
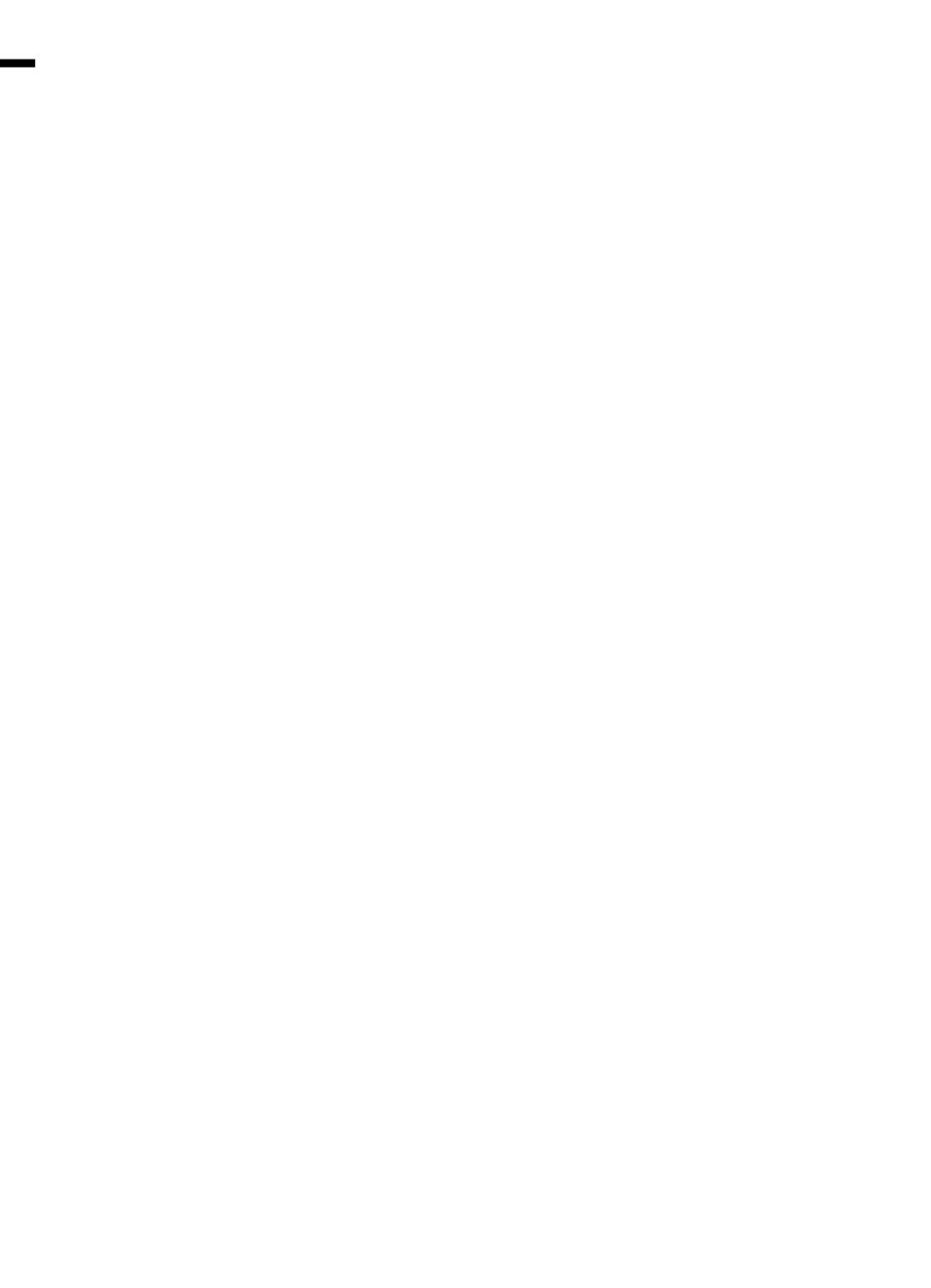
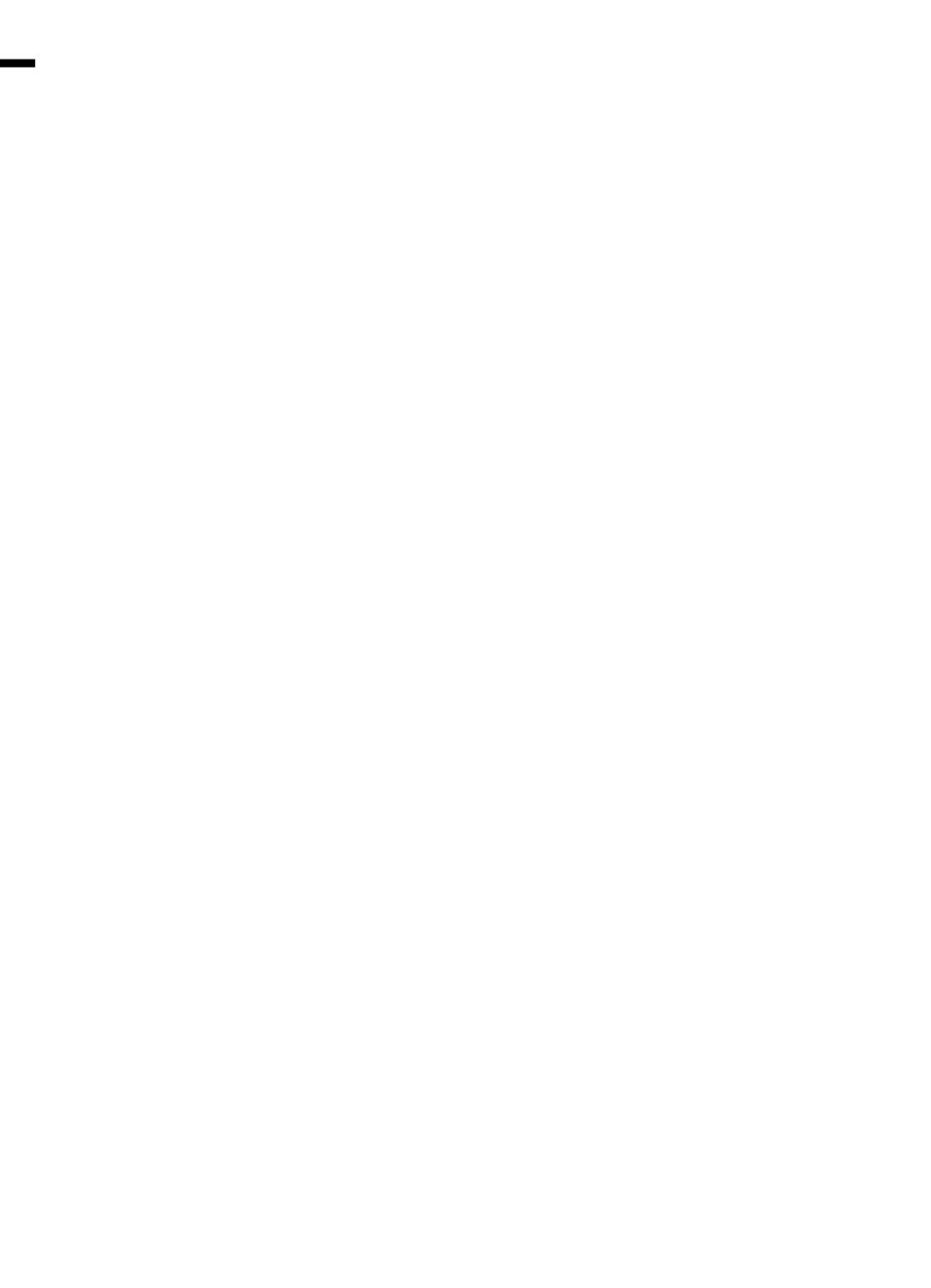
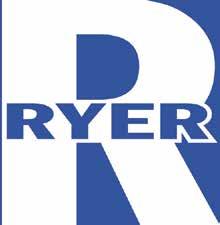
• At RYER, all our feedstocks are manufactured to the highest level of quality, with excellent batch-to-batch repeatability.
• RYER is the ONLY commercially available feedstock manufacturer to offer all five debind methods.
• RYER offers the largest material selections of any commercially available feedstock manufacturer.
• RYER offers technical support for feedstock selection, injection molding, debinding and sintering.
• A direct replacement for all current commercially available catalytic debind feedstocks
• Improved flow
• Stronger green and brown parts
• More materials available and better surface finish
• Custom scale-up factors available
• Faster cycle times
• 65°C / 150°F mold temperature
• Water Debind
• Custom scale-up factors available
• Large selection of available materials
• Solvent, Super Critical Fluid Extraction (SFE) or Thermal Debind methods
• Hundreds of materials available
• Custom scale-up factors available
Publisher & Editorial Offices
Inovar Communications Ltd
11 Park Plaza
Battlefield Enterprise Park
Shrewsbury SY1 3AF
United Kingdom
Tel: +44 (0)1743 469909 www.pim-international.com
Managing Director & Editor
Nick Williams, nick@inovar-communications.com
Group News Editor
Paul Whittaker, paul@inovar-communications.com
Advertising Sales Director
Jon Craxford
Tel: +44 (0)207 1939 749 jon@inovar-communications.com
Assistant Editors
Amelia Gregory, amelia@inovar-communications.com Emma Lawn, emma@inovar-communications.com
Assistant News Editor
Charlie Hopson-VandenBos charlie@inovar-communications.com
Digital Marketer
Mulltisa Moung, mulltisa@inovar-communications.com
Production Manager
Hugo Ribeiro, hugo@inovar-communications.com
Operations & Partnerships Manager
Merryl Le Roux, merryl@inovar-communications.com
Office & Accounts Manager
Jo Sheffield, jo@inovar-communications.com
Technical Consultant
Dr Martin McMahon
Consulting Editors
Prof Randall M German
Former Professor of Mechanical Engineering, San Diego State University, USA
Dr Yoshiyuki Kato
Kato Professional Engineer Office, Yokohama, Japan
Professor Dr Frank Petzoldt Ingenieurbüro Dr. Petzoldt, Geestland, Germany
Dr David Whittaker
DWA Consulting, Wolverhampton, UK
Bernard Williams Consultant, Shrewsbury, UK
Subscriptions
PIM International is published on a quarterly basis as either a free digital publication or via a paid print subscription. The annual print subscription charge for four issues is £150 including shipping.
Accuracy of contents
Whilst every effort has been made to ensure the accuracy of the information in this publication, the publisher accepts no responsibility for errors or omissions or for any consequences arising there from. Inovar Communications Ltd cannot be held responsible for views or claims expressed by contributors or advertisers, which are not necessarily those of the publisher.
Advertisements
Although all advertising material is expected to conform to ethical standards, inclusion in this publication does not constitute a guarantee or endorsement of the quality or value of such product or of the claims made by its manufacturer.
Reproduction, storage and usage
Single photocopies of articles may be made for personal use in accordance with national copyright laws. All rights reserved. Except as outlined above, no part of this publication may be reproduced or transmitted in any form or by any means, electronic, photocopying or otherwise, without prior permission of the publisher and copyright owner.
Design and production
Inovar Communications Ltd.
ISSN: 1753-1497 (PRINT)
ISSN: 2055-6667 (ONLINE) © 2024 Inovar Communications Ltd.
The World PM2024 Congress, held in Yokohama, Japan, proved to be the year’s essential gathering for the Powder Metallurgy and Metal Injection Moulding industries. Against a backdrop of stalling growth, particularly evident in Japan and Europe, the event emphasised resilience, adaptation and innovation as critical tools for overcoming today’s economic and geopolitical uncertainties.
A key theme in Yokohama was market diversification. With traditional sectors – such as automotive – experiencing mounting pressures and some major consumer electronics applications being phased out, new growth opportunities are emerging in aerospace, 5G technology, and foldable smartphones. Such emerging markets demonstrate MIM’s flexibility and ability to respond to evolving industry demands.
Sustainability was another primary focus. Industry leaders discussed initiatives to reduce their environmental impact, particularly through the use of recycled materials and green energy solutions for powder production and sintering processes. Sustainability is not just an ethical imperative but a strategic necessity: major customers of the MIM industry are setting increasingly stringent environmental standards, compelling MIM producers to innovate or risk being left behind.
Despite global challenges, the World PM2024 Congress showcased the MIM industry’s collective determination to drive progress. Through cutting-edge technologies, cross-industry collaboration, and an increasing focus on sustainability, the event outlined a clear path for Powder Metallurgy and MIM to navigate the complexities of modern manufacturing – all in keeping with its mantra: “Make a Better World with PM.”
Nick Williams Managing Editor
Cover image
A MIM ring watch created in celebration of Casio Watch’s 50th anniversary (Courtesy Casio Computer Co Ltd)
SIMPLIFY YOUR SINTERING
Affordable, state-of-the-art furnace designed as a total industry solution – not just for sinter-based AM, but also for PM, MIM, and other sectors that could benefit from a compact, highpurity vacuum furnace for combined debinding and sintering.
Breakthrough, patentpending furnace design features a vacuum retort and delivers parts-perbillion levels of purity
Heating elements and insulation are located outside vacuum retort so oxygen, water vapor, and binder cannot contaminate sintering environment
Ti-tested™, delivering better Ti6Al4V performance results for density, tensile strength, and elongation*
More than a dozen fans cool from 1,420°C to 200°C in <4H without watercooled walls
Airtight design and efficient cooling dramatically lower operating costs
Compact footprint and automated, vertical hood enables access to 15.8L retort
*With Ti6Al4V, the PureSinter furnace delivered higher part density — greater than 98% — than a popular, premium third-party vacuum furnace with much less power, in addition to other performance benefits. See complete PureSinter brochure for more details.
PureSinter delivers the highest quality sintered parts, on par or better than industrial furnaces with higher acquisition and operating costs. Even titanium can be easily sintered with a high degree of confidence without the complex preparations and getter materials required with other furnace. SINTERING INNOVATION
Download the brochure and see the video at teamdm.com/puresinter
53 Engineering innovation: Zimmer Group’s success in automation and Metal Injection Moulding
From pioneering early industrial gripper systems to mastering Metal Injection Moulding, Germany’s Zimmer Group is today a leader in advanced automation and manufacturing technologies. With operations in 125 countries and a workforce of 1,300, the company produces MIM parts for both internal applications and a growing portfolio of external clients.
Dr Georg Schlieper recently visited Dr Natalie Salk to learn about the company’s MIM journey, here he reports on how it has leveraged its expertise in automation to enhance efficiency across its MIM operation. >>>
63 Exploring MIM market dynamics: Highlights from the World PM2024 Congress, Yokohama
The 2024 Powder Metallurgy World Congress in Yokohama, Japan, offered an opportunity for the Metal Injection Moulding industry to come together, share market data, and explore emerging trends. The event addressed key issues such as declining sales in major regions, shifts in material demand, and the broader economic and geopolitical challenges affecting the industry. Attendees also explored strategies for innovation, market diversification, and sustainability to drive future growth.
Nick Williams shares key data and insight from this important global industry event. >>>
In September 2024, the 7 th International Conference on Powder Metallurgy and Additive Manufacturing of Titanium (PMTi2024) brought together experts from academia and industry in Madrid.
Hosted by the Universidad Carlos III, the event featured considered PM titanium’s future, with insights into cost reduction, innovative processes, and material advancements.
This article highlights key takeaways, with a particular emphasis on sinter-based processes and their industrial application. Dr Thomas Ebel presents a comprehensive review of the most notable insights. >>>
89 Reverse Engineering legacy components using filament-based metal Additive Manufacturing
Filament-based Material Extrusion (MEX), also known as Fused Filament Fabrication (FFF), combines cost efficiency with versatility, enabling the rapid prototyping of complex geometries. When used with Reverse Engineering and digital scanning technologies, could the technology play a role in the supply of discontinued legacy metal parts?
Here, Sihan Zhang, Saleh Khanjar, Srimanta Barui, Kameswara Pavan Kumar Ajjarapu, and Kunal Kate from the University of Louisville; Lauren Shackleford of the University of Kentucky; and Andrew Pierce, GE Appliances, report on the process undertaken to produce a discontinued stainless steel helical gear. >>>
99 Advertisers’ index & buyer’s guide
Discover the leading suppliers of materials and equipment for MIM, CIM and sinterbased AM, as well as part manufacturing partners and more. >>>
102 Events guide
View a list of upcoming events for the MIM, CIM & sinter-based AM industries. >>>
The PIM International newsletter is sent to several thousand industry professionals worldwide. Register today to ensure you benefit from reading the latest industry news and advances in Metal Injection Moulding, Ceramic Injection Moulding and sinter-based AM technologies.
www.pim-international.com/e-newsletter
Casio Computer Co Ltd, Tokyo, Japan, has released a metal injection moulded ring watch to celebrate Casio Watch’s 50 th anniversary. The newly developed CRW-001-1JR miniature watch is the first functional, ring-sized model produced by Casio and is around 10x smaller than a normal watch.
Metal Injection Moulding was used to manufacture the case, case back, and ring in one piece. The ring watch has an inner diameter of 20 mm and a circumference of 62.8 mm, with the company providing spacers to make it fit different-sized fingers. The sixdigit LCD displays time down to the second, and features calendar, dual time and 1/100-second stopwatch functionalities controllable through three buttons.
Metal Injection Moulding technology has been used by the watchmaking industry for many decades, establishing itself as a cost-
efficient manufacturing technology for innovative watch designs. These can range from everyday stainless steel watches to luxury, diamondclad timepieces. Ceramic Injection Moulding (CIM) is also used, with many high-value designer watchmakers adopting the technology.
Casio has used MIM before in the production of its watch cases, recently highlighting its use in the G-Shock Mudmaster watch. Here, a complex button guard MIM component was produced in stainless steel.
Citizen Watch Co was the first of the watch companies to establish an in-house Metal Injection Moulding facility in Tokyo, Japan, in 1987, for the production of parts such as stainless steel watch cases and tungsten alloy balance weights used in automatic watches.
Swatch Irony watches were also an early application for stainless steel Metal Injection Moulding watch
cases. The first MIM nickel-free 316L stainless steel Irony watch cases for Swatch came off ETA Manufacture Horlogere Suisse’s in-house MIM production line in Grenchen, Switzerland, in October 1994.
The ring watch is another example of the dominance of Metal Injection Moulding in the consumer electronics industry, with major application groups being smartphones, wearable devices, computers, etc. www.casio.com
Vertically integrated medical device contract manufacturer, Biomerics, Salt Lake City, USA, has opened a new Metal Injection Moulding (MIM) facility, including a new Centre of Excellence.
By combining MIM with its other micro metals processing capabilities, Biomerics’ vertically integrated Micro Metals Division is now able to offer a full range of highly specialised, complex interventional medical devices and components. This suite of offerings includes the intricate components used in surgical robotics and minimally invasive surgical device applications.
“This investment in MIM reflects our thirty-year pursuit of innovation
and manufacturing excellence,” stated Travis Sessions, Chief Executive Officer of Biomerics. “I’m thrilled to see our vertical integration on full display throughout our growing global operations, particularly in our Micro Metals Division. This investment also says a lot about the performance of our growing metals teams, the markets we manufacture for and our commitment to delivering the latest innovations in the medical device manufacturing industry. Our new Metal Injection Moulding Center of Excellence will continue to fuel our growth with best-in-class speed-tomarket capabilities.”
Metal Injection Moulding is a proven technology that is routinely
Biomerics has opened a new vertically integrated MIM operation for the production of medical device components (Courtesy Biomerics)
Noritsu Koki Co, Ltd, headquartered in Tokyo, Japan, has announced plans to separate the two core businesses of its subsidiary Teibow Co Ltd, a producer of metal injection moulded parts and nibs for writing instruments. The company will establish the Metal Injection Moulding business as a separate subsidiary under the name Hamamatsu Metal Works Co, Ltd. This, and the remaining pen
nib business (Teibow Co Ltd), will function under the scope of Teibow Holdings Co, Ltd.
In recent years, Teibow has seen growth potential in its MIM operation, with investments in management resources and the establishment of a new factory for mass-producing MIM components.
“Under these circumstances, our group believes that making the
used for medical device manufacturing, capable of producing high-volume, highly repeatable runs of metal components requiring complex geometries, tight tolerances and demanding performance. It is able to overcome the design limitations of other metal fabrication processes and can produce extremely thin-walled, unique-shaped and micro-sized components.
The company stated that the high production efficiency of MIM lowers operational costs while consistently producing high-quality parts. MIM is also an ideal process for components that need to maintain the high-performance mechanical properties of metals, such as high density, homogeneous microstructure, corrosion resistance, magnetic permeability or hermetic sealing functionality. Unlike other metal casting processes, MIM maintains the strength of the wrought metal and achieves 95-99% theoretical density.
“Metal Injection Moulding is a valuable enhancement to our metals manufacturing capabilities,” stated Arun Mohan, president of Biomerics’ Micro Metals Division. “Investing in innovative manufacturing technologies like MIM enables us to better serve our global customers. This exciting addition reflects our ongoing commitment to providing best-inclass services and capabilities that meet the evolving design and manufacturing needs of our partners.”
www.biomerics.com
pen nib business and MIM business independent will strengthen the competitiveness and structure of both businesses, as well as speed up decision-making and improve the efficiency of resource allocation,” the company stated in a press release. “We decided on the company split and joint stock transfer in the judgment that this would lead to an increase in the corporate value of the company.”
The new Hamamatsu Metal Works MIM business is expected to become an independent company on April 1, 2025.
www.noritsu.co.jp www.teibow.co.jp
At Kymera International, we’re not just a powder provider; we’re your strategic partner in the world of specialty material solutions and additive manufacturing.
At Kymera International, we’re not just a powder provider; we’re your strategic partner in the world of specialty material solutions and additive manufacturing.
At Kymera International, we’re driving the future of specialty metals and advanced coatings for powder injection molding applications. Our industry-leading materials and innovative solutions enable precision, reliability, and performance across multiple sectors, from automotive to aerospace.
At Kymera International, we’re driving the future of specialty metals and advanced coatings for powder injection molding applications. Our industry-leading materials and innovative solutions enable precision, reliability, and performance across multiple sectors, from automotive to aerospace.
With our expert team and global presence, we empower manufacturers to push the limits of what's possible. Partner with Kymera and experience unparalleled quality, custom alloy solutions, and superior customer support. Contact us today to revolutionize your projects www.kymerainternational.cominfo@kymerainternational.com
With our expert team and global presence, we empower manufacturers to push the limits of what's possible. Partner with Kymera and experience unparalleled quality, custom alloy solutions, and superior customer support. Contact us today to revolutionize your projects
www.kymerainternational.cominfo@kymerainternational.com
Zoltrix Material International Ltd, one of China’s leading Metal Injection Moulding (MIM) companies, is reported to be using Binder Jetting to additively manufacture hundreds of thousands of metal components for consumer electronic applications. At this year’s Formnext, HP showcased several end-use parts manufactured by Zoltrix using HP’s Metal Jet technology. The parts, made from 316L and 17-4PH stainless steel, included smartwatch cases post-processed to achieve a ‘best-inclass quality.’
Asia’s consumer electronics sector has been a key target market for Binder Jetting technology suppliers, with companies such as Apple and Samsung using huge volumes of highly complex precision metal components. It was the adoption of MIM technology for key applications by Apple more than a decade ago that led to a surge in growth for the MIM industry, and there is an expectation that Binder Jetting will follow the same path.
According to information displayed with the part, Zoltrix delivers ‘end-
Isostatic Toll Services Bilbao SL (ITS Bilbao), Spain, has announced that it intends to commission its fourth MEGA Hot Isostatic Pressing (HIP) unit within the next three years and, by Q2 2025, to commission a fully molybdenum vacuum heat treatment furnace from TAV. Its first heat treatment unit, the 120 x 160 x 120 cm furnace will feature a maximum vacuum of 10-5 mbar, making it suit-
able for titanium. This additional heat treatment capability will enable ITS Bilbao to offer a combined MEGA HIP and MEGA Heat Treatment service to its HIP customers.
ITS Bilbao ran the first cycle of its MEGA HIP unit in 2019. Demand for toll HIP services surged following Covid pandemic, prompting the company to decide, in Q1 2022, to double its existing
to-end mass production solutions with HP Metal Jet for customers in the consumer electronics, industrial and medical device sectors.’ It was stated that the primary benefits of Binder Jetting for Zoltrix’s customers are cost and weight reduction, rapid production development and optimisation, and greater design freedom – including reduced material usage.
According to a video published by Chinese AM media platform Panda3dprinting , Zoltrix has been using HPs Metal Jet technology since 2019 and has since shipped ‘hundreds of thousands’ of AM parts.
The post-processing of MIM and BJT parts at Zoltrix is a key part of its success, and after debinding and sintering, processes such as Hot Isostatic Pressing (HIP), sandblasting, polishing and PVD surface finishing are routinely used. The company is also reported to have more than 500 CNC machines for the post-sintering machining of parts.
Zoltrix’s Technology and Application Design Center is based in Guangzhou, whilst its toolmaking and MIM parts manufacturing operations are located in a state-of-the art plant in Southern China. It is owned by CN Innovations Holdings Limited (CNI), headquartered in Hong Kong which has main production sites spread across Mainland China, including Shenzhen, Guangzhou, Suzhou, Zhejiang and Shanghai. CNI has over 11,000 employees and has frequently appeared on the Apple Suppliers List in the past.
www.zoltrix-intl.com www.hp.com
capacity. A MEGA HIP unit, identical to the original, was commissioned in the following year.
Over the following twelve months, demand for the second unit exceeded its capacity, leading to the installation of a third MEGA HIP unit in 2024. Set to be commissioned in 2025, the unit is identical to the previous, with a Ø1088 x 2570 mm loadable zone corresponding to 2.4 m 3, and an increased maximum working pressure of up to 138 MPa (20,000 psi).
www.isostatictollservices.com
Experience significantly improved printability with Osprey® HWTS 50. This new lean hot-work tool steel powder reduces many of the challenges customers face in hot-work applications. Characterized by lower carbon content it offers higher thermal conductivity together with optimized resistance to tempering and thermal fatigue. With its alloy design philosophy, Sandvik contributes to the shift towards a more sustainable future in several ways.
Learn more and explore how Osprey® HWTS 50 creates opportunities for your business.
Kymera International, a specialty materials company headquartered in Raleigh, North Carolina, USA, has received a private credit loan of $775 million to refinance its existing debt and provide capital for add-on acquisitions, including its recent acquisition of Fiven, reports PitchBook, a financial data and software provider.
According to market sources, HPS provided the entirety of the facility and syndicated a small portion of the debt to other lenders. The facility included a term loan as well
as a delayed-draw term loan. The company also has a separate AssetBased Lending (ABL) facility held by KeyBanc and M&T.
Piper Sandler and Goldman Sachs served as financial advisors on the transaction, which was reported to have been dual tracked between the syndicated market and the private credit market.
“When you have a good credit like Kymera, with a history of growth and strong free cash flow conversion, you have financing options. Private credit has raised so much capital
3D Lab sp zoo, based in Warsaw, Poland, has been granted a USA patent for its ‘Method and Device for Producing Heavy Metal Powders by Ultrasonic Atomization’ innovation. The company has also been granted a Chinese patent for the technology incorporated into its ATO atomisers under ‘A Method for Evacuation of Powder Produced by Ultrasonic Atomization and
a Device for Implementing This Method.’
The patented technology is at the core of the company’s ATO series of ultrasonic metal atomisers. This technology is said to produce high-quality spherical metal powders with precise control over particle size, excellent flowability, and low oxygen content. These characteristics are ideal for
3D Lab has been granted patents in both USA and China for its atomisation process (Courtesy 3D Lab)
that it does create a viable alternative to the syndicated market, a dynamic that benefits the issuers,”
Adam Shebitz, Palladium’s Head of Industrials, told PitchBook LCD.
Palladium first invested in Kymera in 2018, and since the buyout, the company’s EBITDA has reportedly tripled.
The company announced its agreement to acquire silicon carbide developer Fiven from OpenGate Capital on June 4.
“Given the fact that Kymera had an acquisition under LOI, we wanted a timely close and we wanted to avoid market flex on terms,” added Shebitz.
www.kymerainternational.com
Metal Injection Moulding, Additive Manufacturing and other industrial applications.
Commenting on the USA patent, Jakub Rozpendowski, CEO of 3D Lab, said, “We are proud to add this USA patent to our rapidly growing portfolio of global intellectual property. Our patented technologies drive our mission to provide advanced and versatile solutions for metal powder production, ensuring superior material quality and accelerating material innovations. This patent is a significant milestone in our journey, reflecting the dedication and innovative spirit of our team.”
The ATO Lab Plus is an advanced ultrasonic metal atomiser designed for lab-scale production of metal powders. Ideal for research and production environments, it enables the efficient and cost-effective production of reactive and nonreactive metal powders.
The atomiser has a modular construction, allowing for easy expansion of powder production capabilities through the use of the interchangeable modules. The device has advanced safety systems and automatic features, offering a versatile solution for producing metal powder.
www.metalatomizer.com
These two binder systems have excellent characteristics during the production process and combine attractive prices with worldwide availability
High performance as well for the 3D-Printing process based on the water soluble binder system
HP has announced a number of additions to its Additive Manufacturing solutions portfolio and partnerships aimed at reducing cost, scaling production and accelerating the adoption of metal AM.
The company announced new configurations for its HP Metal Jet S100 platform, all intended to enhance quality, repeatability, speed, and reliability across a broader range of production needs. These updates are expected to enable research centres, OEMs, laboratories, and startups to explore metal Binder Jetting at reduced adoption costs.
In parallel, HP is collaborating with Volkmann and Sinterzone to develop respective configurations for the HP S100 platform.
Collaborations
HP has also been taking part in collaborations with ArcelorMittal and Eaton. With ArcelorMittal, HP has combined its own metal Additive Manufacturing experience with ArcelorMittal’s sustainable steel in an effort to reduce production costs,
HP announced new configurations for its Metal Jet S100 Additive Manufacturing platform (Courtesy HP)
expand material options, and drive broader adoption of AM steel in key industries like automotive.
Through its collaboration with Eaton, HP has been working to support testing and validation of advancements in it its Metal Jet Additive Manufacturing solution. Thus far, the companies have worked on nitrogen-enhanced sintering, which is said to improve the mechanical properties of 316L parts, and the S100 Powder Processing Solution, said to reduce cost and improve yield during Binder Jetting. Together, the companies will evaluate the technology’s potential for high-performance applications, ensuring it meets the industry’s demands.
Eric Johnson, Senior Manager of Additive Manufacturing at Eaton Research Labs, added, “Partnering with HP on this programme has been an exciting opportunity to advance the manufacturing readiness of this technology and develop a costeffective process that meets the
Lithoz GmbH, based in Vienna, Austria, launched the CeraFab System S320 at Formnext 2024. With a build platform 5x larger than its industry-proven CeraFab System S65, the S320 is tailored for the high-capacity production of mid-sized technical ceramic components.
The new ceramic Additive Manufacturing machine is part of Lithoz’s extensive lithographybased ceramic manufacturing (LCM) platform. Positioned as a
solution for industries scaling up to mid-sized ceramic serial part production, the S320 is intended to complement the CeraFab System S65.
The CeraFab System S320, with its build volume of 246 x 130 x 320 mm, boosts production capacity and offers the largest build volume of all Lithoz LCM Additive Manufacturing machines. It features a 4K projection system with a lateral resolution of 60 µm. www.lithoz.com
requirements for our most demanding applications.”
In collaboration with AMES, located in Barcelona, Spain, HP is launching the HP Metal Jet Adoption Center. This state-of-the-art facility combines HP’s AM technology with AMES’ metallurgical expertise to facilitate a more efficient transition from prototyping to full-scale metal production. The centre will offer a range of services, application development, and process optimisation to support its European customers.
The Leading Minds Consortium brings together industry leaders like 3D Systems, Ansys, EOS, HP, Materialise, Nikon, SLM, Renishaw, Stratasys, and Trumpf, with the goal of overcoming barriers such as cost, expertise, and system integration, making largescale industrial AM more accessible. www.hp.com
The CeraFab System S320 has a build platform five times larger than the company’s CeraFab System S65 (Courtesy Lithoz)
Inmatec Technologies GmbH, a producer of ceramic feedstocks based in Rheinbach, Germany, has announced changes to its management structure with the appointment of Stefan Weiwadel as its new Managing Director and Sales Director. It was stated that Dr Markus Zwick, who has been Director of Operations for two and a half years, has become an authorised officer and forms the new company management together with Weiwadel.
It was added that the previous Managing Director, Dr Moritz von Witzleben, will continue to contribute his vast expertise and valuable experience to the company through a number of new activities. Dr Karin Hajek, the long-standing Sales Director, is entering her retirement but will continue to work for the company as an advisor and to ensure a seamless handover.
Weiwadel has a wealth of management experience and profound knowledge from many years as a leading executive in the materials industry. In addition to Germany and Switzerland, he also worked in South East Asia and Oceania.
“Together with our ambitious team, I am committed to further strengthening Inmatec’s leading position in the ceramic feedstock market. We will continue to reinforce our role as the renowned experts in ceramic
injection moulding and carry this innovative technology out into the world,” said Weiwadel.
With the appointment of Dr Zwick as an authorised officer, Inmatec is closely linking the executive level with the operational business. As Director of Operations he holds one of the key positions in the company. By being granted power of attorney, Dr Zwick now also has official legacy to represent Inmatec Technologies and, together with Weiwadel, forms the new company management.
“Together, we will continuously develop the company, as well as its products and services, and continue to operate as a stable, reliable partner on the market for our valued customers also in the future,” stated Dr Zwick.
With the new company management, Inmatec emphasised the importance of agile business leadership and efficient decision-making, underlining its ambition to continue its development process and further strengthen its position as a key player in the field of ceramic injection moulding.
With a strong team and a clear vision for the future, Inmatec stated that it is ideally set up to continue providing innovative solutions for its customers, while also setting benchmarks in the materials industry.
www.inmatec-gmbh.com
Inmatec has announced that Stefan Weiwadel (right) and Dr Markus Zwick will lead the company (Courtesy Inmatec Technologies GmbH)
The International Conference on Injection Moulding of Metals, Ceramics and Carbides (MIM2025) is scheduled to take place February 24-26, 2025, in Costa Mesa, California, USA. At this year’s event, it has been announced that the important contribution that Professor Randall M German has made to Powder Metallurgy and Powder Injection Moulding research will be recognised.
After completing his bachelor’s degree in material science and engineering at San José State University, German began his PM industry career at Battelle Lab, Columbus, Ohio, prior to joining Sandia National Labs (SNL). He obtained his master’s degree in metallurgical engineering from The Ohio State University and his PhD in engineering at the University of
California – Davis before taking a director of research position at Mott Corporation, Farmington, Connecticut. Professor German’s six decades of research, including metals, ceramics, carbides, and composites, has influenced countless students, researchers, and collaborators worldwide. MIM2025 will honour his legacy by showcasing the ground-breaking developments in PM and PIM inspired by, or conducted with, Professor German.
MIM2025 is organised by the Metal Powder Industries Federation (MPIF), as well as the Metal Injection Moulding Association (MIMA) and global PIM experts. Those interested in attending can register at a discounted rate until January 24, 2025.
MIM2025 will recognise the important contribution that Professor Randall M German has made to Powder Metallurgy and Powder Injection Moulding research (Courtesy MPIF)
Randall German has been a friend and consulting editor of PIM International magazine since its first issue in 2007. He has authored articles for PIM International , Metal AM and PM Review www.mpif.org
Krahn Ceramics is expanding its production capacities at its facility in Hamburg, Germany, in response to increasing demand and a surge in new projects. The company has installed a third line for the production of Ceramic Injection Moulding compounds.
“The installation of the new production line is a significant step to meet growing market demands. It enables us to better cater to higher volumes and specific customer requirements,” explained Dr Stefan Stolz, Managing Director of Krahn Ceramics.
Krahn Ceramics has more than thirty years of experience in the field of technical ceramics and operates worldwide. As part of the family-owned Otto Krahn Group, it can draw on a comprehensive network in Europe, the USA and Asia. In addition to a technical centre for developing customer-specific solutions, the company has its own production line allowing it to accompany customers throughout all process stages, from the raw material to the finished component.
www.krahn-ceramics.com
Krahn Ceramics is expanding its production capacities at its facility in Hamburg (Courtesy Krahn Ceramics)
Forward AM Technologies GmbH is reported to have entered insolvency proceedings. The measure was said to be an attempt to restructure and move the company towards a sustainable future. Forward AM was keen to note that its local entities have not filed for insolvency and will continue business as usual, focusing on manufacturing and distribution of materials. Tobias Wahl, a partner at Anchor Rechtsanwälte, was appointed as the preliminary insolvency administrator.
Forward AM, the former Additive Manufacturing business of BASF, underwent a management buyout in
July 2024. The acquisition included Forward AM’s materials and solutions, as well as its Sculpteo service business. The company offers a range of Ultrafuse metal filaments, including 17-4 PH and 316L stainless steels.
“We are confident that, together with our partners and investors, we can lay the groundwork for a successful future,” stated CEO Martin Back. “Our focus remains on providing innovative solutions to the success of our customers and further strengthen our leading position in the field of 3D printing solutions.” www.forward-am.com
An EU project coordinated by the European Powder Metallurgy Association (EPMA) has been granted €7.3 million. The funding, divided between thirteen partners under the REPTiS project, is intended to support the responsible extraction and processing of titanium and other primary raw materials for sourcing EU industrial value chains and strategic sectors. In addition to the EPMA, key participants include Ukrainian titanium producer Velta and global aerospace manufacturer GKN Aerospace.
Together, the companies are required to use the grant to demonstrate the feasibility of titanium extraction, processing, and utilisation within the EU through a partnership with Ukraine. The majority of the funding is reportedly designated for Velta and the EPMA; other recipients include companies specialising in Metal Injection Moulding and Additive Manufacturing, research centres, and universities. However, the current allocation of funding does not cover the entire €7.3 million budget.
The collaboration will focus on areas such as energy efficiency and environmental impact, titanium powder production and final product manufacturing. A life cycle assessment will be carried out from the extraction of raw materials to the final products in order to evaluate the differences between the methods used in the REPTiS project and conventional practices.
The project is funded under the EU’s Horizon Europe programme and is scheduled to run for four years, with a planned end date of August 31, 2028.
european-union.europa.eu www.epma.com www.velta.us
Regardless of the complexity of your custom application and formulation, it remains standard for us with our quality systems, technical support, and two proprietary binding systems.
We ensure 100% batch-to-batch consistency, a wide range of alloys, and 36 years of supplying MIM feedstocks for mission-critical parts.
Advanced Metalworking Practices (AMP) manufactures and supplies a wide range of both standard and custom-configured MIM feedstocks for your application. Contact Chris Chapman at cchapman@ampmim.com or 724-396-3663.
Scan the QR code or click here to view our current list of alloys www.ampmim.com/resources
Continuum Powders hosted the grand opening of its global headquarters and manufacturing facility in Houston, Texas, USA, on December 5. Reported to be North America’s largest sustainable metal powder production facility, the company planned to offer guests the chance to see the company’s lowcarbon production methods firsthand.
The completion of the Houston facility is said to reflect the company’s commitment to environmental responsibility, with the entire building operating as a green manufacturing centre. The site is also pursuing green certification goals and is designed to maximise energy efficiency through renewable energy usage and recycling initiatives.
Continuum also stated that the opening of the new facility marks a significant step forward in delivering sustainable solutions that meet the demands of a rapidly evolving industrial landscape. With increased production capacity and multiple US locations, the company is now positioned to deliver products faster at reduced shipping costs, enhancing
Rob Higby, CEO of Continuum Powders, and Rizk Ghafari, COO of Continuum Powders (Courtesy Continuum Powders)
supply chain resilience for customers.
“Our new Houston facility not only expands our production capabilities but also allows us to scale our mission of decarbonising the manufacturing industry,” said Rob Higby, CEO of Continuum Powders. “We are committed to providing high-quality, cost-competitive metal powders while minimising environmental impact. Our technology represents a distinct advantage in the market, offering sustainable solutions that align with the needs of forward-thinking industries.”
The facility features Continuum’s proprietary Greyhound M2P (melt-topowder) plasma atomisation process, which enables the repurposing of alloyed metal waste-stream products into high-quality metal powder in a
single step. By enabling a cradleto-cradle process, the platform can reduce the need for transportation, product handling, primary melting, and extensive long bar processing operations, while also minimising the environmental impact by reducing the mining of elemental metal resources.
“Houston represents a leap forward in our operational efficiency and sustainability efforts,” said Rizk Ghafari, COO of Continuum Powders. “By combining state-of-the-art technology with our commitment to decarbonisation, we are not only supporting our customers’ needs but also setting a new benchmark for responsible manufacturing in the industry.”
www.continuumpowders.com
Arburg GmbH & Co KG, headquartered in Lossburg, Germany, has received another Gold Medal from Ecovadis, maintaining its position as one of the world’s most sustainable industrial companies in 2024. The award evaluates four key areas: environmental impact; sustainable procurement; ethics; and labour and human rights.
Arburg improved its performance across all categories, achieving a score of 78 points – a result that places it in the top 5% of more than 100,000 companies evaluated by Ecovadis.
“We are very proud to have once again been awarded an Ecovadis Gold Medal,” stated Managing Partner Michael Hehl, responsible for Premises Development and Spokesperson for the Management Team. “This is a great result for our sustainability activities. Not only does it prove that we are doing very well with our arburgGREENworld programme, but also that we are continuously improving.”
“Sustainability is firmly rooted in the DNA of our family business,” addded Managing Partner Juliane Hehl, who is responsible for Global Marketing and Business Development. “That’s why we have always invested a great deal in the areas of sustainability and resource conservation, and on reducing our carbon footprint.”
“This year, we also published a report in accordance with Global Reporting Initiative (GRI) Standards, enabling the extensive activities of our company to be compared internationally,” continued Juliane Hehl. “This is an aspect that will continue to gain in importance in the future.”
Arburg reaffirmed its commitment to achieving net-zero greenhouse gas emissions along its entire value chain by 2050. In the shorter term, the company aims to reduce absolute greenhouse gas emissions by 42% in Scopes 1 and 2 and by 25% in Scope 3 by 2030, followed by a long-term reduction of 90% in Scopes 1, 2 and 3 by 2050.
Michael Hehl added, “For years now, our Arburg Sustainability Report has been providing an overview of all arburgGREENworld topics alongside a host of interesting facts and figures. With our climate strategy, we are pursuing greenhouse gas reduction targets validated by the Science Based Targets Initiative (SBTi).”
www.arburg.com
3DCeram Sinto, Bonnac-La-Côte, France, has announced that James Cook University (JCU), Townsville, Australia, has upgraded its C100 Easy Lab to the more advanced C100 Easy Fab ceramic Additive Manufacturing machine.Whilst the JCU has used the C100 Easy Lab in research and numerous successful projects, the decision to upgrade was undertaken to support the growing number of industrial partnerships and the need for more complex, scalable solutions.
“When I was looking for 3D printing technology, especially [stereolithography], there were basically three players in the market,” explained Elsa Antunes, Senior Lecturer at JCU. “There is one player in the market that has basically the same quality as 3DCeram, but I was not just looking for a machine, I was looking for a partnership, and for a relationship, it takes more than the 3D printing. I found when I met the 3DCeram people I found an instant connection, and I could see we were building a partnership for life.”
“The transition to the C100 Easy Fab represents more than just an improvement – it’s a move forward in 3D printing capabilities,” 3DCeram Sinto stated in a press release. “This upgrade addresses the specific needs of industrial applications, enabling JCU to tackle more ambitious projects and drive innovation across various sectors.”
One project the JCU is focusing on is the restoration of the coral reef. Additive Manufacturing allows engineers to design parts with a similar structure to the reef with customised material properties. Because ceramics are inert, there is no negative environmental impact.
The C100 Easy Fab is the smaller version of the ceramics Additive Manufacturing machine developed by 3DCeram, marketed to universities and R&D centres with a build platform of 100 x 100 x 150 cm. The size of the C100 Easy Fab supports open parameters in the production of parts, whilst making the machine more accessible to users with reduced mobility.
Powder Metallurgy parts maker AMES, headquartered in Barcelona, Spain, has opened an HP Metal Jet Adoption Centre for the EMEA region at its Barcelona factory. The collabo -
ration with HP was announced at this year’s Formnext.
The state-of-the-art facility combines HP’s expertise in metal Binder Jetting technology with
AMES has opened an HP Metal Jet Adoption Centre at its Barcelona facility (Courtesy AMES)
James Cook University has added a C100 Easy Fab ceramic AM machine to support its ongoing research projects (Courtesy 3DCeram Sinto)
3DCeram Sinto offers a variety of services tailored to meet the needs of its customers. Its teams and partners are equipped to perform upgrades, routine maintenance and provide technical assistance on site regardless of location. Additionally, the company will provide comprehensive training covering any new features after upgrade as well as best practices and tips for machine use and maintenance.
www.3dceram.com www.jcu.edu.au
AMES’ detailed knowledge of Press and Sinter Powder Metallurgy component production. It is expected to be used to facilitate a more efficient transition from prototyping to full-scale metal parts production.
“We are thrilled to adopt the Metal Binder Jetting technology as an alternative method for the mass production of complex-shape components, expanding the limits of Powder Metallurgy to new applications out of the traditional Press & Sinter tech,” the company stated on LinkedIn.
The centre aims to accelerate the penetration of metal Additive Manufacturing technology across all industries. It will offer a range of services, application development, and process optimisation to support European customers in quickly advancing production goals.
www.ames-sintering.com www.hp.com
Then we could be your match.
With our materials experts, you are in the best of hands. Not only are we passionate of what we are doing, we also bring 30 years of experience in metal powder injection molding to the table.
Your vision is our incentive.
Materials and solutions from Schunk are advancing industries all over the world.
As an expert manufacturer of complex MIM components, we stand for exceptional service, the highest quality and enthusiasm for what we do. In close cooperation with you, we develop innovative and customized solutions for your business.
Rely on our expertise in molding processes such as
> metal injection molding
> graphite injection molding
> axial pressing
EN9100, IATF16949, ISO9001, ISO14001, ISO 50001 certified
Feel free to challenge us.
Schunk Sintermetalltechnik GmbH
Roßtrappenstraße 62 06502 Thale, Germany
+49 3947 7 1560
At thorsten.klein@schunk-group.com schunk-mobility.com
Kyhe Technology (Ningbo) Co Ltd, based in Ningbo, China, is a newly formed company within the titanium alloy sector focused on providing cheaper, more sustainable materials to customers in industries such as aerospace, automotive, consumer electronics, and renewable energy using advanced recycling technologies and proprietary processes.
Kyhe Tech reports that it operates under a framework of sustainability and responsible manufacturing. Its 9,800 m 2 facility has ESG certification, integrating environmental, social, and governance principles into its operations. Additionally, the company is certified under the Global Recycled Standard (GRS).
By sourcing recycled titanium and minimising energy-intensive processes, the company has reported having achieved significant reductions in greenhouse gas emissions and waste generation.
DH-S titanium recycled powders
Kyhe Tech uses a dehydrogenation spheroidal (DH-S) technology for producing titanium alloy powders. Unlike conventional atomisation methods, the use of recycling and reprocessing titanium materials is said to make DH-S a more costeffective and sustainable option. The powders produced are suitable to Additive Manufacturing, Metal Injection Moulding, and coating processes.
DH-S technology is said to offer advantages that differentiate it from traditional Electron Beam Inert Gas Atomisation (EIGA) methods. By accommodating a wide range of raw materials (e.g. titanium alloy scrap, CNC machining chips, and sponge titanium fragments), the DH-S process reduces dependency on virgin resources and significantly lowers production costs.
The powders produced are said to exhibit good mechanical properties - including high tensile strength and fatigue resistance - making them well suited to demanding applications in aerospace, automotive, and medical industries. The DH-S process achieves a reported 60% cost reduction compared to EIGA powders, enabling customers to access premium materials at lower prices. With a single-batch yield rate of approximately 95%, the process minimises material waste while maximising yield. www.kyhe.tech
Mebus MIM-Technik, based in Neuhausen, Germany, has been acquired by the Acrotec Group’s Medtech division, headquartered in Develier, Switzerland. Founded almost twenty years ago by Michael Mebus, Mebus MIM-Technik has a particular focus and expertise in the design and production of small, complex metal and ceramic injection moulded parts with very tight tolerances.
Certified according to DIN EN ISO 13485:2016, the company serves as a strategic supplier to leading medical technology companies. Its products include small, single-use high-end surgical products such as forceps for laparoscopic and endoscopic instruments, components for waterjet surgery, or screws for orthodontic treatment. In addition, customers include companies in the mechanical
engineering, aerospace and other microtechnology industries.
“The acquisition of Mebus is a perfect fit for us to expand Acrotec Medtech’s skills with real experts in their field,” stated Sébastien Virtel, CEO of the Medtech division of the Acrotec Group. “The level of mastery of this company’s MIM and CIM injection technologies allows us to accelerate our development in robotic surgery and endoscopy with complex single-use components, in perfect complementarity with our companies active in precision machining.“
Michael Mebus, CEO of Mebus, added “At a time when the question of my succession is being raised, it is a great opportunity to join a group that, thanks to its wide range of products and skills, remarkably complements Mebus as a holistic strategic partner
Mebus MIM-Technik specialises in small, complex parts with tight tolerances (Courtesy Mebus MIM-Technik)
for its development. I would like to thank my team, our customers and our partners for all the progress they have made, with the deep conviction that this new step will give us additional resources and offer us exceptional synergies to conquer new markets.”
www.mebus-mimtechnik.de www.acrotec-medtech.com
Amazemet Sp Zoo, based in Warsaw, Poland, introduced its new Powder2Powder (P2P) atomisation machine at Formnext 2024. The P2P system is reported to provide a versatile solution for recycling metal powders, and manufacturing custom pre-alloy powders directly from powder feedstock. The technology combines plasma processing and ultrasonic atomisation to transform irregular or oversized particles into highly spherical, satellite-free powders optimised for Additive Manufacturing. Unlike plasma spheroidisation, the P2P technology allows powder size to be independent of the initial feedstock, reportedly making it the only technology capable of direct atomisation of pulverised titanium feedstock.
“The Powder2Powder system goes beyond recycling,” explains Łukasz
Żrodowski, inventor and CEO of Amazemet. ”It gives manufacturers the ability to customise powder compositions, improve powder sphericity, and optimise particle size distribution, solving critical issues in the AM industry.”
Extensive trials using +200 µm oversize and irregular Ti alloy powders have reportedly shown exceptional results with the P2P system. Operating at a frequency of 40 kHz, the system consistently achieved a powder morphology with an aspect ratio (D50) exceeding 0.95. The particle size distribution (PSD) was precisely controlled, producing powders with D90 < 80 µm and yielding particles <63 µm and ≥80%. Nearly 97% of the resulting powder was suitable for AM processes, including Laser Beam Powder Bed Fusion (PBF-LB), Directed Energy
Guangzhou Guangya Messe Frankfurt Co Ltd has announced that Formnext + PM South China will be rebranded as Formnext Asia Shenzhen for its next iteration, scheduled for August 26–28, 2025. Formnext Asia Shenzhen will follow the model of the original
Formnext, showcasing products and technologies across the entire Additive Manufacturing process chain, from pre- to post-production. Alongside AM equipment, the exhibition aims to bring together suppliers of raw materials, post-processing tech -
Powder2Powder (P2P) technology combines plasma processing and ultrasonic atomisation to transform irregular or oversized particles into highly spherical, satellite-free powders
Deposition (DED), and Electron Beam Powder Bed Fusion (PBF-EB), highlighting the machine’s potential to enhance sustainability in metal powder production.
Additionally, the P2P system can process blends of elemental powders, creating pre-alloyed materials tailored to exact chemical compositions. This capability makes it invaluable for both research and industrial applications. Tests conducted with Ti and 10% wt. Mo elemental powders showed that both refractory elements formed homogeneous alloy powders during processing. Set for release in Q1 2025, this patented technology addresses two critical challenges in the AM industry – upcycling of powder waste and custom powder production – delivering advanced functionality that surpasses traditional recycling methods. powdertopowder.amazemet.com
nologies, inspection equipment, AM solutions, services and more. This enables visitors to source core equipment and essential supporting technologies.
The 2025 edition will also expand beyond its existing product coverage to include a wider range of advanced manufacturing solutions, including digital production, automation and precision forming. www.formnext-shenzhen.com
Sweden’s Sandvik AB has introduced Osprey HWTS 50, a hot-work tool steel powder designed for enhanced manufacturability.
Primarily developed for Laser Beam Powder Bed Fusion (PBF-
Sandvik AB has introduced Osprey HWTS 50, a hot-work tool steel powder designed for enhanced manufacturability (Courtesy Sandvik)
LB) Additive Manufacturing, it is also well-suited for Hot Isostatic Pressing (HIP) and Metal Injection Moulding (MIM).
The tempering and thermal fatigue resistance, as well as thermal conductivity of Osprey HWTS 50, are improved when compared with conventional H-class hot work tool steels. These advanced properties are intended to effectively address many common challenges in hot-work applications within general engineering, stated Sandvik.
Osprey HWTS 50 also improves the processability in PBF-LB, lowering the susceptibility of cold cracking compared with conventional H-class hot work tool steels. Typical applications include highpressure die casting dies, injection moulds, and hot forming tools.
m4p material solutions GmbH, with operations in both Austria and Germany, has announced it has received a €3 million investment from Finindus NV and Berkau Beteiligungs GmbH. In addition to the financial backing, the investors will bring valuable connections in the metallurgical and Additive Manufacturing sectors, along with extensive experience in supporting the growth of emerging companies.
m4p specialises in advanced metal powders for industrial Additive Manufacturing. It offers a portfolio of over 160 products designed and manufactured specifically for Laser Beam Powder Bed Fusion (PBF-LB) applications and used by over 400 customers.
The company develops and produces standard alloys optimised for Additive Manufacturing
as well as customised powders which are tailored to specific applications.
The additional funding will facilitate the expansion of m4p’s geographical presence into North America and Asia, the introduction of new innovative alloys for Additive Manufacturing and the support of additional AM technologies besides PBF-LB. Furthermore, m4p will deploy its fully digitised business processes, improving the supply chain and quality experience for existing and new customers.
“m4p impressed us with their strong position in their home market, which we quickly understood is due to their unwavering commitment to customer satisfaction, paired with a profound understanding of both materials and processes,” said Roel Callebaut, Senior Investment Manager at Finindus. “By seamlessly integrating flexibility with stringent
The chemical composition is tailored for improved hot hardness at temperatures exceeding 600°C. It is characterised by lower carbon content compared with those of medium carbon hot work tool steels and modifications to the carbide forming elements. This is to ensure a comparable or even enhanced tempering resistance despite lower carbon wt.%.
The thermal conductivity of Osprey HWTS 50 is higher compared to medium carbon tool steels over a wide temperature range.
Osprey HWTS 50 metal powder is manufactured by either induction melting under Vacuum Inert Gas Atomisation or melting under argon prior to Inert Gas Atomisation. This produces a powder with a spherical morphology, which provides good flow characteristics and high packing density. In addition, the powder has a low oxygen content and low impurity levels.
www.metalpowder.sandvik
contamination control of powders and minimising batch variability they empower their customers to focus on what they do best: building exceptional parts.”
Andreas Berkau, of Berkau Beteiligungs, added, “As one of m4p’s first customers, I have been able to follow the company’s development closely over the years. I have been particularly impressed by the fact that m4p has managed to build up an excellent reputation among users, service providers and machine manufacturers in recent years. I look forward to supporting m4p in the coming years with both capital and technical expertise.”
Philipp Tschertou, CEO of m4p, shared, “We are honoured to have Finindus and Andreas Berkau as new shareholders, as they bring their market knowledge and experience on top of the financial funding for further market penetration. We are looking forward to a successful and rewarding cooperation with our top class shareholder group for the benefit of our customers.”
www.metals4printing.com
Arburg GmbH & Co KG has announced that its next Technology Days event will take place March 19-22, 2025, at its headquarters in Lossburg, Germany. In 2024, the event attracted over 5,000 guests, contributing to a total of over 100,000 visitors during its twenty-five year history.
Over forty exhibits, with applications from a range of industries, will showcase Arburg’s many products and services. In addition to new features
and offerings, the company’s complete portfolio of machines and robotic systems will be displayed.
More than forty exhibits featuring applications from various industries will showcase Arburg’s product and service range. The company will also display its complete portfolio of machines and robotic systems, along with new features and offerings.
As part of the arburgSOLUTIONworld platform, the Arburg team will advise attendees on current and
Canada’s PyroGenesis, headquartered in Montreal, Quebec, has announced that its name has been officially changed to PyroGenesis Inc from PyroGenesis Canada Inc.
Simultaneously, the French version of the company’s name has changed to PyroGènese Inc. from PyroGènese Canada Inc.
“This change to our name is a subtle but important change as it better reflects who we are and what we are doing,” stated P Peter Pascali,
President and CEO of PyroGenesis.
“With sales across twenty-one countries and counting, this name change is part of an initiative to better express in all areas of communication that we are an internationally focused company with global reach.”
This name change does not involve any restructuring, change of control, or other corporate reorganisation. This decision solely pertains to a more inclusive and internationally resonant brand image. The name
Mesago Messe Frankfurt has announced that Formnext Chicago will not take place in 2025, with the show being postponed due to unfavourable scheduling and the challenging situation in the AM industry. The organiser said that the clash of dates with RAPID + TCT Detroit was making it more difficult for exhibitors and visitors to commit to one of two important events.
Whilst Mesago Messe Frankfurt stated that it worked to resolve the scheduling situation with all parties involved, the negotiations were unsuccessful.
“After careful consideration and intensive discussions with our key partners, we have jointly decided to postpone the start of Formnext Chicago, which was originally scheduled for 8-10 April 2025,” explained Sascha Wenzler, Vice President at Mesago Messe Frankfurt GmbH. “This decision was not taken lightly. We are convinced that it is in the best interests of the industry and the companies involved.”
In partnership with AMT – The Association For Manufacturing Technology (organiser of IMTS), Gardner Business Media and Messe
future topics such as energy, efficiency, shortage of skilled labour and future orientation. The company will work with interested parties to make their operations more efficient and future-proof with Arburg’s ‘Action Plan: Energy,’ Arburg host computer system ALS, GESTICA assistants and the arburgXworld customer portal.
In the arburgXworld exhibition area, presenters will give you practical demonstrations of how companies can use digitalisation to make savings and become more efficient. The range of topics extends from assistants to cross-linked production management and digital value-added services.
www.arburg.com
change does not affect the trading of the company’s shares.
Additionally, the company announced that it has moved its headquarters to a larger location in downtown Montreal. The move comes as a result of the company outgrowing its previous facility after more than thirty years. The new office location in Montreal provides more modern amenities and a smarter office layout, while also providing easier access for employees and customers that use public transport.
www.pyrogenesis.com
Frankfurt USA, Mesago Messe Frankfurt is working to develop a new strategic approach for the US market, ensuring future events are well-timed and aligned with the needs of the Additive Manufacturing industry.
“Our priority is to support the buyer and seller community in ways that truly benefit their businesses, and we believe this is the best course of action to achieve that goal,” explained Douglas Woods, AMT President.
“We thank our partners and the entire community for their support and understanding and look forward to working together to shape the next steps for Formnext in the US,” added Petra Haarburger, president at Mesago Messe Frankfurt.
www.formnext.mesago.com
From prototyping to full-scale production, Ipsen has your post-processing heat-treating equipment requirements covered. We build furnaces as small as 12” x 12” x 24” and as large as your needs require. For 75 years, Ipsen has been at the forefront of innovating furnace technology to meet strict and exacting requirements in critical industries. No matter what the future brings, Ipsen is here as your partner in success.
Creatz3D Ceramics recently highlighted its ongoing collaboration with Aliena, both headquartered in Singapore, in supporting the development of the MUSIC plasma propulsion system. Since July 2023, Creatz3D has played an active role in Aliena’s STRIDER mission.
Creatz3D Ceramics was formed in 2017 as a subdivision of its parent company, Creatz3D, with a focus on the Additive Manufacturing of ceramic parts. The company provides ceramic Additive Manufacturing services using Vat Photopolymerisation (VPP).
Aliena is a space-tech company that offers advanced electric propulsion engines for small satellites, enabling them to fly closer to Earth for improved data collection. Both companies are continuing their work on Aliena’s high-current cathode, a key component in an oxygen-
hydrogen Hall thruster that will soon be tested at the European Space Agency (ESA).
Creatz3D Ceramics’ ceramic AM was said to have played a key role in meeting the high demands of space, such as extreme temperatures and harsh environments. By working together, the companies were able to improve performance and cut costs while addressing the specific needs of industries that require durable, high-quality materials.
“On the global market of Hall thrusters, Aliena retains a strong technological entitlement with the MUSIC satellite propulsion system product line,” stated Dr GeorgeCristian Potrivitu, co-founder and Chief Technology Officer of Aliena. “Adoption of innovative engineering solutions such as AM helps Aliena
design robust systems, push the frontier of what’s possible in terms of part design, and fuel the optimisation process of our products. Our work with Creatz3D led to our systems achieving better performance and contributed to the higher reliability of their operation.”
www.c3d-ceramics.com www.aliena.sg
Addimetal, based in Toulouse, France, launched its K2-2 metal Binder Jetting Additive Manufacturing machine at this year’s Formnext in Frankfurt, Germnay. Reported to be the first French-designed metal Binder Jetting machine, the K2-2 includes customisable build parameters and is equipped with the company’s Orion software to enable workflow integration. After four years of development, and a successful year of beta testing, Addimetal is now offering the machine with a starting price of under €200,000.
“The K2-2 represents a game-changing advancement for industries like aerospace, automotive, luxury, and more. Our goal is to become one of the European leaders in metal Additive Manufacturing,” stated Mohamad Koubar, CEO of Addimetal. “With the K2-2, we provide a solution that bridges the gap between lab-scale research and full-scale industrial production.”
The K2-2 is capable of processing a variety of metallic powders and custom binders and features a build box measuring 200 x 200 x 200 mm. It is equipped with a wide build platform and is reportedly the largest print head on the market, covering over half the platform in one pass. The open system allows the use of non-proprietary binders, offering users greater material flexibility. It includes real-time environmental control with visual sensors to optimise the workspace for peak performance.
“Our machine’s ability to use non-proprietary consumables offers unparalleled freedom to manufacturers, providing the flexibility they need to push the limits of innovation,” added Franck Liguori, CCO of Addimetal. “We’ve designed the K2-2 to be versatile, cost-efficient, and easy to integrate
into existing workflows, making it ideal for R&D teams and industrial applications alike.”
Addimetal said it is actively exploring strategic funding opportunities to accelerate its development and drive forward innovation in the metal Binder Jetting field. www.addimetal.com
Over 6,500 production and laboratory furnaces manufactured since 1954
• Metal or graphite hot zones
• Processes all binders and feedstocks
• Sizes from 8.5 to 340 liters (0.3–12 cu ft.)
• Pressures from 10-6 torr to 750 torr
• Vacuum, Ar, N2 and H2
• Max possible temperature 3,500°C (6,332°F)
• Worldwide field service, rebuilds and parts for all makes
Ipsen USA, Cherry Valley, Illinois, USA, has formally launched its Service HUB model, marking a shift in how the company will deliver service and support to customers in the US. To support the rollout of the Service Hub model, Ipsen also introduced its Technical Development Center (TDC) training initiative.
Over the past two years, Ipsen has developed the regional HUB model concept under the direction of Ipsen Global CEO Geoffrey Somary. Now, led by CSO John Dykstra, the HUBs will provide services across a large portion of the American Midwest and Southeast, particularly in areas with a high density of Ipsen customers.
This move to regional service centres is intended to enable quicker response times, dedicated support teams and thorough knowledge of each customer’s facility. This more tailored response is expected to reduce customer downtime and optimise heat-treating operation performance whilst also improving the quality of life of its Field Service Engineers (FSEs).
Ipsen USA has formally launched its regional Service HUB model for US customers (Courtesy Ipsen USA)
The Ipsen Technical Development Center (TDC), is an initiative led by Darci Johnson, Program and Transformation Manager, and Cavan Cardenas, Technical Training Lead. The TDC is focused on training and developing new Field Service Engineers (FSEs), including the launch of the Field Service Engineer Academy, a specialised programme intended to equip new and current technicians with the skills and knowledge to best serve customers within the HUB model.
www.ipsenglobal.com
Pfeiffer Vacuum, a member of the global Busch Group based in Asslar, Germany, has announced a rebrand into Pfeiffer Vacuum + Fab Solutions.
Intended to reflect Pfeiffer’s comprehensive portfolio of both vacuum solutions and semiconductor fab solutions, the rebrand marks the seventieth anniversary of the company’s first major development of a turbomolecular vacuum pump.
Today, Pfeiffer is a global provider of solutions for high and ultra-high vacuum technology with a product portfolio including leak detectors, measurement and analysis devices, components, as well as vacuum chambers and systems.
“Our new logo is more than just a trademark. It tells our story, which began with the invention of the turbopump and became a global success. Our teams design and manufacture products that are used in the world’s most high-tech applications and future megatrends, exploring the frontiers of knowledge,” explained Wolfgang Ehrk, CEO of Pfeiffer. www.pfeiffer-vacuum.com
Advanced Powder Products, Inc. (APP), Philipsburg, Pennsylvania, USA, a company specialising in Metal Injection Moulding and metal Additive Manufacturing, has received almost $3 million from the Pennsylvania Industrial Development Authority (PIDA). The funding will enable APP to invest in new machinery and expand its Philipsburg facility, following a fire that damaged the site in February 2023.
The company was approved through the Moshannon Valley Economic Development Partnership (MVEDP) for a fifteenyear, $2.25 million loan, as well as a seven-year Machinery and Equipment Loan Fund (MELF) loan totalling $700,928.
According to the state press release, APP will use the PIDA loan to construct a new 2,700 m 2 building. The MELF loan will allow the company to invest in new CNC machinery, metal injection moulding equipment, and robotics. The total project cost is $7.47 million and is expected to create fifteen new full-time jobs and retain 165 full-time jobs.
Local news outlet The Progress reported that MVEDP Executive Director Stan LaFuria has worked with APP owner Don Heaney since 2002, a year after the creation of the Moshannon Valley Regional Business Park at which Heaney and his partner bought a 1.49-acre plot. “We are very pleased to be working with the owner and staff
of Advanced Powder Products on their expansion efforts,” LaFuria said.
APP Controller Andy Shoop told The Progress , “We continue to see a huge opportunity for our Metal Injection Moulding technology even after the fire we experienced last year. This expansion project will allow us to continue to serve and grow with our customers, create new jobs in the area, and become America’s best and biggest Metal Injection Moulding company.”
“We sincerely appreciate the support from MVEDP and PIDA,” Shoop added. “APP has created roughly 100 new jobs since the first time we worked with Stan and PIDA for financing 2019. Our goal is to continue on our growth path. We’re currently looking for engineers, technicians, and other supporting roles throughout the company.”
www.advancedpowderproducts.com
Plastometrex, a developer of mechanical testing solutions based in Cambridge, UK, has announced a collaboration with Airbus that is intended to streamline mechanical testing processes and enhance material insights. The partnership aims to support the standardisation of PIP (Profilometry-based Indentation Plastometry), a mechanical testing technique developed and commercialised by Plastometrex.
Traditional tensile testing requires test pieces that conform to precise dimensions, which adds significant expense to testing workflows, can limit the speed of a project, and can prohibit testing in various circumstances, including where samples are small or irregularly shaped.
By comparison, PIP sample preparation is said to be simpler. The test operation is more straightforward, and the entire process can be completed in just a few minutes. Also, it can test specimens directly and at a fine scale, which unlocks the testing of small or irregularly shaped pieces and enables the extraction of more data, delivering deeper insights into material behaviour. For example, 160 PIP tests can be fitted onto a standard ASTM E8 tensile coupon, unlocking information about material homogeneity that would be obscured by the single stress-strain curve obtained when tensile testing this part.
Through PIP, Airbus will accelerate testing workflows and enable the generation of richer data, supporting innovation and advancing
the highest levels of safety in aerospace engineering.
Dr Jimmy Campbell, CTO at Plastometrex, shared, “We are thrilled to collaborate with Airbus on standardising PIP. This partnership highlights the transformative potential of our technology, enabling faster, more versatile, and data-rich testing. Together, we’re setting a new standard in mechanical testing that aligns with the rigorous demands of the aerospace industry.”
This collaboration between Airbus and Plastometrex is said to mark a significant advancement in mechanical testing. It offers a streamlined, costeffective, and data-rich complement to traditional methods. As both companies work together, this new approach looks to improve testing efficiency and deliver more detailed insights into material behaviour, benefitting aerospace projects worldwide. www.plastometrex.com www.airbus.com
A high-performance ceramics project, titled “Photochemical and Photothermal Additive Manufacturing of Preceramic Polymers,” has been awarded a fiveyear, $4.5 million Multidisciplinary University Research Initiative grant by the US Department of Defense (DoD), through the Office of Naval Research (ONR). The project is led by Penn State and Michigan State researchers, Robert Hickey, Michael Hickner, but the team also includes the Massachusetts Institute of Technology (MIT) and the University of Southern California (USC).
Priya Vashishta, a professor of chemical engineering and materials science, and Aiichiro Nakano, a professor of computer science, both at the USC, along with Alexander Radosevich, a professor chemistry at the MIT, are co-PIs on the project. Also contributing is Jon-Paul Maria, a professor of materials science and engineering from Penn State.
The project seeks to create a one-step process to produce ultrahigh-temperature ceramic materials without bulk heating. The team is focusing on the potential of using light to convert polymer precursor molecules – easy–to–process starting materials – into the final ceramic product.
“The big problem currently in forming ceramics is the high temperatures and high energy required,” Hickey said. “That has been a detriment, especially for 3D printing, which is currently very hard to do precisely with these materials.”
produce chemical reactions in the precursor materials that will allow them to rapidly densify into hardened ceramic materials without bulk heating. This would enable rapid, high-fidelity Additive Manufacturing, the researchers said, because heating materials with light leads to faster processing than traditional thermal methods.
The scientists said the findings could impact future Department of Defense efforts in advanced hypersonic vehicles. The ability to additively form ceramic materials that can perform at ultra-high temperatures into new shapes significantly opens the design window for advanced re-entry vehicles.
www.psu.edu www.msu.edu www.mit.edu www.usc.edu
Converting polymer precursors to ceramics currently involves heating the materials in bulk to high temperatures – a process that can lose as much as 50% of the precursor material. The process can also change the geometry of the finished ceramic parts, contributing to the trickiness of precise Additive Manufacturing, Hickey added.
Using high-intensity lasers, the scientists estimate that they can
The Fraunhofer Institute for Manufacturing Technology and Advanced Materials (IFAM), Dresden University of Applied Sciences (HTW), and the Fraunhofer Institute for Material and Beam Technology (IWS) are collaborating on the ‘Simsalabim’ project to design a continuous process chain for the sinter-based Additive Manufacturing of nickel-based alloys. Alongside the process chain, the project aims to establish new materials and processes in order to offer future industrial partners a broader range of solutions.
The end goal of the project is to reach TRL 5 whilst keeping resource efficiency in mind. The partners are aiming to save two to three development cycles and accelerate the calibration of new materials by a factor of five. In the long term, the project is also intended to serve as the nucleus for a regional network for sinter-based Additive Manufacturing processes. Based on the results of this project, other material classes (e.g. tool steels and cobalt-based alloys) are also to be investigated in the future.
To date, metal Additive Manufacturing has primarily focused on laserbased processes. Although these are
characterised by a high level of technological maturity, they can’t meet certain challenges in the realms of materials, geometries and productivity. This gap is why the industry’s interest in sinter-based additive processes is growing; the technology’s advantages include the ability to process difficult-to-weld materials, high productivity, good surface quality and cost-effective production.
Sinter-based Additive Manufacturing processes metal powder without complete melting, reducing thermal gradients and the formation of residual stresses as well as susceptibility to cracking and the formation of harmful phases.
This offers a great potential for high-strength nickel-based superalloys in particular, as these alloys cannot be processed crackfree using laser-based processes. Characterised by high strength and corrosion resistance at high temperatures, these alloys are often the first choice for high-temperature applications in the energy, transport and hydrogen industries. The lower degree of maturity of sinter-based Additive Manufacturing processes compared to laser-based processes is causing reservations on the part of the industry with regard to the achievable properties, such as proximity to the final shape and material
Kick-off meeting for the project Simsalabim on October 25, 2024 (Courtesy IFAM)
microstructure. There is, therefore, a need to digitally predict the sintering shrinkage of complex structures and the adjustment of material properties in particular.
Invitation to exchange ideas within a network
Manufacturers and users of hightemperature materials are invited to an initial network meeting on November 27-28, 2024, in order to incorporate the specific requirements, needs and applications of the industry into the developments right from the start. The continuing network exchange will work to jointly advance the cost-effective production of components using sinterbased Additive Manufacturing.
With the Saxon scientific institutions Fraunhofer IFAM, Fraunhofer IWS and HTW Dresden – three research partners with distinctive expertise and in-depth experience in aviation, energy technology, Additive Manufacturing and Powder Metallurgy – are available on the development side. www.ifam.fraunhofer.de www.htw-dresden.de www.iws.fraunhofer.de
The 7 th International Conference on Powder Metallurgy in Asia (APMA 2025) will take place October 19-22, 2025, in Qingdao, China.
The event is organised by the China Powder Metallurgy Alliance (CPMA) and the Chinese Society for Metals (CSM), and supported by the Asian Powder Metallurgy Association (APMA).
The International Conference on Powder Metallurgy in Asia began in 2011, and is held every two years. The 2025 conference will cover the following topics:
• Metal powder preparation and processes
• Sintering and post-processing
• Powder Injection Moulding (PIM)
Additive Manufacturing
• Hot Isostatic Pressing (HIP)
• Functional materials & magnetic materials
Powder superalloys
• Cemented carbide and refractory metals
• Porous materials
Energy materials
• Materials genome engineering
• Standards
The MPIF has released the proceedings of PowderMet2024 and AMPM2024, which took place earlier this year in Pittsburgh, Pennsylvania, USA.
‘Advances in Powder Metallurgy & Particulate Materials – 2024’ contains thirty-five technical papers over 424 pages. As the leading technical conference on Powder Metallurgy and particu -
late materials in the Americas, PowderMet2024 is a hub for technology transfer for professionals from every part of the industry, including metal powders, compacting presses, sintering furnaces, quality-control, particlesize and powder-characterisation equipment and more.
‘Advances in Additive Manufacturing with Powder
The new materials networking association Forschungsvereinigung Neue Materialien eV has named Vincent Müller the winner of its 2024 New Materials Innovation Award for his bachelor’s thesis centred on the industrial Additive Manufacturing of hardmetals.
‘Erforschung der Prozessparameter für den Filamentdruck von porenfreien Bauteilen aus Hartmetall’ (’Research into the process parameters for filament printing of non-porous components made of
hardmetal’) was supervised by Prof Dr-Ing Stephan Tremmel, Dr-Ing Tobias Rosnitschek (both of Universität Bayreuth), and Dr-Ing Dehua Chen of Neue Materialien Bayreuth GmbH. The results were developed in close collaboration with industry partners Klaus Trott (GMtec) and Peter Würtele. This work was conducted as part of the project KK5027509KL2, funded by the Bundesministerium für Wirtschaft und Klimaschutz (Federal Ministry for Economic Affairs and
Following the welcome and opening ceremony, the APMA will hold a Council Meeting. Plenary and technical sessions will then take place, followed by an awards ceremony and opening of the exhibition. apma2025.scimeeting.cn
Metallurgy – 2024’ contains forty technical papers over 475 pages. Every metal Additive Manufacturing technology is represented within the proceedings, including: Laser and Electron Beam Powder Bed Fusion (PBF-LB and PBF-EB), Binder Jetting, Material Extrusion and Cold Spray technologies. Application discussions included representative presentations on the adoption of AM by the medical, aerospace, art world, and conventional industrial components. www.mpif.org
From left: H Ruckdaeschel (NMB), H Rausch (Forschungsvereinigung Neue Materialien), winner V Müller, W Brehm (IHK Oberfranken Bayreuth) (Courtesy IHK Oberfranken Bayreuth)
Climate Protection) through the Central Innovation Programme for SMEs.
www.fvnm.org www.nmbgmbh.de www.uni-bayreuth.de
Farsoon Technologies, based in Changsha, China, has announced that it can now produce titanium parts on polymer Additive Machines using ColdMetalFusion technology, a sinterbased Additive Manufacturing process developed by Headmade Materials GmbH, Wuerzburg, Germany.
To achieve high-yield, sustainable metal parts production, Headmade Materials has invested in the Farsoon SS403P Polymer Powder Bed Fusion (PBF) machine, now installed at its
facility. Leveraging Farsoon’s open parameter strategy, Headmade’s technical team can continuously develop and refine processing parameters across various material families to meet industry-specific applications.
Farsoon’s polymer PBF Additive Manufacturing machine is central to the CMF process, allowing metal parts to be produced without complex support structures. Integrated into the CMF workflow,
Titanium alloy Ti6Al4V parts produced using ColdMetalFusion Technology (Courtesy Headmade)
D3-AM GmbH, based in Bressanone, Italy, introduced its new LAB II Large Format ceramic Additive Manufacturing machine at this year’s Formnext. The new machine uses the company’s proprietary Micro Particle Jetting (MPJ) technology and is capable of producing ceramic components up to 400 x 480 x 160 mm.
With the development of a unique printhead, the D3-AM enables direct deposition of waterbased suspensions with high solids content and almost any particle size and distribution. Once built,
the additively manufactured parts can be sintered directly – without any additional debinding steps.
The LAB II Large Format allows the production of larger ceramic components and higher quantities in a single run, helping to streamline manufacturing for industries that demand complex, high-performance parts.
D3-AM GmbH is a spin-off of Durst Group, a global manufacturer of digital printing and production technology. D3-AM is based at the ‘Durst Kraftwerk’ innovation centre at the Durst Group. The Durst
Headmade Materials has successfully developed CMF-specific Ti64 parameters, exemplified by the production of a large-format impeller for industrial applications. This achievement underscores the scalability and reliability of the CMF process in producing advanced components.
“By working together with our individual expertise, Farsoon and Headmade Materials are jointly advancing ColdMetalFusion to achieve our common goal of reliable and scalable series metal production. The high productivity of Farsoon’s machines opens up many new opportunities for ColdMetalFusion,” said Christian Fischer, co-founder and Managing Director, Headmade Materials GmbH.
This addition marks a significant breakthrough in the cost-effective production of Titanium Grade 5 (Ti64) parts. The collaboration between Headmade and Farsoon is poised to streamline the sourcing of Ti64 components for industries such as aerospace and medical, tackling challenges that have long hindered reliable and affordable production. www.farsoon.com
www.headmade-materials.de
D3-AM has launched its new LAB II Large Format ceramic Additive Manufacturing machine (Courtesy D3-AM)
Group employs more than 800 people worldwide and has contributed to the digital transformation and the replacement of traditional production processes with technological innovations in various industries.
www.d3-am.com
Material Options (Metal)
Material Options (Ceramics)
Build Envelope
Quantity
Tolerance capability
CONTACT FOR MORE DETAILS
17-4PH, SS 316, Tool Steel M2 & S-7, Inconel 625, 4140
Alumina 99.5%, Zirconia
~ 300 grams max, Footprint equivalent of baseball size or less, 0.02” (0.50 mm) wall thickness minimum
10~50 samples based on footprint. Larger quantities up to 1,000 pcs welcome depending on the part size.
Within 2% of the feature size, 2~3 Ra Surface finish, Option of finishing to closer tolerances available.
NORTH AMERICA Email: Mukund.N@indo-mim.com Ph: +1 (210) 557-1594
EUROPE Email: InfoEU@indo-mim.com Ph: +49 1732656067
ASIA Email: InfoHQ@indo-mim.com Ph: +9198459 47783 / +91 98450 75320
ISO 9001:2015 / IATF 16949:2016 / AS
Thermo Fisher Scientific, headquartered in Waltham, Massachusetts, USA, has highlighted the ability of Scanning Electron Microscopy (SEM) to successfully capture defects when conducting failure analysis on metals. In the report, Dr Franz Kamutzki, Sales Account Manager at Thermo Fisher Scientific, explains how new elemental analysis approaches can help ensure the quality of metal components.
“In the metals industry, the difference between success and failure often hinges on microscopic details,” begins Dr Kamutzki. “Since component failure is often a direct result of microscopic defects, SEM helps establish metrics for quality control to help manufacturers get to the root cause of their material concerns.”
With demand for steel expected to grow by 2030, there is an opportunity to reindustrialise and modernise production processes, the report adds. An increasingly popular method of regenerating production is engineering materials at the nanoscale; tailoring structures at this size can improve durability, reliability and cost.
Nishimura Advanced Ceramics Co.,Ltd
Ko Nishimura (Global sales)
3-2 Kawata Kiyomizuyaki Danchi-cyo, Yamashina-ku, Kyoto - 607-8322 JAPAN
Phone: +81-80-8305-9205
Phone (Kyoto Office): +81-75-591-1313
npc-e3@nishimuratougyou.co.jp http://www.nishimuratougyou.co.jp/english/
Copper-rich T1 (green) and Zircon-rich beta-prime (red) precipitates in the heat-affected zone of an aluminium alloy friction-welded aerospace part (Courtesy Thermo Fisher Scientific)
“An example of this,” explains Dr Kamutzki, “is when engineering metals for the aerospace sector, reducing weight and increasing stiffness can help to improve performance and extend the working life of the component parts.”
Metals
Even traditional processes now incorporate microscopic inspection to determine the material’s elemental and structural composition. Precise control of inclusions and precipitates is essential for effective metal production, but whether these additions strengthen the material or act as contaminants depends on their consistency and distribution. Examples of these microscopic properties include nanoprecipitates, which form when the metal is rolled, annealed or hot pressed. Steel strengthened with nanoprecipitation offers good weldability and a high strength-to-weight ratio, making them ideal in aircraft structures.
“However, the presence of inclusions and precipitates can also have detrimental effects on material quality,” highlights Dr Kamutzki. “In the range of industries that use metal or steel, quality control measures are implemented to ensure material quality before it is used. For example, quality engineers must detect nanoscale morphological changes such as crack initiation sites, which can occur due to microstructural alternations during fatigue loading.”
CIM Feedstock
Ko Nishimura (Global sales)
High Strength Translucent Alumina FS (Al2O3 99.99%)
96% ~ 99.9% Alumina FS (White, Black)
Zirconia FS (White, Black, Blue) Mullite FS
Given that the metal used in demanding applications, such as aircraft frames, must withstand vibrations, pressure fluctuations and thermal stresses, accurately detecting crack initiation sites is an essential part of quality control. Other nanoscale structural changes that require detection and control include grain boundaries, which are defects that can decrease the material’s electrical and thermal conductivity, as well as oxide inclusions that cause casting interruptions in steelmaking. Since steelmaking is a highly oxidising process, the quality is easily jeopardised by inclusions.
Here, Dr Kamutzki is keen to point out that microscopy can detect any major faults in the final product and help maintain compliance with industry standards. “For example, ASTM E45, which provides methods for microscopic examinations to evaluate non-metallic inclusions in steel, and E2283, which offers statistical methods for analysing the distribution of these inclusions.”
Simplifying microscopy with SEM SEM plays a vital role in characterising the composite materials employed. “Take for instance, refractories, which are commonly used in steel production as protection in extreme environments such as heating furnaces and refining vessels,” adds Dr Kamutzki. “Due to high temperatures and corrosive conditions, the physical and chemical properties of the refractories are hugely important for stability and wear resistance. Typically fabricated by combining material types such as ceramic (oxide) powders, reactive metals or carbides, the refractories may be employed in pressed bricks, monolithic linings and carbon-bonded products used in continuous steel casting.”
While conventional electron microscopy is useful, providing a backscattered or scattered electron (BSE and SE, respectively) image of materials distribution, the images can’t disclose grain composition or distinguish different phases and possible contaminations, explains Dr Kamutzki. “However, elemental analysis based on instantaneously displayed information from the SEM image is much quicker and more informative.”
In the report, Thermo Fisher highlights its own ChemiSEM technology, which enables high-throughput chemical analysis with energy-dispersive X-ray spectroscopy (EDS) mapping. This allows for an overview of the elemental and structural composition of hundreds, if not thousands, of inclusions to be given in hours, as opposed
BSE image of a refractory oxides sample and the determination of different phases from the detected elements using ChemiPhase (Courtesy Thermo Fisher Scientific)
to the days it may take for manual analysis to achieve the same results, the company states.
Not only is statistical information on the bulk available, but individual precipitates can also be seen in the Transmission Electron Microscope (TEM) with high detail, providing a multi-scale overview of the metal. Within steel and aluminium production, where reducing weight is a priority, Thermo Fisher’s automated instruments can also carry out the critical task of nanoparticle counting.
“Since metal components are frequently used in demanding environments, detecting and controlling microscopic material defects is crucial. While this requires extensive structural analysis, advanced approaches to SEM can simplify the process and save time, without compromising quality testing standards,” concludes Dr Kamutzki.
www.thermofisher.com
FEATURES
FEATURES
• Metal or Graphite Hot Zones
• Metal or Graphite Hot Zones
• Metal and Graphite Retorts
• Metal and Graphite Retorts
Debinding & Sintering
APPLICATIONS
APPLICATIONS
• Additive Manufacturing
•
• Additive Manufacturing
• Metal Injection Moulding
• Ceramic Injection Moulding
• Powder Metallurgy
Lithoz GmbH, based in Vienna, Austria, showcased filtration technology from Evove at this year’s Formnext. Evove utilised Lithoz’s new CeraFab S320 to manufacture Separonics ceramic filter membranes. These membranes are designed to reduce energy use by 80%, increase output fivefold, and recycle 80% more water.
Using twenty filter membrane segments, each with a diameter of 10 cm and measuring 5 cm in height, the complete filter module has a final length of 1 m – making this the largest application ever built by Lithoz LCM technology.
With Lithoz’s lithography-based ceramic manufacturing (LCM) technology, Evove achieved a high level of control over the manufacture of these ceramic filtration membranes, enabling uniform pore size and distribution for optimal water recycling applications. The design freedom provided by the LCM process allowed for more complex geometries and, therefore, enhanced membrane performance, as well as custom
designs tailored for higher flux and selectivity. Thanks to the lack of tools required, these additively manufactured alumina parts benefitted from significantly reduced production costs.
Ceramics, with their inherent durability, make Evove’s filters far more resistant to high temperatures, aggressive chemicals, and physical wear than traditional materials like polymers. As a result, these alumina membranes last longer and require less maintenance, making them ideal for the demanding filtration environments involved when reusing industrial discharge and extracting lithium.
Andrew Walker, Evove CCO, stated, “Water touches 60% of global GDP, and the ability to recycle even the most challenging of feeds is a
lynchpin of the circular economy and decarbonisation. Ceramic materials offer great advantages but, until now, have suffered from the high cost of manufacture and susceptibility to random filtration performances. With Lithoz’s 3D printing technology, it’s proven that we can precision engineer and manufacture cost-effectively at scale.”
Lithoz CEO Dr Johannes Homa shared, “Disruptive breakthroughs like this are crucial in today’s world, as they improve manufacturing efficiency and reduce resource waste. We’re seeing ever more ceramic solutions for challenges in manufacturing, as they are used where other materials fail. We’re proud to have provided the technology that enabled this success story in sustainability!” www.lithoz.com
Advanced Technology (Bazhou) Special Powder Co.,Ltd
No.76 Xueyuan Nanlu, Haidian, Beijing 100081,China
Tel: +86-13701029643
Email: powdermetal@atmcn.com
• Powders for magnetic core and SMD
• Powders for MIM
• Pre-alloy powders for diamond tools
• Powders for auto engine valve seats and guides
• Powders for filtering materials
Sales Agent in Europe Burkard Metallpulververtrieb GmbH
Tel. +49(0)5403 3219041
E-mail: burkard@bmv-burkard.com
Professor Suk-Joong L Kang, president of the Korean Powder Materials Society (KAIST), recently published a textbook titled ‘Problems and Solutions in Sintering Science and Technology.’
The text collates the questions posed to Kang’s students attending the sintering course at KAIST from 1984-2019, most of which were developed to test the students’ knowledge and enhance their understanding of sintering fundamentals and processes.
“I believe most of them and their solutions are correct and appropriate,” stated Kang in the publication’s preface. “Some of them, however, may be incorrect and inappropriate. In such cases, I hope the readers can find the correct solutions and answers. Some others may be unrealistic; they are included to emphasise the physical meaning behind them.”
For several solutions and answers, Kang added references that provide more details on the subject.
The textbook separates the problems and solutions into four categories. These are:
1. Basis of sintering science
2. Bonding and densification 2.1
Solid state sintering 2.2 Liquid phase sintering
3. Grain growth and microstructural evolution 3.1 Solid state sintering
3.2 Liquid phase sintering
4. Supplementary subjects 4.1 Sintering of ionic compounds
4.2 Diffusion induced interface migration
In the above, Part 1 collects problems and questions about general sintering processes, thermodynamics of the interface, and polycrystalline microstructures. In Parts 2 and 3, the problems concerning solid-state sintering and liquid-phase sintering are listed separately. Part 4 contains
Union Process, based in Akron, Ohio, USA, has announced the development of a customised SL5 wet-grind attritor, providing efficient and highprecision metal powder milling. The SL5 attritor, designed for a customer who needed to process an alcoholbased silver slurry, reduces particle size and creates a unique particle morphology.
The new attritor is powered by a 10 HP, explosion-proof motor. The variable frequency drive is installed in a NEMA 12 enclosure and the LCD Operator Interface Module (OIM) is programmed to display agitator RPM, motor amperage, and motor HP.
The attritor is outfitted with a ten-gallon stainless-steel, jacketed
grinding tank for temperature control. The stainless-steel agitator shaft is configured with 440C hardened stainless steel L-arms. The machine includes a mechanical tachometer, an explosion-proof operator station, and a one-piece cover with a special floating Teflon shaft seal to limit solvent vapour loss.
Since 1946, Union Process has been developing and building custom Attritors. As well as this technology, the company manufactures wet & dry grinding mills and horizontal bead mills and provides material characterisation services for a range of research and industrial applications.
www.unionprocess.com
One of the many questions posed in the book looks to question the entrapped pores within this BaCeO 3 material. It asks to explain the possible causes of the formation of the crystallographically aligned pores with elongated shape (Courtesy Prof Suk-Joong L Kang)
problems concerning the sintering of ionic compounds and diffusioninduced interface migration.
“I hope this solution book can help readers further their understanding of sintering science and technology,” added Kang.
The full book, ‘Problems and Solutions in Sintering Science and Technology,’ can be downloaded via the KPMI website. www.kpmi.or.kr
Union Process has announced the development of the SL5 wet-grind attritor, providing efficient and high-precision metal powder milling (Courtesy Union Process)
Professor Randall M. German’s 6 decades of Powder Metallurgy (PM) and Powder Injection Molding (PIM) research, including metals (MIM), ceramics (CIM), carbides, and composites, has influenced countless students, researchers, and collaborators worldwide. To honor his legacy, the Metal Powder Industries Federation (MPIF), Metal Injection Molding Association (MIMA), and global PIM experts will gather to showcase groundbreaking developments in PM and PIM inspired by or conducted with Prof. German.
From pioneering early industrial gripper systems to mastering Metal Injection Moulding, Germany’s Zimmer Group is today a leader in advanced automation and manufacturing technologies. With operations in 125 countries and a workforce of 1,300, the company produces MIM parts for both internal applications and a growing portfolio of external clients. Dr Georg Schlieper recently visited Dr Natalie Salk to learn about the company’s MIM journey, here he reports on how it has leveraged its expertise in automation to enhance efficiency across its MIM operation.
Günther Zimmer originally aspired to be a farmer. In 1979, he bought a run-down farm in Rheinau, a small town in southwest Germany, to pursue his dream. Today, however, he is co-owner of the Zimmer Group; a company with annual sales of €165 million and 1,300 employees. Reflecting on the origins of his company, he shared that, “In order to service the originating loan, I remembered what my father had already given me in the cradle: metalworking.”
He explained, “My father was, at that time, a teacher at a technical school for metalworking and also a much sought-after expert in mechanics, hydraulics and pneumatics.”
Brothers Günther and Martin Zimmer founded Zimmer GmbH Technische Werkstätten (later the Zimmer Group) in 1980 from a converted cowshed. Initially, the brothers took on a wide range of metalworking orders, such as the production of turned and milled parts and work for construction. The company soon established close contacts with furniture factories, for which it manufactured automated drilling units.
Supported by their imaginative and technically adept father Herbert, Günther and Martin Zimmer launched the first gripping systems for industrial applications in 1982. These were immediately in high demand from domestic companies producing mechanical engineering and plant equipment, because advances in
automation translated directly into the need for versatile grippers, pickand-place systems, and other such machines. Buoyed by success, the company’s management decided to align its corporate strategy with this automation technology. Today, gripping systems remain an essential pillar of the company.
“The vertical integration of manufacturing at Zimmer Group is unusually deep. Most of the individual components used in the company’s products – whether made of metal, plastic or elastomers – are manufactured in-house and assembled into the finished product.”
Zimmer Group’s gripping systems were originally marketed by one of Herbert’s friends, who owned the sales company Sommer Automation GmbH. At the time, the company exclusively manufactured for Sommer, allowing both companies to grow in parallel. When Sommer’s owner retired in 1999 with no successor, Zimmer GmbH acquired the company and integrated its sales operations.
In 1992, the company expanded with the launch of a new type of
industrial shock absorber. Herbert Zimmer’s unique spiral groove technology had significant advantages over conventional industrial shock absorbers in terms of damping behaviour. Over time, more product lines were added, including clamping elements for linear slides. Over a few decades, the company grew substantially.
The vertical integration of manufacturing in the company is unusually deep. Most of the individual components used in the
company’s products – whether made of metal, plastic or elastomers – are manufactured in-house and assembled into the finished product. A subsidiary, Zimmer GmbH Dämpfungssysteme, specialising in damping systems, was founded in Rheinau in 2004. The best-known components from this product line are damping elements used by the furniture industry in the millions in drawers and cabinet doors. The growing demand for plastic parts was met by the subsidiary Zimmer GmbH Kunststofftechnik, founded in 2007.
In 2013 the Zimmer Group was formed as the overall holding company. Over the years, several large buildings were constructed to meet the growing need for production space. Today, the Zimmer Group’s 1,300 worldwide employees work in seventeen international subsidiaries, and the sales network spans 125 countries.
As a successful company of its size, Zimmer Group has implemented a quality management system certified to meet all relevant standards. Continuous improvements are also being sought in certified energy and environmental management. Fundamental values, such as improving sustainability in all areas and striving to ensure the highest standards of working practices and social responsibility within its supply chain, are central to its management.
Clemens Kimmig, a trained gunsmith, is Zimmer Group’s Head of Development. In 2008, Kimmig discovered that many components for sporting and hunting weapons were manufactured using the MIM process, and so he familiarised himself with the technology. Since the group’s products use a large number of small, intricate parts, the decision was soon made to establish MIM production in-house. This
was in line with Zimmer Group’s corporate philosophy of having the deepest possible vertical integration.
Widely used polyoxymethylene (POM)-based feedstock technology, which has advantages that include high green part strength and high dimensional stability, was chosen for the company’s production process. With POM feedstocks, a catalytic debinding process is used to remove the first-stage binder. In a final processing stage, the backbone binder is thermally removed prior to sintering the parts in an inert gas atmosphere or a vacuum.
Dr Natalie Salk, Key Account Manager (Fig. 3), joined the Zimmer GmbH in 2012, having already gained extensive experience in MIM technology. Salk studied mineralogy and crystallography at the University of Freiburg, where, as part of her doctoral thesis, she produced germanium and silicon semiconductor crystals. During her thesis work, she secured a job at the Fraunhofer
IFAM research institute in Bremen, a renowned centre of expertise for Metal Injection Moulding technology. At IFAM, she worked on a project to grow diamond crystals and then joined the Powder Metallurgy Group after the project ended. Salk spent ten years at Fraunhofer IFAM as a project manager, with a focus on micro-MIM. “Semiconductors and metals are very similar in some
respects, and both are variants of materials science,” she explained. “That’s why the switch to Powder Metallurgy was easy for me.”
When she received an offer from PolyMIM GmbH to take over the management of the company, she jumped at the chance and joined this highly-regarded MIM feedstock producer. Here, she established connections with numerous metal
“Since the group’s products use a large number of small, intricate parts, the decision was soon made to set up a MIM production in-house. This was in line with Zimmer Group’s corporate philosophy of having the deepest possible vertical integration.”
powder manufacturers as well as MIM part producers. After leaving PolyMIM, she moved to south west Germany with her family, having accepted a job from Zimmer Group, where she is now responsible for the sales of MIM parts and technical customer service.
Salk told PIM International that, when she first joined Zimmer Group, the company had already succesfully produced a 100Cr6 bearing steelpart. However, it was clear that the company’s young MIM department had much to learn and needed to undergo a steep learning curve before it could become a reliable link in the wider group’s operations.
Once the issues had been resolved, the group was able to reliably produce MIM parts for internal use. However, it turned out that the need for MIM parts within the company was far from sufficient to fully utilise the MIM department’s capacity. This led to the company offering its MIM technology externally in 2010.
Today, Salk describes her chief task as securing new parts for production. Her extensive background knowledge of MIM technology and materials science allows her to advise both customers and her project development team with a high level of expertise. When she talks with customers about possible MIM applications, she quickly sees where this technology could bring advantages and which applications might better suit other manufacturing processes.
“Thanks to being well known in the MIM community, I receive many enquiries and have significantly advanced the MIM department,” said Salk. “First and foremost, I work in sales but, since I come from the research department at the Fraunhofer IFAM, I of course like to participate in new part development projects. Although I have never worked directly operating the injection moulding machines, I know a few tricks, so I’m able to give useful tips to the MIM production team. If there are problems with the production of new parts, I am often asked for advice by the product development department.”
Zimmer Group’s MIM department has four injection moulding machines, two catalytic debinding machines, a thermal debinding furnace and three sintering furnaces. An in-house tool shop supplies injection moulding tools. To meet growing demand, a new sintering furnace for the thermal debinding and sintering MIM parts was recently commissioned.
“This new furnace can reach temperatures of up to 1,550°C in an argon atmosphere and enables sintering under vacuum, partial pressure and overpressure,” stated Salk. “The flexible atmosphere selection means that various gases such as nitrogen, argon or hydrogen can be used. With a usable space of 188 litres, the furnace significantly expands our previous production capacities. In addition, metals such as titanium and titanium alloys can be processed more efficiently, which opens new manufacturing
“With the new furnace, Zimmer Group is able to produce a wide range of MIM materials. In addition to the commonly used low- and high-alloy steels, the portfolio also includes tungsten carbides, tungsten heavy metals, pure titanium and the titanium alloy Ti-6Al-4V.”
possibilities and makes the selection of materials more flexible for customers.”
With the new furnace, Zimmer Group is able to produce a wide range of MIM materials. In addition to the commonly used low- and high-alloy steels, the portfolio also includes tungsten carbides, tungsten heavy metals, pure titanium and titanium alloy Ti-6Al-4V.
One noteworthy MIM application is the encoding ring shown in Fig. 4.
This component, part of a pressure sensor, is designed to ensure that an electrical connection is only possible in a specific position.
In another application example, Zimmer Group’s electric grippers use opening and closing jaws controlled by gears (Fig. 5). To do this, these gears need linear toothing. Due to space constraints, the toothing is set back and cannot be economically produced through machining, instead requiring production via MIM.
Fig. 6 Top: damping piston with tapered spiral groove – green part, brown part, sintered part. Bottom: a view of an industrial shock absorber with housing (1), damping piston with tapered spiral groove (2), piston rod (3), check valve (4), return spring (5), volume compensation (6), fixed stop (7), high-pressure chamber (11), low-pressure chamber (12) (Courtesy Zimmer Group)
“After consideration, the company adopted sinter-based Material Extrusion (MEX) technology. This was selected because MEX machines can be operated with the same commercially available feedstock that is commonly used in its MIM production.”
Although the jaws are still mechanically machined on all sides for tolerance reasons, the production of the preform is undertaken by MIM.
The industrial shock absorbers mentioned earlier in this article, launched in 1992, are an ingenious Zimmer Group invention. Today, MIM is the only technology that makes it possible to economically produce key components used in them in large numbers. While conventional shock absorbers force oil through a piston with fine bores, Zimmer Group’s shock absorbers are designed with a spiral groove and a tapered cross-section (Fig. 6). This causes the resistance of the piston to increase the further the oil penetrates into the spiral groove. As a result, the damping effect increases depending on the piston travel, allowing the shock absorbers to exhibit low-vibration damping characteristics as compared to conventional dampers. The shape of the helical groove is reliably reproduced by MIM.
In addition to components for Zimmer Group’s own products, the MIM department manufactures parts for external customers that span a wide range of industrial applications. These application areas include automotive, sensor technology, electronics, mechanical engineering, sporting and hunting weapons, leisure and sports equipment, aviation, power tools, jewellery, surgical tools, and lock parts. Parts range in weight from a few tenths of a gram to as much as 160 g.
As with so many MIM producers, Zimmer Group has invested in metal Additive Manufacturing. After consideration, the company adopted sinter-based Material Extrusion (MEX) technology. This was selected because MEX machines can be operated with the same commercially available feedstock that is commonly used in its MIM
production (Fig. 7). The green parts produced can be debound and sintered in the same furnaces as MIM parts. Zimmer Group uses MEX technology to rapidly prototype MIM parts so that the customer can test for fit and function without having to invest in expensive injection moulding tooling.
Of course, Zimmer Group also implements the extensive automation it offers its customers in its own production. During my tour of the company, I was particularly struck by the many fully automatic milling centres, which are operated by a small number of employees and produce milled parts around the clock. The assembly and functional testing of the company’s damping pistons is also automated.
“...Zimmer Group also implements the extensive automation it offers its customers in its own production... I was particularly struck by the many fully automatic milling centres, operated by a small number of employees and producing milled parts around the clock.”
One in-house automation development is the ZiMo mobile robot, which is used for pick-andplace tasks. Its robotic arm can be equipped with a mechanical or a vacuum gripper. The arm is mounted on the control unit, which stands on rollers, allowing the robot to be easily moved from one workstation to another. Thanks to the
visual user interface, programming is intuitive and straightforward, making the robot suitable for use at companies that have little experience with industrial robots. For safety, the surrounding area is monitored by optical sensors that detect when a person approaches and immediately interrupts the robot’s activity, meaning the cell with the
robot does not have to be physically cordoned off. The system is used in MIM operations to pick and place green and sintered parts (Fig. 8).
Zimmer Group’s in-house injection moulding experts have also developed a quick clamping system that enables tool changes in a matter of minutes. Two quick clamping plates are mounted on the stationary machine side and the movable ejector side of the injection moulding machine. With the help of eccentric screws mounted in the quick clamping plates, the two halves of the tooling are precisely fixed extremely quickly (Fig. 9). The quick clamping plates have a thickness of 30 mm; if required, they can be equipped with a 6 mm thick thermal insulation plate.
Fig. 10 outlines the sequence of tool setup with quick clamping plates. All Zimmer Group injection moulding tools are equipped with these quick clamping plates. With a trend towards smaller batch sizes, lower inventories and frequent
Fig. 10 Sequence of a tool setup with quick clamping plates (shown in blue). First, the tooling is hooked into the clamping plate on the fixed side of the machine (1) and fixed with the eccentric screws (2). Then, the pipes for the tempering oil are fastened (3). This is followed by the closing of the movable machine side (4). The tooling is hooked into the second clamping plate and fixed (5). Finally, the ejector rod is attached (6) and the tool halves are moved apart (7) (Courtesy Zimmer Group)
just-in-time deliveries, a high degree of production flexibility is required. The quick clamping solution offers considerable advantages for this flexibility.
As a technology-driven company, Zimmer Group has advanced the MIM industry on two levels. Firstly, the company’s development of new MIM applications in a variety of market segments helps to increase the awareness and adoption of MIM. Salk contributes to this task with her extensive expertise and intimate knowledge of MIM technology, which she disseminates to both potential and established customers. Secondly, its innovations have provided the MIM industry with solu -
tions that can increase efficiency and productivity. Examples of these developments are the ZiMo robot and the quick clamping systems for injection moulding tools.
By combining in-house expertise with a focus on the needs of external customers, Zimmer Group not only strengthens its internal operations, but also offers significant value to new partners, setting a benchmark for excellence in the MIM sector.
Dr Natalie Salk
Zimmer Group
D-77866 Rheinau Germany
natalie.salk@zimmer-group.com www.zimmer-group.com
Author
Dr Georg Schlieper
D-45133 Essen, Germany georg.schlieper@hotmail.de
Honorary sponsor
As the hub for Additive Manufacturing, Formnext is the international meeting point for industrial 3D Printing experts and production professionals from a wide range of application industries. With the trade show in Frankfurt as well as content throughout the year, Formnext bundles expertise and creates a unique experience focused on an intensive, professional exchange and access to the latest AM solutions.
Be part of Formnext and learn how you can be ahead of your competition thanks to Additive Manufacturing.
Where ideas take shape.
formnext.com
The 2024 Powder Metallurgy World Congress in Yokohama, Japan, offered an opportunity for the Metal Injection Moulding industry to come together, share market data, and explore emerging trends. The event addressed key issues such as declining sales in major regions, shifts in material demand, and the broader economic and geopolitical challenges affecting the industry. Attendees also explored strategies for innovation, market diversification, and sustainability to drive future growth. Nick Williams shares key data and insight from this important global industry event.
After a twelve-year gap, the Powder Metallurgy World Congress series returned to Yokohama, Japan, from October 13-17. Organised by the Japan Powder Metallurgy Association (JPMA) and the Japan Society of Powder and Powder Metallurgy (JSPM), under the auspices of the Asian Powder Metallurgy Association (APMA), the event attracted nearly 800 congress delegates from twenty-seven countries, alongside numerous additional visitors to the exhibition. Whilst MIM technology was prominently featured throughout World PM2024’s comprehensive technical programme, the Japanese Metal Injection Moulding pavilion in the World PM2024 exhibition hall stood out as a particular highlight (Fig. 1). The pavilion featured fourteen Japanese companies, each engaged in either MIM production or the provision of materials and technology to the MIM sector. Partners in the pavilion were atect Corporation, Castem Co Ltd, Iwaki Diecast Co Ltd, Juki Aizu
Corporation, Nakahara Precision Co Ltd, Nippon Piston Ring Co Ltd, Oriental Chain Mfg Co Ltd, Osaka Titanium Technologies Co Ltd, Osaka Yakin Kogyo Co Ltd, Pacific Sowa Corporation, Repton Co Ltd, Taisei Kogyo Co Ltd, Teibow Co Ltd, and Toko Tsusho Corporation.
The MIM industry meets at a time of stalling growth
World PM2024 took place at a time when MIM industry growth appears to be stalling in many regions. In the case of Japan, evidence for this comes from the JPMA’s recently
published MIM industry statistics. The data – covering 2023 – was provided by eighteen MIM partproducing companies, including members and non-members of the JPMA.
Total sales of MIM parts by Japanese producers for 2023 were reported as ¥12.581 billion ($82.444 million), a 13% decrease from the previous year’s ¥14.35 billion. Fig. 2 shows Japanese MIM parts production by sales value, from 2016 to 2023. No specific reason was given for the reduction in sales in the data’s source, ‘2023 Report for MIM Market’, and no individual markets can
be identified as showing significant changes (Fig. 3), so the sales reduction has to be attributed to the overall business climate, which has been impacted by a challenging economic and geopolitical environment worldwide.
Industrial machinery parts were reported as accounting for 34.1% of the market (previous year: 36.5%); medical appliance parts accounted for 21.4% (previous year: 21.9%); and automotive applications accounted for 12.4% (previous year: 12.0%).
In terms of the MIM materials mix, stainless steels accounted for 74.7% of sales (previous year: 75.8%); and together, stainless steels, Fe-Ni base alloys, low-alloy steels, and magnetic materials accounted for over 90% of sales. The JPMA stated that the sales value for stainless steels was ¥9,401 million ($61,620 million), a 14.4% decrease from the previous year (Fig. 4).
It should be noted that Europe also recorded a drop in sales for 2023, according to data presented by the European Powder Metallurgy Association (EPMA), shown in Fig. 5. Commenting on the state of MIM in Europe during his global market review presentation, EPMA President Ralf Carlström stated, “It looks like MIM has lost a bit of its momentum in Europe, after showing steady growth for many years. We think that the decline that we saw in 2023 is connected to the downturn in German industry.” Carlström noted, however, that the aerospace industry, in particular, will be an important growth market for MIM in Europe.
Even the world’s largest MIM-producing nation, China, appears to be seeing a dip in MIM sales as reported in the Spring 2024 issue of PIM International , driven by the loss of some key Apple applications, such as the Lightning connector (Fig. 6).
No published data is available for MIM sales in North America. However, given reduced gun sales – a market in which MIM parts are extensively used – it would be no surprise if the picture were similar.
5 Estimated European MIM component sales, 2009-2023 (Courtesy EPMA)
MIM
MIM sales to Apple
Fig. 6 The relationship between Apple’s MIM orders and total MIM sales in Greater China (As published in PIM International Vol. 18 No. 1)
“Even the world’s largest MIM-producing nation, China, appears to be seeing a dip in MIM sales as reported in the Spring 2024 issue of PIM International, driven by the loss of some
key
Apple applications, such as the
Lightning connector.”
Source:CPMA
Speaking with MIM producers at World PM2024, the reported figures do not appear to be a cause for panic. Many MIM producers serve a diverse range of markets, and these companies are, therefore, protected from any crisis that hits one particular sector. Whilst the challenging global economic and geopolitical situation can be cited as a reason for the decline in MIM shipments, there is also a continuing ‘ripple effect’ of post-COVID-19 supply chain disruptions.
• Low specific weight
level of awareness among designers and engineers. This is a challenge that the industry is still grappling with. In some cases, opportunities will arise on the back of increasing demand for specific materials, such as titanium, where MIM offers a compelling business case, particularly with the greater availability of more cost-competitive powders. There was certainly evidence of Ti-MIM’s success in the consumer electronics sector on display at the World PM2024 exhibition.
significantly by global region, it is becoming apparent that improved sustainability and improved efficiency can go hand-in-hand and that it will, in the not-so-distant future, be the MIM industry’s biggest customers who set strict sustainability targets, not the industry itself. Those who are prepared, therefore, will be at a significant advantage.
• High specific surface area
However, there is a recognition that the MIM industry has to continue developing new markets. This is particularly the case in world regions that have traditionally been dominated by one particular enduser sector: in the case of China, smartphone parts, and in Europe, automotive applications.
• Good mechanical properties
• Excellent Thermal/Electrical conductivity
• Energy absorption capacity
• Air/Water permeability
In China, whilst small and medium firms press ahead with diversification, the larger companies are eyeing a new generation of smartphone and 5G applications (in the former for foldable devices where MIM is used for hinge mechanisms) (Fig. 7).
However, success in leveraging new markets for MIM is easier said than done and requires a greater
Whilst the MIM industry is also becoming ever more globally competitive, the trend to re-shore production, particularly in the US and Europe, appears to be continuing. The value of local suppliers, with reduced supply chain risk and easier communication, is a significant factor in supporting MIM operations.
Filter material (titanium) porous microstructure
With sustainability being a main theme of World PM2024, a number of conversations and presentations addressed how the industry could become more sustainable through a wide range of measures, from more efficient part design to the use of recycled materials produced with green energy and the use of green energy for sintering processes. Whilst the enthusiasm for a sustainability drive in MIM varies
Fuel cell (titanium)
In 2012, the JPMA and JSPM organised the first PM World Congress MIM party, bringing MIM industry professionals from across the world for an evening of informal networking and entertainment. Now a firmly established tradition, the World PM2024 MIM party once again brought together MIM experts from Europe, the Americas and Asia.
Explosion proof panel (316L stainless steel)
Catalytic converter (iron-based alloy)
Source www.gminsights.com
The event – held on October 15 on the 70 th floor of the Landmark Tower Hotel – was sponsored by Atmix, Iwaki Diecast Co Ltd, NMC, Pacific Sowa Corporation, Teibow, Castem, Osaka Yakin Kogyo Co Ltd, Taiyo Nippon Sanso, and the Society for Injection Molding Technical Research.
Delegates received a warm welcome from Kenji Doi, of Osaka
Yakin Kogyo, who spoke on behalf of the entire Japanese MIM community in expressing a desire for continued international collaboration and a common effort between world regions to further grow awareness of the potential of MIM technology. Kei Takenum, from Epson Atmix, expertly performed the role of Master of Ceremonies.
Amongst several dignitaries who spoke at the event was Prof Hideki Kyogoku, Kindai University and President of Japan’s Technology Research Association for Future Additive Manufacturing (TRAFAM). Kyogoku stated that there was a growing desire to embrace metal Additive Manufacturing technology in Japan – including sinter-based AM – but he also acknowledged that the country had some catching up to do.
It was encouraging to see the MIM party tradition continue, with the networking opportunities fuelled by a sake selection from northern Japan (Denshu, Hassen, Kamekichi, and Kikunoi) sponsored by Epson Atmix, served with traditional ‘masu’ wooden drinking boxes.
With PM2024, the PM World Congress series once again lived up to its reputation as providing the opportunity to interact with a far more diverse group of participants than the regional industry events allow. Participants gained new perspectives and established valuable connections. The PIM International team looks forward to the next successful event in the series, WorldPM2026, scheduled to take place in Montreal, Canada, June 25-29, 2026.
Author Nick Williams Managing Editor PIM International nick@inovar-communications.com
www.pim-international.com
April 8-10, 2025 | Huntington Place | Detroit, MI
Four world-class manufacturing events, together in one location
SME is bringing together these four events, providing access to more than 600 manufacturers while showcasing advanced manufacturing, smart technologies and mobility advancements. Combined Audiences, Magnified Impact!
At RAPID + TCT 2025, you’re under the same roof with SME’s AeroDef Manufacturing; SAE’s trademark mobility event, the World Congress Experience (WCX); and America Makes’ project success showcase, Technical Review & Exchange (TRX).
Claim your complimentary Expo Pass! Use promo code METALAM when registering
In September 2024, the 7 th International Conference on Powder Metallurgy and Additive Manufacturing of Titanium (PMTi2024) brought together experts from academia and industry in Madrid. Hosted by the Universidad Carlos III, the event featured considered PM titanium’s future, with insights into cost reduction, innovative processes, and material advancements. This article highlights key takeaways, with a particular emphasis on sinterbased processes and their industrial application. Dr Thomas Ebel presents a comprehensive review of the most notable insights.
From September 4-6, 2024, Professors Elena Gordo and Elisa Ruiz-Navas, alongside their organising committee, welcomed titanium specialists from the Powder Metallurgy community to Madrid for the 7 th edition of the International Conference on Powder Metallurgy and Additive Manufacturing of Titanium (PMTi2024). More than a hundred attendees from seventeen different countries considered the current status of titanium PM through papers presented in fifty-three oral presentations and twenty-five posters. Notably, 27% of the participants came from industrial companies.
The conference was hosted by the Universidad Carlos III de Madrid at its Puerta de Toledo campus. As in previous meetings, an increasing number of studies focused on Laser and Electron Beam Powder Bed Fusion (PBF-LB and PBF-EB). However, this article will focus largely on materials development and sinter-based processes, summarising key oral presentations.
One of the main issues discussed at PMTi is the relatively high cost
of titanium parts. Presentations on ways to improve this situation –either by the provision of lower-cost powders or cheaper, more flexible manufacturing – have been given at all past PMTi conferences. In his keynote talk, Prof Zak Fang from the University of Utah, USA, pointed
out that it is actually the combination of both lower-cost powders and processing which will prove to be the solution to the problem. Without adjustment in both areas, it will be impossible to enter new markets with PM titanium products or widen existing markets and applications.
Production of pure titanium dioxide (grades 1-4)
Production of titanium containing raw materials (grades 5-38 and other)
Ilmenite Spherical powder Irregular shape powder
Production of titanium containing raw materials (titanium based intermetallic grades)
Two-stage reduction of pure TiO2/TiO 2-alloying elements oxides solid solution
While low-cost powders are vital to future Ti market penetration, these powders still have to fulfil the common processing requirements for existing production processes. Vladislav Kruzhanov, a consultant at PM Consulting, based in Germany, reported on a study on the suitability of novel titanium powders for Metal Injection Moulding [1]. The study’s powders were produced by the Ukrainian company Velta LCC, which has been globally active in providing titanium raw materials since 2006.
The route to low-cost powders outlined in the paper involves two
steps. The first is a ‘waste-free’ method developed by Velta (Fig. 2) for transferring ilmenite concentrate into technical titanium dioxide, which serves as the base material for the extraction of metallic titanium (this is in contrast to the commonly applied Kroll process, which uses titanium tetrachloride). As well as pure titanium dioxide, these processes also produce other titanium-containing raw materials (e.g. intermetallics). The second step is to reduce these raw materials by putting them through a two-step deoxidation process wherein:
1. Mg vapour is used to remove around 80-90% of the oxygen
Magnesium hydroxide (flame retardant) Spheroidisation
Aluminium hydroxide (flame retardant)
Precipitated calcium carbonate Ammonium sulfate
Black iron oxide
Red iron oxide Yellow iron oxide
Veltilit BF (additive for iron and steel industry)
2. Ca vapour lowers the oxygen level further to 0.05-0.2 wt.%
All waste generated during the first step is converted into highvalue byproducts, contributing to environmental sustainability goals. Velta’s novel process is expected to lower the costs for titanium powders by 50-65% compared to the application of the Kroll process. Upscaling is currently under development.
In the study reported by Kruzhanov, titanium powders produced by the above process were used for further processing by MIM. Before covering this in more detail, it is important to note that the powders produced by the Velta process are typically roundish, but not an ideal
spherical shape. While it’s possible to apply a spheroidisation step, the extra cost means that this step is ideally avoided. The powder in the relevant study was used as-produced and sieved to a particle size smaller than 45 µm.
Two different feedstocks were manufactured: one based on watersoluble polyethylene glycol (PEG) and a backbone polymer, the other based on polyoxymethylene (POM) in connection with catalytic debinding. Both feedstocks were shaped by MIM into flat tensile specimens and discs. The sintered parts were then characterised with respect to density, microstructure, contents of O, N, C and H and the resulting mechanical properties.
Both feedstocks showed very good sintering behaviour, possibly favoured by a high percentage of very small powder particles (below 2 µm). The residual porosity amounted to 2-4%. The tensile tests revealed high strength of up to 600 MPa yield strength, though elongation was between only 3.4-4.0%. The probable reason for this is the relatively high levels of oxygen (0.3 wt.%), nitrogen (0.1 wt.%) and carbon (0.13 wt.%) of the sintered parts, significantly exceeding the values of the powders. Thus, the uptake of contaminants is due to debinding and sintering, something which should be able to be remedied by optimisation.
This study has shown that the powders produced by Velta’s fabrication process are suitable for MIM processing, even without undergoing further processing such as spheroidisation.
Ultimately, it is the price of a produced component that is relevant to PM’s customers, rather than that of the powders. So, where applicable, another approach for cost reduction is applying near-net-shape processing. Christian Doblin from CSIRO Manufacturing, Australia,
Fig. 3 A billet fabricated by Cold Spray Additive Manufacturing. Tensile test specimens with two different orientations were removed by wire cutting [2]
introduced a collaborative work with Boeing aimed at lowering the costs of titanium parts exposed to high temperatures [2].
The companies used Cold Spray Additive Manufacturing to manufacture Ti-6Al-2Sn-4Zr-2Mo-Si alloy (Ti-6242) pre-forms with a geometry close to the final shape of the components. One benefit of Cold Spray is that the microstructure will not change during processing because the powder is neither melted nor exposed to a heat treatment, only plastic deformation, because the particles are only in contact with hot gas for a short time. However, this deformation process can introduce residual stress into the component which can be critical to the application. Thus, one focus of this study was on minimising these residual stresses.
For the experiments, gas atomised alloy powder – nominally in the range of 15-45 µm – was used, though Doblin pointed out that plans are in place to use low-cost powders in the future. Two kinds of billets were manufactured: one smaller and one larger.
For the ‘small’ cylindrical billet, a pre-form was generated by axial growth CS using nitrogen gas at 900°C at 6.0 MPa and 4 m 3/h, with a powder feed of 480 g/h. The distance between the nozzle and the part was kept constant at 30 mm. After spray forming, the billet was machined to a diameter of 25 mm and a length of 76 mm. Because of the risks associated with supporting a large rotating mass from one end, the larger billet was built in two steps. First, a billet with a diameter of 34 mm and length of 250 mm was axially cold sprayed with 970 g/h and afterwards the free end was mounted in a rotating chuck. Then, the diameter was increased by radial spraying to 67 mm. The total mass was 3.0 kg and the build time was 133 minutes.
Analyses of the additively manufactured billets displayed homogenous microstructure and porosity of around 7%. The oxygen content increased from 0.08 wt.% of the powders to 0.14 wt.% in the final parts. Nitrogen increased from less than 0.01 wt.% to 0.04 wt.%. Tensile test specimens were fabricated from the large billets by wire cutting. As Fig. 3 illustrates,
two different orientations were tested, using radially and tangentially extracted samples. The radial specimens broke during handling, revealing a very weak joint between the central core and the outer deposited layer. The tangential specimens showed an Ultimate Tensile Strength (UTS) of 285 MPa and an elongation of 0.43%. These values are typical for cold-sprayed Ti-6242, but much lower
than the corresponding properties of wrought material.
To identify the reason for the weak bonding and facilitate up-scaling to larger dimensions, a digital twin of the Cold Spray Additive Manufacturing technology was developed. The digital twin follows a holistic approach and showcases a model of the nozzle, the particle at impact, the substrate temperature
profile and the residual stress inside of the final billet after cooling. The modelling results of particle velocity (a) and temperature (b) in relation to the distance between the powder injection point and preform surface are shown in Fig. 4.
There is a direct relationship between particle size and velocity: the smaller the size, the higher the speed. There is a peak temperature of 600°C for the particles 33 µm in diameter; for larger particles, that peak temperature decreases again, leading to insufficient deformation and bonding. Modelling also reveals that a distance of 25 mm between the nozzle and the preform surface instead of 30 mm could be beneficial for optimising the particle velocity.
Fig. 5 shows the analysis of the particles’ velocity compared to the critical velocity. The critical velocity v cr is the minimum velocity necessary for deposition; the data show that particles larger than 55 µm do not reach a velocity sufficient for bonding.
Further modelling was performed to analyse surface temperature and residual stress (RS) after cooling. In this case, the behaviour of a larger diameter of 130 mm was simulated. The calculations showed that a
surface temperature of about 300°C is achieved by the given processing parameters. The RS in the interface between core and deposited layer amounts to around 390 MPa depending on the diameter of the billet. The larger the diameter, the higher the RS and the broader the RS zone. However, if the large particles can achieve better densification and fewer pores, the residual stress should not be an issue. The UTS of the wrought material is 1,100 MPa.
In summary, Doblin showed that Cold Spray AM appears to be a suitable technique for manufacturing large preforms from Ti-6242. Furthermore, a holistic digital twin is a valuable tool for understanding critical processing parameters and for up-scaling the process towards larger components. In particular, it was revealed that the working distance should be decreased and larger particles should be removed.
Another topic of several talks was the strengthening of material without affecting ductility, for example by adding small particles to create Metal Matrix Composites (MMC). In his presentation, Carl Boehlert from Michigan State University, USA, discussed the dependence of Ti-6Al4V-1B‘s mechanical properties – in
particular fatigue and creep – on the processing route [3]. Boron is a typical Ti-6Al-4V additive, enhancing its strength by forming titanium boride particles, which leads to grain refinement. Boehlert compared casting, casting and extrusion (CE), powder rolling (PM rolling) and powder extrusion (PM extrusion). For PM rolling, pre-alloyed powder was HIPed (3 h at 1,018°C and 103 MPa) and rolled after an additional heat treatment (6 h at 1,300°C). After three rolling passes, the plate was annealed for 1h at 760°C. In the case of PM extrusion, the powder was first packed and heated at 1,200°C for one hour, subsequently pressed at 1,200°C for 180 seconds at 1,400 MPa, air-cooled to room temperature, and finally extruded at 1,100°C with an extrusion ratio of 16:1. Fig. 6 shows
the microstructures of the two differently processed materials. As is visible in the micrographs, the titanium borides in the rolled material appear randomly oriented while there is a clearly visible alignment in the extruded material. Further, the rolled alloy shows a duplex structure consisting of lenticular α + β ( α -lath: 2.7 µm) and equiaxed α -phase (7.4 µm). Fine equiaxed α is the microstructure of the extruded material with a grain size of 3.6 µm. Boehlert explains the possible mechanism: during hightemperature extrusion, the β phase is aligned and, during the transformation into α , this alignment is adopted. XRD analysis revealed almost no texture in the rolled material, while, the extruded example showed the texture of both α with the basal plane
“...Doblin showed that Cold Spray AM appears to be a suitable technique for manufacturing large preforms from Ti-6242. Furthermore, a holistic digital twin is a valuable tool for understanding critical processing parameters and for up-scaling the process towards larger components.”
Fig. 7 Tensile test results of the Ti-6Al-4V-1B alloy processed by different routes, explained in the text [3]
Fig. 8 Fatigue test results of the Ti-6Al-4V-1B alloy processed by different routes, explained in the text [3]
Fig. 9 Creep test results of the Ti-6Al-4V-1B alloy processed by different routes, explained in the text [3]
perpendicular to the extrusion direction and the TiB particles. This texture led to the anisotropy of the tensile properties and a significant increase in Young’s modulus in the extrusion direction (117 GPa compared to 103 GPa for the as-cast alloy).
Fig. 7 compares the tensile properties at 455°C for the different processing routes. Compared to as-cast Ti-6Al-4V, it is obvious that both adding boron and extrusion increase the strength drastically. However, when extrusion is applied, cast and PM material show almost the same tensile properties.
The fatigue behaviour was tested at 455°C, R=0.1 and 5 Hz, and the runout was considered to be larger than 1 million cycles. In contrast to its tensile properties, Fig. 8 reveals that the PM extruded material is superior to the cast and extruded alloy. The reason is probably the fine equiaxed microstructure of the PM extrusion material, which is known to be beneficial for both low cycle fatigue (LCF) behaviour and fatigue resistance.
Finally, Fig. 9 shows that – as far as creep properties are concerned –the existence of the lenticular α phase is beneficial as it exists in both cast and extruded material. The latter one reveals the highest creep properties. To summarise, the study shows that adding boron to a Ti-6Al-4V alloy increases the beneficial properties and that PM-processed material could replace Ti-6Al-4V at both room and elevated temperatures.
Strengthening by the introduction of hard particles is especially effective when the particles are on the nanoscale. In this case, smaller additions are sufficient, and the effect on ductility is less pronounced. José Manuel Martín from CEIT-Basque Research and Technology Alliance, Spain, spoke on safe – and comparatively simple – routes to manufacture nanoparticle-reinforced titanium alloys with only a small loss in ductility [4].
To determine an optimised composition of the final alloy, the authors used Ti-6Al-4V as the master alloy powder, mixed with elemental carbon and silicon powders (carbon is known to form titanium carbides if the solubility of the matrix is exceeded; these carbides lead to higher strength, while silicon enhances the creep resistance by forming Ti 5Si 3 particles). After mixing, one part of the powders was HIPed while the other part was only sintered. Then a few of the samples were heat-treated.
The titanium alloy powder had a particle size smaller than 100 µm, and was produced using Electrode Induction Melting Inert Gas Atomisation (EIGA); the oxygen content was only 0.08 wt.%. Synthetic graphite powder and 99.5% pure silicon powder – with a size smaller than 45 µm – were added. The powders were blended in a tubular mixer utilising alumina balls.
To investigate the combined effect of C and Si, three compositions were selected. While the carbon content was kept constant at 0.15 wt.%, the silicon content varied at 0, 0.15 and 0.3 wt.%, respectively. Both sintering and HIPing were performed at 930°C for 4 h. The applied HIP pressure was 140 MPa. The heat treatment
consisted of a solution treatment at 925°C for 1 h under Ar with subsequent water quenching following precipitation ageing at 480°C for 8 h under Ar. All parameters were chosen such that the coarsening of precipitates – as well as the possibility of forming of α ’ martensite due to fast cooling – were avoided. Indeed, neither martensite nor Ti-carbides nor Ti-silicides could be detected by SEM and XRD. Fig. 10 shows micrographs of the HIPed compositions. Fig. 11 shows the microstructures after the described additional heat treatment.
Although no particles could be detected, the addition of C and Si clearly affected tensile tests. Table 1 summarises the impact of Si additions on Ti-6Al-4V + 0.15 C and on heat treatment. The respective data for the pure alloy are also listed as a reference.
In particular, the heat-treated Ti-6Al-4V-0.15C-0.15Si shows very high performance and a significant improvement in strength without any loss in ductility compared to the pure Ti-6Al-4V alloy. Martín explained that the drastic drop in ductility for the heat-treated
2- θ [degrees] (a) (b) 2- θ [degrees]
composition with 0.3 wt.% Si was probably due to the incomplete dissolution of silicon into the matrix during the heat treatment (i.e. Si concentration exceeded the solubility limit of the matrix), leading possibly to the excessive, unfavourable precipitation of titanium silicide nanoparticles. Their detection of these mechanisms and a more thorough understanding of the strengthening processes will be addressed in the objectives of the upcoming studies.
Future studies plan to add processes such as Additive Manufacturing in order to produce actual components. For example, by utilising the EIGA technique, the HIPed rods could be atomised to powder. The study is part of the NANOTUN3D project funded by the European Union.
The impact of oxygen on mechanical properties is a topic fundamentally connected to the processing of titanium powders. Despite a number of research studies and collected practical experience, there are still many unanswered questions regarding fundamental mechanisms and the exact relationships between oxygen content and mechanical performance. Oxygen is commonly regarded as a strong cause of embrittlement. Published guidance generally suggests avoiding it as much as possible. However, in recent years, there has been a slow change in perception: oxygen has become regarded as a very valuable – and
cheap – alloying element when introduced into a titanium alloy in a controlled way. Fascinating research is underway, focusing on the role of oxygen at the atomic level.
At PMTi2024, Prof Ma Qian from the RMIT University in Melbourne, Australia, presented a related study on the effect of oxygen on the tensile properties of a biomedical alloy based on the elements Ti, Nb, Zr and Ta. Previously, Qian had spoken about very detailed studies on the impact of interstitial elements on the mechanisms of strengthening and plastic deformation. This year, he had planned to speak about strong and ductile titanium alloys with high levels of interstitials, but a related study by his group was submitted for publication in the interim, causing him to change the topic.
The biomedical alloy Qian reported on at PMTi2024 was a high-entropy alloy (HEA) with a composition of Ti-40Zr-25Zr-25Nb-10Ta (all values in at.%) [5]. It was deduced from the equiatomic TiZrNbTa HEA by replacing 15 at.% Ta with 10 at.% Ti. The resulting effect was a reduction in lattice distortion, leading to a significantly higher tensile ductility (18% compared to 1.24%), but lower strength (yield strength of 875 MPa compared to 1,100 MPa). Compared to a typical cast Ti-6Al-4V alloy, both values are still higher, with the benefit of a lower Young’s modulus (77 GPa compared to 110 GPa).
The aim of the presented study was to gain higher yield strength by adding oxygen whilst maintaining good tensile ductility, with the goal of expanding the choice of feedstock materials for the alloy. For this, the alloys were cast with additions of 0.5, 1.0 and 2.0 at.% oxygen, respectively. The X-ray Diffraction (XRD) results in Fig. 12 reveal that, for all alloys, only β phase could be detected. Further, the lattice’s obvious dependence on constant oxygen content is evident, proving that the oxygen atoms occupy interstitial lattice sites. No compounds were formed. Further investigations by Scanning Electron Microscopy (SEM), backscattered electrons mode (BSE) and Electron
Backscatter Diffraction (EBSD) detected no significant differences between the different oxygen-doped alloys.
Transmission Electron Microscopy (TEM) and Scanning Transmission Electron Microscopy (STEM) investigations revealed a homogeneous distribution of all principal elements. For a more detailed examination, Atom Probe Tomography (APT) was performed. The results, shown in Fig. 13, further confirm a homogenous elemental distribution, including oxygen atoms in the selected grain area, with no clusters visible. However, the tensile tests uncover the expected dependence on oxygen content. Results are shown in Fig. 14 and reveal a significant increase in strength and a decrease in ductility as the typical effect of high oxygen levels. In comparison to the un-doped alloy, pronounced discontinuous yielding can be observed for all oxygen-doped alloys as an indication of dislocation pinning by oxygen atoms or insufficient mobile dislocations.
To understand the differences in plastic behaviour, the authors investigated the underlying deformation mechanisms as a function of oxygen content by TEM. Fig. 15 shows that dislocations, shear bands and spots of dislocation pinning (yellow arrows) were detected for the alloys with 0.5, 1.0 and 2.0 at.% oxygen, respectively. A comparison of the images reveals a proportional change in the formation of shear bands and dislo
Ti(O): Metallic
Ti(II): TiO
Ti(III): Ti2O3
Ti(IV): TiO2
cation pinning to planar slip with the increasing oxygen content of the alloy. This explains the differences in mechanical properties. At 0.5 at.% oxygen, plastic deformation occurred with prevalent dislocation pinning and dislocation loops. In contrast, at 2.0 at.% oxygen content, primary shear bands were less prominent and did not exhibit secondary shear bands. Instead, planar slip bands became the dominant feature, which is typical for brittle deformation behaviour.
The alloy with 0.5 at.% oxygen added appears to be a very promising candidate for biomedical applications. Its Young’s modulus is only slightly higher (79.2 GPa) than that of the un-doped alloy (77 GPa) and much lower than that of Ti-6Al-4V (110 GPa) while offering a tensile
ductility of about 12% and a yield strength of about 950 MPa in the as-cast condition. Further, the first electrochemical evaluation indicated a corrosion resistance comparable to that of Ti-6Al-4V.
Louis-Philippe Lefebvre from the National Research Council Canada also presented the results of a study related to oxygen in titanium alloys [6]. In contrast to the previous study, the goal of this work was to investigate the effect of oxygen located on the surface of powder particles. This relates to practical considerations regarding how the storage and handling of the powders during
“The alloy with 0.5 at.% oxygen added appears to be a very promising candidate for biomedical applications. Its Young’s modulus is only slightly higher (79.2 GPa) than that of the un-doped alloy (77 GPa) and much lower than that of Ti-6Al-4V.”
processing impact both the manufacturing process and the properties of the final parts. The authors of the study provided detailed insights into the evolution of the surface layer with respect to oxygen, carbon and moisture. In the second step, the influence of this layer on flowability and Additive Manufacturing was examined.
Lefebvre’s talk began with a detailed analysis of the surface layer, the basic structure of which is shown in Fig. 16. In the study, the exact composition of the layer was analysed by a number of processes such as TEM, Electron energy loss spectroscopy (EELS), STEM, Auger spectroscopy, X-ray photoelectron spectroscopy (XPS) and moisture analysis. The analysis shows that the surface of titanium powder is composed of small amounts of water, carbon (adventitious carbon: inorganic and hydrocarbons coming from the surrounding air and present on most surfaces observed with Auger and XPS), titanium (Ti xO y; Ti(OH) x), oxygen (Ti xO y; Ti(OH) x), hydrogen (10 ppm in total), aluminium (on Ti-6Al-4V), but no traces of vanadium (on Ti-6Al-4V).
Earlier studies show that storage over several months or years does not influence the oxygen content of titanium powders. In contrast, with regard to moisture, the study
Fig. 17 (Left) Increased water content of cp-Ti powder after conditioning at 20°C and 80% relative humidity. (Right) Removal of water by exposing for 24 h in an anhydrous lab (middle bar) and after 1 h at 200°C under vacuum (right bar) [6]
presented by Lefebvre revealed a different behaviour: the rather fast uptake of moisture at the powder particle surface. The water molecules can be bound in a chemisorbed as well as in a physisorbed manner. Because the amount of adsorbed water depends on a particle’s surface area, particle size and geometry play an important role.
The thickness of the layer in the paper was measured to be a few nanometers; adsorption is slower if the powder is not fluidised, as water has to diffuse through the bulk of the powder. Fig. 17a shows the increased water content in a small amount (2 g) of 0-25 µm cp-Ti powder after conditioning in a 30 ml glass bottle at 20°C and 80% relative humidity. Fig. 17b reveals that the moisture can be removed again by storage in a dry room or heating. Heating for 1 h at 200°C under a vacuum helps to reduce moisture content, but does not sufficiently remove all the water (the water content analyses were conducted at 260°C).
Interestingly, analysis of the oxygen and hydrogen content of the powder particles did not detect any significant changes related to moisture adsorption. The flowability of the powders was shown to decrease with increasing humidity. However, a comparison of the as-received Ti-6Al-4V powder and the same powder stored for three weeks under 70% relative humidity showed
“In contrast, with regard to moisture, the study presented by Lefebvre revealed a different behaviour: the rather fast uptake of moisture at the powder particle surface.”
that this appears not to be relevant for the fabrication of parts. Both powders were processed by Laser Beam Powder Bed Fusion and no significant differences were observed during the manufacturing, in the final parts, nor in the mechanical properties. In contrast, if the powders are re-used, an increase in oxygen content can be detected with each recycling step. This increase is especially prominent when processing via PBF-EB, although PBF-LB results in a significantly smaller increase. This difference is probably due to the higher process temperatures in PBF-EB promoting the uptake of oxygen from the atmosphere.
The flexibility of sinter-based Additive Manufacturing technologies is well accepted. Many different shaping
processes can be applied, with the majority originating in the processing of polymers. At PMTi2024, a number of examples of sinter-based Additive Manufacturing processes were given.
production
(DIW) Tània Vilella, from Universitat Politècnica de Catalunya in Barcelona, Spain, reported on the fabrication of biomedical scaffolds by Direct Ink Writing (DIW), a variant of the Material Extrusion (MEX) process [7]. Aiming at developing a particularly biocompatible alloy with potential shape memory properties, Vilella utilised a mixture of elemental titanium and niobium powders to create Ti-Nb alloys. The challenges involved identifying suitable processing parameters for manufacturing scaffold structures with thin struts and for the consolidation of the elemental powders into parts with the required mechanical properties
and density. Niobium is known as a slow diffuser, meaning the sintering temperature is a critical factor.
For DIW, the powder is mixed with a binder and a solvent to create a homogenous ink with controlled rheological properties. A green part is additively manufactured based on a CAD model and then dried to remove the solvent. After this, the part undergoes debinding and sintering to achieve the final part.
For the study presented by Vilella, 75 wt.% Ti+Nb powders were mixed with the binder Pluronic F-127 in water to form an additively manufacturable hydrogel. The machine’s nozzle diameter was 410 µm and the layer height was 350 µm. After drying, debinding took place at 275°C for twelve hours with subsequent sintering under vacuum and argon purging for 2 h. The sintering temperature was varied between 1,200-1,400°C. Fig. 18. shows an example of the additively manufactured scaffolds. The strut size was about 300 µm.
Vilella chose pure Ti, Ti-15Nb and Ti-30Nb for the compositions. In Fig. 19, shrinkage depends on both the sintering temperature and the composition. Niobium diffuses slowly; thus, a sintering temperature of 1,400°C appears necessary in order to achieve the desired density and complete solution of the niobium. The investigation showed that the titanium diffused into the niobium powder particles rather than the other way around. Fig. 20 shows the microstructure of the three materials sintered at 1,400°C.
The study showed successful DIW Additive Manufacturing and sintering of the blended powders to scaffolds. First cell viability tests proved promising biocompatibility.
Over the past decade, the application of the Vat Photopolymerisation (VPP) process (the ISO/ASTM 52900 for stereolithography) on a paste containing fine metal powders has become increasingly popular among sinter-based AM processes. Referred to as Lithography-based Metal Manufacturing (LMM) by machine suppliers such as Austria’s Incus GmbH, the process is capable of producing extremely small and detailed structures (Fig. 21) with high accuracy in an acceptable timeframe. However, because of the necessary light-sensitive polymers, the binder composition is rather complex. For the formulation of titanium feedstocks, comparatively simple polymers such as polyethylene or polypropylene are often selected because of their good removability during debinding
with the titanium only seeing a small uptake of carbon. This issue means that the binder used successfully for the LMM of stainless steel does not work well for titanium powders. Santiago Cano Cano, from Incus, summarised a comprehensive work on this issue, with the goal of developing an appropriate LMM binder for titanium [8].
LMM binders are based on crosslinked thermosets and typically consist of photocurable resins, solidification agents, photoinitiators and other additives. The powder load is in the range of 50-60 vol.%. Crosslinking means that rather high
decomposition temperatures are necessary, though these leave higher char contents than, for example, in the case of Polymethyl-methacrylate (PMMA)-containing binders. For titanium, this means high levels of interstitials (carbon and oxygen) in the sintered parts, resulting in high tensile strength but low plastic elongation. Although this combination of properties is sufficient for many applications, some applications need higher deformability of the part. Cano Cano explained the binder development process as one of multiple steps. First, a suitable monomer has to be found. For this,
“For the formulation of titanium feedstocks, comparatively simple polymers such as polyethylene or polypropylene are often selected because of their good removability during debinding with the titanium only seeing a small uptake of carbon.”
different monomers were analysed by TGA with respect to their char residue after heating. The goal was to find simple monomers with low decomposition temperatures for the corresponding polymer. These same monomers were then tested in a sintering experiment, and the carbon content of the sintered part was analysed. Ultimately, the most promising monomer was selected.
In a second step – due to the high polymerisation shrinkage of this selected monomer – a second monomer was added to limit the overall shrinkage of the part, something which could decrease the achievable accuracy of the LMM process.
During the third step, a special adaption of the powder was utilised, which led to a better recyclability of the feedstock and lower carbon and oxygen content of the sintered parts. The density achieved was around 98% of the theoretical one, the carbon content was 0.15 wt.% and oxygen content was 0.31 wt.%.
The fourth step was to find out the best solvent, which was discovered to be acetone. Compared to ethanol and water, acetone removed the highest amount of the binder, leading to the lowest deformation during drying.
In the final optimisation step, the soluble fraction of the binder was increased, leading to higher sintering density and less distortion. Accordingly, tensile test specimens were fabricated and tested. Table 2 shows the current properties provided by the authors after the conference. Compared to those shown in the presentation, they are similar, though improved with regard to reproducibility.
It is obvious that the novel binder makes it feasible to manufacture parts with very good properties by LMM. However, the ductility still varies from part to part and could be improved. This variation might be due to the still-high level of interstitials, especially of carbon. Improvement will be the focus of further work.
“It is obvious that the novel binder makes it feasible to manufacture parts with very good properties by LMM. However, the ductility still varies from part to part and could be improved. This variation might be due to the still-high level of interstitials, especially of carbon.”
LMM was also the focus of the study presented by Lucas Vogel, Head of R&D at MetShape GmbH, Germany [9]. However, he developed a process for manufacturing parts from NiTi by LMM. NiTi is an alloy well-known for its pseudoelastic and shape-memory properties, making it particularly suitable for dedicated applications like medical instruments and devices, as well as for actuators in the automotive and aerospace fields.
NiTi is rather difficult to process by conventional methods, requiring multiple production steps. While LMM could be a way to manufacture complex and detailed parts at lower costs, the challenges for the binder are the same as described for titanium alloys. To achieve the desired mechanical properties, chemical composition and phase distribution have to be kept very precisely. This is a very challenging requirement when binders and sintering are applied, as in LMM.
Initially, the paper suggested that the powders could be processed into parts with high geometrical accuracy and sintered to densities higher than 97%. However, the carbon content was very high (more than 1.2 wt.%), the same for oxygen (more than 0.7 wt.%) and unwanted phases like titanium carbides and titanium-nickel oxides were formed.
The first step of optimisation was to select an adequate powder, ideally one produced by EIGA. However, even this powder had an initial oxygen content of 0.06 wt.%, which exceeds
the standard ASTM F2663 of the material, demanding a limit of 0.05 wt.%. For feedstock production, 55 vol.% powder was used. The binder was developed by careful evaluation of the individual ingredients, as described in the prior paper. As a result, the decomposition start temperature could be reduced from about 350°C to 270°C.
After adapting the build parameters to the properties of the novel feedstock, a debinding strategy based on the evaluation of thermal, catalytic and solvent debinding mechanisms was developed. Similar to the previous study, acetone turned out to be the best agent leading to a reduction of the carbon level of the sintered parts by 0.3 wt.%. Sintering parameters were also optimised; sintered densities achieved were better than 96% of the theoretical density. The results of tensile tests on samples produced by using this novel strategy are shown in Fig. 22 and Table 3.
Comparing the measured properties with the requirements from the ASTM standard reveals that the LMM-produced material shows sound properties, but does not reach the standard in all cases. In particular, the Young’s modulus is too low, UTS is not high enough and the typical plateau in the stress-strain curve is missing.
Vogel explained these differences on the basis of performed analysis of chemical composition and microstructure. The required phase distribution is not precisely met and the formation of detrimental Ni 4Ti 3 particles can be observed. Further, carbides and oxides still exist and cracks perpendicular to the load direction during testing can be found. However, the reduction of oxygen and carbon content after performing this study
was drastic. Oxygen was reduced to values smaller than 0.27 wt.% and carbon smaller than 0.14 wt.% –almost a tenth of the original value. This very promising data will be further built on in upcoming studies. Vogel pointed out that the evaluation of applications with customers is already ongoing.
Tim Marter from Element 22 GmbH, Germany, also discussed LMM in his presentation [10]. He showed a comparison of geometrical, chemical and mechanical properties of sintered parts processed by LMM, MIM and Cold Metal Fusion (CMF). CMF uses
feedstock granules processed on a Powder Bed Fusion machine, usually one intended for polymer Additive Manufacturing. Similar to LMM and MIM, the resultant green parts are debound and sintered. While MIM is the most suitable for the mass production of comparably small, complex parts and LMM for intricate parts, CMF is capable of producing rather large parts (e.g. bicycle components).
Marter started his talk with a comparison of geometrical capabilities, particularly in terms of creating sharp edges. Fig. 23 shows clearly that MIM can produce very sharp edges, while LMM creates small radii to the edge. CFM forms a sharp –
Table 4 A comparison of typical oxygen and carbon contents of sintered parts in dependence on production technique compared to standard values [10]
Interestingly, PMTi2024 featured four talks centring on titanium aluminides; intermetallic alloys with a high aluminium content (around 45 at.%), mostly for lightweight applications at high temperatures. These titanium aluminides are difficult to process conventionally. Today, PBF-EB is often used to process these, but sinter-based processes could potentially lower the associated manufacturing costs.
Table 5 Comparison of typical values for sintered density and tensile properties as a function of production process, compared to standard values. Green means the requirements are fulfilled [10]
though not clearly defined – edge. The same is true for top-down holes: MIM produces sharp edges at both the top and the bottom; LMM, only at the bottom; and CFM has less sharp and defined edges. Furthermore, the surface roughness tends to be lowest when MIM is used (Ra 1 µm), compared to LMM (Ra 2 µm) and CFM (Ra 7 µm).
Tables 4 and 5 compare the typical range of interstitial content and mechanical properties, respectively, of the three processes. The limits of these properties are those outlined by ASTM F-2885-17, the relevant
standard for medical Ti-6Al-4V parts made by MIM. Obviously, only MIM can fulfil both chemical and mechanical requirements for medical parts. However, excellent mechanical properties can be achieved in all cases.
In his talk, Marter showed that, to date, several binder-based sintering processes are considered productionready when working with titanium. Which one is best for a specific application must be decided upon based on a part’s individual geometry, required properties, necessary standards fulfilment, and – of course – cost.
“...Marter showed that, to date, several binder-based sintering processes are considered production-ready when working with titanium. Which one is best for a specific application must be decided upon based on a part’s individual geometry, required properties, necessary standards fulfilment, and – of course – cost..”
In his presentation, Wolfgang Limberg from Helmholtz Zentrum Hereon, Germany, discussed the use of spherical TNM (Ti-43.5Al-4Nb1Mo-0.1B, in at.%) powder, atomised in-house by EIGA and sieved to a particle size smaller 20 µm [11]. The oxygen content was 698 µg/g. The study compared the properties of parts made by MIM and a pelletbased Material Extrusion process, in this instance referred to as Fused Granular Fabrication (FGF).
Pellet-based MEX is an almost perfect complement to MIM because identical pellet feedstocks can be used for both processes. This allows users to additively manufacture prototypes or a small series, so they can test the functional performance of parts before ordering an expensive MIM mould. The main subject of Limberg’s presented study was to check how comparable the final properties actually are.
Applying both processes, Limberg fabricated dog-bone-shaped tensile test specimens and cylindrical samples for compression creep tests. For a binder, he mixed 35% PE-EVACopolymer, 60% paraffin wax and 5% stearic acid; the powder load was around 66 vol.%. The feedstock was prepared in-house and pellets in a diameter range of 1-3 mm were fabricated and used for both injection moulding and Additive Manufacturing. All green samples were processed in the same way: debound in hexane and sintered under vacuum furnace at 1,500°C for 2 h under 300 mbar Ar. Sintering took place around the solidus temperature of the alloy.
The forming liquid phase promoted sintering. Thus, a final density of 99.7% could be achieved.
Because of the high sintering temperature, titanium-aluminides tend to lose aluminium in the surface-near region by evaporation. Therefore, a special sintering set-up, as displayed in Fig. 24, is used. A vapour barrier with a Ti-50Al (at.%) part as an Al-source provided an aluminium-containing atmosphere around the samples, which limited Al depletion in the samples. The result was a homogenous microstructure in both MEX and MIM samples (as shown in Fig. 25).
There is no visible difference in the microstructure of the samples shaped by the two different processes. A former study on Ti-6Al-4V revealed that FGF-fabricated specimens showed build defects like elongated pores between the layers. In contrast, no defects were found in the FGF production of the TNM alloy. The reason might be the liquid phase, formed during sintering, may have helped close pores and small defects.
Fig. 26 shows the results of tensile tests. The MIM samples appear to perform slightly better. One reason could be the different oxygen content; while the oxygen level of the MIM samples was determined to be 1,834 µg/g, the content in the FGF specimens amounted to 2,195 µg/g. Plastic elongation of the MIM specimens was 0.19% at room temperature, which is an acceptable
value for titanium-aluminides. The strength was comparable to that of cast material.
Preliminary creep tests reveal a similar tendency (Fig. 27). MIM and FGF materials show comparable results, though the MIM material performs slightly better. This could be because of the higher oxygen content and hidden defects in the FGF samples.
Our final presentation on tailored microstructures was from Benoît Fer from Université Sorbonne Paris Nord, France [12]. He reported on a study that aimed to create a dedicated microstructure in the Ti-24Nb-4Zr-8Sn alloy.
Ti-24Nb-4Zr-8Sn is a metastable β -titanium alloy, primarily intended for use in biomedical implants. Again, the goal here was to enhance the strength without sacrificing ductility. The approach of Fer and his co-authors was to produce a so-called ‘harmonic microstructure’ consisting of regions of larger grains (‘cores’) within the network of fine grains (‘shells’).
In the study, ball milling of pre-alloyed, gas-atomised powder particles in the size range of 100-160 µm was used to create a fine microstructure at the surface of the particles by severe plastic deformation. After ball milling, Spark Plasma Sintering (SPS) was used for consolidation. In Fig. 28, micrographs after SPS are shown as a function of ball milling time. The SPS parameters were kept constant at 800°C for 30 min at 100 MPa pressure.
After the first trials, it was discovered that oxygen uptake during ball milling led to the formation of α -precipitates. Thus, another experiment wherein ball milling was performed for 50 hours within a vacuum. The result – shown in Fig. 29 – reveals the desired harmonic network structure with two distinct grain size ranges. In this case, only a very small amount of α phase was detected by XRD measurement.
Tensile specimens were fabricated and tested from this material. Fig. 30 shows a significant increase in strength compared to the material that was not ball-milled. Furthermore, as desired, the ductility appears not to have been affected.
Further, the authors investigated the deformation mechanisms by interrupted compression tests and analysis of the evolution of dislocations. It appears that the deformation mostly happens in the interface between the core and shell and that Geometrically Necessary Dislocations play an important role in the improved mechanical behaviour. The study shows that the chosen processing route is capable of creating a harmonic structure, enhancing the materials’ strength without loss of ductility. The ball milling parameters turned out to be a crucial parameter.
This article covers only a small excerpt of all the oral and poster presentations at PMTi2024. Titanium Powder Metallurgy is a living topic in research and industry, continuing to raise fundamental questions. Despite
the successful laser and electronbeam-based processing technologies, sintering continues to prove its relevance and possible expansion in the field. The main reasons for this are the potential for lower costs and more flexibility.
At the end of the conference, it was announced that the next PMTi will take place in Taipei City, Taiwan, in 2026. This promises to be another exciting opportunity to connect with those passionate about titanium alloys and gain an insightful perspective on the industry’s future.
Author
Dr Thomas Ebel Head of Powder-Based Material Development
Helmholtz-Zentrum Hereon
Max-Planck-Straße 1 21502 Geesthacht Germany
thomas.ebel@hereon.de www.hereon.de
[1] Vladislav Kruzhanov et al., Suitability of Novel Titanium Powder for Metal Injection Moulding Application
[2] Christian Doblin et al., Large titanium preforms manufactured by cold spray
[3] Carl Boehlert et al., Characterization of the Microstructure, Tensile, Fatigue, and Creep Behavior of Powder Metallurgy Processed Rolled and Extruded Ti-6Al-4V-1B(wt.%) Alloys
PMTi2024 conference review
[4] José Manuel Martín et al., Improvement of the mechanical properties of a P/M Ti-6Al-4V alloy with additions of carbon and silicon
[5] Ma Qian et al., Strong and ductile titanium alloys containing high interstitial elements
[6] Louis-Philippe Lefebvre et al., Effect of surface on the properties of titanium based powders
[7] Tània Vilella et al., TiNb-based Shape Memory Alloy Scaffolds produced by Direct Ink Writing
[8] Santiago Cano Cano et al., Development of Materials and Processes for the Lithography-Based Metal Manufacturing of Ti6Al4V
[9] Lucas Vogel et al., Advances in Lithography Based Metal Manufacturing of Nickel Titanium Alloys
[10] Tim Marter et al., Comparing Lithography-based Metal Manufacturing for Titanium with established processes such as Cold Metal Fusion
[11] Wolfgang Limberg et al., TiAl powder based Fused Granular Fabrication (FGF)
[12] Benoît Fer et al., Microstructural and mechanical optimization of a harmonic structured Ti 24Nb 4Zr
8Sn processed through Powder Metallurgy
Filament-based Material Extrusion (MEX), also known as Fused Filament Fabrication (FFF), combines cost efficiency with versatility, enabling the rapid prototyping of complex geometries. When used with Reverse Engineering and digital scanning technologies, could the technology play a role in the supply of discontinued legacy metal parts? Here, Sihan Zhang, Saleh Khanjar, Srimanta Barui, Kameswara Pavan Kumar Ajjarapu, and Kunal Kate from the University of Louisville; Lauren Shackleford of the University of Kentucky; and Andrew Pierce, GE Appliances, report on the process undertaken to produce a discontinued stainless steel helical gear.
Filament-based Material Extrusion (MEX), widely known as Fused Filament Fabrication (FFF), is a desktop-scale Additive Manufacturing process often used for rapid prototyping [1, 2]. As the name suggests, filaments are the feedstock for FFF; these filaments are created by blending metal powders with a polymer binder. As with parts produced by Metal Injection Moulding, after the build process the parts undergo debinding and sintering, resulting in a near 100% dense component that is smaller in size from the ‘green’ part due to the loss of polymer and binder agents [3-7].
Additive Manufacturing enables the production of complex geometries able to meet the design and requirements of a targeted application. While Additive Manufacturing processes such as Binder Jetting [8-10], Laser Beam Powder Bed Fusion (PBF-LB) [11, 12] and Electron Beam Powder Bed Fusion (PBF-EB) [13, 14] are capable of engineering components with an impressive resolution, filamentbased AM offers a cost-effective
and rapid fabrication process with a more moderate resolution. It is worthwhile to point out that the future of replacing legacy components may lie in Additive Manufacturing. This is especially true when looking to match the geometric details of convention -
ally manufactured components for which designs are not currently available, such as those made by companies that have long since closed down. Quantitative AM scanning allows the archiving of digital twins of these legacy parts in case of unpredicted failure.
Fig. 1 Filament-based metal Additive Manufacturing offers a cost-effective path towards the production of legacy parts
“The hand-in-hand quantum leap of Computer Aided Design (CAD) and AM over the past two decades has bolstered Reverse Engineering (RE), enhancing the processes’ precision, reliability and affordability. Today, it is quite straightforward to acquire 3D scanned data of a physical structure –regardless of its complexity.”
The hand-in-hand quantum leap of Computer Aided Design (CAD) and AM over the past two decades has bolstered Reverse Engineering (RE), enhancing the processes’ precision, reliability and affordability. Today, it is quite straightforward to acquire 3D scanned data of a physical structure – regardless of its complexity. A laser-based 3D scanner (recording the 3D point clouds and reconstructing them in a CAD file) only gathers surface data, while a volumetric scan using X-ray Computed Tomography (CT) – in this case, micro-CT – captures the outer as well as the inner intricacies of the three-dimensional body [15-18].
The University of Louisville-led AM accelerator focuses on using Additive Manufacturing to produce stainless steel legacy parts in support of small manufacturing businesses. The National Institute of Standards and Technology Manufacturing Partnership (NIST-MEP) works with companies to survey a conventionally manufactured parts catalogue, create a business case, and identify legacy parts that small companies can manufacture using AM. These organisations are working together to enable the widespread adoption of FFF as a reliable technology for the production of spare and/or replacement parts.
Wang et al. presented an example of how Reverse Engineering and Additive Manufacturing were used in fabricating subject-specific head gear [19]. A life-size human head was scanned with a 3D scanner; the collected information was then used to develop a CAD model of the helmet based on the cranium’s specific geometric details. The generated CAD was sliced and imported to a filament extrusion Additive Manufacturing machine for production, using polylactic acid (PLA) as the binding agent.
In a similar work, Baronio et al discussed the feasibility of Reverse Engineering and AM in developing patient-specific orthosis devices [20]. In this work, the wrist and fingers of a human forearm were 3D scanned. Using a rapid (less than 2 h) processing protocol, a CAD model of the orthosis device was developed before it was fabricated on a low-cost FFF Additive Manufacturing machine.
Using a more advanced approach, one of the authors’ groups combined a novel Reverse Engineering solution with Binder Jetting to reconstruct the cranial vaults of patients compromised in decom -
pressive craniectomy [21]. The partially missing cranial vault was scanned by CT and developed into a computer-aided design. Using CAD editing software, the skull defect was able to be repaired for the individual patient, with the bone ‘patch’ created by casting acrylic bone cement in a ceramic Binder Jetted skull mould. These synthetic bone patches are designed to preserve the patient’s specific facial features and were provided to neurosurgeons prior to medical-grade sterilisation and implantation. The chemical and mechanical properties of the synthetic bone patches were also quantified.
Helle et al . demonstrated a case study on the development of the additively manufacturable CAD design of a cylindrical engineering component [22]. To mimic environmental degradation, researchers applied rough coating to the component before 3D scanning to assess the effectiveness of the CAD reconstruction process in the presence of surface damage. Using a multi-surface reconstruction technique, the study found that the scanning and point cloud processing steps were relatively straightforward. However, the surface reconstruction step was comparatively complex and time-consuming.
Helle et al . noted that RE is especially useful when dealing with complex, non-trivial physical structures that may be challenging to design manually.
Kladovasilakis et al . demonstrated the digital restoration and rapid manufacturing of a centrifugal impeller using PBF-LB [23]. To integrate RE and AM into the restoration process, the authors scanned the damaged impeller at 500 dpi, achieving a dimensional accuracy of ±125 µ m and a scanning speed of 50,000 points per second. The team additively manufactured an impeller, the dimensions and morphology of which were examined through a similar laser scanner and the dimensional deviations quantified. The results showed that the restoration was achieved with high dimensional accuracy.
To harness the potential of Fused Filament Fabrication in restoring legacy parts, complex gear parts were scanned using advanced laser 3D scanning, after which that data was manually edited in design software to ‘repair’ the damage areas. Based on the sintering-induced shrinkage data obtained from the additively manufactured coupon samples, the repaired designed file was scaled up to obtain the best post-sintering dimensional tolerance. The tensile and flexural strength properties were also quantified to showcase the process reliability of producing legacy parts through Reverse Engineering and FFF.
Material and machine
Researchers selected the Ultrafuse 17-4 PH filament from BASF to produce the helical gear. The filament – with a density of 7.8 g/cm³ and a diameter of 1.75 mm – contains over 80% 17-4 PH stainless steel particles in a polymer base. Based on the mass, the metal content in the metal-polymer blended filament was calculated to be approximately 87.3 wt.%.
The component was additively manufactured using a MakerBot Method X machine equipped with a Labs extruder.
“This conversion from a mesh into a solid body has different methods – faceted, prismatic and organic – each of which has its advantages and limitations. In view of its faster conversion rate, faceted mesh conversion was selected for this study.”
To produce a digital twin of the stainless steel helical gear part (Fig. 2a), the researchers used the blue-laser GOM ATOS Core 200 to create a 3D scan of the helical gear. As this is an optical laser, the scan was limited to surface features and unable to penetrate through features in the way X-ray CT is able to. This led to challenges in capturing geometrical details in the core areas, especially in the gear’s central shaft hole (Fig. 2b).
Repair of the scanned helical gear was performed using three different software applications: Autodesk Meshmixer, Autodesk Fusion360, and SolidWorks (Dassault Systèmes).
After importing the scan data into Fusion360, the mesh body was converted into a solid. This conversion from a mesh into a solid body has different methods – faceted, prismatic and organic – each of which has its advantages and limitations. In view of its faster conversion rate, faceted mesh conversion was selected for this study (Fig. 2c).
Undertaking this conversion helped patch the open surfaces of the 3D scanned data; the mesh conversion process also closed the hole of the gear intended for the rotating shaft. A curvature analysis on the mesh revealed high curvature areas, something which would lead to significant surface roughness – a second design was necessary to prevent sharp edges. The scanned geometry was then imported into SolidWorks and used as a reference to reconstruct the helical gear; this reconstruction was then compared against the original scanned geometry for accuracy (Fig. 2d). It was noted that the redesigned gear aligned perfectly with the 3D scanned helical gear.
To further ensure the accuracy of the redesigned helical gear, the researchers additively manufactured a mirrored version of the updated helical gear using PLA filaments. The fit of this prototype was assessed to ensure the teeth aligned with the original legacy part; once the accuracy and fit of the redesigned helical gear were confirmed, the next step
Table 1 FFF Additive Manufacturing parameters for stainless steel-based filaments
was to manufacture the design using metal FFF.
Based on the filament manufacturer’s Technical Data Sheet (TDS), a scaling factor of 119% was applied
to the Z. In addition to the gears, ten 50 x 10 x 3.5 mm cuboids (size before scaling) were additively manufactured for characterisation purposes. Rectangular specimens (50 x 10 x 3.5 mm) were also fabricated to
assess the tensile and flexural strengths. Table 1 shows the build parameters used to manufacture the redesigned helical gears.
Fig. 3 shows the original helical gear part next to the redesigned and additively manufactured stainless steel gear. Fig. 4 shows the scaledup green parts and the sintered parts. The green parts were sent to DSH Technologies LLC, USA, for debinding and sintering (the sintering profile is proprietary to BASF and cannot be disclosed in
Fig. 5 Summary of the mechanical properties analysis on the coupon samples manufactured using an identical FFF process to fabricate the legacy parts. (a) shows a representative stress-strain behaviour of the sintered specimen under tensile force, while (b) shows the flexural strength and modulus summary (avg. ± std dev).
Mechanical properties analysis
Tensile and flexural strengths of the sintered specimens produced by Fused Filament Fabrication were measured using a universal testing machine (Zwick 2010, USA) with a 20 kN load cell and a crosshead speed of 0.5 mm/min. The data was analysed to determine the Ultimate Tensile Strength (UTS), flexural strength and modulus.
Sintering shrinkage and density measurement
The sintered cuboids were used to determine the actual threedimensional shrinkage, density and microstructure characteristics. The average of actual shrinkage was 17.32% in the X direction, 17.68% in the Y direction and 22.97% in the Z direction; this was slightly higher than the values provided by the postprocessing partner (15.97% in the X and Y directions, and 18.03% in Z direction). The researchers expect that these measured shrinkage values will be used as future reference points.
Following binder removal, the post-sintered average weight loss for all the structures was found to be ~10.2%. The density of the sintered
parts obtained using Archimedes’ principle - was 7.28 g/cm 3. Notably, the Fused Filament Fabrication process – along with the postprocessing – could achieve about 94% of the nominal density of 17-4 PH stainless steel (7.75 g/cm 3). The researchers noted, however, that optimising AM parameters is crucial to achieving optimum densities.
Mechanical properties of the manufactured and sintered parts
The average UTS of the sintered parts was calculated to be ~712 MPa, whereas the average tensile modulus was found to be 4.7 GPa. The tensile strength of the finished components was observed to be lower than the ingot tensile strength, generally in the range of 1360-1380 MPa [24-26]. The inferior properties compared to
monolithic 17-4 PH steel primarily stem from defects produced during the FFF process, particularly the voids and porosities among the adjacent strands and between layers. The flexural strength and modulus were measured to be 1.38±0.03 GPa and 72.1±10.6 GPa, respectively. Fig. 5 shows the representative stressstrain behaviour (strength and elastic modulus) under tensile stress (a) and the flexural strength and modulus (b) obtained from three-point bending tests.
Overall, the researchers found that the intelligent deployment of Reverse Engineering and Fused Filament Fabrication, as done in this study, is effective in restoring legacy parts for which the design details
“The inferior properties compared to monolithic 17-4 PH steel primarily stem from defects produced during the FFF process, particularly the voids and porosities among the adjacent strands and between layers.”
were missing. An issue does arise, however, when it comes to adequate part scanning: optical, light-based 3D scanning can’t capture data on inner geometries, and the scanning method that may be most suitable isn’t always suitable.
While X-ray based computed tomography can conduct internal scans, it is not a cost-effective solution for industrial-scale manufacturing where – even without considering the cost – the overall size and shape can vary wildly. Indeed, X-ray attenuation and image acquisition can prove challenging if the legacy component is particularly large. For cases such as these, the optical laser-based scan is straightforward and can accommodate a wider variety of specimens. If inner geometries are a necessary design component, additional (even manual)
reconstruction may be required to replicate these.
To overcome this pain point, the researchers worked on establishing a process flow to solve the issue of manual reconstruction with the commonly used trio of 3D modelling and CAD editing software: Autodesk Meshmixer, Autodesk Fusion360 and SolidWorks.
The dimensional tolerance of the redesigned gears was impressive, and they fitted well with the legacy parts still in use. The relative density of the legacy components reached approximately 94% of the theoretical, but their tensile and flexural strengths were found to be inferior compared to wrought 17-4 PH steel.
These issues can be explained by the defects ingrained in the
“The dimensional tolerance of the redesigned gears was impressive, and they fitted well with the legacy parts still in use. The relative density of the legacy components reached approximately 94% of the theoretical.”
micro- and macro-structures of the inter-strands as well as inter-layer voids and porosities. Although a 100% infill density was used during the Additive Manufacturing process, there were still visible porosities between the two adjacent strands extruded in a rectilinear pattern. When a strand had a higher length in the Z-direction, the defects were eventually suppressed/compensated by the next layers; this means that the relative density could reach an even higher value. Unfortunately, this isn’t the case for the relatively thinner flexural and tensile bars. Having a limited number of layers, there was no opportunity for the initial layer defects to be compensated, and the mechanical strength properties were measured to be inferior to the theoretical values. The manufacturing-induced defects in the coupon samples can be visualised in Fig. 6; these were consistent even after sintering.
In a follow-up study, it would be worthwhile to investigate the effect of different infill patterns on the resultant part’s strength properties. This may be especially interesting when considering that once the refurbished CAD is developed, production isn’t limited strictly to any one Additive Manufacturing process. While this study focused on Fused Filament Fabrication, the researchers note that AM technologies like Binder
Jetting, Laser or Electron Beam Powder Bed Fusion would lead to higher density, better microstructure and enhanced strength properties. It was interesting to record the higher flexural strength properties compared to the tensile properties of the sintered specimens. 17-4 PH stainless steel is precipitation-hardened martensitic steel which exhibits compromised ductility compared to conventional 304/316 stainless steel. Having brittle behaviour, the tensile strength becomes inferior compared to the flexural strength properties (similar to ceramics). In the flexural test, the bar only experiences tensile strength to half its depth, while in the tensile strength test, the specimen experiences pure tensile forces throughout its length. As a result, fewer defects are exposed under tensile force during three-point bending, resulting in higher strength and modulus compared to the tensile strength properties.
Reverse Engineering and Fused Filament Fabrication successfully recreated stainless steel legacy components. The complex and intricate inner geometries of the legacy part were manually refurbished and built into the incomplete 3D scanned data. After reconstructing the completed part as a CAD file, the redesigned gears were additively manufactured using model material, PLA, to test the fit with the existing legacy component. After the successful quality test, the actual components were produced via FFF; these also demonstrated an impressive tooth-to-tooth fit with the legacy parts.
Although higher as-sintered relative density (~94%) was observed in the additively manufactured legacy components, inferior strength properties were recorded. A 100% rectilinear infill pattern was ineffective in eliminating initial interstrand and inter-layer porosities in thinner test samples. Higher flexural strength and modulus (1.4 GPa
“This study shows the effectiveness of 3D scanning, Reverse Engineering and Fused Filament Fabrication in creating digital backups of discontinued legacy components. These solutions prove worthwhile in the absence of original design files and manufacturers.”
and 72.1 GPa, respectively) were observed compared to the tensile strength and modulus (712 MPa and 4.7 GPa, respectively). These behaviours were explained in view of the composition of the material (precipitation-hardened steel) and different loading conditions in the two test types.
This study shows the effectiveness of 3D scanning, Reverse Engineering and Fused Filament Fabrication in creating digital backups of discontinued legacy components. These solutions prove worthwhile in the absence of original design files and manufacturers.
Indeed, the combination of Reverse Engineering and AM is suited to problems small – like helical gears – or mammoth: in Jurassic Park III (2001), the nasal resonating chamber of a raptor was reverse-engineered and additively manufactured, allowing the team to survive!
The authors would like to sincerely thank Jerry Morgan (Monticello Tool and Die) for providing the legacy parts, Sheila Martin (Association of Public and Land Grant Universities) for helping in the funding for the NIST-APLU grant, Scott Broughton as the MEP partner for bringing together the companies and William Metcalf for leading industry outreach coordination effort that enabled the team to collaborate with the industry, MEP and the University. The authors are also indebted to the Small Business Administration
(SBA) for providing funding to support the 3D printing accelerator program at the UofL. Funding for this work was sponsored by the Minority Business Development Agency grant MB21OBD8020222.
Authors
Sihan Zhang 1, Saleh Khanjar 1 , Srimanta Barui 1*, Kameswara Pavan Kumar Ajjarapu 1 , Lauren Shackleford 2, Andrew Pierce 3 , and Kunal Kate 1*
1University of Louisville, KY, USA 2University of Kentucky, KY, USA
3GE Appliances, USA
Contact Kunal Kate kunal.kate@louisville.edu
Srimanta Barui srimanta.barui@louisville.edu
References
[1] S. Khanjar, Digital design and thermomechanical process simulation for 3D printing with ABS and soyhull fibers reinforced ABS composites, Mechanical Engineering, University of Louisville, 2021.
[2] M.Q. Shaikh, S.D. Nath, A.A. Akilan, S. Khanjar, V.K. Balla, G.T. Grant, S.V. Atre, Investigation of Patient-Specific Maxillofacial Implant Prototype Development by Metal Fused Filament Fabrication (MF3) of Ti-6Al-4V, 9(10) (2021) 109.
[3] M.Q. Shaikh, P.-Y. Lavertu, K.H. Kate, S.V. Atre, Process Sensitivity and Significant Parameters Investigation in Metal Fused Filament Fabrication of Ti-6Al-4V, Journal of Materials Engineering and Performance 30(7) (2021) 5118-5134.
[4] P. Singh, V.K. Balla, S.V. Atre, R.M. German, K.H. Kate, Factors affecting properties of Ti-6Al-4V alloy additive manufactured by metal fused filament fabrication, Powder Technology 386 (2021) 9-19.
[5] K. Sudan, P. Singh, A. Gökçe, V.K. Balla, K.H. Kate, Processing of hydroxyapatite and its composites using ceramic fused filament fabrication (CF3), Ceramics International 46(15) (2020) 23922-23931.
[6] P. Singh, V.K. Balla, A. Gokce, S.V. Atre, K.H. Kate, Additive manufacturing of Ti-6Al-4V alloy by metal fused filament fabrication (MF3): producing parts comparable to that of metal injection molding, Progress in Additive Manufacturing 6(4) (2021) 593-606.
[7] K.P.K. Ajjarapu, C. Barber, J. Taylor, T. Pelletiers, D. Jackson, C. Beamer, S.V. Atre, K.H. Kate, Advancements in 3D printing and hot isostatic pressing of copper: bridging the gap between green and sintered states for enhanced mechanical and electrical properties, Progress in Additive Manufacturing (2024).
[8] S. Barui, A.K. Panda, S. Naskar, R. Kuppuraj, S. Basu, B. Basu, 3D inkjet printing of biomaterials with strength reliability and cytocompatibility: Quantitative process strategy for Ti-6Al-4V, Biomaterials 213 (2019) 119212.
[9] S. Barui, D. Mishra, N.H. Gowtham, B. Basu, No more ‘core-shell’ in binderjetting of bioceramics: Novel solution and experimental validation in microstructure and mechanical properties, Journal of the European Ceramic Society 43(3) (2023) 1178-1188.
[10] S. Barui, S. Chowdhury, R. Samajdar, S. Chakraborty, M. Gavade, B. Basu, Impact of ‘core-shell’ mode of printing on properties of 3D binderjet printed zirconia-alumina based bioceramics, Open Ceramics 3 (2020) 100026.
[11] F. Bartolomeu, M. Sampaio, O. Carvalho, E. Pinto, N. Alves, J.R. Gomes, F.S. Silva, G. Miranda, Tribological behavior of Ti6Al4V cellular structures produced by Selective Laser Melting, Journal of the Mechanical Behavior of Biomedical Materials 69 (2017) 128-134.
[12] K. Wissenbach, S. Höges, P. Robotti, A. Molinari, L. Facchini, E. Magalini, Ductility of a Ti‐6Al‐4V alloy produced by selective laser melting of prealloyed powders, Rapid Prototyping Journal 16(6) (2010) 450-459.
[13] M. Koike, K. Martinez, L. Guo, G. Chahine, R. Kovacevic, T. Okabe, Evaluation of titanium alloy fabricated using electron beam melting system for dental applications, Journal of Materials Processing Technology 211(8) (2011) 1400-1408.
[14] L.E. Murr, E.V. Esquivel, S.A. Quinones, S.M. Gaytan, M.I. Lopez, E.Y. Martinez, F. Medina, D.H. Hernandez, E. Martinez, J.L. Martinez, S.W. Stafford, D.K. Brown, T. Hoppe, W. Meyers, U. Lindhe, R.B. Wicker, Microstructures and mechanical properties of electron beam-rapid manufactured Ti–6Al–4V biomedical prototypes compared to wrought Ti–6Al–4V, Materials Characterization 60(2) (2009) 96-105.
[15] L. Li, F. Yu, J. Shi, S. Shen, H. Teng, J. Yang, X. Wang, Q. Jiang, In situ repair of bone and cartilage defects using 3D scanning and 3D printing, Scientific Reports 7(1) (2017) 9416.
[16] Q. Jiang, X. Feng, Y. Gong, L. Song, S. Ran, J. Cui, Reverse modelling of natural rock joints using 3D scanning and 3D printing, Computers and Geotechnics 73 (2016) 210-220.
[17] S.D. Laycock, G.D. Bell, N. Corps, D.B. Mortimore, G. Cox, S. May, I. Finkel, Using a Combination of Micro-Computed Tomography, CAD and 3D Printing Techniques to Reconstruct Incomplete 19th-Century Cantonese Chess Pieces, 7(4 %J J. Comput. Cult. Herit.) (2015) Article 25.
[18] A.J. CRESSWELL-BOYES, A.H. BARBER, D. MILLS, A. TATLA, G.R. DAVIS, Approaches to 3D printing
teeth from X-ray microtomography, 272(3) (2018) 207-212.
[19] P. Wang, J. Yang, Y. Hu, J. Huo, X. Feng, Innovative design of a helmet based on reverse engineering and 3D printing, Alexandria Engineering Journal 60(3) (2021) 3445-3453.
[20] G. Baronio, S. Harran, A. Signoroni, A Critical Analysis of a Hand Orthosis Reverse Engineering and 3D Printing Process, Applied Bionics and Biomechanics 2016 (2016) 8347478.
[21] B. Basu, N. Bhaskar, S. Barui, V. Sharma, S. Das, N. Govindarajan, P. Hegde, P.J. Perikal, M. Antharasanahalli Shivakumar, K. Khanapure, A. Tekkatte Jagannatha, Evaluation of implant properties, safety profile and clinical efficacy of patient-specific acrylic prosthesis in cranioplasty using 3D binderjet printed cranium model: A pilot study, Journal of Clinical Neuroscience 85 (2021) 132-142.
[22] R.H. Helle, H.G. Lemu, A case study on use of 3D scanning for reverse engineering and quality control, Materials Today: Proceedings 45 (2021) 5255-5262.
[23] N. Kladovasilakis, T. Kontodina, P. Charalampous, I. Kostavelis, D. Tzetzis, D. Tzovaras, A case study on 3D scanning, digital reparation and rapid metal additive manufacturing of a centrifugal impeller, IOP Conference Series: Materials Science and Engineering 1037(1) (2021) 012018.
[24] s.s. 17-4, https://en.wikipedia. org/wiki/17-4_stainless_steel.
[25] A. Caballero, J. Ding, S. Ganguly, S. Williams, Wire + Arc Additive Manufacture of 17-4 PH stainless steel: Effect of different processing conditions on microstructure, hardness, and tensile strength, Journal of Materials Processing Technology 268 (2019) 54-62.
[26] P. Ponnusamy, B. Sharma, S.H. Masood, R.A. Rahman Rashid, R. Rashid, S. Palanisamy, D. Ruan, A study of tensile behavior of SLM processed 17-4 PH stainless steel, Materials Today: Proceedings 45 (2021) 4531-4534.
The Fraunhofer Direct Digital Manufacturing Conference DDMC 2025 is a bi-annual cuttingedge forum for discussion on Additive Manufacturing, which will take place from March 12 to 13, 2025 at the ParkInn by Radisson Berlin Alexanderplatz, located in the vibrant heart of Berlin, Germany.
The Fraunhofer Direct Digital Manufacturing Conference DDMC 2025 is a bi-annual cuttingedge forum for discussion on Additive Manufacturing, which will take place from March 12 to 13, 2025 at the ParkInn by Radisson Berlin Alexanderplatz, located in the vibrant heart of Berlin, Germany.
Fraunhofer Direct Digital Conference DDMC 2025 a bi-annual cuttingforum for on Additive which will take place from 12 to 13, 2025 at the by Berlin located in the heart of Berlin, Germany.
Fascinating developments in additive manufacturing and 3D printing technology will be presented over two days at Fraunhofer DDMC 2025. Over 50 presentations by AM experts from industry and research will create an exciting program. In addition to AM technology development for metals, plastics and ceramics, the presentations will cover the topics of material innovations, process monitoring and artificial intelligence as well as sustainability. The traditional evening event in an attractive Berlin event location will take place on the evening of the first conference day and offers an excellent opportunity to make contacts, exchange experiences and develop new collaborations.
Fascinating developments in additive manufacturing and 3D printing technology will be presented over two days at Fraunhofer DDMC 2025. Over 50 presentations by AM experts from industry and research will create an exciting program. In addition to AM technology development for metals, plastics and ceramics, the presentations will cover the topics of material innovations, process monitoring and artificial intelligence as well as sustainability. The traditional evening event in an attractive Berlin event location will take place on the evening of the first conference day and offers an excellent opportunity to make contacts, exchange experiences and develop new collaborations.
developments in manuand 3D printing technology presented two days at Fraunhofer DDMC 2025. Over 50 by AM experts industry research will an exciting In addition AM technology for metals, plastics and the will topics of mate innovations, process and artiintelligence as well as sustainability. event in attractive Berlin event location will take place the evening of the conference day and offers an excellent to make contacts, exchange experiences develop new collaborations.
We are particularly pleased to once again welcome renowned experts in additive manufacturing from research and industry as keynote speakers to our conference - Prof. Bianca Colosimo (Politecnio di Milano, Italy), Prof. Wojciech Matusik (MIT, USA), Prof. Enrico Stoll (TU Berlin, Germany), Ben Hartkopp (Quantica GmbH, Germany) as well as Dr. Sebastian Piegert and Dr. Cynthia Wirth (Siemens Energy, Germany).
We are particularly pleased to once again welcome renowned experts in additive manufacturing from research and industry as keynote speakers to our conference - Prof. Bianca Colosimo (Politecnio di Milano, Italy), Prof. Wojciech Matusik (MIT, USA), Prof. Enrico Stoll (TU Berlin, Germany), Ben Hartkopp (Quantica GmbH, Germany) as well as Dr. Sebastian Piegert and Dr. Cynthia Wirth (Siemens Energy, Germany).
particularly pleased to once againme in additive manufacturing research and as keynote speakers conference - Bianca Colosimo di Milano, Italy), Wojciech (MIT, USA), Prof. Enrico (TU Berlin, GermaBen (Quantica GmbH, as well as Sebastian Piegert and Cynthia Wirth Energy,
Please that the conference is three away. Registration has just opened encourage you to take advantage of bird fees! also you to a sponsor or at DDMC 2025. Collect more info our program, and sponsoring exhibition opportunities
Please note that the conference is just three months away. Registration has just opened and we encourage you to take advantage of the early bird registration fees! We also encourage you to become a sponsor or exhibitor at DDMC 2025. Collect more info on our program, registration and sponsoring and exhibition opportunities on our website.
Please note that the conference is just three months away. Registration has just opened and we encourage you to take advantage of the early bird registration fees! We also encourage you to become a sponsor or exhibitor at DDMC 2025. Collect more info on our program, registration and sponsoring and exhibition opportunities on our website.
www.ddmc-fraunhofer.de
www.ddmc-fraunhofer.de
PIM International is the only business-to-business publication dedicated to reporting on the technical and commercial advances in the MIM, CIM, and sinter-based Additive Manufacturing industries. Available in both digital and print formats, PIM International is the perfect platform to promote your company to a global audience.
PIM International is dedicated to driving awareness and development of the MIM, CIM and sinter-based AM industries and their related technologies. Key to this aim is our support of a range of international partner conferences.
View our complete events listing on: www.pim-international.com
International Conference on Injection Molding of Metals, Ceramics, and Carbides (MIM2025)
February 24–26 - Costa Mesa, CA, US www.mim2025.org
PM China 2025
March 10–12 - Shanghai, China en.pmexchina.com
Fraunhofer Direct Digital Manufacturing Conference DDMC 2025
March 12–13 - Berlin, Germany www.ddmc-fraunhofer.de
AM Forum Berlin
March 17–18 - Berlin, Germany www.am-forum.de
AMUG 2025
March 30–April 3 - Chicago, IL, US www.amug.com
The 14 th International Conference on Hot Isostatic Pressing (HIP 2025)
April 6–10 - Aachen, Germany www.hip2025.com
RAPID + TCT 2025
April 8–10 - Detroit, MI, US www.rapid3devent.com
EPMA – Use of Powder Metallurgy Technologies in Aerospace
May 20–21 - Sandviken, Sweden www.seminars.epma.com/event/ aerospace-seminar
21 st Plansee Seminar
June 1–6 - Reutte, Austria www.plansee-seminar.com
+INDUSTRY 2025
June 3–5 - Bilbao, Spain plusindustry.bilbaoexhibitioncentre.com
ADDIT Ɛ D 2025
June 3–5 - Bilbao, Spain addit3d.bilbaoexhibitioncentre.com
PowderMet 2025 | AMPM 2025
June 15–18 - Phoenix, AZ, US www.powdermet2025.org | www.ampm2025.org
The Advanced Ceramics Show
July 9–10 - Birmingham , United Kingdom www.advancedceramicsshow.com
The Advanced Materials Show
July 9–10 - Birmingham , United Kingdom www.advancedmaterialsshow.com
Euro PM2025 Congress & Exhibition
September 14–17 - Glasgow, Scotland www.europm2025.com
The European Additive Manufacturing Congress 2025
September 14–17 - Glasgow, Scotland www.euroam2025.com
Formnext 2025
November 18–21 - Frankfurt, Germany www.formnext.com
2026
Ceramitec 2026
March 24–26 - Munich, Germany www.ceramitec.com
WorldPM2026
June 25–29 - Montreal, Canada www.worldpm2026.org
If you would like to see your CIM, MIM or sinterbased AM related event listed in this magazine and on our websites, please contact Merryl Le Roux: merryl@inovar-communications.com