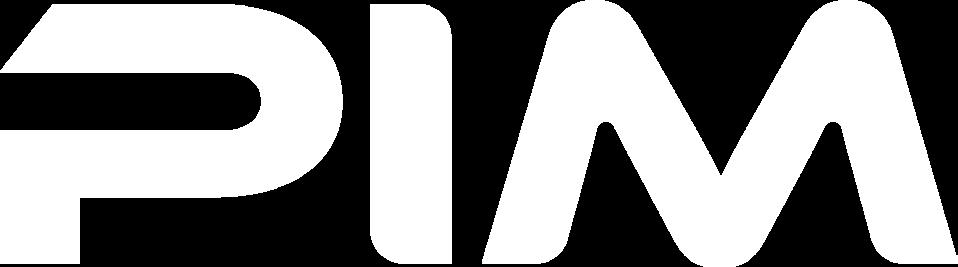


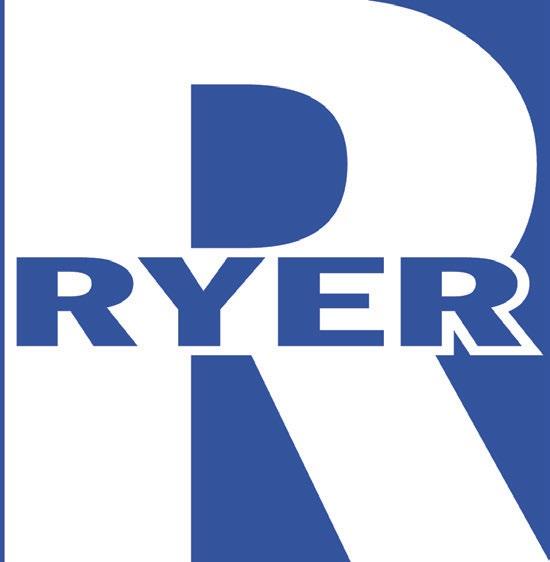
• At RYER, all our feedstocks are manufactured to the highest level of quality, with excellent batch-to-batch repeatability.
• RYER is the ONLY commercially available feedstock manufacturer to offer all five debind methods.
• RYER offers the largest material selections of any commercially available feedstock manufacturer.
• RYER offers technical support for feedstock selection, injection molding, debinding and sintering.
• A direct replacement for all current commercially available catalytic debind feedstocks
• Improved flow
• Stronger green and brown parts
• More materials available and better surface finish
• Custom scale-up factors available
• Faster cycle times
• 65°C / 150°F mold temperature
• Water Debind
• Custom scale-up factors available
• Large selection of available materials
• Solvent, Super Critical Fluid Extraction (SFE) or Thermal Debind methods
• Hundreds of materials available
• Custom scale-up factors available
Publisher & Editorial Offices
Inovar Communications Ltd
11 Park Plaza
Battlefield Enterprise Park
Shrewsbury SY1 3AF
United Kingdom
Tel: +44 (0)1743 469909 www.pim-international.com
Managing Director & Editor
Nick Williams, nick@inovar-communications.com
Group News Editor
Paul Whittaker, paul@inovar-communications.com
Advertising Sales Director
Jon Craxford
Tel: +44 (0)207 1939 749 jon@inovar-communications.com
Assistant Editor
Amelia Gregory, amelia@inovar-communications.com
Assistant News Editor
Charlie Hopson-VandenBos charlie@inovar-communications.com
Digital Marketer
Mulltisa Moung, mulltisa@inovar-communications.com
Production Manager
Hugo Ribeiro, hugo@inovar-communications.com
Operations & Partnerships Manager
Merryl Le Roux, merryl@inovar-communications.com
Office & Accounts Manager
Jo Sheffield, jo@inovar-communications.com
Technical Consultant
Dr Martin McMahon
Consulting Editors
Prof Randall M German
Former Professor of Mechanical Engineering, San Diego State University, USA
Dr Yoshiyuki Kato
Kato Professional Engineer Office, Yokohama, Japan
Professor Dr Frank Petzoldt
Ingenieurbüro Dr. Petzoldt, Geestland, Germany
Dr David Whittaker
DWA Consulting, Wolverhampton, UK
Bernard Williams
Consultant, Shrewsbury, UK
Subscriptions
PIM International is published on a quarterly basis as either a free digital publication or via a paid print subscription. The annual print subscription charge for four issues is £150 including shipping.
Accuracy of contents
Whilst every effort has been made to ensure the accuracy of the information in this publication, the publisher accepts no responsibility for errors or omissions or for any consequences arising there from. Inovar Communications Ltd cannot be held responsible for views or claims expressed by contributors or advertisers, which are not necessarily those of the publisher.
Advertisements
Although all advertising material is expected to conform to ethical standards, inclusion in this publication does not constitute a guarantee or endorsement of the quality or value of such product or of the claims made by its manufacturer.
Reproduction, storage and usage
Single photocopies of articles may be made for personal use in accordance with national copyright laws. All rights reserved. Except as outlined above, no part of this publication may be reproduced or transmitted in any form or by any means, electronic, photocopying or otherwise, without prior permission of the publisher and copyright owner.
Design and production
Inovar Communications Ltd.
ISSN: 1753-1497 (PRINT)
ISSN: 2055-6667 (ONLINE) © 2024 Inovar Communications Ltd.
It’s interesting how quickly conversations can shift from debating when sinter-based AM technologies might find commercial success to celebrating real-world applications, many with noteworthy production volumes.
Two companies featured in this issue of PIM International exemplify this shift in the conversation. Take Azoth, a company solely focused on the sinter-based AM production of metal parts, chiefly in the automotive sector. It now has over fifty PPAP (Production Part Approval Process)approved parts in production for two OEMs and ten Tier 1 suppliers.
Bosch Advanced Ceramics is also making strides in the ceramic AM sector. Here, we highlight a micro-ceramic application that is now enjoying production volumes of 50,000 parts a year, with a remarkable 1,400 parts squeezed onto each build platform. The fact that the application’s walls are a mere 90 µm thick tells us all we need to know about the level of process control achieved.
Of course, this shift in the conversation can only happen when end-users allow their applications to be shared. I have no doubt that there are many more successes out there, but if they never see the light of day, then the industry’s progress will be hampered by unnecessary hesitation about the technology on the part of its potential users.
Nick Williams Managing Director & Editor
Cover image
A seatbelt pillar adjustable guide loop produced by Azoth for General Motors (Courtesy MPIF/General Motors)
SIMPLIFY YOUR SINTERING
Affordable, state-of-the-art furnace designed as a total industry solution – not just for sinter-based AM, but also for PM, MIM, and other sectors that could benefit from a compact, highpurity vacuum furnace for combined debinding and sintering.
Breakthrough, patentpending furnace design features a vacuum retort and delivers parts-perbillion levels of purity
Heating elements and insulation are located outside vacuum retort so oxygen, water vapor, and binder cannot contaminate sintering environment
Ti-tested™, delivering better Ti6Al4V performance results for density, tensile strength, and elongation*
More than a dozen fans cool from 1,420°C to 200°C in <4H without watercooled walls
Airtight design and efficient cooling dramatically lower operating costs
Compact footprint and automated, vertical hood enables access to 15.8L retort
*With Ti6Al4V, the PureSinter furnace delivered higher part density — greater than 98% — than a popular, premium third-party vacuum furnace with much less power, in addition to other performance benefits. See complete PureSinter brochure for more details.
PureSinter delivers the highest quality sintered parts, on par or better than industrial furnaces with higher acquisition and operating costs. Even titanium can be easily sintered with a high degree of confidence without the complex preparations and getter materials required with other furnace. SINTERING INNOVATION
Download the brochure and see the video at teamdm.com/puresinter
67 Azoth: Driving the acceptance of sinter-based Additive Manufacturing in the automotive industry and beyond
Everyone had high expectations of Binder Jetting. Of all the metal Additive Manufacturing processes, it suffered from the most hype. What transpired was the realisation amongst machine vendors that it was harder than expected to ‘get it right’. However, while public success stories are few and far between, progress is being made.
Azoth is one company that has successfully embraced Binder Jetting, along with related sinter-based AM processes. With a ‘feet firmly on the ground’ approach, and a base near Detroit, it has found commercial success in the automotive industry and beyond. Bernard North reports on a recent visit. >>>
81 Ceramic AM at scale: How Bosch Advanced Ceramics produced 1,400 MedTech parts with 90 µm wall thickness in a single batch
Bosch Advanced Ceramics is a global leader in the production of technical ceramics, serving a variety of industries from automotive to medical devices and the chemical industry. Today, the company sees a bright future in ceramic Additive Manufacturing for the series production of parts in increasingly ambitious volumes.
This article will present a case study that clearly demonstrates how, using Lithoz’s AM technology, Bosch Advanced Ceramics has been able to develop a micro-sized medical device component that is now in production with an annual run of 50,000 parts. >>>
89 Elnik: Relocation and expansion as a leading MIM furnace maker prepares for the rise of sinter-based Additive Manufacturing
Vacuum debinding and sintering furnaces from Elnik Systems LLC are a common sight in Metal Injection Moulding plants throughout Europe and the Americas. Thanks in part to the technical guidance and training available through its sister company, DSH Technologies, Elnik Systems’ market-leading position has seen it support a multitude of new manufacturing operations.
Now, with the rise of sinter-based Additive Manufacturing, the need to meet the high demand for the company’s products has driven a relocation and major expansion. Nick Williams reports for PIM International >>>
101 MPIF Design Excellence Awards: New MIM and sinter-based Additive Manufacturing applications in the spotlight
Metal Injection Moulding is one of the most capable manufacturing processes for small precision components, yet it is also one of the least well known.
This article presents 2024’s awardwinning MIM parts from the Metal Powder Industries Federation’s PM Design Excellence Awards. In addition, we also highlight the growing number of award-winning parts produced by sinter-based Additive Manufacturing.
These examples present an opportunity for product designers and engineers to consider how they might use MIM and AM in their own projects. >>>
111 Advertisers’ index & buyer’s guide
Discover the leading suppliers of materials and equipment for MIM, CIM and sinterbased AM, as well as part manufacturing partners and more. >>>
View a list of upcoming events for the MIM, CIM & sinter-based AM industries. >>>
The PIM International newsletter is sent to several thousand industry professionals worldwide. Register today to ensure you benefit from reading the latest industry news and advances in Metal Injection Moulding, Ceramic Injection Moulding and sinter-based AM technologies.
www.pim-international.com/e-newsletter
Callaway Golf, based in Carlsbad, California, USA, has introduced a new range of golf clubs manufactured using Metal Injection Moulding. The Opus Platinum Chrome Wedges, launched earlier this year, feature tungsten elements that are reported to provide more ball control and spin for the golfer.
MIM construction is said to have opened the door for Callaway to deliver precision in wedge construction, enabling the company
to adjust the touch and feel to better suit players. The Opus Platinum wedge uses tungsten high in the top line of the clubface for a lower launch and more controlled flight.
The ‘Spin Gen Face’ technology, incorporated in the club design,
Alfa MIMtech, based in Éibar, Basque Country, Spain, reports that it is using Metal Injection Moulding to produce guitar saddles. The MIM process is enabling the company to achieve the
exceptional geometric accuracy and quality required, meeting the highest industry standards.
Guitar saddles play a crucial role in the performance of musical instru -
has a tighter pitch which puts more grooves on the face. It also has offset groove-in-groove for spin when opening the face and a new aggressive face blast that provides spin and bite on partial shots. www.callawaygolf.com
ments. They are responsible for holding and allowing precise height and length string adjustments, which is essential for the tuning and action of the instrument.
Correct manufacturing of these parts ensures that each string is correctly supported, reducing friction and improving vibration transmission.
Alfa MIMtech stated that its guitar bridge parts fit into their holders without the need for additional adjustments. They also have a superior surface finish that provides increased durability and wear resistance, crucial factors in maintaining aesthetic appeal, intonation and sound quality over time.
In the development of the guitar saddles, Alfa MIMtech partnered with Schaller, one of the world’s leading manufacturers of guitar bridges and hardware. A high number of Schaller’s products are fitted as standard on many of the leading musical instrument brands. www.alfamimtech.com
Nano Dimension, based in Waltham, Massachusetts, USA, and Desktop Metal, Inc, headquartered in Burlington, Massachusetts, USA, have jointly announced that they have entered into a definitive agreement under which Nano Dimension will acquire all outstanding shares of Desktop Metal in an all-cash transaction for $5.50 per share, subject to possible downward adjustments to $4.07 per share. At $5.50 per share, the transaction represents a 27.3% premium to Desktop Metal’s closing price and a 20.5% premium to the 30-day VWAP as of July 2, 2024, for total consideration of approximately $183 million, possibly down to $4.07 per share or $135 million in total.
Together, the combined company is expected to have a strong financial profile and cash reserves, to support a path to profitability and strategic initiatives. The combination will enable pooling of resources in administration, sales, marketing and R&D and generate efficiencies
and cost savings opportunities, while enhancing R&D and innovation capabilities.
It is anticipated that the deal will generate in excess of $30 million in run-rate synergies over the next few years, in addition to previously announced cost savings from each of the two organisations. Business operations and capabilities will provide for consolidation opportunities as the combined company focuses on core geographies, including offices, R&D and manufacturing facilities in multiple US locations, UK, Germany, Switzerland, Netherlands, Italy, Israel and APAC.
Yoav Stern, Nano Dimension’s Chief Executive Officer and member of the board of directors, said, “Our combination with Desktop Metal is another step in Nano Dimension’s evolution to become the leader in digital manufacturing, with capabilities in mass manufacturing for critical industrial applications. We’re excited to join forces with
Dowlais Group plc, the UK-based parent company of GKN Automotive and GKN Powder Metallurgy, has published its half year 2024 results. In the report, the company confirmed it has commenced a strategic review of the Powder Metallurgy business, as it eyes a potential sale of the division.
GKN Powder Metallurgy noted a good start to the year, with adjusted revenues growing by 0.2%, ahead of the market, while adjusted operating profit increased by 6.0%, resulting in an adjusted operating margin expansion of 50 bps, to 9.5%.
The company stated that proactive management of the cost base had enabled GKN Powder Metallurgy to offset inflationary increases through operational efficiencies. This led to
restructuring activities continuing in the first half of the year, with one site closed in the US and another set to close by the end of the year. The location of the second site closure was not stated, but this was expected to further optimise the manufacturing footprint, Dowlais stated.
It was added that GKN Powder Metallurgy continued to advance its EV transition, winning new EV-specific contracts and identifying additional growth areas for propulsion-agnostic products.
For the group as a whole, Dowlais reported adjusted revenue of £2,571 million for the six months ending June 30, 2024, a reduction of 5.1% on the prior year, said to be driven by weakness in the ePowertrain product line of the Automotive busi -
an excellent group of technology leaders, all of whom share our vision for transforming manufacturing to Digital Industry 4.0. I look forward to working with Ric Fulop and his team to drive value for all our stakeholders, including creating opportunities for our employees as part of a larger, more diversified global innovative company, driving customer support and generating long-term growing value for shareholders as we focus on profitable growth.”
Ric Fulop, Desktop Metal’s co-founder and Chief Executive Officer, stated, “We’re excited to bring together our pioneering, complementary product portfolios that will further enhance our ability to serve our customers in high-growth industries with a more complete offering of digital manufacturing technologies for metal, electronics, casting, polymer, micro-polymer and ceramics applications. We look forward to working with Nano Dimension to join two great companies and their devoted teams that can serve our stakeholders to the maximum extent possible.”
www.nano-di.com
www.desktopmetal.com
Liam Butterworth, Dowlais CEO, has announced a strategic review of GKN Powder Metallurgy (Courtesy Dowlais Group)
ness. Driveline, China and Powder Metallurgy, totalling more than 75% of the group’s revenues, were reported to be performing above their markets.
The group posted adjusted operating profit of £151 million, including £7 million of operating losses from Hydrogen operations, a decline of 9.0% compared to the prior year, said to be driven by lower volumes.
www.gknpm.com
At Kymera International, we’re not just a powder provider; we’re your strategic partner in the world of specialty material solutions and additive manufacturing.
At Kymera International, we’re driving the future of specialty metals and advanced coatings for powder injection molding applications. Our industry-leading materials and innovative solutions enable precision, reliability, and performance across multiple sectors, from automotive to aerospace.
With our expert team and global presence, we empower manufacturers to push the limits of what's possible. Partner with Kymera and experience unparalleled quality, custom alloy solutions, and superior customer support.
Contact us today to revolutionize your projects
www.kymerainternational.cominfo@kymerainternational.com
Forward AM, the Additive Manufacturing business of BASF, has undergone a management buyout (MBO), creating a new independent company named Forward AM Technologies. Led by CEO Martin Back, and supported by BASF, the acquisition includes Forward AM’s materials and solutions, as well as its Sculpteo service business.
Forward AM offers a range of Ultrafuse metal filaments, including 17-4 PH and 316L stainless steels, for
Forward AM offers a range of Ultrafuse metal filaments, including 17-4 PH and 316L stainless steels
(Courtesy Forward AM)
the Material Extrusion (MEX)-based Additive Manufacturing process, Fused Filament Fabrication (FFF). The new company will retain control over intellectual property and, with its strong supply chain, reports that it expects to meet future demands and fulfil all contractual obligations without disruption.
“I would like to express my gratitude to BASF for all their support during the MBO process,” stated Martin Back, CEO at Forward AM. “By working together, we could ensure that our team of experts and the innovative tools currently in place can continue to provide leading AM solutions to the manufacturing industry in times of volatility. The team at Forward AM is truly passionate about shaping the future of manufacturing and all the exciting opportunities to build and grow within this innovative AM community. I’m looking forward to this empowering journey ahead.”
Forward AM has posted strong performance, with a consistent 30% annual growth rate over the past two
IperionX, based in Charlotte, North Carolina, USA, has announced the successful commissioning of its commercial-scale Hydrogen-Assist Metallothermic Reduction (HAMR) furnace. This marks the first titanium de-oxygenation production run at the Titanium Manufacturing Campus in Virginia, USA.
“The IperionX team delivered an important technological and commercial milestone for the global titanium industry,” stated Anastasios (Taso) Arima, IperionX CEO.
“Over the last two years, we have successfully operated our pilot titanium production facility in Utah, producing high performance titanium products for customers and - importantly – delivering first revenues for
our company. Today, we demonstrated that our HAMR technology works at commercial scale. We successfully increased the furnace production capacity by ~60x and produced high performance titanium that exceeds industry quality standards,” continued Arima.
IperionX’s proprietary HAMR technology offers a range of competitive advantages, including lower operating temperatures, reduced energy consumption, enhanced process efficiency, and accelerated production cycles – all achieved with lower capital investment intensity.
Produced entirely from 100% scrap titanium (Ti6Al4V alloy, Grade 5 titanium), quality assessments confirmed a large reduction in oxygen levels
years, said to stand at more than double the industry average.
During the transaction, BASF provided strong support to enable the formation of an independent company, while also saving jobs along with all the advanced technologies developed by the team at Forward AM.
“It is a very exciting time to be part of the AM industry. Building on excellence in materials, services, and solutions, we’re going to continue to drive innovation through our work and collaborative efforts with our partners,” said Back. “We know the manufacturing sector faces growing volatility and uncertainty, creating a demand for more resilient and sustainable materials and agile solutions. Forward AM is here to deliver on that demand head-on. This new venture emphasises our continued commitment and dedication to providing expedient and robust AM solutions, focusing on the success of our customers and partners. Together, we are proving that AM technologies are integral to the future of manufacturing. Together, we will keep moving forward.”
www.forward-am.com
from 3.42% to below 0.07%, exceeding the ASTM standard requirement of 0.2% for Grade 5 titanium.
Over the coming months, IperionX will commission and optimise the supporting process equipment to achieve full system production capacity in Virginia, with end-to-end system operations expected in late 2024.
“IperionX plans to expand the capacity of its Titanium Manufacturing Campus by adding modular, low-risk and low-cost HAMR furnaces. IperionX aims to be a leading US titanium producer of +10,000 metric tons per annum by 2030. Our goal is to re-shore the full titanium supply chain to the United States, at lower costs for our customers, and deliver the most sustainable titanium products on the market,” Arima concluded. www.iperionx.com
We’ve expanded our webshop selection of premium-quality titanium, maraging steel, nickel-based superalloys, and stainless steels to include Osprey® C18150. This new copper-based metal powder for additive manufacturing is tailored for excellent conductivity and strength at high temperatures. The checkout process is simple, and we accept credit card payments. Just add to cart at any time, and we’ll ship within 48 hours.
Nano Dimension, based in Waltham, Massachusetts, USA, has announced the completed installation of an Elnik Systems’ MIM 3000 series sintering furnace at its Formatec facility in Goirle, the Netherlands.
“This state-of-the-art Metal Injection Moulding furnace from Elnik Systems will undoubtedly drive further growth in this technology segment, enhancing our ability to produce high-end, complex metal components alongside our renowned ceramic components,” the company posted on LinkedIn.
The new furnace will enable Formatec to debind and sinter MIM components in-house rather than using a toll-sintering specialist.
Prior to this investment, sintering services were outsourced to DSH Technologies, a company affiliated to Elnik Systems with toll-sintering operations in both the US and Germany.
Formatec has provided MIM services to its customer base since 2020. Prior to this, it was focused on Ceramic Injection Moulding (CIM) and ceramic Additive Manufacturing, serving sectors that include luxury goods such as watchcases, as well as industrial components.
Elnik’s MIM 3000 sintering furnace is able to process any metal with any binder in a one-step debinding and sintering cycle without having to move the parts. This is accomplished through a gas-tight refractory metal retort and gas management system.
The gas management system consists of mass flow controllers for the retort and hot zone, and a partial pressure valve at the inlet of a specially designed and modified dry vacuum pump. Different
flows of gases into the hot zone and retort ensure a minimum of binder materials stick to the cold walls of the furnace. The retort has gas plenums on each side with a hole pattern to allow the heated gas flow evenly across each shelf in the retort.
The furnace includes ACCUTemp, a linearisation technique which allows each of the six zones within the furnace to run within +/- 1ºC of the actual temperature inside the retort. Wire-certified thermocouples with different calibration points are used and any difference in calibration is corrected via this proprietary linearisation programme. This enables the user to achieve higher densities of MIM materials by programming the sintering temperature closer to the actual melting temperature without running the risk of overheating and therefore distorting the parts.
www.elnik.com www.nano-di.com
www.formateceurope.com
These two binder systems have excellent characteristics during the production process and combine attractive prices with worldwide availability
High performance as well for the 3D-Printing process based on the water soluble binder system
Desktop Metal, Inc, headquartered in Burlington, Massachusetts, USA, has announced the launch of its PureSinter furnace. Capable of debinding and sintering metal parts created via Binder Jetting (BJT) Additive Manufacturing, the new furnace is also suitable for parts produced using traditional Metal Injection Moulding and Press and Sinter Powder Metallurgy methods.
In development for more than five years, PureSinter features hot walls that prevent contamination buildup and an airtight processing environment to enable efficient waste exit and high levels of purity.
Contamination can be caused by hydrocarbons and other waste emitted by the powdered metal parts, explains Desktop Metal. This builds up on walls and other surfaces inside the furnace and can cause undesirable chemical reactions and furnace reliability.
PureSinter has undergone extensive testing and is reported to show little to no contamination or buildup inside the furnace, even after hundreds of runs.
“Rather than trying to simply mitigate the factors that lead to poor performance in an all-in-one debinding and sintering furnace, we have eliminated them with an innovative all-new design,” stated Ric Fulop, founder and CEO of Desktop Metal. “This is the first product from Desktop Metal aimed at manufacturers using both Additive Manufacturing and traditional manufacturing methods.”
“We have put the PureSinter through a prolonged period of testing to rigorously verify our new design, and it has exceeded all expectations. PureSinter is an exemplary demonstration of the innovation for which Desktop Metal and our engineers are known. We believe this furnace will revolutionise sinter-based AM and the traditional furnace industry.”
The PureSinter furnace can reach a maximum temperature of 1,420°C and is qualified for use with a variety of processing gases, including argon, nitrogen, forming gas, and air. The machine features a total of seventeen fans and a pop-out ceiling vent for active, rapid, and consistent
cooling, lowering temperatures from 1,420°C to 200°C in less than four hours and without expensive water-cooled walls.
PureSinter features a vertical furnace design, an automated thermal hood lift, touchscreen controls, and visibility inside the retort. With an oxygen-tight retort seal, and its efficient cooling system, the energy requirements are also reported to be lower than similar machines.
The new furnace is compatible with all of Desktop Metal’s metal AM machines and binders. It is also validated with fourteen metal powder and binder combinations, including stainless steels, tool steels, superalloys, and reactives. PureSinter can also process titanium with a high degree of confidence without the complex preparations which may be required with other furnaces. It was added that additional material validations are in process.
The first PureSinter furnace has been installed at FreeFORM Technologies, a metal Binder Jetting contract manufacturer based in St. Marys, Pennsylvania, and the largest owner of a fleet of twenty-four Desktop Metal AM machines, to validate new materials.
Shipments of the PureSinter furnace are slated to begin in the third quarter of 2024. www.desktopmetal.com
Levine Leichtman Capital Partners, headquartered in Los Angeles, California, USA, has announced that it has acquired NSL Analytical Services, Inc, based in Cleveland, Ohio, in partnership with its management.
NSL, founded in 1945, is a materials testing provider serving a diverse client base across highly regulated and technologically advanced end markets, including aerospace and defence, advanced materials, and electronics. NSL’s experienced chemists, metallurgists and technicians are experts in testing a wide range of materials and finished components, serving the recurring and non-discretionary testing needs of clients throughout the US and the world.
Levine Leichtman Capital Partners
partnership
“We are thrilled to partner with NSL, a leader in the materials testing and analysis sector,” stated Matthew Frankel, Managing Partner at LLCP. “NSL has established itself as a trusted partner for a loyal client base across numerous high-performance industries. We are excited to work with the NSL team to broaden the company’s testing capabilities and geographic footprint through both organic initiatives and strategic acquisitions.”
“Our new partnership with LLCP will further guide and fuel NSL’s growth in support of the critical quality assurance testing our team delivers to clients world-wide,” CEO Ron Wesel shared. “In an everincreasing technology-driven world, NSL’s material testing capabilities provide the confidence and security demanded by traditional and evolving production methods such as AM.” www.nslanalytical.com www.llcp.com
Seco/Warwick Group, headquartered in Swiebodzin, Poland, has announced plans to expand its operations in the USA. The group, parent company of Seco/Vacuum and Seco/Warwick USA, has committed to expanding its manufacturing capacity in Pennsylvania by relocating a portion of its manufacturing, and a metallurgical lab for vacuum furnaces, from Poland to Crawford County.
In support of the expansion plans, the government of Pennsylvania has awarded the company a $2 million package of matching fund grants from the Department of Community and Economic Development through its Redevelopment Assistance Capital Program (RACP). The primary use and intent of the RACP fund is for reimbursement of eligible construction costs which Seco/Warwick Group companies will match on a 1:1 basis.
Seco/Vacuum manufactures heat-treating furnaces specialised for heat-treatment processes that must be conducted inside a vacuum chamber to prevent contamination from atmospheric gases. Seco/ Warwick USA manufactures atmosphere heat-treatment furnaces, aluminium melting furnaces and controlled aluminium brazing (CAB) furnaces.
The expanded facility will benefit the community as well as the heattreatment equipment manufacturer’s customers. The company will begin upfitting their now-empty factory floor in the Crawford Business Park, which itself was recently redeveloped from the long-abandoned American Viscose Corporation’s synthetic textile mill in Meadville, Pennsylvania, USA.
At its peak in the 1950s, the mill employed nearly half of Meadville. After many decades of operation, the mill closed in 1986. Beginning in 1989, the Crawford County Redevelopment Authority, the predecessor to today’s Economic Progress Alliance of Crawford County, invested in cleaning, remodelling, and subdi -
viding the million-square-foot plant into more than fifty smaller commercial and industrial spaces.
The added capabilities look to improve the company’s response to its North American customers’ needs, not only through manufacturing but also through the addition of parts, service, and training capacity. At the same time, the new facility will
require an expanded staff, at both entry-level and skilled positions.
“We look forward to working with our local partners including the City of Meadville, the Economic Progress Alliance of Crawford County (EPACC), the Workforce and Economic Development Network (WEDnet), and the Pennsylvania Department of Community and Economic Development (DCED) to make this expansion happen,” said Piotr Zawistowski, SECO/ VACUUM President, Managing Director. www.secovacusa.com
Over 6,500 production and laboratory furnaces manufactured since 1954
• Metal or graphite hot zones
• Processes all binders and feedstocks
• Sizes from 8.5 to 340 liters (0.3–12 cu ft.)
• Pressures from 10-6 torr to 750 torr
• Vacuum, Ar, N2 and H2
• Max possible temperature 3,500°C (6,332°F)
• Worldwide field service, rebuilds and parts for all makes
The Wittmann Group, headquartered in Kottingbrunn, Austria, is launching a new range of FlexCell automation cells. Designed to be extremely compact and flexible, the FlexCell is based on a standardised concept that is reported to bring together maximum efficiency and cost savings in the automation of injection moulding systems. The footprint of production equipment is an important efficiency key figure, explains Wittmann. As a supplier of turnkey injection
moulding systems, the company has harnessed this potential for space saving with the protective housing, linear robot, and conveyor belts all integrated into a single compact, safe unit.
With its three different versions — Basis, Primus and Plus — the FlexCell is intended to cover the entire range of injection moulding applications, from simple pick-and-place tasks to planned integration of downstream equipment, such as packaging stations for moulded parts.
6K Additive, a division of 6K, based in North Andover, Massachusetts, USA, has expanded its metal powder portfolio to include both titanium and chromium angular powders. Angular powders are used in a variety of technologies including Additive Manufacturing, Press & Sinter Powder Metallurgy, Metal Injection Moulding, and thermal spray. The move follows the acquisition of Global Metal Powders in November 2023, enabling 6K Additive to bring additional proprietary metal processing in-house to expand its breadth of sustainable revert
streams and recycling capabilities for producing angular chromium and titanium powders.
The powder range, produced via a sustainable manufacturing process, is reported to be highly pure, with low residual content (such as iron).
“The combination of the acquisition of GMP and our own expertise in sizing and metal upcycling for our spherical powders, allows us to offer a sustainable alternative to what is currently available on the market,” explained Frank Roberts, president of 6K Additive. “For years, customers have asked
All versions share a modular design. The cells are compatible with injection moulding machines of all brands and can be retrofitted to existing production equipment. Since these cells are mounted directly onto the injection moulding machine and allow production with the machine safety door open, the automation equipment can be positioned very close to the clamping unit. In the Primus and Plus models, the housing is mounted on the conveyor belt and thus requires no separate floor space.
The FlexCell automation cells are extendable by integrating additional modules. All automation components have their fixed place and are safely enclosed inside the FlexCell. In this way, there it greater occupational safety as well as more efficient setup processes. Temperature controllers can also be integrated in a spacesaving way, being placed underneath the conveyor belt.
Special emphasis was placed in product development on easy access to the mould space for manual interventions, servicing and maintenance work. Therefore, the conveyor belts with the protective housing can be moved very easily to one side in the Primus and Plus models.
www.wittmann-group.com
for angular titanium and chromium powder for applications like thermal spray, welding, and MIM. Adding these products to our portfolio is a natural extension of the powders we currently manufacture. We’re excited to supply our customers with products they’ve been seeking from 6K Additive.”
6K Additive has a powder test process with extensive quality control, including in-house analytical capabilities, micro-CT, gas analysis, ICP, XRD, SEM, and EDS. The company’s production facility is ISO certified and qualified to produce metal powders for high-performance markets such as aerospace, defence, and energy. www.6kadditive.com
Regardless of the complexity of your custom application and formulation, it remains standard for us with our quality systems, technical support, and two proprietary binding systems.
We ensure 100% batch-to-batch consistency, a wide range of alloys, and 36 years of supplying MIM feedstocks for mission-critical parts.
Advanced Metalworking Practices (AMP) manufactures and supplies a wide range of both standard and custom-configured MIM feedstocks for your application. Contact Chris Chapman at cchapman@ampmim.com or 724-396-3663.
Scan the QR code or click here to view our current list of alloys www.ampmim.com/resources
Molymet, headquartered in San Bernardo, Chile, reports it has acquired plasma atomisation equipment to enable the production of highly spherical powders of rhenium,
molybdenum, and their alloys, all specifically designed for industrial applications.
The spherical powders produced through this process are intended for various advanced manufacturing technologies, including Additive Manufacturing, Metal Injection Moulding, Thermal Spray, and Hot Isostatic Pressing. These methods, state Molymet, allow users to benefit from enhanced flowability, purity, and density and support the creation of complex parts with lower production costs and processing time.
“We are excited to launch Molymet 3D metal powders. These powders, created through a spheroidisation process, will meet the growing demand of industries that require high-performance materials,” stated Mario Lama, Market Development Executive Manager at Molymet.
Kennametal Inc., based in Pittsburgh, Pennsylvania, USA, has announced its fourth quarter and fiscal 2024 results. For 2024, sales of $2,047 million decreased 2% from $2,078 million in the prior year, said to reflect an organic sales decline of 1% and an unfavourable currency exchange effect of 1%.
“Thanks to the hard work and diligence of our global team, we delivered a strong finish in fiscal year 2024 despite persistent market softness, foreign exchange headwinds and a natural disaster affecting our facility in Arkansas. We successfully met our revenue and EPS outlook and generated $277 million in cash from operations, the highest as a percent of sales in over twenty-five years,” said Sanjay Chowbey, president and CEO.
Operating income for the year was $170 million, or 8.3% margin,
compared with $192 million, or 9.3% margin, in the prior year. The decrease in operating income was primarily due to lower sales and production volumes, higher wages and general inflation, higher restructuring and related charges of approximately $6 million, charges of approximately $4 million, consisting of repairs and impairments of fixed assets and inventory due to the tornado that affected the company’s Rogers, Arkansas facility during the fourth quarter, and unfavourable foreign currency exchange of approximately $2 million.
These factors were partially offset by pricing, restructuring benefits of approximately $21 million and lower raw material costs. Adjusted operating income was $183 million, or 8.9% margin, compared with $199 million, or 9.6% margin, in the prior year.
“As the world’s largest Rhenium producer, Molymet is committed to responsibly responding to market trends. The targeted markets are expanding, and we are particularly enthusiastic about the applications in the medical, aerospace, and high-end jewellery industries,” Lama added.
The plasma spheroidisation system, which has completed its trial phase at MolymetNos’ facilities, is now operational. The system is reported to be transforming the company’s capabilities, reinforcing its position as the world’s leader in rhenium and molybdenum processing.
Edgardo Cisternas, Research and Development Manager at Molymet, added, “Our new plasma atomisation equipment positions us at the forefront of technological innovation in Additive Manufacturing, meeting the highperformance material demands of our growing markets.” www.molymet.com
Net cash flow provided by operating activities in fiscal 2024 was $277 million compared to $258 million in the prior year. The change in net cash flow from operating activities was driven primarily by working capital changes including improved inventory levels, partially offset by lower net income compared to the prior year.
Free operating cash flow (FOCF) was $175 million compared to $169 million in the prior year.
The increase in FOCF was driven primarily by working capital changes, including improved inventory levels, partially offset by higher capital expenditures and lower net income compared to the prior year. FOCF was 146% of adjusted net income in fiscal 2024.
In fiscal 2024, Kennametal returned $129 million to the shareholders through $65.4 million in share repurchases and $63.4 million in dividends, while investing $108 million in capital expenditures. www.kennametal.com
Lithoz GmbH, based in Vienna, Austria, has installed a second industrial CeraFab Additive Manufacturing machine at Sandia National Laboratories’ facilities in Albuquerque, New Mexico, USA. As a direct result of Lithoz’s technology, the company states that Sandia can manufacture parts with previously unachievable geometries at a far more rapid rate, producing components, which normally take months, within a week and at a tenth of the cost when compared to conventional production processes.
Sandia plans to increase research and development into additively manufactured ceramics and scale up production efforts of optimised AM ceramic subcomponents using
Lithoz GmbH has installed a second industrial CeraFab Additive Manufacturing machine at Sandia National Laboratories facilities (Courtesy Lithoz)
multiple Lithoz AM machines and ceramic materials.
The CeraFab S65, as Lithoz’s industrial-level AM machine, looks to enable the serial production of highly complex ceramic parts. Due to the high degree of automation enabled by Lithoz’s Lithography-based Ceramic Manufacturing (LCM) process, Sandia has reduced costs to just one-tenth of that of conventional methods.
“By combining LCM technology with the attractive material properties of AM ceramic, Sandia have already opened the door to printing ceramic shapes and parts previously impossible to produce,” said Shawn Allan, Vice President of Lithoz America. “We look forward to seeing their future achievements with the greater capacity of a second Lithoz printer!” www.lithoz.com
Arburg GmbH + Co KG, headquartered in Lossburg, Germany, has announced that the refurbished Arburg Technology Centre (ATC) in Radevormwald, Germany, is back to normal operations after a two-year modernisation project. To celebrate the refurbishment, Arburg organised an open house event attended by around 250 guests.
“Our decision to undertake a multi-million Euro investment in the renovation of the ATC not only demonstrates how important our customers and staff are to us, but also emphasises the great significance of the German market for Arburg,” Michael Hehl, Managing Partner and spokesperson for the Arburg management team, shared in a speech. “Today, you can see that the wait has been more than worth it. We’re all very proud of what has been created here: a building for the future that marries aesthetics with functionality and environment protection in an outstanding way.”
In August 2022, shortly after the 40th anniversary celebrations, the ATC was cleared and gutted. All that was left was a shell, which was then outfitted from the ground up with the latest technology. The comprehensive renovations and modernisations included installing photovoltaic and geothermal systems, a tripleglazed glass façade and efficient roof insulation. Following the renovation and thanks to the use of renewable energies, the annual primary energy requirement of the ATC Radevormwald is around just 40% of that of a newly built reference building. The photovoltaic system alone, which produces almost 100,000 kWh a year, covers 60% of the total consumption.
Ulf Moritz, Manager of ATC Radevormwald, stated, “In the technical centre, seven injection moulding machines of the latest design with clamping forces ranging from 400-1,600 kN are available for our customers, for sampling, testing and training. Each is equipped with a robot
system – from the sprue picker and linear Multilift robot systems to the six-axis robot. The high-quality machine technology and equipment leaves nothing to be desired.”
The invited customers and partners took advantage of the opportunity to take in the new facilities and equipment. All seven Allrounder machines were in operation, showcasing applications live to demonstrate the company’s range of injection moulding products and services.
www.arburg.com
The Indian Institute of Technology Madras (IIT) has received its largest ever single donation of Rs 228 crore (approximately $27 million) from Dr Krishna Chivukula, founder and CEO of INDO-MIM and an IIT Madras alumnus. This donation is reported to be one of the largest ever made to an educational institution in India.
In honour of the award, IIT Madras has now named one of its academic buildings the Krishna Chivukula Block. The naming was celebrated during an event held at the campus on August 6, attended by Dr Chivukula; Prof V Kamakoti, Director of IIT Madras; Prof. Mahesh Panchagnula, Dean of Alumni and Corporate Relations at IIT Madras; Kaviraj Nair, CEO of the Office of Institutional Advancement at IIT Madras; as well as faculty, researchers, staff, and students.
Dr Chivukula introduced Metal Injection Moulding to India in 1997, when it was still an emerging technology in the USA. IIT Madras recognised Dr Chivukula’s professional excellence and contributions to the community by conferring its Distinguished Alumnus Award in 2015.
During the announcement, Prof V Kamakoti, Director, IIT Madras, shared, “That our alumnus still remembers his Alma Mater after several decades reinforces the fact that education is the only immortal wealth that we can give to mankind. Grateful to Shri Krishna Chivukula for his big contribution, which will benefit several future generations of students in their pursuit of knowledge.”
Speaking about his motivations for his support, Dr Chivukula stated, “My education at IIT Madras, in addition to
Prof V Kamakoti, Director, IIT Madras; Kaviraj Nair, CEO, OIA (Courtesy IIT Madras)
The European Powder Metallurgy Association (EPMA) has announced that its next WINTEREV hard materials seminar will take place December 10 – 11 at the National Physical Laboratory (NPL) based in Teddington, UK. The WINTEREV meetings, organised by the EPMA’s
European Hard Materials Group (EuroHM), aim to bring together experts for in-depth discussion of technical issues at a precompetitive level.
This year’s meeting will provide a thematic approach to hard material evaluation, looking at fusion
being extremely memorable and enjoyable, enabled me to accomplish much in life and put me in a position whereby I can give back to the Institute a gift –one of the largest single donations to date to a university in India!”
The donation is expected to be used for a number of purposes, including supporting international students to study at IIT Madras through a Scholarship, a Research Excellence Grant Programme, a UG Fellowship Programme for freshers at IIT Madras, Sports Scholar Programme, Shaastra Magazine development and maintenance of the Krishna Chivukula Block. Thanking Dr Chivukula for his generous support, Prof Panchagnula, said, “Dr Krishna Chivukula is not just a successful techno-businessperson but also an ideal alumnus. His humility and generosity will stand as exemplar characteristics for generations of alumni.”
Nair, added, “We are profoundly grateful to Dr Krishna Chivukula, an esteemed alumnus of IIT Madras, for his extraordinary generosity and unwavering commitment to our institution. His monumental contribution, the largest ever single donation received by IIT Madras, stands as a testament to his dedication to fostering excellence in education, research, and innovation. Dr Krishna Chivukula’s visionary support will significantly enhance our capabilities and propel IIT Madras to new heights. His contribution not only elevates our institution but also serves as an inspiring example of how our alumni community continues to drive meaningful change.”
www.iitm.ac.in
www.indo-mim.com
energy applications, effects of radiation, modelling and mapping, as well as looking at coating technologies, thermodynamics and processing low metal carbides.
The event will provide networking opportunities, including a group dinner on the Tuesday evening.
The full seminar programme and registration can be found on the event website.
www.seminars.epma.com
Then we could be your match.
With our materials experts, you are in the best of hands. Not only are we passionate of what we are doing, we also bring 30 years of experience in metal powder injection molding to the table.
Your vision is our incentive.
Materials and solutions from Schunk are advancing industries all over the world.
As an expert manufacturer of complex MIM components, we stand for exceptional service, the highest quality and enthusiasm for what we do. In close cooperation with you, we develop innovative and customized solutions for your business.
Rely on our expertise in molding processes such as
> metal injection molding
> graphite injection molding
> axial pressing
EN9100, IATF16949, ISO9001, ISO14001, ISO 50001 certified
Feel free to challenge us.
Schunk Sintermetalltechnik GmbH
Roßtrappenstraße 62 06502 Thale, Germany
+49 3947 7 1560
At thorsten.klein@schunk-group.com schunk-mobility.com
Ervin Metal Powders, headquartered in Ann Arbor, Michigan, USA, is now offering a range of Amapowder metal powders, suitable for Additive Manufacturing and Metal Injection Moulding, to customers in Europe through its sales office in Berlin, Germany.
Ervin currently includes 304L, 316L and 17-4 PH stainless steel powders in the Amapowder range. The powders are produced using the company’s Rapid Solidification Rate (RSR) and Centrifugal Atomisation technology, reported to create finegrained (nanometre-scale) and amorphous metals with uniform chemistry and a highly spherical shape. These characteristics are said to give the powders good flow and packing behaviours.
“We are delighted to be able to offer this exciting new range of prod -
ucts and are already collaborating with several Additive Manufacturing companies to help them deliver better quality and value solutions to their customers,” stated Florian Götz, Innovation Director for Ervin Europe.
Using RSR atomisation, Ervin states that it has developed a wide variety of metal powders for many industries and applications. The company has been able to collaborate with a range of industries and research professionals to advance spherical metal powder technology. Ervin also operates several centrifugal atomisation rigs that enable it to produce both small R&D powder batches and maintain the continuous production of powders at large scales.
Amapowder is suitable for a variety of Additive Manufacturing production processes, including
Amapowder 316L is suitable for metal Additive Manufacturing and Metal Injection Moulding, as well as Hot Isostatic Pressing and thermal spray (Courtesy Ervin Metal Powders)
Laser Beam Powder Bed Fusion (PBFLB), Binder Jetting (BJT), and Directed Energy Deposition (DED). In addition to Metal Injection Moulding, it is also suited to thermal spraying and Hot Isostatic Pressing (HIP).
www.ervin.eu
Himed, based in New York, USA, and Lithoz, Vienna, Austria, have announced the launch of a new Bioceramics Center of Excellence (BCoE) at Himed’s New York headquarters. The BCoE looks to offer a holistic approach to R&D with bioceramics for medical device manufacturers by integrating various analytical services to support the rapid prototyping process.
The newly founded centre will unite Himed’s three decades of experience of working with bioceramics for efficient human bone healing with the design freedom offered by Lithoz’s ceramic LCM technology, a form of Vat Photopolymerisation Additive Manufacturing. It will provide a comprehensive suite of services, including design support and optimisation, SEM imaging, material analysis and characterisation, biomaterial customisation, and bioceramic AM using a Lithoz CeraFab S65 Medical AM machine.
“Lithoz’s technology is unlike anything else out there — they’ve solved some meaningful challenges in this field, and their printers can take you from concept all the way through production. That’s going to open up new avenues for invention in implant design,” said Dana Barnard, CEO of Himed.
The company aims to promote the development of innovative manufacturing processes for bioceramic materials and help customers explore new compositions and manufacturing techniques that may have previously been out of reach for some companies. The BCoE will particularly benefit medtech startups and other businesses looking to costeffectively prototype and optimise designs using bioceramics.
“Before investing in a medical 3D printer, companies can effectively lease time on one, along with the support and materials expertise of Himed’s engineers and scientists supporting them from concept
through optimisation,” explained Himed President Craig Rosenblum.
The news follows the strategic partnership announced last year between Lithoz and Himed. The partnership outlined plans for an R&D collaboration to design new slurries for use in Lithoz’s ceramic medicalgrade AM machines.
Dr Johannes Homa, CEO of Lithoz, concluded, “This new Bioceramics Center of Excellence will open up a new chapter in 3D-printed medical applications for North America! We are excited to be the technology partner enabling Himed’s bioceramic innovation –with the combination of Himed’s experience and Lithoz technology, new applications will certainly be enabled which are currently unthinkable.”
www.lithoz.com www.himed.com
IMR Metal Powder Technologies, Velden am Wörthersee, Austria, has finalised its agreement with KBM Advanced Materials, LLC, based in Fairfield, Ohio, USA, for sale and distribution of IMR’s aluminium powders through KBM’s metal powder distribution network.
IMR has been a provider of industrial metals, semi-finished products, and chemical products for over thirty years, marketing its products globally. There will now be a dedicated stock of IMR material at KBM’s warehouse in Ohio, providing access to producers of aluminium parts.
IMR primarily produces aluminium alloy powder for the Additive Manufacturing industry. It partners in the development and production of customer-specific powders for Laser Beam Powder Bed Fusion (PBF-LB), Direct Energy Deposition (DED), and other processing technologies.
Thomas Rimmer, IMR CEO, stated, “By offering our aluminium alloy powders on the platform of KBM, our US customers now have access to their products on short-term notice which supports their inventory management optimisation as well as fast response to new business opportunities in a still evolving and
Metal Powder Group, Stockholm, Sweden, has named Rajiv Tandon as its new Technical Director. Tandon is an experienced technologist, noted as having a deep understanding of metal powder processing, specifically in process development,
powder production, and powder metal characterisation.
“I am pleased to have Rajiv joining us at Metal Powder Group,” stated Greg Chirieleison, Group CEO. “He brings a wealth of powder processing experience and will ensure our customers receive topquality tech support and engineering assistance. I look forward to seeing the innovations and improvements he will bring to our family of companies.”
sometimes difficult to predict market environment. The availability of IMR’s products to the US AM community from a local warehouse with the expert service of KBM were the main reasons for moving into this exciting opportunity.”
KBM offers products and services to AM powder consumers in the USA and Canada. Its business model results in KBM having large amounts of stock available for order at any given time, allowing customers to order and receive metal powder quickly and efficiently. KBM is reputedly North America’s largest marketplace for metal powders, allowing customers access to a variety of alloys and producers. It also offers transparent pricing and access to a variety of producers.
Kevin Kemper, KBM CEO, shared, “KBM is excited to partner with IMR to increase accessibility of their metal powders in North America. On-demand availability of products differentiates producers into those that can ship product when consumers need it and those that have a lead time. Our e-commerce solution features an easy-to-use interface, secure online transactions, detailed product information, pricing transparency, and the ability to ship products within a day of purchase. We want it to be easy and efficient for part producers to procure the raw materials they need to be successful. IMR is a strong and exciting addition to our offering.”
www.kbmadvanced.com
www.imr-metalle.com
Tandon has previously held positions at Phillips Metal Injection Moulding, Parmatech, Amulaire Thermal Technology, Magnesium Elektron Powders, Luxfer Magtech, and Chemalloy. He holds a Bachelors Degree in Metallurgical Engineering from the Indian Institute of Technology, Kanpur, and a PhD in Engineering Science and Mechanics from Penn State University, USA.
www.metalpowdergroup.com
Lucideon, headquartered in Stone, Staffordshire, UK, has acquired new scientific equipment using a £5.6 million equipment finance loan, alongside funding from UK Research and Innovation (UKRI).
Tony Kinsella, Chief Executive at Lucideon, said, “The new equipment acquired using this funding will have a transformative impact, boosting our capabilities and productivity so we can work with more clients on bigger projects. We are committed to investing into Staffordshire, and have invested nearly £4 million locally. This new equipment is not just a boost for our company, but also marks a significant step forward in strengthening the UK’s scientific offering.”
The equipment includes spectrometers, X-ray machines, ultra-high temperature and multi-atmosphere
furnaces, and ceramic Additive Manufacturing machines. This is expected to accelerate Lucideon’s ability to test and develop materials for specialist applications, such as in aerospace or net-zero technologies.
The additions will be used to fit-out the recently opened Applied Materials Research, Innovation, & Commercialisation Company (AMRICC) centre in Stone, which Lucideon hosts and manages on behalf of AMRICC’s members. The site is reputed to be the first laboratory in the country to house all the tools needed to replicate an advanced ceramics production process from start to finish at pilot scale, allowing businesses to trial new materials without pausing production in-house.
Additionally, Lucideon will use the funding to purchase replacements for its existing equipment and grow its
assets as the company expands and takes on more customers.
Lucideon offers materials science consultancy to businesses in the UK, United States, and around the globe, with three facilities across the US. Clients include Rolls-Royce, GE, and SpaceX.
www.lucideon.com
Thermal processing technologies company Inductotherm Group, headquartered in Rancocas, New Jersey, USA, has announced that Gary Doyon has stepped down after fifteen years as CEO, and thirty-eight years with the company. Mick Nallen and Satyen Prabhu will act as Inductotherm Group’s new co‐leaders, leveraging their complementary strengths and experiences.
Inductotherm Group is the parent company of Consarc Corporation, known for its design and manufacture of a wide range of advanced vacuum and controlled atmosphere furnaces for the processing of metals, specialty alloys, and engineered materials. The first Consarc specialty furnace was developed over sixty years ago and, today, it is said that over half the vacuum or controlled-atmosphere melting furnaces around the globe bear the Consarc name.
Although stepping down as CEO, Doyon intends to remain actively involved with the company. He will continue to serve as the only non‐family member on the parent company board, assisting with specific operational needs of other businesses owned by the Rowan family and pursuing new business avenues and opportunities for the Inductotherm Group. This transition is part of Doyon’s planned succession strategy, which aims to ensure the continued growth and success of the Inductotherm Group.
“We greatly appreciate and thank Gary Doyon for his exceptional leadership over the past fifteen years,” stated Virginia Rowan Smith, Inductotherm Group Chairman. “The Inductotherm Group is positioned for great things in the future based on its strength today. As we move forward with our succession plans, we are confident that the new leadership will continue to uphold the high standards and legacy that Gary has established.”
“We are pleased to announce that Mick Nallen and Satyen Prabhu have been selected to be Co‐Leaders,” added Smith. “This management strategy fits perfectly with the fact that our business is large, growing fast, and becoming wider in product technologies around the world. Mick and Satyen have come up with strong business plans that meet our family’s goal of maintaining a stable, customer‐focused, and technology‐centric business. We have an exciting future ahead of us.”
As part of their new roles, Nallen and Prabhu will focus on thought leadership, market comprehension, and a deep understanding of the thermal processing industry’s various sectors. Their strategic vision is expected to ensure that the group continues to deliver cutting‐edge induction technologies while preserving the core values and vision of its founder, Henry Rowan. www.inductothermgroup.com
www.erowa.com
Japan 13.10.-07.10.2024 The EROWA PM Tooling System is the standard interface of the press tools between the toolshop and the powder press machine. Its unrivalled resetting time also enables you to produce small series profitably.
EURO PM2024
Sweden
PM2024
Velta LLC, located in Dnipro, Ukraine, has announced the successful testing of its Velta Ti Process powder for Metal Injection Moulding. The results were presented at the 7 th International Conference on Powder Metallurgy and Additive Manufacturing of Titanium (PMTi2024) in Madrid.
The powder was assessed by an independent research institute, and tested in final product manufacturing by PolyMIM, a prominent German company.
The testing confirmed the suitability of Velta’s titanium powder for producing final titanium products using MIM technology. The move represents a significant advancement in manufacturing capabilities through Velta Ti Process as a zero-waste and low-to-zero carbon method for obtaining titanium metal powder.
“Velta is evolving in sync with market demands,” said Artem Yarovinsky, Velta’s Chief Business Development Officer. “We are meeting the rising demand for sustainability, increased titanium powder usage, and the development of titanium alloys, ensuring we offer a reliable titanium solution. The conference also gave us a great opportunity to establish collaborations with companies interested in further practical testing of Velta’s titanium powder for manufacturing final products.”
www.velta.us
CMG Technologies, based in Woodbridge, UK, has announced that it is now a member of Make UK, an organisation set up to help boost the British manufacturing sector. In addition to helping promote the UK industry, membership of Make UK will provide the Metal Injection Moulding company with access to knowledge, expertise and support from over 5,000 UK businesses.
Mark Leonard, Technical Sales Manager, said membership will provide opportunities for the future growth of CMG. “Make UK membership is really going to help us integrate with other like-minded businesses and help us gain valuable knowledge and expertise. There are always changes to legislation, so it’s ideal to have access to expertise on things that affect our industry. It helps us stay ahead.”
Make UK’s current goals include calling on the government to develop a robust, long-term industrial strategy and creating a sustainable workforce equipped with the skills needed for the future. Other services it offers include employment law and HR support, cyber security advice and learning and development opportunities.
www.makeuk.org
www.cmgtechnologies.co.uk
The NASA Marshall Space Flight Center, in collaboration with Jacobs Space Exploration Group, has ordered a C1000 Flexmatic Ceramic Additive Manufacturing machine from 3DCERAM Sinto. It was also stated that 3DCERAM has been added as a partner working with NASA.
The C1000 Flexmatic will be used to produce small and large samples of new and innovative materials that will be tested in space and other extreme environments.
The first parts will be tested under the Materials International
Space Station Experiment (MISSE) programme. This will involve the sample parts being secured to a panel that will be mounted outside of the International Space Station in an attempt to study the effects of outer space on additively manufactured products.
It was reported that 3DCERAM Sinto Inc, the company’s US facility located in Grand Ledge, will produce twenty sample parts that will be launched to the space station for the MISSE programme in 2025. These parts will be evaluated as potential
Ceramic test parts will be mounted outside of the International Space Station to study the effects of outer space on additively manufactured ceramic materials (Courtesy NASA)
The MPIF Technical Board has critically evaluated and completed its review of the manuscripts presented at the PowderMet2024 and AMPM2024 conferences, held in Pittsburgh, for the Outstanding Technical Paper Awards.
The winner of the 2024 Howard I Sanderow Outstanding Technical Paper Award is Comparison of
Soft Magnetic Composites (SMC) Lamination Assemblies by Bruce Lindsley and Neal Kraus of Hoeganaes Corporation. The winner of the 2024 Metal AM Outstanding Technical Paper Award was announced as Development of an Abrasion Resistant Alloy for the Metal Binder Jet Process by Chris Schade, Tom Murphy, and Kerri
The NASA Marshall Space Flight Center, in collaboration with Jacobs Space Exploration Group, has ordered a 3DCERAM C1000 Flexmatic Ceramic AM machine (Courtesy 3DCERAM)
ceramic materials that may one day be used on the outside of vehicles in space.
The samples will remain in space for six months in order to gain knowledge of the additively manufactured ceramic material’s ability to withstand the space environment. These tests will demonstrate the effects of in-space environmental exposures, such as zero gravity and radiation from the sun.
Once the ceramic materials and manufacturing processes are characterised in space, flight-worthy hot structures and heat shields could be manufactured on the C1000 Flexmatic, stated 3DCERAM. www.nasa.gov www.3dceram.com
Horvay of Hoeganaes Corporation. Both award-winning papers will be included in the appropriate conference proceedings. Advances in Powder Metallurgy & Particulate Materials — 2024 and Advances in Metal Additive Manufacturing with Powder Metallurgy — 2024
The winning authors will be presented with their awards during PowderMet2025 and AMPM2025, scheduled to take place in Phoenix, Arizona, USA, from June 15-18, 2025. www.mpif.org
From prototyping to full-scale production, Ipsen has your post-processing heat-treating equipment requirements covered. We build furnaces as small as 12” x 12” x 24” and as large as your needs require. For 75 years, Ipsen has been at the forefront of innovating furnace technology to meet strict and exacting requirements in critical industries. No matter what the future brings, Ipsen is here as your partner in success.
In 2024, Centorr Vacuum Industries (CVI) is celebrating its 70th anniversary in the vacuum furnace industry. CVI was formed from the combination of Vacuum Industries, founded in 1954 in Somerville, Massachusetts, USA, and the Centorr Furnace company, founded in 1962 in Suncook, New Hampshire. The two were merged in 1989, with new facilities in Nashua, New Hampshire, where the company is still located. In 1997, CVI became 100% management-owned and is now run as a private company under president and CEO William Nareski. “We have enjoyed long-term success over the past seventy years because our highest priority is customer satisfaction with our equipment and service” stated Nareski.
Vacuum Industries was started by the principles of the original National Research Corp. in Boston. It had a long history in the design and building of production size furnaces, primarily for the metals and hardmetals industry. Centorr Furnaces was a Laboratory and R&D furnace manufacturer, and was known for doing some of the first high temperature 3000°C furnaces for the growing ceramics market. In later years, Centorr was known as a world leader in fibre optics and high-temperature hydrogen sintering furnaces for the lighting industry. Today, Centorr is best known for its line of metals and ceramics sintering furnaces, large equipment sold into the nuclear industry, and for its line of furnaces sold into the
Centorr’s facility in New Hampshire, USA (Courtesy Centorr Vacuum Industries)
carbon, graphite, and composites industry for aerospace and hypersonics. The company is one of the leading custom and standardised vacuum furnace manufacturers, and has an installed base of over 7000 high temperature vacuum and controlled atmosphere furnaces worldwide. CVI operates a fully staffed Aftermarket Field Service group and an Applied Technology Center, offering R&D support and toll production service. www.centorr.com
Eiichi Ukai, CEO of Japan’s NTN Corporation, Osaka, has been appointed Chairperson of the Japan Bearing Industry Association (JBIA).
JBIA is an association of corporations that manufacture bearings. It was established in July 1948 to address issues such as technical standardisation, the prevention of unauthorised products, environmental protection, and measures for small- and medium-sized enterprises throughout the industry.
Eiichi Ukai joined NTN Corporation (then NTN Toyo Bearing Co, Ltd) in 1980, and became Operating Officer in 2011 before being promoted to Managing Operating Officer and
Eiichi Ukai, CEO, NTN Corporation, has been appointed Chairman of the Japan Bearing Industry Association (Courtesy NTN Corporation)
General Manager of ASEAN, Oceania & West Asia Region, in 2014. He was appointed a director in 2017, and has been in his current position since April 2021.
As chairperson of JBIA, he will continue to work for the sustainable development of the bearing industry as a whole.
www.ntnglobal.com www.jbia.or.jp
The Plansee Group has issued a Call for Abstracts for the 21 st Plansee Seminar. Set to take place June 1–6, 2025 at Plansee’s headquarters in Reutte, Austria, the seminar will focus on refractory metals and hard materials.
The seminar will cover a variety of topics, from materials science to the latest achievements in extractive metallurgy, manufacturing technology, industrial applications and sustainability. Of particular focus will be presentations covering Rhenium, an important alloying element for tungsten and molybdenum celebrating the 100 th anniversary of its discovery.
Abstracts submissions are due no later than October 4, 2024. www.plansee-seminar.com
Powder metallurgical parts must be cut using careful cutting processes and precision cut-off wheels tailored to the powder composition in order to determine material characteristics such as porosity. With the new cooling system, precise guides and the wide range of accessories for precision cut-off wheels, the Qcut 200 A provides optimum conditions for these challenges.
I Precise and vibration-free cutting processes
I Efficient coolant distribution
I Automatic cleaning function
I Optional flow monitoring for sensitive samples
I Material-matched precision cut-off wheels in diamond, CBN and aluminium oxide
www.qatm.com
Kennametal Inc, based in Pittsburgh, Pennsylvania, USA, has announced that David Bersaglini will join the company as Vice President of Kennametal Inc and President of the Metal Cutting segment, effective August 26, 2024. Bersaglini will serve on the company’s Executive Leadership Team and will report directly to company president and CEO Sanjay Chowbey.
Bersaglini has nearly twenty-five years of experience and joins the company from Copeland, a spin-off of Emerson, where he was vice president and general manager of the $1 billion Global Refrigeration segment. In this role, he was responsible for developing and implementing strategy to deliver long-term profitable growth for the Americas, Europe and Asia. He was also responsible for manufacturing, global product strategy,
engineering development, sales and marketing. Prior, he managed a $650 million P&L as Vice President and General Manager, Refrigeration.
“Dave brings a strong track record of success to Kennametal, with extensive experience leading businesses in the global industrial space and a proven ability to develop and implement strategic initiatives,” said Chowbey.
Bersaglini joined Emerson in 2001 and progressed through leadership roles in product management, marketing, sales, strategic planning and general management before transitioning to Copeland during the 2023 spin-off. Throughout his tenure with Emerson, Bersaglini focused on driving value creation through growth by developing market strategies and new products to deliver differentiated solutions
to end customers. As Vice President, Marketing and Development, he was responsible for the Asia Pacific market and he also held an enterprise-level leadership role as Vice President, Corporate Planning.
Chowbey added, “His valuable commercial expertise, growth mindset and results orientation make him the ideal choice to lead the Metal Cutting business. Dave will be instrumental in our journey to create shareholder value through growth, margin expansion and a balanced capital allocation strategy.”
Bersaglini earned a Bachelor of Science in mechanical engineering and a Master of Business Administration from Ohio State University.
As President of the Metal Cutting segment, Bersaglini will be accountable for all aspects of the global business, including advancing the strategy, driving operational excellence and delivering profitable growth.
www.kennametal.com
● GAS AND ULTRASONIC ATOMIZERS FOR SPHERICAL POWDERS WITHOUT ANY SATELLITES for LPBF, MIM, Binder Jetting and other Additive Manufacturing applications. High purity, sphericity and wide range of reproducible particle size distribution.
● WATER ATOMIZERS FOR MORE IRREGULAR POWDERS ideal for recycling/re ning process, press & sinter process and others.
● MAXIMUM PURITY BY OXIDATION-FREE PROCESSING
● AIR CLASSIFIERS FOR THE PRECISE SEPARATION OF METAL POWDERS into ne and coarse powder fractions especially in the range < 25 µm
● FOR A WIDE RANGE OF METALS AND FOR SMALL TO MEDIUM AMOUNTS
● ALL SYSTEMS DESIGNED FOR EASY HANDLING AND CLEANING, QUICK ALLOY CHANGE WITH MINIMUM CROSS CONTAMINATION
Kymera International, a speciality materials company headquartered in Raleigh, North Carolina, USA, has signed an agreement to acquire Fiven ASA from OpenGate Capital. The deal is expected to close following customary regulatory approvals.
With production facilities in Norway, Belgium and Brazil, as well as a global distribution network, Fiven works in the development of technically advanced silicon carbide materials for a wide range of highgrowth end markets. Through its recent R&D initiatives, Fiven has developed and marketed high-purity materials for the power electronics industries such as semiconductors and lithium-ion batteries.
“Fiven has all of the strong attributes we look for in an acquisition. They have an excellent reputation
for quality and service, are aligned with Kymera’s strategy of focusing on attractive end markets such as electronics, aerospace and defence, and have an outstanding management team and dedicated workforce,” Barton White, CEO of Kymera, commented. “We are excited to partner with Falk and his team to continue growing Fiven and capitalise on the numerous operational and commercial synergies we have already identified.”
Kymera has been owned by affiliates of Palladium Equity Partners, LLC, a middle-market private equity firm with over $3 billion in assets under management, since 2018.
“The acquisition of Fiven will accelerate Kymera’s mission to become a high-growth specialty materials and chemicals platform, and unlocks substantial organic
The acquisition of Fiven is expected to accelerate Kymera’s mission to become a high-growth specialty materials and chemicals platform (Courtesy Kymera)
growth opportunities for the combined business,” added Adam Shebitz, Partner at Palladium Equity Partners. “Altogether, Kymera is well on its way towards achieving Palladium’s investment objectives, having more than tripled in size from our initial investment, while creating a more resilient business oriented towards the industries of tomorrow.” The terms of the transaction were not disclosed.
www.kymerainternational.com www.fiven.com
Zimmer GmbH Kunststofftechnik, part of the Zimmer Group, Rheinau, Germany, has invested in an additional vacuum sintering and debinding furnace. By adding this furnace to its production facilities, the company reports that it is increasing its operational efficiency and expanding its Metal Injection Moulding material capacity.
The new sintering furnace can reach temperatures of up to 1,550°C in an argon atmosphere and enables sintering under vacuum, partial pressure and overpressure. The flexible atmosphere selection means that various gases
such as nitrogen, argon or hydrogen can be used.
With a usable space of 188 litres, the furnace expands the company’s previous production capacity. In addition, titanium and titanium alloys can now be processed more efficiently,
opening new manufacturing possibilities for customers.
Zimmer GmbH Kunststofftechnik offers a range of process technologies, from plastic injection moulding to elastomer technology and MIM. www.zimmer-group.com
As a leading provider of turbine propulsion engines for business aircraft, military trainers and helicopters, Honeywell is developing a new family of turbofan engines that will be lighter, quieter and more powerful, while running on 100% sustainable aviation fuel. The company is reported to be using Additive Manufacturing to trim many months off the development timeline.
“Turbine blades are made through an investment casting process that only a few foundries in the world can handle,” explained Honeywell Chief Manufacturing Engineer Brian Baughman. “It involves machining extremely complex metal dies and tooling to create ceramic moulds [casting cores], which are then cast with a molten superalloy to form the blades.”
Instead, Honeywell is now using a Vat Photopolymerisation (VPP) Additive Manufacturing technology to process ceramic slurry and manufacture the cores directly. Using a ceramic AM machine developed by Prodways Group, Honeywell has dramatically reduced the time and cost of producing the first-stage high-pressure turbine blades needed to develop the new engine family.
“With the conventional investment casting process, it can take 1-2 years to produce the turbine blades needed for the development process,” added Mike Baldwin, Principal R&D Scientist. “Additive Manufacturing lets us take the design, print the mould, cast it, test it and get real numbers to validate our models – and the whole process takes just 7-8 weeks. If we need to tweak the design, we can change it electronically and get another blade in about six weeks.”
Even minor changes to the blade design cost up to $1 million or more before the days of Additive Manufacturing, he added. “Additive Manufacturing enables rapid prototyping and gives us greater flexibility to accelerate development, manage costs and create the best possible product for our customers. Reducing development cycle time is our primary objective, but we also anticipate saving several million
dollars in development costs compared to using the traditional blade casting process.”
Honeywell installed Prodways’ latest MOVINGLight ceramic AM machine, the CERAM PRO 365, at its Additive Manufacturing centre in Phoenix, Arizona, in 2023. “Our 3D printers are a perfect match for this use case,” said Michaël Ohana, Prodways Group CEO. “We can process ceramics slurries to build a large number of parts in a single day and deliver consistent manufacturing results at every print.”
Additive Manufacturing is ideal for companies like Honeywell that need to produce precision components in relatively low volumes, Baughman said. “Low volumes are often a struggle since the upfront tooling cost for a turbine blade is very high and fabrication requires a long lead time. Additive Manufacturing makes a lot of sense in cases like this.”
Honeywell began metal Additive Manufacturing in 2007 at its lab in Phoenix. Today, the company is reported to produce hundreds of aircraft components with Additive Manufacturing and has expanded its efforts to additional operations in China, Europe, India and the United States.
www.honeywell.com www.prodways.com
Malvern Panalytical, part of Spectris plc, Egham, Surrey, UK, has agreed to acquire Micromeritics, headquartered in Norcross, Georgia, USA, for $630 million, plus a deferred element of up to $53 million. Micromeritics focuses on analytical instrumentation for the physical characterisation of particles, powders, and porous materials.
With the addition of Micromeritics’ suite of analytical technology, Malvern Panalytical aims to provide the broadest material characterisation offering in the market. It will offer a single suite of integrated instruments from a single manufacturer to support the entire customer workflow, thereby improving workflow efficiency and enabling deeper analytical insights.
As part of the acquisition, Terry Kelly, president and Chief Executive of Micromeritics, has agreed to join the group as Malvern Panalytical President. Kelly will be a key member of the Spectris Scientific leadership team.
Micromeritics’ technologies enable the comprehensive characterisation of particles by detailing their size, count, surface properties and behaviour, for fundamental research, product development and production quality control.
“Together, Micromeritics and Malvern Panalytical provide a unique opportunity to create a leading and highly differentiated position and a fully integrated offering in mate -
rial characterisation,” stated Derek Harding, current CFO at Spectris and soon-to-be president of Spectris Scientific. “Micromeritics is an excellent business with a strong track record of growth and innovation and excellent future growth prospects.”
Terry Kelly added, “Micromeritics is a world leader in particle characterisation. Our market-leading technologies are used daily in the labs of the world’s most innovative companies and institutions. Our end markets are strong and growing, and we have a robust new product pipeline. The integration with Malvern Panalytical is powerful. Together our companies will be able to unlock more answers for customers and provide expert applications and technical support that cannot be matched by any other company.”
www.malvernpanalytical.com
www.micromeritics.com
The Wittmann Group, headquartered in Kottingbrunn, Austria, welcomed over 1,000 customers to its 2024 Competence Days event. Held June 19-20 in the Marx Hall, Vienna, the event offered a variety of specialist presentations focused on digitalisation as well as a showcase of the company’s range of injection moulding machines, robots and auxiliary equipment. Michael Wittmann, president and co-owner of the Wittmann Group, shared, “The Competence Days surpassed our expectations. We were able to welcome more than 1,000 guests from thirty-seven different countries. The interest in our presentations and exhibits was enormous, and the general atmosphere was excellent.”
The first speaker at the event was Dr Mikula Thiem from the Association of German Machine manufacturers (VDMA), who discussed the topic of digitalisation from many different angles. This was followed by specialists from the Wittmann Group, who led several interactive presentations to familiarise guests with the group’s current developments in the area of digitalisation. The topics included production integration using Wittmann 4.0, as well as data transparency through intelligent assistance systems, plus the use of artificial intelligence for further improvements in customer service.
ervation of resources in the form of in-line recycling, lightweight construction, as well as the use of DC energy in the injection moulding process, including solutions in the field of automation. In micro injection moulding – a specialty of the Wittmann Group – nanostructures could be viewed under a microscope.
Sites open to visitors included the premises of Wittmann Battenfeld in Kottingbrunn, where several operational injection moulding machines were on display. Visitors also enjoyed a guided tour of the company’s production plant. Further visits included a tour of the robot production plant at Wittmann Technology in Vienna and a visit to the Wittmann facility in Mosonmagyaróvár, Hungary. www.wittmann-group.com
Following a keynote speech by Dr Alexander Kronimus, Acting Chief Executive Officer of PlasticsEurope Germany, guests were invited to finish the day with a networking event.
Both days, visitors were given the opportunity to view the latest developments at Wittmann via numerous exhibits. The work cells presented tangible evidence of digitalisation, the use of AI, pres -
Markforged, headquartered in Watertown, Massachusetts, USA, has introduced the FX10 Metal Kit, a bolt-on that brings metal capability to the company’s FX10 Additive Manufacturing machine. With the new kit, the FX10 can now process both metal filaments and composites with continuous fibre reinforcement.
Markforged also announced a new 316L stainless steel metal filament to be used with the FX10 Metal Kit. The company added that users will also be able to use 17-4PH, with additional support for other Markforged metal filaments coming in the future.
“Customers no longer have to choose between a metal and a composite printer. Years of R&D investment and field experience have come together to provide an all-in-one solution for 3D printing to provide immediate return on investment once installed on a factory floor,” stated Shai Terem, CEO of Markforged. “The FX10 supercharges other equipment on the factory floor to be better utilised and run more
efficiently, increasing productivity and reducing potential line down events.”
The FX10 Metal Kit consists of a swappable build engine that includes a metal-specific print head, material feed tubes, routing back, and dual pre-extruders. The FX10 can be swapped between metal and composite as many times as needed, with the process said to take around fifteen minutes.
“We designed the FX10 to be a modular platform, so that we are able to release new innovations and upgrades without customers having to purchase a new printer every year,” continued Terem. “Along with new software capabilities we release regularly, the FX10 Metal Kit is poised to provide continuously growing value on factory floors for years to come.”
Similar to the 5 th Generation Continuous Fibre Reinforcement (CFR) build system in the FX10, that is nearly twice as fast as previous composite machines, the
2 nd Generation Metal FFF engine, built on years of Markforged’s experience in metal Additive Manufacturing, is said to be significantly faster than its previous metal systems. The FX10 also has a build volume twice as large as Markforged’s earlier industrial metal AM machines.
With the Markforged AM process, metal parts are built from the metal filament and a ceramic release filament. The ceramic release is extruded as an interface between the part and supports for ease of separation and removal. Once the green metal parts are produced, they must be solvent debound (or ‘washed’ in Markforged’s terminology) and sintered in the company’s Wash-1 and Sinter-2 systems. Eiger, Markforged’s slicer and build management software automates the process, including scaling parts to account for shrinkage during the sintering stage.
The Digital Forge is the Additive Manufacturing platform that enables every aspect of the FX10 and is purpose-built to integrate into existing manufacturing ecosystems. With the Digital Forge, users can share parts across their organisation, and monitor fleet performance from a central location.
www.markforged.com
Advanced Technology (Bazhou) Special Powder Co.,Ltd
No.76 Xueyuan Nanlu, Haidian, Beijing 100081,China
Tel: +86-13701029643
Email: powdermetal@atmcn.com
1958
• Powders for magnetic core and SMD
• Powders for MIM
• Pre-alloy powders for diamond tools
• Powders for auto engine valve seats and guides
• Powders for filtering materials
Sales Agent in Europe Burkard Metallpulververtrieb GmbH
Tel. +49(0)5403 3219041
E-mail: burkard@bmv-burkard.com
Nabertherm GmbH, headquartered in Lilienthal, Germany, recently celebrated the twenty-fifth anniversary of its Chinese subsidiary. Founded in 1999, the subsidiary’s opening was regarded as a milestone in the company’s international expansion and underscored the importance of the Chinese market.
Nabertherm China’s headquarters are in Shanghai, with further sales specialists in Shenzhen, Beijing and Wuhan. Since its founding, the subsidiary is reported to have developed a reputation for high-quality industrial and laboratory furnaces, supporting customers from areas
Nabertherm offers a range of furnaces, including this retort furnace for sintering MIM components (Courtesy Nabertherm GmbH)
Continuum Powders, based in Los Gatos, California, USA, has announced the completion of its official rebrand from MolyWorks and the appointment of Rob Higby as the company’s Chief Executive Officer. Higby succeeds previous CEO Phil Ward, who will now assume the role of President — Asia Pacific, where he will lead Continuum’s Asia Pacific operations. Since 2020, Ward has led the organisation through customer adoption, IP development, quality systems certification and the establishment of funding partnerships.
“I’m excited to be partnering with Rob as we accelerate our metal powder and service offerings to our customers,” stated Ward. “Rob’s experience and track record of delivering next-generation manufacturing and MRO services to customers is the perfect focus for Continuum as we scale our global business being served out of Texas, California and Singapore.”
Higby has experience in building service teams for the delivery of next-generation offerings to customers. Most recently, he served
of high technology, production, research, dental and the arts in solving relevant daily tasks in the field of thermal process technology.
Nabertherm has stated that a key factor in its Chinese subsidiary’s success is its well-developed service network. “Regional presence to our customers is particularly important to us in China,” stated Timm Grotheer, Managing Director of Nabertherm GmbH, Germany. “Our goal is to best understand their needs and offer innovative solutions that meet the needs of the Chinese market.”
Nabertherm intends to continue working closely with its Chinese subsidiary in the coming years. The company added that it will continue to develop thermal process solutions for Chinese customers, offer first-class products and address questions in the usage phase through service activities that meet its customers’ high standards.
Grotheer concluded, “We are pleased with the appreciation we have earned in the Chinese market and will do everything to continue to meet our customers’ expectations with high standards.”
www.nabertherm.com
as an Executive Partner with AEA Investors, where he led the firm’s Aerospace and Defense investment practice. He led several investments for the firm and advised other companies, including Velo3D Inc, where he also served as Advisor to the Board of Directors and interim Chief Commercial Officer.
Under the rebrand, MolyWorks Materials Corporation has changed its corporate naming to Continuum Powders Corporation to become a single, unified brand that more accurately represents the future and differentiators of the company. All company assets, patents, employees and locations are now officially Continuum Powders. www.continuumpowders.com
Alleima, headquartered in Sandviken, Sweden, has signed an agreement with KTH Royal Institute
Alleima and KTH Royal Institute of Technology partner for research and education (Courtesy KTH Royal Institute of Technology)
of Technology, Stockholm, Sweden, to deepen collaboration in research and education, enhance scientific excellence, strengthen societal benefits, and increase innovative capacity in addressing the major challenges faced by society today.
Alleima, formerly part of Sandvik, and KTH have a longstanding collaboration across various fields. This includes joint research and development activities, exchanges through industrial PhD students, study visits, and guest lectures. Alleima has also contributed an industrial perspective to the design of university programmes to better align with labour market needs.
The collaboration is now further strengthened through the strategic partnership, which is intended to support both existing and new forms of cooperation between Alleima and KTH. It seeks to deepen collaboration in the fields
Sweden’s Höganäs AB has announced that it is now able to provide product-specific carbon footprint (PCF) reports for all products with complete lifecycle assessment (LCA) models in place. The move is intended to support customers in their emissionreduction goals, and contribute to Höganäs’ long-term target of reaching net-zero emissions by 2037.
“Many of our customers already face demands from their own customers to reduce carbon dioxide emissions from the value chain (scope 3),” stated Fredrik Vinnerborg, Product Portfolio Manager. “This will become increasingly important as many
car manufacturers have set netzero targets. Thanks to the data we provide in our PCFs, our customers gain a powerful tool to reduce their scope 3 emissions.”
Höganäs is the first metal powder producer to provide full transparency on its cradle-to-gate productspecific emissions to the market. The PCF calculations follow the ISO 14067:2018 standard and communicate how many kg of CO 2 equivalents are emitted for every kg of metal powder produced.
Sofia Poulikidou, LCA Specialist, added, “To ensure transparency and enhance communication with customers we have created Product Carbon Footprint summary reports,
of materials science, chemistry, and chemical engineering – areas where both parties conduct research and development at an international level.
“In close collaboration with Alleima, we can develop innovative solutions for leading research and education. In this way, we jointly contribute to a more sustainable society and accelerate the transition. The partnership ensures a secure supply of talent, access to knowledge and cutting-edge research, and enhances competitiveness and innovative capacity,” said Björn Glaser, Partnership Manager Director of Alleima at KTH.
“It feels fantastic that through this strategic partnership with KTH we have the opportunity to further deepen the collaboration in research and education. This means that with joint ambitious research, we can increase the power of innovation in areas where the world and society today face major challenges,” Tom Eriksson, EVP & Head of Strategic Research, at Alleima, stated.
www.alleima.com www.kth.se
for all base powders which have LCA models in place.”
The PCFs cover all greenhouse gas emissions throughout the entire production chain, from a cradleto-gate perspective. This includes all activities, from raw material acquisition and inbound transport to energy and fuel production, as well as processing activities at Höganäs’ sites. Downstream activities, such as product distribution to customers, components manufacturing, use, and end-of-life, are excluded.
Vinnerborg continued, “We encourage our customers to reach out to their usual contact person at Höganäs to learn more about how we can support them in their sustainability journey and help reduce their scope 3 emissions with the assistance of PCFs.”
www.hoganas.com
Material Options (Metal)
Material Options (Ceramics)
Build Envelope
Quantity
Tolerance capability
CONTACT FOR MORE DETAILS
17-4PH, SS 316, Tool Steel M2 & S-7, Inconel 625, 4140
Alumina 99.5%, Zirconia
~ 300 grams max, Footprint equivalent of baseball size or less, 0.02” (0.50 mm) wall thickness minimum
10~50 samples based on footprint. Larger quantities up to 1,000 pcs welcome depending on the part size.
Within 2% of the feature size, 2~3 Ra Surface finish, Option of finishing to closer tolerances available.
NORTH AMERICA Email: Mukund.N@indo-mim.com Ph: +1 (210) 557-1594
EUROPE Email: InfoEU@indo-mim.com Ph: +49 1732656067
ASIA Email: InfoHQ@indo-mim.com Ph: +9198459 47783 / +91 98450 75320
ISO 9001:2015 / IATF 16949:2016 / AS
In a recent webinar hosted by Metal AM magazine, Metal Injection Moulding company INDO-MIM, Bengaluru, India, discussed in detail the use of its new M2 tool steel for the Additive Manufacturing of mould inserts. The company is now using Binder Jetting from HP to produce a wide range of tooling.
During the presentation, Harish Irrinki, Sr Applications Engineer and Strategic Account Manager at HP, also provided detailed information on HP’s Metal Jet S100 Binder Jetting solution. The Metal Jet S100 has an effective build volume of 430 x 309 x 140 mm and meets MPIF standards for stainless steel with HP Metal Jet SS 316L and HP Metal Jet SS 17-4PH materials. The HP Metal Jet workflow includes a powder manage -
ment station, the Metal Jet S100 AM machine, a curing station and a powder removal station. Sintering equipment is provided by a third party, giving users the choice of either investing in a furnace or using a toll service for this stage of the process.
INDO-MIM is the world’s largest MIM company, with over 3,000 employees producing over 150 million parts annually. Jag Holla, Sr. VP-Marketing at INDO-MIM Ltd, discussed the company’s use of Additive Manufacturing to produce mould inserts. Holla talked about how the company began with Laser Beam Powder Bed Fusion (PBF-LB) AM machines but then moved to using Binder Jetting as the preferred production method. This was, in part, due to the speed advantage over
PBF-LB, but also enabled the company to use its M2 tool steel powder for the production of mould inserts.
In addition to the design capabilities of AM, such as the inclusion of conformal cooling channels, a key advantage of AM is the speed at which the process can produce the tooling. This can save many weeks, or months, in getting a product to the customer.
Over the last eighteen months, INDO-MIM has produced around 1,800 M2 steel inserts for production use, stated Holla.
Not only is BJT quicker for producing the tooling, it also offers improved properties compared to wrought material. INDO-MIM’s M2 shows superior wear and machinability performance, compared to wrought, explained Holla. This can result in a 30-50% tool life improvement, it was stated.
The full webinar can be viewed here: https://bit.ly/3MSTqcs www.indo-mim.com www.hp.com
Tritone Technologies, based in Tel Aviv, Israel, has announced a strategic partnership with Allendale Machinery Systems, Inc, located in Upper Saddle River, New Jersey, USA. The move is expected to enhance Tritone’s presence, technical support, and integration capabilities in New Jersey, New York, and Pennsylvania, and is seen as a key step in Tritone’s broader North American expansion strategy.
“We monitor the market constantly for innovations that can help our customers stay competitive in their markets,” said Neil McGill, VP of Operations, Allendale Machinery Systems. “We have had success with polymer 3D printing for several years now and believe Tritone’s MoldJet technology is the right platform to launch into metals. We believe that eliminating loose powder from the metal AM process is an important step forward.”
Tritone’s growing footprint in North America is built on strategic machine installations and sales partnerships.
“The Allendale team represents three generations of customer relationships in their market,” said Ben Arnold, VP Business Development NA, Tritone Technologies. “Customers rely on Allendale to introduce technologies that keep them ahead of their competitors.”
Tritone offers two AM systems that utilise Tritone’s proprietary MoldJet technology. This powder-free AM technology enables the industrial production of metal and ceramic parts. MoldJet is specifically designed to produce large quantities of parts with complex geometries.
www.tritoneam.com | www.allendalemachinery.com
The Metal Powder Industries Federation (MPIF) has announced a call for presentations for the MIM2025: International Conference on Injection Moulding of Metals, Ceramics, and Carbides. The event is scheduled to take place from February 24-26, 2025, at Hilton Orange County/Costa Mesa, Costa Mesa, California, USA, and is sponsored by the Metal Injection Moulding Association (MIMA), APMI International and the MPIF. All abstracts must be submitted by September 30, 2024. Authors will be notified of acceptance or rejection by October 31, 2024. www.mpif.org | www.mimaweb.org
Researchers at Politecnico di Torino, Turin, Italy, have published a paper in Materials & Design entitled ‘Ultraviolet–Visible-Near InfraRed spectroscopy for assessing metal powder cross-contamination: A multivariate approach for a quantitative analysis.’ The paper assesses three binary systems obtained from
the cross-contamination of three components, A92618, C10200 and S31603, in a low contamination range, from 0.5 vol% to vol. 6%, and in a high contamination range of 25 vol% and vol. 50%.
The past few years have seen increasing use of spherical metal powders to produce bulk parts
SEM image (a) of the surface morphology of the three different commercial powders atomised powders; b-c) size distribution of the three types of powders (As published in Ultraviolet–Visible-Near InfraRed spectroscopy for assessing metal powder cross-contamination: A multivariate approach for a quantitative analysis. Courtesy Materials & Design)
Wall Colmonoy, headquartered in Madison Heights, Michigan, USA, has announced the acquisition of Indurate Alloys Ltd., a supplier of hardfacing products, located in Edmonton, Alberta, Canada. The acquisition is intended to strengthen Wall Colmonoy’s position in the Canadian market and provide customers with a wider range of products and expertise to meet their wear resistance and corrosion protection needs.
Indurate Alloys supplies metallic and carbide powders in HVOF, plasma spray, thermal spray, laser and plasma trans -
ferred arc (PTA) forms, as well as wires and electrodes. Indurate also provides Additive Manufacturing powders and collaborates with companies that use the latest AM technologies, including Powder Bed Fusion and Direct Energy Deposition.
Wall Colmonoy stated that it recognises the value of Indurate’s established and growing customer base, high-quality thermal spray products, and excellent vendor relationships, which will add new products to complement Wall Colmonoy’s portfolio.
“We are excited to welcome the talented Indurate Alloys team to Wall
through metal-forming technologies like Additive Manufacturing and Metal Injection Moulding, the authors state. This, paired with the wide availability of metal powders, leads to a critical issue: contamination across different systems in different process steps. As a result, it is necessary to find a new, faster, and more reliable analysis sensitive to traces of contamination.
This work by Politecnico di Torino’s researchers evaluates the applicability of UltravioletVisible-Near-InfraRed (UV-Vis-NIR) spectroscopy, a technique providing information on powders’ reflectance, for studying contaminated powders.
After the UV-Vis-NIR analysis, multivariate analysis has been used to obtain quantitative results. The results show that, as the contamination level increases in the binary system, the shape of spectra changes and becomes progressively more similar to the contaminant one. The chemometric analysis allows for the detection of the contaminant type and its concentration percentage in the contaminated powder.
www.sciencedirect.com
www.polito.it
Colmonoy,” stated Nicholas Clark, President, Wall Colmonoy. “This strategic acquisition extends our reach into the Canadian marketplace and allows us to better serve our customers across the country.”
“Wall Colmonoy stood out as the right partner for us, thanks to its extensive history in the hardfacing industry and its shared commitment to strong customer relationships,” said Lorne Chrystal, Founder & CEO of Indurate Alloys Ltd. “We are excited to merge the expertise and experience of both companies and eagerly anticipate expanding opportunities together.”
www.induratealloys.com www.wallcolmonoy.com
Ceramics
ceramic
Stainless steel parts produced by Metal Injection Moulding find extensive application in medical instruments, dental orthodontic brackets, electronic devices, consumer products, automotive components, wristwatch parts such as cases and bracelets, and many more. 316L austenitic stainless steel is a grade commonly used for the above sectors with the primary alloying constituents after iron being Cr (16-18%), Ni (10-12%) Mo (2-3%) and up to 2% Mn, giving this grade excellent corrosion resistance and also high yield and tensile strength similar to conventional 316L grade. 904L is also an austenitic stainless steel grade but its higher contents of Ni (24-26%), Cr (19-21%), Mo (4-5%) and Cu addition (1-2%) gives this grade superior corrosion resistance in extremely corrosive environments.
Watchmakers have traditionally produced 316L and 904L stainless steel bracelet parts such as links by machining drawn metal profiles. However, the MIM process has, in recent decades, been found to be a less expensive manufacturing process and a number of watch
producers now routinely use the MIM process to produce both bracelet links and watch cases from these grades of stainless steel.
One of the drawbacks of using 316L and 904L grades stainless steel is in applications where the alloy parts, which contain high amounts of Ni, come into contact with human skin causing skin sensitivity. Nickel is said to be the most widespread cause of all contact allergies with an estimated 10–15% of adult females and 1–3% of adult males in Europe being allergic to nickel. Of nickelsensitive people in the general population, 30% develop hand eczema. The role of nickel in the biological response to 316L alloys used in medical devices, implants and orthodontic dental brackets is also of significant concern regarding toxicology and biological performance.
There are two European Union Directives: 94/27/CE and 2004/96/ that regulate the use of nickel in jewellery and other products that come into contact with the skin. Since June 2009 these Directives have been subsumed into Annex XVII of the REACH Regulation which outlines the restrictions on the ‘manufacture, placing on the market and use of certain dangerous substances, mixtures and articles’. It is stated in REACH that Ni-containing alloys cannot be used in articles intended to come into direct and prolonged contact with the skin, such as wristwatch cases, watch straps and tighteners and other products if the rate of nickel release from the parts of these articles coming into direct and prolonged contact with the skin is greater than 0.5 µg/cm 2/week. Thus, in the manufacture of bracelets and other articles specific to watches, there is now a trend of replacing Ni containing stainless steel grades with nickel-free austenitic steels.
Nishimura Advanced Ceramics Co.,Ltd
Ko Nishimura (Global sales)
3-2 Kawata Kiyomizuyaki Danchi-cyo, Yamashina-ku, Kyoto - 607-8322 JAPAN
Phone: +81-80-8305-9205
Phone (Kyoto Office): +81-75-591-1313
npc-e3@nishimuratougyou.co.jp
http://www.nishimuratougyou.co.jp/english/
CIM Feedstock
Ko Nishimura (Global sales)
High Strength Translucent Alumina FS (Al2O3 99.99%)
96% ~ 99.9% Alumina FS (White, Black)
Zirconia FS (White, Black, Blue)
Mullite FS
A research group based in Marin-Epargnier and Neuchâtel, Switzerland, and Saint-Laurent-du-Pont, France, was requested by a Swiss watchmaking group to carry out an in-depth study of the corrosion behaviour of a number of 316L and 904L stainless steels obtained by MIM and MIM + HIP using different electrochemical techniques. Conventional stainless steels of the same austenitic grades were also tested using the same techniques. In the manufacture of bracelets in link and pin assembly, galvanic currents can be generated by the presence of sweat or other aqueous electrolytes (sea water, swimming pool water, rain or condensation of atmospheric humidity). For this reason, direct measurements of the galvanic couplings between MIM alloys and conventional stainless steels were carried out. The pitting potential of these alloys was also evaluated by applying the ASTM G48-11 standard for ferric chloride.
The results of this in-depth study were published in the paper, ‘Evaluation of the Corrosion Resistance of Watch Links from 316L and 904L Austenitic Stainless Steels Obtained by the Metal Injection Moulding (MIM) Technique Intended to Be in Contact with Human Skin’, by the authors Lucien Reclaru, Florina Ionescu and
Frederic Diologent, in the journal Coatings Vol. 14, 412, March 30, 2024. 28 pp.
The study involved testing ten MIM samples in the form of 10 mm diameter mirror polished discs – six 316L samples from one supplier, and two of each grade 904L and 316L from a second supplier. Table 1 lists the samples and the manufacturing conditions used including green and milled discs, short and long sintering cycles and any post sintering HIP operation. For comparison, a complementary study was conducted on 316L and 904L bulk alloys.
The authors reported that the evaluation of corrosion resistance of the ten MIM alloys (eight samples of MIM type 316L and two samples of MIM type 904L) was done using electrochemical techniques, rotating electrodes and galvanic coupling (Fig. 1). Different electrochemical parameters were measured and calculated (the open
#1 316L Green Long Sintering and HIP
#2 316L Green Long Sintering and
#3
#5
#6
#7
#8 904L
#9 316L
#10 316L
Sintering and
Sintering
Sintering and HIP
Short Sintering and HIP
Milling × 1 Time Short Sintering and HIP
Milling × 2 Times Short Sintering
Milling × 1 Time Long Sintering
Table 1 MIM sample identifications and the processes used for their manufacture (From the paper ‘Evaluation of the Corrosion Resistance of Watch Links from 316L and 904L Austenitic Stainless Steels Obtained by the Metal Injection Moulding (MIM) Technique Intended to Be in Contact with Human Skin’, by L Reclaru, F Ionescu and F Diologent, Coatings Vol. 14, 412, March 30, 2024. 28 pp.)
circuit potential, the polarisation resistance, the corrosion current and Tafel slopes, the coulometric analysis and galvanic coupling current). Tests
to evaluate the resistance of the MIM 316L and 904L stainless steels to pitting corrosion in a ferric chloride medium and the measure of the
REST-DEBINDING AND SINTERING FOR ALL METALS
Our most distinctive furnace in production of metal injected moulded parts.
I 1450 °C continuous operating temperature
I 10 – 900 mbar Partial pressure
I Argon or Nitrogen
I 0 – 100 % Hydrogen
I Overall low CO2 footprint
I Low energy consumption
1 2 3 4
Fig. 1 Rotating electrode technique (a) Rotating electrode cell used in the tests; (b) Electrode composition: 1 PTFE electrode holder; 2 Sample to be tested; 3 Collar; 4 PTFE electrode holding head (From the paper ‘Evaluation of the Corrosion Resistance of Watch Links from 316L and 904L Austenitic Stainless Steels Obtained by the Metal Injection Moulding (MIM) Technique Intended to Be in Contact with Human Skin’, by L Reclaru, F Ionescu and F Diologent, Coatings Vol. 14, 412, March 30, 2024. 28 pp.)
1 2 3 4
Fig. 2 Evaluation of the pit density (number.cm−2) after the ferric chloride test (FeCl3 , 2 h at 50°C) (From the paper ‘Evaluation of the Corrosion Resistance of Watch Links from 316L and 904L Austenitic Stainless Steels Obtained by the Metal Injection Moulding (MIM) Technique Intended to Be in Contact with Human Skin’, by L Reclaru, F Ionescu and F Diologent, Coatings Vol. 14, 412, March 30, 2024. 28 pp.)
Fig. 3 Nickel cations released according to EN1811 (From the paper ‘Evaluation of the Corrosion Resistance of Watch Links from 316L and 904L Austenitic Stainless Steels Obtained by the Metal Injection Moulding (MIM) Technique Intended to Be in Contact with Human Skin’, by L Reclaru, F Ionescu and F Diologent, Coatings Vol. 14, 412, March 30, 2024. 28 pp.) (a)
released nickel cations were also completed in this study. The authors concluded that if the MIM stainless steels studied are compared with conventional bulk stainless steels, then their corrosion resistance behaviour is inferior (Fig. 2).
In the couplings studied, the galvanic currents generated are very important. The shape of the curves also reveals the presence of localised corrosion phenomena. According to tests in ferric chloride, MIM stainless steels were noted to have inferior behaviour compared to conventional stainless steels (Fig. 3). However, MIM type 904L stainless steels are comparable in behaviour to conventional type 316L steels. The quantities of nickel released according to EN 1811 were very significant (2 mg cm −2 week −1 up to 24 mg cm −2 week −1), and did not meet the requirements of the European Directive (0.5 µg cm −2 week −1).
The authors stated that the parameters studied to characterise corrosion behaviour of the two MIM austenitic stainless steels did not reveal any correlation with the manufacturing parameters proposed as technological criteria. They concluded that there is a strong trend of developing nickel-free austenitic stainless steels which adhere to the EU and ASTM standards for medical and other applications such as watch components, and they believe these alloys could also be used in the MIM industry for articles in contact with the human body. www.mdpi.com/journal/coatings
The use of the Metal Injection Moulding process to produce titanium components has been extensively studied in recent years due to the benefits that MIM offers as a netshaping process for small, intricate shaped components. These benefits include high material utilisation and lower production costs compared with conventional processes such as CNC machining and casting. However, despite the many advantages that the MIM process offers, its adoption for mass production of Ti components has been limited.
One reason is said to be the challenge of controlling the interstitial elements such as carbon and oxygen in green Ti-MIM compacts during the debinding stage of the MIM process. This is especially the case for binder systems used in Ti-MIM where commercial backbone polymer binders such as polypropylene (PP), polyethylene (PE), and poly(methyl methacrylate) (PMMA), have a decomposition temperature above 400°C, and it is well-known that at above 260°C, binders may introduce impurities during the thermal debinding of the titanium parts.
friendly binder system for Ti-MIM. The new binder system is based on polypropylene carbonate (PPC) and polyoxymethylene (POM), which is said to offer lower decomposition temperatures during thermal debinding with effective mitigation of impurities such as O 2 and C. The results of this research were published in a paper entitled: ‘Formulating titanium powder feedstocks for metal injection moulding from a clean binder system’ by K Lim, M D Hayat, K D Jena, Z Yuan , L Li, and P Cao, Powder Technology Vol 433, 2024, 119214, 7 pp.
A group of researchers at the University of Auckland and University of Waikato in New Zealand and the Kunming University of Science and Technology in China, have undertaken work to develop a low decomposition temperature and environmentally
The authors reported using a commercial purity gas atomised Ti powder with mean particle size D50 = 45 µ m. The maximum interstitial contents in the Ti powder are: 0.122% O 2, 0.003% C and 0.008% N (in wt.%). The newly developed binder system presented in the paper is composed of polyethylene glycol (PEG) as the primary component removed at the solvent debinding stage, with polypropylene carbonate (PPC) and polyoxymethylene (POM) as the major and minor backbone components which are removed during thermal debinding, and stearic acid (SA) as a surfactant. The compositions of the binders studied are listed in Table 1. Ti powder loading in the feedstock was 63 vol.%.
Table 1 Compositions studied in the new PEG/PPC/POM binder system for MIM titanium (From the paper ‘Formulating titanium powder feedstocks for metal injection moulding from a clean binder system’ by K. Lim, et al, Powder Technology Vol 433, 2024, 119214, 7 pp)
The injection moulding parameters were: injection pressure 19 MPa, holding pressure 16 MPa, injection time 5 s, and injection temperature and mould temperature were 170°C and 30°C, respectively. All feedstocks were said to exhibit pseudoplastic behaviour, indicating rotation and re-arranging of polymeric binders and metallic particles within the feedstock along the flow direction. This facilitates inter-particle motion, making the feedstock well suited for MIM.
The authors stated that PEG was incorporated into the PPC/POM feedstock to compensate for the poor shape retention of the PPC/POM binder system by allowing the formation of a network of pore channels within the compact structure during the initial water debinding stage. This porous network then facilitates the efficient removal of residual PPC/POM binder during subsequent thermal debinding.
The results showed that increasing the PEG content leads to a higher binder removal rate, while adding POM enhances shape retention during thermal debinding and PCC, as the predominant backbone binder, enhances the adhesion between the titanium powder and the binder system. The optimal PEG/PPC/POM binder system composition was identified as 40/48/10% w/w, respectively, offering a higher PEG removal rate at a shorter debinding time and improved shape retention. However, all feedstocks tested were successfully injection moulded without any defects.
The injection moulded Ti green parts were first subjected to water debinding at 30°C for different intervals up to 21 h to remove the majority of PEG. This was followed by thermal debinding of the PPC/ POM under flowing argon gas. The
authors stated that the advantages of using PPC and POM are their low to moderate decomposition temperatures and clean decomposition behaviour. PPC and POM degrade entirely in a single step at 275°C and 370°C, respectively, which is below 400°C. Microstructural observations in the debound samples after thermal debinding (Fig. 1 (d-f)) showed the complete combustion of the PPC/ POM binder, resulting in binder-free titanium compacts.
The authors concluded that the environmentally friendly binder system based on PEG/PPC/POM also resulted in Ti-MIM samples with admissible impurity levels, with oxygen content of 0.27 wt% and carbon content of 0.05 wt%. These levels comply with the stringent requirements outlined in ASTM F2989 for Grade 3 titanium products.
www.journals.elsevier.com/ powder-technology
SEM
of Ti-MIM feedstock studied (a) 40PEG/5POM, (b) 40PEG/8POM, (c) 40PEG/10POM after water debinding, and (d) 40PEG/5POM, (e) 40PEG/8POM, (f) 40PEG/10POM after thermal debinding (From the paper
‘Formulating titanium powder feedstocks for metal injection moulding from a clean binder system’ by K. Lim, et al, Powder Technology Vol 433, 2024, 119214, 7 pp)
We Convene...
The most brilliant minds from industry and academia We Coordinate... Transformative technical and workforce data We Catalyze... High-value, high-impact collaborative projects
America Makes is the leading collaborative partner for additive manufacturing and 3D printing technology research, discovery, and innovation in the U.S.
Structured as a public-private partnership, we innovate and accelerate AM/3DP to increase global manufacturing competitiveness. ®
Focused on additive manufacturing, America Makes is the first institute of the Manufacturing USA® network.
Join Us for Our Technical Review Exchange (TRX) November 12-14, 2024 Tucson, AZ
Learn more at www.AmericaMakes.us
Everyone had high expectations of Binder Jetting. Of all the metal Additive Manufacturing processes, it suffered from the most hype. What transpired was the realisation amongst machine vendors that it was harder than expected to ‘get it right’. However, while public success stories are few and far between, progress is being made. Azoth is one company that has successfully embraced Binder Jetting, along with related sinter-based AM processes. With a ‘feet firmly on the ground’ approach, and a base near Detroit, it has found commercial success in the automotive industry and beyond. Bernard North reports on a recent visit.
Ann Arbor is a large town some 40 miles west of Detroit, Michigan, and is best known as the home of the University of Michigan. It is also the home of Azoth, a rapidly growing manufacturer of AM parts with a strong automotive focus. The company has become very visible within the broader PM industry as a result of its numerous presentations at Metal Powder Industry Federation (MPIF) conferences and its successes in the annual MPIF’s Design Excellence Awards competition. The company’s seatbelt pillar guide loop for General Motors, used in Cadillac Celestiq (Fig. 1), is an award-winning part that has resulted in significant visibility for metal AM in automotive circles.
Azoth’s facility is located in a modern light industrial plan on the outskirts of the city. The entire morning of the visit was spent with Cody Cochran, General Manager and co-founder, and Mattia Forgiarini, Lead Process Engineer. We were joined for the first hour by Scott Burk and Jay Mullick, co-presidents of Azoth’s larger sibling company EGC, part of the EWIE Group of Companies.
“EWIE has developed a high level of familiarity and expertise in the field of subtractive manufacturing but, several years ago, it became apparent to its leadership that at least some of this technology would be replaced and/or complemented by Additive Manufacturing.”
The author was quite familiar with EWIE, which stands for East West Industrial Engineering, from his earlier life in the metal cutting tooling industry. At large manufacturing plants, especially those producing automotive engines and transmissions, it is the norm
for manufacturers to contract the purchasing and inventorying of consumables to an ‘integrator’.
This is where EWIE operates as a major player. A private company, and also headquartered in Ann Arbor, EWIE has grown since its formation in 1981 to achieve around $600 million in annual sales, employing around 1,200 people. A thousand or so of these employees are based at
customers’ facilities. The company serves forty-five customers worldwide, most of whom have multiple manufacturing sites.
Burk explained that EWIE has developed a high level of familiarity and expertise in the field of subtractive manufacturing but, several years ago, it became apparent to its leadership that at least some of this technology would be replaced and/or complemented by Additive Manufacturing, and that it was important to develop expertise in the field. Azoth was therefore formed as a division of EGC in 2017 to develop the necessary expertise.
At the time of co-founding Azoth, Cochran had already worked for EGC for seven years, most recently at a General Motors transmission plant. The name ‘Azoth’ was selected from alchemy, a medieval scientific philosophy; azoth was believed to be the material that could transform lesser metals into more valuable ones. Additive Manufacturing embodies the same principles, combining raw materials to build something new and more valuable.
Initially, Azoth’s focus was on the Additive Manufacturing of polymers and D2 tool steel for fixturing and grippers etc. needed by EWIE’s clients, where AM’s short lead times were a big advantage. The first metal AM process the company investigated was Fused Filament Fabrication (FFF), specifically Desktop Metal’s Studio System, marketed as ‘Bound Metal Deposition.’ In 2019, the company purchased its first Digital Metal Binder Jetting (BJT) machines. Digital Metal was acquired by Markforged in 2022. BJT technology has formed the bulk of its development and production work since.
Forgiarini joined Azoth in 2019, shortly after which Azoth was announced as a separate brand within EGC. By 2022, development work and prototyping continued apace with a major milestone: the commercialisation of bespoke gear shift knob emblems for the Cadillac CT5-V and CT4-V Blackwing performance sedans.
In the same year, Azoth also adopted XJet’s NanoParticle Jetting (NPJ) technology to complement its BJT equipment. In the meantime, further equipment capabilities needed for both the AM processes themselves and for post-sintering processing have been added, and numerous further customer applications established.
Mullick emphasised that EGC’s background dealing with large manufacturing companies, all of which have very detailed quality management systems, has given Azoth an advantage because the management and staff understand that, to succeed in the AM parts business, “you must develop and maintain a truly production-capable infrastructure; in brief, you must have the whole thing.”
Expanding on this, Cochran suggested that reasons for disappointing growth, over-valued companies, and business failures in the AM industry were sometimes because players underestimated the importance of all processes, such as sintering, finishing, and QA, to AM
rather than just the build process itself.
“Many people do not fully appreciate the rigour required to satisfy customers’ quality management systems. In particular, parts need to go through a full PPAP (Production Parts Approval Process). Another
“Many people do not fully appreciate the rigour required to satisfy customers’ quality management systems. In particular, parts need to go through a full PPAP (Production Parts Approval Process). Another cause for delay and failure is the fact that there is a learning curve to Design for AM (DfAM) concepts.”
cause for delay and failure is the fact that there is a learning curve to Design for AM (DfAM) concepts. It typically takes time to cement it with customers and establish the trust required for redesign. This sort of change doesn’t happen overnight,” stated Cochran.
Short lead times are critical; Cochran stated that first parts are typically delivered to a potential customer within fifteen days following the provision of the item’s CAD model and that “generally, Azoth is not the bottleneck” during the subsequent testing and approval processes required by the customers before placing production orders.
Cochran succinctly summarised Azoth’s advantage when he stated that, “We are a true manufacturing organisation with Additive Manufacturing capabilities, rather than a service bureau.”
During the plant tour, we passed through office areas where engineers interacted with customers, using Solidworks to create 3D models of parts to be manufactured. The manufacturing area is currently about 500 m 2 and includes powder preparation, metal AM machines, curing and de-powdering stations, debinding and sintering capabilities, and multiple post-processing and finishing processes such as polishing and coating.
That metal Binder Jetting is the predominant AM process became clear with the sight of multiple Markforged and Desktop Metal machines running with 20-hour door-to-door cycle times, allowing an overall 24-hour ‘takt time’ for much of the plant.
The machines have different assignations by material type: one of the Markforged machines runs copper and MAR247, while the others are used for 316L and 17-4PH stainless steels. Desktop Metal machines run both stainless steel alloys. After the build cycle, the loads are cured in ovens at approximately 200°C before
being de-powdered at dedicated stations; recycled powder is blended back in with virgin powder in strictly controlled proportions. The XJet Carmel machine uses two ‘inks’: a suspension of submicron 316L stainless steel powder and a separator/ support material which is dissolved in an aqueous solution after the manufacturing process.
Green parts are then placed on molybdenum trays with ceramic separator plates and are then either debound in separate ovens and then sintered, or else a combined debindsinter cycle is run in the large Elnik Systems MIM 3015 batch furnace, equipped with a molybdenum retort and heating elements. This has a hot zone of approx. 0.6 x 0.6 x 0.9 m and
“That metal Binder Jetting is the predominant AM process became clear with the sight of multiple Markforged and Desktop Metal machines running with 20-hour door-to-door cycle times, allowing an overall 24-hour ‘takt time’ for much of the plant.”
is capable of complex cycles under vacuum or flowing N 2, Ar, and H 2 gases. It also has a fan and heat exchanger to reduce cycle times. At one end of the production area, a variety of post-sintering capabilities were apparent, including a small heat treatment furnace; abrasive tumbling for polishing, abrasive blasting, buffing, and Cerakote coating application equipment, although external service providers are also partnered with for various post-sinter operations.
The Quality Assurance lab equipment included full optical metallography specimen preparation and microscopy capability, together with the Archimedes’ method for measuring density, as well as hardness testing, surface finish measurement, and a 3D scanner
with 5 µ m resolution used for both QA and for reverse engineering of customer-supplied components. Chemical analysis is outsourced. Powder suppliers provide particle size and compositional data, but Azoth also obtains certification through a third-party laboratory.
During our tour, we witnessed the seatbelt adjustable guide loop shown in Fig. 1 being strength tested with a length of seat belt; the desired result
was observed when the belt itself failed but the additively manufactured metal component did not.
Currently, Azoth is housed on one side of a ~3,000 m 2 building which, until recently, was primarily used by EWIE, with Azoth using less than about 20% of its space. Most
“New production machinery slated for delivery includes a Markforged DMP Pro BJT machine, another Elnik Systems debind/sinter furnace, a five-axis Mazak machining centre, and more surface finishing equipment.”
EWIE staff have since relocated to another facility in the area and, at the end of our plant tour, we walked through two empty spaces – one of 1,500 m 2 and another of about 500 m 2 – that are earmarked to enable a significant expansion of production capacity and output.
Cochran stated that volume could grow to between 5-10x current levels without needing to relocate to another facility. New production machinery slated for delivery includes a Markforged DMP Pro BJT machine, another Elnik Systems debind/sinter furnace, a five-axis Mazak machining centre, and more surface finishing equipment.
Even with these additions, there will be space available for far more equipment as the business grows. Azoth management stated they can see the business, which currently employs around twenty people, growing to the order of $100 million in annual sales.
Sinter-based
By material, metals account for around 90% of Azoth’s output, with polymers accounting for the balance. Stainless steels are used for the vast majority of metal production, divided roughly equally between 17-4PH and 316L, though there are also significant quantities of pure copper and MAR247, a nickel-based superalloy, as well as a small amount of D2 tool steel, reflecting Azoth’s earlier focus on tooling and fixtures. Ti-6Al-4V has been technically qualified and should join the offering soon.
Azoth describes its product range as small, highly detailed parts. By weight and physical size, the products range from 0.015 g in weight and a few mm in length up to parts with a weight of 1.5 kg and a largest dimension of 15 cm.
By market, the automotive industry accounts for some 65% of output, and Azoth currently has over fifty PPAP-approved parts in production for two OEMs and ten Tier 1 suppliers. Approximately 5% of output is for tooling, jigs, and fixtures, with most of the remaining 30% split between medical and defence. The company also supplies a few consumer products; during the plant tour, we saw an order of guitar saddles being made. Geographically, the split is ~90% North America, 10% international.
Quantities of specific parts vary greatly, but typical volumes are 10–250 pieces during product development and 250-70,000 pieces per year in production, although Azoth is entertaining business prospects for specific components of over 1,000,000 per year. In most cases, replenishment orders are released monthly or bi-monthly. By repeat orders versus new business, the split is approximately 65%:35%.
Azoth has, from its beginnings, chosen to focus on sinter-based metal AM processes. Forgiarini and
Cochran described the reasons for selecting sinter-based methods as being a combination of their ability to deliver serial production at scale, with better fine feature and surface finish capabilities than Laser Beam Powder Bed Fusion (PBF-LB). Better material utilisation as a result of not needing to build support structures which then have to be recycled as
scrap is also seen as an advantage. At this time, they do not see a need to expand into other, fundamentally different, AM technologies.
When asked if there were any serious concerns about the business stability issues affecting some AM equipment manufacturers, the answer was a clear ‘no’ for several reasons. Azoth performs its own
“Forgiarini and Cochran described the reasons for selecting sinter-based methods as being a combination of their ability to deliver serial production at scale, with better fine feature and surface finish capabilities than Laser Beam Powder Bed Fusion (PBF-LB).”
maintenance work on equipment and, even if some companies have become overvalued through overly optimistic estimates of market growth, each supplier’s basic technology was sound and would continue to be supported, even if that may be under different ownership.
In addition, while new equipment is initially qualified using powders supplied by or through the manufacturer, Azoth has developed qualified second sources for all three equipment types.
When it comes to process selection, Azoth staff stated that when a new component comes in for prototyping, they can usually quickly see which process to apply based on the composition, physical size, complexity, and surface finish requirements of the part. Very small parts with fine features and smooth surface finish requirements are best made by the XJet process, which uses sub-micron metal powders in a
slurry deposited as 10 µ m layers. The much finer grain size can also deliver superior mechanical properties [1]. Larger parts with less fine feature complexity are better suited to one of the Binder Jetting systems.
Azoth is ISO 9001-certified and ITAR (International Traffic in Arms Regulations) registered, is IATF 16949 (automotive industry) compliant with third-party auditing and is also working towards ISO 13485 medical industry certification.
Azoth is enjoying considerable success in the automotive industry and the team has shared considerable insight on its journey at several of the MPIF’s annual and co-located PowderMet/AMPM conferences.
Automotive interior components
At AMPM2022, in Portland, Oregon, Cochran described the company’s work using BJT as a fabrication process for automotive components for vehicle interior applications [2]. Such components are parts exposed in customer-facing interior applications and require cosmetic surface finishes and detail resolutions superior to the capabilities of fusion-based Additive Manufacturing processes.
To validate the material and function of the components, Cochran stated that various tests have to be performed to predict effects on part quality through long-term consumer use for the lifetime of the vehicles in which they are installed and many factors have to be taken into consideration to match the level of standardisation and quality control required for automotive production.
The components shown in Fig. 12 passed all automotive PPAP quality requirements and are installed in production vehicles. Cochran stressed the importance of standards (MPIF 35, ISO 9001, AS9100, IAT 16949) and a robust process control plan including FMEAs (Failure
12 Left: General Motor’s 120th anniversary edition shift knob emblems, manufactured for single edition of only 120 vehicles; Right: Emblem for General Motor’s special edition competition package vehicles, manufactured in limited edition. Both are produced from 316L by BJT (Courtesy Azoth)
13
Mode and Effect Analyses), an AIAG (Automotive Industry Action Group) Advanced Product Quality Checklist and familiar testing equipment to gain the confidence of automotive customers.
AM process selection
A year later, at AMPM2023 in Las Vegas, Forgiarini compared the production of 316L stainless steel parts using Binder Jetting
(with 15 µ m powders) with XJet’s Nanoparticle Jetting process (<1 µ m powders) [1]. The latter process allows sintering at much lower temperatures in a combined vacuum/ H 2 cycle. While cost and throughput favour Binder Jetting, the XJet process can produce parts with much higher surface detail and higher yield strength and Forgiarini described the two processes as being complementary rather than competitive.
At this year’s AMPM2024 conference in Pittsburgh, Pennsylvania, Cochran presented a case study [3] explaining the lead time and cost issues involved in bringing a metal AM part to production for the automotive industry.
The main lesson shared was that AM can be just a small part (in this case ~25%) of the total lead times and component costs. Drivers are complex designs, mass customisation (in some cases), rapid product development, and low cost compared to MIM, investment casting, or machined parts.
Example parts were left- and right-hand versions of a badge for the front fenders (wings) of a Chevrolet Camaro Garage 56 variant, produced by BJT from 316L stainless steel. Besides the complexities of the badges per se (Fig. 14), their rear surfaces had to precisely match the contours of the respective fender. After sintering, the parts had to be finished and adhesive foam backing of the correct shape applied (Azoth had to design the fixturing to correctly apply this to the AM parts).
Even though successful prototyping of the AM parts took less than three weeks, the total project time – from the initial RFQ through seven design iterations, three finish variants, and the PPAP (Production Parts Approval Process) to actual deliveries – took about four months.
“Even though successful prototyping of the AM parts took less than three weeks, the total project time – from the initial RFQ through seven design iterations, three finish variants, the PPAP (Production Parts Approval Process) to actual deliveries – took about four months.”
At the same event, Forgiarini explored the development, approval, and production of a safety-critical automotive component, specifically the seatbelt pillar adjustable guide loop for the General Motors Cadillac Celestiq [4] shown in Fig. 1.
Forgiarini summarised the significant design iterations required to go from the traditional four-part assembly to a single piece AM component, while satisfying structural, cosmetic, cost, depowdering, polish media clogging prevention, and electropolish liquid draining considerations, as well as the PPAP
checklist, Technical Drawing Review, Process Flow Diagram and Control Plan, and required Quality Assurance checks. All of these steps need to be done and implemented before production orders can be received.
17-4PH stainless steel was selected for its mechanical strength and corrosion resistance, and after the Binder Jetting process, curing, depowdering, delubing and sintering the secondary processes selected were abrasive flow machining, polishing, and NiCr electroplating.
When Cadillac revealed its Celestiq vehicle, it marked a significant milestone on the path to achieving the company’s goal of creating an all-electric, ultra-luxury vehicle. John Roth, Vice President of Global Cadillac at General Motors, stated that the team at GM “rethought everything, resulting in the most technologically advanced vehicle in the brand’s history.”
The development of the vehicle resulted in numerous innovations, including 115 parts produced by Additive Manufacturing. The seatbelt pillar adjustable guide loop is GM’s first safety-related metal AM part. “BJT allows the assembly of this part to be reduced from four separate components to one complete component, saving time and money. BJT makes this part optimised for targeted strength and weight performance. As GM’s first safety-related 3D printed metal part, this pushes the boundaries of what we can accomplish and facilitates Cadillac’s place at the forefront of innovation and luxury,” Roth stated at the time of the launch [5].
Beyond participating in its conferences and awards competitions, Azoth is very active in other areas of the Metal Powder Industries Federation’s activities. Cochran is on the Board of Directors of the Association for Metal Additive Manufacturing (AMAM), while
“BJT makes this part optimised for targeted strength and weight performance. As GM’s first safety-related 3D printed metal part, this pushes the boundaries of what we can accomplish and facilitates Cadillac’s place at the
forefront of innovation and luxury.” - John Roth, Vice President of Global Cadillac, General Motors.
Forgiarini is a member of the AMAM Standards Committee and served on the Technical Program Committees for the 2023 Las Vegas and 2024 Pittsburgh conferences.
In response to a question about how Azoth markets its capabilities to gain new business, Cochran and
Forgiarini stressed the importance of conferences such as those organised by the MPIF, not only for the technical knowledge exchange and industry networking they provide, but also the marketing reach they give. “Our first customer in a company is often a R&D person,”
they explained, “who is intrigued to see how successfully Azoth can make a specific, often newly designed and developed, part using metal AM. If such efforts are technically successful, the customer’s quality system requirements are met, and the business case makes sense, commercial production orders often ensue.”
Having attended Azoth presentations at the AMPM2023 and 2024 conferences, the author was already familiar with the company’s strong understanding of their customers’ quality system requirements and how they realise that the AM process
itself is just one part of the total value flow, and not necessarily even the most time- or resource-intensive part thereof.
The visit to the company’s site, and the detailed conversations with company management, strongly reinforced those earlier impressions, and understanding Azoth’s relationship with EGC – a strong, established, and pragmatically led organisation with significant resources and clear strategic vision – further explained Azoth’s familiarity with, and rigour in, implementing strict quality management disciplines for both its own and its customers’ requirements.
Combining that with the company’s obviously strong technical skills, process capabilities and savvy
technical marketing, it becomes easy to understand why they have grown to such an extent since their formation in 2017, and are also very confident of significant further expansion in the years ahead.
[1] M. Forgiarini, C. Cochran” Metal Binder Jetting and Metal Material
Jetting as complementary technologies: a user perspective”, Advances in Additive Manufacturing with Powder Metallurgy, 2023, pp. 203-213, ISBN 978-1-943694-40-2)
[2] M. Forgiarini and C. Cochran
Metal Binder Jetting of Automotive Components as presented at the AMPM2023 International Conference
[3] C. Cochran: Speed to Production: A Case Study on Automotive Exterior Badging with Metal Binder Jetting as presented at AMPM2024 Pittsburgh
[4] M. Forgiarini: Metal Binder Jetting of Safety Critical Automotive Components as presented at AMPM2024 Pittsburgh
[5] www.linkedin.com/posts/ activity-7209565381735133184-IAtC/
Cody Cochran
Co-Founder and General Manger Azoth
Ann Arbor, Michigan, USA ccohran@azoth3d.com www.azoth3d.com
Author Bernard North
North Technical Management, LLC Greater Pittsburgh area, Pennsylvania, USA bnorth524@msn.com
MANUFACTURING INNOVATIONS: • Part design
Part Inspection • Tooling • Secondary Operations • Molding • Simulation
• Debinding • Competing Technologies • Sintering
• Coatings
MATERIALS ADVANCEMENTS:
• Metals & alloys
• Ceramics
• Hardmaterials
• Binder Technologies
• Mixing
• Mechanical Properties
TARGETED AUDIENCE:
• Product designers
• Engineers • End users
Manufacturers
Researchers
Educators
Students
Honorary sponsor
Demand for more complex, customized parts is rising fast. Product cycles are shortening, traditional supply chains are evolving, and the importance of sustainability continues to grow. Additive Manufacturing offers you the solutions to meet these challenges and inspire your customers.
Bosch Advanced Ceramics is a global leader in the production of technical ceramics, serving a variety of industries from automotive to medical devices and the chemical industry. Today, the company sees a bright future in ceramic Additive Manufacturing for the series production of parts in increasingly ambitious volumes. This article will present a case study that clearly demonstrates how, using Lithoz’s AM technology, Bosch Advanced Ceramics has been able to develop a micro-sized medical device component that is now in production with an annual run of 50,000 parts.
Bosch Advanced Ceramics purchased its first Lithoz Additive Manufacturing machine in 2014. A decade later, this Bavaria-based ceramic AM pioneer has firmly established itself as a leading global contract manufacturer in its field. With a machine park that includes four Lithoz LCM (Lithography-Based Ceramic Manufacturing) AM machines, among other AM technologies, Bosch Advanced Ceramics is keeping pace with the rapid maturation of ceramic AM as a powerful manufacturing technology.
When contacted to produce thin-walled alumina sleeves for a laparoscopic tool, the hollow part’s small size and complexity presented a variety of new obstacles. This article shows how Bosch Advanced Ceramics successfully achieved and stabilised the parameters necessary to ramp up to serial production, manufacturing an impressive 1,400 parts per batch and, ultimately, reaching an output of 50,000 parts per year on Lithoz’s CeraFab AM machines.
Having been integrated into Bosch’s Blaichach facility in Southern Germany – a site widely known for
producing millions of automotive parts per year – Bosch Advanced Ceramics has benefited from a synergy of in-house expertise and powerful technology since its foundation. Historically, the company was active in Ceramic Injection Moulding as well as ceramic AM. When it invested in its first ceramic AM
machine, it was with the aim of exploring the benefits of the technology and provide functional prototypes for its CIM business. Today, rapidly growing demand has moved AM centre stage as the sole production process, with a machine park of six ceramic AM machines installed, four of which are Lithoz CeraFab machines.
It was early in 2023 when Bosch Advanced Ceramics was contacted by a leading MedTech company looking to design and build a ceramic insulating sleeve as part of a newly developed laparoscopic device used in minimally invasive surgery. After being briefed on the technical specifications of the part, it was clear that as long as the part’s filigree size did not pose too big a challenge to the development team, a positive project outcome would result in the largest number of parts ever produced on a single Lithoz CeraFab build platform.
Thanks to the meticulous quality standards of medical devices, the goal was to combine challenging design features with the repeatable quality levels demanded by the customer – all while achieving a scheduled production of 20,000 parts per year. Key features of the insulating sleeve are shown in Table 1. Due to the limited space available in a laparoscopic instrument, and the high degree of functional integration needed, it was evident that the part would pose a significant challenge to the development team.
Tolerance band requested vs achieved: +/- 50 vs +/- 30 µm
Units requested vs achieved 20,000 vs 50,000
Development time requested vs achieved 6 vs 5 months
“Thanks to the meticulous quality standards of medical devices, the specific challenge was to combine these unprecedented design features with the level of reproducible quality required by the customer – all while achieving a scheduled production of 20,000 parts per year.”
In laparoscopic instruments, electrical insulators separate two conductive components from each other. For safety reasons, a certain electrical creepage distance must be observed to avoid any electrical flashover between the conductive components. The requested ceramic sleeve therefore had to fit inside a laparoscopic device with a maximum external diameter of just 1.3 mm. The miniaturised design follows the growing trend towards smaller, minimally invasive instruments which enable smaller cuts during surgical interventions and thus allow for significantly faster and less painful healing processes for patients.
The ceramic sleeve itself (Figs. 3, 5 and 6) would function as the electrical insulator around a conducting wire with a 0.35 mm cross section. The restricted diameter of the
instrument, as well as the necessary wire width for conducting sufficient electric energy, resulted in an internal diameter of 0.43 mm and a calculated wall thickness of just 90 µm in the upper part of the sleeve.
The sleeve’s complex design and tiny dimensions meant that the customer would only be able to select from two manufacturing processes: micro Ceramic Injection Moulding (µCIM); or an AM approach. When using µCIM, considerations include the potentially high cost of a highprecision micro-mould, challenges in achieving the thin wall thicknesses needed, and limitations in relation to component design and complexity. In contrast, Additive Manufacturing can realise such tiny dimensions while still maintaining
“As AM enables an extremely high level of functional integration, this technology would allow the components to act as electrical insulators that can simultaneously also fulfil mechanical functions.”
maximum precision and resolution – all while offering a near-unlimited level of design freedom which is unachievable using conventional manufacturing methods. As AM enables an extremely high level of functional integration, this technology would allow the components to act as electrical insulators that can simultaneously also fulfil mechanical functions. Thus, the OEM decided upon AM as the process of choice.
When looking at different material options, the desirable properties of technical ceramics (i.e. high chemical and thermal shock resistance and perfect insulating behaviour) made them a perfect choice. For insulation reasons, metal was naturally not considered during the selection process. The use of polymers was quickly decided against for several
reasons – namely, that polymeric materials would be subject to severe chemical corrosion caused by the aggressive sterilisation process for such surgical instruments. Another risk would have been insufficient resistance to high temperatures, as surgical instruments are often sterilised in high-temperature environments. Finally, the risk of bearing sudden electrical discharges meant that polymers were simply not suitable for this application.
Having concluded that the combination of ceramics and Additive Manufacturing would best deliver this application, the OEM turned to Bosch Advanced Ceramics to develop the part. Because of their precision and repeatability in the serial production of highly intricate parts, Lithoz’s LCM AM machines, with a nominal resolution of 40 µm, were chosen as the key technology for this application. The project team also decided on Lithoz’s LithaLox 360 alumina as the ceramic material of choice as this flexible oxide ceramic perfectly satisfied all of the customer’s required specifications in terms of size, precision, and insulation.
Due to its function as a critical MedTech part, any small deviation in quality or dimension would render the overall part useless, meaning only absolute accuracy and reproducibility could be accepted. The Bosch Advanced Ceramics team had to focus on three decisive factors:
“The project team decided on Lithoz’s LithaLox 360 alumina as the ceramic material of choice as this flexible oxide ceramic perfectly satisfied all of the customer’s required specifications in terms of size, precision, and insulation.”
• Fine-tuning the parameters for perfect repeatability even in serial production
• Achieving a smart design of the support structures for the vertically built parts
• Utilising an automated cleaning process to enable risk-free handling of the tiny parts.
After setting a time-scale of six months to enter serial production, an initial volume goal of 20,000 parts per year was agreed.
AM’s ability to fast-track the production and testing of design iterations
Collaboration with the customer during the five-month long sample phase raised the initial challenge of achieving an optimal balance between a minimum wall thickness and sufficient electrical insulation. In order to avoid over-polymerisation and reproduce the tiny features as accurately as possible, various versions of the component would have to be tested to determine the ideal process parameters.
Two central challenges arose during the development of the component. The first was achieving absolute reproducibility, even at series level production. While 1,400 parts on a single platform is certainly possible, it had to be ensured that every part would adhere perfectly to the build plat-
“...four iterations with the same internal diameters were tested, with combinations of varying wall thickness and external diameter. The wall thickness was reduced for each variant before undergoing testing.”
form; any error would damage the batch. Secondly, the team had to try to achieve as thin a wall as possible. Here, four iterations with the same internal diameters were tested, with combinations of varying wall thickness and external diameter. The wall thickness was reduced for each variant before undergoing testing. In case of a successful test, the team attempted even lower wall thicknesses.
It is in these sample phases, where many iterations must be tested to find an optimal design, that ceramic Additive Manufacturing truly comes into its own. When using conventional forming technologies, each iteration requires roughly ten weeks for a full test: four to six weeks for construction and delivery of a mould as well as three to four weeks testing against the fit of the component.
“Using a partially automated cleaning solution developed by Bosch Advanced Ceramics, it was possible to simultaneously clean a large number of these parts very gently without damage. This was a crucial step in achieving consistent quality...”
Using ceramic Additive Manufacturing, however, the entire mould step could be skipped and the four sample part iterations created directly. In this way, Bosch Advanced Ceramics ultimately saved its customer a minimum of eight months of lead time, as well as the related tooling costs associated with producing moulds.
The cleaning of the components also played a key role. After the build step, the ‘green’ parts are particularly fragile, with excess material still attached. Green parts must be handled extremely carefully using a very specific procedure to remove this excess material and avoid any damage to their fragile structure. Using a partially automated cleaning solution developed by Bosch Advanced Ceramics, it was possible to simultaneously clean a large number of these parts very gently without damage. This was a crucial step in achieving consistent quality and manufacturing reliable parts even at a large scale.
Ultimately, a suitable balance was found between effective part design, ideal process parameters and the technological and material limits to realise the part requested by the customer. However, the next challenge arose: figuring out how to scale up from sample to high-volume
series production. When scaling up, it is essential to maintain the same level of quality and consistency in every batch. This level of reproducibility must be achieved regardless of the material batch, number of build jobs or furnace cycles. When leaving the sample phase, every single step of the entire process chain plays a critical role in reducing the scrap rates of the parts produced and fulfilling the requirements of the customer.
When considering the design restrictions, it was crucial that series production of the final part had as little fluctuation as possible. The customer defined a maximum tolerance of ± 50 µm, meaning there was very little room for deviation. Thanks to its long experience manufacturing and scaling up multiple production processes, however, Bosch Advanced Ceramics could leverage its knowledge to ensure that every part produced complied with the rigorous quality standards required for this application.
As the project reached its conclusion, 200 parts were randomly selected out of each 1,400 batch to undergo quality testing. After individually testing each of these parts, the final design was determined to have a tolerance band of ± 30 µm – significantly below that specified by the customer.
After five months of cooperation with the customer, Bosch Advanced Ceramics achieved the set volume goal of 20,000 parts per year. Such
a large part volume was possible due to the extremely high number of parts produced in one build run. Using a combination of smart design, powerful LCM technology, an alumina material, and the expertise of both Bosch Advanced Ceramics and Lithoz, it is remarkable that 1,400 medical device parts could be produced using just a single build platform.
Thanks to this outstanding achievement in serial production, the initial goal was then increased even further. A new target of 50,000 parts per year was set – more than double the initial requirement ordered by the customer. Further testing and cooperation were needed to scale up by such a significant amount, with the main focus once again being placed on achieving the highest possible level of quality at an exactly reproducible scale.
Bosch Advanced Ceramics was then able to ramp up serial production to 50,000 parts per year. This significant scale-up marked the project as a true success, proving the power of LCM technology and ceramics when entering serial production for complex parts. Despite the vast number of parts produced per batch, each part maintained the same high level of quality and achieved an outstandingly low wall thickness as required for the application.
The transition from prototyping to large-scale serial production was enabled by the unique advantages of LCM technology, which offered unparalleled precision, repeatability, and design flexibility – all critical factors in the manufacture of the complex and miniature components required for modern laparoscopic tools.
The use of high-performance ceramic materials such as LithaLox 360 alumina played a pivotal role in meeting the stringent technical requirements, such as high thermal resistance, chemical stability, and electrical insulation. These prop -
erties, combined with the CeraFab machine’s ability to produce extremely fine details with a resolution of 40 µm, allowed Bosch Advanced Ceramics to achieve the necessary wall thickness of just 90 µm, a challenging feat for traditional manufacturing processes. Bosch Advanced Ceramics’s expertise in handling the fragile green parts post-build, through its proprietary cleaning processes, ensured the integrity and quality of each piece, further demonstrating its comprehensive mastery over the entire production chain.
By successfully scaling production from 20,000 to 50,000 parts annually, while maintaining consistent quality, Bosch Advanced Ceramics has set a new benchmark in the
industry. This achievement not only validates the capabilities of Lithoz’s technology and materials in highvolume, high-precision manufacturing but also highlights Bosch Advanced Ceramics’s role as a pioneer in the field. Its journey reflects a seamless integration of innovative technology, materials science, and industrial expertise, paving the way for future advancements in ceramic Additive Manufacturing.
Contact
Ashu Sharma Chief Sales Officer
Bosch Advanced Ceramics ashu.sharma@bosch.com www.bosch-advanced-ceramics.com
Authors
Norbert Gall and Alice Elt Lithoz GmbH Mollardgasse 85a 1060 Vienna Austria sales@lithoz.com www.lithoz.com
Vacuum debinding and sintering furnaces from Elnik Systems LLC are a common sight in Metal Injection Moulding plants throughout Europe and the Americas. Thanks in part to the technical guidance and training available through its sister company, DSH Technologies, Elnik Systems’ market-leading position has seen it support a multitude of new manufacturing operations. Now, with the rise of sinter-based Additive Manufacturing, the need to meet the high demand for the company’s products has driven a relocation and major expansion. Nick Williams reports for PIM International .
Elnik Systems is a specialist manufacturer of debinding and sintering furnaces whose technology has been widely used by the Metal Injection Moulding industry for more than thirty years. The rise of sinter-based Additive Manufacturing processes such as Binder Jetting has created an upsurge in demand for the company’s products and, as a result, the company outgrew its original home in Cedar Grove, New Jersey, and recently completed a major expansion and relocation to Pineville, a suburb of Charlotte, North Carolina.
In explaining the decision making process behind the move, Stefan Joens, president of Elnik Systems, told PIM International , “Elnik achieved considerable growth from 2018-2022, almost doubling our annual equipment output. We simply ran out of space in our building. We needed to make a decision between either relocating to a new facility elsewhere in our home state of New Jersey, which would require many of the team members to move closer to a new base, or finding a completely
new home that would provide additional opportunities for both our team and the company.
“Relocating out of a high-cost state that is not manufacturing friendly to a lower-cost state that makes a big effort to support manufacturing
was a great motivator. As a former financial planner, I also recognised the improvement in our team’s lives that would come with the move. So, collectively, we made the decision to find a new home for our future. That home is Charlotte, North Carolina.”
The company’s new facility is more than double the size of its former home. Whilst the move has transformed operations, continuity was achieved thanks to so many team members taking the decision to relocate. Joens stated, “We increased our building space from 20,000 ft 2 to 50,000 ft 2 [1,850 m 2 to 4,650 m 2], and the new building is also double the height of our old building. We were fortunate enough to relocate twenty-one of our forty teammates, and we retained eight onboard in New Jersey working remotely. Since our relocation, we have also hired nine people in North Carolina. We are at thirty-eight teammates now, and still hiring for a few roles.”
Bruce Dionne, VP of Operations, stated, “The new facility has been designed to place Elnik in the best position to meet the challenging demands of industry growth. Production efficiency and safety considerations were paramount in the facility design, and every aspect of the production process was carefully considered so that the new facility provided solutions to the challenges that we experienced in the old facility. I am very excited about the future in this space. It allows us to fully implement lean manufacturing principles and scale up or down to meet our customers’ needs efficiently and agilely.”
“The new facility has been designed to place Elnik in the best position to meet the challenging demands of industry growth. Production efficiency and safety considerations were paramount in the facility design, and every aspect of the production process was carefully considered.”
The extra space now available for operations has allowed the company to handle incoming and outgoing shipments with the greatest of ease and allows it to manage workflows in a far more efficient manner. “In the old building, having to prepare days in advance for the shipment of a large furnace would cost us days of downtime in the shop. The walkways and lanes being much bigger also add a major upgrade to safely move machines and equip -
ment. The training room in the new building is something that the team feels very good about and is glad to have the space,” stated Kyle Rech, Shop Foreman at Elnik Systems.
Joens stated, “The move to this new facility will allow us to continue to improve our operations in order to support our expanding customer base. We onboarded three new pieces of equipment to allow us to do more of our fabrication in-house, helping control our schedule. We’re also developing additional equipment for our product offering, which will allow us to push innovation and create opportunities for the industry.
“Additionally, with our new large training room, we plan to start holding seminars and workshops with our customers, industry partners and potential technology starters. The move puts Elnik in the best position to support its customers throughout the world.”
“...with our new large training room, we plan to start holding working seminars and workshops with our customers, industry partners and potential technology starters.”
Nick Cifaratta, Engineering Manager at Elnik Systems, stated, “The things I reflect on most contrasting our new facility to old are the atmosphere, the opportunities, and the possibilities. The atmosphere in the new shop is very different from the New Jersey shop, mainly in the sense that our new shop displays our commitment to excellence and quality so much more
effectively. In the old shop, the welding area, the machine shop, the electrical department – really, everywhere – was so densely packed. While everyone had the same commitment to excellence and quality there as we do here, the layout, cleanliness, and general appearance of the shop in North Carolina demonstrates these core values much more clearly.”
Over the last thirty years, Elnik Systems grew in line with the rise of the MIM industry. More recently, however, there has been a surge of interest in sinter-based AM. Commenting on whether this move would have been possible without the boost that AM has brought, Joens stated, “The metal AM industry has been a big part of our growth since 2017. We’ve built solid relationships with technology partners, supporting their knowledge and customer base, and that has afforded us a great start. The growth of sinter-based metal AM sparked the need for more space. The relocation out of state was driven by a number of factors, but the ability to control more of our production processes in house was critical.”
“There are companies that are using this technology and making money with it, but their actual number is currently small. Those companies that are successful either have a proven background in processing powder metal parts, including sintering, or have taken the time to learn the science.”
Whilst sinter-based AM processes such as Binder Jetting are dominating the AM industry’s headlines, as well as conference presentations and activity in the wider research community, there are few signs that serious volume production is underway. Commenting on the status of the sinter-based AM industry, Joens stated, “The future of this industry is extremely bright but, like all new technologies, there were technical challenges that had to be overcome. The MIM industry had a similar start: over hype and excitement with a few companies leading the way, then some disillusionment, followed by success and eventual the growth of a new industry - the Gartner Hype Cycle all over again.”
“There are companies that are using this technology and making money with it, but their actual number is currently small. Those companies that are successful either have a proven background in processing powder metal parts, including sintering, or have taken the time to learn the science, work with training and development partners like our sister company, DSH Technologies, and implement what they have learned.
“The processes work, but there are factors that have caused hesitation among newcomers. Inflation is still high in 2024, and working through distribution channels has caused some equipment pricing to be inflated. There was also an ‘overpromise/underdeliver’ start to the technology’s launch. Of course, the entire AM market is heavily funded by investment money which demands returns. Sinter-based AM, being one of the more challenging groups of AM processes from a technology perspective, doesn’t necessarily suit a fast return approach. That said, the technology does present new manufacturing approaches that will open doors we didn’t even know existed. MIM partsmakers are now very successful with their technology, but it took time to get MIM to become a known, proven manufacturing process – and even now it doesn’t have the full visibility that it deserves. Sinterbased AM will follow the same path, but the timing can be accelerated if companies dedicate time to learning the science and work with companies that are willing to help.”
Commenting on how he sees the timescale for the rise of Binder Jetting, and where we’ll see the biggest successes, Joens stated, “As previously mentioned, the process will most likely follow the MIM industry growth pattern, but faster. There are more resources to draw upon to help become successful. I also believe that the successes of the technology will follow that of the MIM industry, where, broadly speaking, each world region is now known for its specific applications. For example, the European MIM industry has been historically strong in automotive and luxury goods applications, North America has had a strong medical device and firearms focus, and Asia found success in consumer electronics applications such as smartphones.
“People and companies tend to work in the spheres that are familiar to them. Still, until users of the technology understand how to promote and sell the value add of sinter-based AM vs other proven technologies, it will struggle.”
Joens stated that there have been some great recent successes in sintering aluminium which, he believes, will entice new markets to open their doors to the use of this technology. “Copper is also a unique material that, when the processing requirements are followed properly, will excite the electronics world as it enables the production of compo -
nents that require good electrical conductivity and heat transfer with designs that are not possible through existing technologies,” explained Joens.
“I strongly believe that each material type, including stainless steels, low alloy steels, and titanium, will offer considerable design freedoms that other technologies have lacked the ability to provide in the past – so long as the processing requirements are properly followed.”
Binder Jetting, on the back of companies such as Desktop Metal, HP, and Digital Metal (now Markforged) is the most visible of the sinter-based AM technologies. There are, however, a diverse range of other sinter-based AM processes, from Headmade’s ColdMetalFusion (CMF) to those developed by companies such as Incus, Tritone and XJet.
Commenting on this diverse technology landscape, Joens stated, “This complex landscape highlights one of the challenges that we face: all these companies and their technologies have pros and cons, but one single technology isn’t capable of making every part that you may need. For example, BJT technology is challenged by some design limitations due to the potential to trap powder. Other sinter-based AM processes eliminate this issue and provide better opportunities for certain design concepts, but they may not be able to meet the throughput potential of BJT.”
Joens added, “Vat Polymerisationbased process used by Incus, and XJet’s Material Jetting process, are, on the other hand, opening doors for applications where there is a high requirement for surface finish and fine detail that other technologies struggle to match. The CMF process is also very unique and has a ton of potential. Having an isotropic shrink rate, similar to MIM, means that there are fewer variables to consider when making parts. However, like other newer technologies before higher volumes are available, raw material costs are still a tough conversation point, especially when comparing to known part making technologies. But this will improve and allow CMF to be a more adopted technological process.”
The issue of cost comparisons with other technologies, believes Joens, is still one of the biggest challenges when evaluating sinter-based AM. “When comparing sinter-based AM to an established manufacturing method, it is hard to justify
the cost since existing technologies have worked through the cost model challenges. Sinter-based AM therefore needs to promote its ability to reduce total cost based on inventory reduction, part consolidation or, most importantly, being able to make a part with functions and features that are not possible by any other manufacturing process. As with any manufacturing technology, there is no one-size-fits-all method.”
DSH Technologies supports businesses with consultancy services, technical support and toll debinding/ sintering as they start on their MIM or sinter-based AM journey. Commenting on how the demands from customers have changed with the arrival of sinter-based AM, Joens stated, “We have supported the metal powder part-making industry’s adoption of MIM for more than twenty-five years. With sinter-based AM, many of the problems are the same; it’s all science at the end of the day. Engineers designing parts need to understand the part life cycle. Chemistry (carbon, oxygen, nitrogen, etc), metallography/mechanical properties (hardness, grain size, tensile strength, surface finishes, etc) are all the same analysis points being used once the parts have been sintered.
“One of the biggest challenges the AM industry suffers from is that too many people consider the debinding and sintering process steps as ‘postprocessing.’ They are not – they are critical ‘in-process’ steps, just like they are with MIM. Many of the same variables of MIM part making apply to sinter-based AM technology.”
Bryan Sherman, Chief Metallurgist and project manager at DSH Technologies, stated, “With the recent rapid growth in powder-based Additive Manufacturing, we have seen a similar increase in the need for process education and process development. Many of the people getting involved in this rapid growth have never heard of debinding or sintering.
Whilst Elnik is US-based, it has an operation in Germany to support the onboarding of European customers. Joens explained, “Elnik is headquartered in the US and has been for fifty-five years. In 2017, we decided to open Elnik Systems GmbH, a European branch, to better support our customer base there. This facility is located in the Black Forest area of Southern Germany. At this facility, we have two local field service technicians,
spare parts for all our equipment, a MIM3045 debind/sinter furnace with all the bells and whistles, as well as a CD 3045 debind oven.”
“These pieces of equipment allow local companies to experiment with our technology and we offer small-batch production processing as well. Based on our continued growth in Europe and the desire to serve that customer base better, we realised the need to have a local facility and team.”
“One of the biggest challenges the AM industry suffers from is that too many people consider the debinding and sintering process steps as ‘postprocessing.’ They are not - they are critical ‘in-process’ steps, just like they are with MIM. Many of the same variables of MIM part-making apply to sinter-based AM technology.”
It is in these cases we can really shine at DSH through our educational and process development work. When given the opportunity to get one-onone with customers and really teach them about the science behind what is happening in the various process steps, we can help customers build the fundamental base of understanding that is much needed for new entrants into sinter-based AM.”
Responding to the question of what advice would he give to anyone considering setting up a sinter-based AM production line who has never been involved in sintering before, Sherman stated, “Don’t try to figure it all out by yourself. Ask for help and recognise that the investment in that help will reduce the total cost over time. We are big believers in failures as a lesson – but it’s great to reduce the potential for failure and learn from people who have made them already. Be open to working together with neutral companies like DSH Technologies.
“The single most important piece of advice we can give to new sinterbased AM participants is to take the time to understand the fundamental science that drives a successful process. Without that, it is very difficult to understand what actions and reactions are correlated and to answer the ‘why’ when a process failure occurs,” concluded Sherman.
Despite appearing to be in the shadows of sinter-based AM, there is still huge potential in the MIM industry. Commenting on how he sees the current state of MIM, Joens stated, “There is still plenty of growth in the MIM industry, but there are changes happening. In recent years I have seen many companies bringing the technology in-house instead of buying parts from external – and primarily overseas – suppliers. This
was due to quality, lead times, and a renewed focus on supply chain security and a desire to reshore manufacturing.”
“Technologies such as Binder Jetting have caused people to take a step back and ask if they are doing all they can to save money and take control of the process. The AM industry has helped to shine a light on MIM and, in some cases, has helped companies expand into new markets.”
With regards to the overall awareness of MIM, Joens believes that progress has been made over the last twenty years, most recently as a result of the attention that sinterbased AM processes have received. “MIM is a small manufacturing technology that has had a big impact on the world. MIM missed its ‘marketing potential’ in the early years, and I feel still falls short of the visibility that it deserves. Binder Jetting, in contrast, had amazing visibility early on, but then so much of it became tainted by hype.
“What MIM and sinter-based AM both need in order to succeed is more awareness of the actual parts being made with the technologies. When engineers who design parts are aware of the full range of manufacturing processes, success begins. It’s amazing how many automotive company engineers have no idea what MIM even is! We need to promote established applications more, and for that we have to find ways to address the NDA [Non Disclosure Agreement] culture and make allowances for part promotion without giving away Intellectual Property. It’s not an easy discussion or solution, but it’s needed in order for part makers to have an eye on potential.”
Commenting on technology trends in the MIM industry, Joens stated, “The way first stage debinding is approached appears to be changing. Parts makers debinding with solvents are trying to move away from flammable solvents. I see the US market being a big leader in this push. In catalytic debinding, there is also a push to move towards oxalic acid
debinding instead of using nitric acid. The reduction in operational risk will be a big win for part-makers.
“Furnace technology use still remains company specific: some users like small batch furnaces to have control over production flow; some users enjoy large batch furnaces to help reduce part costs, whilst others have experience working with continuous furnaces over batch. While each furnace type provides its unique advantages, I believe company operational philosophies will continue to rule for years to come.
“We have also noted the integration of sinter-based AM into MIM houses for a number of different reasons. These can be to help onboard new customers through small-batch part production that is unsuitable for MIM cost structures; to open doors to new part concepts related to consolidation of various parts or additional part functionality; and to improve the part-making process for MIM itself with innovations in mould design and the
“We would recommend that a MIM company is completely clear why they are looking to add sinter-based AM. Is it to develop prototypes that will become MIM parts? If so, that will be one type of AM machine recommendation. If it’s to add new production methods to develop new parts [....] that would be a different machine recommendation.”
reduction in cost or time to make a mould by using inserts to standard mould tools.”
There has been a clear trend in MIM companies taking the lead in the adoption of sinter-based AM technologies. When asked what specific advice would be given to MIM companies that are looking
at the technology, Joens stated, “We would recommend that a MIM company is completely clear why they are looking to add sinter-based AM. Is it to develop prototypes that will become MIM parts? If so, that will be one type of AM machine recommendation. If it’s to add new production methods to develop new
There is a world of difference between industrial metal Binder Jetting machines and sub-$1,000 Fused Filament Fabrication (FFF) machines that have the ability to make ‘green’ parts using any number of off-the-shelf filaments.
When asked if there is a future for ‘hobbyist’ or small-scale sinter-based AM, using either coupon-based sintering services or mini-furnaces for those who can afford them, and if this is the democratisation of industrial technologies taken too far in a hobbyist’s garage, Joens responded, “This is a great question. While I believe almost anything can be achieved in life if you put your mind to it and surround yourself with creative people, getting the full line of
equipment needed to process sinterbased AM parts into the hands of a hobbyist is a really big challenge. In order to get processing equipment costs low enough for something like this, end results will be sacrificed.”
“Everything comes down to what kind of part is trying to be made and what its use is. Coupon- or batchbased debind/sinter services are the best way to get involved in this part-making method without the big expense, but with that comes longer process times to get a complete part. Another option would be to have established AM part makers offer up space in their machines if that is available. I know companies that do this in the polymer AM industry – maybe this concept can apply to sinter-based AM and offer another lower cost option for the hobbyist.”
“...getting the full line of equipment needed to process sinter-based AM parts into the hands of a hobbyist is a really big challenge. In order to get processing equipment costs low enough for something like this, end results will be sacrificed.”
parts and expand their offerings to customers, that would be a different machine recommendation.”
“Moving a company across a parking lot is challenging – moving it 600 miles to a new home is a major undertaking. The most gratifying part of this entire process for me is
looking back, knowing we made the decision as a team and managed the entire process together as a team,” explained Joens. “What made the process successful was the culture we’ve built at Elnik over the years. When faced with challenges, our team continuously steps up and takes action.”
From a manufacturing perspective, Dionne stated, “Losing a few talented senior team members created challenges that needed to
be overcome. This challenge was bittersweet in that we lost some manufacturing experience but, in exchange, we met this challenge by rewriting how certain processes are completed, with improved results.”
Claudia Baumgartner, Elnik Systems’ Finance and HR Manager, shared insight into the move and how the process was managed. “The New Jersey facility was the centre of our operations, but we needed to grow and develop new technologies, and increase production, while simultaneously introducing these new technologies to the world. To do this, we needed more space. Pineville is a fabulous area that is developing and growing just as fast as we are. Our new facility is 2.5x bigger, which offers the possibility of expansion, growth and advancement. The most important thing about the move is that we were also able to pack the heart and soul of our company for this new journey.
“Everybody in the company was involved in the process, and everyone had a role in this incredible opportunity. The company’s management was central to the move’s success, providing employees with information, options, and knowledge about the area as they shared the future vision of the company. The final agreement was signed as a group in front of everybody who was part of Elnik.”
Baumgartner continued, “A few people couldn’t make the move, but they agreed to assist and support the rest of the members. We moved over twenty families; that implies new homes, new areas and, in many cases, new schools and new jobs for their partners. Even though everybody’s case was different, we all shared the same goal: to help and make this a great opportunity for our future success. As a result, we helped the person next to us achieve their goals, whether it was learning to operate a new piece of equipment or simply being supportive through all these changes.”
Elnik Systems is, of course, a family business, founded by Stefan
Joens’s father, Claus. “Claus has been an incredible role model in the industry, to our team, and to me. I’ve learned so much watching how he handled business challenges over the years that provided me with the grit and strength to even suggest this concept to our team. I remember that, during the presentation to the team, Claus shared how proud he was of what we had accomplished since he retired and that he was extremely excited about the opportunity. He has always been a big believer in the fact that change brings opportunity. While he is sad that the business is now a flight away instead of a drive away, he is incredibly proud that the future of Elnik is strong, and our new home provides a lot of opportunities to support new markets,” stated Stefan Joens.
When considering the success of Elnik Systems to-date, Joens stated, “We work together with our customers to solve their problems with real-world solutions. Our furnace technology lasts for years; our first MIM furnace is still in operation thirty years later and we are still supporting furnaces that were built in the late ‘70s and early ‘80s. We have not strayed from this philosophy of ‘workhorse equipment that lasts.’
“Additionally, we are focused solely on industries that debind and sinter parts. For the last twenty-plus years, this has equated to 90% of our throughput. Claus was a strong believer in finding something you enjoy and being the best at it. When it comes to the batch furnace industry for debinding and sintering, we have done just that. We do not offer continuous furnaces, or ceramic furnaces, we make graphite and metal versions of debind and sinter furnaces. And we use them ourselves as well.”
“Started by Claus and Bryan Sherman in 1999, led by Satyajit Banerjee for fourteen years, and now having Bryan Sherman back leading the efforts, our ability to support the technical and science-based process side of this technology is paramount. There are great furnace makers in this world, many of which we hold in high regard. But when it comes to helping customers, it is about more than just keeping the furnace running; supporting customers in the science is where we stand out. And it’s one of the critical steps that Elnik’s customer base is most proud of when looking back on making the decision to work together,” stated Joens. “Elnik’s future will continue to focus on how to best support powder metal part makers with more product offerings and levels of support through improved technology and user experience. We have listened to
our customer base a lot over the last five years and are working on some amazing innovations to help improve the part making process.”
“DSH Technologies will continue to offer process services through its equipment in house, but where DSH will really grow will be in process support and engineering. There has been a ‘changing of the guard’ so to speak over the last five years, with many technology experts exiting the industry due to retirement or new opportunities. The next five years are going to see even more of this take place. We believe strongly that our mission needs to be knowledge transfer, science-based solutions based on real-world experiences, and helping to grow the metallurgical knowledge of the next generation.”
Contact Stefan Joens President Elnik Systems sjoens@elnik.com
www.elnik.com
Metal Injection Moulding is one of the most capable manufacturing processes for small precision components, yet it is also one of the least well known. This article presents 2024’s award-winning MIM parts from the Metal Powder Industries Federation's PM Design Excellence Awards. In addition, we also highlight the growing number of award-winning parts produced by sinter-based Additive Manufacturing. These examples present an opportunity for product designers and engineers to consider how they might use MIM and AM in their own projects.
The winners of the 2024 PM Design Excellence Awards competition, sponsored by the Metal Powder Industries Federation (MPIF), were announced at PowderMet2024. Ten Grand Prizes and seventeen Awards of Distinction were presented in this year’s competition, and entries were divided into three categories: Conventional Press and Sinter PM, Metal Injection Moulding, and metal Additive Manufacturing.
The winners demonstrate outstanding examples of the PM industry’s diversity and ability to meet critical requirements. From musical instruments to surgical devices, part manufacturers have demonstrated PM’s versatility and unique ability to challenge competing technologies.
This article highlights award winners in the MIM category, and parts in the AM category that are produced by a sinter-based process. It is encouraging to see MIM and sinter-based AM components finding applications in electric vehicles, as well as continuing to enjoy success in established markets.
In the Military/Firearms category for MIM components, a Grand Prize was awarded to TriTech Titanium Parts LLC, Detroit, Michigan, US, and its customer, Primary Weapons Systems, Boise, Idaho, for a titanium universal trunnion in an innovative rifle platform that provides quick barrel changing and allows one weapon to fire multiple calibers with minimal changeover of parts and time (Fig. 2).
The trunnion requires annealing for post-machining ease but does not need Hot Isostatic Pressing (HIP) processing in order to meet customer performance requirements. CMM inspection was followed by a 20,000 round firing test. The part was originally intended to be made via Laser Beam Powder Bed Fusion Additive (PBF-LB) Manufacturing, but inconsistent strength, rougher surfaces, and higher cost made that option unviable.
In the Hand Tools/Recreation category for MIM components, a Grand Prize was awarded to APG-MIM, a Division of Nichols Portland Inc based in Ridgway, Pennsylvania, and its customer, Paige Musical, for a six-string guitar capo assembly comprising a saddle, adjustment guide, bar, and yoke (Fig. 3). A capo is used to temporarily shorten the strings on a guitar, raising the pitch of the unfretted or ‘open’ strings and changing the key of the openposition chords.
The very challenging part design led to issues with tool design, moulding, debinding, and sintering operations. Customised ceramic setters, and an optimised two-stage injection moulding process, were required for the successful manufacture of the part. The adjustment guide has an as-moulded thread, and no secondary operations are needed for manufacture and function.
Medical/Dental: MIM
In the Medical/Dental category for MIM components, a Grand Prize was awarded to Advanced Powder Products, Inc, Pittsburgh, Pennsylvania, for a screw chuck used in orthopaedic surgery (Fig. 4). The part is used in a larger assembly that allows a surgeon to drill screws into the spinal regions of patients. Once the screw is inserted, the assembly needs to be broken in two and easily removed. Initially, the part was presented as a one-piece design. However, after extensive design modifications, the MIM solution was a two-piece assembly that needed to be joined by laser welding.
Medical/Dental: AM
In the Medical/Dental category for metal AM components, a Grand Prize was awarded to 3DEO Inc and its customer, Zimmer Biomet, for bone marrow harvester parts (Fig. 5). Advanced suction curettage technology can harvest small to large volumes of cancellous (trabecular) bone and non-diluted bone marrow aspirate in a few minutes through a minimally invasive incision.
3DEO’s sinter-based Additive Manufacturing process eliminates
the complexity and expense associated with tooling, and postprocessing operations and waste is minimised. 3DEO is an Additive Manufacturing service bureau that uses an in-house patented process
called Intelligent Layering. The technology is a fusion of Binder Jetting (BJT) and CNC machining that, the company claims, is faster, cheaper and capable of higher resolution than BJT alone.
A Grand Prize was awarded in the Electronic/Electrical Components category for MIM components to MPP, Noblesville, Indiana, and its customer, Tactile Engineering, Lafayette, Indiana, for a core plate used in its Cadence Tablet that has a refreshable braille display for the vision impaired (Fig. 6).
The core plate is an extremely challenging part to produce that requires strict adherence to tight tolerances, flatness, absence of flashing, and magnetism. The device uses magnetic latching that requires a specific amount of holding force for effective operation. Traditional machining waste would be more than 40%, and machined parts would cost at least 10x that of MIM parts.
In the Automotive–Engine category for MIM components, an Award of Distinction was given to INDO-MIM Pvt Ltd, Bengaluru, India, for a lever used as a gas-flow controller in the turbocharger of internal combustion engines (Fig. 7). The lever has a U-shaped geometry with an open slot at the rear end, a through-hole at the front, with another through-hole passing through the slot.
MIM processing reduced lead times and was able to produce the high volume of parts needed weekly by the customer while significantly reducing waste material compared with a forging process.
In the Automotive–Electric Vehicle category for MIM components, an Award of Distinction has been given to Hangzhou Sino-MIM Technology Co Ltd, China, for a ratchet shaft used in the parking brake system for new electric vehicles (Fig. 8). The motor moves the splined part to rotate the ratchet shaft so that the cam contacts the disc brake for
locking and parking. The spline of the ratchet shaft has a tight tolerance, so fixturing was used during sintering to maintain the part geometry and reduce final machining. The MIM part results in a 20% cost saving compared with a fully machined component.
An Award of Distinction, in the Automotive–Electric Vehicle category for metal AM components, was presented to Azoth for a seatbelt pillar adjustable guide loop for its customer, General Motors (Fig. 9). The part is used in the all-electric Cadillac Celestiq. The stainless steel part is produced by Binder Jetting (BJT) and sintered to 97% relative density. The surface of the part is semiautomatically polished prior to a multi-layer bright nickel-chrome plating operation to improve corrosion performance and provide a hard, scratch-resistant surface.
In the Military/Firearms category for MIM components, an Award of Distinction has been given to PTI Tech, Clifton, New Jersey, for an inertia weight in a bolt assembly for a blowback firearm (Fig. 10). Tungsten heavy alloy was selected as the material choice for the part that requires a high specific gravity material to obtain the necessary mass in the allotted volume. Tungsten heavy alloys cost 5–10x that of alloy steels and near-net shape processing is needed to minimise raw material costs. Machining the part from bar stock would result in over 70% swarf.
An Award of Distinction, in the Military/Firearms category for MIM components, was also given to ARC Group Worldwide, Longmont, Colorado, and customer Halo Ammunition for a 45-caliber bullet. The bullet is a solid copper projectile that uses a copper feedstock along with a proprietary binder formulation to ensure even
MPIF)
and complete sintering with minimal distortion (Fig. 11). The petals were redesigned to be better suited for injection moulding. There is no machining scrap and scrap from tool set up can be recycled.
In the Industrial Motors/Controls & Hydraulics category for MIM components, an Award of Distinction was given to INDO-MIM for a cone
that acts as a fluid controller in a fuel pump (Fig. 12). Moulding this complex part, with thirteen multiple steps and cross-holes, without merging lines and weld-line defects is a challenge. The intricate profiles of the part have tight tolerances.
In the Electronic/Electrical Components category for MIM components, an Award of Distinction was also given to SMTG for an aluminium alloy smart-watch case (Fig. 13). The thin, complex sections of the part require use of a high-fluidity feedstock and a high-speed moulding machine. The curved surface of the watch cases necessitates manual polishing to a mirror finish and the parts are anodised to various colours. The light weight of the aluminium alloy parts compared with ones made using stainless steel is a significant benefit.
An Award of Distinction, in the Electronic/Electrical Components category for MIM components, was given to Hangzhou Sino-MIM Technology Group (SMTG) for an ultra-thin base plate used as a heatdissipation module in an optical communication 5G base-station (Fig. 14). Numerous components
are mounted on the product’s surface, which serves not only as the mounting base but also conducts and dissipates heat. MIM processing cut the product cycle time and reduced the cost of the product by 45%.
An Award of Distinction in the Hardware/Appliances category for metal AM components, was presented to APG-MIM, a Division of Nichols Portland Inc, for 150 mm pneumatic chuck jaws for work-holding during precision turning (Fig. 15). The parts are made using Moldjet technology from Tritone Technologies. This sinter-based Additive Manufacturing process allows inner-lattice structures to be formed without having to de-powder, eliminating the risk of any powder entrapment in difficult-to-access areas. Moldjet processing generates little waste, and the wax used to form the in-process mould is recovered and can be re-used for the next build.
15 APG-MIM, a division of Nichols Portland Inc, won an award for these 150 mm pneumatic chuck jaws for work-holding during precision turning. The parts are made by a sinter-based AM process, called Moldjet, developed by Tritone Technologies (Courtesy MPIF)
Fig. 16 Azoth and its customer, Sur-Set Connect LLC, won an award for these electromedical connector components comprising a set screw, set screw block, and a spring housing. These sinter-based AM parts are made using XJet's Material Jetting (MJT) process (Courtesy MPIF)
In the Medical/Dental category for metal AM components, an Award of Distinction was awarded to Azoth3D and its customer, Sur-Set Connect LLC, for electromedical connector components comprising a set screw, set screw block, and a spring housing (Fig. 16). These components mate with the associated catheter and provide mechanical feedback to the
surgeon ensuring proper insertion of the catheter in the patient.
The very small size and complexity of these components led to depowdering issues when made using Binder Jetting. The problem was overcome by changing to XJet’s material jetting (MJT) process. The parts are produced in 316L stainless steel with high resolution and good surface finish.
Metal Powder Industries Federation 105 College Road East Princeton, NJ 08540 USA info@mpif.org www.mpif.org
PIM International is the only business-to-business publication dedicated to reporting on the technical and commercial advances in the MIM, CIM, and sinter-based Additive Manufacturing industries. Available in both digital and print formats, PIM International is the perfect platform to promote your company to a global audience.
Advanced Technology & Mat. Co., Ltd.
www.atmcn.com/english
Powders 24 www.continuumpowders.com Epson Atmix Corporation 08 www.atmix.co.jp
Hunan Hualiu New Materials Co., Ltd. 40 www.hlpowder.com
Indo-US MIM Tec Pvt Ltd 51 www.indo-mim.com
Jiangxi Yuean Advanced Mat. Co., Ltd. 62 www.yueanmetal.com Kymera International 11 www.kymerainternational.com
Metal
www.ldpowder.com
www.schunk-mobility.com
print edition is distributed at numerous industry events worldwide as well as to a core subscriber base. All past editions of PIM International magazine are freely accessible via our digital archive, adding extended exposure for your brand and products. For more information contact: Jon Craxford, Advertising Sales Director Tel: +44 207 1939 749 jon@inovar-communications.com
PIM International is dedicated to driving awareness and development of the MIM, CIM and sinter-based AM industries and their related technologies. Key to this aim is our support of a range of international partner conferences.
View our complete events listing on: www.pim-international.com
Euro PM2024 Congress & Exhibition September 29 – October 2, 2024 Malmö, Sweden www.europm2024.com
The Advanced Materials Show USA October 8–9, 2024 Pittsburgh, PA, US advancedmaterialsshowusa.com
World PM2024
October 13–17, 2024 Yokohama, Japan www.worldpm2024.com
AM Ceramics 2024
October 23–24, 2024 Berlin, Germany www.amceramics.cc
Advanced Engineering October 30–31, 2024 Birmingham, UK www.advancedengineeringuk.com
Formnext November 19–22, 2024 Frankfurt, Germany www.formnext.com
FPM 42 nd Hagen Symposium 2024 November 28–29, 2024 Hagen, Germany www.hagener-symposium.de
ASEAN Ceramics
December 11–13, 2024 Ho Chi Minh City, Vietnam www.aseanceramics.com
International Conference on Injection Molding of Metals, Ceramics, and Carbides (MIM 2025)
February 24–26, 2025 Costa Mesa, CA, US www.mim2025.org
PM China 2025
March 10–12, 2025 Shanghai, China en.pmexchina.com
Fraunhofer Direct Digital Manufacturing Conference DDMC 2025
March 12–13, 2025 Berlin, Germany www.ddmc-fraunhofer.de
AM Forum Berlin
March 17–18, 2025 Berlin, Germany www.am-forum.de
AMUG 2025
March 30–April 3, 2025 Chicago, IL, US www.amug.com
Formnext Chicago 2025
April 8–10, 2025 Chicago, IL, US www.formnextchicago.com
RAPID + TCT 2025
April 8–10, 2025 Detroit, MI, US www.rapid3devent.com
PowderMet 2025 | AMPM 2025
June 15–18, 2025 Phoenix, AZ, US www.powdermet2025.org | www.ampm2025.org
Ceramitec 2026
March 24–26, 2026 Munich, Germany www.ceramitec.com
If you would like to see your CIM, MIM or sinterbased AM related event listed in this magazine and on our websites, please contact Merryl Le Roux: merryl@inovar-communications.com
Organised by:
Dive into the heart of the PM industry at Euro PM2024, where industry leaders, academics, and professionals converge.
With 250 presentations over three days, including Keynote paper presentations and Special Interest Seminars, this event promises to redefine industry standards and unveil the latest PM advancements.
Explore the latest trends and advancements in PM as you connect with industry-leading suppliers, engage with potential clients, and discover cutting-edge PM solutions
New this year: Micro stands can be reserved by new exhibitor at the Euro PM2024 and the Exhibition will provide an area dedicated to showcasing Sweden’s PM industry!
Embark on a journey to meet the driving forces behind powder metallurgy technology, industry and innovation at Euro PM2024.
Don’t miss out the opportunity to attend our social events: The Welcome reception on Sunday evening, the poster reception on Monday and the congress dinner at Slagthuset on Tuesday.