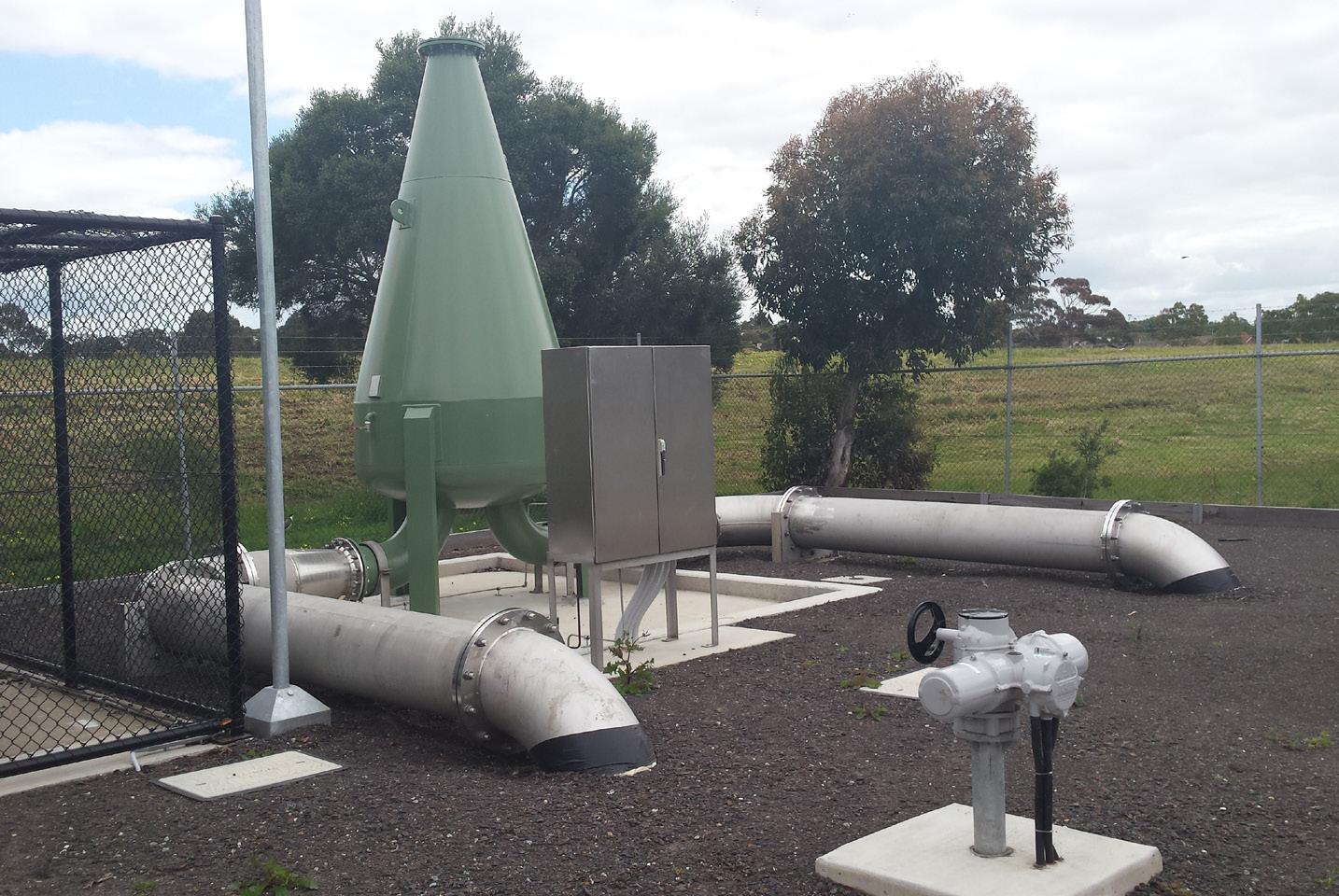
10 minute read
Energy, Waste & Recycling
Finally, a solution for reducing odor in sewers
BICONETM installation & reliable oxygen supply @ Barwon Region Water, Boundary Rd Site
Advertisement
Excess hydrogen sulfide (H2S) can lead to lingering odors in your sewerage treatment facility. Too much hydrogen sulfide can be created if there isn’t enough dissolved oxygen in the water. With more dissolved oxygen, H2S should decrease. For the chemistry heads, this is the reaction:
H2S + 3 O2 -> SO42- + 2 H3O+
To deal with increasing odor emissions, as well as foam formation, gas injection is recommended. Historically, compressed air has been used in an attempt to reduce odors. However this is an inefficient solution
for wastewater composition, as the ‘flow’ is too high and it has the opposite effect than expected by stripping out odorous substances and increasing foam formation.
Sewer Water
Air Liquide pure oxygen injection – a highly efficient solution
Pure oxygen considerably decreases “nitrogen unnecessarily inputted from the air” by approximately 80%, very quickly, and therefore reduces odors and the tendency for foam formation. In addition, it considerably reduces corrosion in pipes and equipment that is caused by aggressive compounds (for example, reduced sulfur molecules) creating significant savings on maintenance costs.
To inject oxygen efficiently, Air Liquide offers customers a variety of solutions for oxygen dissolution, depending on specific needs. One such solution is the INJECTORBICONE, an economical static mixer designed to ensure a high efficiency of gas enrichment with minimal hydraulic loss.
Overall for the water treatment industry, Air Liquide offers two main water treatment solutions – pure oxygen enrichment for biological treatment and carbon dioxide to be used for ph control. Providing these sewer odor reduction solutions highlights Air Liquide’s commitment to solving the critical ‘pain points’ facing the industry. Air Liquide supports sewer treatment projects globally by providing incredibly efficient oxygen injection systems and offers customers this ‘know how’ and expertise locally in Australia, as well as a highly reliable and stable supply of oxygen.
Air Liquide
airliquide.com.au

Recycling Technology. Shredders, Raspers, Granulators, Wash Plants, C&D, eWaste Lines, Tyre Plants, Repelletising and more. That’s Applied Thinking.
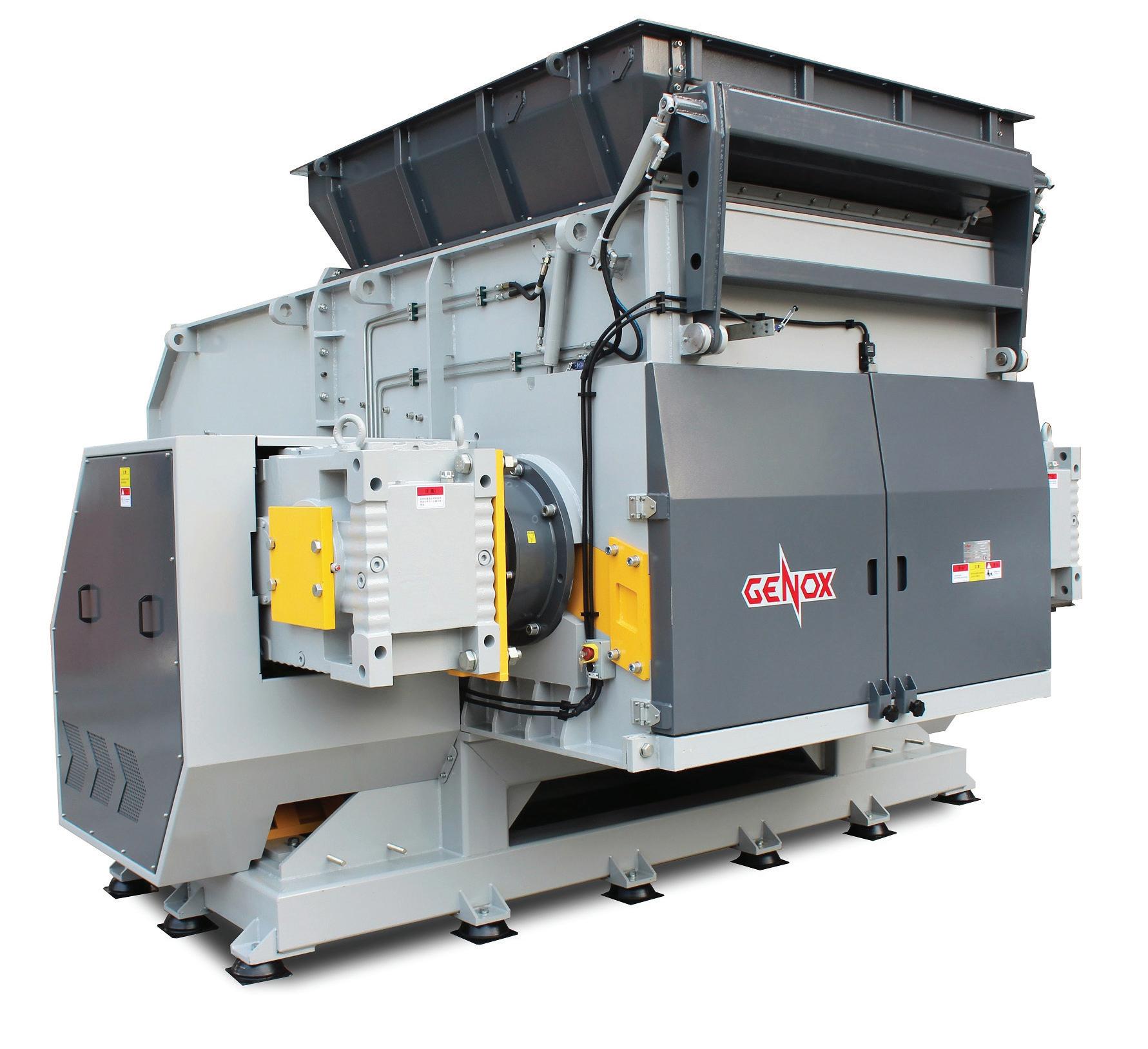
To find out more, call: 03 9706 8066, Email: sales@appliedmachinery.com.au, or visit: www.appliedmachinery.com.au
Woolworths-Pact recycling partnership set to deliver big investment in local recycling and manufacturing
Woolworths Group and Pact are working to establish a new partnership that could result in 18,000 tonnes of recycled plastic used in Woolworths’ own brand packaging each year, in a move that would see a multimillion-dollar investment in local recycling and manufacturing capacity.
Woolworths Group has already committed to removing plastic from packaging wherever feasible, and to date has removed more than 5,800 tonnes of virgin (newly made) single-use plastic and packaging from its own brand range
in FY22. Where there is currently no viable alternative to plastic for food safety or quality, Woolworths Group is working to use recycled plastic to reduce the environmental impact.
Projections that the partnership could see 18,000 tonnes of newly made plastic replaced with locally-produced recycled plastic each year would correspond to a decrease in carbon emissions of almost 25,000 tonnes (equivalent to planting more than 37,000 trees) and a saving of almost 500 Olympic swimming poolsworth of water annually by one estimate.
The intent of the proposed partnership is to establish Pact as Woolworths Group’s key strategic partner by volume in its efforts to deliver more sustainable packaging across its own brand range and deliver the most significant boost to date towards Woolworths Group’s goal to halve the use of virgin (new) plastic across its own brand packaging by 2024.
Under the proposed partnership, Pact will use recycled plastic to make more sustainable packaging for products across Woolworths’ product range, including in milk bottles, meat trays and beverage bottles, drawing on plastic collected from household recycling and container deposit schemes.
Pact currently operates five plastic recycling facilities in Australia, including the recently opened PET recycling plant in Albury-Wodonga which can recycle up to 1 billion PET beverage bottles a year. Another four facilities are planned for construction by 2025.
Woolworths Group Managing Director of Format & Network Development, Rob McCartney, oversees Woolworths 360 - the business’s sustainability innovation unit responsible for the development of the partnership. He said: “As Australia’s largest retailer we have a responsibility to make the products our customers put in their shopping baskets better for the environment.
“We’re working hard to remove plastic from packaging like our bakery trays, however it can be necessary to protect quality and food safety in some products - which is why replacing it with recycled plastic is the next best thing.
“Across the scale of our range, the real challenge is sourcing quality recycled material in the volumes we need and ensuring it’s coming from within Australia to support the development of our local circular economy and avoid shipping emissions.
“We’re working with Pact on a partnership that would propel us closer towards our sustainable packaging goal than we’ve ever been before, while also helping to grow the Australian recycling industry to meet demand in the years to come.”
Pact Group CEO and Managing Director, Sanjay Dayal said: “We know that consumers and businesses are increasingly demanding recycled and recyclable plastic packaging and Pact is working with committed partners like Woolworths Group to drive that change.
“Plastic packaging that is designed effectively, that is recyclable and recycled properly in Australia can be used again and again, creating a truly local circular economy for plastics.”
NSW Minister for Environment James Griffin said: “This exciting initiative will support the NSW Government’s ambitious goal to triple the plastics recycling rate by 2030 and reduce plastics from entering our environment as litter or going to landfill.
“It is great to see businesses working in partnership with their customers, to move to more sustainable packaging and help develop a circular economy.”
In addition to its recycling facilities, Pact is also investing $76 million to install new technology and equipment across its packaging manufacturing facilities as it continues to grow local capacity to support increased use of recycled plastic in Australian packaging. The investment is supported by a $20 million grant from the Australian Government through the Modern Manufacturing Initiative.
Woolworths Group and Pact’s latest work on recycled plastic is the next chapter of a long-term relationship between the two businesses, with Pact already supplying Woolworths Group with 50 million reusable and recyclable plastic produce crates to replace traditional single-use cardboard and polystyrene boxes.
Woolworths Group has also co-founded plastic recycling startup, Samsara, to help commercialise plastic-eating enzyme technology that could see plastic become infinitely recyclable. The business is still in its infancy with its first commercial scale plant expected to open in the next 18 months, from which Woolworths will take the first 5,000 tonnes of recycled plastic produced for use in its own products.
Earlier this year, Woolworths became the first major supermarket to announce the removal of reusable plastic bags from all stores nationwide by June next year. The progressive state-by-state transition is expected to remove 9,000 tonnes of plastic from stores and online orders annually.
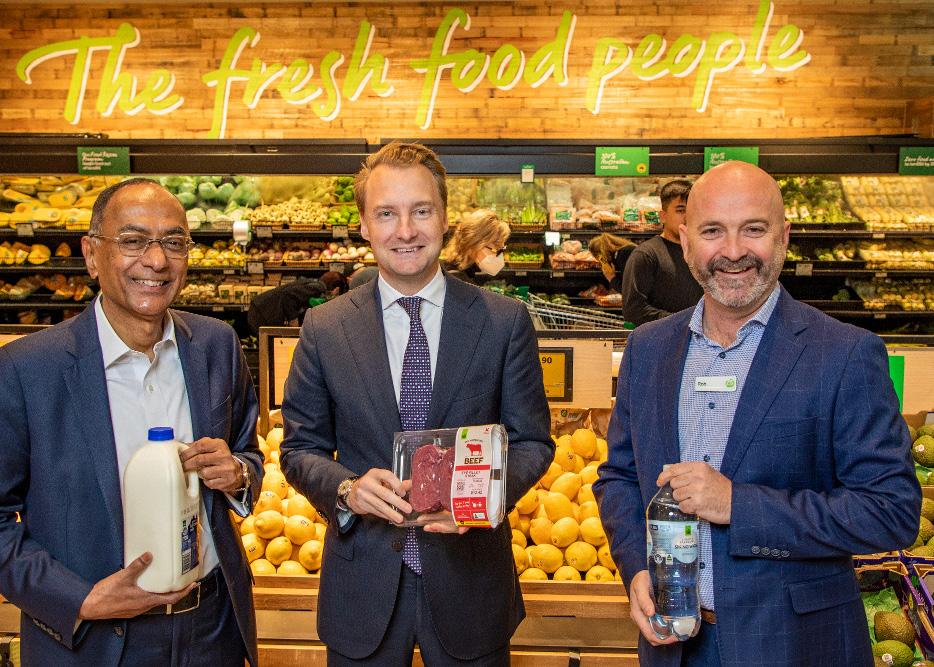
Pact Group CEO & MD Sanjay Dayal, NSW Environment Minister James Griffin and Woolworths Group executive Rob McCartney - holding products that could see packaging sustainability boosted under Pact partnership
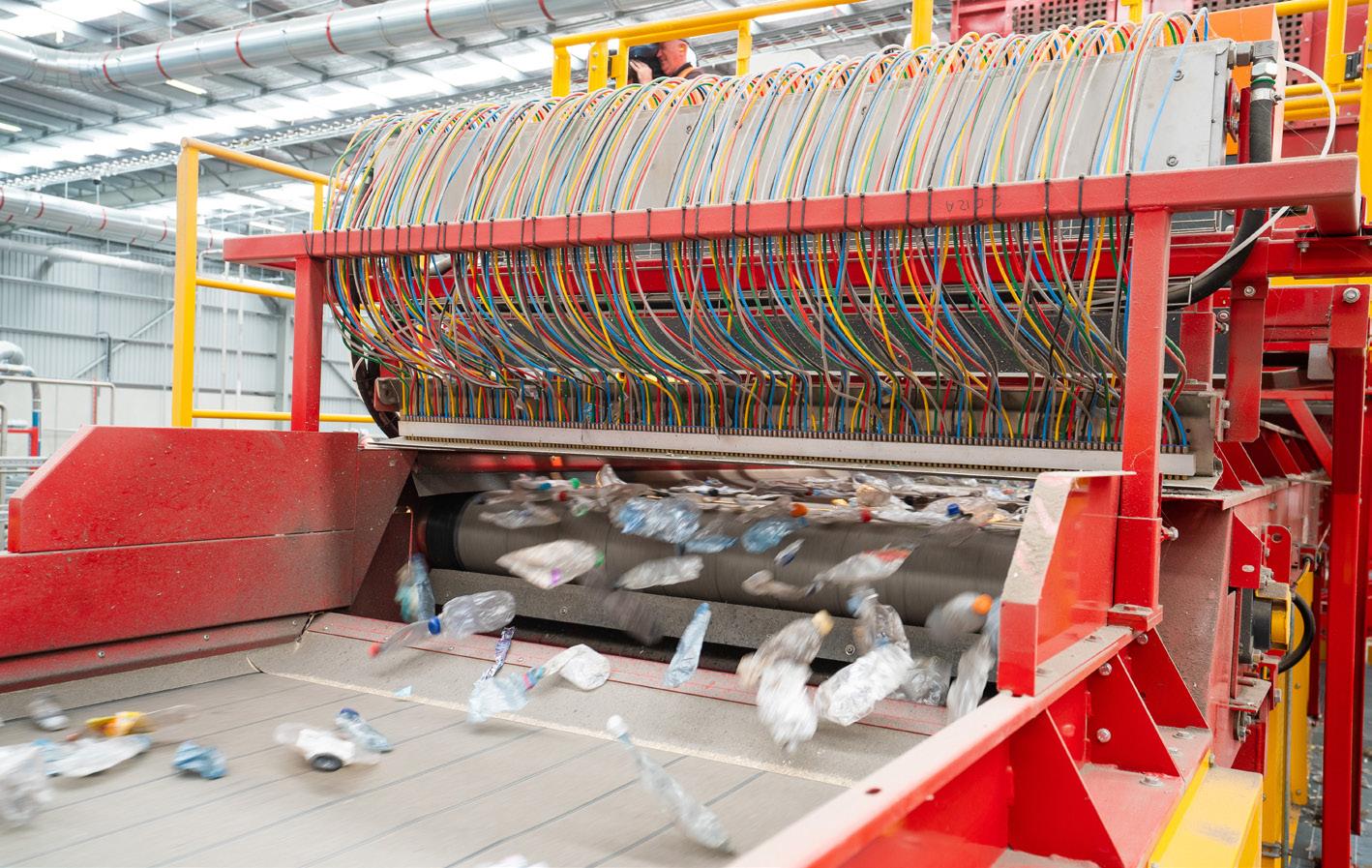

KEEP COOL
ENCLOSURE CABINET PRECISION COOLING
Designed to keep your electronics cool and operating at optimum performance.
- Cooling capacities range from 200W to 6kW. - IP Ratings – IP54 & IP56. - Mild Steel and Stainless Steel finishes. - Seifert also offer Heat Exchangers, Peltier Coolers and Fan Systems - complete Thermal Solutions.
info@seifertsystems.com.au / +61 3 9801 1906 seifertsystems.com.au
Bathurst Water Treatment Plant upgrades to Ragazzini peristaltic pumps
Achance meeting at an industry exhibition prompted David Cashen, Supervisor at the Bathurst Water Treatment Plant, to upgrade the plant’s pumps with technology from Ragazzini, supplied by Hydro Innovations.
The problem
The Bathurst plant had two peristaltic pumps transferring carbon slurry for use in the plant’s treatment process. The slurry is quite abrasive, so hoses needed replacing once or twice per year. This in itself was okay, but the hose changes were exceedingly messy because the pump casing needed to be filled with lubricating fluid (due to its “shoe on hose” design).
In the event of a hose failure, a mixture of carbon slurry and lubricating oil resulted in a mammoth mess to clean up, both inside and outside the pump itself. Hose replacements and the consequential clean-up of carbon mixed with lubricating oil could take days, and on top of hose costs, Cashen also had the cost of the (not inexpensive) lubrication fluid to replace each time.
The solution
Cashen had previously won the Operator of the Year Award from the Water Industry Operators Association of Australia (WIOA), and it was at a WIOA exhibition that a solution to his problem emerged. In the carpark he bumped into Phil Rothheudt, NSW Regional Manager for Hydro Innovations, an Australian-owned pump engineering company. Hydro Innovations is the exclusive Australian distributor for the world-recognised Gorman Rupp pump range, which includes the EchoStorm venturi aerator, Edur Pumps from Germany, and the Ragazzini peristaltic pump range from Italy.
Cashen’s chance meeting with Rothheudt prompted him to visit the Hydro Innovations exhibition stand, which featured a Ragazzini peristaltic pump. Once Cashen had been shown the features and benefits of the Ragazzini pump over his existing ones, he was convinced he had found the answer to his messy hose-changing issues.
The Ragazzini peristaltic pump features a number of enhancements over other brands, which make them highly reliable and easy to service and maintain. Key features include: • A “roller on bearings” design eliminates the need for lubricating oil and reduces friction on the hose (due to the use of rollers instead of “shoes”), resulting in extended hose life. • An automatic retractable roller system delivers easy maintenance, simple hose changeover, and reduced pressure on hoses during pump rest periods. • A leak detector automatically stops the pump when a hose fails and sends an alarm, minimising product loss. • With no lubricating oil in the pump chamber, there is no mess to clean up and no potential for contamination of pumped product or the surrounding area in the event of a hose failure, greatly simplifying hose change-outs. • A choice of seven different hoses ensures the right hose for the right product. • Duties range from one litre/hour up to 180,000 litres/hour, with operating pressures up to 15 bar.
The result
Two Ragazzini model MSO pumps were subsequently supplied, with one fitted immediately to ensure it performed to expectations and met the promises made. One pump has now been operating since July 2018 (running continuously for up to 18-20 hours per day in hotter periods); at a follow up inspection, there had been no hose failure or need to change-out the original hose.
Cashen’s expectations have been more than realised, with not only a clean and reliable system for pumping carbon slurry, but a hose life that has exceeded nine months. The initial outlay has also been vindicated by the cost savings in down-time and clean-up time, reduced need for hose replacements, and increased reliability and all-round efficiency.
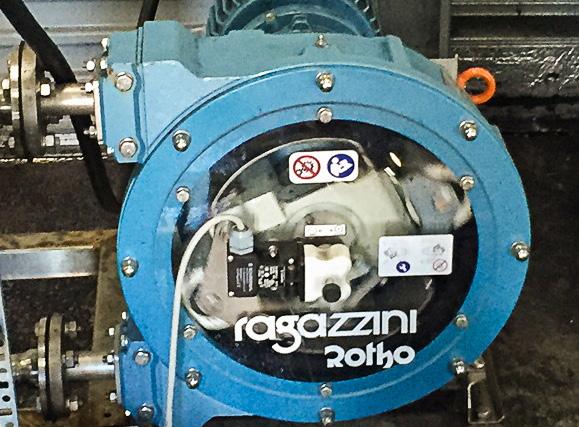
Hydro Innovations
hydroinnovations.com.au
Reduce your environmental impact with Air Liquide
WATER TREATMENT SOLUTIONS
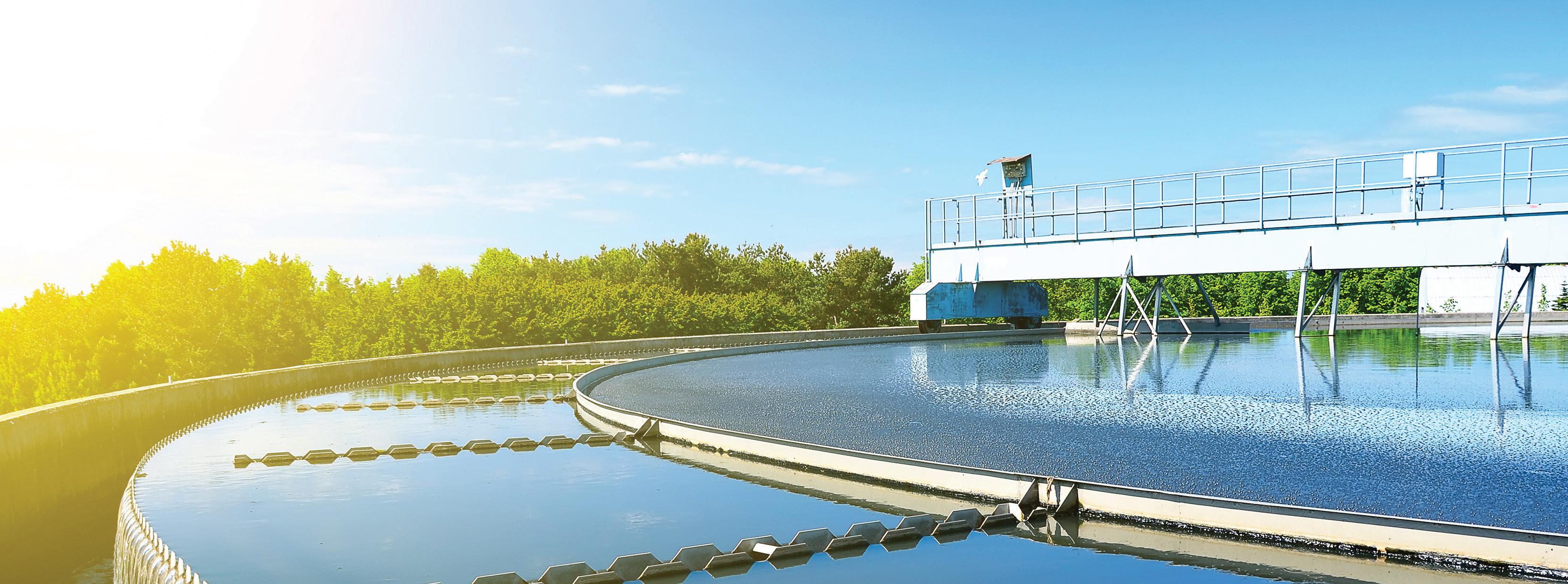
Air Liquide has more than 40 years experience in water treatment and servicing private and public companies with industrialised gas solutions for all three sector domains: Wastewater, Process water and Drinking water. Providing comprehensive gas and equipment solutions, Air Liquide can help improve your plant’s performance and reduce your environmental impact across a wide range of water treatment applications.
OXYGEN FOR BIOLOGICAL TREATMENT
CARBON DIOXIDE FOR PH CONTROL
Simple solutions with minimum maintenance costs and no hazardous saline residuals that use carbon dioxide for fine pH adjustment for overly basic effluents. Introduction of pure oxygen into biological basins to meet challenging water discharge limits; capacity increase and removal of foam and odors with OPEX savings and the reduction of CAPEX.
OZONE FOR PURIFICATION AND TERTIARY TREATMENT
Solutions using ozone to remove pathogenic organisms or pollutants which are difficult to biodegrade, such as micro-pollutants, surfactants, or inks. Discover More. www.airliquide.com.au
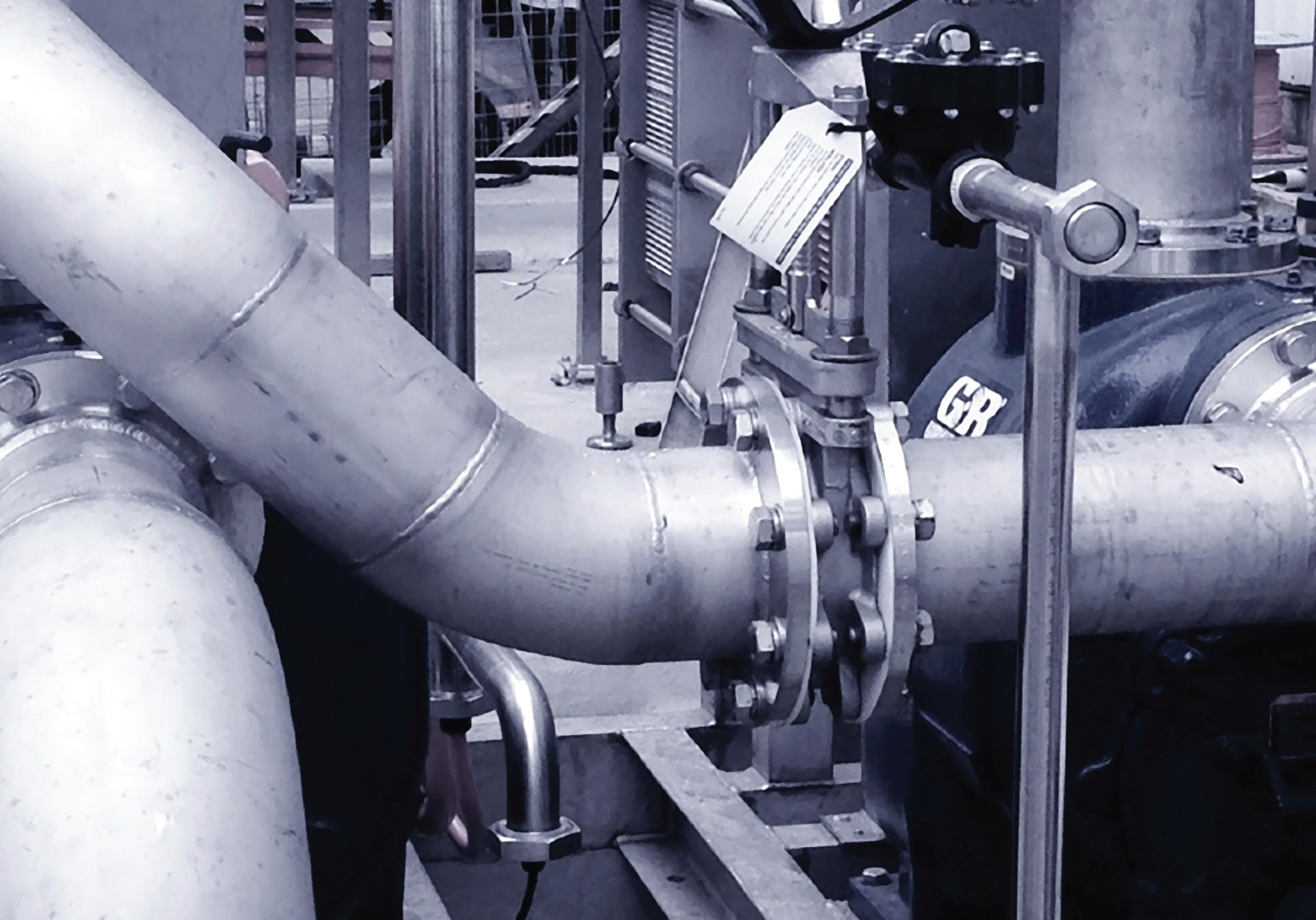
