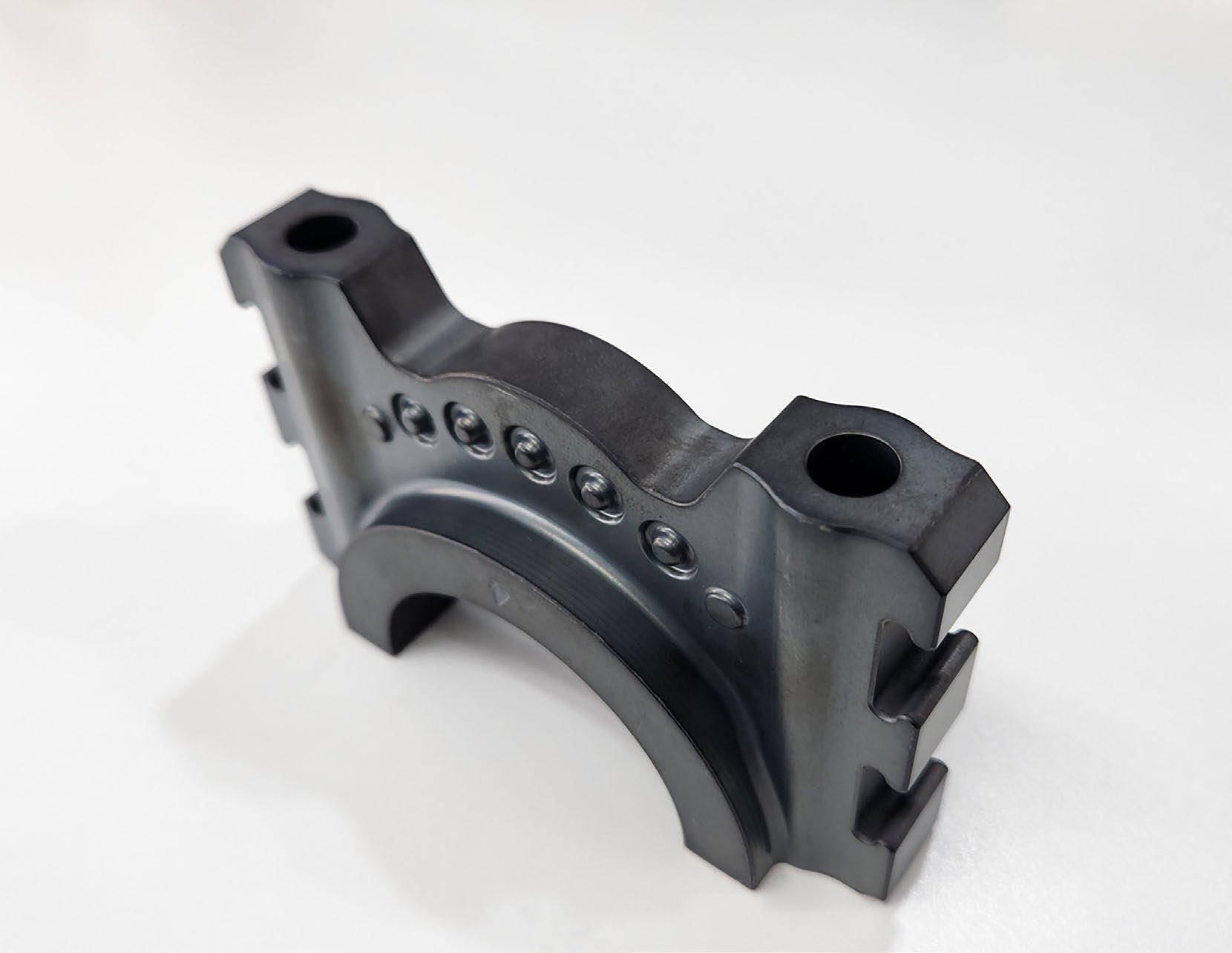
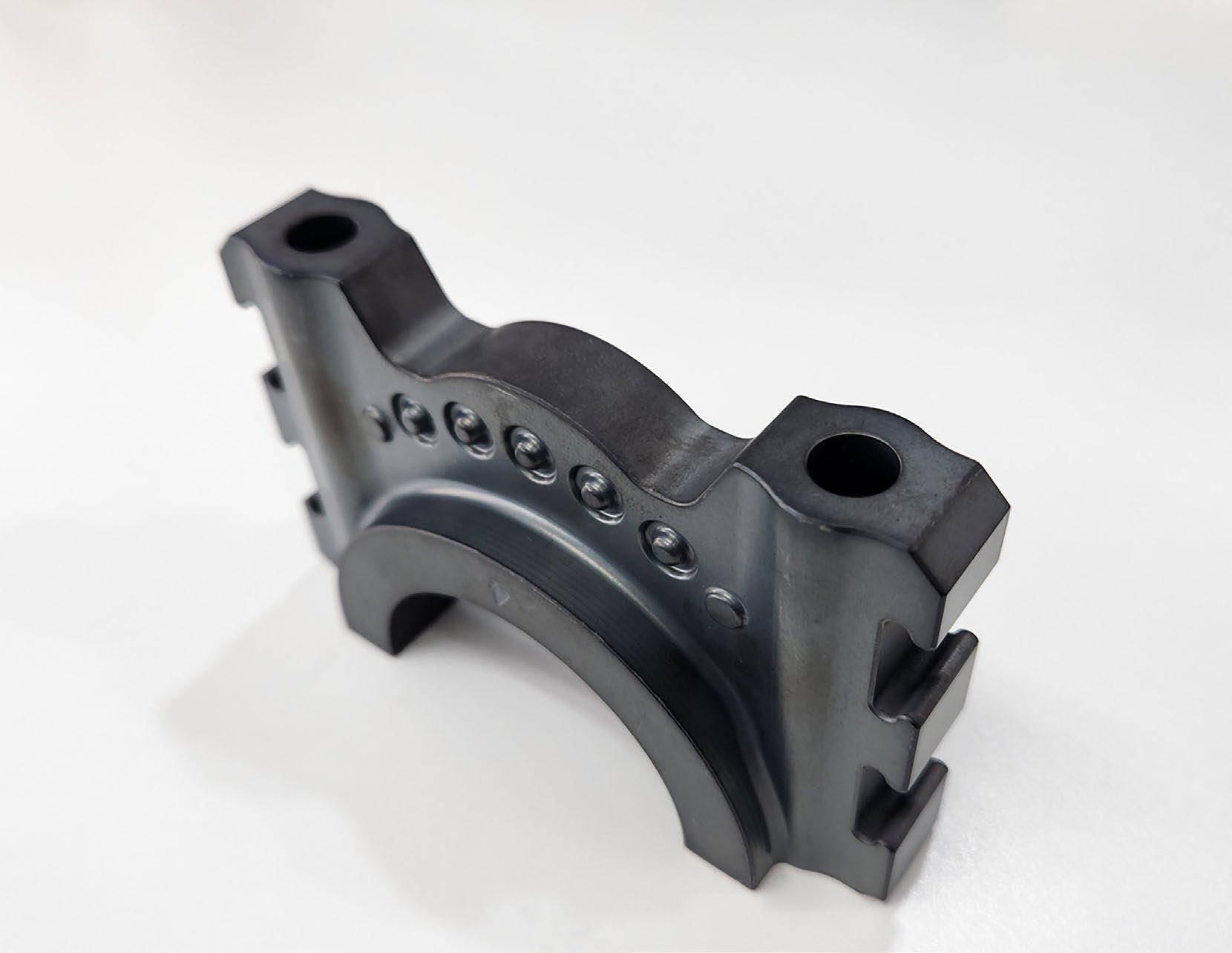
For a sustainable tomorrow
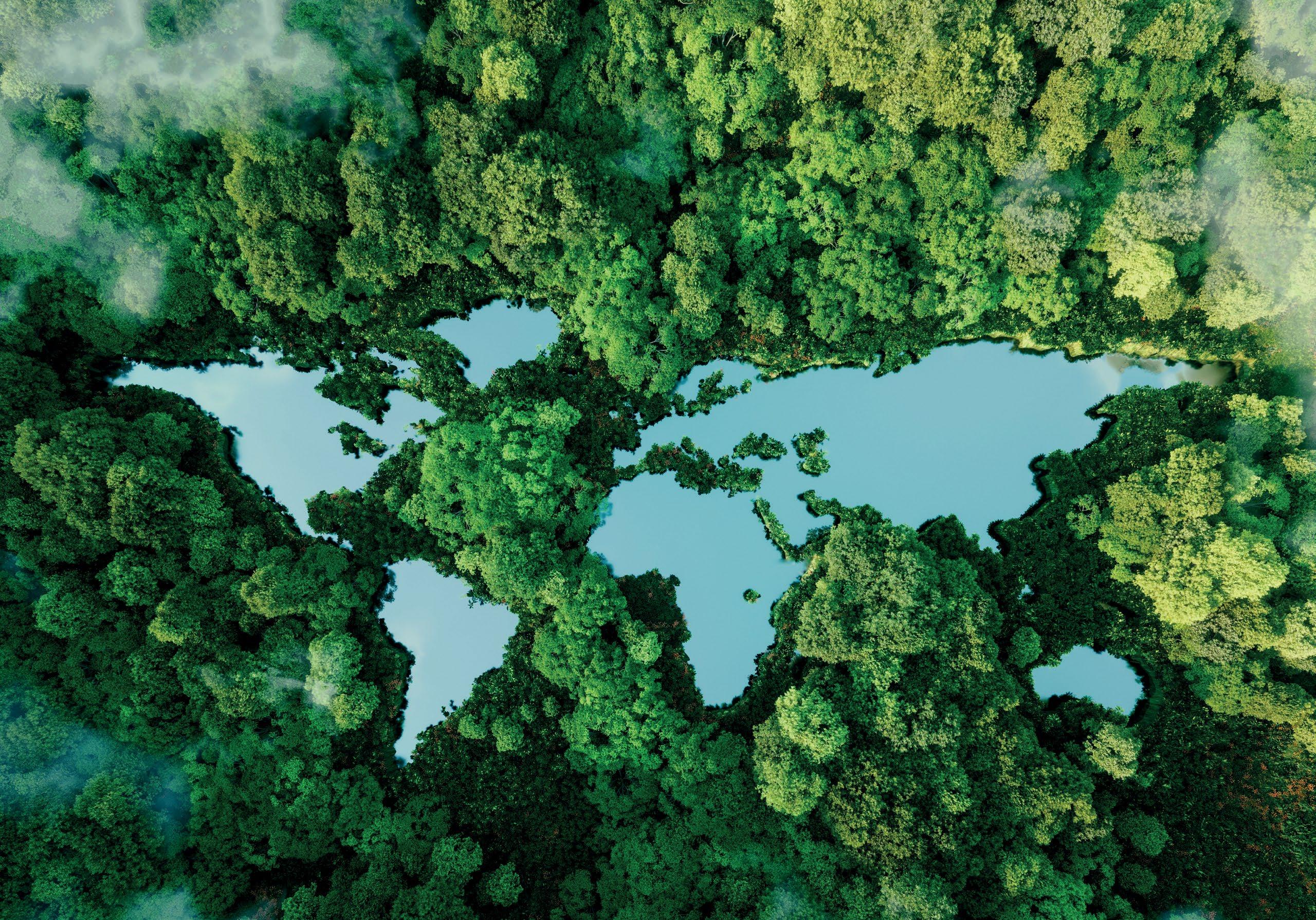
Höganäs AB commits to reduce absolute scope 1 and 2 GHG emissions 51% by 2030 from a 2018 base year.* Höganäs AB also commits to reduce absolute scope 3 GHG emissions from purchased goods and services, upstream transportation and distribution, and business travel 30% within the same timeframe.
*The target boundary includes land-related emissions and removals from bioenergy feedstocks.
Our climate tagret is validated by Science Based Targets initiative.
For more info scan the QR Code
www.hoganas.com

Publisher & Editorial Offices
Inovar Communications Ltd
11 Park Plaza
Battlefield Enterprise Park Shrewsbury SY1 3AF United Kingdom
Tel: +44 (0)1743 469909 www.pm-review.com
Managing Director & Editor
Nick Williams, nick@inovar-communications.com
Group News Editor
Paul Whittaker, paul@inovar-communications.com
Advertising Sales Director
Jon Craxford, jon@inovar-communications.com Tel: +44 (0)207 1939 749
Assistant News Editor
Charlie Hopson-VandenBos charlie@inovar-communications.com
Editorial Assistant
Amelia Gregory, amelia@inovar-communications.com
Consulting Editor
Dr David Whittaker
Technical Consultant
Dr Martin McMahon
Digital Marketer
Mulltisa Moung, mulltisa@inovar-communications.com
Production Manager
Hugo Ribeiro, hugo@inovar-communications.com
Operations & Partnerships Manager
Merryl Le Roux, merryl@inovar-communications.com
Office & Accounts Manager
Jo Sheffield, jo@inovar-communications.com
Subscriptions
PM Review is published on a quarterly basis. It is available as a free electronic publication or as a paid print subscription. The annual subscription charge is £150.00 including shipping.
Accuracy of contents
Whilst every effort has been made to ensure the accuracy of the information in this publication, the publisher accepts no responsibility for errors or omissions or for any consequences arising there from. Inovar Communications Ltd cannot be held responsible for views or claims expressed by contributors or advertisers, which are not necessarily those of the publisher.
Advertisements
Although all advertising material is expected to conform to ethical standards, inclusion in this publication does not constitute a guarantee or endorsement of the quality or value of such product or of the claims made by its manufacturer.
Reproduction, storage and usage
Single photocopies of articles may be made for personal use in accordance with national copyright laws. All rights reserved. Except as outlined above, no part of this publication may be reproduced or transmitted in any form or by any means, electronic, photocopying or otherwise, without prior permission of the publisher and copyright owner.
Design and production
Inovar Communications Ltd.
ISSN: 2050-9693 (PRINT)
ISSN: 2050-9707 (ONLINE)
© 2024 Inovar Communications Ltd.
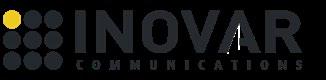
A celebration of PM’s success
The Powder Metallurgy industry continues to innovate, supporting end-users around the world with costcompetitive, high-precision components for the automotive industry and beyond. Combined with the technology’s superior material utilisation and lower overall energy consumption compared to competing technologies, PM is a compelling solution for the next generation of applications.
In this issue of PM Review , we present two such nextgeneration PM components, developed for Hyundai Motors by Korea Sintered Metal and Höganäs AB. These components, one of which won an internal award at Hyundai, will feature in a new generation of ICE engines and serve to raise awareness of PM technology within the company and, more widely, within automotive producers worldwide. Further PM innovations are also highlighted in our coverage of the Metal Powder Industries Federation’s 2024 PM Design Excellence awards where applications beyond automotive –in green energy, agricultural equipment, power tools and the medical sector – are celebrated.
We cannot, of course, dismiss what is happening in the automotive industry when considering the future trajectory of PM; how the shift towards an electrified future plays out is a matter on everyone’s mind. This is only further complicated by the rise of China as a global automotive superpower – a development that happened faster than many predicted.
Let us hope that conversations at World PM2024 Yokohama bring insight and a new vision of the global PM industry’s future. I look forward to seeing you there.
Nick Williams Managing Director, PM Review
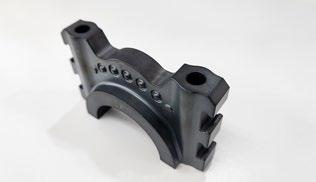
Cover image
A Powder Metallurgy bedplate insert (Courtesy Hyundai Motor/ Korea Sintered Metal/Höganäs Korea)

Find out more at www.riotinto.com Our materials, your life
Rio Tinto Metal Powders (RTMP) is committed to finding better ways to provide the materials the world needs now and in the future.
As a producer of iron and steel powders at our plant located in Quebec, Canada, RTMP is a key supplier to the automotive industry, which is undergoing a transition towards electrification. RTMP is contributing to the development of new Soft Magnetic Composite (SMC) materials for electric components, from pump assemblies to small electric motors in e-bikes and EV’s to support the energy transition. Together, we can create a better life for the generations to come.
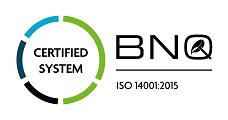
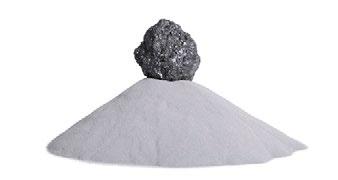
Metal Powders www.qmp-powders.com


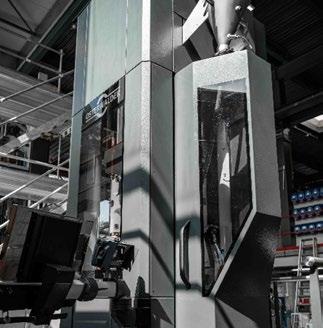
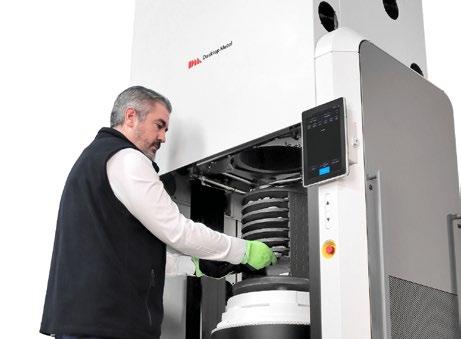
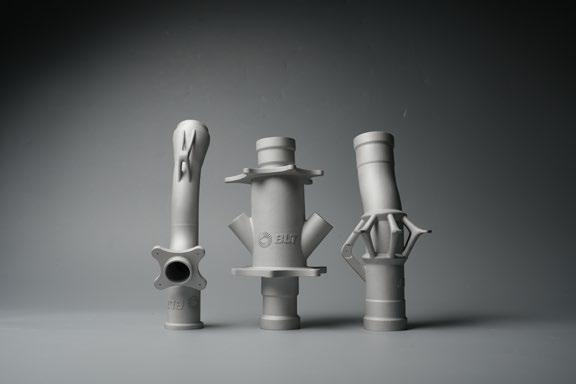
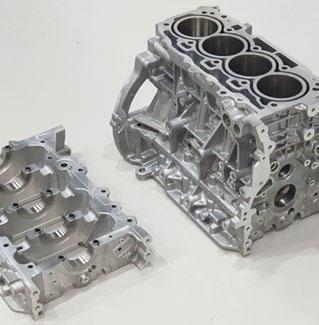
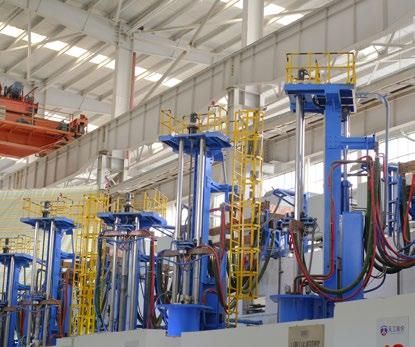
53 Collaboration drives success for PM: New Hyundai Motor applications developed with Korea Sintered Metal Co. and Höganäs AB
Despite the shift towards electrification, the further development and optimisation of internal combustion engines (ICEs) is still necessary in order to meet society’s diversified transportation needs. As it has done in the past, Powder Metallurgy is able to deliver the innovative solutions that are required for a new generation of engines.
In this article, Hak-Soo, Kim, Hyundai Motors, reports on a collaborative project between Hyundai Motor Company and Korea Sintered Metal Co. that resulted in the development of two innovative new PM automotive applications. >>>
63 PowderMet2024 and AMPM2024 report: Cemented Carbides brought into focus in Pittsburgh
The fact that a high proportion of North America’s Powder Metallurgy structural parts and cemented carbide industries are located close to Pittsburgh, the host city for this year’s PowderMet2024 and AMPM2024 conferences, ensured a good turnout for the organiser, the Metal Powder Industries Federation (MPIF).
In the following report, Bernard North shares his overall impressions of the event and reports in detail on a particularly well-attended Carbide Forum, in which developments in the $20 billion cemented carbide industry were presented by a very knowledgeable panel of presenters. >>>
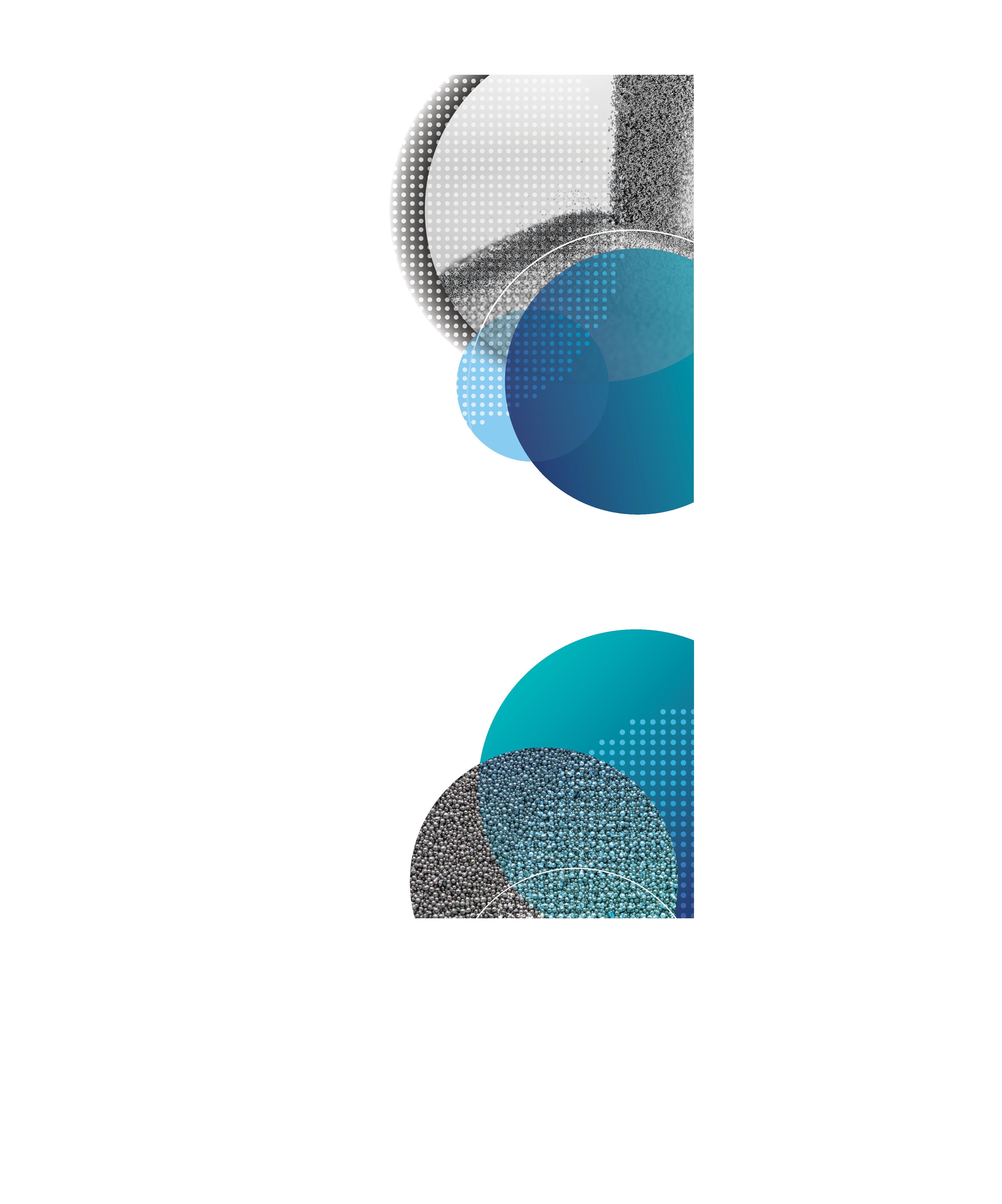
Experience the power of performance, the spark of innovation, and the strength of partnership
Performance:
As a global leader in powders, pastes, and granules, we excel in materials like Aluminum, Copper, Titanium, and more. Our precision manufacturing ensures superior product attributes tailored to your requirements.
Innovation:
Utilizing state-of-the-art research and development alongside cutting-edge technologies, we provide tailored solutions for PM and additive manufacturing. Our emphasis on materials and process advancements positions us as industry leaders in quality, service, and operational excellence.
Partnership:
Count on us as your trusted development and production ally. Our expertise in metal powders and alloys ensures top-tier materials for critical applications, empowering industries worldwide.
At Kymera International, we’re not just a powder provider; we’re your strategic partner in the world of specialty material solutions and additive manufacturing. Contact us today to revolutionize your projects
www.kymerainternational.com
info@kymerainternational.com
79
Powder Metallurgy shines in the MPIF’s 2024 Design Excellence Awards competition
The annual Powder Metallurgy Design Excellence Awards competition, organised by the Metal Powder Industries Federation (MPIF), is an opportunity for PM part producers to showcase the capabilities of the full range of metal powder-based technologies to a global audience.
This year’s winners were announced at a special ceremony at the International Conference on Powder Metallurgy & Particulate Materials (PowderMet2024), held in Pittsburgh from June 16-19. This report reviews the winners in the conventional Press and Sinter PM category. >>>
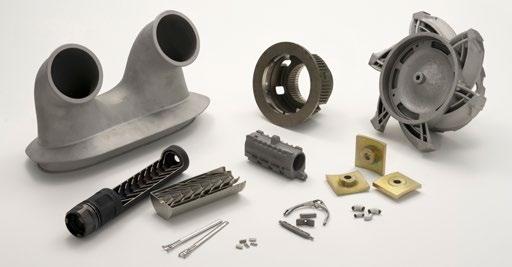
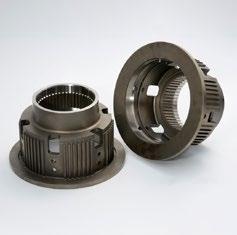

85 PowderMet2024: The state of the Powder Metallurgy industry in North America
A highlight of the Metal Powder Industries Federation’s annual International Conference on Powder Metallurgy & Particulate Materials (PowderMet) is the ‘State of the PM Industry’ presentation, in which key industry data are presented alongside analysis of the performance of PM in major markets. This year’s presentation was delivered by Michael Stucky, president of the MPIF and Business Unit Director at Norwood Medical. Stucky’s presentation, published here in full, brings the current challenges facing PM into focus, as well as highlighting opportunities for growth. >>>
93 The wire that makes the powder: TGTi’s development of titanium wire feedstock for plasma atomisation
When it comes to titanium powder production for Additive Manufacturing, Metal Injection Moulding and other advanced production processes, plasma gas atomisation is regarded as a gold standard – particularly for demanding applications in the aerospace and medical sectors. The quality of the wire feedstock that is used in the process, of course, directly impacts the quality of the powder that comes out. In this article, Jiangsu Tiangong Technology (TGTi) shares insights into its production processes, its rise to becoming a market leader, and its goal of meeting the needs of the international community. >>>

Advertisers’ index & buyer’s guide
Our advertisers’ index and buyer’s guide serves as a convenient guide to suppliers across the PM supply chain. In the digital edition of PM Review magazine, available at www.pm-review.com, simply click on a company name to view its advert, or on the company’s weblink to go directly to its website.
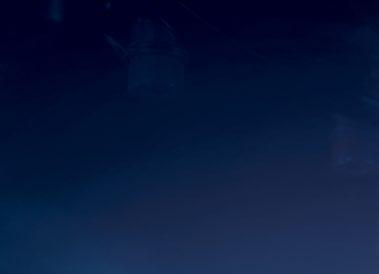
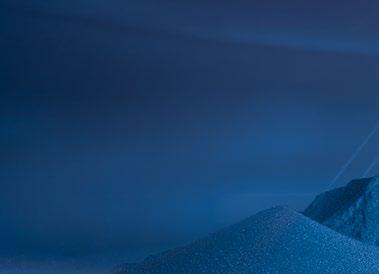
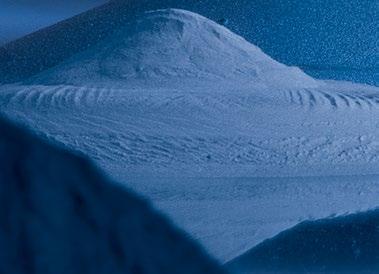
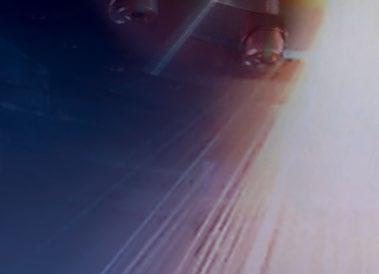
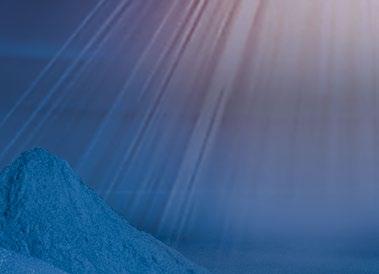
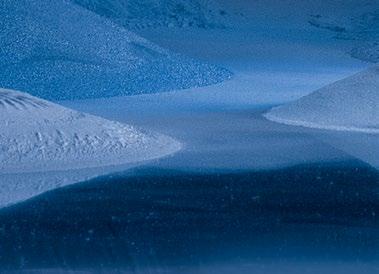

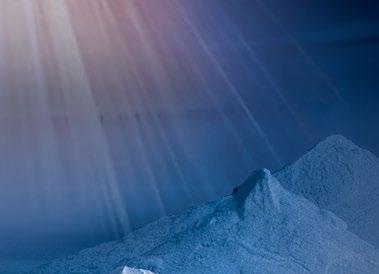

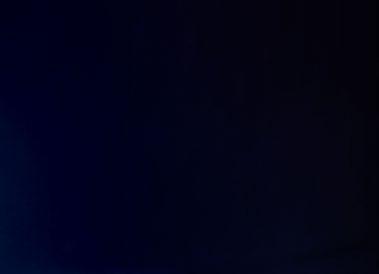




























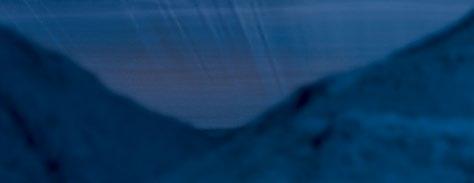













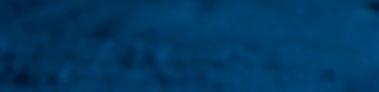



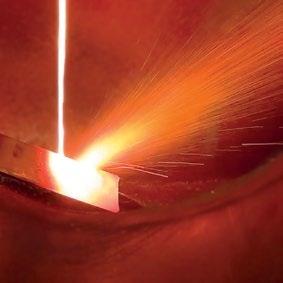
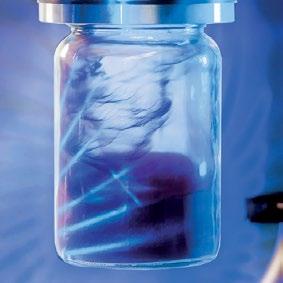
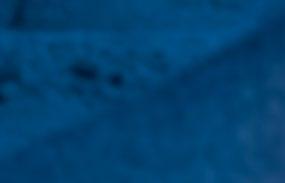
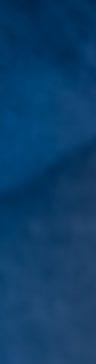
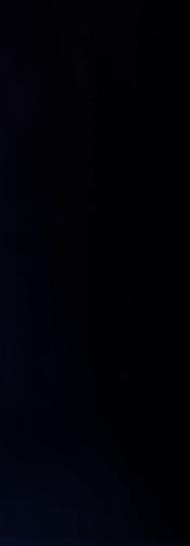





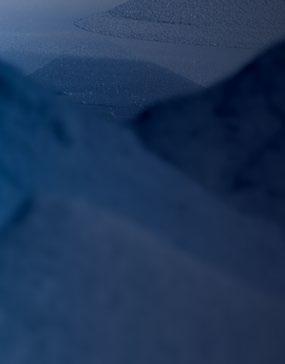







● GAS AND ULTRASONIC ATOMIZERS FOR SPHERICAL POWDERS WITHOUT ANY SATELLITES for LPBF, MIM, Binder Jetting and other Additive Manufacturing applications. High purity, sphericity and wide range of reproducible particle size distribution.
● WATER ATOMIZERS FOR MORE IRREGULAR POWDERS ideal for recycling/re ning process, press & sinter process and others.

● AIR CLASSIFIERS FOR THE PRECISE SEPARATION OF METAL POWDERS into ne and coarse powder fractions especially in the range < 25 µm
● MAXIMUM PURITY BY OXIDATION-FREE PROCESSING
● ALL SYSTEMS DESIGNED FOR EASY HANDLING AND CLEANING, QUICK ALLOY CHANGE WITH MINIMUM CROSS CONTAMINATION

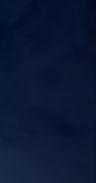





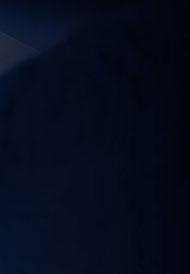

● FOR A WIDE RANGE OF METALS AND FOR SMALL TO MEDIUM AMOUNTS
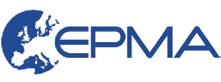
To submit news for inclusion in Powder Metallurgy Review contact Paul Whittaker at paul@inovar-communications.com
IDEX to acquire Mott Corporation for $1 billion
IDEX Corporation, Northbrook, Illinois, USA, announced in July that it has entered into a definitive agreement to acquire Mott Corporation, headquartered in Farmington, Connecticut, USA, and its subsidiaries for cash consideration of $1 billion, subject to customary adjustments.
When adjusted for the present value of expected tax benefits of approximately $100 million, the net transaction value is approximately $900 million. This represents approximately 19x Mott’s forecasted full-year 2024 EBITDA and a mid-teens multiple based on forecasted 2025 EBITDA. The transaction is expected to be accretive to adjusted earnings per share in fiscal year 2026.
“Mott’s business fits the IDEX sweet spot of highly engineered, configurable mission-critical components focused on scalable select applications. The addition of Mott represents an important step in our evolution, as we continue building our differentiated capabilities in applied materials technologies. Mott brings advanced technical and application expertise that will expand our capabilities in highvalue end markets and open new organic growth opportunities. Our focus on driving profitable growth through the enterprise-wide application of 80/20 is expected to yield material benefits,” said Eric D Ashleman, Chief Executive Officer and President of IDEX.
“The addition of Mott supports our strategy to deliver longterm, compounding value to our customers, employees, and shareholders, which includes targeted inorganic growth funded by strong cash flow generation. With shared cultural values, including a deep passion for solving customer challenges through technical capabilities and innovative solutions, our great teams combine to offer meaningful go-to-market opportunities. We look forward to welcoming the over 500 Mott employees to IDEX,” Ashleman continued.
In 2024, Mott is expected to generate approximately $200 million of revenue, with an EBITDA margin in the low 20s. Mott will join IDEX’s Health & Science Technologies segment. The transaction will be funded through a combination of cash on hand, borrowings from
IDEX’s current credit facility, and potential debt issuance.
“We’re excited to join an industry leader with a strong record of helping customers solve their toughest problems. Mott brings applied material science, chemistry, and application expertise, an additive and complementary customer base, and a growing pipeline of opportunities. When combined with the scale of IDEX, industry-leading positions, and deep technological know-how, this will yield meaningful synergies and benefits. Our culture and capabilities align with IDEX, and our employees will add tremendous value to the company, just as they’ve driven Mott’s growth for generations,” stated Boris Levin, president and Chief Executive Officer of Mott.
The deal is expected to close by the end of the third quarter of 2024, subject to regulatory approvals and customary closing conditions.
www.idexcorp.com
www.mottcorp.com
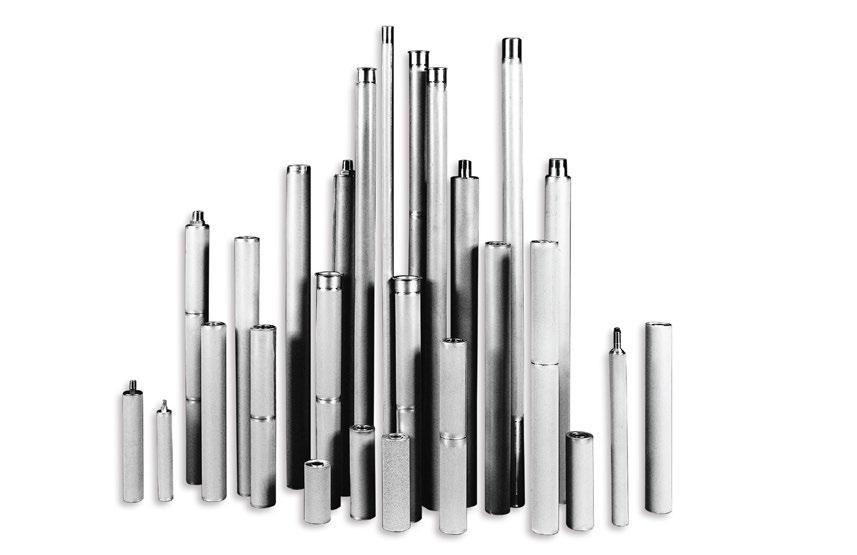
Mott Corporation produces a range of sintered filters, amongst other products (Courtesy Mott Corporation)

Dowlais considers sale of GKN Powder Metallurgy business
Dowlais Group plc, the UK-based parent company of GKN Automotive and GKN Powder Metallurgy, has published its half year 2024 results. In the report, the company confirmed it has commenced a strategic review of the Powder Metallurgy business, as it eyes a potential sale of the division.
GKN Powder Metallurgy noted a good start to the year, with adjusted revenues growing by 0.2%, ahead of the market, while adjusted operating profit increased by 6.0%, resulting in an adjusted operating margin expansion of 50 bps, to 9.5%.
The company stated that proactive management of the cost base had enabled GKN Powder Metallurgy to offset inflationary increases through operational efficiencies. This led to restructuring activities continuing in the first half of the year, with one site closed in the US and another set to close by the end of the year. The location of the second site closure was not stated, but this was expected to further optimise the manufacturing footprint, Dowlais stated.
It was added that GKN Powder Metallurgy continued to advance its EV transition, winning new EV-specific contracts and identifying additional growth areas for propulsion-agnostic products.
For the group as a whole, Dowlais reported adjusted revenue of £2,571 million for the six months ending June 30, 2024, a reduction of 5.1% on the prior year, said to be driven by weakness in the ePowertrain product line of the Automotive business.
Driveline, China and Powder Metallurgy, totalling more than 75% of the group’s revenues, were reported to be performing above their markets.
The group posted adjusted operating profit of £151 million, including £7 million of operating losses from Hydrogen operations, a decline of 9.0% compared to the prior year, said to be driven by lower volumes.
“In this challenging market environment, we focused on what we can control and took several decisive actions to mitigate the impact from lower volume as well as unlock value from our portfolio,” stated Liam Butterworth, Chief Executive Officer.
Gevorkyan reports acquisition of Altha PM’s customers and production of PM parts for SKF Group
Gevorkyan, headquartered in Vlkanová, Slovakia, has reported on its recent agreement with Poland’s Altha Powder Metallurgy and the ongoing transfer of PM part production from Sweden’s SKF Group to Gevorkyan’s manufacturing plant in Vlklanová.
In April 2024, an agreement between Gevorkyan and Altha Powder Metallurgy, a division of Altha Group based in Radom, Poland, resulted in the acquisition of customers for whom Altha PM was no longer able to serve. The deal did not involve the
purchase of any shares in Altha PM – rather, Gevorkyan has taken over the portfolio for a number of its customers and is transferring production of the related products to its manufacturing plant in Vlklanová. The company added that it has since negotiated new and more favourable terms of cooperation with Altha PM’s customers.
Gevorkyan is currently negotiating with the Polish company regarding the purchase of certain assets, including machinery. If they reach an agreement, the machinery
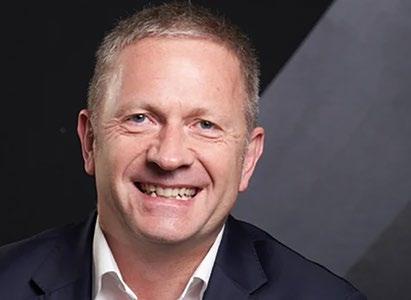
Liam Butterworth, Dowlais CEO, has announced a strategic review of GKN Powder Metallurgy (Courtesy Dowlais Group)
“First, we implemented a relentless focus on cost control, limiting the impact on adjusted operating profit and mitigated the margin decline to 30 bps. Second, we initiated a comprehensive programme of commercial recovery initiatives with our customers which, together with the ongoing restructuring programmes and performance initiatives, will limit the impact from expected lower revenues in the second half of the year. Finally, today’s announcement of a strategic review of Powder Metallurgy and the disposal of our Hydrogen operations underscores our commitment to unlocking value from our portfolio and delivering shareholder returns,” Butterworth concluded. www.gknpm.com
would be transferred to Gevorkyan’s plant in Vlkanová to further increase its production capacity.
Gevorkyan also announced that it is continuing to produce Powder Metallurgy parts for Sweden’s SKF Group.
SKF group is one of the largest bearing and seal manufacturers in the world, present in 130 countries. In 2023, it employed over 40,000 people and generated sales of €8.5 billion.
Having established itself as a stable and reliable supplier, SKF Group has entrusted Gevorkyan with the production of several PM components that the group previously produced itself, opting for outsourcing rather than opening a larger plant.
www.gevorkyan.sk
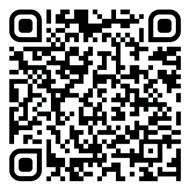
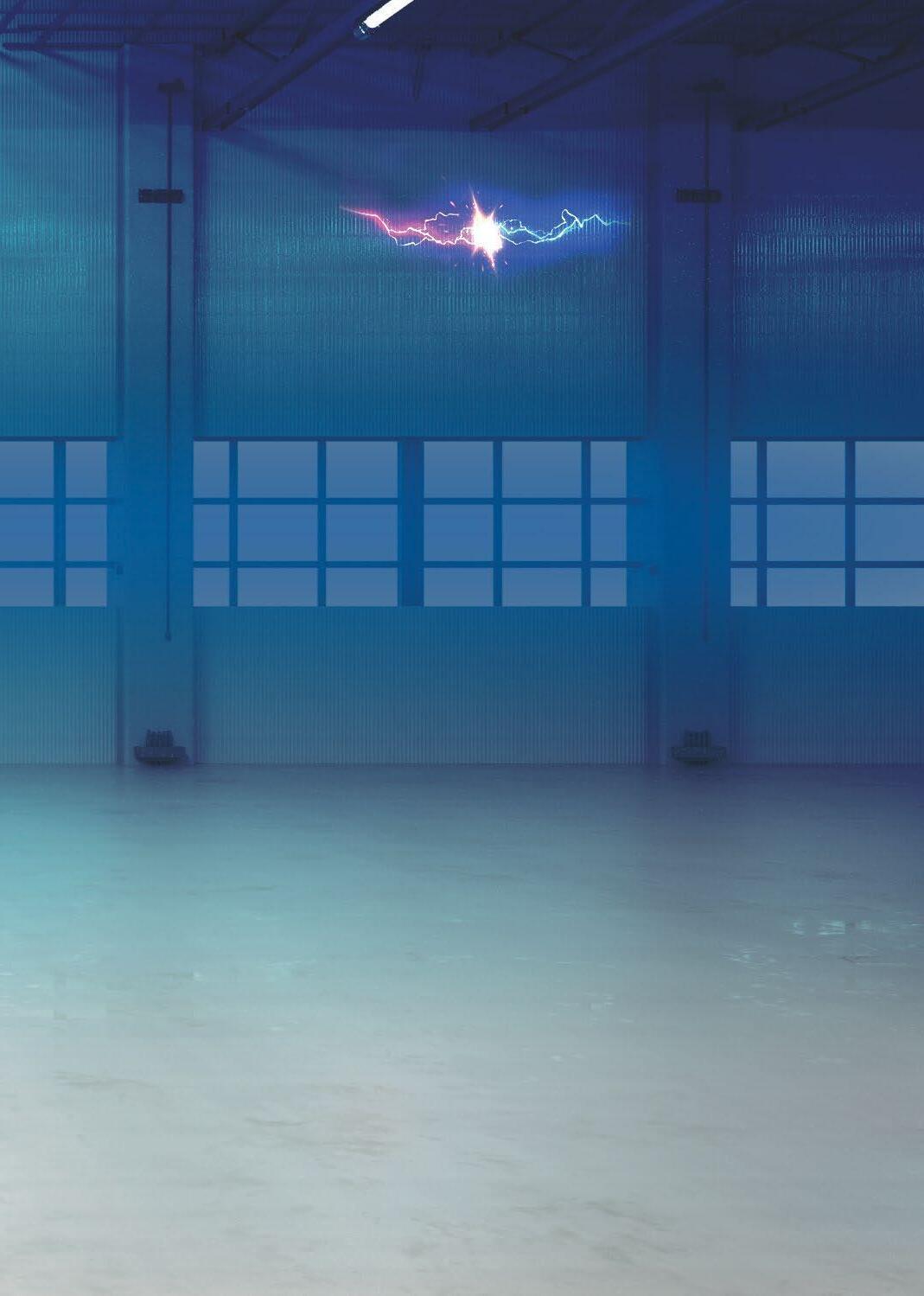

HC Starck Tungsten to be sold to Mitsubishi Materials Corporation
Masan High-Tech (MHT) Materials Group, headquartered in Ho Chi Minh City, Vietnam, parent company of HC Starck Tungsten, has signed a binding agreement with Mitsubishi Materials Corporation Group (MMC), Tokyo, Japan, for the sale of all
shares in HC Starck Holding GmbH. MMC, which operates its own site for the recovery and processing of tungsten as well as the manufacturing of tungstenbased tools, is a long-standing customer of the Goslar-based
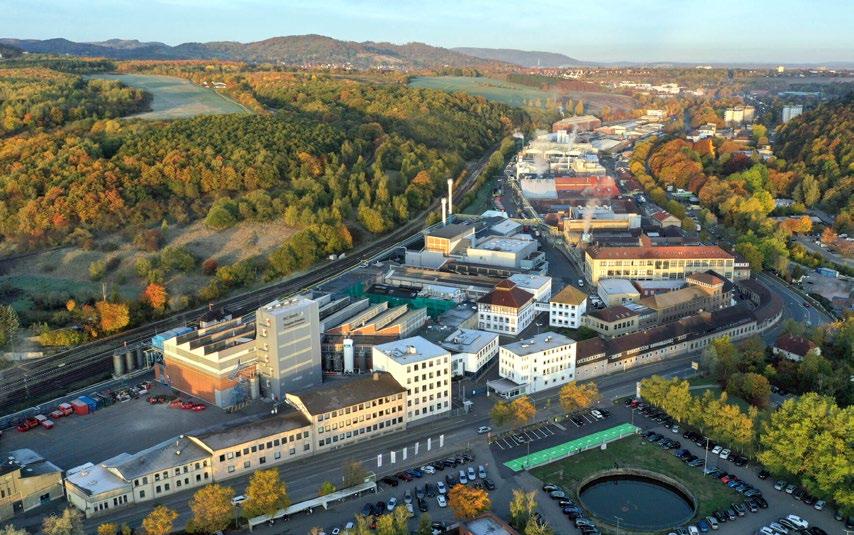
China unveils new rare earth regulations to protect domestic supply
China has unveiled a list of rare earth regulations that are aimed at protecting supplies for national security purposes, reports Reuters These regulations encompass rules governing the mining, smelting, and trading of critical materials used in the production of items ranging from magnets in electric vehicles (EVs) to consumer electronics.
The regulations, issued by the State Council, announced that rare earth resources belong to the state, and the government will oversee the development of the rare earths industry. In recent years, China has become the world’s dominant producer of the seventeen minerals, accounting for nearly 90% of global refined output.
China’s global industrial significance is such that the European Union has set ambitious 2030 targets for domestic production of crucial minerals, particularly rare earths. This is in line with the green transition as rare earths are used in permanent magnets powering motors in electric vehicles and wind energy. The law came into force in May to support this initiative. The demand for rare earths in the EU is projected to increase sixfold by 2030 and sevenfold by 2050.
The new Chinese regulations, which will take effect on October 1 st, state that the State Council will establish a rare earth product traceability information system. Under this system, enterprises
company. It acquired a 10% stake in MHT in 2020, shortly after the latter took over HCS from the former HC Stark Group.
As a result of the acquisition, MMC Group will have tungsten operations in four major markets: Japan, Europe, North America and China.
MMC stated that Japan New Metals Co, Ltd (a wholly owned subsidiary of MMC) and HC Starck will work together to create synergies and increase corporate value by strengthening R&D capabilities and promoting cross-selling, as well as developing a global tungsten recycling business.
Dr Hady Seyeda, CEO of HCS, stated, “We know and appreciate Mitsubishi Materials as a longstanding customer and as an investor whose activities in Japan perfectly complement our global presence. Following the signing of the agreement, we will now focus on discussing the relevant strategic and operational issues and taking the appropriate steps.”
www.masanhightechmaterials.com www.mmc.co.jp www.hcstarck.com
involved in rare earth mining, smelting and separation, as well as the export of rare earth products, will need to establish a product flow record system and accurately record the flow of products when entering them into the traceability system.
Last year, China imposed restrictions on the export of germanium and gallium, which are used in chip-making, in order to protect national security and interests. Additionally, China banned the export of technology used to produce rare earth magnets and placed restrictions on technology used for the extraction and separation of rare earths.
These new rules raise concerns that limitations on rare earth supplies could further escalate tensions with the West, especially the United States.
www.reuters.com
Mitsubishi Materials Corporation Group will acquire all shares in H C Starck Holding GmbH (Courtesy H C Starck Holding GmbH)
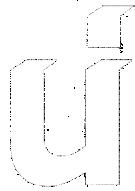
A SOLID LINE OF THINKING: SINTERING WITH A SOLID INFILTRANT
SOLIDIFY YOUR CASE FOR ULTRA INFILTRANT
There’s a solid line of thinking in the copper infiltration of ferrous PM parts and it can change the way you do business. Ultra Infiltrant is a wrought, homogeneous copper-based alloy that offers significant benefits over powder form copper infiltrants. Benefits like less waste, improved productivity, reduced erosion, no adherent residue and increased strength and hardness values. Benefits that affect your production line and ultimately your bottom line. Ultra Infiltrant is available in single and multi-turn wire rings, straight-length slugs, or other configurations to accommodate virtually any automated process. Ultra Infiltrant was designed for copper infiltration of ferrous PM parts in today’s cost competitive manufacturing environments, where the handling of fragile green infiltrant slugs is difficult and can lead to excessive waste. Additionally, it performs well in nitrogen-hydrogen based atmospheres so widely used in sintering operations globally.
SOLIDIFY YOUR INFILTRATION PROCESS FOR ULTRA INFILTRANT
Less waste, easier production, superior product: what more is there? Ultra Infiltrant revolutionizes the PM industry by eliminating all the negatives associated with infiltrant powders and improving on the process as a whole. The net result? How about overwhelmed customers and a boost to your bottom line? That’s what Ultra Infiltrant offers, so put it to work and get started on a solid line of thinking.
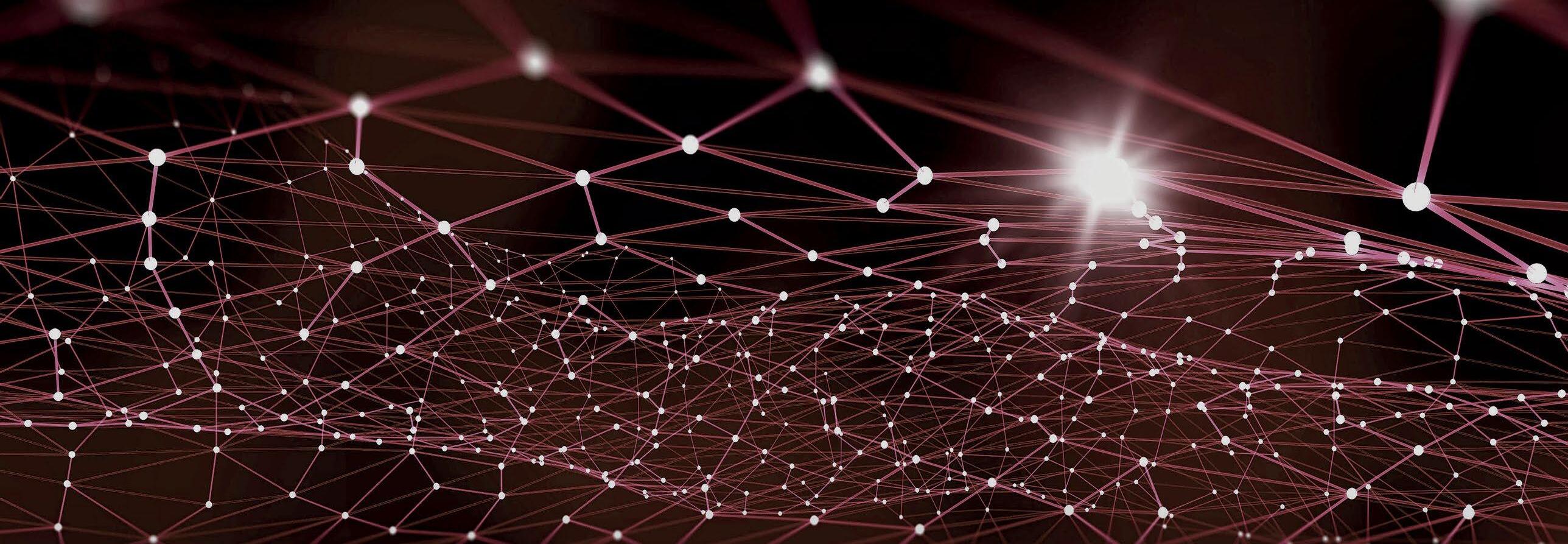
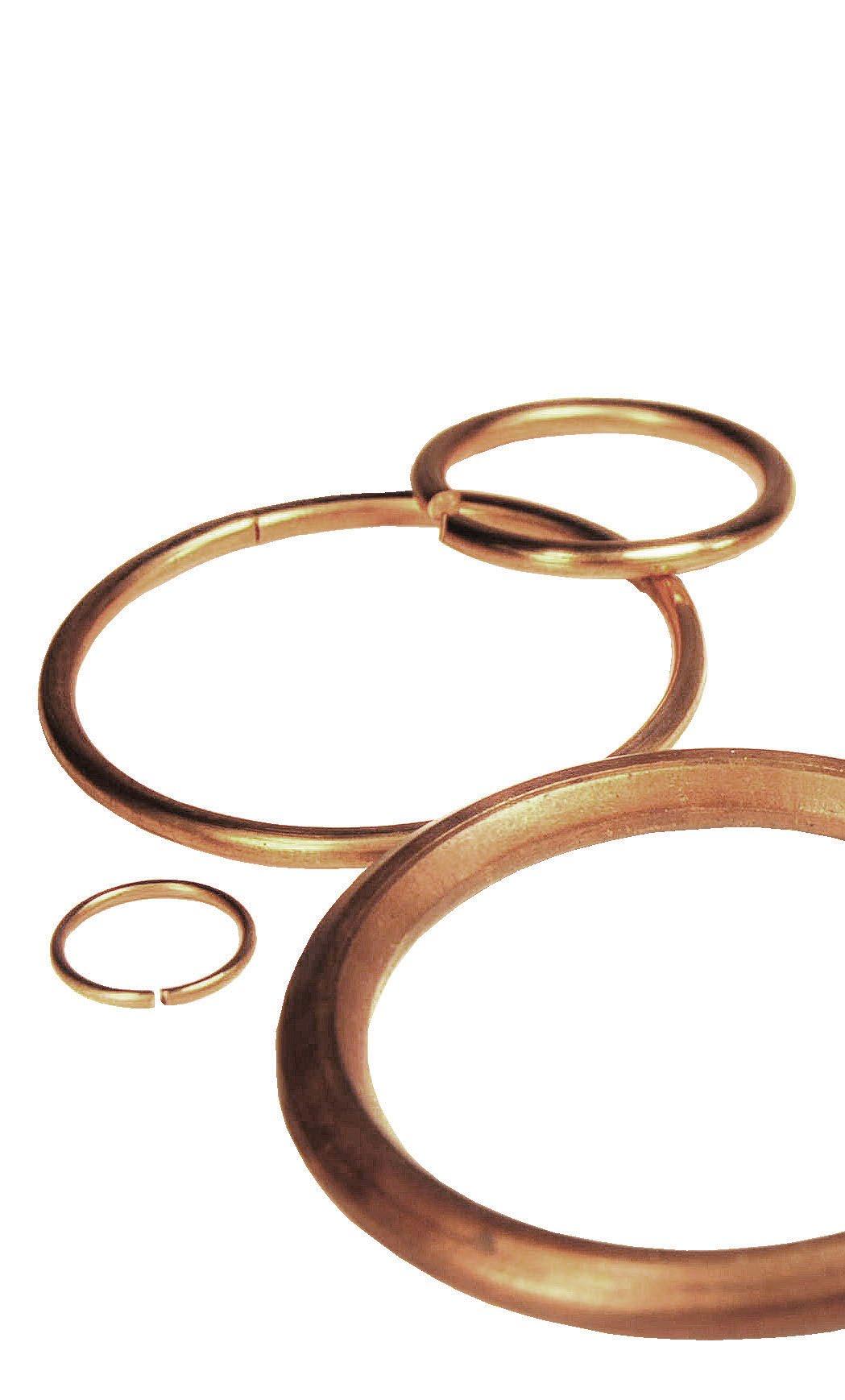
Levine Leichtman Capital Partners acquires NSL Analytical Services
Levine Leichtman Capital Partners, headquartered in Los Angeles, California, USA, has announced that it has acquired NSL Analytical Services, Inc, based in Cleveland, Ohio, in partnership with its management.
NSL, founded in 1945, is a materials testing provider serving a diverse client base across highly regulated and technologically advanced end markets, including aerospace and defence, advanced materials, and electronics. NSL’s experienced chemists, metallurgists and technicians are experts in testing a wide range of materials and finished components, serving the recurring and non-discretionary testing needs of clients throughout the US and the world.
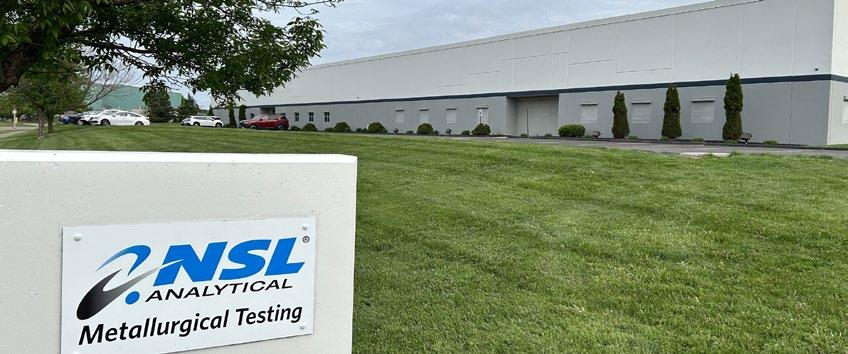
Levine Leichtman Capital Partners has acquired NSL Analytical Services in partnership with its management (Courtesy NSL Analytical Services)
“We are thrilled to partner with NSL, a leader in the materials testing and analysis sector,” stated Matthew Frankel, Managing Partner at LLCP.
“NSL has established itself as a trusted partner for a loyal client base across numerous high-performance industries. We are excited to work with the NSL team to broaden the company’s testing capabilities and geographic footprint through both organic initiatives and strategic acquisitions.”
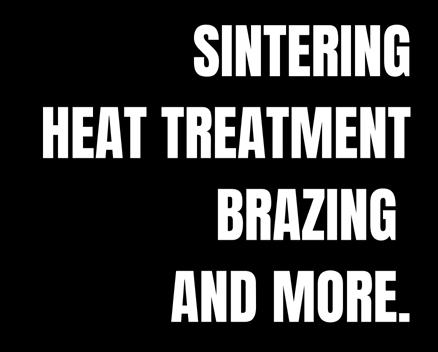
“Our new partnership with LLCP will further guide and fuel NSL’s growth in support of the critical quality assurance testing our team delivers to clients world-wide,”
CEO Ron Wesel shared. “In an everincreasing technology-driven world, NSL’s material testing capabilities provide the confidence and security demanded by traditional and evolving production methods such as AM.” www.nslanalytical.com www.llcp.com
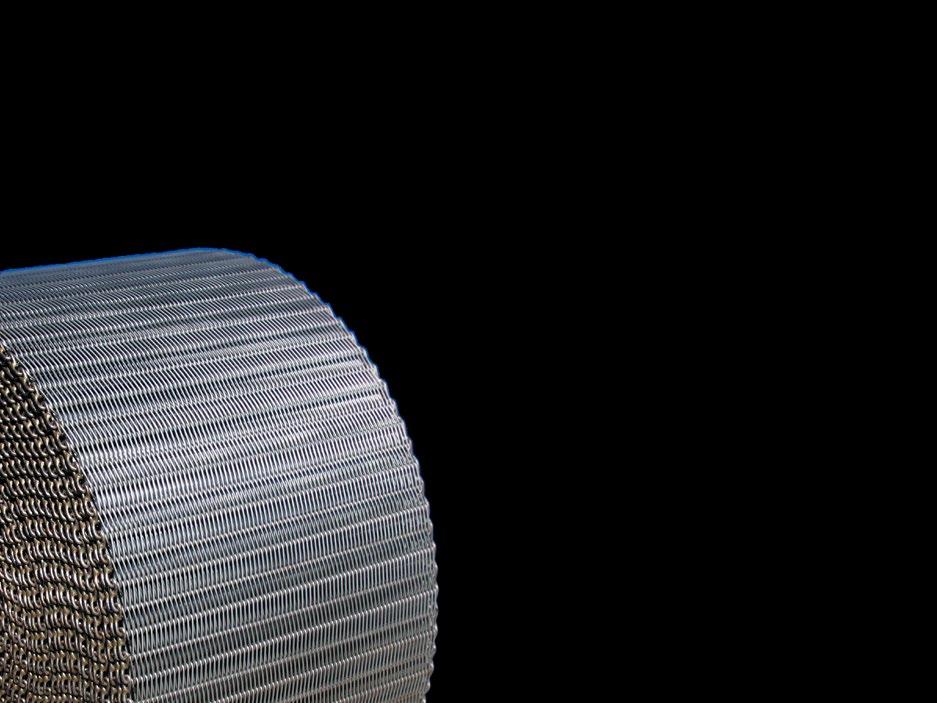
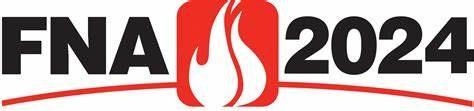
October 14-16,2024 - Columbus Convention Center
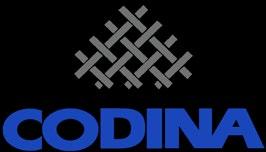
Established in Barcelona, We are the biggest manufacturer of mesh belts for sintering furnaces with global presence around the globe
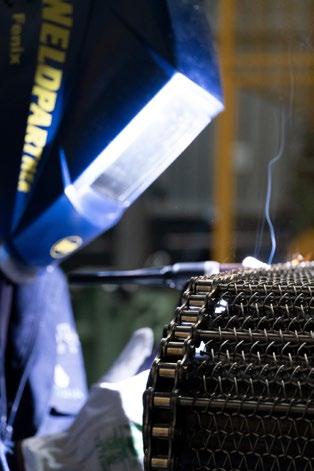
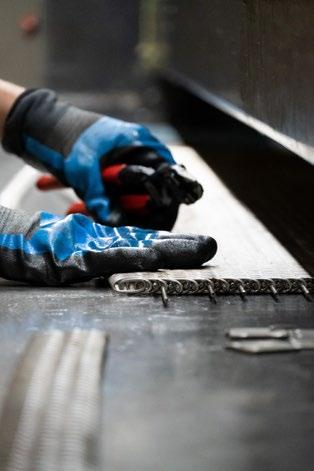

Seco/Warwick expands USA furnace manufacturing operations
Seco/Warwick Group, headquartered in Swiebodzin, Poland, has announced plans to expand its operations in the USA. The group, parent company of Seco/Vacuum and Seco/Warwick USA, has committed to expanding its manufacturing capacity in Pennsylvania by relocating a portion of its manufacturing, and a metallurgical lab for vacuum furnaces, from Poland to Crawford County.
In support of the expansion plans, the government of Pennsylvania has awarded the company a $2 million package of matching fund grants from the Department of Community and Economic Development through its Redevelopment Assistance Capital Program (RACP). The primary use and intent of the RACP fund is for reimbursement of eligible construction costs which Seco/Warwick Group companies will match on a 1:1 basis.
Seco/Vacuum manufactures heat-treating furnaces specialised for heat-treatment processes that must be conducted inside a vacuum chamber to prevent contamination from atmospheric gases. Seco/Warwick USA manufactures atmosphere heat-treatment furnaces, aluminium melting furnaces and controlled aluminium brazing (CAB) furnaces.
The expanded facility will benefit the community as well as the heat-treatment equipment manufacturer’s customers. The company will begin upfitting their nowempty factory floor in the Crawford Business Park, which itself was recently redeveloped from the long-abandoned American Viscose Corporation’s synthetic textile mill in Meadville, Pennsylvania, USA.
At its peak in the 1950s, the mill employed nearly half of Meadville. After many decades of operation, the mill closed in 1986. Beginning in 1989, the Crawford County Redevelopment Authority, the predecessor to today’s Economic Progress Alliance of Crawford County, invested in cleaning, remodelling, and subdividing the millionsquare-foot plant into more than fifty smaller commercial and industrial spaces.
The added capabilities look to improve the company’s response to its North American customers’ needs, not only through manufacturing but also through the addition of parts, service, and training capacity. At the same time, the new facility will require an expanded staff, at both entrylevel and skilled positions, providing new opportunities to workers in Meadville and the surrounding communities.
“We look forward to working with our local partners including the City of Meadville, the Economic Progress Alliance of Crawford County (EPACC), the Workforce and Economic Development Network (WEDnet), and the Pennsylvania Department of Community and Economic Development (DCED) to make this expansion happen,” said Piotr Zawistowski, SECO/VACUUM President, Managing Director.
www.secovacusa.com
Meet the all new LAUFFER E- CELL
Powder Press System with integrated automation
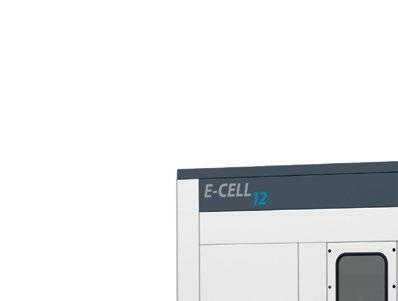
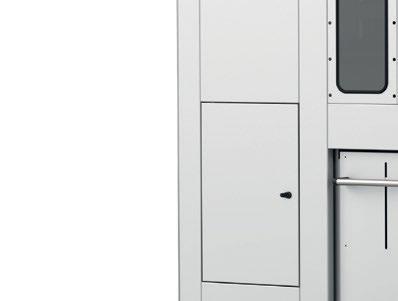
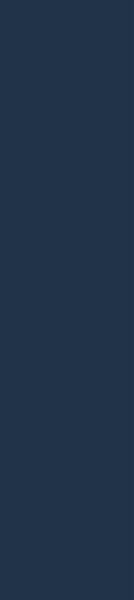
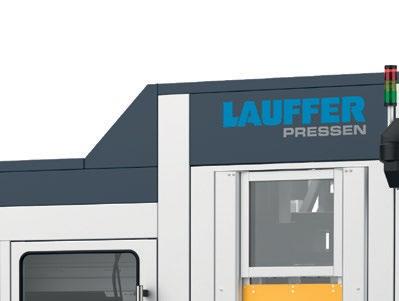
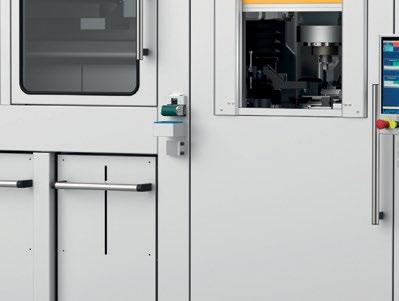

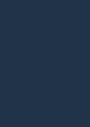


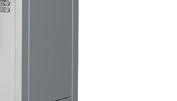
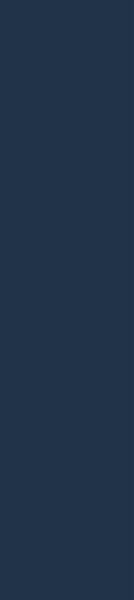
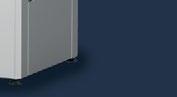
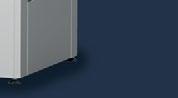
Powder Press System with integrated Automation:
• Fully integrated ejection press system with robot-based parts handling
• One LAUFFER control unit for the complete press cell
• State of the art drive technology for highly energy efficiency
• Unmatched press precision
• IoT ready
LAUFFER GmbH & Co. KG
Industriestr. 101, 72160 Horb, Germany T +49 7451 902-0 F +49 7451 902-100 E lau er.pressen@lau er.de W www.lau er.de
Maschinenfabrik
Osterwalder delivers its first 1000kN multi-plate servo electric press
Osterwalder AG, Lyss, Switzerland, reports that it delivered its first 1,000 kN servo-electric multi-plate press, the OPP 1000, in July 2024. The press is said to use a unique combination of the servo electric main-drives, hydraulic plate-drives for the powder transfer phase and CNC controlled mechanical stops.
“Around 2015 it became clear to us that the future of powder pressing is electric. These presses have only advantages: more precision, reduced energy consumption, reduced noise, reduced maintenance costs, etc. With the latest developments in electro-mobility and micro-mobility, it also became clear that, after the successful launch of the OPP 2000 (Osterwalder’s 2000 kN press) in 2018 and the OPP 5000 (Osterwalder’s 5000 kN press) in 2022, the next one will be smaller again,” commented Rolf Graf, owner and CEO.
“This press is not only the latest of the new multi-plate product-line, it is also the most mature press Osterwalder has made,” stated David Benczur, Global Head of Sales Iron Powder. “The structure is based on the successful design of the previous hydraulic presses of the same size, the Control System is derived of larger OPP presses, and it operates with the latest version of our wellknown HMI. But it also includes some new tricks, for example a kinetic energy battery that reduces the peak-currents.”
Osterwalder launched the world’s first CNC-controlled powder press in 1989. The OPP 1000 is the latest member of the multi-plate series.
“Our discussions with our customers conclude usually on short returns on investment (ROI), typically within one to three years, sometimes even comparing to already amortised used presses. High stroke-rates
Neo Performance Materials sells Quapaw rare metals facility
Neo Performance Materials Inc, headquartered in Toronto, Canada, has announced that it has entered into an agreement to sell its equity ownership interest in Neo Rare Metals, LLC, Quapaw, Oklahoma, USA, to Kevin Reading, the current General Manager and co-founder of the facility. The transaction is said to continue Neo’s drive to simplify its business globally, by focusing on portfolio assets that reflect the company’s scale and growth ambitions in a competitive global business environment.
Reading has agreed to purchase Neo’s 80% equity interest in the Quapaw location in consideration for an aggregate cash purchase price equal to $1.4 million plus cash on closing, subject to normal closing adjustments, which represents a 9.0x multiple of trailing
twelve months of the EBITDA of the facility.
The transaction is part of Neo’s operational transformation and production optimisation commitment to simplify global operations. It includes a five-year agreement for the purchase by Quapaw of gallium and indium from the company’s recycling facility in Peterborough, Ontario, as well as for the processing and transfer of gallium scrap to the company’s Peterborough recycling facility.
“We continue Neo’s global transformation and optimisation of our asset base. The sale of the Quapaw facility back to its founder is an exciting opportunity for both of us to benefit in the long-term. I look forward to our continued partnership with the entrepreneurial owner-operator team at Quapaw. Mr Reading has
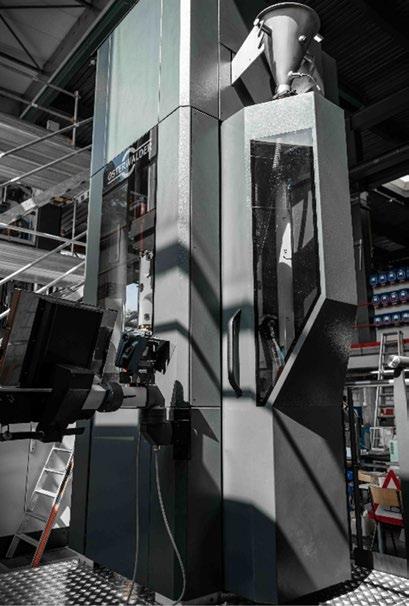
Osterwalder offers a range of multi-plate presses (Courtesy Osterwalder AG)
play a role of course, but precision, reliability and also short set-up and learn-in times for the work force are equally important to maximise good parts produced continuously week after week.”
www.osterwalder.com
always been a valued partner and great business leader. We are excited for Kevin, the team at Quapaw and for the continued growth opportunities for this facility as a focused entity,” stated Rahim Suleman, president and Chief Executive Officer of Neo.
“We are thrilled to purchase back the business we founded as we look to grow operations in Quapaw, Oklahoma,” shared Kevin Reading, General Manager of Quapaw. “Our relationship with Neo over the years has led this facility to improvements in health and safety initiatives that has truly made us a better facility. Our strong management team will continue to work closely with our Neo partners to ensure that together, we can meet the needs of both facilities and our customers’ needs.” The transaction is subject to customary conditions to closing and is expected to close in the third quarter of 2024. www.neomaterials.com
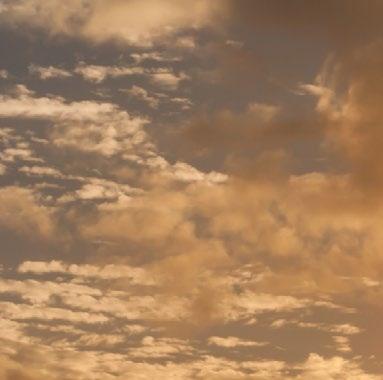
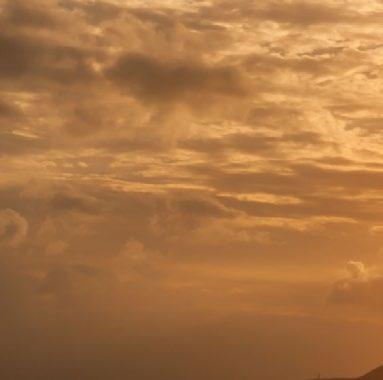

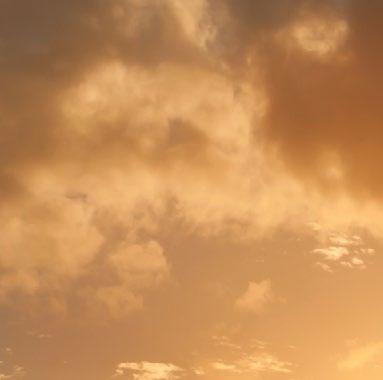
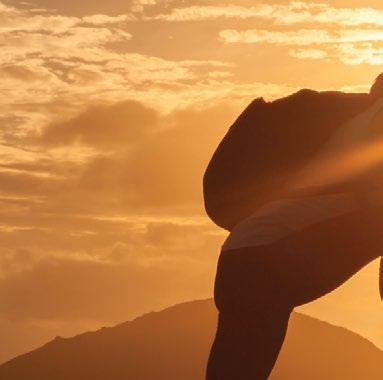
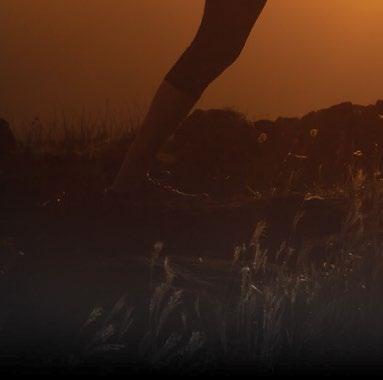
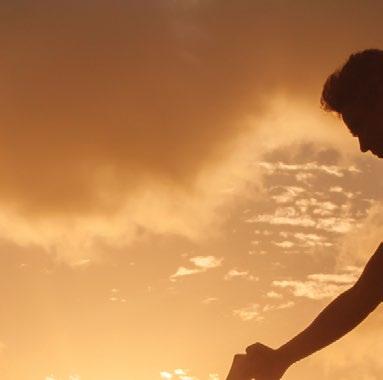
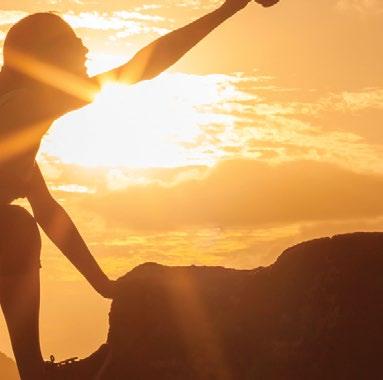
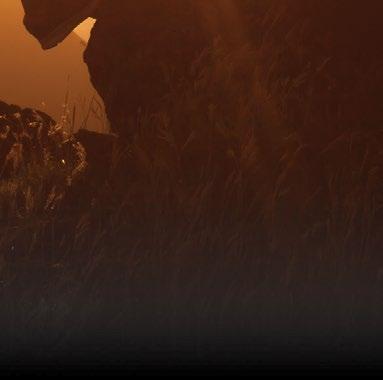
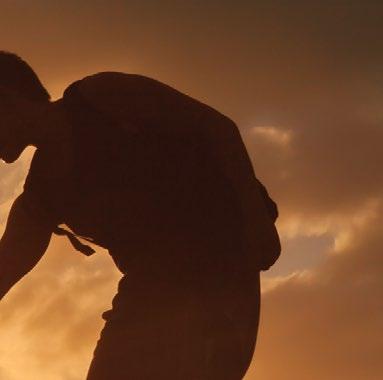
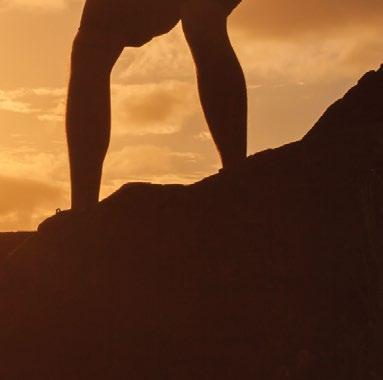
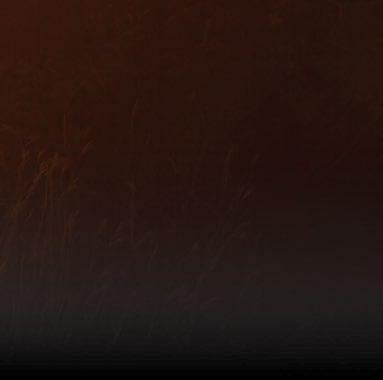
A remarkable milestone
A quarter of a century. We could have only accomplished this by forging solid partnerships, friendships and collaborations build on trust, integrity and commitment.
DSH Technologies is the GO-TO support team for helping to process metal powder parts and materials. Real world solutions to real world problems, we can help solve technical, process and engineering related issues.
• Remote or In-Person process support
• Toll Debind and Sinter Services – “You Print It, You Mold It – We Debind & Sinter It”
• In person facility walk through, process evaluation, and education programs For the past twenty five years, DSH is the only source for the best process support, toll processing and educational resource for your MIM and Metal AM applications.
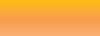



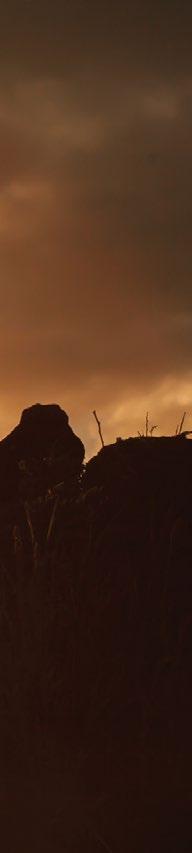

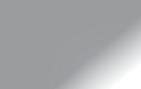




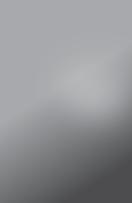












Tooling for Powder Compacting Technology
• Simple, quick set-up • High accuracy • Low scrap rate • Maximal machine utilization
Increased productivity
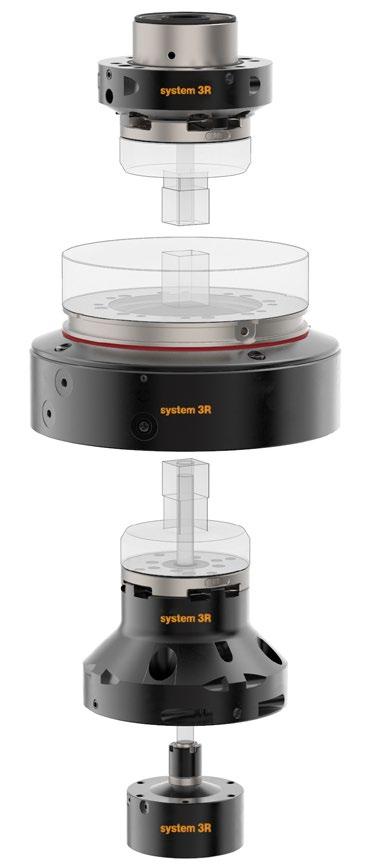
Ametek SMP launches new High Green Strength Stainless Steel Powders for Powder Metallurgy
Ametek Specialty Metal Products (SMP), Collegeville, Pennsylvania, USA, has announced the launch of its new ‘High Green Strength Stainless Steel Powders’, suitable for a wide range of automotive and industrial Powder Metallurgy parts.
The new High Green Strength Powders consistently provide a 50% or greater improvement in green strength in 300 and 400 series stainless steel grades relative to powders mixed with standard EBS wax. This enhancement is said to have minimal impact on sintered density, dimensional change, and other properties.
Manufactured using advanced water atomisation technology, the High Green Strength Powders are reported to reduce part damage during die ejection and part transfer, leading to more efficient processing and lower manufacturing costs.
www.ametekmetals.com
Plansee and Ceratizit open shared office in Singapore
Plansee, headquartered in Reutte, Austria, and Ceratizit, part of the Plansee Group and headquartered in Mamer, Luxembourg, have announced the official opening of their new shared office at the German Centre, Singapore. The event was attended by guests and key partners.
The new office is designed to foster collaboration and efficiency, supporting the companies’ mission to drive sustainable growth and deliver value to their customers in the expanding Southeast Asian markets.
Alexander Tautermann, Director – Marketing & Sales, Plansee, stated, “Ten years ago, Plansee started our own sales office in Southeast Asia. I am delighted that we can celebrate the ten-year anniversary together with the announcement of a very close cooperation between Plansee and the Ceratizt Group. Our shared office in Singapore is a testament to the strong partnership between both companies in this very important region. It will serve as a hub for our mutual cooperation and be our centre of excellence, allowing us to better serve our customers and achieve our strategic goals.”
Andreas Fritz, President – Asia Pacific, Ceratizit Group, added, “This new office represents our commitment to expanding our footprint in Southeast Asia and delivering superior support and services to our customers in the region. We look forward to leveraging this space to drive innovation and strengthen our market presence.”
www.plansee.com | www.ceratizit.com

IperionX reports first successful HAMR titanium furnace production run
IperionX, based in Charlotte, North Carolina, USA, has announced the successful commissioning of its commercial-scale Hydrogen-Assist Metallothermic Reduction (HAMR) furnace. This marks the first titanium de-oxygenation production run at the Titanium Manufacturing Campus in Virginia, USA.
“The IperionX team delivered an important technological and commercial milestone for the global titanium industry,” stated Anastasios (Taso) Arima, IperionX CEO.
“Over the last two years, we have successfully operated our pilot titanium production facility in Utah, producing high performance titanium products for customers and - importantly – delivering first revenues for our company. Today,
we demonstrated that our HAMR technology works at commercial scale. We successfully increased the furnace production capacity by ~60x and produced high performance titanium that exceeds industry quality standards,” continued Arima.
IperionX’s proprietary HAMR technology offers a range of competitive advantages, including lower operating temperatures, reduced energy consumption, enhanced process efficiency, and accelerated production cycles – all achieved with lower capital investment intensity.
Produced entirely from 100% scrap titanium (Ti6Al4V alloy, Grade 5 titanium), quality assessments confirmed a large reduction in


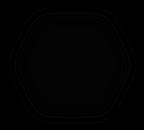
oxygen levels from 3.42% to below 0.07%, exceeding the ASTM standard requirement of 0.2% for Grade 5 titanium.
Over the coming months, IperionX will commission and optimise the supporting process equipment to achieve full system production capacity in Virginia, with end-to-end system operations expected in late 2024.
“IperionX plans to expand the capacity of its Titanium Manufacturing Campus by adding modular, low-risk and low-cost HAMR furnaces. IperionX aims to be a leading US titanium producer of +10,000 metric tons per annum by 2030. Our goal is to re-shore the full titanium supply chain to the United States, at lower costs for our customers, and deliver the most sustainable titanium products on the market,” Arima concluded. www.iperionx.com
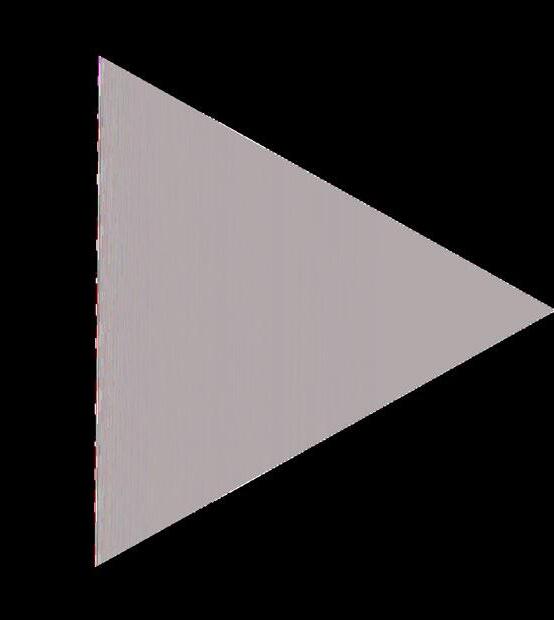
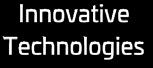
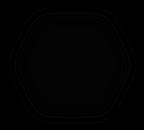
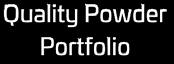

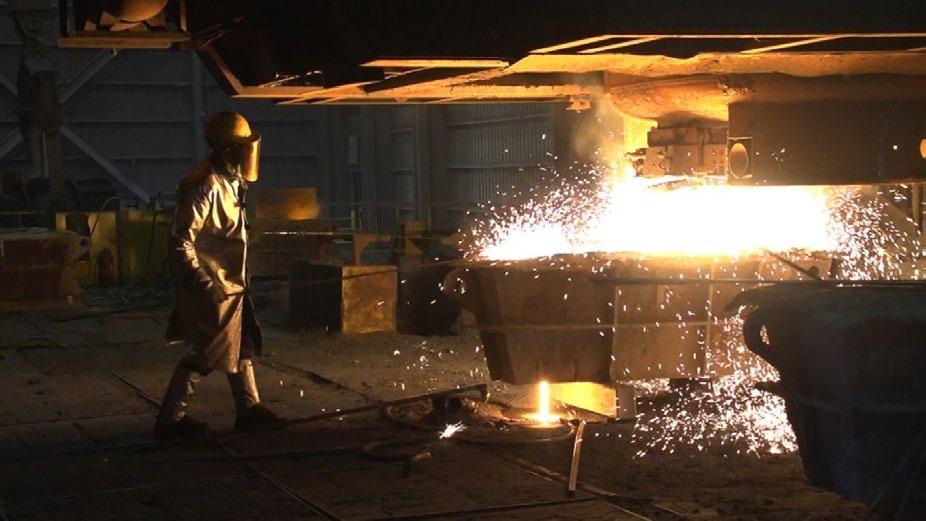





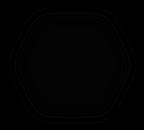
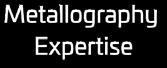
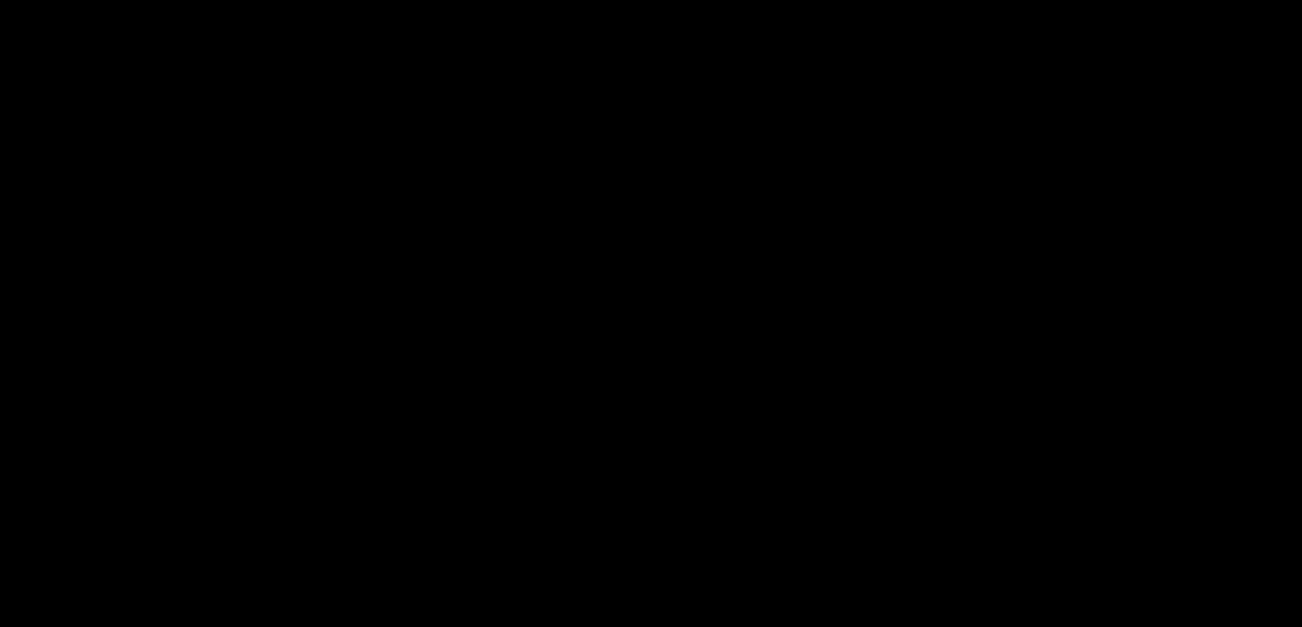
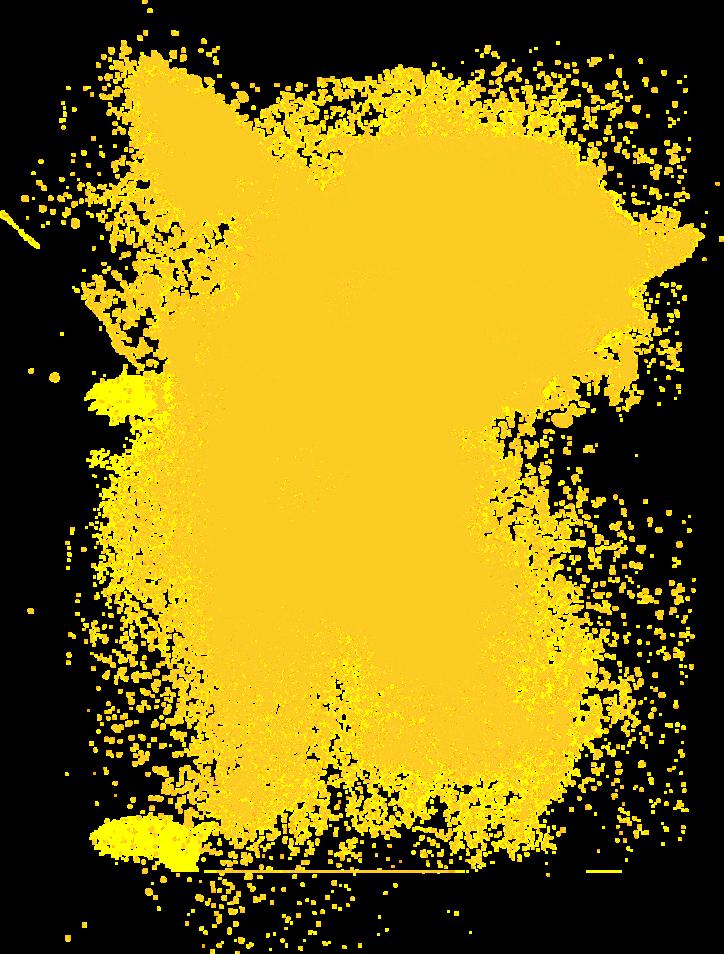







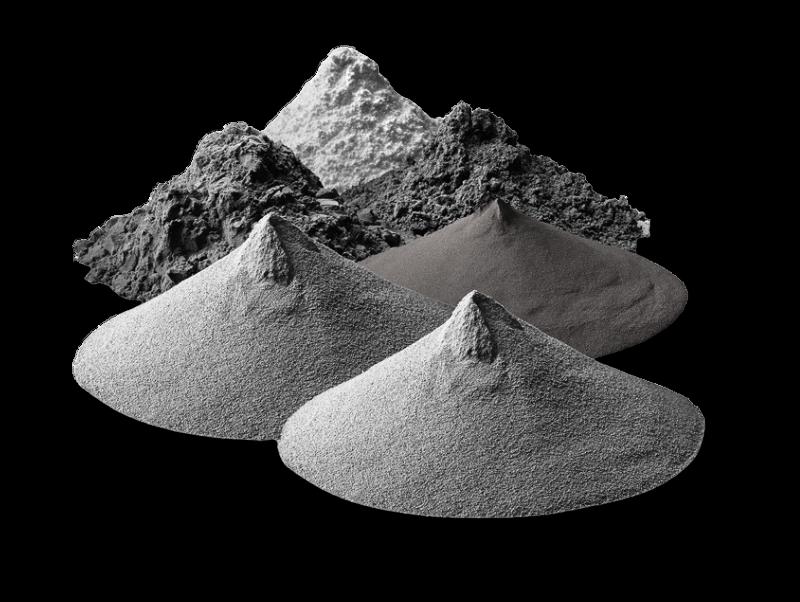

KBM adds IMR’s aluminium powders to its online marketplace
IMR Metal Powder Technologies, Velden am Wörthersee, Austria, has finalised its agreement with KBM Advanced Materials, LLC, based in Fairfield, Ohio, USA, for sale and distribution of IMR’s aluminium powders through KBM’s metal powder distribution network.
IMR has been a provider of industrial metals, semi-finished products, and chemical products for over thirty years, marketing its products globally. There will now be a dedicated stock of IMR material at KBM’s warehouse in Ohio, providing access to producers of aluminium parts.
IMR primarily produces aluminium alloy powder for the Additive Manufacturing industry. It partners in the development and production of customer-specific powders for Laser Beam Powder Bed Fusion (PBF-LB), Direct Energy Deposition (DED), and other processing technologies.
Thomas Rimmer, IMR CEO, stated, “By offering our aluminium alloy powders on the platform of KBM, our US customers now have access to their products on short-term notice which supports their inventory management optimisation as well as fast response to new business opportunities in a still evolving and

Metal Powder Group names new Technical Director
Metal Powder Group, Stockholm, Sweden, has named Rajiv Tandon as its new Technical Director. Tandon is an experienced technologist, noted as having a deep understanding of metal powder processing, specifically in process development,
powder production, and powder metal characterisation.
“I am pleased to have Rajiv joining us at Metal Powder Group,” stated Greg Chirieleison, Group CEO. “He brings a wealth of powder processing experience and will ensure our customers receive topquality tech support and engineering assistance. I look forward to seeing the innovations and improvements he will bring to our family of companies.”
sometimes difficult to predict market environment. The availability of IMR’s products to the US AM community from a local warehouse with the expert service of KBM were the main reasons for moving into this exciting opportunity.”
KBM offers products and services to AM powder consumers in the USA and Canada. Its business model results in KBM having large amounts of stock available for order at any given time, allowing customers to order and receive metal powder quickly and efficiently. KBM is reputedly North America’s largest marketplace for metal powders, allowing customers access to a variety of alloys and producers. It also offers transparent pricing and access to a variety of producers.
Kevin Kemper, KBM CEO, shared, “KBM is excited to partner with IMR to increase accessibility of their metal powders in North America. On-demand availability of products differentiates producers into those that can ship product when consumers need it and those that have a lead time. Our e-commerce solution features an easy-to-use interface, secure online transactions, detailed product information, pricing transparency, and the ability to ship products within a day of purchase. We want it to be easy and efficient for part producers to procure the raw materials they need to be successful. IMR is a strong and exciting addition to our offering.”
www.kbmadvanced.com www.imr-metalle.com
Tandon has previously held positions at Phillips Metal Injection Moulding, Parmatech, Amulaire Thermal Technology, Magnesium Elektron Powders, Luxfer Magtech, and Chemalloy. He holds a Bachelors Degree in Metallurgical Engineering from the Indian Institute of Technology, Kanpur, and a PhD in Engineering Science and Mechanics from Penn State University, USA. www.metalpowdergroup.com
IMR Metal Powder Technologies produces a range of metal powders, including aluminium powder (Courtesy IMR Metal Powder Technologies)
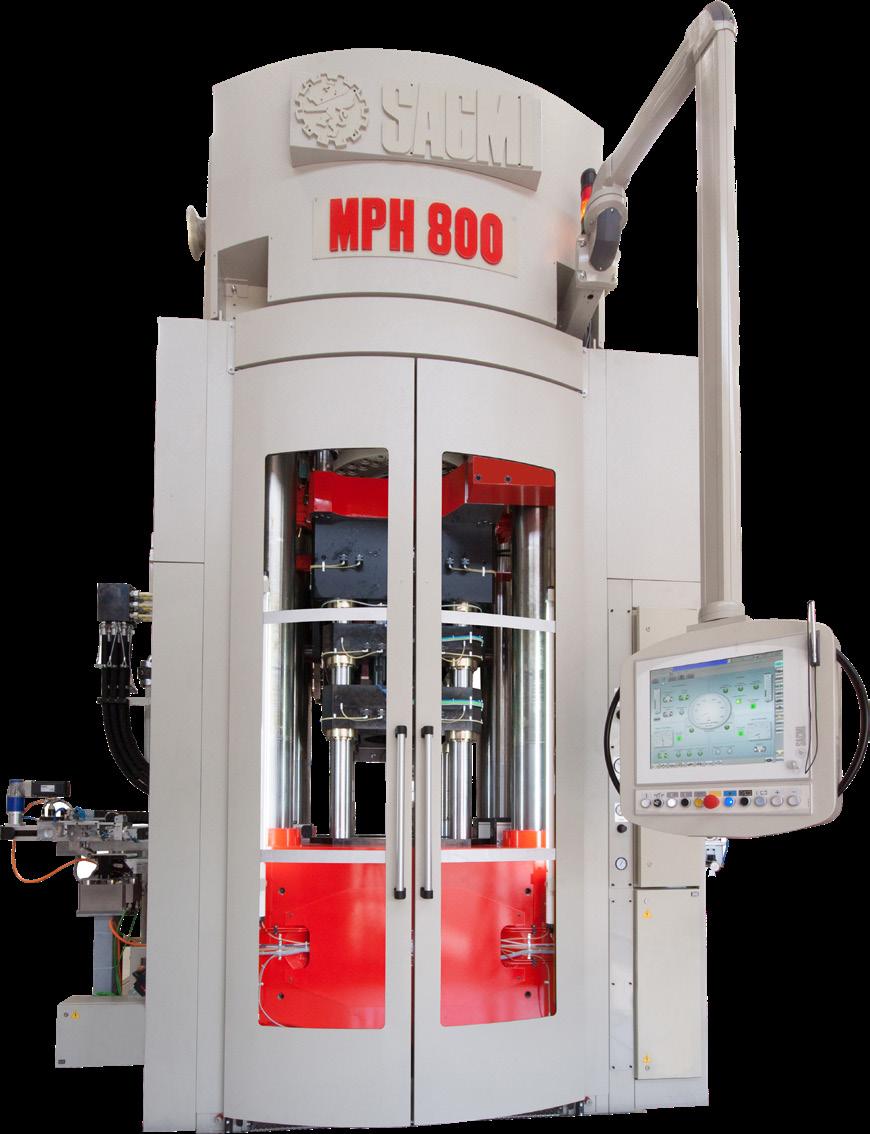
POWDER METAL SOLUTIONS
The transformation of the Automotive Industry toward electrification is driving the Powder Metal world to innovations related to the production of components that had never been produced before.
The result can be observed in the recent production of powder metal parts with full density and helical gears with angles up to 45°, which is a decisive goal for the Press&Sinter technology.
In addition, besides the Automotive industry, even companies involved in different industries have the opportunity to take advantage from these new techologies to enter new sectors. Follow SACMI in its journey towards electrification.
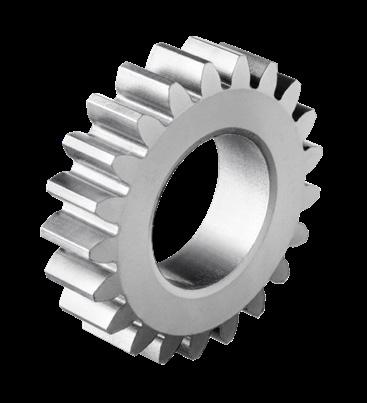
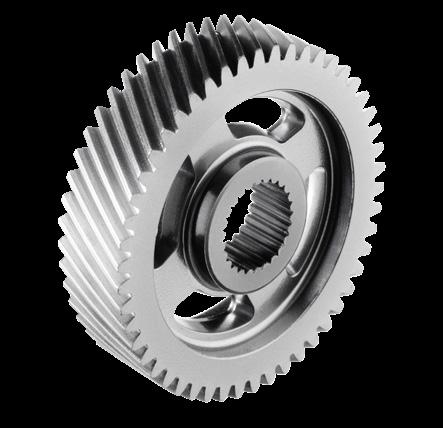
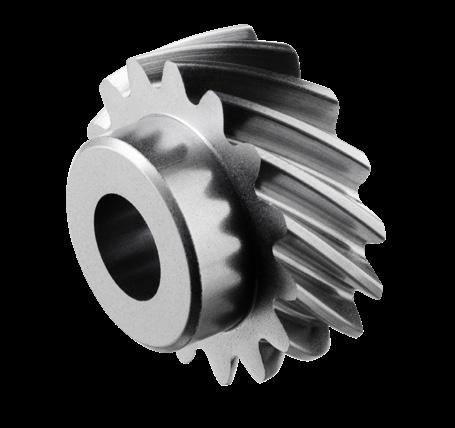
Desktop Metal launches PureSinter sintering furnace
Desktop Metal, Inc, headquartered in Burlington, Massachusetts, USA, has announced the launch of its PureSinter furnace. Capable of debinding and sintering metal parts created via Binder Jetting (BJT) Additive Manufacturing, the new furnace is also suitable for parts produced using traditional Metal Injection Moulding (MIM) and Press and Sinter Powder Metallurgy (PM) methods.
In development for more than five years, PureSinter features hot walls that prevent contamination buildup and an airtight processing environment to enable efficient waste exit and high levels of purity.
Contamination can be caused by hydrocarbons and other waste emitted by the powdered metal parts, explains Desktop Metal. This builds up on walls and other surfaces inside the furnace and can cause undesirable chemical reactions and furnace reliability.
PureSinter has undergone extensive testing and is reported to show little to no contamination or buildup inside the furnace, even after hundreds of runs.
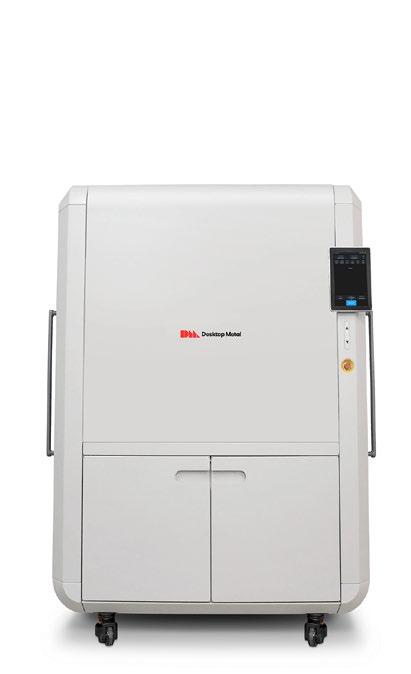
“Rather than trying to simply mitigate the factors that lead to poor performance in an all-in-one debinding and sintering furnace, we have eliminated them with an innovative all-new design,” stated Ric Fulop, founder and CEO of Desktop Metal. “This is the first product from Desktop Metal aimed at manufacturers using both Additive Manufacturing and traditional manufacturing methods.”
“We have put the PureSinter through a prolonged period of testing to rigorously verify our new design, and it has exceeded all expectations. PureSinter is an exemplary demonstration of the innovation for which Desktop Metal and our engineers are known. We believe this furnace will revolutionise sinter-based AM and the traditional furnace industry.”
The PureSinter furnace can reach a maximum temperature of 1,420°C and is qualified for use with a variety of processing gases, including argon, nitrogen, forming gas, and air. The machine features a total of seventeen fans and a pop-out ceiling vent for active,


rapid, and consistent cooling, lowering temperatures from 1,420°C to 200°C in less than four hours and without expensive water-cooled walls.
PureSinter features a vertical furnace design, an automated thermal hood lift, touchscreen controls, and visibility inside the retort. With an oxygen-tight retort seal, and its efficient cooling system, the energy requirements are also reported to be lower than similar machines.
The new furnace is compatible with all of Desktop Metal’s metal AM machines and binders. It is also validated with fourteen metal powder and binder combinations, including stainless steels, tool steels, superalloys, and reactives. PureSinter can also process titanium with a high degree of confidence without the complex preparations which may be required with other furnaces. It was added that additional material validations are in process.
The first PureSinter furnace has been installed at FreeFORM Technologies, a metal Binder Jetting contract manufacturer based in St. Marys, Pennsylvania, and the largest owner of a fleet of twentyfour Desktop Metal AM machines, to validate new materials.
Shipments of the PureSinter furnace are slated to begin in the third quarter of 2024. www.desktopmetal.com
The PureSinter furnace is suitable for the debinding and sintering of Binder Jetting parts as well as MIM and PM parts (Courtesy Desktop Metal)
Loading the PureSinter furnace is straightforward (Courtesy Desktop Metal)

Ervin’s Amapowder metal powders now available in Europe
Ervin Metal Powders, headquartered in Ann Arbor, Michigan, USA, is now offering a range of Amapowder metal powders, suitable for Additive Manufacturing and Metal Injection Moulding, to customers in Europe through its sales office in Berlin, Germany.
Ervin currently includes 304L, 316L and 17-4 PH stainless steel powders in the Amapowder range. The powders are produced using the company’s Rapid Solidification Rate (RSR) and Centrifugal Atomisation technology, reported to create fine-grained (nanometre-scale) and amorphous metals with uniform chemistry and a highly spherical shape. These characteristics are said to give the powders good flow and packing behaviours.
“We are delighted to be able to offer this exciting new range of prod -
ucts and are already collaborating with several Additive Manufacturing companies to help them deliver better quality and value solutions to their customers,” stated Florian Götz, Innovation Director for Ervin Europe.
Using RSR atomisation, Ervin states that it has developed a wide variety of metal powders for many industries and applications. The company has been able to collaborate with a range of industries and research professionals to advance spherical metal powder technology.
Ervin also operates several centrifugal atomisation rigs that enable it to produce both small R&D powder batches and maintain the continuous production of powders at large scales.
Amapowder is suitable for a variety of Additive Manufacturing production processes, including
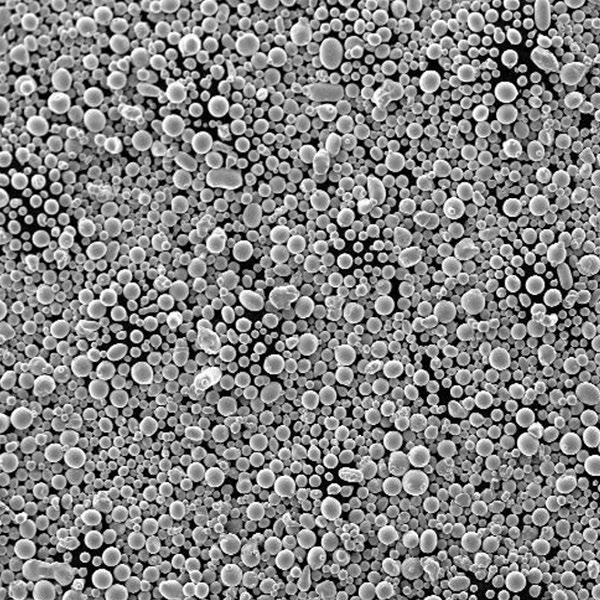
Amapowder 316L is suitable for metal Additive Manufacturing and Metal Injection Moulding, as well as Hot Isostatic Pressing and thermal spray (Courtesy Ervin Metal Powders)
Laser Beam Powder Bed Fusion (PBFLB), Binder Jetting (BJT), and Directed Energy Deposition (DED). In addition to Metal Injection Moulding, it is also suited to thermal spraying and Hot Isostatic Pressing (HIP).
www.ervin.eu

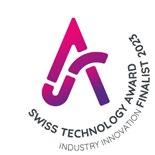

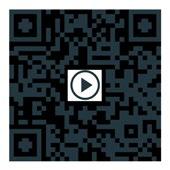
UK’s Langley Holdings acquires GKN Hydrogen
Langley Holdings, based in Retford, UK, has acquired GKN Hydrogen from parent company Dowlais Group plc. Headquartered in Pfalzen, Italy, with subsidiaries in Germany and the United States, GKN Hydrogen will become part of Langley’s Power Solutions Division.
Anthony Langley, chairman and CEO, Langley Holdings, stated, “This acquisition underscores Langley Holdings’ strategic focus on sustainable energy solutions and commitment to a greener future.”
Formerly part of GKN Powder Metallurgy, the company has brought together materials science and engi -
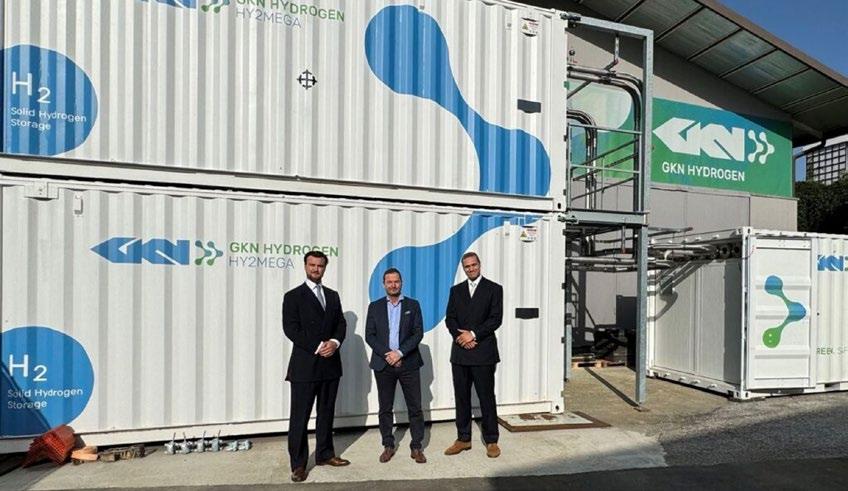
Malvern Panalytical to acquire Micromeritics
Malvern Panalytical, part of Spectris plc, Egham, Surrey, UK, has agreed to acquire Micromeritics, headquartered in Norcross, Georgia, USA, for $630 million, plus a deferred element of up to $53 million. Micromeritics focuses on analytical instrumentation for the physical characterisation of particles, powders, and porous materials.
With the addition of Micromeritics’ suite of analytical technology, Malvern Panalytical aims to provide the broadest material characterisation offering in the market. It will offer a single suite of integrated instruments from a single manufacturer to support the entire customer workflow, thereby improving workflow efficiency and enabling deeper analytical insights.
As part of the acquisition, Terry Kelly, president and Chief Executive of Micromeritics, has agreed to join the group as Malvern Panalytical President. Kelly will be a key member of the Spectris Scientific leadership team.
Micromeritics’ technologies enable the comprehensive characterisation of particles by detailing their size, count, surface properties and behaviour, for fundamental research, product development and production quality control.
“Together, Micromeritics and Malvern Panalytical provide a unique opportunity to create a leading and highly differentiated position and a fully integrated offering in mate -
neering to create advanced metal hydride compounds. This technology captures and stores hydrogen in a solid state form at 16x the density of compressed hydrogen gas without degradation for up to thirty years, according to company literature.
Hydrogen is converted back to a gas when required by heating the hydride to 60ºC. The company has proven the system over 7,000 charge/discharge cycles with 99% efficiency.
Langley Holdings, established in 1975, is a privately owned engineering and industrial manufacturing group, principally producing capital equipment for diverse global markets. The Group operates in three principal areas: Power Solutions, Print Technologies and Other Industrials.
The Group’s operations are based in Germany, Italy, France, the UK, and Norway, with eighteen production facilities in Europe, the UK, and the USA. The group has more than ninety sales and service subsidiaries worldwide and employs around 5,500 people.
www.langleyholdings.com www.gknhydrogen.com
rial characterisation,” stated Derek Harding, current CFO at Spectris and soon-to-be president of Spectris Scientific. “Micromeritics is an excellent business with a strong track record of growth and innovation and excellent future growth prospects.”
Terry Kelly added, “Micromeritics is a world leader in particle characterisation. Our market-leading technologies are used daily in the labs of the world’s most innovative companies and institutions. Our end markets are strong and growing, and we have a robust new product pipeline. The integration with Malvern Panalytical is powerful. Together our companies will be able to unlock more answers for customers and provide expert applications and technical support that cannot be matched by any other company.”
www.malvernpanalytical.com www.micromeritics.com
Langley Holdings’ main board members Bernard Langley and William Langley (left & right) together with Guido Degen (centre), CEO of GKN Hydrogen (Courtesy Langley Holdings)
ADDING VALUE TO ADDITIVE MANUFACTURING
Bodycote provides a complete service solution for metal parts built by the additive manufacturing process, including stress relief to minimise distortion and residual stress, EDM to prepare the component for hot isostatic pressing (HIP), heat treatment or HIP to remove microporosity, and associated quality assurance testing.
Reduction in rejection rates and inspection costs
Fatigue properties on par with wrought material
Significant improvement in fatigue strength, fracture toughness, and tensile ductility
100% reduction in porosity possible
Improved machined surfaces and consistency in properties
Improved microstructure
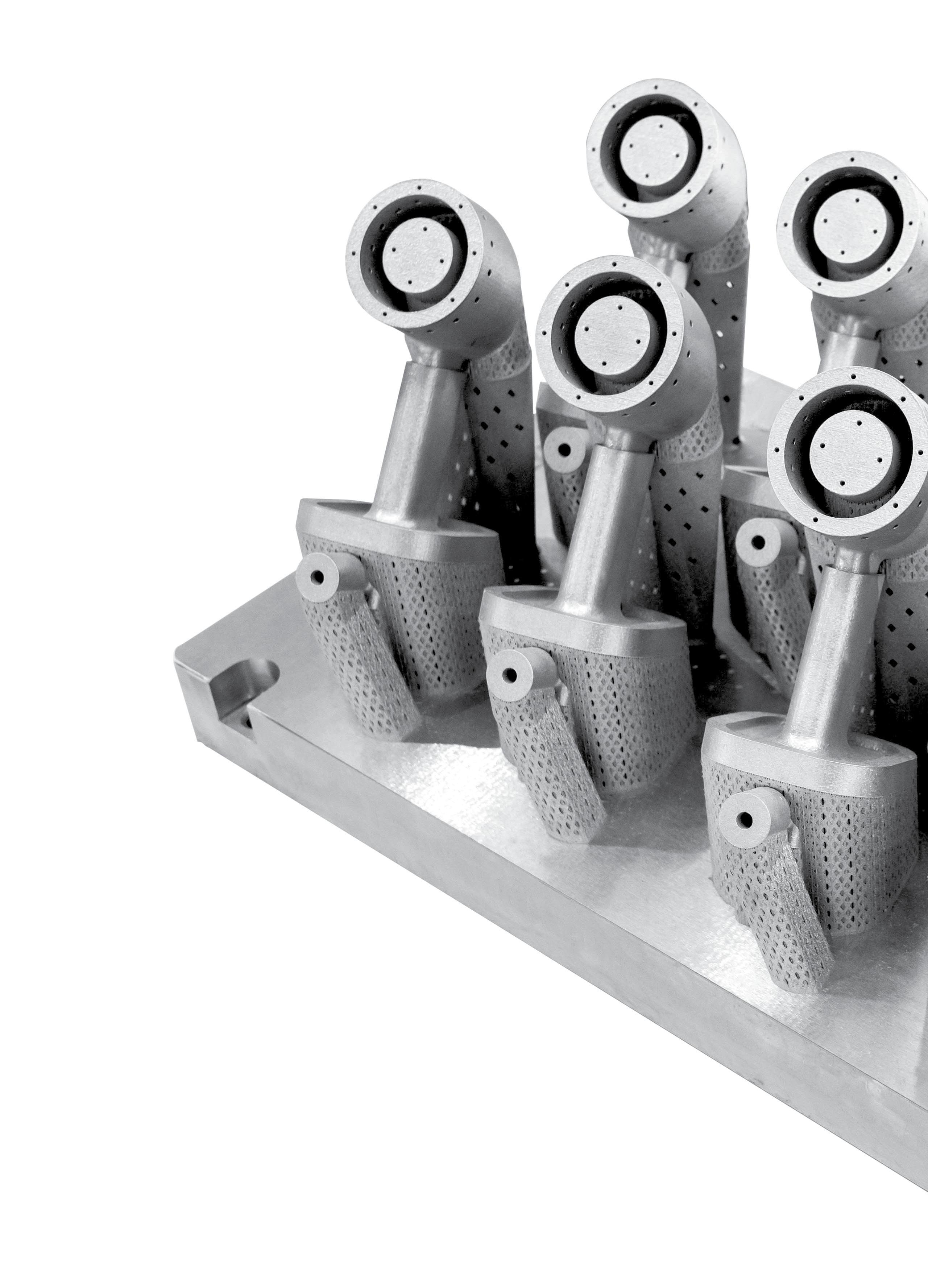
the partner of choice for additive manufacturing
heat treatment | metal joining | hot isostatic pressing | surface technology
Kymera acquires Fiven to expand specialty materials portfolio
Kymera International, a speciality materials company headquartered in Raleigh, North Carolina, USA, has signed an agreement to acquire Fiven ASA from OpenGate Capital. The deal is expected to close following customary regulatory approvals.
With production facilities in Norway, Belgium and Brazil, as well as a global distribution network, Fiven works in the development of technically advanced silicon carbide materials for a wide range of highgrowth end markets. Through its recent R&D initiatives, Fiven has developed and marketed high-purity materials for the power electronics industries such as semiconductors and lithium-ion batteries.
“Fiven has all of the strong attributes we look for in an acquisition. They have an excellent reputation
for quality and service, are aligned with Kymera’s strategy of focusing on attractive end markets such as electronics, aerospace and defence, and have an outstanding management team and dedicated workforce,” Barton White, CEO of Kymera, commented. “We are excited to partner with Falk and his team to continue growing Fiven and capitalise on the numerous operational and commercial synergies we have already identified.”
Kymera has been owned by affiliates of Palladium Equity Partners, LLC, a middle-market private equity firm with over $3 billion in assets under management, since 2018.
“The acquisition of Fiven will accelerate Kymera’s mission to become a high-growth specialty materials and chemicals platform, and unlocks substantial organic
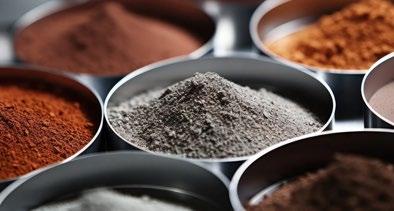
The acquisition of Fiven is expected to accelerate Kymera’s mission to become a high-growth specialty materials and chemicals platform (Courtesy Kymera)
growth opportunities for the combined business,” added Adam Shebitz, Partner at Palladium Equity Partners. “Altogether, Kymera is well on its way towards achieving Palladium’s investment objectives, having more than tripled in size from our initial investment, while creating a more resilient business oriented towards the industries of tomorrow.”
The terms of the transaction were not disclosed.
www.kymerainternational.com www.fiven.com
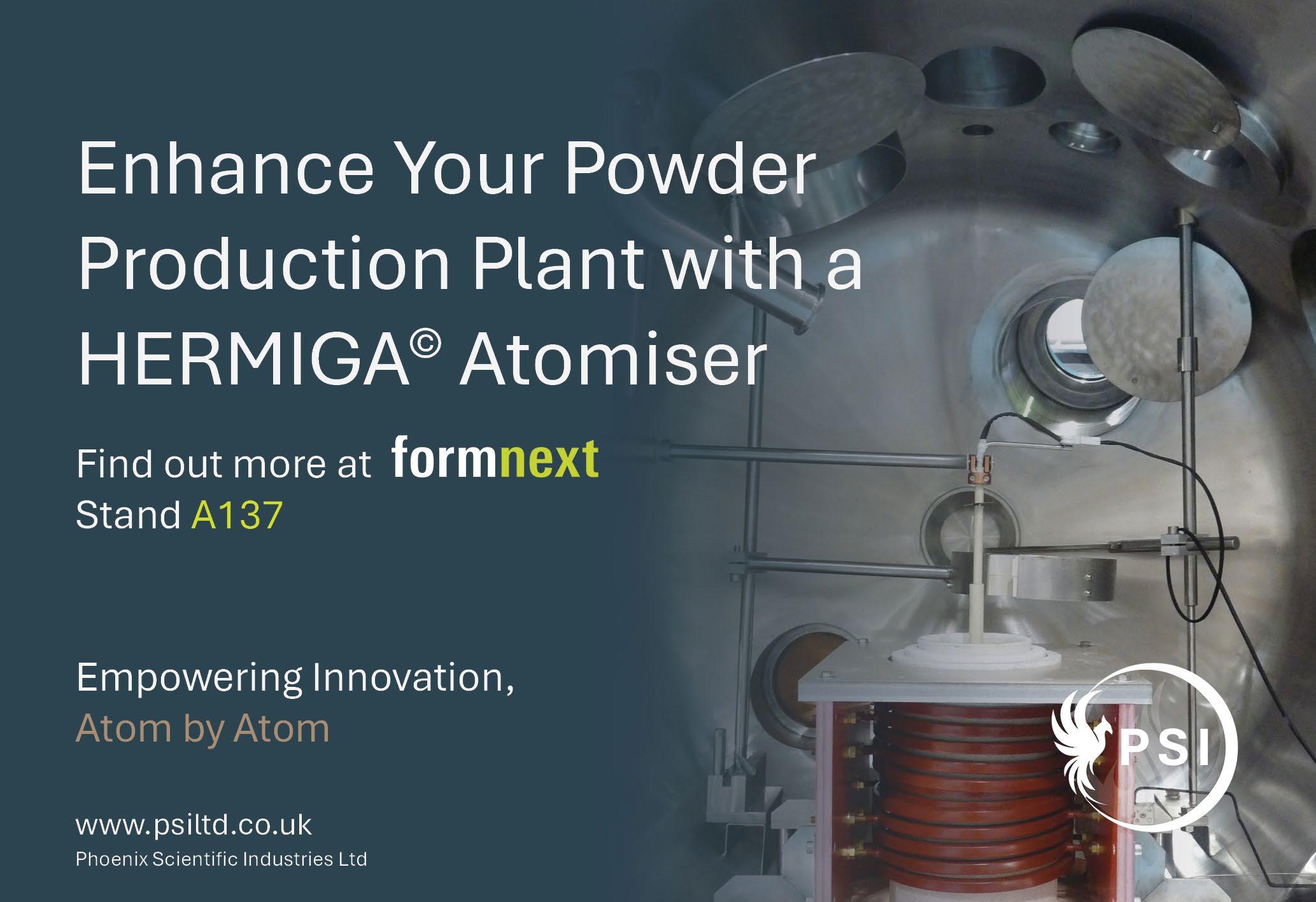
voestalpine reports solid results despite extremely difficult environment
The voestalpine Group has reported a solid result in the first quarter of the 2024/25 business year. The group’s stability was said to be attributed to its global positioning and sector diversification, despite a poor European economic environment.
“In an extremely difficult environment, especially for European steel companies, we were able to perform very well both in steel production and in the area of downstream processing. Our high-quality steel products are highly sought after in the most technologically demanding segments, such as the rail and aerospace industries. Our strategic goal remains continued growth in high-yield markets,” stated Herbert Eibensteiner, CEO of voestalpine AG.
The rail infrastructure and aerospace sectors performed particularly strongly in the first quarter. The energy sector recorded positive demand, especially in the renewable energy segment. By contrast, the construction and mechanical engineering industries remained at a persistently low level. The ongoing weak development, particularly in the German automotive industry, led to low demand for tool steel and in the Automotive Components business segment. In contrast, demand from the automotive industry for products from voestalpine’s Steel Division was satisfactory. Demand for voestalpine’s high bay warehousing systems made from the most robust steel profiles remains strong.
At €4.1 billion, revenue in the first quarter of the business year 2024/25 was slightly below the same period in the first quarter of the business year 2023/24 (€4.4 billion).
The EBITDA operating result decreased by 16.5% year-onyear to €417 million (Q1 2023/24: €499 million). The EBITDA is influenced by negative one-off effects of €28 million from the ongoing sales process for Buderus Edelstahl.
Profit from operations (EBIT) fell by 26.7% year-onyear to €228 million (Q1 2023/24: €311 million). Earnings before taxes amounted to €189 million (Q1 2023/24: €273 million). Profit after tax fell to €150 million (Q1 2023/24: €213 million). Cash flow from operating activities increased significantly from €10 million in the previous year to €215 million.
Equity increased by 0.8% compared to the reporting date (March 31, 2024) and amounted to €7.6 billion as of June 30, 2024. Net financial debt increased by 6.3% compared to the reporting date to reach €1.8 billion as of June 30, 2024. At 23.2%, the gearing ratio (net financial debt in relation to equity) increased slightly compared to the balance sheet date (22.0%).
As of June 30, 2024, the number of employees in the voestalpine Group worldwide amounted to 51,400 (full-time equivalent), which is 0.4% more than in the previous year (51,200).
www.voestalpine.com
PM Tooling System
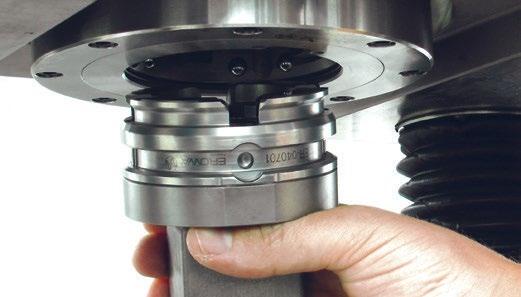
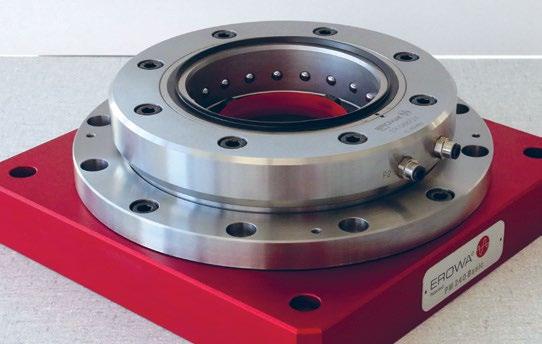
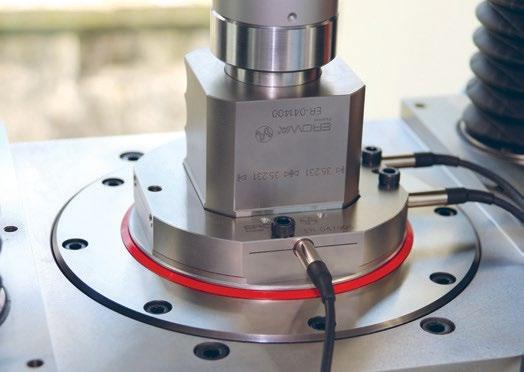


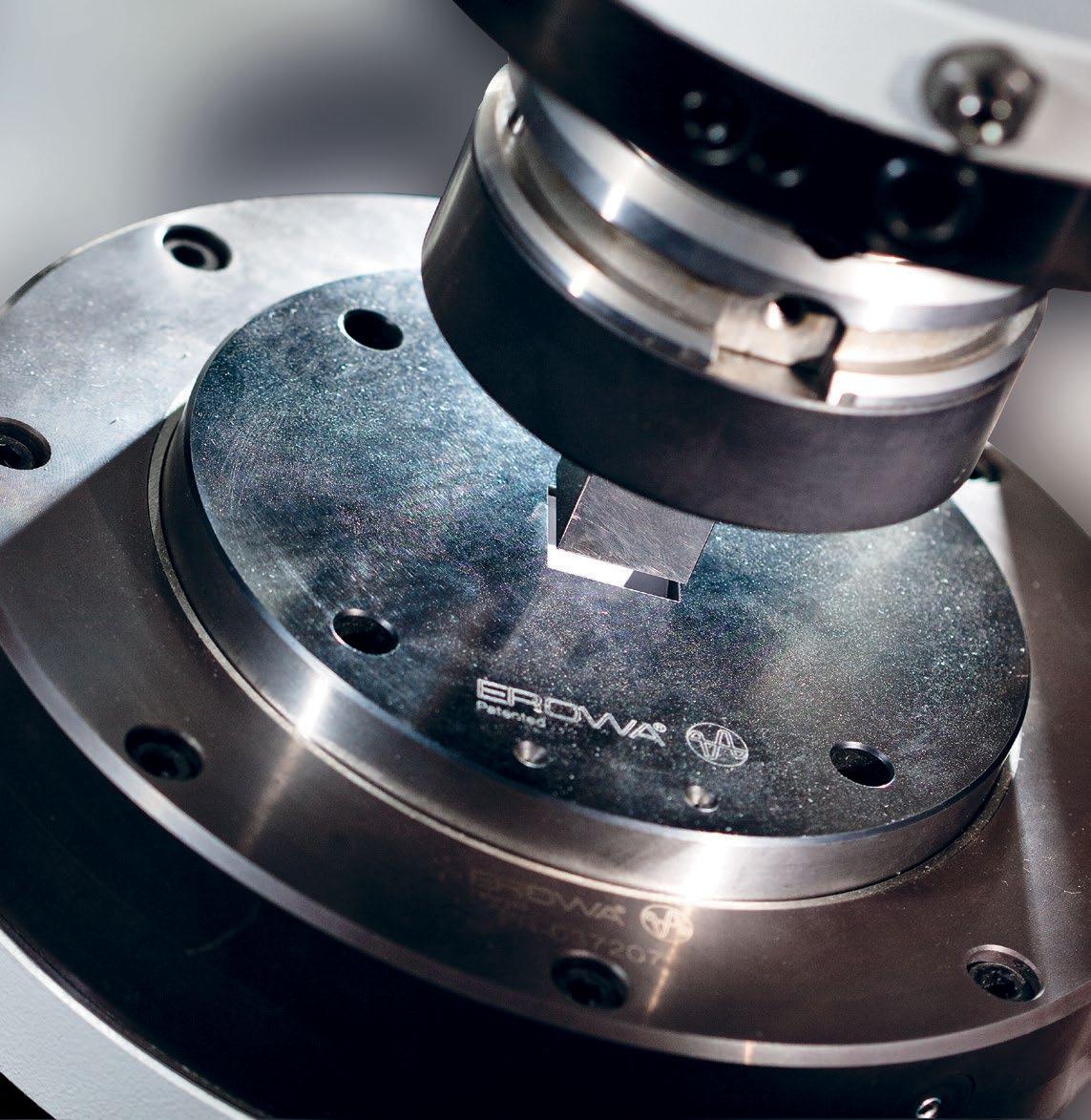

Amaero commissions its new atomiser ahead of schedule
Amaero International Ltd, based in McDonald, Tennessee, USA, has announced the installation and testing of its new metal powder atomiser supplied by ALD Vacuum Technology GmbH, Hanau, Germany. The atomiser has achieved all technical specifications stipulated in the contract, and acceptance has been formally acknowledged by both parties.
“Amaero’s leadership team is relentlessly focused on execution,” stated Hank Holland, chairman and CEO. “With final acceptance and commissioning of the atomiser, we have achieved a significant milestone and we have achieved the milestone ahead of schedule.”
With this installation completed, Amaero’s technical and manufacturing team will begin work on proprietary modifications of the atomisation process and parameter optimisation.
“Given the importance of advancing priority hypersonic and strategic missile programmes from development and demonstration phases to serial production as quickly as possible and the pressure to achieve material properties and performance criteria, Additive Manufacturing plays an important role,” Holland continued. “The insertion of Additive Manufacturing in hightemperature applications is enabled by improved resiliency, scalability and responsiveness of US domestic production of C103 and speciality alloy powders. Amaero is committed to collaborating with the US government, the Department of Defense, prime defence contractors and suppliers, to address priority initiatives to re-shore strategic industrial base capabilities.”
www.ald-vt.com
www.amaeroinc.com
AP&C offering coarse Ti-6Al-4V powder for Additive Manufacturing
AP&C, a Colibrium Additive company, based in Québec, Canada, is now offering a coarse titanium Ti-6Al-4V (Ti64) powder suitable for Laser Beam Powder Bed Fusion (PBF-LB) Additive Manufacturing machines. The new coarse grade is reported to offer the same quality as AP&C’s finer powders, but with larger-size particles.
Ti64 is a key material for Additive Manufacturing, explains AP&C, especially in the orthopaedic industry, alongside cobalt chrome. There are also many Ti64 applications in the aerospace sector as well as in consumer goods products, so it is relatively easy to find new, niche applications for it. Ti64 has already been widely adopted by the additive community compared to other alloys, which has led to optimised parameters for this material, making it easier to find business use cases.
What is coarse Ti64?
When metal AM was first developed, the data was lacking to identify the ideal powder, continues AP&C. Therefore, the industry started with powder from more conventional technologies, such as Metal Injection Moulding. The emergent

AP&C is now offering a coarse titanium Ti-6Al-4V powder suitable for Laser Beam Powder Bed Fusion Additive Manufacturing machines (Courtesy Colibrium Additive)
PBF-LB technologies selected the 15-45 µm and 15-53 µm particle size distribution (PSD) grades.
PBF-LB technology is now the largest market for spherical Ti64 powders, reports AP&C, but by using only the finer fraction of the ‘as-produced’ PSD, coarser Ti64 powder becomes available and in need of a market. However, there is no technical reason why coarser Ti64 powder could not be used in the PBF-LB process with slight tuning on deposition parameters. Of course, larger Ti64 particles also exhibit the same quality as the finer powders, as they have been created using the same validated process. In fact, similar coarse powders are used in Electron Beam Powder Bed Fusion (PBF-EB) and Direct Energy Deposition (DED) with great results.
Academic research, and AP&C’s own internal data, have shown that using larger particles with a tuned deposition process produces highquality AM parts with comparable mechanical properties and excellent process stability. After extensive work and validations, AP&C is now commercialising a parameter for the Colibrium Additive M2 platform for coarse Ti64.
Coarse Ti64 powder is safer
Another important advantage highlighted by AP&C is that coarse Ti64 is also safer than finer powder, since the higher PSD is substantially less reactive. Powder handling, storage and reuse can be significantly simplified and local regulations for powder storage are easier to meet. For example, coarse Ti64 powder is not classified as flammable (while fine Ti64 is) and, more importantly, its minimum ignition energy is high enough that the powder is not sensitive to electrostatic discharge which can change the applicable safety controls associated with using this powder.
www.advancedpowders.com www.colibriumadditive.com
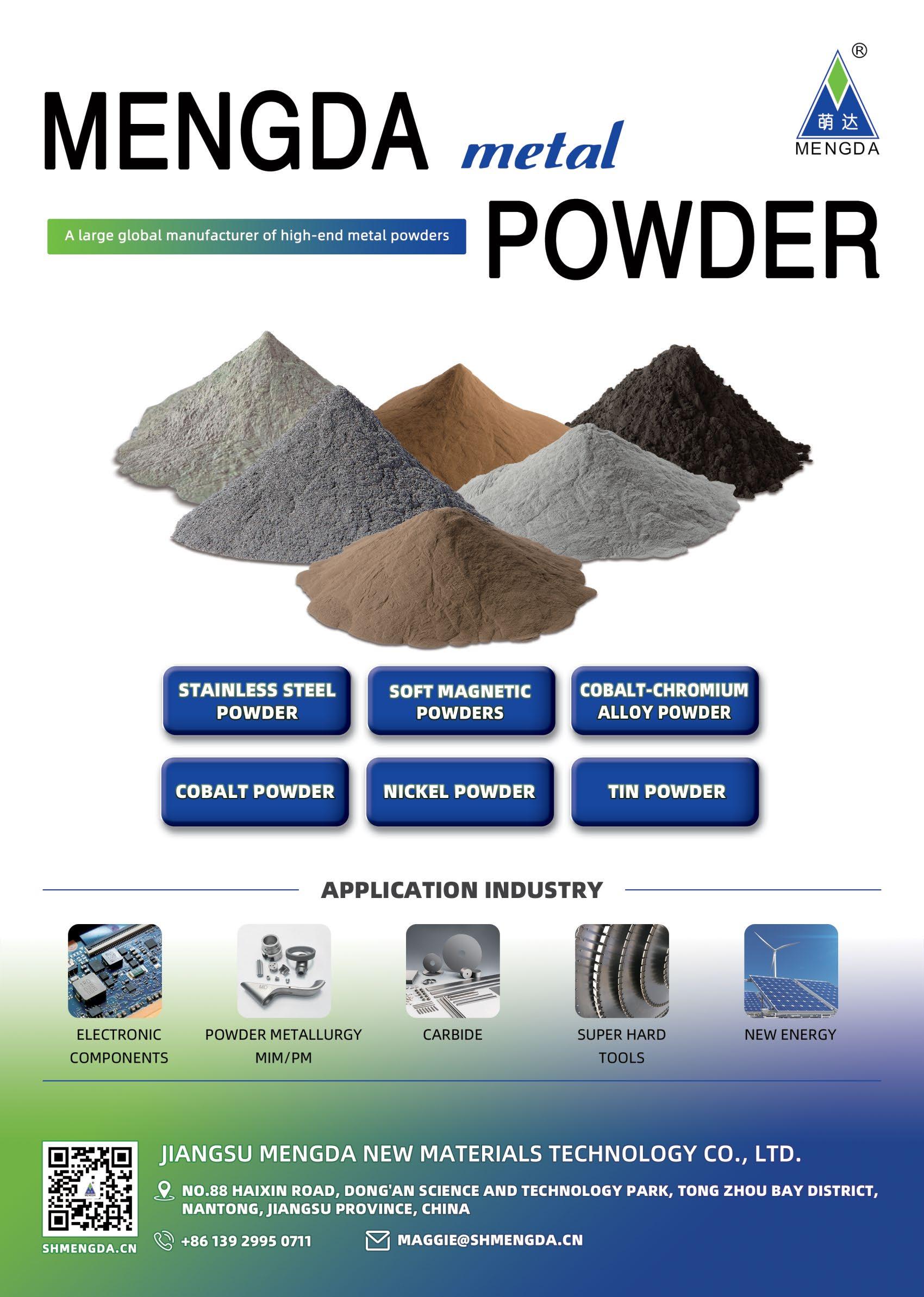
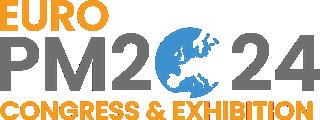
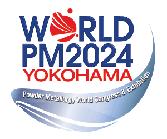
BOOTH #66
BOOTH #1-05
Miba begins construction of €12 million training centre for skilled workers and apprentices
Miba AG, headquartered in Laakirchen, Austria, is building a new €12 million training and further education centre for employees and apprentices at the Miba Campus in Laakirchen. Miba CEO F Peter Mitterbauer, numerous guests of
honour and local politicians attended the groundbreaking ceremony.
The new 2,400 m 2 two-storey building will offer a wide range of usage options. It will include workshops for mechanical engineering training, CNC, CAM/CAD, and welding
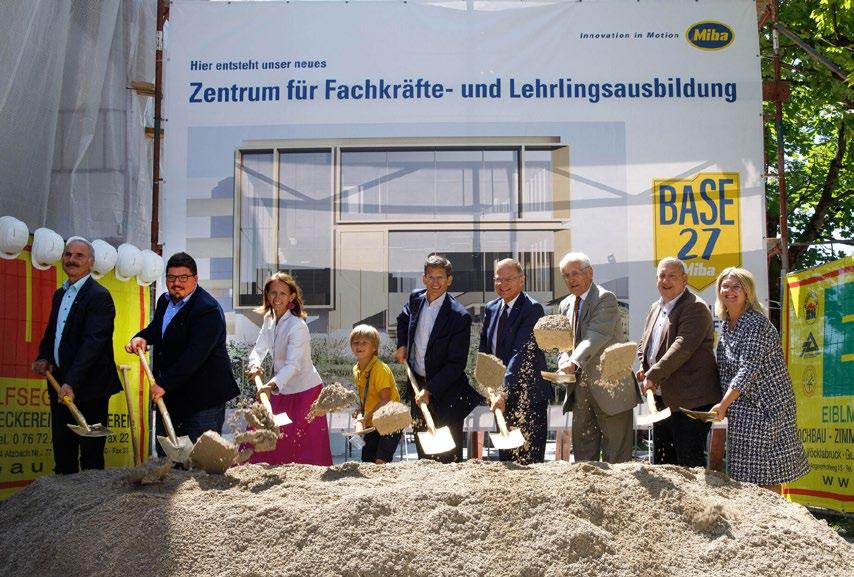
Höganäs introduces powder-specific carbon footprint reports
Sweden’s Höganäs AB has announced that it is now able to provide product-specific carbon footprint (PCF) reports for all products with complete lifecycle assessment (LCA) models in place. The move is intended to support customers in their emissionreduction goals, and contribute to Höganäs’ long-term target of reaching net-zero emissions by 2037.
“Many of our customers already face demands from their own customers to reduce carbon dioxide emissions from the value chain (scope 3),” stated Fredrik Vinnerborg, Product Portfolio Manager. “This will become increasingly
important as many car manufacturers have set net-zero targets. Thanks to the data we provide in our PCFs, our customers gain a powerful tool to reduce their scope 3 emissions.”
Höganäs is the first metal powder producer to provide full transparency on its cradle-to-gate productspecific emissions to the market.
The PCF calculations follow the ISO 14067:2018 standard and communicate how many kg of CO 2 equivalents are emitted for every kg of metal powder produced.
Sofia Poulikidou, LCA Specialist, added, “To ensure transparency and enhance communication with customers we have created Product Carbon Footprint summary reports,
applications, as well as an automation and mechatronics laboratory.
“In order to offer our employees a training environment that corresponds to everyday work in our production facilities, we are investing in state-of-the-art machinery,” stated Mitterbauer.
The new facility, named Base 27, is seen as the next step in the company’s decades-long success in training skilled workers and apprentices.
“We have achieved a lot. Around 1,500 people have already completed a Miba apprenticeship, 25 have joined this year alone and 28 apprentices will begin their training in the autumn,” continued Mitterbauer. “With the ‘second-chance apprenticeship’ we have set up a very successful qualification programme to become skilled metal workers, which 45 people have already completed. And we offer an extensive training programme for specialists, from support when starting work at Miba to training for team or shift leaders. With ‘Base 27’ we want to take our skilled worker and apprentice training to the next level.”
Miba plans to complete the building in spring 2026.
www.miba.com
for all base powders which have LCA models in place.”
The PCFs cover all greenhouse gas emissions throughout the entire production chain, from a cradleto-gate perspective. This includes all activities, from raw material acquisition and inbound transport to energy and fuel production, as well as processing activities at Höganäs’ sites. Downstream activities, such as product distribution to customers, components manufacturing, use, and end-of-life, are excluded.
Vinnerborg continued, “We encourage our customers to reach out to their usual contact person at Höganäs to learn more about how we can support them in their sustainability journey and help reduce their scope 3 emissions with the assistance of PCFs.”
www.hoganas.com
The ground-breaking ceremony was attended by Miba CEO F Peter Mitterbauer along with guests of honour and local politicians (Courtesy Miba AG)

Global aerospace OEM to place PyroGenesis and its NexGen titanium powder on approved supplier list
PyroGenesis Canada Inc, based in Montreal, Quebec, has announced its NexGen™ Ti64 ‘coarse’ powder has been approved by a global aerospace OEM for inclusion in its approved supplier list. The client, who remains confidential for competitive reasons, will now begin the formal process of adding PyroGenesis to its internal approved supplier list for this specific powder, a process that is expected to be completed this summer.
This coarse powder has a size fraction in the range of 45-150µm and is typically used in Additive Manufacturing applications such as Electron Beam Powder Bed Fusion (PBF-LB) and Direct Energy Deposition (DED).
The qualification process – which involved extensive evaluations including quality management system review, work instructions review, and a rigorous on-site audit of Pyrogenesis’ production facility – was successfully completed over the course of several years. The final step required the company to submit samples of its powders for chemical and mechanical properties evaluation to confirm matching client specifications.
“Having our ‘coarse’ Ti64 powder accepted for addition to the approved supplier list of one of the largest aerospace companies in the world underscores the quality and reliability of our NexGen plasma atomisation process, our post-processing process, our quality assurance management process, and our quality control system,” said Massimo Dattilo, Vice President, PyroGenesis Additive. “This achievement is a testament to the hard work and dedication of our team over the past several years. We look forward to officially being added to the approved supplier list and leveraging this success.”
“This is a colossal achievement for PyroGenesis, particularly for the PyroGenesis Additive division,” said P Peter Pascali, PyroGenesis President and CEO. “While we have been confident from the outset, this notification from a global aerospace OEM is confirmation that our board’s decision to re-enter the metal powder market, with a ground-up redesign in the form of the patented NexGen plasma atomisation production system, was indeed the right one. This news is even more exciting when taken in the context of the recent announcement of a joint $415 million government/corporate aerospace initiative, to establish an aerospace innovation zone in Montreal, right in our backyard. Today’s announcement positions PyroGenesis well to also be included in one of the world’s foremost aerospace technology developments.”
www.pyrogenesis.com www.pyrogenesisadditive.com
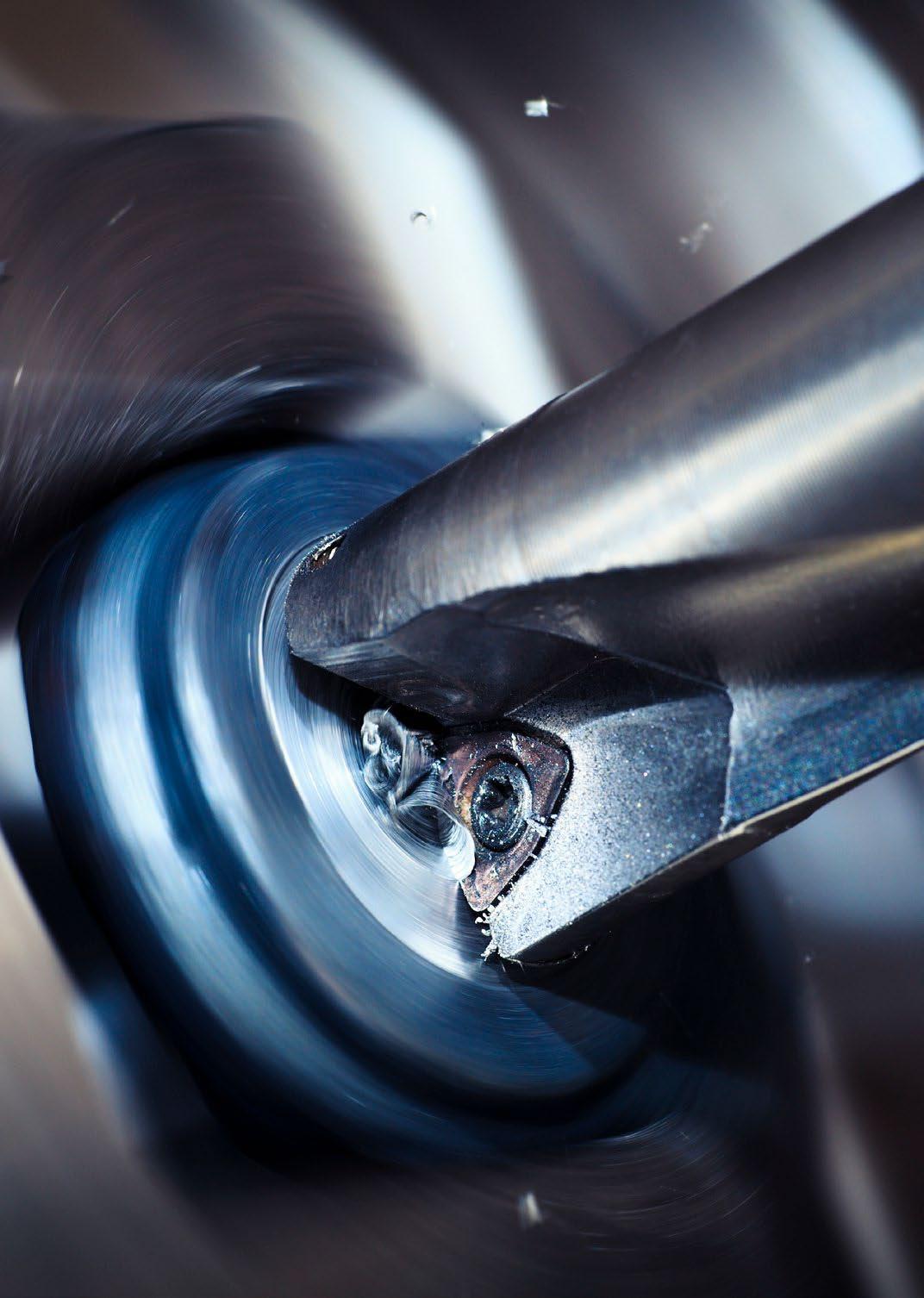
Powder engineering expertise.
GEA is a worl-leading specialist in powder engineering with exceptional patented Spray Drying Solutions. Be it a powder, a granulate or an aglomerated product, our solutions define and deliver superior quality powders to your exact specifications in the most energy-and-costefficient way.
Neo’s new European sintered rare earth magnet subsidiary wins major EV supply contract
Neo Performance Materials, Toronto, Canada, has announced that its wholly-owned Estonian subsidiary, NPM Narva OÜ (Magnequench Sintered Magnets), has been awarded a contract to supply sintered rare earth magnets to a European Tier 1 supplier of EV traction motors. The sintered magnets will be supplied by the company’s new European rare earth magnet manufacturing facility, currently under construction in Narva, Estonia.
The new facility, scheduled for completion in 2025, is expected to be the first sintered magnet plant to come online outside of Asia. It will produce 2,000 tonnes per year of magnets in Phase 1, enough to supply approximately 1 to 1.5 million electric and hybrid vehicle traction motors. Phase 2 of the project is expected to see around 5,000 tonnes/year, enough for 4.5 million electric cars.
The volumes represented by the new supply order will be approximately 35% of Phase 1 magnet capacity, with production revenues projected for the second half of
2026 through 2033, and peak supply to the customer expected in 2029.
“We welcome this significant commercial validation from a Tier 1 EV motor manufacturer. Neo is focused on becoming the first manufacturer and supplier of made-in-EU rare earth magnets for EV traction motors. This is one more endorsement that the need for parallel, local-for-local supply chains is defining the future of the EV manufacturing transition in Europe and North America – an inflection point that is at the core of Neo’s strategy,” stated Rahim Suleman, Neo’s President and Chief Executive Officer.
The new magnet facility is located close to Neo’s existing operating rare earth separation facility and began construction in 2023. It was awarded the first Just Transition Fund grant in the European Union and gained the recognition and support of the President of the EU Commission, Ursula von der Leyen, amongst other European government and industry leaders.
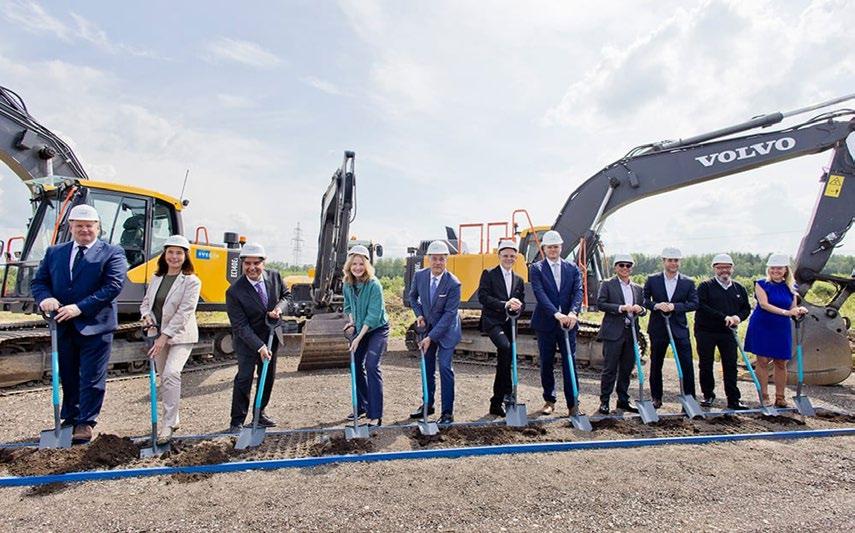
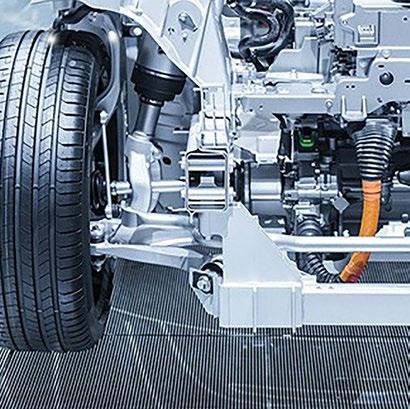
Neo’s Magnequench division has supplied the automotive industry for more than two decades with rare earth magnetic materials – more than half of its sales attributed to the automotive industry (Courtesy Neo Performance Materials)
Data from Adamas Intelligence, the US Geological Survey, and customer discussions estimate that approximately 90% of sintered magnet production is concentrated in China today. The EU Critical Raw Materials Act has set targets such as 40% of rare earths material consumed annually to have been processed in the EU, 25% of rare earths magnetic materials to be sourced from recycling in the EU, and no more than 65% of rare earth magnets to be sourced from a single jurisdiction outside the EU. Similarly, the US recently announced a new 25% tariff on rare earth magnets from China in effect from 2026 onward.
Historically, Neo’s Magnequench division has supplied the automotive industry for more than two decades with rare earth magnetic materials – more than half of its sales attributed to the automotive industry. Since its founding more than three decades ago, Neo’s Magnequench has developed, manufactured, and supplied rare earth magnetic products to customers with high qualification standards in vehicle traction motor, water circulation, residential appliances, and industrial automation applications globally. www.neomaterials.com
The rare earth sintered magnet manufacturing facility is located close to Neo’s existing rare earth separation facility and began construction in 2023 (Courtesy Neo Performance Materials)

NASA selects Elementum 3D as co-exclusive licensee for GRX-810 high-temperature Additive Manufacturing alloy
Elementum 3D, based in Thornton, Colorado, USA, has announced that NASA has selected the company as one of four to produce and distribute GRX-810 alloy under a commercial co-exclusive licence. The high-temperature metal superalloy will be offered to original equipment manufacturers of airplanes and rockets, as well as the entire supply chain.
NASA’s goal of the licensing agreement is to quickly accelerate the adoption of GRX-810 to benefit US technologies, industry, and space exploration. The material is capable of creating lighter and thinner engine parts, reducing fuel burn, lowering operating costs, increasing durability, and lowering
the tolerance for failure for critical applications.
GRX-810 is an oxide dispersion strengthened (ODS) alloy that can endure higher temperatures and stress. Its strength is derived from the dispersion of tiny particles containing oxygen atoms.
The breakthrough superalloy was specifically developed for the extreme temperatures and harsh conditions of aerospace applications, including liquid rocket engine injectors, combustors, turbines, and hot-section components, capable of enduring temperatures up to 1,100 °C.
Compared to other alloys, GRX-810 can endure higher temperatures and stress up to
2,500x longer. It’s also 3.5x better at flexing before breaking and twice as resistant to oxidation damage.
Over the past nine years, Elementum 3D has gained extensive knowledge and experience in developing, commercialising, and distributing “impossible-to-print” dispersion-strengthened materials similar to GRX-810.
“We are excited to be working with Tim Smith and NASA to bring this exceptional new alloy to the commercial market,” stated Jeremy Iten, Elementum 3D Chief Technology Officer.
NASA’s investment in developing GRX-810 is said to demonstrate its dedication to advancing Additive Manufacturing. It was added that Elementum 3D, and the other co-exclusive licensees, now assume the responsibility of investing the time and resources to supply the industry with a stronger, more durable superalloy.
www.elementum3d.com
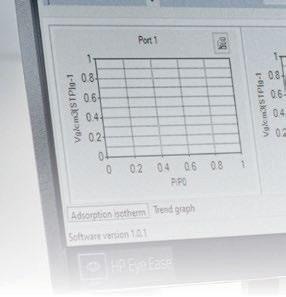

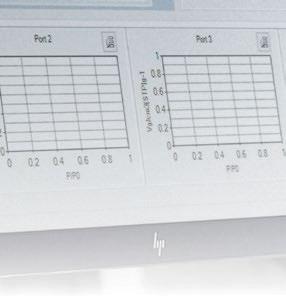

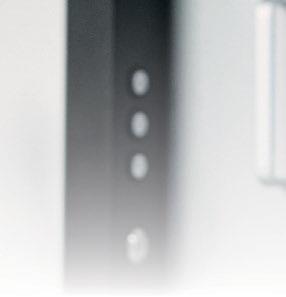
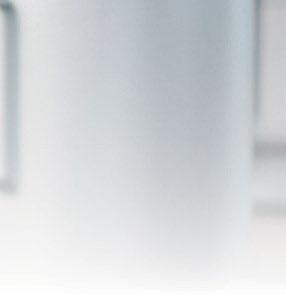
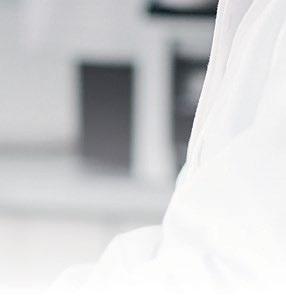

PARTICLE CHARACTERIZATION OF METAL POWDERS
Determine BET surface areas of metal powders quickly, accurately, and economically with MICROTRAC’s BELSORP MAX X Sorption Analyzer:
I The specific surface area (m²/g) is an important parameter in the evaluation of metal powders regarding their processability.
I Simultaneous measurement of up to 4 samples with high precision.
I Rapid determination of BET surface areas with up to 12 analyses per hour - perfect for quality control of fine powders with high sample throughput.
www.microtrac.com
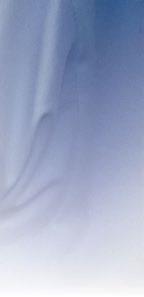
Nabertherm celebrates 25 years of its Chinese subsidiary
Nabertherm GmbH, headquartered in Lilienthal, Germany, recently celebrated the twenty-fifth anniversary of its Chinese subsidiary. Founded in 1999, the subsidiary’s opening was regarded as a milestone in the company’s international expansion and underscored the importance of the Chinese market.
Nabertherm China’s headquarters are in Shanghai, with further sales specialists in Shenzhen, Beijing and Wuhan. Since its founding, the subsidiary is reported to have developed a reputation for high-quality industrial and laboratory furnaces, supporting customers from areas
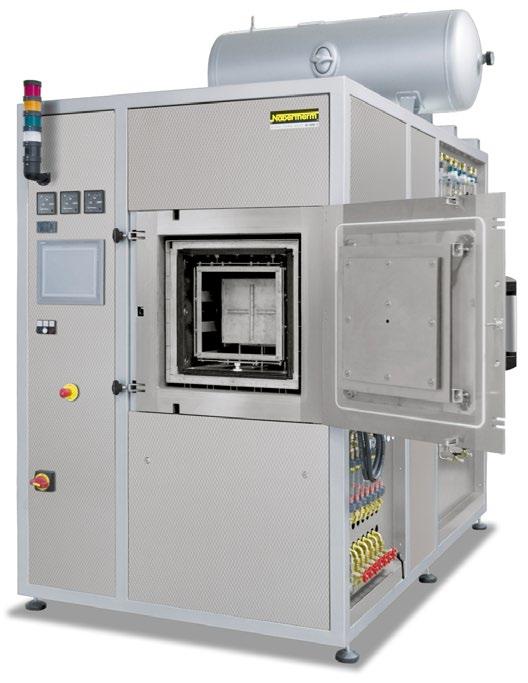
Nabertherm offers a range of furnaces, including this retort furnace for sintering MIM components (Courtesy Nabertherm GmbH)
Continuum Powders completes rebrand from MolyWorks, names Higby as CEO
Continuum Powders, based in Los Gatos, California, USA, has announced the completion of its official rebrand from MolyWorks and the appointment of Rob Higby as the company’s Chief Executive Officer. Higby succeeds previous CEO Phil Ward, who will now assume the role of President — Asia Pacific, where he will lead Continuum’s Asia Pacific operations. Since 2020, Ward has led the organisation through customer adoption, IP development, quality systems certification and the establishment of funding partnerships.
“I’m excited to be partnering with Rob as we accelerate our metal powder and service offerings to our customers,” stated Ward. “Rob’s experience and track record of delivering next-generation manufacturing and MRO services to customers is the perfect focus for Continuum as we scale our global business being served out of Texas, California and Singapore.”
Higby has experience in building service teams for the delivery of next-generation offerings to customers. Most recently, he served
of high technology, production, research, dental and the arts in solving relevant daily tasks in the field of thermal process technology.
Nabertherm has stated that a key factor in its Chinese subsidiary’s success is its well-developed service network. “Regional presence to our customers is particularly important to us in China,” stated Timm Grotheer, Managing Director of Nabertherm GmbH, Germany. “Our goal is to best understand their needs and offer innovative solutions that meet the needs of the Chinese market.”
Nabertherm intends to continue working closely with its Chinese subsidiary in the coming years. The company added that it will continue to develop thermal process solutions for Chinese customers, offer first-class products and address questions in the usage phase through service activities that meet its customers’ high standards.
Grotheer concluded, “We are pleased with the appreciation we have earned in the Chinese market and will do everything to continue to meet our customers’ expectations with high standards.”
www.nabertherm.com
as an Executive Partner with AEA Investors, where he led the firm’s Aerospace and Defense investment practice. He led several investments for the firm and advised other companies, including Velo3D Inc, where he also served as Advisor to the Board of Directors and interim Chief Commercial Officer.
Under the rebrand, MolyWorks Materials Corporation has changed its corporate naming to Continuum Powders Corporation to become a single, unified brand that more accurately represents the future and differentiators of the company. All company assets, patents, employees and locations are now officially Continuum Powders. www.continuumpowders.com
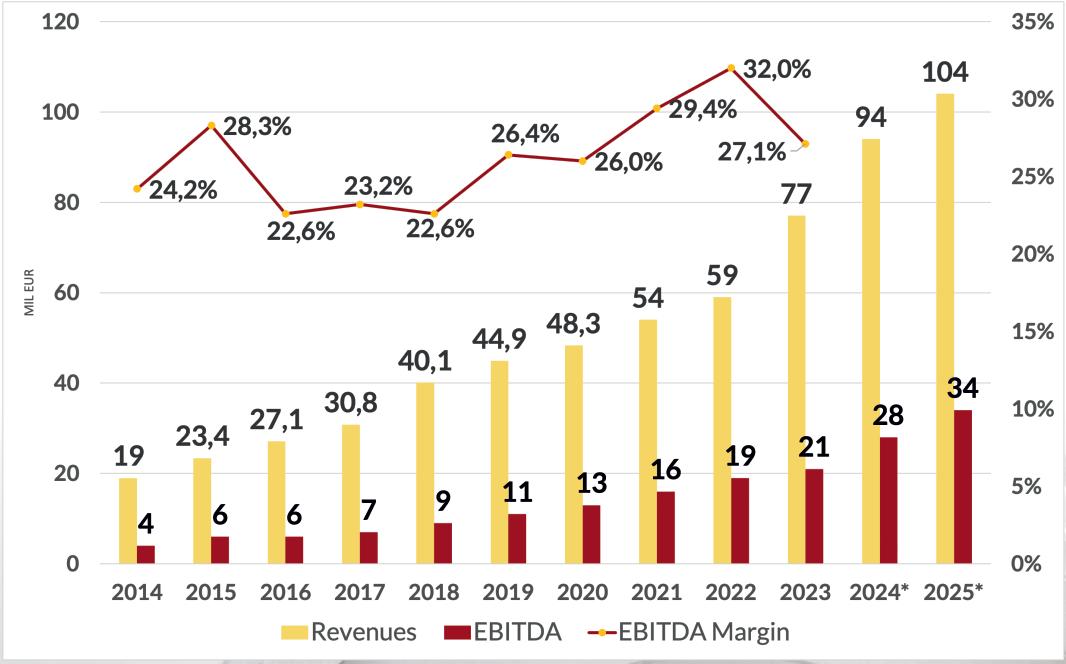


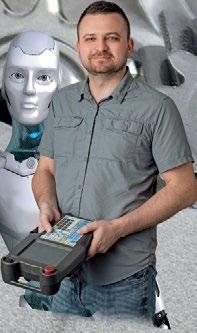

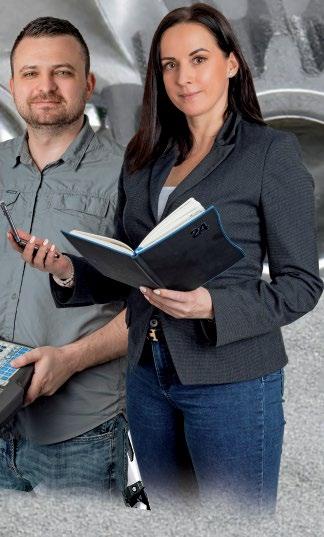
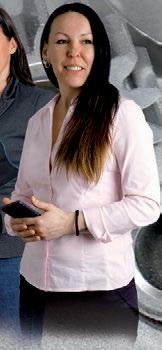
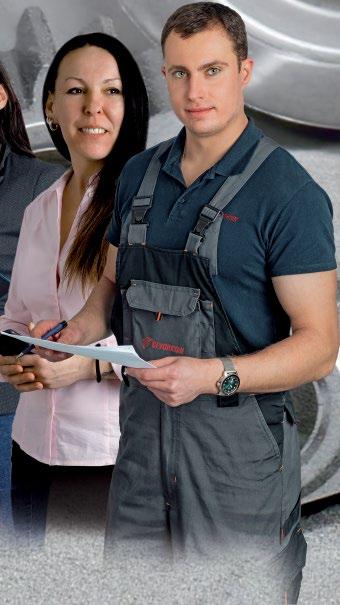
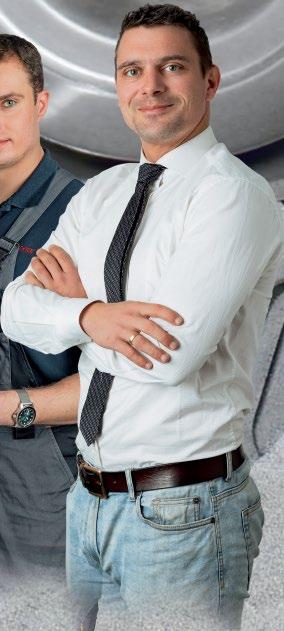
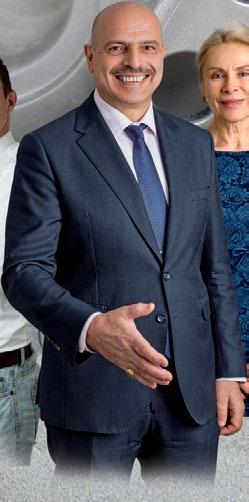
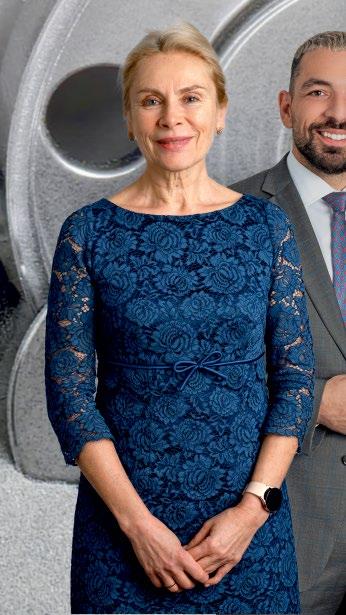
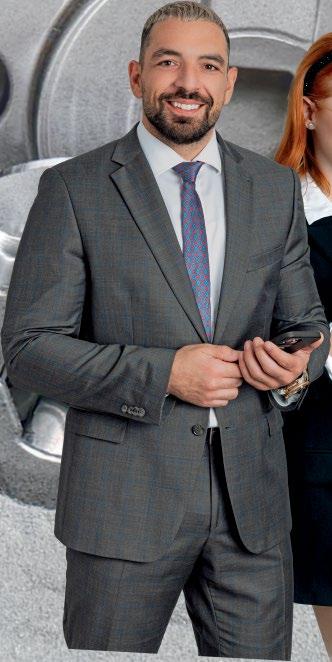
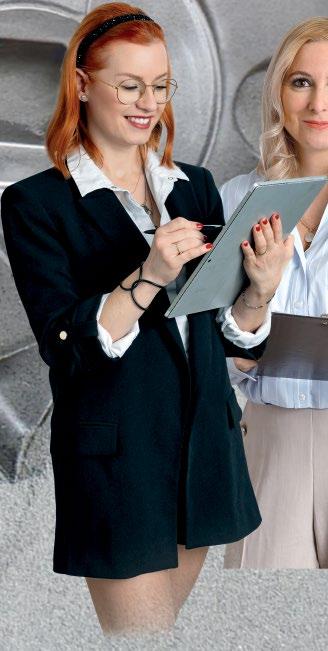

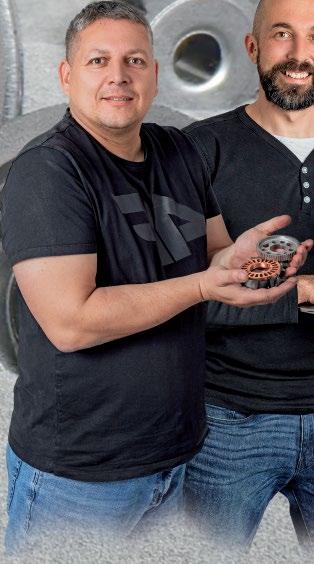

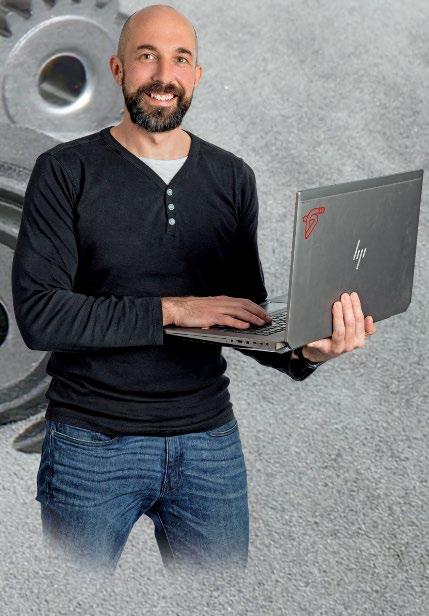
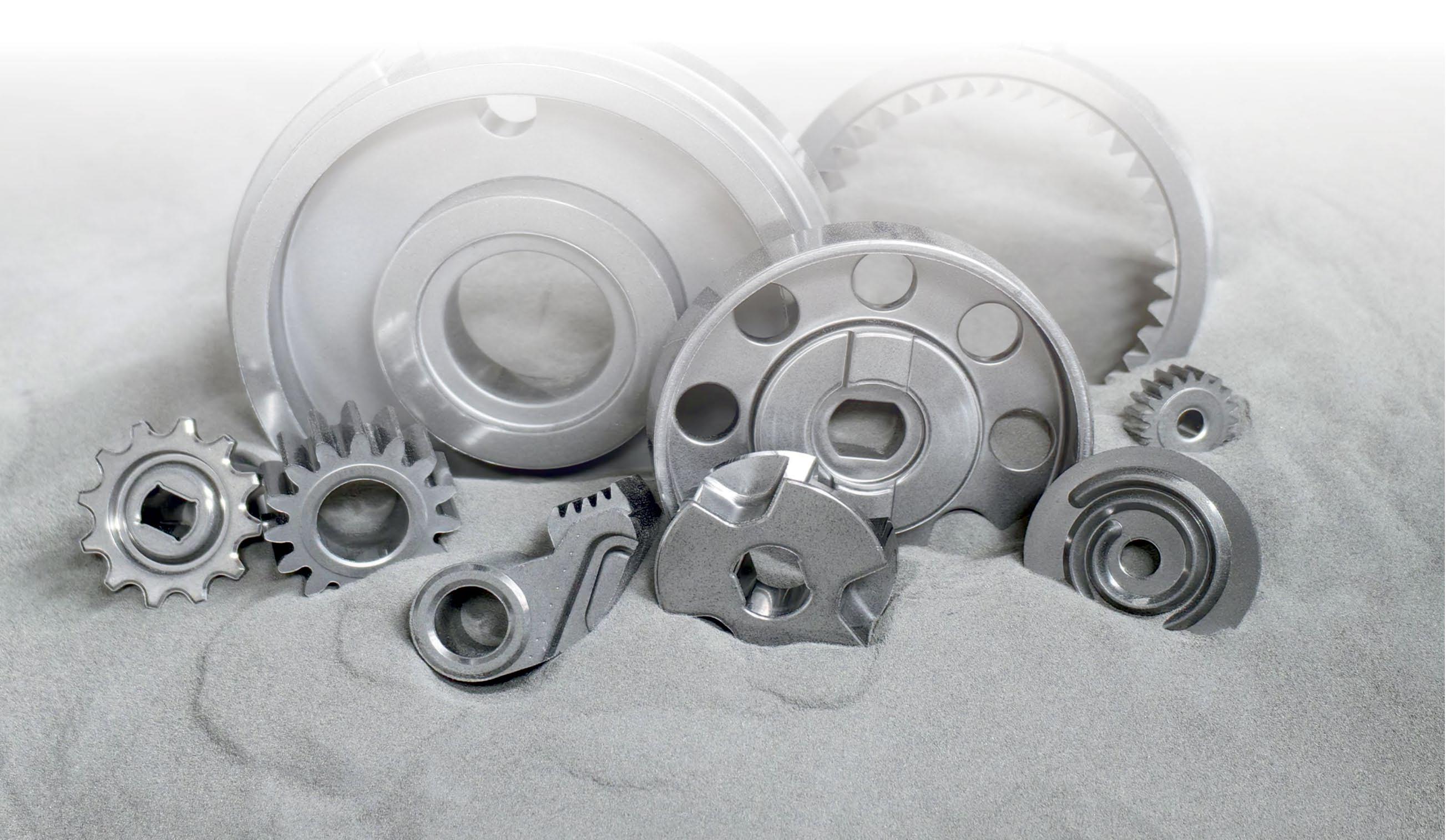
Metal powder cross-contamination analysis
Researchers at Politecnico di Torino, Turin, Italy, have published a paper in Materials & Design entitled ‘Ultraviolet–Visible-Near InfraRed spectroscopy for assessing metal powder cross-contamination: A multivariate approach for a quantitative analysis.’ The paper assesses three binary systems obtained from
the cross-contamination of three components, A92618, C10200 and S31603, in a low contamination range, from 0.5 vol% to vol. 6%, and in a high contamination range of 25 vol% and vol. 50%.
The past few years have seen increasing use of spherical metal powders to produce bulk parts
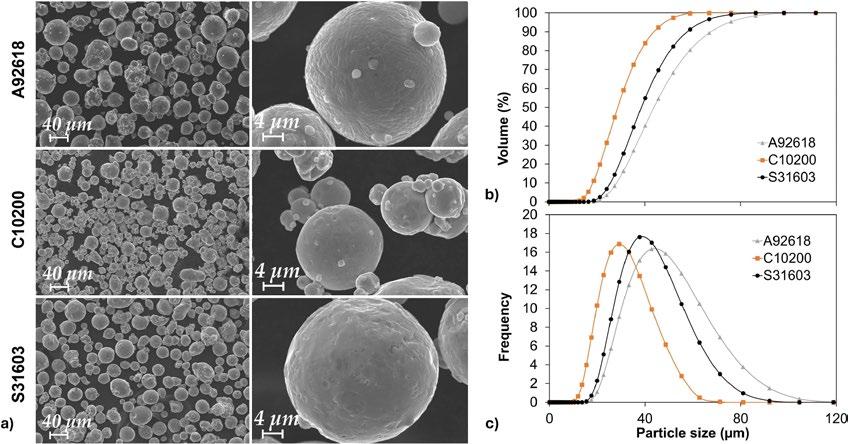
SEM image (a) of the surface morphology of the three different commercial powders atomised powders; b-c) size distribution of the three types of powders (As published in Ultraviolet–Visible-Near InfraRed spectroscopy for assessing metal powder cross-contamination: A multivariate approach for a quantitative analysis. Courtesy Materials & Design)
Wall Colmonoy acquires thermal spray powder supplier Indurate Alloys Ltd
Wall Colmonoy, headquartered in Madison Heights, Michigan, USA, has announced the acquisition of Indurate Alloys Ltd., a supplier of hardfacing products, located in Edmonton, Alberta, Canada. The acquisition is intended to strengthen Wall Colmonoy’s position in the Canadian market and provide customers with a wider range of products and expertise to meet their wear resistance and corrosion protection needs.
Indurate Alloys supplies metallic and carbide powders in HVOF, plasma spray, thermal spray, laser and plasma trans -
ferred arc (PTA) forms, as well as wires and electrodes. Indurate also provides Additive Manufacturing powders and collaborates with companies that use the latest AM technologies, including Powder Bed Fusion and Direct Energy Deposition.
Wall Colmonoy stated that it recognises the value of Indurate’s established and growing customer base, high-quality thermal spray products, and excellent vendor relationships, which will add new products to complement Wall Colmonoy’s portfolio.
“We are excited to welcome the talented Indurate Alloys team to Wall
through metal-forming technologies like Additive Manufacturing and Metal Injection Moulding, the authors state. This, paired with the wide availability of metal powders, leads to a critical issue: contamination across different systems in different process steps. As a result, it is necessary to find a new, faster, and more reliable analysis sensitive to traces of contamination.
This work by Politecnico di Torino’s researchers evaluates the applicability of UltravioletVisible-Near-InfraRed (UV-Vis-NIR) spectroscopy, a technique providing information on powders’ reflectance, for studying contaminated powders.
After the UV-Vis-NIR analysis, multivariate analysis has been used to obtain quantitative results. The results show that, as the contamination level increases in the binary system, the shape of spectra changes and becomes progressively more similar to the contaminant one. The chemometric analysis allows for the detection of the contaminant type and its concentration percentage in the contaminated powder.
www.sciencedirect.com
www.polito.it
Colmonoy,” stated Nicholas Clark, President, Wall Colmonoy. “This strategic acquisition extends our reach into the Canadian marketplace and allows us to better serve our customers across the country.”
“Wall Colmonoy stood out as the right partner for us, thanks to its extensive history in the hardfacing industry and its shared commitment to strong customer relationships,” said Lorne Chrystal, Founder & CEO of Indurate Alloys Ltd. “We are excited to merge the expertise and experience of both companies and eagerly anticipate expanding opportunities together.”
www.induratealloys.com www.wallcolmonoy.com

Kennametal names Bersaglini as VP and President of Metal Cutting Segment
Kennametal Inc, based in Pittsburgh, Pennsylvania, USA, has announced that David Bersaglini will join the company as Vice President of Kennametal Inc and President of the Metal Cutting segment, effective August 26, 2024. Bersaglini will serve on the company’s Executive Leadership Team and will report directly to company president and CEO Sanjay Chowbey.
Bersaglini has nearly twenty-five years of experience and joins the company from Copeland, a spin-off of Emerson, where he was vice president and general manager of the $1 billion Global Refrigeration segment. In this role, he was responsible for developing and implementing strategy to deliver long-term profitable growth for the Americas, Europe and Asia. He was also responsible for manufacturing, global product strategy,
engineering development, sales and marketing. Prior, he managed a $650 million P&L as Vice President and General Manager, Refrigeration.
“Dave brings a strong track record of success to Kennametal, with extensive experience leading businesses in the global industrial space and a proven ability to develop and implement strategic initiatives,” said Chowbey.
Bersaglini joined Emerson in 2001 and progressed through leadership roles in product management, marketing, sales, strategic planning and general management before transitioning to Copeland during the 2023 spin-off. Throughout his tenure with Emerson, Bersaglini focused on driving value creation through growth by developing market strategies and new products to deliver differentiated solutions
to end customers. As Vice President, Marketing and Development, he was responsible for the Asia Pacific market and he also held an enterprise-level leadership role as Vice President, Corporate Planning.
Chowbey added, “His valuable commercial expertise, growth mindset and results orientation make him the ideal choice to lead the Metal Cutting business. Dave will be instrumental in our journey to create shareholder value through growth, margin expansion and a balanced capital allocation strategy.”
Bersaglini earned a Bachelor of Science in mechanical engineering and a Master of Business Administration from Ohio State University.
As President of the Metal Cutting segment, Bersaglini will be accountable for all aspects of the global business, including advancing the strategy, driving operational excellence and delivering profitable growth.
www.kennametal.com
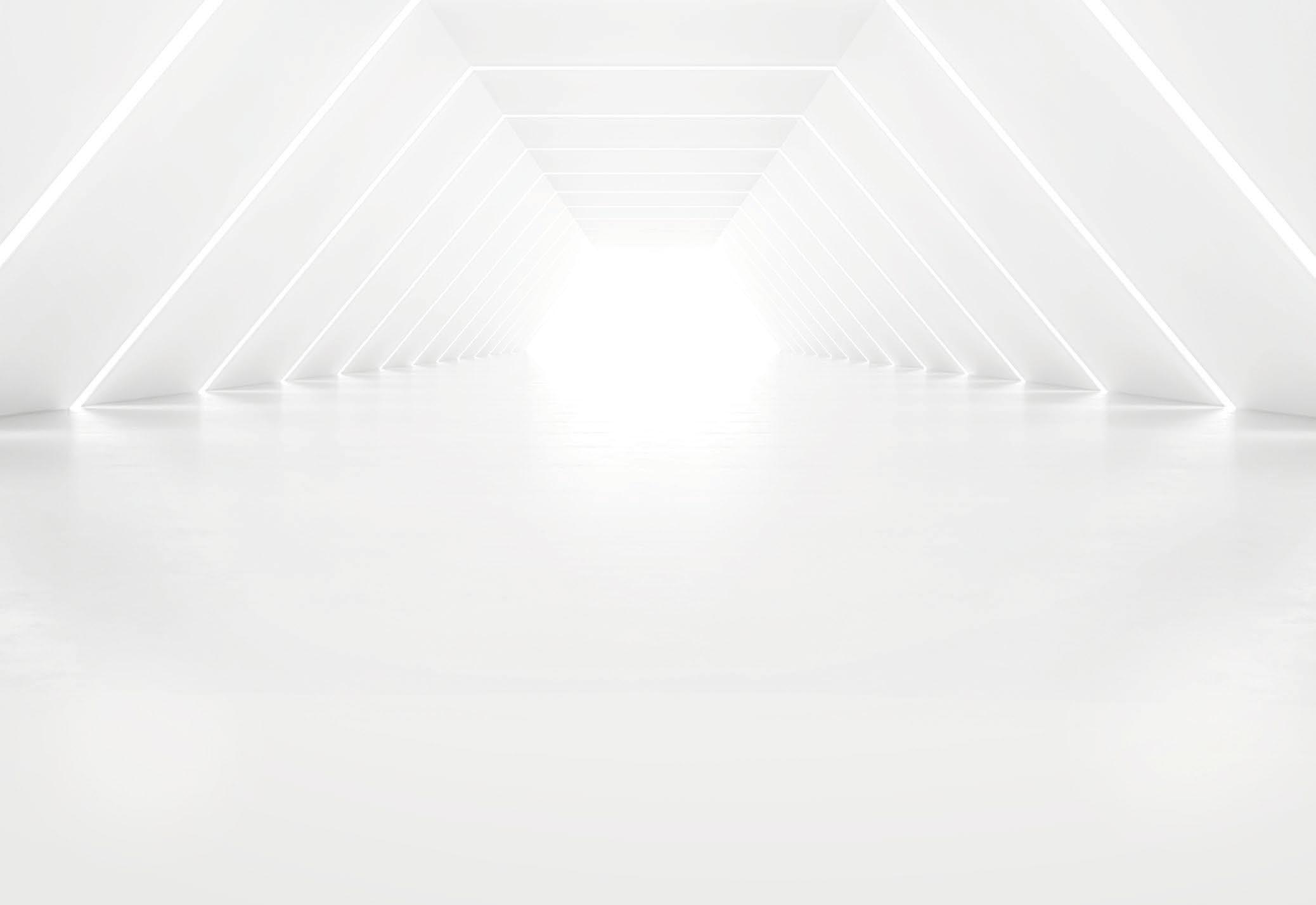
MANUFACTURING


LEARN MORE!
Centorr Vacuum celebrates 70 years in vacuum furnace industry
In 2024, Centorr Vacuum Industries (CVI) is celebrating its 70th anniversary in the vacuum furnace industry. CVI was formed from the combination of Vacuum Industries, founded in 1954 in Somerville, Massachusetts, USA, and the Centorr Furnace company, founded in 1962 in Suncook, New Hampshire. The two were merged in 1989, with new facilities in Nashua, New Hampshire, where the company is still located. In 1997, CVI became 100% management-owned and is now run as a private company under president and CEO William Nareski. “We have enjoyed long-term success over the past seventy years because our highest priority is customer satisfaction with our equipment and service” stated Nareski.
Vacuum Industries was started by the principles of the original National Research Corp. in Boston. It had a long history in the design and building of production size furnaces, primarily for the metals and hardmetals industry. Centorr Furnaces was a Laboratory and R&D furnace manufacturer, and was known for doing some of the first high temperature 3000°C furnaces for the growing ceramics market. In later years, Centorr was known as a world leader in fibre optics and high-temperature hydrogen sintering furnaces for the lighting industry. Today, Centorr is best known for its line of metals and ceramics sintering furnaces, large equipment sold into the nuclear industry, and for its line of furnaces sold into the

Centorr’s facility in New Hampshire, USA (Courtesy Centorr Vacuum Industries)
carbon, graphite, and composites industry for aerospace and hypersonics. The company is one of the leading custom and standardised vacuum furnace manufacturers, and has an installed base of over 7000 high temperature vacuum and controlled atmosphere furnaces worldwide. CVI operates a fully staffed Aftermarket Field Service group and an Applied Technology Center, offering R&D support and toll production service. www.centorr.com
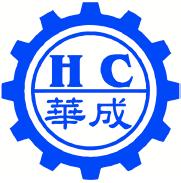
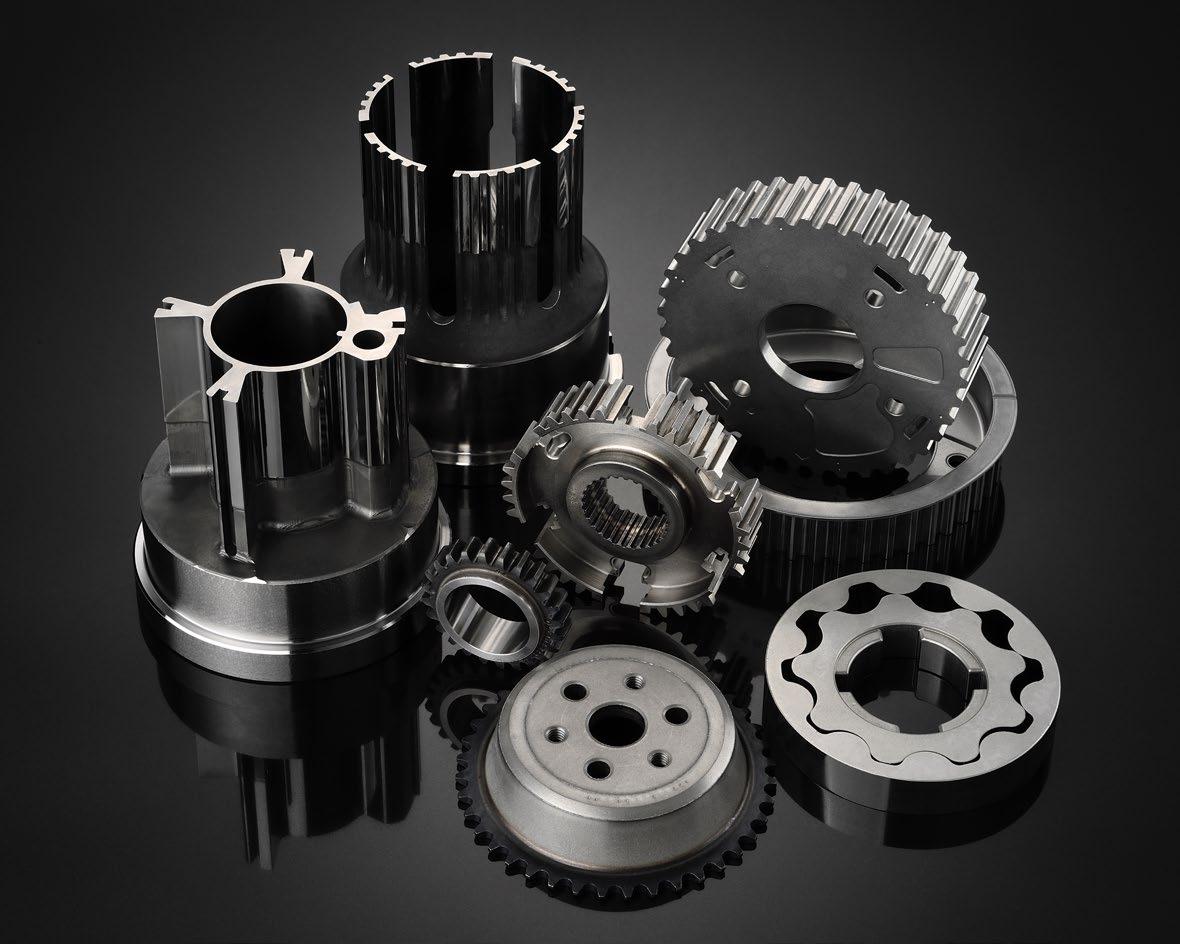
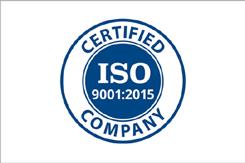

Aubert & Duval and Alloyed unveil new high-temperature Ni superalloy
ABD-1000AM
Aubert & Duval, a subsidiary of the High Performance Alloys Division of Eramet Group based in Paris, France, and Alloyed Ltd, based in Oxford, UK, have announced the release of Alloyed’s nickel superalloy ABD-1000AM, the latest in its range of alloys developed specifically for the Additive Manufacturing process. Designed using Alloyed’s computational Alloys-by-Design platform, the alloy provides excellent environmental resistance and hightemperature strength, with a working temperature range beyond 1,000°C (1,832°F) in its age-hardened state. Compared to cast alloy Ni247LC, the alloy is said to offer near-equivalent stress rupture life while allowing crack-free Additive Manufacturing and heat treatment, enabling complex part design for components within the aerospace, power, automotive, defence and space industries.
The agreement between Alloyed and Aubert & Duval expands upon the successful partnership already in place covering ABD-900AM, a readily processable ultra-high temperature nickel alloy. Under the terms of the agreement, Aubert & Duval will be Alloyed’s production partner for ABD1000AM, supplying Alloyed with the powder feedstock that it is using to manufacture components.
“We are very pleased to extend our metallic powder activities with our long-term partner Alloyed through this new agreement for ABD-1000AM; for Aubert & Duval, the ABD alloys demonstrate the potential that can be realised by designing materials for the AM process, so adding a bestin-class alloy such as ABD-1000AM as part of our powder range portfolio is an exciting next step,” said Jean-François Juéry, EVP Business Development & Strategy of Aubert & Duval. “We are convinced that
Additive Manufacturing technology combined with high-temperature powder alloys is a promising solution in particular to achieve carbon footprint reduction in various industries: over the last five years, we have indeed seen huge growth in interest and orders for these innovative alloys across all industrial sectors, so we are excited to see what new products and performance gains will be enabled by the commercial availability of ABD-1000AM.”
Designed to be free of solidification, liquidation, and strain-age
cracks, ABD-1000AM is said to showcase exceptional processability for such a high-performance alloy. The typical microstructure is characterised by a relative density above 99.9% and low defect levels, consisting of 55% gamma prime phase fraction in the age-hardenable state, a characteristic that attributed to its development on Alloyed’s ABD platform, enabling the alloy to be specifically designed for the characteristics of the AM process.
www.aubertduval.com www.alloyed.com
HOT & COLD
ISOSTATIC PRESSES MANUFACTURERS
Equipment for metal and ceramic components post-processing
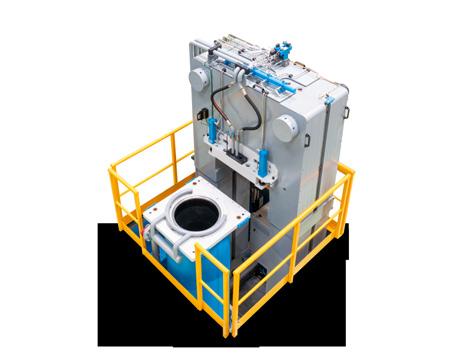
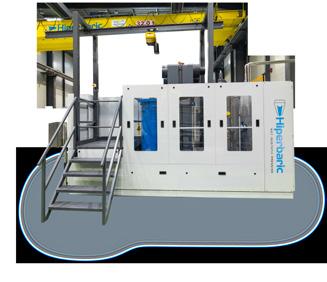
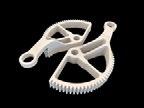
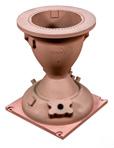
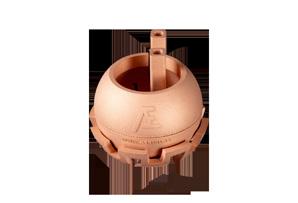
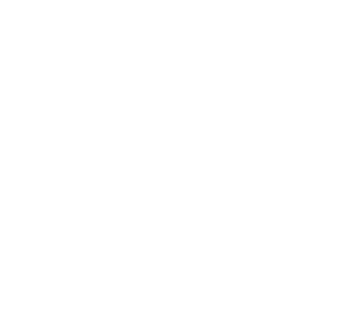
Molymet invests in plasma atomisation technology for rhenium and molybdenum powders
Molymet, headquartered in San Bernardo, Chile, reports it has acquired plasma atomisation equipment to enable the production of highly spherical powders of rhenium,
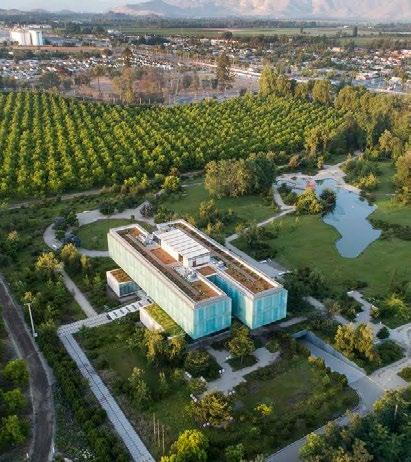
molybdenum, and their alloys, all specifically designed for industrial applications.
The spherical powders produced through this process are intended for various advanced manufacturing technologies, including Additive Manufacturing, Metal Injection Moulding, Thermal Spray, and Hot Isostatic Pressing. These methods, state Molymet, allow users to benefit from enhanced flowability, purity, and density and support the creation of complex parts with lower production costs and processing time.
“We are excited to launch Molymet 3D metal powders. These powders, created through a spheroidisation process, will meet the growing demand of industries that require high-performance materials,” stated Mario Lama, Market Development Executive Manager at Molymet.
Kennametal reports a strong finish in fiscal year 2024 results
Kennametal Inc., based in Pittsburgh, Pennsylvania, USA, has announced its fourth quarter and fiscal 2024 results. For 2024, sales of $2,047 million decreased 2% from $2,078 million in the prior year, said to reflect an organic sales decline of 1% and an unfavourable currency exchange effect of 1%.
“Thanks to the hard work and diligence of our global team, we delivered a strong finish in fiscal year 2024 despite persistent market softness, foreign exchange headwinds and a natural disaster affecting our facility in Arkansas. We successfully met our revenue and EPS outlook and generated $277 million in cash from operations, the highest as a percent of sales in over twenty-five years,” said Sanjay Chowbey, president and CEO.
Operating income for the year was $170 million, or 8.3% margin,
compared with $192 million, or 9.3% margin, in the prior year.
The decrease in operating income was primarily due to lower sales and production volumes, higher wages and general inflation, higher restructuring and related charges of approximately $6 million, charges of approximately $4 million, consisting of repairs and impairments of fixed assets and inventory due to the tornado that affected the company’s Rogers, Arkansas facility during the fourth quarter, and unfavourable foreign currency exchange of approximately $2 million.
These factors were partially offset by pricing, restructuring benefits of approximately $21 million and lower raw material costs. Adjusted operating income was $183 million, or 8.9% margin, compared with $199 million, or 9.6% margin, in the prior year.
“As the world’s largest Rhenium producer, Molymet is committed to responsibly responding to market trends. The targeted markets are expanding, and we are particularly enthusiastic about the applications in the medical, aerospace, and high-end jewellery industries,” Lama added.
The plasma spheroidisation system, which has completed its trial phase at MolymetNos’ facilities, is now operational. The system is reported to be transforming the company’s capabilities, reinforcing its position as the world’s leader in rhenium and molybdenum processing.
Edgardo Cisternas, Research and Development Manager at Molymet, added, “Our new plasma atomisation equipment positions us at the forefront of technological innovation in Additive Manufacturing, meeting the highperformance material demands of our growing markets.”
www.molymet.com
Net cash flow provided by operating activities in fiscal 2024 was $277 million compared to $258 million in the prior year. The change in net cash flow from operating activities was driven primarily by working capital changes including improved inventory levels, partially offset by lower net income compared to the prior year.
Free operating cash flow (FOCF) was $175 million compared to $169 million in the prior year.
The increase in FOCF was driven primarily by working capital changes, including improved inventory levels, partially offset by higher capital expenditures and lower net income compared to the prior year. FOCF was 146% of adjusted net income in fiscal 2024.
In fiscal 2024, Kennametal returned $129 million to the shareholders through $65.4 million in share repurchases and $63.4 million in dividends, while investing $108 million in capital expenditures. www.kennametal.com
Molymet has installed plasma atomisation equipment at its facility in Chile (Courtesy Molymet)


Purdue researchers develop ultrastrong aluminium alloys for AM
Material engineers from Purdue University, West Lafayette, Indiana, USA, have created a patent-pending process to develop ultra-highstrength aluminium alloys with a plastic deformity that makes them suitable for Additive Manufacturing.
The project team – led by Haiyan Wang, the Basil S Turner Professor of Engineering, and Xinghang Zhang, School of Materials Professor – introduced cobalt, iron, nickel and titanium into aluminium via nanoscale, laminated, deformable intermetallics.
“Our work shows that the proper introduction of heterogenous microstructures and nanoscale medium-entropy intermetallics offers an alternative solution to design ultra-strong, deformable aluminium alloys via Additive Manufacturing,” Zhang said. “These alloys improve upon traditional ones that are either ultra-strong or highly deformable, but not both.”
Wang and Zhang disclosed the discovery to the Purdue Innovates Office of Technology Commercialization, which has applied for a US trademark.
Drawbacks of traditional aluminium alloys
Lightweight, high-strength aluminium alloys are used in industries from aerospace to automotive manufacturing. “However, most commercially available high-strength aluminium alloys cannot be used in Additive Manufacturing,” stated Anyu Shang, a Materials Engineering graduate student involved in the project. “They are highly susceptible to hot cracking, which creates defects that could lead to the deterioration of a metal alloy.”
A traditional method to alleviate hot cracking during the Additive Manufacturing process is the introduction of particles that strengthen aluminium alloys by impeding the movements of dislocations.
“But the highest strength these alloys achieve is in the range of 300 to 500 megapascals, which is much lower than what steels can achieve, typically 600 to 1,000 megapascals,” Wang said. “There has been limited success in producing high-strength aluminium alloys that also display beneficial large plastic deformability.”
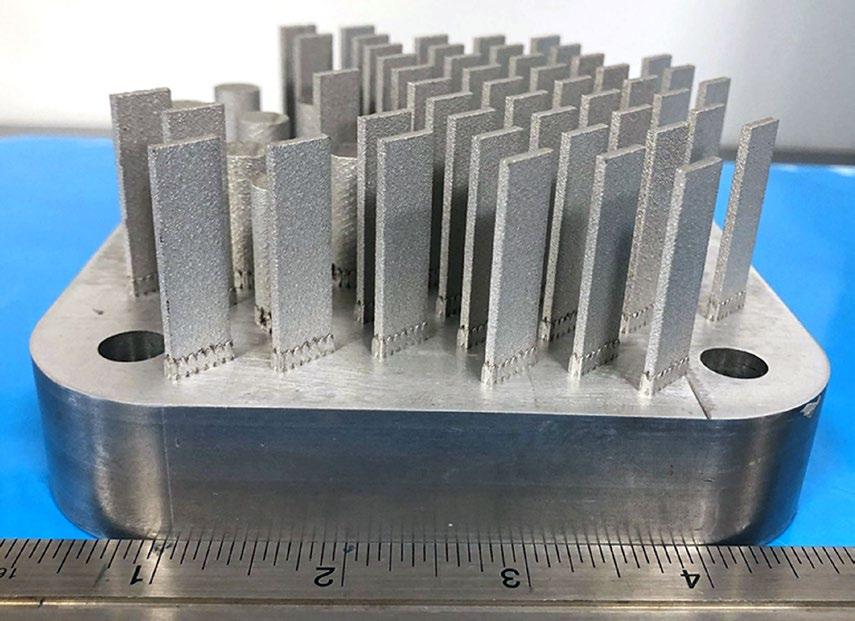
The Purdue method and its validation
The Purdue researchers have produced intermetallics-strengthened aluminium alloys for AM by using several transition metals including cobalt, iron, nickel and titanium.
Shang explained that these metals have traditionally been avoided in the manufacture of aluminium alloys. “These intermetallics have crystal structures with low symmetry and are known to be brittle at room temperature,” he stated. “But our method forms the transitional metal elements into colonies of nanoscale, intermetallics lamellae that aggregate into fine rosettes. The nanolaminated rosettes can largely suppress the brittle nature of intermetallics.”
Wang added, “The heterogeneous microstructures contain hard nanoscale intermetallics and a coarse-grain aluminium matrix, which induces significant back stress that can improve the work hardening ability of metallic materials. Additive Manufacturing using a laser can enable rapid melting and quenching, and thus introduce nanoscale intermetallics and their nanolaminates.”
During the course of the project, the research team has conducted macroscale compression tests, micropillar compression tests and post-deformation analysis on the Purdue-created aluminium alloys.
“During the macroscale tests, the alloys revealed a combination of prominent plastic deformability and high strength, more than 900 megapascals,” reported Shang. “The micropillar tests displayed significant back stress in all regions, and certain regions had flow stresses exceeding a gigapascal.”
He stated that post-deformation analyses revealed that, in addition to abundant dislocation activities in the aluminium alloy matrix, complex dislocation structures and stacking faults formed in monoclinic Al 9Co 2-type brittle intermetallics.
www.purdue.edu
A patent-pending Purdue University method has been able to create ultrahigh-strength aluminium alloys that demonstrate high plastic deformability (Courtesy Purdue University/Anyu Shang)

Aclara and Vacuumschmelze
to develop permanent magnet supply chain
Aclara Resources Inc, Las Condes, Chile, has announced that it has signed a Memorandum of Understanding with Vacuumschmelze GmbH & Co. KG (VAC), a producer of advanced magnetic materials and rare earth permanent magnets headquartered in Hanau, Germany. The agreement establishes a non-binding, non-exclusive, preliminary agreement to jointly approach potential clients as a ‘mine-to-magnets’ solution for ESGcompliant permanent magnets.
Aclara and VAC believe that there is a significant market opportunity driven by the rising demand for electric vehicles, wind turbines, and other clean technologies that require rare earth permanent magnets produced pursuant to ever-increasing ESG standards. Such permanent magnets require significant quantities of both
light and heavy rare earth minerals. Currently, obtaining these rare earth mineral materials, whilst also having the capacity to process them and the industrial technology needed to fabricate permanent magnets, is very limited and concentrated among a few Asia-based suppliers.
“We are thrilled to announce the fortification of our partnership with Aclara, a frontrunner in the development of ionic clay mines in South America,” stated Erik Eschen, CEO of VAC. “This collaboration is aimed at streamlining the supply chain for rare earth elements, specifically Dysprosium and Terbium. These elements play a pivotal role in the decarbonisation of the transportation sector and the generation of renewable energy. By joining forces with Aclara, VAC is committed to
tackling one of the most pressing issues of our era. Our joint efforts not only create value for our customers and shareholders but also contribute significantly to the well-being of our planet.”
VAC and Aclara are two of the very few potential suppliers of dysprosium and terbium. These heavy rare earth minerals are key in the production of permanent magnets and are reportedly not easily available outside of Asia. Aclara is currently developing two ionic clay projects – one in Chile and another in Brazil – for the production of a high-purity heavy rare earth carbonate. In addition, the company is developing processing technology through its US-based subsidiary to be able to receive this carbonate and produce magnetic alloys with it. These alloys, in turn, are the key input required by VAC to produce permanent magnets. www.vacuumschmelze.com www.aclara-re.com
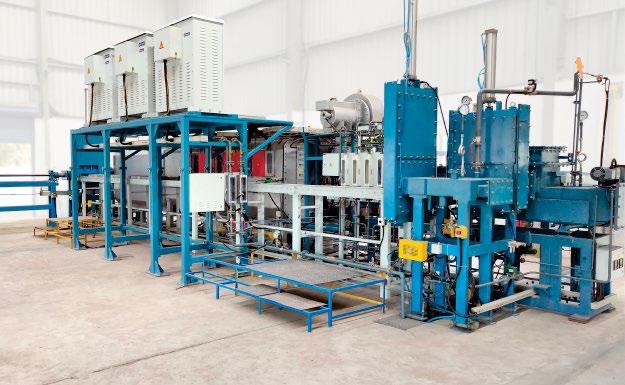

BLT launches high-strength aluminium and titanium alloys for Additive Manufacturing
Xi’an Bright Laser Technologies Co, Ltd (BLT), Xi’an, China, has introduced a new high-strength aluminium alloy for Laser Beam Powder Bed Fusion (PBF-LB) and a new titanium alloy for PBF-LB and Directed Energy Deposition (DED) Additive Manufacturing.
BLT-AlAM500 aluminium alloy
BLT’s new high-strength aluminium alloy, BLT-AlAM500, is specifically designed for aerospace applications. High-strength aluminium alloys are renowned for their strength, thermal stability, and superior processing performance, making them ideal for aircraft structural components and engine parts. Beyond aerospace, high-strength aluminium alloys are also essential in high-speed trains, lightweight automotive parts, and premium sports equipment.
At TCT Asia 2024, BLT showcased parts made from BLT-AlAM500, these included the bent tube, ventilation duct, and connecting pipe seen below.
These components, characterised by thin-walled, irregularly shaped tubular structures with internal cavities, demand high precision. Traditional manufacturing methods are complex, challenging, and costly.
BLT optimised the design for Additive Manufacturing, and used its highstrength aluminium alloy and the company’s BLT-S400 metal PBF-LB machine, to produce the parts. Each component takes approximately thirty hours to form, and achieved an average weight reduction of around 20% compared to the original.
Post-heat treatment, the material achieves tensile strengths of 530-550 MPa, yield strengths of 480-500 MPa, and elongation rates of 11-17%. The material also boasts excellent fracture toughness and fatigue performance, with a room temperature fracture toughness of 30.8 MPa ·m 1/2 and a high-cycle fatigue strength of 245 MPa (smooth sample) at room temperature. Compared to similar imported powders, the BLT-AlAM500 material is reported to offer a cost reduction of about 40-50%, significantly lowering manufacturing costs.
BLT-Ti65 titanium alloy
BLT’s new Ti65 is a multi-component, near-alpha high-temperature titanium alloy, said to maintain excellent strength, plasticity, creep resistance, and thermal stability at temperatures up to 650°C. This performance exceeds the limitations of traditional
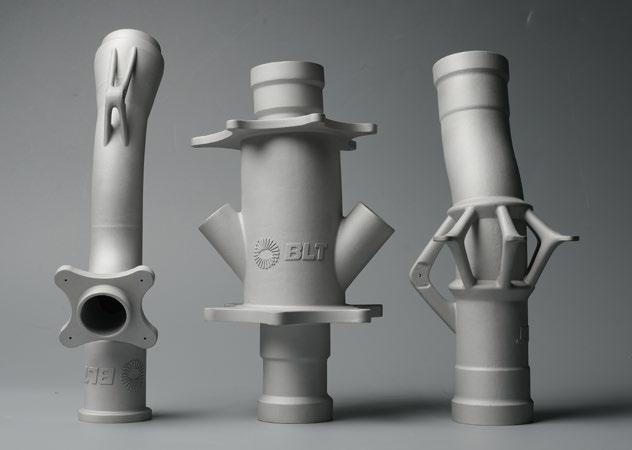
high-temperature titanium alloys, making Ti65 favoured in aerospace, chemical equipment, and marine engineering applications.
However, Additive Manufacturing Ti65 powder can result in defects such as unmelted or partially melted powder particles, inter-track and inter-layer porosity, and cracking, explains BLT. These can concentrate stress and increase the likelihood of material failure. These difficulties led BLT to develop and introduce its BLT-Ti65 powder.
The nominal chemical composition of BLT-Ti65 is Ti-5.9Al-4Sn-3.5Zr0.3Mo-0.4Si-0.3Nb-2.0Ta-1.0W-0.05C, available in 15-53 µ m (for PBF-LB) and 75-180 µ m (for DED). Post-heat treatment, parts produced with 15-53 µ m BLT-Ti65 powder can achieve yield strengths of 483-503 MPa, tensile strengths of 604-624 MPa, and elongation rates of 16.5%26.5% at 650°C. Parts produced with 75-180 µ m BLT-Ti65 powder can achieve yield strengths of 478-538 MPa, tensile strengths of 588-648 MPa, and elongation rates of 22%-32% at 650°C.
BLT’s material portfolio now includes over eighty types, including titanium alloys, high-temperature alloys, aluminium alloys, titaniumaluminium alloys, copper alloys, stainless steel, tool steel, highstrength steel, tantalum-tungsten alloys, silver, and hard alloys.
www.xa-blt.com

The bent tube, ventilation duct, and connecting pipe are additively manufactured from BLT-AlAM500 aluminium alloy powder (Courtesy BLT)
BLT demonstrated the capabilities of its new BLT-Ti65 titanium alloy by producing this high density sample aerospace part (Courtesy BLT)
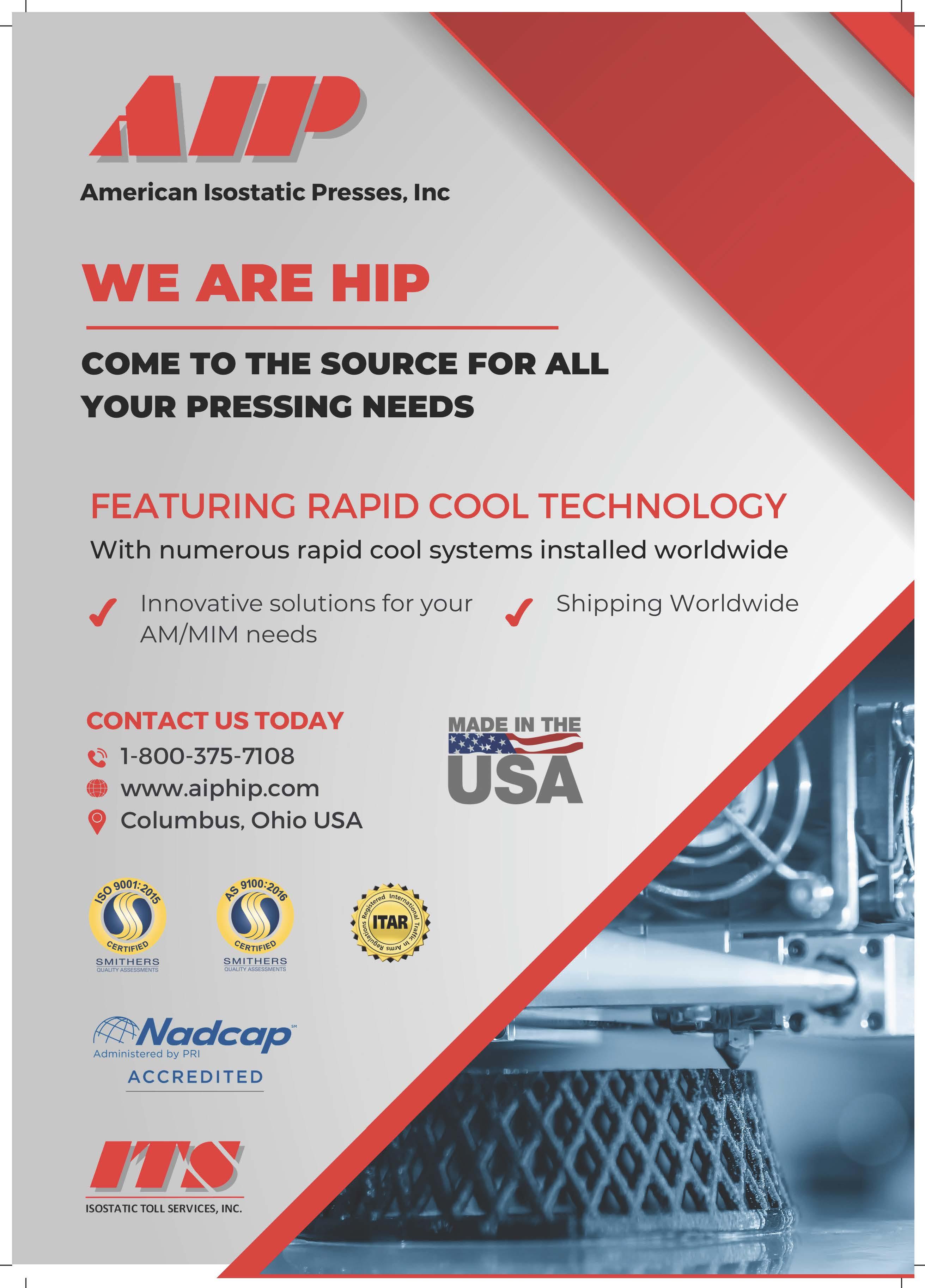
Höganäs Brazil celebrates twenty-fifth anniversary
Höganäs Brazil, based in Mogi das Cruzes, near São Paulo, has celebrated its 25 th anniversary.
Founded through the acquisition of Belgo Brasileira in 1999, the
company is home to operations and sales for Brazil, as well as the head office for Region South America. There are around 140 employees at Höganäs Brazil and, to recognise
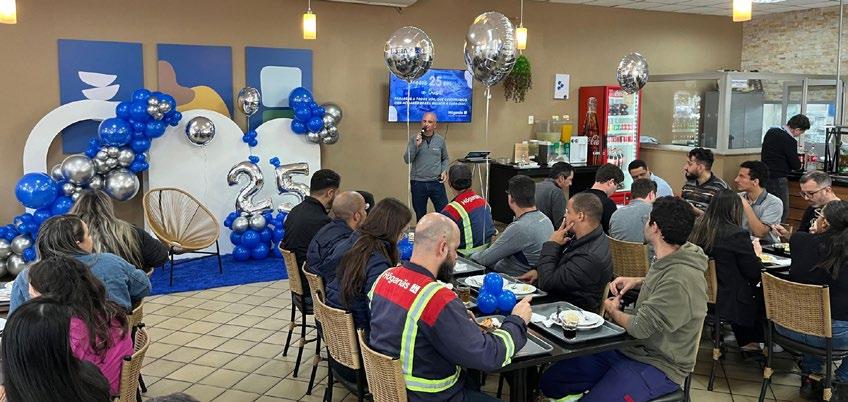
Höganäs Brazil celebrated its 25 th anniversary with a special lunch for all employees (Courtesy Höganäs)
USA announces
$1.7B
to convert auto manufacturing sites to electric vehicle production
As part of the US government’s Investing in America agenda, the Department of Energy (DOE) has announced $1.7 billion to support the conversion of eleven shuttered or at-risk auto manufacturing and assembly facilities to manufacture electric vehicles. The funding will support sites in Michigan, Ohio, Pennsylvania, Georgia, Illinois, Indiana, Maryland, and Virginia, with the investments helping create and retain thousands of jobs and support the American auto communities that have historically driven the domestic economy.
“There is nothing harder to a manufacturing community than to lose jobs to foreign competition and a changing industry,” stated US Secretary of Energy Jennifer M Granholm. “Even as our competitors invest heavily in electric vehicles, these grants ensure that our automotive industry stays competitive and does it in the communities
and with the workforce that have supported the auto industry for generations.”
“President Biden set out to build a clean energy economy that benefits everyone,” said John Podesta, Senior Advisor to the President for International Climate Policy. “Today’s awards from the Department of Energy help bring that vision to life by investing in the future of the auto industry, creating thousands of good-paying union jobs, and tackling the existential threat of climate change by cutting pollution from the transportation sector.”
The selectees of Domestic Manufacturing Auto Conversion Grants programme will negotiate for awards to enable them to manufacture products covering a broad range of the automotive supply chain, including parts for electric motorcycles and school buses, hybrid powertrains, heavy-
their efforts, the company recently hosted a special lunch. The president of Höganäs Brazil, Adriano Machado, spoke with attendees and Höganäs CEO Henrik Ager sent a message directly from Sweden.
“We appreciate the dedication of each one of you to make Höganäs Brasil a better company every day. Let’s continue to work with Safety and promote positive change through innovation in materials!” stated Ager.
Reporting on the event, Adriano Machado, President at Höganäs Brasil stated on LinkedIn, “Proud to be part of this history full of achievements, evolving with customers, employees, society and the regional economy – from Höganäs and Mogi das Cruzes to Brazil and the world! Thank you to everyone who believed and invested their most precious asset – time – in this journey so far! Let’s go together!”
www.hoganas.com
duty commercial truck batteries, and electric SUVs.
This announcement complements the $177 billion in private sector investment in EV and battery manufacturing spurred to date by the Investing in America agenda. The programme is also intended to support the administration’s efforts to strengthen domestic supply chains, support American workers, and bolster America’s global position in manufacturing.
The award selections are subject to negotiations to ensure that commitments to workers and communities are met. DOE will also complete environmental reviews to ensure that the awards are consistent with the Administration’s commitments to clean, environmentally responsible manufacturing, and include appropriate mitigation as needed. If awarded, the selected projects would collectively create over 2,900 new high-quality jobs and help ensure over 15,000 highly skilled workers are retained across all eleven facilities.
www.energy.gov
Taniobis introduces DIN ISO 14021-certified closed-loop recycling for tantalum
The Taniobis Group, a subsidiary of JX Metals Corporation, headquartered in Goslar, Germany, has furthered its sustainability goals with the introduction of a DIN ISO 14021-certified closed-loop range of materials. The company has developed a 100% recycling route for various tantalum-containing synthetic concentrates, metals, oxides, and chemicals.
“Thanks to our recycling process, we are in a position to recover tantalum from almost all waste containing tantalum, to produce high-purity tantalum metals and oxides to meet customer requirements,” stated Guido Klages, Head of HSEQ at Taniobis.
The company is also compliant with all management systems and certified for DIN ISO 9001, DIN ISO
14001, DIN ISO 45001, and DIN ISO 50001. The goal is to demonstrably meet the demands and responsibilities towards customers, employees, and the environment. Requirements are constantly developing and advancing in the areas of the environment, quality assurance, health and safety, and energy and management systems.
“In all cases, certification is not just a one-off process, but rather requires continuity. We look forward to this mission, and we will always continue to develop,” explained Klages.
As the leading supplier of tantalum and niobium powders and alloys, Taniobis states that it is working to make progress on issues that are relevant to society through research and development.
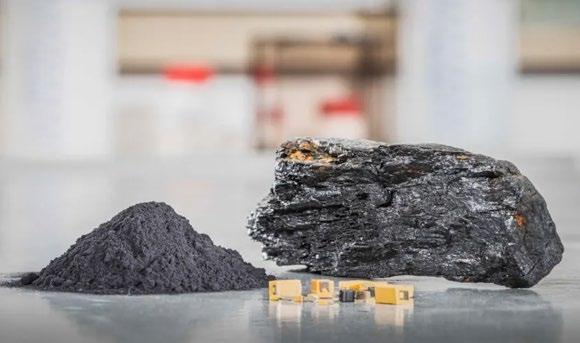
The Taniobis Group has a closed-loop range of tantalum materials (Courtesy Taniobis)
For example, tantalum and niobium powders are critical for the manufacturing of biocompatible implants, and high-voltage tantalum capacitor powders are ideal for capacitors used in electronic mobility devices.
“We are working intensively on issues that will determine our future. Therefore, it is only logical for us to make sure we don’t take more from the world than we need, and to produce in a resource-efficient manner,” concluded Masafumi Ishii, CEO of the Taniobis Group. www.taniobis.com


Researchers assess powder quality with triboelectric charging concept
Researchers from McGill University, Montreal, Canada, have demonstrated a new method of assessing the quality of metal powders for Additive Manufacturing using a triboelectric charging concept on using CpTi, Ti6Al4V, AlSi10Mg, IN 738, and SS 316L powders. The results were published in Scientific Reports
In many Additive Manufacturing processes based around powder beds, such as Laser Beam Powder Bed Fusion (PBF-LB) and Binder Jetting (BJT), the quality of the spread layer – characterised by its continuity, uniformity, and packing density – must be maximised to
reduce surface defects and porosity in the resultant components. Under the scope of ‘A method to assess the quality of Additive Manufacturing metal powders using the triboelectric charging concept,’ the authors introduced a new methodology for triboelectric charging. Modifications introduced to the GranuCharge setup, including an electronic flow rate measuring tool to assess tribocharging as a function of flow rate, were noted as successful.
The authors propose to measure the tribocharging behaviour at several flow rates instead of just
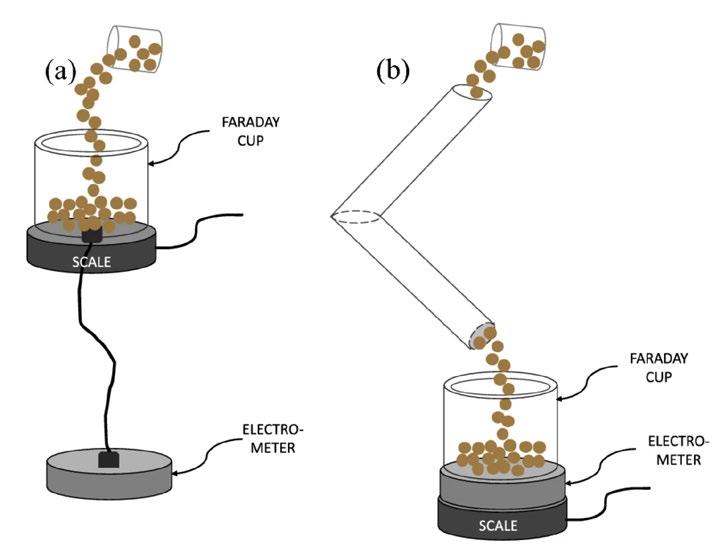
GranuCharge measurement of (a) initial charge and (b) final charge with modification (As published in ‘A method to assess the quality of Additive Manufacturing metal powders using the triboelectric charging concept,’ courtesy Scientific Reports)
MPIF announces winners of 2024 Outstanding Technical Paper Awards
The MPIF Technical Board has critically evaluated and completed its review of the manuscripts presented at the PowderMet2024 and AMPM2024 conferences, held in Pittsburgh, for the Outstanding Technical Paper Awards.
The winner of the 2024 Howard I Sanderow Outstanding Technical Paper Award is Comparison of Soft
Magnetic Composites (SMC) Lamination Assemblies by Bruce Lindsley and Neal Kraus of Hoeganaes Corporation. The winner of the 2024 Metal AM Outstanding Technical Paper Award was announced as Development of an Abrasion Resistant Alloy for the Metal Binder Jet Process by Chris Schade, Tom Murphy, and Kerri Horvay of Hoeganaes Corporation.
one, because some flow rates may not indicate significant variation between two indistinguishable yet dissimilar powders, while other flow rates do. Minor variation of powder’s surface chemistry has proved to have affected the tribocharging response of the metal powders; tribocharging behaviour may not be the same even with powders having the same passivation oxide (e.g. CpTi and Ti6Al4V). The presence of negligible amounts of extra oxide, such as Al2O3, can cause considerable variation in powder tribocharging behaviour. Even a small amount of water produced a significant deviation from the expected tribocharging behaviour.
Recognising the degree of influence of moisture to the triboelectric behaviour of AM powders is paramount to assessing the degradation of powder quality, explained the authors. Hence, further studies on the interaction of moisture with AM powders and how it affects their tribocharging response are recommended.
The authors have stated their intentions to evaluate other powder systems than the ones studied in this work and expand the database of tribocharging constants for AM powders, which could open the gate to use the technique to identify surface states by the tribocharging constants knowledge as an alternative to analytical techniques like XPS.
www.nature.com www.mcgill.ca
Both award-winning papers will be included in the appropriate conference proceedings. Advances in Powder Metallurgy & Particulate Materials — 2024 and Advances in Metal Additive Manufacturing with Powder Metallurgy — 2024
The winning authors will be presented with their awards during PowderMet2025 and AMPM2025, scheduled to take place in Phoenix, Arizona, USA, from June 15-18, 2025.
www.mpif.org

NTN CEO named Chairman of Japan’s
Bearing Industry Association
Eiichi Ukai, CEO of Japan’s NTN Corporation, Osaka, has been appointed Chairperson of the Japan Bearing Industry Association (JBIA).
JBIA is an association of corporations that manufacture bearings. It was established in July 1948 to address issues such as technical standardisation, the prevention of unauthorised products, environmental protection, and measures for small- and medium-sized enterprises throughout the industry.
Eiichi Ukai joined NTN Corporation (then NTN Toyo Bearing Co, Ltd) in 1980, and became Operating Officer in 2011 before being promoted to Managing Operating Officer and

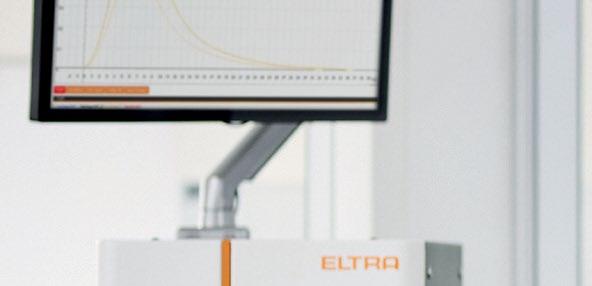
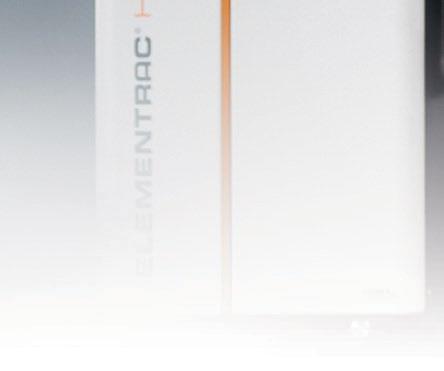
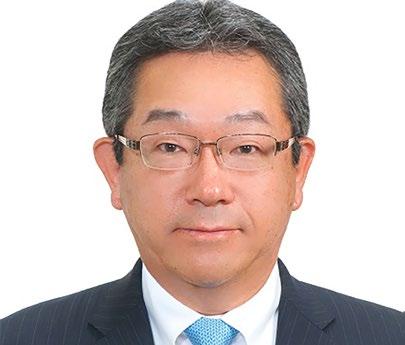
Eiichi Ukai, CEO, NTN Corporation, has been appointed Chairman of the Japan Bearing Industry Association (Courtesy NTN Corporation)
General Manager of ASEAN, Oceania & West Asia Region in 2014. He was appointed a director in 2017, and has been in his current position since April 2021.
As Chairperson of JBIA, he will continue to work for the sustainable development of the bearing industry as a whole.
www.ntnglobal.com www.jbia.or.jp
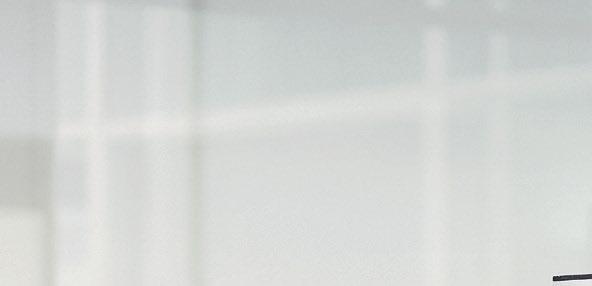
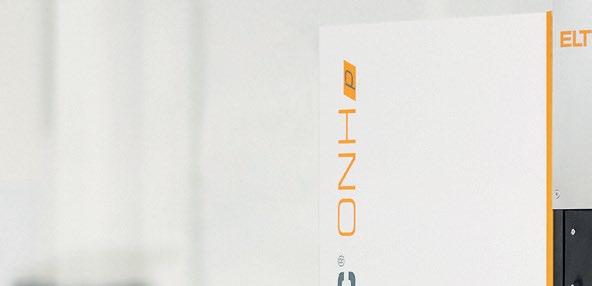
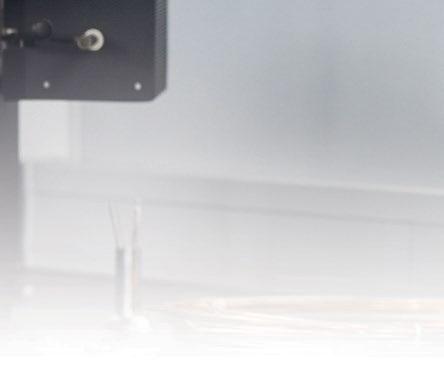
Plansee Seminar Call for Abstracts
The Plansee Group has issued a Call for Abstracts for the 21 st Plansee Seminar. Set to take place June 1–6, 2025 at Plansee’s headquarters in Reutte, Austria, the seminar will focus on refractory metals and hard materials.
The seminar will cover a variety of topics, from materials science to the latest achievements in extractive metallurgy, manufacturing technology, industrial applications and sustainability. Of particular focus will be presentations covering Rhenium, an important alloying element for tungsten and molybdenum celebrating the 100 th anniversary of its discovery.
Abstracts submissions are due no later than October 4, 2024. www.plansee-seminar.com
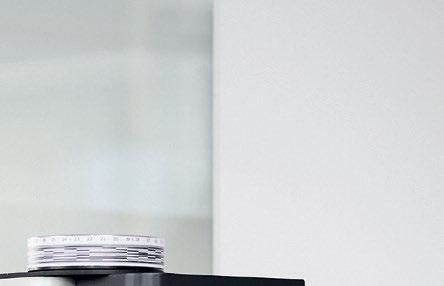
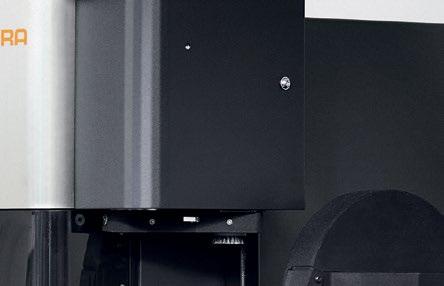
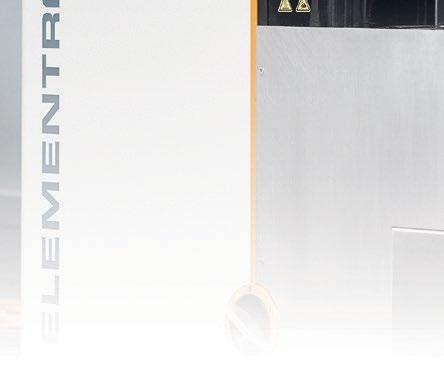
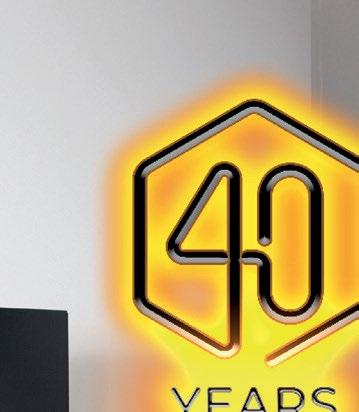
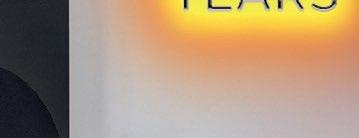

ELEMENTAL ANALYSIS OF METAL POWDERS & FEEDSTOCK
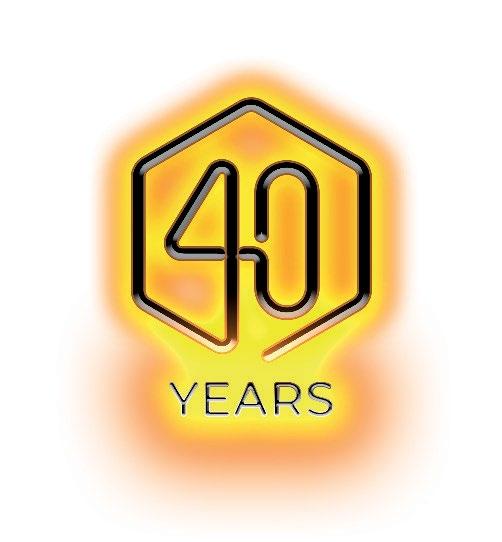
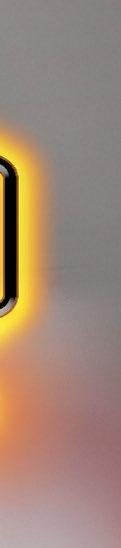
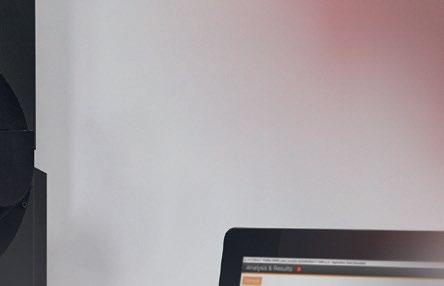
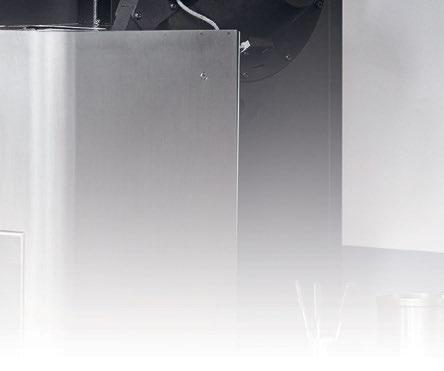
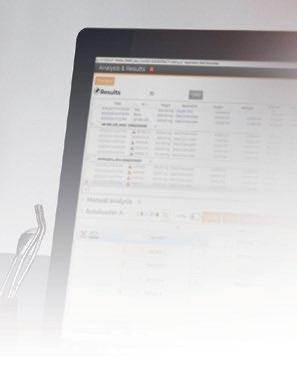

ELTRA’s new and innovative ELEMENTRAC series is a mile stone for C/S and O/N/H analysis in Powder Metallurgy and Additive Manufacturing: easy to use, fast analysis times and reliable results for metal powders and processed samples.
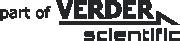
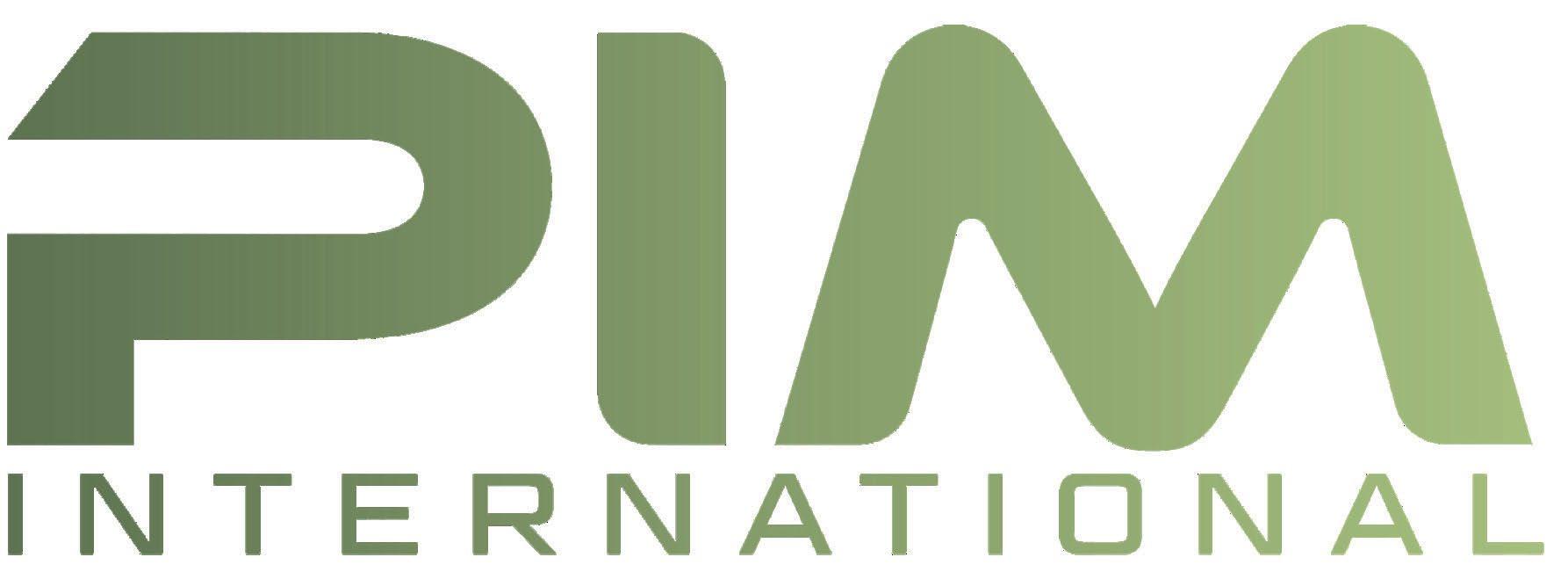
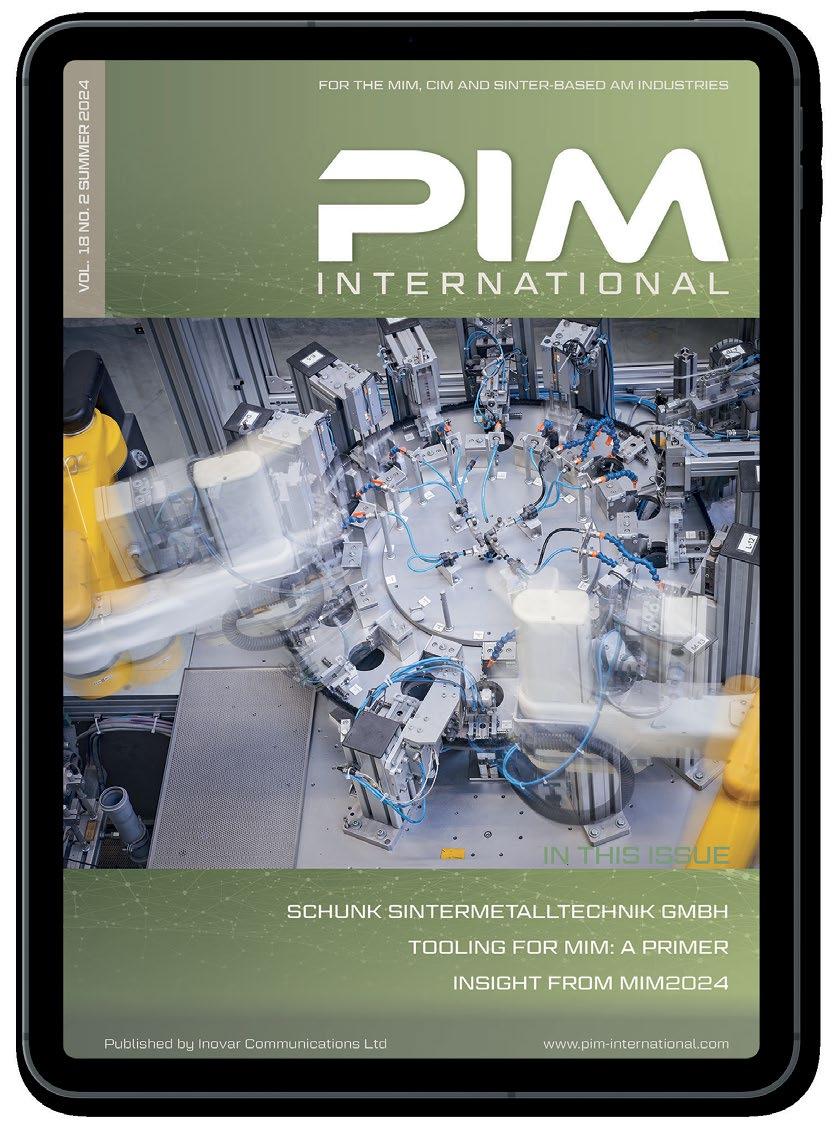
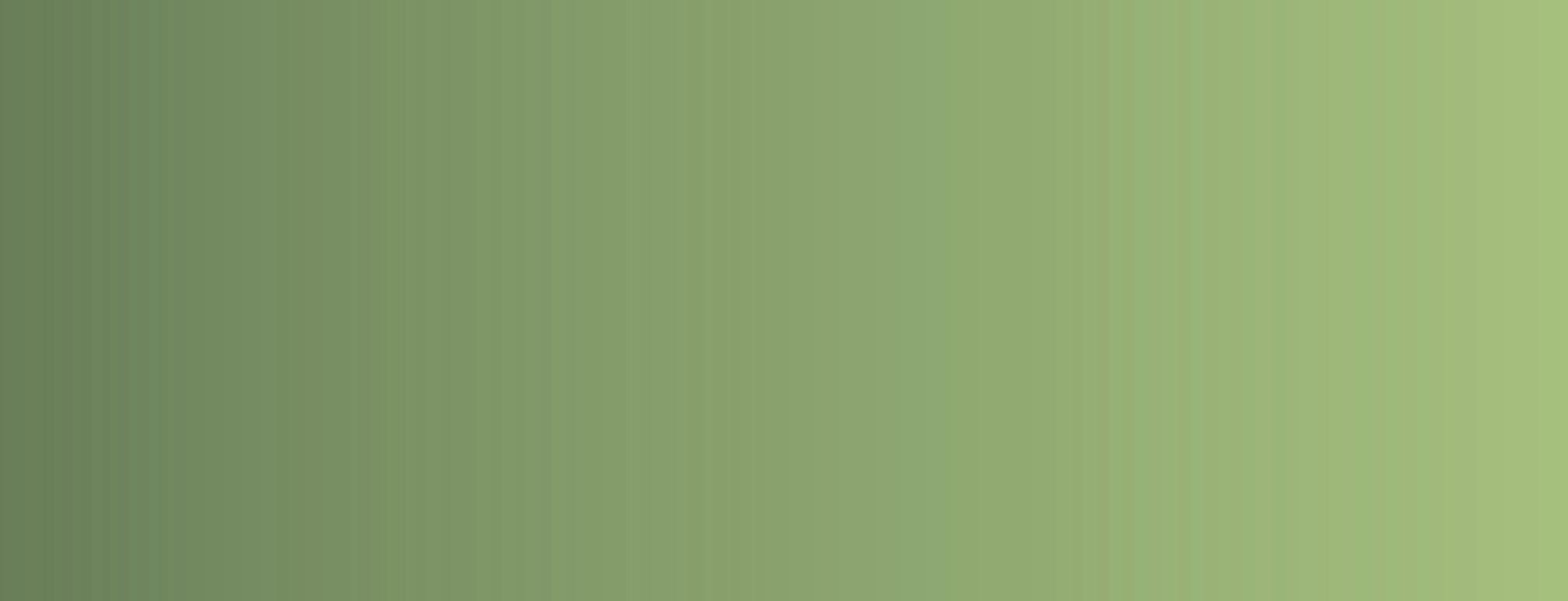
Our exclusive deep-dive articles, company profiles, conference reports and newsletters are of great value to those interested in this advanced manufacturing technology for the production of complex, high volume netshape components

Inductotherm Group announces leadership transition
Thermal processing technologies company Inductotherm Group, headquartered in Rancocas, New Jersey, USA, has announced that Gary Doyon has stepped down after fifteen years as CEO, and thirty-eight years with the company. Mick Nallen and Satyen Prabhu will act as Inductotherm Group’s new co‐leaders, leveraging their complementary strengths and experiences.
Inductotherm Group is the parent company of Consarc Corporation, known for its design and manufacture of a wide range of advanced vacuum and controlled atmosphere furnaces for the processing of metals, specialty alloys, and engineered materials. The first Consarc specialty furnace was developed over sixty years ago and, today, it is said that over half the vacuum or controlled-atmosphere melting furnaces around the globe bear the Consarc name.
Although stepping down as CEO, Doyon intends to remain actively involved with the company. He will continue to serve as the only non‐family member on the parent company board, assisting with specific operational needs of other businesses owned by the Rowan family and pursuing new business avenues and opportunities for the Inductotherm Group. This transition is part of Doyon’s planned succession strategy, which aims to ensure the continued growth and success of the Inductotherm Group.
“We greatly appreciate and thank Gary Doyon for his exceptional leadership over the past fifteen years,” stated Virginia Rowan Smith, Inductotherm Group Chairman. “The Inductotherm Group is positioned for great things in the future based on its strength today. As we move forward with our succession plans, we are confident that the new leadership will continue to uphold the high standards and legacy that Gary has established.”
“We are pleased to announce that Mick Nallen and Satyen Prabhu have been selected to be Co‐Leaders,” added Smith. “This management strategy fits perfectly with the fact that our business is large, growing fast, and becoming wider in product technologies around the world. Mick and Satyen have come up with strong business plans that meet our family’s goal of maintaining a stable, customer‐focused, and technology‐centric business. We have an exciting future ahead of us.”
As part of their new roles, Nallen and Prabhu will focus on thought leadership, market comprehension, and a deep understanding of the thermal processing industry’s various sectors. Their strategic vision is expected to ensure that the group continues to deliver cutting‐edge induction technologies while preserving the core values and vision of its founder, Henry Rowan. www.inductothermgroup.com
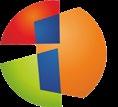
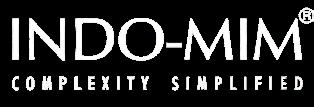


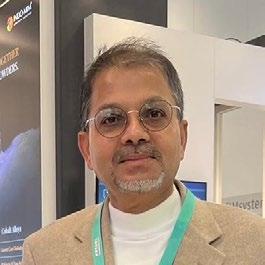


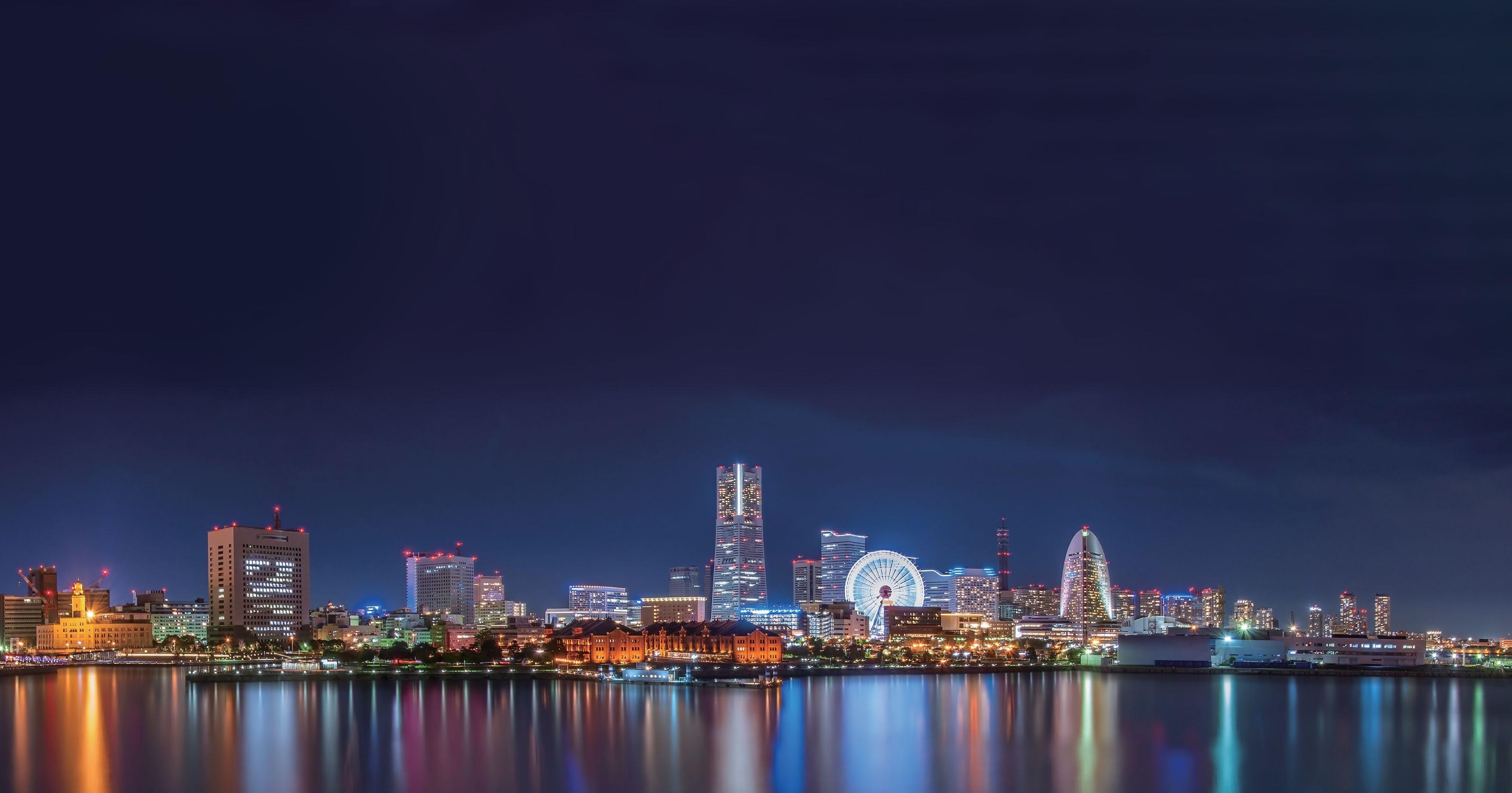
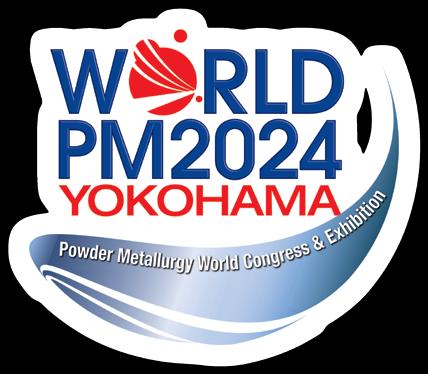
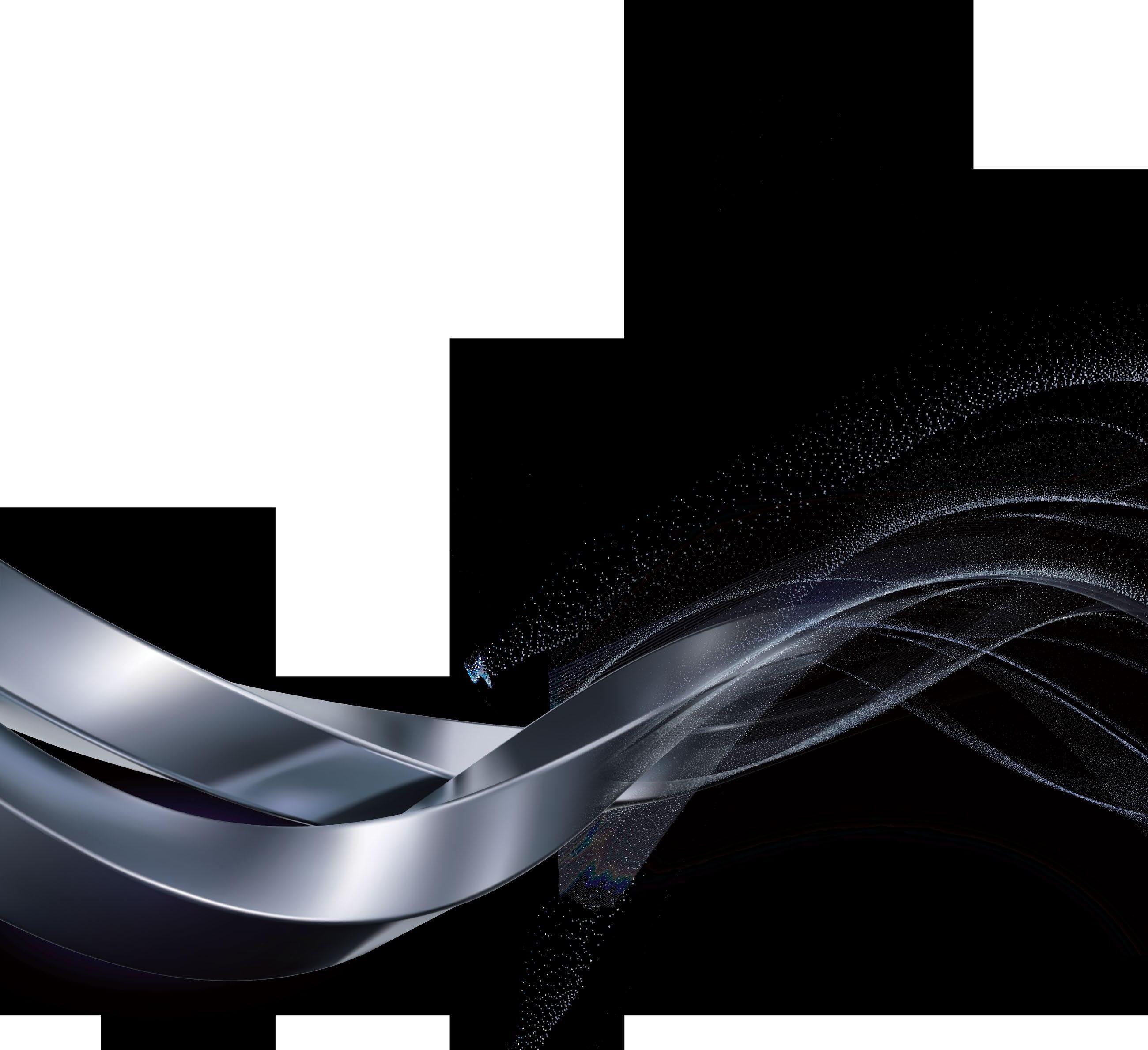
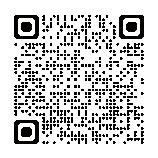
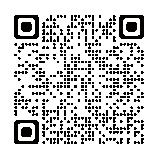
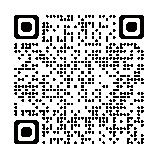
Collaboration drives success for PM: New Hyundai Motor applications developed with Korea Sintered Metal Co. and Höganäs AB
Despite the shift towards electrification, the further development and optimisation of internal combustion engines (ICEs) is still necessary in order to meet society’s diversified transportation needs. As it has done in the past, Powder Metallurgy is able to deliver the innovative solutions that are required for a new generation of engines. In this article, Hak-Soo, Kim, Hyundai Motors, reports on a collaborative project between Hyundai Motor Company and Korea Sintered Metal Co. that resulted in the development of two innovative new PM automotive applications.
Developing and bringing new Powder Metallurgy parts to market is generally a lengthy process. This is especially true when the sintered parts are replacing current massproduced components; production teams – spanning engineering, design, testing, procurement, and quality control – will almost always be concerned about the hours of labour required for this development process and the risk of the new parts falling short in quality. Nevertheless, the possibility of significant cost reductions compared with conventional manufacturing processes can drive a team towards the decision to develop new PM parts. Although addressing all the issues required for a mass production process requires optimisation, teams are also generally under time constraints, which must be taken into account. When Hyundai Motor Company began to focus on optimising certain components, Höganäs Korea and Korea Sintered Metal Co. were able to quickly provide solutions.
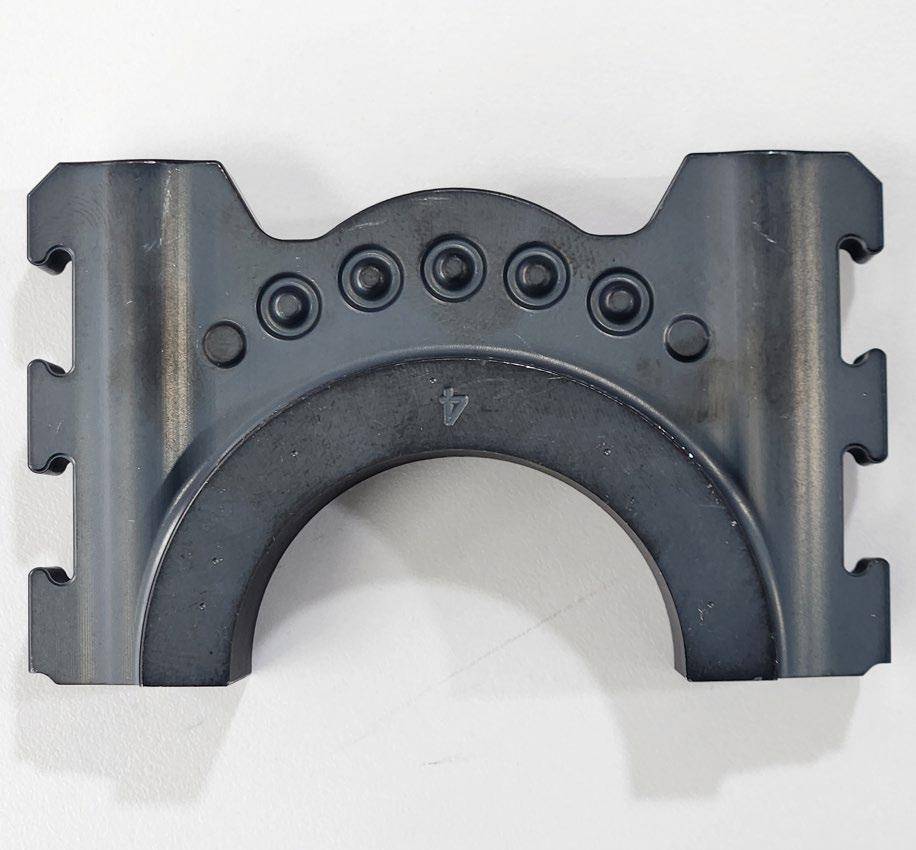
Fig. 1 Bringing new sintered PM parts to market is generally a lengthy process, however, as in the case of this bedplate insert, the advantages achieved can bring significant benefits (Courtesy Hyundai Motor/Korea Sintered Metal/Höganäs Korea)

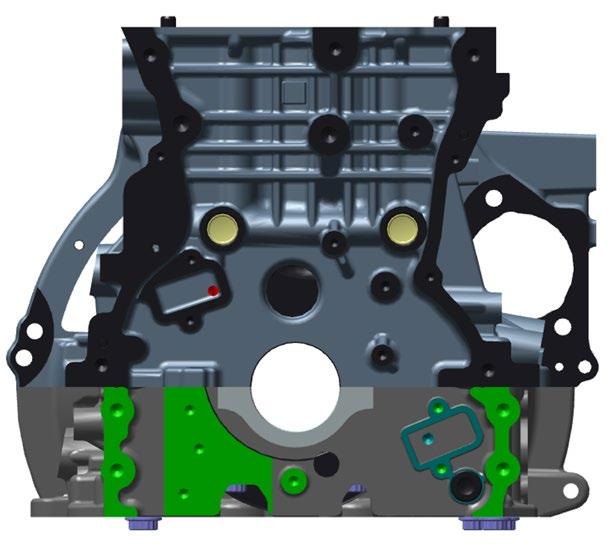

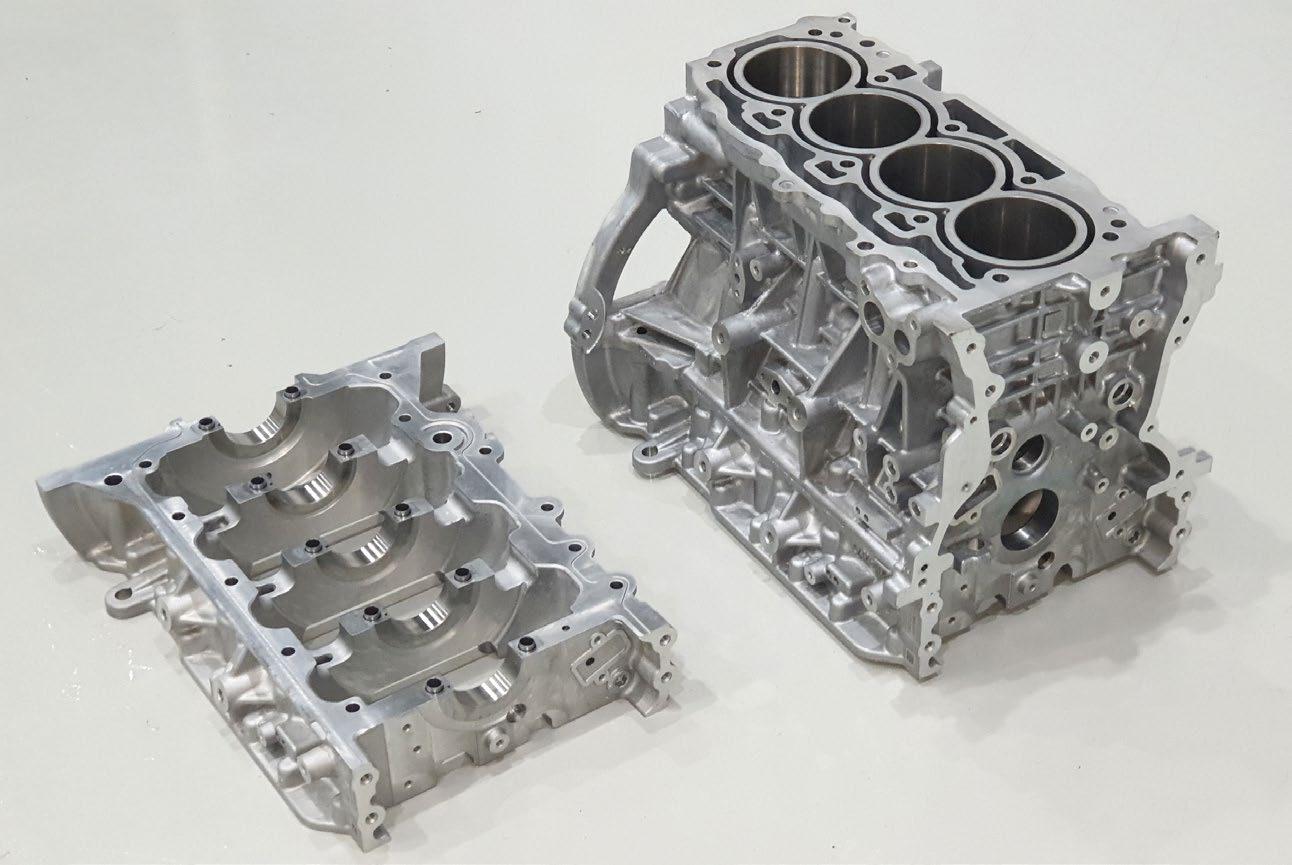
Fig. 2 Top: engine block and bedplate schematic showing the location of the bedplate insert components. Above: the bedplate and engine block with the PM parts inserted (Courtesy Hyundai Motor/Korea Sintered Metal/Höganäs Korea)
The following newly developed applications are the result of such ongoing activities. By detailing these new PM parts and their development, we hope that this article will be a good reference point for those who plan to develop new sintered parts.
Bedplate inserts
A bedplate in the engine block is also called a lower crankcase; and the cast iron insert is also termed a bedplate insert (Fig. 2). This structure is used to enhance NVH (noise,
vibration and harshness) suppression characteristics and to distribute stress from the crankshaft. This is done by combining a ladderframe bedplate and bedplate insert, thereby preventing the oil film on the main bearing from becoming too
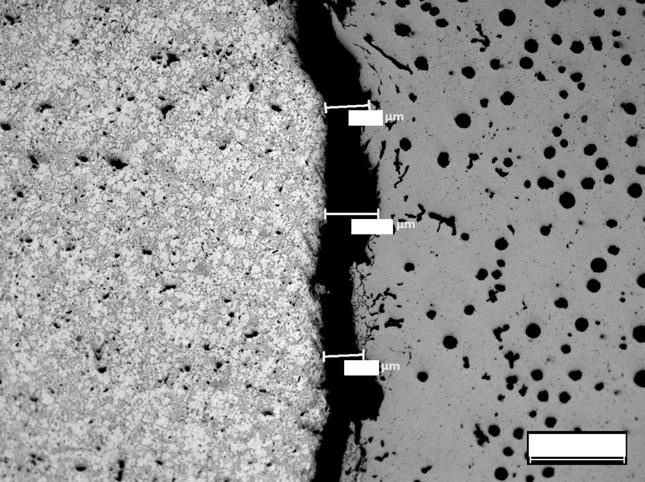
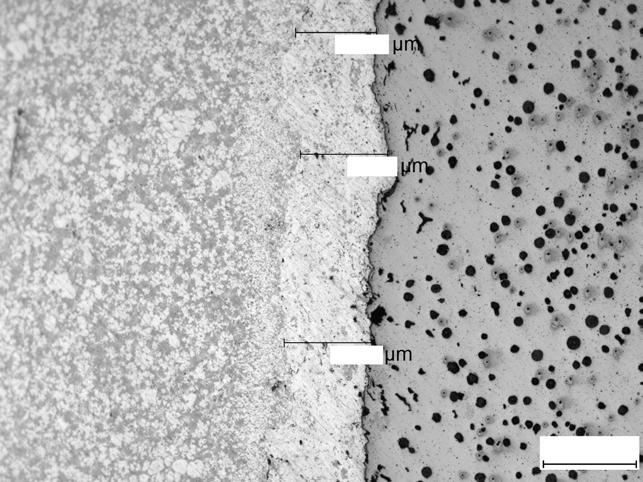
thin. Sometimes, an aluminium-only bedplate is used, but this can result in oil leaks under heavy loads. In practice, most bedplates are made by placing cast iron inserts into die casting moulds and incorporating them into the aluminium casting.
Aluminium parts and inserts must be well-designed to distribute the load from the crankshaft, but optimisation can be difficult to achieve by analysing and testing dissimilar materials within the limited development schedule. Moreover, the design of a bedplate necessarily has a low degree of freedom as it is complementary to the geometry of the crankshaft. As the inserts’ volume increases, the volume of aluminium parts on the surface decreases, making the thin aluminium section attached to cast iron inserts vulnerable to vibrations when in use.
“An aluminium spray coating was applied to the surface of the cast iron inserts to overcome this issue but was found to be too costly a solution. To reduce the cost, we developed sintered PM inserts with a removable coating.”
Inspection of the aluminium die casting after sectioning showed a partially separated interface between the aluminium and cast iron. This caused a concern over potential cracks developing in the aluminium due to movement at the interface of the two dissimilar materials if excessive external force is applied. An aluminium spray coating was
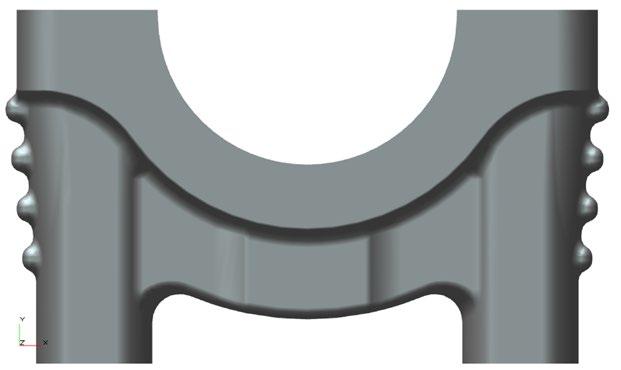
applied to the surface of the cast iron inserts to overcome this issue but was found to be too costly a solution (Fig. 3). To reduce the cost, we developed sintered PM inserts with a removable coating (Figs. 4 and 5). To improve the mechanical joints with the aluminium and prevent movement slips between dissimilar materials, we implemented a dovetail structure
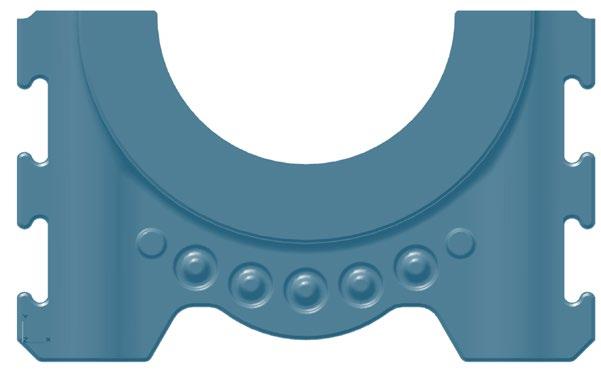

Fig. 4 The cast insert (left) and the Powder Metallurgy insert (right) (Courtesy Hyundai Motor/Korea Sintered Metal/ Höganäs Korea)
Fig. 3 The interface before and after thermal spraying (Courtesy Hyundai Motor/Korea Sintered Metal/Höganäs Korea)
Aluminium
Ductile iron
Coating layer
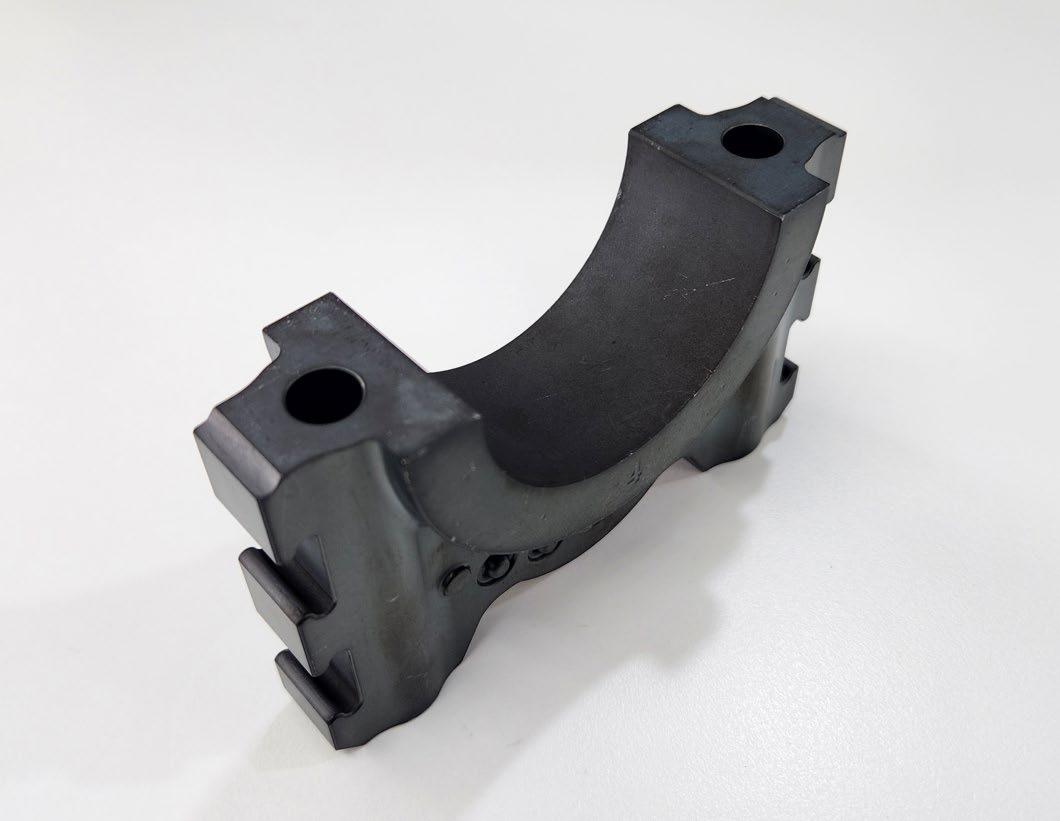
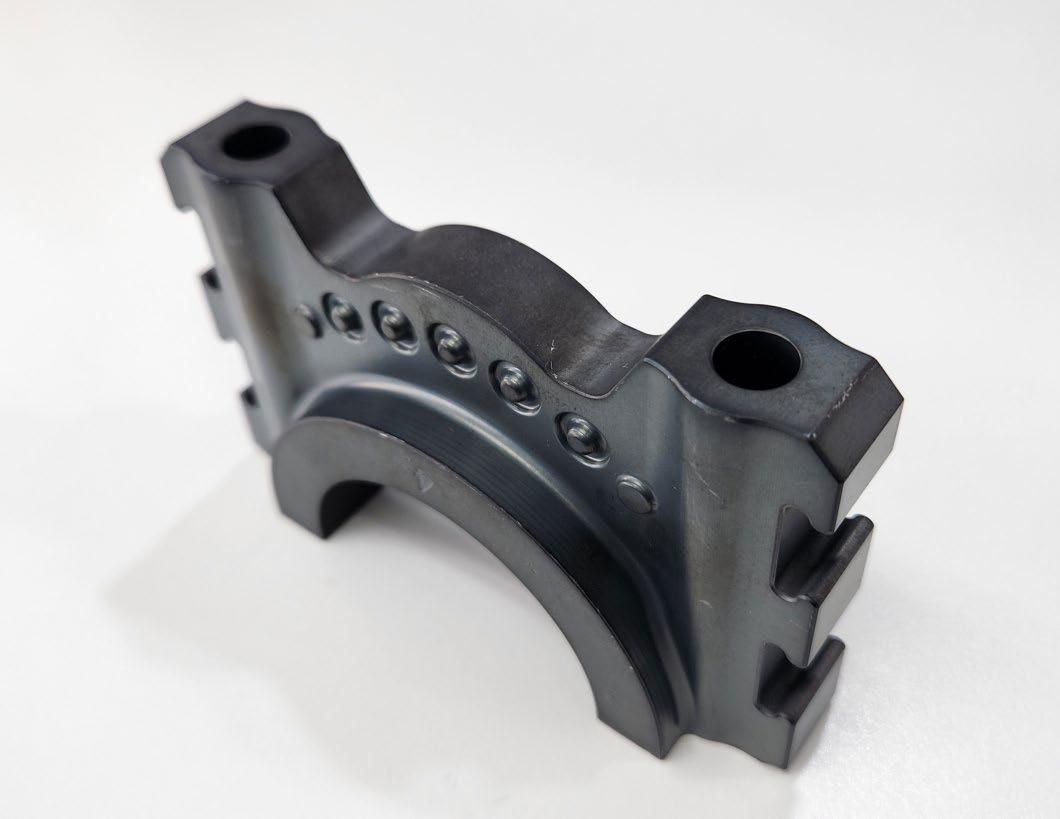
“In looking for alternatives, we overcame the problem of property degradation in the sintered inserts by selecting Höganäs AB’s new lean Cr-Mo pre-alloyed steel powder. This powder produces parts with lower porosity, resulting in better air tightness during the steam treatment process.”
and concave and convex protrusions, later filled with aluminium during the casting process. Korea Sintered Metal determined that the PM press and sinter process was suitable for the creation of such a structure and began reviewing the suitability of the component-process combination for mass production.
However, an issue occurred when producing a prototype of the bedplate. During preheating – which is necessary before placing sintered inserts into a mould – the working fluids and rust-prevention oil in the sintered inserts were found to evaporate. Since this poses a health risk to workers, steam treatment was applied to the PM inserts as a preventative measure. Unfortunately, the properties of the sintered Fe-Cu-C material used degraded when exposed to high temperatures during the steam treatment, preheating, and die casting processes. Our analysis established that solid Cu finely precipitated and separated on the PM insert surface during preheating (Fig. 6). This was presumed to be the cause of the property degradation.
In looking for alternatives, we overcame the problem of property degradation in the sintered inserts by selecting Höganäs AB’s new lean Cr-Mo pre-alloyed steel powder. This powder produces parts with lower porosity, resulting in better gas tightness during the steam treatment process. Additionally, it had advantages in terms of cost, carbon emissions, and recycling. Although the high hardness resulting from the steam treatment led to poorer machinability compared to cast iron inserts, we found significant improvements in machinability when adding a new machining additive to the Cr-Mo prealloyed powder from Höganäs AB, and the use of a minimal steam treatment process.
The resulting sintered inserts have slightly lower tensile strength, fatigue strength, and elastic modulus compared to the existing cast iron, raising concerns regarding oil leaks and engine durability. However, the simplified near-net shape compaction process for complex shapes
Fig. 5 Two views of the PM bedplate insert (Courtesy Hyundai Motor/Korea Sintered Metal/Höganäs Korea)
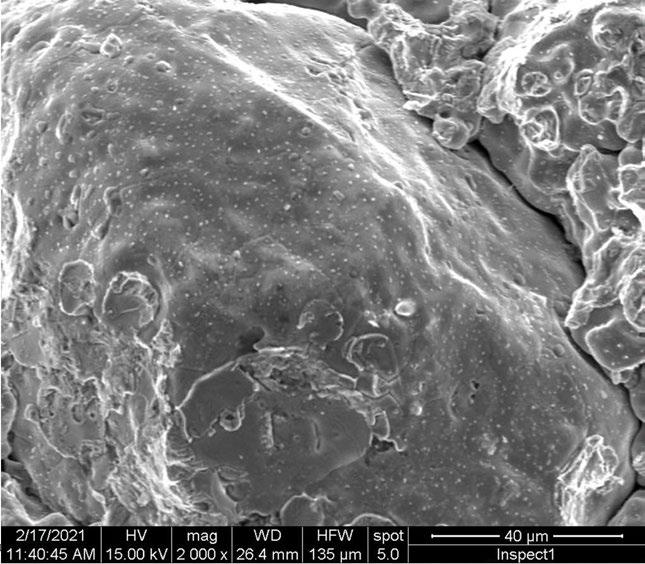
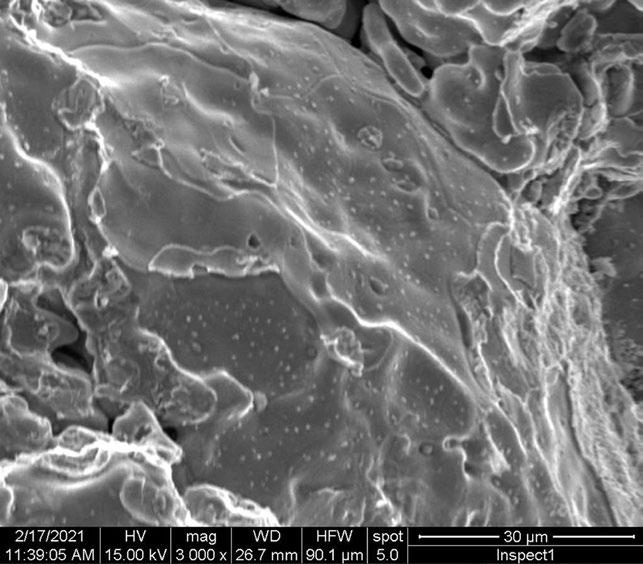
reduced total cost compared to existing manufacturing methods. Durability was verified through rig tests and engine durability tests, and PM pressed and sintered inserts are expected to be mass-produced for two engine models in 2026 and 2027. This application was recognised with an award in the Engine category at the Hyundai Motor R&D Academic Conference.
“Durability was verified through rig tests and engine durability tests, and PM pressed and sintered inserts are expected to be massproduced for two engine models in 2026 and 2027.”
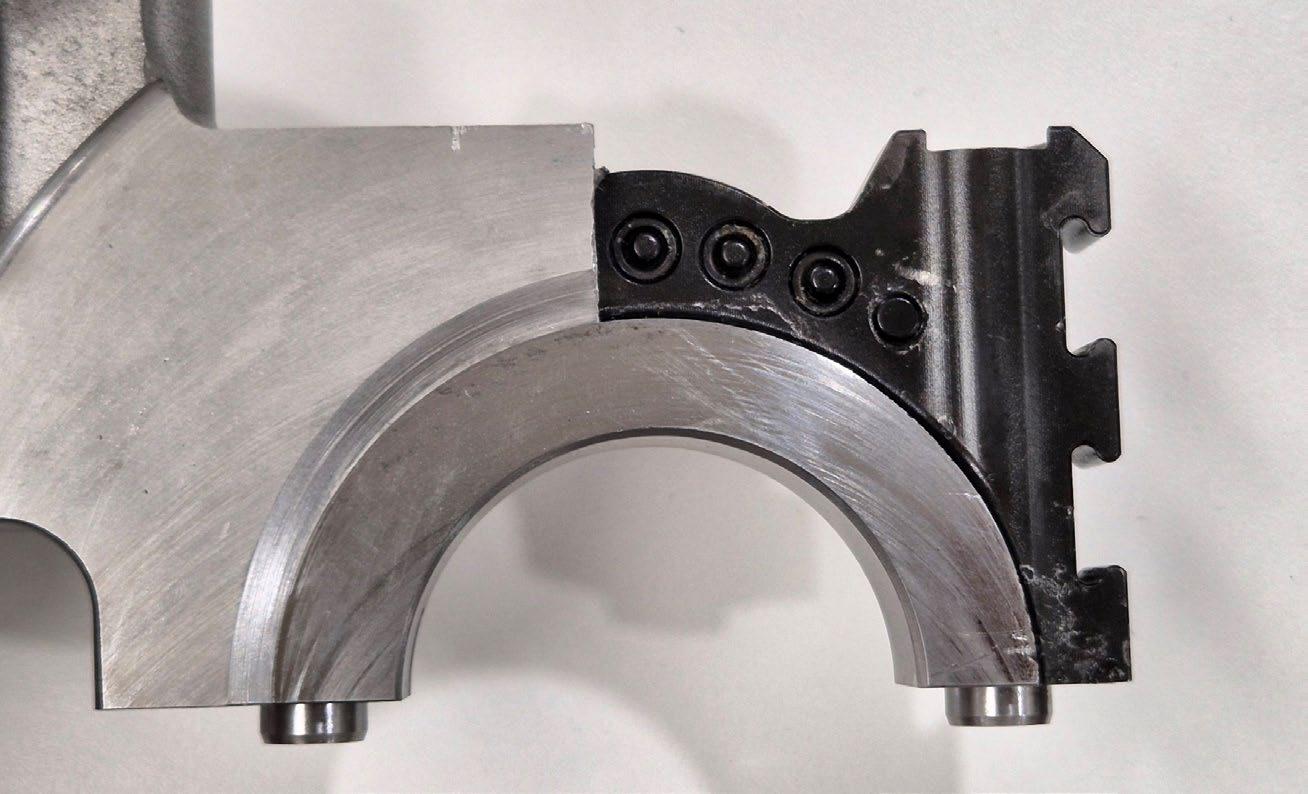

Fig. 6 SEM images showing Cu precipitation (Courtesy Hyundai Motor/Korea Sintered Metal/Höganäs Korea)
Fig. 7 Cutaway section showing PM parts in-situ (Courtesy Hyundai Motor/Korea Sintered Metal/Höganäs Korea)
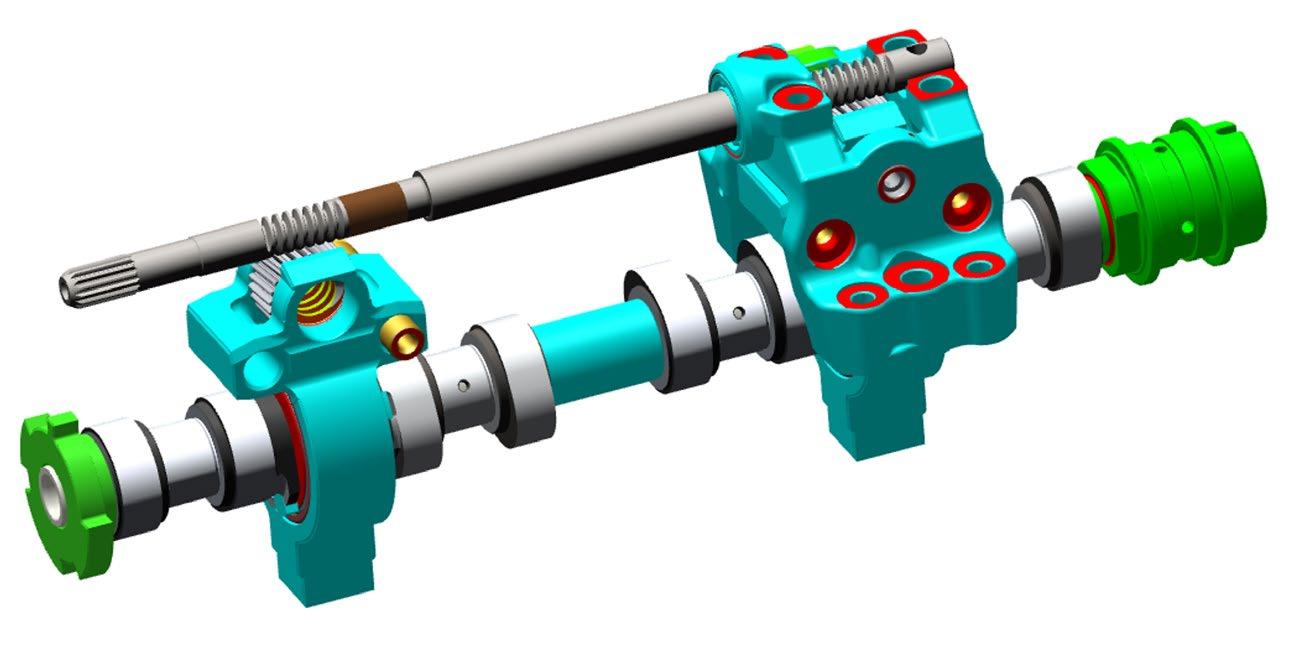

Continuous Variable Valve Duration (CVVD) lifthousing
CVVD technology, which was first applied to Hyundai’s G1.6 T-GDI, launched in 2019, changes the duration of the opening of valves depending on the driving conditions, leading to improved engine performance and fuel efficiency. As the lift housing has a complicated structure resulting in high part cost when produced by precision casting, we focused on the cost reduction potential using the powder pressing, green machining and sintering process.
“As the lift housing has a complicated structure resulting in high part cost when produced by precision casting, we focused on the cost reduction potential using the powder pressing, green machining and sintering process.”
The material used for the current cast part is a 42CrMo4 steel. Since there was a stick-slip wear mechanism in the inner shaft for a 35 mm hole in the parts, we applied gas nitrocarburising to this steel to achieve HV 600 surface hardness. However, FL5208 – the standard commercial sintered material based on fully prealloyed steel powder containing 1.5%Cr and 0.2%Mo – did not reach HV 500. Because nitrocarburising of the sintered FL5208 material forms brittle nitrides near pores in the inner portion of the sintered parts, we proceeded to implement plasma nitriding. Plasma-nitriding materials
Fig. 8 CAD images of the Continuous Variable Valve Duration (CVVD) mechansim (top) and the PM CCVD lift housing component (Courtesy Hyundai Motor/Korea Sintered Metal/Höganäs Korea)
with high amounts of alloy additions increases surface hardness. However, it was difficult to use high alloy PM materials due to their poor machinability.
To address this, we conducted further plasma nitriding on microstructures including martensite, bainite, and pearlite based on FL5208 and compared the surface hardness. The results show that the pearlite structure had low hardness, as expected. The martensite structure was tempered when exposed to the plasma nitriding temperature of about 600°C and showed a similar hardness to the pearlite structure. Only the bainitic structure showed a relatively high hardness after plasma nitriding. FL5208 mostly consists of a bainite structure, when carbon content and cooling rate are controlled, but it was difficult to prevent some pearlite from forming, thus constituting a quality issue. Consequently, the range of hardness specifications would have had to be wider than currently used, which was not acceptable to the manufacturer. However, following a suggestion from Höganäs AB supported by material data, we blended materials of different compositions and conducted measurements on test specimens to address this issue.
As a result, we found a composition that formed a stable bainite structure and achieved a surface hardness equivalent to 42CrMo4 steel from the test after plasma nitriding on actual PM parts. However, the diffusion depth was relatively low due to the impact of porosity in the sintered parts.
Even though the cost of the newly developed pre-bonded mixed powder is higher than that of FL5208 powder, we developed a customised powder mix that meets the target properties and allowed the compaction of a largesized component using a single pressing step. The limits of the press compaction step for green part formation were overcome through the use of green machining, resulting in extended tool life and
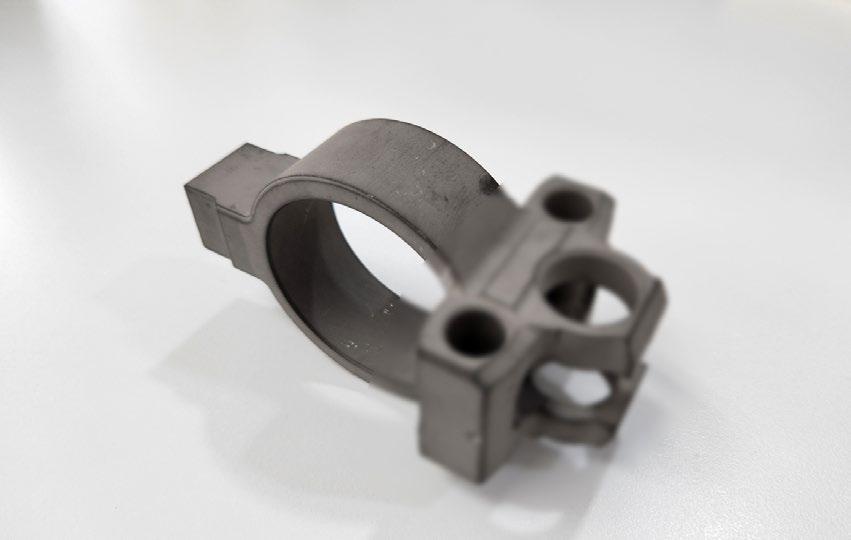
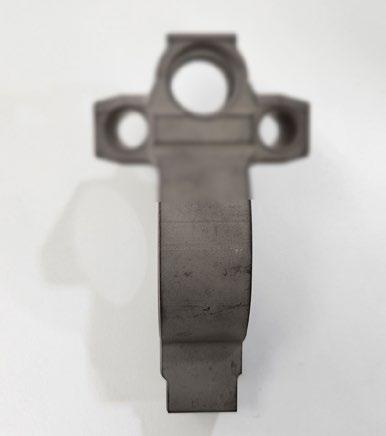
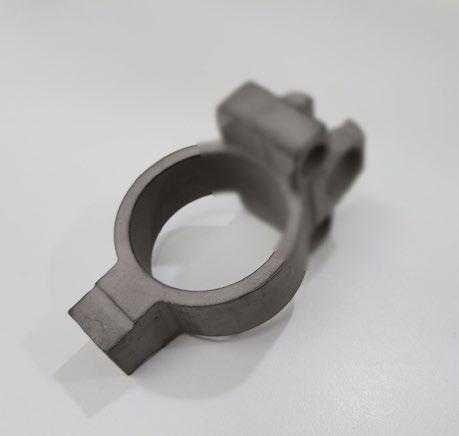

Fig. 9 Views of the PM CVVD lift housing (Courtesy Hyundai Motor/Korea Sintered Metal/Höganäs Korea)
Materials C Mo Cr Fe
Table 1 The customised material composition for the PM CCVD parts
Fig. 10 Diffusion layer hardness: PM vs casting (Courtesy Hyundai Motor/ Korea Sintered Metal/Höganäs Korea)
Diffusion layer hardness
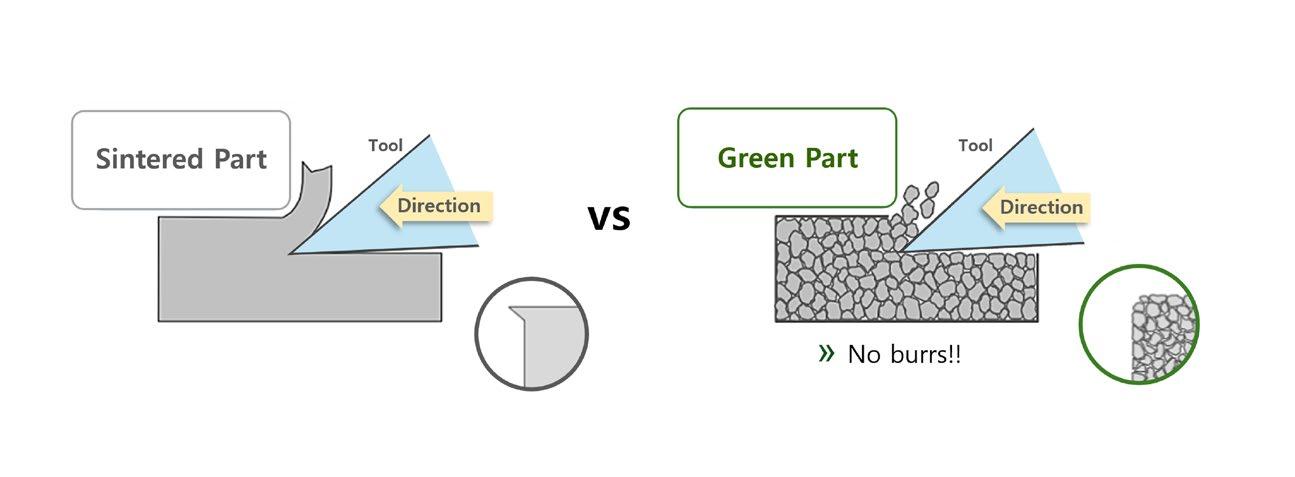
Fig. 11 Comparing conventional machining and green machining (Courtesy Hyundai Motor/Korea Sintered Metal/ Höganäs Korea)
“The limits of the press compaction step for green part formation were overcome through the use of green machining, resulting in extended tool life and improved productivity. Overall part cost reduction becomes possible by changing
from
precision casting to the PM process.”
improved productivity (Fig. 11). Overall part cost reduction becomes possible by changing from precision casting to the PM process.
This component is expected to enter mass production during the fourth quarter of 2024, after completing the final durability testing conducted as a part of the production release process.
The PM insert and lift housing components highlighted in this article will be displayed at the Höganäs AB booth during Euro PM 2024, which will take place from September 29 – October 2 in Malmö, Sweden, and World PM2024, taking place from October 13-17 in Yokohama, Japan.
Author and contacts
Kim Hak Soo
Senior Researcher
Electrification PE Materials Development Team Hyundai Motor Group echo@hyundai.com
Park Joo Sung
Deputy Manager Korea Sintered Metal h9600@hanmail.net www.iksm.co.kr
Kim Martin
PMT Manager Höganäs Korea martin.kim@hoganas.com www.hoganas.com
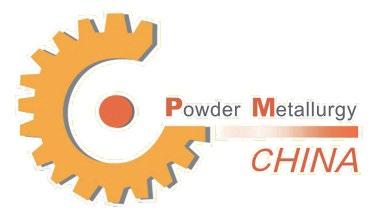


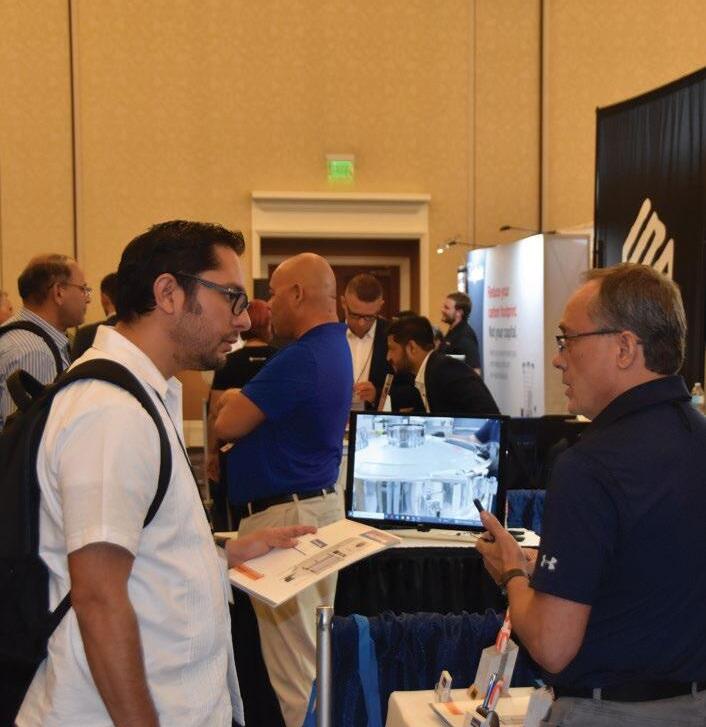
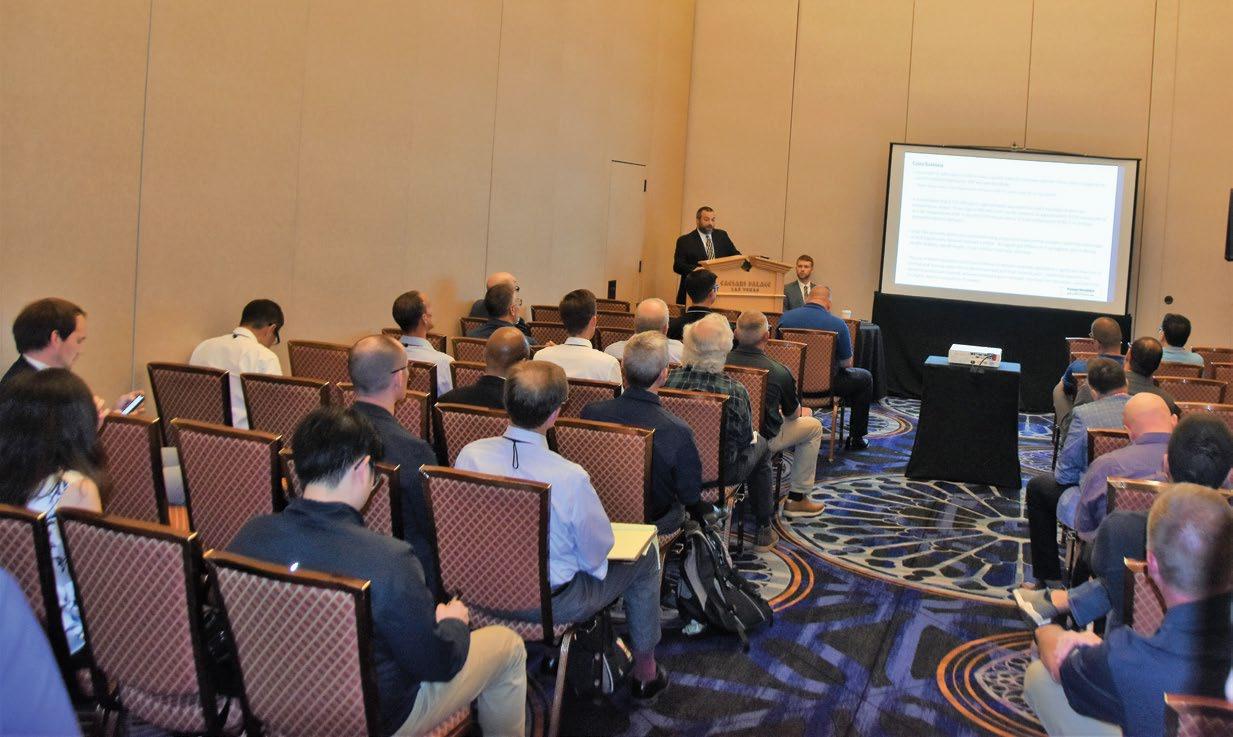
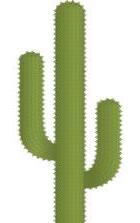
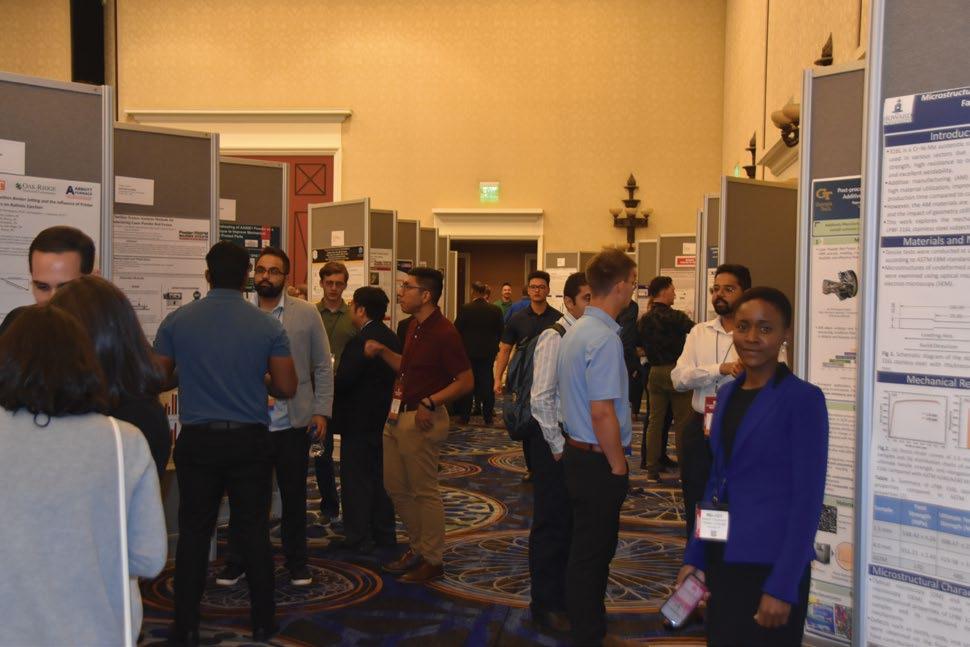
TRADE EXHIBIT


PowderMet2024 and AMPM2024 report: Cemented Carbides brought into focus in Pittsburgh
The fact that a high proportion of North America’s Powder Metallurgy structural parts and cemented carbide industries are located close to Pittsburgh, the host city for this year’s PowderMet2024 and AMPM2024 conferences, ensured a good turnout for the organiser, the Metal Powder Industries Federation (MPIF). In the following report, Bernard North shares his overall impressions of the event and reports in detail on a particularly well-attended Carbide Forum, in which developments in the $20 billion cemented carbide industry were presented by a very knowledgeable panel of presenters.
During the height of the COVID-19 pandemic, the Metal Powder Industries Federation (MPIF) cancelled its 2020 international annual conference. In 2021, the organisation held a hybrid conference in Orlando, Florida, USA, which was attended by about 500 delegates, 400 of them in-person; and about thirty companies exhibited at the trade show. Then, in 2022, the Portland, Oregon, event drew about 570 attendees, followed by about 700 attendees and seventy-five exhibitors at the Las Vegas, Nevada, event in 2023.
The 2024 event took place from June 16-19 at the David L Lawrence Convention Center, adjoining the Westin Hotel, in Pittsburgh, Pennsylvania, placing it within easy driving distance of not only a high proportion of Powder Metallurgy parts manufacturing, but also much of the cemented carbide industry. The author was hopeful that this location meant that turnout would be very high.
As usual, the PowderMet International Conference on Powder Metallurgy and AMPM (Additive Manufacturing with Powder Metallurgy) events were co-located, with a single registration and shared trade show, general session, meals
and receptions, although respective technical sessions were separately delineated. In addition, there were special interest programmes, a Carbide Forum with separate registration, tutorials, and student presentations.
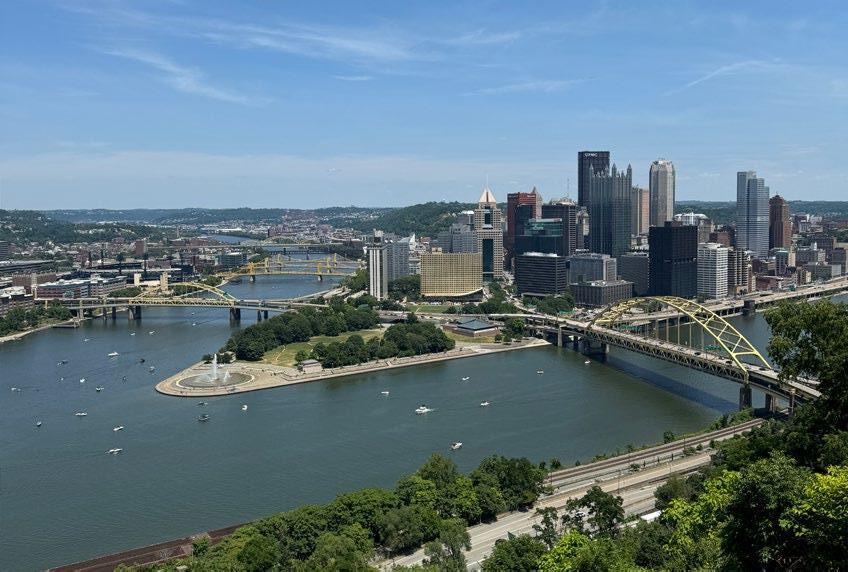
Fig. 1 The PowderMet2024 and AMPM2024 conferences were held in Pittsburgh, Pennsylvania

In the event’s plenary session
Jim Adams, Executive Director and CEO of MPIF, announced that attendance was nearing 900 participants from twenty-five countries, with about ninety exhibitors in the trade show. There were approximately 200 presentations including about fifty technical posters. In addition, graduate students in recipience of grants for working in Powder Metallurgy and related areas gave forty-one ten-minute summaries of their work. Three tutorials (Press and Sinter PM, Metal Additive Manufacturing, and Metal Injection Moulding) – each given by an industry expert and comprising three seventy-five-minute sessions – were also included.
Adams acknowledged the hard work of over 140 volunteers who worked with MPIF staff to organise the presentations into appropriate technical sessions and chair them. He also recognised the technology programme chairs of PowderMet2024 (Wiley Abner of MPP and Mark Saline of Gasbarre Thermal Processing Systems) and AMPM2024 (Raj Kelkar of GE Aerospace and Jerome Stanley of Höganäs).
Damon West’s keynote presentation
MPIF continued its recent practice of bringing in a motivational speaker to give the keynote talk. This year, the attendees heard an inspiring presentation by Damon West, co-author of the best-selling book How to be a Coffee Bean . Jim Adams noted that West was chosen in response to the ‘down’ mood at 2023’s events.
In his talk, West described how an addiction to hard drugs led him to commit burglaries to finance the habit. This was followed by arrest, trial, and a very long prison sentence in an especially tough Texas state prison. Through great strength of will, he did not let the experience destroy him and was
APMI International President Rob Hayes of Phoenix Sintered Metals discussed the benefits of the PMT Certification Program and announced that Deepak Madan of Danik Innovations was the recipient of the 2024 Fellow Award, recognising his decades of significant contributions to the PM industry. MPIF Awards Committee Chair Michael Lutheran of Kymera International had the pleasant task of introducing Tom Murphy of Hoeganaes Corporation as the fifth-ever recipient of the Kempton H Roll PM Lifetime Achievement Award, honouring a lifetime of contributions to Powder Metallurgy, with a strong specialisation in metallographic preparation and analysis.
The State of the North American PM Industry
The State of the North American PM Industry summary was presented by MPIF President Michael Stucky of Norwood Medical. It is published in its entirety in this issue of PM Review , but, in brief, he compared 2023 tonnages of the most commer -
paroled unusually early for both good behaviour and his positive impact on his fellow inmates.
Likening tough experiences to being in a pot of boiling water, he stressed the need to avoid being like a carrot (soft) or an egg (hard, especially on the outside)
cially significant metal powders with that of 2022, with the overall picture being one of very slight (~1%) decline for the biggest category (ferrous powders) and stable production volumes for nickel. A mixed picture was presented for other metals: ~10% up for aluminium and molybdenum, but ~10% down for copper-based materials and stainless steel; and larger declines were seen for tungsten and tungsten carbide.
In MIM and AM, parts production increased, but powder purchases declined in 2023 as excess inventory was depleted. The automotive industry continues to account for at least 70% of North American PM tonnage, with ~15.5 million cars and light trucks sold in 2023 (2024 is expected to be at a similar level). The overall weighted average of 15.6 kg (~35 lbs) PM parts per vehicle has remained constant.
Stucky mentioned the now very clear trend in the North American automotive market of rapid growth of hybrids and much slower growth than earlier expected for full battery electric vehicles, and how this represents new opportunities – albeit with
but rather like a coffee bean: changing the environment around you to something good. His point was that if he could survive and thrive in such an extreme environment, then we can all do well in tough situations, and he outlined five key principles to succeed.
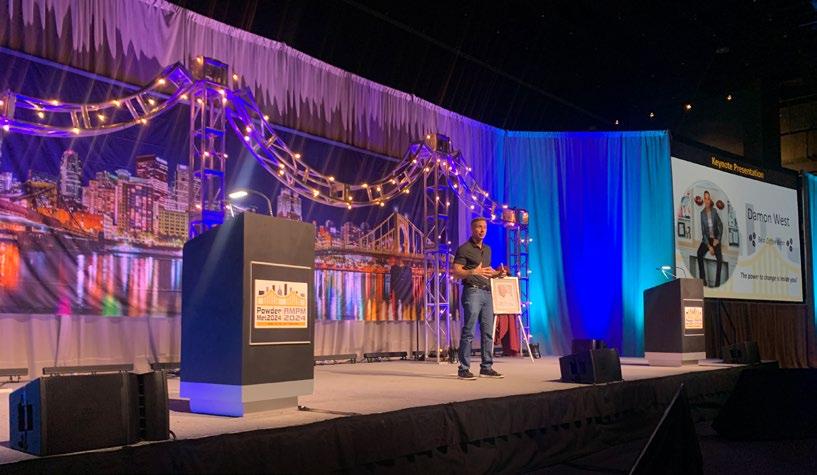
Damon West speaking at PowderMet 2024 (Courtesy MPIF)

PowderMet: Developments in cemented carbides
The PowderMet exhibition: sector analysis
Table 1 gives a breakdown (somewhat simplified, as some companies provide more than one product or service type) of the organisations exhibiting at the
TYPE OF SERVICE
Powders and lubricants
Powder processing equipment
MIM feedstock
Powder Presses
Die tooling
Materials/process analysis
Furnaces
Furnace components and accessories
Metal AM technology
Industrial gases
Hot Isostatic Pressing
Post-sinter processing
Cemented carbide powders and components
event. The author counted eightysix contributors to the trade show and, looking at the list of organisations exhibiting, a very full range of products and services in the Powder
Metallurgy value chain was present. As is common at these trade shows, the target customers were primarily PM parts manufacturers and the PM development community.
COMPANIES
Ametek Specialty Metal Products | Asbury Carbons | Globus Metal
Powders | Hoeganaes Corp. | Kymera International | Makin Metal
Powders | North American Höganäs | Novamet/Ultra Fine Specialty Products | Rio Tinto Metal Powders | AMG Graphite | H.L. Blachford | Jiangxi Yuean Advanced Materials | Metal Powder Works | Valimet
Elcan Industries | Herding Filtration | M.O. Industries
Ryer Inc. | Advanced Metalworking Practices
Dorst America | Gasbarre Press and Automation | Osterwalder | SACMI IMOLA S.C. | Cincinnati Inc. | Yangzhou Haili Precision
Machinery Manufacturing
GFMS System 3R | Bronson and Bratton | Chung Yi Mold (Suzhou) | Da Chen Mold Co. | Guandong Cincy Intelligent Equipment
LECO Corporation | The Modal Shop, Inc. | Advanced Materials Solutions | Foerster Instruments | Granutools | Mercury Scientific
Abbott Furnace | ALD Vacuum Technologies | Centorr Vacuum Industries | CM Furnaces | Elnik Systems | Consarc Corp. | Harper International | MUT Advanced Heating | Retech Systems | Thermcraft
Alloy Engineering | Orton Ceramic Foundation | Bandas Metallicas Codina, S.L. | Blasch | GeoCorp, Inc. | PLANSEE USA | Zircoa
Amazemet | Exentis North America | Nano Dimension US | SPEE3D
Airgas | Messer North America | Air Products and Chemicals | NEL Hydrogen
American Isostatic Presses | Bodycote IMT Inc.
Abtex | NLB Corp. | Allegheny Coatings | Bluewater Thermal Solutions | Forge Nano | Godfrey and Wing | Lap-Tech Industries | Precision Finishing
Global Tungsten and Powders | Hyperion Materials and Technologies | Penn United Technologies | Tungco | Wolfram Bergbau und Hütten
Automation and materials handling Erowa Systems | Hans Weber Maschinen Technik
Universities
Contract R&D
Consulting
Technical publishing
Government
Ames National Laboratory (Iowa State University) | Penn State University DuBois | University of Utah
Veloxint (Touchstone Laboratories)
DSH | Transformative Sales Systems
Inovar Communications
Cybersecurity and Infrastructure Security Agency | North Central Pressed Materials Strategy Development Consortium
Table 1 A breakdown of the organisations exhibiting at PowderMet2024
“Reflecting the metrics quoted in the plenary session, the general mood amongst the attendees was one of guarded optimism and relief that business was, at least, generally flat and not in steep decline. Some attendees, however, noted that business volumes were ‘very uneven’...”
a less urgent timescale than previously thought – for the PM industry to find new applications both in the automotive market and elsewhere. MPIF is working on standards in various materials to encourage their adoption.
Overall, the expectation for 2024 is for slow growth in the 0-5% range but accelerating in 2025, with Stucky emphasising that the PM industry needs to continue to invest in people and new developments to ensure a bright future.
Reflecting the metrics quoted in the plenary session, the general mood amongst the attendees was
one of guarded optimism and relief that business was, at least, generally flat and not in steep decline. Some attendees, however, noted that business volumes were ‘very uneven’, with some PM parts manufacturers doing very well but others still experiencing low production levels. Equipment suppliers indicated that most of their sales were outside the PM industry, which is still generally slow to invest in new equipment, with some manufacturers even delaying service or planned upgrades as they waited to see when business would improve.
Technical sessions overview
The technical focus (as determined from the abstracts) of the presentations and posters is summarised in Table 2, organised both by the materials type and the predominant process under consideration. A very broad range of materials and processes were covered, with multiple papers/posters in all areas except for MIM, which recently had its own MPIF event which included sinter-based metal AM in Raleigh, North Carolina [1], so it was a very technically comprehensive conference with something for everyone.
A little over half of the papers and posters were on metal AM, and there were numerous papers on conventional press and sinter, Hot Isostatic Pressing, powder atomisation or granulation, and polymer-bonded soft magnetic composites. By material type, the largest categories – in line with their production volumes – were ferrous and stainless steels, but, largely due to the Carbide Forum, cemented carbides were well-represented, as were nickelbased alloys, refractory metals, and titanium. There were also several
Table 2 Classification of presentations and posters by material and process
contributions in hard magnetic materials, aluminium, and copper.
Any given individual cannot ‘do justice’ to all the contributions in a review; in this article, the author concentrates on the several cemented carbide presentations anchored by the Carbide Forum, while the winter issue of PM Review will include a summary of the papers on PM developments driven largely by vehicle electrification.
Carbide Forum
The cemented carbide industry is a critical and commercially significant portion of Powder Metallurgy that shares many similarities in processing (albeit with major detail differences) with metallic PM. Cemented carbides, however, have a distinct range of applications compared to metallic PM parts, with the largest portion of applications being consumables for machining, cutting, or crushing of metals, wood, composites, coal, rocks, asphalt and concrete.
Usually, cemented carbides form a fairly small portion of MPIF activities, but with the 2024 conference being in Pittsburgh, which has the largest concentration of cemented carbide production companies in the Americas, the Refractory Metal Association saw an opportunity to highlight the industry and encourage a high level of participation, organising four Special Interest Sessions of three presentations each (twelve in total) covering a range of relevant subjects. Another four presentations in the field were given in ‘regular’ technical sessions.
A special limited-access registration category was created, and both this author and industry colleagues were eager to see how well the initiative worked. The event was very successful – MPIF staff informed the author that sixty-seven people checked into the opening three talks, which is a sizeable audience for a non-plenary session, and the numbers held up well throughout the forum.
PowderMet: Developments in cemented carbides
Cemented carbides: combining wear resistance with toughness – and more
• High hardness HVN30 (900-2200 kg/mm2)
• High fracture surface energy © and toughness K1c (7-25 MPa/m2)
• High Young’s Modulus E (430-690 GPa)
• Very low thermal expansion coefficient @ (4.8-6.0 x 10-6/K)
• Ability to minimise critical flaw sizes c to a few um or less
• High thermal conductivity k (70-150 W/mK)
• Deformation-resistant binder metals
3 High wear resistance
3 Very high strength E© / πc (Griffith flaw theory) (compressive 3-9 GPa)
3 High temperature capabilities
3 High thermal fatigue resistance K1c k / E@
Fig. 2 Typical range of properties for cemented carbides (Data from Hyperion website and K J A Brookes’ ‘Hardmetals and Hard Materials’)
“Usually, cemented carbides form a fairly small portion of MPIF activities, but with the 2024 conference being in Pittsburgh, which has the largest concentration of cemented carbide production companies in the Americas, the Refractory Metal Association saw an opportunity to highlight the industry...”
Cemented Carbides: overview
Bernard North (North Technical Management, LLC) opened the Carbide Forum with an overview [2] summarising the key properties of cemented carbides (combining toughness with hardness and thermal fatigue resistance), flexibility (trading properties with grain size, binder level and composition variation), ease of processing, scaling, prototyping, and recycling, ability to bond to other engineering materials, ability to form Functional Gradient
Materials (FGMs) and its common ‘gating’ role in determining the productivity of metal, wood, rock, coal, asphalt, concrete etc. cutting ‘systems’ (Fig. 2). This unique combination of technical and economic attributes has enabled the global industry to grow to ~$20 billion, employing ~100,000 people directly, with millions of people directly using the product and most of the world’s population being impacted indirectly. The greatest threat to the industry is commoditisation through the fact that most of the critical inventions are now decades old, and companies

Plastifier
PVA (polyvinyl alcohol), separate vacuum drying and granulation processes, and spray drying (which combines drying and granulation into 3 Grade Powder Preparation
Kneading
Plastified
must innovate both technically and in their business models and practices to compensate. Possible game changers for the industry include the use of tungsten niobium oxide as an anode in lithium batteries; first wall materials in nuclear fusion reactors, which is still a very uncertain tech nology, but one receiving substantial private and government funding; and (already scaling rapidly), drilling and hydraulic fracturing of hard rock for deep geothermal wells.
Side Action Tool Designs
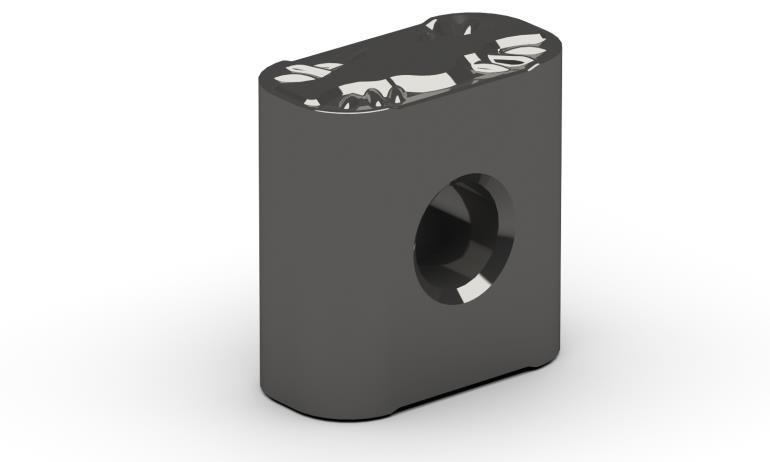
Cemented Carbides: processing
Grade powder production
Side Action Tool Designs
Courtesy Dorst Technologies
Courtesy Dorst Technologies
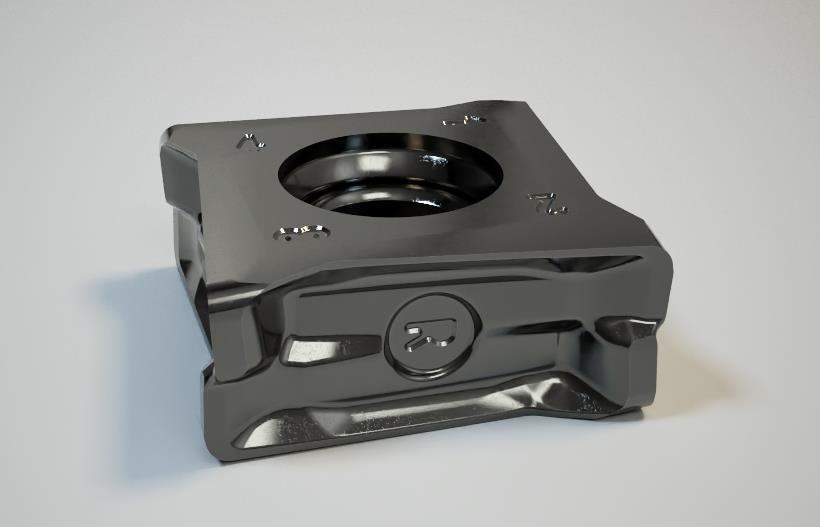
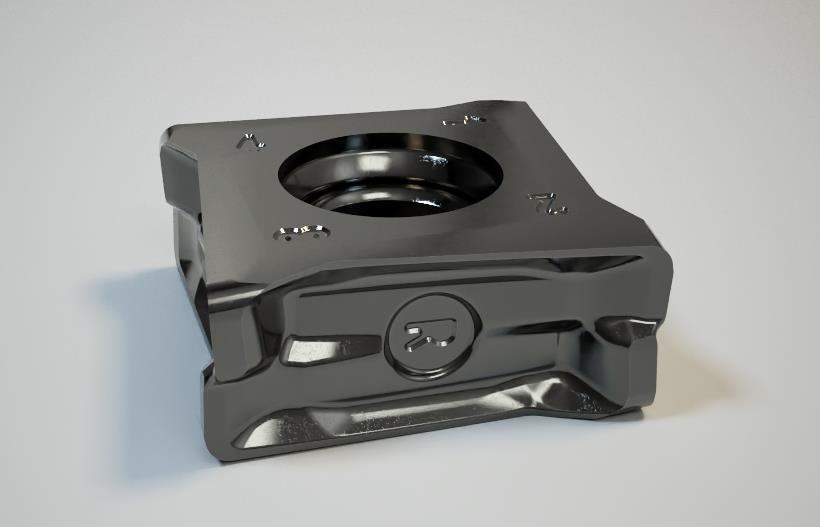
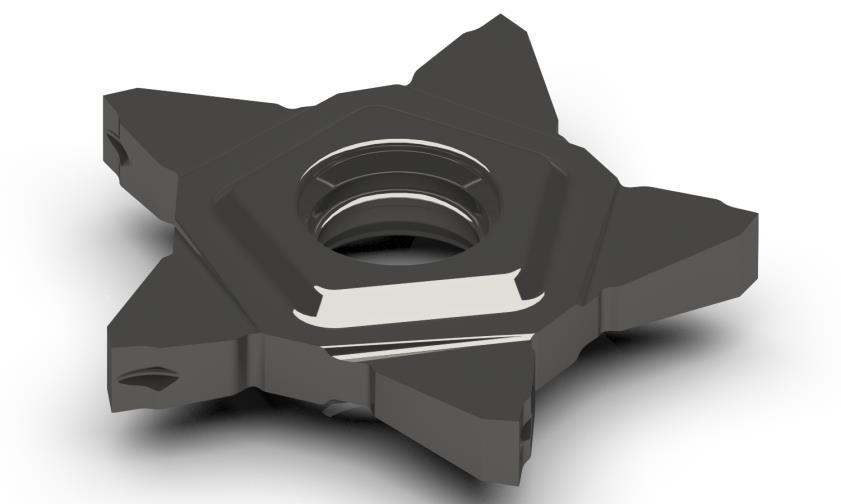
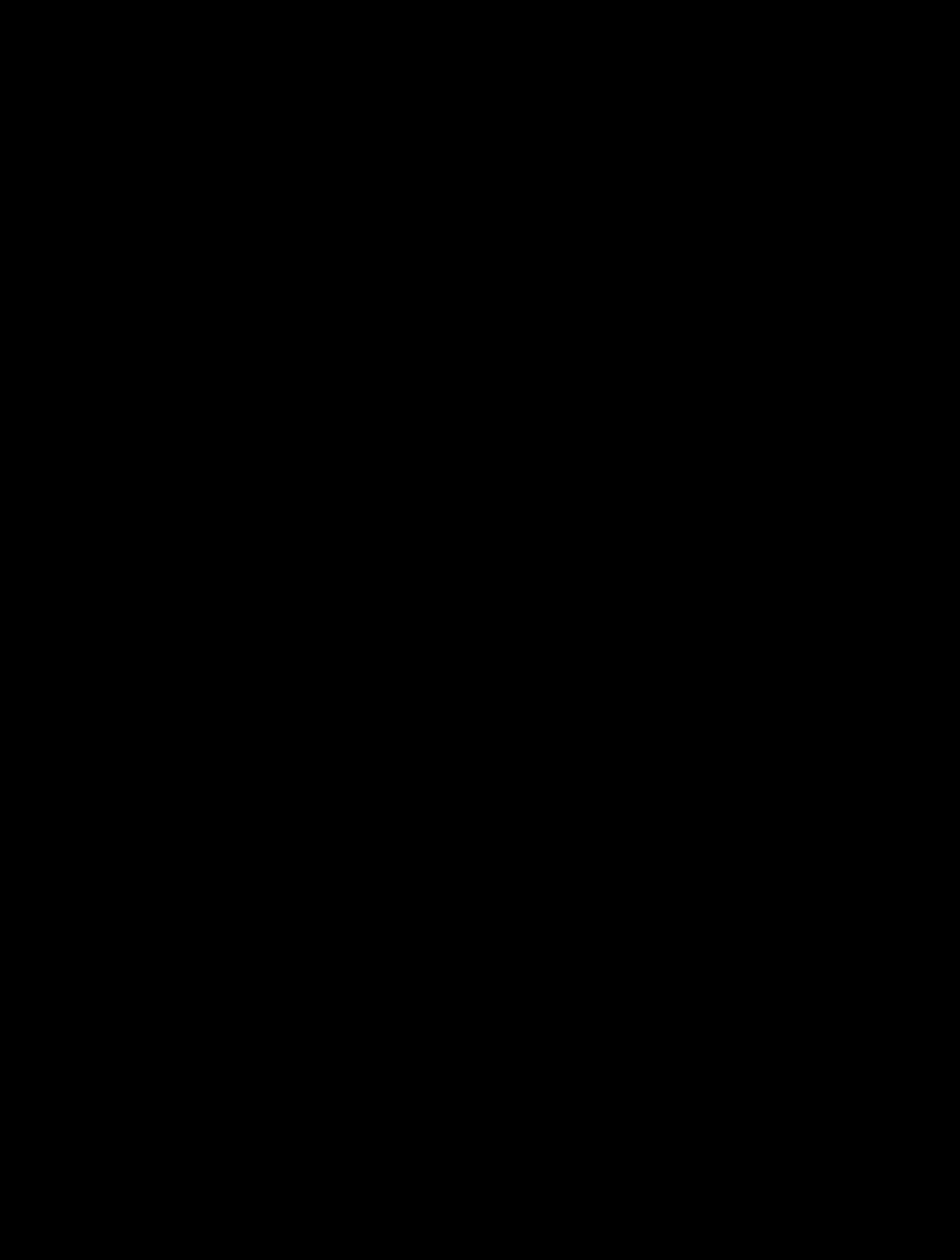
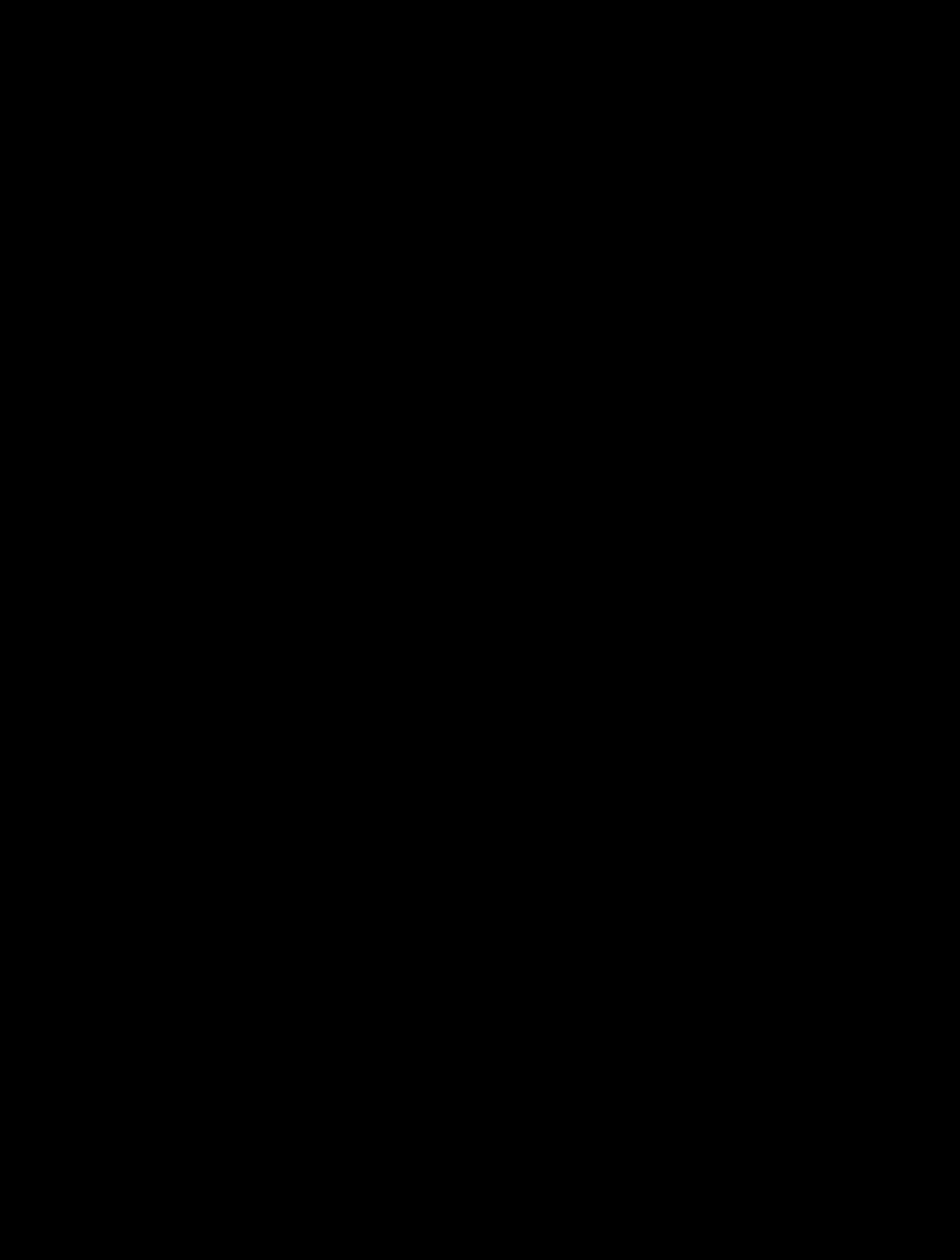
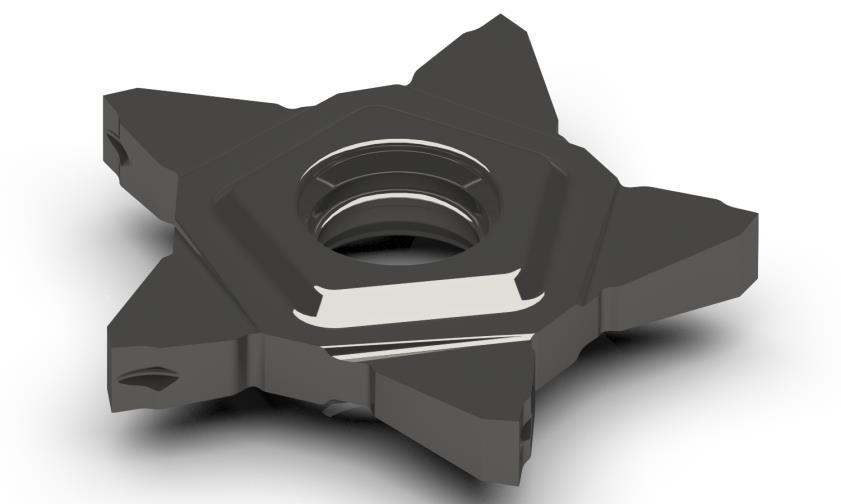
Fig. 3 Overview of cemented carbide grade powder production (Courtesy GTP/MPIF)
Fig. 4 Complex metal-cutting insert geometries made by uniaxial pressing with side action tooling (Courtesy Kennametal/MPIF)
Graphite load box
Graphite heating elements
Graphite felt insulation
Steel Vacuum/HIP rated vessel, water cooled
Graphite construction produces a carbon potential and reducing atmosphere of CO/CO 2
Sintering trays and boats are typically made of graphite, painted with a parting agent to avoid carbon pickup into the parts
Green shaping
Neal Myers of Kennametal gave two presentations, the first a very comprehensive one on green shaping methods [4]. He discussed the trade-offs – in terms of powder flow on the one hand and green density and ease of porosity removal on the other – of a uniform vs mixed granule size distribution and optimising pressing pressure in uniaxial pressing to avoid cracks while minimising porosity. Also discussed were different die geometries for common carbide part geometries (e.g. negative and positive rake metal cutting inserts, mining and construction conical tools, and short rods) and the key relationship between the allowable width of pressing ‘flash’ on unground periphery inserts and their subsequent edge preparations.
Complex ‘side-pressing’ tooling to make innovative insert geometries was summarised (Fig. 4), as were the pros and cons of mechanical, CNC hydraulic, and CNC electric presses. Extrusion (commonly used for round tool blanks, often with coolant holes), injection moulding (for high volume, complex shapes), and both conventional and dry bag isostatic
PowderMet: Developments in cemented carbides
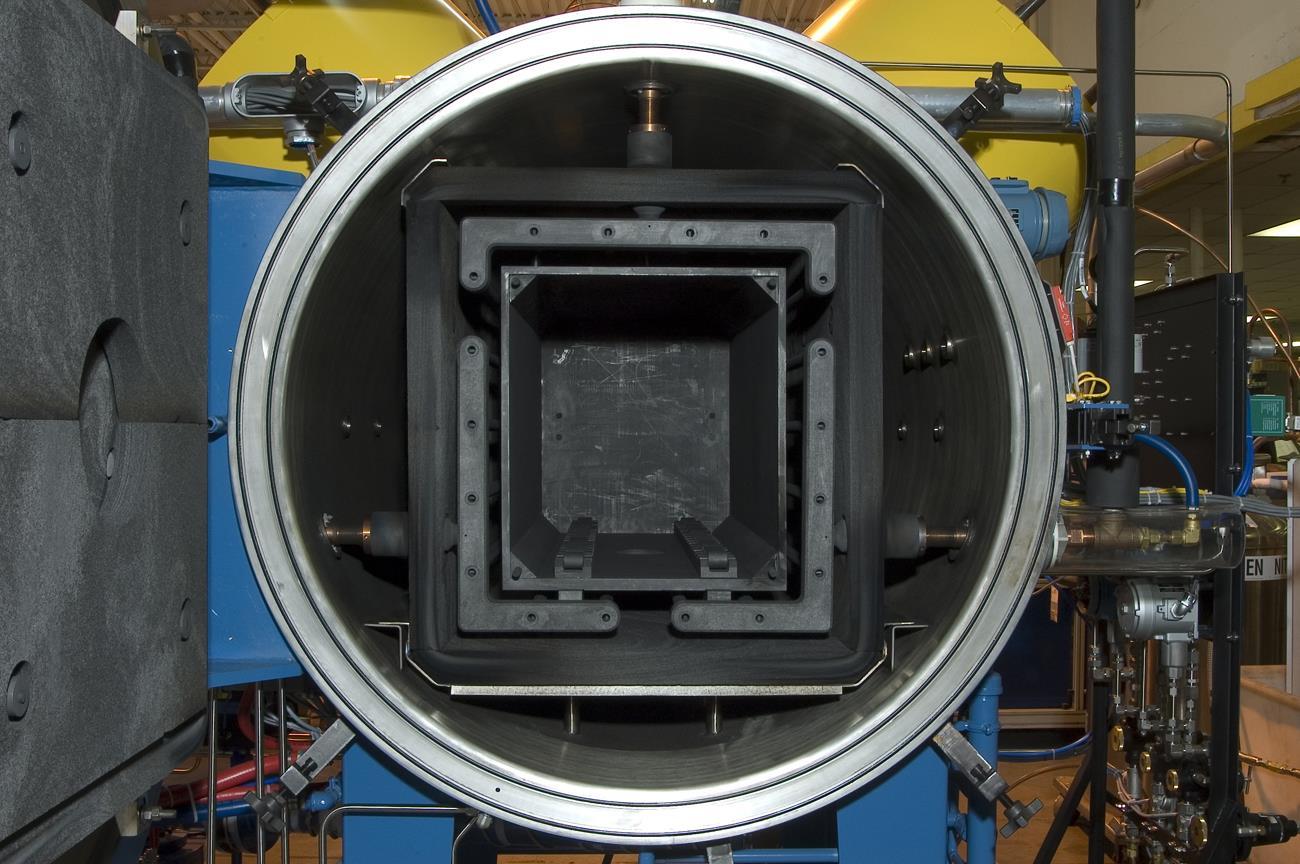
pressing, commonly followed by some green machining for low volume production or prototype parts, were also discussed.
Sintering cycle processes
Myers also gave a very detailed description of the processes occurring during a sintering cycle [5]. As temperatures increase, a succession of outgassing events take place:
1. Adsorbed water evaporation
2. Lubricant removal
3. Cobalt oxide reduction
4. Tungsten oxide reduction
5. Alloy carbide oxide surface layer reduction
These latter stages coincide with pre-sintering and solid-state sintering. After these, liquid-phase sintering to close to, or full, density occurs.
A simple vacuum may be used, but process gases are usually selected – at different stages of the cycle – to assist in heat transfer, lubricant removal, reduction of the less stable oxides, suppression of Co evaporation at full sintering temperature, and, in pressure sinter furnaces, ‘squeezing out’ any remanent porosity. Myers summarised the sintering refinements used to
create Co-rich surfaces which, when married to chemical vapour deposition (CVD) of hard coatings, are almost ubiquitous for steel turning grades.
Also discussed was the use of metals with lower melting points to coat steel surfaces with bonded WC grains. After summarising various undesirable microstructural features which can be minimised by good processing techniques and parameters, Myers concluded with a description of different sintering furnace design concepts (Fig. 5) as well as the less-commonly used Hot Isostatic Presses (HIPs), uniaxial hot presses, and spark plasma sintering.
Cemented Carbides: properties
Tom Jewett (GTP) also presented a detailed overview [6] on the critical properties of cemented carbides used in both product and process development and in production quality assurance: sintering shrinkage, density, hardness, fracture toughness, transverse rupture (TR) strength, wear resistance, and magnetic saturation and coercivity (which properties correlate directly to, respectively, the level of W or C

Fig. 5 Cemented carbide sintering furnace hot zone (Courtesy Centorr Vacuum Industries/MPIF)
solution in the Co binder, and to the WC grain size). All these property measurements are governed by ISO, ASTM, or MPIF standards, and Jewett referenced their respective numbers.
Tungsten manufacturing process
Robert Scott of HC Starck Tungsten gave a summary [7] of the manu -
facturing process for tungsten and tungsten carbide, including the wet chemistry and furnacing processes to get from low-grade scrap or Scheelite or Wolframite ore concentrates to WC powder. He went on to discuss the role of additives to WC-Co (different binder metals and carbides, in particular TiC, NbC, TaC,

6 Effect of acidity or alkalinity on corrosion susceptibility of different cemented carbides (Courtesy Hyperion Materials/MPIF)
VC, and Cr 3C 2) in affecting grain size and, in turn, toughness, hardness, corrosion resistance and other properties.
Material choice for corrosion
Madison Rase of Hyperion Materials & Technologies comprehensively overviewed [8] the variables influencing the choice of material for applications where corrosion is a significant factor. Acidic conditions lead to the corrosion of the binder metal, but this can be reduced by using a grade with less binder metal; using a lower magnetic saturation (i.e. more W dissolved in the binder) grade; partial or total replacement of Co by Ni, Cr, or Mo (Fig. 6); or coarser grain size.
In contrast, strong alkaline conditions cause corrosion of the WC phase. This, in turn, can be minimised with a finer grain size or by significantly replacing WC with other transition metal carbides.
In practice, the situation is often complicated by simultaneous wear and corrosion (tribo-corrosion), and by the need to consider the effect of grade design changes on key mechanical properties, so a very careful, holistic approach including (where possible) changing the nature of the environment is called for.
Cemented Carbides: alternative materials
Matching conventional carbide compositions
Johannes Pötschke, Fraunhofer IKTS Dresden, characterised [9] the success of the 1923 invention of cemented carbide as largely due to WC and Co being a ‘perfect match’ with good wetting during liquid phase sintering, no solubility of Co in WC, but significant solubility of W and C in Co.
Matching it is difficult, but attempts have been made for decades with considerable success in some areas (especially where corrosion resistance is a driver), and recently with greatly enhanced development activity due to the
Fig.
Fig. 7 Sources of primary cobalt by country of origin (Courtesy Fraunhofer IKTS/MPIF)
PowderMet: Developments in cemented carbides
Electron image 4
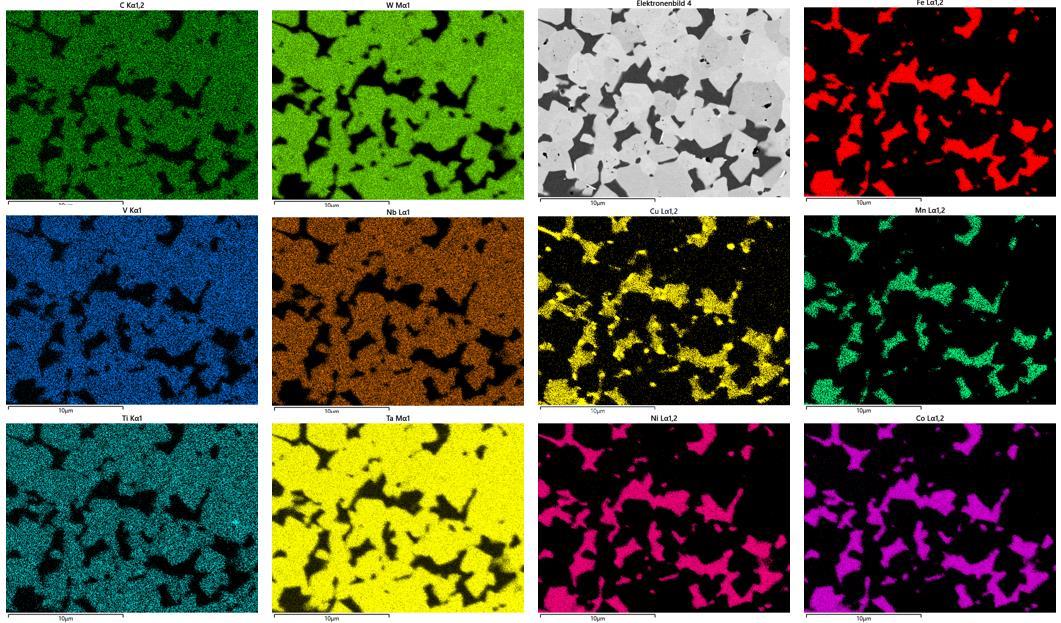
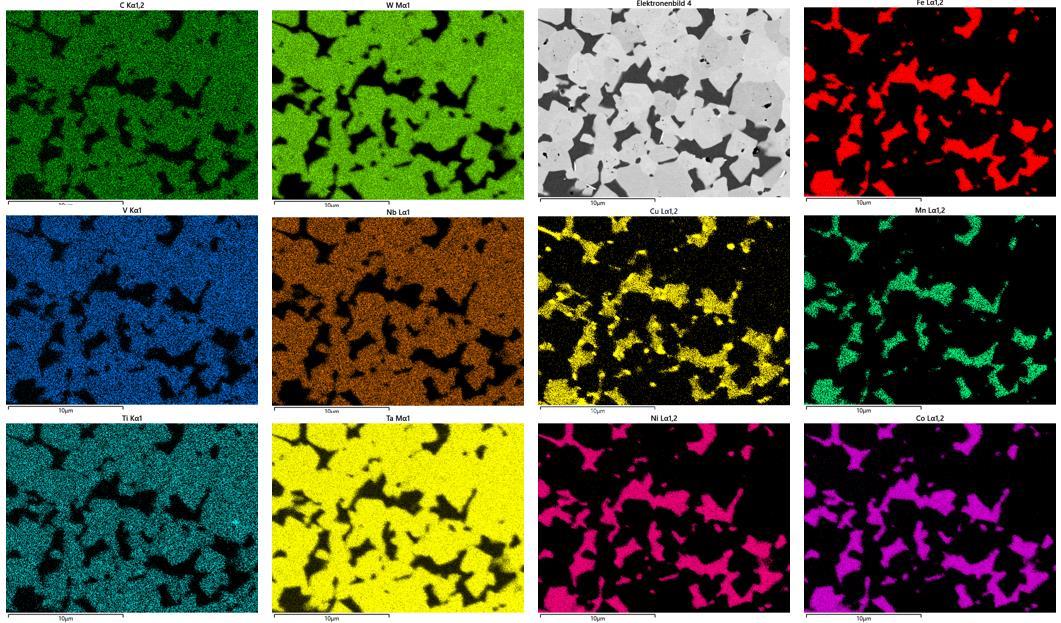
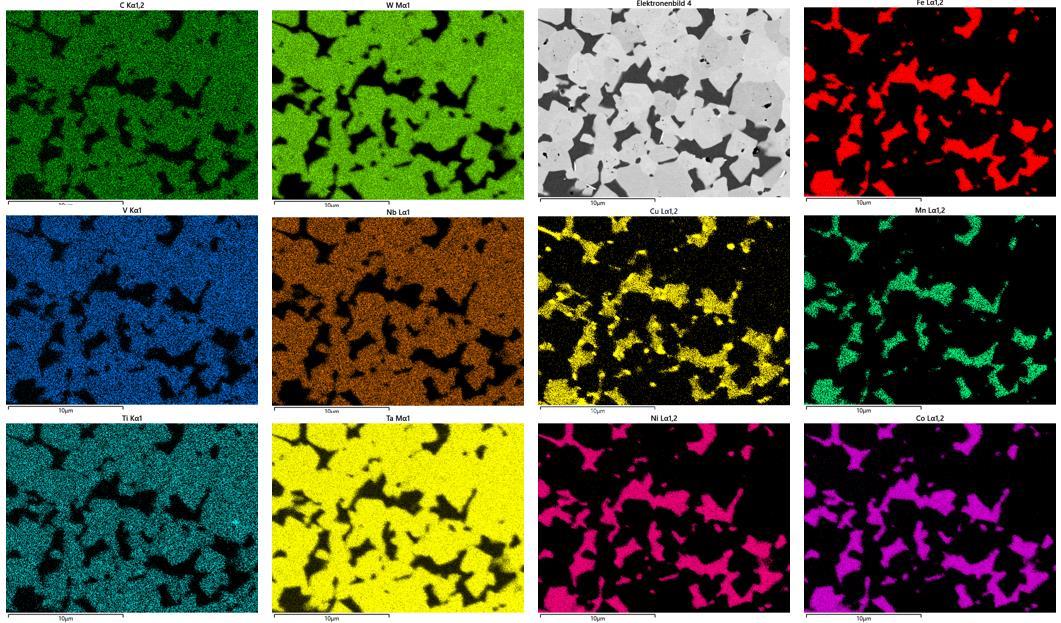
8 EDS mapping of a HEC-HEA sample with the composition: (TiVNbTaW)C-MnFeCoNiCu showing a two phase microstructure of a HEC hard phase and a HEA binder phase (plus small Cu precipitations) (Courtesy Fraunhofer IKTS/ MPIF)
increased demand for cobalt for batteries, its limited global supply and some EHS concerns. Sources of primary cobalt by country of origin are shown in Fig. 7.
The following summarises different actual or potential Co substitutes:
• Ni has a broad C solubility ‘window’ but produces low-hardness materials
• Fe has a very small C-window and poor corrosion resistance
• FeNiCo binder gives good corrosion and high-temperature properties.
• FeMn has a very narrow C window,
• Stainless steels (FeNiCr) have too much Cr for easy densification
• Precious metals Ru and Re stabilise the hexagonal close packed (HCP) phase which can have benefits, but are very expensive
• Strong carbide-forming elements such as Ti reduce toughness
• High-entropy binder alloys (five or more elements, chosen from twenty-one possible metals, in roughly equal proportions) show great promise, but at present it seems that ease of sintering is impacted, meaning Co will still be required, and recycling is complicated
High-entropy alloy binders
Pötschke, in a technical session outside the Carbide Forum, also presented work [10] where highentropy alloys were used for both the binder metal (HEA) and the hard carbide phase (HEC). Using conventional pressing and sintering methods, Pötschke demonstrated that a MnFeCoNiCu HEA binder formed uniform, homogeneous twophase microstructures with either WC or TiCN hard phases, as did a WTaNbVTiC hard phase with a Co or Ni binder.
Similar microstructures were seen when combining a HEC hard phase and a HEA binder metal alloy (Fig. 8). Promising hardness and toughness combinations versus conventional WC-Co controls were measured, with major scope for further property optimisation.
Cemented Carbides: Additive Manufacturing
AM techniques for cemented carbides
Zhuqing Wang of Kennametal overviewed [11] published work on different metal AM processes as applied to cemented carbides, illustrated by examples from several academic and industrial organisations. Beam-based methods – Laser and Electron Beam Powder Bed Fusion (PBF-LB and PBF-EB, respectively) and Directed Energy Deposition (DED) – generally result in inhomogeneous microstructures with discontinuous grain growth,

Fig.
Ti Ka1
V Ka1
C Ka1,2
Co La1,2
La1,2
La1,2
Ta Ma1
Nib La1
W Ma1
Ni La1,2
Cu La1,2
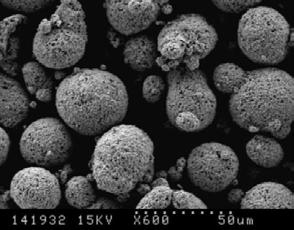
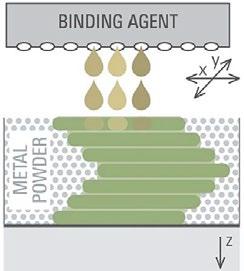

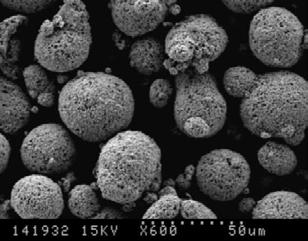
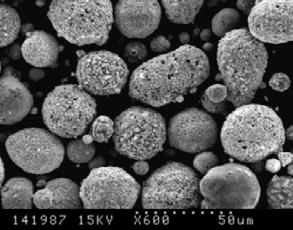
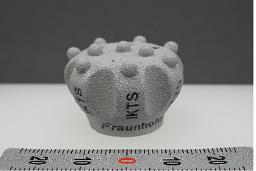
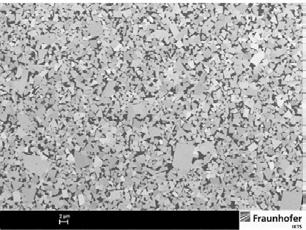
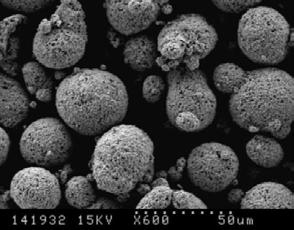
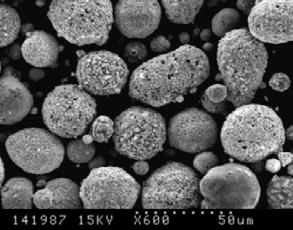
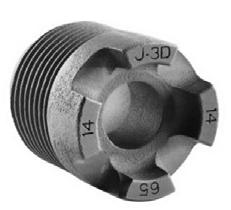
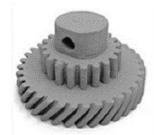
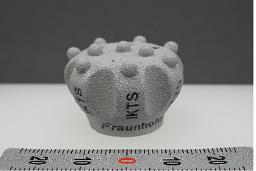
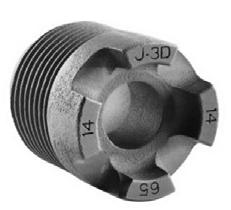
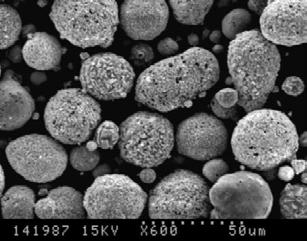
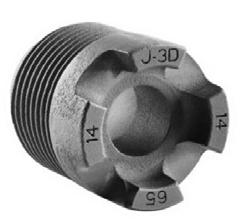
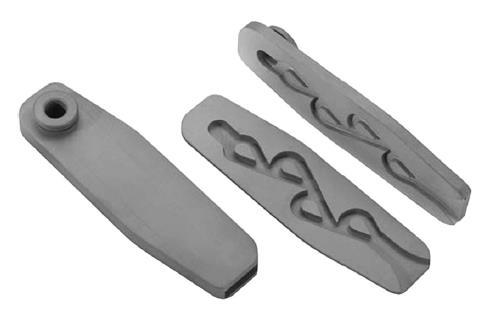
• Uniform microstructure and good material properties
• High productivity
• High MRL
• Relatively low resolution and rough surface x
• High equipment and powder feedstock cost x
unwanted phases, pores, cracks, and thermal stresses, although the more favourable (near vacuum) local environment and lower thermal gradient of PBF-EB show promise with coarse
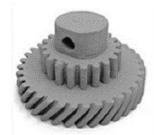
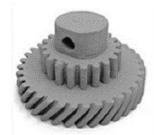
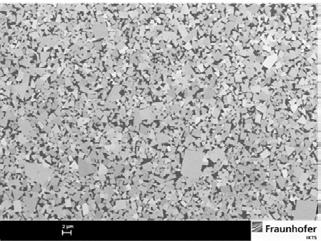
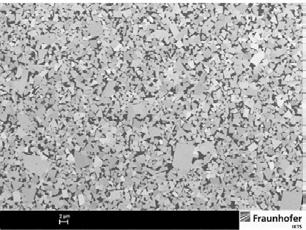
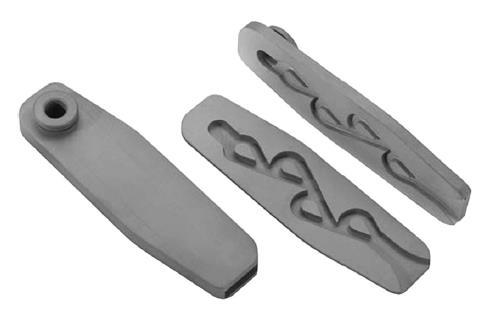
• Uniform microstructure and good material properties
• High productivity
• High MRL √
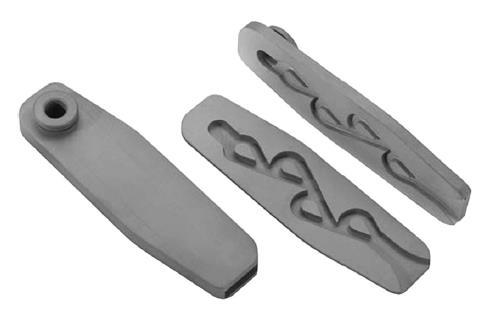
• Uniform microstructure and good material properties
• High productivity √
• Relatively low resolution and rough surface x
• High equipment and powder feedstock cost x
• High MRL √
• Relatively low resolution and rough surface x
• High equipment and powder feedstock cost x
grained, high metal content compositions.
By comparison, several sinterbased AM techniques can produce high-quality components, albeit with
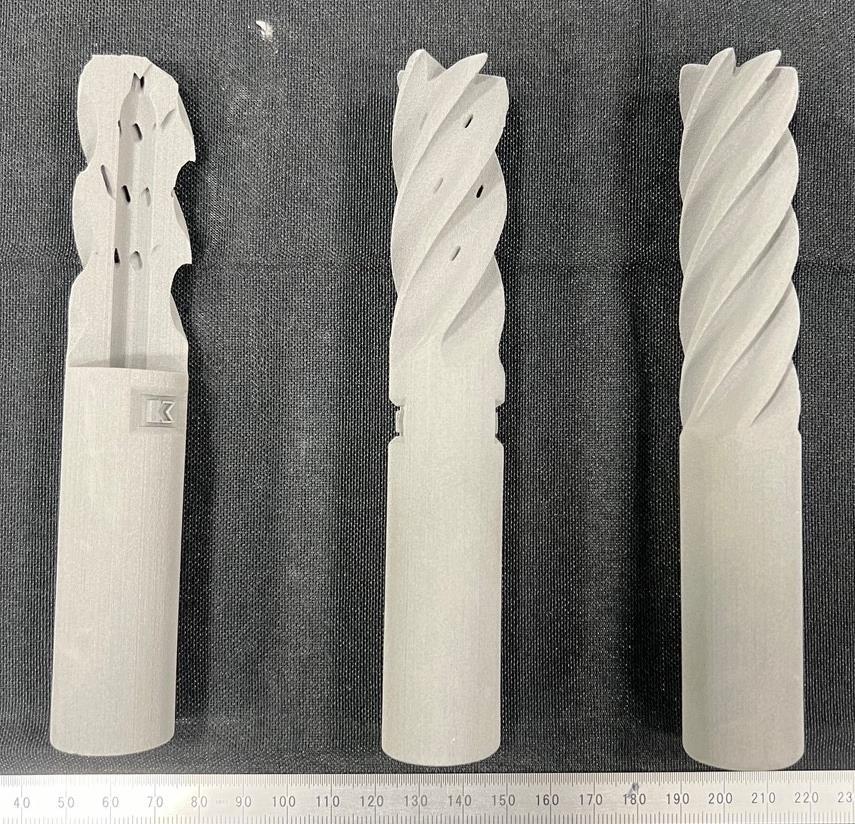
pros and cons depending on the technique. Binder Jetting (BJT) is the most advanced and already commercialised, using either granulated and pre-sintered or plasma-spheroidised powder that flows and spreads well in a BJT powder bed. This technology has a high production rate with a ‘fair’ surface finish, albeit with rather high equipment and feedstock costs (Fig. 9). Material Jetting techniques can give improved surface finishes and allow multi-material part fabrication but have low productivity. Material Extrusion (MEX)-based processes such as Fused Filament Fabrication (FFF) or slurry techniques produce good microstructures in a broad grade range. Equipment and materials costs are low, but the technology suffers from low productivity and stepped surfaces on components. Vat polymerisation shows some promise but is limited by the high optical reflectivity of WC powders.
Grade qualification
In a technical session on AM, Wang also described [12] Kennametal’s sequence of grade qualification via BJT. This began at a high Co, coarse grain grade, with an example
Fig. 9 Cemented carbide powder feedstock and representative parts made by Binder Jetting (Courtesy Kennametal/ MPIF)
Fig. 10 BJT solid carbide end mills with integral coolant holes produced at Kennametal (Courtesy Kennametal/MPIF)
Fraunhofer IKTS
Sandvik

PowderMet: Developments in cemented carbides
used for near net shape, optimised coolant delivery polycrystalline diamond (PCD) tools, through to a lower metal binder level medium grain size grade (that has been applied to the oil and gas industry, among others), to a 10% Co submicron grade (of a type almost ubiquitous for solid round metal cutting tooling applications, and which can also be applied to wear solutions in various industries).
The latter two show microstructures with slightly less homogeneity; this leads to marginally lower transverse rupture strength compared to conventionally manufactured controls, but performance is equivalent. Solid end mills made from the 10% Co submicron grade were lab metal cutting tested under aggressive loading conditions and performed similarly to conventionally manufactured controls. Wang showed images of whole and sectioned near-net shape end mills manufactured via BJT, including directed coolant delivery passages (Fig. 10) – an excellent example of the power of AM.
AM cemented carbides in various industries
Jerry Dominguez of Kennametal presented [13] several examples of AM cemented carbide components used in the mining, oil and gas, power generation, wastewater, and metal cutting industries, highlighting the benefits over the prior technology/materials used (Fig. 11). When replacing a metallic component, the main benefit was dramatically longer life with consequent reduction in maintenance needs and downtime, while when replacing cemented carbides made by traditional methods the benefits were typically shorter lead times (often replacing multiple process steps with a single one) and greater geometrical freedom for the components. In practice, parts range from about 6 mm up to 20 cm in lateral dimensions.
Dominguez also discussed the current challenges that constrain
Control Valve
• High temperature
• High Pressure
• Cavitation Erosion
• Safety - Noise Reduction
• Solids containing fluids
• Corrosion
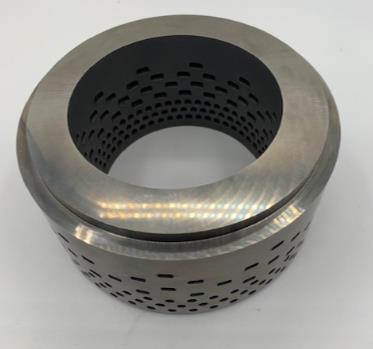

the growth of the technology: the currently limited (albeit growing) range of qualified grades, geometryspecific dimensional tolerances, customers having previous bad experiences with AM parts, and (a common factor in metal AM in general) the lack of industry standards which are important for increasing user comfort levels.
Bound Metal Deposition
Animesh Bose of Optimus Alloys described joint work [14] with GTP and Desktop Metals co-authors on the latter company’s Bound Metal Deposition (BMD) Additive Manufacturing technology – a form of FFF that uses rods of material rather
than filaments. BMD has much in common with MIM in terms of raw materials, the formation of a polymer-blended ‘extrusion’ mix, debinding, and sintering, but does not need tooling. However, it has a much rougher surface finish on components compared to MIM. Advantages include the ability to use a wide variety of grades employing standard raw materials and to make complex parts including internal closed cavities. A ceramic separation layer allows for easy separation from fixturing. Bose detailed the processing of a medium grain sized, WC-10 wt.% Co grade, including the 45-49 vol.% solids extrusion mix blending; the forma -
“...replacing cemented carbides made by traditional methods the benefits were typically shorter lead times (often replacing multiple process steps with a single one) and greater geometrical freedom for the components.”
Fig. 11 Binder jet-produced cemented carbide process control valve for oil and gas, waste water, or power generation industries (Courtesy Kennametal/ MPIF)
Increases in Tungsten Scrap will result in a decrease in usage of Tungsten Concentrates
*Some exceed these percentages in their current processes
Impact of consumer initiatives ~ most targeting >80% scrap consumption by 2030
tion of feedstock rods for the BMD unit; and extrusion through a 400 µ m nozzle to form AM green parts. After forming, they were solvent debound at 44°C prior to thermal debinding and either vacuum or pressure sintering to form high-quality parts. Sintering shrinkage was ~23% in the xy plane and ~25% in the z direction.
AM toolholders for carbide tooling
In the cemented carbide industry, the highest commercial value is in the field of metal cutting tooling. To date, there has been little or no use of Additive Manufacturing for producing consumable carbide tools themselves, but these tools can only function when mounted on
metallic toolholders. Zhuqing Wang (Kennametal), in one of the regular technical sessions devoted to metal AM, described PBF-LB production [15] of H13 and M300 steel toolholders, exemplified by one for machining aluminium stator bore housings.
In Wang’s example, AM allowed a 45% weight reduction versus a conventionally manufactured comparison, in turn allowing faster acceleration and deceleration in the machining process, thus halving cycle time. The technology also allows vibrational damping and the use of the fluidic oscillator mechanism to improve metal chipbreaking and removal.
“This precarious situation means that recycling scrapped components (e.g. used metal cutting tools) and in-process materials (grinding sludges, ‘loose’ grade powder, etc.) is critical, and is already at a creditable ~55% of total demand globally.”
Cemented Carbides: recycling
Amy Herron of Tungco began by summarising the situation with primary (mined) tungsten, the ores of which predominantly originate from China, with smaller amounts from Bolivia, Europe, and Africa [16]. While there are significant reserves in North America, there are no active mines (Fig. 12).
Tungsten is listed by the US Government as a Critical Material. Growth in global tungsten use since 2007 has averaged ~2.7% annually and is expected to continue at this level for at least the next decade. Current and potential new or re-opened mines are often physically remote and require major capital and long lead times to activate, which – combined with annual demand fluctuations and volatile pricing – generally discourages the commitment of major investments.
This precarious situation means that recycling scrapped components (e.g. used metal cutting tools) and in-process materials (grinding sludges, ‘loose’ grade powder, etc.) is critical, and is already at a creditable ~55% of total demand globally. This demand consists of mostly low-
The demand for tungsten units will likely outpace the supply
(Chemical) Feed ~ Current State 2024
Tungsten Scrap (Hard & Soft) Tungsten Concentrates
APT (Chemical) Feed ~ Future State 2030
Tungsten Scrap (Hard & Soft) Tungsten Concentrates Other (ST, etc)
Fig. 12 Current and forecast sources of ammonium paratungstate (APT) (Courtesy Tungco/MPIF)

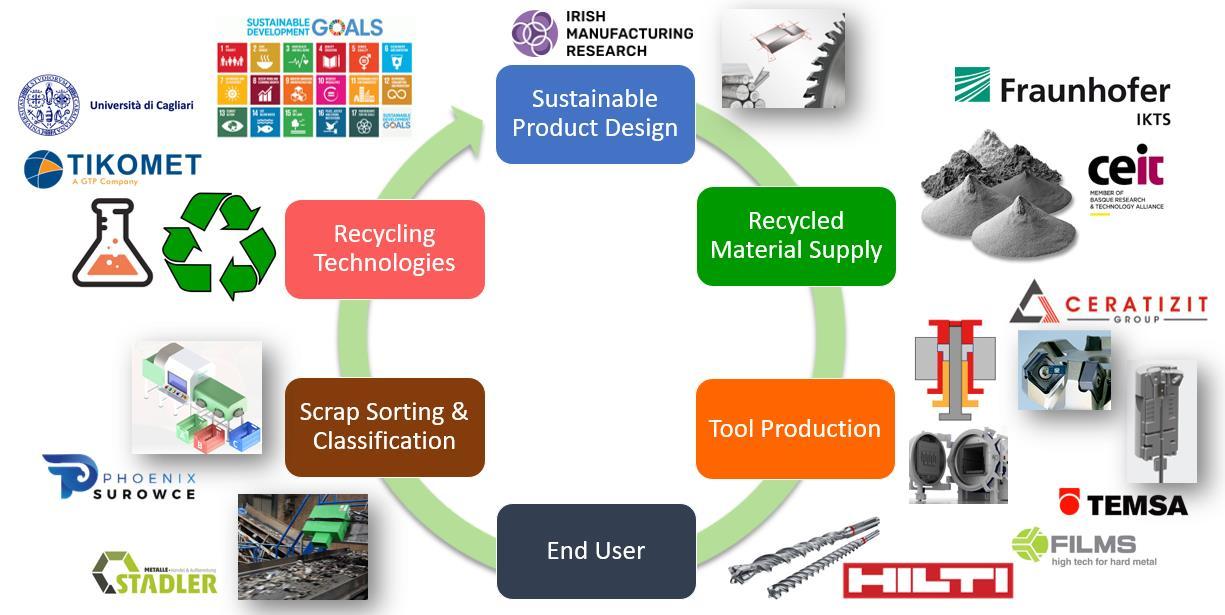
grade materials which go through chemical and furnace processing similar or (latter stages) identical to primary W from ores, but also ‘zinc reclaim’ where well-sorted ‘clean’ scrap is converted to usable powder via a simpler, cheaper process.
Concerns about the CO 2 footprint of organisations and specific products give additional incentives to increase recycling levels to 80% or more (recycled material consumes far less energy than that from ores); some major industry players with a high level of vertical integration are already publicising levels higher than this.
Technical advances in product performance and near-net shaping, meanwhile, tend to reduce the amount of scrap available. The overall result is that scrap demand will soon exceed supply and prices will rise accordingly, in turn eliminating the historic economic benefits of recycled material. Higher scrap prices, education to avoid valuable materials being landfilled, and practice changes to reduce the percentage of unrecoverable material (in mining and construction applications especially) will help, but it is difficult to see ambitious, publicly announced targets being met industry-wide.
“Technical advances in product performance and near-net shaping, meanwhile, tend to reduce the amount of scrap available. The overall result is that scrap demand will soon exceed supply and prices will rise accordingly...”
RESQTOOL HE-Project
Johannes Pötschke (Fraunhofer IKTS), in a technical session on sustainability, summarised the recently formed RESQTOOL HE-Project, a consortium of thirteen partners co-funded by the European Union [17]. The project is aimed at improving scrap source identification and utilisation, sorting and classification via a robust coding/marking regimen and process efficiency (Fig. 13).
This scrap source identification is expected to lead to more optimal processing route selection, improving the economics and envi -
ronmental impact of both the zinc reclaim cemented carbide reclaim route (used on very clean, wellsorted scrap) and the hydro- and pyro-metallurgical process route used for the majority of scrap which is either lower grade or poorlysorted, the latter via the use of chemicals derived from agricultural waste. Both processes (especially the former) already reduce energy needs, CO 2 footprint, and water use compared with making material from primary ores, but further optimisation is expected.
The project will also qualify the use of higher scrap percentages in

Fig. 13 Overview of project partners and workflow of RESQTOOL program (Courtesy Fraunhofer IKTS/MPIF)
“In the North American carbide wear parts and blanks sector, it is notable that – in the last year or two – significant forward integration has occurred through sintered blank manufacturing and finish grinding coming together, either organically or through mergers or acquisitions...”
finished products through analytical studies and property testing on powder and sintered materials, and by lab and field performance testing of finished products.
General comments on the Cemented Carbide industry
Considering the aforementioned drops in W and WC production volumes as well as the financial reports of publicly reported companies, it is fairly clear that the cemented carbide industry is having a difficult time at present.
In part, this reflects a decline in coal mining and oil & gas drilling, but it is also impacted by the fact that the key metal-cutting tools portion of the industry is adversely affected (albeit less than ferrous PM) by vehicle electrification and ICE engine downsizing. In addition, the simple fact is that many of the most significant technical developments are now several decades old which tends to drive commoditisation. Companies need some combination of cost reduction, new product and service innovation, and exemplary service levels on both standard and customer-specific products to compensate.
In the North American carbide wear parts and blanks sector, it is notable that – in the last year or two – significant forward integration has occurred through sintered blank
manufacturing and finish grinding coming together, either organically or through mergers or acquisitions; witness recent (and some not so recent) actions involving General Carbide [18], Hyperion Materials and Technologies [19], and Basic Carbide [20].
Another critical area is that of sustainability, especially since Euro PM2023 [21], where some cemented carbide companies are using the percentage of recycled material in their products not just as a raw material cost reduction method, but also as an externally focused marketing tool, in turn linked to their customers’ drive to reduce their entire value chain carbon footprints. This may be a factor driving more vertical integration of larger carbide companies, specifically Sandvik’s recent acquisition of Buffalo Tungsten [22], and Mitsubishi Materials’ of HC Starck [23], insofar as that increases their access to, and control over, recycled material.
There is simply not enough scrap in the system today for the industry as a whole to achieve the very high recycled content percentage targets publicly stated [24, 25] by some of the largest, most vertically-integrated players, who – by segregating WC made from reclaim processed by hydro and furnace routes from WC that went through similar or identical processes but originating in ore – can increase this metric for their own products. Very high
recycling targets will also drive up material costs and could eliminate the traditional cost benefit of using reclaim. Clearly, then, complications lie ahead, but increasing the use of recycled materials and improving the various steps in collection, sorting, classification, and processing are nevertheless highly beneficial.
In closing
Overall, the PowderMet2024/ AMPM2024 Pittsburgh event was very well organised, and participants seem to have had a great time amidst the atmosphere of healthy knowledge exchange. It will be interesting to hear what further developments have occurred in the PM industry at PowderMet2025 and AMPM2025, to be held June 16-19, 2025, at the Sheraton Downtown in Phoenix, Arizona.
References
[1] Industry insight from the 2024 International Conference on Injection Molding Metals, Ceramics and Carbides, Animesh Bose, PIM International, Vol 18 No 2, https://bit. ly/3YQWGMR
[2] Introduction to W/WC, Bernard North, North Technical Management, LLC, as presented at the PowderMet2024 International Conference on Powder Metallurgy & Particulate Materials and AMPM2024 Additive Manufacturing with Powder Metallurgy Conference.
[3] Grade Powder Production Methods, Tom Jewett, Global Tungsten & Powders Corporation, as presented at the PowderMet2024 International Conference on Powder Metallurgy & Particulate Materials and AMPM2024 Additive Manufacturing with Powder Metallurgy Conference.
[4] Consolidation of RTP Powder, Neal Myers, Kennametal Inc., as presented at the PowderMet2024 International Conference on Powder Metallurgy & Particulate Materials
and AMPM2024 Additive Manufacturing with Powder Metallurgy Conference.
[5] Sintering Methods and Processes for Cemented Carbides, Neal Myers, Kennametal Inc., as presented at the PowderMet2024 International Conference on Powder Metallurgy & Particulate Materials and AMPM2024 Additive Manufacturing with Powder Metallurgy Conference.
[6] Properties and Measurement Methods for Cemented Carbides, Tom Jewett, Global Tungsten & Powders Corporation, as presented at the PowderMet2024 International Conference on Powder Metallurgy & Particulate Materials and AMPM2024 Additive Manufacturing with Powder Metallurgy Conference.
[7] Grade Design of Cemented Carbide, Tungsten Carbide with Binders; and the Effect of Minor Additive Additions, Robert Scott, H. C. Starck Tungsten LLC, as presented at the PowderMet2024 International Conference on Powder Metallurgy & Particulate Materials and AMPM2024 Additive Manufacturing with Powder Metallurgy Conference.[8] Corrosion Resistant Carbide Grades, Madison Rase, Hyperion Materials & Technologies
[9] Alternative WC Binder Materials, Johannes Pöschke, IKTS – Dresden, as presented at the PowderMet2024 International Conference on Powder Metallurgy & Particulate Materials and AMPM2024 Additive Manufacturing with Powder Metallurgy Conference.
[10] Introducing the High Entropy Concept into Cemented Carbides, Johannes Pötschke, Fraunhofer IKTS, as presented at the PowderMet2024 International Conference on Powder Metallurgy & Particulate Materials and AMPM2024 Additive Manufacturing with Powder Metallurgy Conference.
[11] Additive Manufacturing IOverview Examining the Different Processes and Powders, Zhuqing Wang, Kennametal, as presented at the PowderMet2024 International Conference on Powder Metallurgy & Particulate Materials and AMPM2024 Additive Manufacturing with Powder Metallurgy Conference.
[12] Develop Low Binder Tungsten Carbide Grades Using Binder Jetting, Zhuqing Wang, Kennametal Inc., as presented at the PowderMet2024 International Conference on Powder Metallurgy & Particulate Materials and AMPM2024 Additive Manufacturing with Powder Metallurgy Conference.
[13] Additive Manufacturing IIKennametal Additive – Additive II (Process Capabilities and Market Opportunities/Threats), Jerry Dominguez, Kennametal Inc., as presented at the PowderMet2024 International Conference on Powder Metallurgy & Particulate Materials and AMPM2024 Additive Manufacturing with Powder Metallurgy Conference.
[14] Fused Filament Fabrication of Hardmetals, Animesh Bose, FAPMI, Optimus Alloys, LLC, as presented at the PowderMet2024 International Conference on Powder Metallurgy & Particulate Materials and AMPM2024 Additive Manufacturing with Powder Metallurgy Conference.
[15] Additive Manufacturing of Steels for Tooling Applications, Zhuqing Wang, Kennametal Inc., as presented at the PowderMet2024 International Conference on Powder Metallurgy & Particulate Materials and AMPM2024 Additive Manufacturing with Powder Metallurgy Conference.
[16] Recycling of Hardmaterials, Amy Herron, Tungco, as presented at the PowderMet2024 International Conference on Powder Metallurgy & Particulate Materials and AMPM2024
Additive Manufacturing with Powder Metallurgy Conference.
[17] RESQTOOL HE-Project - Recycling of High-Quality CRM Resources from Machining Tools for Re-use
Applications, Johannes Pötschke, Fraunhofer IKTS, as presented at the PowderMet2024 International Conference on Powder Metallurgy & Particulate Materials and AMPM2024
Additive Manufacturing with Powder Metallurgy Conference.
[18] General Carbide to add 100 jobs in $14 million expansion at its Hempfield facility, Trib Live, Dec. 10, 2018
[19] Hyperion Materials & Technologies signs agreement to acquire Aggressive Grinding Service, PR Newswire, Nov 3, 2021
[20] Basic Carbide Corporation press release, March 27, 2024
[21] Bernard North PM Review Euro PM2023 “Scrap is the new gold” and other hardmetal and hard materials insights from Euro PM2023 Congress, Lisbon. PM Review , Vol 12 No 4, https://bit.ly/3yLjFhJ
[22] Sandvik completes Buffalo Tungsten acquisition, PM Review Dec 26, 2023, www.pm-review.com/ sandvik-completes-buffalo-tungstenacquisition/
[23] HC Starck Tungsten to be sold to Mitsubishi Materials Corporation, PM Review May 22, 2024, https://www.pm-review.com/ hc-starck-tungsten-to-be-sold-tomitsubishi-materials-corporation/
[24] CERATIZIT Launches Aggressive Sustainability Strategy and Gains Recognition for Green Carbide, Fabricating Metalworking, February 15, 2023
[25] Sandvik AB Annual Report 2023
Author Bernard North North Technical Management, LLC Greater Pittsburgh area, Pennsylvania, USA bnorth524@msn.com

Honorary sponsor
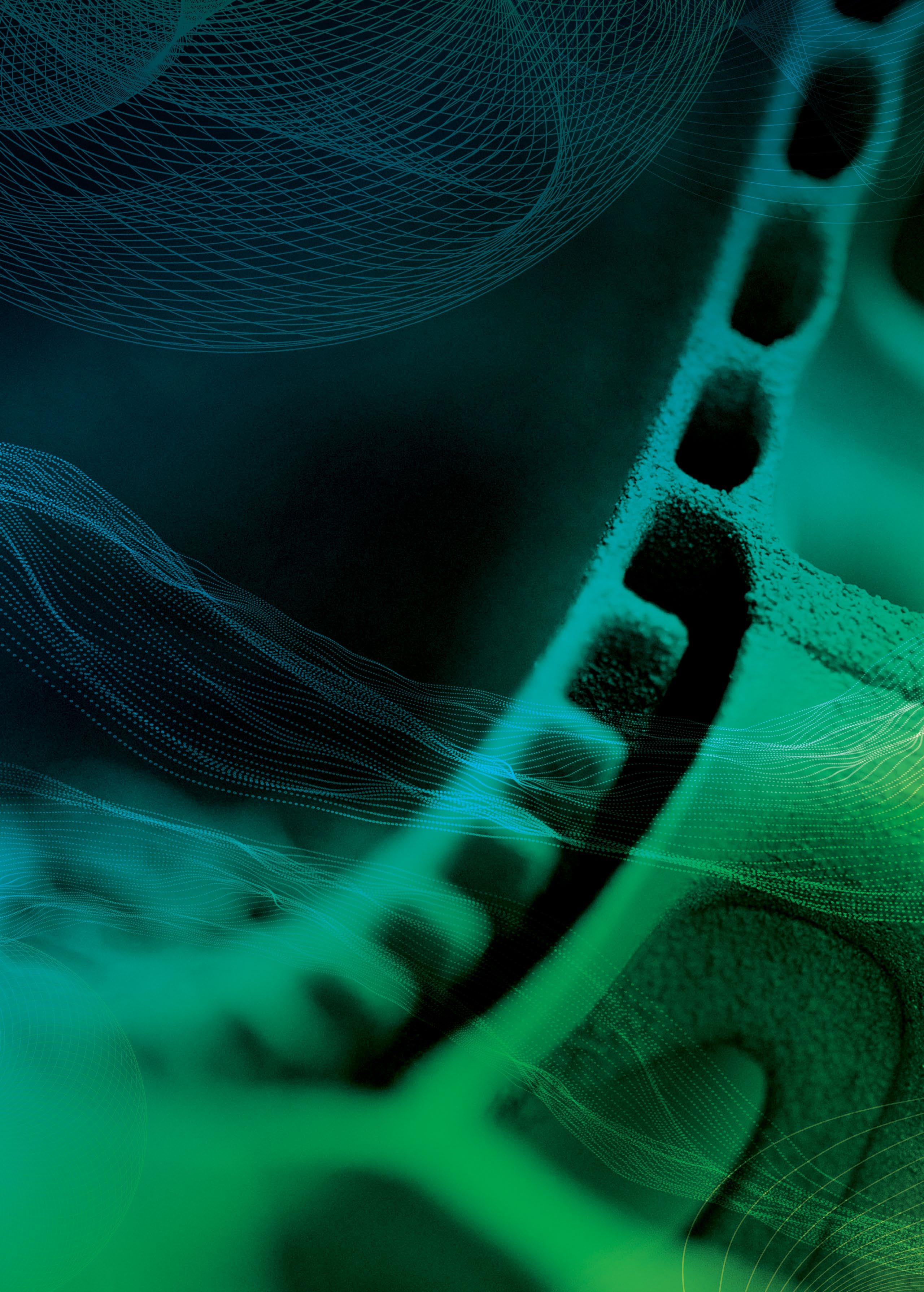
Demand for more complex, customized parts is rising fast. Product cycles are shortening, traditional supply chains are evolving, and the importance of sustainability continues to grow. Additive Manufacturing offers
the solutions to meet these challenges and inspire your customers.
Powder Metallurgy shines in the MPIF’s 2024 Design Excellence Awards competition
The annual Powder Metallurgy Design Excellence Awards competition, organised by the Metal Powder Industries Federation (MPIF), is an opportunity for PM part producers to showcase the capabilities of the full range of metal powder-based technologies to a global audience. This year’s winners were announced at the International Conference on Powder Metallurgy & Particulate Materials (PowderMet2024), held in Pittsburgh from June 16-19. This report reviews the winners in the conventional Press and Sinter PM category.
The winners of the 2024 Powder Metallurgy Design Excellence Awards competition, sponsored by the Metal Powder Industries Federation (MPIF), were announced at PowderMet2024. Ten Grand Prizes and seventeen
Awards of Distinction were presented in this year’s competition. Entries were divided into three categories: Conventional Press and Sinter PM; Metal Injection Moulding (MIM) and metal Additive Manufacturing (AM).
The winners once again demonstrate outstanding examples of the PM industry’s diversity and ability to meet critical requirements. From electric vehicles to medical implants, parts fabricators have demonstrated
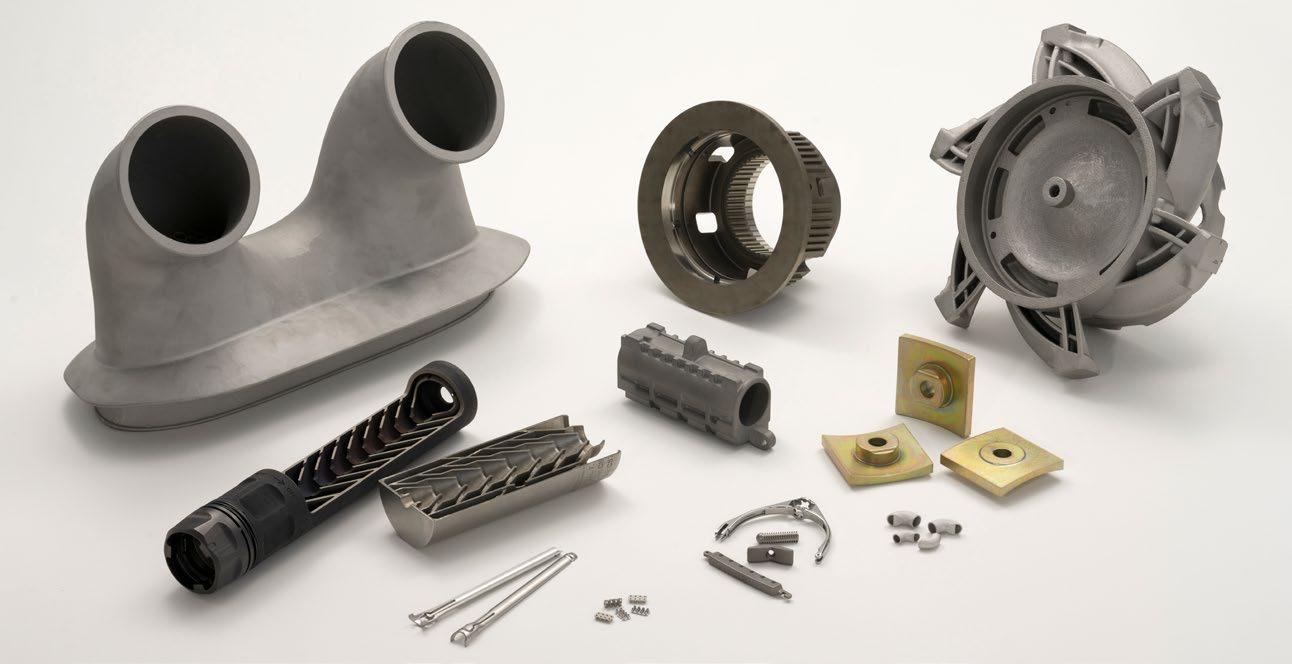
Fig. 1 Grand Prize winners in the MPIF 2024 Powder Metallurgy Design Excellence Awards, showing the advanced capabilities of press and sinter PM, Metal Injection Moulding (MIM) and metal Additive Manufacturing (Courtesy MPIF)

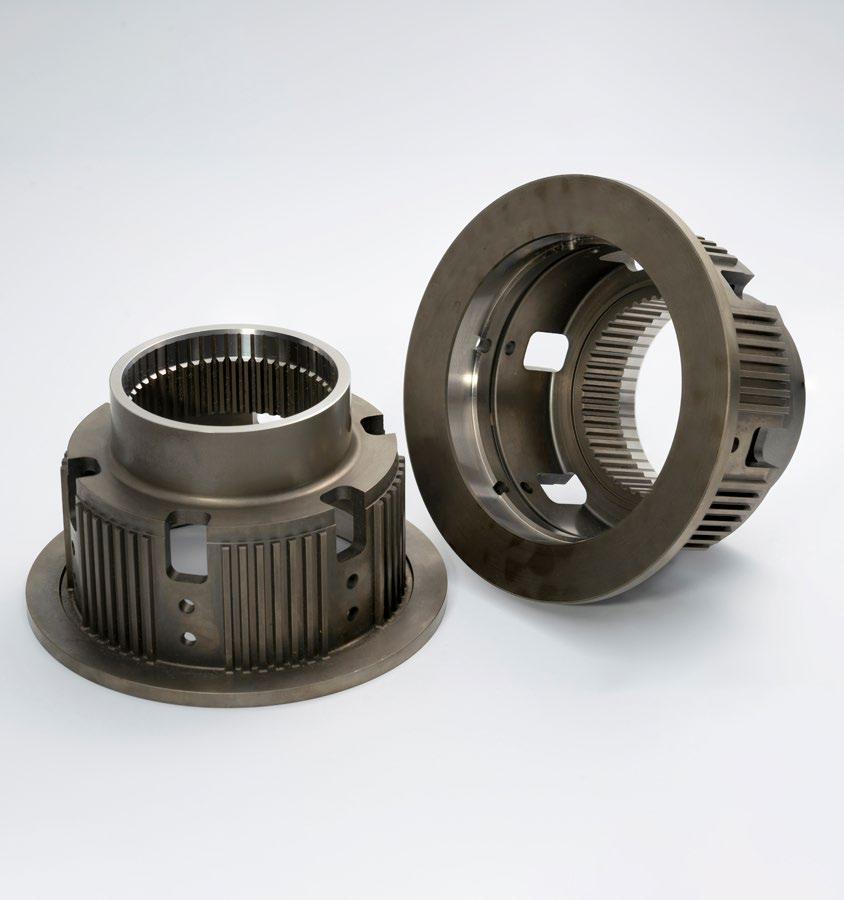

PM’s versatility and unique ability to challenge competing technologies.
The components presented here were recognised in the Conventional Press and Sinter PM category. Winners in the Metal Injection Moulding category are published in PIM International magazine (https:// bit.ly/3XaYBcG) and winners in the metal Additive Manufacturuing category are covered in Metal AM magazine (https://bit.ly/3Xk4JiW).
Grand prize awards
Automotive – Transmission
A Grand Prize in the Automotive – Transmission Category for Conventional PM components was awarded to AMES Group Sintering S.A. for a hub used in the clutch of a transfer case of a four-wheel-drive car (Fig. 2). The customer qualified the parts by applying four bench tests – a static strength test, a pulse fatigue test, a dynamic fatigue test, and a balancing rotary test.
The Powder Metallurgy route was selected rather than a machined forging due to PM technology’s ability to combine complex part shape, high accuracy of some characteristics without machining, low material waste, and a competitive cost. A 25% reduction in material waste was achieved compared with machining the part from a forging.
Hardware/Appliance
A Grand Prize in the Hardware/ Appliances Category for Conventional PM components was awarded to FMS Corporation and its customer, Dynamis Solutions, for support bushings that serve as clamping washers in a concentrated solar-power generation application (Fig. 3). The parts solve a problem encountered during cleaning and maintenance of the heliostats. The original connection used a fastener and a common lock washer to secure the azimuth drive to the pylon and the hole elongated in service. Heliostats, equipped with large mirrors, are arranged in a circle around a central receiver
Fig. 3 Support bushings that serve as clamping washers in a concentrated solar-power generation application by FMS Corporation for Dynamis Solutions (Courtesy MPIF)
Fig. 2 Hub used in the clutch of a transfer case of a four-wheel-drive car by AMES Group Sintering S.A. (Courtesy MPIF)
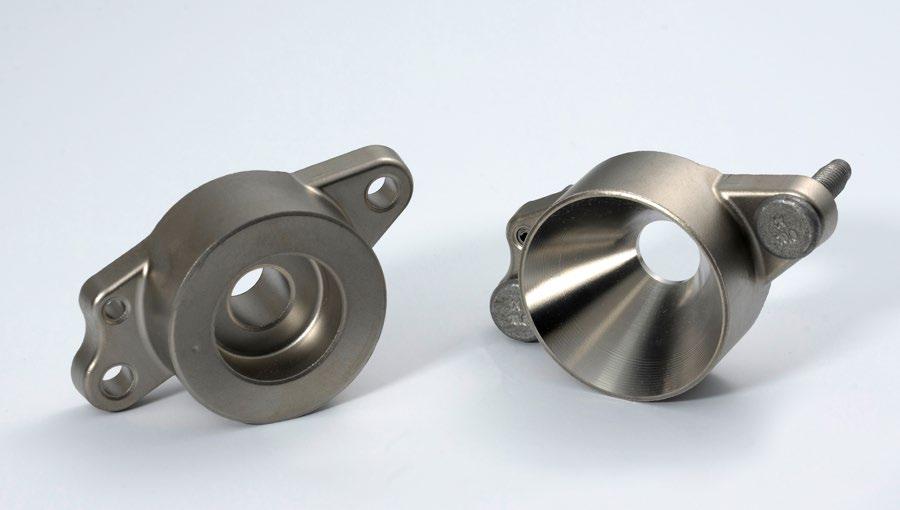
tower and focus solar rays to heat a synthetic oil that is used to generate steam to power a turbine and generate electricity. The PM component facilitates an improved connection between the azimuth drive of a heliostat and a fixed steel support pylon in the ground.
Awards of distinction
Automotive – Engine
In the Automotive–Engine Category for Conventional PM components, an Award of Distinction was awarded to APG Sintered Metals, Ridgway, a Division of Nichols Portland Inc., for a stainless steel diesel exhaust fluid injector flange used in a midsize pick-up truck (Fig. 4). Diesel emission fluid (DEF) injectors have become a vital technology in diesel engine after-treatment systems as they reduce the amount of NOx gas exiting the tailpipe.
An Award of Distinction was also given, in the Automotive–Engine Category for Conventional PM components, to AAM – Subiaco Manufacturing Facility for a camshaft position sensor exciter wheel used in
full-size pick-up trucks and sportutility vehicles (Fig. 5). The exciter wheel mounts on the camshaft and provides target corners for the cam sensor to input data to the engine control module to deter -
mine the camshaft position and velocity. The PM process has better material utilisation compared with stamping and the parts can be recycled as they do not contain copper.


Fig. 4 Stainless-steel diesel exhaust fluid injector flange by APG Sintered Metals, Ridgway, a Division of Nichols Portland Inc. (Courtesy MPIF)
Fig. 5 Camshaft position sensor exciter wheel by AAM – Subiaco Manufacturing Facility (Courtesy MPIF)
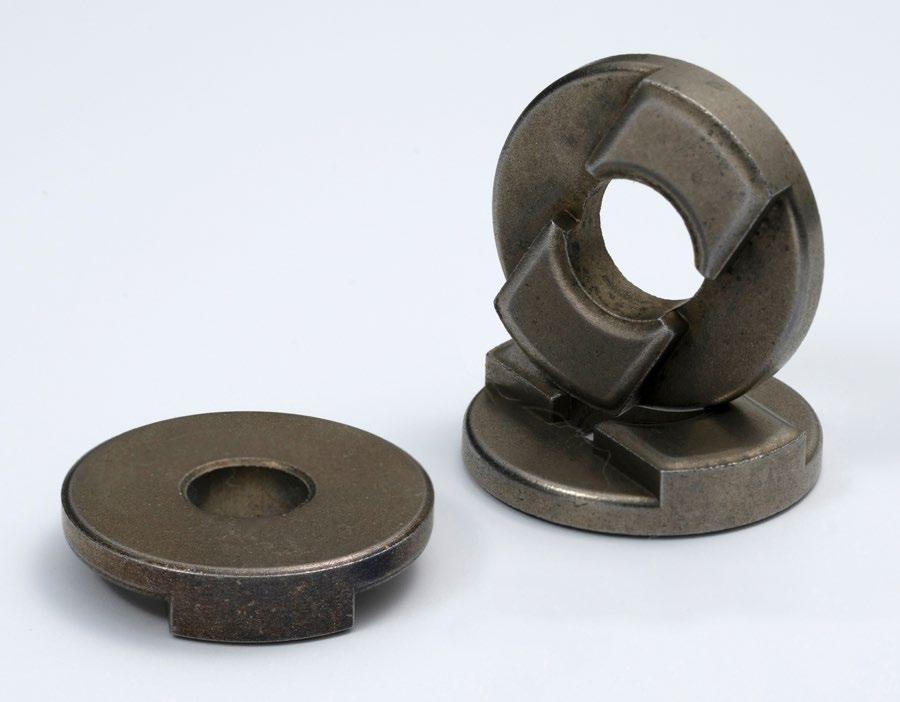
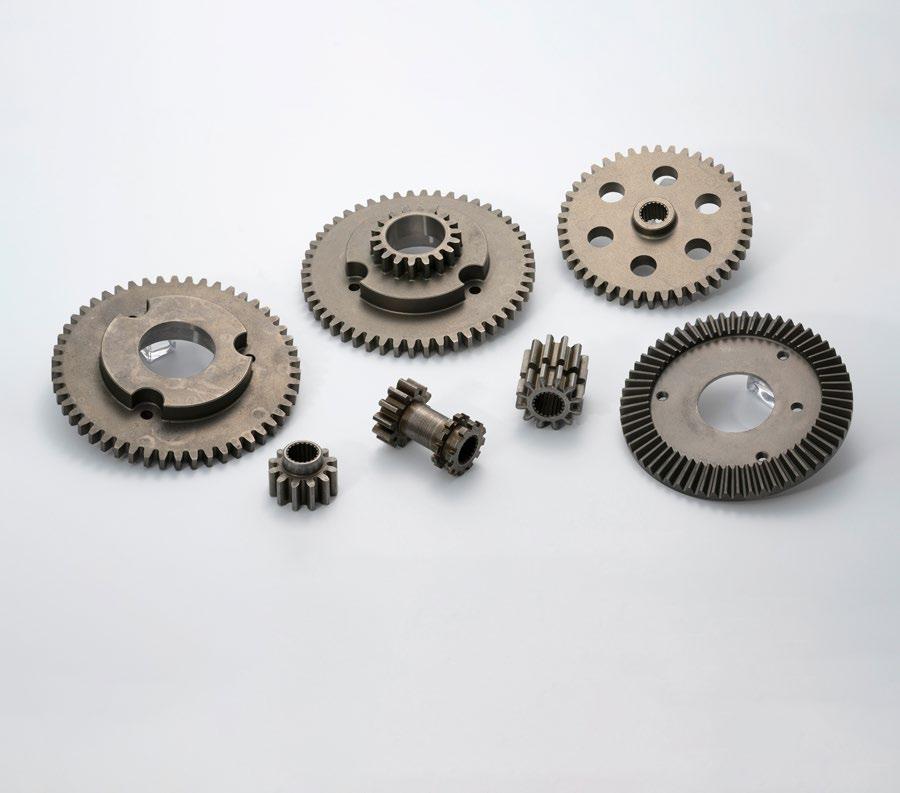
“A special heat-treatment cycle was developed to maintain hardness but also maximise ultimate tensile strength and impact energy. Tight tolerance machining and machining of the teeth without burrs required development of special machining cycles and insert materials.”
Automotive – Chassis
An Award of Distinction was presented, in the Automotive–Chassis Category for Conventional PM components, to Metalpo Industria e Com Ltda for a truck steering column tilt adjustment component for its customer Knorr Bremse (Fig. 6). The part is compacted using a single upper and two lower punches and a core rod. It is required to slide into a stamped guide and a carbonitrided PM part was unable to meet the dimensional tolerances needed by the customer.
Lawn & Garden/Off-Highway
In the Lawn & Garden/Off-Highway Category for Conventional PM components, an Award of Distinction was given to Capstan Atlantic and its customer Ardisam Inc. for a multi-component gear assembly used in Ardisam’s Earthquake brand – Pioneer Rear Tine Tiller (Fig. 7). A special heat-treatment cycle was developed to maintain hardness but also maximise ultimate tensile strength and impact energy. Tight tolerance machining and machining of the teeth without burrs required development of special machining cycles and insert materials.
Hand Tools/Recreation
In the Hand Tools/Recreation Category for Conventional PM components, an Award of Distinction was given to Capstan for a stainless-steel drive gear used in a throttle system with a stack-up of three stainless-steel PM gears (Fig. 8).
Multi-level tooling was used to create the five separate levels of the part and intricate powder transfer and motions were required to displace material for the ‘slot’ surface due to the thin cross-section. The compaction process achieved about 60% of the final shape of the part and secondary CNC lathe turning and milling operations were used to achieve the bore depths, hub diameter, groove, and tapped hole.
Fig. 6 Truck steering column tilt adjustment component by Metalpo Industria e Com Ltda (Courtesy MPIF)
Fig. 7 Multi-component gear assembly by Capstan Atlantic for Ardisam Inc. (Courtesy MPIF)
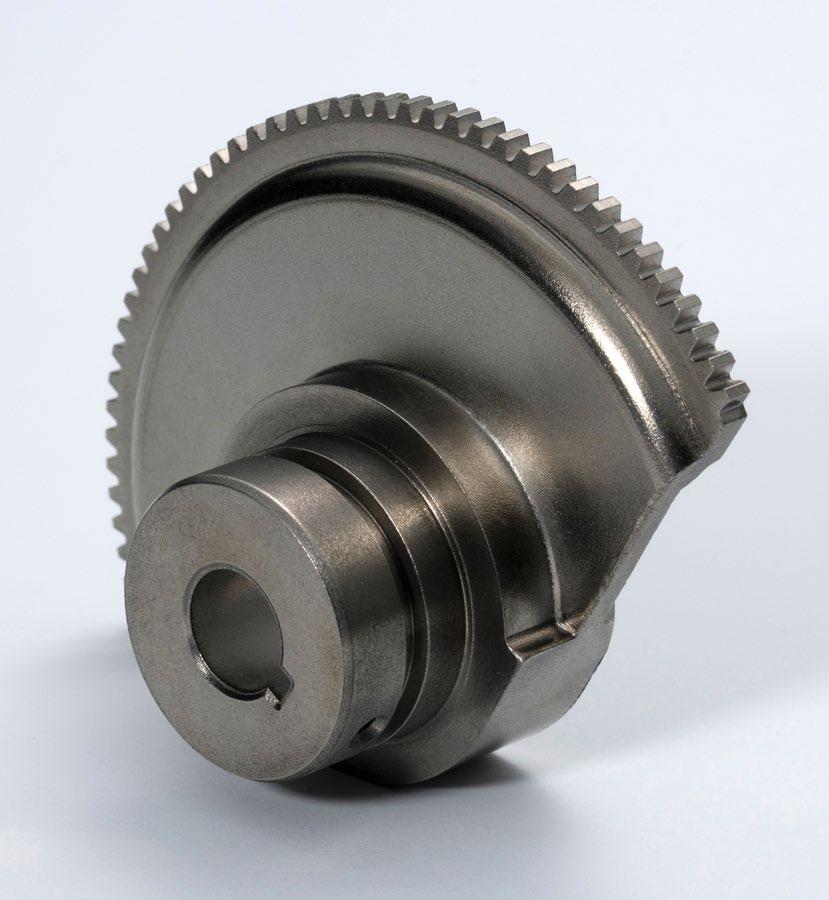
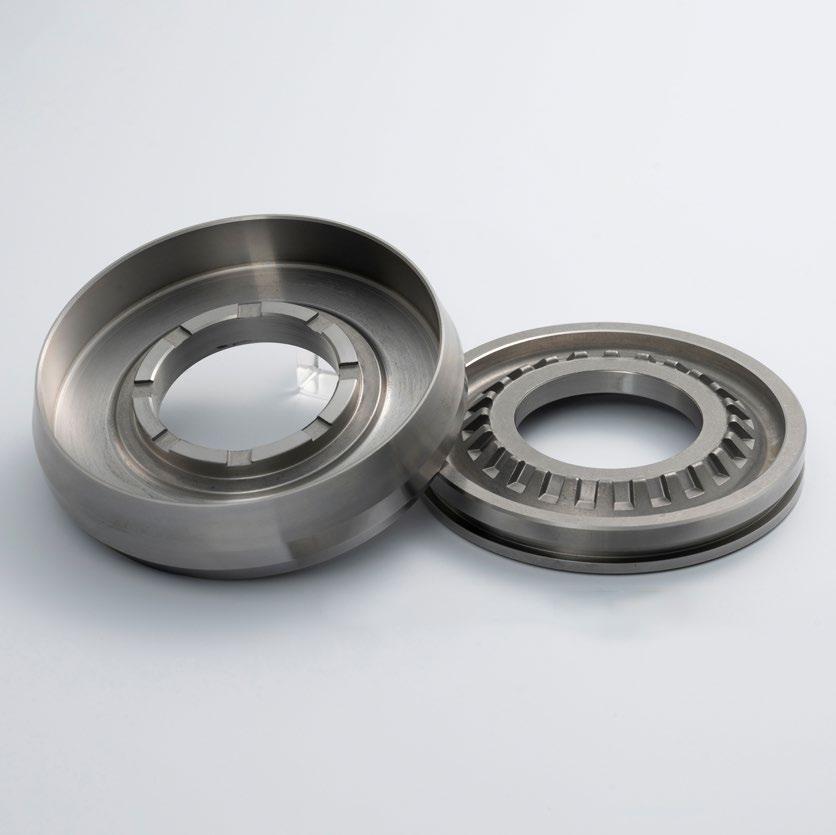
Industrial Motors/Controls & Hydraulics
An Award of Distinction, in the Industrial Motors/Controls & Hydraulics Category for Conventional PM components, was given to Phoenix Sintered Metals LLC for a piston brake spring-return assembly for its customer Muncie Power Products, Inc (Fig. 9). The piston engages the clutch-pack under pressure and the taper feature acts as a brake when disengaged. This was the first use of this unique design power-takeoff system. The ability to form the tone-ring feature on the inner hub of the piston was a feature not available on the prior part design that was machined from bar stock.
Medical/Dental
In the Medical/Dental Category for Conventional PM components, an Award of Distinction was given to Metco Industries for a heavyduty hospital bed rail latch-lock assembly (Fig. 10). Two PM parts are included in this nine-part assembly. The latch-lock lever is made in a single level tool that utilises a special feature to maintain the density of the ramp,
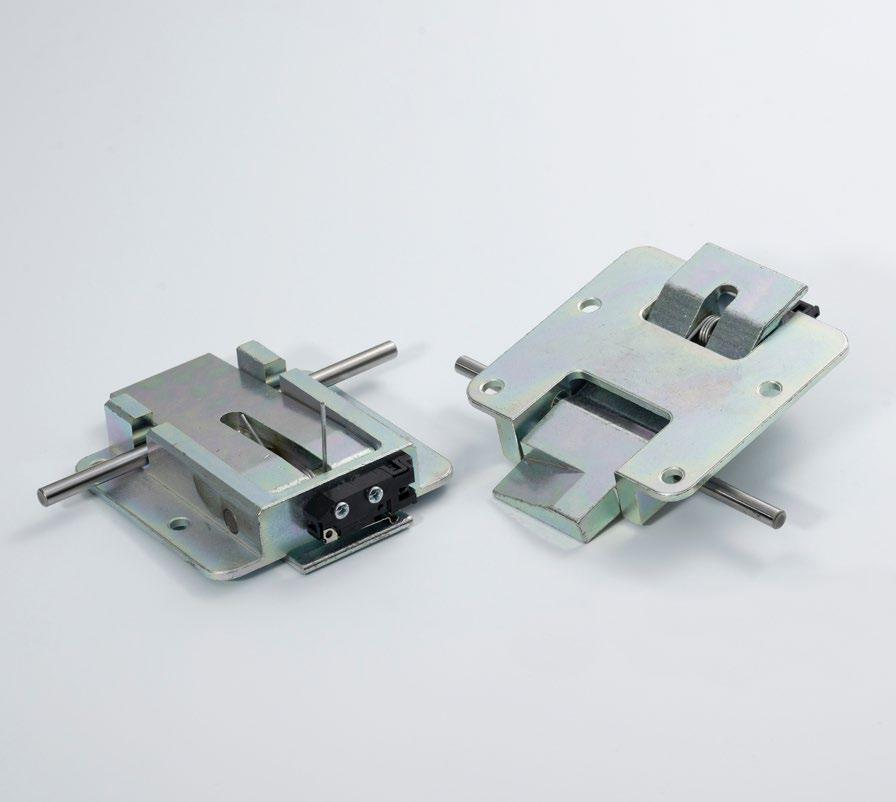
Fig. 10 Heavy-duty hospital bed rail latch-lock assembly by Metco Industries (Courtesy MPIF)
which is a critical wear zone. After sintering the parts are milled, heat treated, and plated. Maintaining flatness and minimising warpage is a challenge with the given wall thickness. The infiltrated parts are resin impregnated prior to zinc plating and this provides a sterile surface unlikely to absorb contaminants in a hospital environment.
www.mpif.org

Fig. 8 Stainless steel drive gear used in a throttle system by Capstan Atlantic (Courtesy MPIF)
Fig. 9 Piston brake spring-return assembly by Phoenix Sintered Metals LLC for Muncie Power Products, Inc. (Courtesy MPIF)

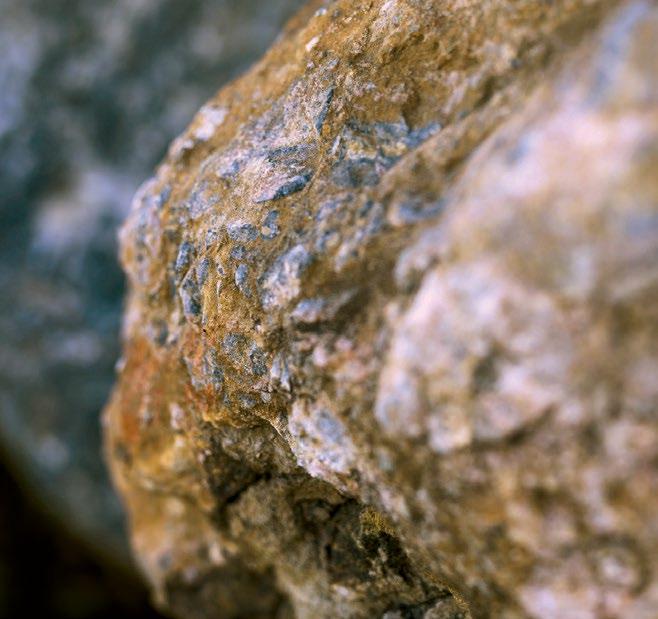

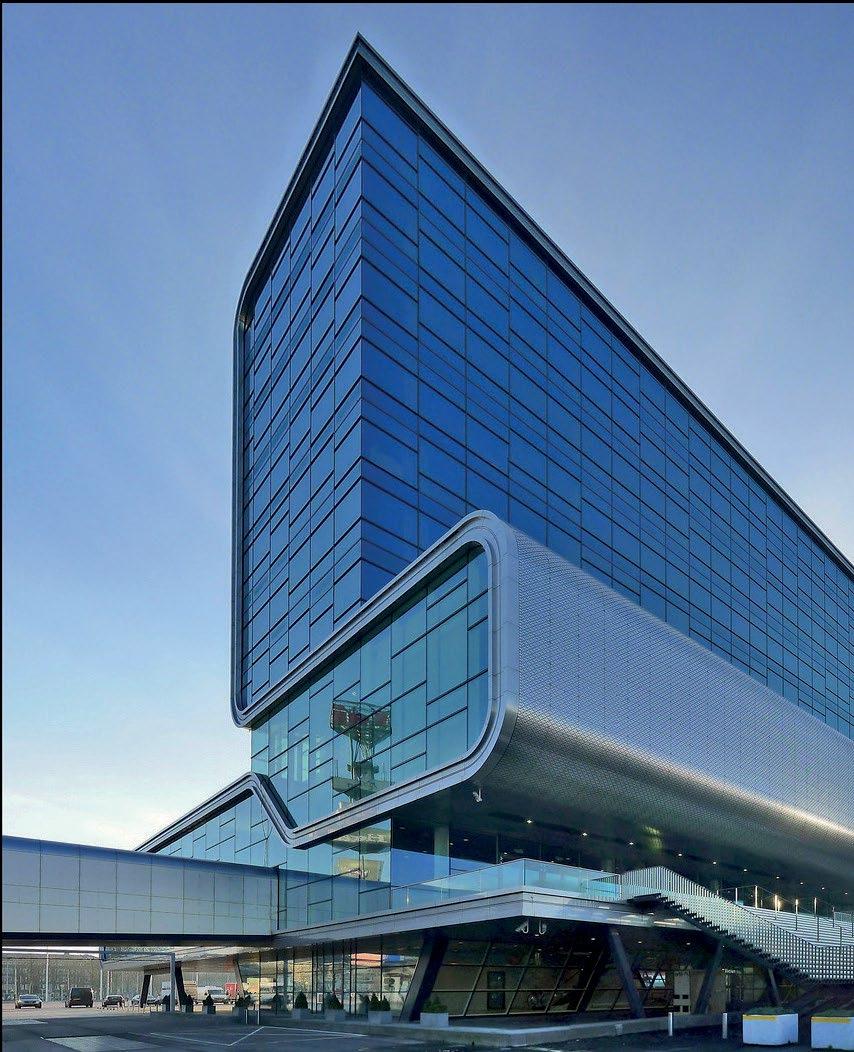
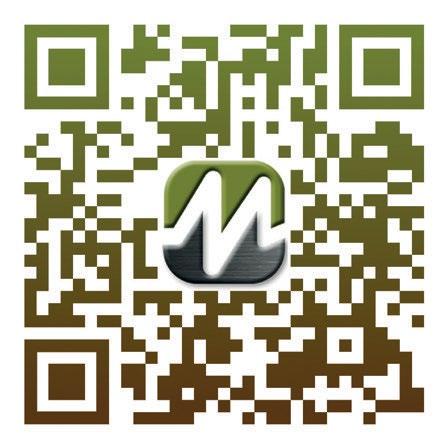
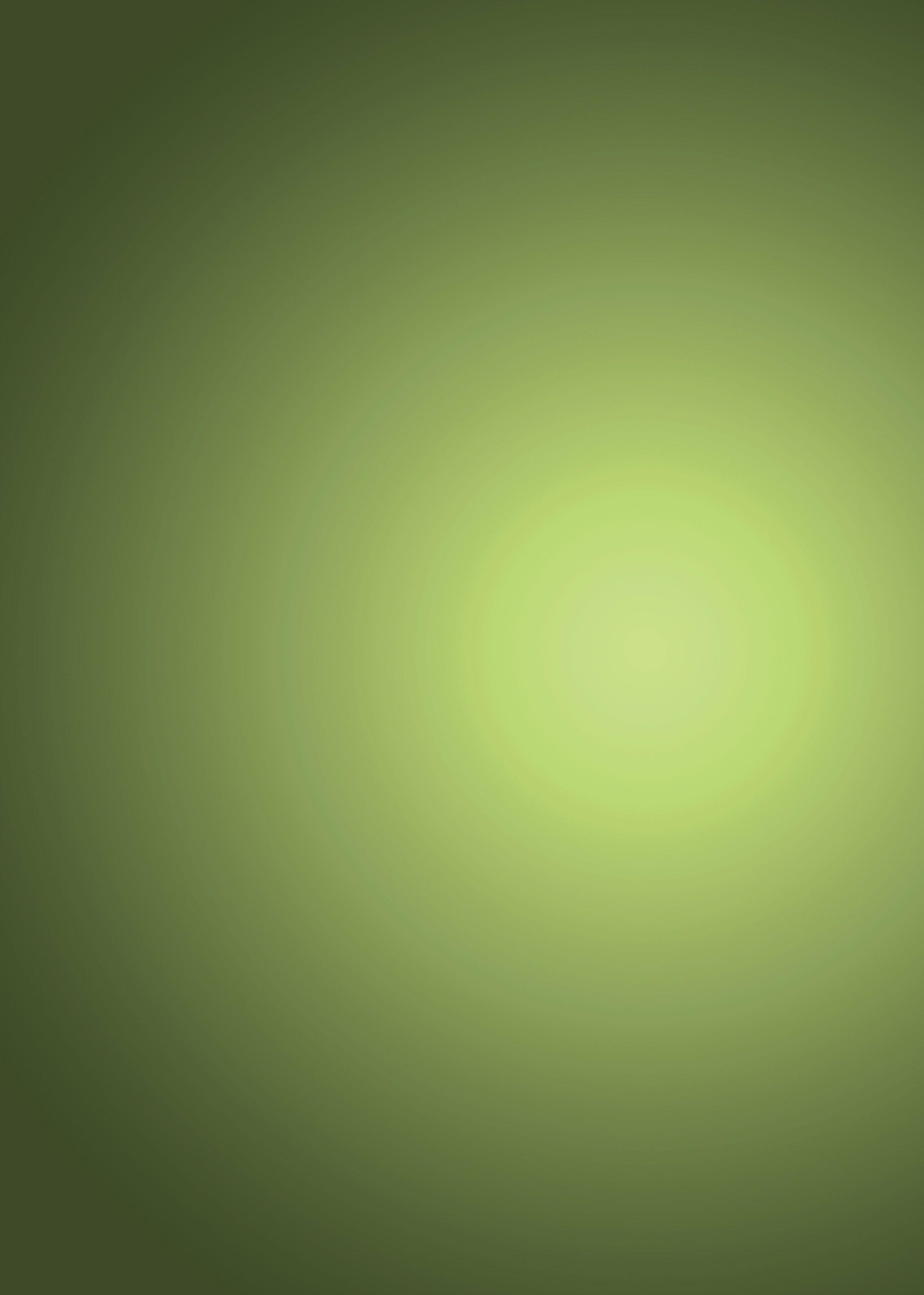
PowderMet2024: The state of the Powder Metallurgy industry in North America
A highlight of the Metal Powder Industries Federation’s annual International Conference on Powder Metallurgy & Particulate Materials (PowderMet) is the ‘State of the PM Industry’ presentation, in which key industry data are presented alongside analysis of the performance of PM in major markets. This year’s presentation was delivered by Michael Stucky, president of the MPIF and Business Unit Director at Norwood Medical. Stucky’s presentation, published here in full, brings the current challenges facing PM into focus, as well as highlighting opportunities for growth.
Powder Metallurgy is comprised of four major categories: Press and Sinter (P&S); Metal Injection Moulding (MIM), Additive Manufacturing (AM), and Hot or Cold Isostatic Pressing (HIP/CIP). Many areas of PM can be considered a circular economy as they reduce material use; redesign materials, products, and services to be less resource intensive; and recapture ‘waste’ as a resource to manufacture new materials and products. An advanced manufacturing process that can produce robust net-shape components, PM’s high material utilisation promotes efficient use of raw materials, reduces energy consumption, and improves labour efficiency.
The current North American PM industry is driven by applications in the automotive market. Environmental concerns have significantly altered the focus of the automotive sector, to say the least. Just a few years ago, most automotive companies went ‘all in’ with battery
electric vehicles (BEV); in line with this, they discontinued Research & Development on internal combustion engines (ICE) and announced massive reductions in their engineering workforce. PM companies became increasingly concerned.
Today, there is a new focus on hybrid electric vehicles (HEV), including plug-in hybrid vehicles (PHEV). These represent the best of both worlds, with reduced emissions while operating primarily on battery power and increased distance with
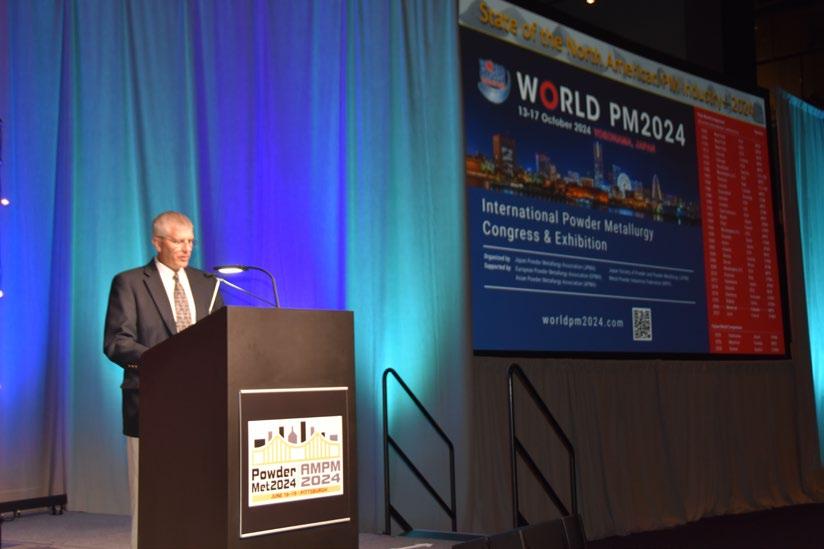

Fig. 1 Michael Stucky, president of the MPIF and Business Unit Director Norwood Medical, presenting on the state of the PM industry at PowderMet2024, Pittsburgh, June 16-19 (Courtesy MPIF)
(E) estimate. 1 short ton = 0.907 metric ton | * PM parts only
** From 2023 forward, this estimate will be 4.5% of the iron powder shipments for PM & Friction
Table 1 North American Metal Powder Shipments (Courtesy MPIF)
“Optimism was high heading into 2023, but short-lived. By the end of January, iron powder shipments – the best indicator of the health of the PM industry – were down over 10% from January 2022, and projected shipments never came to fruition.”
the backup ICE. Higher fuel efficiency through improvements in engine performance, weight reduction, and alternative or supplemental power systems will be key drivers. The use of lightweight metals – such as aluminium, magnesium, and titanium – will increase, but ferrous alloys will remain the most used metals due to their high specific strength and lower cost. Powder Metallurgy should benefit from this new focus. Other growth opportunities for PM technology over the next ten years include energy, aerospace, medical/dental, electrical and magnetic, defence, and industrial and consumer products. The need
for alternative energy sources will drive new markets and applications for PM; the ageing population will continue to create a need for PM applications in the medical industry; global economic development and rising living standards will have a significant impact on PM in consumer products.
Metal powder shipments
Optimism was high heading into 2023, but short-lived. By the end of January, iron powder shipments –the best indicator of the health of the PM industry – were down over 10%
from January 2022, and projected shipments never came to fruition. The total estimated 2023 North American metal powder shipments decreased by 1.2% to 341,420 metric tons (376,428 short tons) (Table 1).
Total iron & steel powder shipments decreased 1.0% to 290,452 mt (320,234 st). Estimated copper and copper base powder shipments – along with stainless steel powders – decreased 10% to 11,842 mt (13,056 st) and 5,714 mt (6,300 st), respectively. Nickel powder decreased 1.1% to 3,991 mt (4,400 st), while aluminium powder shipments increased 8%.
Refractory powders were strong during the first half of 2023 but finished the year down an estimated 10.9% compared with 2022. Molybdenum shipments increased an estimated 10.1% to 765 mt (843 st). However, tungsten powder shipments decreased by an estimated 14.7% to 2,890 mt (3,186 st) and tungsten carbide powder shipments decreased by an estimated 11.4% to 4,316 mt (4,759 st).
PM and friction-grade iron powder shipments were flat at 263,157 mt (290,140 st) (Table 2). Welding applications decreased by 4.3% to 13,990 mt (15,424 st). Cutting, scarfing, and lancing
decreased by 1.3% to 820 mt (904 st).
Miscellaneous uses decreased 14.0% to 12,486 mt (13,766 st).
MIM and AM powder producers entered unchartered waters in 2023, but most expected this to be an anomaly and not reflective of its long-term trajectory. Feedstock producers, who are large powder consumers, maintained significant inventories of raw powder to ensure consistent supply for customers. At the same time, parts makers worked through the unusually high inventories that resulted from over purchasing in 2021-2022, a reaction to disrupted powder supplies. Adding to the unstable conditions were declining orders throughout the year. The unusual circumstances affected both powder and feedstock producers.
Spherical stainless steels and low-alloy steels are the primary MIM and AM materials, but considerable Research & Development has resulted in successful components from aluminium, copper, titanium, tungsten, and an array of other metal powders and alloys. North American metal powder consumption for AM is estimated to have increased by 10% in 2023 to 434,088 kg (957,000 lb). However, the combined MIM and AM metal powder shipments decreased by an estimated 10% to 3,706,7573,963,944 kg (8,172,000-8,739,000 lb). Some industry insiders believe the decrease in shipments for MIM could be even greater, but all expected a correction during 2024-2025.
Conventional press and sinter PM
There are mixed feelings from the P&S parts makers, depending on the markets served. The indecisiveness of the automotive industry took a toll on P&S, resulting in consolidations and company closures; reduced workforces; minimised capital investments for equipment; and a reduction in R&D where the automotive industry drove technological advancements. However, it also offered new opportunities.
Table 2 North American Iron Powder Shipments (Courtesy MPIF)
“There are mixed feelings from the P&S parts makers, depending on the markets served. The indecisiveness of the automotive industry took a toll on P&S, resulting in consolidations and company closures; reduced workforces; minimised capital investments for equipment; and a reduction in R&D...”
Some saw the global shift to electric motors as an opportunity for magnetic materials to come to the forefront over the next decade. Development continues in soft-magnetic-composite (SMC) materials with higher permeability, increased strength, and improved temperature resistance for AC applications. Advanced motor designs are demonstrating the potential of axial-flux motors (AFM) and transverse-flux motors (TFM) utilising SMC parts for automotive and non-automotive applications.
The current outlook for automotive applications is relevant to the make and model, but most parts makers anticipate the automotive market to be flat to mid-single digit growth for the remainder of the year. However, many anticipate new applications launching for HEV/BEVs, and they are waiting with open arms for the resurgence of ICE vehicle applications.
Non-automotive projections range from high single-digit to mid-doubledigit growth. These applications tend to be quicker time to market, lower volumes, but the low-hanging fruit is gone and most require some type of value-added secondary operations. Automation, reduced energy consumption, data monitoring, and efficiency continue to be the focus of P&S equipment manufacturers. These manufacturers continue to introduce equipment to support value-added, near-net-shape parts requiring high precision secondary operations, opening new opportunities for the parts makers. Additionally, continuous improvement of advanced premix lubricants, binders, and machining additives allows tailored customer support for all applications, ensuring a stable raw material supply chain for parts makers.
Sustainability, supply chain localisation, and electrification will remain key challenges for P&S, forcing


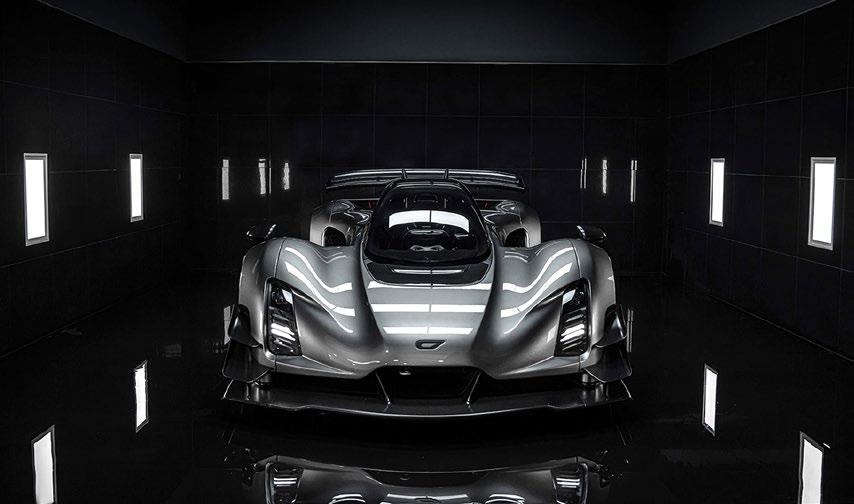
automotive and industrial suppliers to adapt, evolve, and cultivate new opportunities.
Metal Additive Manufacturing
Metal AM has the potential to change the production, time-to-market, and simplicity of components and assemblies. But continued growth depends on advancements in materials and material properties, processes, and manufacturing efficiencies. New materials developed to support the metal AM industry include high-wear-resistance alloys, water atomised iron, copper, tool steels, nickel-based superalloys, cobaltbased alloys, aluminium alloys, and titanium alloys for specialised applications.
Thanks to the materials advancements, new equipment is hitting the market. Research & Development atomisers are being utilised for small production batches of powders until large volumes support the scaled-up atomisers that will further commercialisation. Furnace manufacturers are satisfying the needs of Binder Jetting (BJT) parts producers. Metal AM parts producers are taking advantage of Hot Isostatic Pressing to ensure the integrity of their parts. New software leverages advanced simulation to enable users to correct for distortion experienced by metal Additive Manufacturing parts during sintering due to gravity, friction, and shrinkage.
“Metal AM has the potential to change the production, time-to-market, and simplicity of components and assemblies. But continued growth depends on advancements in materials and material properties, processes, and manufacturing efficiencies.”
To expedite the acceptance of metal AM, the Association for Metal Additive Manufacturing (AMAM) has issued standard test methods for tension test specimens and anticipates the release of a new MPIF Std 35-AM Materials Standards for Metal Additive Manufactured Parts this year that will standardise Binder Jet 316L and 17-4 PH stainless steels. After the Binder Jetting materials are approved, work will commence on materials for Laser Beam Powder Bed Fusion (PBF-LB).
The overall outlook for metal AM is the same as for all advanced
Fig. 2 A 2024 MPIF Design Excellence Awards Grand Prize in the Automotive – Engine category for metal AM components was awarded to Divergent Technologies, Inc for its CZV engine exhaust tip for the Czinger 21C. The part was produced by Laser Beam Powder Bed Fusion (PBF-LB) (Courtesy MPIF/ Czinger Vehicles)
manufacturing processes - increased efficiency, reduced cost, and digitisation of the process are required for the technology to be accepted and mature. If metal AM lives up to its expectations, it could significantly affect the overall use of metal powders and positively influence market penetration. For many applications, metal AM will become increasingly competitive with all metal-forming processes.
Metal Injection Moulding
The North American MIM industry remains healthy with an overall optimistic outlook for the industry, though few are predicting high rates of growth in the short-term. MIM occupies a small niche amongst all metalworking processes and remains subject to significant fluctuations. The ability to create complex shapes reliably and economically in high volume remains MIM’s core strength. Growth for companies working in MIM depends on the success of parts makers in gaining increased market share against other metalworking technologies, and R&D efforts are focused on increasing dimensional control/reliability and overall cost reduction. The medical and firearms sectors continue to be the prime consumers of MIM components, but the demand for firearms has steadily decreased over the past three years. However, general industrial applications and automotive MIM components continue to increase annually.
The MIM powder/feedstock suppliers’ outlook is positive for the future. This positive view includes the stability of standard offerings like stainless steels, low-alloy steels, and titanium alloys. There has also been increased interest in superalloys that are coming into commercialisation. The Metal Injection Molding Association’s (MIMA) Standards Committee is currently reviewing its first titanium standard. Moulding equipment demand is stable as overall production demands are being met by existing
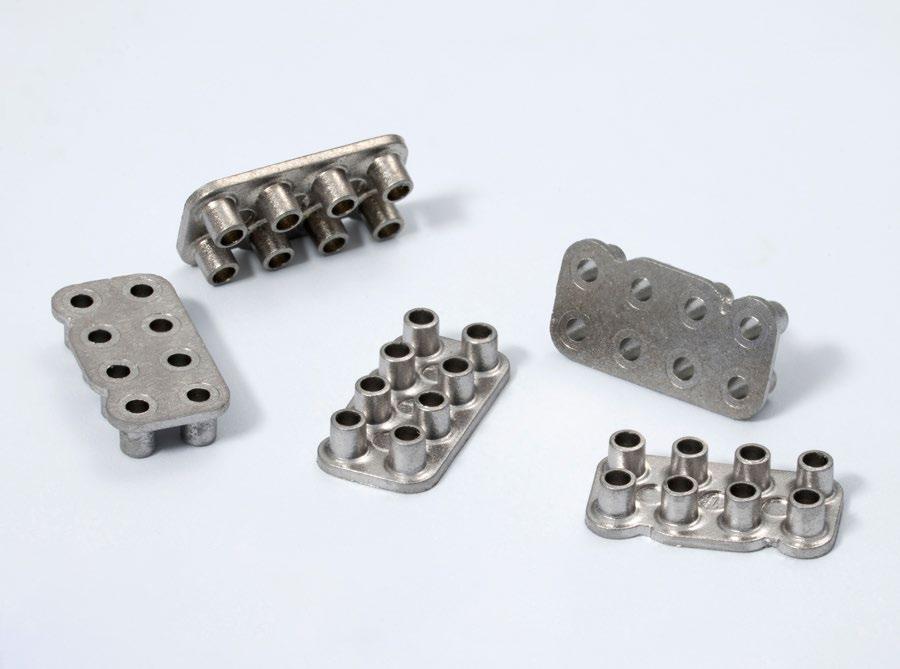
Fig. 3 A 2024 MPIF Design Excellence Awards Grand Prize in the Electronic/ Electrical Components Category for MIM components was awarded to MPP, Noblesville, Indiana, and its customer, Tactile Engineering, Lafayette, Indiana, for MIM core plates used in its Cadence Tablet that has a refreshable braille display for the vision impaired (Courtesy MPIF)
“The medical and firearms sectors continue to be the prime consumers of MIM components, but the demand for firearms has steadily decreased over the past three years. However, general industrial applications and automotive MIM components continue to increase annually.”
equipment. MIM furnace demand continues to grow. Automation is expected to increase as skilled workers become scarcer. There are a considerable number of MIM manufacturers that have a presence in AM, primarily utilising Binder Jetting technology due to its process similarities.
The status of MIM in North America appears to be reflective of the industry worldwide, with all geographic regions facing similar issues and concerns. Most MIM parts
producers anticipate single-digit growth in 2024 with expectations of double-digit growth in 2025 and beyond.
Refractory metals
The Russian-Ukrainian war is still having an impact on the demand for tungsten powder. Several highvolume defence applications utilised by Ukraine and surrounding allies were delayed due to funding in the

Estimate of the amount of PM in a North American passenger vehicle, 2023
second half of 2023. Funding has now been approved for Ukraine and for rebuilding inventory in the US, increasing powder volumes.
To reduce lead times and the dependence on Chinese tungsten, North American companies are trying to source domestically by recycling tungsten waste and developing more tungsten mines. Additionally, Section 301 tariffs and US Department of Defense contract clauses will have more of an impact in 2024 and 2025.
The demand for tungsten carbide cutting tools and wear parts was mixed. Vehicle production was up in 2023 and machining in manufacturing remained about the same. The rest of the wear market was negatively impacted by a continued slowness in oil and gas exploration, coal production, and weaker demand in the housing construction market. It is forecasted that the EV
market will continue to reduce the amount of cutting tools used in the production of vehicles.
North American oil and gas rig counts finished the year down 18% over 2022. At the end of 2023, the North American rig count was 708 compared with a twenty-year average of 1,467 and the most recent five-year average of 712. In 2023, coal production in the US was down 2.9% over 2022 according to the US Energy Information Agency. North American molybdenum powder demand increased in 2023. Molybdenum applications include aerospace, automotive, electronics, defence, industrial, and medical. Demand for these applications continues to remain strong in these growth areas and there are few substitutes available. Ukraine continues to consume these items while the US is trying to rebuild its inventory.
In 2023 and 2024, the industry experienced delays and shortages in raw material supply due to mine closures and reductions in output in Chile, China, and other parts of the world. Molybdenum is often found with copper and as a result can be a by-product of copper refining, typically 50-60% of molybdenum comes from copper refining. China, the largest molybdenum ore contributor, reduced its output in 2022 and 2023; this is expected to continue throughout 2024. These shortages, reduced output, and closures have led to price volatility for molybdenum.
Powder Metallurgy outlook
All manufacturing segments, not just PM, have faced challenges in recent years due to geopolitical uncertainty, supply chain disruptions, changing consumer preferences, and increasing regulatory scrutiny. However, several positive factors, such as rising global demand, ongoing technological advancements, and increasing investment in automation and digitalisation, continue to influence the market, and the outlook for manufacturing remains positive. Manufacturers who can effectively balance cost pressures and maintain a strong focus on quality are likely to survive the current crisis and come out more resilient in the end.
Among the factors that could affect manufacturing in 2024 is the continuing adoption of advanced technology, such as artificial intelligence, robotics, and the Internet of Things (IoT), which have the potential to improve overall efficiency and productivity while reducing costs.
Over 70% of the iron powder shipped in North America is estimated to be used for parts in passenger vehicles. In 2023, approximately 15.5 million passenger vehicles were sold in the US, of which only 3.12 million were sedans. The current consensus is new-vehicle sales will be 15.5-15.8 million units in 2024.
Fig. 4 The estimated average weight in a 2023 North American passenger vehicle remained stable at 15.9 kg (35 lb) (Data MPIF)
Annually, we estimate the amount of PM in a North American passenger vehicle (Fig. 4). The large platform pick-up trucks and SUV passenger vehicles consume an average 24.9 kg (55 lb) per vehicle, followed by the midsize platform crossover vehicles at 13.6 kg (30 lb) and the sedans at 9.1 kg (20 lb). Our best estimate for a PHEV is 6.8 kg (15 lb) and BEV, less the battery, is 2.3 kg (5 lb) of PM. Taking everything into consideration, the estimated average weight in a 2023 North American passenger vehicle remained stable at 15.9 kg (35 lb), the same as 2022.
Sales of EV growth in the US continues to slow. In the first quarter of 2024, just under 270,000 new EVs were sold, 7.3% of all new automobile sales. While annual EV sales continue to grow, the growth rate has slowed considerably. Sales in the first quarter of 2024 rose 2.6% year over year but fell 15.2% compared with the fourth quarter of 2023, the first quarter-over-quarter downturn since the second quarter of 2020.
Previously, PHEV and BEV manufacturers reduced time-to-market at any cost, but are now more cost conscious, opening the door for PM as a solution. This could be the opportunity the PM industry and SMC materials have been seeking, and the MPIF Standards Committee expects to issue its first SMC standards later this year.
Strategic and reshoring production of electromagnet and permanent magnets is a supply chain opportunity for the PM industry, including powder and component production. Development of rare-earth-free magnets would provide a competitive advantage over rare-earth magnets.
PM HIP and metal AM technologies will expand opportunities in aerospace applications. The need for more efficient engines will continue to drive development of higher-strength materials that can operate at higher temperatures. PM superalloys will continue to be used in extremely demanding
applications. Additionally, Oak Ridge National Laboratory and MPIF are collaborating in assessing largescale components via HIP.
As MIM and metal AM continue to be identified as the solution, additional opportunities in the medical market will develop. The medical market encompasses a broad spectrum of sub-markets or segments that include products ranging from dental, cosmetic enhancements, diagnostic equipment, hospital furniture and equipment, implants, medical mobility equipment (i.e. wheelchairs and prostheses) and surgical devices, to first-aid and wound-care products.
Homeland security requirements will drive the development of innovative technologies to meet the detection, energy, lethality, mobility, and protection needs for defence. Advances in security screening (such as X-ray scanning) will continue to make use of tungsten-based collimators and shielding that are processed by PM. Refractory metals will continue to be used in kinetic-energy weapons, hypersonic systems, and for maintaining proper weight distribution in missiles and aircraft.
PM light-weighting is a solution to improve fuel efficiency and enhance mobility. Components with unique combinations of properties may be produced by merging PM processes. Fabrication and repair of parts, both in manufacturing facilities and in the field, may be performed by metal AM technologies.
Computers, farm/off-road equipment, firearms, home appliances, jewellery, lawn and garden, power and hand tools, recreation transportation, sporting goods, and telecommunications, as well as other high-tech industries, will need component solutions as they provide new products and services to consumers.
PM is a resource-efficient alternative to other metal-forming technologies, providing endless opportunities for creating a more sustainable world. Innovative design considers both the strategic advantages of sustainability and
minimising adverse environmental impact. Powder Metallurgy’s sustainable value is primarily derived from its net-shape capabilities and its high material utilisation that minimises energy inputs, reducing the impact on the environment.
As an industry, we need to highlight our strengths and work together to advance the PM technology. We need to invest in R&D to create new applications for metal powders and PM parts. The PM industry will need to continue to invest in the development of our people, acknowledging and valuing their contributions to its success, and encouraging them to share their ideas. The industry must respond to the changing needs and demands of existing and potential customers with agility and ingenuity, while maintaining higher value than competing manufacturing technologies. We have a lot to look forward to as Powder Metallurgy advances.
About the Metal Powder Industries Federation
Metal Powder Industries Federation is the North American trade association formed by the Powder Metallurgy industry to advance the interests of the metal powder producing and consuming industries and provides a single point of reference for all MPIF member companies.
www.mpif.org
About APMI International
APMI International is a non-profit professional society that promotes the advancement of Powder Metallurgy and particulate materials as a science. Its purpose is to disseminate and exchange information about PM and particulate materials through publications, conferences, and other activities of the society.
www.apmiinternational.org

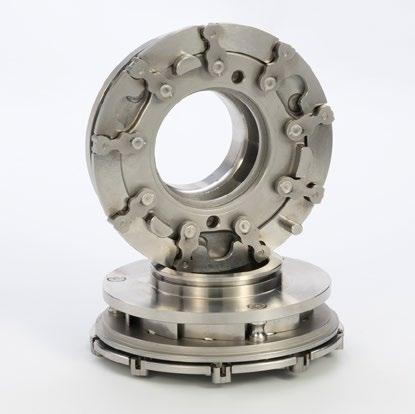
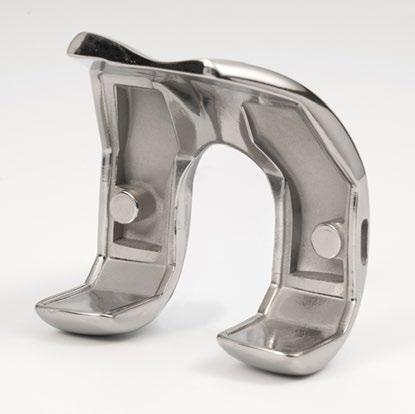
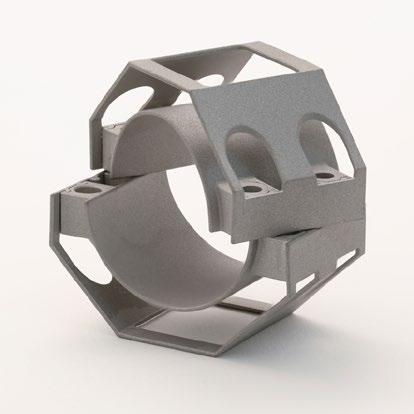
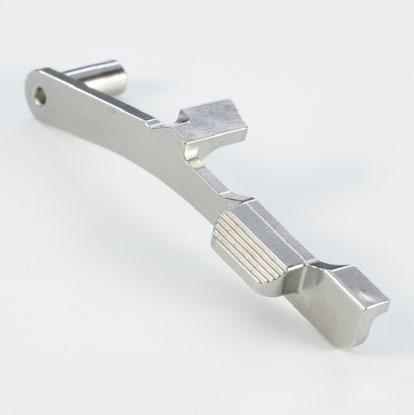
MANUFACTURING INNOVATIONS:
• Part design
• Tooling
• Molding
• Debinding
• Sintering
• Part Inspection
• Secondary Operations
• Simulation
• Competing Technologies
• Coatings
MATERIALS ADVANCEMENTS:
• Metals & alloys
• Ceramics
• Hardmaterials
• Binder Technologies
• Mixing
• Mechanical Properties
TARGETED AUDIENCE:
• Product designers
• Engineers
• End users
• Manufacturers
• Researchers
• Educators
• Students
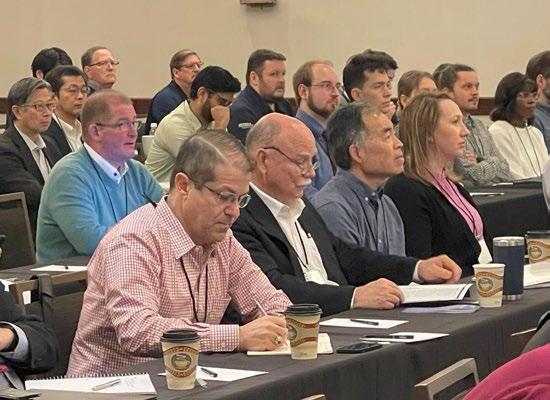
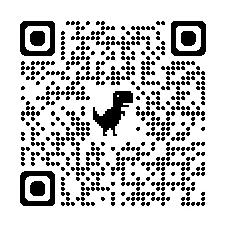

TGTi: The wire that makes
The wire that makes the powder: TGTi’s development of titanium wire feedstock for plasma atomisation
When it comes to titanium powder production for Additive Manufacturing, Metal Injection Moulding and other advanced production processes, plasma gas atomisation is regarded as a gold standard – particularly for demanding applications in the aerospace and medical sectors. The quality of the wire feedstock that is used in the process, of course, directly impacts the quality of the powder that comes out. In this article, Jiangsu Tiangong Technology (TGTi) shares insights into its production processes, its rise to becoming a market leader, and its goal of meeting the needs of the international community.
Plasma gas atomisation is a cutting-edge technology that converts wire into high-purity, fine, spherical powder using supersonic jets of heated plasma. Now industrialised, the technology is considered a gold standard for powder used in Additive Manufacturing (AM) and Metal Injection Moulding (MIM), especially in demanding markets such as aerospace and medical. Early on in its history, titanium was an ideal subject for plasma atomisation due to its high reactivity and relatively high melting point, meaning the newer technology could produce metal powder at a lower cost than conventional methods. Any companies developing and exploiting plasma atomisation technologies are necessarily dependent on the quality of their wire supply – think of the adage ‘garbage in, garbage out.’
Jiangsu Tiangong Technology (TGTi) produces 10,000 tons of wire annually and employs 600 people, mainly serving powder producers
in markets such as aerospace, as well as some of the best-selling international smartphone companies. TGTi is the titanium division of the global Tiangong International (TG), among the top five high-speed steel producers in the world. The main product for TGTi is wire.
A founder’s vision underscores that of his company
TG founder, Zhu Xiaokun, is known to have a relentless work schedule even into his 70s, often leaving the company’s headquarters at 11.30

Fig. 1 A view of the TGTi facility (Courtesy TGTi)
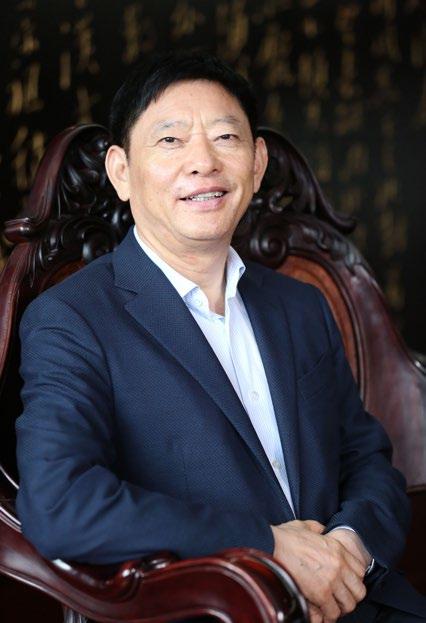
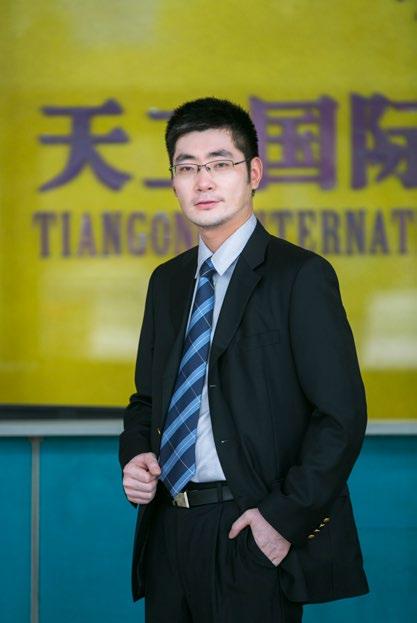
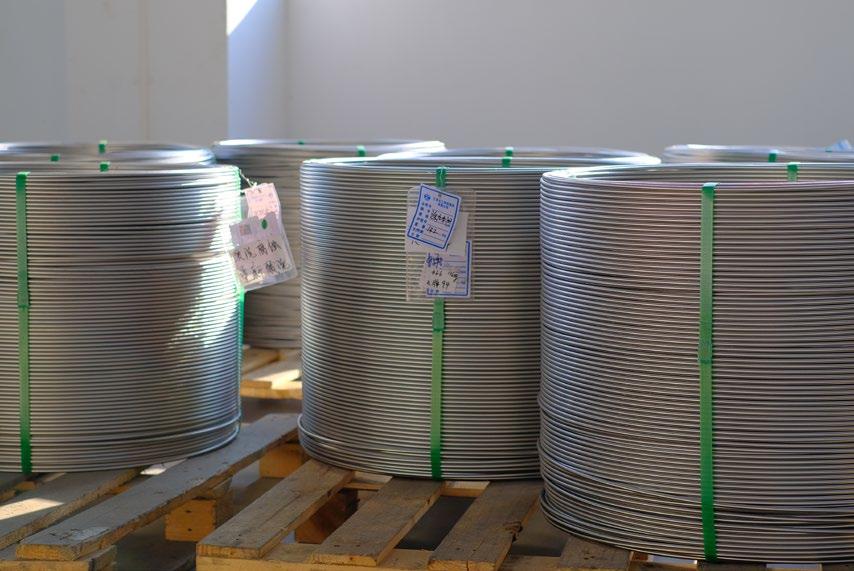
“The company leverages advanced machinery and technology from around the world, ensuring that its production processes are state-of-the-art. This focus on high-quality foreign technology, operated within China, has allowed TGTi to maintain a competitive edge.”
PM and returning early the next day. From his desk in the lobby, Zhu makes himself available to any employees with issues to bring to his attention.
This dedication stems from a mission larger than himself. Starting a company in a rural village of farmers in China with just a few hundred dollars, Zhu built an empire beyond what anyone could have imagined; his home village has transformed into a thriving city thanks in large part to Tiangong. Zhu’s mantra of ‘Work hard, and hard again, or you might fall into poverty again’ underscores his keen memory of the company’s – and his own – origins. Today, TG employs over 3,600 people and occupies a total combined facility area of 1.3 million m². If you have ever bought drill bits at a hardware store, there’s a good chance they were made by Tiangong.
When listening to Zhu speak, he often shares the principles that have kept TG going as part of conversation, highlighting, for example, the need to prepare, set up and reorganise during downtimes or times of crises, so that the company emerges stronger than before. Principles such as these are also those on which TGTi was founded.
TGTi is helmed by Zhu Zhefeng, the son of Zhu Xiaokun. The principles and values that propelled TG to success have been integrated into TGTi’s operations in an effort to ensure a continuity of excellence and innovation.
With a deep understanding of the industry, Zhu Zhefeng is following in his father’s footsteps and steering the company towards new heights. The workforce is led by General Manager Jiang Ronnie, who has been with TG from its early years, ensuring that the company’s core values are upheld.
The company leverages advanced machinery and technology from around the world, ensuring that its production processes are state-ofthe-art. This focus on high-quality foreign technology, operated within China, has allowed TGTi to maintain
Fig. 2 TG’s founder, Zhu Xiaokun, (left) and, his son (right), Zhu Zhefeng (Courtesy Tiangong International/TGTi)
Fig. 3 Titanium wire for plasma gas atomisation is an important market for TGTi (Courtesy TGTi)
TGTi: The wire that makes the powder
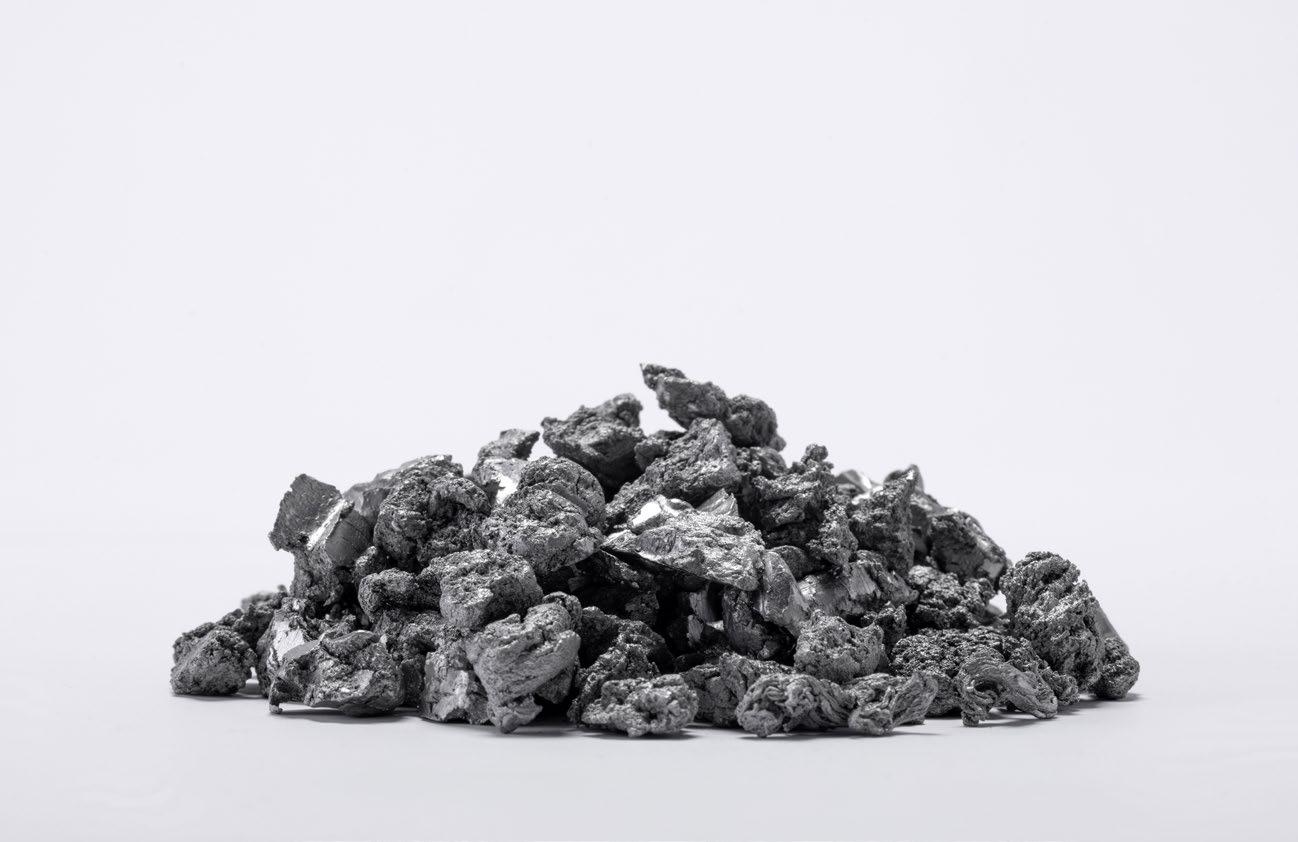
a competitive edge. The company embodies a culture of relentless improvement, constantly striving to refine processes and enhance product quality. A focus on continuous improvement ensures that the company remains agile and resilient in a fast-paced industry, able to adapt quickly to market changes. As a whole, Chinese factories are known for their productivity. TGTi adheres to these expectations whilst maintaining a stringent focus on quality. The company’s commitment to excellence is reflected in its high standards and continuous pursuit of innovation.
TGTi’s wire production
TGTi’s strength lies in its advanced capabilities and extensive production capacity, making it a formidable player in the titanium industry. The company has invested heavily in state-of-the-art equipment and facilities to ensure it can meet the demanding needs of its clients.
“The production process begins with a fully automated sponge mixing system, which meticulously measures and blends the high purity Ti sponge in a clean, controlled environment, ensuring consistent quality from the very start.”
The production process begins with a fully automated sponge mixing system, which meticulously measures and blends high purity Ti sponge in a clean, controlled environment, ensuring consistent quality from the very start. It is mixed with a master alloy to reach the desired Ti-6Al-4V (Grade 5) composition. Contamination is primarily prevented at the sponge mixing stage. There is a magnetic separator, as well as a colour-based separator,
which together eliminate anything that does not have the right composition or appearance. Sponge mixing is done under a controlled atmosphere, and the mixer itself is isolated from ambient air.
The mixed sponge is then compressed into compacts using high-quality presses, ready for the next stage of production. The process has resulted in a clear improvement in the compaction quality compared to past practice, primarily because

Fig. 4 The Ti sponge used in the wire production process (Courtesy TGTi)
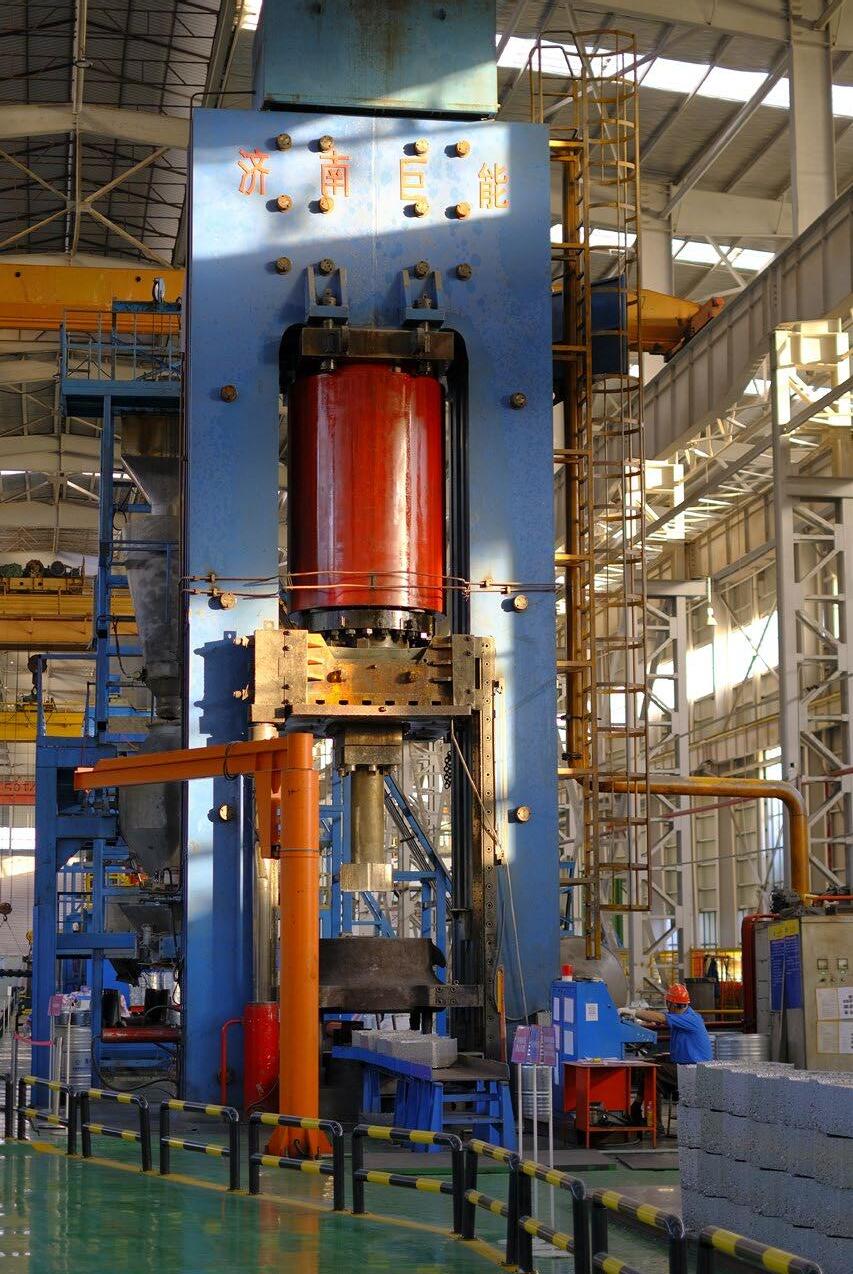
“Compaction pressure is very high, using 5000 to 7000 MT hydraulic press technology, which ensures that the master alloy and the sponge are well combined and can be transported without deterioration to the next stage.”
overly compressed sponges tend to be shinier, and are now being rejected, resulting in a more homogeneous compact.
Compaction pressure is very high, using 5000 to 7000 MT hydraulic press technology, which ensures that the master alloy and the sponge are well combined and can be transported without deterioration to the next stage. This is especially important for chemical composition.
One of the unique aspects of TGTi is its extensive use of Vacuum Arc Remelting (VAR) technology. The company boasts numerous sets of VAR equipment in various capacities: 1.5 tons, 3 tons, and 11.5 tons. Specifically, TGTi operates ten sets of 1.5-ton VARs, two sets of 3-ton VARs, and six sets of 11.5-ton VARs. This extensive array of equipment allows TGTi to produce a remarkable 600 metric tons of titanium wire and 2,000 metric tons of bar annually.
Three different sizes of crucibles are used, and typically larger ingots/ VAR crucibles require three melts to reach satisfactory homogeneity. The company, however, favours 1.5 ton size because this provides superior homogeneity with only two melts.
In the wire production process, TGTi employs specialised equipment for size reduction that uses rollers in series instead of forcing the wire through a die. This method creates less stress on the wire, enhancing its quality. Additionally, the company uses an advanced Italian-made continuous annealing system under argon, which further ensures a more uniform and consistent wire in terms of mechanical properties compared to traditional vacuum annealing. A wire size reduction system, from the same Italian supplier, uses rolls to progressively reduce the size without creating tension, as opposed to forcing the wire through dies.
TGTi also boasts in-house forging capabilities, including a GFM 750 T precision forging machine and an SMS Meer 1300 T precision forging machine. These machines allow TGTi to maintain stringent control over the forging process, ensuring the highest quality standards.
Fig. 5 A press used to make the Ti sponge/master alloys compacts (Courtesy TGTi)
Complementing its production capabilities, TGTi maintains an in-house laboratory for internal quality control purposes. Although the lab is not ISO-certified, it plays a crucial role in maintaining the company’s high quality standards. By integrating advanced technology and maintaining a focus on quality, TGTi ensures it can meet the rigorous demands of the aerospace industry, particularly in the realm of metal Additive Manufacturing. Standards are defined by the supplier for each element, and for each analysis, which are always ASTM standards for Aerospace in North America, such as ASTM E2371, ASTM E1941, ASTM E1409-13 , ASTM E1447-09, ASTM E384, ASTM E8, ASTM E112.
Rebranding for the Western market
For many Western companies, the prospect of auditing suppliers in China can be daunting. Language barriers, cultural differences, and the logistical challenges of international travel often create significant friction. Recognising these obstacles, TGTi has embarked on a rebranding effort aimed at making the company more accessible and appealing to the Western market.
A central goal of this rebranding initiative is to increase transparency to a level where clients feel as though they have already visited the facility before setting foot in it. This involves not only improving communication but also providing detailed insights into TGTi’s operations, capabilities, and quality control measures.
Jeff Zhu, the chairman of TGTi, emphasises the importance of this approach, “Communication with Chinese suppliers for wire and their qualification used to be very painful. My intent is to reduce that friction to a minimum, where it is actually simpler to deal with us than anyone else, because I know exactly what powder producers are looking for.”
To bridge the gap caused by China’s isolated internet infrastruc -
TGTi: The wire that makes the powder

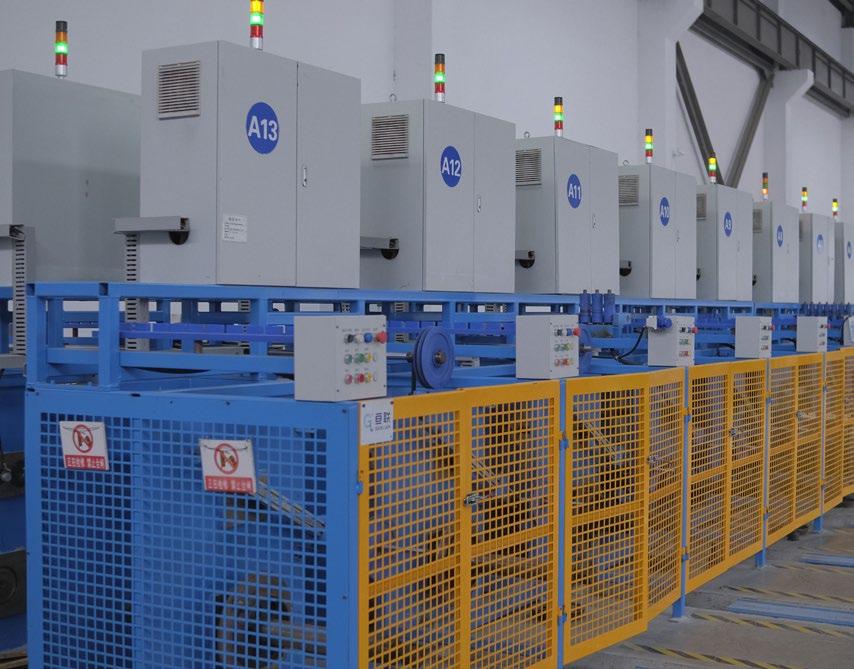
ture, TGTi has established a strong LinkedIn presence and built a new website entirely in English. The website aims to be as transparent as possible, featuring extensive pictures of the actual equipment and detailed explanations of the wire manufacturing process. Unlike many websites that use stock images, TGTi showcases real photos to give
potential clients a genuine feel for the facility before they even consider an audit.
TGTi also strongly encourages customers to visit its facilities. The company has translated its quality documentation into English and simplified the auditing process to accommodate Western clients. Given the rigorous auditing requirements

Fig. 6 Vacuum Arc Remelting (VAR) sets at TGTi (Courtesy TGTi)
Fig. 7 An in-line annealing system (Courtesy TGTi)
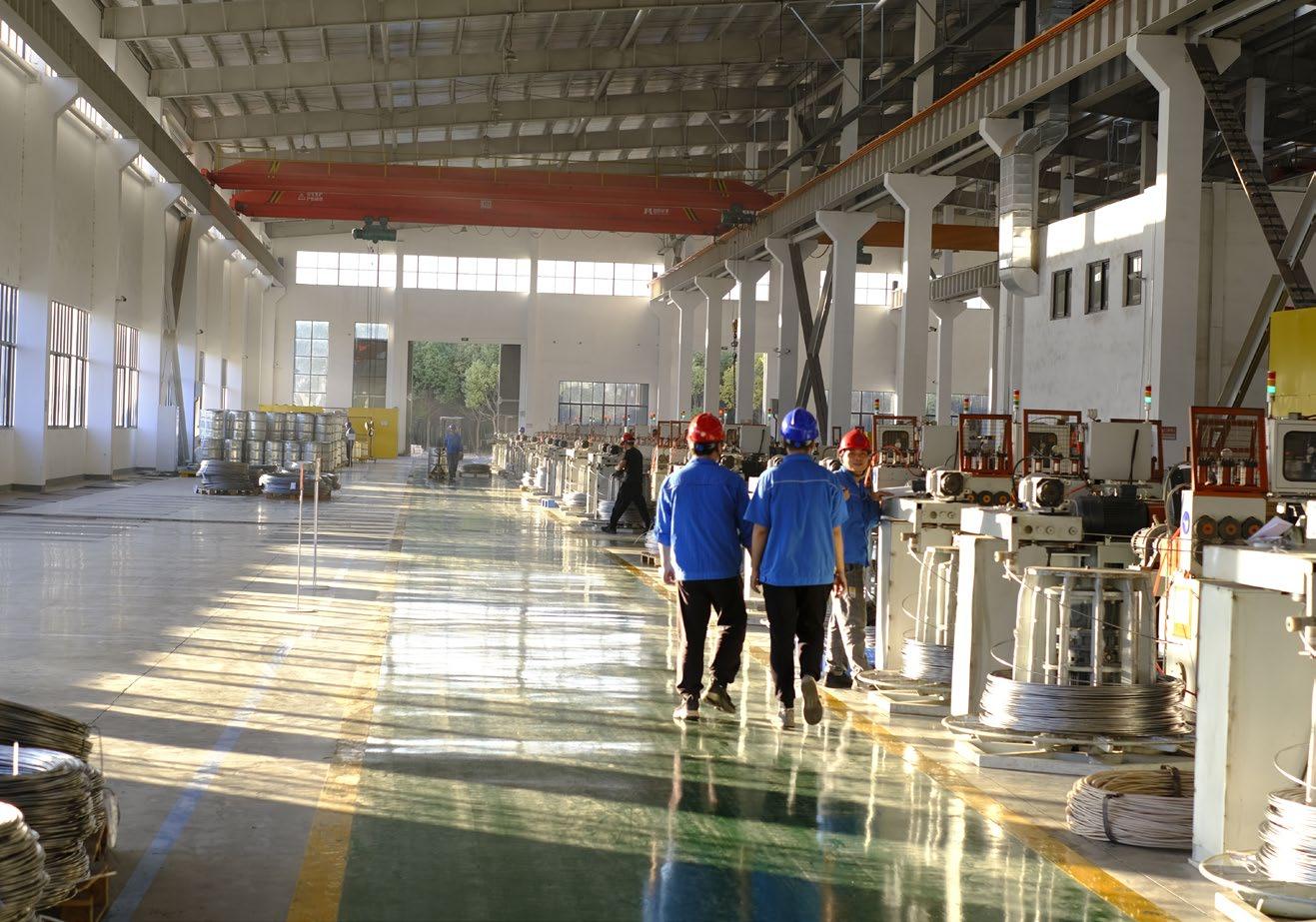
“As Additive Manufacturing continues to grow at an impressive rate, TGTi is positioning itself to meet the increasing demand for high-quality titanium wire. The company sees significant opportunities for improvement, not only in terms of pricing but also in delivering superior quality.”
of the aerospace industry, TGTi invites clients to review documentation, tour the facilities, and ask any questions they may have.
As Additive Manufacturing continues to grow at an impressive rate, TGTi is positioning itself to meet the increasing demand for highquality titanium wire. The company sees significant opportunities for
improvement, not only in terms of pricing but also in delivering superior quality.
Over the past two decades, plasma atomisation technologies have evolved from R&D prototypes to full-scale production technologies. As this technology matures, prices are trending downward, and powder producers are now aiming
for near-continuous 24/7 operations. To achieve this, they need reliable suppliers who can provide consistent, high-quality materials. TGTi is prepared to meet these needs, ensuring a robust supply chain.
Quality and continuous improvement
At the core of TGTi’s operations lies an unwavering commitment to quality and continuous improvement. This dedication is not just a company mantra but a deeply ingrained culture that drives every aspect of business.
TGTi understands that in the competitive world of aerospace and Additive Manufacturing, the margin for error is incredibly slim. Founder Zhu Xiaokun once remarked, “Because of low margins, a defective part produced requires ten defectfree parts to compensate for it.” This philosophy underscores the high
Fig. 8 A view of the wire size reduction facility (Courtesy TGTi)
cost of low quality, something often echoed by powder producers who emphasise that even a single defect can have significant repercussions.
To ensure exceptional quality, TGTi employs a rigorous quality control system. This begins with their advanced production facilities, which utilise state-of-the-art equipment sourced from around the world. From the fully automated sponge mixing system to the precision forging machines, every step of the production process is designed to minimise errors and enhance product integrity.
TGTi’s in-house laboratory, although not ISO-certified, plays a crucial role in internal quality control. The lab is equipped with advanced testing and analysis tools, allowing the company to conduct thorough inspections and maintain strict quality standards. This commitment to quality is further reinforced by the company’s AS9100D certification (Bureau Veritas), a testament to their adherence to aerospace industry requirements.
Continuous improvement is another cornerstone of TGTi’s success. The company fosters a culture of innovation and efficiency, constantly seeking ways to refine their processes and improve product quality. This relentless pursuit of excellence ensures that TGTi remains at the forefront of the industry, capable of adapting to market changes and meeting the evolving needs of their clients.
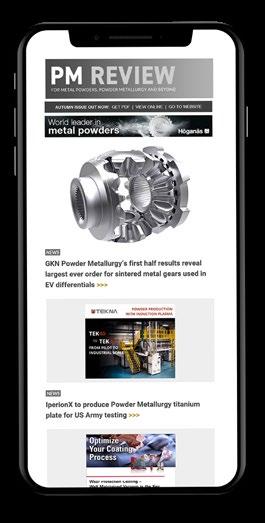

TGTi: The wire that makes the powder
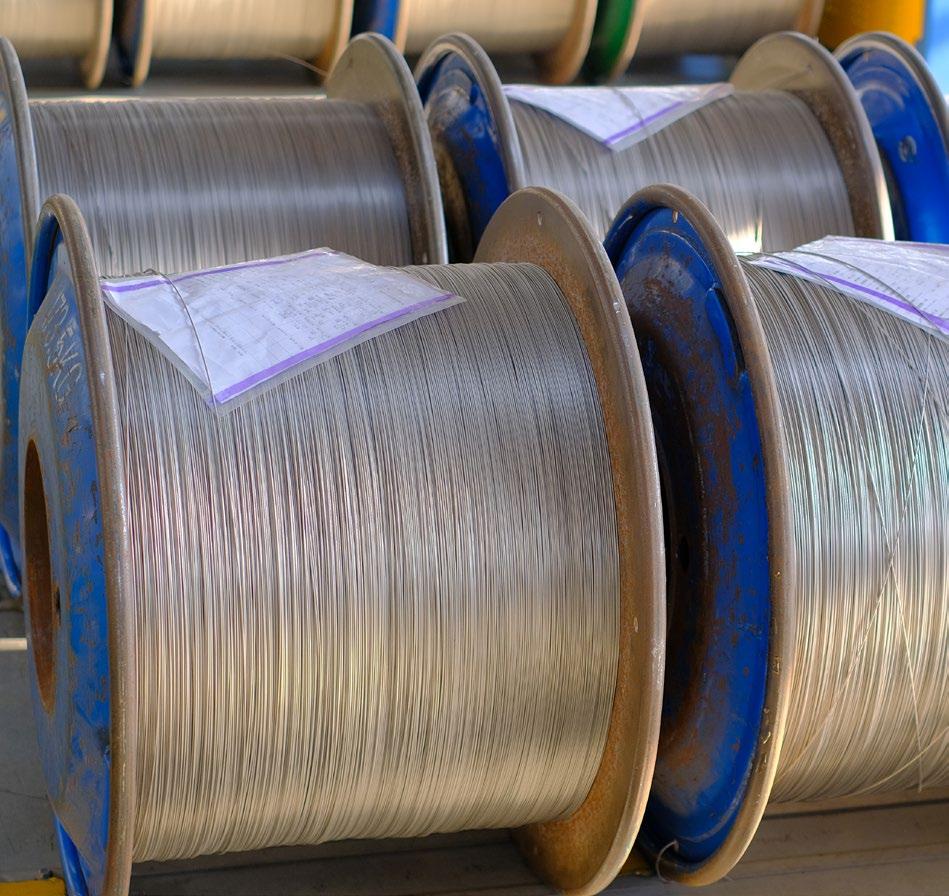
The leadership at TGTi, led by Zhu Zhefeng, and General Manager Jiang Ronnie, emphasises the importance of teamwork and a unified effort. By instilling a sense of responsibility and promoting a collaborative environment, they ensure that every employee is committed to the company’s goals. This collective drive for excellence is what sets TGTi apart from its competitors.
Contact
Christopher A. Dion, Eng., M.A.Sc. Director of International Operations
TGTi: Tiangong Titanium cdion@tiangongti.com www.tiangongti.com

Fig. 9 Wire ready for shipping to plasma gas atomised powder producers (Courtesy TGTi)
Advertisers’ index & buyer’s guide
Our advertisers’ index and buyer’s guide serves as a convenient guide to suppliers across the PM supply chain. In the digital edition of PM Review magazine, available at www.pm-review.com, simply click on a company name to view its advert, or on the company’s weblink to go directly to its website.
shmengda.cn/english.php

COMPACTION PRESSES, TOOLING
Dorst Technologies
www.dorst.de Erowa AG
www.erowa.com
Huacheng Moulding (Changshu) Co. Ltd 38 www.szhcjm.com
Maschinenfabrik Lauffer GmbH & Co. KG 15 www.lauffer.de
Osterwalder AG 23 www.osterwalder.com
PVA TePla AG
www.pvatepla.com
SACMI Imola
www.sacmi.com
www.system3r.com
www.europm2024.com
www.formnext.com
www.mim2025.org
PM China 2025
en.pmexchina.com
PowderMet2025 / AMPM2025 62 www.powdermet2024.org / www.ampm2024.org
The Magnectics Show Europe
www.magnetics-eu.com
World PM2024
www.worldpm2024.com
Advertise with us...
Combining digital and print publishing for maximum exposure
Reach out to our rapidly expanding international audience that includes component manufacturers, end-users, industry suppliers, analysts, researchers and more. For more information contact: Jon Craxford, Advertising Sales Director Tel: +44 207 1939 749 jon@inovar-communications.com
PM Review is dedicated to driving awareness and development of Powder Metallurgy and its related technologies. Key to this aim is our support of a range of international conferences and events. View our complete events listing on www.pm-review.com
2024 2025 Industry events
The Atomising Systems Course on Atomization for Metal Powders
September 26–27 – Manchester, UK www.atomising.co.uk/news
Euro PM2024
September 29 – October 2 – Malmö, Sweden www.europm2024.com
The Advanced Materials Show USA
October 8–9 – Pittsburgh, PA, USA www.advancedmaterialsshowusa.com
World PM2024
October 13–17 – Yokohama, Japan www.worldpm2024.com
Advanced Engineering
October 30–31 – Birmingham, UK www.advancedengineeringuk.com
MSIT Seminar on Rare-Earth Materials & Magnet Technology
November 12–13 – Stuttgart, Germany www.msiport.com/msit-events/seminar-onmagnet-technology/seminar-2024/
Formnext
November 19–22 – Frankfurt, Germany www.formnext.com
FPM 42 nd Hagen Symposium
November 28–29 – Hagen, Germany www.pulvermetallurgie.com/symposiumtermine/symposium-aktuell/
The Magnetics Show Europe
December 3–4 – Amsterdam, Netherlands www.magnetics-eu.com
Looking for an event partner?
International Conference on Injection Molding of Metals, Ceramics, and Carbides (MIM 2025)
February 24–26 – Costa Mes CA, USA www.mim2025.org
PM China
March 10–12 – Shanghai, China en.pmexchina.com
RAPID + TCT 2025
April 8–10 – Detroit, MI, USA www.rapid3devent.com
Formnext Chicago April 8–10 – Chicago, IL, USA www.formnextchicago.com
International Critical Minerals Expo & CMI
Summit IV May 14–15 – Pasadena CA, USA www.mineral-expo.com
The Magnetics Show USA May 14–15 – Pasadena CA, USA www.magnetics-show.com/home1
PowderMet 2025 / AMPM 2025
June 15–18 – Phoenix, AZ, USA www.powdermet2025.org www.ampm2025.org
EMO Hannover 2025
September 22–27 – Hannover, Germany www.deutschemesse.co.uk/emo
PM Review collaborates with a variety of Powder Metallurgy and associated events throughout the year, ranging from major trade shows to smaller technical conferences and seminars. If you would like to partner with us for your event, contact Merryl Le Roux: merryl@inovar-communications.com
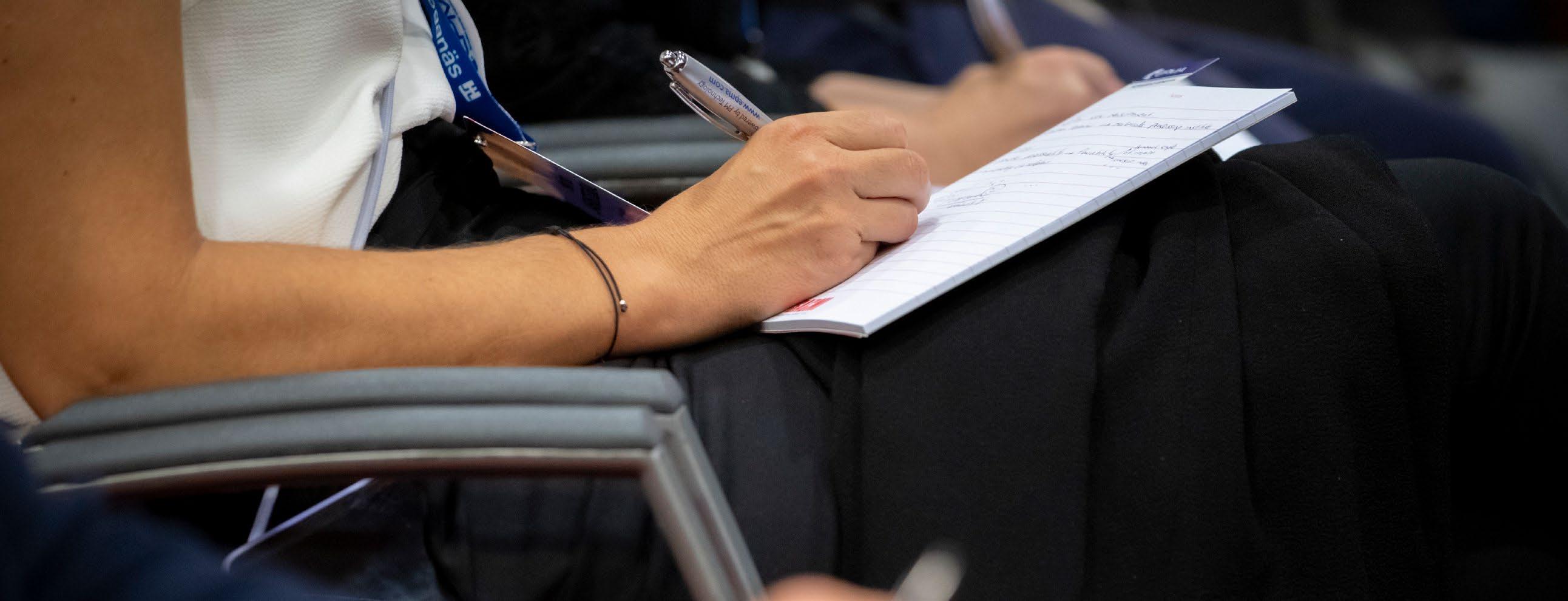
REGISTER NOW
Organised by:
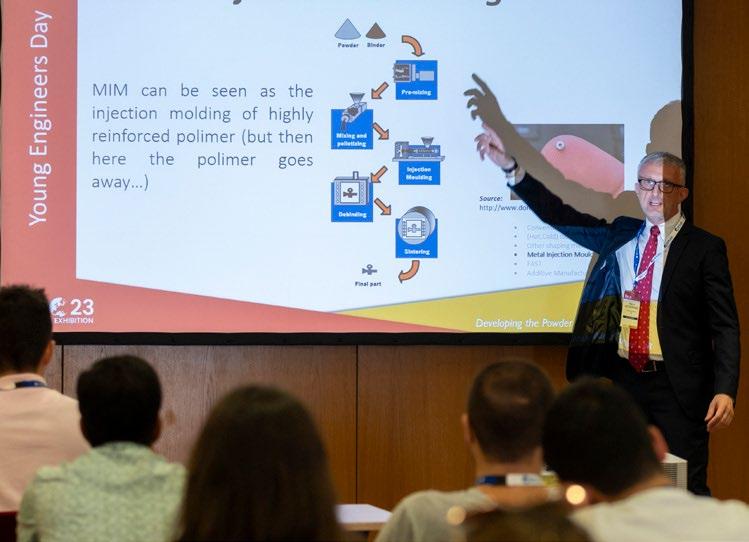
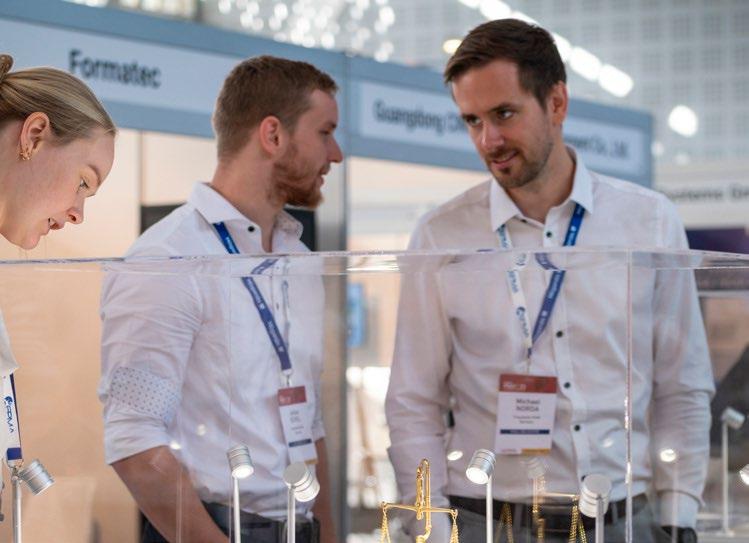

EXHIBITION CONGRESS
Dive into the heart of the PM industry at Euro PM2024, where industry leaders, academics, and professionals converge.
With 250 presentations over three days, including Keynote paper presentations and Special Interest Seminars, this event promises to redefine industry standards and unveil the latest PM advancements.
Explore the latest trends and advancements in PM as you connect with industry-leading suppliers, engage with potential clients, and discover cutting-edge PM solutions
New this year: Micro stands can be reserved by new exhibitor at the Euro PM2024 and the Exhibition will provide an area dedicated to showcasing Sweden’s PM industry!
SOCIAL MEETING
Embark on a journey to meet the driving forces behind powder metallurgy technology, industry and innovation at Euro PM2024.
Don’t miss out the opportunity to attend our social events: The Welcome reception on Sunday evening, the poster reception on Monday and the congress dinner at Slagthuset on Tuesday.
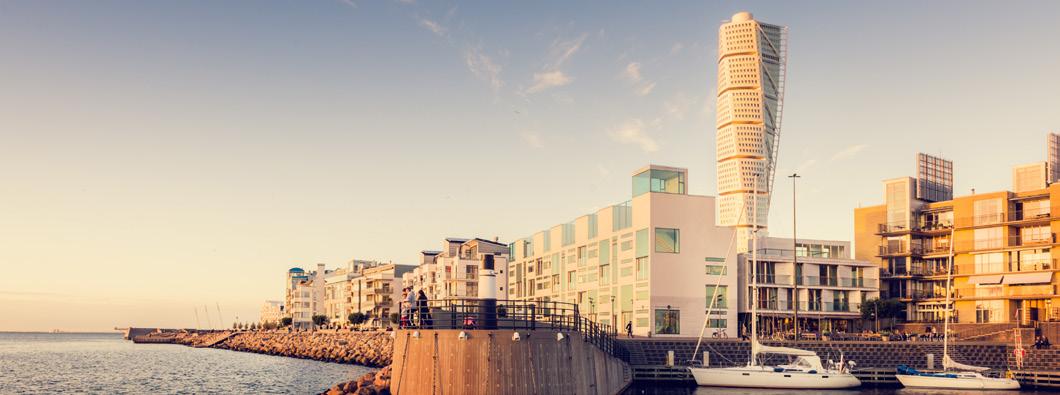


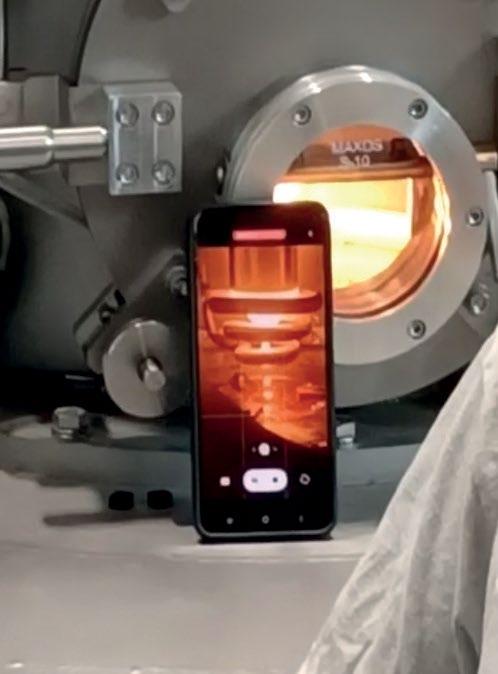
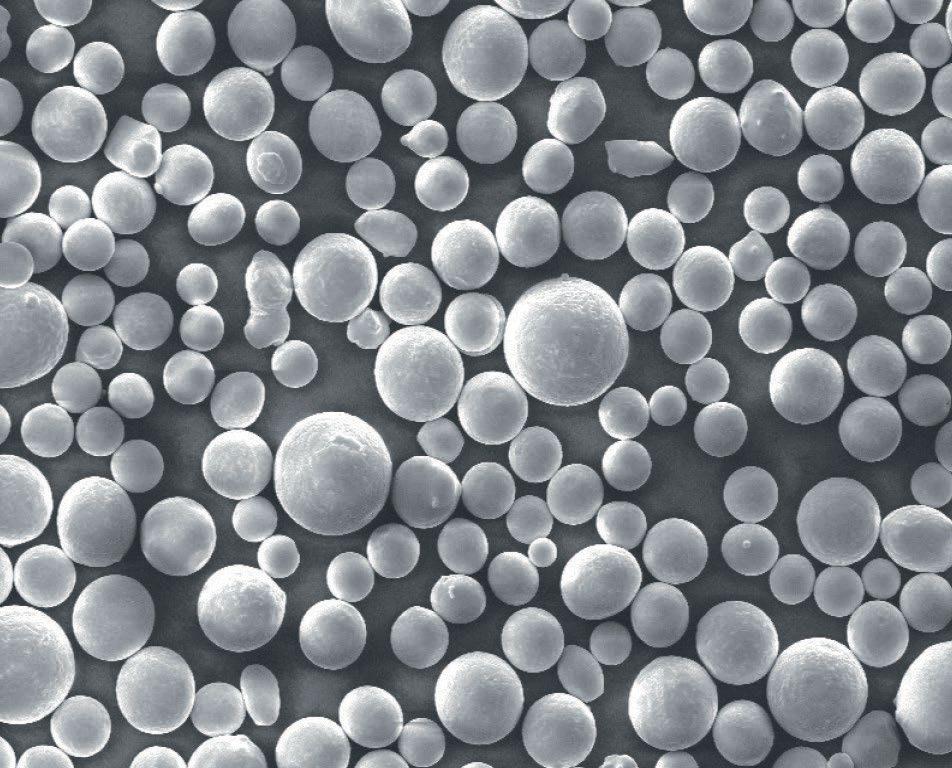
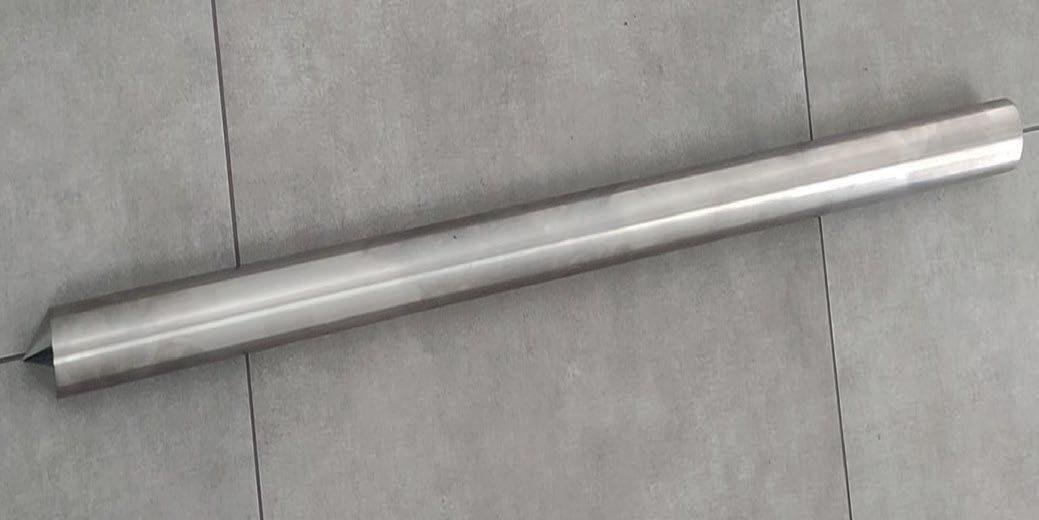
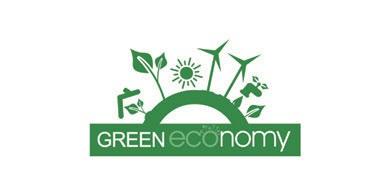