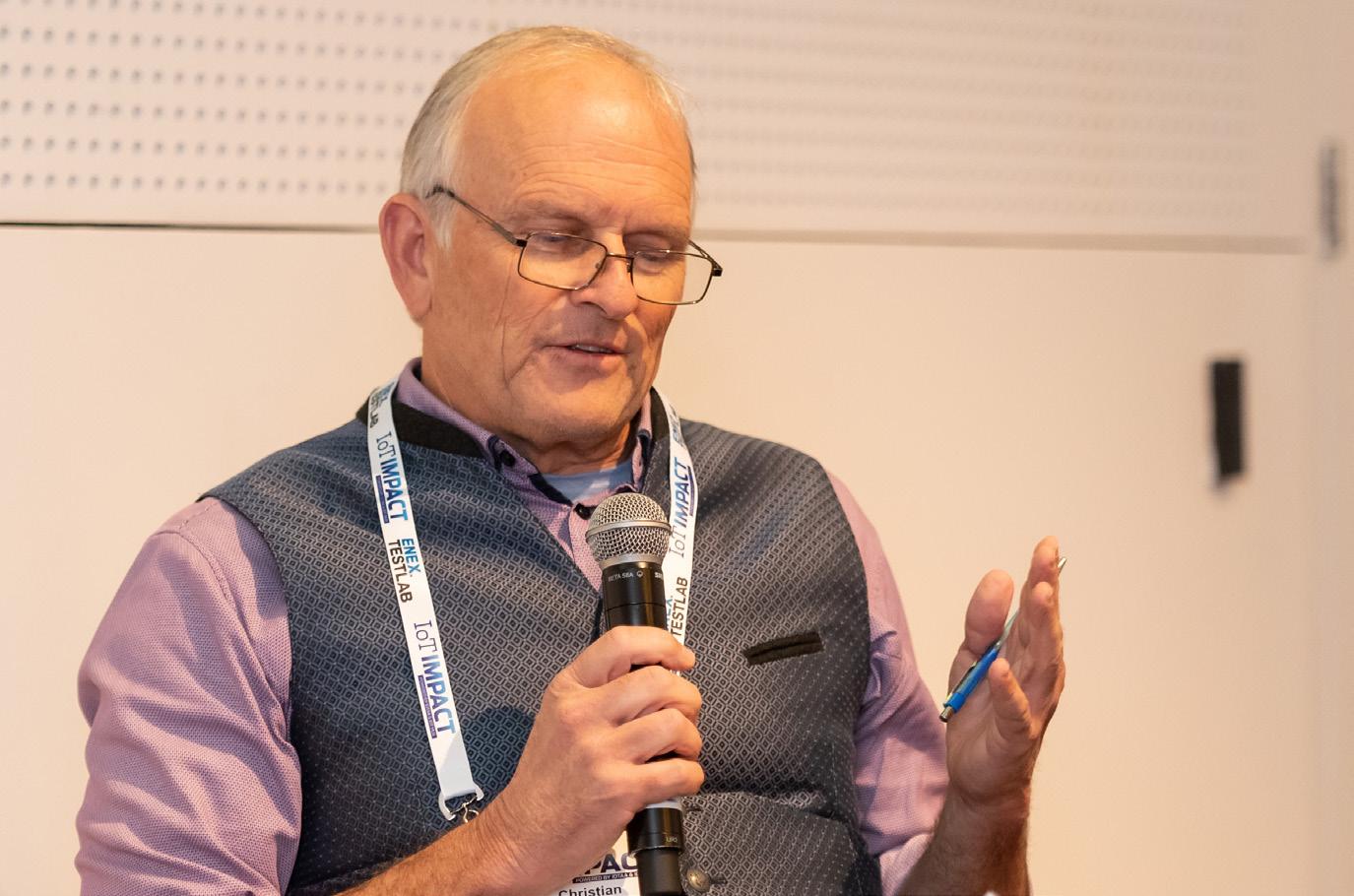