

For a sustainable tomorrow

Höganäs AB commits to reduce absolute scope 1 and 2 GHG emissions 51% by 2030 from a 2018 base year.* Höganäs AB also commits to reduce absolute scope 3 GHG emissions from purchased goods and services, upstream transportation and distribution, and business travel 30% within the same timeframe.
*The target boundary includes land-related emissions and removals from bioenergy feedstocks.
Our climate tagret is validated by Science Based Targets initiative.
For more info scan the QR Code
www.hoganas.com

Publisher & Editorial Offices
Inovar Communications Ltd
11 Park Plaza
Battlefield Enterprise Park Shrewsbury SY1 3AF United Kingdom
Tel: +44 (0)1743 469909 www.pm-review.com
Managing Director & Editor
Nick Williams, nick@inovar-communications.com
Group News Editor
Paul Whittaker, paul@inovar-communications.com
Advertising Sales Director
Jon Craxford, jon@inovar-communications.com Tel: +44 (0)207 1939 749
Assistant News Editor
Charlie Hopson-VandenBos charlie@inovar-communications.com
Editorial Assistants
Amelia Gregory, amelia@inovar-communications.com Emma Lawn, emma@inovar-communications.com
Consulting Editor
Dr David Whittaker
Technical Consultant
Dr Martin McMahon
Digital Marketer
Mulltisa Moung, mulltisa@inovar-communications.com
Production Manager
Hugo Ribeiro, hugo@inovar-communications.com
Operations & Partnerships Manager
Merryl Le Roux, merryl@inovar-communications.com
Office & Accounts Manager
Jo Sheffield, jo@inovar-communications.com
Subscriptions
PM Review is published on a quarterly basis. It is available as a free electronic publication or as a paid print subscription. The annual subscription charge is £150.00 including shipping.
Accuracy of contents
Whilst every effort has been made to ensure the accuracy of the information in this publication, the publisher accepts no responsibility for errors or omissions or for any consequences arising there from. Inovar Communications Ltd cannot be held responsible for views or claims expressed by contributors or advertisers, which are not necessarily those of the publisher.
Advertisements
Although all advertising material is expected to conform to ethical standards, inclusion in this publication does not constitute a guarantee or endorsement of the quality or value of such product or of the claims made by its manufacturer.
Reproduction, storage and usage
Single photocopies of articles may be made for personal use in accordance with national copyright laws. All rights reserved. Except as outlined above, no part of this publication may be reproduced or transmitted in any form or by any means, electronic, photocopying or otherwise, without prior permission of the publisher and copyright owner.
Design and production
Inovar Communications Ltd.
ISSN: 2050-9693 (PRINT)
ISSN: 2050-9707 (ONLINE)
© 2024 Inovar Communications Ltd.
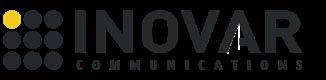
Different visions for the future of PM at World PM2024
As at every PM World Congress, the informal exchange of views, whether in the exhibition hall or at social events, provides invaluable insight into PM companies’ fears and aspirations.
What set this PM2024 event apart from previous years were the diverging views on PM’s future. The trajectory of the automotive industry – PM’s most significant consumer – was at the heart of many discussions. It became clear that the future development of PM is, to some extent, beyond the industry’s control, influenced by the unpredictable shifts within the automotive industry.
Official policy amongst governments may dictate an acceleration towards Electric Vehicle (EV) adoption, but this often seems to conflict with consumer demands. This contrast places significant pressure on Western automotive companies; future government policies are uncertain, and such companies contend with the heat from the rapid rise of China’s automotive industry.
However, as highlighted in the three articles in this issue, there are paths forward. There are promising opportunities for using PM technologies in EVs and hybrids, particularly in magnetic materials. Beyond the automotive sector, more diversified markets do exist for conventional PM parts. PM stands to benefit from regional growth hot spots, notably in India, where the demand for region-specific transportation solutions is rich in opportunity.
The PM2024 mantra, “Make a better world with PM,” captures the PM industry’s potential to drive change and embrace the evolving global demands of both industries and societies.
Nick Williams Managing Director, PM Review
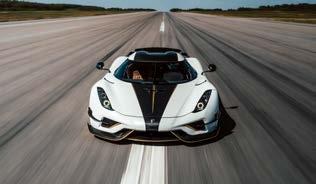
Cover image Koenigsegg’s Regera hybrid supercar features three SMC motors from YASA (Courtesy Koenigsegg)

Our materials, your life
Rio Tinto Metal Powders (RTMP) is committed to finding better ways to provide the materials the world needs now and in the future.
As a producer of iron and steel powders at our plant located in Quebec, Canada, RTMP is a key supplier to the automotive industry, which is undergoing a transition towards electrification. RTMP is contributing to the development of new Soft Magnetic Composite (SMC) materials for electric components, from pump assemblies to small electric motors in e-bikes and EV’s to support the energy transition. Together, we can create a better life for the generations to come.
Find out more at www.riotinto.com
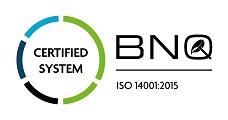
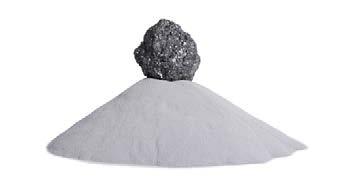




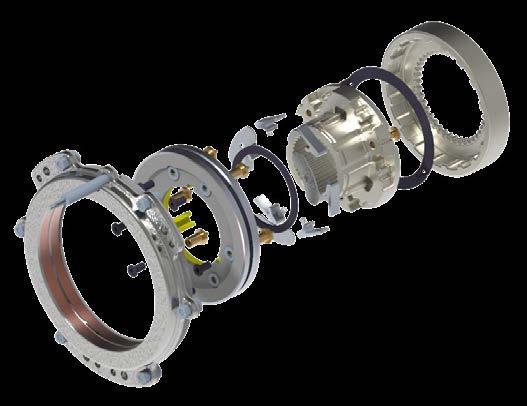
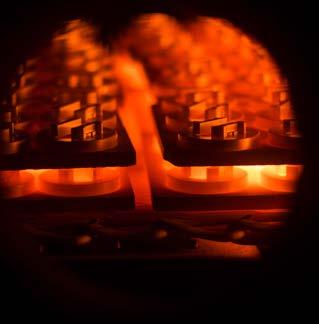
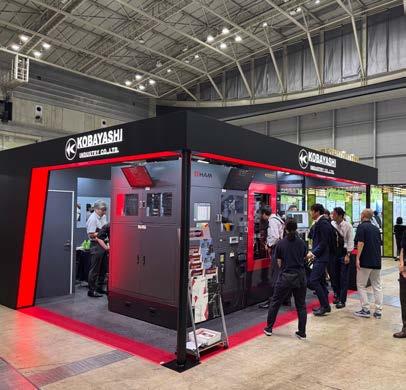
49 Powder Metallurgy: Discover innovative technologies meeting the demands of vehicle electrification
Vehicle Electrification is transforming the PM industry, providing new opportunities as Battery Electric Vehicles and Hybrid Electric Vehicles continue to gain market share.
At MPIF’s PowderMet2024 conference, a series of Special Interest Sessions delved into the innovative PM technologies used to meet current demands. Advances in Soft Magnetic Composites, PM permanent magnets, new electric motor designs, and evolving drivetrain mechanisms are discussed. Bernard North gives a comprehensive analysis of how industry leaders are adapting to these changes and explores the implications for future PM applications in the rapidly evolving automotive sector. >>>
65 Gevorkyan a.s.: Europe’s fastgrowing Powder Metallurgy company achieving success through a diversified customer base
Slovakia’s Gevorkyan a.s., founded in 1996 by Artur Gevorkyan, has grown into one of the fastest growing Powder Metallurgy companies in Europe. With a diverse product portfolio and a broad range of powder-based technologies, the company has proven itself to be highly adaptable and resilient during economic challenges.
Dr Georg Schlieper visited the company for PM Review and reports on its extraordinary journey, culminating in a recent expansion following a successful IPO in 2022. >>>
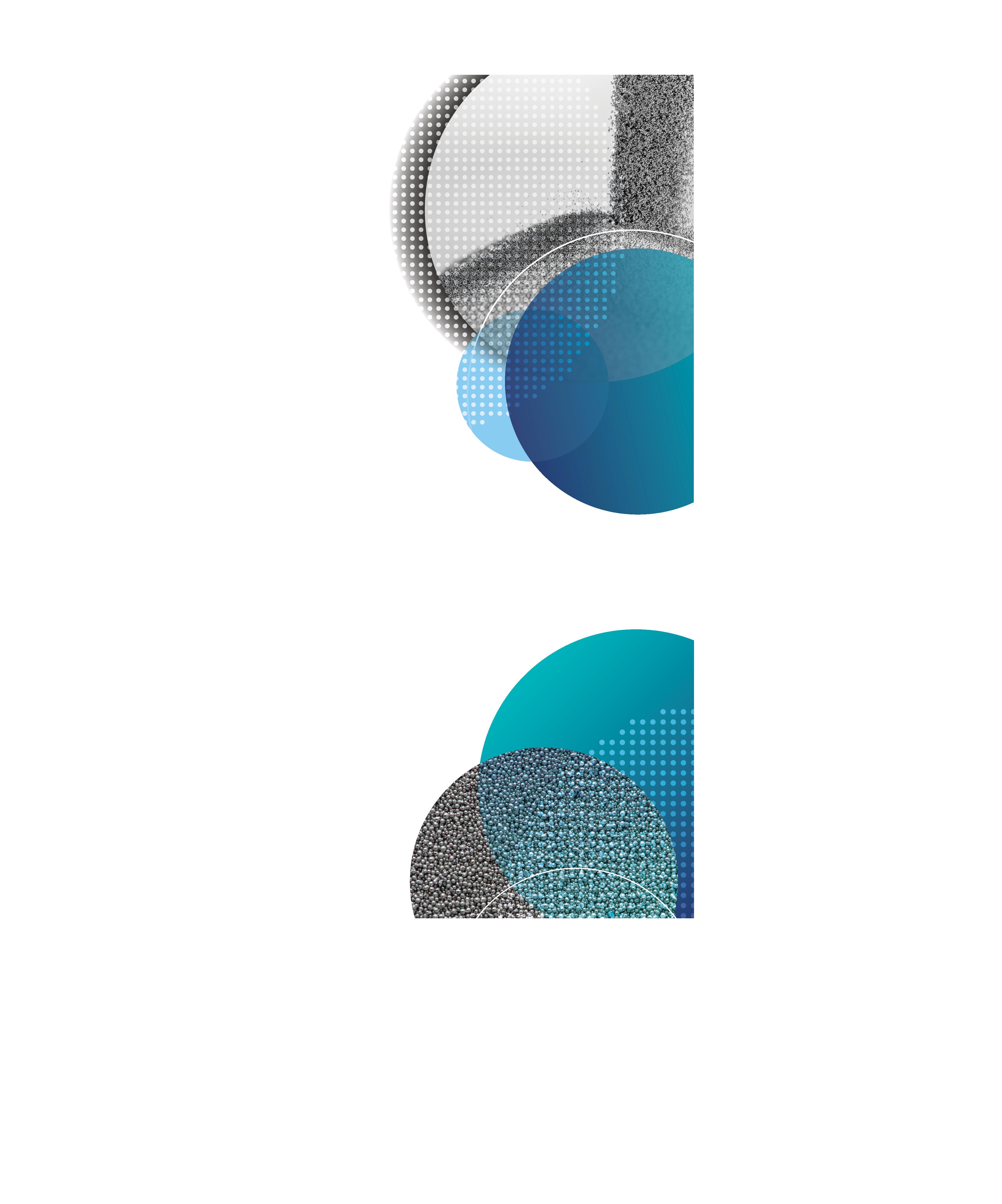
Experience the power of performance, the spark of innovation, and the strength of partnership
Performance:
As a global leader in powders, pastes, and granules, we excel in materials like Aluminum, Copper, Titanium, and more. Our precision manufacturing ensures superior product attributes tailored to your requirements.
Innovation:
Utilizing state-of-the-art research and development alongside cutting-edge technologies, we provide tailored solutions for PM and additive manufacturing. Our emphasis on materials and process advancements positions us as industry leaders in quality, service, and operational excellence.
Partnership:
Count on us as your trusted development and production ally. Our expertise in metal powders and alloys ensures top-tier materials for critical applications, empowering industries worldwide.
At Kymera International, we’re not just a powder provider; we’re your strategic partner in the world of specialty material solutions and additive manufacturing. Contact us today to revolutionize your projects
www.kymerainternational.com
info@kymerainternational.com

75 Powder Metallurgy in Asia: A status update from the World PM2024 Congress, Yokohama
The Powder Metallurgy World Congress series has long been a cornerstone event for the PM industry, offering a vital platform for global collaboration and innovation.
Following disruptions caused by COVID-19, World PM2024 marked the series’ successful return, attracting nearly 800 delegates and offering a comprehensive technical programme. The event also highlighted the Powder Metallurgy industry’s resilience amidst significant ongoing challenges.
Here, Nick Williams reports on the status of Powder Metallurgy in Asia as presented during the Plenary Session, including market trends, regional growth potential, and opportunities for Powder Metallurgy in an evolving global landscape. >>>
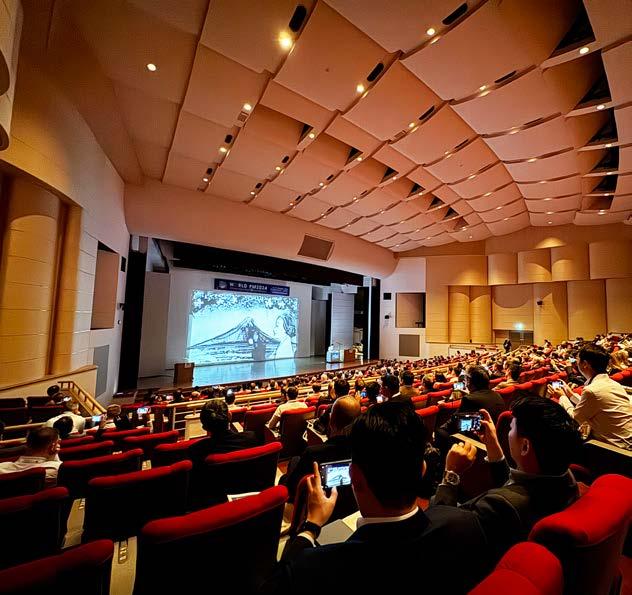


Our advertisers’ index and buyer’s guide serves as a convenient guide to suppliers across the PM supply chain.
In the digital edition of PM Review magazine, available at www.pm-review.com, simply click on a company name to view its advert, or on the company’s weblink to go directly to its website.


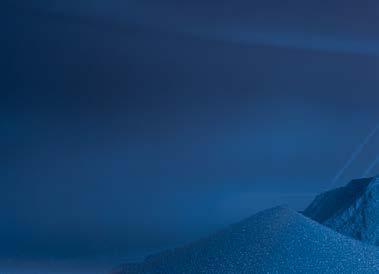
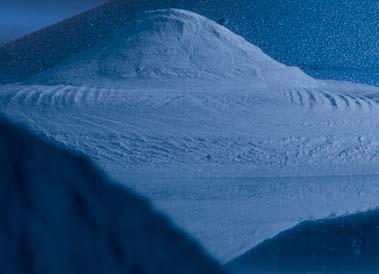

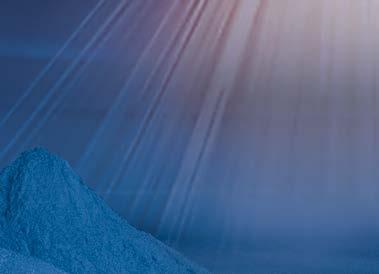
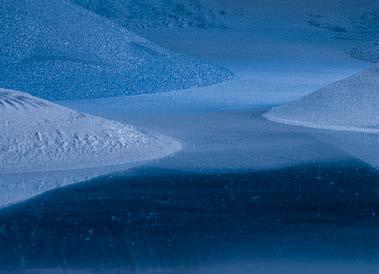

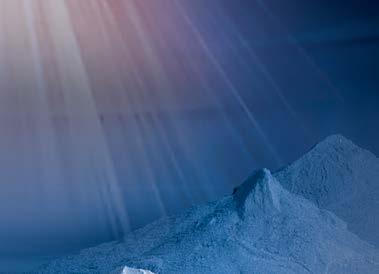





























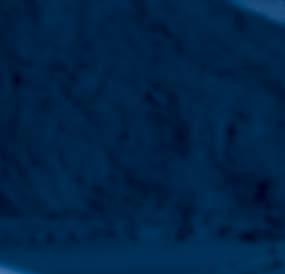
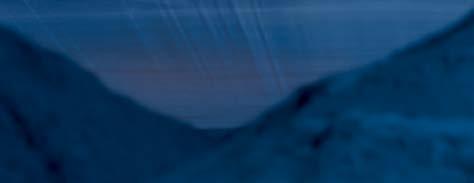






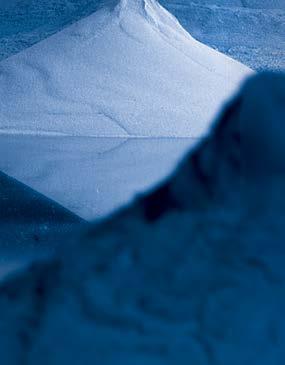






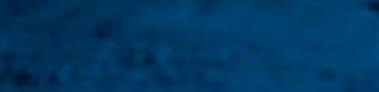



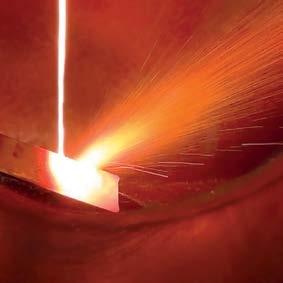
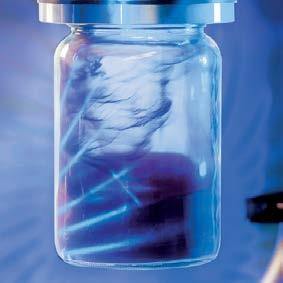
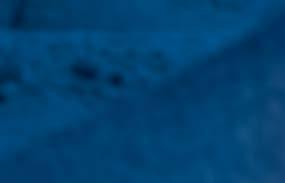

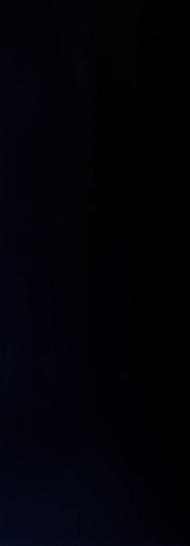





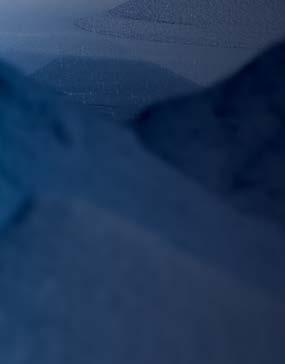







● GAS AND ULTRASONIC ATOMIZERS FOR SPHERICAL POWDERS WITHOUT ANY SATELLITES for LPBF, MIM, Binder Jetting and other Additive Manufacturing applications. High purity, sphericity and wide range of reproducible particle size distribution.
● WATER ATOMIZERS FOR MORE IRREGULAR POWDERS ideal for recycling/re ning process, press & sinter process and others.

● AIR CLASSIFIERS FOR THE PRECISE SEPARATION OF METAL POWDERS into ne and coarse powder fractions especially in the range < 25 µm
● MAXIMUM PURITY BY OXIDATION-FREE PROCESSING
● ALL SYSTEMS DESIGNED FOR EASY HANDLING AND CLEANING, QUICK ALLOY CHANGE WITH MINIMUM CROSS CONTAMINATION

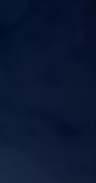





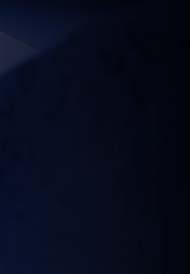

● FOR A WIDE RANGE OF METALS AND FOR SMALL TO MEDIUM AMOUNTS
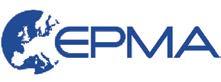
To submit news for inclusion in Powder Metallurgy Review contact Paul Whittaker at paul@inovar-communications.com
GKN Hoeganaes and First Phosphate collaborate to supply EV battery cathode materials
GKN Hoeganaes, a division of GKN Powder Metallurgy, based in Cinnaminson, New Jersey, USA, has announced a strategic collaboration with First Phosphate, a mineral development company located in Saguenay-Lac-SaintJean, Canada. The partnership is intended to help establish a North American supply chain for lithium iron phosphate (LFP) batteries, a critical component for the electric vehicle (EV) and energy storage industries.
The partnership follows GKN Hoeganaes’ successful integration of First Phosphate’s magnetite into its proprietary Ancorsteel melting process. This process has led to the development of a high-purity iron powder, which serves as a precursor to lithium iron phosphate cathode active material, necessary for the production of LFP batteries. These batteries are growing in popularity due to their cost-effectiveness, safety and stable raw material availability.
In support of this growing demand, the collaboration marks one of the first substantial efforts to establish a North American production line for LFP battery components, helping reduce dependency on international supply chains.
“Partnering with First Phosphate enables us to contribute our advanced iron powder
technology to a rapidly growing industry that is focused on clean and efficient energy storage solutions,” said Matthias Voss, president at GKN Hoeganaes. “This collaboration underscores our commitment to fostering a local supply chain for LFP batteries, addressing both sustainability and technological innovation.”
First Phosphate is set to integrate high-purity Ancorsteel into its upcoming iron phosphate precursor (FP pCAM) and lithium iron phosphate cathode active material (LFP CAM) Saguenay-Lac-St-Jean production facility, with ambitions to reach 400,000 tonnes per annum by 2032. Supporting this vision, GKN Hoeganaes is prepared to scale its Gallatin, Tennessee, opera -
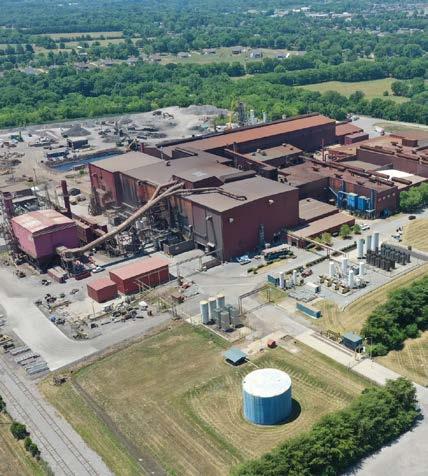
tions – already recognised as the world’s largest steel atomising plant – and will be providing its research and development facilities in Cinnaminson, New Jersey, for process enhancement and optimisation.
“Working with GKN Hoeganaes to bring Ancorsteel to the market is a vital step in advancing our mission to create a sustainable and locally sourced LFP battery supply chain,” said John Passalacqua, CEO at First Phosphate. “This partnership combines our high-quality phosphate resources with GKN Hoeganaes’ expertise in iron powder production, setting the stage for a robust North American battery ecosystem.”
The newly developed Ancorsteel material is composed of sustainable North American iron scrap and magnetite, aligning with non-FEOC standards for domestic production. www.gknpm.com www.firstphosphate.com
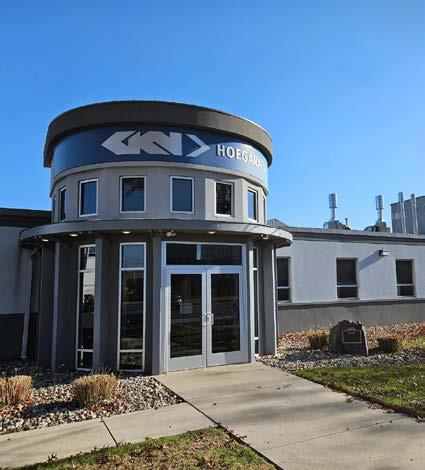

GKN Hoeganaes produces metal powder for battery applications at its Powder Production Center in Gallatin, Tennessee, (left), with R&D undertaken at its Powder Innovation Center in Cinnaminson, New Jersey (Courtesy GKN Hoeganaes)
Neo secures US$50 million for sintered magnets facility in Europe
Neo Performance Materials Inc, headquartered in Toronto, Canada, has entered into a loan agreement with Export Development Canada (EDC) for a US$50 million credit facility to finance the ongoing construction of its sintered magnets plant in Narva, Estonia.
Construction of the new facility began in 2023, and is reported to be progressing on time and on budget at an estimated cost of US$75 million. The facility has obtained significant
support, including a grant of up to US$20 million (€18.7 million) from the European Union’s Just Transition Fund (JTF) in 2022. As of the first half of 2024, Neo has capitalised US$24.9 million since the project’s inception. The remaining estimated cost of US$50.1 million (prior to the JTF grant) is anticipated to be spent through the end of 2024 and into 2025.
The Estonian facility is strategically located near Neo’s existing rare earth separation plant. Phase One of the
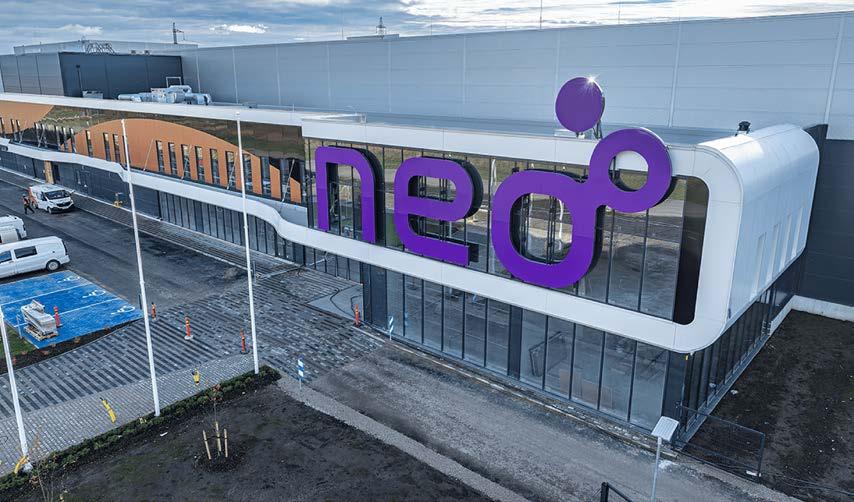
Kymera International secures $775M for debt refinancing and acquisitions
Kymera International, a specialty materials company headquartered in Raleigh, North Carolina, USA, has received a private credit loan of $775 million to refinance its existing debt and provide capital for add-on acquisitions, including its recent acquisition of Fiven, reports PitchBook, a financial data and software provider.
According to market sources, HPS provided the entirety of the facility and syndicated a small portion of the debt to other lenders. The facility included a term loan as well
as a delayed-draw term loan. The company also has a separate AssetBased Lending (ABL) facility held by KeyBanc and M&T.
Piper Sandler and Goldman Sachs served as financial advisors on the transaction, which was reported to have been dual tracked between the syndicated market and the private credit market.
“When you have a good credit like Kymera, with a history of growth and strong free cash flow conversion, you have financing options. Private credit has raised so much capital that it
new facility’s operations is expected to produce 2,000 metric tons per year, with plans for future growth to support the growing use of sintered magnets.
“Neo is pleased to have EDC’s support to advance our new sintered magnets manufacturing facility. Strategically located in Estonia to support the mid-to-downstream integration with our Silmet rare earth separation facility, this manufacturing facility will be Neo’s first to produce madein-EU rare earth magnets for electric vehicle traction motors. It will service the growing demand for localised, parallel supply chains, shaping the future of EV manufacturing in Europe and North America,” said Rahim Suleman, Neo President and Chief Executive Officer.
The loan will be advanced in two tranches of US$25 million and will mature five years from the date of each instalment, with repayment of principal beginning in two years. The outstanding principal amount carries an interest rate equal to the secured overnight financing rate, as administered by the Federal Reserve Bank of New York, plus an applicable margin.
Several of Neo’s subsidiaries, including the entity that owns the Narva project, are expected to provide guarantees and/or security in favour of EDC.
www.neomaterials.com
does create a viable alternative to the syndicated market, a dynamic that benefits the issuers,” Adam Shebitz, Palladium’s Head of Industrials, told PitchBook LCD.
Palladium first invested in Kymera in 2018, and since the buyout, the company’s EBITDA has reportedly tripled.
The company announced its agreement to acquire silicon carbide developer Fiven from OpenGate Capital on June 4.
“Given the fact that Kymera had an acquisition under LOI, we wanted a timely close and we wanted to avoid market flex on terms,” added Shebitz.
www.kymerainternational.com
The rare earth sintered magnet manufacturing facility is located close to Neo’s existing rare earth separation facility and began construction in 2023 (Courtesy Neo Performance Materials)
Press Systems for Shaping Magnets & Magnetic Materials
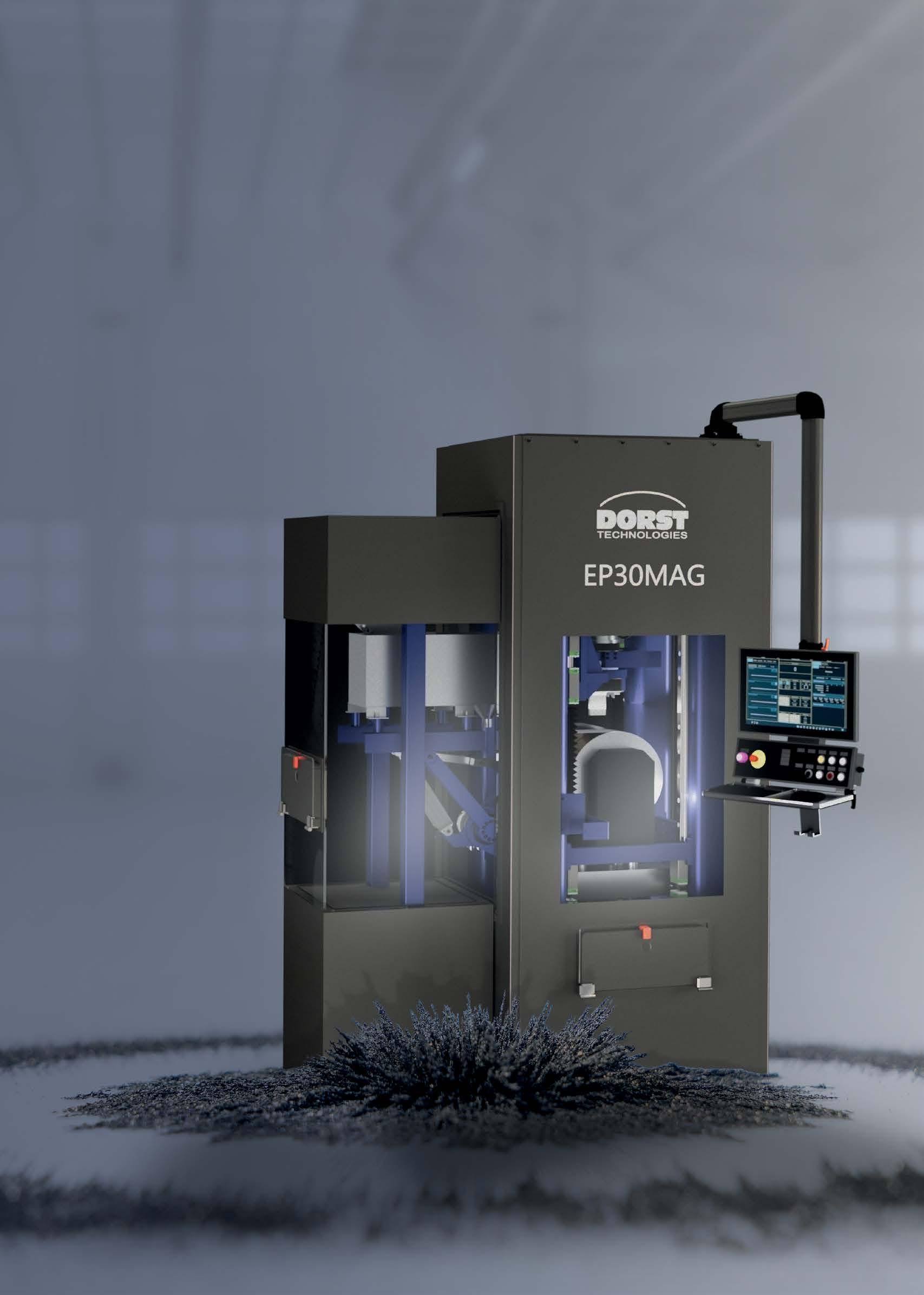

AM 4 AM funding round to expand facilities and boost powder production
AM 4 AM, a producer of metal powders for Additive Manufacturing based in Foetz, Luxembourg, has announced the successful completion of a €1.3 million seed funding round. The round was led by Luxembourg Space Sector Development, EIT RawMaterials, and further supported by the Young Innovative Enterprise initiative from the Ministry of Economy of Luxembourg.
AM 4 AM announced that the €1.3 million investment will fund the expansion of its facilities, as well as enhance its production and product development capabilities. The company aims to install a complete powder development platform in its facility by the end of the year to meet the growing demand for high-performance materials.
“With this funding, AM 4 AM is entering a new phase in its development. The future infrastructures we will put in place will allow us to enhance production capacity, broaden our product portfolio, and accelerate our innovation efforts,” stated Maxime Delmée, CEO and founder of AM 4 AM. “The 3D printing market is expanding rapidly, yet there remains a shortage of suitable
Höganäs introduces
metal materials. With HiperAL, our high-performance aluminium, we’ve demonstrated a groundbreaking ability to provide metals with the required properties, meeting the demands of this growing sector.”
From its founding in 2019, AM 4 AM has pioneered an innovative technology for powder modification using cold plasma. This technology is said to enhance the properties of materials when additively manufactured, with the company’s flagship product, HiperAL, reported to be one of the strongest aluminium alloys on the market.
“It’s a real pleasure to see AM 4 AM continuing to grow and succeed from Luxembourg! After taking part in Fit 4 Start in 2022, the company continued its successful development from the Technoport in Foetz. Now, by leveraging the Young Innovative Enterprise scheme, AM 4 AM is set to expand and scale its operations internationally,” said Sven Baltes, Manager of Start-up Relations at Luxinnovation.
The Luxembourg Space Sector Development Fund, under the oversight of the Luxembourg government and satellite connectivity solutions
Starmix
Nova for optimised compaction
Höganäs AB, headquartered in Höganäs, Sweden, has launched Starmix Nova, a new bonded mix solution said to offer high apparent density and good filling performance, without the use of metal stearates.
Starmix Nova is reported to enable more efficient compaction in terms of productivity, quality and sustainability. Its high apparent density reduces filling height and allows for compact tool design.
The solution enables the compaction of larger and more geometrically
complex components as well as the compaction of components with narrow sections. It also improves density distribution.
The fillability performance also reduces the green scrap rate by minimising weight scatter and dimension deviations, cracks and edge defects. Additionally, the improved lubricity extends tool life while the zinc-free lubricant ensures clean burn-off with no residues in the sintering furnace. Both ejection properties and density can be further improved
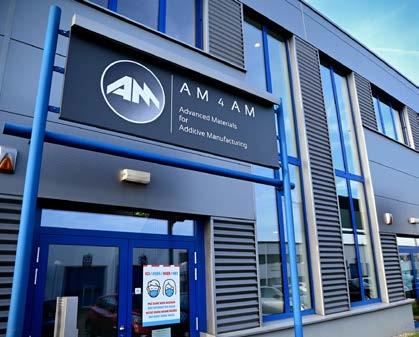
AM 4 AM has announced the successful completion of a €1.3 million seed funding round. The company plans to expand its facilities and enhance its production and product development capabilities (Courtesy AM 4 AM)
provider SES, is intended to support the fund’s mission of bolstering Luxembourg’s space ecosystem. AM 4 AM’s powders, with their high strength, are well-suited to use in Additive Manufacturing intended for space.
Speaking about the investment, Bernd Schäfer, CEO and Managing Director of EIT RawMaterials, said, “Companies like AM 4 AM who work on advancing raw materials play a crucial role in the future of the European economy and its sustainability. EIT RawMaterials’ focus on innovation and AM 4 AM’s mission show perfect synergies, and I’m excited that we are part of this journey.” www.am-4-am.com
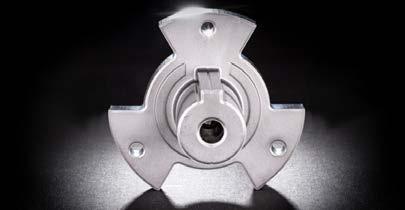
Starmix Nova is a bonded mix solution developed for improved compaction (Courtesy Höganäs)
by applying warm die compaction (60-80°C). Starmix Nova can be utilised to either increase the green density by decreasing the lubricant content or to improve the ejection process.
www.hoganas.com

6K closes $82 million funding round, names Saurabh Ullal as CEO
6K Inc, located in North Andover, Massachusetts, USA, announced that it has raised $82 million as part of its Series E funding round. The capital is expected to enable the company to scale up production for battery cathode active materials (CAM) and expansion for producing Additive Manufacturing metal powders.
In addition to the funding round, 6K announced that Dr Saurabh Ullal has assumed the role of CEO, replacing Dr Aaron Bent. The company has also appointed LaunchCapital’s Chief Investment Officer Bill McCullen as chairman of the board, with Volta’s CEO Dr Jeff Chamberlain and auto industry veteran Beda Bolzenius also joining the board.
“Thanks to Aaron, 6K is wellpositioned today as a leader for sustainable, critical material produc -
tion for lithium-ion batteries and additive manufacturing. Saurabh’s expertise in technology and operations ensures the company’s scaling strategy while meeting the material specifications and reliability levels customers demand,” McCullen stated.
“The $82 million raised underscores the confidence investors have in 6K, the UniMelt platform, and the leadership team.”
Incoming board member Beda Bolzenius has over thirty years of experience in leadership roles across the global automotive industry in Germany, United States, Mexico, South Africa, China, and Japan. Beda has an automotive technical background with operational experience in engineering, manufacturing, logistics, and supply chain management. He served as CEO of global manu -



facturer Marelli and held leadership positions in market-leading companies such as Bosch and Johnson Controls. He is expected to bring corporate, operational and automotive industry insights to his role on the board.
Dr Chamberlain is the CEO of Volta Energy Technologies, LLC, a venture capital firm launched out of Argonne National Laboratory. Chamberlain has a long record of industrial product R&D and commercialisation in energy, integrated circuit, and water treatment technology.
In addition to these activities, Chamberlain spent ten years leading energy storage initiatives at Argonne National Laboratory. In collaboration with the US Department of Energy, he led the effort to successfully transfer advanced battery technology from Argonne to organisations such as LG Chem, BASF, General Motors, Toda Kogyo, and General Electric. www.6KInc.com
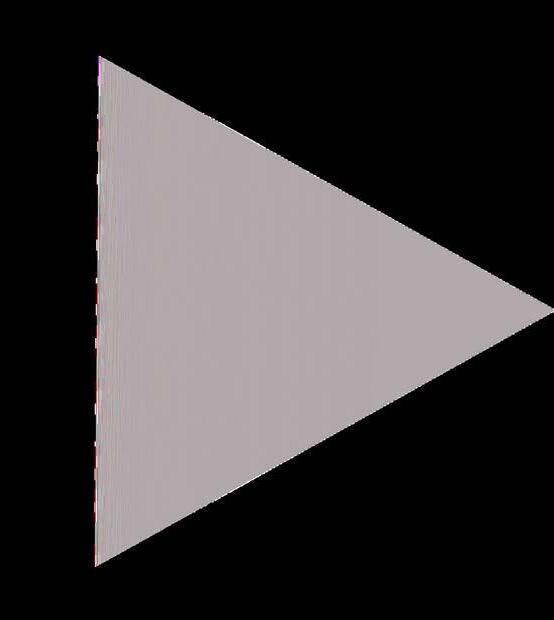
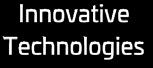

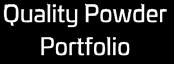









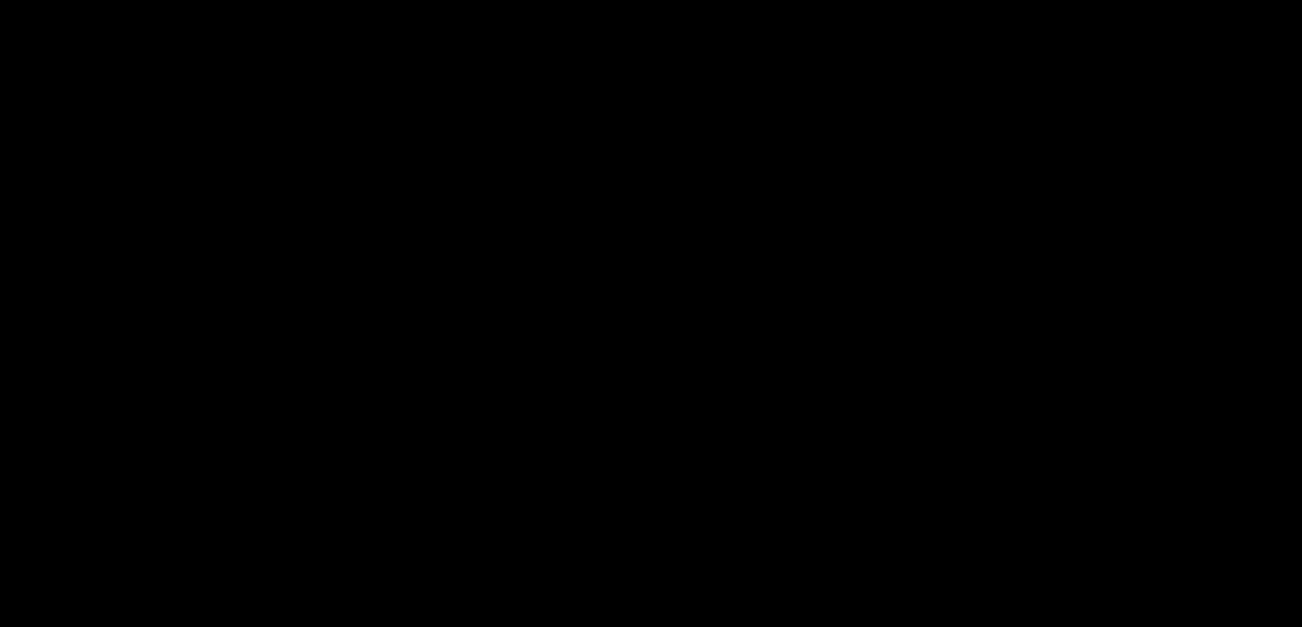
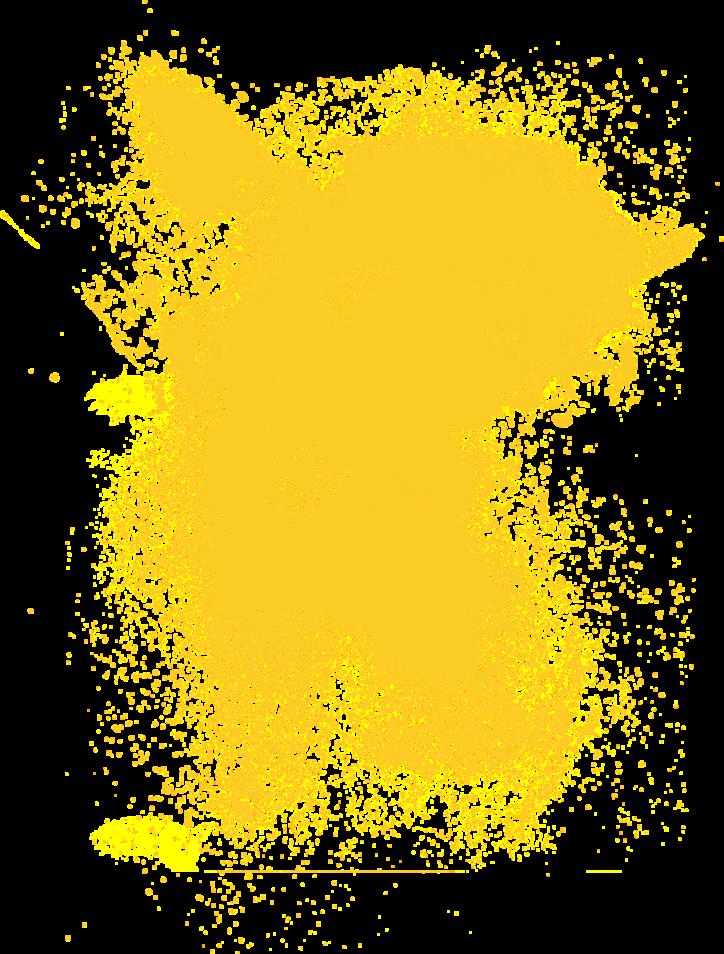







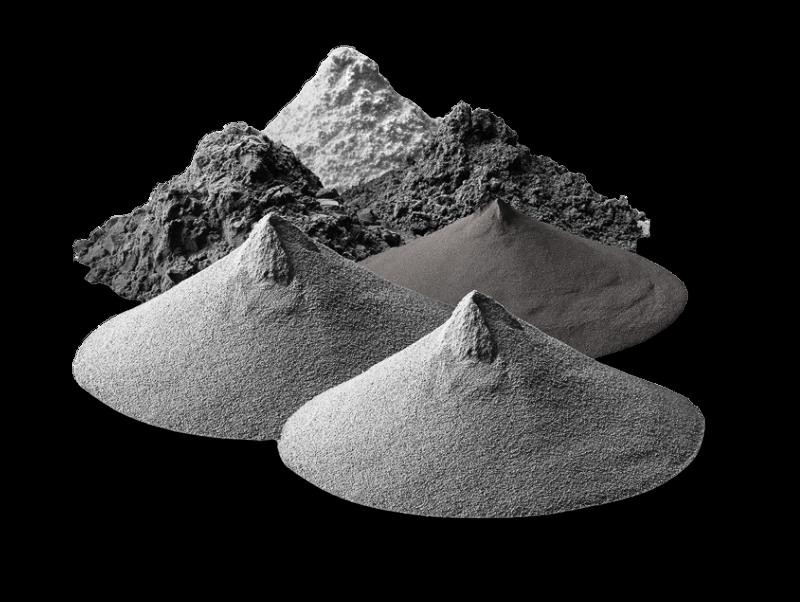

United Grinding acquires GF Machining Solutions
United Grinding Group, based in Miamisburg, Ohio, USA, has signed an agreement with Georg Fischer AG, Schaffhausen, Switzerland, to acquire its division GF Machining Solutions (GFMS), based in Biel, Switzerland. The move is expected to strengthen United Grinding’s

GF Machining Solutions offers a range of tooling for PM presses under its System 3R brand (Courtesy GF Machining Solutions)
market position and serve its global customers with more comprehensive solutions. The transaction is valued between US$714–737 million (CHF 630-650 million) and is expected to close in Q1/Q2 2025, subject to regulatory approvals.
GF Machining Solutions provides solutions for manufacturers of precision parts and tools and mould and die makers. Its portfolio includes machines for milling, eroding, laser texturing, laser micromachining and Additive Manufacturing. The group currently employs around 3,500 people at over forty global locations. Through its System 3R brand, GFMS provides a range of tooling for the Powder Metallurgy industry. When producing punches and dies, the tooling reduces setup times and is said to improve accuracy and quality with fewer rejections. When used in the powder compaction press, setup times are also drastically reduced, with improved accuracy and quality of parts.
For metal Additive Manufacturing, GFMS partners with 3D Systems to offer a range of machines. These include the DMP Flex/Factory 350 and DMP Factory 500.
Sandvik launches Osprey HWTS 50 hot-work tool steel powder
Sweden’s Sandvik AB has introduced Osprey HWTS 50, a hot-work tool steel powder designed for enhanced manufacturability. Primarily developed for Laser Beam Powder Bed Fusion (PBF-LB) Additive Manufacturing, it is also well-suited for Hot Isostatic Pressing (HIP) and Metal Injection Moulding (MIM).
The tempering and thermal fatigue resistance, as well as thermal conductivity of Osprey HWTS 50, are improved when compared with conventional H-class hot work tool steels. These advanced properties are intended to effectively address many common
challenges in hot-work applications within general engineering, stated Sandvik.
Osprey HWTS 50 also improves the processability in PBF-LB, lowering the susceptibility of cold cracking compared with conventional H-class hot work tool steels. Typical applications include highpressure die casting dies, injection moulds, and hot forming tools. The chemical composition is tailored for improved hot hardness at temperatures exceeding 600°C. It is characterised by lower carbon content compared with those of medium carbon hot work tool steels
The DMP Flex 350 enables the efficient production of very dense, pure metal parts and includes improved gas flow technology for improved uniform part quality across the entire build area. The DMP Factory 500 is a workflow-optimised metal Additive Manufacturing machine that produces parts of up to 500 x 500 x 500 mm in size. Engineered using 3D Systems’ metal additive technology along with GF Machining Solutions’ technical and industrial knowledge, the DMP 500 incorporates precision System 3R clamping systems.
United Grinding is one of the world’s leading manufacturers of grinding, eroding, laser, and measuring machines, as well as machine tools for Additive Manufacturing. The company employs around 2,000 people at over twenty locations.
United Grinding’s majority shareholder is Patinex AG, a Swiss holding company. Through its Mägerle, Blohm, Jung, Studer, Schaudt, Mikrosa, Walter, EWAG, and IRPD brands and competence centres in America and Asia, the company offers a large product portfolio and a full range of services for the production of highprecision components. www.grinding.com www.gfms.com
and modifications to the carbide forming elements. This is to ensure a comparable or even enhanced tempering resistance despite lower carbon wt.%.
The thermal conductivity of Osprey HWTS 50 is higher compared to medium carbon tool steels over a wide temperature range.
Osprey HWTS 50 metal powder is manufactured by either induction melting under Vacuum Inert Gas Atomisation or melting under argon prior to Inert Gas Atomisation. This produces a powder with a spherical morphology, which provides good flow characteristics and high packing density. In addition, the powder has a low oxygen content and low impurity levels.
www.metalpowder.sandvik

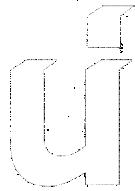
A SOLID LINE OF THINKING: SINTERING WITH A SOLID INFILTRANT
SOLIDIFY YOUR CASE FOR ULTRA INFILTRANT
There’s a solid line of thinking in the copper infiltration of ferrous PM parts and it can change the way you do business. Ultra Infiltrant is a wrought, homogeneous copper-based alloy that offers significant benefits over powder form copper infiltrants. Benefits like less waste, improved productivity, reduced erosion, no adherent residue and increased strength and hardness values. Benefits that affect your production line and ultimately your bottom line. Ultra Infiltrant is available in single and multi-turn wire rings, straight-length slugs, or other configurations to accommodate virtually any automated process. Ultra Infiltrant was designed for copper infiltration of ferrous PM parts in today’s cost competitive manufacturing environments, where the handling of fragile green infiltrant slugs is difficult and can lead to excessive waste. Additionally, it performs well in nitrogen-hydrogen based atmospheres so widely used in sintering operations globally.
SOLIDIFY YOUR INFILTRATION PROCESS FOR ULTRA INFILTRANT
Less waste, easier production, superior product: what more is there? Ultra Infiltrant revolutionizes the PM industry by eliminating all the negatives associated with infiltrant powders and improving on the process as a whole. The net result? How about overwhelmed customers and a boost to your bottom line? That’s what Ultra Infiltrant offers, so put it to work and get started on a solid line of thinking.

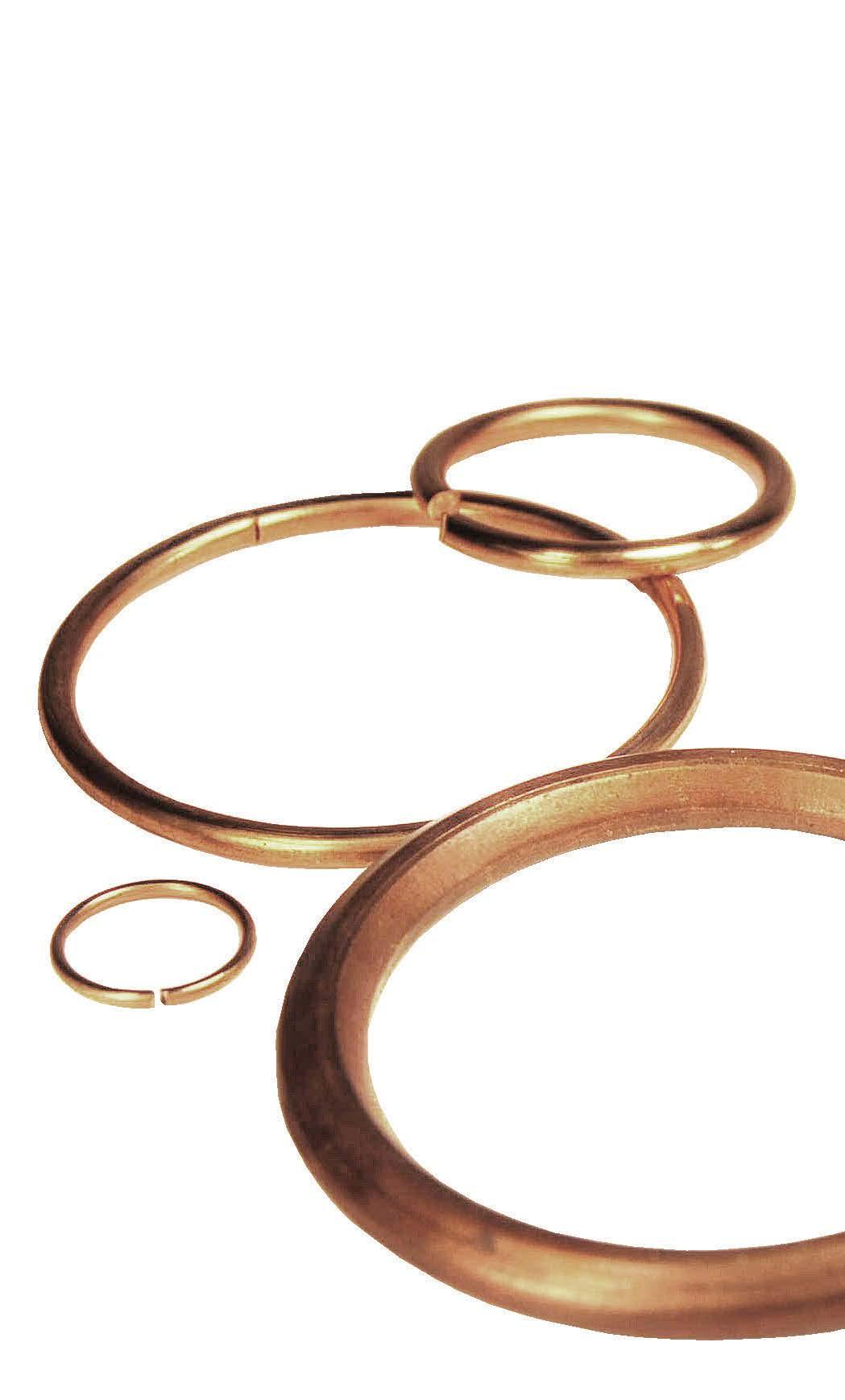
ORNL and NETL develop alloy for crackfree, lightweight turbine blades
Researchers at Oak Ridge National Laboratory (ORNL), Tennessee, USA, and the US National Energy Technology Laboratory (NETL), have developed and additively manufactured a light, crack-free alloy capable of operating at temperatures above 1,316ºC (2,400ºF) without melting.
LE-237i-2023.ps
T:\MISC\ADS\LE-237\LE-237i-2023.cdr
The alloy combines seven elements in a niobium-rich, complex
Thursday, February 23, 2023 8:16:40 AM
Color profile: Disabled
concentrated alloy whose melting point is at least 48% higher than the nickel and cobalt superalloys previously developed by ORNL. Researchers fine-tuned the electron beam melting process to make test parts from the novel alloy.
“No one has been able to develop and print alloys with such a high melting temperature and low density without cracks before,” said
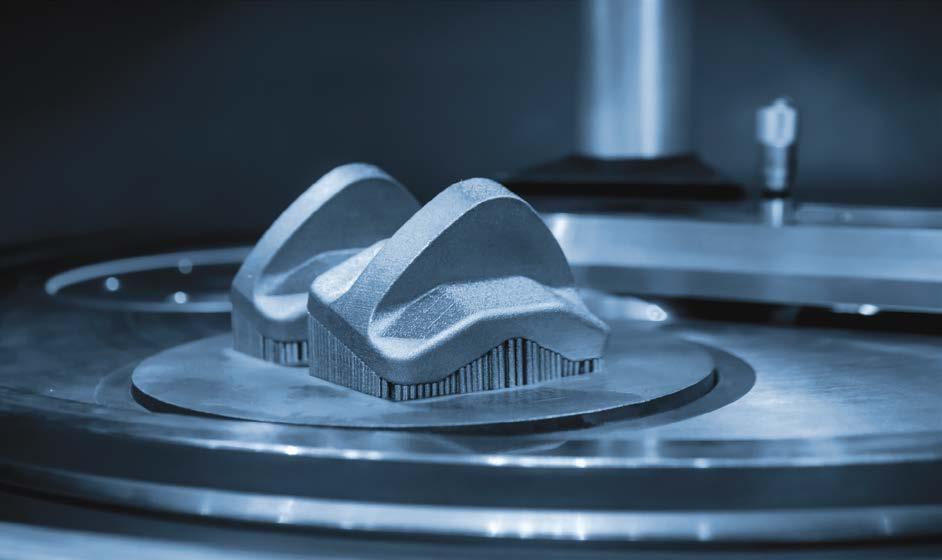
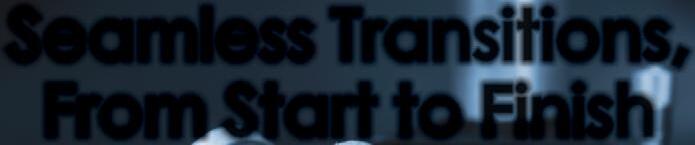
ORNL’s Saket Thapliyal. “This is significant. We’re making something lighter that can hold its structural integrity at ultra-high temperatures.”
The new alloy’s light weight and ability to withstand such high temperatures could enable additively manufactured turbine blades to better handle extreme temperatures, reducing the carbon footprint of gas turbine engines like those found in aeroplanes.
www.ornl.gov www.netl.doe.gov
AMES reduces environmental impact of Tamarite facility with photovoltaic installation
AMES Sintered Metallic Components, Barcelona, Spain, has announced the installation of a photovoltaic system at its Tamarite facility. The installation consists of 1,125 modules and six 100 kW power inverters.
This move is expected to generate over 937,000 kWh of energy annually, with Ames announcing it plans to reduce CO 2 emissions by around 187,000 kg per year.
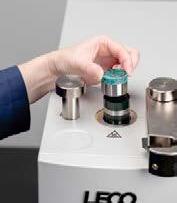
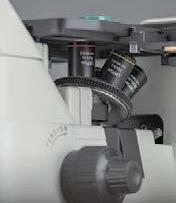
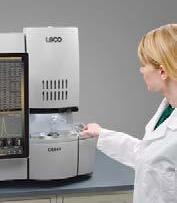
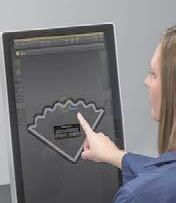
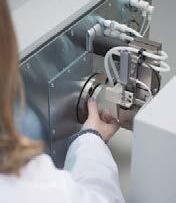
AMES Tamarite manufactures a range of Powder Metallurgy gears and mechanical sintered components. Finishing processes include treatments such as case hardening, carbonitriding, induction hardening and steam treatment.
AMES is able to manufacture high-density, high-performance gears using its AmesDens-A and AmesDens-C processes. The process to be used depends on the geometry and density that are required. For top-performance gears, AMES offers its SurfaDens surface densification process, which achieves an accurate tooth profile and a surface density comparable to that of a conventional wrought steel component.
www.ames-sintering.com

3D Lab secures USA and Chinese patents for its atomisation process
3D Lab sp zoo, based in Warsaw, Poland, has been granted a USA patent for its ‘Method and Device for Producing Heavy Metal Powders by Ultrasonic Atomization’ innovation. The company has also been granted a Chinese patent for the technology incorporated into its ATO atomisers under ‘A Method for Evacuation of Powder Produced by Ultrasonic Atomization and a Device for Implementing This Method.’
The patented technology is at the core of the company’s ATO series of ultrasonic metal atomisers. This technology is said to produce high-quality spherical metal powders with precise control over particle size, excellent flowability, and low oxygen content. These characteristics are critical for Additive Manufacturing and various industrial applications.
Commenting on the USA patent, Jakub Rozpendowski, CEO of 3D Lab, said, “We are proud to add this USA patent to our rapidly growing portfolio of global intellectual property. Our patented technologies drive our mission to provide advanced and versatile solutions for metal powder production, ensuring superior material quality and accelerating material innovations. This patent is a significant milestone in our journey, reflecting the dedication and innovative spirit of our team.”
The ATO Lab Plus is an advanced ultrasonic metal atomiser designed for lab-scale production of metal powders. Ideal for research and production environments, it enables the efficient and cost-effective production of reactive and nonreactive metal powders.
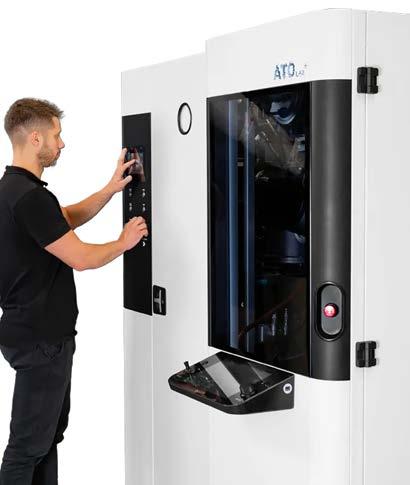
3D Lab has been granted patents for its atomisation process (Courtesy 3D Lab)
The atomiser has a modular construction, allowing for easy expansion of powder production capabilities through the use of the interchangeable modules. The device has advanced safety systems and automatic features, offering a versatile solution for producing metal powder. www.metalatomizer.com

CNPC Powder gains SCS certification for recycled aluminium and titanium powders
CNPC Powder, headquartered in Vancouver, Canada, has achieved a Certificate of Carbon Footprint for Aluminium and a Certificate of Achievement for Aluminium made from recycled materials from SCS Global Services, said to demonstrate sustainable development at scale. The company is reported to be the first manufacturer of titanium and aluminium alloy powders with production based in China to achieve SCS certification.
“Our technologies are focused on ensuring that we can sustainably scale for large applications in AM
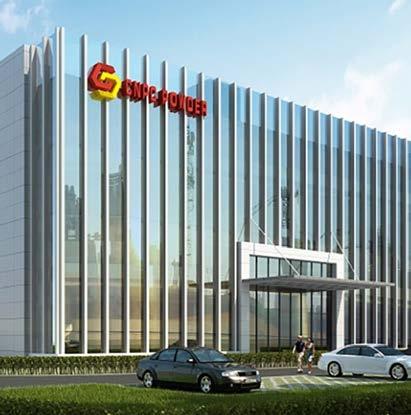
without compromising the environment,” stated Paul Shen, CEO of CNPC Powder. “Our mission is rooted in transforming the industry by implementing eco-friendly practices and promoting the recycling and reuse of critical materials, including aluminium alloys, titanium alloy powders, and beyond. This milestone is merely the first step on our path to carbon neutrality.”
CNPC has been producing metal powders for Additive Manufacturing in China for more than a decade, over which time it has developed a proprietary Additive Manufacturing Production (AMP) technology. AMP is said to have a better composition ratio, less gas consumption and lower cost than other powder production methods, aiding the production team in achieving up to a 400% reduction in the carbon footprint of materials produced whilst tailoring properties to better suit Additive Manufacturing.
In expanding its research and development of green technologies, including refining recycling processes and enhancing product performance, CNPC has also finalised the facility expansion at its Anhui AM Campus. The additional
Höganäs celebrates 25 years of innovation and growth in North America
Höganäs in North America recently celebrated its 25 th anniversary. The event took place on October 24, 2024, at the North American headquarters in Hollsopple, Pennsylvania, USA, bringing together employees, customers, vendors, and community members to celebrate the milestone.
The anniversary celebration featured a mix of videos, guest speakers and facility tours, where
the attendees had the opportunity to discover more about the manufacturing processes and innovations at Höganäs.
“It was a true pleasure to celebrate our twenty-five-year anniversary in North America with our employees, customers, suppliers, group management and other important partners,” stated Dean Howard, Market President, North America. “Our team has built
floor space will be used for the production of 45 tons of recycled Al powder per month.
At the same time CNPC says that it has been an active participant in developing industrial standards that promote the ecological advancement of the entire Additive Manufacturing industry, including partnerships with leading local Universities and global companies in the electronics, automotive and aerospace sectors.
“Our journey to 100% recycled materials has begun with the most reactive and high-value applications, meeting rigorous aviation and automotive standards without compromising quality,” said Kathy Liu, Global Sales Manager. Currently, CNPC has a resource utilisation rate of over 90% for recycled aluminium and titanium.
By utilising recycled raw materials, CNPC states that it is contributing to both environmental sustainability and potential cost savings for customers. “Our efforts are geared toward reducing carbon emissions, lessening the impact of global warming, and setting a new standard for sustainability in the metal powder industry,” it was added. “Through sustainable practices and innovative technologies, we are committed to reducing the carbon footprint of metal manufacturing and contributing to a greener future.”
www.cnpcpowder.com
a great foundation over these years through hard work, dedication and perseverance. Everyone should be very proud of their contribution in reaching this important milestone. I look forward to continuing the journey!”
The company stated that as it marks this significant anniversary, it looks ahead with optimism and excitement. “With a clear vision, Höganäs is committed to driving positive change through material innovation and setting the stage for continued growth in the years to come.”
www.hoganas.com
CNPC has finalised the facility expansion at its Anhui campus (Courtesy CNPC)


Roger Dubuis utilises Powder Metallurgy for Excalibur Double Tourbillon Cobalt watch case
Luxury watch maker Roger Dubuis, based in Geneva, Switzerland, has unveiled a limited edition of its Tourbillon watch featuring a cobalt chrome case made using Powder Metallurgy.
The Excalibur Double Tourbillon Cobalt has a 45 mm case that is reported to be produced using a Powder Metallurgy process. The use of PM gives the case a silvery-grey colour and creates a
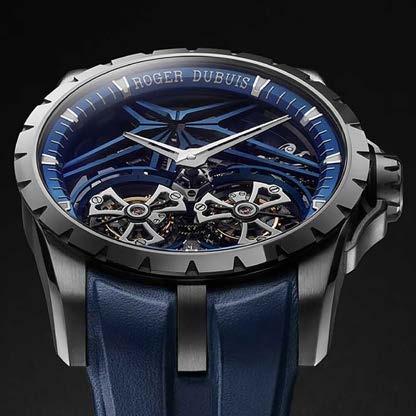
Dubuis
completely homogeneous material without impurities.
The Roger Dubuis designers paired the alloy with cobalt-blue details to emphasise the materials used for the case.
With a limited run of just twenty-eight, the Roger Dubuis Excalibur Double Tourbillon Cobalt has a retail price of €264,585.
www.rogerdubuis.com
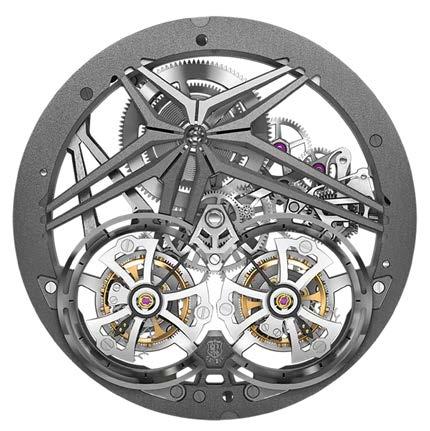
Sumitomo Electric’s A.L.M.T. Corp acquires Esteves Group
Sumitomo Electric Industries, Ltd, headquartered in Osaka, Japan, has announced that its wholly owned subsidiary, A.L.M.T. Corp, has completed the acquisition of all the shares of Esteves Group from Diamond Tools Group B.V., The Netherlands.
Esteves Group manufactures precision diamond tools for the wire and cable industry. Its product portfolio includes wire drawing dies, extrusion tools, and speciality tools. The company has been in existence for more than 100 years and has seven strategically located facilities in six countries in Europe, North America, and Asia.
Through this acquisition, A.L.M.T. Corp will use both companies’ diamond die product lineups, technological capabilities, sales networks, and service bases to further strengthen its global business development, including expanding sales channels in Europe and the United States.
The company added that the Esteves Group brand will continue to be used after this acquisition, and there will be no major changes to the existing service and support structure.
www.allied-material.co.jp www.sumitomoelectric.com www.estevesgroup.com
€7.3 M
An EU project coordinated by the European Powder Metallurgy Association (EPMA) has been granted €7.3 million. The funding, divided between thirteen partners under the REPTiS project, is intended to support the responsible extraction and processing of titanium and other primary raw materials for sourcing EU industrial value chains and strategic sectors. In addition to the EPMA, key participants include Ukrainian titanium producer Velta and global aerospace manufacturer GKN Aerospace.
Together, the companies are required to use the grant to demonstrate the feasibility of titanium extraction, processing, and utilisation within the EU through a partnership with Ukraine. The majority of the funding is reportedly designated for Velta and the EPMA; other recipients include companies specialising in Metal Injection Moulding and Additive Manufacturing, research centres, and universities. However, the current allocation of funding does not cover the entire €7.3 million budget.
The collaboration will focus on areas such as energy efficiency and environmental impact, titanium powder production and final product manufacturing. A life cycle assessment will be carried out from the extraction of raw materials to the final products in order to evaluate the differences between the methods used in the REPTiS project and conventional practices.
The project is funded under the EU’s Horizon Europe programme and is scheduled to run for four years, with a planned end date of August 31, 2028.
european-union.europa.eu www.epma.com www.velta.us
The Roger
Excalibur Double Tourbillon Cobalt watch features a 45 mm case made from cobalt chrome using a PM process (Courtesy Roger Dubuis)

American Isostatic Presses expands Ohio manufacturing facility
American Isostatic Presses Inc (AIP), headquartered in Columbus, Ohio, USA, has announced that it recently expanded its manufacturing operations in central Ohio.
“With this new expansion, we look forward to continuing meeting the unique demands of our diverse customer base, ensuring highquality and comprehensive isostatic pressing solutions,” the company stated in a release.
A provider of Hot Isostatic Pressing equipment, AIP also installs every system it sells. The company reports that it has never experienced failure on the part of any of its pressure systems or subsystems.

AIP holds ASME U1, U2 and U3 code stamps, US National Board approval, and European Union PED certification. Its systems have been tested by F2 Labs for UL and CE compliance and is reputedly the only company certified by South Korea for high-pressure vessels. AIP is also in application for Chinese certification.
Beyond its Ohio headquarters, the AIP family of companies consists of Isostatic Pressing Services (IPS) in Oregon City, Oregon; Isostatic Toll Services (ITS) in Olive Branch, Mississippi; and Isostatic Toll Services Bilbao SL, Bilbao, Spain. ITS Bilbao is a collaborative effort bringing the company into the EU. www.aiphip.com

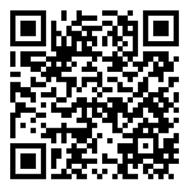
AIP has expanded its Ohio headquarters (Courtesy American Isostatic Presses)
KOMAGE begins shipping new HMI system for powder compacting presses
German press manufacturer KOMAGE Gellner Maschinenfabrik, located in Kell am See, Germany, has begun delivering its first presses featuring a new Human Machine Interface (HMI), which was unveiled at the recent Ceramitec exhibition.
The new HMI, with a modern and clean design, includes a larger visualisation panel allowing the operator to have more information available on the same page. On the hardware front, the prominent side LED strips indicate the working status of the press.
In terms of security and access control, the new HMI panel includes an RFID sensor that enables users to log in quickly. Depending on the user’s access level, some areas of
the software may be restricted. Regardless of the user, all software changes are recorded and can be audited later.
The new software has been designed as an upgrade of the current software to ensure a smooth transition for users. The main functions, such as the main structure of the software menus, the setup and programming pages, and the custom functions, remain unchanged.
A significant number of new features are available, such as the graphic simulation of the press cycle to help avoid programming errors and the oscilloscope function for fine-tuning the press cycle or troubleshooting by the customer’s maintenance team.
m4p material solutions secures funding to expand metal powder production
m4p material solutions GmbH, with operations in both Austria and Germany, has announced it has received a €3 million investment from Finindus NV and Berkau Beteiligungs GmbH. In addition to the financial backing, the investors will bring valuable connections in the metallurgical and Additive Manufacturing sectors, along with extensive experience in supporting the growth of emerging companies.
m4p specialises in advanced metal powders for industrial Additive Manufacturing. It offers a portfolio of over 160 products designed and manufactured specifically for Laser Beam Powder Bed Fusion (PBF-LB) applications and used by over 400 customers.
The company develops and produces standard alloys optimised for Additive Manufacturing as well as customised powders which are tailored to specific applications.
The additional funding will facilitate the expansion of m4p’s geographical presence into North America and Asia, the introduction of new innovative alloys for Additive Manufacturing and the support of additional AM technologies besides PBF-LB. Furthermore, m4p will deploy its fully digitised business processes, improving the supply chain and quality experience for existing and new customers.
“m4p impressed us with their strong position in their home market, which we quickly understood is due to their unwavering commitment to customer satisfaction, paired with a profound understanding of both materials and processes,” said Roel Callebaut, Senior Investment Manager at Finindus. “By seamlessly integrating flexibility with stringent contamination control of powders and minimising batch variability

KOMAGE has begun delivering presses with its new Human Machine Interface (Courtesy KOMAGE)
Another new feature is the possibility for the user to select the information seen on the main screen, with access to the new KOMConnect features also available.
www.komage.de
they empower their customers to focus on what they do best: building exceptional parts.”
Andreas Berkau, of Berkau Beteiligungs, added, “As one of m4p’s first customers, I have been able to follow the company’s development closely over the years. I have been particularly impressed by the fact that m4p has managed to build up an excellent reputation among users, service providers and machine manufacturers in recent years. I look forward to supporting m4p in the coming years with both capital and technical expertise.”
Philipp Tschertou, CEO of m4p, shared, “We are honoured to have Finindus and Andreas Berkau as new shareholders, as they bring their market knowledge and experience on top of the financial funding for further market penetration. We are looking forward to a successful and rewarding cooperation with our top class shareholder group for the benefit of our customers.”
www.metals4printing.com

GelSight and Flexxbotics partner for autonomous robotic precision inspection
Tactile intelligence technology provider GelSight, Waltham, Massachusetts, USA, has announced a partnership with Flexxbotics, Boston, a provider of scaled digital solutions for robot-driven manufacturing. This partnership will focus on providing a solution for robot-enabled non-destructive testing (NDT) with autonomous control, incorporating GelSight’s tactile sensing technology into Flexxbotics machinery. The resultant precise quality and digital thread traceability is anticipated to reduce inspection time by 40%.
“Together, GelSight and Flexxbotics provide a new level of inspection productivity, scrap reduction, and cost savings powered by tactile sensing and production robotics,” said GelSight CEO Youssef Benmokhtar. “Now, even the most challenging aspects to dimensionally measure accurately can be consistently inspected in a fraction of the time using robotics.”
Next-generation smart factories in industries where measurement accuracy is critical in tight tolerance processing often use industrial and collaborative robots to dramatically speed up inspection processes, increase throughput, and improve margins. GelSight’s technology uses 3D imaging to map surface finish and defects on any materials at the micron level.
By robot-enabling GelSight’s tactile sensing devices with Flexxbotics, users can quickly perform hundreds of precision measurements during processing on the production line, as opposed to transporting parts to utilise specialised lab equipment or relying on outside laboratory services.
Flexxbotics provides interoperable communication between the robots and GelSight devices to coordinate the entire process and connect directly with existing business systems in the plant — including the CAD/PLM, QMS, IIoT and others for closed-loop quality compliance. Geometric Dimensioning and Tolerancing (GD&T) for each part is automatically fed by Flexxbotics directly into the robot and GelSight programs, enabling critical characteristic measurement integrity with inspection results collected for nonconformance tracking and analysis. Optionally, data can transfer to quality repositories and MES systems of record.
“We believe robot-driven manufacturing is the future, and our partnership with GelSight combines some of the most advanced automated inspection capabilities on the planet with Flexxbotics production robotic orchestration for next level factory autonomy,” added Tyler Bouchard, CEO & co-founder of Flexxbotics. “Using GelSight tactile sensing to inspect during production enables robots to achieve micron-scale measurement accuracy, bringing autonomous process control with Flexxbotics to the most complex geometry parts.”
www.gelsight.com | www.flexxbotics.com
Tooling for Powder Compacting Technology
• Simple, quick set-up
• High accuracy
• Low scrap rate
• Maximal machine utilization
• Increased productivity
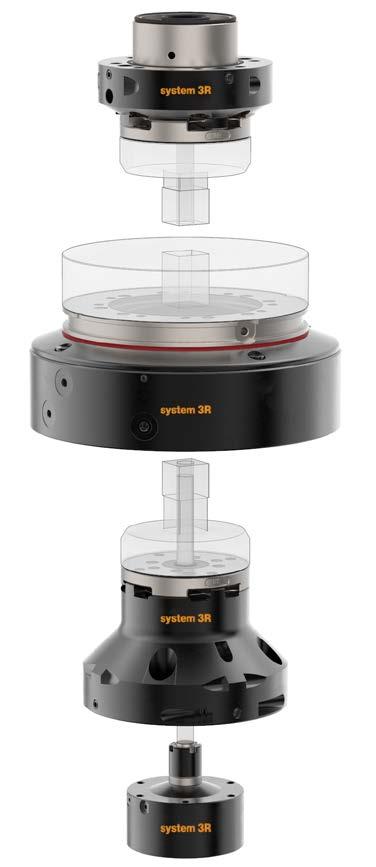
www.system3r.com
Upper punch with Macro
Die with Matrix
Lower punch with Macro Core rod
Continuum to open sustainable metal powder production facility in Houston
Continuum Powders has announced the grand opening of its global headquarters and manufacturing facility will take place on December 5th in Houston, Texas, USA. Reported to be North America’s largest sustainable metal powder production facility, the company will offer guests the chance to see the company’s low-carbon production methods firsthand.
The completion of the Houston facility is said to reflect the company’s commitment to environmental responsibility, with the entire building operating as a green manufacturing centre. Net-zero carbon energy partners and lowemission gas systems are integrated throughout, enabling the plant to have a very low carbon footprint.
The site is also pursuing green certification goals and is designed to maximise energy efficiency through renewable energy usage and advanced recycling initiatives.
Continuum also stated that the opening of the new facility marks a significant step forward in delivering sustainable solutions that meet the demands of a rapidly evolving industrial landscape. With increased production capacity and multiple US locations, the company is now positioned to deliver products faster at reduced shipping costs, enhancing supply chain resilience for customers.
“Our new Houston facility not only expands our production capabilities but also allows us to scale our

PyroGenesis rebrands and relocates HQ
Canada’s PyroGenesis, headquartered in Montreal, Quebec, has announced that its name has been officially changed to PyroGenesis Inc from PyroGenesis Canada Inc. Simultaneously, the French version of the company’s name has changed to PyroGènese Inc. from PyroGènese Canada Inc.
“This change to our name is a subtle but important change as it better reflects who we are and what we are doing,” stated P Peter Pascali,
President and CEO of PyroGenesis. “With sales across twenty-one countries and counting, this name change is part of an initiative to better express in all areas of communication that we are an internationally focused company with global reach.”
This name change does not involve any restructuring, change of control, or other corporate reorganisation. This decision solely pertains to a more inclusive and internationally resonant brand image. The name change does not affect the trading of the company’s shares. The shares will continue to trade on the TSX under the symbol PYR and through the OTCQX under the symbol PYRGF. The new corporate name was effec -
mission of decarbonising the manufacturing industry,” said Rob Higby, CEO of Continuum Powders. “We are committed to providing high-quality, cost-competitive metal powders while minimising environmental impact. Our technology represents a distinct advantage in the market, offering sustainable solutions that align with the needs of forwardthinking industries.”
The facility features Continuum’s proprietary Greyhound M2P (melt-topowder) plasma atomisation process, which enables the repurposing of alloyed metal waste-stream products into high-quality metal powder in a single step. By enabling a cradleto-cradle process, the platform can reduce the need for transportation, product handling, primary melting, and extensive long bar processing operations, while also minimising the environmental impact by reducing the mining of elemental metal resources.
“Houston represents a leap forward in our operational efficiency and sustainability efforts,” said Rizk Ghafari, COO of Continuum Powders. “By combining state-of-the-art technology with our commitment to decarbonisation, we are not only supporting our customers’ needs but also setting a new benchmark for responsible manufacturing in the industry.”
www.continuumpowders.com
tive on the Canadian and US capital markets as of November 11, 2024, with no change to the stock symbols. Additionally, the company announced that it has recently moved its headquarters to a larger location in downtown Montreal. The move comes as a result of the company outgrowing its previous headquarters after more than thirty years in Montreal’s historic Griffintown neighbourhood. The new office location resides in the heart of downtown and provides more modern amenities and a smarter office layout, while also providing easier access for employees and customers that use public transport.
www.pyrogenesis.com
The new Continuum Powders site is reported to be North America’s largest sustainable metal powder production facility (Courtesy Continuum Powders)
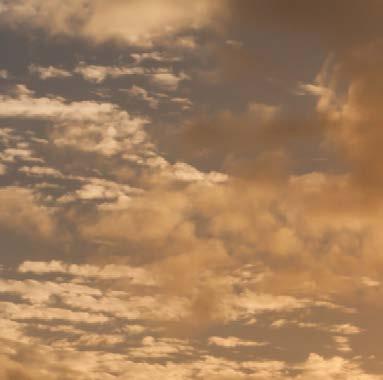


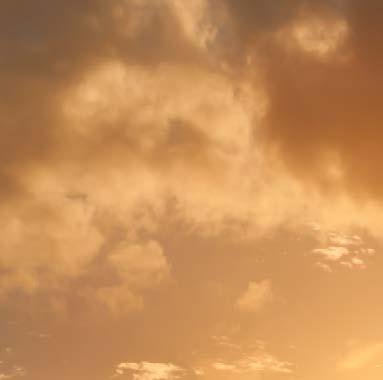


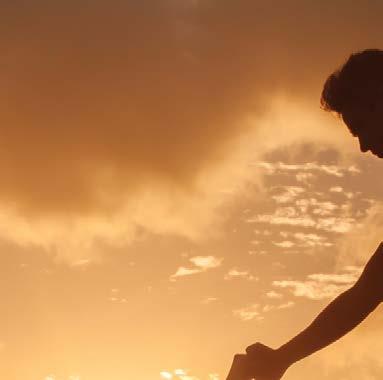


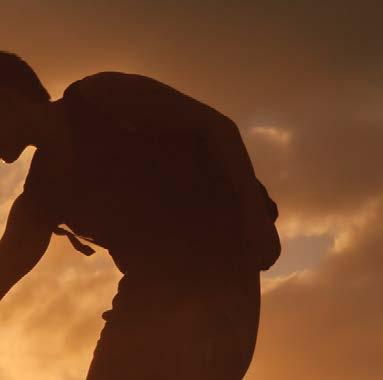

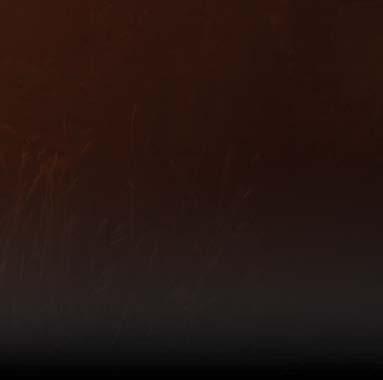
A remarkable milestone
A quarter of a century. We could have only accomplished this by forging solid partnerships, friendships and collaborations build on trust, integrity and commitment.
DSH Technologies is the GO-TO support team for helping to process metal powder parts and materials. Real world solutions to real world problems, we can help solve technical, process and engineering related issues.
• Remote or In-Person process support
• Toll Debind and Sinter Services – “You Print It, You Mold It – We Debind & Sinter It”
• In person facility walk through, process evaluation, and education programs
For the past twenty five years, DSH is the only source for the best process support, toll processing and educational resource for your MIM and Metal AM applications.
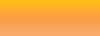





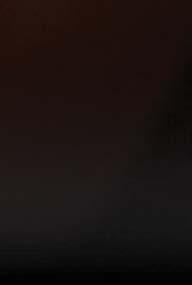
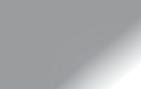




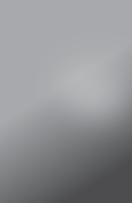












Ipsen USA introduces regional Service HUBs to expand customer support
Ipsen USA, Cherry Valley, Illinois, USA, has formally launched its Service HUB model, marking a shift in how the company will deliver service and support to customers in the US. To support the rollout of the Service Hub model, Ipsen also introduced its Technical Development Center (TDC) training initiative.
Over the past two years, Ipsen has developed the regional HUB model concept under the direction of Ipsen Global CEO Geoffrey Somary. Now, led by CSO John Dykstra, the HUBs will provide services across a large portion of the American Midwest and Southeast, particularly in areas with a high density of Ipsen customers.
This move to regional service centres is intended to enable quicker response times, dedicated support teams and thorough knowledge of each customer’s facility. This more tailored response is expected to reduce customer downtime and optimise heat-treating operation performance whilst also improving the quality of life of its Field Service Engineers (FSEs).
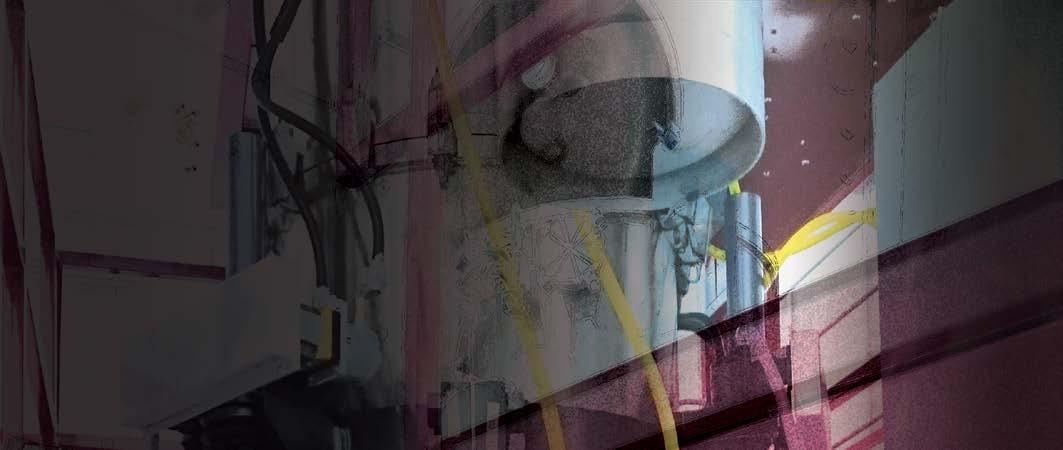
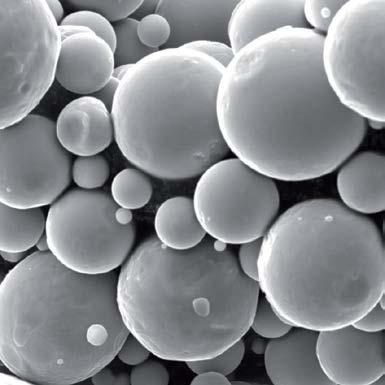
Our powder is:
Spherical •
Free-flowing •
•
Due to the efficiency of our cuttingedge technology we can offer the lowest priced powder on the market with no compromise in quality.
D50 of 35µm for most materials
• Has high tap density •
D50 of 20µm for titanium super alloys
We process directly from: Raw elemental material
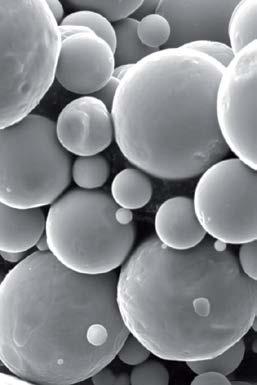
We can handle refractory and reactive alloys
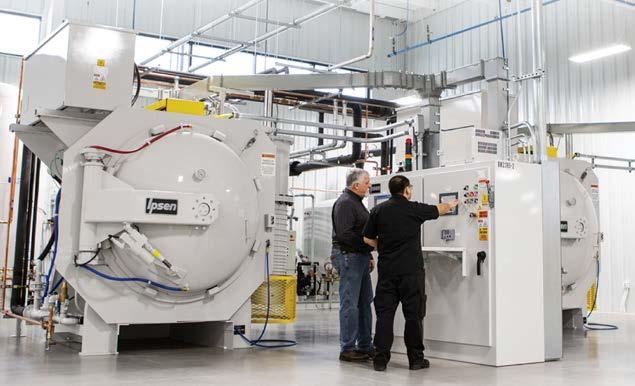
Ipsen USA has formally launched its regional Service HUB model for US customers (Courtesy Ipsen USA)
The Ipsen Technical Development Center (TDC), is an initiative led by Darci Johnson, Program and Transformation Manager, and Cavan Cardenas, Technical Training Lead. The TDC is focused on training and developing new Field Service Engineers (FSEs), including the launch of the Field Service Engineer Academy, a specialised programme intended to equip new and current technicians with the skills and knowledge to best serve customers within the HUB model.
www.ipsenglobal.com
Sandvik revises AM strategy as it divests BEAMIT
Sandvik AB has announced a revised Additive Manufacturing strategy, with its focus returning to metal powder production. As a result, it has announced the decision to exit its minority stake (approximately 30%) in the Italian Additive Manufacturing service provider BEAMIT. Sandvik has been a shareholder in BEAMIT since 2019. As part of a wider strategic shift, the engineer-to-order business of DWFritz Automation (DWFritz) has also been divested.
Charges totalling approximately SEK 390 million will be accounted for in the third quarter and reported as items affecting comparability. Out of the total charges, approximately SEK 250 million relates to a capital loss, including transactional costs, from the divestment of DWFritz, and about SEK 140 million relates to a write-down of the stake in BEAMIT.
Sandvik has sold DWFritz’s engineer-to-order business to the US-based private equity firm Balmoral Funds. It bought DWFritz in 2021 to expand its ZeroTouch business. The ZeroTouch platform is a unique inspection gauging equipment that enables near-line and in-line metrology and is an important part of Sandvik’s closed-loop strategy.
www.home.sandvik

GKN PM develops high-performance Porous Transport Layers for green hydrogen production
GKN Powder Metallurgy has announced the development of a new generation of high-performance, high-porous, and high-purity Porous Transport Layers (HP-PTL) for Proton Exchange Membrane (PEM) electrolysis. The solution, developed from a decade of research, is designed to improve hydrogen production by increasing efficiency and reducing overall environmental impact. By significantly reducing the required amount of catalyst materials such as iridium, GKN’s HP-PTL lowers stack costs, increasing the affordability of advanced PEM electrolysers compared to traditional solutions.
Utilising Powder Metallurgy, the HP-PTL has a highly porous structure comprised of a fine powder
layer which increases surface area connectivity. This design also reduces electrical resistance, meaning it requires a lower voltage to produce equal amounts of hydrogen, reducing energy consumption and improving the overall efficiency of electrolysis stacks.
The microstructure shows a high titanium surface in addition to a high porosity. This results in a further reduction of electrical and mass transport resistance, leading directly to a system efficiency increase of up to a reported 30% when compared to current metal sheet solutions on the market.
“Through the development of the HP-PTL, GKN Powder Metallurgy is driving the energy transition forward,” stated Stefan Zeier,
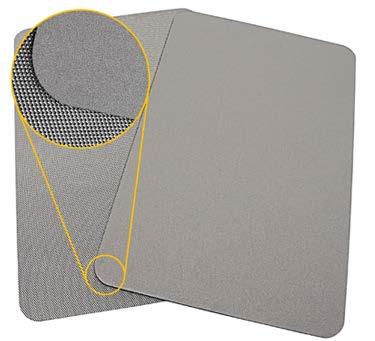
Porous Transport Layers for Proton Exchange Membrane electrolysis (Courtesy GKN Powder Metallurgy)
Senior VP Operations. “By reducing operational costs and enhancing the efficiency of PEM electrolysis, this innovation plays a crucial role in making renewable hydrogen production economically viable. As a result, it opens new possibilities for a safer, more cost-efficient future based on environmentally sustainable energy.” www.gknpm.com
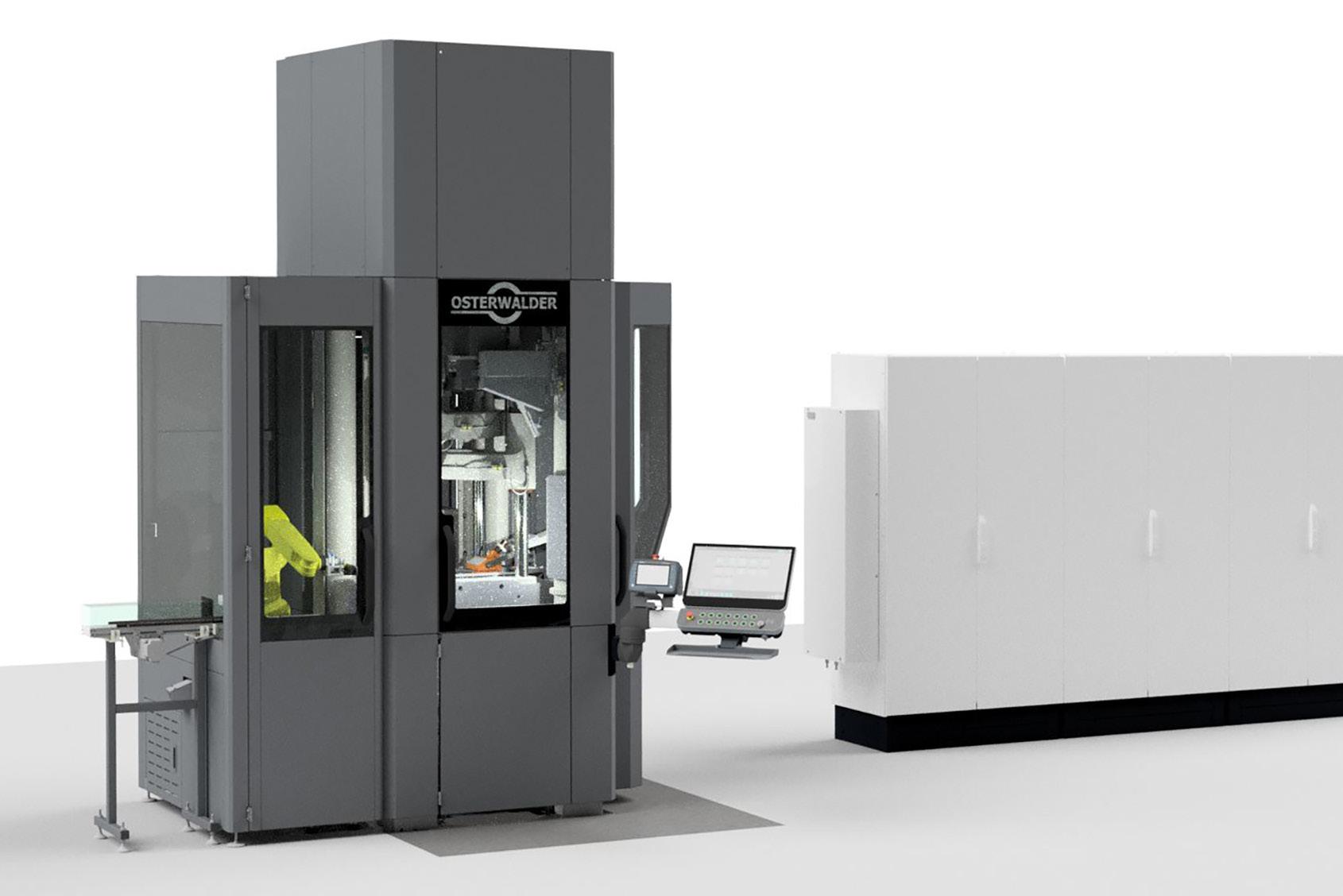
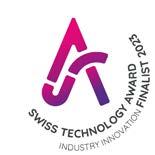
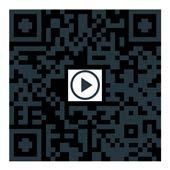
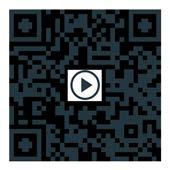
Airbus and Plastometrex collaborate on standardisation of PIP mechanical test
Plastometrex, a developer of mechanical testing solutions based in Cambridge, UK, has announced a collaboration with Airbus that is intended to streamline mechanical testing processes and enhance material insights. The partnership aims to support the standardisation of PIP (Profilometry-based Indentation Plastometry), a mechanical testing technique developed and commercialised by Plastometrex.
Traditional tensile testing requires test pieces that conform to precise dimensions, which adds significant expense to testing workflows, can limit the speed of a project, and can prohibit testing in various circumstances, including where samples are small or irregularly shaped.
By comparison, PIP sample preparation is said to be simpler. The test operation is more straightforward, and the entire process can be completed in just a few minutes. Also, it can test specimens directly and at a fine scale, which unlocks the
Sumitomo
testing of small or irregularly shaped pieces and enables the extraction of more data, delivering deeper insights into material behaviour. For example, 160 PIP tests can be fitted onto a standard ASTM E8 tensile coupon, unlocking information about material homogeneity that would be obscured by the single stress-strain curve obtained when tensile testing this part.
Through PIP, Airbus will accelerate testing workflows and enable the generation of richer data, supporting innovation and advancing the highest levels of safety in aerospace engineering.
Dr Jimmy Campbell, CTO at Plastometrex, shared, “We are thrilled to collaborate with Airbus on standardising PIP. This partnership highlights the transformative potential of our technology, enabling faster, more versatile, and data-rich testing. Together, we’re setting a new standard in mechanical testing that aligns with the rigorous demands of the aerospace industry.”
reports rise in sales of Powder Metallurgy components
In its Integrated Report 2024, Sumitomo Electric Industries, Ltd, headquartered in Osaka, Japan, has reported a year-on-year rise in the sales of Powder Metallurgy components. In 2023, the company posted net sales of sintered powder metal parts at 82.9 billion yen (around $555 million), up
from 75.1 billion yen (approx $503 million) in 2022.
There was, however, a small fall reported in the category of cemented carbide tools, diamond and CBN tools, and laser optics. The company reported that in 2023, net sales for this segment totalled 110.2 billion yen (approx $738
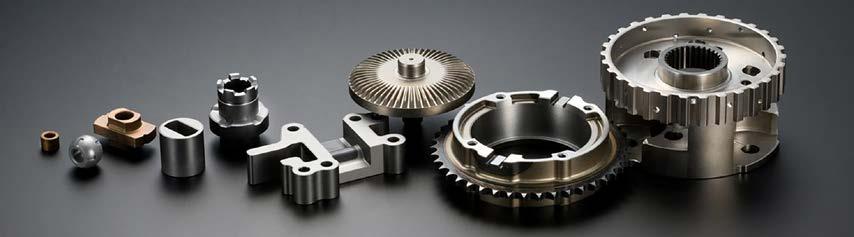
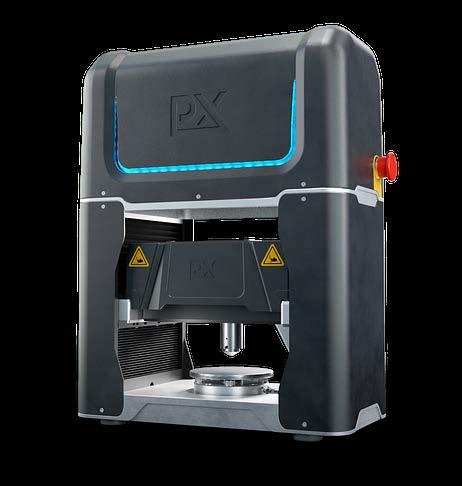
The PLX-Benchtop by Plastometrex which uses the PIP mechanical testing technique (Courtesy Plastometrex)
This collaboration between Airbus and Plastometrex is said to mark a significant advancement in mechanical testing. It offers a streamlined, cost-effective, and data-rich complement to traditional methods. As both companies work together, this new approach looks to improve testing efficiency and deliver more detailed insights into material behaviour, benefitting aerospace projects worldwide.
www.plastometrex.com www.airbus.com
million), down from 113.1 billion yen (around $757 million) in the previous year.
In the sintered products division, Sumitomo stated that it plans to develop new products for electric vehicles and non-vehicle use applications. It also announced it will review the production structure to enhance cost-competitiveness.
Regarding the cemented-carbide tools sector, Sumitomo added that it aims to expand global sales, develop new markets such as electric vehicles, and increase market share.
Responding to the growing demand for machining in India, Sumitomo also reported that it had established a cutting tool sales company in Navi Mumbai and began operations to better serve local customers.
www.sumitomoelectric.com
Sumitomo reported a year-on-year rise in sales of Powder Metallurgy components, but slight fall in cemented carbide and diamond tools (Courtesy Sumitomo Electric Industries)

High Pressure Heat Treatment: Enhancing AM/PM reliability and performance
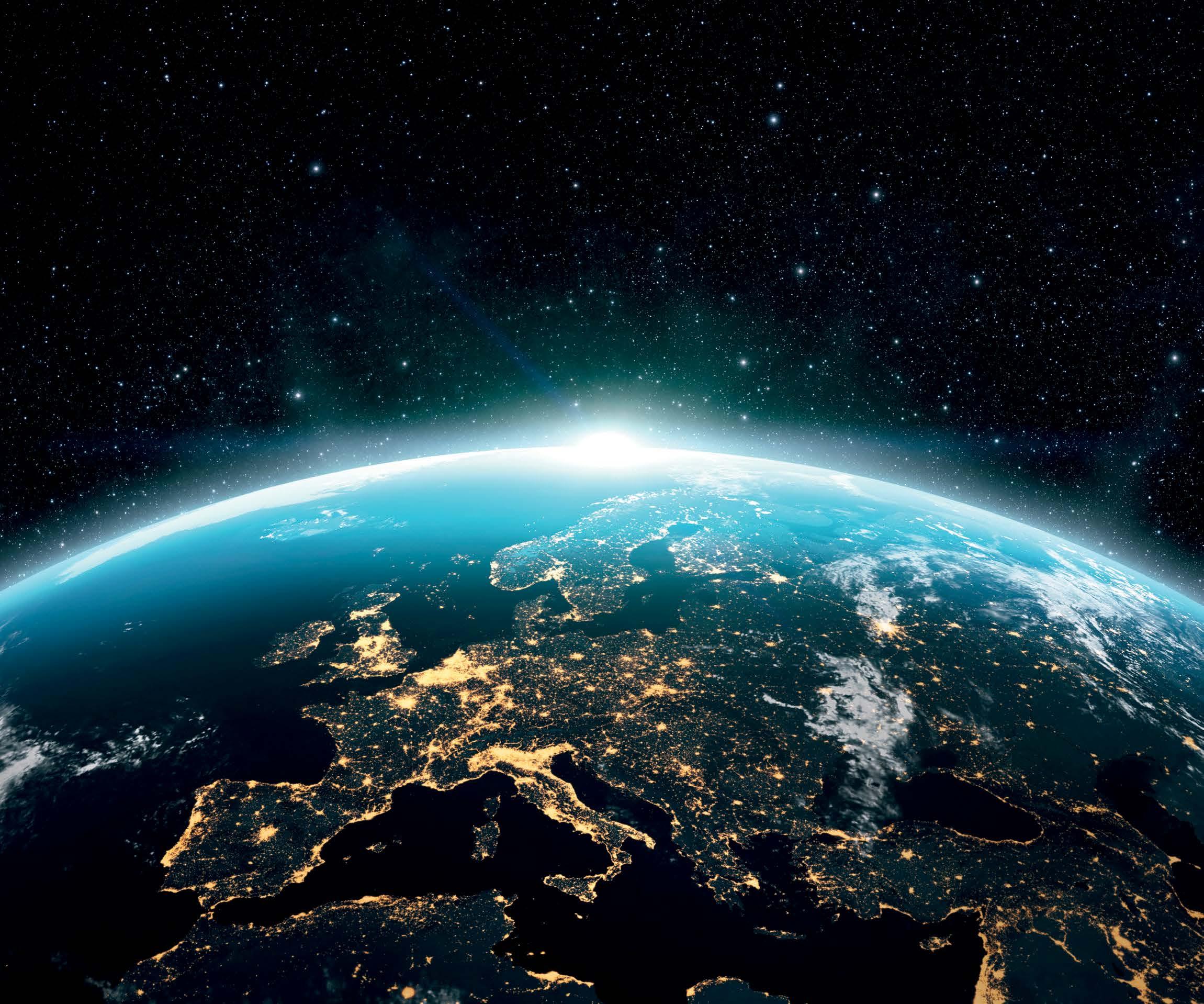
Reaching full density and uniform microstructures of your AM/PM components even with complex shapes with Quintus High Pressure Heat Treatment (HPHT TM) solution!
By combining Hot Isostatic Pressing with the heat treatment process in a single cycle, you can produce high-quality AM/PM parts more efficiently, achieving consistent material properties throughout the component while minimizing costs and lead times. This solution is vital for processing advanced and high-performance alloys in critical applications across aerospace, automotive, energy, and medical industries.
Find out more about Quintus HIP and HPHTTM capability on our website.
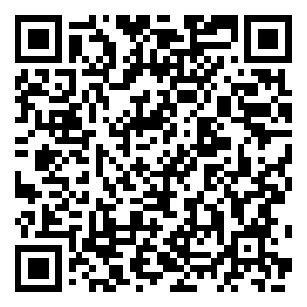
Gränges invests in post-processing line for aluminium Additive Manufacturing powders
Gränges Powder Metallurgy SAS, based in Saint-Avold, France, has invested in a new post-processing line used in the production of aluminium powders for Additive Manufacturing. The post-processing line includes ATEX-classified sieving, homogenising and packing equipment in a closed workspace to ensure the highest safety and cleanliness. The line is planned to be fully operational in the first quarter of 2025.
Gränges Powder Metallurgy has been producing high-performance Powder Metallurgy aluminium alloys by inert gas atomisation for over thirty years. The company is mainly known for the Dispal range of low-thermal expansion AlSi alloys, commonly used in the semi-conductor and precision
optics industries. As well as Dispal, standard AlSi10Mg powder and customer-specific aluminium alloys are also produced.
“The investment is a step in our ambition to become a leading producer of aluminium AM powders. With the investment, Gränges can supply large quantities of homogeneous, spherical aluminium powders with sharp powder size cuts and processed under inert gas,” said Peter Vikner, Managing Director, Gränges Powder Metallurgy. “The dedication to aluminium alloys guarantees cleanliness from crosscontamination with other alloys. It also enables synergies in raw material purchase, in processing and in R&D, ensuring that we have the right capacity, price and quality for the market.”

Gränges Powder Metallurgy has invested in a new post-processing line for the production of aluminium powders for AM (Courtesy Gränges Powder Metallurgy)
Gränges Powder Metallurgy is part of the Gränges Group, an organisation dedicated to aluminium with a total net sales in 2023 of MSEK 22,518 and an operating profit of MSEK 1,576 (€1.92 billion and €135 million, respectively). The plant in Saint-Avold, France, is dedicated to aluminium powder production and spray forming with a total capacity of 3,500 metric tonnes per year. www.granges.com
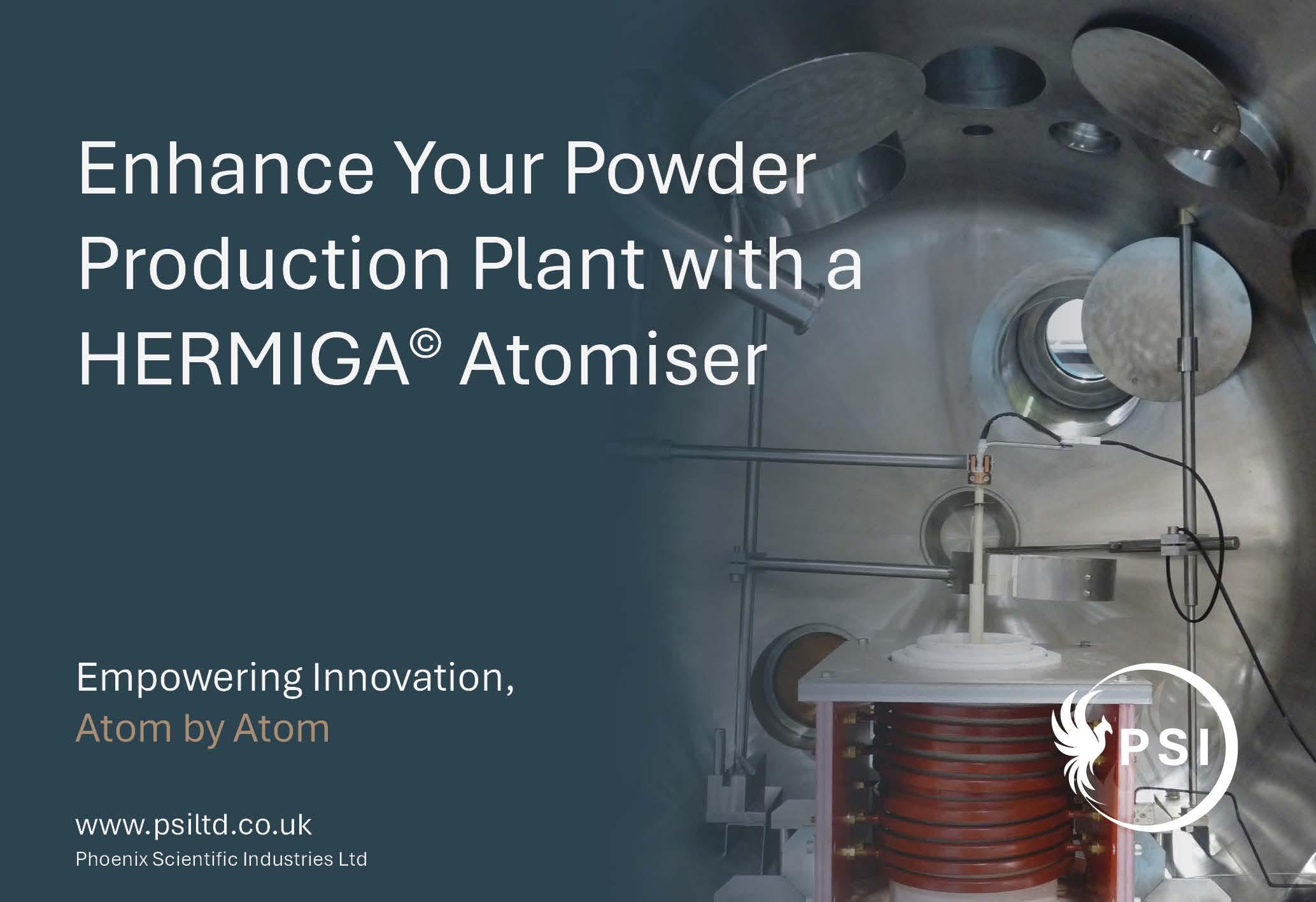

CNPC to manufacture APWorks’ Scalmalloy powder
CNPC Powder, headquartered in Vancouver, Canada, has formed a strategic alliance with APWorks GmbH, based in Taufkirchen, Germany, to manufacture and commercialise Scalmalloy, its high-performance aluminium-magnesiumscandium alloy developed for Additive Manufacturing.
“We are excited about this agreement with APWorks and an impressive milestone for the company to expand our portfolio and production line with the manufacturing of an important material such as Scalmalloy,” stated Kathy Liu, General Manager of CNPC Powder. “We are also prepared for possible future joint development of new Scalmalloy formulations.”
Developed for Additive Manufacturing, Scalmalloy has a proven track record in a wide range of applications in aerospace, robotics, marine and motorsport, and is an approved material under the FIA regulations. Combining high strength with excellent ductility and processability, it is said to be an ideal material for use in highly loaded and safety-critical parts.
Jon Meyer, CEO of APWorks, added, “We see this agreement as important for the industry. CNPC has demonstrated a high level of quality control and their powder is achieving excellent results. We look forward to working with CNPC to further improve the economics and availability of Scalmalloy powder, for the benefit of the industry as a whole.”
www.cnpcpowder.com www.apworks.de
Pfeiffer Vacuum rebrands to Pfeiffer Vacuum+Fab Solutions
Pfeiffer Vacuum, a member of the global Busch Group based in Asslar, Germany, has announced a rebrand into Pfeiffer Vacuum + Fab Solutions.
Intended to reflect Pfeiffer’s comprehensive portfolio of both vacuum solutions and semiconductor fab solutions, the rebrand marks the seventieth anniversary of the company’s first major development of a turbomolecular vacuum pump.
Today, Pfeiffer is a global provider of solutions for high and ultra-high vacuum technology with a product portfolio including leak detectors, measurement and analysis devices, components, as well as vacuum chambers and systems.
“Our new logo is more than just a trademark. It tells our story, which began with the invention of the turbopump and became a global success. Our teams design and manufacture products that are used in the world’s most high-tech applications and future megatrends, exploring the frontiers of knowledge,” explained Wolfgang Ehrk, CEO of Pfeiffer. www.pfeiffer-vacuum.com
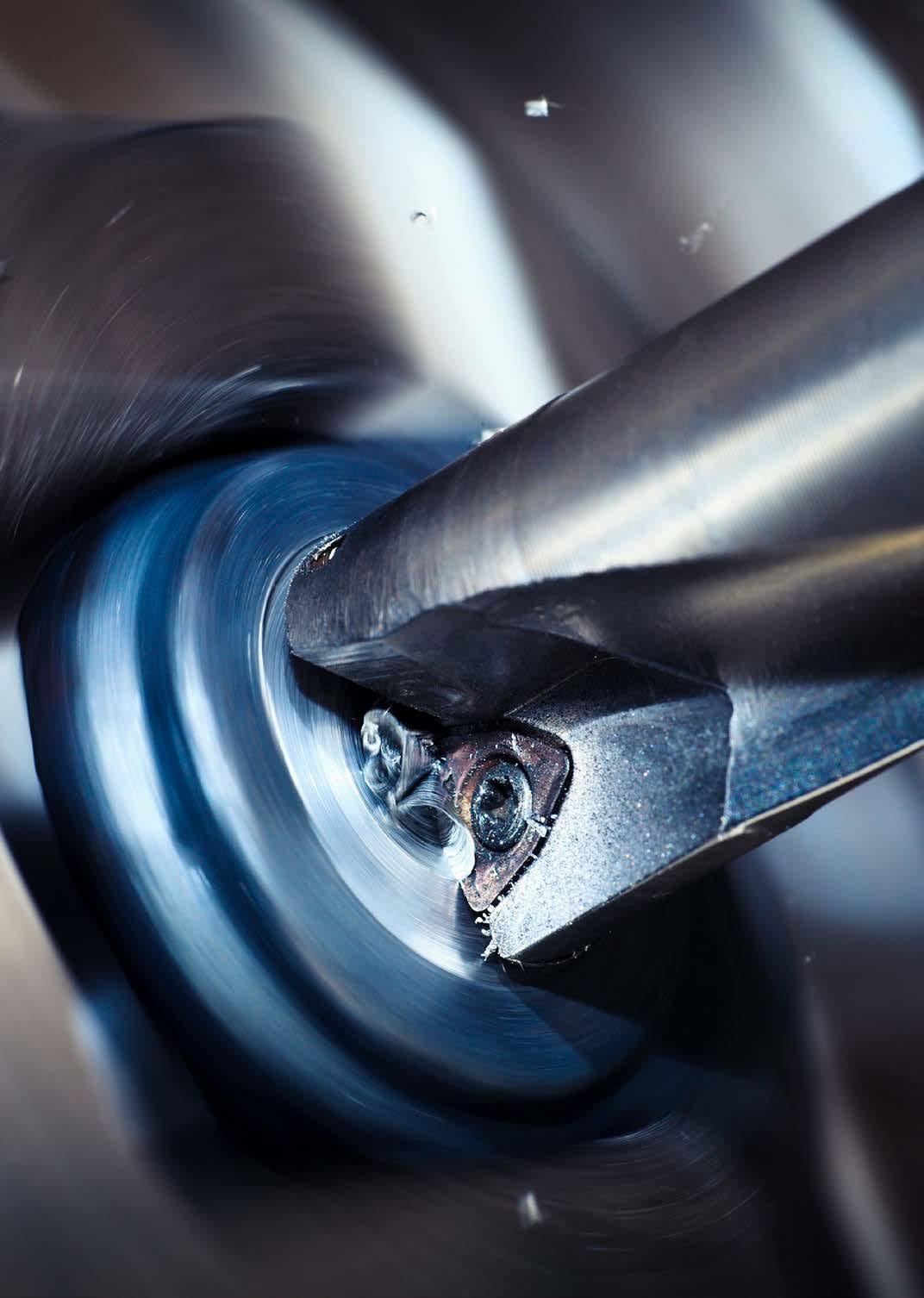
Powder engineering expertise.
GEA is a worl-leading specialist in powder engineering with exceptional patented Spray Drying Solutions. Be it a powder, a granulate or an aglomerated product, our solutions define and deliver superior quality powders to your exact specifications in the most energy-and-costefficient way.
California Nanotechnologies opens state-of-the-art spark plasma sintering facility
California Nanotechnologies Corp (Cal Nano), based in Cerritos, California, USA, has announced the commissioning of its new manufacturing facility in Santa Ana, California. The new facility is now operational and houses a large-scale MSP5 Spark Plasma Sintering (SPS) machine and cryomills.
The commission marks an important milestone in expanding its manufacturing capabilities and footprint. The expansion provides the necessary infrastructure to operate its recently purchased equip -
ment and creates additional space for potential production requirements, warehousing, and custom tooling. This infrastructure includes increased electrical current capacity, liquid nitrogen storage, and other associated upgrades.
Dr Fritsch GmbH & Co. KG, headquartered in Fellbach, Germany, supplied the new MSP5, which is the largest SPS press built by Dr Fritsch.
“We are proud to open a first-ofits-kind facility in North America, which will bring commercial access to state-of-the-art technologies and
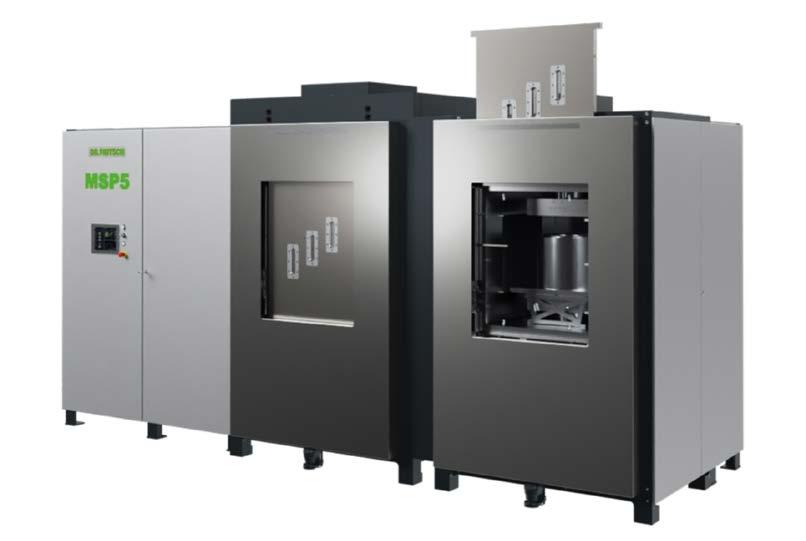
Expansion of HIP and vacuum heat treatment capabilities at ITS Bilbao
Isostatic Toll Services Bilbao SL (ITS Bilbao), Spain, has announced that it intends to commission its fourth MEGA Hot Isostatic Pressing (HIP) unit within the next three years and, by Q2 2025, to commission a fully molybdenum vacuum heat treatment furnace from TAV. Its first heat treatment unit, the 1200 x 1600 x 1200 mm furnace will feature a maximum vacuum of 10-5 mbar, making it suitable for titanium. This additional
heat treatment capability will enable ITS Bilbao to offer a combined MEGA HIP and MEGA Heat Treatment service to its HIP customers.
ITS Bilbao ran the first cycle of its MEGA HIP unit in December 2019. While the COVID-19 pandemic followed shortly after, with its impact on the aerospace sector felt by the company, demand for toll HIP services surged again following the recovery. This increased demand
machinery for processing advanced materials,” stated CEO Eric Eyerman. “We have already started to run our first parts on the new MSP5 machine for our green steel ‘cleantech’ customer. Our mission is to help clients push the boundaries of material science and innovation, and the new equipment will allow us to execute on larger volumes, batches, and part sizes.”
Cal Nano said it expects other equipment, including multiple cryomills and a mid-sized SPS2000 machine, to come online over time.
In addition, pre- and postprocessing services and custom tooling manufacturing are becoming more important aspects of the company’s manufacturing services. To complement existing processing offerings, a molybdenum wire EDM (Electrical Discharge Machine), an advanced cutting mill, and additional machining capabilities are expected to be available at the new facility for customers who require ancillary parts and services.
All these investments have resulted in a portfolio of advanced material processing technologies across its Cerritos and Santa Ana facilities. This includes the largest SPS machine commercially available for production and R&D manufacturing services, cryomills with batch sizes ranging from 0.5 kg to 25.0+ kg, and ancillary machinery and services.
www.calnanocorp.com
prompted the company to decide, in Q1 2022, to double its existing capacity. A MEGA HIP unit, identical to the original, was commissioned in the following year.
Over the following twelve months, demand for the second unit exceeded its capacity, leading to the installation of a third MEGA HIP unit in 2024. Set to be commissioned in 2025, the unit is identical to the previous, with a Ø1088 x 2570 mm loadable zone corresponding to 2.4 m 3, and an increased maximum working pressure of up to 138 MPa (20,000 psi).
www.isostatictollservices.com
The new manufacturing facility at Cal Nano will house a Dr Fritsch MSP5 Spark Plasma Sintering machine (Courtesy Dr Fritsch)


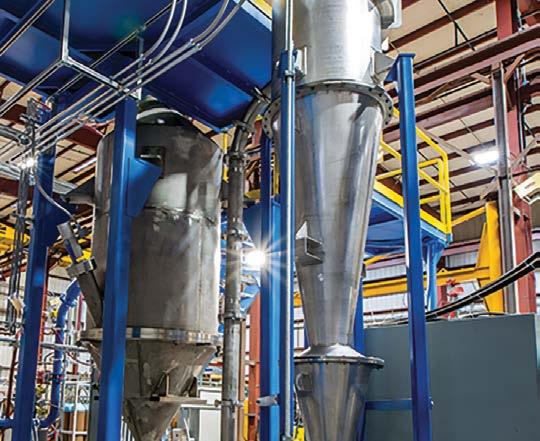
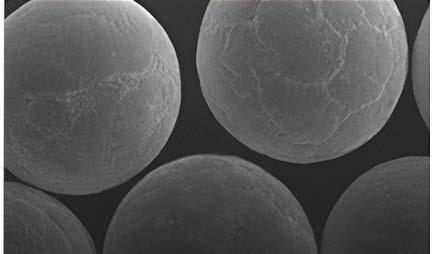


Retech’s new Plasma Gas Atomizer will atomize reactive and refractory metals faster, cheaper, and better than ever.
Our Plasma Atomization technology not only atomizes reactive and refractory metals at unprecedented rates, but includes features that eliminate many other obstacles to cost effective atomization of titanium and other refractory metals.
• Highest Throughput in the Industry – Produces powders far faster than any other available technology
• Simplified Feedstock Preparation – Accepts elemental feedstock, scrap, sponge, recycled materials and other low-cost feed
• Retech’s Proprietary Hearth Melting Technology – Production of ultra-high purity product
• Versatile Atomization of Multiple Alloys – Suitable for any alloy that can be plasma melted
ASM secures AU$5 million government grant for Dubbo rare earth project development
Australian Strategic Materials Limited (ASM) has received an AU$5 million grant under the Australian Federal Government’s International Partnerships in Critical Minerals (IPCM) Program. The grant will be matched by ASM and used to support efforts to identify potential lower capital and shorter implementation pathways to rare earth production (RE Options Assessment and Pilot Program) at the company’s Dubbo Project in New South Wales. The RE Options Assessment and Pilot Program will be conducted as a preliminary step before the Front-End Engineering Design (FEED) services contract awarded to US-owned Bechtel Mining and Metals Inc in March 2024.

The Dubbo Project is ASM’s main critical minerals deposit, which will produce a variety of rare earth and critical mineral oxides that are essential for the global energy transition. The IPCM Program was launched in February 2024 to provide funding for critical minerals businesses to develop end-to-end supply chains with Australia’s international partners.
In a media release, Minister for Resources the Hon Madeleine King MP, said, “Government support to refine rare earths is important for our sovereign capabilities and will help our trading partners meet their economic, national security and emission reduction commitments.”
The RE Options Assessment and Pilot Program will enable ASM to identify alternative, capital-efficient and nearer-term options for producing rare earth elements at the Dubbo Project before commencing the FEED services contract and conducting an updated feasibility study on the construction and operation of the Dubbo Project. The RE Options Assessment and Pilot Program will involve engineering, sampling, metallurgical testing, and a pilot programme at ASM’s pilot facility located at ANSTO, New South Wales. ASM will collaborate with international partners DRA Global and Stantec, as well as local service providers, Mining One and Core Metallurgy, to deliver this programme. These activities are critical to ASM progressing key funding activities and making a final investment decision on the Dubbo Project, which is targeted for the first half of 2026. www.asm-au.com
Huacheng Moulding (Changshu) Co.,
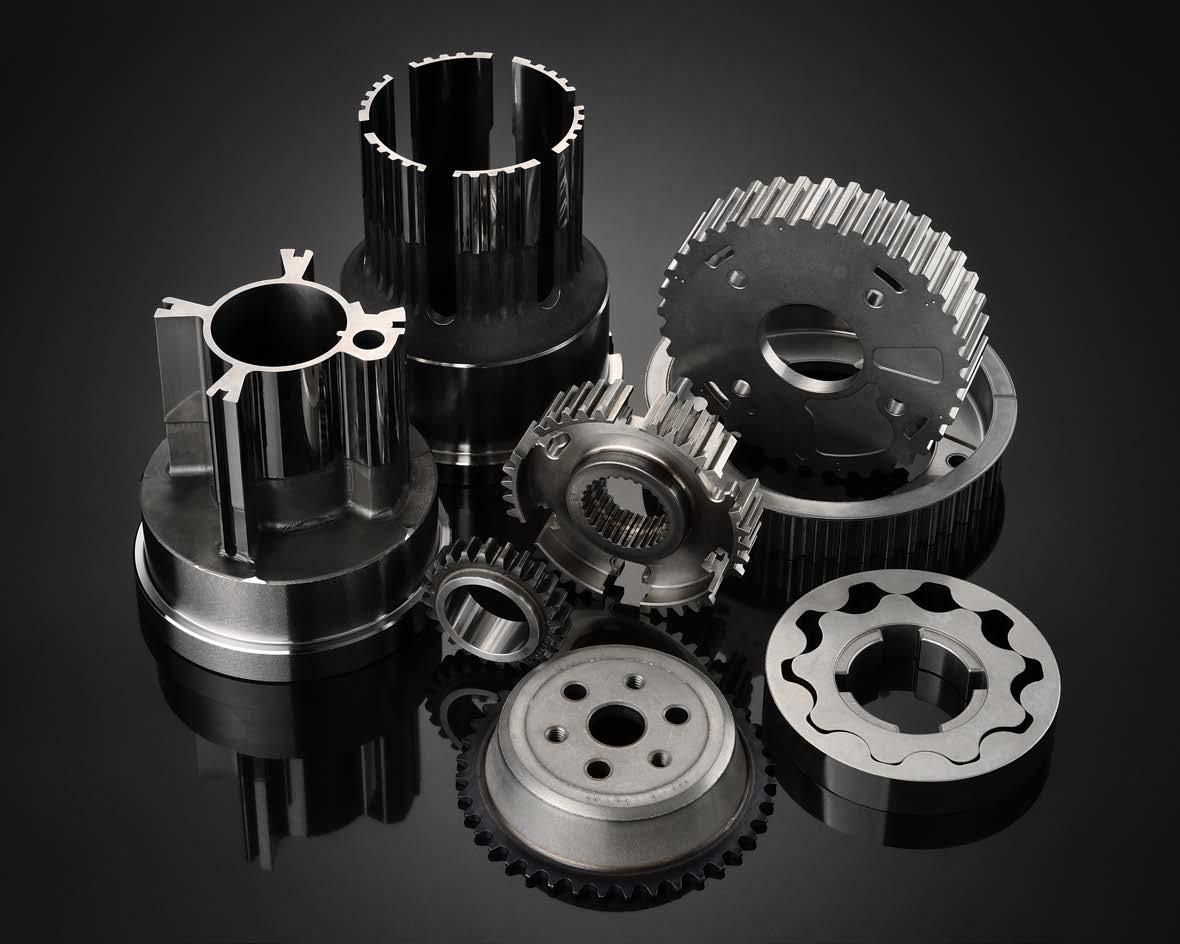
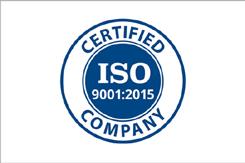
Mikron Tool unveils highperformance hardmetal tools for titanium and delicate components
Mikron Tool, based in Agno, Switzerland, has introduced three new solid hardmetal tools. The company has added the high-performance bit CrazyDrill Titanium TN/TK for all types of titanium and two highperformance mills, CrazyMill Cool CF and CrazyMill Cool SF, specially designed for delicate components.
The CrazyDrill Titanium TN/TK microdrill has been developed especially for drilling titanium alloys, including pure titanium, at diameters from 0.2 to 2 millimetres and depths of 3 x d and 6 x d. It can already be used from 15 bar internal cooling, so a high-pressure cooling lubricant system is not necessary.
The CrazyMill Cool CF (ChatterFree) is a high-performance
micro mill designed for very high machining rates and is reported to be capable of handling very challenging, delicate component structures. Its specific cutting geometry, combined with a dynamic milling process, makes it the ideal mill for delicate, thin-walled parts or parts that are not stable when clamped, which is particularly common in the medical field (bone plates), aerospace industry (structural components), and watch industry.
The CrazyMill Cool SF (Super Finishing) has been developed as a super-finishing mill that produces milled surfaces at a grinding or polishing level of quality, with roughness of less than Ra 0.3. This greatly reduces the effort required for
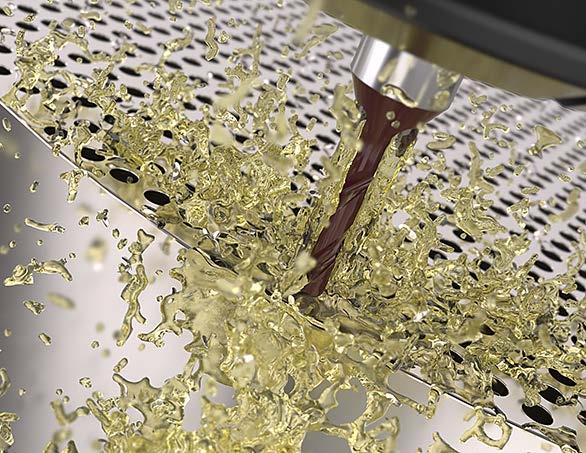
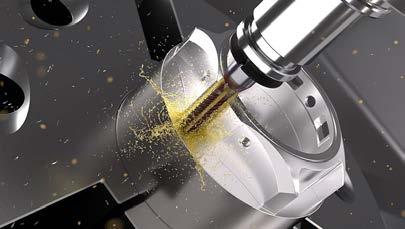
Mikron Tool has introduced three new high-performance solid hard metal tools, a drill bit and two mills (Courtesy Mikron Tool)
polishing. The CrazyMill Cool SF also produces excellent surface quality of less than 0.3 µm in (chromium) steel, lead-free brass, copper, cobaltchromium, and Inconel. www.mikrontool.com
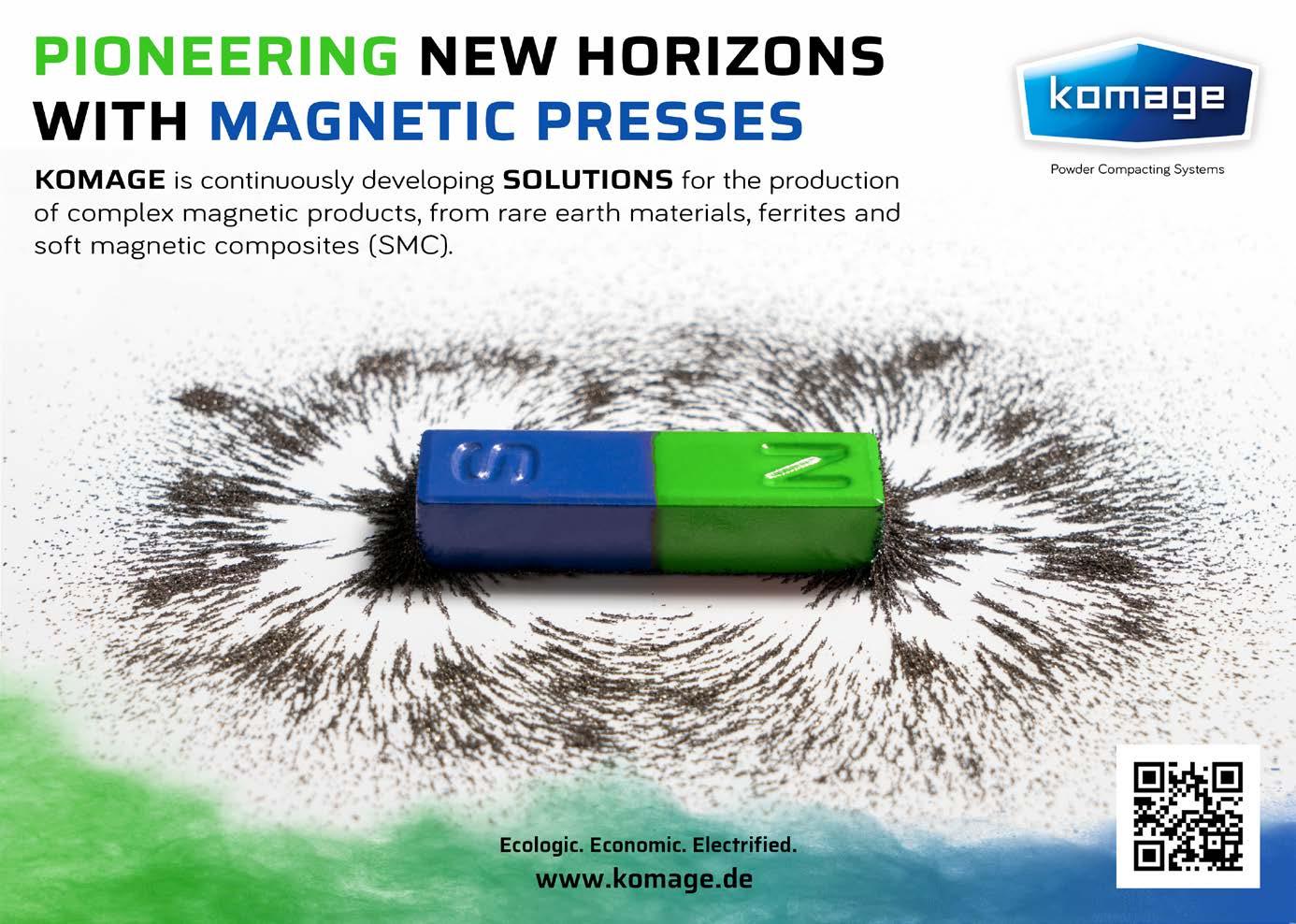

APMA 2025 conference on Powder Metallurgy in Asia first announcement
The 7 th International Conference on Powder Metallurgy in Asia (APMA 2025) will take place October 19-22, 2025, in Qingdao, China.
The event is organised by the China Powder Metallurgy Alliance (CPMA) and the Chinese Society for Metals (CSM), and supported by the Asian Powder Metallurgy Association (APMA).
The International Conference on Powder Metallurgy in Asia began in 2011, and is held every two years. The 2025 conference will cover the following topics:
MPIF
• Metal powder preparation and processes
• Sintering and post-processing
• Powder Injection Moulding (PIM)
• Additive Manufacturing
• Hot Isostatic Pressing (HIP)
• Functional materials & magnetic materials
• Powder superalloys
• Cemented carbide and refractory metals
Porous materials
• Energy materials
• Materials genome engineering
• Standards
releases proceedings of PowderMet2024 and AMPM2024
The MPIF has released the proceedings of PowderMet2024 and AMPM2024, which took place earlier this year in Pittsburgh, Pennsylvania, USA.
‘Advances in Powder Metallurgy & Particulate Materials – 2024’ contains thirty-five technical papers over 424 pages. As the leading technical conference on Powder Metallurgy and particu -
late materials in the Americas, PowderMet2024 is a hub for technology transfer for professionals from every part of the industry, including metal powders, compacting presses, sintering furnaces, quality-control, particlesize and powder-characterisation equipment and more.
‘Advances in Additive Manufacturing with Powder Metallurgy
6K Additive adds angular titanium and chromium powders
6K Additive, a division of 6K, based in North Andover, Massachusetts, USA, has expanded its metal powder portfolio to include both titanium and chromium angular powders. Angular powders are used in a variety of technologies including Additive Manufacturing, Press & Sinter Powder Metallurgy, Metal Injection Moulding, and thermal spray.
The move follows the acquisition of Global Metal Powders in November 2023, enabling 6K Additive to bring additional proprietary metal processing in-house to expand its breadth of sustainable revert
streams and recycling capabilities for producing angular chromium and titanium powders.
The powder range, produced via a sustainable manufacturing process, is reported to be highly pure, with low residual content (such as iron).
“The combination of the acquisition of GMP and our own expertise in sizing and metal upcycling for our spherical powders, allows us to offer a sustainable alternative to what is currently available on the market,” explained Frank Roberts, President of 6K Additive. “For years, customers have asked
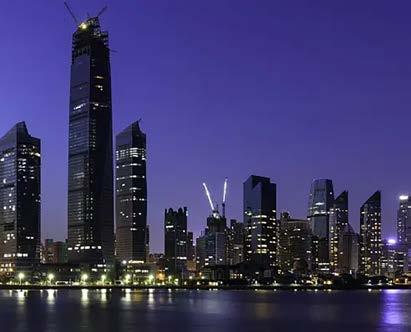
Following the welcome and opening ceremony, the APMA will hold a Council Meeting. Plenary and technical sessions will then take place, followed by an awards ceremony and opening of the exhibition. apma2025.scimeeting.cn
– 2024’ contains forty technical papers over 475 pages. Every metal Additive Manufacturing technology is represented within the proceedings, including: Laser and Electron Beam Powder Bed Fusion (PBF-LB and PBF-EB), Binder Jetting, Material Extrusion and Cold Spray technologies. Application discussions included representative presentations on the adoption of AM by the medical, aerospace, art world, and conventional industrial components.
www.mpif.org
for angular titanium and chromium powder for applications like thermal spray, welding, and MIM. Adding these products to our portfolio is a natural extension of the powders we currently manufacture. We’re excited to supply our customers with products they’ve been seeking from 6K Additive.”
6K Additive has a powder test process with extensive quality control, including in-house analytical capabilities, micro-CT, gas analysis, ICP, XRD, SEM, and EDS. The company’s production facility is ISOcertified and qualified to produce metal powders for high-performance markets such as aerospace, defence, and energy. www.6kadditive.com
APMA 2025 is scheduled to take place in Qingdao (Courtesy APMA)


PUT THE POW IN POWDER

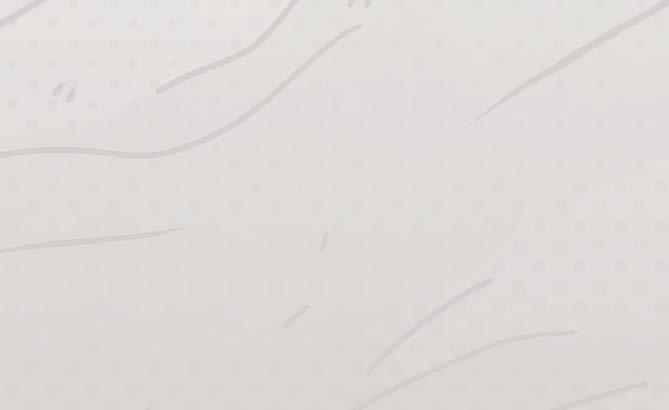
Metal powder that packs a punch
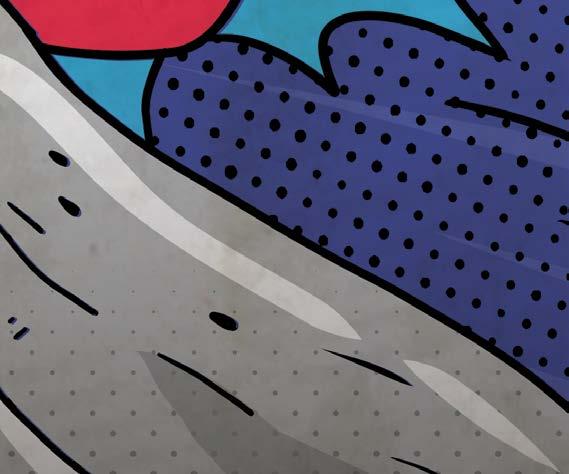
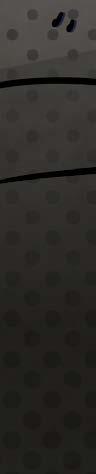
• Alloys backed by 134+ years of metallurgy leadership
• In-house alloy development, atomization, and QC
• Global distribution, ships within 48 hours
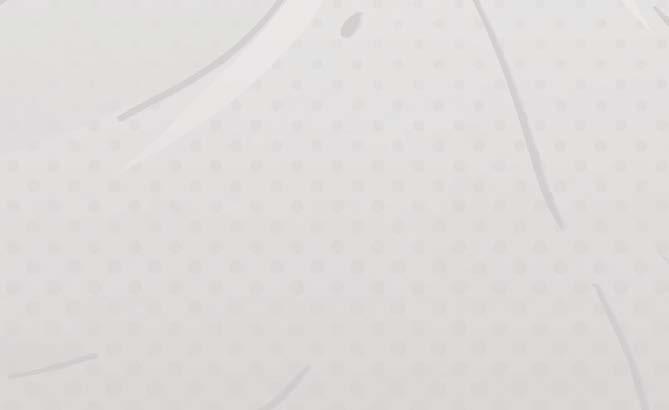

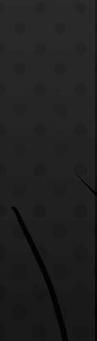
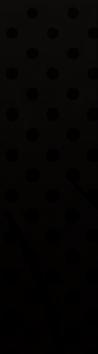
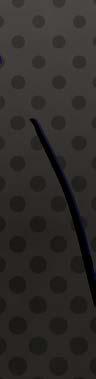




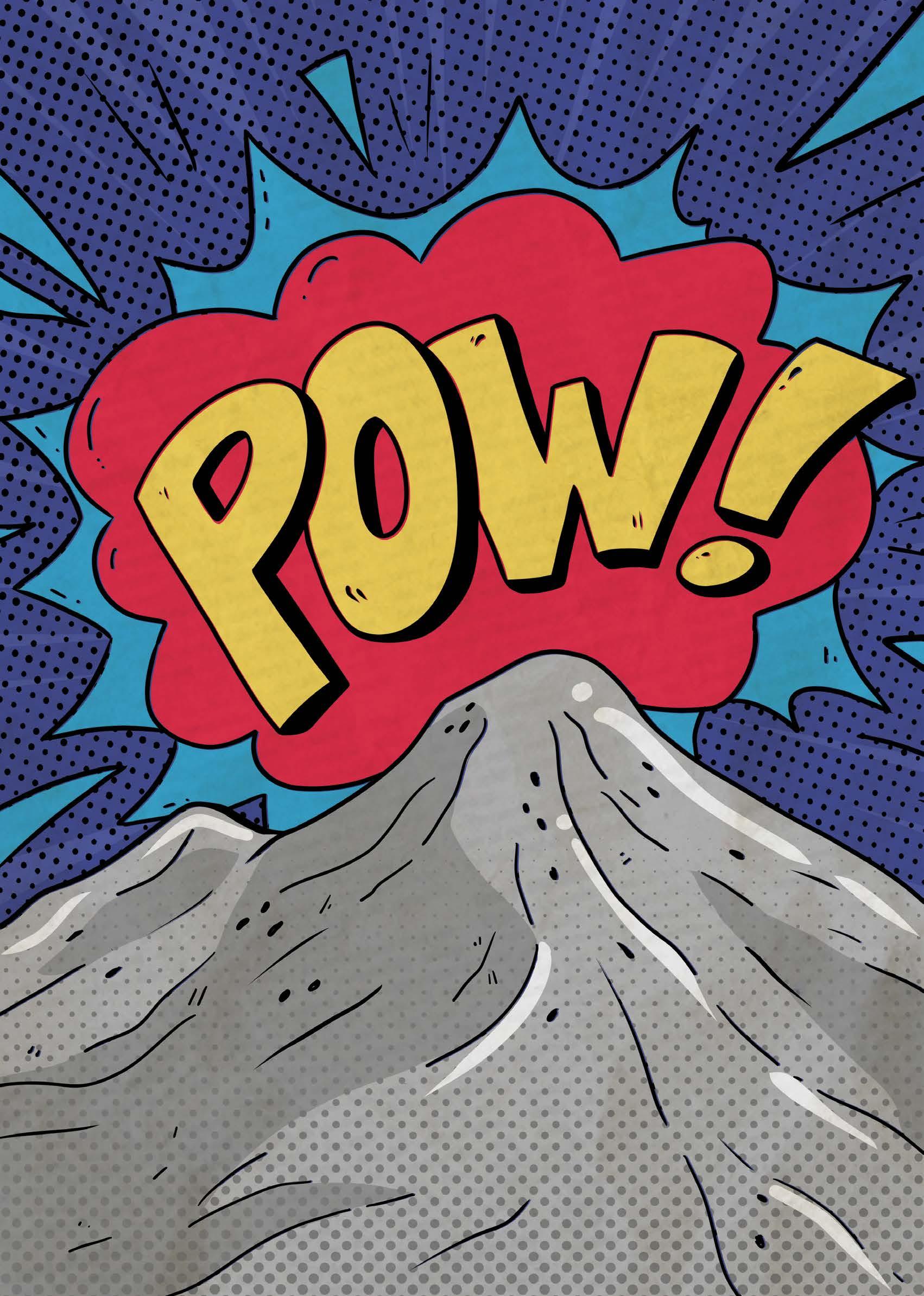

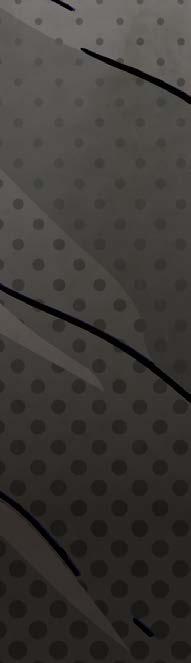
Novel wet etching technique boosts absorptivity of metal powders for Additive Manufacturing
A team from the United State’s Lawrence Livermore National Laboratory (LLNL), Stanford University and the University of Pennsylvania, has developed a novel wet chemical etching process that modifies the surface of conventional metal powders used in Additive Manufacturing. By creating nanoscale grooves and textures, the researchers have increased the absorptivity of the powders by up to 70%, allowing for more effective energy transfer during the Laser Beam Powder Bed Fusion (PBF-LB) process, particularly for challenging materials such as copper and tungsten.
One of the persistent challenges in PBF-LB metal Additive Manufacturing is the high reflectivity of certain metals, which can lead to inefficient energy absorption during the manufacturing process and can even damage some AM machines. This inefficiency often results in inadequate build quality and increased energy consumption, the researchers explain.
“Currently, with standard commercial laser-based machines, high-quality pure copper metal AM is gener -
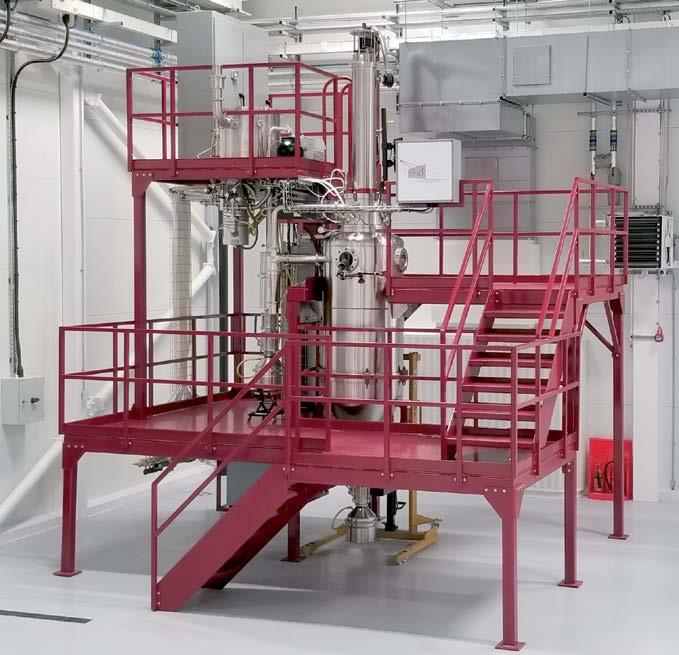
Arcast Atomizers are custom built and competitively priced to meet the growing demand to produce high quality, low cost, technically advanced metal powders fulfilling the requirements of today’s pioneering manufacturing processes.
We can supply machines to atomize titanium alloys, super alloys, refractory and reactive metals, and ferrous and non-ferrous alloys in high vacuum purged vessels with inert gas replacement atmospheres.
We have installed machines all over the world, from 1 kg research furnaces to 1000 kg production units.
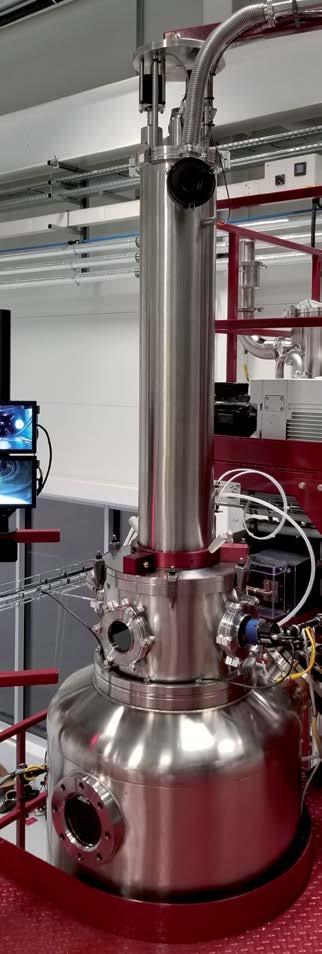
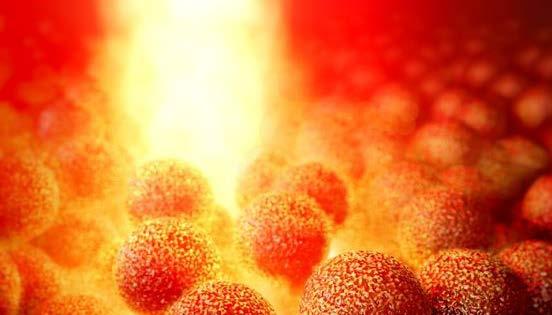
ally considered infeasible,” said co-lead author and LLNL materials scientist Philip DePond. “Our method combines the effects of traditional surface treatments [that increase absorptivity] but doesn’t compromise the purity or material properties of copper that make it desirable — namely its high thermal and electrical conductivity. More fundamentally, we showed that laser-powder interactions extend to regions beyond the melt pool. This has been shown in simulations, especially those of high-fidelity done at LLNL, but not really detailed experimentally. We demonstrated that those interactions exist and can be beneficial to the process.”
The wet-etching technique is said to be relatively simple, but highly effective. The team immersed metal powders, such as copper and tungsten, in specially formulated solutions that selectively removes material from the surface. This process results in the formation of intricate nanoscale features that enhance the powder’s ability to absorb laser light. To characterise the surface features of the etched powders, the researchers employed advanced imaging techniques including synchrotron X-ray nanotomography, which provided detailed 3D representations of the powder particles, allowing the team to analyse and accurately model the electromagnetic influence of the nanoscale modifications.
The team conducted extensive experiments to demonstrate and attribute the mechanism of increased absorptivity to the modified powders. Process optimisation studies and eventually bulk and complex sample Additive Manufacturing was performed using custom-built Laser Beam Powder Bed Fusion (PBF-LB) systems housed at LLNL’s Advanced Manufacturing Laboratory and MIRILIS laser-material interaction laboratory.
Researchers said that the enhanced absorptivity of metal powders is a promising step forward for reducing energy consumption in manufacturing, particularly as the demand for more sustainable and efficient manufacturing processes continues to grow. One of the team’s key findings was that they could manufacture high-purity copper and tungsten structures using lower energy input, less than 100 J/mm 3 for copper, which is around the range for high-density titanium and stainless steel alloys, and ~700 J/mm 3 for tungsten, around 1/3 less energy than is typically employed.
A rendering of laser energy striking powder (Courtesy Brendan Thompson/Lawrence Livermore National Laboratory)
“In a broad sense, we are enabling the printing of copper without the risk of damaging the AM system itself,” DePond explained. “The process parameter window becomes wider as well, which allows a wider variety of scanning conditions to be explored, which often are needed when printing complex geometries. Finally, a handful of machine manufacturers have even gone the great lengths of creating entirely new machines to process copper and other highly reflective materials. These turn out to be nearly double the cost of a traditional machine, so the barrier of entry to printing these materials is prohibitively high.”
The potential applications of the findings could have an immediate impact on production. Researchers said the ability to manufacture with less energy not only reduces operational costs but also minimises the environmental impact of the manufacturing process and opens copper Additive Manufacturing up to a whole new contingent of producers.
“This method enables even commercial machines of fairly low laser power output to print copper, thus democratising the process and providing access to a wider community,” Energy Security Program leader Dan Flowers said, adding that he hopes the work will allow industry to better utilise copper in advanced manufacturing. “From heat exchange to catalysis, more efficient
printing of copper supports development of many clean energy and decarbonisation technologies,” Flowers said. “The LLNL community and our low-carbon energy mission stand to benefit from this capability.”
The enhanced absorptivity and improved powder dynamics also could enable the production of highquality AM parts with greater relative densities. In their experiments, the researchers achieved relative densities of up to 92% with half the energy input compared to other additively manufactured copper components, and over 99% with higher energies, indicating the potential for producing stronger and more durable metal parts.
The team is next looking to examine the effects of nanotexturing on elemental mixing of powders, such as materials that typically need drastically different energies to melt. Funding for the research came from the National Science Foundation, the US Department of Energy’s Office of Science, and LLNL.
Co-authors on the paper include LLNL’s Manyalibo Matthews; co-lead author Ottman Tertuliano and Luc Capaldi of the University of Pennsylvania; and Andrew Lee, Jiho Hong, David Doan, Mark Brongersma, X Wendy Gu, Wei Cai and Adrian Lew of Stanford.
www.llnl.gov www.stanford.edu www.upenn.edu
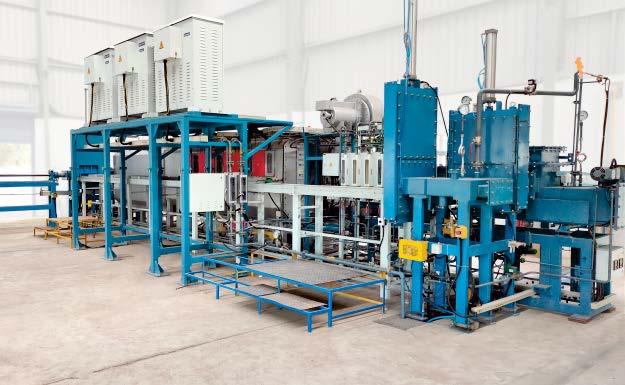
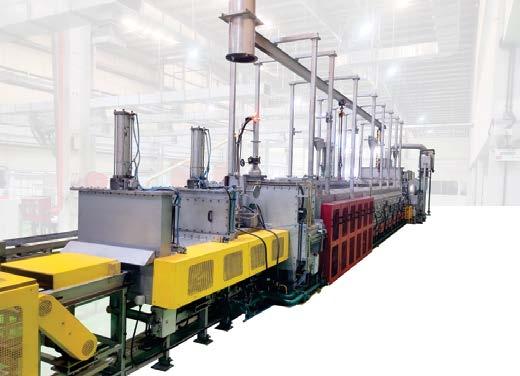

HYBRIT results pave way for industrial fossil-free iron and steel production
The HYBRIT (Hydrogen Breakthrough Ironmaking Technology) initiative is a collaboration between the steel company SSAB, the mining company LKAB and the energy company Vattenfall. Launched in an effort to virtually eliminate carbon dioxide emissions in the steel industry, the final report has now been published and presented to the Swedish Energy Agency. The report shows that direct reduced iron produced with the HYBRIT process has superior characteristics compared to iron produced with fossil fuels.
By replacing coal and coke in the production of iron with fossil-free hydrogen and electricity, the HYBRIT process is expected to reduce Sweden’s total carbon dioxide emissions by more than 10%. HYBRIT has already applied for and received several patents based on the successful results, and the project will now continue into the next phase, where the process is to be implemented on an industrial scale.
“I am incredibly proud of everything HYBRIT has achieved since
its launch in 2016. Thanks to the successful results of the pilot project, we are well on our way to fundamentally changing the iron and steel industry. At SSAB, we are now investing heavily to convert the entire Nordic production system to fossil-free steel production and have already started delivering fossil-free steel to customers on a smaller scale,” says Martin Pei, Chief Technology Officer at SSAB and Chairman of the Board of Hybrit Development AB.
The project is noted as the first to demonstrate that the fossil-free value chain – from iron ore to steel – works on a semi-industrial scale. It is reported that, thus far, more than 5,000 tonnes of hydrogenreduced iron have been produced at HYBRIT’s pilot plant in Luleå. Customers such as Volvo Group, Epiroc, Peab and many more are already using the fossil-free steel in vehicles, heavy machinery, buildings and consumer products. Interest in the technology is said to be high.
www.hybritdevelopment.se
NTN Corporation expands in Vietnam with new Ho Chi Minh sales branch
NTN Corporation, headquartered in Osaka, Japan, is set to establish a new sales base in Ho Chi Minh, Vietnam, for its subsidiary NTN Bearing Vietnam Co, Ltd. Once established, the new facility will play a central role in the ASEAN region, where further market growth is expected.
NTN Corporation stated that it will work to expand the aftermarket business, through aggressive sales activities and the provision of technical services. Vietnam has continued to achieve stable economic growth in
recent years, driven by investment from multinational companies across various industries, including the automotive sector, and the expansion of local businesses.
In 2016, NTN Corporation established NTN Bearing Vietnam Co, Ltd, in the Dong Da District of Hanoi City, to provide sales and technical services to customers of automotive and industrial machinery manufacturers, as well as sales to distributors.
www.ntnbearing.vn www.ntnglobal.com
MMC RYOTEC to construct new plant in Thailand for mining and civil engineering tools
MMC RYOTEC Corporation, a consolidated subsidiary of Japan’s Mitsubishi Materials Corporation, has announced plans to expand its manufacturing capacity in Thailand. The company will construct a new facility at OTEC (Thailand) Co, Ltd, its base for manufacturing mining and civil engineering tools.
Tools for drilling holes in bedrock, called bits and rods, are widely used in civil engineering work such as mining, stone crushing and tunnelling. Demand for these tools is rising due to the growth of infrastructure development. Consequently, there’s a need to provide products that meet customer needs and establish a stable manufacturing supply.
Since its establishment in 1997, OTEC has steadily grown as MMC RYOTEC’s overseas manufacturing base for construction tools. The new plant is scheduled to start operation in October 2025 and will be equipped with new machining and heat treatment facilities. As demand grows, production capacity is expected to be doubled.
www.ryotec.co.jp

MMC RYOTEC produces a range of mining and civil engineering tool products (Courtesy MMC RYOTEC)

Centorr Vacuum celebrates 70 years in vacuum furnace industry
In 2024, Centorr Vacuum Industries (CVI) is celebrating its 70 th anniversary in the vacuum furnace industry. CVI was formed from the combination of Vacuum Industries, founded in 1954 in Somerville, Massachusetts, USA, and the Centorr Furnace company, founded in 1962 in Suncook, New Hampshire. The two were merged in 1989, with new facilities in Nashua, New Hampshire, where the company is still located.
In 1997, CVI became 100% management-owned and is now run as a private company under president and CEO William Nareski. “We have enjoyed long-term success over the past seventy years because our highest priority is customer satisfaction with our equipment and service” stated Nareski.
Vacuum Industries was started by the principles of the original National Research Corp in Boston. It had a long history in the design and building of production size furnaces, primarily for the metals and hardmetals industry. Centorr Furnaces was a Laboratory and R&D furnace manufacturer, and was known for doing some of the first high temperature 3000°C furnaces for the growing ceramics market. In later years, Centorr was known as a world leader in fibre optics and high-temperature hydrogen sintering furnaces for the lighting industry.
Today, Centorr is best known for its line of metals and ceramics sintering furnaces, large equipment sold into the nuclear industry, and for its line of furnaces sold into the carbon, graphite, and composites

Vacuum Industries is celebrating its 70 th anniversary (Courtesy Centorr Vacuum Industries)
industry for aerospace and hypersonics. The company is one of the leading custom and standardised vacuum furnace manufacturers, and has an installed base of over 7,000 high temperature vacuum and controlled atmosphere furnaces worldwide. CVI operates a fully staffed Aftermarket Field Service group and an Applied Technology Center, offering R&D support and toll production service.
www.centorr.com
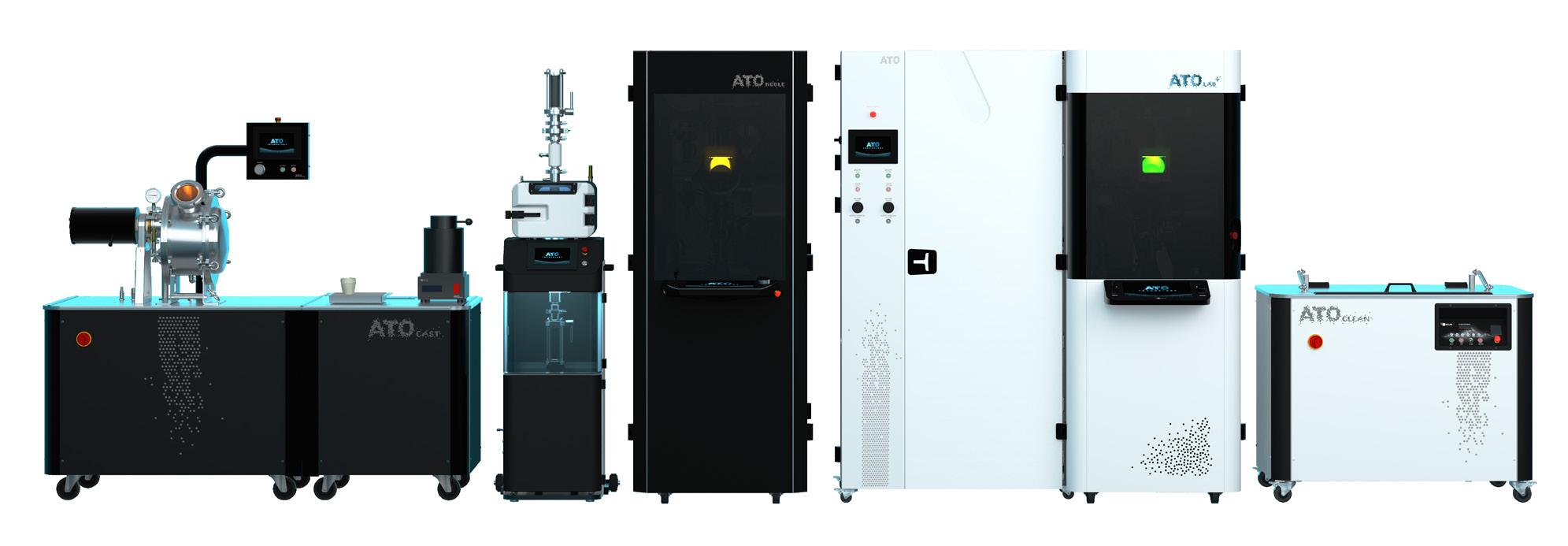
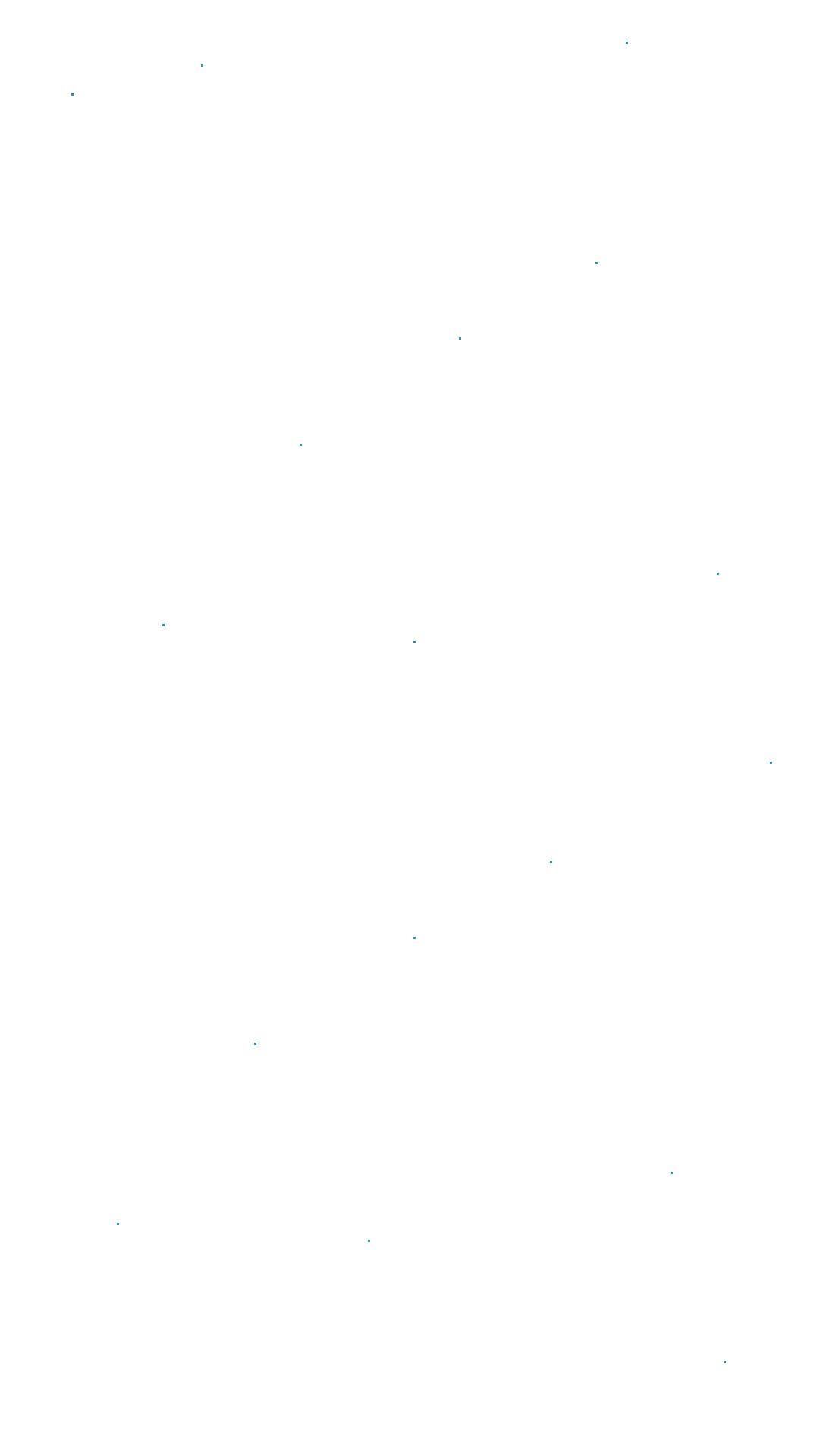
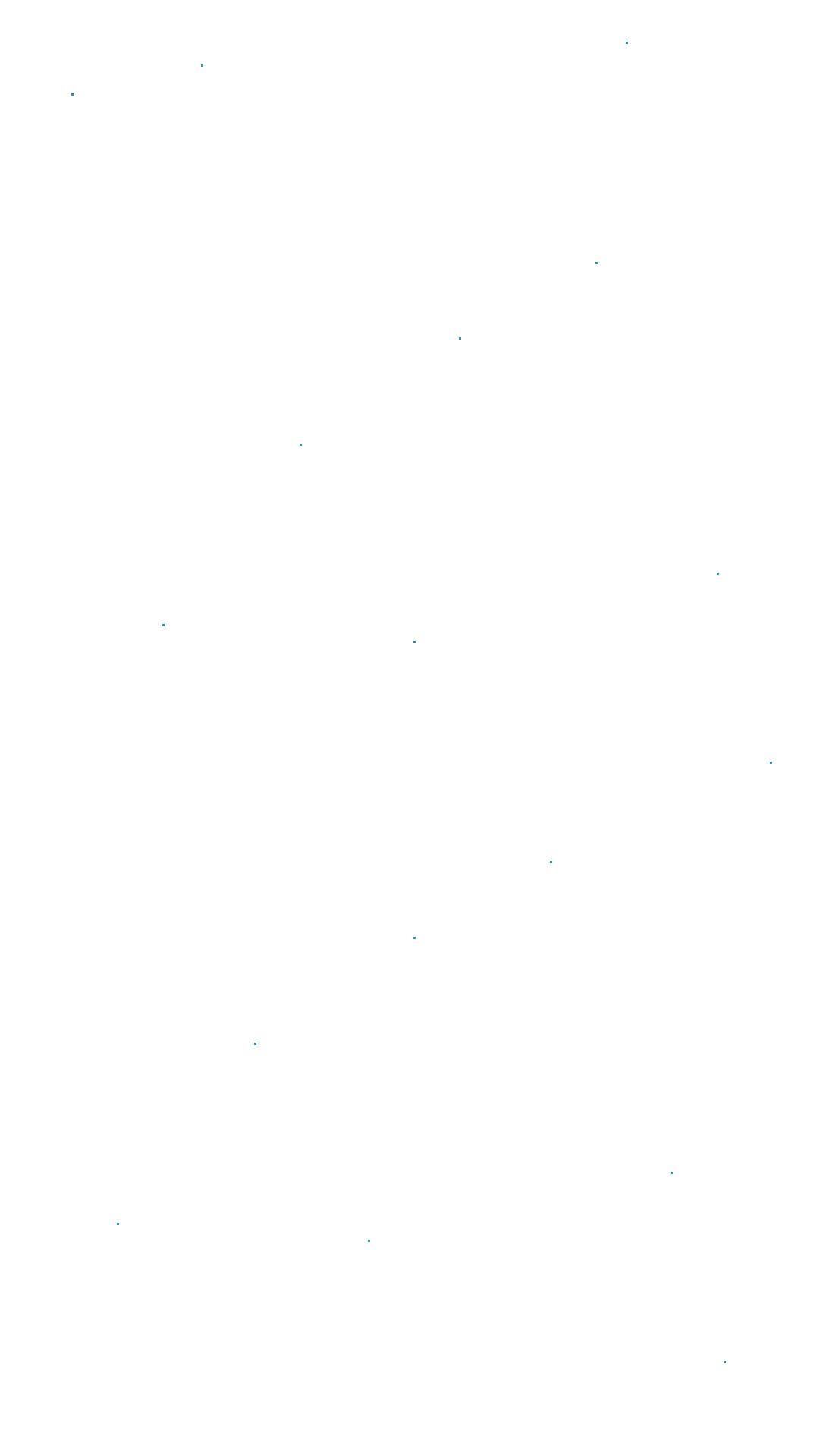
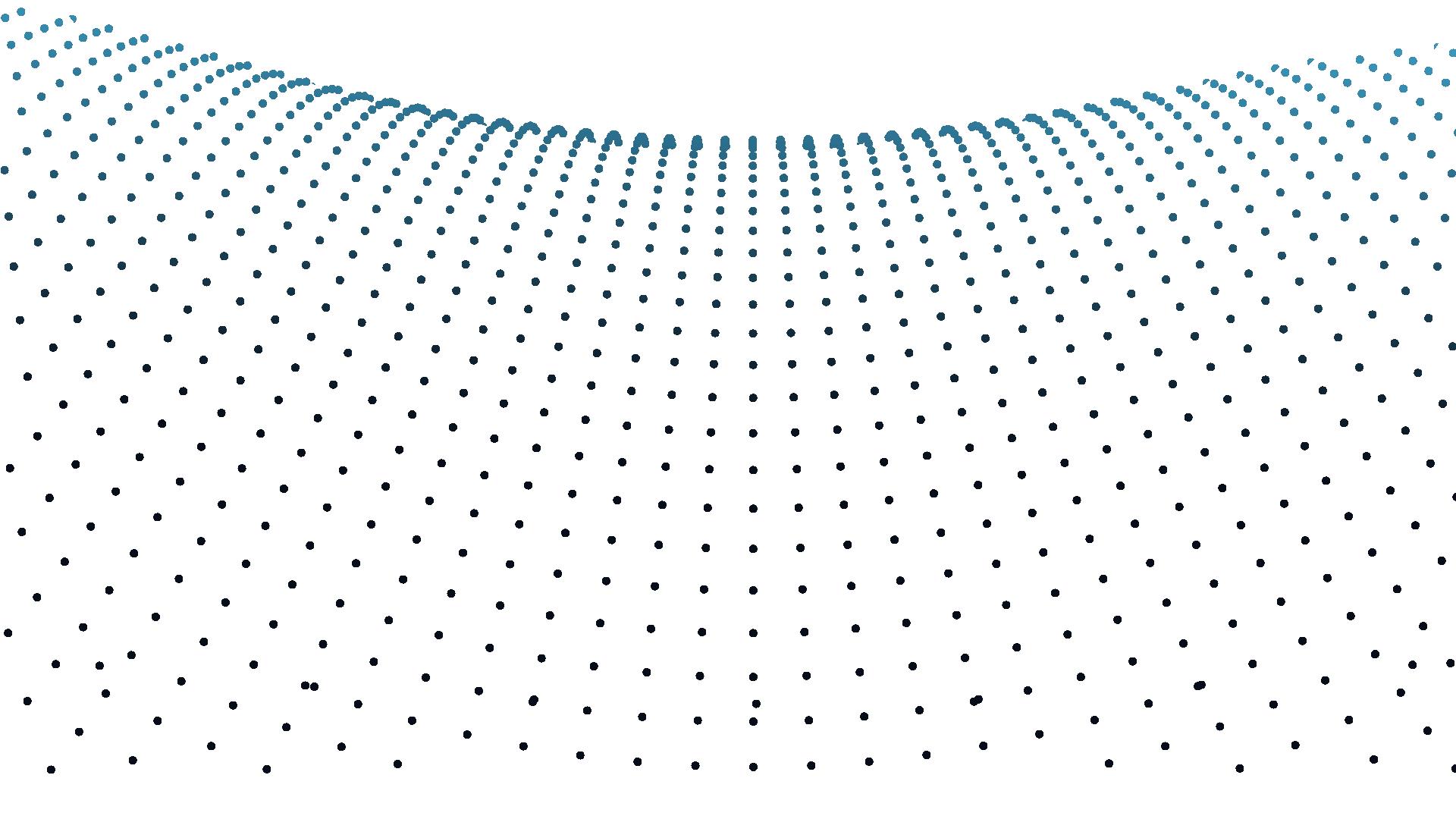
Centorr
Amazemet’s Powder2Powder atomiser for recycling metal powders
Amazemet Sp Zoo, based in Warsaw, Poland, recently announced its new Powder2Powder (P2P) atomiser. The new system is reported to provide a versatile solution for recycling metal powders, and manufacturing custom pre-alloy powders directly from powder feedstock.
The technology combines plasma processing and ultra -
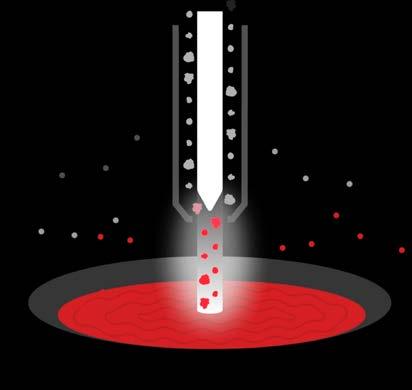
Powder2Powder (P2P) technology combines plasma processing and ultrasonic atomisation to transform irregular or oversized particles into highly spherical, satellite-free powders
sonic atomisation to transform irregular or oversized particles into highly spherical, satellite-free powders optimised for Additive Manufacturing. Unlike plasma spheroidisation, the P2P technology allows powder size to be independent of the initial feedstock, reportedly making it the only technology capable of direct atomisation of pulverised titanium feedstock.
“The Powder2Powder system goes beyond recycling,” explains Łukasz Żrodowski, inventor and CEO of Amazemet. ”It gives manufacturers the ability to customise powder compositions, improve powder sphericity, and optimise particle size distribution, solving critical issues in the AM industry.”
Extensive trials using +200 µm oversize and irregular Ti alloy powders have reportedly shown exceptional results with the P2P system. Operating at a frequency of 40 kHz, the system consistently achieved a powder morphology with an aspect ratio (D50) exceeding 0.95. The particle size distribution
EQ Resources to supply Elmet Technologies with tungsten concentrate
EQ Resources Limited (EQR), Mount Carbine, Australia, has agreed to a strategic collaboration involving a multi-year offtake agreement with Elmet Technologies LLC, a US-owned and fully integrated tungsten manufacturer headquartered in Lewiston, Maine. Under the agreement, EQR and Elmet will leverage their respective experience and expertise in mining, minerals processing and downstream tungsten manufacturing for the mutual benefit of both parties, working collaboratively to develop and enhance the global tungsten supply chain.
The two companies have agreed on a basic framework in which Elmet is to purchase from EQR tungsten concentrate, with an estimated
value of AU$30 million, over a fiveyear period. Elmet is to secure the offtake allocation through an advance payment of AU$2.0 million to EQR.
“We are extremely pleased to extend our industry relations with Elmet Technologies. Through Elmet, we found a partner that shares ambitions with regards to the development of sustainable and resilient supply chains for critical raw materials. EQ Resources’ rapidly growing tungsten mines in Australia and Spain will provide Elmet with the improved industrial resiliency to support their mission critical US defence customers,” stated EQ Resources Chief Executive Officer, Kevin MacNeill. “Raw
(PSD) was precisely controlled, producing powders with D90 <80 µm and yielding particles <63 µm and ≥80%. Nearly 97% of the resulting powder was suitable for AM processes, including Laser Beam Powder Bed Fusion (PBFLB), Directed Energy Deposition (DED), and Electron Beam Powder Bed Fusion (PBF-EB), highlighting the machine’s potential to enhance sustainability in metal powder production.
Additionally, the P2P system can process blends of elemental powders, creating pre-alloyed materials tailored to exact chemical compositions. This capability makes it invaluable for both research and industrial applications. Tests conducted with Ti and 10% wt. Mo elemental powders showed that both refractory elements formed homogeneous alloy powders during processing. Set for release in Q1 2025, this patented technology addresses two critical challenges in the AM industry - upcycling of powder waste and custom powder production - delivering advanced functionality that is said to surpass traditional recycling methods. www.amazemet.com
material security has become a top priority, geopolitically and in many board rooms around the world and investing in sustainable mining in Australia and Spain provides a unique market solution.”
Elmet Technologies is a producer of pure tungsten and related tungsten alloys, such as tungsten lanthanum (W-La), potassium doped tungsten (W-K), tungsten rhenium (WRe), and tungsten heavy alloy (WHA). Through unique processes, these materials are pressed, sintered, swaged, and forged into rod, drawn into fine wire, and hotrolled into plate, sheet and foil, along with several other speciality processes that support the most mission-critical defence, aerospace, medical, industrial, and semiconductor segments.
www.elmettechnologies.com www.eqresources.com.au

Elementum 3D celebrates a decade in Additive Manufacturing powders
Elementum 3D, based in Thornton, Colorado, USA, is celebrating ten years in the Additive Manufacturing materials industry. The company produces gas atomised aluminium, copper, nickel, steel, tantalum, tungsten and bespoke alloy powders for AM.
“I never would have predicted where Elementum 3D would take me,” stated said Dr Jacob Nuechterlein, president and founder of Elementum 3D. “I’ve travelled all over the world, gone to factories, and worked with customers I would have never thought possible. It’s been incredible. I appreciate all those who have supported and even cheered on Elementum 3D from the sidelines over the past ten years. I can’t wait to see what’s next.”
In 2014, the Additive Manufacturing industry was functioning at a different scale, with suitable materials for AM limited compared to traditional CNC manufacturing. Elementum3D was founded in an effort to fill the metal materials gap in the Additive Manufacturing market, developing metal alloy materials suited for AM without compromising on material properties.
The next stage planned in Elementum 3D’s journey will be transitioning from supporting R&D programmes and projects to full-scale production and commercialisation. Leadership and staff are preparing to match large materials orders associated with the next phase of AM, overcoming the shortages in raw materials which can
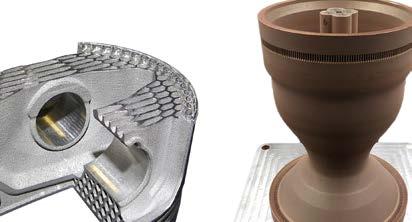
Elementum 3D offers a range of metal powders for Additive Manufacturing, including aluminium, nickel and copper (Courtesy Elementum 3D)
create a bottleneck in a growing industry.
“We’re seeing the AM industry shift from hypothetical to the real phase of commercialisation, this transition to serial production capability and capacity will be the most exciting thing I’ve seen or been a part of since Elementum 3D was founded in 2014,” Nuechterlein added. “Everything leading up to now has been practice, preparing to be ready for the real show.”
www.elementum3d.com



International Conference on
Isostatic Pressing 6 - 10 April 2025 in Aachen, Germany
6 - 10 April 2025 in Aachen, Germany
6 - 10 April 2025 in Aachen, Germany
This conference will cover research and development within the complete scope of HIP technology, from fundamental process development and materials technology over application related improvements and new developments in HIP equipment up to current market trends from all parts of the world. Learn more under https://hip2025.com/information/contact
This conference will cover research and development within the complete scope of HIP technology, from fundamental process development and materials technology over application related improvements and new developments in HIP equipment up to current market trends from all parts of the world.
This conference will cover research and development within the complete scope of HIP technology, from fundamental process development and materials technology over application related improvements and new developments in HIP equipment up to current market trends from all parts of the world.
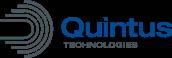
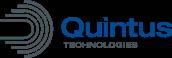
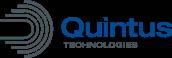
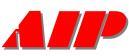
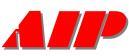
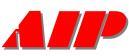
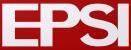
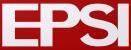
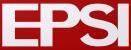
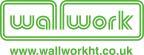
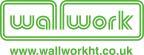
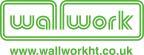
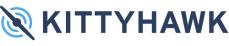
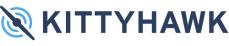
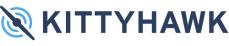
Alloy development with InssTek’s MX-Lab at global academic institutions
InssTek, headquartered in Daejeon, South Korea, has reportedly seen significant global success with its metal Additive Manufacturing machine, MX-Lab, which continues to attract leading universities and research institutions worldwide.
A recent sale to the Institut Jean Lamour (IJL), Université de Lorraine, Nancy, France, further accelerates MX-Lab’s successful global expansion. Additionally, installations are currently underway at other universities and research institutions.
The MX-Lab, independently developed by InssTek, is a dedicated
Additive Manufacturing machine for material research using Directed Energy Deposition (DED) technology. The most notable feature of this AM machine is its ‘Hexa Powder Feeder’ system, which allows for the precise control of up to six different material ratios during experiments. This system ensures accurate powder feeding, even in micro-amounts, making it ideal for detailed and precise research applications.
The MX-Lab is designed specifically for research purposes, offering a compact size that allows researchers to design and conduct
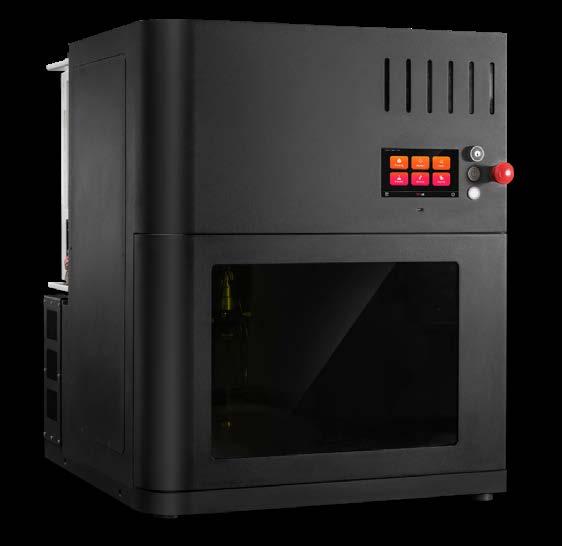

Velta’s titanium powder for Metal Injection Moulding succeeds in EU tests
Velta LLC, located in Dnipro, Ukraine, has announced the successful testing of its Velta Ti Process powder for Metal Injection Moulding (MIM) applications. The results were presented at the 7th International Conference on Powder Metallurgy and Additive Manufacturing of Titanium (PMTi2024) in Madrid.
The powder was assessed by an independent research institute, and tested in final product manufacturing
by PolyMiM, a prominent German company.
The testing confirmed the suitability of Velta’s titanium powder for producing final titanium products using MIM technology. The move represents a significant advancement in manufacturing capabilities through Velta Ti Process as a zerowaste and low-to-zero carbon method for obtaining titanium metal powder.
experiments with high flexibility and ease. Its user-friendly interface and advanced capabilities enable scientists and engineers to explore a wide range of material compositions and properties efficiently.
The MX-Lab has been adopted by universities and research institutions across 15 countries, leveraging its technology for research and development. Key customers include:
• Brown University (USA): Focusing on innovative research in materials science and engineering
• University of Michigan (USA): Studies on high-performance alloys and Additive Manufacturing process optimisation
University of North Dakota: (USA): Utilising MX-Lab for the development of multi-material structures and machine learning applications in Additive Manufacturing
• VTT (Finland): Alloy optimisation
• COMTES FHT a.s. (Czech Republic): To make Functionally Gradient Material samples
• KAIST (South Korea): To find new compositions of High Entropy Alloys
An InssTek spokesperson stated, “The high interest and trust in MX-Lab’s performance and potential from research institutions are driving our success in the global market. We aim to continue partnering with more institutions to contribute to innovative technology development.” www.insstek.com
“Velta is evolving in sync with market demands,” said Artem Yarovinsky, Velta’s Chief Business Development Officer. “We are meeting the rising demand for sustainability, increased titanium powder usage, and the development of titanium alloys, ensuring we offer a reliable titanium solution. The conference also gave us a great opportunity to establish collaborations with companies interested in further practical testing of Velta’s titanium powder for manufacturing final products.”
www.velta.us
The MX-Lab is a dedicated AM machine for material research DED technology (Courtesy InssTek)

Tekna offers coarse titanium powders developed for PBF-LB Additive Manufacturing
Tekna Holding ASA, Sherbrooke, Quebec, Canada, reports it is now offering coarse titanium alloy (Ti-6Al-4V) powders for Laser Beam Powder Bed Fusion (PBF-LB) Additive Manufacturing.
The company states that the advancement of PBF-LB machines has opened new possibilities for using larger powder sizes, marking a transformative shift in the market. Addressing this emerging demand, Tekna has developed a range of Ti64 coarse powders specifically engineered for PBF-LB applications. The powders are optimised for use with varying layer thicknesses, including 60 µm, 90 µm, and above.
By leveraging its proprietary plasma atomisation technology, Tekna produces Ti64 powders that are reported to be spherical and free from internal porosity. This results in powders with higher density and flowability, which translates into superior mechanical properties in the final manufactured parts. Consequently, this enhances the end-user production yield and part reliability, the company states.
Economic and safety advantages
The use of thicker deposition layers leads to reduced production times, which enhances productivity and lowers the end-user overall production costs. This economic advantage, combined with the reduction in powder costs, makes the process more cost-effective. Furthermore, the ability of the end-user to procure Ti64 coarse powders and finer PBF-LB size fractions manufactured from the same dedicated plasma atomisers accelerates the industrial qualification.
From a safety perspective, finer powders commonly used in PBF-LB applications are often classified as flammable. In contrast, Ti64 coarse powders produced by Tekna have a lower sensitivity to oxygen thus reducing risks related to powder handling and recycling as well as costs associated with storage and transport.
“Our commitment to safety is essential, both for users and the environment. Thanks to their reduced reactivity, Ti64 coarse powders are not classified as flammable and are not sensitive to static electricity, making them safer to handle. This also simplifies logistics, allowing for easier transportation and compliance with local storage regulations. Ultimately, these advancements reflect our dedication to delivering high-quality products that prioritise safety and efficiency at every stage,” shared Rémy Pontone, VP Sales & Marketing at Tekna.
Productivity boost
Ti64 coarse powders can significantly improve productivity. Based on recent qualifications performed on well-known manufacturing platforms, the productivity
for a given part increased from 123 cm³/hr at a 60 µm layer thickness to 254 cm³/hr at a 90 µm layer thickness. Manufacturing thicker layers provides better energy dissipation, which contributes to fewer deformations. This reduces the number and complexity of part supports required during manufacturing. It, therefore, contributes to decreased post-processing time and costs.
Compliance with industry standards
Parts manufactured using Tekna’s Ti64 coarse powders reportedly fulfil critical industry standards, including B348-21, F3001, and F136. These compliances highlight the quality and reliability of the produced parts.
Comparison between actual values measured on parts manufactured with Tekna’s Ti64 coarse powders and ASTM B348-21, F3001-14, and F136-13 standards.
Outlook
Tekna’s development of Ti64 coarse powders marks a significant milestone in the Additive Manufacturing industry. As the market continues to evolve, Tekna remains committed to pioneering innovations that drive economic, safety, and productivity advancements, setting new benchmarks for quality and performance. www.tekna.com
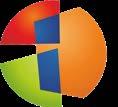
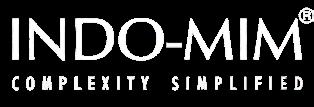

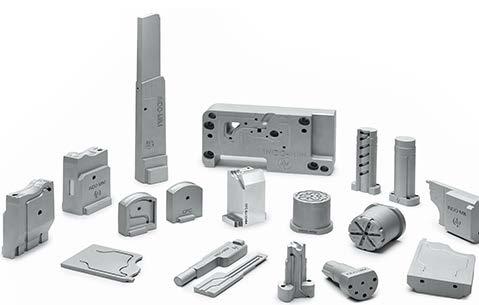
www.metal-am.com/ webinar-the-future-of-tooling-manufacturing-exploring-indomim-m2-propertieswith-hp-metals-3d-printing/
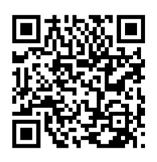
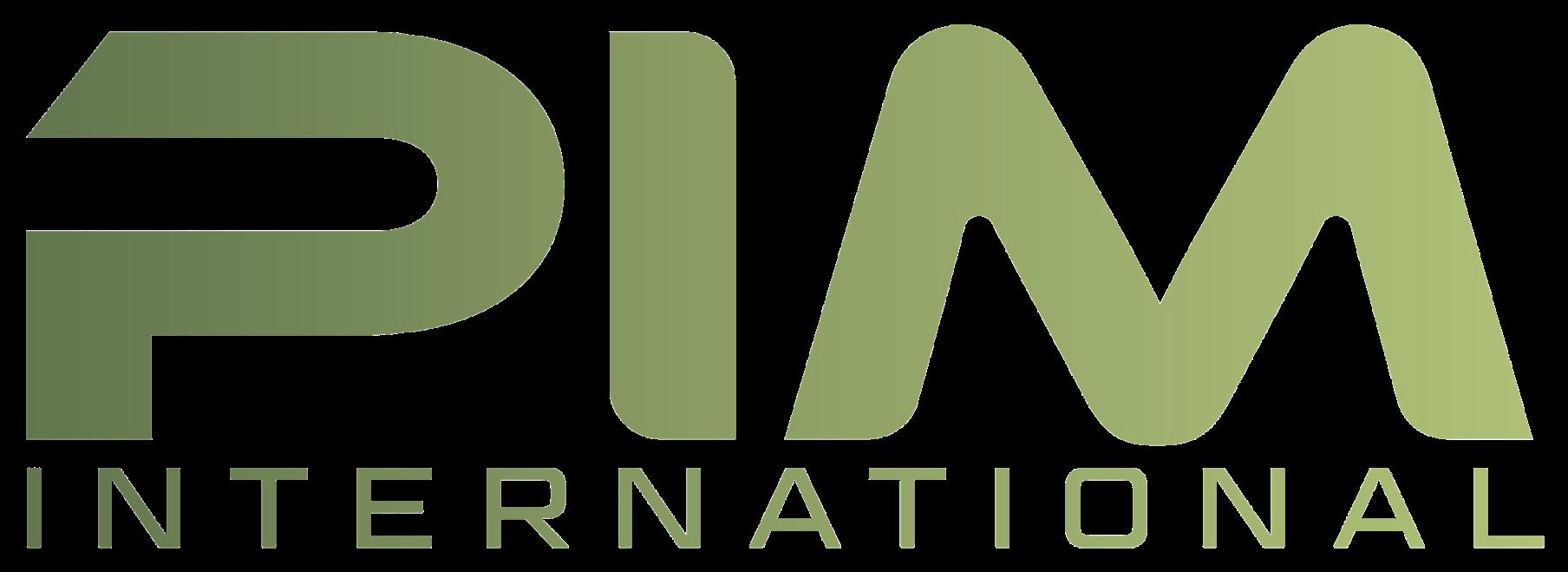

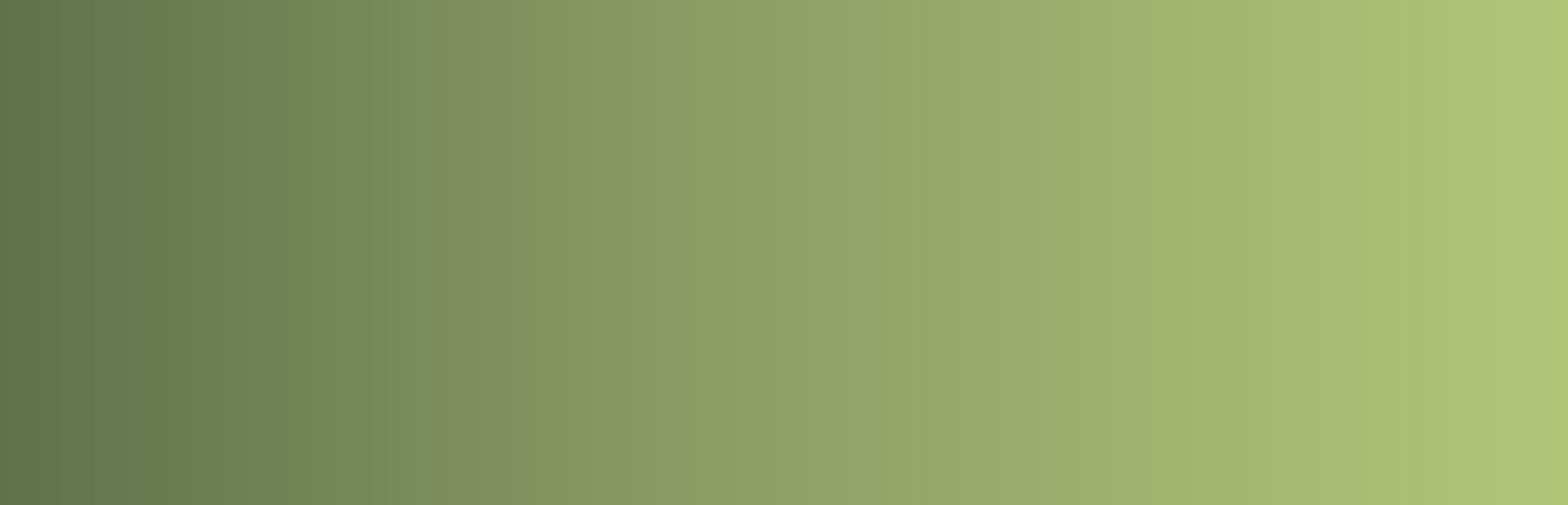
Our exclusive deep-dive articles, company profiles, conference reports and newsletters are of great value to those interested in this advanced manufacturing technology for the production of complex, high volume netshape components

2024 Excellence in Metallography Award won by AM powder research paper
The Metal Powder Industries Federation (MPIF) has selected the paper “Impact Resistance of a Free Sintering Low Alloy Steel Produced by Powder Bed Fusion Using a Laser Beam,” by Thomas F Murphy, FAPMI, Christopher T Schade, FAPMI, & Kerri M Horvay, Hoeganaes Corporation as the winner of the 2024 Excellence in Metallography Award.
The paper was selected from the highly qualified manuscripts presented at the PowderMet2024/ AMPM2024 conference in Pittsburgh, USA, and critically evaluated for the prestigious award.
The full paper is available for download on the APMI website. It is also included in ‘Advances in Additive Manufacturing with Powder Metallurgy-2024’ and published in the autumn issue of the International Journal of Powder Metallurgy
The authors will be officially recognised during PowderMet2025 in Phoenix, Arizona, June 15-18, 2025.
www.mpif.org

voestalpine becomes first European steel company to place a green bond
voestalpine announced that it has successfully issued its first green corporate bond for €500 million, the entire proceeds of which will finance sustainable projects such as greentec steel. The bond was scheduled to start trading on the Vienna Stock Exchange in October.
“voestalpine has been an environmental benchmark in the industry for decades, and has a clear plan to transform its steel production with greentec steel,” stated Herbert Eibensteiner, CEO. “As early as 2027, we will partially
switch from the traditional blast furnace route to electric arc technology using green electricity, thereby reducing our emissions by around 30% by 2029. This makes greentec steel the largest climate protection programme in Austria. By issuing the first green bond in the European steel industry, we are now also taking on a pioneering role in the capital market.”
The bond has a term of five years and a coupon of 3.75%, and has met with high investor
demand. Private investors may also subscribe during the subscription period running from September 26 to its launch on the Vienna Stock Exchange.
Forming the basis of the bond is the recently released Green Financing Framework, the first of its kind for a European steel company. Gerald Mayer, CFO, explained, “Our Green Financing Framework fulfils the stringent requirements of the International Capital Market Association whose standards are considered best practice worldwide. Our framework for this first green bond and future green financing is the gold standard.” www.voestalpine.com
A selection of images of fracture surfaces from representative bars. All photos are oriented with the progression of fracture moving from the top of the frame to the bottom (Courtesy MPIF)
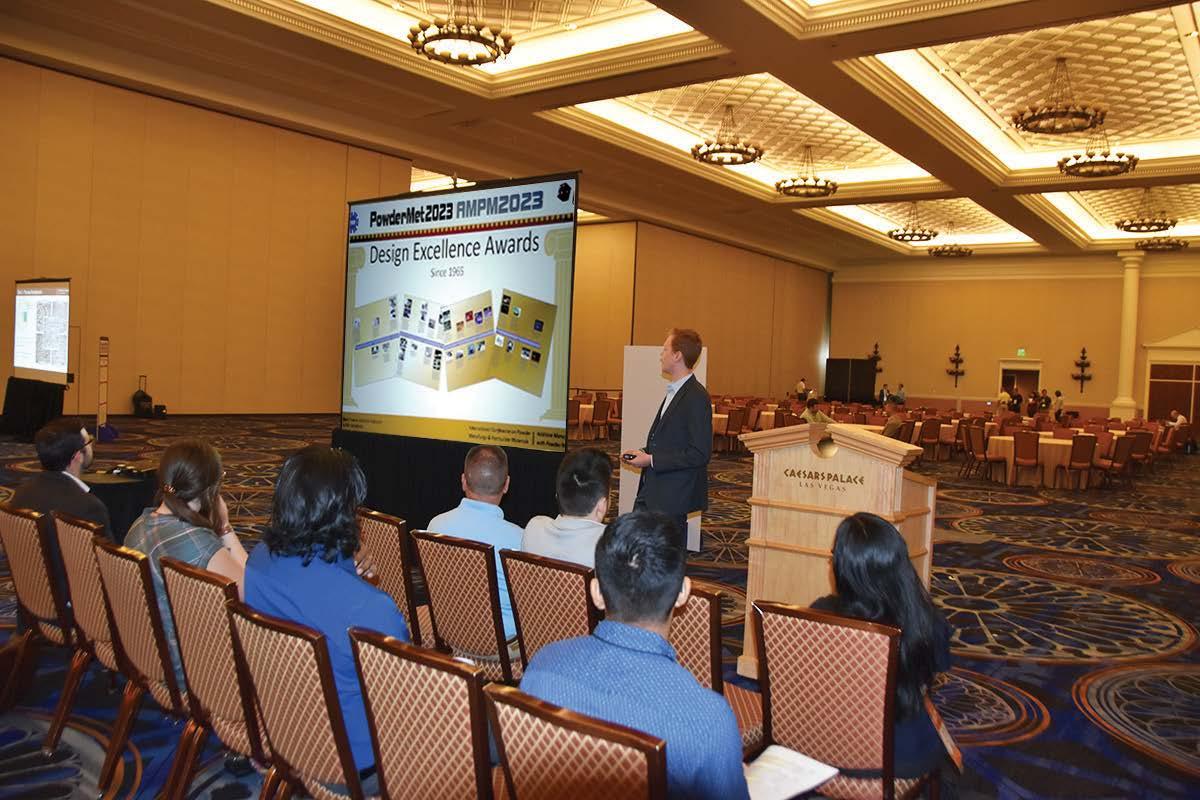
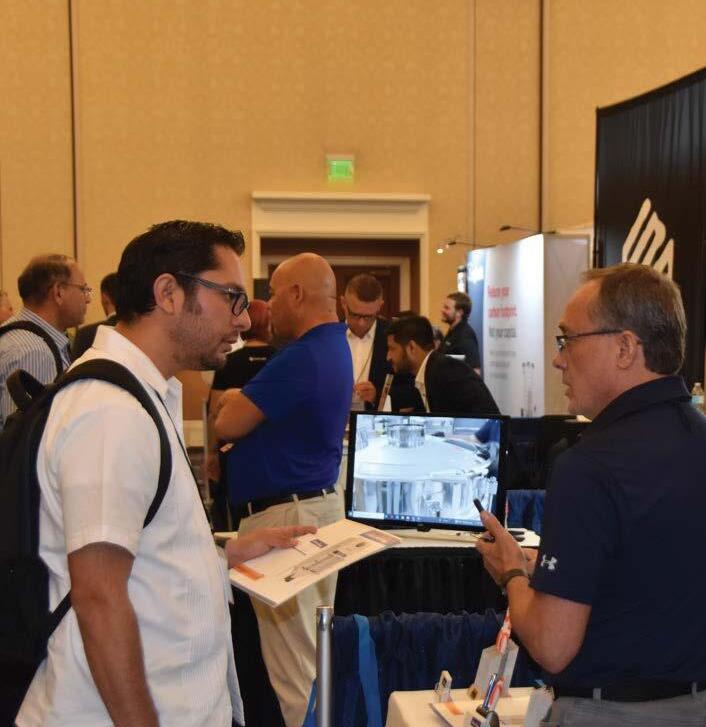
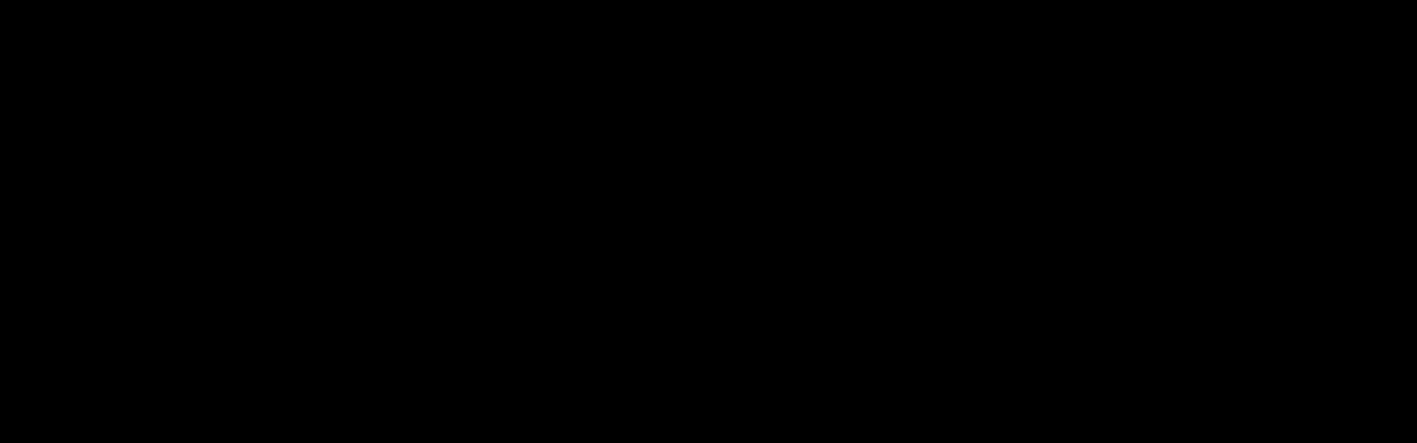
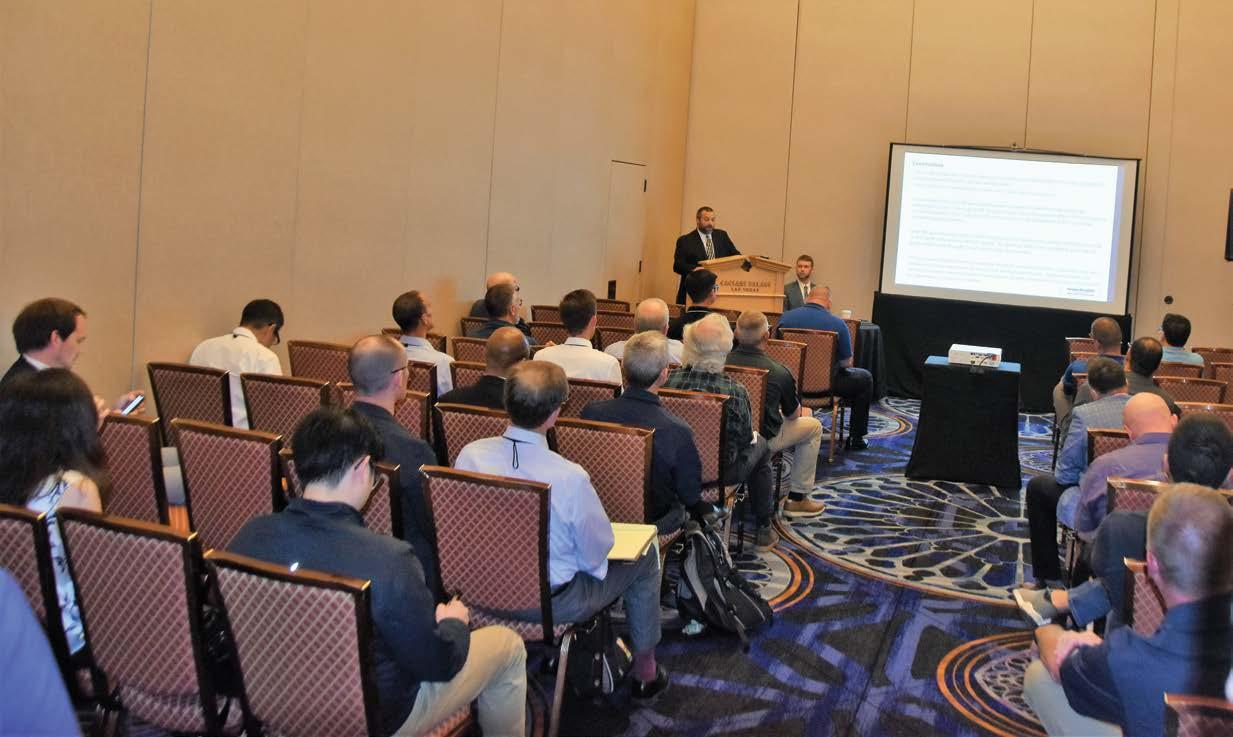
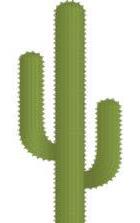
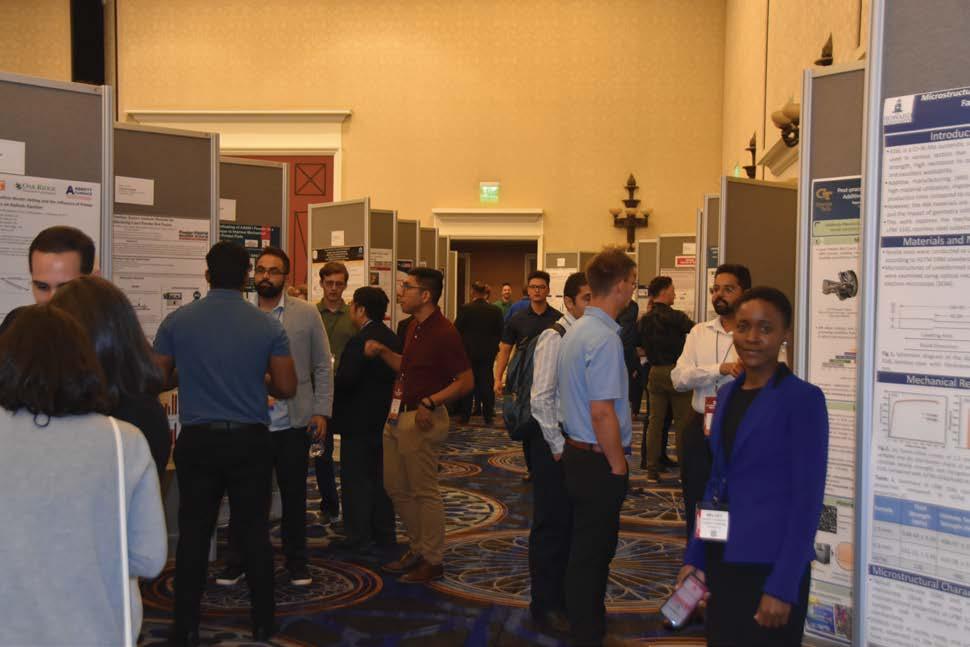
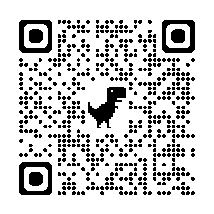

Powder Metallurgy: Discover innovative technologies meeting the demands of vehicle electrification
Vehicle Electrification is transforming the PM industry, providing new opportunities as Battery Electric Vehicles (BEVs) and Hybrid Electric Vehicles (HEVs) continue to gain market share. At MPIF’s PowderMet2024 conference, a series of Special Interest Sessions delved into the innovative PM technologies used to meet current demands. Advances in Soft Magnetic Composites (SMCs), PM permanent magnets, new electric motor designs, and evolving drivetrain mechanisms are discussed. Bernard North gives a comprehensive analysis of how industry leaders are currently adapting to these changes and explores the implications for future PM applications in the rapidly evolving automotive sector.
The MPIF’s combined PowderMet2024 and AMPM2024 conferences and trade exhibit were held at the David L Lawrence Convention Center in Pittsburgh, Pennsylvania, from June 16-19, 2024. The event is summarised in some detail in the Autumn issue of PM Review [1]. It was very well-attended, with nearly 900 participants from twenty-five countries, and about ninety-three exhibitors in the trade show. There were approximately 200 presentations, including around 50 technical posters. In addition, forty-one select graduate students gave ten-minute summaries of their work in Powder Metallurgy and related fields. Three tutorials – on press and sinter, metal AM, and Metal Injection Moulding –were also included.
Some technical sessions during such events are designated as ‘Special Interest Programs (SIPs)’. This year, the SIPs included nine presentations on vehicle electrification given over three sessions on the final morning of the conference. This author attended this SIP to
learn more about this interesting and important area of Powder Metallurgy, which is presented, in summary, here.
Over the past several years, a recurring theme – and for many a recurring concern – in the PM industry is the extent to which it is impacted by vehicle electrification, and how much this will affect PM in the future, in particular, in terms of the volume and type of PM compo -
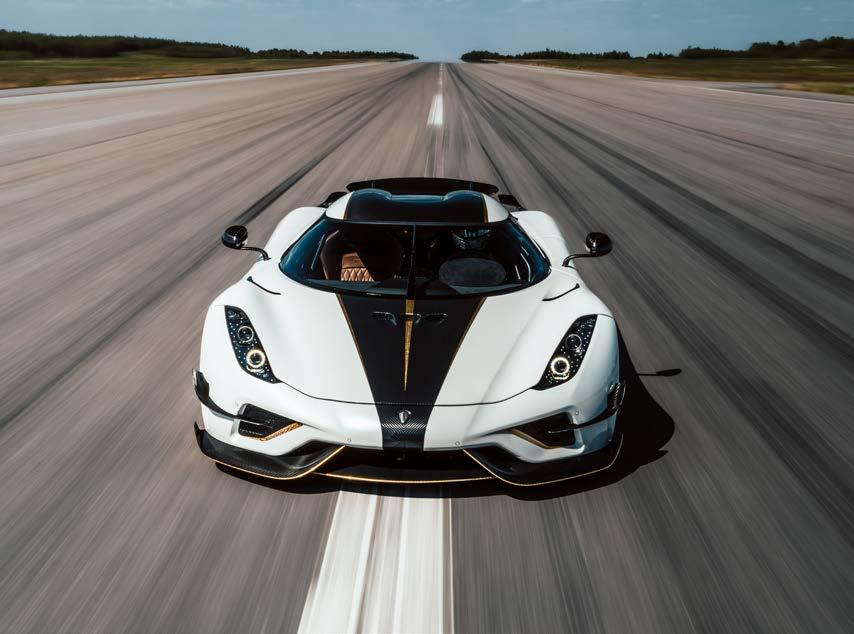

Fig. 1 Koenigsegg’s Regera hybrid supercar features three SMC motors from YASA (Courtesy Koenigsegg)

Ignition Coils
motor stators
Burgess Norton






“...recent trends in the North American automotive market have seen rapid growth of hybrids and much slower growth than anticipated for full battery electric vehicles. This gap between expectation and reality presents new opportunities – and more time to adjust – for the PM industry...”
Nine presentations, separated into three sessions, were given on the final morning of PowderMet. Because of their importance and topicality, some of the focus areas of the SIP sessions on vehicle electrification were repeated from the MPIF conferences in Portland, Oregon, a year earlier. Seven of the presentations were on SMCs and different electric motor designs and how variants of
the latter can favour SMC adoption; some of the papers emphasised the SMC materials science aspects while others were more focused on the electric motor designs. One presentation was on ‘hard’ permanent magnets, while another covered the important subject of drivetrain mechanisms in BEVs and HEVs and the opportunities for PM iron components to be used in the same.
Soft Magnetic Composite presentations
Vehicle electrification and the application of SMCs
Bruce Lindsley of GKN Hoeganaes gave a high-level presentation on vehicle electrification and the associated use of SMCs in electrified vehicle drivetrains [3]. Battery Electric Vehicles (BEVs) now comprise at least 50% of car and light truck sales in China, but only ~9% in the USA; in the latter market, BEV growth appears to have stalled, while hybrids (primarily Full Hybrid Electric Vehicles and, to a much lesser extent, Plug-in Hybrid Electric Vehicles) are in rapid growth mode. ‘Announced pledges’ for combined BEV and PHEV growth (for example, the US Government’s target of 50% of car and light truck sales being BEV or PHEV by 2030, and similar pronouncements from some automakers) will clearly not be met. Most automakers with ambitious BEV growth plans have scaled them back in light of growing inventories and expectations of lower BEV market share.
Lindsley also highlighted the simple calculus most US car buyers are dealing with, referencing how a family vehicle like a FHEV Honda Accord sedan averages 50 miles per US gallon (4.7 litres/100 km, or 60 miles per imperial gallon). While policy goals of tailpipe emission reductions aided by vehicle electrification are occurring, these are primarily through hybrids, not full BEVs. These hybrids require both conventional ICE and electric motor components.

Flux density
Retentivity
Saturation
Coercivity Magnetising
Magnetising force in opposite direction
Saturation in opposite direction Flux density in opposite direction
“SMCs are an alternative to steel sheet laminates, which work by amplifying the magnetic field generated around copper coils in motor armatures, solenoids, or other actuators; for high efficiency, they must have little or no ‘memory’ and thus demagnetise quickly...”
SMCs are an alternative to steel sheet laminates, which work by amplifying the magnetic field generated around copper coils in motor armatures, solenoids, or other actuators; for high efficiency, they must have little or no ‘memory’ and thus demagnetise quickly when the field is removed. In practice, this means high-purity iron is needed: for laminates, efficiency is achieved by a very high number of very thin pure steel sheets with air gaps between (up to 95% steel/5% air by volume); for SMCs, pure iron particles are separated by an inorganic coating. Laminated sheets have a strong directionality aspect which tends to favour the much more common radial flux motor design, while SMC armatures work better at higher frequencies and favour the less
common axial or transverse electric motor design types. The steel cores for such motors are also more ‘PM design-friendly’, although the low mechanical strength of SMCs is a concern. Such motors are also more compact, use less copper wire and require less permanent magnet material. Still, it will take time for the electric motor industry to make a widespread switch to wholly different designs, and collaboration with PM parts markets is key to accelerating this shift.
The effect of compaction temperature and insulation components on the magnetic properties of SMCs Lindsley [4] also gave a detailed presentation on the effect of compaction temperature and insulation components (coating and lubricant)

Fig. 3 Magnetic hysteresis curve [4]
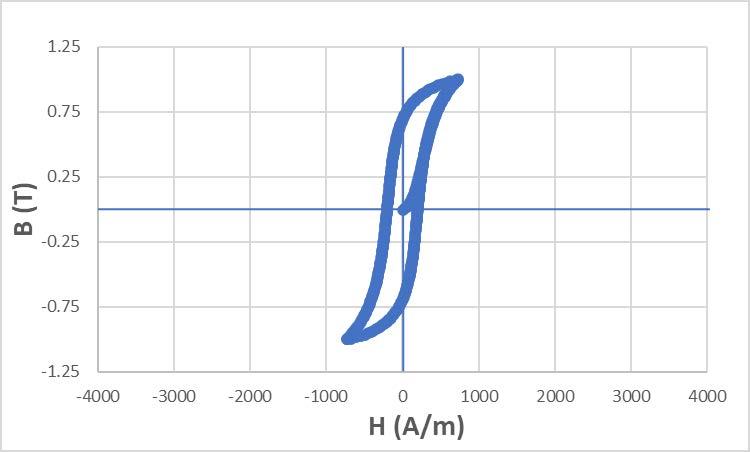
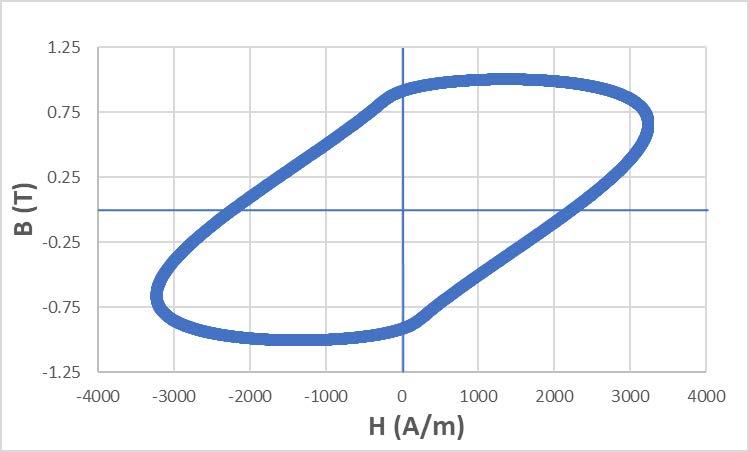
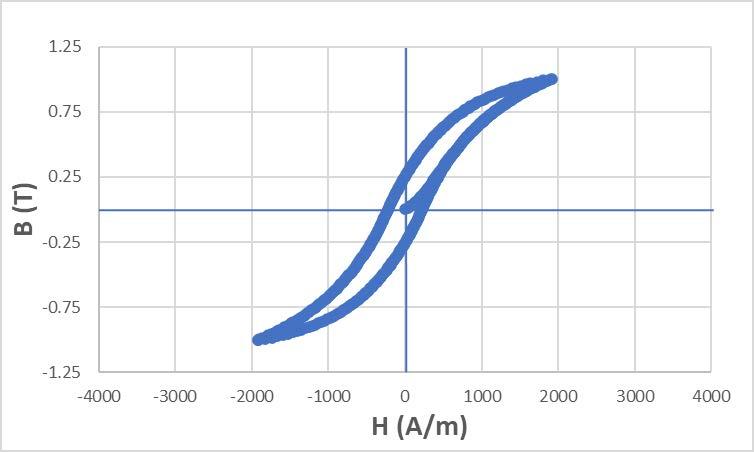
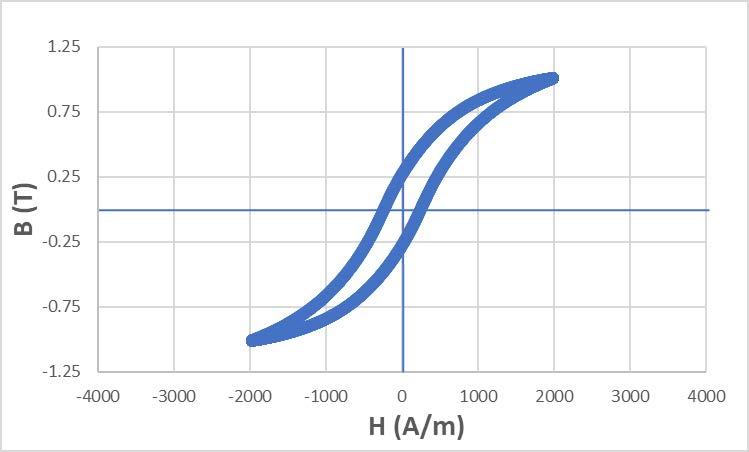
on magnetic properties (illustrated with hysteresis curves (Fig. 3)) of SMCs. Specifically, direct current (DC) and alternating current (AC) properties varied as a function of lubricants, die wall lubrication, and warm die compaction temperature. In brief, plots of magnetic flux density
against magnetising force, during magnetising and demagnetising, are used to determine how good SMC properties are, with a ‘steep, narrow’ form being strongly preferred, and with the frequency of the magnetising and demagnetising cycle also being a factor.
“Fe powder particle size is important –larger particles give lower hysteresis loss, while smaller ones give lower eddy current losses – depending on the application details, one or the other may be a better choice.”
Fe powder particle size is important; larger particles give lower hysteresis loss, while smaller ones give lower eddy current losses. Depending on the application details, one or the other may be a better choice. Lindsley described detailed designed experiments using Ancorsteel 1000C (a very pure, high compressibility iron powder) with and without an insulation coating, with and without admixed lubricant (zinc stearate die wall lubrication was used with no admixed lubricant), at different compaction pressures over a range of die temperatures from 4-175°C, followed by curing in nitrogen gas at 500°C (Fig. 4). Increased compaction temperatures improve permeability but worsen core loss, while the effects of coating and lubricant are additive with respect to the creation of insulation between particles.
Fig. 4 Effect of die wall lubrication, particle coating, and pressing lubricant on direct and alternating current hysteresis curves in a study using Ancorsteel 1000C [4]
Micro-Indentation Hardness


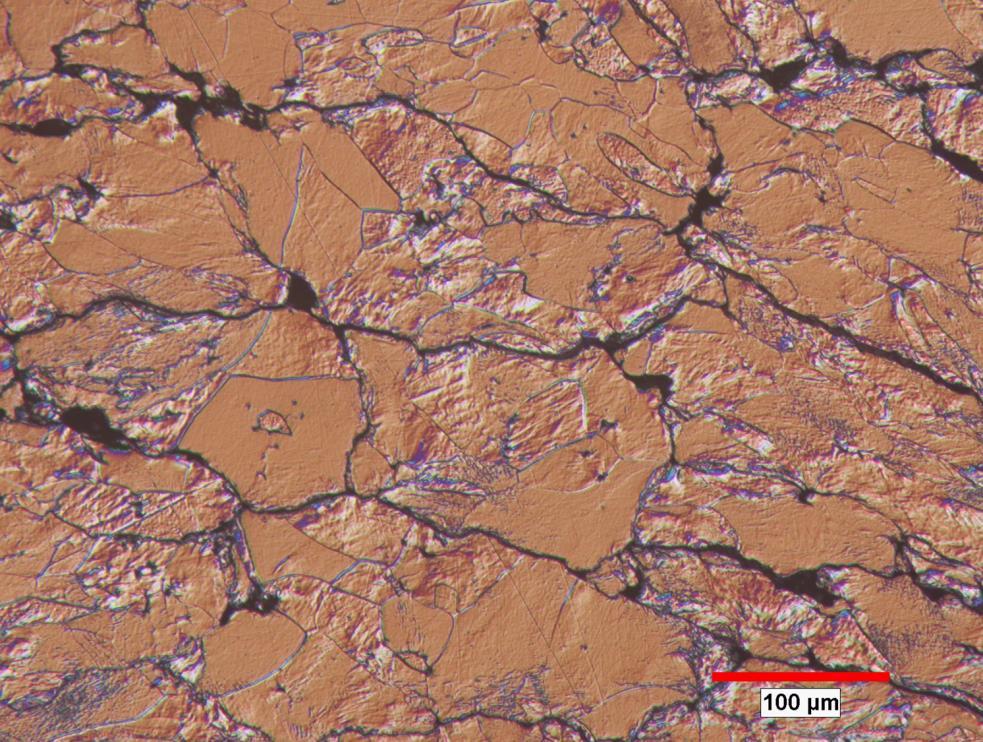





4 °C
DW, 100 °C
Coat+Lube, 4 °C
Coat+Lube, 100 °C
Fig. 5 Microindentation hardness testing gives higher readings in deformed (D) than in smooth, undeformed (S) areas of SMC Fe grains. There is some effect also of die temperature, powder coating, and lubricant [4]
and DC (direct current) motors, but being unsuitable for AC (alternating current) applications due to high eddy current losses. For such applications, SMCs (polymercoated Fe powder composites) were developed, with advantages over the conventionally used steel sheet laminates at high frequencies (especially above ~400 Hz) and/or due to the non-directional properties of the PM product.
Narasimhan summarised the processing route: melting of pure Fe, atomisation to (typically) ~100 µm particle size (although finer particles are better for very highfrequency applications), annealing, polymer coating (often carried out in a fluid bed with the polymer dissolved in a fungible solvent) followed by warm die pressing at high compaction pressures and then curing in N 2 gas at ~450°C to produce dense (~7.5 g/cm 3) compacts. Post-pressing after curing can be used to further
increase density. He explained that developments date back to 1993, when Hoeganaes worked with Unique Mobility on proof-of-concept and with General Motors on claw pole design motors.
In 2004, SMCs were used in a brushless electric bicycle motor, while other early applications included common rail fuel injection systems for diesel engines and choke coil cores. Narasimhan mentioned the common theme of the good fit between axial flux electric motors and SMCs, largely due to the iron part being a stator (not a rotor) and hence the relatively low mechanical properties of a nonsintered material being less of a concern, though the cost compared to steel laminates is still problematic.
In summary, after three decades, commercial applications have been
patchy, with SMCs having both strong and weak aspects. MPIF standards and a design manual are critical to capitalising on the expanded opportunities that vehicle electrification brings.
Electric motor design and SMCs
Recent vehicles using SMCs in electric motors
Roland Warzel of North American Höganäs summarised [6] recent vehicles using SMCs in electric motors, some non-automotive applications and, lastly, reviewed SMC-related work performed by a subcommittee of MPIF’s Standards Committee, of which he is a member. He started by summarising five BEV or hybrid vehicles using axial flux electric motors with SMC components:
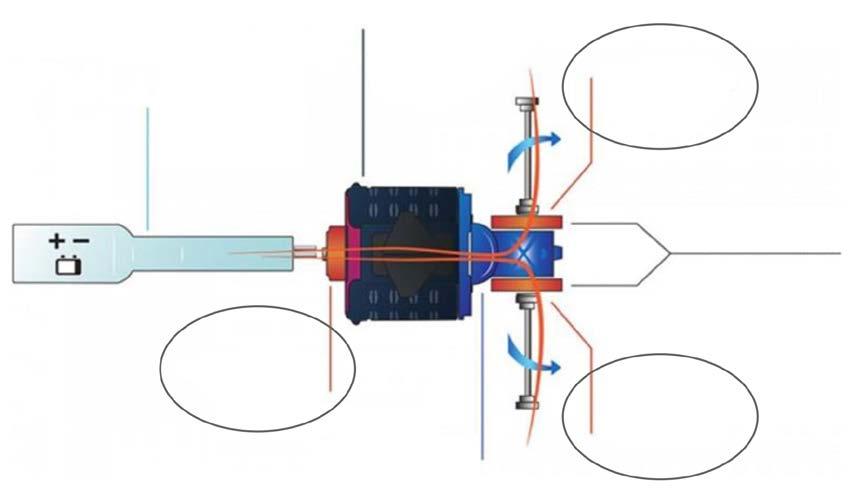
Ford Mustang Mach-E 1400
This experimental BEV car uses seven axial flux SMC motors. The ‘street’ versions use laminate steel motors.
Mercedes Benz Vision AMG
Expected to be launched in 2025 at ~ $100,000, the car features YASAdeveloped axial flux SMC motors.
Overall, the use of SMCs in eMotors is slowly increasing – initially through very expensive vehicles, but very gradually approaching the mass market nonetheless. The YASA motor concept simplifies production and reduces the need for all the key materials involved – iron, copper windings, and rare earth magnets, leading to very high power densities and better vehicle range. The technology was promising enough that Mercedes purchased YASA in 2021. Electrified bicycles are another area where SMCs are being investigated, with transverse flux design SMC eMotors in (currently limited) use, with advantages in terms of compact design and good low-speed power.
“Overall, the use of SMCs in eMotors is slowly increasing – initially through very expensive vehicles, but very gradually approaching the mass market nonetheless. The YASA motor concept simplifies production and reduces the need for all the key materials involved...”
The Koenigsegg Regera
Approximately eighty of these cars have been made since 2015, ~$3.2 million per car, with each car featuring three YASA motors.
Detailed information on the Regera’s propulsion system is shown in Fig. 6.
Ferrari SF90 Stradale
This hybrid ~$500,000 car features two radial flux sheet steel laminate
motors and one SMC-using axial flux motor with almost twice the power density (14 vs 8 kW/kg), and also less need for rare earth magnets.
McLaren Artura
This hybrid ~$200,000 car features one SMC axial flux motor driving the front wheels with ~1/3 higher power density than the laminate eMotor used on an earlier model.
Warzel also summarised the work of the subcommittee of the MPIF Standards Committee working towards an SMC standard under MPIF Standard 35, with powder producers having completed two rounds of testing, making toroidal and transverse rupture bars, testing mechanical properties, and having a third-party laboratory measure magnetic properties. A third round is in progress, after which the data will be reviewed and material property proposals will go to ballot. Such standards data are critical to building end-user confidence, with benefits for both BEVs, FHEVs, and PHEVs, as well as numerous smaller automotive and also non-automotive applications.
An analysis of published papers and patents for materials and design concepts critical to the large-scale electrification of vehicles
Chantal Labrecque of Rio Tinto Metal Powders gave a presentation [7] summarising analyses of
Fig. 6 Koenigsegg Regera propulsion overview and eMotor characteristics [6]

SMC by patent assignees–Companies* 2021-2024
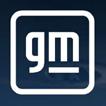
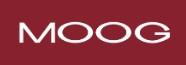
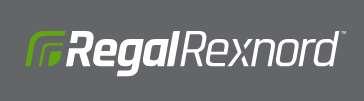
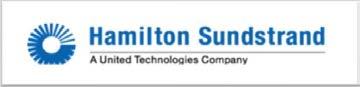
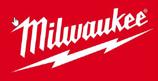
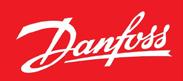
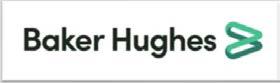
EU USA ASIA
published papers and patents as well as market forecasts for materials (electrical steels and permanent magnets) critical to large-scale electrification of vehicles and many other markets. These markets show significant growth, with CAGR forecasts ranging from 6-9%, as well as strong growth of vehicle electrification (defined as hybrids, both plug-in and otherwise, and battery electric vehicles) comprising ~30% share of the global automotive market in 2023 and with estimated 12% CAGR until 2030.
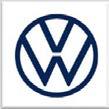

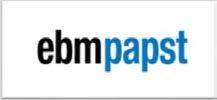
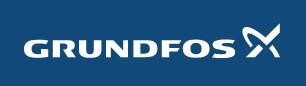
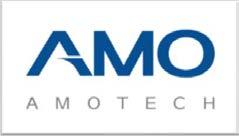
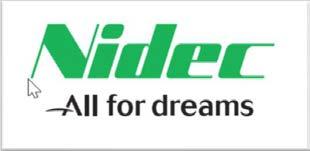
+ Multiple Chinese Companies
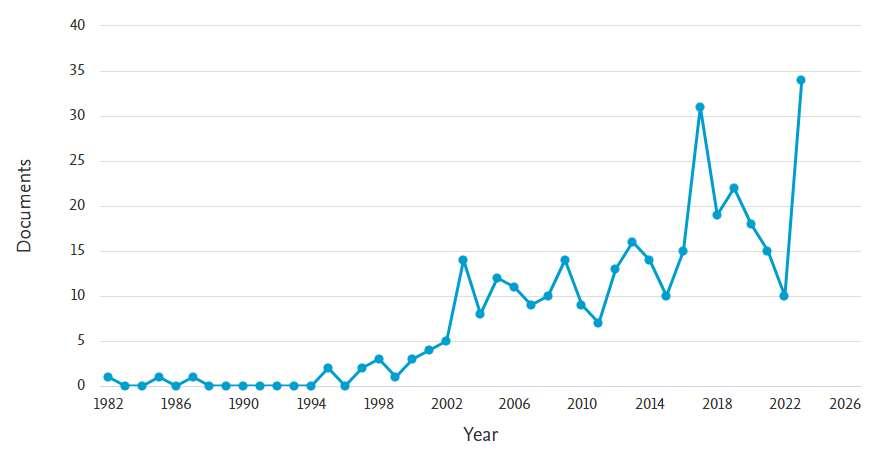
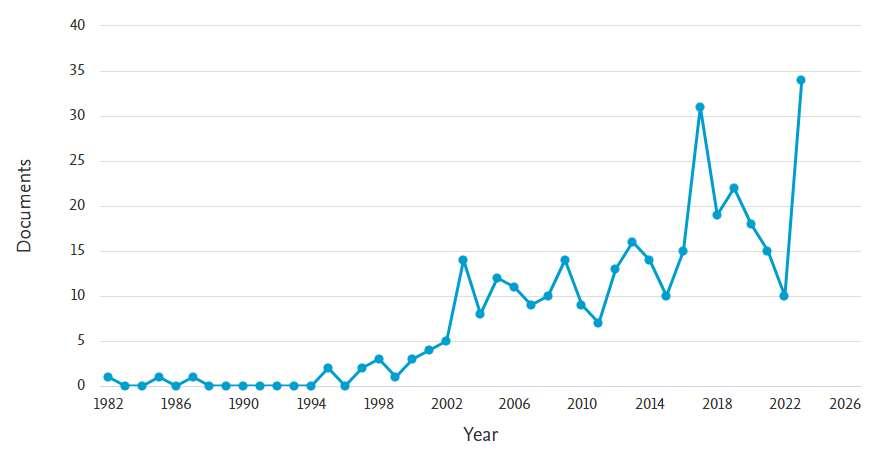
expectation is that SMCs will grow in all motor design variants, sometimes combined with traditional steel laminates for the stator and often in non-automotive applications, primarily (in the near-term at least) for secondary automotive applications such as coolant pumps. Key drivers include the growth of BEV, PHEV, and FHEV markets; the demand for more efficient, compact,

• Between 2014 and 2023 the number of papers on SMC in electric motors nearly doubled compared to that of 2004-2013
• SMC materials are almost exclusively used in the stator
• Since 2020, two types of electric motor designs are predominant in the literature for SMC: axial flux and claw-pole designs
Fig. 7 SMC/eMotor recent patent assignees [7]
Fig. 8 Growth of SMC/eMotor published paper frequency [7]
Motor Topologies with SMC
Three 15 kW PM motors containing SMC were designed and simulated using 3D FEA


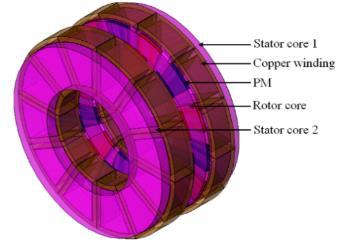
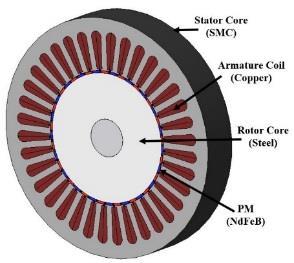
Advantages:
▪ High torque density (high pole number)
▪ Simple copper winding
Challenges:
▪ Unconventional
▪ High torque within low axial length
Challenges:
▪ Mechanical challenge with axial force Advantages:
Advantages:
▪ Reliability and mature technology
Challenges:
▪ High copper loss in the end-windings
Efficiency Comparison for Different Designs
and advanced motor designs with reduced reliance on critical materials; and supportive government incentives. However, these factors are tempered by the current small scale of SMC production, resistance to change, and a generally low tolerance for risk.
Opportunities for SMCs in future e-mobility programmes
Comparison for Different Designs
Troy Goldschmidt of Alvier Mechatronics GmbH summarised [8] SMCs as comprising Fe particles in the range 20-500 µm in size, bonded with polymeric materials 0.5 µm or less in layer thickness. SMCs’ low mechanical strength results in them being considered primarily for stator applications. The company mainly works with automotive clients, but also in other markets, including agriculture, mining, and lawn and garden, where companies are looking for electrification upgrades or new applications.
In agreement with other speakers, Goldschmidt sees automotive uses for SMCs initially in auxiliary applications like cooling pumps, before becoming mainstream for traction motors in BEVs or hybrids. He summarised a detailed study looking at the radial flux, electrical steel laminated motor used in the VW iD3, which indicated that using SMCs with some design optimisation would reduce the weight and CO 2 footprint by ~10% for a motor of similar
Fig. 9 Motor topologies with SMC [9]
Fig. 10

output. He also discussed the YASA axial flux motor characteristics, in particular its space and weight benefits.
The advantages of SMCs over sheet steel laminates
Fabrice Bernier of the National Research Council (NRC) Canada [9] summarised the advantages of SMCs over sheet steel laminates as low eddy current loss, the ability to ‘carry’ a three-dimensional flux, reduced part counts, and highfrequency performance. SMCs shortcomings are low magnetic permeability, high hysteresis loss, and low mechanical strength. Fe particle size is an important variable; typically, SMCs have ~100 µm particle size, but this can be varied to fine-tune properties: a coarser size increases magnetic permeability and saturation while reducing resistivity and hysteresis loss. Other important variables include lubricant content, compaction pressure, and ‘curing’ temperature. Bernier mentioned the 2007 review by Shokrollahi and Janghorban [10] as a good reference work. He then summarised the pros and cons of the three main eMotor design families (claw pole/transverse flux, axial flux, and radial flux) (Fig. 9) and described a redesign exercise on a 15 kW claw
pole motor which demonstrated a 20% weight reduction with similar output. A detailed modelling exercise of all three motor design types – at the 15 kW power level, using the published properties of three different commercial SMC grades and in both acceleration and cruise modes – was described, showing much higher efficiencies for the claw-pole and axial flux motor designs as well as the need to select SMC grade carefully with respect to the design and expected duty cycle of the motor (Fig. 10).
Permanent PM magnets
Permanent hard magnets and their relevance to vehicle electrification
Fabrice Bernier of NRC Canada gave an overview [11] of permanent hard magnets and their relevance to vehicle electrification. ~85% of the drivetrain eMotors used in BEVs and hybrids employ permanent magnets made by a PM process (Fig. 11), averaging 1.5 kg per motor, and with a range from 1-4 kg per vehicle. The most common are NdFeB compositions due to their excellent power densities, but with ~10% of the composition being Dy or Tb to improve the high-temperature performance needed for compact,
powerful motors used under a range of conditions. The high cost (~5-10x) premium of these heavy rare earth elements is a problem, especially as they are disproportionately needed for automotive applications – estimated 2025 demand for precursor Nd 2O 3 material is 12% for electric vehicles but 43% for Dy 2O 3, and they rank very highly on the US Department of Energy’s analysis of both importance and supply risk. Bernier summarised several approaches to address these concerns:
Increase and localise production
Bernier mentioned the MP Materials Mountain Pass, California mine and Houston, Texas, magnet production plant and $58.5 million US government support for them; the GM – Vacuumschmelze agreement for a North American factory; and Quadrant Magnetic’s announcement of a Kentucky factory.
Develop new rare earth-free magnets
MnBi, MnGa, and MnAl were mentioned, but the highest promise is with alpha Fe 16N 2. This clearly has no strategic materials concerns but still needs further development, with GM, Stellantis, and Magna having partnered with Niron Magnetics on same.

Fig. 11 NdFeB magnet production process [11]
5
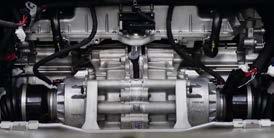
EV & Hybrid Drivetrain Disconnects
Functional Options
• On/Off disconnect
• Next-Gen disconnect with One-Way-Clutch
D Drivetrain Integration
• Integrated in Gears
• Differential disconnect
Modular Side Shaft
Wheel Hub


EV 2 Speed Powershift Systems
Functional
• No torque interruption
• Passive One-Way-Clutch
C Configurations
• Co-Axial Planetary Parallel-Axis Combination
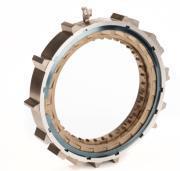

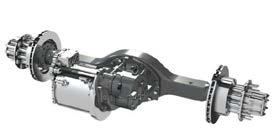
Multi-Speed OWC Based Shift Systems
Functional
• No Friction Elements
• Neutral / Disconnect Mode
• 3-5 mode systems
C Configurations
• Co-Axial Planetary
• Parallel-Axis
• Combination
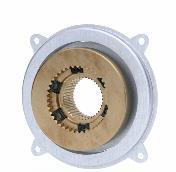
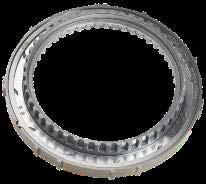
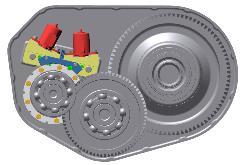
Electronic Park-Lock
Functional
• Park Lock / Hill Hold
• Multi-Mode:
C Configurations
Stand alone
• Combine with disconnect or shift system
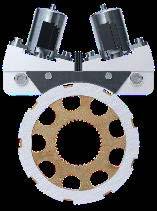
Reduce cost
Use cheaper, more widely available rare earths, for example Nichia’s development of SmFeN.
Reduce the weight of magnets required
Reduce magnet need through motor re-design: axial vs radial flux design types; Bernier also mentioned a 3D curved motor design. In addition, the use of MIM or AM techniques can provide benefits through more advanced geometries in both weight reduction and anisotropic magnetic properties.
More widespread and efficient recycling
Bernier noted a major increase in technical literature on this subject in the past decade, and the use of H 2 embrittlement followed by crushing.
PM steels in BEV and Hybrid powertrains
PM for mechanical interconnects used in drivetrains
George Coppens of Amsted Industries discussed [12] a very different aspect of PM use driven by vehicle
“George Coppens of Amsted Industries discussed [12] a very different aspect of PM use driven by vehicle electrification: complex mechanical interconnects used in the drivetrain, which may include PM steel components, with variants of such mechanisms being used by BEVs and hybrids...”
electrification: complex mechanical interconnects used in the drivetrain, which may include PM steel components, with variants of such mechanisms being used by BEVs and hybrids, and with all-wheel drive (AWD) capability also affecting what systems are required (note that Amsted Industries is the parent of Burgess Norton, a major supplier of PM steel components for automotive applications [13], recently including components for the types of mechanisms covered in the presentation).
Coppens summarised that the key differences between an ICEonly vehicle and a BEV are that the latter has a dedicated eMotor for each driven axle and a one- or two-speed transmission combined with the drivetrain. BEVs require great attention to minimising power losses to maximise range or minimise battery capacity for a given range, while hybrids benefit by reducing fuel consumption, thus making it critical to avoid or minimise the use of hydraulic systems. NVH (Noise, Vibration, Harshness) reduction is also more critical than for ICE-only vehicles. He proceeded to describe several torque management solutions in production and/
Fig. 12 Torque management solutions for electrified vehicle drivetrains [12]
Radial Dynamic Controllable Clutch
Electro-magnetic actuator
Pocket plate
Controllable clutch
Features

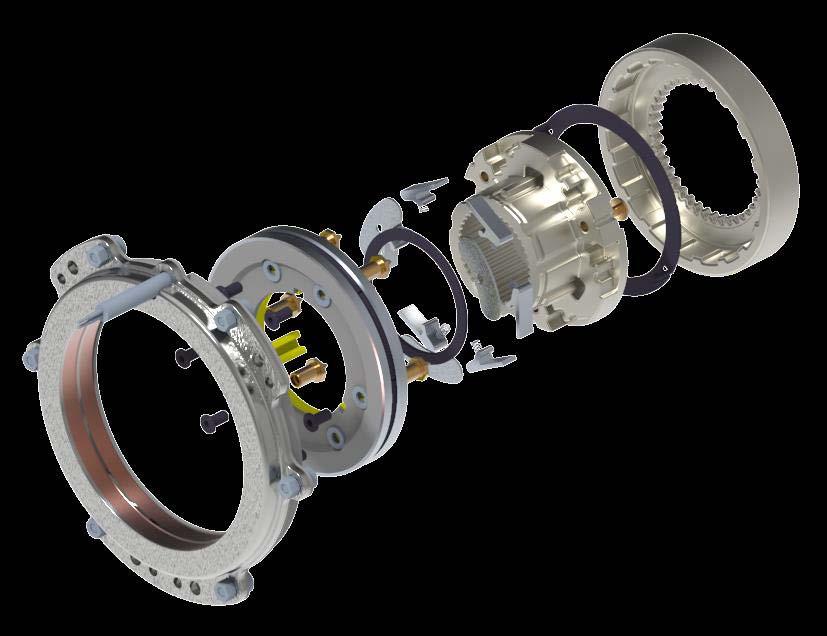
or development: EV and hybrid drivetrain disconnects (in simplified terms, analogous to providing freewheeling capability on a bicycle), EV two-speed powershift systems, multispeed shift systems, and electronic park locks (Fig. 12). A common factor in most of these systems is that they must handle the very high torque generated by eMotors. Automotive engineers want the systems to be very compact and lightweight, which in turn leads to very high stresses in some components.
Coppens outlined both the current and potential applications of PM steels in various systems, including: a second-generation axle disconnect utilising three PM plates; a radial dynamic controllable clutch (Fig. 13) featuring a PM steel notch plate and pocket plate (note that larger versions for Class 8 trucks exclude PM due to high torque and long lifespan demands); a differential controllable disconnect with multiple PM components; a lockable, limited-
• Used for shifting in passenger
• Actuation system in-state
• Functions at
Notch plate
“BEVs require great attention to minimising power losses to maximise range or minimise battery capacity for a given range, while hybrids benefit by reducing fuel consumption, thus making it critical to avoid or minimise the use of hydraulic systems.”
slip differential in development with six possible PM components; an overrunning dynamic controllable clutch incorporating a PM pocket plate; and several other possibilities across approximately twenty customer-driven projects. Coppens was very frank in expressing concerns about the future of PM in such applications – on the technical side, the trend
is towards ever higher material yield strength requirements which represent a stretch for MPIF Standard 35’s conservative data, and which drive developments in die wall lubrication and other techniques to increase density (7.45 g/cm 3 and ultimate tensile strength (UTS) of 1,600 MPa were mentioned as approximate targets. Cost issues associated with die
Fig. 13 Components of a Radial Dynamic Controllable Clutch. The notch plate and pocket plate may be made from PM steel [12]
2023
Quarterly Market Share Sales for US Light Cars and Trucks by Drivetrain Type
BEV
“Vehicle efficiency improvement, and for that matter the general drive to improve energy efficiency, is driving new applications for SMCs, not only within various types of powertrain systems but also in ancillary systems. To improve energy efficiency across all vehicles, parasitic power losses are being minimised through the use of small
motors and electromechanical devices...”
tooling amortisation driven by the currently low production volume of EVs, lack of PM knowledge in EV startup companies, and vertical integration and likely collaboration of OEMs may also tend to ‘shut out’ PM. Since PowderMet 2024, mechanical property targets have been more precisely defined [14] as 1,670 MPa UTS at 50 Rockwell C hardness, and 1,965 MPa UTS at 55 Rockwell C hardness.
Discussion
The author admits to being no expert on SMCs or hard permanent magnet materials, but is familiar with PM and other closely related materials, and is also a vehicle ‘buff’ who follows trends in vehicle electrification, so this SIP was very interesting and educational to attend. Attending each of the presentations and doing some reading about the subject permits some summary observations:
Much of the technology has been around a long time Narasimhan’s references to work going back as far as 1993 brought out the fact that – as is common with many developments in PM (and indeed materials science in general) – SMCs have been around for decades with, so far, (apparently) only rather modest levels of commercialisation.
Vehicle efficiency improvement is bringing opportunities
Vehicle electrification, and for that matter the general drive to improve energy efficiency, is driving new applications for SMCs, not only within various types of powertrain systems but also in ancillary systems. To improve energy efficiency across all vehicles, parasitic power losses are being minimised through the use of smaller electric motors and electromechanical devices for functions such as cooling, braking, and air conditioning. This trend is already opening up significant opportunities for SMCs, with even greater potential on the horizon.
Fig. 14 2023 passenger vehicle sales by drivetrain type and major geographical market [16-20]
Fig. 15 Quarterly sales market share of US market light cars and trucks [20]
There is a diverse range of use cases
SMCs may be used to good effect in a variety of electromechanical applications, including the three main types of eMotor designs: clawpole (transverse flux), axial flux, and radial flux. SMCs characteristics best fit the former two designs, which are, however, far less common at present than the conventional radial flux design type. Fine-tuning of SMCs is required according to the details of motor design and their duty cycles.
There are clear benefits in terms of compactness, weight reduction, reduced critical materials requirements, and efficiency, which are obvious drivers for automotive manufacturers to move towards those eMotor designs (claw-pole and axial flux) that are best-suited to SMC use.
Conventional technologies should not be underestimated
As mentioned in some of the SIP presentations and expressed especially clearly by Bruce Lindsley of Hoeganaes in a presentation given in a regular session [15], it is important to remember that the conventional sheet steel laminates that SMCs compete with are actually superior at low frequencies and, thus, in DC (direct current) motors.
Bridges need to be built between the PM industry and the electric motor industry
Speakers expressed the opinion that the lack of much crossover between the electric motor and PM communities, the need to develop and implement different manufacturing processes for high-volume production of new motor designs, and general conservatism and long development timelines will be manifested as slow growth of SMC use in such motors.
EVs offer different opportunities to hybrids
It is reasonable to conclude that the benefits (in terms of initial cost and/or range) to the vehicle user of moving to transverse or axial flux
“...the PM industry must heed Coppens’ caution that the trend to make such mechanisms more compact, while handling the very high torque of eMotors, will tend to drive designers to wrought, machined steel components unless PM parts makers shift to higher density, higher-yield-strength steels backed by MPIF Standards.”
motors are greatest for BEVs (which have the most powerful eMotors and where initial cost and vehicle range are very dependent on the eMotor characteristics), less for PHEVs, and less still for FHEVs.
In this regard, it is interesting to consider how vehicle electrification is proceeding in different major markets. The large markets where electrification is most advanced are China, Japan, and Europe, but in very different ways. In China, for example, BEVs are very prevalent [16,17]. By comparison, the Japanese market is dominated by hybrids [18]. 2023 data [19] for the European Union indicates a more balanced split by electrification type, while the US market [20] has the lowest degree of electrification (Figs. 14, 15). Electrification is rising in all the automotive markets, but with a recent development seen both in sales data [17, 20, 21] and announcements of major automotive manufacturers (and mentioned in the 2024 MPIF State of the North American PM Industry) being a – possibly temporary – softening of demand for BEVs, but continued and possibly accelerating growth of hybrids.
Applications evolve slowly and bring unique challenges
The speakers shared a common expectation that increased SMC application will initially come more from ancillary automotive and non-
automotive applications, due to an expected slow rate of fundamental eMotor redesign for the main drivetrain units.
Regarding the use of PM steels in drivetrain mechanisms used in electrified vehicles, it was good to hear from Coppens of Amsted Automotive about the existing actual and potential greater use of PM components in such mechanisms; the geometry of said components is a good fit with multi-level uniaxial die pressing. However, the PM industry must heed Coppens’ caution that the trend to make such mechanisms more compact, while handling the very high torque of eMotors, will tend to drive designers to wrought, machined steel components unless PM parts makers shift to higher density, higher-yield-strength steels backed by MPIF Standards to increase designer confidence.
Permanent PM magnet use will also rise as electric motors grow in use, and their critical raw materials aspect should be a key factor encouraging motor redesign, which would also benefit SMC use. However, this trend could be lessened somewhat if vehicle electrification proceeds more heavily along the hybrid rather than BEV route; hybrid eMotors are generally less powerful, require lower quantities of strategic raw materials, and their efficiency is also less critical to overall vehicle performance

It will be both fascinating and crucial for the PM industry to observe the pace and direction of vehicle electrification, as well as how it translates into new PM opportunities and products.
References
[1] B North, ‘Cemented Carbides brought into focus in Pittsburgh,’ PowderMet2024 and AMPM2024 report, PM Review, Autumn 2024.
[2] M Stuckey, ‘PowderMet2024: The state of the Powder Metallurgy industry in North America,’ PM Review, Autumn 2024.
[3] B Lindsley, ‘Current State of SMC Technology and Electrification Trends in the Auto Industry,’ Vehicle Electrification Special Interest Program, PowderMet2024, MPIF.
[4] B Lindsley, ‘Iron-based Powder Solutions for Soft Magnetic Composite Applications,’ Vehicle Electrification Special Interest Program, PowderMet2024, MPIF.
[5] K Narasimhan, ‘Coated Iron Powder in Soft Magnetic Applications, Challenges, and Benefits,’ Vehicle Electrification Special Interest Program, PowderMet2024, MPIF.
[6] R Warzel, ‘Trends and Standards Committee Update,’ Vehicle Electrification Special Interest Program, PowderMet2024, MPIF.
[7] C Labrecque, ‘SMC and E-motor Case Studies,’ Vehicle Electrification Special Interest Program, PowderMet2024, MPIF.
[8] T Goldschmidt, ‘Soft Magnetic Composite Opportunities in Future E-Mobility,’ Vehicle Electrification Special Interest Program, PowderMet2024, MPIF.
[9] F Bernier, ‘SMC Materials Selection for EV Applications,’ Vehicle Electrification Special Interest Program, PowderMet2024, MPIF.
[10] H Shokrollahi & K Janghorban, ‘Review: Soft Magnetic Composite Materials (SMCs),’ Journal of Materials Processing Technology 189 (2007) 1-12.
[11] F Bernier, ‘Permanent Magnets for EV Applications: Opportunities for the PM Industry,’ Vehicle Electrification Special Interest Program, PowderMet2024, MPIF.
[12] G Coppens, ‘Applications and Opportunities for Powder Metallurgy in Next-Gen Electric Vehicle Drivetrains,’ Vehicle Electrification Special Interest Program, PowderMet2024, MPIF.
[13] B North, ‘Burgess-Norton and Amsted Automotive: How a legacy automotive supplier is growing with, not despite, electrification,’ PM Review Winter 2022.
[14] G Coppens, Communication to B North.
[15] B Lindsley & N Kraus, ‘Comparison of Soft Magnetic Composites (SMC) and Lamination Assemblies,’ PowderMet2024, MPIF.
[16] 26% BEV Share in China! – China EV Sales Report, CleanTechnica 2023/12/01.
[17] Cheap and efficient: hybrid cars gain favour in China as EVs stoke range anxiety, South China Morning Post, August 30, 2024.
[18] Share of electrified passenger car sales in Japan in 2023, by type of vehicle, Statista 13937749.
[19] New passenger car registration in the European Union in 2023, by leading powertrain, Statista, 1301925.
[20] Q3 2024 Electric Vehicle Market Share and Sales (US), CarEdge, October 15, 2024.
[21] 2024 (Half Year) Europe: Car and BEV Sales by Country (EU, UK, EFTA), Best Selling Cars, July 18, 2024.
Author
Bernard North North Technical Management, LLC Greater Pittsburgh area Pennsylvania, USA
brnrdnorth@gmail.com
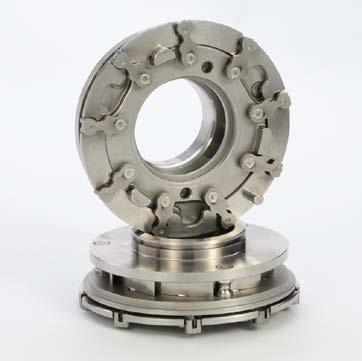

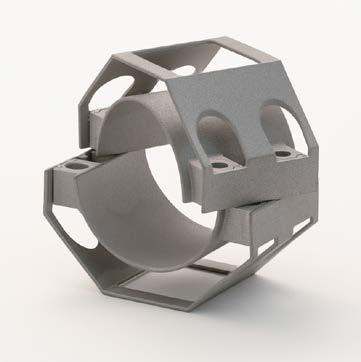
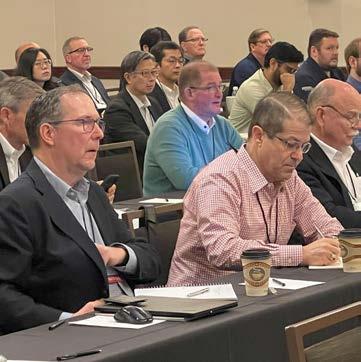
Professor Randall M. German’s 6 decades of Powder Metallurgy (PM) and Powder Injection Molding (PIM) research, including metals (MIM), ceramics (CIM), carbides, and composites, has influenced countless students, researchers, and collaborators worldwide. To honor his legacy, the Metal Powder Industries Federation (MPIF), Metal Injection Molding Association (MIMA), and global PIM experts will gather to showcase groundbreaking developments in PM and PIM inspired by or conducted with Prof. German.


Honorary sponsor
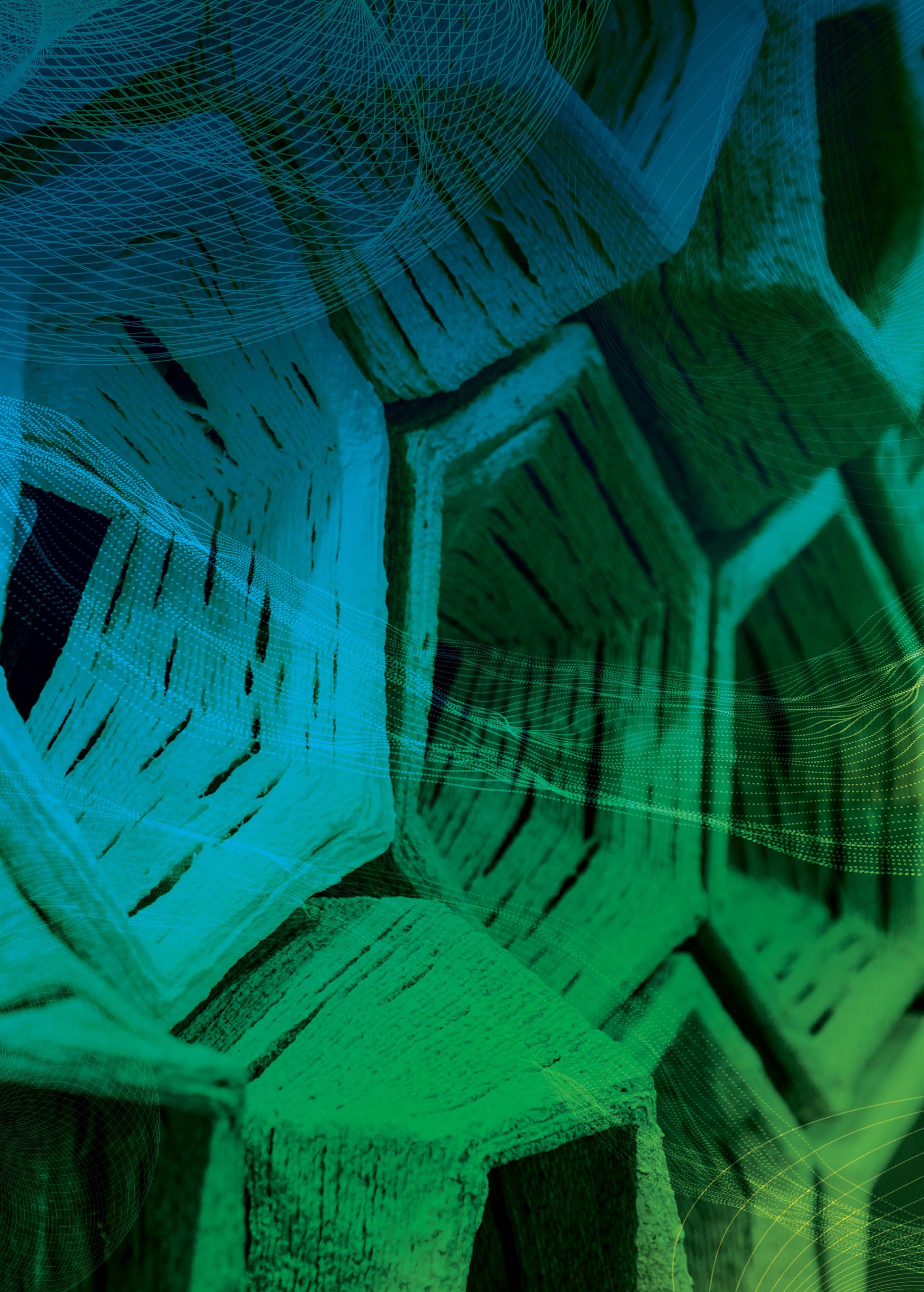
The hub for Additive Manufacturing
As the hub for Additive Manufacturing, Formnext is the international meeting point for industrial 3D Printing experts and production professionals from a wide range of application industries. With the trade show in Frankfurt as well as content throughout the year, Formnext bundles expertise and creates a unique experience focused on an intensive, professional exchange and access to the latest AM solutions.
Be part of Formnext and learn how you can be ahead of your competition thanks to Additive Manufacturing.
Where ideas take shape.
formnext.com
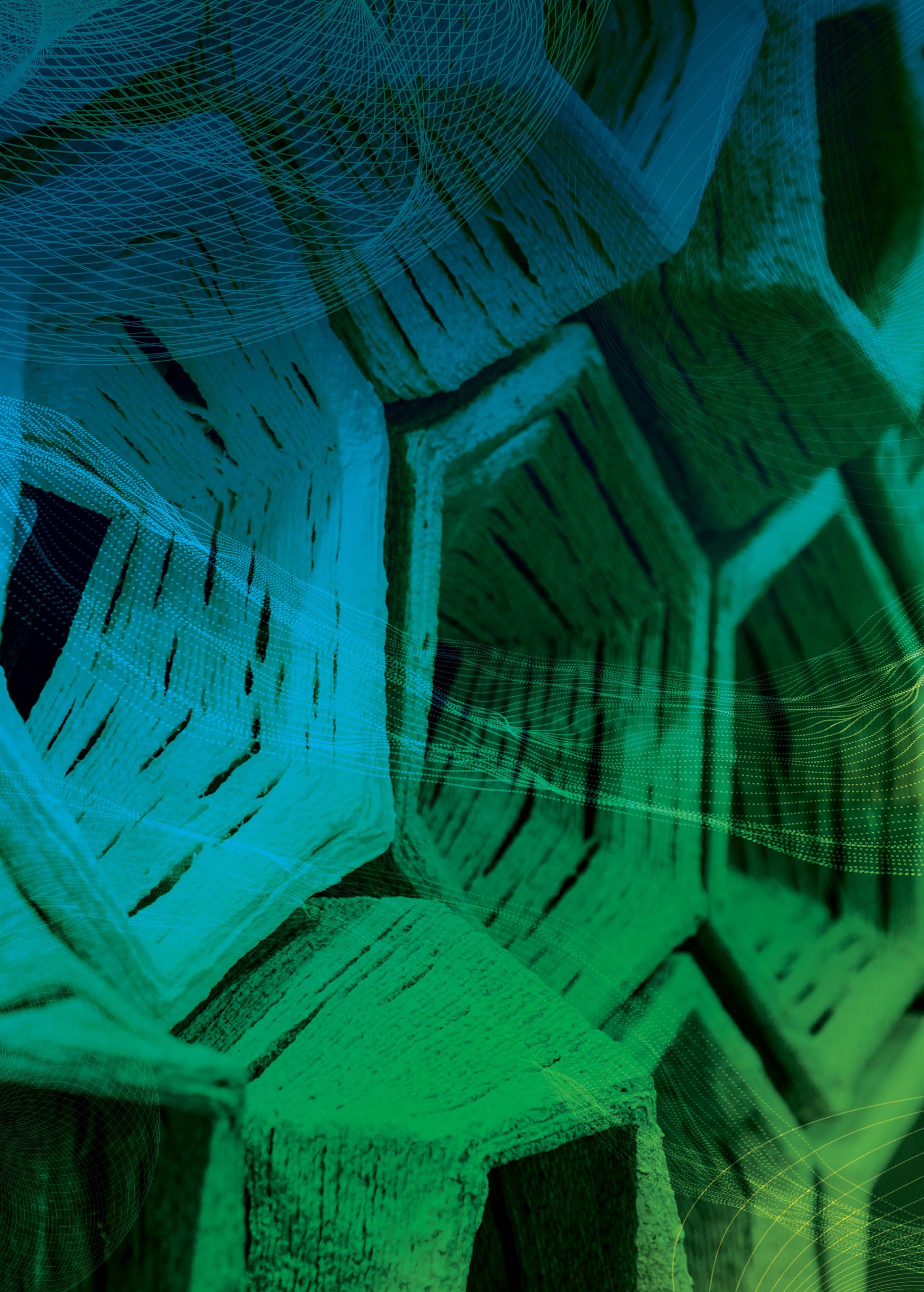
Gevorkyan a.s.: Europe’s fastgrowing Powder Metallurgy company achieving success through a diversified customer base
Slovakia’s Gevorkyan a.s., founded in 1996 by Artur Gevorkyan, has grown into one of the fastest growing Powder Metallurgy companies in Europe. With a diverse product portfolio and a broad range of metal powder-based technologies, the company has proven itself to be highly adaptable and resilient during economic challenges. Dr Georg Schlieper visited the company for PM Review and reports on its extraordinary journey, culminating in a recent expansion following a successful IPO in 2022.
Gevorkyan a.s. is situated in Vlkanová, a village not far from the former mining town Banská Bystrica in the Slovak low mountain ranges. The company was founded in 1996 by its General Manager and majority shareholder, Artur Gevorkyan. While the political changes resulting from the collapse of the Soviet Union were largely over by the time of its founding, its impact still overshadowed the company’s early years. Artur was born in Armenia, then part of the Soviet Union, in 1964. As a young adult, he joined the Soviet military and studied metallurgy at the National Aerospace University in Kharkiv, Ukraine, where he focused on the development of composite materials for military aircraft. An interest in Powder Metallurgy may have been genetic: his father, Robert Gevorkyan Snr, introduced the technology to Armenia in the 1970s when he set up the production of hard carbides and magnets. When Mikhail Gorbachev became president of the Soviet Union in 1990, the political principles of
glasnost and perestroika opened up new freedoms for the population. Artur took advantage of his position as a high-ranking Soviet Air Force officer to seize these new opportunities, leaving the military and returning to Armenia to work with his father. However,
when Armenia broke away from the Soviet Union, energy supplies from Russia were interrupted. The family business had to stop production and Artur moved to Kharkiv, where he applied to establish a private factory for magnets and diamond tools.
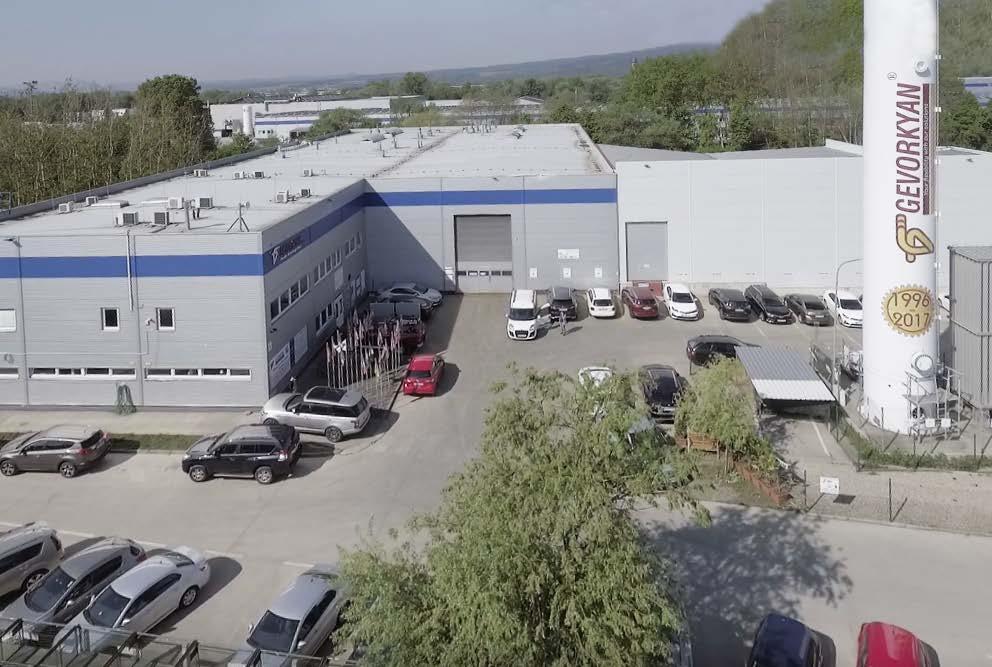

Fig. 1 Aerial view of the Gevorkyan factory in Vlkanová, Slovakia (Courtesy Gevorkyan)
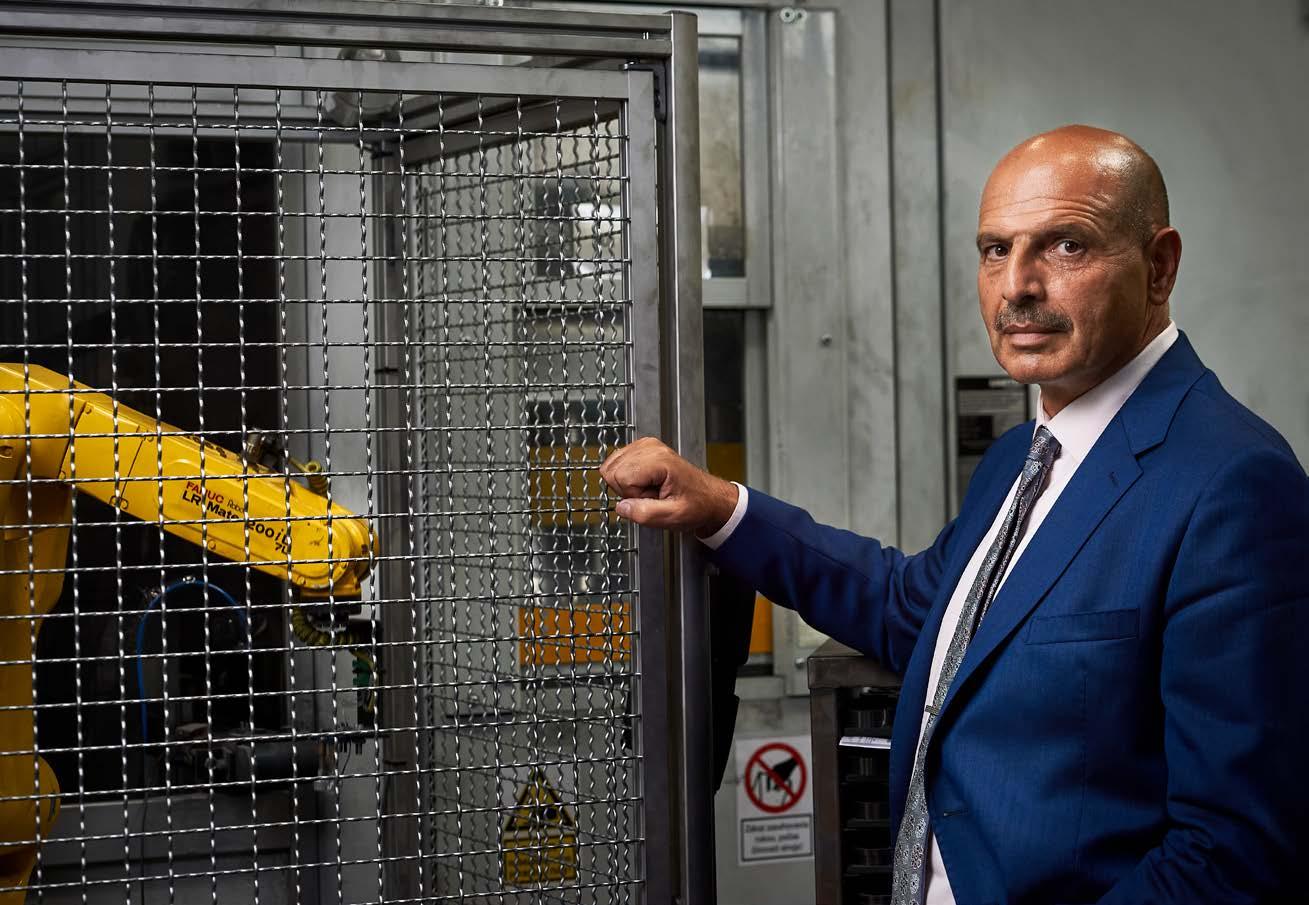
The first few years were difficult. The transition from a communistplanned economy to a free market economy saw many administrative challenges. It took nine months before Artur was able to register his company for the production of magnets. Once established, Artur had to be resourceful. He recalls manufacturing products using a selfbuilt press and a self-built sintering furnace; even constructing a
hydrogen generator from a hairdryer. He travelled widely to generate sales, often accepting payment in the form of goods, which he then resold to generate profit.
When the first enquiries came in from countries outside the former Soviet Union, Gevorkyan realised that these customers would have higher material quality demands than Russian customers. He began to import high-quality raw materials
“When the first enquiries came in from other countries outside the former Soviet Union, Gevorkyan realised that these customers would have higher material quality demands than Russian customers. He began to import high-quality raw materials from Western Europe to meet the quality requirements.”
from Western Europe to meet the quality requirements. However, the trucks used for shipments faced waiting times of up to two weeks each time they crossed a border. To meet delivery times, Artur considered setting up interim storage facilities in different customer countries, but this was not a costeffective solution.
Instead, production itself was moved closer to the company’s new customers. Slovakia – which had only separated from Czechoslovakia in 1993 – was chosen. Thus, in 1996, Gevorkyan was founded as a limited company in Banská Bystrica and existing production equipment was transferred from Ukraine to the new site. “After a year,” Artur recalled, “we realised that our raw materials from Western Europe were just as expensive, or even more expensive, than finished magnets from China.” As a result, Gevorkyan’s production equipment for magnets had to be sold or scrapped.
Fig. 2 Artur Gevorkyan inside the factory in factory Vlkanová, Slovakia (Courtesy Gevorkyan)
But Artur did not give up. Alongside two engineers, he established a sintered bearings factory. Since neither machines nor money were available, both the press and sintering furnace, and a device for the electrolytic production of hydrogen, were again developed in-house. To obtain investment funds, 10% of the company was sold in 1998 for $10,000, with a further 10% later sold for $12,000.
“In the first few years, we worked under parlous conditions,” Artur remembered. “Our company was small and dirty; we had no money to equip a laboratory. As a result, we only received orders that our competitors in Europe rejected. We had to accept all the orders that were offered to us in order to have any income at all, even if the quantities were often very small. This was challenging, but sometimes also technically very appealing, because we learned to produce unusual sintered products. Over time, we became more confident and gradually ventured into more complicated parts.”
Diversification in times of crisis
In its early years, the firm was not taken seriously by the automotive industry, leading the company to seek out applications in other markets instead. Artur sees the experience he gained in this early period as a great advantage because the structure of his customers and the portfolio of his products differed significantly from that of other PM companies, something that is still the case today. This is reflected in the fact that the automotive industry still accounts for only 32% of sales (Fig. 4). Gevorkyan’s portfolio of ‘fantastic diversification’ also contributes to power tools (16%), lock and security systems (15%), oil industries (12%), and the medical device sector, as well as a number of other, smaller markets.


Fig. 3 Sintering of PM parts (Courtesy Gevorkyan)
Fig. 4 Gevorkyan serves a highly diversified customer base
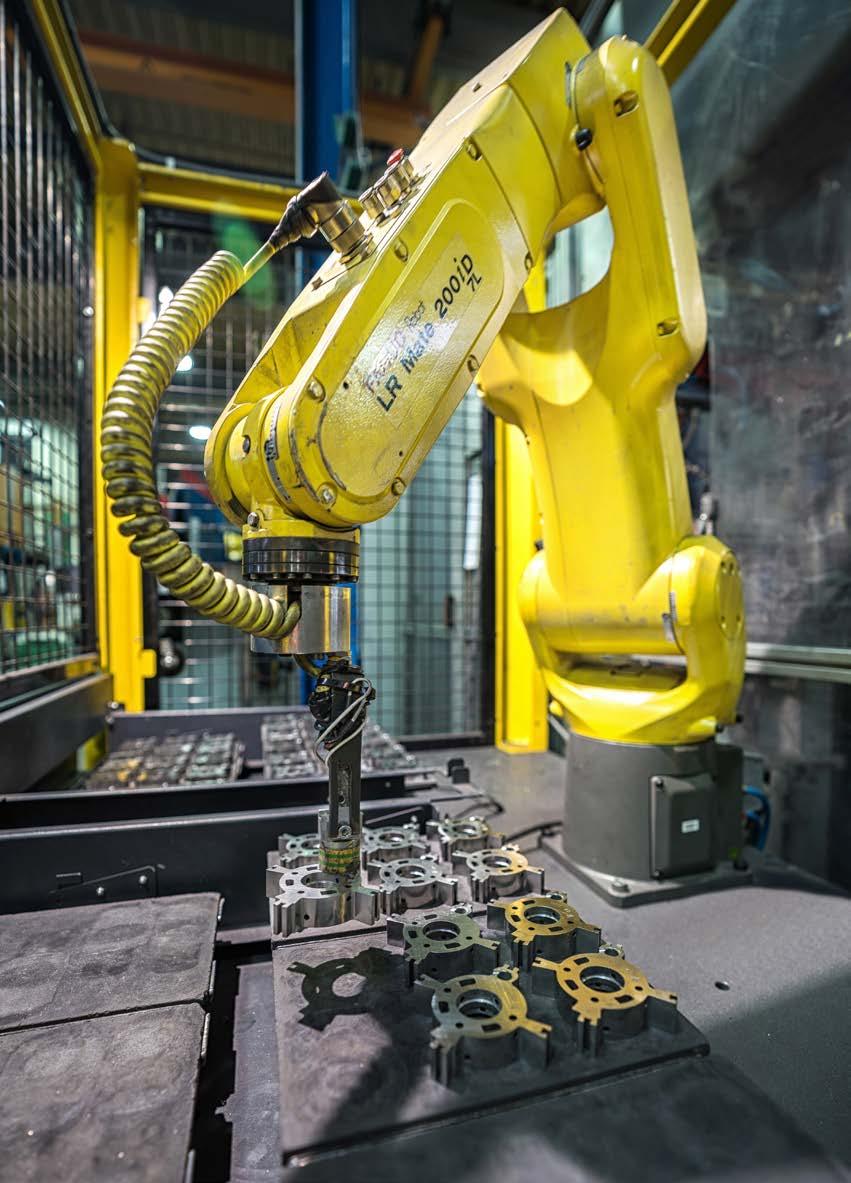
During the two economic crises faced by the PM industries in recent years, this diversification allowed the company to cope much better than many other PM companies. Gevorkyan was able to increase sales against the trend in the rest of the PM industry. In the crisis of 2008, Gevorkyan’s incoming orders fell as abruptly as every other company’s. But, out of the blue, a significant order was received, which not only brought the company through the crisis unscathed but led to a doubling of the powder volumes used.
Artur told PM Review that the origins of this order date back to before the crisis began. Several parts, produced by machining and subsequently welding together, were to be redesigned into a complex sintered component. Gevorkyan was confident in the production of these parts and submitted a bid, but a German competitor declared the project too complicated and declined to continue the process. This made the customer hesitate and hold off giving the order to Gevorkyan, fearing the risks involved. However, when the economic crisis hit, the cost savings offered by the sintered part were suddenly so attractive that the customer, now under time pressure, finally ordered the parts.
The various lockdowns during the COVID-19 pandemic also led to massive slumps in sales in the PM industry. However, Gevorkyan noticed that, after a short time, the demand for PM parts for power and garden tools suddenly increased because many people bought these devices and used the enforced time at home to take up DIY projects or carry out repairs in their homes and gardens that they wouldn’t have previously had time for. This reduced the impact of the pandemic on the company, allowing sales volumes to grow steadily (Fig. 6).
Artur explained, “For a long time during this period, the logistics department was under particularly great pressure. On the one hand, customers who urgently needed their parts pushed hard for rapid
Fig. 5 The efficiency gains achieved through automation have been central to the company’s growth (Courtesy Gevorkyan)
Fig. 6 Sales growth and staff count, from 2014 to the present day

deliveries and, on the other hand, production could hardly keep up with the demand for so many different parts. Sometimes, the parts weren’t even allowed to cool down before they were dispatched in passenger cars.”
For the past thirty years, production has been running continuously around the clock in four shifts. Even on religious holidays, production continues. On Catholic holidays, the Orthodox part of the workforce operates the plant, and on Orthodox holidays, the Catholic part of the workforce take over.
Gevorkyan’s transformation into a modern PM factory
Between 2015 and 2019, Gevorkyan’s workforce was temporarily reduced as a result of rationalisation initiatives (see line in Fig. 6), even though sales volumes increased continuously. Today, employment is at a new high at around 200, with around
10% comprising the R&D department, making Gevorkyan the most significant industrial employer in the area. About a third of the workforce has a university education. From the very beginning, Artur attached great importance to staff training, with opportunities for staff
to develop their professional skills. With an average age of thirty-five, the workforce is relatively young. Gevorkyan feels closely connected to the country and its people, receiving awards from public organisations for its social commitments. The company also hosts social activities to estab -
“Today, employment is at a new high at around 200, with around 10% comprising the R&D department, making Gevorkyan the most significant industrial employer in the area. About a third of the workforce has a university education. From the very beginning, Artur attached great importance to staff training...”

Fig. 7 A selection of PM parts produced by Gevorkyan (Courtesy Gevorkyan)


lish and maintain relationships with employees, their families, and the wider community.
“People are reliable and hardworking; staff turnover is low. The job at Gevorkyan is the first job for many employees,” Artur stated. He suggested that it may, in part, be that the company’s Slovakian location offers many advantages. Energy prices are relatively low, and the site is conveniently located between the metropolises of Bratislava, Budapest, Kraków, and Vienna.
From 2009-2020, production capacity was continuously expanded and production equipment modernised. In 2015, the first robotic arms were installed for the automation of production. While the company is able to produce powder mixtures in-house, the preference is for pre-mixes produced by powder suppliers. The company has received numerous awards from customers for delivery reliability.
The in-house tool shop, which has forty employees, supplies the
Fig. 8 Metal Injection Moulding now accounts for 15% of sales (Courtesy Gevorkyan)
Fig. 9 Detail of textured MIM parts (Courtesy Gevorkyan)
company with press, sizing, and injection moulding tools. 2015 also saw the installation of a Hot Isostatic Press (HIP) furnace. The HIP process is used when the residual porosity that is usually present in PM parts has to be eliminated in order to achieve the highest mechanical strength. Parts with closed surface porosity can be HIPped without encapsulation. At temperatures of 1,000°C, the parts are recompressed with gas pressures of up to 1,500 bar.
Gevorkyan has about forty mechanical and hydraulic powder and sizing presses with press forces between 15 and 300 tons. While a key focus of PM part production is on small-to-medium sizes, Gevorkyan has ordered new 500-ton and 700-ton presses for projects that lean towards larger dimensions. Continuous sintering furnaces and batch sintering furnaces are also available, including high-temperature sintering in hydrogen for stainless steels.
In recent years, Metal Injection Moulding (MIM) and sinter-based Additive Manufacturing (AM) technologies have been introduced. MIM parts account for 15% of sales, and the number is rising, with parts for handguns – mainly exported to the USA – being a growing demand (Fig. 10). Gevorkyan uses solvent debinding technologies to remove most of the binder from the green parts, with any residual binder then thermally removed before the parts are sintered.
About half of the company’s turnover is generated by conventional press-and-sinter technology, and a further fifth of sales is contributed by special products for the oil industry, while one-tenth of sales is generated from soft magnetic components. AM production accounts for around 6% of the sales volume (Fig. 11).
A wide range of PM materials are produced at Gevorkyan, from low-alloy, case-hardening and quench-and-temper steels to stainless steels, copper-based materials, soft magnetic alloys and silver. Most of the secondary processes


11 Sales by process type at Gevorkyan
Fig.
Fig. 10 A selection of MIM and PM parts, including at the top, a large MIM firearms component (Courtesy Gevorkyan)

commonly used in the PM industry, such as CNC machining, turning, grinding, honing, case hardening, soldering, and plastic impregnation, are available in-house. Production capacities have been, and are being, continuously expanded.
Quality assurance is based on a fully equipped test laboratory for mechanical tests and material analyses. Gevorkyan’s quality management system is certified according to the ISO 9001 standard. Other certifications include ISO 14001 (environment), IATF 16949 (automotive industry), ISO 13485 (medical technology) and ISO 45001 (occupational safety).
Expanding the range of applications for PM
Most of Gevorkyan’s products are exported. Customers in Europe account for 58% of sales; North America, 23%; Central and South America, 9%; and Asia, 10% (Fig. 13). Gevorkyan maintains international relations through numerous agencies worldwide and is a member of the European Powder Metallurgy Association (EPMA).
Overseas representatives provide customers with on-site technical support for the development of new parts. The company’s philosophy is not to refuse any request; the word ‘impossible’ does not exist for Artur. When a customer has a technical problem, Gevorkyan’s engineers do everything they can to find a solution. This includes material selection, design and the entire manufacturing process. In this way, Gevorkyan makes a significant contribution to product development for its customers and, at the same time, expands the field of application of Powder Metallurgy. According to Artur, about half of all PM parts from his production have never been produced by the process before, so they are new PM applications.
For the development of new parts, Gevorkyan relies primarily on his experienced R&D team. The company launches 150 new parts
Fig. 13 Gevorkyan’s sales by global region
Fig. 12 A selection of stainless steel PM parts (Courtesy Gevorkyan)

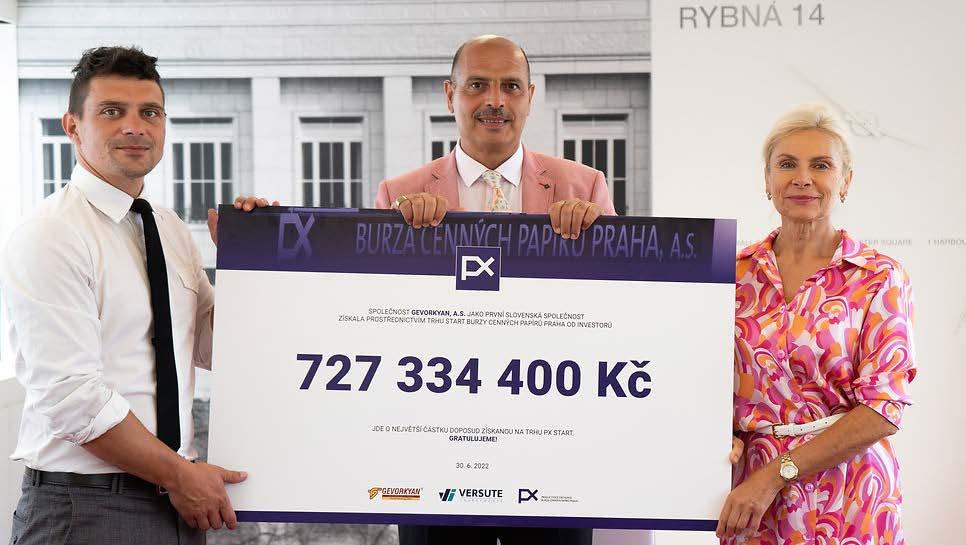
“Gevorkyan’s financial situation changed fundamentally when the company went public on the Prague Stock Exchange in 2022. After the IPO, Gevorkyan received €30 million and invested the money in a larger production hall and modernised production facilities.”
every year. Technical solutions that are satisfactory in terms of both function and cost-effectiveness are developed in close contact with the customer, building trust with customers so that they are more likely to reach out to Gevorkyan in the early stages of any further projects.
The company promotes Powder Metallurgy as a raw-material-saving and low-polluting process for the production of metallic components. Gevorkyan has an environmental manager tasked with implementing changes to reduce environmental pollution. Improvements have
already been undertaken to reduce the company’s carbon footprint, including the installation of nitrogen and hydrogen generators on the factory premises, as well as solar panels.
2022: Gevorkyan lists on the Prague Stock Exchange
Gevorkyan’s financial situation changed fundamentally when the company went public on the Prague Stock Exchange in 2022 (Fig. 14). After the IPO, Gevorkyan received €30 million and invested the money
in a larger production hall and modernised production facilities. Despite Gevorkyan’s transformation from a private family business to a listed company, the characteristics of a family business remain intact. Artur still owns 77% of the shares, is chairman of the supervisory board, and has sole decision-making power over the company. Artur’s son, Robert Gevorkyan Jr, is already working in the company, ensuring that the company’s future stays in the family when Artur retires.
Contact
Artur Gevorkyan SK-97631 Vlkanová, Slovakia artur.gevorkyan@gevorkyan.sk www.gevorkyan.sk
Author
Dr Georg Schlieper D-45133 Essen
Germany georg.schlieper@hotmail.de
Fig. 14 Artur Gevorkyan (centre) with his wife, Iryna Yeumianenka, and financial director Andrej Batovsky presenting the revenue of the IPO (Courtesy Gevorkyan)
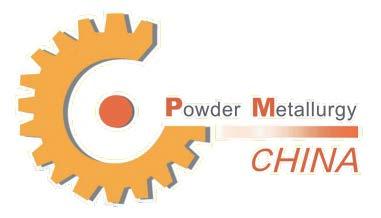
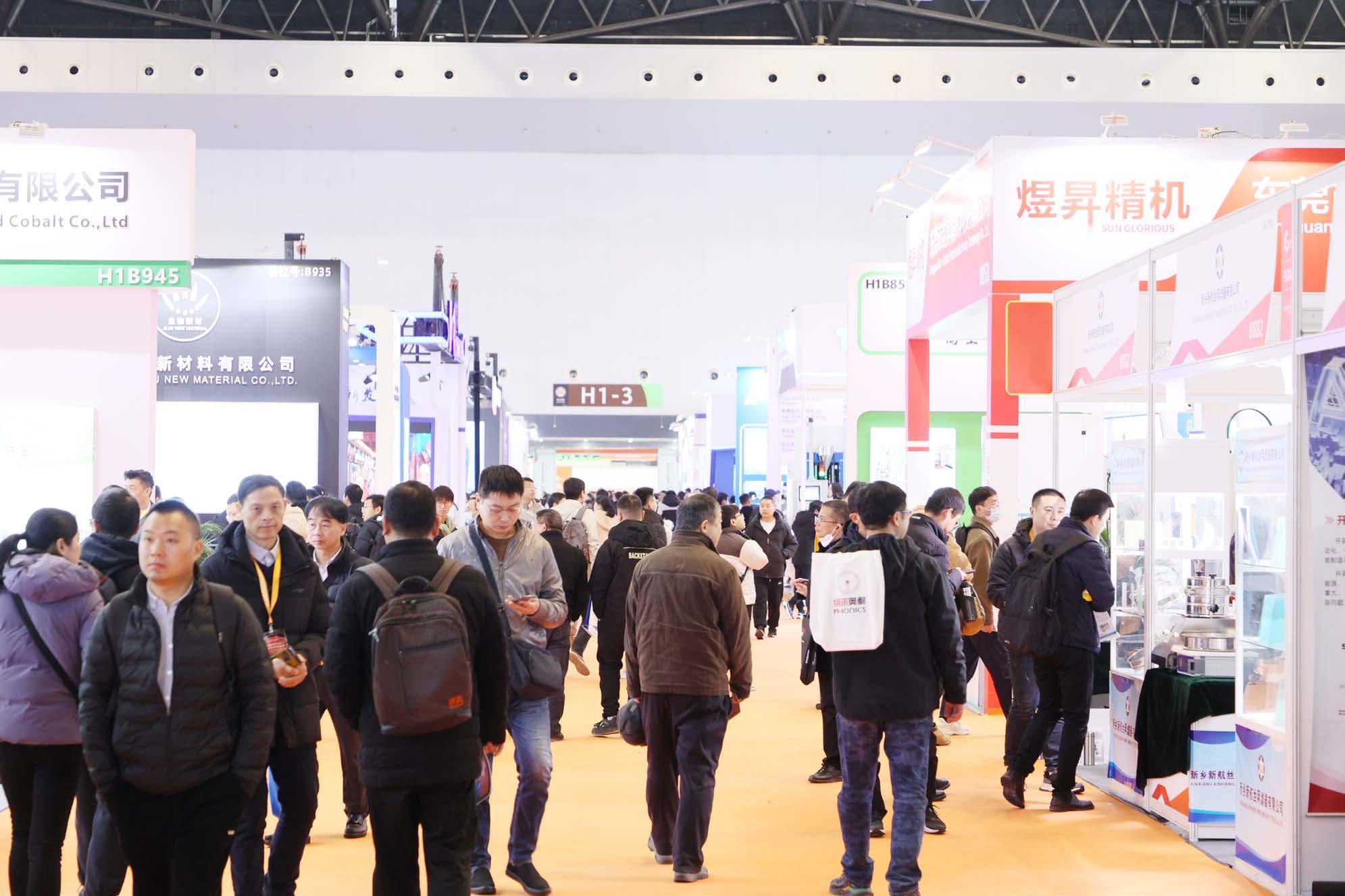
50,000+
Powder Metallurgy in Asia: A status update from the World PM2024 Congress, Yokohama
The Powder Metallurgy World Congress series has long been a cornerstone event for the PM industry, offering a vital platform for global collaboration and innovation. Following disruptions caused by COVID-19, World PM2024 marked the series’ successful return, attracting nearly 800 delegates and offering a comprehensive technical programme. The event also highlighted the Powder Metallurgy industry’s resilience amidst significant ongoing challenges. Here, Nick Williams reports on the status of Powder Metallurgy in Asia as presented during the Plenary Session, including market trends, regional growth potential, and opportunities for Powder Metallurgy in an evolving global landscape.
The Powder Metallurgy World Congress series has been a highlight of the industry’s event calendar for many decades. Since 1994, PM World Congresses have taken place every two years, rotating between Asia, Europe and North America. COVID-19 disrupted the schedule with the cancellation of the 2020 Montreal, Canada, congress. Following World PM2022 in Lyon, France, the series returned to Yokohama, Japan, from October 13-17, organised under the auspices of the Asian Powder Metallurgy Association (APMA). Given widespread geopolitical uncertainty, a seemingly reduced appetite for intercontinental business travel following the COVID-19 pandemic, and the rapid proliferation of new international events focused on metal Additive Manufacturing, the continued viability of the PM World Congress series is something that the industry cannot take for granted. A successful return of the series to Asia was, therefore, crucial for the global
PM industry, and its outcome was highly anticipated.
The good news is that, despite all of the PM industry’s current and future challenges, the Japan Powder Metallurgy Association (JPMA) and the Japan Society of Powder and Powder Metal -
lurgy (JSPM) proved that many in the global PM community still have the willingness to support the event and foster the spirit of international collaboration and exchange that has been the driving force of past PM World Congresses.


Fig. 1 World PM2024 took place in Yokohama, Japan, October 13-17


History of PM associations in Asia
Chu started by outlining the history of PM associations in Asia. The Japan Powder Metallurgy Association, he stated, is the oldest of Asia’s PM Associations, formed in 1956. Two years later, in 1958, the Japan Society of Powder and Powder Metallurgy was formed. The Powder Metallurgy Association of India (PMAI) was formed in 1973, followed by the Taiwan Powder Metallurgy Association (TPMA) in 1980. The growth of PM in Korea in the 1990s resulted in the formation of the Korean Powder Metallurgy & Materials Institute (KPMI) in 1993 and the Korean Powder Metallurgy Association (KPMA) in 2000. In the same year, the China Powder Metallurgy Society was formed.
In 2008, the Asian Powder Metallurgy Association was inaugurated, driven by the goal of ensuring the development of Powder Metallurgy in Asia. The APMA’s functions include coordinating the venues for the Asian PM World Congress and the APMA’s conference, fostering communications and networking between Asia’s PM-producing nations, collecting and preparing statistics on PM in Asia, and the advancement of standardisation activity. Following the formation of the APMA, the China Powder Metallurgy Alliance (CPMA) joined in 2013, and the Thailand Powder Metallurgy Association joined in 2015.
Attracting nearly 800 congress delegates from twenty-seven countries, as well as many more visitors to the extensive exhibition of PM industry suppliers, World PM2024 featured a technical programme that encompassed the full scope of the Powder Metallurgy industry and the rising field of metal Additive Manufacturing. A busy exhibition and lively social events offered ample networking and a warm welcome was given by the whole Japanese PM community, whose members
were keen to take the opportunity to grow their international networks.
From the perspective of visitors from outside of Asia, the event presented an opportunity to better understand the status of the region’s Powder Metallurgy industry through presentations and informal conversations. The presentation ‘Overview and Trends of the PM Industry in Asia’ by ChiuLung Chu, president of APMA, in the opening session of World PM2024 offered a broad insight.
Statistical overview of PM in Asia
Chu shared comprehensive data on PM part production over the period of 2017-2023 (in tonnes), broken down by country and differentiated by iron-base materials or copperbase materials (Table 1). Looking at Asia as a whole, the impact of COVID-19 and the shift to Electric Vehicles (EV) and Hybrid Electric Vehicles (HEV) production is clear.
Fig. 2 Delegates at the World PM2024 opening ceremony
Fig. 3 The congress’ ‘Make a better world with PM’ theme was illustrated in a live show by an artist working with metal powders

Iron powder usage in Asia 2017-2023
Fig. 4 Estimated usage of iron powder in Asia, 2017-2023 (Data courtesy JPMA, PMAI, KPMI, TPMA, CPMA)
Copper powder usage in Asia 2017-2023
Fig. 5 Estimated usage of copper powder in Asia, 2017-2023 (Data courtesy JPMA, PMAI, KPMI, TPMA, CPMA)
Table 2 Estimated number of PM parts, metal powder and PM equipment producers in Asia in 2023 (Data courtesy JPMA, PMAI, KPMI, TPMA, CPMA)
Number of Manufacturers in2023

India Vehicles Production Trends
2017-182018-192019-202020-212021-222022-232023-24
Production in Japan of ferrous PM parts has been declining in recent years and in 2023 output was down a further 2.8% to 70,311 tonnes. China remains by far the region’s largest PM part producer and saw ferrous PM production increased by 6.7% in 2023 to reach a new high of 174,961 tonnes, and copper-based PM production increased by 16.6% to 14,665 tonnes. Korea has also seen a good recovery with an 8% increase in ferrous PM part production to 70,012 tonnes in 2023, and India is benefitting from increased vehicle production with ferrous PM part shipments up 8.9% to 49,000 tonnes in 2023.
Growth opportunities for PM in Asia
India 2W/3W Production
Chu believes that the growth potential for PM in Asia is closely tied to overall economic growth. Based on OECD data, he stated that year-onyear GDP growth projections for India for 2024 are 6.1% and 6.5% for 2025. For Indonesia, both 2024 and 2025 are projected at 5.2%, with China projected at 4.7% in 2024 and 4.2% in 2023.
Fig. 4 shows ferrous PM parts production from 2017-2023, based on powder consumption, and Fig. 5 shows copper-based parts production. Driven by vehicle electrification, an increased demand for copper-base PM parts is expected to continue. Table 2 shows the estimated number of PM part producers, metal powder producers, and PM equipment producers in Asia in 2023. PM product producers include Metal Injection Moulding (MIM) operations, helping to explain the very high number of producers in China. As the table highlights, PM’s success spans many countries.
The reasons for GDP growth vary by country, but Chu highlighted that in India, the drivers were significant foreign investment, a ready supply of manpower, and increasing income levels leading to increased consumption. Indonesia’s growth, on the other hand, is expected to be driven by the EV supply chain thanks to its nickel reserves. China’s growth is being driven by renewable energy technologies, such as solar
Source:SIAM
and EVs. Taiwan, on the other hand, is seeing growth on the back of the semiconductor industry and the rise of Artificial Intelligence. Korea is also anticipating growth driven by the semiconductor sector, as well as construction.
A focus on India
Chu stated that India would be a major driver of growth for PM in Asia over the next decade. The country, he stated, has a population of 1.4 billion people, with two-thirds below the age of thirty-four and a median age of twenty-eight. The population’s GDP per capita is expected to grow from $2,278 in 2022 to an estimated $5,242 in 2032. This is driving a massive increase in spending power, which, in turn, is seeing billions of dollars in foreign investment. India’s vehicle mix, shown in Fig. 6, illustrates well
“China remains by far the region’s largest PM part producer and saw ferrous PM production increased by 6.7% in 2023 to reach a new high of 174,961 tonnes, and copper-based
tonnes.”
Fig. 6 Vehicle production trends in India (Courtesy SIAM)
India 2W/3W Production
PM Market for Auto Components in India
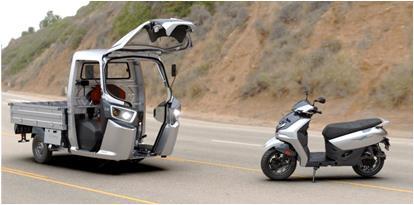
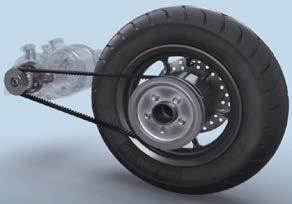
Fig. 7 Electric two- and three-wheeler vehicles offer significant growth potential for PM in India (Courtesy APMA/JPMA)
PM Market for Auto Components in India
(E)
Source: PMAI, CRISIL Research, CRISIL Ratings
China Vehicles Market
Fig. 8 The growing market for PM automotive components in India (Data courtesy PMAI, CRISIL Research, CRISIL Ratings)
China Vehicles Market
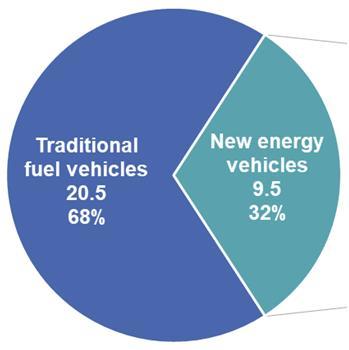
where the growth opportunities for PM are. Compared with 4.9 million conventional vehicles produced in India in 2023, there were more than 21 million twoand three- wheelers produced. There is still expected to be further growth in two- and threewheeled vehicle production which is estimated to reach 100 million units by 2030.
Whilst there will still be growth in car sales, two-wheel and three-wheeled vehicles present the biggest opportunities. Chu believes that this is a significant opportunity for PM, as many parts are needed –both conventional PM parts and Soft Magnetic Composite (SMC) parts – as shown in Fig. 7. He noted, however, that two- and three-wheeled vehicles are lowcost items. “The price issue is very important. You must have a cheaper powder to make these big parts. It’s very important.” Fig. 8 illustrates the growth of the PM parts market in India since 2010.
China’s rapidly growing automotive industry
China Vehicles Market

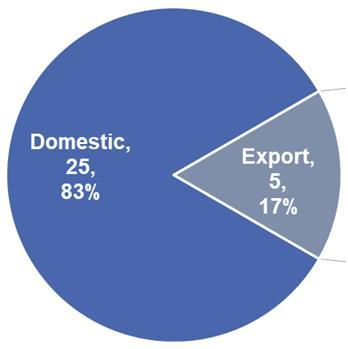
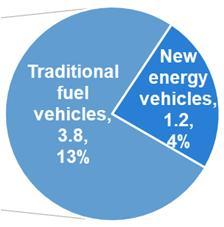
Fig. 9 Breakdown of the Chinese vehicles market (in million vehicles). The country produced 30 million vehicles in 2023 (Courtesy China Association of Automobile Manufacturers)
Chu commented that everyone will have seen the news about the rapid growth of China’s automotive industry. In 2023, China produced approximately 30 million cars, with 83% of production for the domestic market, and the balance for export. As seen in Fig. 9, ‘new energy vehicles’, namely Battery Electric Vehicles (BEV) and Hybrid Electric Vehicles (HEV), account for a significant and rising percentage of production.
Fig. 10 The growth of the market for PM automotive components in China, 2012-2023 (Courtesy CPMA)
Source: CPMA
The growth of China’s automotive industry has, stated Chu, led to a growing trade war, with the European Union (EU) recently adding up to 45% import tariffs on some Chinese vehicles. Despite the rapid rise of BEVs in China, the market for PM automotive components is still growing (Fig. 10).
Source:China Association of Automobile Manufacturers

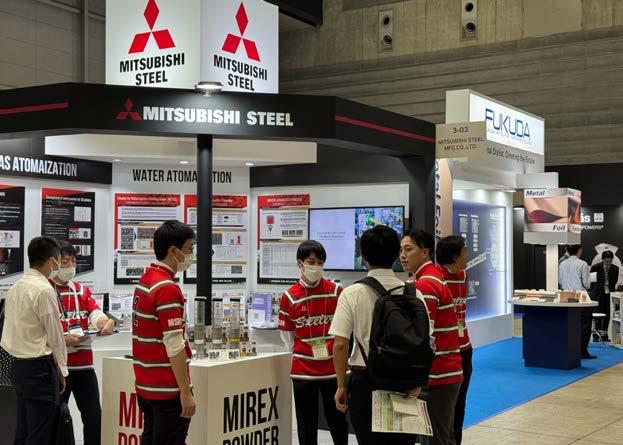
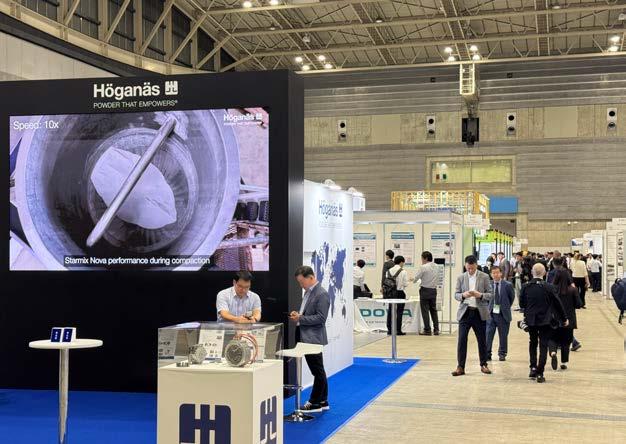
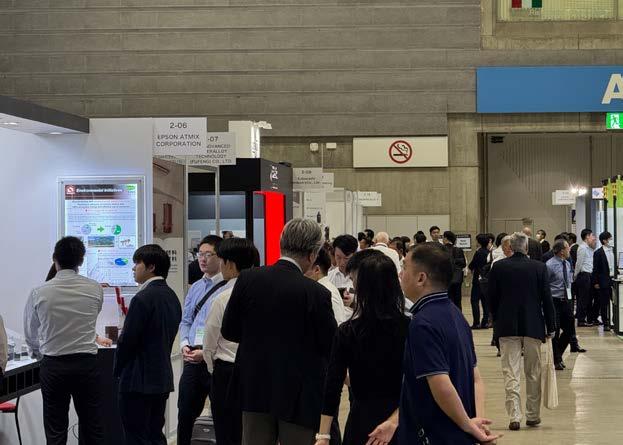
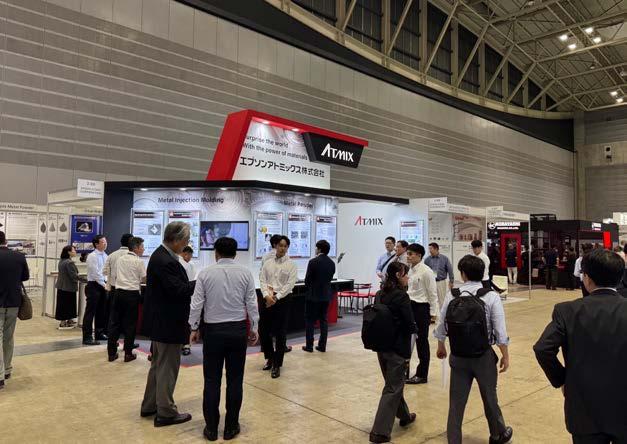
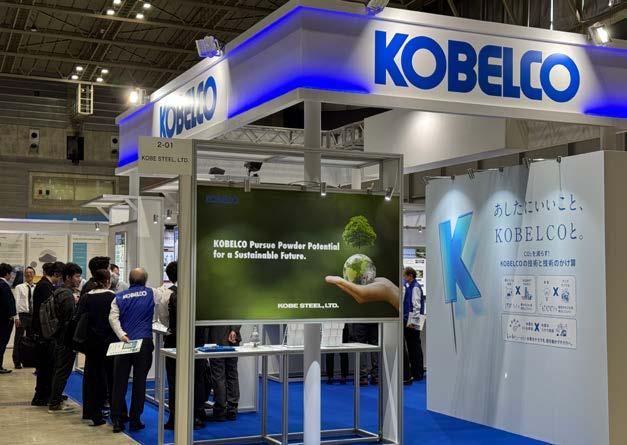
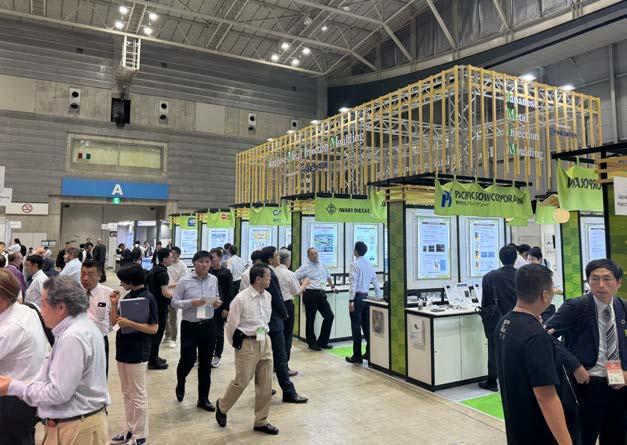


Images from the World PM2024 exhibition
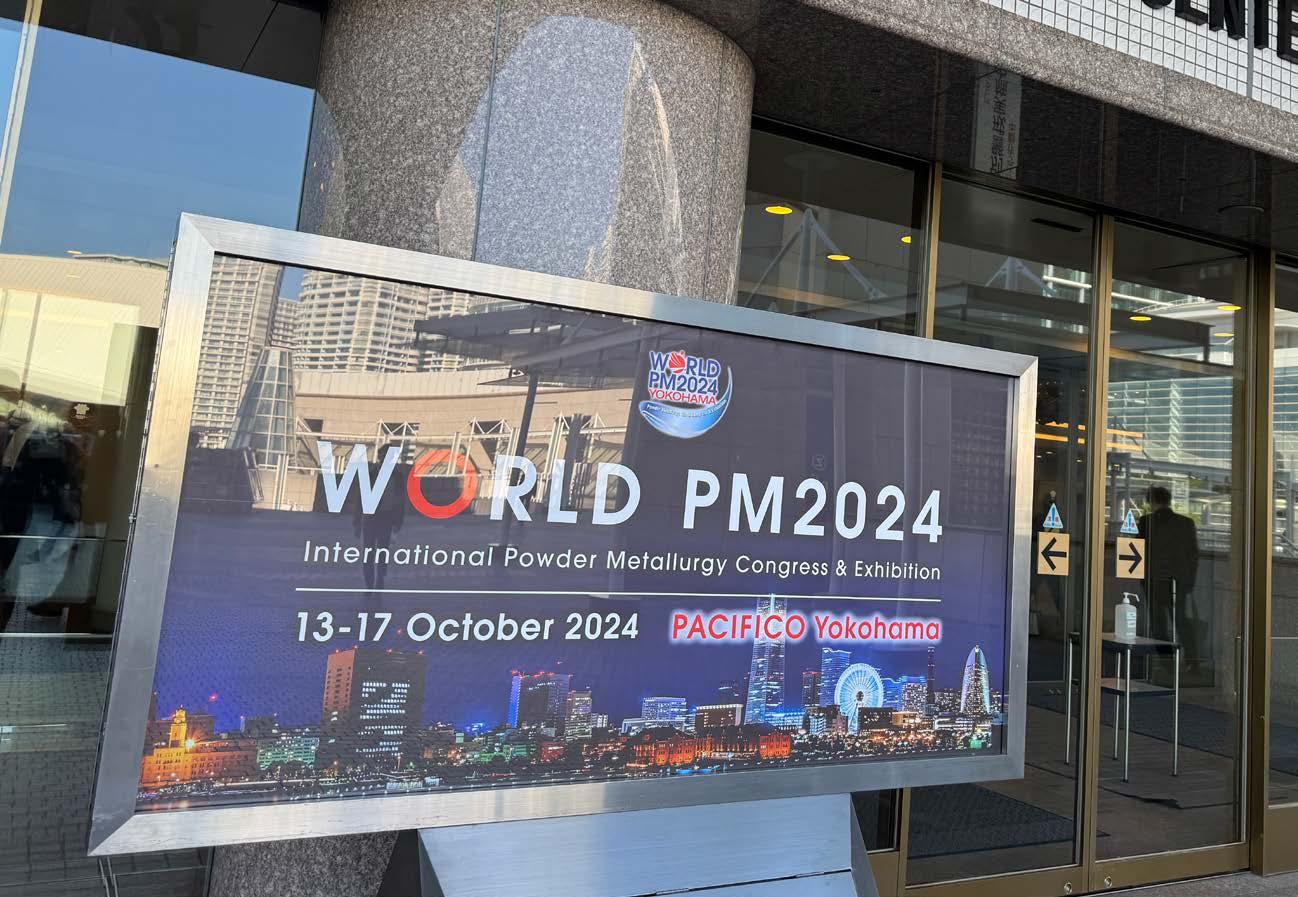
Global challenges
Chu stated that global challenges have “introduced unprecedented challenges and variables” that have impacted the growth of PM in Asia. These include the COVID-19 pandemic, the escalation of the
Russo-Ukrainian war, the Israel-Gaza war and the Red Sea Crisis, as well as other geopolitical issues.
An example given was the impact on shipping. Chu stated that the shipping of goods between Asia and Europe would, in the past, have taken six or seven weeks. “Now, we
“When it comes to the growth of BEVs and their impact on PM, Chu
urged the industry not to panic. He cited projections that suggest that by 2030 EVs will only account for 30% of the global market, rising to 46% by 2035. ‘Our conventional PM industry will still have VVT transmissions and hybrid vehicles, so there will still be a need for a lot of PM parts.’”
need three months,” he stated. “So it’s a very big challenge for all those trading. The increases in cost of shipping, as well as many other costs, drives inflation up.”
When it comes to the growth of BEVs and their impact on PM, Chu urged the industry not to panic. He cited projections that suggest that by 2030 EVs will only account for 30% of the global market, rising to 46% by 2035. “Our conventional PM industry will still have VVT transmissions and hybrid vehicles, so there will still be a need for a lot of Powder Metallurgy parts.”
Opportunities and outlook
Away from the automotive industry, Chu stated that significant opportunities remain for PM in Solid Oxide Fuel Cells (SOFCs), where PM is able to produce the
Fig. 11 Entrance to the World PM2024 International PM World Congress and Exhibition
interconnecting plates used in fuel cell stacks. He cited the inherent unpredictability of wind and solar power as a driver of SOFC power generation, along with the fact that a 1 MW SOFC power plant requires 125x less space than an equivalent solar PV facility.
Even with the rise of BEVs, he stated that there are still opportunities for PM in these vehicles. He explained that from suspension and steering components to wipers, door locks and seat adjustment mechanisms, these cars still need a lot of PM. New opportunities for PM also exist in thermal management systems and traction motors, where, in the latter, ironpowder-based SMCs promise to play a major role. “So this is a chance for our Powder Metallurgy industry,” Chu explained. “The EV is an opportunity, but it is also a big challenge.”
WorldPM2026 World Congress & Exhibition
Metal Powder Industries Federation (MPIF) has announced that the next WorldPM2026 World Congress & Exhibition will be held June 25-29, 2026, at the Palais des congress de Montreal (Montreal Convention Center) in Montreal, Canada.
The event will be co-located with the AMPM2026 – Additive Manufacturing with Powder Metallurgy and Tungsten2026 – Tungsten, Refractory, and Hardmaterials conferences.
www.mpif.org



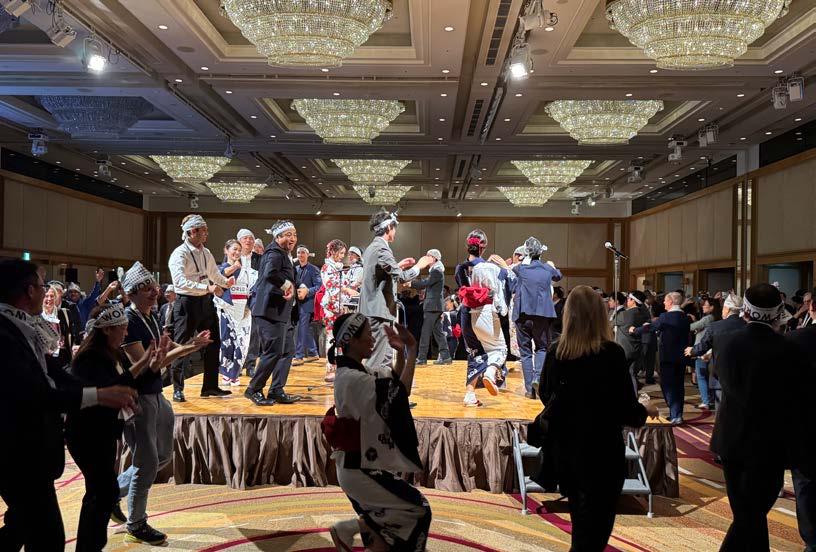

Above: Yoshio Uetsuki, Executive Director of the Japan Powder Metallurgy Association, and Secretary General of World PM2024, addressing guests at the World PM Congress Party. James Adams, Executive Director, MPIF, then invited participants to WorldPM2026, Montreal, Canada
Advertisers’ index & buyer’s guide
its advert, or on the company’s
to go directly to its website.
Dorst Technologies 11 www.dorst.de
Huacheng Moulding (Changshu) Co. Ltd 34 www.szhcjm.com
Komage Gellner Maschinenfabrik KG 35 www.komage.de
Osterwalder AG 27 www.osterwalder.com
System 3R International AG 23 www.system3r.com
PM2025
www.europm2025.com
64 www.formnext.com
HIP International Conference 2025 43 www.hip2025.com
MIM 2025 63 www.mim2025.org
PM China 2025 74 en.pmexchina.com
PowderMet2025 / AMPM2025 48 www.powdermet2024.org / www.ampm2024.org
Advertise with us...
Combining digital and print publishing for maximum exposure
Reach out to our rapidly expanding international audience that includes component manufacturers, end-users, industry suppliers, analysts, researchers and more. For more information contact:
Jon Craxford, Advertising Sales Director Tel: +44 207 1939 749 jon@inovar-communications.com

Industry events
PM Review is dedicated to driving awareness and development of Powder Metallurgy and its related technologies. Key to this aim is our support of a range of international conferences and events. View our complete events listing on www.pm-review.com
2025
International Conference on Injection Molding of Metals, Ceramics, and Carbides (MIM 2025)
February 24–26 – Costa Mesa, CA, USA www.mim2025.org
Advanced Manufacturing for Aerospace & Materiel
February 26–27 – Bristol, United Kingdom www.defenceiq.com/events-advancedmanufacturing
PM China 2025
March 10–12 – Shanghai, China en.pmexchina.com
HIP International Conference on Hot Isostatic Pressing
April 6–10 – Aachen, Germany www.hip2025.com
RAPID + TCT 2025
April 8–10 – Detroit, MI, USA www.rapid3devent.com
International Critical Minerals Expo & CMI Summit IV
May 14–15 – Pasadena, CA, USA www.mineral-expo.com
The Magnetics Show North America
May 14–15 – Pasadena, CA, USA www.magnetics-show.com/home1
Looking for an event partner?
EPMA – Use of Powder Metallurgy Technologies in Aerospace
May 20–21 – Sandviken, Sweden seminars.epma.com/event/aerospace-seminar/
21 st Plansee Seminar
June 1–6 – Reutte, Austria www.plansee-seminar.com
PowderMet2025 / AMPM2025
June 15–18 – Phoenix, AZ, USA www.powdermet2025.org | www.ampm2025.org
Dritev 2025
July 9–10 – Baden-Baden, Germany www.vdiconference.com/dritev/
Euro PM2025 Congress & Exhibition
September 14–17 – Glasgow, Scotland www.europm2025.com
The European Additive Manufacturing Congress 2025
September 14–17 – Glasgow, Scotland www.europm2025.com/the-european-additivemanufacturing-congress/
Formnext 2025
November 18–21 – Frankfurt, Germany www.formnext.com
PM Review collaborates with a variety of Powder Metallurgy and associated events throughout the year, ranging from major trade shows to smaller technical conferences and seminars. If you would like to partner with us for your event, contact Merryl Le Roux: merryl@inovar-communications.com

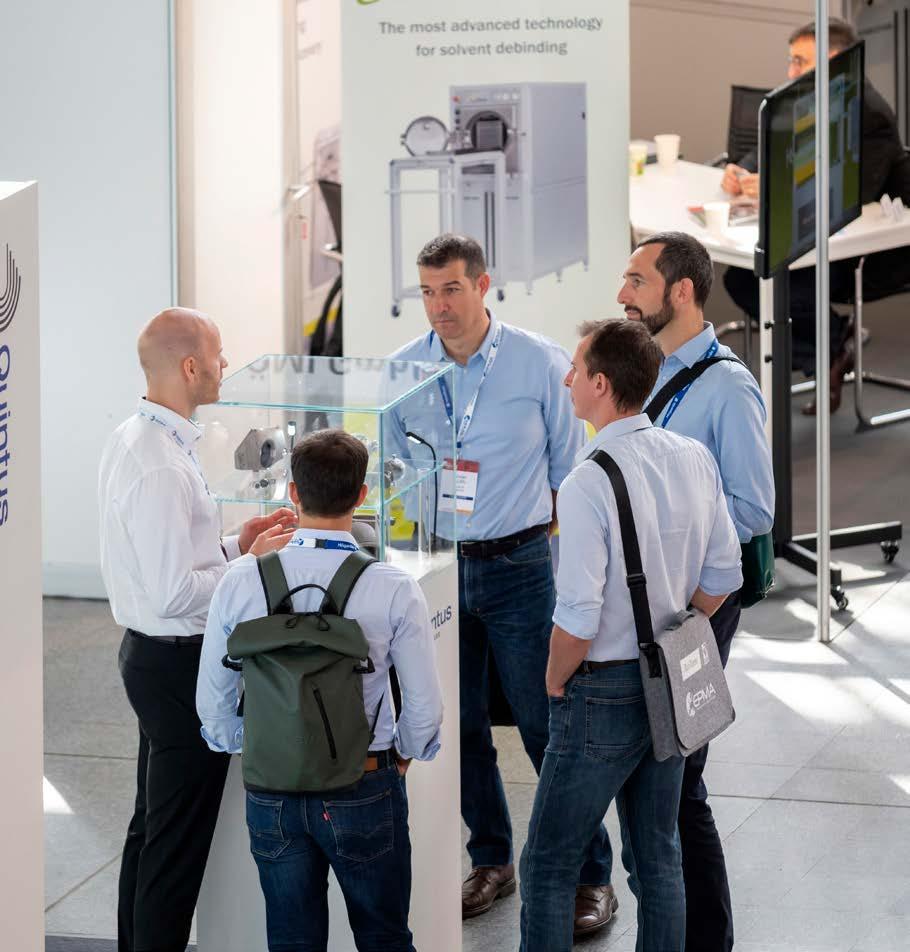


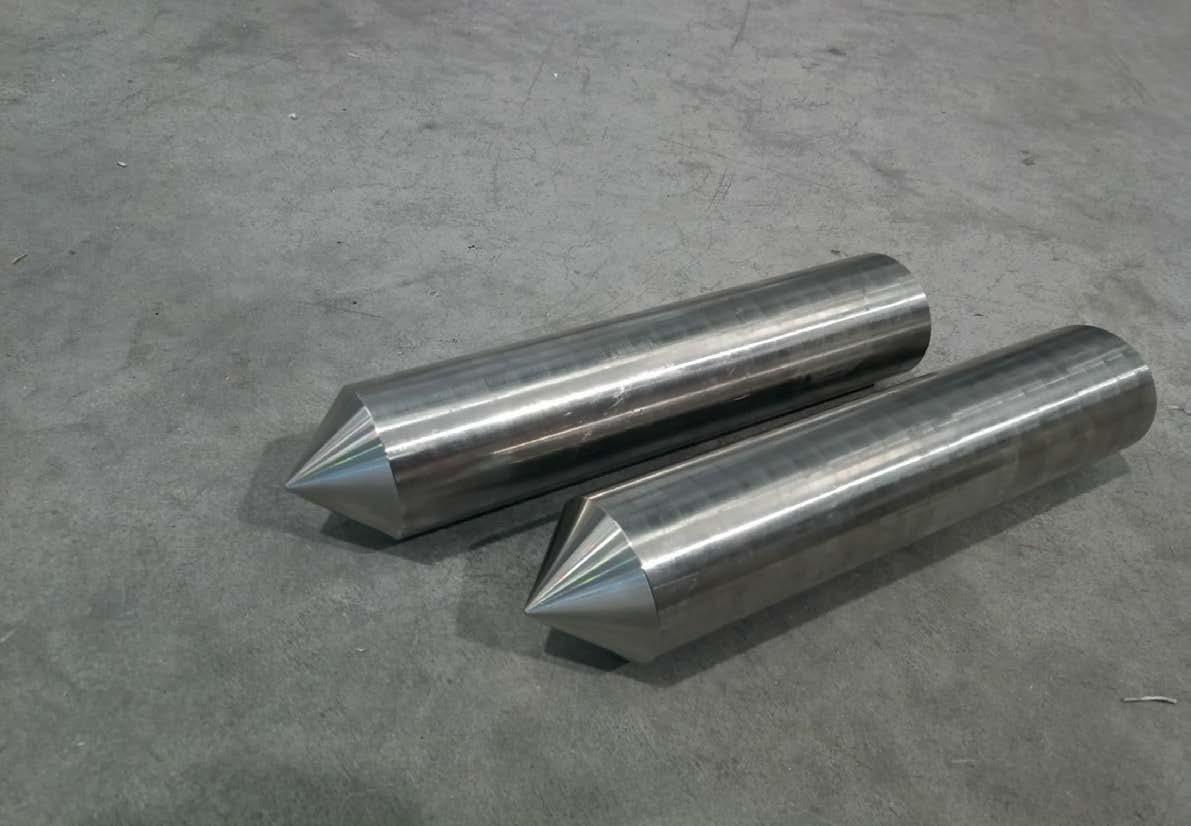
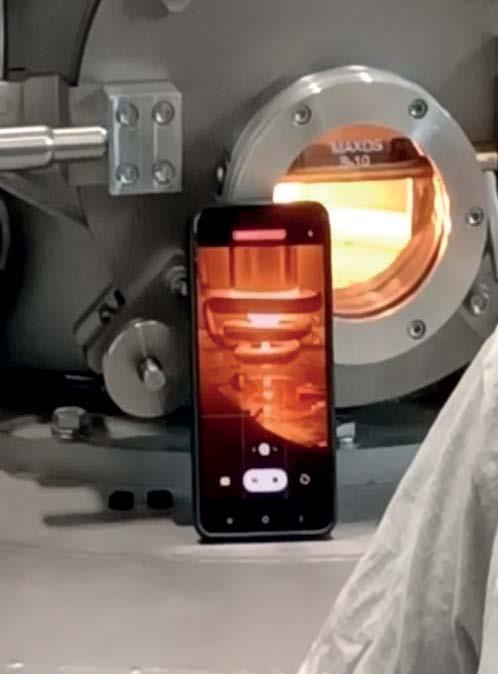
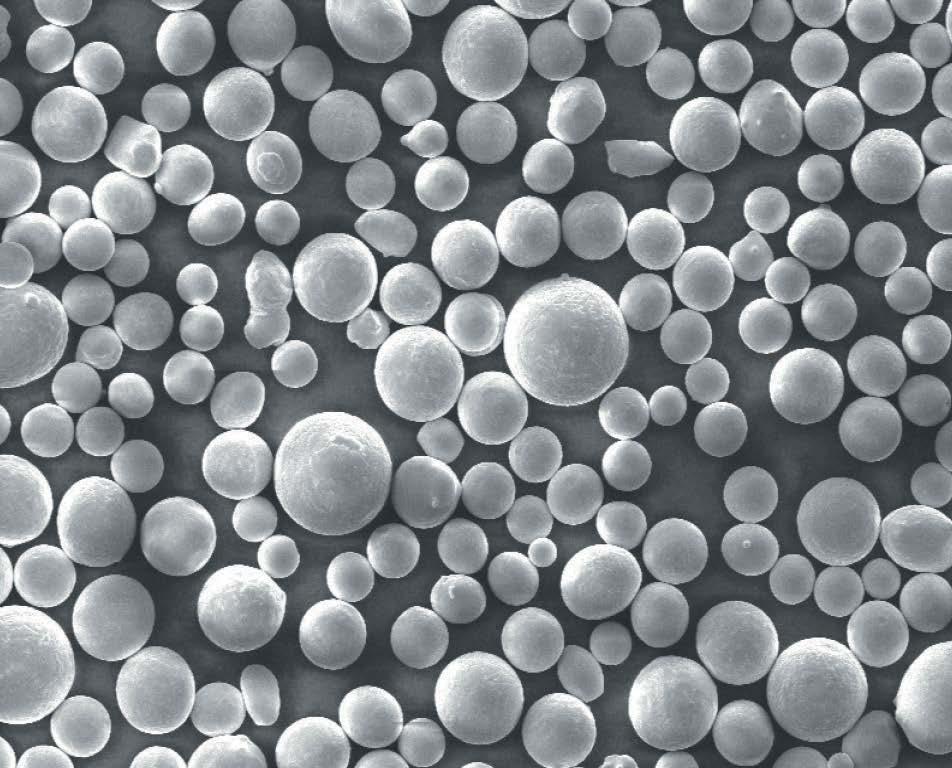
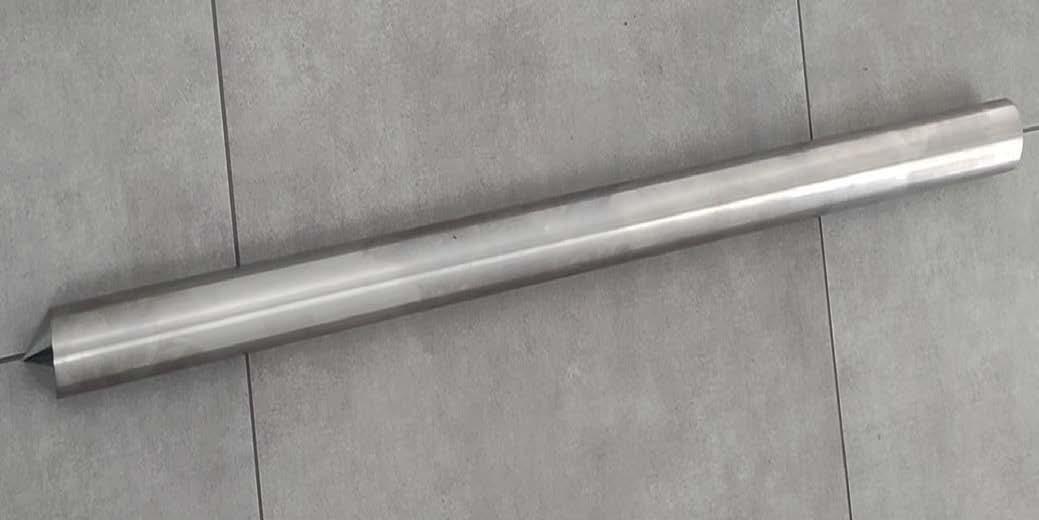
