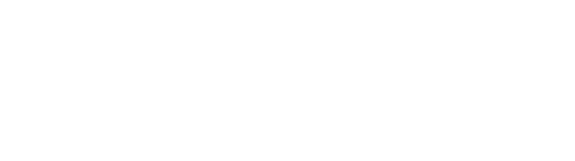
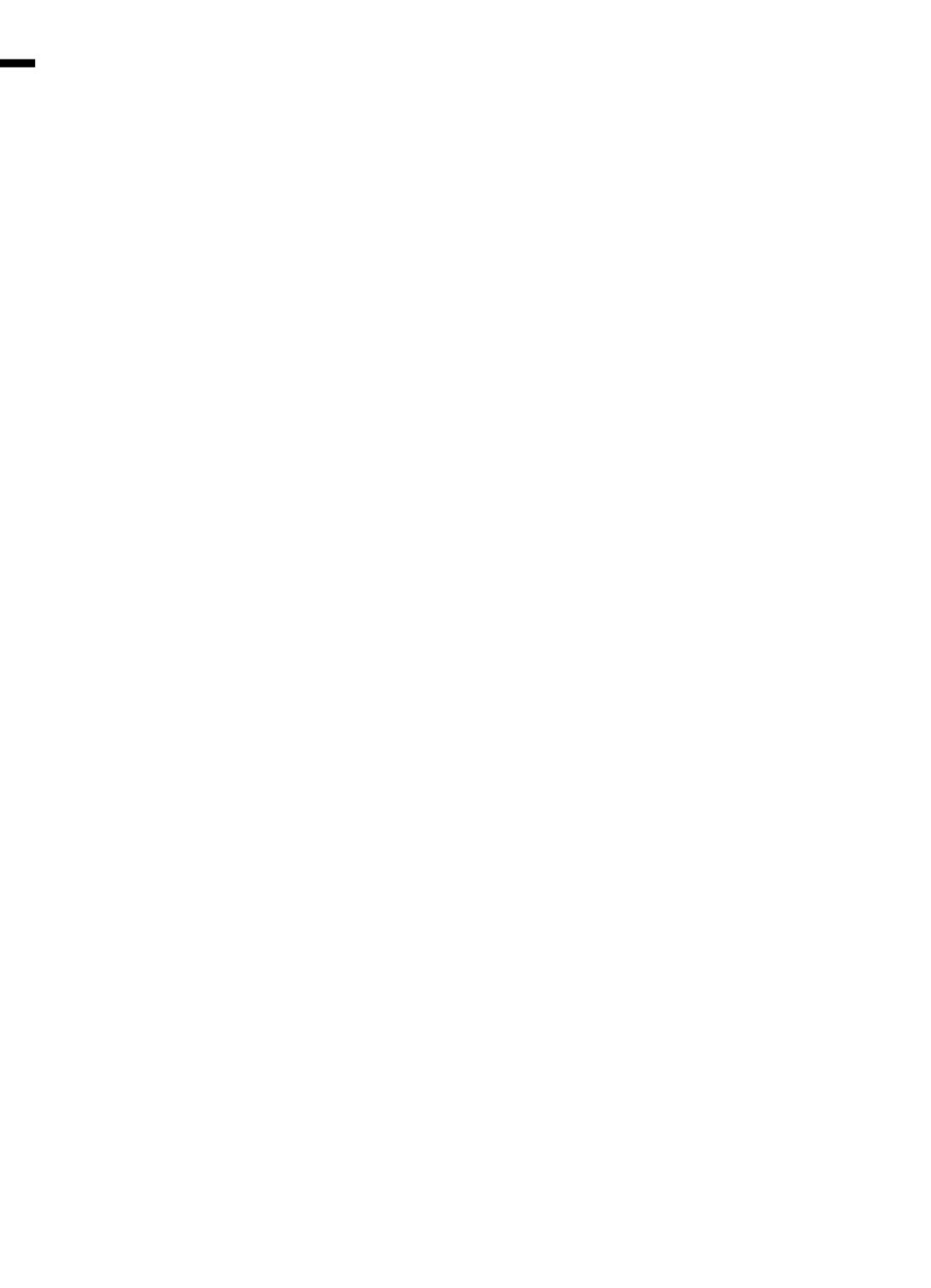
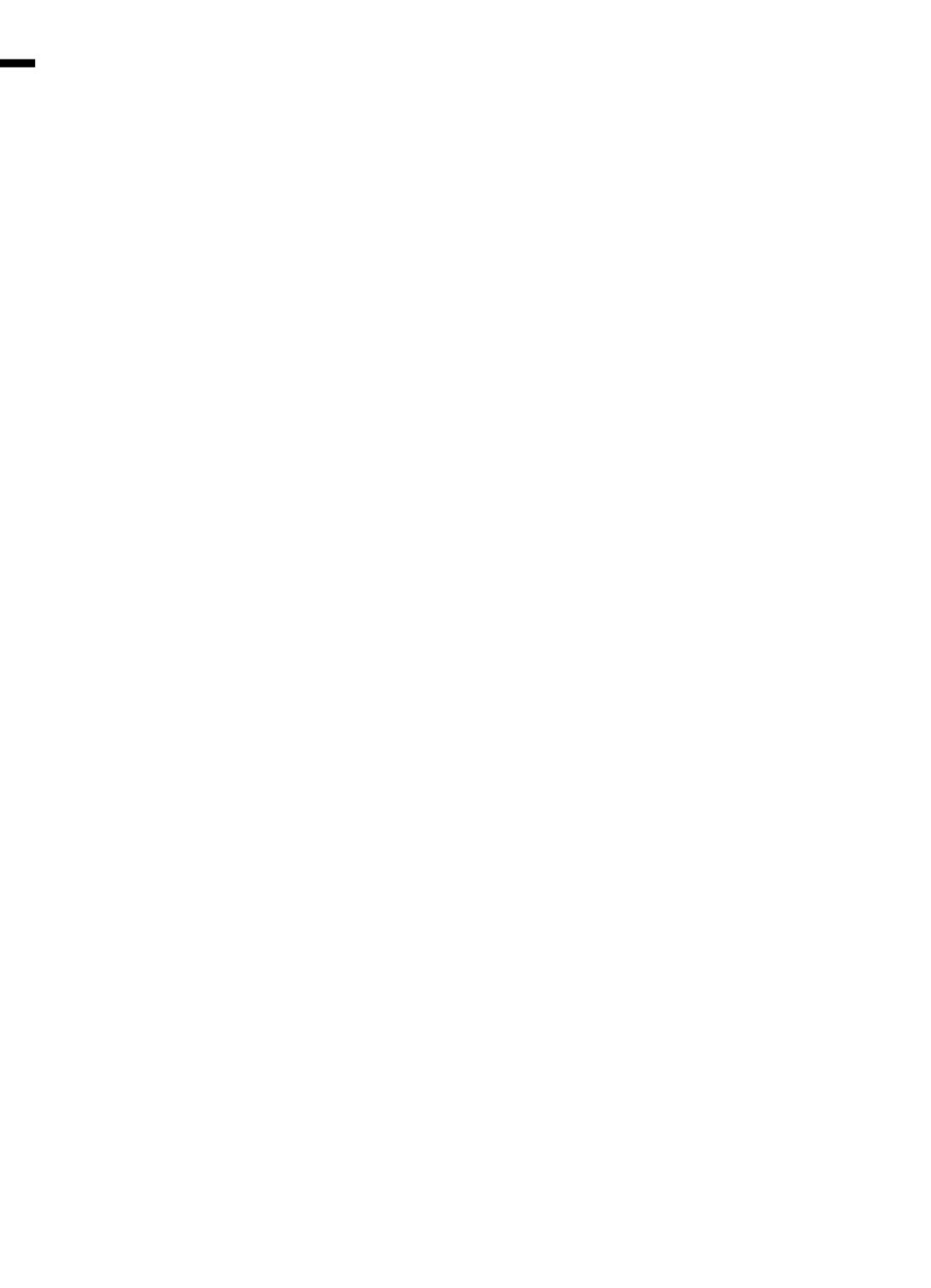
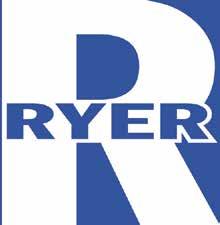
• At RYER, all our feedstocks are manufactured to the highest level of quality, with excellent batch-to-batch repeatability.
• RYER is the ONLY commercially available feedstock manufacturer to offer all five debind methods.
• RYER offers the largest material selections of any commercially available feedstock manufacturer.
• RYER offers technical support for feedstock selection, injection molding, debinding and sintering.
• A direct replacement for all current commercially available catalytic debind feedstocks
• Improved flow
• Stronger green and brown parts
• More materials available and better surface finish
• Custom scale-up factors available
• Faster cycle times
• 65°C / 150°F mold temperature
• Water Debind
• Custom scale-up factors available
• Large selection of available materials
• Solvent, Super Critical Fluid Extraction (SFE) or Thermal Debind methods
• Hundreds of materials available
• Custom scale-up factors available
Publisher & Editorial Offices
Inovar Communications Ltd
11 Park Plaza
Battlefield Enterprise Park
Shrewsbury SY1 3AF
United Kingdom
Tel: +44 (0)1743 469909 www.pim-international.com
Managing Director & Editor
Nick Williams, nick@inovar-communications.com
Group News Editor
Paul Whittaker, paul@inovar-communications.com
Advertising Sales Director
Jon Craxford
Tel: +44 (0)207 1939 749 jon@inovar-communications.com
Assistant Editors
Amelia Gregory, amelia@inovar-communications.com Emma Lawn, emma@inovar-communications.com
Assistant News Editor
Charlie Hopson-VandenBos charlie@inovar-communications.com
Digital Marketer
Mulltisa Moung, mulltisa@inovar-communications.com
Production Manager
Hugo Ribeiro, hugo@inovar-communications.com
Operations & Partnerships Manager
Merryl Le Roux, merryl@inovar-communications.com
Office & Accounts Manager
Jo Sheffield, jo@inovar-communications.com
Technical Consultant
Dr Martin McMahon
Consulting Editors
Prof Randall M German
Former Professor of Mechanical Engineering, San Diego State University, USA
Dr Yoshiyuki Kato
Kato Professional Engineer Office, Yokohama, Japan
Professor Dr Frank Petzoldt Ingenieurbüro Dr. Petzoldt, Geestland, Germany
Dr David Whittaker
DWA Consulting, Wolverhampton, UK
Bernard Williams Consultant, Shrewsbury, UK
Subscriptions
PIM International is published on a quarterly basis as either a free digital publication or via a paid print subscription. The annual print subscription charge for four issues is £150 including shipping.
Accuracy of contents
Whilst every effort has been made to ensure the accuracy of the information in this publication, the publisher accepts no responsibility for errors or omissions or for any consequences arising there from. Inovar Communications Ltd cannot be held responsible for views or claims expressed by contributors or advertisers, which are not necessarily those of the publisher.
Advertisements
Although all advertising material is expected to conform to ethical standards, inclusion in this publication does not constitute a guarantee or endorsement of the quality or value of such product or of the claims made by its manufacturer.
Reproduction, storage and usage
Single photocopies of articles may be made for personal use in accordance with national copyright laws. All rights reserved. Except as outlined above, no part of this publication may be reproduced or transmitted in any form or by any means, electronic, photocopying or otherwise, without prior permission of the publisher and copyright owner.
Design and production
Inovar Communications Ltd.
ISSN: 1753-1497 (PRINT)
ISSN: 2055-6667 (ONLINE) © 2025 Inovar Communications Ltd.
For decades, Metal Injection Moulding has been a go-to technology for the high-volume production of military and sporting firearms. In the US, firearm parts form one of the largest markets for the technology, as is the case in South America and, no doubt, China. Even Russia’s Kalashnikov embraced MIM over a decade ago for a new generation of military hardware.
In Europe, however, while firearms producers use MIM extensively in-house, many MIM companies have traditionally been shy about openly discussing firearms component production or have hesitated to operate in this market. Now, with a rapidly changing global security situation, the time to increase defence spending and re-arm has arrived.
So, as Europe’s MIM industry scrambles to fill the capacity left by weakening demand from the automotive industry, its potential role in bolstering Europe’s defences has to be recognised.
MIM’s use in defence applications goes far beyond firearms component production, it includes ammunition, missile and UAV components. Any stigma around defence manufacturing among European investors faded with Russia’s invasion of Ukraine. With geopolitical shifts driving greater demand for military production, now is the time to explore how MIM technology can produce armament parts more efficiently and economically, thereby strengthening global security.
Nick Williams Managing Editor
Cover image
Interlocking parts for an aerospace application (Courtesy 3DEO)
53 Scaling metal Additive Manufacturing: 3DEO’s unique approach to sinterbased parts production
3DEO has risen to become a significant player in metal Additive Manufacturing, producing over 1.5 million parts since 2018 for customers in the aerospace, medical, and semiconductor industries, among others.
Uniquely, the company uses its own Intelligent Layering® technology rather than relying on commercially available AM processes such as Binder Jetting.
Bernard North visited the company for PIM International and reports on how it has achieved commercial success in an industry where more widely known processes are struggling to make progress. >>>
65 Finding opportunities in a challenging market: AFT-Hungary’s Metal Injection Moulding strategy
AFT-Hungary, a key European player in Metal Injection Moulding, has navigated industry challenges through strategic adaptation and market diversification. Facing intense price competition, shifting trade policies, and evolving regulations, the company has focused on expanding MIM applications beyond traditional sectors. By identifying new opportunities and refining its manufacturing processes, AFT-Hungary remains competitive in a rapidly changing landscape.
Emma Lawn explores the company’s approach to sustaining growth, enhancing efficiency, and overcoming obstacles in today’s demanding manufacturing environment. >>>
Experience significantly improved printability with Osprey® HWTS 50. This new lean hot-work tool steel powder reduces many of the challenges customers face in hot-work applications. Characterized by lower carbon content it offers higher thermal conductivity together with optimized resistance to tempering and thermal fatigue. With its alloy design philosophy, Sandvik contributes to the shift towards a more sustainable future in several ways.
Meet our metal powder experts at Rapid + TCT 2025, 8 – 10 April, booth 3940.
The Metal Injection Moulding industry in Asia is experiencing significant shifts in feedstock sourcing and material usage. While BASF’s Catamold remains a key player, competition is growing, reshaping supply chains and production strategies.
In this article, Dr Q (Y H Chiou) explores the evolving landscape, examining market and application trends, regional variations, and the increasing role of domestic Chinese feedstock manufacturers. As demand for complex, highperformance MIM parts rises, understanding these changes is essential for industry stakeholders. >>>
85 Sinter-based Additive Manufacturing technologies in focus at ASTM’s ICAM 2024 conference
Sinter-based Additive Manufacturing has gained significant traction within ASTM’s International Conference on Advanced Manufacturing (ICAM), growing from a niche topic to a major area of discussion. Since its introduction as a dedicated track in 2022, interest in sinter-based AM has expanded rapidly, covering technologies such as Binder Jetting (BJT), Material Extrusion (MEX), Vat Photopolymerisation (VPP), Cold Metal Fusion, and emerging hybrid approaches.
In this article, Dr Animesh Bose highlights key presentations and insights from ICAM 2024 that are shaping the future of sinter-based AM. >>>
113 Advertisers’ index & buyer’s guide
Discover the leading suppliers of materials and equipment for MIM, CIM and sinterbased AM, as well as part manufacturing and more. >>>
117 Events guide
View a list of upcoming events for the MIM, CIM & sinter-based AM industries. >>>
The PIM International newsletter is sent to several thousand industry professionals worldwide. Register today to ensure you benefit from reading the latest industry news and advances in Metal Injection Moulding, Ceramic Injection Moulding and sinter-based AM technologies.
www.pim-international.com/e-newsletter
Based on the success of its collaboration with HP, INDO-MIM, headquartered in Bengaluru, India, is adding five additional HP Metal Jet S100 to its fleet of Additive Manufacturing machines. Two of the new metal Binder Jetting (BJT) machines have already been installed at the company’s US facility in San Antonio, Texas. The remaining systems will be delivered throughout 2025 and 2026.
INDO-MIM initially partnered with HP in late 2023, purchasing three HP Metal Jet S100s. In April 2024, the company opened its Additive Manufacturing production cell, supported by the HP metal AM machines. The partnership has combined the technical expertise of both companies to advance Binder Jetting applications and accelerate the development of new materials
for the HP Metal Jet S100 platform. INDO-MIM reports having used the machines for a wide range of applications, both for internal use in tooling and for OEMs in various industries.
“The quality of the HP Metal Jet S100 platform, combined with our extensive experience in sintering and robust in-house processing capabilities, has enabled us to rapidly adopt and optimise the BJT process,” stated Jag Holla, Senior Vice President at INDO-MIM Ltd.
A key advantage for the company is its ability to produce its own metal powders. INDO-MIM currently offers 17-4PH, SS 316, and M2 Tool Steel powders for the HP S100 platform. The additional machines will not only enable the company to grow its metal Additive Manufacturing business, but will be
The powder management stations mix, sieve and load powder (Courtesy INDO-MIM)
used to support its in-house powder development capabilities. INDO-MIM stated that in 2025 it plans to introduce additional material options, further expanding the versatility of the Binder Jetting process.
The Metal Jet S100 has an effective build volume of 430 x 309 x 140 mm. The Metal Jet workflow includes a powder management station, the Metal Jet S100 AM machine, a curing station and a powder removal station.
INDO-MIM is the world’s largest Metal Injection Moulding company, with over 3,000 employees producing over 150 million MIM parts annually. As a leading BJT service provider, the company added that it is poised to launch multiple serial production programmes utilising its BJT technology in 2025.
www.hp.com www.indo-mim.com
At Kymera International, we engineer high-performance metal powders, pastes, granules, and master alloys to power innovation across industries. From additive manufacturing and aerospace to medical, electronics, and beyond—our advanced materials enable breakthrough solutions. With a legacy of metallurgical expertise and a commitment to quality, sustainability, and customer collaboration, we provide tailored material solutions designed to meet the most demanding applications.
PARTNER WITH US AND UNLOCK NEW POSSIBILITIES. Learn more at kymerainternational.com
Germany’s Additive Drives GmbH, Dresden, has highlighted the potential of the Metal Injection Moulding of copper for a new generation of electric motors. The development of new electric drive technologies is one of the company’s specialties, and the company most recently reported on the potential of MIM for the production of parts such as bus bars.
It is suggested that MIM’s advantage is its ability to deliver complex designs in series production. However, Additive Drives noted that it has identified the technology as being suited to both simple and highly complex copper components in high quantities of up to several tens of millions per year or more.
Initial studies have shown that the mass can be reduced by at least 40% compared to conventional designs (Courtesy Additive Drives)
For electrical motor designers, the company states that the process enables design approaches such as function integration, mass reduction, and the avoidance of thermal hotspots. Initial studies have shown that the mass can be reduced by at least 40% compared to conventional designs; this enables more compact electric motor solutions and cost savings. In addition, functional elements such as press-fit nuts, special connectors and temperature sensors can be easily integrated to reduce overall manufacturing costs. Excellent electrical conductivity has been reported, and other physical properties (e.g. density and thermal conductivity) were stated to be very close to those of conventionally drawn copper.
Gasbarre Products Inc, headquartered in DuBois, Pennsylvania, USA, has revealed that its new St Mary’s, Pennsylvania, facility became fully operational in 2024. The 14,000 m 2 (150,000 ft 2) expanded floor space,
with upgraded infrastructure and state-of-the-art equipment, is designed to optimise workflow and increase manufacturing capacity.
The new multi-million dollar facility is home to a team of technical
www.additive-drives.de
sales managers, applications engineers, metallurgists and design engineers. All of the company’s manufacturing is kept in-house, with skilled fabricators, assemblers, pipe fitters and electricians responsible for ensuring quality and accuracy.
Gasbarre manufactures a wide range of powder compaction presses, including mechanical, hydraulic, high-speed, isostatic, and electric press types. The company also has an extensive line of industrial thermal processing systems, including continuous atmosphere to batch atmosphere and continuous vacuum to batch vacuum furnaces.
Additional product lines include precision tooling, industrial automation, and contract manufacturing. www.gasbarre.com
American Axle & Manufacturing (AAM), headquartered in Detroit, Michigan, USA, has agreed terms to acquire Dowlais Group plc, the UK-based parent company of GKN Automotive and GKN Powder Metallurgy. The $1.44 billion deal, consisting of cash and AAM shares, was unanimously agreed by the boards of directors of both Dowlais and AAM. Upon closing of the transaction, it is expected that AAM shareholders will own approximately 51% of the combined group and Dowlais shareholders will own approximately 49%. The combined company will be headquartered in Detroit and led by David C Dauch, AAM’s chairman and Chief Executive Officer.
“This announcement marks another key milestone in our continued longterm strategic growth plan,” stated Dauch. “We are excited to bring together these two outstanding companies to create a leading driveline and metal-forming supplier serving the global automotive industry as it continues to evolve. The combination will create significant immediate and long-term shareholder value while helping to power a more sustainable future. Together with Dowlais, we will have the powertrain-
agnostic product portfolio, global reach, commitment to innovation and financial strength to meet the needs of customers and succeed in a dynamic market environment.”
GKN Powder Metallurgy and GKN Automotive, together with the rest of the GKN plc, were taken over by Melrose Industries in 2018. In 2023, Melrose announced the demerger of the GKN Powder Metallurgy, GKN Automotive and GKN Hydrogen businesses, forming the new independent holding company, Dowlais Group plc. GKN Hydrogen was acquired by Langley Holdings in August, 2024.
“Today’s announcement marks a significant opportunity to build on the success of Dowlais Group. The combination of the two companies accelerates the execution of our strategy by leveraging our combined scale, resources, capabilities, and outstanding management teams,” added Liam Butterworth, Dowlais’ Chief Executive Officer. “Our product portfolios and technological expertise are highly complementary, positioning us to better serve our customers and exceed their expectations. This transaction also combines our respective strengths in innovation,
technology, and talent, creating a solid foundation for delivering longterm value to our shareholders.”
GKN Powder Metallurgy employs over 5,000 people across its twentyseven manufacturing facilities in nine countries. The company lists 3,000 customers, ships 250,000 tons of metal powder each year and produces around ten million Powder Metallurgy parts each day. Together with GKN Automotive, Dowlais’ businesses comprise over seventy manufacturing facilities in nineteen countries worldwide.
AAM is a Tier 1 automotive supplier that designs, engineers and manufactures driveline and metal forming technologies to support electric, hybrid and internal combustion vehicles. The company has over seventy-five facilities in sixteen countries. With a combined portfolio of products, the new company is expected to be wellpositioned to serve a customer base spanning multiple geographies and support changing propulsion trends. The combined company expects to achieve approximately $300 million in cost synergies during its first full year of operation. Upon completion, AAM will continue to trade on the New York Stock Exchange under the ticker symbol AXL, with Dowlais de-listed from the London Stock Exchange. www.gknpm.com www.gknautomotive.com www.aam.com
Ceramic Additive Manufacturing (AM) offers a revolutionary step change in design and manufacture for ceramics
The possibilities include the ability to rapidly prototype designs, minimise material wastage and tooling costs, shorten lead times, and produce complex, near-net shape geometries that could not otherwise be obtained through conventional forming methods
From commercially available vat polymerisation techniques to novel AM processes, Lucideon can optimise printing and process parameters as well as develop novel formulations for your applications
www.lucideon.com/ceramicam
query@lucideon.com
www.lucideon.com/company/lucideon
Roland DG Corporation, headquartered in Hamamatsu, Japan, has launched two new ceramic Binder Jetting Additive Manufacturing machines, the PB-600 and PB-400. Both machines are calibrated to use Brightorb ceramic powder, developed by AGC Ceramics Co, Ltd, Tokyo, Japan.
“The printers are capable of producing ceramic objects, even those with complex structures that could previously only be dreamed of, including artistic interior decor, ceramic panels and walls, and fine art replicas as well as arts and crafts, earthenware, and other items,” stated Ryugo Nimura, President, Global Sales and Marketing Division.
The PB-600 has a maximum work area of 595 x 600 x 250 mm, while the PB-400 has a maximum work area of 390 x 290 x 200 mm. These sizes enable one large object or several smaller ones to be produced at once.
Both ceramic AM machines include slicing software that converts 3D designs into output data. The machines can be operated from a monitor attached to the machine itself, making it easy to run.
“Since its establishment in 1981, Roland DG has been supporting the digitalisation of various industries by providing digital solutions that make it easy for anyone to create things,” Nimura continued. “The PB
series allows users to create one-ofa-kind and premium 3D objects utilising the unique characteristics of 3D printing technology, and has the power to revolutionise conventional processes, expand the possibilities of creative expression, and bring new value and sales opportunities to the interior decoration, architecture, fine art, and arts and crafts industries, as well as educational and research institutions in history and culture. We will continue to contribute to the creation of an environment in which people can demonstrate their unlimited creativity through innovative technologies.”
www.rolanddg.com
DG Corporation has launched two new ceramic Binder Jetting Additive Manufacturing machines, the
and the
(right) (Courtesy Roland DG Corporation)
Cobra Golf, headquartered in Carlsbad, California, USA, has announced the launch of its new King and King-X wedges, with every
built using MIM (Courtesy Cobra Golf)
wedge in the range built using Metal Injection Moulding technology. Using MIM allows for exceptionally precise manufacturing and is said to result in approximately 50% tighter tolerances than traditional cast wedges.
“Achieving optimum spin and trajectory control on wedge shots is key to scoring,” stated Chad DeHart, Senior Product Line Manager at Cobra Golf. “MIM technology helps us produce wedges with tighter tolerances for exceptional consistency while FWT [Flight Window Technology] allows for optimal CG [centre of gravity] location throughout the full range of lofts. Together, the two technologies, with the addition of the new grind options, provide golfers the ultimate versa -
tility in our most advanced wedges to date.”
The company has been working with MIM for a number of years, adopting the technology first for its King MIM wedges in 2019, followed by the King MIM Black wedges and MIM King Tour irons in 2020.
Like the standard King model, the King-X wedges are manufactured with MIM technology for exceptionally tight tolerances and feature a strategically placed TPU (thermoplastic polyurethane) insert for enhanced feel at impact. To further improve forgiveness, a deep undercut design allows 20 g of weight to be redistributed to the perimeter of the clubhead, making the King-X more stable on off-centre hits.
The new models will be available from Cobra Golf in March.
www.cobragolf.com
These two binder systems have excellent characteristics during the production process and combine attractive prices with worldwide availability
High performance as well for the 3D-Printing process based on the water soluble binder system
Lithoz GmbH, based in Vienna, Austria, has installed its first CeraFab Multi 2M30 in the United States at Embry-Riddle Aeronautical University’s campus in Daytona Beach, Florida. The multi-material Additive Manufacturing machine, which can combine ceramic material with another ceramic or metal materials, is expected to be used for the development of advanced lunar exploration systems, among other aerospace and energy sector applications.
Dr Seetha Raghavan, Professor of Aerospace Engineering at Embry-Riddle, emphasised the transformative impact this
technology can offer. “The Lithoz CeraFab Multi 2M30 enables our researchers to manufacture ceramics with intricate geometric features across scales with remarkable precision. Its capability to print combinations of ceramics tailored for specific needs is pivotal in accelerating material design.”
The CeraFab is said to have already played a crucial role in campus projects, including aiding the C.R.A.T.E.R team during NASA’s Human Lander Challenge. Using the Lithoz machine, the team successfully developed bio-inspired ceramic patterns to mitigate dust adhesion on lunar surfaces. These precision-engineered patterns,
At this year’s MIM2025, organised by the Metal Powder Industries Federation, David Smith of APG-MIM, a Division of Nichols Portland Inc based in Ridgway, Pennsylvania, USA, illustrated the use of Additive Manufacturing in the production of MIM components through a discussion on APG-MIM’s six-string guitar capo assembly. This assembly was recently named Grand Prize winner in the Hand Tools–Recreation category of the MPIF Awards. Developed in collaboration with Paige Musical, each assembly –consisting of a saddle, adjustment guide, bar, and yoke – is crafted from MIM-17-4 PH stainless steel. The component is designed to temporarily shorten the strings of a guitar, raising the pitch of unfretted strings and enabling key changes in openposition chords.
The challenging part design (with a hole diameter of 0.04 mm as sintered) reportedly led to
issues with tool design, moulding, de-binding, and sintering operations. All hole diameters had to be within 0.04 mm as sintered and, as the component is fitted together through joins by the user, the star-shaped design on the yoke had to precisely fit
Lithoz GmbH has installed a CeraFab Multi 2M30 at EmbryRiddle Aeronautical University (Courtesy Lithoz)
modelled after hydrophobic surfaces like the lotus leaf, underscore the AM machine’s capabilities. www.lithoz.com
the threaded bar design. Customised ceramic setters and an optimised two-stage injection moulding process were required to successfully manufacture the component. Manufacturing the pieces in a single location allowed for multiple iterations of the design to be easily tested before the final one was selected and allowed the quality to be carried through all pieces. www.mpif.org www.alphaprecisionpm.com
Goodfellow, a specialist metals and material supplier based in Huntingdon, UK, has shared that international expansion and accelerating the acquisition trail will be key priorities for the company in 2025.
Goodfellow, which employs 140 people across its HQ in Huntingdon and sites in Europe, Asia and the US, has set its sights on increasing group sales to more than £30 million through a combination of new material ranges, organic growth and targeting potential companies that add new capabilities, additional products or geographic reach.
CEO Simon Kenney believes that last year’s investment in an ERP system and the launch of a new website will be key to achieving these aims, not to mention tapping into significant demand from customers in medical devices, battery development, space exploration and electrification and fusion technology globally.
He also outlined his firm’s ability to provide 98% of materials in fortyeight hours as a major differential and something he wants to build on.
“2024 was all about laying the foundations for growth this year, from enhancing operational performance and the customer journey through our digital transformation project to
Nanoe, based in Ballainvilliers, France, has reported the launch of its new Zetasinter 4L sintering furnace to complete its current line of Zetamix metal and ceramic filaments, machines and sintering furnaces. Nanoe partnered with Cerinnov Group to develop this new sintering furnace, aimed at filling a gap in Nanoe’s current product offerings for the medium-size
the strategic purchase of Potomac Photonics,” Kenney explained.
“The latter represents our first US manufacturing facility and gives us microfabrication capabilities that we didn’t previously have and is the type of deal we want to do more of over the next twelve months,” he continued. “The UK market has been challenging this year, not just for us but for other businesses in our area of expertise. International sales are where we see the big opportunity, with customers now present in more than sixty different countries.”
“For example, a new distribution agreement with MicroPlanet in 2024 is projected to boost turnover in the Iberian market by 50% alone,” Kenney shared.
Goodfellow, which received an investment from Battery Ventures in 2021, supplies a comprehensive range of metals, alloys, ceramics, polymers, compounds, and composites. The company has built a reputation as a trusted supplier to firms involved in R&D, advanced engineering, space and the scientific sector, with subsidiaries across Europe, North America and China helping it extend its global reach.
From its HQ in Cambridge, the materials specialist also provides a
production of sinter-based Additive Manufacturing parts.
The new Zetasinter 4L furnace, manufactured by Cerinnov in France, features a sintering volume of 4 litres (140 mm diameter, 250 mm length).
The model is four times bigger than the previous Zetasinter tubular furnace, allowing sintering of small production batches. It has full digital control, a part loading system, and a maximum operating temperature of 1,350°C.
The Zetasinter 4L is available for a price of €25,000, with first deliveries expected in Q1 2025. www.nanoe.com
Goodfellow CEO Simon Kenney (Courtesy Goodfellow)
range of post-processing facilities, including rolling, electroplating, sputtering, heat treatment, disk punching/turning and guillotining/ sawing.
“We have seen increased demand for specialist metals and materials to support global R&D projects,” Kenney added. “Our ongoing investment in stockholding allows us to meet this requirement and there has been a definite shift towards needing materials quickly for prototype work, which is where our ‘no minimum’ order quantity really comes into its own.”
“Another important development in 2024 was increasing our 170,000strong product range even further with the addition of three new ranges, including custom alloy powders and high entropy alloy powders, metal microfoils and rare earth metal oxides,” Kenney concluded. “The intention is to introduce a new collection of premium materials early into 2025.”
www.goodfellow.com
The Zetasinter 4L is four times bigger than the previous Zetasinter tubular furnace, allowing sintering of small production batches (Courtesy Nanoe)
● GAS AND ULTRASONIC ATOMIZERS FOR SPHERICAL POWDERS WITHOUT ANY SATELLITES for LPBF, MIM, Binder Jetting and other Additive Manufacturing applications. High purity, sphericity and wide range of reproducible particle size distribution.
● WATER ATOMIZERS FOR MORE IRREGULAR POWDERS ideal for recycling/refining process, press & sinter process and others.
● AIR CLASSIFIERS FOR THE PRECISE SEPARATION OF METAL POWDERS into fine and coarse powder fractions especially in the range < 25 µm
Tethon 3D, based in Omaha, Nebraska, USA, has acquired Technology Assessment and Transfer (TA&T), a subsidiary of Sintx Technologies, Inc., Salt Lake City, Utah, USA. This acquisition looks to enhance Tethon’s manufacturing capabilities, expand its portfolio, and increase its global market share.
“We are excited to have the TA&T team join us at Tethon. Together, as the US leaders in ceramic Additive Manufacturing, we will continue our domestic and global growth, while continuing to innovate our resin portfolios and ensuring our materials are compatible with more hardware platforms than ever before,” said Trent Allen, CEO of Tethon
3D. “With Tethon’s resources and distribution network, TA&T can fully commercialise its technologies. This acquisition also enables the combined dual-use company to streamline efforts and expand its leadership in advanced ceramic manufacturing.”
“At TA&T, we are committed to bridging the gap between the lab and marketplace. Tethon’s acquisition ensures that commitment is stronger than ever. With the resources and expertise of Tethon, we are wellpositioned to scale and enhance our impact in ways we couldn’t before. We are excited about this next phase of growth,” said Ann Kutsch, President of TA&T.
www.tethon3d.com
The Supervisory Board of Oechsler AG, located in Ansbach, Germany, has extended Karl Ostler’s contract as Spokesman of the Executive Board and appointed him as Chairman of the Executive Board (CEO), effective January 1, 2025. Karl Ostler was initially appointed as Spokesman of the Management Board on January 1 of this year in addition to his role as Chief Financial Officer (CFO). In addition to Ostler, the Management Board of Oechsler AG will continue to consist of Raik Lüder as Chief Products and Markets Officer (CPMO) and Alexander Wortberg as Chief Operating Officer (COO).
“The Supervisory Board is convinced that Karl Ostler is the right person to lead the Executive Board. He is approaching the transformation of the company with courage and dedication and is not afraid to make the changes that are urgently needed,” stated Wolf Matthias Mang, Chairman of the Supervisory Board of Oechsler AG. “He is proceeding with a sense of proportion and is aware
Oechsler AG has named Karl Ostler as Chairman of the Executive Board (Courtesy Oechsler)
of the sacrifices that our employees are making in order to successfully restructure our company. This has earned him the trust of the entire Supervisory Board and the shareholders of Oechsler.”
“The extension of his contract and his appointment as CEO are an expression of this. The Supervisory Board is grateful that the entire Management Board with Karl Ostler, Raik Lüder and Alexander Wortberg will accept the challenges posed by the markets and customers and lead our traditional company into a successful future,” concluded Mang.
www.oechsler.com
Atomik AM, a spin-off from the University of Liverpool, UK, has received a £125,000 investment from LYVA Labs. LYVA Labs creates engineering solutions for the advanced manufacturing sector from its base at the University of Liverpool’s School of Engineering.
Having developed a number of techniques and binders intended to improve the process of Binder Jetting (BJT) Additive Manufacturing, Atomik AM plans to use the investment from LYVA Labs to accelerate product commercialisation by enabling the team to convert pipeline opportunities into commercial contracts.
The funding will also support the business in developing new intellectual property (IP), filing a patent, securing eight jobs, and creating the role of Chief Operating Officer. Since its inception, Atomik AM
has successfully collaborated with blue-chip companies, filed multiple patents, and established an IP pipeline.
“This investment is a testament to the groundbreaking work our team is doing to advance Additive Manufacturing processes,” stated Professor Kate Black FREng, founder and CEO of Atomik AM. “It allows us to expand our capabilities, accelerate innovation, and bring sustainable, cutting-edge solutions to the industry. At Atomik AM, we believe in driving change in manufacturing to create a better future for everyone.”
LYVA Labs’ Head of Investments, Akshay Bhatnagar, added, “We hope this will be the first of many investments alongside the University of Liverpool, Atomik AM exemplifies the excellence found in advanced manufacturing R&D across Liverpool
The Atomik AM team has received funding to accelerate the commercialisation of its Binder Jetting solutions (Courtesy Atomik AM)
City Region, and we are pleased to be part of this business’s exciting innovation journey.”
Recently, Liverpool City Region Combined Authority invested £10.5 million in LYVA Labs in bolstering companies into high-growth businesses, as part of Liverpool Mayor Rotheram’s plan to invest 5% of regional GVA into research and development (R&D) by 2030. Advanced manufacturing is said to be key to this goal, representing a significant sector.
www.lyvalabs.com
Sandvik AB, headquartered in Stockholm, Sweden, is celebrating fifty years of manufacturing its Osprey line of products at its Neath, South Wales, UK, facility. From humble beginnings, the unit has evolved to become a leading manufacturer of gas-atomised metal powders and a novel range of controlled expansion (CE) alloys.
“This milestone is a testament to the dedication, hard work, and innovation of all employees, partners, and customers who have been part of the journey,” stated Andrew Coleman, VP Business unit Additive Manufacturing at Sandvik. “It demonstrates Sandvik’s long-term experience that makes us a trusted partner for customers in areas such as Additive Manufacturing (AM) and Metal Injection Moulding (MIM), and across a range of demanding industries.”
Today, the Neath production site is the cornerstone of Sandvik’s metal powder manufacturing capability.
The company states that the Osprey range of metal powders is the broadest on the market with over 2,000 different alloys, specialising in fine and mid-fraction sizes.
This scope of its atomising technology also enables Sandvik to manufacture its range of HIPed CE alloys which are suitable for various applications, including those with extreme temperature variations. www.metalpowder.sandvik
Faraz Deirmina, Principal Metallurgist in metal powders, Sandvik, demonstrating recently launched Osprey HWTS 50 metal powder (Courtesy Sandvik)
Applications are now open for the European Powder Metallurgy Association’s 2025 Powder Metallurgy Summer School. The 23 rd edition will be held from June 22–27, 2025, at Lund University in Sweden.
The EPMA PM Summer Schools provide participants from across Europe with advanced insights into PM’s advantages and limitations, delivered by some of the leading academic and industrial experts in the field.
Every summer, students, researchers, and professionals from around the world gather to partake in direct technical discussions with other young scientists and engineers.
The five-day event is designed for master’s students, PhD candidates, young professionals, and anyone eager to learn and broaden their academic and professional horizons.
The participation fee covers course materials, five nights of accommodation, refreshments, a welcome reception, and a networking dinner. Additionally, participants receive 18 months of EPMA student membership, granting discounted rates for Euro PM congresses and exhibitions. Those interested in applying can do so here. The application deadline is April 21, 2025. summerschool.epma.com
Schunk Sintermetalltechnik GmbH
Discover the future of power electronics with our cutting-edge heat sinks, crafted using advanced Metal Injection Moulding (MIM) technology. These innovative heat sinks offer unparalleled thermal management, ensuring optimal performance and longevity for your electronic devices.
MIM allows for complex geometries and superior material properties, resulting in highly efficient heat dissipation. Perfect for high-power applications, our MIM heat sinks are lightweight, durable, and cost-effective. Upgrade your power electronics with our state-of-the-art MIM heat sinks and experience the difference in performance and reliability. Embrace the next generation of thermal solutions today!
� Roßtrappenstraße 62 06502 Thale, Germany
� +49 3947 7 1560 At thorsten.klein@schunk-group.com � schunk-mobility.com
Seco/Warwick Group has announced it will deliver a Vector vacuum furnace to a global supplier of metal injection moulded products. This is Seco/ Warwick’s second collaboration with the MIM parts maker, who plans to use the new furnace in the production of components for the aviation industry.
The Vector furnace is expected to increase capacity to provide hardening process services, while meeting all aviation standards required by the industry. Material heating processes require high purity, explains Seco/ Warwick, which is why the 1200˚C furnace uses an additional argon hydrogen partial pressure system.
Seco/Warwick will deliver a Vector vacuum furnace to a global supplier of metal injection moulded products (Courtesy Seco/Warwick)
“The Seco/Warwick advantage is that we can adapt standard products to non-standard expectations. When choosing the solutions they need, our partners can feel like they are working with the best tailor who will tailor the solution to their specific needs and expectations. Thanks to the flexibility we offer, we can modify standard solutions to create a unique product with an attractive price,” stated Maciej Korecki, Vice President
of the Vacuum Furnaces Segment in the Seco/Warwick Group.
The un-named customer is reportedly one of the largest MIM manufacturers. Its capabilities include vertical integration of finishing technologies such as Ni and trivalent chromium electroplating, vacuum heat treatment and seal hardening, as well as precision grinding and CNC machining with micron tolerances. www.secowarwick.com
If you are looking for the best in purity, homogeneity, reproducibility, and ease in sintering, come to TOSOH. With our line of yttria stabilized “TZ” zirconia powders, you will find the ultimate in your processing and sintering properties. As the world leader in high purity zirconia powder for advanced engineering ceramic applications, our powders have set the standards that have come to be accepted worldwide, including various regulatory approvals on sintered bodies. Whether it is for injection molding, pressing, slipcasting or extrusion, our zirconia will provide you with outstanding properties, so that you can take the lead. With the largest capacity in the world, and worldwide technical support through offices in Europe, USA and Japan, you can depend on TOSOH for the ULTIMATE in zirconia!
Y2O3 (mol%)
The Metal Powder Industries Federation (MPIF) has released the 2025 edition of ‘Standard Test Methods’. This new volume contains fifty-two standards covering terminology and recommended methods of testing for metal powders, Powder Metallurgy and Metal Injection Moulding, PM equipment, and metal Additive Manufacturing.
The 2025 edition includes many revised standards and updated figures, as well as four new standards:
• Standard 76 Determination of Ejection Stresses for Uniaxially Compacted Powder Metallurgy (PM) Test Specimens
• Standard 77 Test Method for Preparing and Evaluating
Over 6,500 production and laboratory furnaces manufactured since 1954
• Metal or graphite hot zones
• Processes all binders and feedstocks
• Sizes from 8.5 to 340 liters (0.3–12 cu ft.)
• Pressures from 10-6 torr to 750 torr
• Vacuum, Ar, N2 and H2
• Max possible temperature 3,500°C (6,332°F)
• Worldwide field service, rebuilds and parts for all makes
Un-notched Charpy Impact
Energy Specimens of Materials Produced from Metal Powders by Sinter-Based Metal Additive Manufacturing (Metal AM) Technologies
• Standard 78 Test Method for Preparing and Evaluating V-Notched Charpy Impact Energy Specimens of Materials Produced from Metal Powders by Fusion-Based Metal Additive Manufacturing (Metal AM) Technologies
• Standard 79 Test Method for Preparation of AC and DC SoftMagnetic Powder Metallurgy (PM) Test Specimens
The most current versions of all included standards are required by quality assurance programmes in order to maintain full compliance. All earlier editions of ‘Standard Test Methods’ are now obsolete. Those interested can order here. MPIF members receive a discount on purchasing. www.mpif.org
Ipsen USA, Cherry Valley, Illinois, has announced the promotion of two team members to its management. Matt Clinite is now Sales Director and Christina Connelly is Director of Ipsen Customer Service.
Since joining Ipsen in 2014, Clinite is noted as having demonstrated outstanding leadership and exceeding expectations in roles of increasing responsibility.
The company has attributed Connelly’s leadership to the significant growth and improvements within the parts team, which now includes production control, parts engineers, and pricing. www.ipsenusa.com
Regardless of the complexity of your custom application and formulation, it remains standard for us with our quality systems, technical support, and two proprietary binding systems.
We ensure 100% batch-to-batch consistency, a wide range of alloys, and 36 years of supplying MIM feedstocks for mission-critical parts.
Advanced Metalworking Practices (AMP) manufactures and supplies a wide range of both standard and custom-configured MIM feedstocks for your application. Contact Chris Chapman at cchapman@ampmim.com or 724-396-3663.
Scan the QR code or click here to view our current list of alloys www.ampmim.com/resources
Professor José Manuel Torralba, Director of the IMDEA Materials Institute and professor at the Carlos III University of Madrid (UC3M), has been elected as a new full member of the Royal Academy of Engineering of Spain (RAI). This appointment recognises Torralba’s career and contributions to the field of Powder Metallurgy.
A key area of Prof Torralba’s research has focused on developing and characterising metal powders and advanced consolidation methods such as Metal Injection Moulding, Additive Manufacturing and electric-fieldassisted sintering. His research has covered a range of materials, including low-alloy and stainless steels; super-, light and high-entropy alloys; and metal matrix composites. He has over 500 scientific publications and has supervised thirty doctoral theses.
“Powder Metallurgy is a key discipline for the development of more sustainable and efficient technologies,” Torralba stated. “I hope that this recognition will help to further highlight its importance in the development of new materials and in the technological challenges of the future.”
“Being elected a full member of the Royal Academy of Engineering is a personal and professional honour. It is always gratifying to know that the work of a lifetime is recognised by such a prestigious institution,” Torralba added. “It is also a recognition of the effort and dedication of all my colleagues at IMDEA Materials, UC3M and all the institutions with which I have had the opportunity to collaborate. Without them, many of the advances we have achieved would not have been possible.”
Throughout his career, Prof Torralba has held various important positions in both the academic and administrative fields, including ViceRector for Research and Innovation at UC3M and Director General of Universities and Research of the Community of Madrid; he currently leads the IMDEA Materials’ Sustainable Powder Technology research group. He has a doctorate in Metallurgy from the Polytechnic University of Madrid (UPM) and one in Armament from the Higher Polytechnic School of the Army.
“I hope to be able to represent at the Academy the sensibilities
The Metal Powder Industries Federation (MPIF) Awards Committee has announced the recipients of the 2025 MPIF Distinguished Service to Powder Metallurgy (PM) Award. The Distinguished Service to Powder Metallurgy Award was created to recognise individuals who devote the major part of their working careers to one or more segments of the field of Powder Metallurgy. This award recognises individuals who have actively served the North American PM industry for a minimum of twenty-five years and
deserve special recognition in the minds of their peers.
The 2025 Award Recipients are:
• Wiley Abner, formerly MPP
• Sundar Atre, University of Louisville
John Blauser, Gasbarre Precision Tooling
• Roy Christensen, VALIMET, Inc
• Wayne K Daye, Kymera International Gregory (Jerry) Falleur, PMTII, AAM-Metal Forming
Professor José Manuel Torralba has been elected as a new full member of the Royal Academy of Engineering of Spain (Courtesy IMDEA Materials/ Professor José Manuel Torralba)
linked to my two profiles as an engineer (Mining-Metallurgical and Armament) as well as my professional profile linked to Materials Science and Engineering,” he added.
Prof Torralba has also received numerous awards, including the FEMS Gold Metal (2021) and fellowships from both the European Metallurgy Association (EPMA) in 2018 and the American Powder Metallurgy Institute in 2015. In 2007, he received Honorary Doctorates from Romanian institutions the University of Craiova and, in 2001, from the Technical University of Cluj-Napoca. www.materials.imdea.org www.euro-case.org
• Jason Gabler, PMT, Advantage Metal Powders, Inc
• Jane LaGoy, Bodycote
Ray Serafini, PMT, Messer North America
• Mike Stawovy, Elmet Technologies
Mark Thomason, PMT, Gasbarre Products, Inc
• Trevor Towns, PMT, Höganäs
The awards ceremony will take place during the PowderMet2025 International Conference on Powder Metallurgy & Particulate Materials, June 15-18, Phoenix, Arizona, USA. www.mpif.org
Metalysis, based in Rotherham, UK, has acquired a 40 kW spheroidiser from Tekna Holding ASA, Sherbrooke, Quebec, Canada. The spheroidiser is designed to produce spherical powders for niche markets with high added value, and for the discovery of new alloys at development scale. This acquisition comes as Metalysis is scaling up production of its refractory alloys – which includes tantalum and high-entropy alloys – and plans to serve the hightemperature niobium market with materials such as niobium C103 and FS85. Metalysis explained that this underscores its ongoing commitment to enhancing efficiency, sustainability and innovation in Powder Metallurgy. Using the patented FFC Cambridge electrolysis process, Metalysis reduces metal oxides
in the solid state, a method that contrasts with traditional melting processes. Typically, this process outputs powders with an angular shape, but the spheroidiser can be used to produce spherical particles for Powder Metallurgy applications. Use of the spheroidiser enhances Metalysis’ in-house capabilities, improving attributes such as powder flowability, reducing internal porosity, and delivering higher packing density. This can meet the most demanding Powder Metallurgy applications, including Additive Manufacturing, Metal Injection Moulding, Spark Plasma Sintering, and Hot Isostatic Pressing.
A key feature of the Metalysis FFC Cambridge technology is the ability to tailor particle size for
a given process while generating minimal under- or oversize particles. This characteristic is maintained post-spheroidisation, resulting in negligible waste powder being created compared to conventional atomisation processes, and, consequently, energy is not consumed in the generation of scrap powder.
Nitesh Shah, CEO of Metalysis, shared, “The acquisition of a 40 kW spheroidiser marks a major step forward in Metalysis’ capability to produce advanced powders in-house and serve our niche but high-value markets – particularly in refractory alloys and lightweight refractory high entropy alloys. By controlling our spheroidisation processes, we’re not only reducing lead times and mitigating global supply chain risks, but also reinforcing our sustainable footprint. This is a pivotal moment for Metalysis as we strengthen our position in the critical materials supply chain – now able to provide spheroidised powders in-house.”
www.metalysis.com
Researchers from Mexican institutions Universidad Michoacana de San Nicolás de Hidalgo, Tecnológico Nacional de México, and Universidad Autónoma de Coahuila, along with France’s University Grenoble Alps, recently published a study in Materials on the tailoring of porous Ti6Al4V for biomedical purposes.
As metallic bone replacements are in increasingly high demand, implants must have more tailored properties to ensure their long-term use in the human body. ‘Development of Tailored Porous Ti6Al4V Materials by Extrusion 3D Printing’ sought to develop components with the necessary characteristics via Additive Manufacturing.
Using MIM pellet feedstock, the researchers additively manufactured hexagonal channels of three different sizes. The densification kinetics were then evaluated by dilatometry tests before the parts were sintered. After post-processing, the samples were characterised by scanning electron microscopy (SEM) and X-ray computed tomography to analyse their respective microstructures. Compression tests were used to evaluate the parts’ mechanical strength.
The researchers found that the hexagonal shape was better defined as the channel size increased. The results showed similar behaviour for each of the channel sizes
during sintering; however, greater densification was obtained as the channel size decreased. Additionally, microporosity was obtained at the particle level, which is completely interconnected, ensuring the passage of fluids through the entire sample. As the channel size increased, however, Young’s modulus and yield strength were considerably reduced. The main conclusion is that parts with two scales of porosity can be achieved by Additive Manufacturing.
Permeability values were shown to be in the range of trabecular bones, which the researchers noted as promising for the osseointegration of such materials. The mechanical properties are a little higher in comparison to those of trabecular bones, but these are properties which can be tuned by increasing the pore volume fraction during the manufacturing stage.
Evaluation of cell attachment and bone ingrowth with this kind of sample is in progress to determine what size will be the most effective. This is expected to lead to the fabrication of bone implants like hip, knee or vertebral implants, with the best size and configuration of channels and tailored porosity according to requirements.
www.mdpi.com/journal/materials www.umich.mx
www.tecnm.mx
www.uadec.mx www.univ-grenoble-alpes.fr
Images of the designed samples using the Simply 3D software: (a) small canals, (b) medium canals, (c) large canals and (d) the resulting additively manufactured samples for each canal size (Courtesy Materials 2025)
Air Products, headquartered in Allentown, Pennsylvania, USA, has announced the appointment of Eduardo F Menezes as Chief Executive Officer, effective February 7, 2025. Menezes will succeed Seifollah Ghasemi, who is leaving the company after over ten years of service. Menezes will also join the Air Products Board.
The company’s board of directors has also appointed Wayne T Smith as chairman and Dennis H Reilley as vice chairman. As part of the full board, they will collaborate with Menezes and the leadership of Air Products in an effort to advance the company.
Commenting on the appointment of Eduardo Menezes, Smith stated, “After evaluating various exceptional candidates for the CEO role, the Board determined that Eduardo’s knowledge, skills and extensive
experience in the industrial gases sector, including more than threeand-a-half decades in progressively senior roles at Linde plc and operating experience across the world, make him uniquely qualified to take Air Products forward and maximise value for shareholders.”
Menezes added, “Air Products is a fantastic company with a great future, and I am honoured to have this opportunity to work with the talented team to build on the company’s strong positions. I look forward to applying the experiences and perspectives I’ve gained in working across various sectors of industrial gases in different countries around the world. With our collective focus and discipline, I am confident in our ability to drive superior value.”
Menezes brings international experience in all key sectors of industrial gases, including on-site,
Air Products has announced the appointment of Eduardo F Menezes as Chief Executive Officer (Courtesy Air Products)
merchant liquid, packaged gases and hydrogen. In his last position, he was the executive vice president (EVP) of Linde plc for Europe, the Middle East and Africa, with responsibility for operations in more than forty countries with over $8 billion in sales and 18,000 employees. Prior to that, Menezes worked for Praxair in a variety of senior roles, including as EVP accountable for North America and in a series of general management and business development positions in the US, Spain, Mexico and Brazil. www.airproducts.com
IperionX, based in Charlotte, North Carolina, USA, has announced that it has been awarded a contract for up to $47.1 million in funding by the US Department of Defense (DoD) to strengthen the US Defense Industrial Base by accelerating development of a resilient, low-cost, and fullyintegrated US mineral-to-metal titanium supply chain.
This strategic partnership represents a combined investment of $70.7 million between IperionX and the DoD to fund a two-phase development programme over a two-year period. The agreement aims to strengthen US titanium production capabilities, supporting national security and economic resilience.
As part of the initial phase, the DoD has obligated $5 million through the Industrial Base Analysis and Sustainment (IBAS) programme and
IperionX will contribute $1 million, to expedite the Titan Critical Minerals Project in Tennessee to ‘shovelready’ status, an important milestone in securing a new domestic source of titanium, rare earths and zircon critical minerals.
The remaining $42.1 million awarded under the contract is expected to be obligated by the DoD over the duration of the agreement, with the funds to be applied to facilitating vertical integration and increased titanium production capacity at IperionX’s Titanium Manufacturing Campus in Virginia.
IperionX CEO, Anastasios Arima, shared, “This award is a pivotal moment in IperionX’s mission to re-shore the US titanium industry. For too long, American industry has been reliant on foreign-controlled supply chains for this critical
high-strength metal. IperionX’s proprietary technologies, combined with the Titan Project, offer a pathway for a resilient end-to-end US titanium supply chain. We are proud to be selected by the DoD as a key partner in strengthening US industrial and defence capabilities.” Titanium is a critical material for the aerospace, defence, automotive, space, and consumer industries, but its high cost and reliance on foreign supply chains have limited its broader adoption. IperionX’s Hydrogen-Assisted Metallothermic Reduction (HAMR) and Hydrogen Sintering and Phase Transformation (HSPT) technologies are reported to provide a pathway to produce low-cost, high-performance titanium.
This funding from the DoD’s IBAS programme reflects the US government’s focus on securing domestic critical minerals and metals supply chains. www.iperionx.com
• Trapping Systems to Suit The Best Thermal Processing Solution for the Powder Industry Our experienced team is ready to solve your toughest thermal processing challenges and will design, manufacture, install and maintain
FEATURES
• Metal or Graphite Hot Zones
• Metal and Graphite Retorts
• Debinding & Sintering
• Additive Manufacturing
• Metal Injection Moulding
• Ceramic Injection Moulding
• Powder Metallurgy
Citing sources familiar with the issue, Nikkei Asia has reported that Apple is exploring the possibility of manufacturing iPhones in Indonesia. The move is said to be in response to the Indonesian government’s recent ban on smartphones with fewer than 40% of components produced domestically.
The ban – imposed in October 2024 – is intended to create local jobs and bolster the country’s technological manufacturing sector. In November 2024, reports first emerged that Apple proposed a $100 million manufacturing facility in Bandung, West Java, to comply with the new regulations.
If the new facility is announced, it would mark Apple’s first production venture in Indonesia.
Chinese sales slump
Nikkei Asia also reported that Apple is seeing significant sales decline in China. In an effort to overcome this, Apple has partnered with the Alibaba Group to develop AI features targeting the Chinese market.
www.asia.nikkei.com www.apple.com
ASEAN Ceramics has announced that it will be hosting this year’s event in Bangkok, Thailand, from October 15-17, 2025. Thailand is emerging as a leading manufacturing hub in the Southeast Asia region; supported by its strong infrastructure and governmentbacked Thailand 4.0 initiative, the demand for advanced and technical ceramics is on the rise.
Thailand is known for its electronics manufacturing, automotive production and high-tech industries, making it an ideal location for global suppliers looking to tap into the burgeoning market. The ASEAN region is expected to be one of the fastest-growing markets for advanced and technical ceramics, fuelled by industrialisation and technological innovation.
ASEAN Ceramics Thailand will host a 5,000 m 2 exhibition space, showcasing over 200+ companies and brands, along with over 4,000 trade visitors and buyers, fostering collaborative opportunities. This event aims to be a dynamic platform for comprehensive knowledge exchange and collaboration within the ceramics industry.
www.aseanceramics.com
The EROWA PM Tooling System is the standard interface of the press tools between the toolshop and the powder press machine. Its unrivalled resetting time also enables you to produce small series profitably.
www.erowa.com
HP Additive Manufacturing, based in Barcelona, Spain, and Legor, Bressanvido, Italy, have partnered to produce a customisable, sustainable, Italian-made watch. Designed and developed by Thomas Lehman and his Milanese team in AnalogLab, the Amano+ is manufactured in stainless steel using Binder Jetting Additive Manufacturing.
customise their Amano+ in real-time, selecting cases, dials and straps to match their stylistic preferences.
The Best Thermal Processing Solution for the Powder Industry
FEATURES
• Metal or Graphite Hot Zones
• Metal and Graphite Retorts
• Debinding & Sintering
• Trapping Systems to Suit
Clients can customise their Amano+ in real-time, selecting cases, dials and straps (Courtesy Amano+)
APPLICATIONS
“We have created a groundbreaking innovation in the industry,” stated Lehman, founding partner of AnalogLab. “By working with our Legor and HP, material and production contributors, we seek to develop a closed loop production system harnessing the power and innovation of 3D printing in 316L stainless steel to allow our buyers to create for the first time their own
“We are proud to be part of this project, as it has once again allowed us to highlight Italian excellence and the ‘Made in Italy’ mark, enhancing the expertise and tradition that have defined our country over the years,” stated Fabio Di Falco, Marketing & Customer Support Manager at Legor. “In collaborations like this, we put innovation at the service of designers to bring unique and ever-more exclusive products to life, pushing the boundaries of creative possibilities.”
Our experienced team is ready to solve your toughest thermal processing challenges and will design, manufacture, install and maintain the Best Sintering Furnace you’ll ever own.
Through an advanced sintering process, HP’s Binder Jetting technology enables the production of metal components with density,
• Additive Manufacturing
Discover more in our webinar
• Metal Injection Moulding
• Ceramic Injection Moulding
• Powder Metallurgy
We recently hosted the ‘Beyond extraordinary: Crafting time with HP Metal Jet S100’ webinar. The presentation included a more detailed view of the ups and downs of the Amano+ journey, ending on the high of the remarkable reality. The webinar can be viewed in full on the www.metal-am.com website.
SYSTEMS, INC.
Best Thermal Processing Solution for the Powder Industry
FEATURES
ever own.
• Metal or Graphite Hot Zones
• Metal and Graphite Retorts
• Debinding & Sintering
• Trapping Systems to Suit
APPLICATIONS
• Additive Manufacturing
• Metal Injection Moulding
• Ceramic Injection Moulding
• Powder Metallurgy
The 10 th edition of AM Ceramics will take place in Vienna from October 21–22, 2025. Hosted by TU Wien, the event will once again bring together experts in ceramic Additive Manufacturing to showcase the latest advancements – from
industrial use cases to material research.
The event looks to offer innovators, manufacturers and researchers the ideal opportunity to network with top players in the ceramic industry.
www.amceramics.cc
Krahn Ceramics, based in Hamburg, Germany, is celebrating its fifth anniversary and reflecting on its successful journey in the ceramics industry. Originally founded over thirty years ago as a distribution segment of Krahn Chemie, Krahn Ceramics has evolved into an independent company in the past five years.
Important milestones include the acquisition of the binder manufacturer eMBe in 2019 and the launch of its own technical centre in Dinslaken – the core for new developments and the continuous optimisation of ceramic feedstocks. Krahn Ceramics first presented itself as an independent entity at Formnext 2019, which was followed by its debut under the new Krahn Ceramics name and branding at Ceramitec 2020, showcasing its product and service portfolio to the industry.
Since then, the company has experienced significant growth, not only in team size but also in capabilities. At the beginning of 2023, Krahn Ceramics established its own production facility at the Mühlenhagen site, which it is now further expanding to meet increasing demands.
“Our focus is on growth and innovation, and we are seeing rising demand with numerous new projects,” explained Dr Stefan Stolz, Managing Director of KRAHN Ceramics. “The expansion of an additional production line for Ceramic Injection Moulding compounds and the growing market requirements demonstrate how much we have accomplished in the past five years. The dedication of our entire team is truly paying off.” Dr Stolz added that the company is also working on projects in prototyping and toolmaking, emphasising the readiness for future challenges.
www.krahn-ceramics.com
Mesago Messe Frankfurt GmbH has announced that Spain will be its partner country for Formnext 2025, scheduled to take place from November 18-21, 2025, in Frankfurt, Germany. Spain has been selected to bring an array of innovative exhibitors and the next generation of production to the event, explains Mesago Messe Frankfurt. In addition to its highly dynamic and rapidly growing Additive Manufacturing industry, its shared language is hoped to bolster representation from South American industry.
The strength of the Iberian AM sector is readily apparent at Formnext, where Spain has been one of the nations with the most exhibitors for a number of years – including around thirty in 2024.
“We’re thrilled to be hosting such an incredibly exciting partner country and all its innovative AM firms,” stated
Sascha F Wenzler, Vice President for Formnext at Mesago Messe Frankfurt GmbH. “Spain is a perfect example of how AM helps ensure growth and new developments and gives a boost to the entire manufacturing industry, even in challenging times.”
Spain’s AM sector currently employs over 1,200 people and grows by double-digits every year. According to Wohlers Report 2024, 1.5% of the Additive Manufacturing machines installed around the world are located there.
“Although the market size is still small, the forecast for the incoming years is promising,” said Naiara Zubizarreta, director of the Spanish Additive Manufacturing association ADDIMAT.
At the same time, the Spanish AM industry is highly diverse and features numerous internationally renowned system manufacturers
such as HP Printing and Computing, Meltio, Triditive, Reinforce 3D, and Supernova, as well as many material producers, software developers, specialised service providers, and research institutes.
This year, ADDIMAT and the AM network IAM3DHUB are supporting Formnext as partners. “These highly engaged organisations play essential roles in Spain’s AM industry and will once again be on hand to demonstrate the remarkable potential of their country’s AM landscape along with their member companies and cooperation partners,” Christoph Stüker, Vice President Formnext at Mesago Messe Frankfurt GmbH, commented.
To help support the process of technological evolution, Spain has constructed a strong manufacturing network. ADDIMAT is operating under the umbrella of AFM Cluster, an industry cluster covering seven Associations, offering tailored services for the advanced manufacturing industries.
www.formnext.com
Material Options (Metal)
Material Options (Ceramics)
Build Envelope
Quantity
Tolerance capability
CONTACT FOR MORE DETAILS
17-4PH, SS 316, Tool Steel M2 & S-7, Inconel 625, 4140
Alumina 99.5%, Zirconia
~ 300 grams max, Footprint equivalent of baseball size or less, 0.02” (0.50 mm) wall thickness minimum
10~50 samples based on footprint. Larger quantities up to 1,000 pcs welcome depending on the part size.
Within 2% of the feature size, 2~3 Ra Surface finish, Option of finishing to closer tolerances available.
NORTH AMERICA Email: Mukund.N@indo-mim.com Ph: +1 (210) 557-1594
EUROPE Email: InfoEU@indo-mim.com Ph: +49 1732656067
ASIA Email: InfoHQ@indo-mim.com Ph: +9198459 47783 / +91 98450 75320
ISO 9001:2015 / IATF 16949:2016 / AS
The European Powder Metallurgy Association (EPMA) has announced its 2025 Powder Metallurgy Thesis Competition is now open. The EPMA has been organising the Powder Metallurgy Thesis Competition since 1994, promoting Powder Metallurgy research among European academics at both Masters and Doctorate levels.
The competition is open to all graduates of European universities whose theses have been officially accepted or approved by their respective institutions within the past three years. An international panel of project management experts
from academia and industry will evaluate the submissions.
The competition has two categories:
Diploma/Masters category
• Cash prize: €500
• Complimentary registration to the Euro PM2025 Congress and Exhibition
Three-minute presentation of the winning thesis during the opening plenary session
Doctorate/PhD Category
• Cash prize: €1,000
• Complimentary registration to the Euro PM2025 Congress and Exhibition
• Three-minute presentation of the winning thesis during the opening plenary session
The application deadline is April 23, 2025.
www.epma.com www.thesiscompetition.epma.com
TekSiC, based in Linköping, Sweden, has announced its new Xforge HT, a modular high-temperature induction heating furnace. The Xforge HT is designed for various high-temperature heat treatment applications, such as post processing of additively manufactured components, sintering, various diffusion treatments, material testing, etc.
“The Xforge HT represents the next step in our evolution as a company,” stated Joachim Tollstoy, CEO of TekSiC. “This product is a result of our dedication to innovation, designed with the flexibility to meet the specific needs of processes in high temperatures, low pressures, and introduction of process gases. We engineered it to provide the highest performance in the most demanding environments while offering a modular solution that can
be customised to each customer’s unique requirements.”
The Xforge HT is designed for high-temperature performance, reportedly able to stably exceed 2500°C. Its pressure and gas management system is said to enable the precise regulation of the processing environment, allowing optimal conditions for complex heat treatment applications. The machine’s design is also focused on versatility, enabling the generation of high-vacuum environments while allowing the controlled introduction of multiple gases, including hydrogen. Its advanced control algorithms enable precise thermal management, making it even possible for processing refractory metals such as tungsten, niobium, and tantalum. Throughout its development, Xforge HT underwent industrial
The new Xforge HT furnace (Courtesy TekSiC)
reliability testing at customer sites over several years, demonstrating its ability to function during extreme high-temperature applications. Additionally, Xforge HT is CE-marked, certifying compliance with EU health, safety, and environmental standards. www.teksic.com
The 4 th Asia-Pacific International Conference on Additive Manufacturing (APICAM) is scheduled to take place at RMIT University, Melbourne, Australia, from June 30 – July 3, 2025. The event will feature leading experts from biomedical, defence, and aerospace industries to address
pressing challenges and innovative solutions shaping the future.
APICAM was created to provide an opportunity for industry professionals and thinkers to come together, share knowledge and engage in the type of networking that is vital to the furthering of the AM industry.
www.apicam2025.com.au
TMS2025 Annual Meeting & Exhibition, scheduled to take place from March 23-27, 2025, at MGM Grand Las Vegas Hotel & Casino, Las Vegas, Nevada, is expected to attract more than 4,000 engineers, scientists, business leaders, and other professionals in the minerals, metals, and materials fields for a comprehensive, cross-disciplinary exchange of technical knowledge.
Our vacuum furnaces solutions for INDUSTRY and R&D LAB: - High Temperature Vacuum Sintering - Debinding & Sintering - Debinding/Pre-Sintering - High Pressure Sinter-HIP Vacuum thermal technologies: MIM, CIM, Hard Metal
The event will present more than one hundred symposia planned by all five TMS technical divisions, covering a broad range of topics related to minerals, metals, and materials science and engineering. The symposia have been divided into the following eleven technical tracks:
• Additive Manufacturing
• Advanced characterisation methods
Biomaterials
• Data-driven and computational materials design
Electronic, magnetic, and energy materials
• Light metals
• Materials degradation and degradation by design
• Materials synthesis and processing
• Mechanics of materials
• Nuclear materials
• Special topics
In addition to the technical conference, the event will include an exhibition where delegates can meet with exhibitors, and attend a number of special networking events. View the website to access the most current list of exhibitors and to learn more about exhibiting companies. www.tms.org
The inaugural Vicenza Symposium, an event focused entirely on technologies and manufacturing trends in the jewellery sector, will take place September 2-4, 2025. Basilica Palladiana, a UNESCO World Heritage Site in Vicenza, Italy, will host the event, which is aimed at professionals, academics and industry leaders.
The programme will feature a schedule of professional development sessions, networking opportunities, and discussions on key topics for the industry, including Additive Manufacturing and Powder Metallurgy, the integration and use of artificial intelligence, regulatory updates, and quality control. Innovative technologies in the field of jewellery and fashion accessories production will also be presented.
The Vicenza Symposium will be structured around two main sectors: fine jewellery and fashion accessories made from non-precious metals. It will be a non-commercial, highly technical event featuring twenty-one international speakers across seven daily sessions. Each session will last about forty-five minutes and focus on sharing advancements and innovations in the industry. The symposium will also include daily Q&A sessions, during which participants can interact with the speakers.
A significant part of the event will be dedicated to the presentation of numerous papers that will explore the most relevant topics for professionals in the goldsmithing and jewellery industry. Approximately 25% of the
papers will delve into the world of fashion jewellery, with particular attention given to precious metals and production techniques, with a balanced approach intended to reflect the symposium’s mission: to foster the exchange of knowledge and technological advancements among experts and researchers, thus contributing to the growth of the sector. A complete agenda is available via the event’s site.
The Vicenza Symposium was introduced to the global industry community during the January 2025 edition of Vicenzaoro Europe’s leading International jewellery, goldsmithing, and watchmaking exhibition organised by the Italian Exhibition Group together with T.Gold – International exhibition for goldsmithing machinery and technology.
Early-bird rates are available until April 15; the mid-rate discount is available until May 31.
www.thevicenzasymposium.com
The German Ceramic Society (DKG), Köln; Fraunhofer IKTS, Dresden; and Fraunhofer IFAM, Dresden, have announced a jointly sponsored workshop: Sustainability in Powder Technology Processes. The event is scheduled to take place March 25-26.
The ecological, economic, and legal aspects of sustainability are increasingly influencing industrial practice. The workshop will provide an overview based on industrial examples from powdertechnological production in Powder Metallurgy and ceramics. It is aimed at industrial users to help them get started with the topic and offer suggestions for their own approach. In addition to the basics of sustainability,
documentation options and relevant legal framework will be addressed.
The lecture programme, including numerous contributions from experienced industrialists, also offers space for individual discussions and for tours of the laboratories of the two neighbouring Fraunhofer institutes IKTS and IFAM. Here, the process chains of Powder Metallurgy and high-performance ceramics are shown in their entirety. Besides the equipment for powder preparation, press granulate and feedstock development, numerous shaping systems for conventional and Additive Manufacturing will be available, as well as heat treatment systems and machines
The Sustainability in Powder Technology Processes workshop will be held in March (Courtesy German Ceramic Society)
for green and hard machining of components. A joint dinner offers the opportunity for an exchange of ideas and further networking.
The workshop will be held in German.
www.dkg.de
www.ikts.fraunhofer.de www.ifam.fraunhofer.de
Ricoh Company, Ltd, headquartered in Kanagawa, Japan, has developed a process to join aluminium parts fabricated by Binder Jetting (BJT) to wrought aluminium alloy. This new technique not only eases the restriction on the size of parts fabricated by Binder Jetting, but it also has the potential to significantly reduce costs.
Metal Binder Jetting is a highly productive and low-cost Additive Manufacturing technology that can be used for prototyping and series manufacturing. However, because BJT requires sintering, it can be difficult to ensure accuracy when manufacturing very large parts, explains Ricoh.
Ricoh’s newly developed diffusion bonding technology for sintered materials fabricated by the BJT method solves the above issues. The company is using its proprietary liquid-phase sintering technology, which is useful in the fabrication of high-efficiency heat exchangers and other applications.
A heat exchanger consists mainly of fins that determine cooling performance and a case that determines the component’s dimensional accuracy. Ricoh’s idea is to use BJT to make fins of complex shapes and join them to an aluminium case prepared using an existing method. BJT’s ability to fabricate complex shapes allows for highly efficient cooling performance, while the machining accuracy of existing methods ensures the dimensional accuracy of the component.
Fig. 2 shows a sample of 6061 aluminium bonded to a gyroid-type fin. The fin is fabricated with the aluminium BJT and joined to the base using the newly developed diffusion bonding technique. Its appearance shows that the gyroid shape created by the BJT machine is joined to the 6061 block without distortion. The cross-sectional image also shows
that there are few voids at the interface between the BJT sintered body and the 6061 block. By utilising this bonding technique, a component with three fins (gyroid) bonded to the case can be made, producing a heat exchanger as shown in Fig. 1.
Fig. 3 shows an example of a large component fabricated by combining this diffusion bonding technique with conventional brazing. Ten gyroids made by aluminium BJT are diffusion bonded inside a 1050 aluminium case. The case and lid are joined by conventional brazing. The external dimensions of this component are 400 x 160 x 10 mm. Such a large cooling component can be difficult to make in one piece using BJT, explains Ricoh, but is possible using the diffusion bonding technology.
In addition to 6061 and 1050 aluminium alloys, Ricoh’s diffusion bonding technology has also been confirmed to be capable of joining 6063 aluminium and BJT sintered bodies.
The diffusion bonding method is based on technology that controls the amount of aluminium liquid phase accumulated in the development of the sintering process for Ricoh’s aluminium BJT machine. Unlike brazing, this technique does not require flux or brazing material. Brazing is a typical technique for joining aluminium, but there are limitations to the aluminium alloy compositions that can be used for brazing. Aluminium alloys for Additive Manufacturing, including Powder Bed Fusion, have been developed to make the method work, but they are not necessarily suitable for brazing. Ricoh’s technology is reported to be novel, in that both the Binder Jetting and the joining process are effective.
Takafumi Sasaki, head of the metal BJT project at Ricoh, stated, “This unique bonding technology will achieve both improved cooling efficiency and reduced component costs, and also allow for larger
Fig. 1 Example of a heat exchanger component fabricated by joining the sintered aluminium BJT part and a wrought alloy (Courtesy Ricoh)
Fig. 2 Example of an aluminium BJT sintered part joined to a wrought alloy base (Courtesy Ricoh)
Fig. 3 Example of a large component fabricated using this diffusion bonding technique with conventional brazing. Photograph and X-ray CT images are shown (Courtesy Ricoh)
component sizes. This technology will bring our customers closer to utilising aluminium BJT in the manufacturing field. We plan to further validate its manufacturing feasibility in the real market through collaborations with our customers.” www.ricoh.com
3DEO has risen to become a significant player in metal Additive Manufacturing, producing over 1.5 million parts since 2018 for customers in the aerospace, medical, and semiconductor industries, among others. Uniquely, the company uses its own Intelligent Layering® technology rather than relying on commercially available AM processes such as Binder Jetting. Bernard North visited the company for PIM International and reports on how it has achieved commercial success in an industry where more widely known processes are struggling to make progress.
During a January 2025 visit to 3DEO’s Torrance, California, facility, a simple phrase on a company notepad caught my eye: Launch Better Products, Faster. This succinct statement encapsulates much of 3DEO’s philosophy. While many Additive Manufacturing companies make similar claims, 3DEO truly delivers by harnessing its proprietary Intelligent Layering® technology. Coupled with a customer-centric, partnershipdriven approach, this technology is enabling the company to stand out in an increasingly competitive industry. The half-day visit – hosted by Scott Dennis, Chief Executive Officer, and Emily Elpes, Head of Human Resources and Communications – provided further insight into the company’s approach. 3DEO takes a distinctive path in the Additive Manufacturing landscape. Unlike most, it not only develops its own AM technology but also builds its own machines and operates as a contract manufacturer – producing parts at scale using its proprietary process. This vertically
integrated approach is rare, if not unique, but highly effective. While much of the industry’s focus is on the commercialisation of Binder Jetting (BJT) and other processes, 3DEO is already among the world’s highest-volume producers of metal AM parts.
The company is the brainchild of Matt Petros and Payman Torabi, who worked on their PhDs in the same lab at the University of Southern California (USC) in Los Angeles. Driven by a shared belief that they could develop a sinter-based Additive Manufacturing process superior
2 Scott Dennis has been 3DEO’s Chief Executive Officer since August 2024. He is a co-founder of FusionX Ventures, 3DEO’s lead investor, and brings extensive experience in the AM machine business (Courtesy 3DEO)
“Dennis summarised 3DEO’s investment backers as primarily venture capital partners specialising in highly technical startups, led by FusionX Ventures, Alpha Edison, and Razor’s Edge... Recently, several Japan-based organisations have taken significant equity positions.”
to conventional Binder Jetting, they set out to innovate. As PIM International readers will know, BJT was invented in the 1990s but struggled to achieve widespread commercial success.
In 2016, Petros and Torabi founded 3DEO, initially operating out of a small space in Los Angeles’ garment district about two miles from the USC campus. In 2018, they relocated to the LA suburbs,
establishing a 1,500 m 2 facility in Gardena. As 3DEO continued to grow, the company moved again in 2020 to its current home near Torrance Municipal Airport, just a few miles from the previous location. Employment has since expanded to approximately fifty people. Petros and Torabi took good care to protect their technology, amassing eighteen patents and trademarking the term ‘Intelligent
Layering’ to describe their unique technical approach.
Torabi served as Chief Technical Officer, a role he still holds, while Petros was Chief Executive Officer until the transition to Dennis in August 2024. Petros remains closely involved with 3DEO, continuing in both consulting and ownership roles.
When Dennis joined 3DEO, he brought extensive experience in Additive Manufacturing and related technology. His career began with five years at Hewlett-Packard in its inkjet R&D group before co-founding D&K Engineering in 2000 – a turnkey product development company that worked on complex products, including AM machines, for various clients. Through his work at D&K Engineering, Dennis collaborated with 3D Systems and other AM companies, playing a key role in the development and production of over ten thousand AM machines. He was also closely involved with 3DEO during the development of its first production platform.
In 2015, he co-founded FusionX Ventures, a venture firm based in San Diego, California, that specialises in the technology, industrial, and medical/life science sectors.
As 3DEO’s lead investor, FusionX supports startups developing innovative solutions at the intersection of hardware, software, and cloud technologies.
Dennis summarised 3DEO’s investment backers as primarily venture capital partners specialising in highly technical startups, led by FusionX Ventures, Alpha Edison (Los Angeles, California) and Razor’s Edge (Reston, Virginia), along with smaller holdings by other investors.
Recently, several Japan-based organisations have taken significant equity positions, notably (in chronological order) DBJ (the Development Bank of Japan), Seiko Epson [1], IHI Aerospace [2], and Mizuho Bank [3]. Dennis attributed the strong
Japanese interest to a combination of aerospace and industrial applications for 3DEO’s technology, strong connections between FusionX Ventures and Japanese institutions, and the merit that investors saw in 3DEO’s technology and prospects.
Dennis summarised the sequence of events in the green part forming stage of the Intelligent Layering production cycle. The differences between Intelligent Layering and BJT are described in more detail in the following section.
Firstly, the powder is pre-coated in a proprietary process to improve its uniformity and packing density during subsequent spreading. It is then evenly spread to create a uniform thickness layer across the working bed of the machine. A binder treats the fresh layer of powder, which is deposited via a propri -
etary process. A heating pass dries the powder, making it friable and increasing its green strength. Then, CNC green machining of the layer is performed using ganged (in production machines) 1 mm diameter carbide end mills driven by high-speed (60,000 rpm) spindles. The machined powder is vacuumed off. In three-axis green machining, the end mills move in the xy plane, and raising or lowering the whole bed provides the z-axis movement, allowing the cutting of 3D curved surfaces. The end mills are cleaned of any adherent powder during their
‘idle’ period in the cycle. In-process, vision-based dimensional measurement enhances dimensional control, provides detailed quality assurance data, and enables ‘hands-off’ process correction.
The layering and machining processes are repeated until the full height of the parts is reached. Finally, at the end of a build run, the green machined parts are lightly attached to and surrounded by a ‘cake’, from which they are removed, followed by any depowdering from cavities or intrusions and final trimming.
“In three-axis green machining, the end mills move in the xy plane, and raising or lowering the whole bed provides the z-axis movement, allowing the cutting of 3D curved surfaces.”
Dennis highlighted key differences between Intelligent Layering and conventional Binder Jetting. Notable distinctions include full-layer bonding, in-process green machining for precision, standardised part production per cycle, and a unique powder recycling approach.
In Intelligent Layering, the entire powder layer is bonded, whereas in conventional BJT, only cross-sections of the parts being produced are bonded.
Unlike Binder Jetting, 3DEO’s Intelligent Layering incorporates in-process green machining. This hybrid additive/subtractive approach allows precision machining of green parts, resulting in superior dimensional accuracy and surface finish
compared to standard BJT methods. In-process dimensional measurement data are automatically fed into the CNC programme, controlling the green machining process and further improving dimensional consistency.
The use of ganged end mills in production machines means that a machine’s output in any given cycle comprises identical parts – unlike BJT, where a mix of part geometries can be made in a cycle. Dennis explained that, in practice, this is not a disadvantage due to the relatively small size of the machines’ working powder bed and typical order quantities of specific components. Additionally, singlespindle versions of 3DEO’s equipment allow for multiple-part geometries within a given cycle.
Intelligent Layering differs from Binder Jetting when it comes to
handling unused powder. In Binder Jetting, the powder around the components is not bonded with a binder and, after depowdering, it can be mixed with virgin powder to create feedstock for future runs. In contrast, 3DEO returns all unused coated or machined powder to its suppliers for reprocessing. Plans are underway to develop an in-house system for recycling this powder.
One exciting aspect of the 3DEO plant tour was seeing multiple generations of machines. With ample space and a commitment to both IP protection and company history, older machines remain on-site alongside those currently in operation.
The tour showcased 3DEO’s machine evolution, from the first basic single-spindle unit used for early development to a prototype with four spindles and modern
controls. Currently, three singlespindle machines support research, while a development lab houses eight upgraded early versions of the latest eight-spindle units used for piloting, cycle refinement, and new material production – including a dedicated copper component cell.
Finally, a production room had fourteen eight spindle units. As indicated by their green Andon lights, seven were running at the time of the tour. The machines have a build volume of approximately 23 cm x 23 cm, with a height of up to 12 cm. In practice, though, the actual depth used depends on part dimensions, with the tallest part so far reaching 80 mm in height.
3DEO purchases metal powders from qualified suppliers and rigorously evaluates each batch using a combination of supplier-provided data, internal testing, and accredited laboratory analysis before releasing batches for production.
3DEO receives CAD product files from potential customers and processes them using its proprietary software, which plays a key role throughout all stages of production. Engineers analyse factors such as powder layer depth, sintering shrinkage, and depowdering capabilities to ‘slice’ the components into thin layers that correspond to individual powder layers and their respective green machining passes. This information is then used to generate the CNC programme for the three-axis machining process and the total number of layers required for manufacturing the whole green part.
Process optimisation is carried out based on the alloy being used, the complexity of the geometry, and/or the degree of difference from previously qualified components. This is first conducted on single-spindle machines in the research area and/ or eight-spindle machines in the development area. Then, a production sintering cycle is used to confirm part geometry conformance, reducing
the need for additional machining or grinding. Once qualified and production orders are received, the optimised slicing and machining cycle is implemented on production eightspindle machines, as outlined in the previous section.
Once the build is complete – typically around eight hours (one shift) – though this varies based on part quantity and geometry – the ‘cake’ is removed from the machine, and green parts are separated. In some cases, minor trimming is performed prior to placement on ceramic separators atop molybdenum sintering trays. Usually, this is conducted manually, but the production area included a robot machine employed for certain high-volume products. Numerous small ovens are used for further drying and to avoid any moisture pick-up prior to the subsequent combined debinding/sintering cycle.
The plant has three debinding/ sintering furnaces. However, most prototyping and production work is conducted in an Elnik Systems batch sintering furnace with sophisticated gas partial pressure and flow capabilities in addition to a vacuum.
Dennis stressed that, despite the dimensional accuracy and surface finish control offered by 3DEO’s process, some components still require finish machining or grinding to meet customer specifications. This is a standard practice in the Metal Injection Moulding industry, and the final products achieve comparable tolerances to those offered by conventional precision machining. For better control and reduced lead times, 3DEO generally prefers to perform these post-sintering processes in-house whenever feasible.
During the tour, we passed by two Haas CNC machines, bead blasting equipment, a magnetic pin finisher, centrifugal barrel tumblers, vibratory tumbling units, and ultrasonic cleaning stations. Certain postsintering processes, such as brazing, nickel plating, black oxide coating, and Hot Isostatic Pressing (HIP), are subcontracted. Additionally, 3DEO will qualify other processes if requested
by a customer. A small heat treatment furnace is used to achieve the H900 condition, which is commonly applied to 17-4 PH stainless steel.
Machining is also conducted in-house on non-AM parts supplied by other companies; 3DEO then combines these parts with its own finished AM parts to provide customers with completed assemblies.
Finally, in-house quality assurance is performed using various techniques, including hard gauging, dimensional imaging, physical and mechanical property measurements, and metallographic analysis. Despite the very high capability of 3DEO’s processes, many product characteristics are 100% inspected, reflecting the critical nature of their customer’s applications in areas such as medicine, aerospace, and semiconductors.
Dennis stressed the fully integrated nature of 3DEO’s in-house manufacturing software, which enables full traceability of individual components from the initial computer ‘slicing’ of CAD models right up to finished product inspection and every step in between. 3DEO achieved ISO 9001:2015 certification in February 2020 and is working to achieve the industry-specific aerospace AS9100 and medical ISO 13485 certifications.
In discussions with Elpes and Dennis, it became clear that 3DEO’s approach to Additive Manufacturing is deeply pragmatic, shaped by firsthand experience at what is surely a company with one of the highest volumes of sinter-based metal AM part production. One of the biggest challenges they observed was that many companies struggled to leverage AM fully – not due to limitations in technology but because of a lack of Design for Additive Manufacturing (DfAM) expertise. Elpes explained, “Without this know-how, AM was often relegated to being a one-for-one replacement for traditional manufacturing rather than the game-changer it truly is.”
Fig. 10 The microstructure of a 316L stainless steel part produced using 3DEO’s Intelligent Layering process (Courtesy 3DEO)
11 Quality control inspection of sintered parts (Courtesy 3DEO)
“In
discussions with Elpes and Dennis, it became clear that 3DEO’s approach to Additive Manufacturing is deeply pragmatic, shaped by firsthand experience at what is surely a company with one of the highest volumes of sinter-based metal AM part production.”
Other Elements: Total may not exceed 1.00% combined. Same chemical composition as the built parts. In accordance with MPIF Standard 35 MIM (2018 Edition) and ASTM A240.
To address this gap, 3DEO shifted its focus in 2022, evolving from a high-volume AM manufacturer to an end-to-end AM solutions provider. Now, the company combines DfAM expertise, engineering support, and scalable production, working closely with customers to optimise designs. Elpes described, “By doing this, we’ve made AM more accessible and impactful for our customers, helping them reimagine products and unlock new efficiencies.” This transformation has not only reshaped 3DEO but has also provided significant value to the industries served.
Summing up 3DEO’s mission, Elpes described its goal as “unlocking the power of Additive Manufacturing – to help customers optimise their products.” In other words, 3DEO functions as both a service provider and manufacturer, ensuring customers receive not just built parts but fully finished components – and, in some cases, even assemblies. To meet these expectations, several non-additive finishing processes have been integrated, either in-house or through qualified subcontractors.
A crucial part of 3DEO’s approach is DfAM, which Dennis explained exists at two levels: “The first is fairly generic for all AM processes, but the second, deeper level is highly process-specific.” Since detailed DfAM expertise remains rare among product designers, 3DEO prioritises working closely with customers who truly believe in AM and are willing to evolve their part designs to reduce costs and enhance manufacturability and performance.
Furthermore, Dennis emphasised that successful AM adoption – and the building of strong, lasting partnerships – requires strong executive sponsorship within customer organisations. Without leadership support, even enthusiastic ‘AM champions’ within companies may struggle to
push projects forward. Genuine partnerships in AM, much like effective DfAM processes, don’t happen overnight – they take time and mutual commitment.
Dennis shared his thoughts on the challenges facing the Additive Manufacturing industry, particularly in relation to the equipment manufacturing business. He noted that unrealistic growth projections in the industry led to over-investment, inflated valuations, and disappointments, resulting in some business failures. As Dennis put it, “AM is not the answer for every component,” and even when it is a good fit, it can take years to fully integrate DfAM into the customer-supplier relationship. Additionally, non-AM processes are often needed to produce finished parts, which many businesses fail to account for. Quality issues with some early AM products – an issue also reported by other companies – have further exacerbated the problem.
Despite these challenges, Dennis highlighted that there are success stories in the industry, with 3DEO being a prime example. One advantage of AM, according to Dennis, is the economy of scale it offers when customers have multiple parts that can benefit from Additive Manufacturing. The ‘sweet spot’ for AM components typically ranges from a few hundred to a few tens of thousands of units annually. Beyond that, it may be more cost-effective for customers to switch to MIM or even redesign components and revert to conventional manufacturing techniques.
A significant advantage of AM is short lead times. Since AM does not require press or MIM tooling, products can typically be turned around in a week if they have already been qualified. For parts still going through optimisation, the process takes around two to four weeks, depending on the level of fine-
“A significant advantage of AM is short lead times. Since AM does not require press or MIM tooling, products can typically be turned around in a week if they have already been qualified.”
tuning required. When 3DEO and the customer have already collaborated on DfAM, the process can be significantly quicker.
3DEO currently produces three different alloys on a commercial basis: 17-4 PH and 316L stainless steel, which together account for about 70% of production, and pure copper, making up around 30%. The stainless steel alloys cater to a wide range of industries and applications,
while copper is primarily focused on electrical applications, such as heat sinks for high-power semiconductors. Copper’s high electrical and thermal conductivity makes it ideal for cooling systems in AI applications, where AM’s ability to produce complex geometries helps dissipate heat effectively from integrated circuits. Additionally, Inconel 625 will soon be added to its offerings, with a focus on aerospace applications. Parts vary in weight, ranging from 0.4-420 g, and in size, from approximately 4 x 6 mm to 90 x 95 mm.
Medical and semiconductor industry applications are produced in the highest volumes, accounting for approximately 35% of 3DEO’s business each, followed by aerospace and various industrial applications each at around 15%. The company is starting to see promise in automotive applications, particularly for electric vehicles and hybrids. There are also some consumer products, such as fly fishing and razor blade holder components. In summary, 3DEO serves a highly diverse range of industries, with no single sector being the primary focus.
Geographically, around half of 3DEO’s business is outside North America, primarily in the Pacific Rim. Medical applications are more concentrated in North America, while aerospace products are predominantly for Japanese customers, including 3DEO’s IHI investor. Semiconductor products are often supplied to customers in Asia.
The split between repeat and new business is approximately even. New business consists of a mix of additional components for customers who have already qualified 3DEO for an initial part, as well as initial components for new customers.
3DEO’s sales team focuses on managing important customer accounts rather than organising their efforts based on different geographic locations. Much of the business growth comes from deeper penetration of existing customers, while new customers are gained through a mixture of sales calls, networking, trade shows, and digital marketing. Dennis noted that recent attendance at IMTS in Chicago and JIMTOF in Tokyo – both trade shows primarily associated with the machining of parts – was a strong indicator that AM is finally going mainstream.
3DEO is a member of several industry organisations, including MPIF, AMT (Association for Manufacturing Technology), and AMAM (Association of Metal Additive Manufacturing). Mahmood Shirooyeh, Senior Materials Scientist, is a member of the ASTM Committee F42 on Additive Manufacturing
Technologies, the AMAM Standard Committee, and MPIF’s PowderMet/ AMPM Technical Programme Committee.
With more than 1.5 million parts shipped since 2018, 3DEO has proven that AM is a truly production-ready technology. The company expects continued organic growth by qualifying more parts from existing customers while also developing business with new customers. Its 4,000 m 2 facility in Torrance has enough space to double its business without needing to relocate. However, the more intriguing question is whether – and if so, when – their proprietary technology will expand geographically and beyond the scope of 3DEO’s own operations.
Dennis made it clear that 3DEO will not sell machines or license technology to “just anyone.” However, the team is developing a version of 3DEO’s Intelligent Layering machine designed for third-party use, and
3DEO is open to partnerships that it has built strong relationships with. In particular, plans are at an advanced stage for a manufacturing capability in Japan. Watch this space!
[1] 3DEO secures investment from Seiko Epson and Development Bank of Japan. Metal AM, January 19, 2024, https://bit.ly/3EF9UnS
[2] 3DEO partners with IHI Aerospace to enhance adoption of Additive Manufacturing in Japan’s aerospace sector. Metal AM, March 14, 2024, https://bit.ly/4hRUmMl
[3] 3DEO secures $3.5million investment from Mizuho Bank. Metal AM September 10, 2024, https://bit. ly/4hwKMhw
Contact Emily Elpes Emily.elpes@3deo.co
Tel: +1 323 214 7665 www.3deo.co
Author Bernard North North Technical Management, LLC Greater Pittsburgh area Pennsylvania, USA brnrdnorth@gmail.com
April 8-10, 2025 | Huntington Place | Detroit, MI
Four world-class manufacturing events, together in one location
SME is bringing together these four events, providing access to more than 600 manufacturers while showcasing advanced manufacturing, smart technologies and mobility advancements. Combined Audiences, Magnified Impact!
At RAPID + TCT 2025, you’re under the same roof with SME’s AeroDef Manufacturing; SAE’s trademark mobility event, the World Congress Experience (WCX); and America Makes’ project success showcase, Technical Review & Exchange (TRX).
Claim your complimentary Expo Pass! Use promo code METALAM when registering
AFT-Hungary, a key European player in Metal Injection Moulding, has navigated industry challenges through strategic adaptation and market diversification. Facing intense price competition, shifting trade policies, and evolving regulations, the company has focused on expanding MIM applications beyond traditional sectors. By identifying new opportunities and refining its manufacturing processes, AFT-Hungary remains competitive in a rapidly changing landscape. Emma Lawn explores the company’s approach to sustaining growth, enhancing efficiency, and overcoming obstacles in today’s demanding manufacturing environment.
AFT-Hungary, based in Rétság, an hour’s drive from Budapest, is a leading European manufacturer of components produced by Metal Injection Moulding. The company was established in 2002 with a primary focus on the automotive sector; however, in 2012, it became part of ARC Group Worldwide, a US-based advanced manufacturing company. Since the acquisition, AFT-Hungary’s markets have expanded to include consumer products, defence, and other industries. ARC Group Worldwide also operates a MIM facility in the US, ARC Colorado, with a focus on the aerospace and firearms markets.
Amid challenging market conditions driven by price competition, regulations, and fluctuating international trade policies, AFT-Hungary has been able to maintain a competitive edge in Europe due to its strategic geographic position. However, it also has its eye on the future through MIM process innovation. “While ARC Group Worldwide is not the largest player in the market, it continues to push the boundaries
of material development,” stated Ádám Kurusa, General Manager of AFT-Hungary, who noted the group’s success in sectors such as aerospace.
Kurusa joined AFT-Hungary in 2020 and, under his leadership, the company has regained profitability
and is on a strong growth trajectory. “Our focus is now on innovation and market expansion,” he shares. The Hungarian facility currently generates annual sales of over $9 million.
Kurusa and the company’s Engineering Manager, Alan Bird, see significant untapped potential
in MIM, particularly in applications currently produced using traditional manufacturing methods. “Based on our expertise and experience over the past four years, we are convinced that many components could be produced far more cost-effectively with MIM,” Bird asserts. “After all, MIM was designed specifically to optimise manufacturing costs.”
Rather than competing within the existing MIM market or taking opportunities from other MIM manufacturers, AFT-Hungary focuses on introducing new applications where MIM technology can deliver longterm benefits for its customers. Bird explained that this approach enables the company to create a “true win-win scenario.”
As global supply chains increasingly shift toward regionalised production, European manufacturers are facing growing instability. “Two years ago, we lost a major customer because regional trade agreements made manufacturing in Europe financially unviable,” Bird notes. This disruption was initially the result of shifting US trade policies under US President Donald Trump’s first administration, which introduced significant uncertainty and left many industries in a state of flux. While the 2020 US-Mexico-Canada Agreement (USMCA) initially presented barriers, more recent proposed policy changes – such as increased tariffs and a focus on reshoring production – have only intensified these challenges. With cost competitiveness under increasing pressure, competing with Asian suppliers has become progressively harder. “Simply put, manufacturing in Europe is expensive,” says Bird, “competing with Asian players is extremely challenging, as pricing often takes precedence over quality.” Kurusa notes that, despite widespread discussions about strengthening regional supply chains within Europe, the “trend has increasingly leaned toward continent-specific preferences.” For example, American customers tend to favour US-based suppliers, while Asian customers show a similar preference for local
Fig. 4 A selection of MIM automotive parts produced by AFT-Hungary, a leading supplier of heat-resistant turbocharger components (Courtesy AFT-Hungary)
suppliers. This shift toward regional sourcing is driven by lengthy programme timelines and the need for closer proximity to reduce lead times.
Despite these challenges, AFT-Hungary has expanded into markets like India, South Korea, and China, demonstrating its ability to compete globally. “While price is often the deciding factor, total cost of ownership tells a different story,” says Bird. “Customers who prioritise long-term value recognise our quality advantage. This demonstrates that we can compete with Asian manufacturers not only in terms of quality but also on price,” Bird adds. European manufacturers are also facing increasing pressure to maintain high-quality production standards while remaining competitive in an increasingly cost-driven market. Kurusa acknowledges that “European regulations and compliance requirements tighten year after year,” and while such regulations are necessary, they place a “significant
“Ensuring adherence to evolving regulations requires continuous adaptation and investment, which adds complexity to an already competitive manufacturing landscape.”
burden on manufacturers. Ensuring adherence to evolving regulations requires continuous adaptation and investment, which adds complexity to an already competitive manufacturing landscape.”
While ARC Colorado focuses on aerospace and firearms, the Hungarian facility has a broader reach, spanning automotive, consumer goods (including power
tools, connectors, and rock climbing parts), and defence.
Kurusa notes that the civilian side of the firearms market is somewhat softer – mainly due to demand from the US market – but for current geopolitical reasons, non-civilian firearms demand is increasing. AFT-Hungary is expanding MIM applications into emerging markets, including appliances, motorcycling, and door-damping systems, as well as other industries, further strengthening its global presence.
Fig. 5 This worm gear, used in an automotive transmission locking mechanism, won an MPIF Design Excellence Award in 2021. MIM was chosen for its ability to produce the complex helical gear teeth and adjacent shaft geometry. Custom setters are used for sintering the parts, which require no secondary operations to function in the mating assembly (Courtesy MPIF)
“AFT-Hungary specialises in manufacturing MIM components for turbochargers, a crucial technology in modern automotive engineering. As turbocharger designs become more advanced, manufacturers require increasingly complex components that can withstand extreme conditions while maintaining performance.”
Despite challenges within the automotive sector, demand for MIM remains strong – particularly among European automotive manufacturers.
“The automotive sector has the most experience with MIM technology and understands its cost benefits,” Kurusa explains.
AFT-Hungary specialises in manufacturing MIM components for turbochargers, a crucial technology in modern automotive engineering. As turbocharger designs become more advanced, manufacturers require increasingly complex components that can withstand extreme conditions while maintaining perfor -
mance. As turbo technology evolves, AFT-Hungary continues to enhance its processes to meet these stringent demands. “MIM can keep up with these design changes and support the demand for turbocharger components,” explains Bird.
Despite the growth of electric vehicles, turbochargers remain crucial in optimising internal combustion engine (ICE) performance. “There’s been a renewed focus on ICE technology, but with greater emphasis on efficiency and emissions reduction,” says Bird. With engine displacements shrinking, turbochargers help maintain power output while improving fuel economy, ensuring sustained demand.
Beyond turbochargers, MIM technology is gaining traction in other automotive applications. “We’re seeing its use in transmission components (Fig. 5), fuel injection systems (Fig. 6), seat assemblies (Fig. 7), and valve supports,” notes Kurusa. Heat-resistant MIM materials are
also being explored for additional turbocharger elements, broadening the scope of the technology within the industry.
AFT-Hungary’s production of fuel injector valve discs stands as a testament to the capabilities of Metal Injection Moulding. The technology enables the efficient mass production of such intricate, highperformance components – a feat that traditional techniques such as casting or machining simply cannot match. The scale of this achievement is significant; notably, AFT-Hungary has produced 38 million valve units, maintaining a flawless quality record with zero reported rejects. The use of hardened 440C stainless steel, combined with the component’s small size, intricate details, and high annual demand, further demonstrates the unmatched capabilities of MIM technology.
Defence and firearms Wars and shifting geopolitical dynamics have driven rising demand for firearms and defence applications, which now account for 35% of AFT-Hungary’s annual revenue. Kurusa explains, “For any manufacturer aiming to produce firearms competitively and at high volumes, MIM components are essential.”
The growing firearms industry presents unique challenges compared to other MIM markets. While volumes can sometimes be lower compared to other MIM markets, firearm components often feature complex designs, which can make it challenging to maintain their ever more demanding tolerances after sintering.
As Bird explains, cost pressures are significant, both in terms of piece price and mould costs. To meet these challenges, AFT-Hungary is exploring interchangeable insert moulds to meet those cost pressures. Additionally, the company is looking into replacing traditionally machined firearm components with MIM solutions, especially for parts that typically require extensive machining time. “These components are not just the small MIM parts, but the main component of the firearm,” Bird adds.
Fig. 6 Automotive fuel injector valve discs. These high-performance parts are engineered to withstand extreme conditions and operate effectively within fuel injectors. They are designed for 1.2 billion cycles, ensuring longevity and reliability in automotive applications. AFT-Hungary developed a specialised material to meet the stringent requirements of the valve disc, achieving nearfull density. More than 38 million parts have been manufactured (Courtesy AFT-Hungary)
Today, the company operates out of a facility that spans more than 5,000 m². It is equipped to handle large-scale production with thirteen fully automated injection moulding machines, two debinding units, and four sintering furnaces. In order to ensure consistent, high-quality production, automation is used as much as possible. Automated inspection equipment is utilised in the secondary processing area to uphold stringent quality standards throughout the production process. Sizing, CNC machining, tapping/ reaming, and tumbling and polishing are all performed in-house. The only post-process steps outsourced are heat treatment and plating.
“AFT-Hungary is developing new Metal Injection Moulding technologies that will help increase the typical current weight limits for economically-viable MIM parts from around 100 g to 400 g.”
AFT-Hungary is developing new Metal Injection Moulding technologies that will help increase the typical current weight limits for economically-viable MIM parts from around 100 g-400 g. This innovation, part of a $3.25 million project with TETT Mérnökiroda Kft and ZalaZONE InnoTech Nonprofit Kft, is supported by a $2 million grant. Expected to be completed in two years, it aims to cut production costs and significantly expand the company’s manufacturing capability. Revenue is expected to increase by approximately $2.5-5 million through the development.
Despite MIM’s advantages, it remains underutilised in many industries, partly due to its limited presence in engineering education. “It is either briefly mentioned or not covered at all in most universities and technical colleges.” As a result, “newly graduated engineers rarely consider MIM as a manufacturing solution and often struggle to adapt their thinking to this technology,” Kurusa stated. This knowledge gap extends beyond academia to industry professionals, presenting both
a challenge and an opportunity.
Unfamiliarity with MIM often leads to inefficiencies in the design process. “Many European engineers find it difficult to break away from what they learned in academia,” Kurusa observes. “They often insist on unnecessarily tight tolerances in technical drawings, even when they serve no practical purpose. This lack of design for manufacturing (DFM) principles can significantly impact production efficiency and cost.”
MIM also requires a shift in design philosophy. “MIM requires a completely different mindset –almost a reverse way of thinking compared to traditional machining processes,” Bird elaborates. “In CNC machining, material is removed from a solid block, whereas in MIM, we build parts from metal powder. It’s a fundamentally different approach.”
Additionally, MIM is a highly specialised manufacturing process that demands significant technical expertise. “For many manufacturers, MIM exists only as a complementary production method rather than a core competency,” Bird notes. “This makes the emergence of new local players extremely rare.”
Recognising these challenges, AFT-Hungary actively supports customers through early project involvement. Regarding support in this area, Kurusa advocates, “By collaborating from the design phase, we can help optimise manufacturability and ensure the project’s success – a shared goal for both us and our customers.” This proactive approach, combined with a focus on demonstrating the efficiency and scalability of MIM technology, allows AFT-Hungary to embrace the challenges of the industry. As a result, the company continues to expand its market presence and strengthen its reputation for highquality manufacturing.
It was also stressed that customers should be better educated about MIM’s environmental benefits. Bird notes, “MIM is inherently a more environmentally friendly manufacturing process due to its minimal material waste.” As
part of the company’s ongoing sustainability efforts, AFT-Hungary continually works to optimise energy consumption within its facility. For instance, the company maximises the number of parts per tray in their furnaces, ensuring greater energy efficiency and minimising unnecessary furnace operation, further reducing their environmental footprint and operational costs.
Kurusa highlights a further sustainability consideration. “If a product is still being purchased, but is instead produced in another part of the world using a much more polluting method, then we have achieved nothing on a global scale. The challenge lies in finding the right balance.”
Despite global competition and regulatory challenges, AFT-Hungary continues to thrive through technological innovation and strategic diversification. By advancing Metal Injection Moulding technology and expanding into new markets, the company continues to strengthen its position as a leader in precision manufacturing.
Ádám Kurusa General Manager akurusa@arcw.com +36 (30) 497 9814
Alan Bird Sales and Engineering Manager abird@arcw.com
AFT-Hungary
Rétság, Ipari park 5, 2651 Hungary www.arcw.com/afthungaryintro/
The Metal Injection Moulding industry in Asia is experiencing significant shifts in feedstock sourcing and material usage. While BASF’s Catamold remains a key player, competition is growing, reshaping supply chains and production strategies. In this article, Dr Q (Y H Chiou) explores the evolving landscape, examining market and application trends, regional variations, and the increasing role of domestic Chinese feedstock manufacturers. As demand for complex, high-performance MIM parts rises, understanding these changes is essential for industry stakeholders.
The recent World PM2024 Congress, held in October in the vibrant city of Yokohama, Japan, brought together MIM industry representatives from around the world. While attending, I unexpectedly met with Nick Williams and Jon Craxford from PIM International – a happy surprise that sparked insightful discussions on the future of Metal Injection Moulding technology in Asia.
My presentation at World PM2024 set the tone for some of these discussions, including how PIM feedstock sourcing is changing across Asian markets. Does BASF SE, with its Catamold product, continue to dominate the feedstock market, or have there been shifts in the competitive landscape? Here, I will address these pressing questions and offer insight for readers from the global MIM industry.
More than fifty years after the earliest form of PIM was developed as a manufacturing process for ceramic applications, BASF’s 1984 invention of polyoxymethylene (POM)-based MIM feedstock
marked a milestone. This innovation provided a stable and efficient alternative to the wax- and waterbased feedstocks that had been the norm from the early days of MIM. This is not to say that wax-based and water-based feedstocks are disappearing; they continue to play an important role in the global MIM market, particularly in the specific applications where their properties are best suited.
Fig. 1 Feedstocks are at the heart of PIM technology and their ongoing development can open up new areas of application and improve process stability
Table 1 provides a comparative analysis of the three major feedstock systems and hybrid wax/POM, highlighting their respective advantages, challenges, and uses across different sectors. While BASF’s POM-based feedstock remains key in indus -
tries such as automotive, aerospace, and consumer electronics, the East Asian market, in particular, is seeing increasing diversity in feedstock sourcing, driven by growing demand for more complex, high-performance parts.
1
2
3
Table 1 A comparison of feedstock types among the three major systems *starting at 5 MPa
Based on data from my ongoing industry analysis, Table 2 shows feedstock usage trends in major PIM-producing countries across Asia. Materials for CIM include alumina, zirconia, ferrite, glass, and other ceramics, with production concentrated in China and Japan. MIM is usually centred around iron-based low-alloy steels, ironnickel alloys, and stainless steels, collectively known as the ‘three brothers’ of the major MIM materials. Their use significantly surpasses other materials. While cobalt and nickel alloys hold a share, their total usage remains far lower than that of high-specific gravity tungsten alloys. The use of other non-ferrous materials such as copper, titanium, and aluminium has been gradually increasing in China.
Table 2 Feedstock usage situation in major PIM-producing countries in Asia. A) in-house production, B) BASF, C) other external suppliers (China, Japan, and Europe, NA/not available)
PIM International readers worldwide may be curious about the continued success of BASF feedstock in Asia: How many tonnes of its feedstock is sold in Asia today? What is its share of the total regional feedstock supply, and what is its total share of MIM feedstock in the Chinese market? The following analysis considers these questions. Asia’s total MIM parts sales value for 2023 is estimated to be just over $2.7 billion, rising to $3 billion in 2024, and is dominated by China and Taiwan, followed by Japan and India. Table 3 provides a detailed estimate of the average
Table 3 MIM feedstock prices in China in 2023 ($/kg without tax, +/- 5%) (1) cost of atomisation ~$1.5, (2) cost of feedstock production ~$1.5 including binder cost, (3) average of approved Apple vendor list price
powder and feedstock prices in China.
In the estimate for 2023, the material cost of a MIM part accounted for approximately 10% of the minimum sale price. Therefore, the Chinese MIM industry spent around $200 million ($2 billion × 0.1) on MIM feedstock that year. According to Table 2, feedstock sources were distributed as follows:
• 30% In-house production (A)
• 30% BASF (B)
• 40% Outsourced (C)
The average unit prices of powder, Chinese feedstock, and BASF feedstock (as listed in Table 3) were used to estimate consumption:
In-house produced feedstock
• Total cost: $60 million (30% of $200 million)
• Average powder price: $8.5/kg
• Estimated powder consumption: ~7,000 tonnes ($60 million, $8.5/ kg)
BASF feedstock
• Total cost: $60 million (30% of $200 million)
• Average feedstock price: $12.5/ kg
• Estimated feedstock consumption: ~4,800 tonnes ($60 million, $12.5/kg)
Purchased Chinese feedstock
• Total cost: $80 million (40% of $200 million)
• Average feedstock price: $10/kg
• Estimated feedstock consumption: ~8,000 tonnes ($80 million, $10/kg)
Based on these calculations, BASF is estimated to have sold between 5,000 and 6,000 tonnes of MIM feedstock in the Asian market. Estimating sales for other MIM and CIM feedstocks remains challenging, however, due to customer confidentiality requirements and product functionality differences.
Sectors Categories % Applications
Non-Apple products 16%
Apple products 43% Mobile phones, tablets, laptops, smart wearables, watches, headphones, accessories
Electronics, 3C devices
Automotive
Jigs/fixtures 9% Accessories for the production of electronic goods
Fibre optic communications 4% Heat dissipation and signal processing
ICE 2% Engines & related applications
Interiors 1% Interior fittings and accessories
Electric vehicles 1% Electronic components, wiring fittings
Locks 6% Conventional lock accessories, smart locks
Power tools 5% Gears, transmission, accessories, instruments
Kitchen hardware 5% Kitchen utensils, tools & knives
Tools and hardware
Health and beauty
Hand tools 2% Wrenches, various clamps etc
Sports equipment 1.5% Golf club heads, fishing equipment, arrows, dart heads
Bathroom hardware 1.5% Bathroom fittings
Study & entertainment items 0.5% Stationery, musical instruments, keychains
Medical/surgical devices 2% Minimally invasive surgical tools, accessories & tools
Beauty tools 0.5% Nail clippers, beauty scissors etc
Table 4, which details applications for MIM products, is based on insights gathered from interviews across the Greater China region (Mainland China, Taiwan, and Hong Kong). Distinguishing these highly interconnected markets remains challenging, something made more difficult by the fact that many Metal Injection Moulding companies from Taiwan and Hong Kong have established manufacturing branches in Mainland China.
Material usage remains dominated by the iron-based ‘three brothers’,
a position further strengthened because Apple no longer uses cobalt-chromium-molybdenum alloy (ASTM F75) in MIM products. Tungsten and titanium alloys continue to find applications, while aluminium and copper alloys are slowly beginning to see more prominent use. Nickel-based alloys are rarely used.
Table 5 shows the classification and market share of materials using CIM/MIM across Greater China. In CIM, aluminium oxide structural materials remain the most used. This is followed by iron oxides, which are widely used as an inductive material. Aluminium oxide plays
Iron-based alloys
Non-ferrous alloys
Stainless steel 28% 304L/316L/310/420/440/17-4PH(630)
Iron-nickel alloys 22% Fe-XNi(2, 4, 6, 8, 10, & 50)
Low alloy steel 16% Low alloy steel
High-strength alloys 10% Tool steel/high strength steel
Soft magnetic alloys 6% FeSi3/FeSiCr/FeCo50
Permanent magnets 3% NdFeB
Cobalt alloys 5% ASTM F75/4J29
Refractory metal alloys 4% W/W-Ni-Cu/W-Ni-Fe/W-Cu/Mo-Cu
Titanium and alloys 3% TA1/TA2/TC4
Aluminium alloys 1% 6063
Copper and alloys 1% Cu/CuCr0.3~1.3/Cu-Ni/Cu-C(Diamond/Nanotube)
Nickel and alloys 1% Ni/Inconel 718/ Inconel 713/A286
a key role in the semiconductor industry’s high-temperature fixtures, while other ceramic materials are used mainly in industrial accessories for semiconductors.
dynamics
Growing demand for functional materials
The demand for magnetic materials is increasing daily. In addition to soft magnetic materials (e.g. iron-based
metals and ferrites), high-flux density neodymium iron boron (NdFeB) permanent magnets also leverage PIM technology to produce complex geometric shapes. Anti-magnetic metals and composite materials have also adopted PIM technology.
The use of thermally conductive materials has expanded significantly, primarily driven by the heat-dissipation challenges of fibre optic communication chips. There is also a demand for GPU chips, which include graphics processing chip
“The production of high-strength, lightweight MIM hinges has increased substantially, and these are now being shipped in large quantities (Fig. 2). This is driven by their use in smartphones with foldable screens and tablets, as well as in the automotive industry... ”
units. Materials with high electrical conductivity, thermal conductivity, and/or insulation properties are in demand. These include the addition of diamond or nanocarbon materials to copper to improve thermal performance. These types of complex parts require MIM technology to achieve both intricate geometries and enhanced thermal performance.
Emerging applications and market shifts
The production of high-strength, lightweight MIM hinges has increased substantially, and these are now being shipped in large quantities (Fig. 2). This is driven by their use in smartphones with foldable screens and tablets, as well as in the automotive industry, where traditional dashboards are being replaced by large tablet-style display screens, with foldable screens a potential development. The development of these technologies relies heavily on high-strength MIM materials.
Chinese MIM factories no longer rely on the demand for consumer
electronics applications; instead, they are exploring opportunities to replace conventional casting, precision investment casting, and die casting applications. Even press and sinter PM processes, in particular for stainless steel parts, now face competition from MIM technology. Numerous commonplace metal hardware components are quietly being replaced with MIM products, and components in larger sizes (1001,500 g) are gradually appearing in the market.
Advancing in green PIM technology
I have actively promoted ways to further reduce the environmental impact of MIM technology in China, with one of the most significant successes being the production of stainless steel 304/316 powders (excluding low-carbon variants with C wt.% > 0.03) from scrap. One example involved the sourcing of a relatively large quantity of high-purity scrap from stainless steel processing waste in the Jieyang area of Guangdong Province. This material was atomised into powder for MIM feedstock, reducing costs by over 10% compared to market prices. Although not lowcarbon, parts made from these powders passed stringent salt spray tests. The key is to sinter with rapid cooling to prevent the formation of chromium carbides (Cr26C6 and Cr6C3), which, by depleting grain boundaries of chromium, can cause local corrosion problems.
Additionally, stainless steel 420 scrap from kitchen knife production in Yangjiang were successfully recycled and atomised into powder, then used to manufacture highquality nail clippers via MIM (Fig. 3). Following the MIM process and heat treatment to achieve >HRC 45, these products demonstrate the potential for increasing MIM-based recycling efforts in the future.
The Shanghai research base is actively developing a process for recycling broken glass for PIM applications. PIM technology is already capable of producing complex
“Even press and sinter PM processes, in particular for stainless steel parts, now face competition from MIM technology. Numerous commonplace metal hardware components are quietly being replaced with MIM products.”
geometric products in a translucent ivory-like colour, with transparent recycled glass PIM products expected to be completed next year.
The injection moulding of complex tungsten alloys with extremely fine powders (D99 < 5 μm) is also advancing. Improved powder dispersion technology has enabled successful feedstock produc -
tion. Meanwhile, the feedstock shrinkage ratio has also exceeded the BASF norm (1.165) and moved towards 1.126, indicating a powder loading capacity of 70 vol.%. This pushes the boundaries of moulds and injection moulding processes while maintaining shrinkage control at approximately <12%, which can help more accurately control sintering distortion.
Although the capabilities of PIM factories in China vary significantly, the vast market demand provides multiple opportunities for PIM products across different levels. Of course, progress in this field requires continuing breakthroughs from powder manufacturers alongside ongoing innovation and refinement from equipment manufacturers.
The impact of Apple’s adoption of BASF’s Catamold feedstock into the region cannot be overstated. This standardised feedstock enabled PIM green parts to have high strength, and the rapid acidcatalysed debinding process substantially reduced the challenges of conventional binder technologies. This ensured that brown (i.e. debound) parts more easily retained their shape and size, significantly improving both production efficiency and the precision of finished PIM products.
Following the expiry of BASF’s patent, however, over fifty POM-based
feedstock companies started to supply variants worldwide, the majority of which were sold in the Greater China region. However, there have also been cases of Chinesemade POM-based feedstock being exported to India, South Korea, Japan, Poland, and several Southeast Asian countries. As a result, PIM ‘whole-plant’ technology has also begun to be exported, including powders, feedstocks, and equipment (such as injection moulding machines, debinding furnaces, sintering furnaces, and heat treatment furnaces) [1-2].
Powder consists of a vast number of fine particles whose collective behaviour depends on their fundamental properties. Before proceeding, it is essential to analyse these particles’ fundamental characteristics to understand how they interact and influence POM-based feedstock development. Fortunately, advanced inspection equipment is now available to assess the key characteristics of powder,
often referred to as the ‘4S’ characteristics of size, shape, surface condition, and safety.
POM is a high-molecular-weight polymer that is prone to decomposition during injection or mixing processes. Over the past decade, many MIM operators have voiced their concerns after experiencing issues with its decomposition. When POM breaks down, it turns into gaseous formaldehyde, which not only has an unpleasant odour but may cause explosions if equipment operation errors occur. This is precisely why I emphasise the importance of the final S in the 4S characteristics: safety must always be a top priority.
In September 2023, a fatal explosion took place in Shanghai during an aluminium alloy build at an Additive Manufacturing equipment company. The reason was straightforward: light metals in a highly reactive fine powder form cannot be exposed to air, for example, when operators are opening and replacing the filter element of a Laser Beam Powder Bed Fusion (PBF-LB) machine [3]. Additionally, once ignited, such fires must never be extinguished with
water. This was the cause of a devastating incident that resulted in the loss of four precious young lives, reinforcing the urgent need for comprehensive safety education in powder-forming industries.
One of the most overlooked aspects of powder management is particle size distribution (PSD) analysis. Most studies focus on D10, D50, and D90 values, assuming that controlling these ensures a wellshaped Gaussian distribution and, consequently, high-quality PIM products. However, little attention is given to the extremes – D1-9 and D91-100 – despite academic research emphasising the significance of D97.
In high-volume factory production, this limited focus can lead to critical oversights. During final quality inspections, rust spots are frequently observed on stainless steel 304L and 316L parts, causing them to fail stringent salt-spray tests and corrode severely within 24 h. This issue is largely attributed to the presence of both coarse and ultra-fine powder particles (Fig. 4) [4]. While it is well understood that finer powders in PIM technology enhance density, reduce surface roughness, and improve dimensional accuracy (Fig. 5), academic research methods often fail to fully align with real-world industrial production.
Powders smaller than 10 μm present significant challenges due to their extremely high specific surface area. As these fine powders move through closed systems – such as the barrel and screw of an injection moulding machine – they generate increasing forming pressure and frictional heat. This, in turn, accelerates the decomposition of POM-based feedstock.
In industrial settings, operators frequently rely on high temperatures, pressures, and injection speeds to maximise efficiency. However, this practice has been a primary concern regarding POM-based feedstock over the past decade.
Shape of powder
Fig. 6 illustrates the ideal powder shape, as proposed by Prof Randall
Fig. 6 Left: German’s suggestion for the optimal shape for PIM powder. Right: rice grains, which closely resemble the simulated powder shape. The spherical powder is able to move in more directions than the rice-like powder (Courtesy Prof Randall German)
German in 2007. In fact, the shape of the rice grains we eat in our daily lives is very similar to the optimum powder used in PIM. Rice, a staple food for many Asians, was something I used to buy by measuring it with a cup as a child. I recall that when
loading rice, intentionally tapping the cup on the tabletop allowed more rice to fit inside.
Similarly, powders with a rugby ball-like shape tend to pack more efficiently than those with a spherical shape. The pulling force of the
process causes the long axis of each powder to advance in the same direction. Much like tapping rice into a cup, this alignment increases the packing density of the powder.
Surface conditions of powder
Powder with a rough surface does not necessarily hinder production with POM base feedstocks; instead, it can improve the powder-binder adhesion. Many research papers discuss this, so we will not go into significant detail about the powder’s surface state.
In addition to the high risk of combustion and explosion associated with highly reactive metal powders, powders with small particle sizes also pose a risk of dust inhalation.
Powder technology practitioners need more on-site operators, guidance, and training. Human negligence and disregard may cause many otherwise avoidable accidents, reinforcing the importance of rigorous safety protocols and ongoing education in the industry.
Various polymers can make up POM-based feedstock. As the feedstock compounding process involves the use of heat and pressure with a high-shear blade, high-molecular-weight polymers experience higher temperatures, at which there is a significant risk of thermal decomposition.
“It is essential to understand that the molecular chains of polymers have a limited lifespan, and the number of rotations of the mixing screw can exceed the lifespan of the polymer molecular chain. As a result, POM-based feedstock becomes brittle and prone to decomposition.”
It is essential to understand that the molecular chains of polymers have a limited lifespan, and the number of rotations of the mixing screw can exceed the lifespan of the polymer molecular chain. As a result, POM-based feedstock becomes brittle and prone to decomposition. We can monitor and control this process by combining screw rotations with temperature and pressure control. This allows us to track degradation and estimate how much useful life remains before it becomes ineffective.
When using a feedstock, one of the standard methods for monitoring its performance is to use the ISO 1133-1 standard to measure the melt flow index (MFI) at a loading of 21.6 kg at 190°C [5]. Instead, the testing should be conducted across a temperature range of 170-240°C, with measurements taken every 5°C. The data are shown in the process trend chart in Fig. 7.
We can immediately determine the optimal flowability range for a given batch of POM-based feedstock. Low-temperature and low-pressure injection moulding is the best solution for POM-based feedstock injection moulding operations.
Additionally, we suggest that every batch of recycled sprues undergoes MFI value measurement. You can then narrow down the temperature range between 175°C and 200°C, with readings still taken at every 5°C scale.
It is important to check whether the recycled material’s flow index has fallen below the supplier’s recommended value. For example, BASF Catamold 316L feedstock should have an MFI value greater than 800 g/10 mins. If the value drops below this threshold, it could indicate issues with material degradation, which may affect the overall quality and performance of the final products.
MFI testing equipment is widely used to inspect traditional plastic injection moulding feedstocks. Figs. 7 and 8 show an MFI tester according to international standards: a heated capillary tube measures the weight of POM-based feedstock after it flows through for a fixed period of time, converting this measurement into a value expressed in g/10 minutes.
When applying the mathematical formulas, we can calculate the stress applied during a test. In fig. 8, the thrust applied to the POM-based feedstock is approximately 67.5 MPa, equivalent to the injection pressure of the injection base. This means the MFI tester can effectively simulate injection conditions, providing valuable insight into the feedstock’s flow characteristics before it undergoes the injection moulding process.
1 - Insulation
2 - Removable weight
3 - Piston
4 - Upper reference mark
5 - Lower reference mark
6 - Cylinder
7 - Piston head
8 - Die
9 - Die retaining plate
10 - Insulating plate
11 - Insulation
12 - Temperature sensor
Fig. 8 The detailed structure of an MFI tester with a diameter = 2 mm hole of die
What makes this even more insightful is the ability to observe the surface of the extruded material strip. By examining this, we can assess the quality of the raw material after injection and determine whether recycled feedstock, which has been used multiple times, is still viable for use in the production process. This helps ensure that feedstock maintains its integrity over numerous cycles, ensuring consistent quality in the final product.
Table 6 shows successful POM-based feedstocks based on my 2024 survey. The ‘4S’ of powder affects the material’s oversize shrinkage factor (OSF) ratio value; these characteristics also play a crucial role in determining the OSF ratio of the powder. It is commonly known that the higher the OSF value, the less powder and the more binder is used. Fine powders,
Table 6 Available materials list for POM-based feedstock
due to their higher specific surface area, require more binder to achieve optimal flowability. Therefore, a larger OSF ratio typically results in an increased shrinkage from the green body to the sintered part.
However, the design of OSF requires continuous experimentation, including chemical properties (such as activity and potential difference) and physical properties (such as specific heat capacity and thermal conductivity) of powders. These factors significantly influence the selection of the optimal ratio.
For reference, most POM-based feedstocks use OSF=1.165, which was the standard adopted by early BASF products. Representing the volume of metal powder: volume of binder = 63.2 vol.%:36.8 vol.% [6-7].
The OSF evaluation method is based on the size tolerance range of MIM parts, typically with a linear error of ±0.5%. Therefore, it is marked as OSF = 1.165 ± 0.5%, with a range of 1.165 × 0.005 = 0.005825. According to this calculation, the OSF range is from 1.1592 to 1.1708. Due to variations in the geometric shapes and surface conditions of powders, each feedstock company uses its own set of calculation methods. The quantity of powder is large and difficult to calculate, making it challenging to establish a unified approach.
Conclusion
Since BASF introduced POM-based feedstock, the standard OSF value of 1.165 has remained largely unchanged. However, the future of
POM-based feedstock is clearly moving toward a lower shrinkage ratio (i.e. a lower OSF value). This shift will result in higher powderloading capacity and a reduced amount of binder, allowing for more precise dimensions in MIM parts post-sintering.
While feedstocks with a low OSF value offer advantages, they also present challenges. These materials are often more difficult to mix and inject successfully, and the corresponding moulds require precise adjustments to accommodate the new feedstock’s characteristics.
A deeper understanding of powder characteristics and OSF optimisation will be key to advancing POM-based feedstock, ensuring greater precision, efficiency, and reliability in future manufacturing. To achieve this, I suggest beginning with a focus on powder particle size and shape. Manufacturers and researchers must develop their own feedstock and conduct multiple experiments to drive continuous improvement.
Author
Dr Q (Y H Chiou) You neeD Technical Office chiou55631966@163.com
References
[1] Y.H. Chiou, “Riding the storm: A review of progress in China and Taiwan’s MIM industry during 2020”, M. Powder Injection Molding
International, Vol.15 No.1 (2021), 99-104.
[2] Y.H. Chiou, “What drives the success of an industry: chance or strategy? Lessons from the growth of MIM in China”, M. Powder Injection Molding International, Vol.15 No.4 (2021), 97-102.
[3] THC Childs, Hauser C., Badrossamay M. “Selective laser sintering (melting) of stainless and tool steel powders: experiments and modelling”, Proc. Inst Mech. Eng. B. J. Eng Manuf. J. 219 (4) (2005), 339–357.
[4] R.M. German, ”Powders, Binders and Feedstocks for Powder Injection Molding”, M. Powder Injection Molding International, Vol.1 No.1 (2007), 34~39.
[5] ISO 1133-1, “Plastics -Determination of the melt mass-flow rate (MFR) and melt volume-flow rate (MVR) of thermoplastics.”
[6] X. Kong, T. Barriere*, J.C. Gelin, “Determination of critical and optimal powder loadings for 316L fine stainless-steel feedstocks for micro-powder injection molding”, J. Journal of Materials Processing Technology 212 (2012), 2173–2182.
[7] Y.H. Chiou, “The math in the magic: Calculating the sintering shrinkage of MIM parts”, Injection Molding International Vol.16 No.2, (2022), 97-101.
• Part Design
AND MANUFACTURING
Metals & Alloys • Tooling
Ceramics
• Molding • Hardmaterials
• Debinding
• Binder Technologies
• Sintering • Mixing
• Part Inspection • Mechanical Properties
• Secondary Operations • Standards
• Process Simulation
• Competing Technologies TARGETED AUDIENCE: • Product Designers
• Coatings
Engineers • End Users
Researchers
Students
Manufacturers
Educators
Business Development
Sinter-based Additive Manufacturing has gained significant traction within ASTM’s International Conference on Advanced Manufacturing (ICAM), growing from a niche topic to a major area of discussion. Since its introduction as a dedicated track in 2022, interest in sinter-based AM has expanded rapidly, covering technologies such as Binder Jetting (BJT), Material Extrusion (MEX), Vat Photopolymerisation (VPP), Cold Metal Fusion, and emerging hybrid approaches. In this article, Dr Animesh Bose highlights key presentations and insights from ICAM 2024 that are shaping the future of sinter-based AM.
The evolution of ASTM’s International Conference on Additive Manufacturing
ASTM launched its largest scientific conference in 2016, creating a platform for the exchange of ideas and the transition of research into practical applications. The conference was designed to address the industry’s need for standards, design principles, and the challenges of qualification and certification. The initiative was spearheaded by two young ASTM member volunteers – Nima Shamsaei (E08 and F42 Committee member, now a professor at Auburn University) and Mohsen Seifi (also an E08 and F42 Committee member, now ASTM’s Vice President).
The inaugural event took place in May 2016 as a workshop in San Antonio, Texas, sponsored by ASTM Committee E08 on Fatigue and Fracture. Encouraged by its success, the second event followed in November 2017 in Atlanta, Georgia, co-sponsored by both the E08 Committee and
the F42 Committee on Additive Manufacturing Technologies. The conference continued to expand, with the third event in November 2018, held in Washington, DC, supported by the F42 and E08 Committees as well as the E07 Committee on Nondestructive Testing. This milestone year also marked
the establishment of the ASTM International Additive Manufacturing Center of Excellence (AM CoE).
Building on this momentum, the fourth event (2019) was again held in the Washington, DC, area. In response to the global pandemic, the fifth event, ASTM ICAM 2020, transitioned to a virtual format, taking place from
Technologies’, reviewed here (Courtesy ICAM2024)
“ICAM 2024 was organised by a dedicated team of over 100 scientific committee members, all recognised as advanced manufacturing experts hailing
from sectors including industry, academia, government and regulatory agencies, national labs, and more.”
November 16-20, 2020. Despite the challenges, the enthusiasm for the conference remained strong.
The sixth event (2021), hosted by ASTM International’s AM CoE, was held in person from November 1-5, 2021, in Anaheim, CA. Even under the lingering effects of the pandemic, the conference demonstrated remarkable resilience and continued to grow in significance.
The seventh event, ASTM ICAM 2022, took place from October 31 – November 4, 2022, in Orlando, FL, once again sponsored by the ASTM AM CoE. By 2023 and 2024, the conference had fully recovered, drawing over 1,000 attendees, reaffirming its status as a premier global forum for Additive Manufacturing. With a renewed focus on transitioning research to real-world applications through standardisation, the conference attracted experts from around the world to exchange the latest advancements in the field.
The 2021 edition of ICAM also saw the introduction of a groundbreaking new track: ‘Sinter-Based AM Technologies.’ This initiative was encouraged by ASTM Staff, Richard Huff, and brought to life by a dedicated team of four experts representing different regions:
• Usama Attia (UK)
• Animesh Bose (USA)
• Amy Elliot (USA)
• Benoit Verquin (France)
With the combined network of the co-organisers and strong support from ASTM, the first-ever sinterbased AM track featured a one-day
session with fifteen technical papers, including eight invited speakers. This truly international effort underscored ASTM’s commitment to fostering innovation and expanding the breadth of topics covered at ICAM.
As ASTM’s International Conference on Additive Manufacturing continues to grow, it remains a cornerstone event for advancing the field, uniting researchers, industry leaders, and standards developers to push the boundaries of Additive Manufacturing.
Interestingly, in 2024, the conference title was changed from ASTM International Conference on Additive Manufacturing to ASTM International Conference on Advanced Manufacturing (ASTM ICAM 2024) to broaden its scope and emphasise the importance of manufacturing generally. As ASTM’s ninth annual flagship event, ICAM 2024 focused on standardisation, qualification, and certification, addressing industryspecific requirements across the entire advanced manufacturing process and value chain.
The comprehensive agenda of this conference included over twenty symposia that covered vital topics and key areas in additive and advanced manufacturing. ICAM 2024 was organised by a dedicated team of over 100 scientific committee members, all recog -
nised as advanced manufacturing experts hailing from sectors including industry, academia, government and regulatory agencies, national labs, and more. The sinter-based AM technologies track was classified under the value chain section of the conference, reflecting its growing importance in the industry.
In sinter-based AM processes, part geometry is created separately, followed by densification and property development in a separate step, which is a different approach from most other AM processes. The track abstract highlighted this distinction, emphasising that sinter-based AM processes offer several advantages over fusion-based AM, including improved resolution, superior surface finish, a wider selection of materials, and faster build speeds. These benefits reduce production costs and open up new application opportunities.
Sinter-based AM includes several technologies, as defined in ISO/ASTM 52900: Binder Jetting (BJT), Material Extrusion (MEX), Material Jetting (MJT), and Vat Photopolymerisation (VPP). Furthermore, several emerging sinter-based AM technologies are gaining attention, such as hybrid processes that combine both additive and subtractive techniques, metal Screen Printing, and multi-material Additive Manufacturing.
A unique feature of sinter-based processes is that the powder feedstock is selectively bound together with a binding agent during the build process, forming what is commonly known as a ‘green’ part. Secondary debinding and sintering steps are then required to remove the binding agent and consolidate the powder material to the desired final part density.
As one presentation explained, “While the potential of these new technologies is high, there are still challenges to address in order to achieve the economy and scale these technologies promise.
Standardisation is needed to reach a positive inflection point in industry adoption.”
As stated, the conference track has grown significantly to a point where it would not be possible to cover the scope within this article. It was a challenge to pick and choose which presentations to cover here. Numerous presentations that were interesting and valuable could not be covered due to space restrictions. However, this article will focus on a select few that made a significant impact on the conference.
Binder Jetting, which has gained significant traction over the past five years and is currently in widespread commercial use, naturally gained significant attention within the sinter-based AM conference track. Approximately half of the presentations were connected to Binder Jetting.
Modelling and experimental validation
The growing significance of Binder Jetting within sinter-based AM is further highlighted by several papers focusing on modelling as well as experimental validation. One notable presentation, titled ‘An Experimentally-Validated Multiphysics, Fluid-Particle Interaction Modelling Framework for
“...the author presented detailed studies on the spreadability of different powders, offering valuable insights into how powder characteristics influence the BJT process...”
Binder Jet 3D Printing’, was delivered by C Fred Higgs III from Rice University.
According to Higgs, Binder Jetting, when compared to other AM processes such as Laser Beam Powder Bed Fusion (PBF-LB), offers advantages such as faster build rates, lower costs, and a broader selection of materials. However, despite these advantages, BJT parts generally exhibit inferior mechanical properties, dimensional accuracy, and repeatability – factors that limit the technology’s adoption in high-performance sectors such as aerospace and defence. According to the presentation, developments in this area are primarily dependent on experimental approaches, which limit the direct observation of the fundamental phenomena due to certain physical constraints. This, in turn, leads to an incomplete understanding of the underlying physics of the process.
To address this gap, Higgs introduced a multi-physics, high-
performance computational modelling approach for BJT. This approach integrates a computational fluid dynamics (CFD) solver based on the volumeof-fluid (VOF) method to simulate liquid binder behaviour and a discrete element method (DEM) to model the powder particle dynamics in the powder bed.
The presentation also delved into the first experimentally validated interfacial fluid-particle interaction simulations of the BJT droplet process. Additionally, the author presented detailed studies on the spreadability of different powders, offering valuable insights into how powder characteristics influence the BJT process, and providing a glimpse into the multi-physics fluid-particle interaction in the BJT process.
Simulation and validation of sintering distortions
In his presentation ‘Simulation and Experimental Variation of Sintered 316L Pipe Tee Connectors Printed by Binder Jetting Additive
Numerical Modeling and Simulation.’ In Binder Jetting, similar to most sinter-based AM processes, the final shape differs significantly from the as-built geometric shape due to shrinkage during sintering. Sintering shrinkage of around 15% or more is common with binder jetted AM parts due to their low green density.
Manufacturing’, Eugene Olevsky (San Diego State University) addressed the challenges associated with sintering in AM.
Olevsky explained that, ideally, the sintering of green components should result in uniform shrinkage and the retention of the original shape. However, in practice, factors such as temperature non-uniformity, external friction forces, and gravity can lead to inhomogeneous densification, causing distortions in the final component geometry. These challenges are particularly relevant to parts produced using sinter-based AM technologies such as Binder Jetting.
Olevsky highlighted the importance of understanding the sintering process and the factors influencing it to develop reliable modelling tools that can predict the resulting shapes and properties of sintered components. In this paper, the aim was to assess the accuracy and limitations of a continuum mechanics-based model in predicting gravity-induced distortions during sintering.
For his study, three connector (Tee pipe) geometries were designed, including horizontal and vertical tubes of different sizes. The parts were first debound at 640°C in air, and sintering was carried out at
1,375°C for 210 minutes in a hydrogen atmosphere. Some actual samples were fabricated to validate the model, and the numerical predictions were compared with actual measurements of the sintered shape.
The results of the study led to the development of a model based on continuum sintering theory that accounts for the effects of gravity and the formation of delta-ferrite during the sintering process. The model effectively estimates gravity-induced deformation of the stainless-steel material behaviour at high sintering temperatures. In general, simulations captured the deformation interaction of the different vertical and horizontal cylinder’s geometrical features.
Two strategies for mitigating distortion were explored: rotational sintering and the pre-deformed geometry approach. Both showed potential for achieving the nominal final shape, with experimental validation to be conducted in future work.
Basil Paudel from Ansys presented a paper on the simulation and modelling of sintering in Binder Jetting: ‘Improving Geometric Accuracy in Sintering-Based Manufacturing via
Additionally, distortions can be associated with gravity-induced warpages in unsupported overhanging regions, introducing nonlinearities that render simple scaling-based compensation methods ineffective. To address these challenges, Paudel and colleagues proposed a generalised sintering model, which was implemented in Ansys. The model used a guided calibration workflow to predict sintering distortion, accounting for gravityinduced warping and frictional effects. The model was also designed to predict instantaneous relative density, microstructural grain size, and other relevant sintering parameters. These predictions would provide valuable insights for process engineering and the design of sintering cycles.
A significant challenge in Binder Jetting is the variability of green density in fabricated parts, particularly in larger builds. The compaction process often leads to a spatially varying green density, which exacerbates issues such as distortion during sintering. Live setters were shown to improve prediction accuracy by reducing gravity-induced warpage and mitigating potential distortion caused by friction.
Experimental results presented in the paper showed that the predictions align closely with the desired target within a 3% margin. The authors also indicated that ongoing work explores how varying green density could further improve distortion compensation.
In their paper, ‘Designing Distortion Compensation and Setters of Binder Jet-Printed Parts’, Andreas Vlahinos from Advanced Engineering Solutions
and Sunil Acharya from Ansys discuss the challenges posed by the significant shrinkage (22%) of parts that occur during the sintering of BJT parts. This shrinkage can cause distortion in the as-sintered parts due to factors such as evaporation of the binder, elimination of any pores left from the binder, thermal strain, friction with the build plate, and gravity.
To address these shrinkage and distortion issues, the authors propose several solutions, including geometric compensation through orthotropic scaling of the green part in the x, y, and z directions (i.e. 18%, 18%, 20%). They also suggest reversing the deformation of unsupported regions, such as overhangs greater than 15 mm, or using sintering setters, which are additional parts made of the same material placed underneath unsupported regions of the central part to prevent sagging and other deformations.
The presentation provided an excellent overview of design strategies, the process of designing the green part and sintering setters using a parametric CAD machine and manufacturing simulation software. To illustrate these methods, the Binder Jetting process and the use of the above tools were demonstrated using an actual AM part.
Powder structure evolution and the importance of powder uniformity
Nathan Crane and colleagues from Brigham Young University presented a study on powder structure evolution during the Binder Jetting process. Their paper, titled ‘Towards Understanding Powder Structure Evolution during Binder Jet Printing’, discussed the effects of manufacturing simple geometries and inspecting the resulting parts, as well as performing in-situ synchrotron imaging of the build process under realistic conditions.
The density and uniformity of the powder bed heavily influence the quality of Binder Jetting parts. Previous investigations on powder bed spreading did not consider the
“Previous investigations on powder bed spreading did not consider the effects of the jetting process itself. However, recent observations and synchrotron imaging have shown that this process can disrupt the powder bed, leading to part defects and variations in density.”
effects of the jetting process itself. However, recent observations and synchrotron imaging have shown that this process can disrupt the powder bed, leading to part defects and variations in density. Their results reveal that both saturation and powder disruption (measured by surface roughness) are dependent on several factors, such as droplet size, velocity, printing frequency, and geometry. Synchrotron imaging demonstrates that the presence of binder in the powder bed from prior lines or close droplet spacing reduces powder ejection and limits the depth of powder rearrangement.
Interestingly, both laboratory and synchrotron imaging experiments showed that adding small amounts of moisture to the powder bed can reduce powder relocation without negatively impacting the part’s saturation levels. By carefully selecting the right fluids, stable builds can be achieved at higher rates, enhancing productivity.
The authors conclude that in the BJT process, the powder properties change during the build process, even in relatively dense powder beds. This insight opens up new strategies to optimise Binder Jetting for various materials, particularly metals and alloys. Several other presentations during the sinter-based AM track at the ASTM ICAM 2024 conference also highlighted the versatility of BJT in fabricating a wide range of ceramics, metals, and alloys.
Mohammad Pourshams et al. from the University of Toledo described the Binder Jetting of NiTi shape memory alloys, which are difficult to process using conventional AM methods such as PBF-LB. Binder Jetting was able to overcome problems associated with melting and solidification during the PBF-LB process. This significantly improves the reliability and isotropic properties of materials, along with precise control over microstructural and mechanical properties through customised sinter and binder compositions. These attributes make the Binder Jetting process suitable for large-scale production.
When produced by BJT, NiTi alloys – intrinsically superelastic and with good shape memory – offer significant potential in demanding applications such as robotics, aerospace, automotive, and durable medical implants.
Pourshams’ presentation focused on refining the mechanical properties of binder jetted NiTi components using advanced analytical techniques such as thermogravimetric analysis (TGA), differential scanning calorimetry (DSC), X-ray diffraction (XRD), electron backscatter diffraction (EBSD), and energy-dispersive X-ray spectroscopy (EDS). These have led to the development of optimised heat treatments to fine-tune phase composition and improve the mechanical integrity of sintered parts.
and nuclear fuel methods
Andrew Nelson from ORNL presented an insightful paper titled ‘Applications and Progress in Use of Additive Manufacturing for Ceramic Nuclear Fuels.’ According to the author, the fabrication of such fuels requires the use of new manufacturing processes.
The presentation provided an overview of the ongoing research activities with examples of contemporary processing methods of interest to the community, including:
• Binder Jetting for ceramic nuclear fuel fabrication
• Vapour phase infiltration of carbide matrix particle fuel forms
• Optimisation of direct ink writing for fabricating heterogeneous architectures
• Actinide feedstock synthesis routes tailored to the unique challenges of oxide, carbide, and nitride nuclear fuel forms
Upcycling glass waste
Binder Jetting of waste glass was discussed in an interesting presentation given by Arish Dasan from the University of Trenčín – Centre for Functional and Surface Functionalized Glass (FunGlass) with several co-authors from the University of Padua. The presentation was titled ‘Upcycling of Glass Waste by Binder Jetting 3D Printing Technology: A Sustainable Approach’, and it highlights the ability of the process to fabricate unusual materials such as glass.
The paper investigated the feasibility of the BJT process in upcycling glass waste into value-added products. To demonstrate the feasibility, waste green glass sourced from JM-GLASS, s.r.o., Slovakia, was used in the experiments. The team carried out the AM process by mixing glass powder with a binder and using it in the powder bed. They applied a greensolvent-based liquid as the binding agent, spraying it on the powder bed. The BJT machine used was Voxeljet VX200.
To study the impact of the build process on microstructure and mechanical properties, the role of various process parameters, such as the layer thickness, build speed, the effect of solvents, binder ratio, and post-processing methods, were analysed and discussed. The samples fabricated exhibited a dimensional accuracy greater than 95% along with appreciable green strength, highlighting the potential for its use in diverse applications such as construction and architectural components, photocatalytic supports, filters, and membranes. These findings demonstrate the potential of Binder Jetting to contribute to sustainable glass recycling, with promising applications in industries that require high-precision, functional materials.
The AM community has always been highly attracted to the Binder Jetting
of aluminium and aluminium-based alloys due to their low density, high thermal conductivity, and relatively low cost. Melt-based processes have extensively used aluminium and aluminium-based alloys. However, despite their potential, their use in Binder Jetting has been limited due to the challenges associated with sintering this class of material.
Reducing sintering deformation of aluminium
‘Material and Process Optimization of Binder-Jetting to Reduce Sintering Deformation of Aluminum’, by Takafumi Sasaki and Daichi Yamaguchi, both from Ricoh, focused on the processing of this challenging material and discussed the latest developments in reducing sinter deformation during the manufacturing of aluminium components using BJT. Aluminium is one of the materials of focus for Binder Jetting due to its suitability for applications such as thermal management and its ability to be lightweight when designing for Additive Manufacturing.
The authors outlined the difficulties associated with the consolidation of aluminium alloys with sintering. Some of the problems include:
Oxide layer formation
Aluminium powder is highly active and readily forms an oxide layer with a melting point of over 2,000°C. This layer must be broken up to enable sintering.
Melting point constraints
Aluminium itself has a much lower melting point (around 600°C), meaning the sintering temperature cannot be raised enough to melt the oxide layer without fully melting the aluminium, making shape retention impossible.
Liquid phase sintering challenges
Aluminium is typically sintered using liquid phase sintering, which causes greater deformation compared to the solid phase sintering used for materials such as stainless steel or titanium.
To overcome this issue, Ricoh is taking a multi-pronged approach that includes developing materials such as powders and binders, process developments such as build, debinding, and sintering parameters, and component design to minimise and anticipate deformation. As a result, sinter deformation has been significantly reduced.
Key strategies discussed by the authors include the manipulation of the powder particle size distribution, the use of some eutectic liquid phase formation, the use of some impurities (which were, understandably, not disclosed during the presentation) and some bonding strategies. The necessary liquid mass for sintering is around 20-30%, with the combination of pure aluminium and eutectic aluminium helping; the larger pure aluminium powder particles can be a part of the rigid skeleton resisting deformation to some extent while the eutectic aluminium can form the liquid to promote sintering.
As with all AM processes, the part cost of components manufactured with this technology is often higher than those manufactured by conventional methods. However, there are some examples of its use in full-scale mass production. The authors hope to overcome this barrier by applying life cycle assessment and life cycle cost analysis methods to AM.
Nicholas Murphy from Kymera International gave another presentation on Binder Jetting of aluminium alloys titled ‘Advancements in Sintering and Distortion for Mass Production of Binder Jet Aluminum
6061.’ Their work was carried out on an ExOne Innovent BJT machine that featured an enclosed glovebox for the safe handling of reactive powders such as aluminium alloys.
Murphy acknowledged that though aluminium Binder Jetting shows excellent potential for highthroughput part manufacturing, many challenges remain in bringing the process to a state of mass production readiness. The study focused on using a continuous belt furnace to sinter BJT aluminium 6061 material in a nitrogen atmosphere.
The investigation outlined the factors that affect the distortion of aluminium BJT parts to control distortion behaviour. The author concluded that consistency between sintering runs remained elusive. Further research will focus on optimising sintering conditions, including cycle speed, length, heating and cooling rates, and gas flow rates.
Matthew Guile from Azoth presented an insightful investigation resulting from a collaboration between Azoth, Lehigh University and Quintus Technologies. The presentation was titled ‘Hot Isostatic Pressing of Additive and Micro-Additive Manufactured 316L Stainless Steel via Metal Binder Jetting and Metal Material Jetting’.
Hot Isostatic Pressing (HIP) is a post-process heat treatment primarily used to improve density and mechanical properties in metal components. Many industries, including aerospace, automotive, and
“Murphy acknowledged that though aluminium Binder Jetting shows excellent potential for high-throughput part manufacturing, many challenges remain in bringing the process to a state of mass production readiness.”
healthcare, widely use HIP as part of their manufacturing processes.
Modern HIP equipment has ushered in rapid cooling or quenching within the HIP process, which allows for better microstructural control within a single-step process. In the past few years, sinter-based AM, especially BJT,
has continued to grow in popularity due to its cost efficiency, medium-to-large-scale production, and a diverse range of available metal powders. However, another sinter-based AM technology that has shown some promise in small component manufacturing is Material Jetting.
The team designed an experimental matrix for the HIP of 316L stainless steel manufactured using both Binder Jetting and Material Jetting, consisting of three temperatures of 1,000, 1,150, and 1,250 ° C and pressures of 100, 140, and 207 MPa. To analyse the results, scanning electron microscopy
Improvement of density after HIP (from ∼ 96% to >99%)
Reduction in δ -Fe Ferrite phase: 1250°C > 1150°C > 1000°C
Changing in δ -Fe morphology (lath to spherical) and location (from grain boundary to within grain)
(SEM) and scanning transmission electron microscopy (STEM) were used to characterise the resulting microstructures following each processing condition, including microstructural phases, defects, inclusions, and their morphologies. Bulk density was also measured to determine the effectiveness of HIP parameters, while tensile properties and microhardness were measured to assess their mechanical performance.
Fig. 7 shows the microstructures of BJT parts sintered and HIPed at various conditions. Table 1 shows the conclusions drawn from Binder Jetting and Material Jetting combined with HIP.
Binder Jetting of high-alloyed steels: innovations in tooling Simon Höges from GKN Additive presented the successful use of BJT high-alloyed steels in his presentation titled ‘Binder Jetting of High Alloyed Steels –Advancements in Tooling’. Höges highlighted that AM is being increasingly used in the tooling industry, particularly to produce injection moulding tools with conformal cooling channels. The
Improvement in density after HIP from ~96% to > 99%
Change in grain size and morphology after HIP
Presence of δ -Ferrite phase due to sintering temperature but decreases with heat treatment
Medium strength / High toughness tensile properties
Little improvement in density after HIP from ~98% to ~99%
No change in grain size or morphology after HIP
Presence of Mn-/Cr-rich and Si-rich oxides due to fabrication method
Medium-High strength / Low toughness tensile properties
Table 1 Conclusions from the Metal Binder Jetting and Metal Material Jetting combined with HIP (Courtesy Matthew Guile, ICAM 2024)
“Höges highlighted that AM is being increasingly used in the tooling industry, particularly to produce injection moulding tools with conformal cooling channels. The design freedom offered by AM enables significant improvements in heat management...”
design freedom offered by AM enables significant improvements in heat management; conformal cooling is expected to have a considerable impact on production yield and moulding cycle times.
Binder Jetting combines efficient build processes and consolidation through sintering, bringinga wide variety of hard-toweld materials to the forefront.
Fig. 8 shows a schematic of the BJT process, and Fig. 9 shows a schematic that outlines some of the application zones occupied by various metal shaping processes, including Binder Jetting.
Höges’ presentation addressed multiple tool steels, such as M2, H13, and S7, along with their application in different tooling industries. Table 2 shows the results of BJT processing of M2 tool steel, and Fig. 10 displays a microstructure of the M2 tool steel. Fig. 11 shows complex geometries produced by BJT-processed hard and nonweldable M2 tool steel. According to Höges, BJT offers a better economic solution compared to PBF-LB, especially when larger volumes of parts are concerned.
10
of
processed
tool steel along with EDS-maps showing the fine distribution of tungsten and vanadium carbides (Courtesy Simon
Key powder considerations for mass production
Another paper on Binder Jetting, presented by Mukund B Nagaraj from Indo-MIM, was titled ‘Key Considerations in Powder Parameters for Mass Production of Binder Jet 3D Printed (BJT) Components’. One key point of interest was the use of a special custom-made grade powder developed by the company for BJT. The presentation outlines the differences between the custommade grade 316L powder and
the standard powder for Binder Jetting. Table 3 outlines some of the characteristics of the two powders used in the presentation.
The Indo-MIM custom-made powder exhibited a significantly higher packing density compared to
Fig. 11 Complex geometries produced by BJT-processed hard and non-weldable M2 tool steel (Courtesy Simon Höges, ICAM 2024)
the standard BJT powder, shown in Fig. 12. As a result, the new powder’s shrinkage is significantly lower, as seen in Fig. 13, which shows the oversize factor analysis of the two powders – an indicator of shrinkage. The lower shrinkage
of the two powders
Mukund B Nagaraj, ICAM 2024)
translates into lower distortion and better shape retention with the Indo-MIM custom-made powder, as shown in Fig. 14.
Another paper, ‘Metal Powders for Sinter-Based Technologies’ by Rohit Reddy from Endeavor 3D, discussed the necessary steps to qualify and produce parts with a new metal powder. In the area of spares, repairs, and replacement parts, Reddy spoke about the processing of a wheel hub replacement part made from 17-4 PH stainless steel. Table 4 shows the details of the product. According to the authors, some of the best practices in powders included the following:
• Storing powders in a controlled environment to prevent contamination and corrosion
• Testing material flow and powder morphology regularly
• Eliminating cross-contamination from depowdering equipment
• Baking and sieving powder between jobs to remove contaminants and residual binder
• Tracking powder usage with lifecycle management
The best practices in sintering include:
• Preventing material and supply cross-contamination
• Calibrating furnace temperatures for consistency
• Designing setters using Design for AM (DfAM) for optimal sintering
• Following safety protocols
• Paying attention to safety considerations
• Tracking data for quality assurance
Fig. 15 shows a wheel hub replacement part that the company is producing. The author concludes that BJT is best positioned as a casting alternative for on-demand
spares and repairs and is arguably the most scalable metal AM technology. Success in AM requires a commitment to quality assurance and testing.
Several other presentations, made by different organisations, covered other areas of the Binder Jetting process. Three of those dealt with overcoming issues of part production.
Production-ready metal BJT
Ross Adams from Markforged presented one key approach to overcoming these part production challenges in his presentation ‘Production-Ready Metal Binder Jetting through Precision Machine Designed Printer’. By focusing on precision engineering, Adams explained how precision engineering not only prioritises quality, reliability, and repeatability but also serves as a cornerstone for seamless production operations.
By operationalising metal Binder Jetting through an investment in a robust platform, manufacturers can achieve heightened uptime, increased yield, and prolonged operational longevity – essential factors for contracted serial production. The presentation discussed how precision machine design can significantly enhance the efficiency and viability of metal Binder Jetting processes across a wide range of industries.
A paper that also dealt with mass production using Binder Jetting was from Eaton Corporation and presented by Jinjie Shi. The presentation was entitled ‘Challenges and Approach to Turn Binder Jet from Prototype into Mass Production’. The author mentioned that the tremendous amount of effort in developing BJT applications was mainly devoted to prototype demonstration, with only a few successes in mass production. The key challenge is how to control the long-term process capability of the Binder Jetting lifecycle to deliver parts
with repeatable geometry and material properties. The presentation outlined the key approaches to overcome the challenge of turning binder jetted components from prototype into mass production.
HP’s approach to scalable Binder Jetting production
Brett Harris gave another presentation dealing with production using Binder Jetting from HP entitled ‘HP Metal Jet S100: Adoption to Production Solution’. The presentation discussed the benefits of HP Metal Jet manufacturing solutions, which include its robust architecture design, its complete powder and parts handling modules, the predictable part quality performance for a variety of production types and the overall operating efficiency of the equipment. The speaker also examined a range of industrial application cases.
The presentation considered the issue of reliable part quality using key metrics known as Overall Equipment Efficiency (OEE) and Overall Operational Efficiency (OOE). Fig. 16 schematically shows some of
the factors that affect OEE and OOE. Fig. 17 shows the laboratory analyses carried out, starting with the powder feedstock through to the green part and the finished part. The overall presentation focused on building a credible ecosystem by offering solutions to various stages of the Binder Jetting process, from raw materials to post-processing.
Though Binder Jetting has established itself as the sinter-based AM technique capable of moderate to high volume production of complex shaped parts in an economical manner (as evidenced by roughly half
of the presentations in the sinterbased AM track being on Binder Jetting), there are numerous other sinter-based AM processes at various stages of development. Some hybrid processes modify the BJT process, while others differ entirely. It would not be possible to cover all the different sinter-based AM processes covered in this conference track, but we will focus on a few selected presentations.
Amy Elliott, from Oak Ridge National Laboratory (ORNL), gave an interesting presentation on sinter-based AM processing. The presentation, entitled ‘Multi-Material Additive Manufacturing for Sinterable Materials’, discussed the Binder Jetting of multi-material, with an example of this shown in Fig. 18. Fig. 19 shows examples of three types of multi-material layup structures (crossed-lamellar, brickand-mortar, and Boulingand) and their tensile stress-strain curves, failure modes, and fracture surfaces. In her presentation, co-firing or co-sintering multi-materials was
extensively discussed, along with the challenges. As a way of overcoming some of the co-sintering challenges, Elliott mentioned Spark Plasma Sintering (SPS) as one of the processes that could enable multimaterial AM processing to overcome the sintering challenges. Some of the advantages mentioned include:
• Reduced sintering time and thermal gradients
• Reduced sintering temperatures (reduces thermal expansion)
• Added pressure avoids tensionbased tearing
• Provides more control over heating/cooling rates to synchronise shrinking behaviour
• Yields smaller, more uniform grain size (large grains shrink at different rates than small grains)
Fig. 20 shows some examples of near-net-shaped BJT parts combined with SPS consolidation (the part on the right was a collaboration effort with San Diego State University).
Fabrication of powder components for advanced applications
Olevsky gave another presentation titled ‘Additive Manufacturing and Spark Plasma Sintering: Fabrication of Powder Components for Advanced Applications’, in which he described
a novel method that combines the Additive Manufacturing technique of solvent jetting and Spark Plasma Sintering (SPS) to produce complex ceramic and metallic parts for advanced applications such as biomedicals and optical components. This innovative net shaping approach synergistically combines the capabilities of AM and SPS to produce complex-shaped components with internal channels.
According to Olevsky, along with geometric customisation of the additively manufactured mould, this process offers a significant advantage by drastically reducing debinding time compared to other AM methods. In the presentation,
he described how they processed high-density ceramics (alumina, hydroxyapatite, and tungsten carbide) and metallic (stainless steel 316L) complex-shaped parts with internal channels, successfully fabricating them to near theoretical densities.
The studies conducted include the development of a model (based on the continuum theory of sintering formulations embedded in a finite element code) capable of predicting the evolution and/or distortions of the complex-shaped powder assembly during the consolidation process.
Material Extrusion and VAT Photopolymerisation
A presentation by Animesh Bose (yours truly) from AMfgLabs LLC, ‘Select Case Studies on Material Extrusion and Vat Photopolymerisation-based Metal AM Processes’, described several of the metal AM technologies (shown in Fig. 21) and then explained in more detail the process and some applications of Material Extrusion and Vat Photopolymerisation. Both processes have similarities with the well-established Powder Injection Moulding process, with MEX being similar, except for the green part
“The studies conducted include the development of a model (based on the continuum theory of sintering formulations embedded in a finite element code) capable of predicting the evolution and/or distortions of the complex-shaped powder assembly during the consolidation process.”
forming process. Fig. 22 shows the schematic of three different MEX material delivery types based on (a) filament-based; (b) rod-based; and (c) pellet-based feedstocks.
Filament-based feedstock
The filament-based feedstock is a process where a feedstock based on a metal powder and binder mix (such as a MIM feedstock) is fabricated into a precise diameter filament that is then coiled onto a spool. The material for extrusion is supplied as a filament that is fed to the heated section of the extruder using wheels that have tiny gear-like teeth.
Rod-based
In this case, the MIM-like feedstock is formed into precision rods (typically with a diameter of 6 mm and length of 150 mm). The rod is pushed toward the heated section of the nozzle for extrusion using a finger-like device that pushes down on the cold end of the rod. Desktop Metal uses this process, which is known as Bound Metal Deposition (BMD).
Proprietary extrusion screw & barrel
Barrel & screw profile adapted to microextrusion for 3D printing application (low residence time to avoid material degradation)
Proprietary extrusion die
Compatible with different alloys and nozzle sizes (up to ⌀ 3.00mm) to fit the required specifications (resolution, abrasive & filled materials, etc.)
Material cartridge
Contains ±1L of pellets, refillable , including a configurable feeder to optimise the material entry flow
Thermal control
Three thermal control points per extruder to ensure a good material processability. Heating parameters are open to the user
Fig. 22 Schematic of three different MEX feedstock types: (a) filament-based; (b) rod-based; and (c) pellet-based (Courtesy Animesh Bose ICAM 2024)
Pellet-based feedstocks
In the last case, the MIM-like feedstock in the form of pellets is fed into a hopper through which the feedstock pellets are fed into a proprietary extrusion screw and barrel that forces the pelletised feedstock through a heated die and is extruded to form the part. This is a process developed by the company, Pollen. In another version of pelletised feedstock extrusion,
“...the MIM-like feedstock in the form of pellets is fed into a hopper through which the feedstock pellets are fed into a proprietary extrusion screw and barrel that forces the pelletised feedstock through a heated die and is extruded to form the part.”
23 As-built and as-sintered hardmetal parts fabricated by MEX. Left: Green, as-built part. Right: Sintered hardmetal part (As published in W. Lengauer et al., Fabrication and properties of extrusion-based additively manufactured hardmetal and cermet components. International Journal of Refractory Metals and Hard Materials 2019;82:141–9)
25 For total
fabricated
the
process with Hydroxyapatite / TCP provides an innovative solution. The combination of resorbable material and defined macroporous geometries enables cell ingrowth and, consequently, both new vessel and bone regeneration (Courtesy Lizoth)
the extrusion is carried out using a plunger that forces the material out through a heated die to result in the desired extrudate; this process is used by AIMD3D, Germany. Fig. 23
shows the as-built and as-sintered hardmetal part fabricated by MEX.
Fig. 24 shows a picture of a copper heat exchanger used in chemical processing fabricated by the bound
metal deposition process. The part also included a cooling channel, as shown on the right side of the figure.
VAT Photopolymerisation and lithography-based processing
The presentation also discussed the process of VAT Photopolymerisation or lithography-based processing of both metals and ceramics.
One of the companies using the Lithography-based process is Lithoz. In their process, once the digital file is in the machine, metal or ceramic slurry is automatically dispensed into a vat. The build platform is then dipped into the slurry, which is exposed to light from below. This cures the entire surface of a layer at once (where the light shines), considerably speeding up the process compared to laser-based technologies. After the parts are built up, they undergo a debinding and sintering process to yield fully dense and high-performance additively manufactured parts. With Lithoz’s new multi-material AM technology, AM is not restricted to single-phase materials.
The CeraFab Multi 2M30 uses the full capability of AM to enable the combined processing of different materials, such as ceramics, metals and polymers, and their properties in one single component. Fig. 25 shows a ceramic component fabricated using the Lithoz process. Incus, an evolution of Lithoz, has introduced a new series of metal AM technology capable of producing metal parts with excellent surface quality and high reproducibility.
Bose also addressed another lithographic process used exclusively for metals developed by Incus. The company’s AM machines fabricate green parts from a photoreactive, metal-filled feedstock using a highperformance projector, resulting in accurate and precise green parts similar to parts fabricated by Metal Injection Moulding. Similarly to MIM parts, they require a debinding and sintering process to yield the final metallic properties.
In this case, the light exposure is from the top (unlike the Lithoz
process, where it is from the bottom). Metallic parts with excellent resolution can be achieved by this process, as shown in Fig. 26, which shows some cell phone components made by this process.
Biomedical advances
A presentation by György Harakály from Incus also discussed the Incus process in more detail in his presentation ‘Recent Advances in the Biomedical Field with the Lithography-Based Metal Manufacturing Process.’ His presentation delved into recent advances in the biomedical field, highlighting examples of applications in dentistry and surgical tools. Fig. 27 shows some small parts made from titanium (left) and 316L (right). The picture on the right shows 316L as-sintered micro-parts measuring 3.7 mm x 1.2 mm x 0.8 mm; when the pieces are combined, the total weight is 9 mg.
Cold Metal Fusion
Christian Fischer from Headmade Materials presented a relatively novel process known as Cold Metal Fusion in ‘The Power of Cold Metal Fusion’. The process involves the use of relatively fine feedstock made using a mix of organic binder with metal or alloy powder (such as MIM feedstock). The feedstock is formed into fine particulates that can be spread
on a powder bed (like the powder bed used in binder jets). A laser beam then exposes the spread powder layer, similar to polymer PBF-LB. The laser melts the organic binder in the powder particles, causing the powders to stick together only in the areas exposed to the laser.
After the full bed of parts has been fabricated, the supporting loose powder is separated from the parts. The parts are quite strong and can even be cleaned by water jet processing. After the powder is removed and the parts cleaned, further processing of the as-built
SLS-Printing
“By leveraging proven equipment and market-available know-how, CMF simplifies the step into industrial series production, enabling outputs in double-digit tonnes per year with just one AM machine.”
green parts can also be done (as these green parts are quite strong). The green parts can then be subjected to a solvent debinding step, like MIM, where part of the organic binder is removed. After solvent debinding, the parts are moved to the sintering furnace, where they are sintered to near full density.
Post-sinter finishing operations can also be carried out. Fig. 28 shows the general processing steps of this Cold Metal Fusion (CMF) process.
Fig. 29 shows the AutoSmooth feature of the processing, which would result in mass-finished sintered parts with a better surface finish. The removal of the step effects using the AutoSmooth process results in a better surface finish after the mass finishing step. Fig. 30 shows a pump impeller made by the CMF process.
According to Fischer, the transition from prototyping and small-series manufacturing to industrial series production can be achieved through the CMF process. By leveraging proven equipment and market-available know-how, CMF simplifies the step into industrial series production, enabling outputs in double-digit tonnes per year with just one AM machine.
This integration of AM’s flexibility with the scalability of the sintering
process marks a significant advancement in industrial AM. Thus, Cold Metal Fusion combines AM flexibility with the maturity and scalability of the sintering process, resulting in a solution that enables the rise of industrial AM.
Another interesting presentation that delved into the binders for sinterbased AM processing was given by Dustin Gilmer from the University of Tennessee Space Institute, entitled ‘A Review of Binders and their Importance for Bind and Sinter Additive Manufacturing’. In the presentation, Gilmer covered a wide range of binders and their uses in sinterbased AM processes.
The author’s conclusion was that binder chemistry is a key to sinterbased AM processes; improved part properties and processing can be achieved by tuning the binder chemistry, and every sinter-based AM process has its unique binder needs. In his presentation, Gilmer pointed out that various binders serve different purposes in the wide variety of sinter-based AM processes. As an example, he has discussed the importance of lubricants that can improve the flow and extrusion properties with smooth extrusion and consistent flow that can improve the overall quality of the build. The use of lubricants can also help increase the solids loading.
Mahmood Shirooyeh from 3DEO presented a process that is somewhat similar to Binder Jetting but is different in several key aspects in his presentation ‘Sinter-Based Additive Manufacturing of Copper’.
In the 3DEO process, the binder is sprayed over the full layer of the powder bed (after the powder is spread), and a tiny, pre-programmed cutting tool then goes over and machines the part in the desired areas. In the presentation, the
250 mm and larger
Uniform surface quality
powder used was a commercial gasatomised Cu powder with:
• Particle size distribution of D50 ~ 10 μ m / D90 ~ 20 μ m
• An apparent density of 4.03 g/cm 3 (45 TD%)
• A tap density of 5.03 g/cm 3 (56 TD%)
Performance metals
Fig. 31 shows an SEM image of the morphology of the powder used in this investigation. For the build, a 3DEO Saffron machine was used to manufacture the pure Cu coupons. The layer thickness was 100 μ m, creating twelve coupons per run (size 6.35 x 30.00 x 30.00 mm).
Table 6 presents the tensile properties of the as-sintered and HIPed copper parts, showing that the UTS and elongation were increased when the parts were subjected to post-sinter HIPing.
Stefan Joens, DSH Technologies, presented on ‘Principles for Success with Sinter-Based Metal AM’. Joens outlined a roadmap for successfully producing parts with sinter-based AM. The key takeaways from the presentation include:
Part design considerations
Emphasising the importance of design in the success of sinter-based AM processes
Customer communication
Stressing the need for early discussions with customers to align expectations and design constraints
Table 5 Density and electrical conductivity of the as-sintered and HIPed copper parts (Courtesy Mahmood
Sintering was carried out at 1,075°C for 3 h using a H 2 partial pressure. The sintered samples were subjected to HIP using a temperature of ~950°C (1,750°F), a pressure of ~100 MPa (14,750 psi), and a hold time of 3 h. The HIP atmosphere used was high-purity argon gas. The microstructure of the sintered and HIPed copper parts is shown in Fig. 32. The as-sintered grain size is around 50-70 μm, and shows anneal twinning, incomplete interlayer pore closure, and anisotropic microstruc -
ture. The HIPed parts showed grain coarsening with grain sizes >250 μm. There was also a reduction in interlayer porosity after HIP, which also exhibited more uniform microstructures. The density and electrical conductivity of the parts were measured; the results are seen in Table 5. Notably, HIPing increases the density from 93 to nearly early 100% of theoretical density, while electrical condutivity rises from 86.3% to 97.4% IACS (International Annealed Copper Standard).
Process variables understanding Addressing the impact of various factors such as powder, binder, and equipment potential on the final part quality
Debind/sinter furnace impact
Detailing how the debinding and sintering processes are influenced by the aforementioned variables
The presentation also provided insights from industry experience, highlighting both the challenges and successes faced by part-makers in today’s manufacturing environment.
In his presentation entitled ‘NextGen-AM – Emerging SinterBased Additive Manufacturing Technologies for Sustainable Innovations’, Thomas Weissgärber from Fraunhofer Institute for Manufacturing Technology and Advanced Materials (IFAM) covered
Basic classification. It always depends on the application.
several emerging sinter-based AM technologies (other than Binder Jetting). His presentation covered three different sinter-based AM technologies in detail: MoldJet, Gel Casting, and 3D Screen Printing.
Fig. 33 shows a picture of some of the AM equipment available at Fraunhofer IFAM Dresden and a graphic representation of the tech -
nology envelopes and the areas they cover in the part size versus parts per year chart.
Weissgärber highlights that while PBF-LB dominates metal AM in manufacturing, research, and applications, its limitations in geometry, materials, and productivity are making sinter-based Additive Manufacturing processes increasingly more popular.
Since 2020, most sinter-based Additive Manufacturing technologies have been moving to higher Technology Readiness Levels (TRL), with Binder Jetting being one of the leading technologies in this area.
Fig. 34 shows the MoldJet machine concept for Tritone Dominant, outlining the six significant steps in the process.
MoldJet - 316L Demonstrators
treatment
• Iso-furnace of the company MUT Advanced Heating GmbH
Debinding under hydrogen between 300-360°C
Sintering 1380°C, 120 min
Fig. 35 shows some 316L parts produced using the MoldJet process.
Fig. 36 shows the Gel casting process, which begins with creating a permanent or lost mould (made via FFF in the figure). This is followed by casting the desired suspension into the mould by first heating the suspension. Once the suspension is cast into the mould, cooling solidifies it into a metallic gel. Various processes, including dissolving the
Gel casting - Process Chain
mould, can remove the part. After demoulding, the part undergoes debinding and sintering to achieve the final metal form. Weissgärber also covered Screen Printing, a technology explored in detail in another presentation from Exentis.
The summary slide was captivating, beginning with the statement, “There is a world beyond laser!... And there is also a world beyond metal Binder Jetting.” Weissgärber
Production of a permanent mould or lost mould by any method (here: FFF)
• Heating of the suspension and casting into the mould
• Cooling and solidification of the suspension to a metallic gel
Demoulding - directly or by dissolving the mould
• Heat treatment: thermal debinding and sintering
ASTM International Conference on Additive Manufacturing ASTM International Conference on Additive Manufacturing
concluded that while sinter-based technologies remain niche compared to PBF-LB, they are rapidly gaining traction, with many exciting new sinter-based AM technologies with the potential to improve cost, productivity, resolution, and material variety.
The author also acknowledged challenges, including distortion, maturity, etc. He summarised by saying that companies need to choose the right technology.
Screen Printing is a sinter-based AM technology that has the capability to fabricate parts at a very high production rate with some limited z-directional shape complexity. Fig. 37 shows a schematic of the Screen Printing process. A detailed description of the Screen Printing process was presented by Eric Bert from Exentis, entitled ‘Additive Screen Printing: Industrialized AM Technology for Powdered Metals, Ceramics, and Beyond’.
Bert described some of the details of the machine, process, and applications in his presentation. He stressed on-screen tools and optical layer alignment to deliver ultra-fine part features repeatably. High-speed automated systems are important for cost-effective mass production volumes.
An advantage of the process is that the paste feedstock used can be formulated using almost any material available in powder form. However,
it is essential to recognise that any change in the XY geometry of a part would require changing the screen tool, which adds cost and time. Also, the parts would have limited overhangs, though internal channels are feasible. Fig. 38 shows some of the possible geometrical features possible with this process. The process can work with numerous materials, including polymers, metals and ceramics. Some of the nonpolymeric materials that have been successfully developed include:
• Alumina
• Zirconia
• Silicon carbide
• Aluminium nitride
• BaTiO 3
• Various metal matrix composites
• 316L stainless steel
• Pure copper
• 6061Al aluminium alloy
• 4041 quench
• Tempered steel
“An advantage of the process is that the paste feedstock used can be formulated using almost any material available in powder form. However, it is essential to recognise that any change in the XY geometry of a part would require changing the screen tool, which adds cost and time.”
Print area 430x430 mm
Height 0.10 to 50 mm
Wall thickness 70 μ m
Min. hole dia 100 μ m
Aspect ratio up to 100:1
Surface roughness Ra = 2 μ m
Solid content - pastes 40-50 vol.%
Density green bodies 60-70 vol.%
Layer thickness 5.0 - 100 μ m (fabric screen), >100 μ m (metal stencil)
Screen mesh 20 to 500 μ m
Screen wire up to 10 μ m
Shrinkage 5-20%
Particle size Between 1 μ m and 50 μ m (d50)
Geometric tolerances ±30 μ m
In Fig. 39, process and screen characteristics are shown on the left side of the picture, and a part is shown on the right. Fig. 40 shows the image of 316L filters that were 2 mm in diameter, 600 μ m thick, with walls thickness of 100 μ m, with holes having a diameter of 120 μ m. Fig. 41 illustrates the year of introducing several industrial production systems from Exentis versus the production capability of various machines.
This report aims to cover what the author believes were the most engaging presentations given at ICAM 2024 within the sinter-based AM track. While reading a condensed version of the presentation offers valuable insight, attending the conference provides a far more productive and comprehensive experience.
The rapid growth of sinter-based AM is particularly interesting, as it extends beyond a single or limited number of processing platforms. Although Binder Jetting has caught the attention of many large manufacturing companies due to its attributes
Fig. 41 Graphic representation showing the year of introduction of various production systems for industrial and cleanroom applications versus the production capability of the machines (Courtesy Eric Bert, ICAM 2024) and the promise of meeting highvolume production requirements cost-effectively, the proliferation of novel sinter-based technologies continues to grow.
Beyond the more established processes, such as BJT and MEX, numerous other technologies are developing. These include Screen Printing, hybrid processes combining additive and subtractive methods, Gel casting, and various
LLC Barnesville, Ohio, USA abose@amfglabs.com Production
MEX variations. The sinter-based AM track within the ASTM ICAM series brings together updates on these new approaches and new materials alongside ongoing advancements in more mature sintering technologies. Readers are encouraged to consider attending the 2025 conference in Las Vegas, Nevada, to explore these exciting developments firsthand.
Author
Dr Animesh Bose CEO AMfgLabs
We Convene...
The most brilliant minds from industry and academia
We Coordinate... Transformative technical and workforce data
We Catalyze... High-value, high-impact collaborative projects
®
PIM International is the only business-to-business publication dedicated to reporting on the technical and commercial advances in the MIM, CIM, and sinter-based Additive Manufacturing industries. Available in both digital and print formats, PIM International is the perfect platform to promote your company to a global audience.
PIM International is dedicated to driving awareness and development of the MIM, CIM and sinter-based AM industries and their related technologies. Key to this aim is our support of a range of international partner conferences. View our complete events listing on: www.pim-international.com
PM China 2025
March 10–12 - Shanghai, China en.pmexchina.com
Fraunhofer Direct Digital Manufacturing Conference DDMC 2025
March 12–13 - Berlin, Germany www.ddmc-fraunhofer.de
AM Forum Berlin
March 17–18 - Berlin, Germany www.am-forum.de
Medical Device Manufacturing & R&D Summit
March 17–18 - Boston, MA, United States www.march25. medicaldevicemanufcturingrdsummit.com
Sustainability in powder technology processes workshop (event to be held in German)
March 25–26 - Dresden, Germany www.bit.ly/4kclW8o
AMUG 2025
March 30–April 3 - Chicago, IL, US www.amug.com
Hannover Messe 2025
March 31–April 4 - Hannover, Germany www.hannovermesse.de
The 14 th International Conference on Hot Isostatic Pressing (HIP 2025)
April 6–10 - Aachen, Germany www.hip2025.com
RAPID + TCT 2025
April 8–10 - Detroit, MI, United States www.rapid3devent.com
Ceramics Expo
April 29–30 - Novi, MI, United States www.ceramicsexpousa.com
Thermal Management Expo North America
April 29–30 - Novi, MI, United States www.thermalmanagementexpo.com
EPMA – Use of Powder Metallurgy Technologies in Aerospace
May 20–21 - Sandviken, Sweden www.seminars.epma.com/event/ aerospace-seminar
21 st Plansee Seminar
June 1–6 - Reutte, Austria www.plansee-seminar.com
+INDUSTRY 2025
June 3–5 - Bilbao, Spain plusindustry.bilbaoexhibitioncentre.com
ADDIT Ɛ D 2025
June 3–5 - Bilbao, Spain addit3d.bilbaoexhibitioncentre.com
PowderMet 2025
AMPM 2025
June 15–18 - Phoenix, AZ, United States www.powdermet2025.org www.ampm2025.org
EPMA PM Summer School 2025
June 22–27 - Lund, Sweden summerschool.epma.com
Ceramic AM Summit
June 30 –July 2 - Berlin, Germany www.amsummit.dkg.de
The Advanced Ceramics Show
July 9–10 - Birmingham , United Kingdom www.advancedceramicsshow.com
The Advanced Materials Show
July 9–10 - Birmingham , United Kingdom www.advancedmaterialsshow.com
Formnext Asia Shenzhen
August 26–28 - Shenzhen, China formnext-sz.hk.messefrankfurt.com/shenzhen/ en.html
Euro PM2025 Congress & Exhibition
September 14–17 - Glasgow, Scotland www.europm2025.com
The European Additive Manufacturing Congress 2025
September 14–17 - Glasgow, Scotland www.euroam2025.com
Formnext Asia Tokyo Forum 2025
September 25–26 - Tokyo, Japan formnextforum.jp.messefrankfurt.com/tokyo/en.html
The Advanced Materials Show USA
Sept. 30 – Oct. 1 - Columbus, OH, United States www.advancedmaterialsshowusa.com
ICAM25 International Conference on Advanced Manufacturing
October 6–10 - Las Vegas, NV, United States www.amcoe.org/event/icam2025/
ASEAN Ceramics
October 15–17 - Bangkok, Thailand www.aseanceramics.com/thailand
APMA 2025 7 th International Conference on Powder Metallurgy in Asia
October 19–22 - Quingdao , China apma2025.scimeeting.cn
AM Ceramics 2025
October 21–22 - Vienna, Austria www.amceramics.cc
Formnext 2025 November 18–21 - Frankfurt, Germany www.formnext.com
Ceramitec 2026
March 24–26 - Munich, Germany www.ceramitec.com
WorldPM2026
June 25–29 - Montreal, Canada www.worldpm2026.org
If you would like to see your CIM, MIM or sinterbased AM related event listed in this magazine and on our websites, please contact Merryl Le Roux: merryl@inovar-communications.com
As the usage patterns of PIM International magazine’s audience develop and change, we have expanded our social media activities, enabling us to connect with our global audience on multiple levels.
As the only magazine for MIM, CIM, and sinter-based AM, our LinkedIn, Twitter, and Facebook channels serve as indispensable sources for the latest industry news.
www.twitter.com/PIMMagazine
www.linkedin.com/company/piminternationalmagazine/
www.facebook.com/PIMInternationalmag
• Gain insights into the latest advancements in Powder Metallurgy.
• Meet experts in Metal Powders, MIM, Hard Materials, and more.
• Full Supply Chain Representation: From materials to applications
• Network with new leads and potential collaborators.
END USERS VISIT FOR FREE FREE TICKETS FOR TECHNICAL SESSIONS