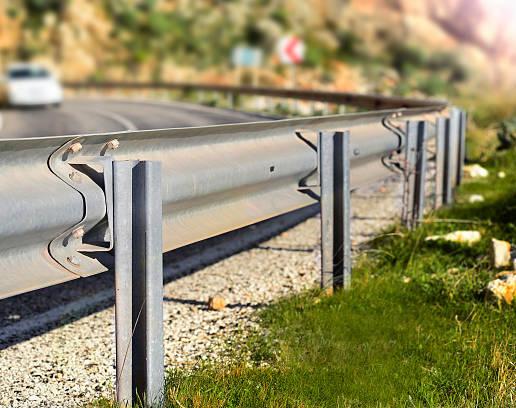
17 minute read
Workplace Health & Safety
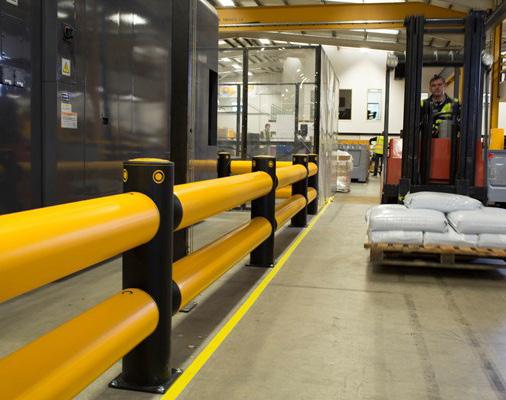
Steel vs polymer: sourcing the best warehouse safety barriers
Advertisement
By Chris Banks, President of Banks Industrial Group
Hard hats, painted floor lines, warning signs, lock out-tag out procedures, handover briefings… these are all hallmarks of a good workplace safety program.
However, in most industrial settings, good is not good enough to fully protect today’s workers.
In most cases, physical barriers are also needed to properly direct vehicle and pedestrian traffic, visually signal danger points in an environment, and better protect machinery and infrastructure during collisions, to name just a few applications.
Depending on the materials used in the barriers and those of the surrounding collision site, energy can be transferred to the human operator and load being carried. These collisions could result in lethal injury to the driver and costly damage to the goods that topple from the lift. Facility owners need to consider the best material for safety barriers to prevent those outcomes.
Currently, there is no official Australian safety standard for the use of safety barriers. But PAS 13 is the first step towards creating legal guidelines for workplace safety, to better protect workers and companies from potential hazards. PAS 13 was created and published by the British Standards Institution in association with the Health and Safety Executive, and with the involvement of A-SAFE as part of the steering group.
What do we mean by appropriate physical barriers?
Guard rails, bollards, and pallet rack leg guards increase protective measures for humans, machinery, and structures in a workplace. Painted lines on a floor are a good start, but they encourage people to look down, not around them. When workers are in moving vehicles, primarily forklifts, they need above-ground, highly visible indicators on how and where to operate safely – like the barriers we put on roads, bridges or even in parking lots. Steel and polymer are the two most common materials used today in worksite safety barriers.
STEEL: Different styles of fabricated steel guard rails were first developed in the early to mid-1900s for use along highways and agriculture.
These rails, strong and cost-effective, were soon adapted for safety purposes in industrial settings. They are still the dominant choice for workplace safety barriers today.
POLYMER: In the latter half of the 20 century, plastic and polymer versions of safety barriers started to gain popularity as an alternative to steel for a variety of reasons.
Steel Guard Rails
An industry standard
Steel is still the prevalent choice on most construction, industrial, and manufacturing sites today.
Initial cost
It’s considered to be a strong and acceptable choice, while also being relatively low-cost up front and disposable when damaged or worn.
What to consider?
During impacts
Steel simply isn’t designed to protect against the much higher forces and more powerful vehicles used in modern industrial environments. When there’s a collision, you’re left with a damaged or destroyed barrier, along with any vehicle, infrastructure impact, or production downtime associated with it (or the added expense if damaged machinery belongs to an outside vendor working on your site).
Durability
Steel is subject to denting, rusting, and chipping, requiring preventative maintenance more often and that runs up the tab on yearly operational costs. Over time, that rusting, denting, and chipping can make the barriers less visible which poses a higher risk to operators and pedestrians.
Facility damage
Steel is very rigid and unyielding, transferring any impact energy into the surrounding floor and other structure. These repeated impacts over time can prematurely damage your concrete, causing more expensive maintenance and repairs sooner.
Visibility
There is no requirement in Australia regarding the colour of safety barriers.
Many safety barriers are bright yellow; a universal signal hazard signal.
Since painted steel chips and fades over time, routine repainting and maintenance costs are higher and require more of the annual operating budget.
Polymer Guard Rails
During impacts
Polymer doesn’t just stop the force of an impact, it absorbs and moves with it. This means during a collision, the barrier takes the force of the blow, flexes, and returns to its original shape with little to no damage on the machine that hit it or the environment around it.
Polymer blends, like A-SAFE’s advanced Memaplex, which is three times stronger than steel, cushions these impacts (up to 80%) and mitigates physical damage to the machines and vehicles during contact.
Eliminate impact shock
Collision energy isn’t transferred to the floor, surrounding structure, machinery, or vehicles. It’s confined within the barrier itself, protecting the floor from premature damage and removing the risk of impact shock to operators and loads.
Durability
The bright polymer coatings make them highly visible and easy to see by workers from all angles. Unlike painted steel, this colour stays intact and vibrant for years, improving guidance to workers and pedestrians through and around the worksite. Additionally, companies using polymer save on operational costs annually by eliminating the need to repaint, repair, or replace steel barriers.
Testing
A-SAFE conducts standardised, realistic testing to PAS 13 compliance, which is published by the British Standards Institution (BSI) and considered the world’s first and foremost safety barrier testing code in industrial workplaces.
All impact products are subjected to rigorous, repetitive collision tests and measured against a high standard of performance and recovery. The tests are monitored by TÜV Nord to receive their independent verification that A-SAFE products reach the industry’s highest standards.
Food and medical environment safe
Polymers perform better in the highly regulated and demanding environments of food processing and healthcare. Both have hygiene requirements that demand much higher performance standards.
A-SAFE’s specially designed hygiene seals prevent the ingress of moisture, bacteria and dirt, while the polymer material is chemical resistant, scratch-resistant and non-corroding. The products are self coloured and do not need painting, eliminating the risk of cross-contamination from rust or paint particles.
Initial cost
Initial investment and installation of polymer guard rails, bollards, and rack protection is typically more expensive than steel. A facility manager would need to run the numbers on total cost of ownership to see how soon polymer options could “pay for themselves” when compared with the annual maintenance, repair, liability, and replacement of steel counterparts.
A-Safe
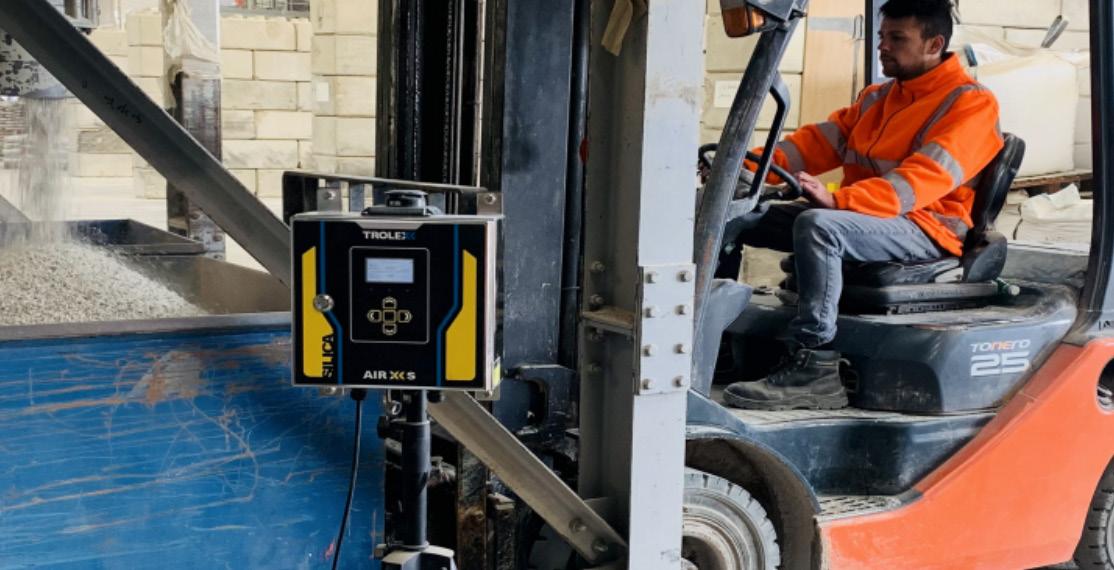
Saving lives — a real-time silica monitor
by Christine Powis
Hundreds of thousands of Australian workers exposed to silica dust particles in their work environments could benefit from a world-first, real-time silica detector developed in partnership with the NSW Centre for Work Health and Safety.
Silicosis is caused by inhaling fine silica dust, or respirable crystalline silica (RCS), and is estimated to be the most common chronic occupational lung disease worldwide. It’s natural to stone, concrete, sand, mortar, and many building products including the growing engineered stone category. RCS dust is released when workers cut, drill, polish, saw or grind products that contain it.
“Silicosis has been around for centuries but NSW saw a spike in diagnoses up from nine cases in 201718 to 40 cases in 2018-19,” said Skye Buatava, Director of the NSW Centre for Work Health and Safety.
Following the rise in diagnoses, the Centre consulted industry and found a significant problem was the inability to detect high levels of exposure to RCS dust in real time.
“As RCS is invisible, workers are often unaware of exposure, and the monitor was designed to warn workers of exposure to encourage them to properly protect themselves,” says Buatava.
The centre partnered with UK-based Trolex Sensors, which spent nine years developing the world’s first real-time silica monitoring and measuring device, the Trolex Air XS. Launched by the NSW centre earlier this year after a $1m investment, the Air XS has already won several awards in the UK.
The need for better monitoring and precautions is laid bare in a Curtin University report commissioned by the ACTU and published this year.
It concluded that approximately 10,390 lung cancers, or just over 1% of projected lung cancer cases, could be expected in the Australian adult population as a result of their exposure to RCS at work.
On top of lung cancers, the report estimates between 83,000 and 103,000 silicosis cases will result from the estimated 584,000 people working with RCS exposure today.
The figures are projections over the lifetime of the population currently exposed so do not include people exposed in future.
Meeting standards
NSW is among the states that have legislated Safe Work Australia’s Model Code of Practice which bans dry cutting or dry processing of stone or stone products without water suppression or dust capture. As well as WH&S standards, Victorian regulations require businesses which use and cut or otherwise manipulate stone products to apply for five-year licences. Businesses have been obtaining licences since last November and licences are mandatory from November 15 this year — or penalties apply.
Importantly, WHS laws apply to organisations of all sizes. In NSW, the workplace exposure standard has also been halved, reducing the eight-hour time-weighted average for particulates from 0.1 mg/ m3 to 0.05 mg/m3. The Breathe SX software which runs the monitor shows both dust and RCS counts of between 1-10 micrometres (a micrometre being 0.001mm). The Air XS monitor can detect just a single particle of RCS, so it more than meets the current standard of 0.05 mg/mg3 and can actually detect smaller than that standard.
Real-time monitoring benefits
Intermittent monitoring, while accurate, is only useful to profile air quality while the monitoring is actually underway. But what if someone starts sweeping the floor afterwards? As AES Regional Manager Peter Richards explained to a coal industry Standing Dust Committee Regional Forum recently, real time data can track exposure levels as they happen, giving far greater protection in multiple ways including: •instant alerts to warn people •immediate identification of problem practices or process inefficiencies •making on-site surveys more effective •improving performance of ventilation, suppression or extraction systems •ensuring ongoing regulatory compliance and giving proof
“Often people know they have a problem with peak exposure of harmful dust through time-weighted averages,” Richards told the forum, “the problem often comes in identifying when and where that exposure has happened so as to be able to know what was going on then, and how to avoid that exposure in future.”
“Only with real-time data can you track exposure levels as they happen and make immediate impactful decisions on processes, procedures, and protection to successfully reduce the risk to people,” Richards said. The Trolex Air XS monitors sell for $18,500 and the Centre for Work Health and Safety’s involvement means NSW businesses receive a $1,000 rebate - or small businesses can apply to SafeWork NSW for a small business grant. On its website, Trolex’ list of distributors includes AES Solutions, Austdac, Cuthbert Stewart, Nome Services, Strata Worldwide Australia and Trident Australia. As Trolex says, with demonstrations of the detector now available for businesses across Australia, the incentive to ‘get real’ on silica monitoring has never been higher.
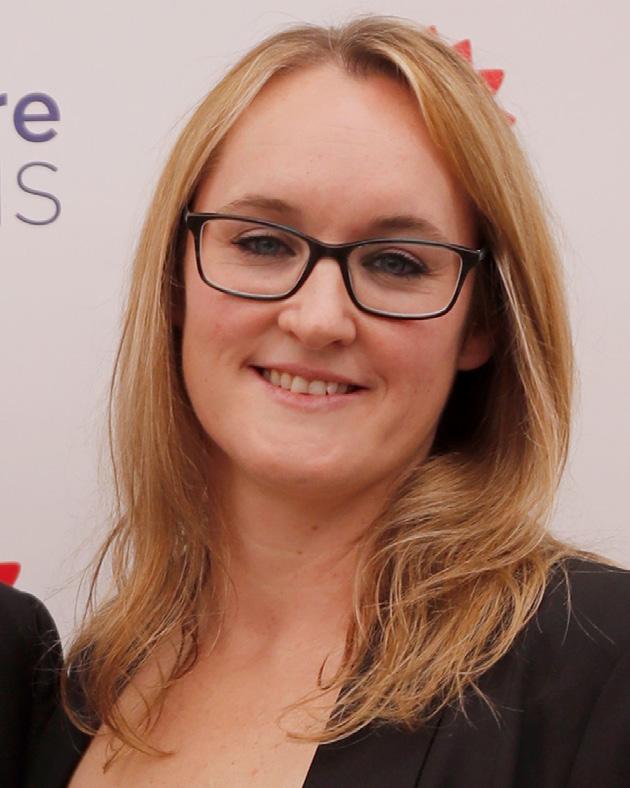
Director of the Centre for Work Health and Safety, Skye Buatava.Director, Centre for Work Health and Safety
The Arntz Optibelt group of companies celebrates its 150th anniversary
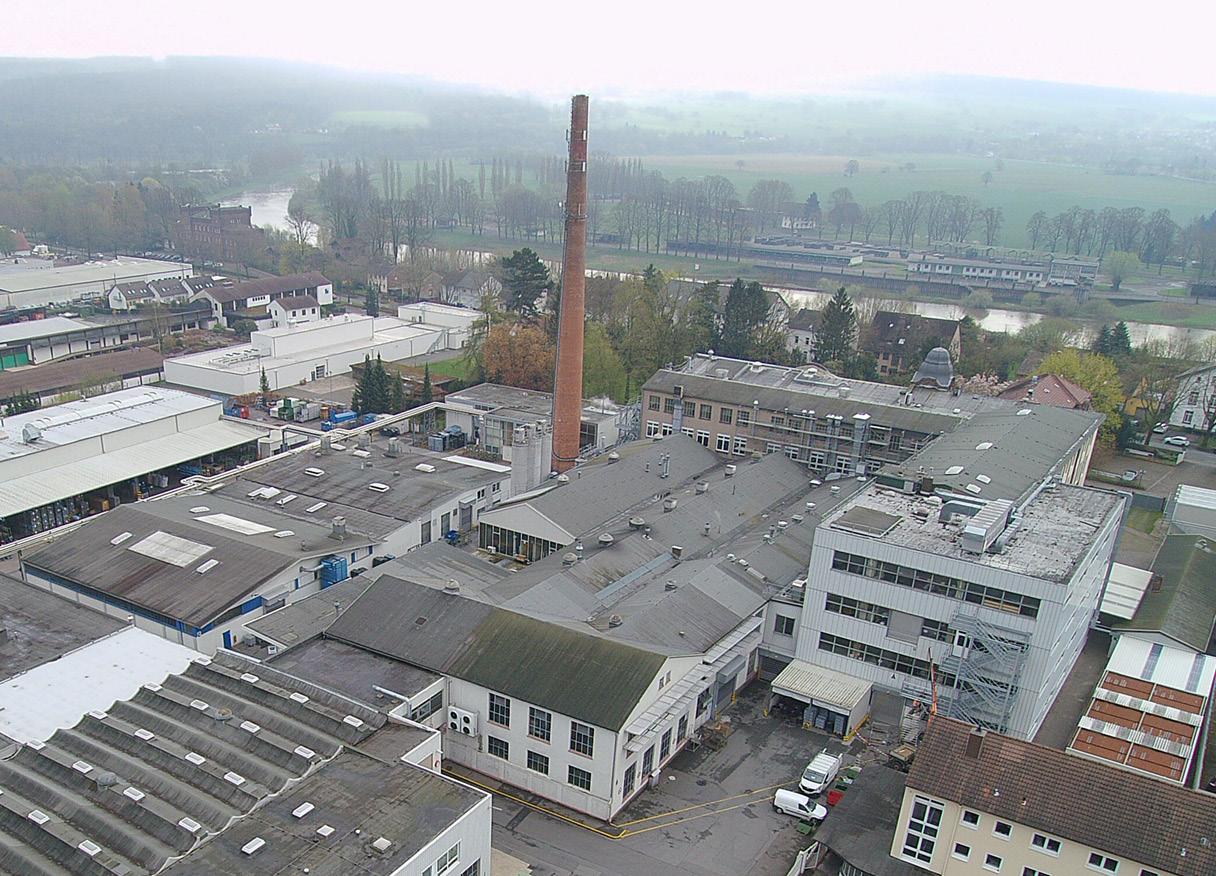
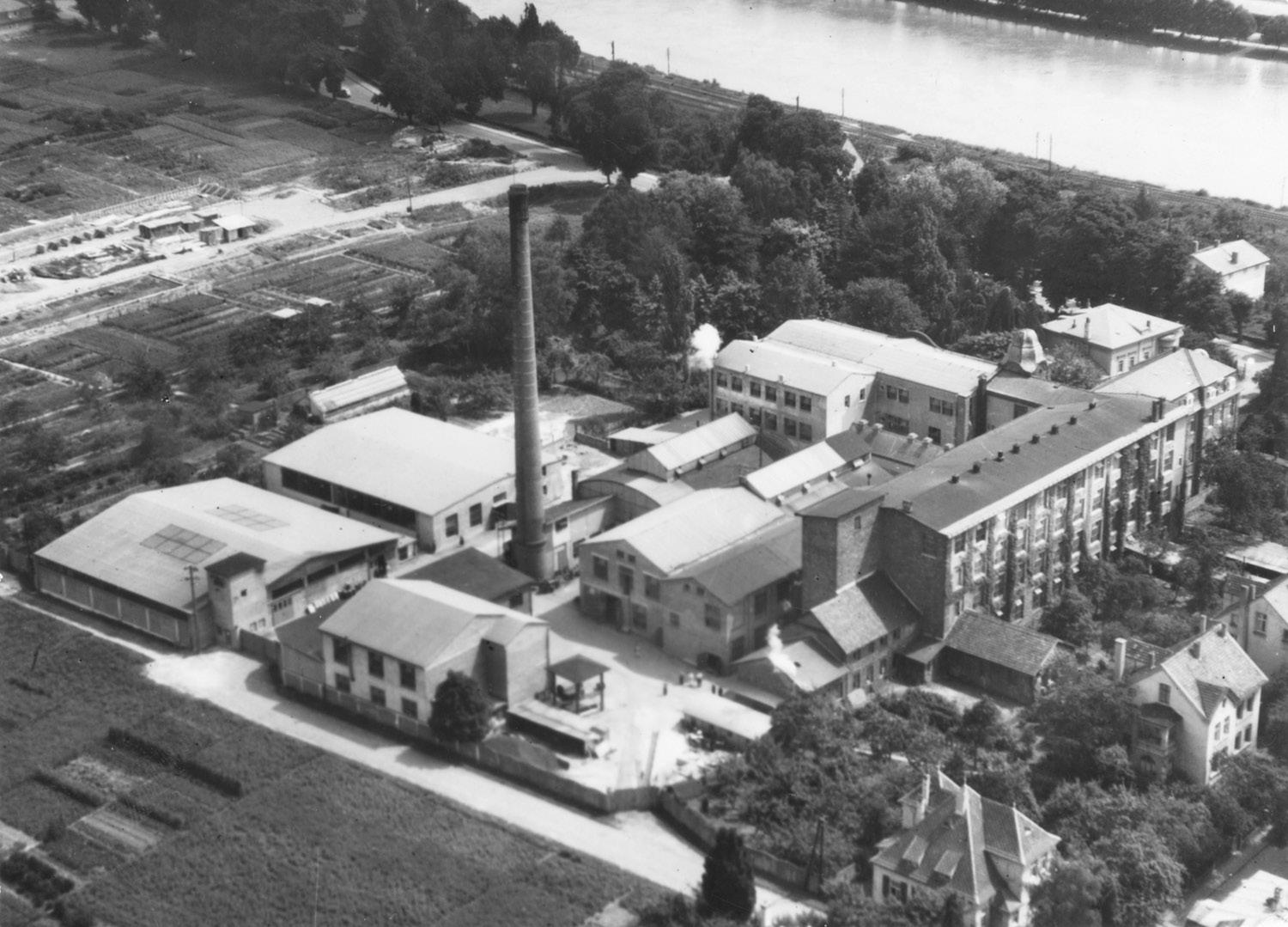
Optibelt Building, Old (Left) and New (Right)
As one of the world’s most important manufacturers of high-performance drive belts and specific drive solutions for a wide range of industries, the Arntz Optibelt group of companies looks back on 150 successful and eventful years and takes a look into the future.
“We keep the world moving sustainably. Innovative solutions are our passion. Our drive: trust and partnership.”
That’s the motto of the Arntz Optibelt group of companies, and over the past 150 years, they’ve become one of the world’s most important manufacturers of high-performance drive belts and specific drive solutions for a wide range of industries.
Founded in 1872 by Emil Arntz with just ten employees, in the early years, ‘Höxtersche Gummifädenfabrik’ produced rubber threads and technical rubber products.
After the first V-belt left the factory in 1948 under the name ‘Optibelt’, the name became a trademark in the industry. 20 years later the first foreign production facility was founded in Northern Ireland and other new production sites followed in China and Romania.
The family-owned company has been in its current form since the end of the 1990s, and continues to be a medium-sized enterprise, today employing more than 2,400 people at eight production sites and 33 sales offices in 30 countries.
“Family-run from the very beginning, down-to-earth, innovative and always orientated towards profitable growth, we focus on uncompromising quality, durability and sustainability,” explains Reinhold Mühlbeyer, Chairman of the Board of Management.
Commitment to the location
Founded in Höxter, Germany, the Arntz Optibelt Group is still headquartered there today.
As one of the special highlights on the occasion of the 150th anniversary, a fashion collection with various Optibelt motifs was designed for the employees, the proceeds of which will be donated to the Höxter-Tisch e.V. in order to help and support the volunteers involved in the association in their work for families and fellow citizens in need.
As the largest local employer in Höxter, Optibelt supports the urban development project both materially and ideally.
Industries
Today the company services industries as diverse as: cement, road construction, pulp & paper, agricultural technology, oil & gas, fans & compressors, food & beverage, automotive, heavy transport, logistics & distribution, textiles, lawn & garden, sealing & damping technology, x-ray protection, and leisure and sport.
Products include v-belts, rubber timing belts, PU timing belts, kraftbands, industrial belting, metal products, technical devices, couplings, automotive & commercial vehicle spare parts, technical elastomer sheeting, personal & industrial x-ray protection.
A look into the future
Optibelt’s long company history also includes the training of its own specialists and executives and the group is constantly increasing the number of apprenticeships in various areas.
In addition, Optibelt offers exciting job opportunities in a wide range of specialist areas.
Whilst looking back on 150 years in the industry; the company is also looking ahead.
One of the key objectives within the Arntz Optibelt Group’s mission statement is to become climate-neutral worldwide by 2040 through our own efforts.
To this end, the company is already calculating its CO2 footprint today in order to determine its own climate impact. Numerous efficiency and sustainability measures at locations worldwide are being vigorously addressed and implemented in order to reduce energy consumption.
“These important milestones also make it clear that we are taking the much-cited turning point seriously in order to set the right course for the future for the company and its employees,” emphasises Managing Director Konrad Ummen.
The Australian regional office and warehouse facility was established in 2009 and today has offices in Melbourne, Brisbane and also in Auckland, New Zealand, servicing the broad range of industries serviced by the parent company.
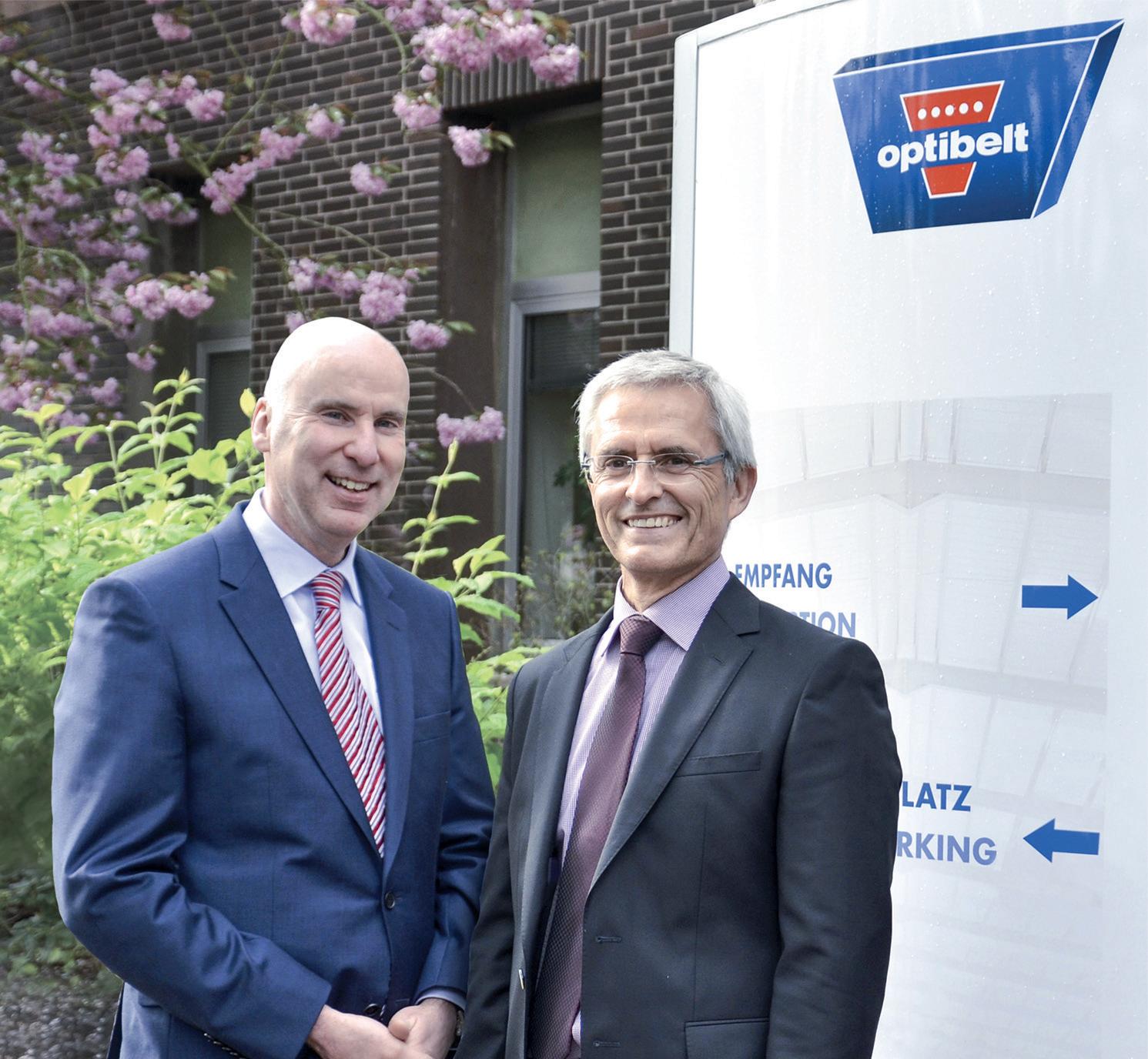
Konrad Ummen, Managing Director (Left) and Reinhold Mühlbeyer, Chairman of the Board of Management (Right) First Optibelt V-Belt
Australian Space Park looking for manufacturing partner
Australia’s only dedicated space manufacturing hub, the Australian Space Park in Adelaide, is seeking expressions of interest for a partner to operate the Common User Facility (CUF).
The hub, announced in December 2021, aims to fasttrack the country’s sovereign space manufacturing capability.
The CUF will offer manufacturers access to facilities with a focus on the production of small satellites and their payloads, rockets and electric vertical take-off and landing vehicles (eVTOL).
The park is seeking expressions of interest from either a single entity (prime contractor) or a consortium with the capability, capacity, and resources to operate the CUF, to drive the development of Manufacturing, Assembly, Integration, and Test (MAIT) activities.
The South Australian Defence and Space Industries Minister Susan Close, when making the announcement at the International Astronautical Congress in Paris, said, “The CFU will provide vital infrastructure to position Australia’s space community to deliver the entire space value chain through the design, manufacture and launch of new space capabilities to orbit and beyond.”
The successful CUF operator will be selected in a two-stage procurement process. This EOI stage focuses on developing a shortlist of respondents with the appropriate approach to operate the CUF.
Companies that have committed to becoming partners and co-investors in the Park include global aerospace giant Airbus, Fleet Space Technologies, Alauda Aeronautics, ATSpace and Q-CTRL.
Funding for the park is split between the South Australian government and the federal government, with the state investing $20 million, and the federal government giving an additional $20 million for the CUF.
The South Australian Government is in discussions with Adelaide Airport as the ideal location identified by industry due to its proximity to traditional aerospace companies, the Australian Space Agency and the central business district.
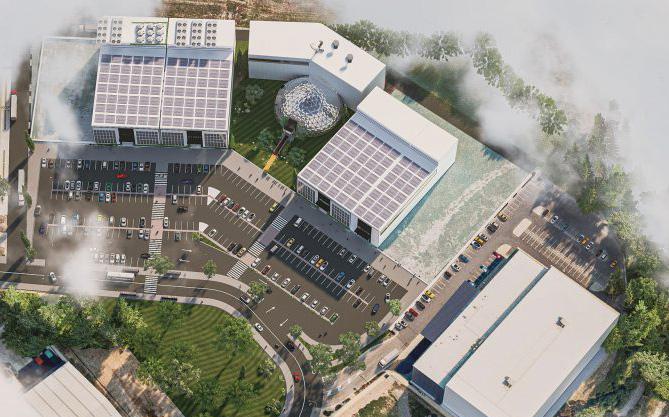
TENTE LINEA
SAFETY BRAKE CASTOR SYSTEM
The Tente Linea Safety Brake is locked by default and can only be moved when the brake is actively released, ideal for slopes – no more runaway trolleys.
Ball bearings hold the cable wire for better mobility.
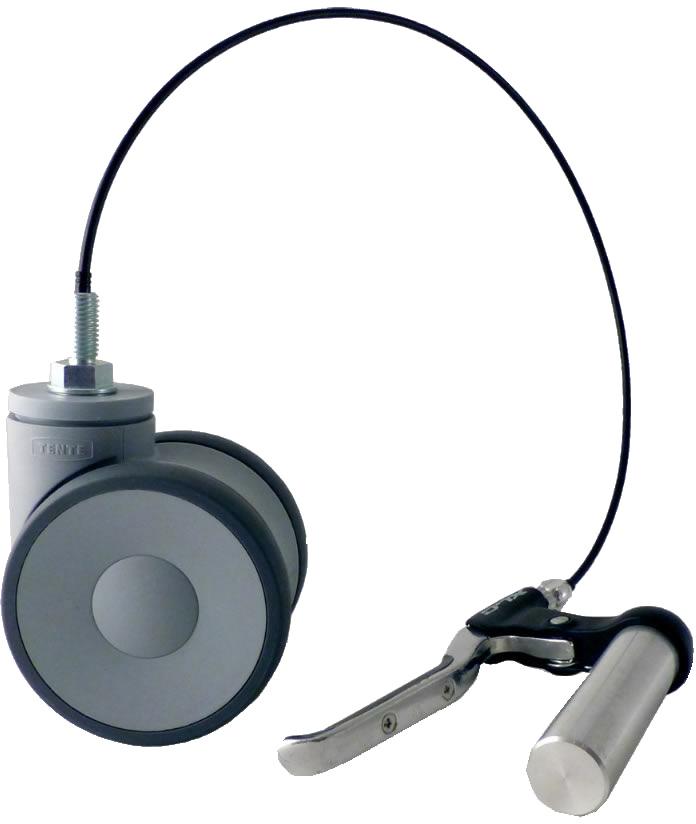
Product Quality Award 2013
Available in 75 & 100mm
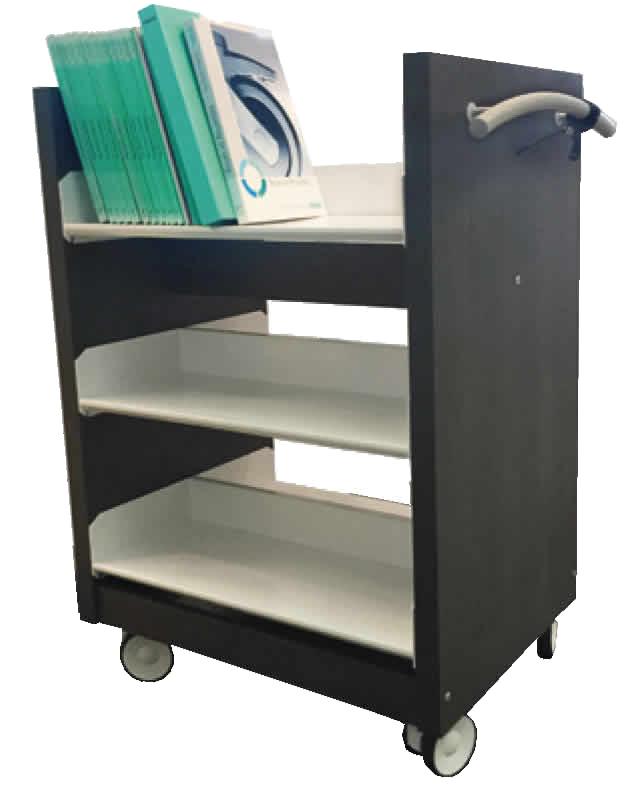
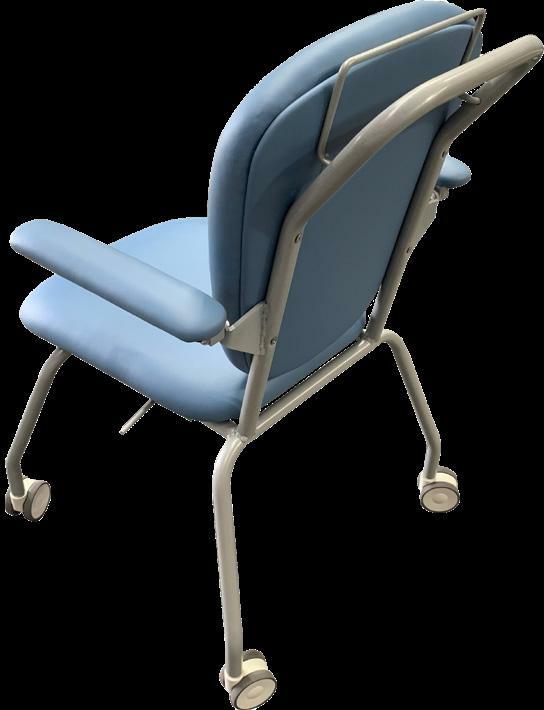
The wheel lock is permanently activated and can be release by hand/ foot lever. The connection between the castor and the trolley is made by operator.
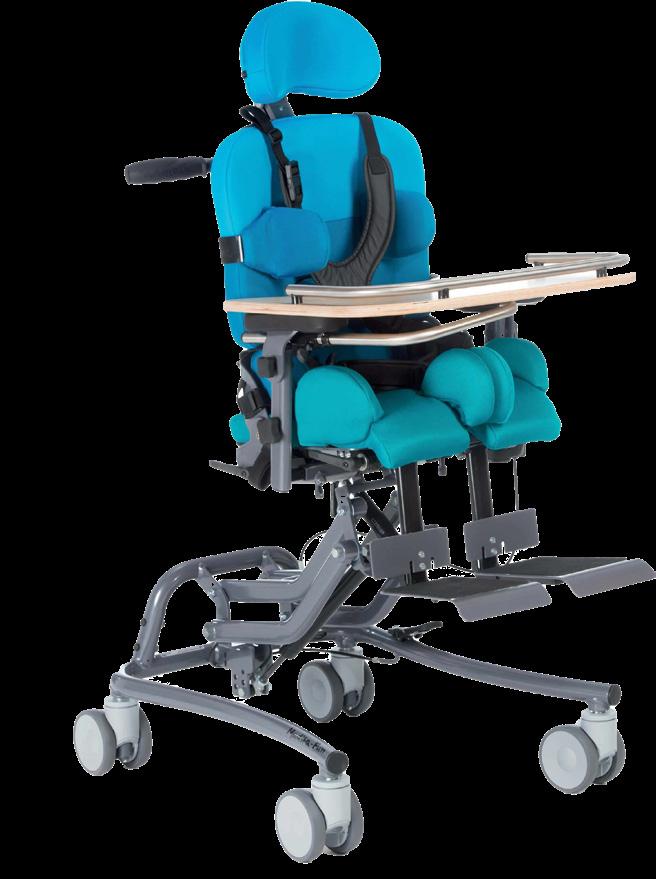
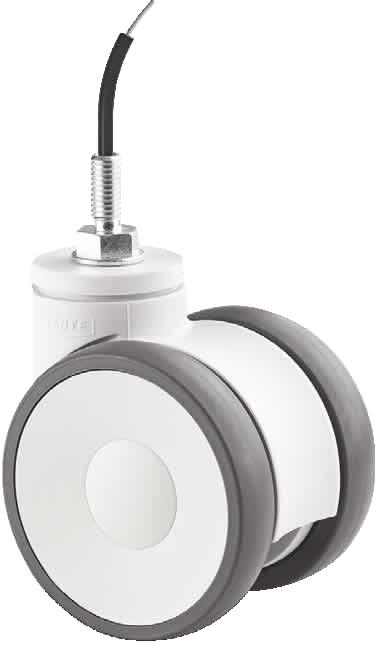
New-energy vehicle giant orders Yizumi
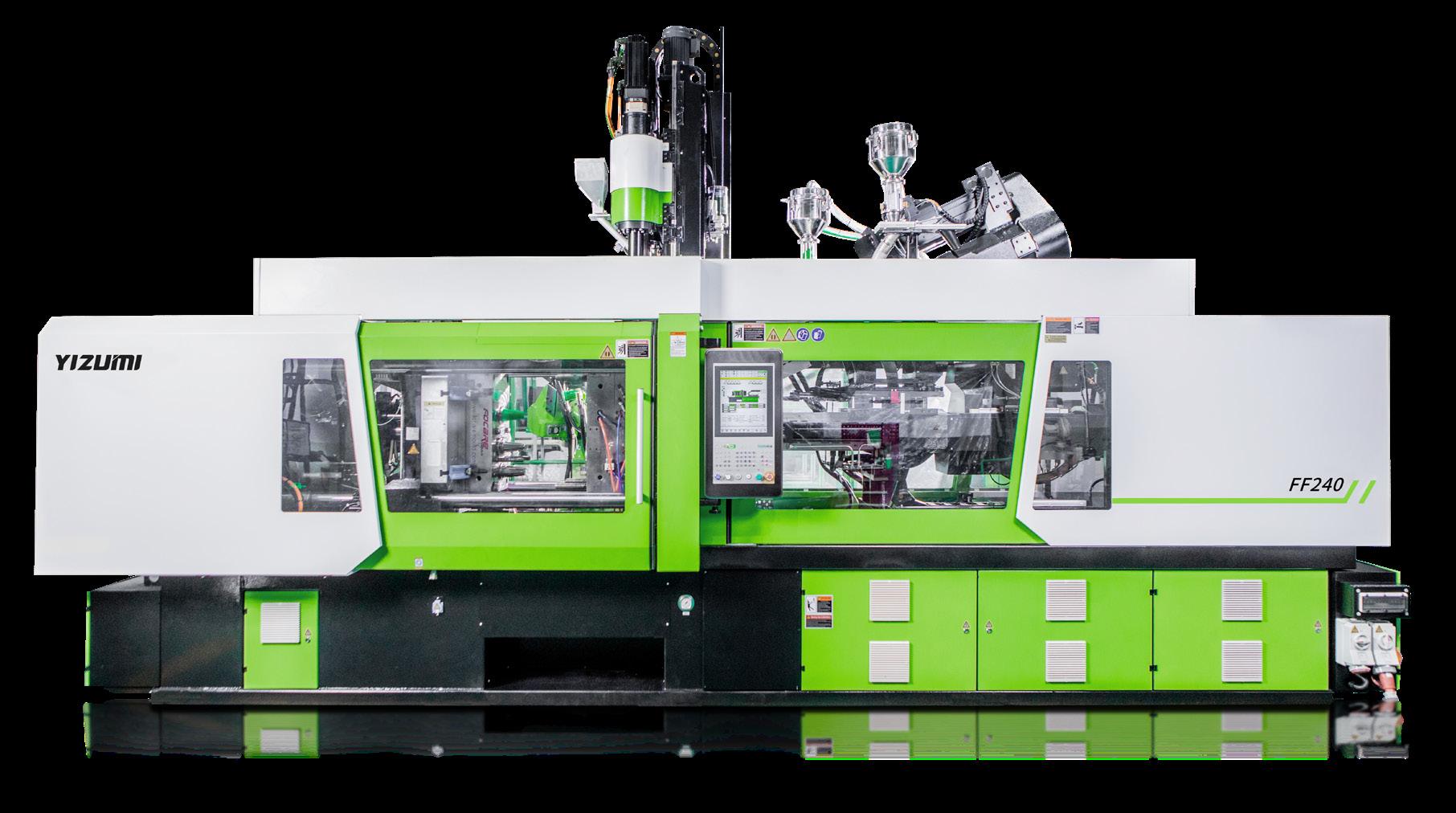
Guangdong-based moulding equipment company YIZUMI has successfully won a major order from BYD, a leading Chinese new energy vehicle (NEV) manufacturer, valued at more than 300m Chinese yuan, or $64 million Australian dollars.
The winning models are mainly all-electric injection moulding machines, with clamping forces from 90 tonnes to 550 tonnes, and suitable for producing different sized interior and exterior car trims in NEVs.
This cooperation indicates the technical strength of YIZUMI and has once again been recognized by the leading Chinese NEV enterprise.
BYD, the biggest manufacturer of NEVs in China, has quickly reached global distribution over twenty years.
In addition, BYD has played a pivotal role in electronics, vehicles, new energy, rail transport, etc.
According to the data released from BYD, it sold 641,400 cumulative NEVs in the first half of 2022 with a YOY growth of 314.9%.
Moreover, BYD has surpassed Tesla as the new top manufacturer globally and entered the Fortune Global 500 2022 for the first time, demonstrating its competitive brand strength.
In July, BYD officially announced its entry into Japan, one of the major automobile production and export countries, indicating its solid confidence and determination to compete in the international high-end market.
Soaring demand for NEVs
With the soaring demand for NEVs, BYD’s development has been constrained by its production capacity.
To address this, BYD has proactively invested in and built new production bases in Hubei Province and Guangdong Province this year.
In Shenzhen and Shantou cities in Guangdong, it won the bids for three pieces of industrial land for NEVs, with a total area of more than 2 million square metres.
With such explosive sales growth in NEVs and the continuous improvement and performance brought by YIZUMI injection moulding machines, the scale of sales and production demand can now be addressed.
Thus far, more than 100 YIZUMI all-electric and two-platen injection moulding machines have been ordered by BYD to fulfil its requirements in NEV production since 2018. Up to 18 YIZUMI two-platen injection moulding machines have been delivered to BYD’s Hefei plant.
The stability and high performance of YIZUMI’s injection moulding machines has strengthened the collaboration between BYD and YIZUMI and was key to winning this major order.
Yizumi design
NEVs are key to transforming the world auto industry to a cleaner status and YIZUMI understands this trend.
YIZUMI’s all-electric injection moulding machines adopt a modularisation design with clamping units and various injection units that can be combined flexibly as per customers’ requirements.
They have an injection speed of about 160-500 mm/s, and position accuracy of injection and mould opening & closing to within 0.03 mm. Advantages of high precision, high efficiency, high stability and automation help satisfy needs of global customers in different sectors.
With a deep and high technical level understanding of the automotive industry, YIZUMI machines fulfil specs for moulding components such as lights, air conditioners, interior and exterior components, etc.
In the future, YIZUMI is expected to enter the high-end automotive manufacturing chain and become a better cost-effective solution provider by continually introducing new processes and turnkey solutions.
Sydney-based PBE-Roboplas is YIZUMI’s agent and provides a versatile range of plastics machinery and ancillary equipment.
PBE Roboplas
pbe-roboplas.com.au
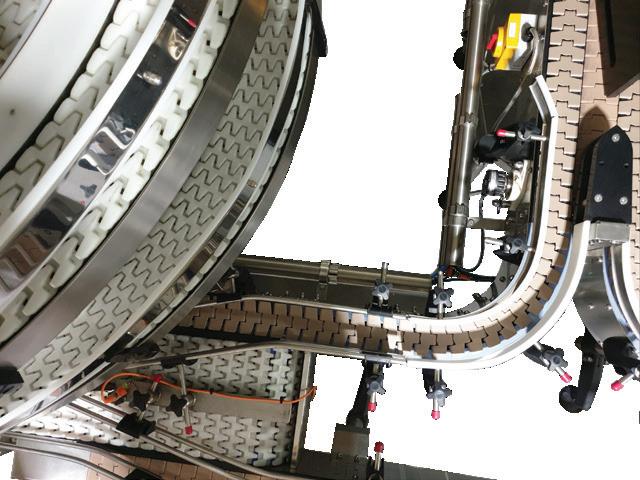
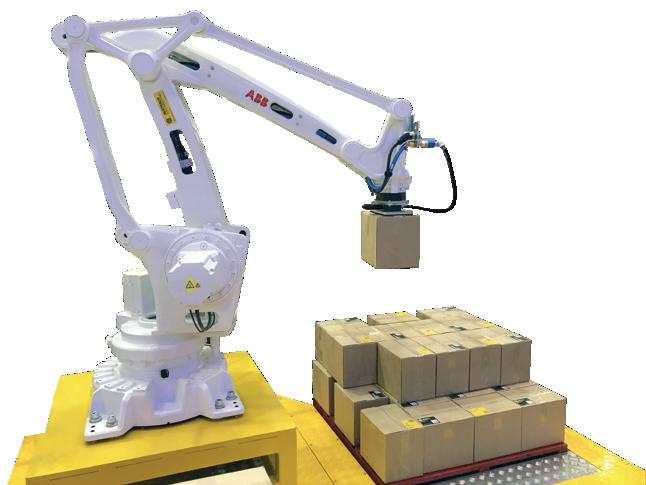
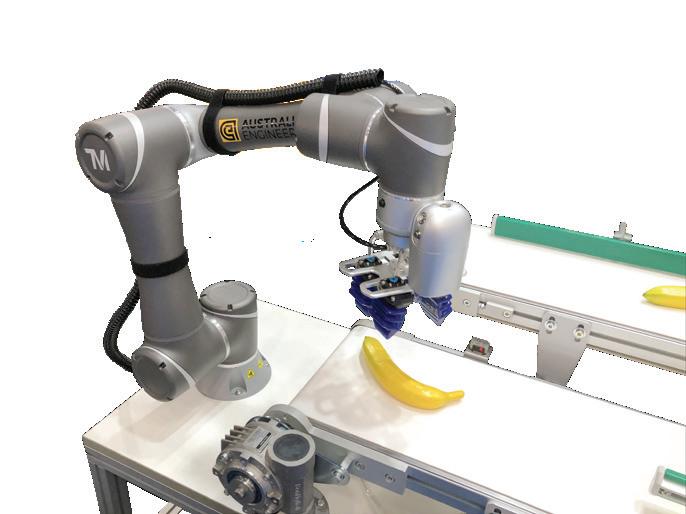
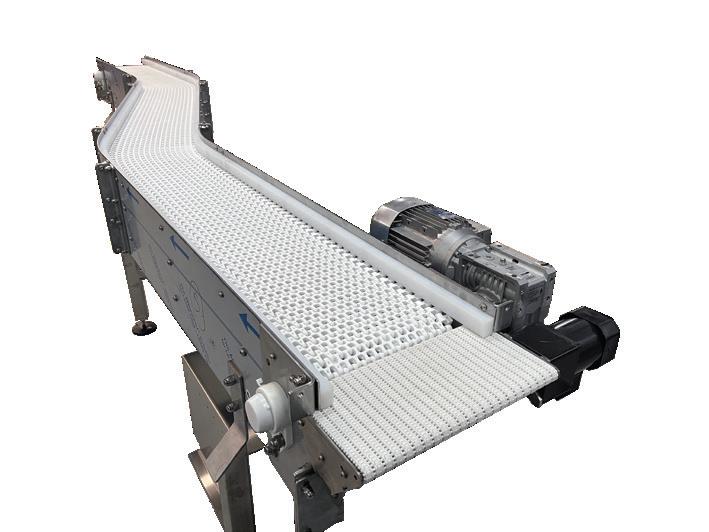