
11 minute read
Universities, Research and Development
UNSW’s retrofitted diesel engines run on hydrogen
The Hydrogen-Diesel Direct Injection Dual-Fuel System has been developed by the UNSW Engine Research Laboratory’s team led by Professor Shawn Kook (right), and including Xinyu Liu (back left) and Jinxin Yang (front left).
Advertisement
Engineers from UNSW Sydney have converted a diesel engine to run as a hybrid hydrogen-diesel engine — reducing CO2 emissions by more than 85% in the process.
Professor Shawn Kook and his team from the School of Mechanical and Manufacturing Engineering developed the patented Hydrogen-Diesel Direct Injection Dual-Fuel System in 18 months.. They believe any existing diesel engines in trucks or power equipment — for manufacturing, transportation, agriculture and mining industries — can be retrofitted this way in just a couple of months to use 90% hydrogen as fuel.
The International Journal of Hydrogen Energy has published the UNSW researchers’ paper which shows their hydrogen injection system reduces CO2 emissions to just 90 g/kWh — 85.9% below the amount produced by the diesel-powered engine. Green hydrogen is produced by clean, renewable energy so it reduces emissions during its production as well as its use as a fuel.
The team aims to convert existing diesel engines at about half the replacement cost of a new diesel engine and anticipates their system will compete against hydrogen fuel cell systems, a widely demonstrated CO2 reduction technology. Prof Kook believes theirs has several advantages over hydrogen fuel cells.
“Our advantage of our system is that is easier to adopt, it uses existing infrastructure and skills, and has lower costs on both development and fuel,” said Prof Kook.
“Hydrogen used for fuel cells must be of extremely high purity which makes it higher cost. In our system the hydrogen can be lower purity and therefore less expensive because the impurities are being burned out during the combustion process.”
“Retrofitting diesel engines that are already out there is much quicker than waiting for the development of completely new fuel cell systems that might not be commercially available at a larger scale for at least a decade,” said Prof. Kook, stressing that climate change means we need more immediate solutions.
“This new technology significantly reduces CO2 emissions from existing diesel engines, so it can play a big part in making our carbon footprint much smaller, especially in Australia with all our mining, agriculture and other heavy industries where diesel engines are widely used,” said Prof. Kook.
High-pressure hydrogen direct injection
Resulting from a collaboration with Dr Shaun Chan and Professor Evatt Hawkes, the new system maintains the original diesel injection into the engine but adds a hydrogen fuel injection directly into the cylinder.
Their research found that timed hydrogen direct injection controls the condition of the mixture inside the cylinder of the engine and this resolves the problem of harmful nitrogen oxide emissions which had been a major hurdle for commercialisation of hydrogen engines.
“If you just put hydrogen into the engine and let it all mix together, you will get a lot of nitrogen oxide (NOx) emissions, which is a significant cause of air pollution and acid rain,” Prof. Kook said.
“In our system, we have shown if you make it stratified — that is in some areas there is more hydrogen and in others there is less hydrogen — then we can reduce the NOx emissions below that of a diesel-only engine.”
Compared to existing diesel engines, an efficiency improvement of more than 26% has been shown in the diesel-hydrogen hybrid. That improved efficiency is achieved by independent control of timing of hydrogen direct injection, as well as diesel injection timing, enabling full control of combustion modes — premixed or mixing-controlled hydrogen combustion.
The research team hopes to be able to commercialise the new system in the next year or two and is keen to consult with prospective investors. They say the most immediate potential use for the new technology is in industrial locations where permanent hydrogen fuel supply lines are already in place.
That includes mining sites, where studies have shown that about 30% of
greenhouse-gas emissions are caused by diesel engines in such items as mining vehicles and power generators. And the Australian market for diesel-only power generators is currently estimated to be worth around $765 million.
“At mining sites, where hydrogen is piped in, we can convert existing diesel engines that are used to generate power,” said Prof. Kook.
“In terms of applications where the hydrogen fuel would need to be stored and moved around, for example in a truck engine that currently runs purely on diesel, then we would also need to implement a hydrogen storage system to be integrated into our injection system.
Prof. Kook believes the technology for mobile hydrogen storage needs to be developed further.
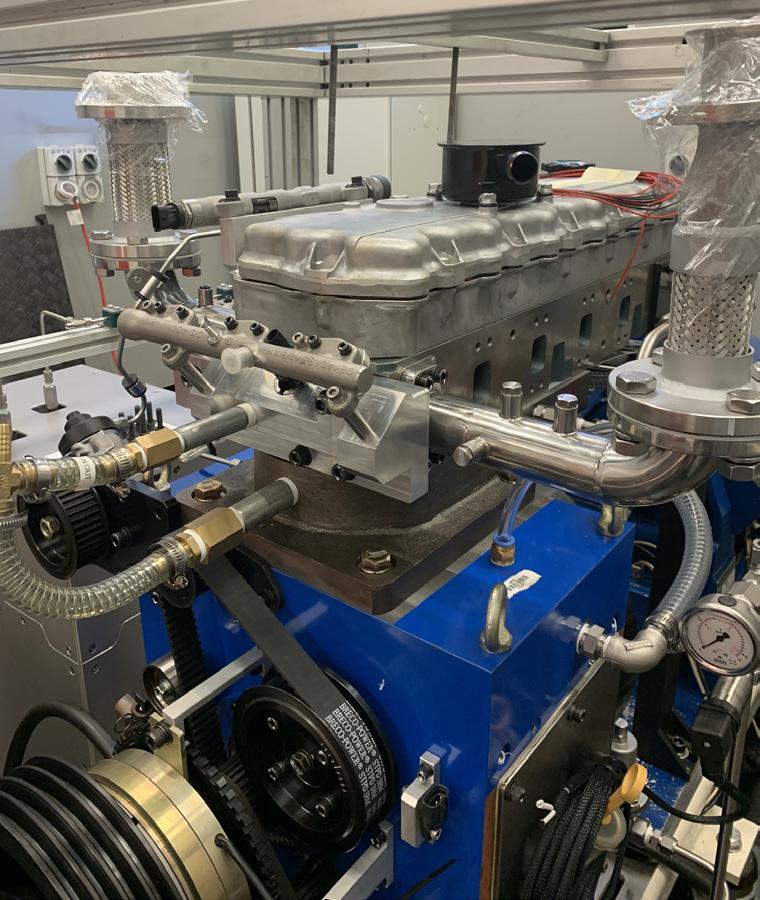
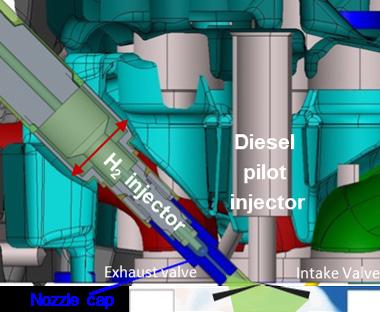
Co-investment in Australian manufacturing drives real growth
The Advanced Manufacturing Growth Centre (AMGC) has released its 2022 Project Report – demonstrating manufacturing transformation and revealing a significant positive industry impact. The report provides an overview of the organisation’s 141 co-invested manufacturing projects and showcases the economic contribution from its first 31 completed projects. All AMGC projects involve collaboration between industry and a research-led organisation.
Analysis of the organisation’s 141 projects provides evidence of real jobs and revenue growth generated from the initiative. Overall, the projects are expected to generate $1.62 billion in additional revenue and the creation of 4,288 new jobs. The returns reflect a combined industry and government co-funded pool of $137.2 million.
Of the 31 completed manufacturing projects, a total of 430 new or upskilled roles have been created while an additional $188 million in revenue was injected into the Australian economy via domestic and export sales. The revenue creation represents an average return on investment of 9:1, based on a co-funding investment of $20.26 million ($7.15 million derived from federal funding and the remainder from industry in cash and in-kind).
Speaking of the Project Report’s impact, Federal Minister for Industry and Science, Ed Husic, said, “Crucially, it [AMGC] has a focus on funding innovative projects that have the potential to make Australia’s manufacturing industry more productive and competitive, but might be in areas where companies may not have the capacity or expertise to tackle the task on their own,
AMGC’s portfolio of co-invested projects incliudes projects in resources, agriculture, forestry, and fisheries, transport, medical sciences, renewables, and low emissions technology, defence, space and, enabling technology – such as AI and robotics.
Some of the first 31 projects locally manufactured, include flying cars, solid-state rocket motors and fuel, prescription eyewear from recycled materials, invasive ventilators, track-and-trace system for the provenance of the wine, carbon fibre reinforced geopolymer to displace concrete, and carbon composite bike wheels.
Managing Director of AMGC, Dr Jens Goennemann said these successes are proof of the manufacturing industry’s readiness to invest, advance, scale, and export if highly targeted assistance is afforded to those who wish to commercialise and scale.
“We can manufacture amazing things in Australia, provided we focus on being better, not cheaper, that we add value to our abundant natural resources, and we embrace advanced practices and processes – our 2022 Projects Report is proof that we can do so much better than Australia’s current ranking of 91st in global complexity rankings,
“AMGC has demonstrated time and time again that by empowering manufacturers, through appropriately sized and supported initiatives, we can create prosperity for Australians and establish the country as a manufacturing powerhouse – we just need long-term commitment at all levels of Government to give the industry the confidence to invest where it matters”, said Goennemann.
Expertise - Passion - Automation
Hey!
Have you checked your air filters?
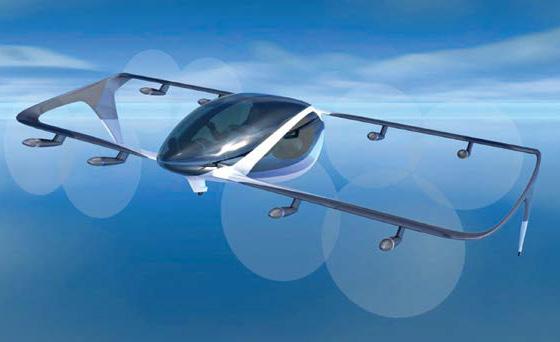
The AMSL Aero Electric VTOL (Vertical Take-off and Landing) aircraft has some design attributes that are viewed as significant advantages over other eVTOL concepts and make it adaptable to a range of different missions.
About Advanced Manufacturing Growth Centre (AMGC)
The Advanced Manufacturing Growth Centre (AMGC) is an industry-led, not-for-profit organisation.

In October, SMC is spreading awareness around the importance of changing the filters on your factory floor.
Why?
• It removes liquid water at the point that it is installed. • It helps machinery to run more efficiently and economically. • It helps keep contaminants out of cylinders, valves and other pneumatic components.
It’s quick and easy, and it makes a big difference to the life of your equipment. We are here to help - it’s as easy as 1,2,3… SMC!
Chat to our team to arrange an inspection!
#SayNotoNoFilter #doyoureallyknowSMC
SMC - more than pneumatics
KEY FORECAST IMPACT FROM AMGC PROJECTS
•141 co-funded industry projects •$137.5 million in co-funding investments •4,288 direct and 15,436 indirect jobs are expected to be created •$1.62 billion in estimated revenues generated •434 nation-wide collaborations
OUTCOMES FROM FIRST 31 COMPLETED PROJECTS
Upon completion of a co-funded project, participants contribute to a substantive finalisation process. The data collated revealed: •Increased revenues of $188 million from local ($136M) and international ($52M) sales •The creation, or upskilling, of 430 direct jobs •Average Return on Investment (ROI) 168% •Participants reported an increase in - Profit – 77% of participants - Range of products and services – 83% of participants - Productivity – 83% of participants - Profit Margin – 57% of participants •The majority of project participants reported improvements at all points along the manufacturing value chain •Many project participants engaged in collaborative endeavours, with: - 75.8 per cent of completed project participants rating working with research institutions as ‘positive’ or ‘very positive’ •Of the 31 completed projects, 89 per cent of participants increased activities around exports, niche or underserved markets •All projects reported an increase in their business resiliency strategies


Students’ sustainable designs to win $15,000
Continued from first page
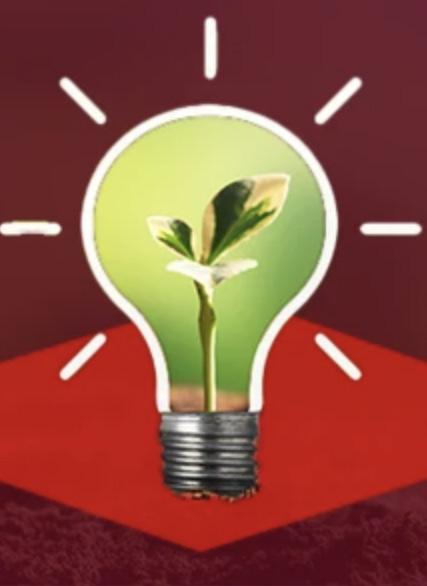
Scott Philbrook, Managing Director ANZ for RS, the parent company of RS PRO, says he is looking to support future generations of engineers through programs such as this.
“The last two years has been a strange and stressful year for the evolution of design and engineering in many sectors,” he said.
“The opportunity to submit your concept and potentially be given the tools to build the project is a kick-start for any entrant into 2023. The sustainable and environmental criteria is commensurate with current expectations in the industries applicable to these projects.”
The competition criteria include:
Socio-technical skills
Sustainable design skills, including the environmental, economic and social impacts
The demonstration of effective communication skills through the design pitch application and the outline of teamwork and skills for the project
A demonstration of how the prize will help the entrant achieve social, economic, and environmental impacts
The five winners will be announced later in the year and entries close Monday 31st October, 11:59pm (AEST). To be eligible you must be aged 18 or over living in Australia & NZ and enrolled in a full or part-time university-level academic, engineering, or technology-related programme.
To enter or for more information visit
Australia
‘Not sexy but fascinating’: uni students fill skills gap in food sector and beyond
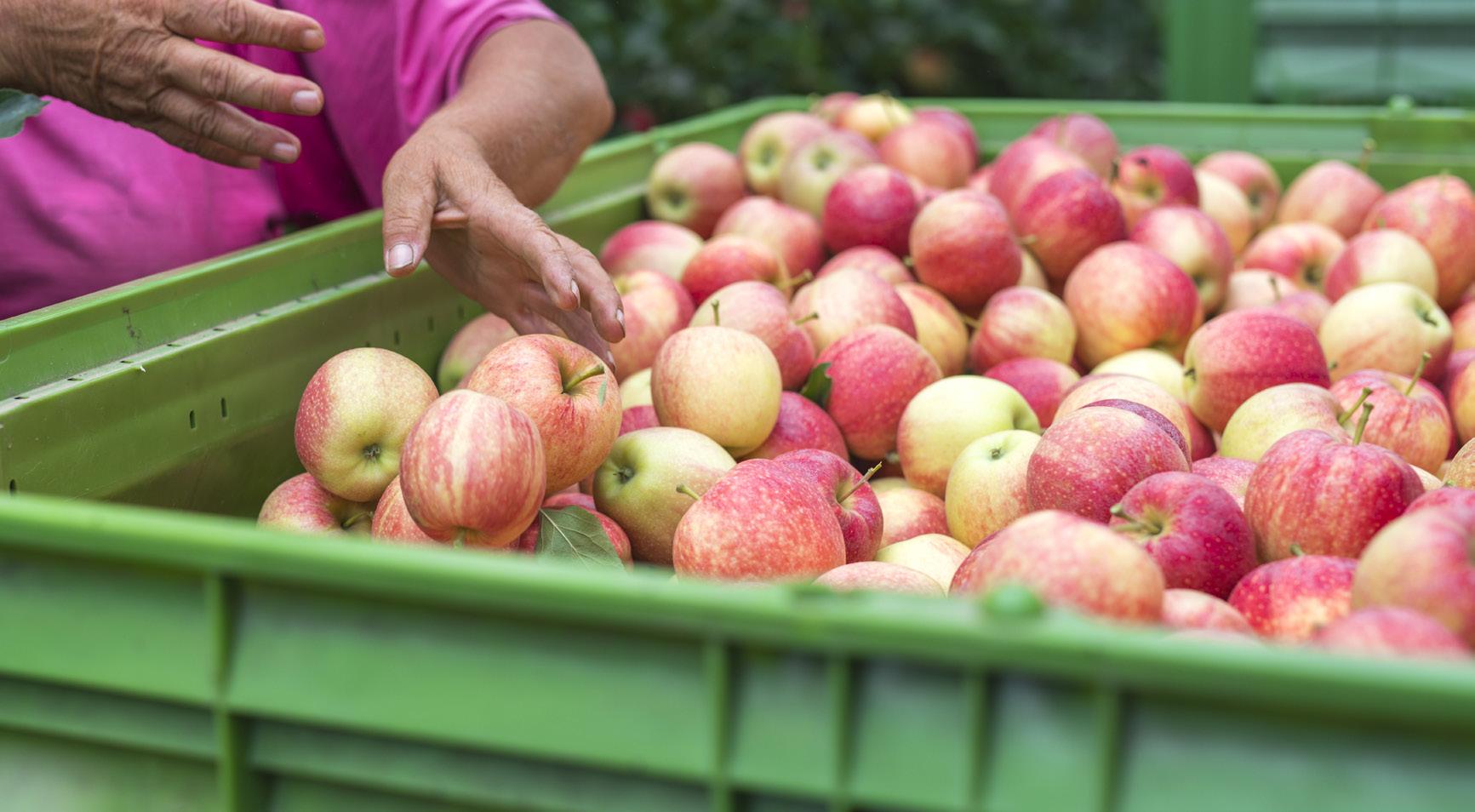
The skills shortage in Australia right now is driving a shift towards ‘dark factories’: ones that are so heavily automated they need minimal human involvement.
However, to get the skills the company does need, Sydney based food manufacturer Beak & Johnston told the Smart Manufacturing Conference in September it now targets university graduates rather than bringing people in from Europe, said Pool, a shift that’s become more critical since Covid closed the borders.
“We network extensively with universities and students. Many find the food industry fascinating, despite the fact it’s not considered particularly sexy.
“Some who we’ve brought on board have been with us for 30 years now.”
Mikael Sandell, of leading global pneumatic manufacturer SMC Corporation, also spoke at the conference, and said they take a similar approach to getting the skills they need.
“We see the future as university graduates, and we try to catch them when they start their courses.”
“We offer training that sets them up so that they’re already being introduced to SMC technologies while they’re at university.
“Our business model is heavily focused on R&D. We have 1771 R&D engineers globally, and five technical centres. This explains why we have managed to stay at the top of the market.”
Alan Lipman from bespoke high-tech manufacturer Romar also attested to the quality of students who go on to work in the industry.
He told the conference the advanced manufacturing sector will continue to grow and become more efficient with help from the “incredibly high” standard of young engineers graduating from Australian universities.
Free education, guidance and leadership for Australian manufacturers seeking advancement, competitiveness and growth. 9 learning modules 20 real stories of Australian success 4+ hours of content
manufacturingacademy.org.au
SCAN TO FIND OUT MORE
MARKET REACH
WORKFORCE
RESILIENCE
THE STATE OF MANUFACTURING
COMPETITIVENESS
PRODUCT VALUE
INDUSTRY 4.0
MANUFACTURING WITH ROSIE
THE CIRCULAR ECONOMY

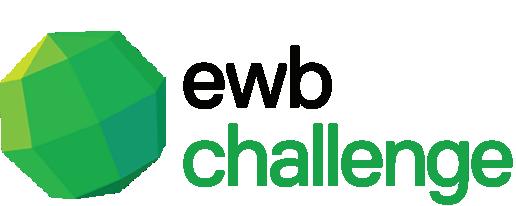