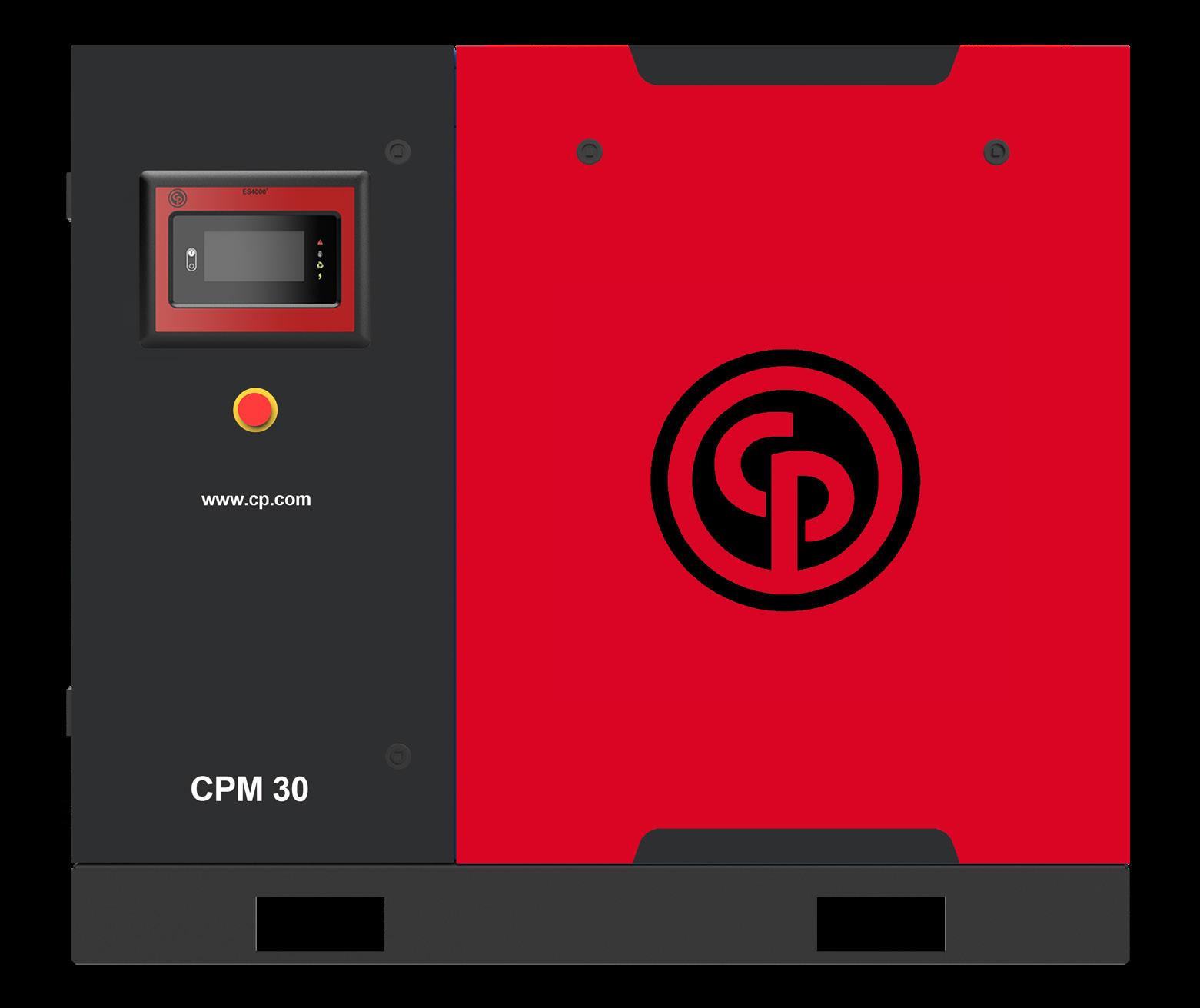
6 minute read
Compressors
New compressor technology adds high powered precision to laser cutting
Chicago Pneumatic CPM 30 Air Compressor
Advertisement
Chicago Pneumatic are proud to introduce a new 16 bar compressor for the laser cutting industry. Our brand-new cut through technology means you can cut through the competition.
Laser cutting, which is a thermal cutting method, uses a focused high-power and high-density laser beam to irradiate the workpiece, so that the material melts, is vaporised, or is blown away.
The main factors affecting the metal laser cutting’s efficiency and thickness are the power of the laser cutting machine, the type of auxiliary gas, the pressure, and the flow rate of auxiliary gas.
Air compressors, as the auxiliary gas provider, play a critical role in laser cutting. When choosing air compressors for laser cutting machines, these factors should be considered:
The quality of compressed air has a direct impact on the quality of laser cutting. Compressed air contains water, mist and oil. If the protective mirror of the laser cutting head isn’t cleaned with a high-pressure jet, there’ll be serious consequences for the transmission of the laser beam. It will disperse the focus, cause the product to be cut incompletely, and lead to waste products. Therefore, the air compressor must be equipped with a good dryer to remove the moisture in the compressed air as much as possible. Highprecision filters must also be installed to fully filter oil and dust particles. Also, once the compressed air is dried, then the temperature returns to normal, which effectively avoids condensation. High-quality compressed air can sustain the long-term stable operation of laser cutting machines.
As laser cutting machines have developed to produce higher power, the pressure requirement of the air compressor supporting the laser cutting has also increased - from an initial 8 bar, to 13 bar, and now to 16 bar.
Higher air pressure brings better cutting quality and higher cutting efficiency.
How can we help you?
With high outlet pressure we ensure: • Cutting speed and thickness • Blow away metal debris • High efficiency in cutting
With stable free air delivery, we can ensure the quality of the surface (smooth like a mirror) and with less water and oil in the air, we can ensure the lifetime of the laser heads.
Key features: • 16 bar outlet pressure • Dew point controlled dry air • High efficiency coalescence filtration • Activated carbon filter for clean oil-free air
Who are we?
Chicago Pneumatic is a market leading manufacturer and distributor of compressed air products such as screw compressors, piston compressors and air treatment. When you are in need of an industrial or professional air compressor system, Chicago Pneumatic is sure to have the right solution.
We have used our years of experience to design compressors that are efficient and reliable. Our products are tailored to suit your needs.
Our people start every single day with a passion to research, develop, manufacture and deliver new products that are meant to meet your needs not only today, but tomorrow as well.
All this has come together because we have consistently practised our brand promise — People. Passion. Performance.
Chicago Pneumatic
cpcompressors.com.au
Experience the Power of Red

www.cpcompressors.com.au 1300 555 284
Brand NEW cut through technology cuts through the competition!
Features:
4 models (11-22kw) 16 bar Cutting speed and thickness Complete package: Compressor; 400L tank; Air Dryer; Pre/Post & Activated Carbon Filters
CPM Series 15-30
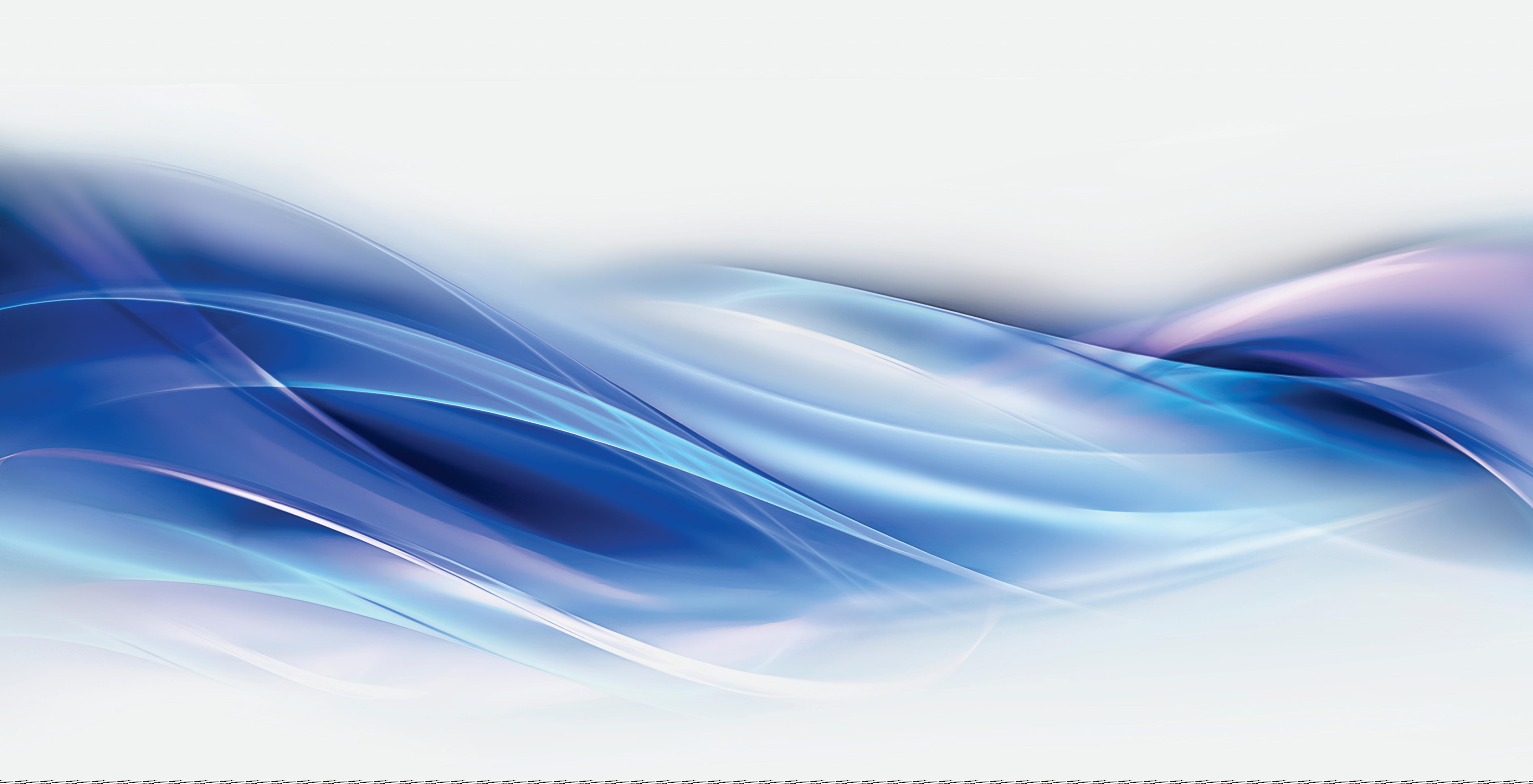

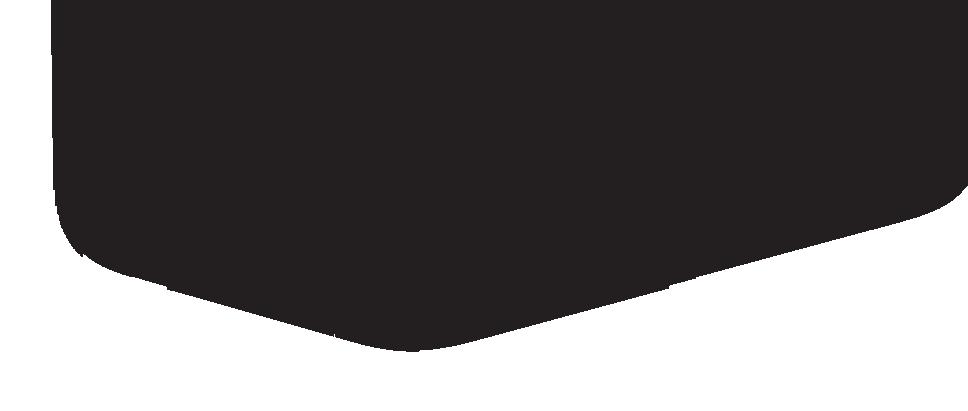
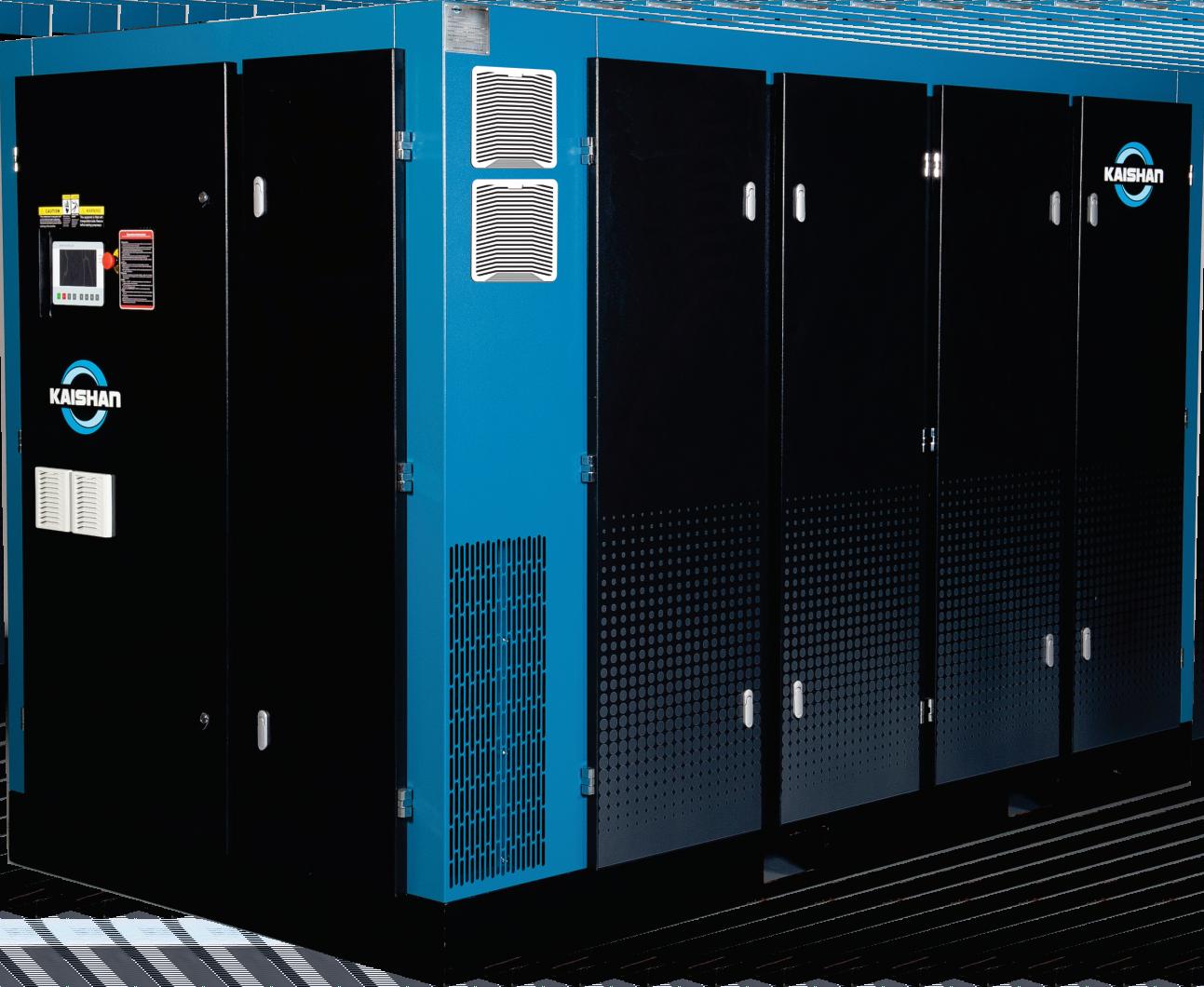
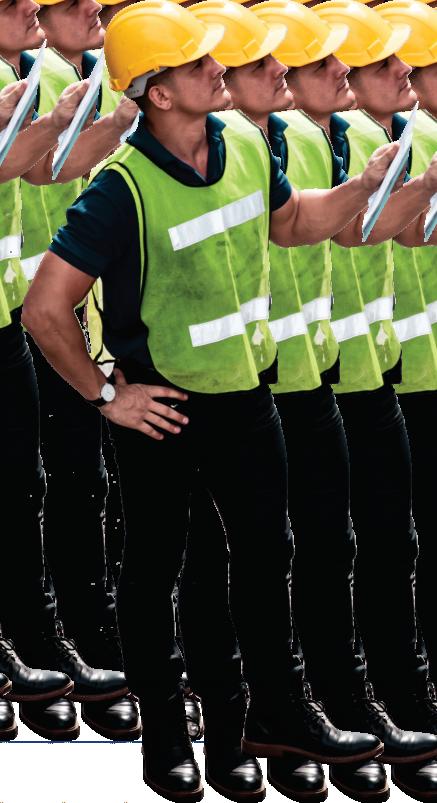
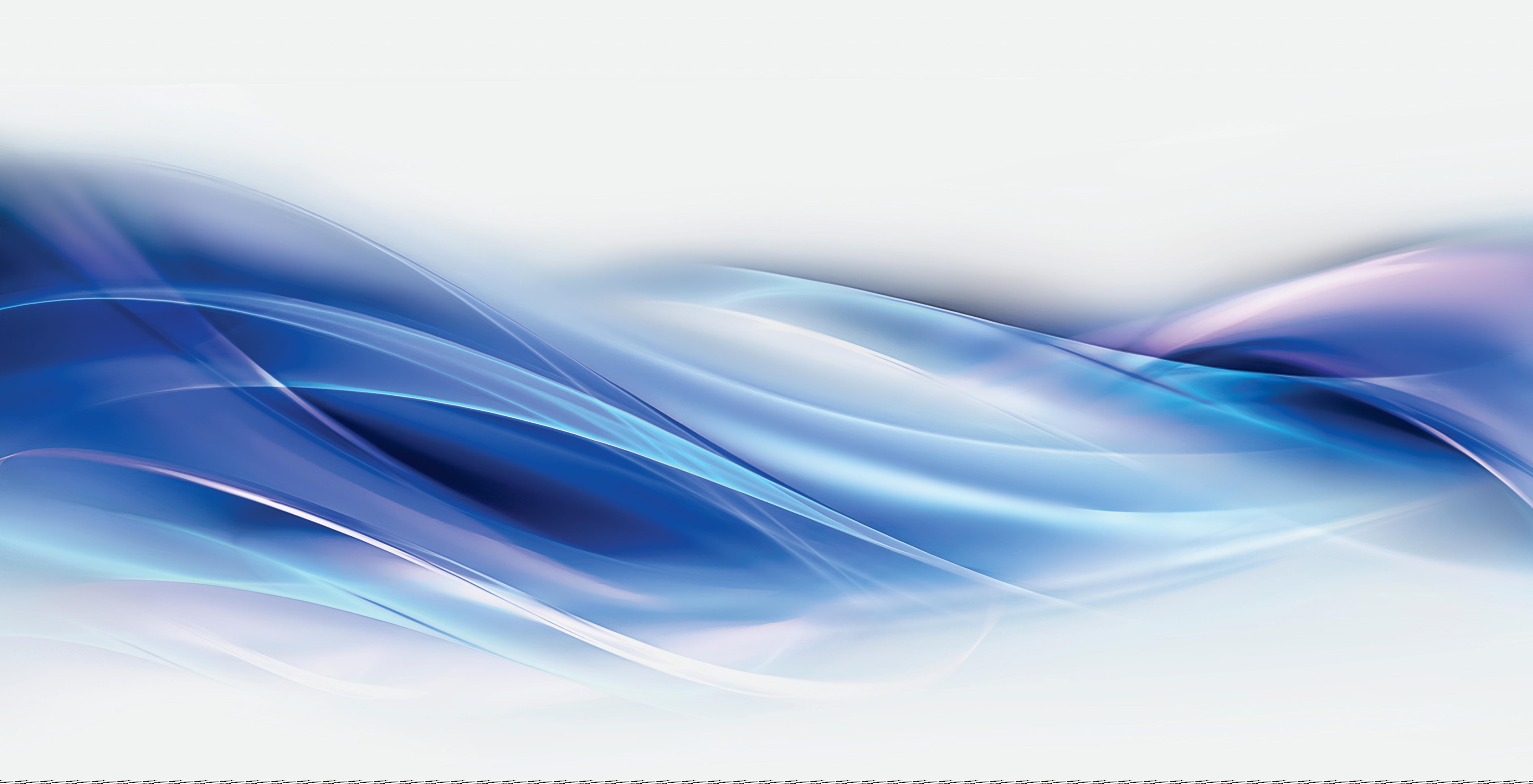
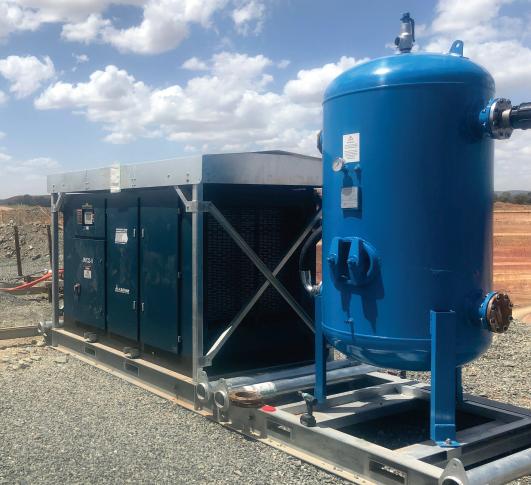
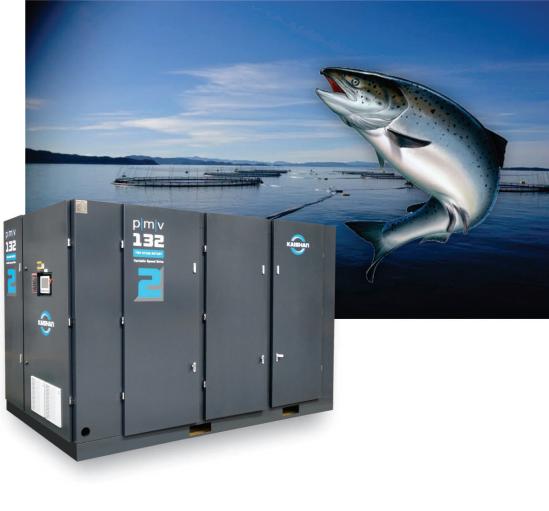
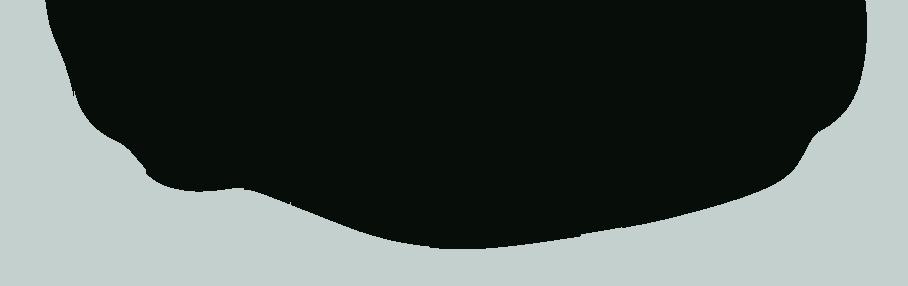
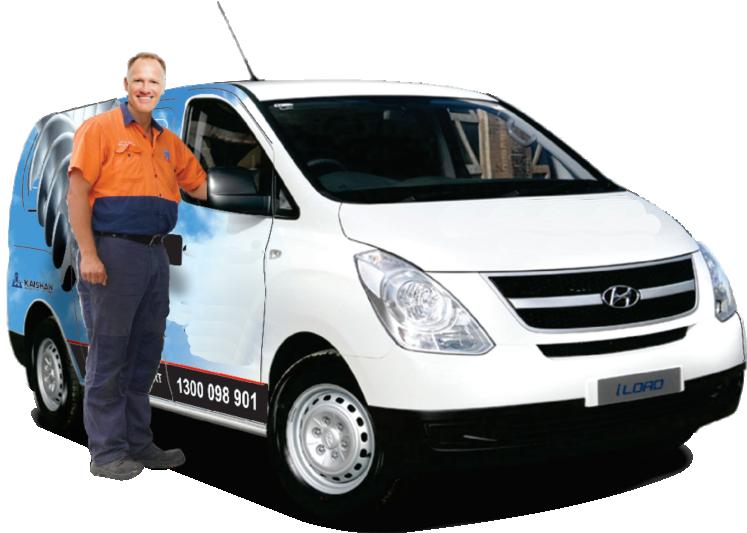

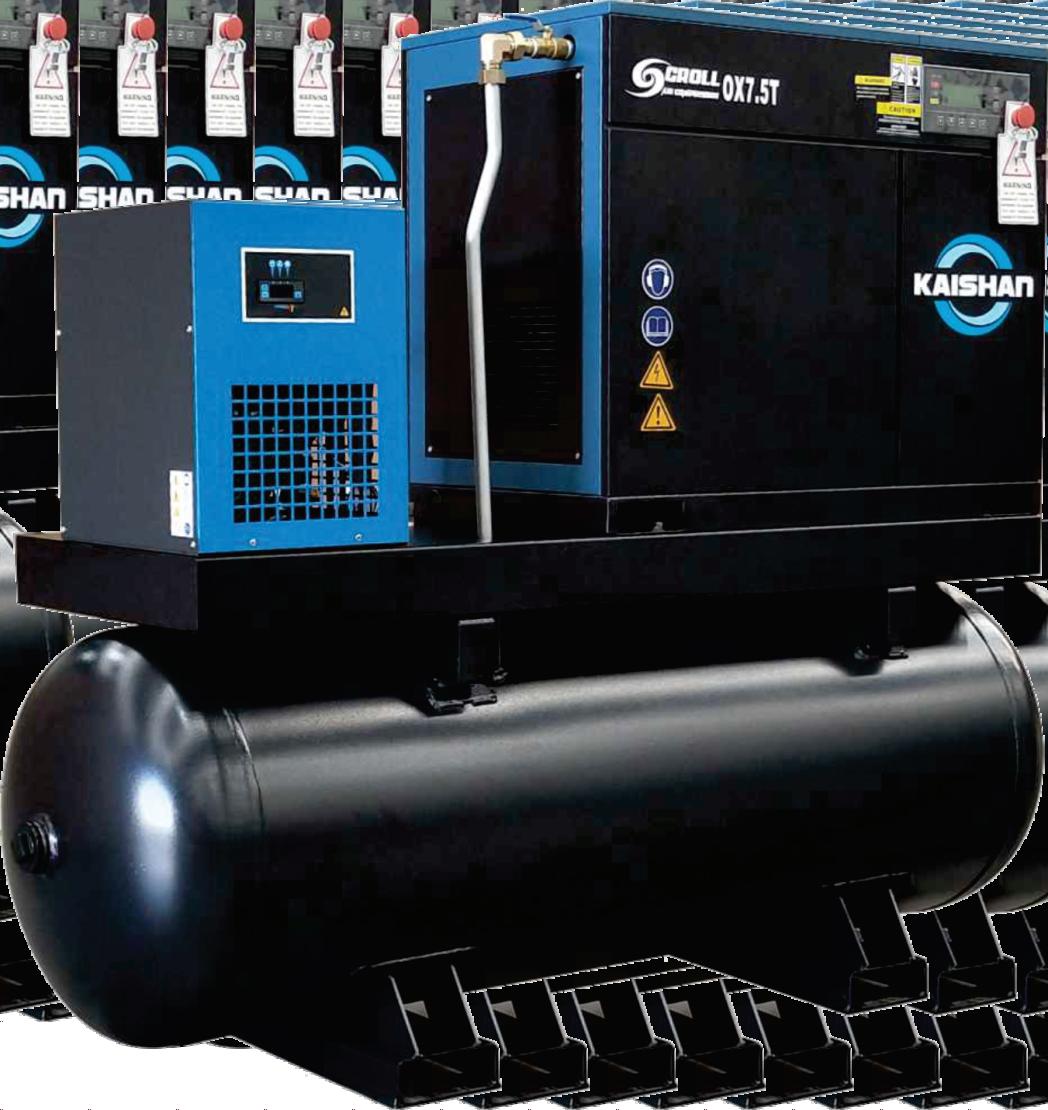
Sustainable air power for recycling operations
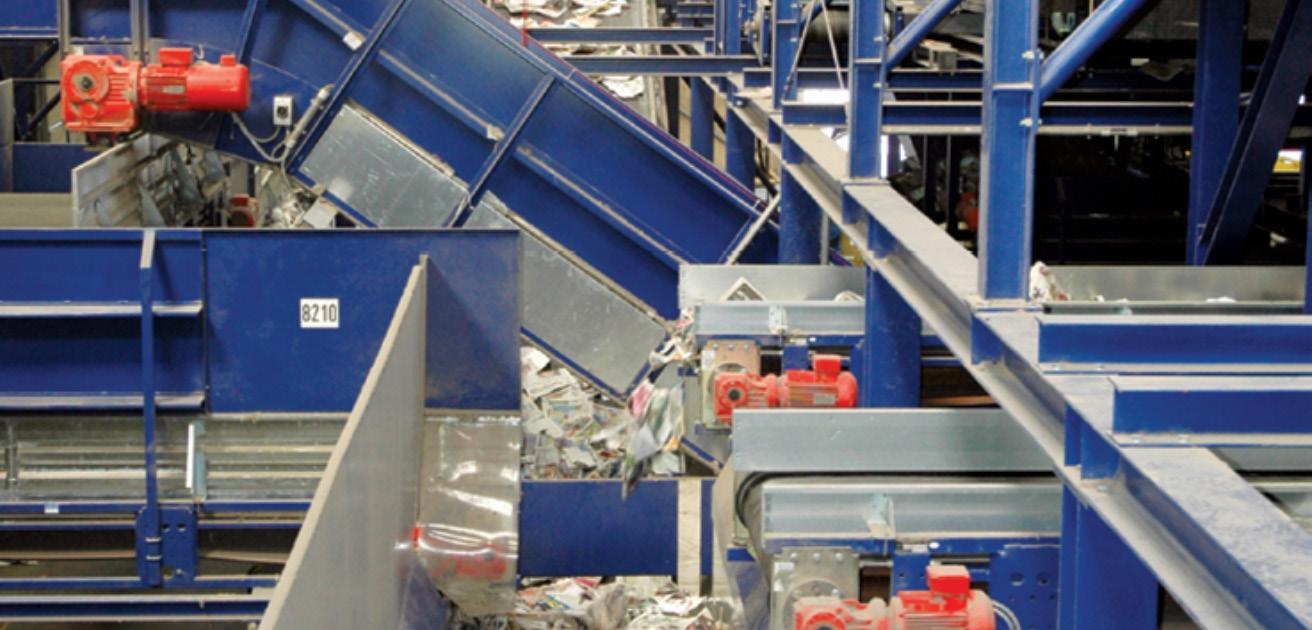
Today’s focus on efficient recycling of industrial and domestic waste is driven by the need to save valuable resources by converting reusable materials into new products, rather than consuming more raw materials while exacerbating problems of landfill and contamination.
The recovery and reconstitution of materials – including cardboard, mixed paper, ferrous and non-ferrous metals, plastics and glass – requires a wide range of scientific, engineering and mechanical processes to collect, identify, clean, sort and convert these materials into reusable form.
A Materials Recovery Facility (MRF) receives, separates, and prepares recyclable materials to be sold to an end buyer. MRFs use a combination of machinery and manual labour to separate and prepare recyclables for reformation into base materials for the manufacture of a wide range of products. The large-scale plant and equipment required to handle these processes must also be run and managed in a way that reflects the purpose they support. For example, if these facilities used more power than justified the environmental benefits of the recycling operation, there would be no real benefit at all.
Australia’s modern mixed recycling facilities incorporate the latest technologies and engineering advances to ensure that all plants function in the cleanest and most environmentally responsible way across the multiple processes. The use of energy to run these plants across the nation is a major cost factor in the recycling process.
Compressors that efficiently convert input power sources into controllable compressed air are vital for an MRF’s sustainable operation. These industrial compressors need to generate highly beneficial ratios of power input to air output, to actually reduce energy costs over older conventional machines.
One large national MRF operator has been achieving remarkable results utilising revolutionary PermanentMagnet, Variable-frequency (PMV) compressors across its operations. The integration of energy-saving two-stage rotary screw air ends and variable-speed technology ensures that the end user’s air demands are met at all times, while the compressor only operates as required depending on demand, from idle to full capacity. This new generation of compressors are powered by permanent-magnet motors that utilise rare-earth technologies to generate more power from lower kW capacities, resulting in substantial energy savings.
With the cost of energy rising at an alarming rate, the generation of sustainable compressed air is vital to the viable operation of MRFs – and indeed any industry needing to maintain a cost-effective compressed air system.
PMV energy-saving air compressors are supplied and serviced throughout Australia by Kaishan Compressors Pty Ltd, with capacities from 15kW to 250kW providing ample clean air to match outputs in a wide range of industrial applications, including certified food-grade requirements. Through Kaishan’s global resources, PMV technology can also be applied to custom-designed and -engineered compressed air systems for highly specialised applications, including scientific, mining and marine applications.
“Worldwide demand for energy-saving technologies in compressor design and engineering puts the Kaishan PMV machines at the cutting edge of sustainable compressed air generation,” says Scott Tamlyn, National Sales Manager at Kaishan. “As one of the largest manufacturers and suppliers of air compressors and systems for industries throughout the world, we support our globally proven technologies with a nationwide network of sales and service centres and personnel.”
Kaishan
kaishan.com.au
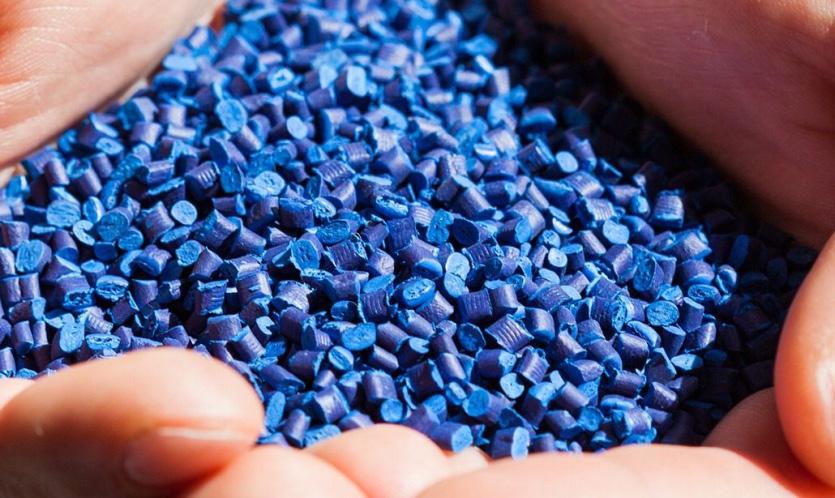
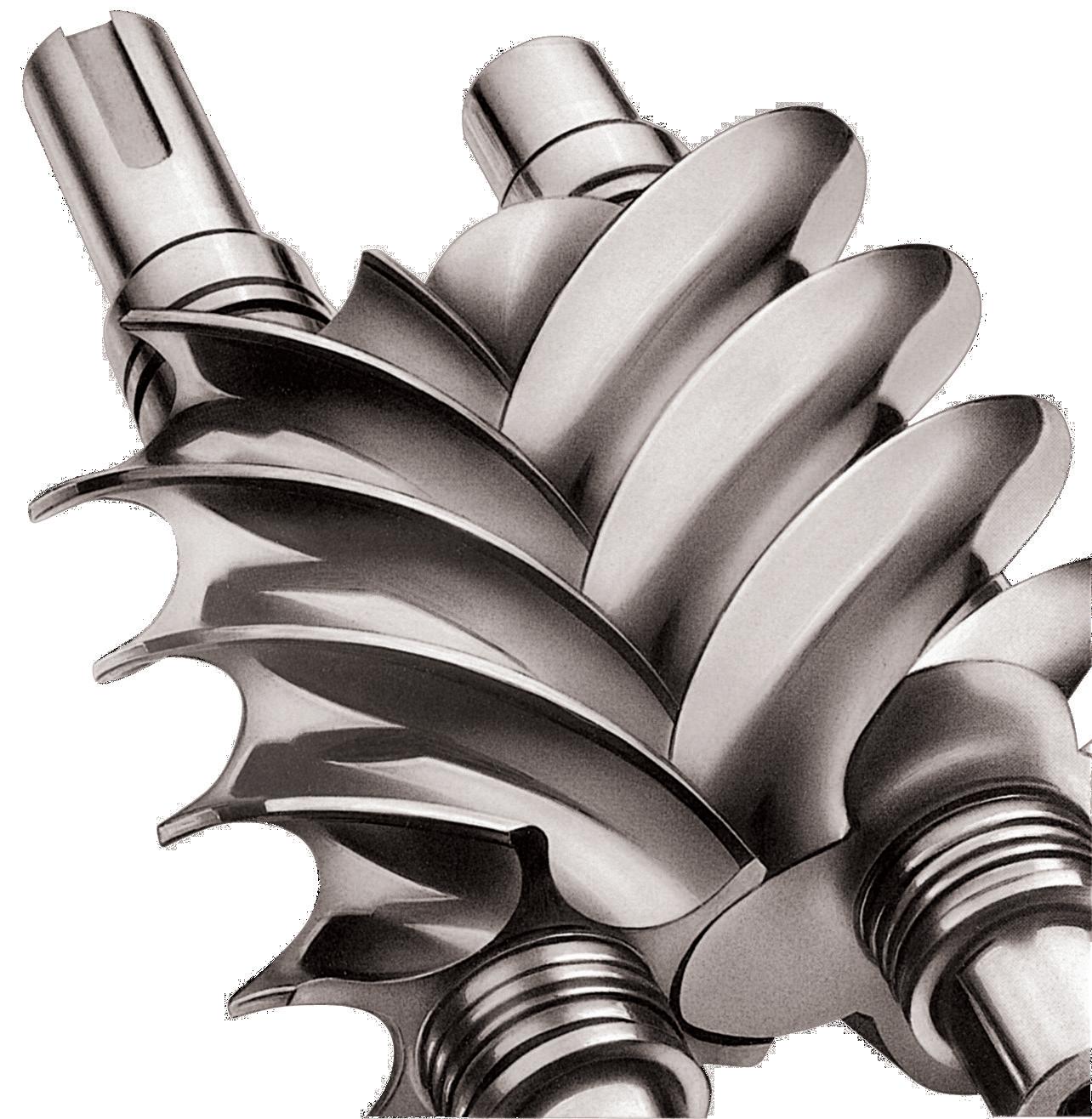
