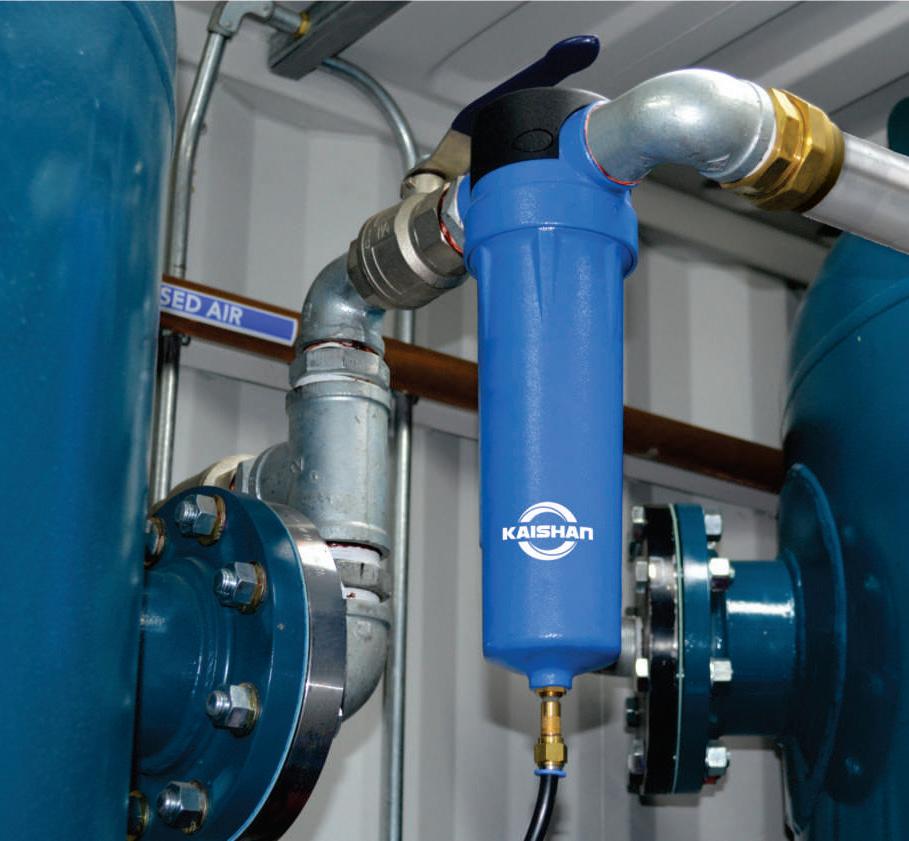
14 minute read
Machinery
Clean, compressed air for all applications
Compressed air is used in industries as a safe and efficient power source for multiple applications. As with most sophisticated equipment, it’s vital to clean and maintain the system to keep it operating at peak performance whilst keeping running costs to a minimum.
Advertisement
Compressed air filters are one of the most effective ways to ensure high-quality, efficient compressed air delivery, filtering out contaminants like solid particulates, water vapour and oil residue. As with all types of filters, compressed air system filters will fill up over time, eventually requiring service and replacement.
Regular maintenance, cleaning and replacement of compressed air filters brings many advantages, including:
Maintaining peak efficiency
Compressed air filters trap contaminants and particles so the flow of air through the filter becomes impeded and eventually results in a significant pressure drop. This means that the air compressor must work harder to deliver the same level of pressure—or that tools and equipment will not receive the level of pressurisation they need.
To prevent these scenarios and ensure equipment runs at its rated efficiency and pressurisation, it’s critical to monitor and service compressed air filters. This might include replacement when cleaning is no longer sufficient.
Compressor filters contain a pressure differential gauge that can provide a fast and easy way to see when efficiency is suffering.
Controlling energy & repair costs
With excessive pressure drop caused by clogged filters, compressors have to work harder to deliver the level of pressurisation required by end applications. This means that energy costs will increase, cutting into margins and throwing budgets askew. Regular filter maintenance is one of the easiest ways to keep operating costs predictable and under control.
Keeping air clean
Compressed air that contains contaminants, particulates or vapour, presents several dangers and risks. In medical-grade applications for example, compressed air will be required to meet cleanliness and purity standards to prevent contamination of lab samples, medical devices and medicines. The same applies for food-grade applications, where it is critical to keep food and beverage products free from contamination. Contaminated compressed air not only presents regulatory risks but it can also cause products to become dangerous to end-users and others who handle them.
Preventing equipment damage
Equipment that runs on compressed air is designed to use clean, well-filtered air. Poorly filtered air that contains contaminants, vapours or particles can damage equipment through corrosion, mechanical damage or oil damage, to name just a few problems. When compressed air is used for applications such as cleaning equipment or products, damage may also occur if the air is not properly filtered.
Depending on the sensitivity of applications and processes, one or more inline air compressor filters could be needed. Choosing the right inline air filter for the application is essential for eliminating damage to the final product. For inline compressed air filters to be effective, they must be placed correctly in the piping system.
Replacing air filters
It is recommended that compressor and inline air filters be replaced every year or after every 8,000 hours of continual operation. Filters should be replaced more often in situations where filtration is inadequate for the system or when increased levels of contamination from high oil carry-over or pipe corrosion occur.
How is a clogged air filter likely to affect the compressor?
When an air filter is clogged, the compressor must work harder to compensate for blockage to air flow. Thisoften causes the blower motor to overheat and lead to system failures.
System operators and maintenance personnel go to great lengths to keep air compressors clean and working at peak efficiency. However, all too often the plant air system the compressor is feeding is neglected. Once the air leaves the compressor, it is important to have superior inline filters in place to ensure that the air going out to its application is as clean as it can be.
Inspecting compressed air systems
Kaishan technicians can assess compressed air system and application requirements to recommend the right type and capacity of air filters to match needs.
Kaishan’s wide range of industrial compressed air filters provide the highest air quality, lowest power consumption, lowest operational differential pressure, lowest CO2 emissions and lowest total cost of ownership.
Other inline decontamination products
Kaishan stocks supplies and fits a range of specialised inline products to ensure peak operation of compressed air systems including: •Air receivers: to increase efficiency and reduce maintenance in every system. •Auto drains: for automatic draining
of excess condensates. •Refrigerated air dryers: for applications where dry air is required. •Oil/water separators: separates lubricants from condensate for easy disposal. •After-coolers: vital for protection from moisture contamination. •Condensate separators: for separation of condensed moisture from air.
Custom maintenance plans
Kaishan deploys a fleet of mobile compressed air technicians who ensure regular preventative maintenance— such as cleaning and replacement of air filters—is carried out. Customised maintenance procedures keep all types and makes of compressors and systems operating at peak efficiency with highest beneficial input/output ratios that minimise the chance of costly breakdowns and emergency callouts.
Kaishan
kaishan.com.au
Savings with new dry block temperature calibrator A new calibrator from IKM Instrutek with touch display offers a calibration interval of up to three years. The TC65 portable
Model
TC65
Range
30 to 650ºC
Stability +/- 0.1ºC Accuracy 1 Yr +/- 1.5ºC Accuracy 3 Yr +/- 3.5ºC dry block temperature calibrator was designed to meet market requirements for cost savings based on this longer calibration interval.
It’s also been developed to meet the toughest environments.
The unit is sufficiently compact and robust for marine, industrial and laboratory use, approved according to relevant parts of DNVGL-CG-0339:2019). This is to ensure users are able to calibrate a vast range of temperature sensors, thermometers and temperature switches or thermostats. The dry block principle excludes the use of oil or other liquids. A dry block insert with various diameters ensures thermal contact to the sensor being tested.
Simply place the sensor to be calibrated in the calibrator, then set the temperature. When stabilisation occurs, read the true temperature from the calibrator and recalibrate the sensor or system accordingly. The new touch display makes it easy to use and read.
AMS
GROW YOUR BUSINESS WITH YAWEI. THAT’S APPLIED THINKING.
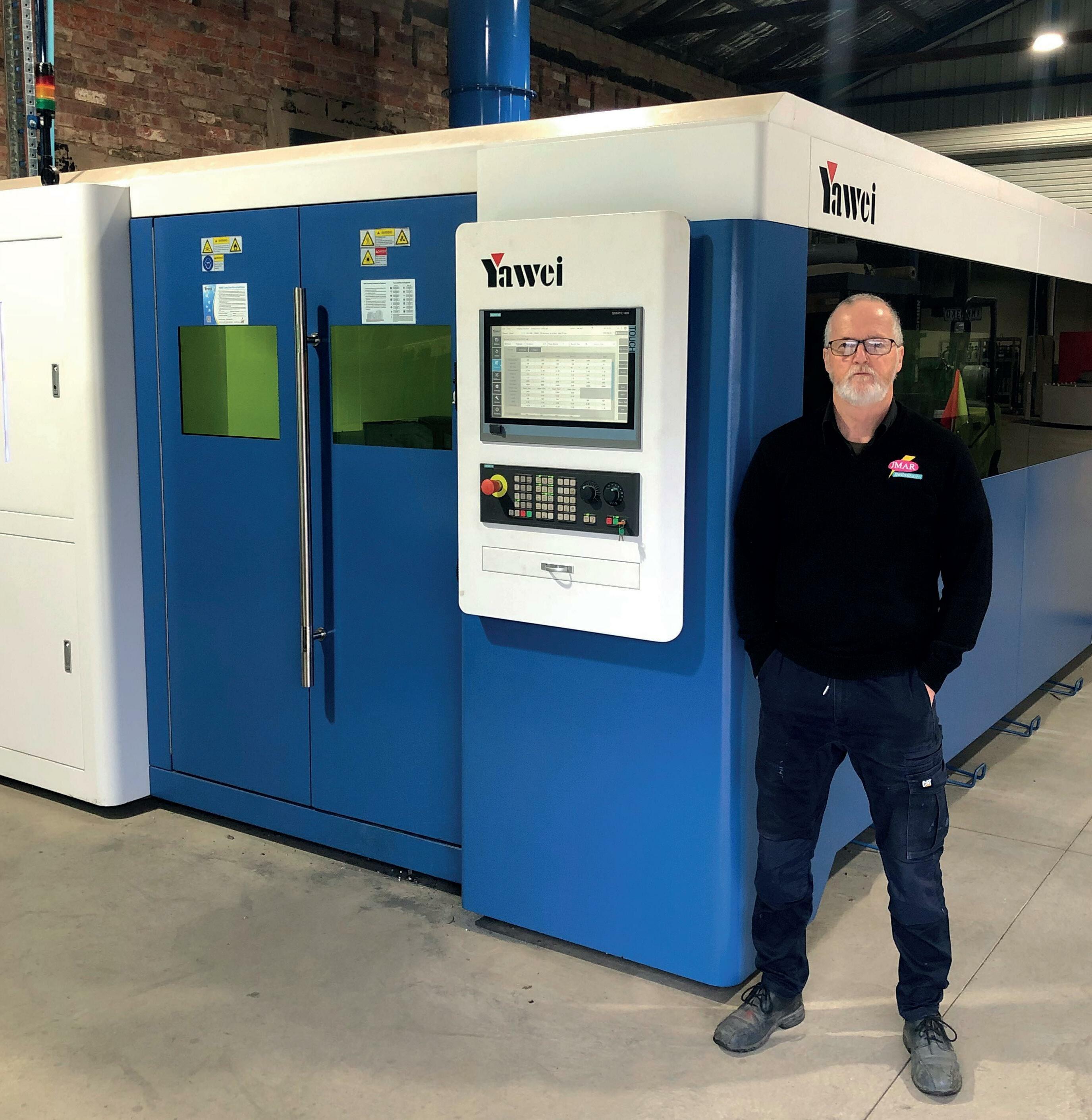
Precision sheetmetal processing solutions. Precision sheetmetal processing solutions.
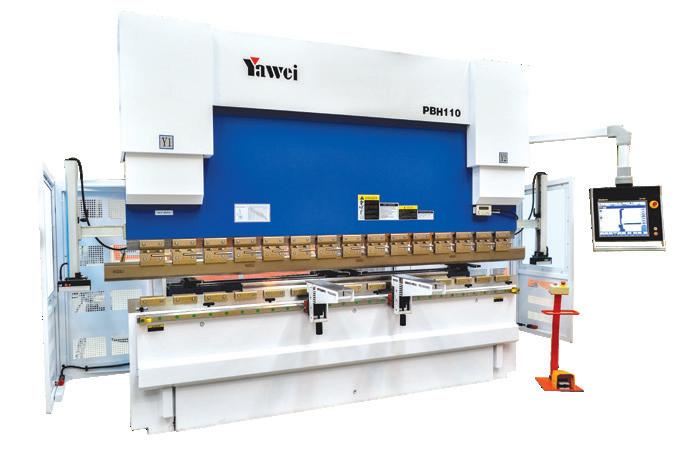
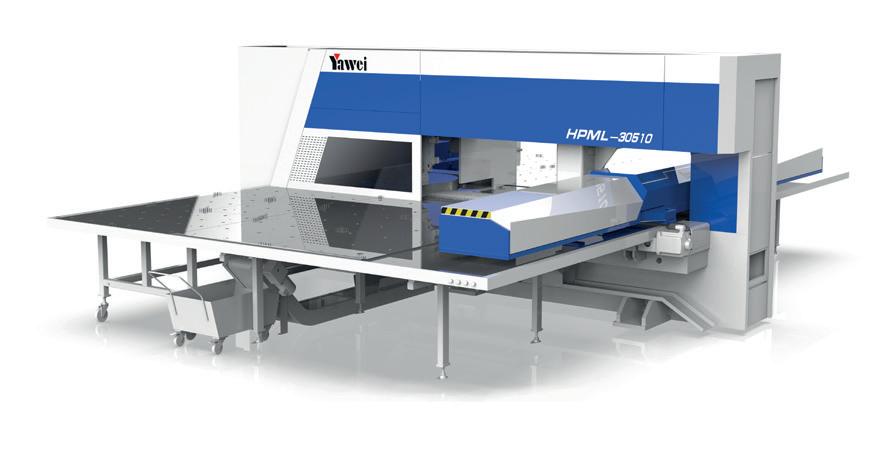
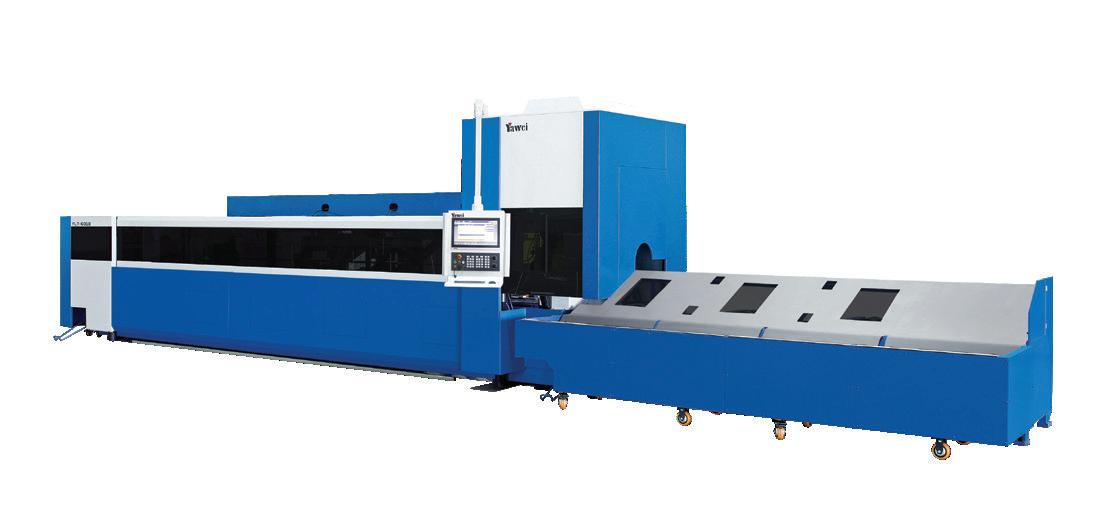
Fiber Lasers • Tube Lasers • Turret Punch Presses • Pressbrakes • Guillotines • Automation
The buzz about modern manufacturing
By Christine Powis
The crowd voted with their feet as the doors opened last week for the Modern Manufacturing Expo, for the first time in tandem with the Workplace Health and Safety Show at Sydney Showground, Homebush.
Most exhibitors at both fairs told Industry Update they were happy with walk-up enquiries, especially on the first day which kicked off with a buzz. People were keen to be networking and doing business face to face after both Sydney and Melbourne events had been cancelled by Covid in 2020 and ’21.
At the Institute of Instrumentation, Control and Automation, Ella AverillRussell said she’d been busy networking as well as doing business at the IICA stand.
“I’ve lined up customers for our tech tours—for example, behind the scenes at a brewery and a chemical plant. I’ve even found speakers for events, too.”
The established Workplace Health and Safety event was the bigger show with 126 exhibitors while Hall 6 held about 100 modern manufacturing exhibitors. Visitors’ interest was piqued by the expo’s smart manufacturing conference and experts’ presentations on topics such as the latest tech and manufacturers’ applications, new opportunities in a ‘net-zero’ economy, and government support including training.
The sophistication of high tech exhibitors has moved up since the previous expo in 2019, partly due to multiplying options in 3D printing and the expos’ new collaborative research and universities category.
Additive manufacturing
The latest in 3D printing was promoted by a handful of exhibitors from printer, scanner and parts supplier Bilby3D and 3D Printers Online all the way up to the EOS printer for metals and polymers and Nano Dimension’s Dragonfly IV for electronic components.
Additive Australia is the distributor for EOS printer and Materialise, the suite of software which runs it to achieve design optimisation on mesh level, automated support generation, reduced data preparation time, and savings on material cost. Customers include a Brisbane orthotics maker and typical applications include tooling inserts and injection moulding components, dental and orthopaedic devices, aerospace and defence, and medical from soft helmets to reshape a baby’s head to titanium medical implants where porosity allows liquid to flow through so bone tissue can grow with the implant’s outer edges.
“Manufacturing customers are becoming more of a trend for us now,” said Kevin Hazlehurst, founder of Additive Australia. “We’re 10 years behind Europe and North America but local industry is catching up.”
The Dragonfly printer from Israeli firm Nano Dimensions gives the flexibility to create proof-of-concept prototypes for anyone wishing to produce a low volume but high mix of components – perhaps even making something different every other day.
“It’s ideal for small, lightweight components which need to be customised to fit exactly into, for example, a satellite,” said Omer Tangi, Nano Dimension’s Australia Country Manager.
“Nano Dimensions offers part of a solution to industry’s supply problems whether they are PCBs, antennae, wearable sensors or micro-fluid devices for bioscience.”
The Dragonfly prints components in up to 30 or sometimes more layers. Nano Dimensions has sold a handful of the pricy Dragonfly IVs in Australia, mainly universities and high-end researchers such as Protospace at University of Technology, Sydney (UTS), which has more than 90 machines for 3D manufacturing and claims 15 additive manufacturing technologies.
Other additive and smart manufacturing companies included Embedded Logic Solutions, Emona Additive Manufacturing and Raymax Applications. Raymax has been developing photonics and laser solutions, as well as supplying equipment, for more than 30 years. The company makes light work for industry and R&D organisations; solutions range from anti-counterfeit and security to car components, to laser cladding and atmospheric packaging.
Centres of collaboration
The group of university and collaboration centres at the expo for the first time included GPC Electronics, CSIRO Future Digital Manufacturing, Western Sydney University, and NSW Defence Innovation Network (UTS and the Defence Science and Technology Group).
Southern Strength Agile Manufacturing Network stood out as a local group of manufacturing and complementary businesses from the Greater Sydney Region where manufacturing is a primary employer. It builds capability and collaboration among members by developing trading and business streams from local, national and international opportunities.
“The network’s bigger members include ANSTO and the University of Wollongong and more typical members are SMEs,” said Greg Bullen, Medina Engineering’s Business Development Manager.
Medina Engineering itself is a 45-year-old SME specialising in computerised numerical control machining and manufacturing including four- and five-axis machining for projects of all sizes for mining, power generation, defence, rail, building products, and steel and aluminium industries.
More typical of the collaboration between tertiary and industry sectors was the Australian Cobotics Centre, a joint venture between UTS, and Swinburne and Queensland Universities of Technology.
It works with a handful of industry partners: Cook Medical, B&R Enclosures (electrical cabinetry), and industry association Weld Australia, Infrabuild (steel recycling, manufacturing and distribution), QUT spin-off Advanced Roboticsfor Manufacturing Hub and IR4 benchmark automation solutions. In its project work with these partners, ACC aims to improve collaboration between robots and humans—on the technical side, and the social and awareness side so each is aware of the other’s activities.
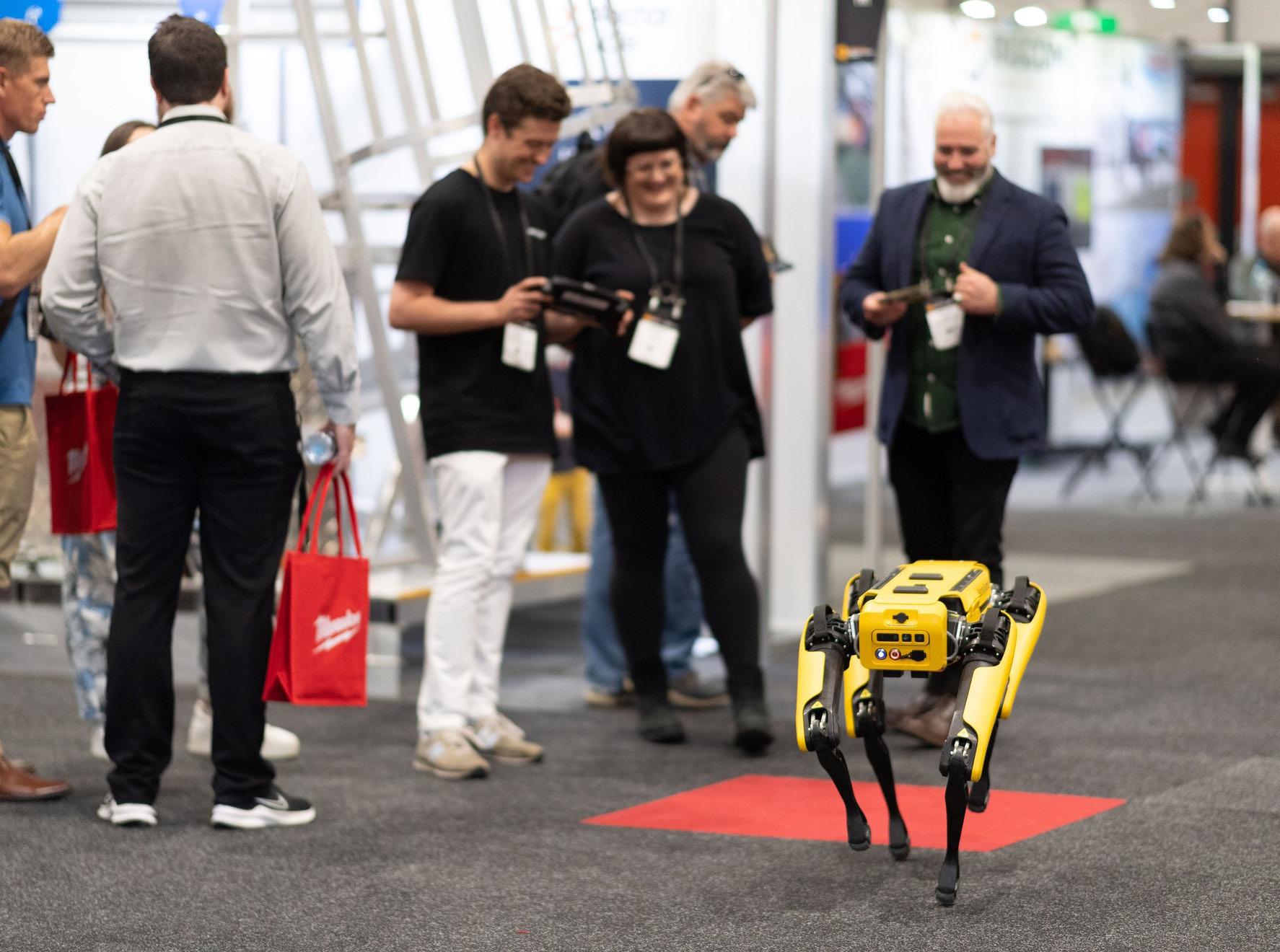
In 2023 the Workplace Health & Safety Show will be held in Brisbane on May 31 and June 1st, as well as in Sydney on 20 and 21 September. The Sydney event will also host the co-located Modern Manufacturing Expo at Sydney Showground.
Register your interest in attending by adding your name to a priority invite list by emailing mmevisitor@iecgroup. com.au




A diverse Workplace Health and Safety show
By Christine Powis

More than 120 exhibitors spruiked their wares last week at the Workplace Health and Safety Show at Sydney Showground, Homebush.
Exhibitors were of all types and sizes: from Brisbane-based family business Rehydraid, an electrolyte drink which is pitting itself against long-established international brands; up to heavy-duty majors like Milwaukee power tools and personal safety gear.
The variety of exhibitors these days has broadened as people’s awareness of wellbeing has become more holistic. Not surprisingly, this has been accelerated by the Covid experience and many firms’ desire to pitch themselves as caring employers.
Mental health focus
Among exhibitors’ stands were allied health services such as on-site psychological support from Axis, which reports strong demand from bigger companies in food and beverage manufacturing, utilities and mining.
“There’s now a heightened awareness in the general public of the importance of mental health,” said Helen Barker, Axis’ GM of Operations, “and workplaces are keen to bring people back on site.”
Axis psychologists first de-stigmatise the consultation before working with people.
“Employee Assistance Programs are really a mandatory ticking of boxes and telephone mental health sessions don’t compare with face-toface sessions,” Barker said.
Axis believes its onsite psychology services eliminate obstacles to a worker seeking assistance by enabling convenient, personal support. The service also aims to provide mental health coaching—teaching practical strategies to promote better health and lifestyle choices, and strong, respectful relationships.
To the same end, the NSW government is offering free training and coaching on workplace mental health to help employers, leaders and managers meet their duty to provide a mentally safe workplace and a more productive organisation.
Individuals, too, can get free training, much of which is supported by the Black Dog Institute.
From hydrolites to podcasts about safety at work
A small company with big aspirations, Rehydraid showcased its rehydration range of hydrolite drinks, jellies and ice blocks, which have been selling for the past few years through pharmacies.
Employers of emergency services teams and outdoor workers, local councils and manufacturers order it direct, often in bulk as a concentrate.
It’s marketed as sugarless, and using all Australian ingredients, aside from ‘better quality’ salt from New Zealand!
ForgeWorks was giving away its blueprint for improving safety at work to help businesses ‘break through the performance plateau with a successful safety strategy’.
“Many companies take the manual and do an excellent DIY safety strategy,” said Associate Director, Nathaniel Bougoure. “And others come back to us for consulting support and refining their strategy. Giving away good intellectual property does encourage people to come back for more.”
Bougoure said that further support is frequently requested for risk management, management systems and often for engaging senior leadership.
“Boards are a bit distant from the frontline or, if they get information filtered through middle management, then messages can change– say, from pointy to sanitised.”
The company develops and supports safety strategies locally for utilities and defence organisations, and internationally with Amazon. Banks such as Macquarie also rely on Forgeworks’ support regarding their asset management portfolio.
Bourgoure recommends the monthly podcast The Safety of Work by Forgeworks’ CEO Dr David Provan and the Safety Science Innovation Lab at Griffith University for the latest safety research and practical management tips.
Safework NSW also gave away its free manual, based on seven elements: commitment, consultation, risk management, reporting, worker capability, safe environment, and workers’ compensation and recovery.
The agency also advises on issues, provides templates for action plans, free health checks plus there’s a $500 rebate for businesses installing a safety item.
Medical response training and safety apps
Gory faux body parts and organs drew attention to stands held by medical response training teams. Real Response’s client list includes logistics firms and food companies such as Sanitarium.
Trainers are experienced first-responders such as paramedics or medical educators who run training both live and as synthetic simulation. They train on sites across Australia, from basic first aid to emergency response skills and advanced tactical training.
Real Response also uses virtual reality technologies to improve learning outcomes where face-to-face training is impractical, too expensive, too dangerous, or otherwise inaccessible.
Eye-catching in a completely different way were accessories by Duress in the shape of neat rings, watches and of course phones running apps.
The phone app enables location check-ins, basic ratings on location safety, alerts to either the user’s team or Duress’ 24/7 Australian monitoring centre, and emergency activation which can include live-stream video. Phoenix, a card, pairs with the app for advanced location markers.
The watch model offers similar welfare checks either requested or automatic, fall detection and heart rate monitor plus live video if needed.
This year’s major exhibition sponsor was Skytrust Intelligence System—the cloud-based management system which provides dashboard-based situational awareness, to drive compliance, due diligence and performance across business.
Next year the Workplace Health & Safety Show will be held in Brisbane on May 31 and June 1st at the Brisbane Convention and Exhibition Centre.as well as in Sydney on September 20 and 21 at Sydney Showground.
Register interest by emailing mmevisitor@iecgroup.com.au
