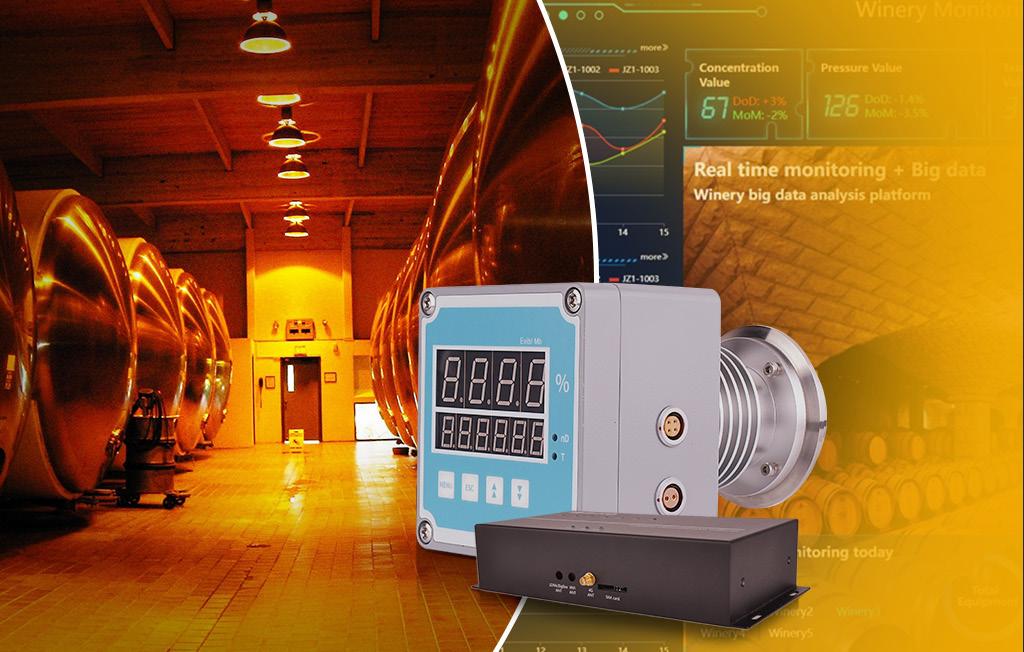
9 minute read
Instrumentation, Collaboration Sensors, Test & Measurement
How winemakers are helped by an intelligent IOT managing and control system
The quality of a bottle of wine is determined by both the quality control of the grape and the method used during the winemaking process.
Advertisement
The quality of the grape is mostly determined by natural and geological factors, such as weather conditions and location. Because that’s hard for humans to control, manufacturers need to focus on monitoring the winemaking process to make sure the quality of their wine stays at a high standard.
Measuring instruments play an important role in the winemaking process, ensuring the product stays at a high-quality standard, especially at the fermentation stage.
Refractive index (nD) and Brix (%) are two major factors that need to be monitored all the time to keep the fermentation process at a certain standard.
A refractometer is the key instrument for such measurement. Instead of the traditional measuring method, a refractometer should be installed in-line or on the tank to improve the accuracy of measurement.
For large scale wineries, it’s hard to control all the working instruments from the production line. Because of that, ZHYQ Sensors has recently invented and designed IOT operating systems for our wine manufacturers who need integrated management.
They consist of 3 major sections and can be connected by a wired or wireless connection. The 3 major sections are the sensors, the data acquisition system and the controlling software.
Our data acquisition system has seven pots for sensors to connect physically. Each pot can support up to 50 sensors and refractometers with standard Modbus RTU Protocol.
All data collected then gets transferred to a control unit (normally a computer) for real-time data management and monitoring.
For multiple site monitoring enquiries, our software can also control multiple sites. The wireless connection can also be managed between our core units.
However, connection and set up methods vary from case to case, depending on what is available at the customer‘s location.
Because they help increase accuracy and efficiency of measurement during production stages, IOT managing systems have been widely used by manufacturers in production lines across many industries.
And they’re set to become a critical tool in beverage industry manufacturing.
With a more accurate monitoring system, wine makers can then improve the quality of their wine, and the increased efficiency also helps save labour in the production process.
ZHYQ
zhyqsensor.com
Bronkhorst introduces new ES-FLOW ES-1x2C flow meter

Available in Australia from AMS Instrumentation & Calibration, Bronkhorst has released the ES-1x2C, the latest model in its ES-FLOW family of flow meters.
The market for low liquid flow measurement and control in ranges around 1,000 kilograms or litres per hour is an important section for Bronkhorst, due to its size and the expected future growth of this segment. The new ES-1x2C meter follows the release in 2021 of Bronkhorst’s ES-FLOW ES-1x3C model. The ES-1x2C will cover the flow range just below the existing ES-1x3I or ES-1x3C models.
The ES-1x2C and ES-1x3C ultrasonic flow meters are compact, easy to clean and versatile (for example, they are liquid independent). They feature a straight sensor tube with low internal volume, offering low-pressure drop in relation to sensor diameter. Both come equipped with advanced signal processing for factors such as dosing functionality.
The ES-FLOW product series offers an impressive performance of ≤ 0.8% Rd, at a very economic price level. While Bronkhorst’s mini CORIFLOW series can offer even higher performance at ≤ 0.2% Rd, this is not always necessary. Both flow meter series always include the same unique Bronkhorst features such as on-board PID-controller, totaliser and alarm functions, and many communication buses, supported by the dedicated Bronkhorst sales and service network.
By bringing the ES-1x2C and ES-1x3C models to the low liquid flow measurement market, AMS is able to offer a variety of economically priced options.
AMS Instrumentation
ams-ic.com.au
INSTRUMENTATION & CALIBRATION PTY LTD SPECIALISTS
www.ams-ic.com.au
AMS have been suppliers of instrumentation and calibration equipment to all industries since 1973 representing some of the world’s leading manufacturers of the equipment in their field.


Flow Measurement Specialists
50 years of sensors
by Ken Collishaw, Product Manager, Turck Australia
Automation has come a long way in the last fifty years. In 1972 relay logic control technology ruled Australian industry. Control cabinets were packed with hardwired relays, timers, contactors, and overloads.
Electricians knew all about racing contacts, leakage voltages and welded contacts. Operating voltages were mostly AC. Motors were started with equipment such as star delta or liquid resistance starters, and input devices were mostly limit switches where the target product pushed an arm, operating an internal mechanical contact.
Non-contact sensors were around too. Mainly inductive sensors, but also reed switch cylinder sensors and basic photoelectric sensors using incandescent lamps. The original 40 x 40 x 120mm rectangular inductive sensor housing was a direct bolt-in replacement for limit switches.
The sensor market was about to explode. PLCs had been invented in the late sixties, but it took time for them to replace relay logic. Inductive sensor manufacturers were mostly industry based with each manufacturer directing their attention to a specific industry and developing unique products to suit the requirements of that market.
Photoelectric manufacturers were branching out, introducing innovations such as optic fibres, polarisation filters and LED emitters. Later, laser emitters were also introduced to provide a more powerful and much narrower beam. Longer life components such as the LED emitters and transistor output circuitry allowed sensors to transition from repairable products into the now familiar sealed throw away devices.
Some smarter sensors had inbuilt timers but eventually PLCs were so common that there was minimal need for this and sensors went back to being basic switching devices. Eventually sensors in various technologies offered analogue output models as well as the diminishing traditional relay output and rapidly growing transistor output options and this meant sensors could now measure or detect.
Europe and the USA embraced PNP transistor output sensors, but Asia preferred NPN. Australia imported products from both regions with PNP representing about sixty percent of our market. Matching the correct sensor to a PLC was often a case of looking at where the PLC was made and trying out a sensor with an output based on that.
Safety and sensors
Safety devices had a slow uptake, but this increased dramatically when machine safety legislation was enacted, and safety guarding became a requirement not an option. Safety light curtains transitioned from an electromechanical retro-reflective configuration to the now universal transmitter and receiver grid arrays. Safety mats and bump strips were available as well as various safety interlock switches.
For a long time, sensor IP ratings topped out at IP67. Wet environments were avoided and where a sensor had to be used in a harsh environment, sealed and potted inductive sensors or solid plastic optic fibres were used. If a standard sensor had to be installed in a cold water wash down area, the recommendation was to leave the power connected to the sensor during the cleaning process, creating internal heat and avoiding moisture being sucked into the housing along with air when the sensor ‘breathed in’ due to rapid temperature change.
Eventually technology, design and sealing became so good that just about everything was IP67 and it became necessary to add the IP69K test to the sensor repertoire to show a difference in capabilities.
The advances in digitisation and electronics during the third industrial revolution in the late 1900s allowed sensor technology to advance rapidly.
Traditional DIN standards for inductive sensors had become limiting. Manufacturers introduced extended range models and then further extended ranges. Improved technology enabled things like variants without de-rating factors and variants with full metal housings.
Technological improvements enabled miniaturisation across all sensor types. Housing sizes decreased and performance increased. Sensors became smarter, first when buttons replaced potentiometers and then when displays enabled a variety of teach functions, performance adjustments and viewing options.
More technologies were introduced. Rotary encoders evolved from simple clockwork mechanisms into more efficient glass and then more robust metal disc type devices and then into fully sealed solid-state units. Ultrasonic and then radar technology was adapted into the sensor field to fill gaps.
Laser line bar code readers enabled unique identification of products then, later on, imaging technology enabled smaller 2D barcodes carrying much more data. RFID technology not only allowed identification in dirty environments and through some materials, it also allowed data to be written enabling full process tracking.
Wireless systems made sensors more versatile and adaptable, capacitive sensor capabilities increased and specialist fluid sensors for pressure, temperature, level and flow measurement were developed.
Sensors were smaller, more powerful and smarter, but they were still a simple input device. In most cases, they detected that a particular situation was present, and they provided a digital output signal. Sure, they were now often connected via fieldbus rather than individual wires, but they were still providing a simple switching or a basic measuring output.
Industry 4.0 and sensors
Recently, Industry 4.0 has driven major changes in what sensors are and how they are utilised. We can collect and collate enormous amounts of data giving us comprehensive visibility across our plants and processes.
Industry is moving away from programmed maintenance, where pre-emptive and sometimes unnecessary maintenance is done to prevent possible future breakdowns, into predictive maintenance where comprehensive condition monitoring information identifies and highlights anomalies so they can be addressed before a major issue occurs.
As a result, modern sensors have evolved, and they now can provide a lot of extra information. A sensor still provides a simple basic digital output, and that is enough for some but, as Industry progresses, more and more users will want access to extra information such as the internal device temperature, device run time and the stability of detection. Many modern sensors provide this.
The other significant change is that technology such as IO-Link lets us configure and adjust sensors remotely without stopping the machine, and for anyone who has had to hang over a running production line in a challenging environment trying to set up a sensor, this is a huge improvement.
In another fifty years today’s sensor technology will be antiquated, but today we have sensors that are smarter, stronger, more cost effective and far more capable than anything seen before, and they just keep getting better. That is just as well because sensors are, and will continue to be, a significant cornerstone of modern automation.
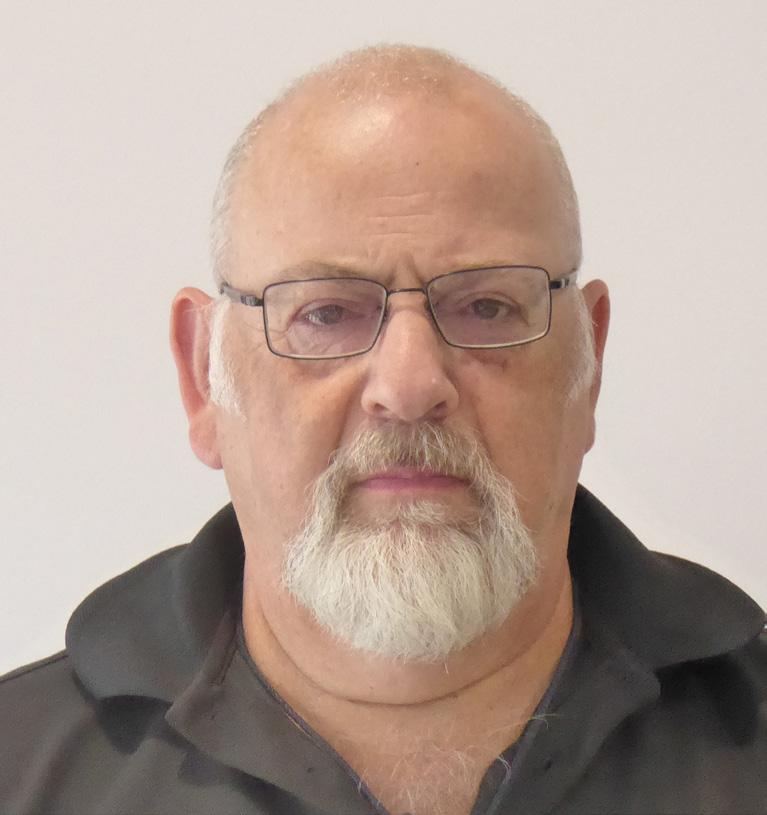
Ken Collishaw, Product Manager, Turck Australia
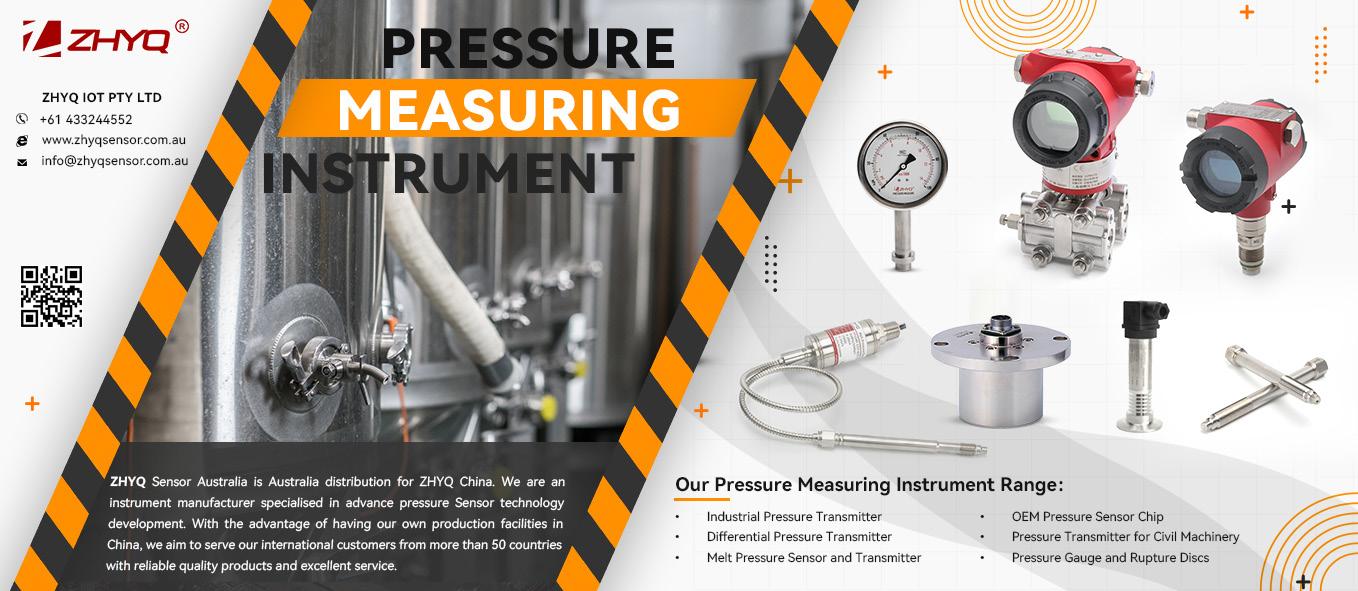