
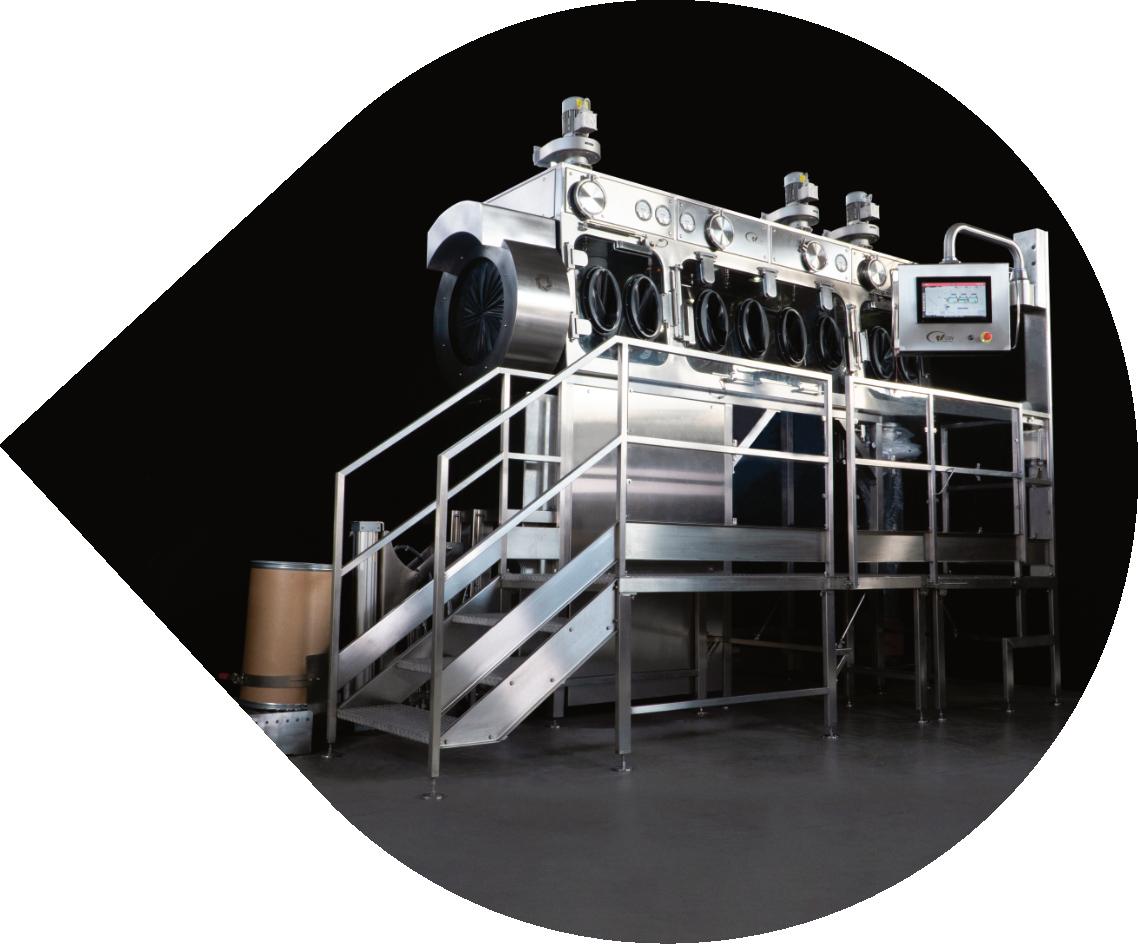
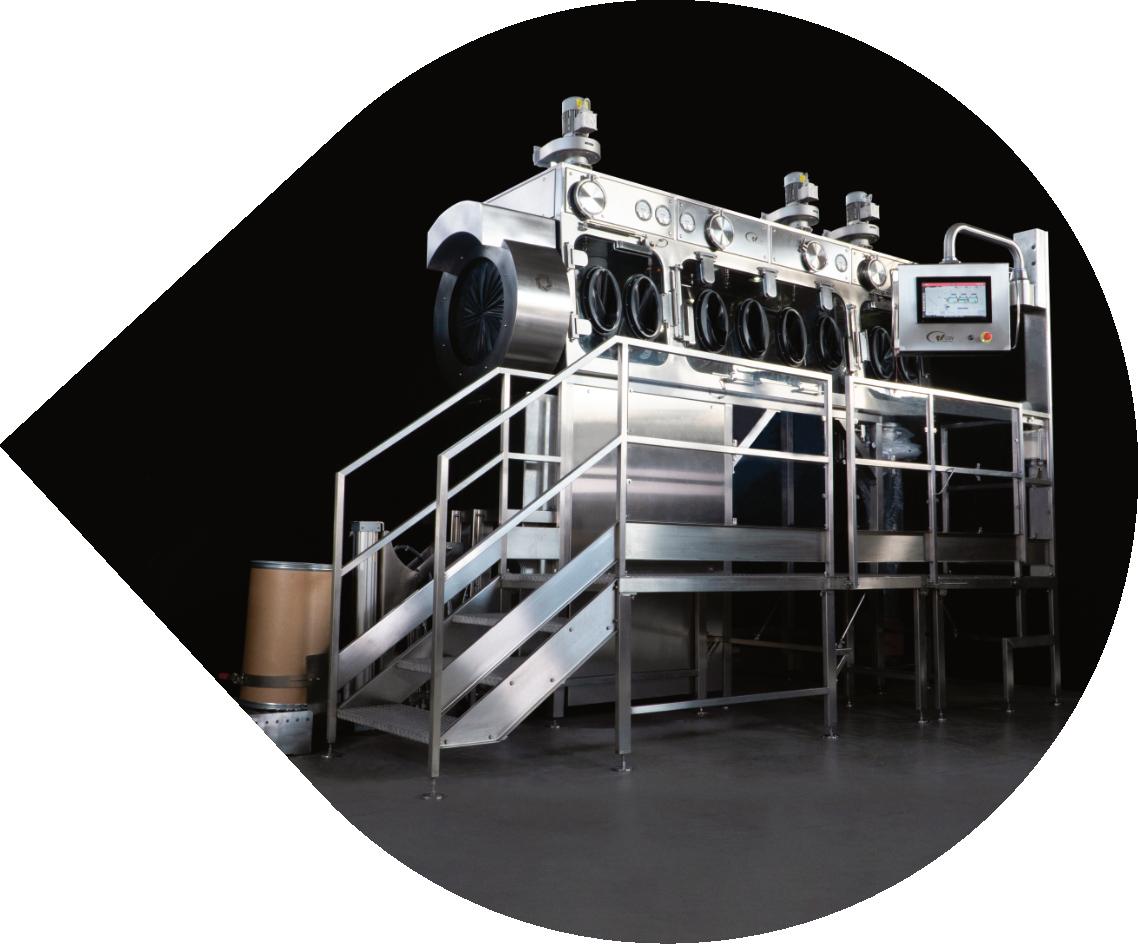





Stainless steel or titanium reversible self-priming motor-driven pumps


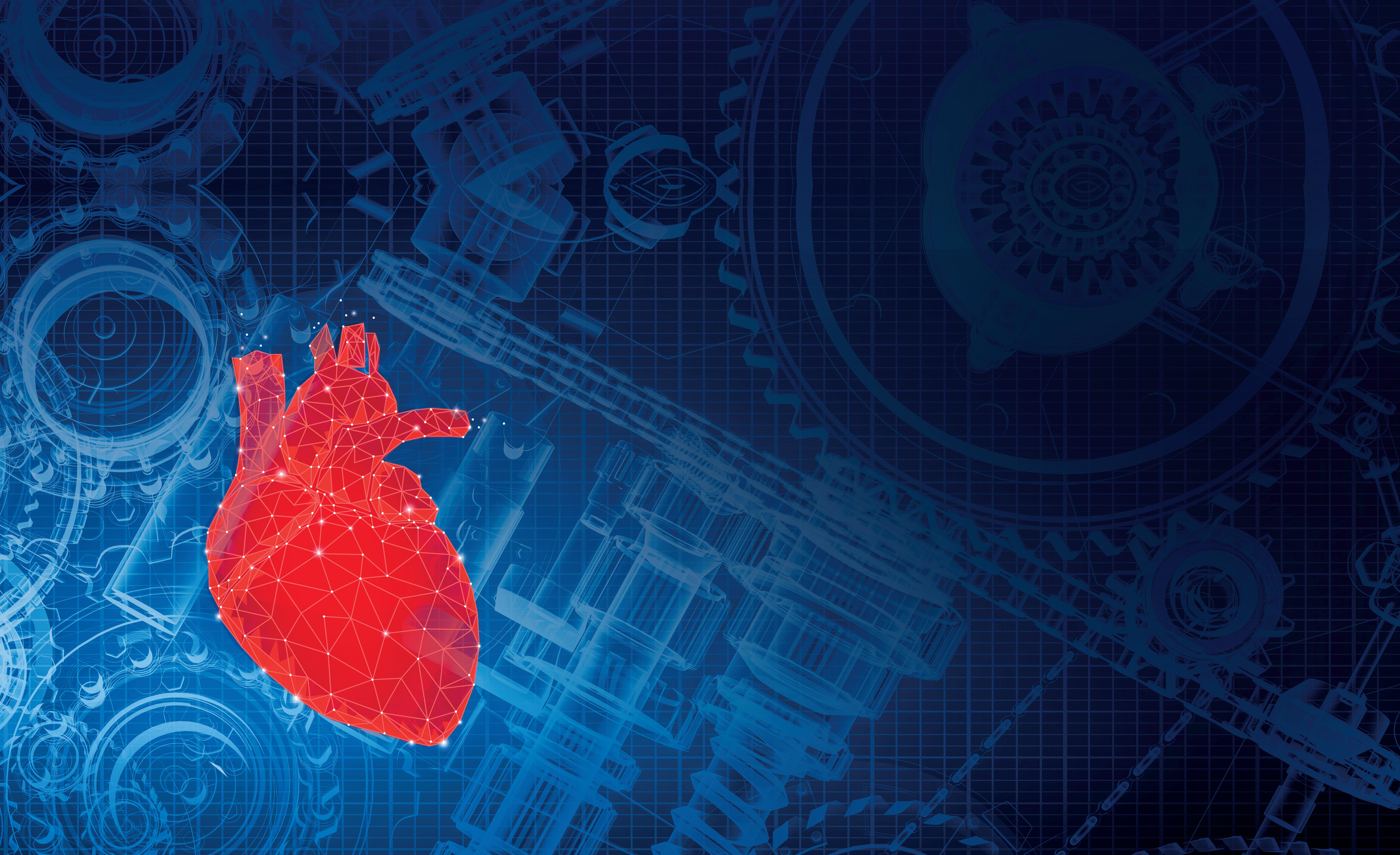
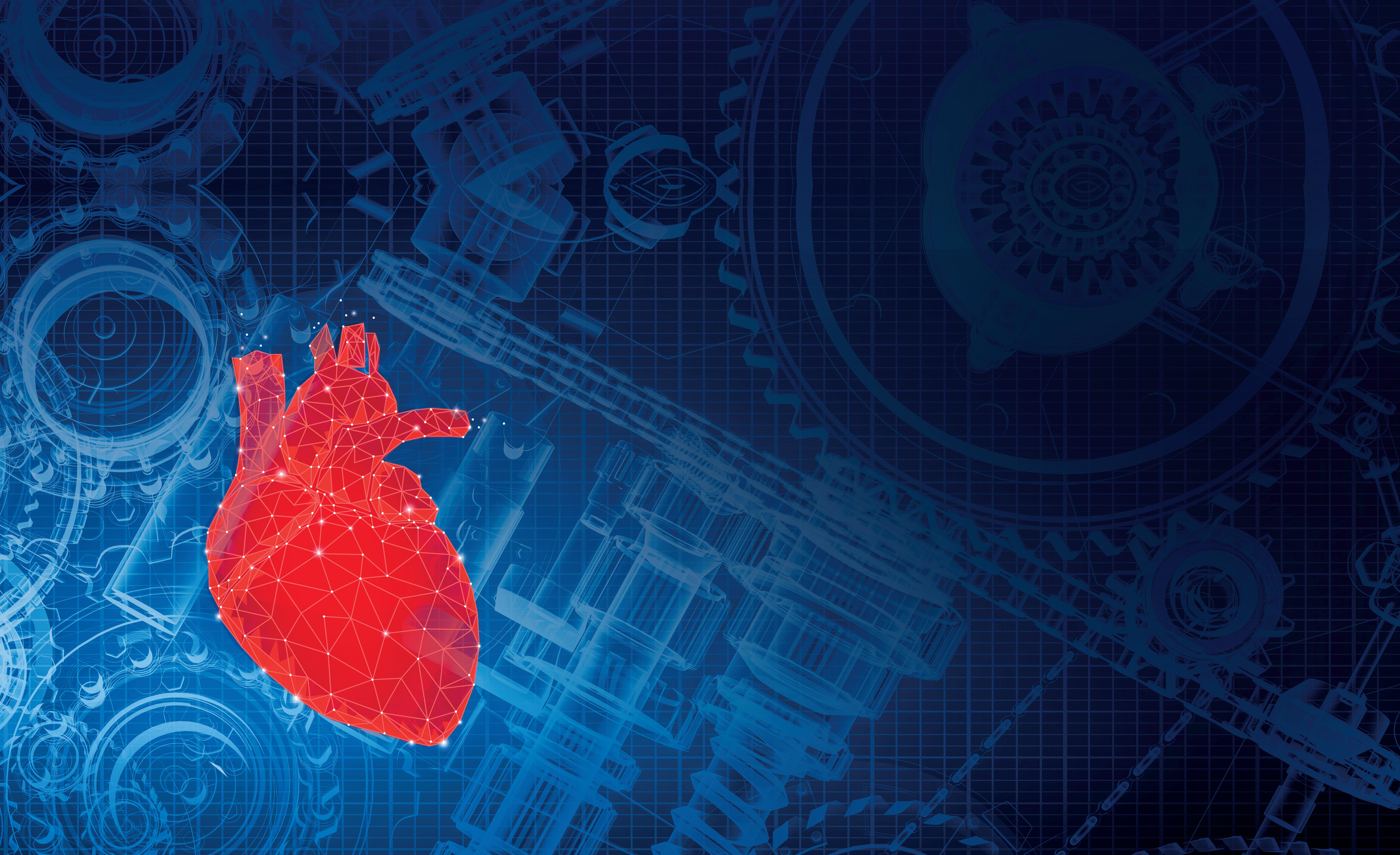
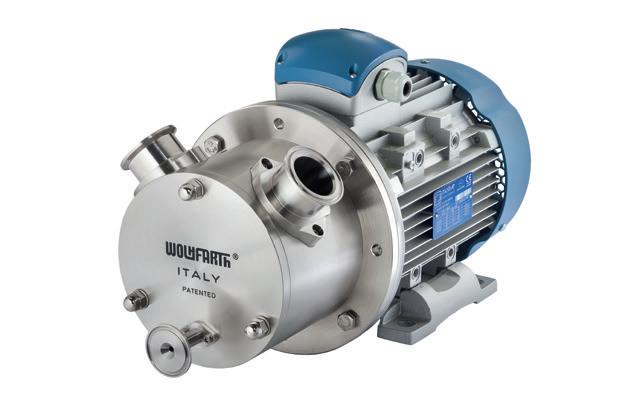
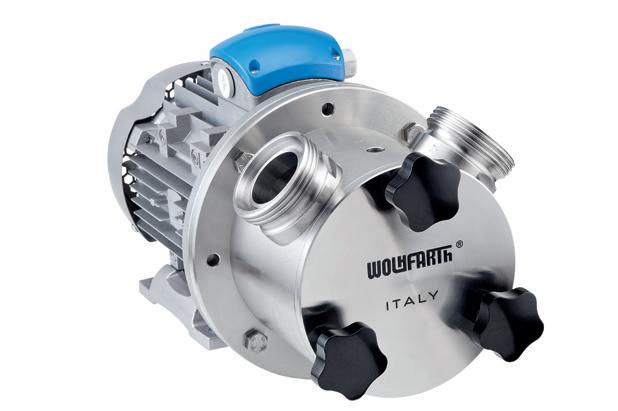
Stainless steel or titanium reversible self-priming motor-driven pumps
Code 3350-3360C
Product in brown ptfe coated glass fabric or in black PTFE coated glass fabric with central PTFE/FEP band
Valve cover and flange cover can be in antistatic brown or black PTFE coated glass fabric with a band transparent central PTFE / FEP for inspection of the coupling point. Equipped with side cords for closing the product on the system connection pipes.
Code 5211
Jointex® Red
High quality jointing sheet made with pigmented, quartz fillers. It is an innovative replacement material for asbestos seals and conventional products in PTFE.
Code 5213 Jointex® White
High quality sheet jointing made of modified PTFE filled by 25% with glass fibres. The material offers valid mechanical properties which enable a high sealing capacity to be achieved and maintained over time.
Cod. 5700
PTFE envelope gaskets
Envelope gaskets consist of an enclosure, commonly called an envelope, which can be made from the more common virgin PTFE and filled PTFE. The thickness of the envelope is usually 0.5 mm. The insert inside the gasket can be made of aramid fibre, graphite, ceramic fibre fabric, elastomers, modified PTFE, corrugated AISI rings and, on request, grounding fins. Such gaskets can be produced in various forms.
Cod. 5200
Texlon® sheets
Texlon® sheets are high quality gasket sheets made from 100% pure, multidirectional PTFE without fillers, coloured pigments or inks. During the production process of Texlon® sheets, the PTFE is elongated in different directions, which confers superior strength in both length and width. Gaskets made from Texlon® foil adapt perfectly to uneven surfaces, facilitating their installation.
Editorial Achema: where Europe shapes industry
6
Cover story Secondary barrier glove box with continuous liner
8 News
14 Exhibitions Six innovation stages to delve the process industry
20 Safety Contamination control: navigating new regulations and sustainability
22 Trend report Emerging trends in the pharmaceutical industry
28 Biotechnologies 30 Validation Ten years’ reliability working for pharma industries
34 Machines Steriline upgrades its zero-loss philosophy
inspection
for blow-fill-seal
tools adapted to the needs of pharma and biotech
High valuable expertise in filtration and purification
The piece of mind of continuous monitoring
More sustainable and data driven technology
Packaging
Which trends are important for pharmaceutical producers and machine manufactures post-Covid
Thirty years of continuous
The pharmaceutical industry moves on with robotics
“In the coming months, our ambition is to see Europe putting industry competitiveness at the heart of Europe’s decision making. The industry leaders want to see Europe become the global hub for innovation, and also a place where technologies can be scaled up effectively, on-time with less bureaucracy, a single market with an industrial policy attracting investments to invest on European soil”.
Ilham Kadri, new President of Cefic, page 8
After the 2022 “interim” edition, in a Europe still weakened by the long trail of Covid, with industrial supply chains loosened and grappling with a disjointed recovery, Achema 2024 comes as an event featuring great expectations, in a scenario which is difficult to find correspondences in the past. The international political and economic framework has completely changed compared to pre-Covid. On the one hand, wars have brought bombs and death to the gates of Europe, while Russia is increasingly threatening, so much so that we can no longer exclude the unthinkable, i.e. a direct clash with NATO. On the other hand, after the post-pandemic shocks of inflation, the energy and raw materials crisis, the market has regained its strength and has started its run again, also boosted by the ecological and digital transition and the growing role of artificial intelligence. Achema 2024 will open its turnstiles the day after the European elections which, among the most important-ones in
recent decades, will give a decisive orientation to the path to EU integration, which is also preparing to include new members. In the midst of so many challenges and uncertainties, the Frankfurt exhibition will have the merit of reminding us that the process industry is still one of the strengths of the old continent, still capable, at least on the technology and innovation front, of playing a central role. Achema actually attracts investors and players from every continent, because it is there that the industry, chemical-pharmaceutical in particular, which we will see in the coming years, takes shape. And the most international edition ever is expected from 10 to 14 June, with visitors from over 130 countries. If community policy stutters in the face of extremely complex and dangerous scenarios and interlocutors, the European process industry nevertheless continues to want to show its international partners the path to follow: and it is the one we are taking at Frankfurt.
The Secondary barrier, which further protects the drum discharge via liner, ensures safety for both the operator and the product.
CSV Containment designed this small-sized skid to allow discharging from a mill into drums via continuous liner.
by CSV Containment newsASecondary barrier around the operating environment introduces a further safety breakthrough within the established practice of liner discharge systems.
In CSV Containment, we designed this small-sized skid to allow discharging from a mill into drums via continuous liner, thus ensuring a second level of OEB5-classified containment.
Operators, thanks to the gloves on the large glass door, can discharge and bring samples outside through a side-mounted RTP port.
Secondary barrier around the point of interest
At the heart of a glove box, there is always a point of interest: safety. We have designed this glove box to offer both comfort and protection. We have planned everything to work most effectively around the discharge point.
A roller conveyor facilitates drum insertion and extraction operations. Moreover, there are dedicated spaces to accommodate closing tools and bag clamps.
In addition, the comfortable RTP door allows the material to exit safely from the beta container.
Finally, the inflatable seal ring mount-
ed on the canister in the glove box serves both to secure the liner, allowing its control with gradual unwinding, and to function as an anti-dust collar, thanks to the internal inflatable gasket. The skid is provided with a cleaning spray ball and provisions for water drainage.
Furthermore, the glove box is equipped to assure inerting cycles designed to further implement the quality and safety of operations.
Main features
The Secondary barrier skid main characteristic are the following:
• AISI316 stainless steel chamber equipped with an openable front glass panel.
• ATEX rated.
• Front glass panel with a pair of EPDM conductive black gloves.
CSV Containment is part of CSV Life Science Group. CSV operates in the fields of pharmaceutical validation, engineering and construction. Over the years, CSV Life Science, has built upon the leading expertise of the engineering professionals who founded and drive the company to provide leading-edge design, construction, validation, compliance and computer system validation services that are closely tailored to the needs of the customers, both large and small companies. The know-how of CSV in the pharmaceutical and chemical industries brings clients total peace of mind, knowing that they can rely on a complete solution that addresses every related issue for their company, with a synergistic integration of validation and engineering experience and expertise. Similarly, it has made CSV recognized for providing the benefits of validation services that are
• Roller conveyor inside the chamber for drum handling, transfer in and out.
• DN190 Rapid Transfer Port (RTP), for containing sampling activities, positioned on the glove box left side.
• Continuous liner kit internally positioned and connected to the discharging point passing through the top ceiling of the glove box.
• A nitrogen system provided with a purging and venting circuit and an automatic valve to manage the inertization cycle.
mainly orientated to resolving rather than simply identifying any detected non-conformity. At the same time, thanks to its know-how, CSV has become an ideal partner for companies seeking the highest standards of professionalism together with outstanding operating flexibility, which is a combination that can make all the difference.
CSV Life Science has the experience and specialist resources to offer integrated solutions covering the entire Life Cycle of a Product or Process: from a simple feasibility study to conceptual design, often based on a production capacity study of a department or an entire production site (Site Master Plan); from basic and detailed engineering, commissioning, qualification, validation to construction and realization, up to the resolution of problems relating to the product release of the in accordance with all current standards and regulations.
• Two H14 HEPA (glove box) filters installed within the chamber, on the inlet and outlet circuits.
• Variable speed fan, positioned far from the glove box on the building top ceiling to ensure the required suction for negative pressure control.
• Differential pressure transmitter (DPT) on the top connected to the variable speed fan via control system.
• Oxygen analyzer/transmitter to monitor the inertization condition inside the chamber.
• Cleaning spray gun inside the chamber mounted through a pass-through connector equipped with hose.
12” grooved canister.
• Anti-dust inflatable seal on a swinging seat.
Pressure regulator.
• Manual switch to manage the gasket status (on/off).
• CSV continuous liner pack. l
Exhibits at Achema: Hall 4.1, Booth F17
Ilham Kadri, CEO of Syensqo, becomes Cefic President, succeeding Martin Brudermueller. Ilham Kadri is one of Europe’s most prominent and well-known business leaders. She holds a degree in chemical engineering from L’École des Hauts Polymères in Strasbourg, and a PhD in macromolecular physico-chemistry from Strasbourg’s Louis Pasteur University. Dr. Kadri served as Cefic’s Vice President before becoming the President and holds several key positions in business associations around the world.
Ilham Kadri is a world citizen with Moroccan-French roots and professional experience across four continents. During her 30-year career, she has
held various positions at leading companies. Her responsibilities have included research & development, strategy, business and digital in industries spanning automotive, aerospace, oil & gas, mining, water desalination, construction, consumer goods, food service, hospitality and healthcare. Ilham Kadri actively speaks out for the role of science, innovation, sustainability, inclusion and diversity, mentoring and promoting female leadership in science, technology, engineering and mathematics.
“I am honoured to take on this role, in what is a pivotal moment for Europe and Europeans, industry at large and the European chemical industry itself. I therefore very much look forward to supporting the next generation of European Politicians and the new European Commission Leadership. If I can relate one message already right now –Go vote in June! It is crucial”.
Ilham Kadri, along with outgoing President Martin Brudermueller, played a key role in the European Industrial Summit, hosting key government of-
Faravelli Pharma Division presents Pearlitol® 200 GT, a reference in the Pearlitol® line by Roquette Pharma.
Pearlitol 200 GT is a direct compression excipient specially designed to optimise the properties of tablets. This granulated mannitol offers outstanding physical and chemical stability, ensuring high compatibility with active ingredients and a reduced tendency to hygroscopicity. Moreover, due to its non-cariogenic and non-acidogenic characteristics, it is suitable for a wide range of people, including paediatric and diabetic patients.
Pearlitol® 200 GT is ideal for the formulation of tablets (including logenzes, swallowable tablets, orodispersible tablets, chewable tablets and effervescent tablets), as well as for powder mixtures
ficials such as European Commission President Ursula von der Leyen, Belgian Prime Minister Alexander de Croo and former Italian Prime Minister Enrico Letta.
The coming months, Brussels will see a series of Antwerp Dialogues, further exploring the key requests in the Antwerp Declaration.
“Our industry has long committed to Europe’s climate neutrality and circularity goals, there has been no question about what we are trying to achieve. With the Antwerp Declaration, which is supported by more than 1100 organisations, spanning 25 sectors, we have laid out how we need to achieve it. In the coming months, our ambition is to see Europe putting industry competitiveness at the heart of Europe’s decision making. The industry leaders want to see Europe become the global hub for innovation, and also a place where technologies can be scaled up effectively, on-time with less bureaucracy, a single market with an industrial policy attracting investments to invest on European soil, and where there is a solid market demand, including the public one, for sustainable products.”
(such as sachets, oral stick packs and gelatin hard capsule fillings). Pearlitol® 200 GT is distributed in Italy by Faravelli Pharma Division.
Bormioli Pharma, an international leader in pharmaceutical packaging and medical devices, announced the third edition of its Sustainability Report. This edition outlines and consolidates the strong progress Bormioli Pharma has made in promoting sustainable growth in the communities where the Company live and work and highlights its strong commitment to supporting the pharmaceutical industry in its transition towards environmentally friendly solutions.
Of the main actions took by the Company during the year, the decision of proceeding with the external assurance of the Report two years ahead of legal obligations has been one of the most pioneering among the industry. In 2023, ESG team and Governance have been also reinforced, leading to the definition of robust processes contained in its ESG Policy. Moreover, the Group is already taking steps to prepare for the adoption of the new reporting system required by the EU Directive “Corporate Sustainability Reporting Directive” (CSRD). In terms of the key sustainability targets, Bormioli Pharma confirmed to be committed in the 30% Carbon Intensity reduction and in 41% reduction of Water Withdrawal Intensity by 2030 (compared to the 2021 baseline). The goal of increasing the share of sustainable materials in sold products continued to advance and has already achieved stunning results: the Company is very close to the 50% target by 2025, reaching
Syensqo announced the completion of the acquisition of JinYoung Bio, a specialty cosmetic ingredients supplier based in South Korea. This investment marks a significant step in expanding Syensqo’s portfolio toward more natural and high-value specialty skin care solutions with both functional and active ingredients.
“This acquisition reflects our deep commitment to innovation and our focus on sustainable solutions leveraging the power of biotechnology,” said Ilham Kadri, CEO of Syensqo. “We are dedicated to making a meaningful impact in the beauty industry, addressing critical environmental and societal challenges with groundbreaking circular solutions.”
The addition of JinYoung Bio’s technology will extend Syensqo’s product portfolio into biomimetic ceramides for skin care and hair care applications, as well as a range of biobased functional ingredients used in skin care and color cosmetic applications. Ceramides, the flagship product line within JinYoung Bio’s portfolio, are produced through biotechnology via a fermentation process, which aligns with the focus of Syensqo’s Renewable Materials and Biotechnology Growth Platform.
“Our aim is to provide our customers with advanced skin care solutions that harness the natural power of specialty ingredients like ceramides,” added Michael Radossich,
45% in 2023 (+15% compared to 2022). “In 2023 we have worked energetically to be an important driver of responsible growth, remarking our role as a partner of the pharmaceutical industry in developing increasingly widespread, effective and sustainable medical practices”, commented Andrea Lodetti, CEO of Bormioli Pharma. “Among the initiatives implemented during this path, we have further extended one of the widest sustainable packaging offering available in the pharma industry, EcoPositive, a concrete action to support the EU’s goals for sustainable packaging.”
Another pillar of Bormioli Pharma’s ESG commitment is related to the promotion of a Diversity & Inclusion culture across the organization, with the objective of reaching the 95% of employees trained on these topics by 2025.
Finally, the document remarks the objective of completing the assessment of 90% of suppliers on the international EcoVadis platform by 2026.
President of the Consumer and Resources division at Syensqo. “This investment puts Syensqo at the forefront of leveraging the dynamic nature of ceramides, a hero ingredient in cosmetic products including the fast-growing dermocosmetics.”
Syensqo’s beauty care business aims to grow JinYoung Bio’s commercial and technical capabilities through its customer access, formulation and application expertise and marketing capabilities. The company plans to launch its first product from the ceramides line and four functional ingredients in Q2 2024 at Suppliers’ Day in New York, supporting the aim of Syensqo’s Home & Beauty Care business to grow twice as fast as the market.
Fibrosis is characterised by marked and pathogenic build-up of the tissue matrix, leading to tissue degeneration in organs, including the liver and lungs. Fibrotic disease contributes substantially to global mortality and morbidity. Despite the chronic nature of fibrotic conditions, widespread impact on various organs, and substantial disease burden, there is currently no curative treatment for these conditions. The strategic partnership leverages Variant Bio’s cutting-edge genomic discovery capabilities and VB-Inference platform as well as Evotec’s extensive expertise in antifibrotic drug discovery. Evotec will identify best-in-class small molecules targeting a key fibrotic
pathway with strong genetic support identified by Variant Bio and progress the programme towards the selection of a clinical development candidate(s) using Evotec’s integrated end-to-end R&D platform. Additionally, the collaboration includes an opportunity to evaluate unrelated nephrology targets based on human multi-omics data with Evotec’s molecular patient database (“E.MPD”).
Under the terms of the risk-sharing partnership, Evotec will receive undisclosed research funding and may receive pre-clinical and clinical milestones and/or royalties dependent on the success of the programme. This strategic framework allows Variant Bio to offset the early costs of
drug development in exchange for a portion of the future upside.
Dr Matthias Evers, Chief Business Officer of Evotec, said: “We are excited to enter this collaboration with Variant Bio. Variant’s genomics-focused model which identi-
fies novel drug targets perfectly aligns with Evotec’s data-driven approach to redefine diseases at the molecular level and enhance probability of success.”
Andrew Farnum, CEO at Variant Bio, said: “Evotec has established and validated in vitro and in vivo models to accelerate programme timelines and is ideally positioned to advance our fibrosis programme.”
Dr David Moller, CSO at Variant Bio, added: “We are thrilled to collaborate with Evotec given their deep expertise in disease biology and their outstanding drug discovery capabilities that complement Variant Bio’s R&D team”.
The demand for innovative measurement technology for industry is also increasing in Scandinavia. With the new subsidiaries in Denmark and Sweden, which will open in spring 2024, VEGA is actively responding to this development and moving even closer to customers with its modern level and pressure measurement technology.
Scandinavia is not new territory for VEGA. A VEGA subsidiary has been operating in Norway since 2015. In Sweden and Denmark, VEGA was represented by local dealers until now. With the establishment of the two new subsidiaries, VEGA’s presence in the two countries with promising markets will now be consolidated.
Jürgen Schuijren, Managing Director of VEGA Netherlands, is currently at the forefront of the
expansion into the north. “We want to offer these markets the level of service that customers are used to from VEGA,” he says – in other words, short logistics routes, a common language with customers, and employees who are experts with VEGA measuring instruments.
“Our goal is to serve customers in Sweden and Denmark in the same way as in other countries: with know-how, excellent service and, of course, our high-quality instruments, which, together with our employees, ensure that every customer gets the best solution for the desired application.” Specific customer training courses also round out the offering in Scandinavia.
There are many possible uses for VEGA sensors in both countries: “In chemical and pharmaceutical companies, in wa-
terworks as well as in food and beverage plants, of which there are many. Besides that, there is a substantial shipbuilding industry in Denmark. In Sweden, we see great potential in mineral extraction, which can provide raw materials for chip production, for example,” says Jürgen Schuijren, pointing out just a few of the myriad pos-
sibilities. Both countries have also experienced huge growth in the hydrogen and renewable energy sectors. In his estimation, “Scandinavia is quite far along in the energy transition.”
Suitable locations for the subsidiaries were found a few months ago. “We were looking specifically for a place that was more than just an office. A place that inspires and offers opportunities to relax every now and then,” explains Schuijren. In Denmark, VEGA can be found in the old Carlsberg City district in Copenhagen, a trendy environment where modern lifestyle meets history. In Sweden, VEGA is located in the innovative Hagastaden neighbourhood in the heart of Stockholm.
Exhibits at Achema: Hall 11.1. Booth C63
Sanofi, Formation Bio and OpenAI are collaborating to build AI-powered software to accelerate drug development and bring new medicines to patients more efficiently. The three teams will bring together data, software and tuned models to develop custom, purpose-built solutions across the drug development lifecycle. This represents a first collaboration of its kind within the pharma and life sciences industries.
Sanofi will leverage this partnership to provide access to proprietary data to develop AI models as it continues on its path to becoming the first biopharma company powered by AI at scale.
Paul Hudson, CEO of Sanofi: “This unique col-
laboration is the next significant step in our journey to becoming a pharmaceutical company substantially powered by AI. Next generation, first-of-its kind AI model customizations will be an important foundation in our efforts to shape the future of drug development for pharma and for the many patients waiting for innovative treatments.”
OpenAI, the world leader in AI technology, will contribute access to cutting-edge AI capabilities, including the ability to fine-tune models, deep AI expertise and dedicated thought partnership and resources.
Brad Lightcap, COO of OpenAI: “There is massive potential for AI to accelerate drug development. We are excited to collaborate with
Sanofi and Formation Bio to help patients and their families by bringing new medicines to market.”
Formation Bio, an AI and tech-driven drug developer with its own pipeline of drug assets, will provide extensive engineering resources, experience operating at the intersection of pharma and AI, and its tech-driven development platform to design, develop and deploy AI technologies across all aspects of the pharma lifecycle.
Benjamine Liu, Co-Founder & CEO of Formation Bio: “I firmly believe that by combining our strengths, Sanofi, OpenAI and Formation Bio can reimagine drug development in the pharma industry.”
At Achema 2024 innovations in the areas of process, pharma, lab, green, digital and hydrogen will be explored against the backdrop of macrothemes, including sustainability and digitalization, that are at the heart of the many changes in this sector.
n June, Frankfurt will once again be the centre of the chemical, pharmaceutical and biotechnology industries: the 34th Achema, which will be held from June 10 to 14, 2024 at Frankfurt am Main, Germany, will be opened by the German Federal Minister for Economic Affairs Robert Habeck on June 10. The Achema kick-off will focus on the question of how the process industry can successfully position itself in a changing world. On all five days of the trade show, a diverse programme for young people will also contribute to securing the future of the industry.
Achema 2024 will once again fully integrate the lecture and supporting programme with the exhibition.
“Science and industry in dialogue has always been Dechema’s credo and
since the last Achema it has also been a living practice in the lecture and congress programme”, says Andreas Förster, Executive Director of Dechema e.V. and thus organiser of Achema. “The success proves us right: with more than 20,000 listeners, the number of attendees in 2022 was significantly higher than at Achema 2018, which had more participants overall”. This year’s congress programme focuses on the topics of hydrogen, sustainability, circular economy and digitalisation. At the six Innovation Stages in the exhibition and in the five highlight sessions of the congress, Achema 2024 will address these and other top topics of the process industry.
Process Innovation
The GEA Process Innovation Stage in
Hall 9.0 will focus on topics such as electrification, flexibilisation and biotechnologisation of chemical processes as well as contributions to smart digital technologies in plant construction and operation. In the Process Highlight Session “Nature as a role model – maximum resource efficiency in the chemical industry”, experts will discuss the vision of a fully resource-efficient chemical industry and its implementation. The highlight session will take place on Friday, 14 June 2024 from 12:00 to 13:00.
The ZETA Pharma Innovation Stage in Hall 4.1 will cover biopharmaceutical production in addition to many other topics related to pharmaceutical production and packaging, which is also
the focus of the Pharma Highlight Session on Monday, 10 June 2024 from 13:00 to 14:00: under the title “Next generation pharma manufacturing – current advances in cell and gene therapy”, the Pharma Highlight Session will have a closer look on the centralised and decentralised production of cell therapeutics and the current challenges of translational research and the marketing of therapies.
More than ever, success in the laboratory is determined by the technologies used in the laboratory and at the interfaces to engineering and production. This is the focus of the presentations on the Lab Innovation Stage in Hall 12.0. In addition to the Lab Innovation Stage, Achema 2024 will also feature an action area dedicated to the digitalised, miniaturised and automated laboratory of the future. Besides innovative bioanalytics and (bio) pharmaceutical applications, sustainability as well as the planning, construction, equipment and operation of laboratories will also be highlighted. The latter is a particular focus in the SEFA Theatre of the Scientific Equipment and Furniture Association.
The challenge of climate-neutral production in the process industries, the circular economy, the integration of molecular and industrial biotechnology, sustainable innovations and in-
vestments – these are the topics that are the focus of the EY Green Innovation Stage in Hall 6.0. “The chemical industry is looking to innovative technologies to bolster sustainability, such as green chemistry and circular economy practices. Achema is a key platform for bringing industry experts together to address these challenges and foster innovation”, emphasises Matthias Brey, Head of Sustainability Consulting Europe West at EY. In the highlight session “Beyond fossil fuels – exploring alternative carbon sources for a sustainable chemical industry”, on Thursday, 13 June 2024 from 13:00 to 14:00, experts from science and industry will discuss how fossil-free production can become a reality.
Digital Innovation
Industry 4.0, artificial intelligence, autonomous systems, digital twins and, last but not least, cybersecurity: the Siemens Digital Innovation Stage in Hall 11.0 offers a comprehensive and practical overview of key digital trends and their use in the process industry. “For the process industry, Achema is the key platform where innovation and practical application come together. We will show how Siemens is connecting the real world with
the digital world to create a more sustainable future for our customers”, says Axel Lorenz, CEO Process Automation at Siemens. The highlight session “Artificial intelligence and autonomous systems in the process industry” on Wednesday, 12 June 2024 from 13:00 to 14:00, will discuss the steps towards autonomous systems and explore the technological and cultural challenges that lie ahead.
Hydrogen Innovation
The process industry stands like no other sector for the technological backbone of a functioning hydrogen economy: the Siemens Hydrogen Innovation Stage in Hall 6.0, the Special Show Hydrogen and numerous other exhibitors at Achema will present the milestones of the hydrogen economy to date as well as future challenges. The highlight session “Hyperscaling hydrogen –turning strategy into reality “ on Tuesday, 11 June 2024 from 13:00 to 14:00 will deal with the central questions of the hydrogen ramp-up.
Solutions for a more sustainable and resilient process industry
The process industry is facing many challenges. The decades-long trend towards greater globalisation is cur-
More than ever, success in the laboratory is determined by the technologies used in the laboratory and at the interfaces to engineering and production
With more than 60 percent of exhibitors coming from abroad, this year’s leading trade show for the global process industry will be the most international Achema ever
rently being replaced by increasing instability and, in some cases, protectionist tendencies in trade policy. Meanwhile, the shift towards greater sustainability, the development of the hydrogen economy and the endeavour to secure raw materials require new global networks.
How do companies in the process industry position themselves in this environment? What technologies are needed to respond to the new challenges? And what political framework conditions need to be created to enable an economic transformation that meets the global challenge of climate change in particular? These questions will be the focus of this year’s Achema opening event on the evening of the first day of the trade show, June 10, 2024 from 5 to 6:30 p.m. in Room Europa in Hall 4.0.
“Achema once again emphasises its role as a central platform and meeting place for all stakeholders in the process industry”, says Björn Mathes,
CEO of Dechema Ausstellungs-GmbH. “With a notable surge in exhibitors and one of the most diverse lecture programmes in recent Achema history, this year’s event also offers an unparalleled opportunity for young technical and scientific talent”.
The floor goes to the students
During the fair, Achema companies will present themselves as employers on site. Their offers are aimed equally at (young) professionals as well as graduates or young professionals. A job board, which will be set up throughout the week, will present the job offers of all participating companies. For school pupils, Achema offers two days of events tailored to their needs: young people can ask industry and research what we can do about resource scarcity and climate change; leading experts from industry and research will provide first-hand insights; students of process engineering, chemistry and biotechnology can also talk
about their day-to-day studies and answer questions from the audience. In addition, in the Start-up Area in Hall 6.0, companies of tomorrow will present their innovations and welcome the global process industry to their booths.
An international trade fair
A few days before the opening of Achema 2024 one thing is already clear: with more than 60 percent of exhibitors coming from abroad, this year’s leading trade show for the glob-
al process industry will be the most international Achema ever. Numerous side events from renowned partners await participants from 130 countries; 2,800 exhibitors from more than 50 nations will showcase their product innovations for the global process industry at the Frankfurt exhibition grounds.
The lecture programme, which has been fully integrated into the exhibition since Achema 2022, is also reporting record numbers: in up to 25 parallel tracks, over 900 lectures, discussions and workshops from more than 1,000 speakers await Achema visitors. “Achema offers the perfect platform to showcase and exchange on the latest innovations, solutions and future trends across the pharmaceutical and chemical industry while directly engaging with those who can benefit from our sustainability-oriented solutions”, says Norbert Strieder, Head of Marketing Chemical Technologies at GEA. l
It is coming the first edition of the only Italian event dedicated to the world of the laboratory, scheduled for June 18 and 19, 2024 at the NH Milano Congress Center in Assago-Milanofiori.
Lab Italia, the new and unique event dedicated to innovation in laboratories in Italy, is about to debut in its first edition, offering participants a cutting-edge experience in the world of scientific and technological research. An opportunity that this year will not be available elsewhere in Italy. Visiting LAB Italia will allow you to network with industry leaders. Over the two days visitors will be able to meet the leading com-
panies active within this industry bringing the solutions and innovations that are revolutionizing the laboratory industry. Visitors will also be able to benefit from a free to attend scientific program dedicated to providing a comprehensive overview of everything new in the world of science and technology applied to laboratories.
The schedule covers key aspects of the industry, with a special focus on four areas: Life Science, Environmental Analysis, Pharmaceutical Sciences and Food Analysis. Developed in collaboration with LabWorld.it and featuring prestig-
ious associations and leading institutions in the sector (including CNR, Order of Biologists of Lombardy, SIBS, SISNIR, SITLAB) and leading companies in the laboratory sector.
Don’t miss the opportunity to participate in refresher sessions, round tables and presentations during which you can ask questions and meet expert speakers. LAB Italia is waiting for you. For more information on what you can find at Lab Italia visit www. lab-italia.com.
This Compact Version is ideal for installations in common mounting spaces on water puri cation or distribution skids. Clearly arranged components and menu-based operation via transmitter makes the analyzer fast and straightforward to handle. Removable stainless steel cover available.
Analytical Instruments ∙ CH-8340 Hinwil www.swaninstruments.ch · swan@swan.ch
The 37th edition of Chemspec Europe 2024, the International Exhibition for Fine and Speciality Chemicals, is to be held from 19th to 20th June in Hall 3 at the Messe Düsseldorf exhibition centre in Germany. Chemspec Europe serves as an essential networking platform, connecting buyers, traders, and agents seeking advanced products and novel solutions from across the globe. With over 380 exhibitors from 24 countries showcased on 7,650 square metres of floorspace, the upcoming edition
Solids
June 5th-6th, 2024
Parma, Italia www.solids-parma.de
Simposio AFI
June 5th-7th, 2024
Rimini, Italia simposio.afiscientifica.it
Achema
June 10th-14th, 2024
Frankfurt, Germany www.achema.de
MedPharmPlast Europe
June 12th-13th, 2024
Malmö, Sweden www.medpharmplasteurope.org
once more promises to be an unmissable event for the fine and speciality chemical industry. Alongside the main exhibition, Chemspec Europe also offers a high-level conference programme, designed to deliver valuable insights into recent industry developments and ongoing research initiatives.
Highlights of the conference programme include Julien Daubignard, Ing., PhD of Institut Carnot IPGG Microfluidique speaking on “Alternative energy sources in
LAB Italia
June 18th-19th, 2024
Milano, Italia www.lab-italia.com
Chemspec Europe
June 19th-20th, 2024
Düsseldorf, Germany www.chemspeceurope.com
Interphex Week
June 26th-28th, 2024
Tokyo, Japan www.interphex.jp
CPhI South East Asia
July 10th-12th, 2024
Bangkok, Thailandia www.cphi.com/sea/en/home.html
flow chemistry and development of automatized microfluidic systems for high-throughput synthesis of APIs’ and the presentation on ‘How to speed up API development using flow chemistry” from Dr. Guillaume Gauron of Corning SAS, both of which will take place in the Royal Society of Chemistry Lecture Theatre.
In the Regulatory Services Lecture Theatre, you can learn more about “Mastering Challenges in SCIP: Best Practices” with Yana Trubitsyna of REGARTIS s.r.o. Another highlight of the programme is the seminar about ‘Korea REACH and How to Prepare for the 2024 deadline’ from Frederik Johanson of REACHlaw Ltd.
In the Agrochemical Lecture Theatre, discover “R&D Trends in Agrochemicals” with Lawrence Middler of AgbioInvestor. The Innovative Startups Presentations will also take place in the theatre on the first day of the show, with the keynote speech ‘”Sustainability reporting in the chemical sector”
being given by Tobias Kirchhoff of BCNP Consultants GmbH.
Dorothee Arns, Director General of the European Association of Chemical Distributors – FECC will speak on ‘Chemical Value Chains - Today and Tomorrow’ in the Pharma Lecture Theatre, where Arvind Singh of SK Pharmteco will also explore ‘How AI can transform the pharmaceutical supply chain’.
Chemspec Europe offers a Matchmaking Programme to amplify networking opportunities for visitors. This programme is beneficial to all participating in the event, as it aims to unite visitors and exhibitors with shared buyer and seller interests. It also facilitates the planning of meetings prior to the event. Enhanced ticket options for upgraded networking opportunities with fellow visitors through the Matchmaking Programme are available. These include access to an on-site Matchmaking Lounge, available exclusively to Visitor PLUS ticket holders to participate in prearranged meetings.
PharmaTech Expo & LabTech Expo
August 8th-10th, 2024
Gandhinagar, India pharmatechexpo.com
Farmaforum
September 25th-26th, 2024 Madrid, Spain www.farmaforum.es
CPhI Milano
October 8th-10th, 2024
Milano, Italia europe.cphi.com
Pharmexpo
October 25th-27th, 2024
Napoli, Italia www.pharmexpo.it
Analytica China
November, 18th-20th 2024
Shanghai, China www.analyticachina.com.cn/en-us
mcT Petrolchimico
November 28th, 2024 Milano www.mctpetrolchimico.com
OMC MED Energy
April 8th-10th 2025
Ravenna, Italia www.omc.it
Pharmintech
May 27th-30th 2025
Milano, Italia www.pharmintech.it
S4S
technologies
are designed to ensure the aseptic environment necessary for drug production, minimizing the risk of contamination in every stage of pharmaceutical manufacturing.
S4S, a leading company in contamination control solutions, plays a crucial role in pharmaceutical manufacturing. Its technologies are designed to ensure the aseptic environment necessary for drug production, minimizing the risk of contamination during production, packaging, and distribution stages.
How S4S contributes to pharmaceutical manufacturing
1. Isolators - These create closed sterile environments where critical operations can be performed without the risk of external contamination. This is essential for the production of sterile products such as vaccines and injectable medicines.
2. Laminar Flow Cabinets - These en-
sure unidirectional airflow to keep the work area free from contaminating particles, which is essential for operations like mixing and filling pharmaceutical solutions.
3. HEPA Air Filtration Systems - HEPA filters installed in S4S devices remove particles and microorganisms from the air, ensuring an environment that meets the sterility standards required by the pharmaceutical industry.
4. Monitoring and Validation - The machines are equipped with monitoring systems that continuously detect contamination levels and ensure that environments remain compliant with GMP (Good Manufacturing Practices) standards.
The importance of contamination control for sustainability Contamination control is not only crucial for the safety and efficacy of pharmaceutical products but also has a significant impact on sustainability.
1. Waste Reduction - Controlling contamination reduces the likelihood of defective production batches that need to be discarded, thereby reducing waste of resources and raw materials.
2. Energy Efficiency - The advanced contamination control technologies in their machines are designed to be energy-efficient, reducing the energy required to maintain sterile environments.
3. Environmental Protection - By minimizing waste and improving process efficiency, S4S solutions help reduce the
environmental impact of pharmaceutical manufacturing.
4. Forward-Thinking and InnovationCompanies investing in advanced contamination control technologies are often at the forefront of sustainable innovation, continually seeking ways to improve processes and reduce environmental impact.
Their machines are essential for maintaining sterility standards in pharmaceutical manufacturing, ensuring product quality and safety. At the same time, rigorous contamination control fosters more sustainable practices, reducing waste and energy consumption, and contributing to environmental protection. In an industry where precision and cleanliness are crucial, S4S solutions bridge the gap between operational excellence and sustainability.
FDA guidelines on contamination control with machines and laminar flows
FDA (Food and Drug Administration) rules and guidelines for contamination control in pharmaceutical manufacturing are periodically updated to reflect technological advances and best practices in the industry. Some of the most recent updates concern the use
of machines and laminar flows to ensure aseptic environments. Here are the key points:
1. Revision of GMP (Good Manufacturing Practices) Guidelines
GMPs are fundamental to pharmaceutical manufacturing and include specific requirements for contamination control. Recent revisions to GMPs by the FDA include:
- Cross-Contamination Control: Increased emphasis on preventing cross-contamination between different batches and products. This includes the use of isolators and physical barriers during production.
- Validation and Qualification: Stricter procedures for the validation and qualification of equipment, including laminar flows and isolators. Companies must demonstrate that their equipment functions as intended to prevent contamination.
2. Specific Updates for Laminar Flows
- Design and Maintenance: Laminar flow equipment must be designed to facilitate cleaning and maintenance, minimizing hard-to-reach areas where contaminants could accumulate. This is one of the hallmarks of S4S machines.
- Air Monitoring: Continuous monitoring of air quality in laminar flow areas is required, using particle and microorganism sensors. Data must be regularly recorded and analyzed to ensure the environment remains compliant with standards.
- Air Filtration and Flow: Laminar flow systems must use HEPA (High-Efficiency Particulate Air) filters to ensure the removal of contaminating particles. Airflow must be unidirectional and constant to avoid turbulence that could introduce contaminants.
3. Guidelines on the Use of Isolators
- Open vs. Closed Isolators: The FDA provides guidance on the appropriate use of open and closed isolators, emphasizing the importance of closed isolators for critical operations with a high
risk of contamination.
- Sanitization and Sterilization: Isolators must undergo rigorous cleaning and sterilization protocols, with periodic checks to ensure no accumulation of contaminants.
4. Advanced Technologies and Automation
- Implementation of Advanced Technologies: The FDA encourages the adoption of advanced technologies like real-time monitoring systems and automation to improve contamination control.
- Data Integrity: Ensuring the integrity of data collected by monitoring systems is crucial, with cybersecurity measures to prevent tampering and unauthorized access
5. Personnel Training and Awareness
- Continuous Training: Personnel must receive continuous training on new regulations and best practices for contamination control. This includes training on the use and maintenance of laminar flow equipment and isolators.
- Quality Culture: Promoting a culture of quality within the company, where every employee understands the importance of contamination control and their responsibility in maintaining a sterile environment.
On this last point, being a partner for its clients allows S4S to always be by their side, both for daily production and with control and maintenance services, to best prepare for FDA inspections and those of all regulatory bodies.
The FDA rule updates for contamination control in pharmaceutical manufacturing reflect the importance of using advanced technologies like laminar flows and isolators, as well as maintaining rigorous monitoring and maintenance protocols. These updates aim to ensure the safety and efficacy of pharmaceutical products, minimizing the risk of contamination, and promoting sustainable and responsible practices. l
Contamination control is not only crucial for the safety and efficacy of pharmaceutical products but also has a significant impact on sustainability
The “CPhI Pharma Trends Report” addresses what is new in the pharmaceutical industry in 2024, which highlight the sector’s shift toward digital transformation, patient-centric approaches, quality management, strategic outsourcing, and sustainability initiatives.
The 2023 CPhI Online Pharma Trends Report delved into critical issues, from reshoring drug production to manufacturing reimagined through Pharma 4.0, exploring how the industry grappled with challenges like supply chain disruption, security, and escalating drug manufacturing costs. To say so is Klaus Fetzer Managing Director Health & Public, Arvato Systems.
Amidst these hurdles, 2023 provided a chance for the pharmaceutical supply chain to proactively address issues, marking a shift towards resilience and quality management. Learning from the past, the industry is embracing a proactive mindset, propelling it into a new era of supply chain robustness. Cross-industry collaboration for sustainability initiatives, the US FDA’s Quality Management Maturity pro-
gram, and patient-centric packaging designs are leading the pharmaceutical industry into the future. Underpinning these strategies is the increased digitisation of the supply chain with generative AI and machine-learning technologies. Arvato CSDB is a leading example of the digitisation of the industry – a software providing proven serialisation solutions to over 80 pharmaceutical companies, ensuring seamless implementation of legal requirements against counterfeit medicines. This positive shift is anticipated to extend into 2024, with initiatives and guidance fostering industry investment and collaboration. The goal is clear: enhance efficiency in delivering medicines to patients securely and on time. The CPhI Online 2024 Pharma Trends Report, sponsored by Arvato Systems, dissects emerging trends. From the impact of generative
AI on the supply chain to mature quality management plans for biomanufacturers, excipient market growth, biologics outsourcing, and more, these expert insights provide a valuable outlook for those navigating the global supply chain in 2024.
Generative AI and supply chain digitization
2024 will see the evolution of digital technologies for supply chain management. “One of the two topics is Big Data Analytics in the pharmaceutical industry”, says Stefan Moch, VP Health of Arvato Systems, who sees this manifesting in two major ways.
“Big Data Analytics is revolutionising pharmaceutical manufacturing, with a significant impact on quality control and regulatory compliance. Manufacturers employ data analytics to monitor and control product quality by analysing data from various sensors and equipment. Additionally, production processes are optimised
through the identification of bottlenecks, waste reduction, and efficiency improvements. Data analysis is integral to supply chain management, enabling better inventory management and minimising risks of shortages or excess inventory”.
“I would like to see AI harnessed to accelerate the flow of information across the supply chain – transparency is a critical element for sustainability and resiliency, and frankly, we are not moving fast enough or with sufficient purpose”, comments Nicola Coles, Phorum Director at Bio Phorum.
“Applying machine learning and artificial intelligence can optimise and accelerate all aspects of bioprocessing, from cell culture and upstream processing to downstream processing with chromatography and filtration”, agrees Bikash Chatterjee, President and Chief Scientific Officer at Pharmatech Associates.
Digitalisation is not restricted to the manufacturing of the drug product it-
self – pharmaceutical packaging is seeing an uptick in active and intelligent design, with the market expected to grow at a compound annual growth rate (CAGR) of 9% by 2025. Active pharmaceutical packaging refers to packaging design engineered to respond to changes in atmospheric conditions inside and outside the package itself. This is in contrast to the standard inert packaging solutions well-known to the industry. With more complex therapeutics entering the market, pharmaceutical packaging must keep pace with changing industry demands. “The use of smart packaging, such as intelligent labels and RFID tags, enables real-time monitoring of medication usage, temperature control, and expiration dates”, states Peter Schmitt, Co-Founder and Managing Director at Montesino.
Consumer driven packaging innovations
2023 saw the rise of the Contract Packaging Organisation (CPO) and an increase of outsourcing activities in the packaging sector; the global pharmaceutical contract packaging market size is projected to grow 7,43% from 2023 to 2030. Advancements in technology and changing industry needs are constantly pushing the pharmaceutical packaging sector to evolve, and 2024 is poised to be a transformative year with incoming regulations around sustainability and safety. Globally, the pharmaceutical packaging market is predicted to reach a value of USD $90 billion by 2030, with some estimates predicting up to USD $1 trillion.
“Many pharma companies have been working on improving their pharmaceutical packaging, and analysing which part of their operations relates to packaging better understand the magnitude of these processes”, says Berta Mota, Circular Economy Director
Digitization is not restricted to the manufacturing of the drug product itself –pharmaceutical packaging is seeing an uptick in active and intelligent design, with the market expected to grow at a compound annual growth rate (CAGR) of 9% by 2025
at Anthesis Group. “Although changes of packaging in pharma can be more complicated and restricted than in other sectors, there is room for improvement – it is a question of identifying where we can create change either in the short term or long term. This also helps the whole company and all departments involved understand which direction to follow and set up internal policies to make pharmaceutical packaging operations be
initiatives, with a particular focus on pharmaceutical packaging.
Last year saw increasing demands for nearshoring and re-shoring efforts to build supply chain resiliency. Ongoing global instability, including conflicts in Ukraine and Gaza, continue to disrupt delicate supply chains. The US FDA reported that while the num-
more sustainable and circular”. Smart packaging can enhance user experience: increased health literacy with QR-enabled packaging, RFID tags to identify and monitor side effects in real-time, and wearable drug delivery devices exemplify the potential of smart packaging to improve health outcomes and trusted interactions between patients and the wider pharmaceutical industry. By 2025, the market for active and intelligent packaging is expected to grow at a CAGR of 9%. The potential for smart packaging reaches beyond just the patient –supply chain logistics are also reaping the benefits first-hand. In the nearer future, sustainable manufacturing practices and a total mindset shift will be at the centre of ESG
ber of new drug shortages had fallen significantly from a high of 250 in 2011 to just 49 in 2022, the US FDA emphasises that continued shortages pose a real threat to public health. The EMA have also released a guidance on shortage preparedness for Autumn/ Winter 2023–2024, citing shortages in critical treatments such as amoxicillin. In 2019, the Federal Drug Shortage Task Force reported that 62% of drugs that went into shortage between 2013 and 2017 were linked to manufacturing or product quality issues, such as substandard manufacturing facilities and quality defects in finished products.
“Predictive maintenance is another key application, allowing for proactive equipment maintenance and reduced
downtime”, states Stefan Moch. Real-time monitoring, support for drug development, and maintaining detailed records for regulatory compliance are all facets of how Big Data Analytics enhances pharmaceutical manufacturing. “Generative AI can create regulatory submission documents by extracting and summarising relevant information from extensive text data sources”.
The continued digitalisation of the pharmaceutical supply chain may very well extend through to active quality control for manufacturers and pharmaceutical companies. Yet, in a highly regulated industry, it is important to place precision and predictability at the centre of business and operational decisions. This makes the implementation of generative AI in the pharma supply chain a challenge due to the “inherent probabilistic nature of AI outcomes”, as Moch states. To encourage pharmaceutical companies to invest in reliable manufacturing policy, the FDA is working on a new quality management protocol (QMM). Through this tool, pharmaceutical and biotechnology companies will be required to develop production systems and measures that indicate the quality performance of production and marketing systems, with the ultimate goal of avoiding drug shortages.
The 2023 CPhI Annual Report, which compiles results from the CPHI Annual Survey of over 250 pharma executives along with expert analysis of the industry, anticipates a rise in biotech funding and growth within the pharmaceutical contract services sector. Additionally, a survey conducted by Scorpius Biomanufacturing revealed that, out of 100 respondents, more than half believed their companies’ outsourcing activities would ins s s
AGENTI FILMANTI - DISGREGANTI - LUBRIFICANTI - GLIDANTI
- LEGANTI - DILUENTI - OPACIZZANTI - AMIDI E DERIVATIPOLIALCOLI - ZUCCHERI - DOLCIFICANTI - VISCOSIZZANTICONSERVANTI - CORRETTORI DI PH - ANTIAGGLOMERANTI - PRINCIPI ATTIVI - PLASTICIZZANTI
Gli eccipienti e le materie prime distribuite da Faravelli ti aiutano a raggiungere la formulazione farmaceutica perfetta, proprio quella che stai cercando: funzionale, sicura, efficace, performante. La formula che rende ogni cliente soddisfatto e felice.
“Accompagniamo con competenza globale e sensibilità locale i nostri partner verso scelte innovative, per formulare il futuro con ingredienti e soluzioni affidabili e sostenibili”.
crease from 2024–2026. Another 37% expected their outsourcing activity levels to remain the same. As more and more complex therapeutics move from R&D to clinical trials and eventually the commercial market, pharmaceutical companies and biotechs are rethinking their biomanufacturing studies for 2024 and beyond. The market for biologics has grown rapidly, despite the biotech slowdown of recent years. With estimated CAGRs of between 4% and 9.24% by 2030, the market is estimated to reach USD $500 billion. Biologics are estimated to make up 55% of all innovative drug product sales by 2027. With a number of biologics losing exclusivity as patents expire, the market is primed for biosimilar development and commercialisation.
“Over the past few years, the contract development and manufacturing organization (CDMO) sector has seen dozens of new entrants, driven by the complexities and technological needs
of cell and gene therapies, and intensified through the COVID-19-driven gold rush”, says Dan Stanton, Managing Editor at BioProcess International.
“But advanced therapies have somewhat stalled in reaching their commercial potential and the post-pandemic landscape has resulted in overcapacity”. The demand for R&D occurring in the biologics arena will require companies to make critical decisions regarding resource management and outsourcing activities for successful and timely delivery of therapeutics.
Collaborative sustainability by all, for all
Environmental, social, and corporate governance (ESG) are a continuing point of discussion for the pharmaceutical industry in 2024. The CPhI Sustainability Report 2023, explored how the pharmaceutical industry produces 55% more emissions than the automotive industry. This makes it one of the largest global contributors to greenhouse gas emissions. “Water scarcity and pharmaceuticals in the environment/antimicrobial resistance”, states Enric Bosch Radó, Global Third-Party Chemicals Manager/Human Pharma Supply Chain at Boehringer Ingelheim. “One of the most problematic issues for the pharmaceutical industry, at present, are scope 3 emissions and overall decarbonisation of the supply chain, which occur throughout the supply chain and are difficult to quantify from indirect third-party contributors”.
“Pharmaceutical companies, realising the urgency of environmen-
tal stewardship, are reporting commitments to curtail greenhouse gas emissions in their ESG reports”, suggest Aurelio Arias, Director, Thought Leadership at IQVIA. “Aggregating the results of companies with extensive audits shows that scope 3 (indirect emissions throughout the supply chain makes up 95% of a company’s average emissions (Figure 1).
The complexities of scope 3 emissions mean that precise reporting is challenging, but we do know that raw material extraction, manufacturing, and the use of medicines are the largest components in scope 3 emissions. In 2022, there were sharp rises across Scope 3 for major companies (Figure 2).
“The majority of the industry has not yet developed clear plans to reduce carbon emissions, which I see as base camp in terms of the transition to a more sustainable industry”, says Nicola Coles who is less optimistic about the future of sustainability, but still emphasises the importance of collaboration. “To be blunt – even as an industry full of scientists we “have yet to fully experience our Enlightenment period. If we did, we might also consider sustainable pharma in the context of sustainable society – truly tackling health inequalities”.
Making excipients great again By 2029, it is expected that the global market for pharmaceutical excipients will reach upwards of USD $12 billion. With a relatively stable market that is expected to only increase in its rate of growth to 2027, it’s little wonder CPhI Barcelona saw an explosion of excipient developers and service providers on the show floor this past year. The boom in excipient R&D and manufacturing is being driven by several factors. An increasing demand for generics, where close to 9 out of 10 prescriptions administered in the US
were for generics in 2023, is leading to an increased need for their excipients. With governments in developing countries boosting local manufacturing of generics to improve healthcare systems and cost burdens, the rise of generic drugs is pushing the global demand for excipients. Advancements in personalised medicine, multifunctional ingredients, and nanotechnology are also enhancing drug delivery solutions, leading to the investigation of other excipient forms and applications.
The future of B2B pharma marketing
The power of in-person interactions cannot be understated – as the events industry recovers from the COVID-19 pandemic, the appetite for a return to face-to-face meeting and events
may be even larger than prepandemic. However, the rise of digital B2B marketing for the pharmaceutical industry during the pandemic years is set to continue in tandem with a return to in-person connections. Traditional channels of brand visibility and marketing saw a leap towards digital and hybrid solutions during the pandemic, but pharma seemed to lag behind.
More than 60% of healthcare providers state they use digital media for professional purposes, and close to 70% of patients are using digital solutions for healthcare monitoring. The successful pharmaceutical service provider will also make the shift towards digital solutions to engage their business and customer base.
B2B pharmaceutical marketing must contend with a changing custom-
er landscape. Healthcare marketeers are shifting towards a digital mindset to continue delivering to their consumers. The rise of digital therapeutics, precision medicine, and customised clinical trials and therapeutics are leading to a digital marketing revolution focused on delivering personalised customer experiences.
In December 2024, CPhI Middle East will launch in Riyadh, Saudi Arabia – a country responsible for 60% of the Gulf’s pharma market. A strategic event for regional drug manufacturers and global suppliers to gather in Saudi Arabia, the event reflects the exponential increase in interest in the Middle East and Africa (MEA) pharmaceutical market and supply chain. According to research from IQVIA, in 2019 the pharmaceutical market in the MEA surpassed UDS $25 billion in value and demonstrated a CAGR of 8%, outperforming a global CAGR of 5.27%.
“The healthcare sector in the Gulf region is experiencing significant growth, presenting substantial opportunities for global healthcare companies”, comments Manel Chikh, CEO of Zaphyr Pharmaceuticals.
“The announcement of the inaugural CPhI event in Saudi Arabia in 2024 not only marks a significant milestone for the country’s growing pharmaceutical and biotechnology sectors but also aligns seamlessly with the aspirations laid out in Saudi Vision 2030”, states Muased Alkholief, Professor and Management Consultant at King Saud University. “Rooted in the Vision’s strategic goals of economic diversification, the event is poised to attract foreign investment and promote the growth of the local pharmaceutical industry, contributing to a more resilient and diversified economy”. l
By 2029, it is expected that the global market for pharmaceutical excipients will reach upwards of USD $12 billion
Berlin Cures, a pioneering clinical-stage biotechnology company, announced the successful completion of patient screening for its pan-European Phase II trial of BC 007 (Rovunaptabin), a novel therapeutic candidate for the treatment of Long COVID. The study has now recruited its target number of participants, marking a significant step forward in the company’s pursuit to help millions of people suffering from Long COVID. The trial is progressing rapidly into its next clinical stages and remains firmly on schedule, with first results anticipated by autumn 2024.
More than 114 patients
across 14 trial centers in Finland, Germany, Austria, Switzerland, and Spain have now been enrolled. With the completion of the screening process, patients are asked to refrain from submitting further applications, as all available places in the study have been filled.
Oliver von Stein, CEO of Berlin Cures, expressed his satisfaction with the trial’s progress: “The completion of recruitment in such a short period of time demonstrates the great need for an effective therapy for Long COVID. This achievement reflects our commitment to rigorous scientific processes and our dedication to developing a
treatment that can significantly improve patient outcomes. We look forward to the forthcoming results, which we believe will bring us closer to a major breakthrough in the fight against Long COVID.”
Berlin Cures is at the forefront of developing innova-
tive aptamer-based drugs to neutralize pathogenic functional autoantibodies (fAABs) that contribute to a variety of autoimmune diseases, including Long COVID, heart failure, glaucoma, ME/CFS and many more. The drug candidate BC 007 targets these harmful fAABs, which are believed to play a critical role in the symptoms associated with Long COVID. With the trial fully recruited, Berlin Cures is actively preparing for the subsequent Phase III study, which will be essential for gaining regulatory approval and bringing BC 007 to market. The company is currently actively seeking funding partners to initiate Phase III as soon as possible following the successful completion of Phase II.
Relief Therapeutics Holding SA, a biopharmaceutical company committed to delivering innovative treatment options for select specialty, unmet and rare diseases, announced it has granted an exclusive license to Eton Pharmaceuticals, Inc. for the commercialization of GOLIKE® family of products in the United States.
“This transition is fully aligned with Relief’s strategy of moving the GOLIKE products into partnership models in the U.S. and Europe. We are very pleased to be establishing this partnership with Eton for GOLIKE patients in the U.S. given their valuable experience in the metabolic area,” said Michelle Lock, interim CEO of Relief.
“We are excited to be partnering with Relief on PKU GOLIKE in the United States.
After extensive discussions with metabolic geneticists, dieticians, and PKU patients, we believe PKU GOLIKE is the best product in the estimated $100 million U.S. PKU medical formula market. With our sales force and existing relationships in the metabolic community, we believe we can significantly increase the awareness, education, and adoption of this important product,” said Sean Brynjelsen, CEO of Eton Pharmaceuticals. Under the terms of the agreement, Relief will receive an upfront payment of $2.2 million and is eligible to receive an additional $2.0 million in sales milestones payments as well as mid-teens royalties on net sales. In the fourth quarter of 2023, PKU GOLIKE’s annualized net sales exceeded $1
million in the U.S., continuing its growth trajectory since its launch in late 2022. As part of the agreement, Eton also received U.S. rights to Relief’s GOLIKE Medical Food line extensions under development for the management of other inherited rare metabolic diseases such as tyrosinemia and homocystinuria, which are both expected to launch in 2025 and 2026 under the same trademark. Relief is also in discussions with Eton related to additional development assets, including RLF-OD032. RLF OD032 is an innovative drug product candidate under development for the treatment of PKU expected to be filed for approval before the FDA in H2/2025 as 505(b)(2) application. Relief will continue to fully own GOLIKE rights outside the United States.
Aggiornati sulle tendenze attuali e future. Ricevi una guida sulle sfide regolamentari e scientifiche all'interno dell'intera industria italiana dei laboratori.
L'area espositiva sarà ricca di innovazioni dei principali fornitori e produttori scientifici che presenteranno gli ultimi sviluppi e attrezzature da laboratorio applicabili a una miriade di settori industriali.
La conferenza di Lab Italia rappresenta un'opportunità unica per esplorare le frontiere della conoscenza, approfondire argomenti di rilevanza internazionale e connettersi con alcune delle personalità più influenti del settore.
NH Milano Congress Centre 2024 18-19 Giugno
FIERA
CONFERENZA TECNICO-SCIENTIFICA
Lab Italia si svolgerà il 18-19 giugno e riunirà la comunità italiana dei laboratori. Supportato da alcune tra le più importanti istituzioni scientifiche italiane. Lab Italia si sta profilando come un evento chiave per l'industria della scienza di laboratorio. Una piattaforma per mettere in mostra soluzioni innovative e all'avanguardia e un punto di incontro per far nascere collaboazioni significative, a contributo dello sviluppo scientifico di tutta la comunità dei laboratori.
Registrati su www.lab-italia.com
Contenuto scientifico sviluppato in collaborazione con:
The expansion of services and resources enabled PVS Group to come as a benchmark partner in the field of qualification and validation processes for the whole pharma supply chain. Waiting for the Compliance Day 2024, the Sales & Business Development managers explain how their company could consolidate its relationship of trust with the market.by Marzia Savino
Starting from consultancy and qualification services for API and HPAPI productions, the PVS (Process Validation Service) Group in a few years has extended its core business along the whole pharma supply chain, subsequently growing in terms of experiences and resources and facing increasingly complex challenges. The opening of three head offices, the participation and organization of
technical-scientific dissemination events, the expansion of services by founding the SolTech company, make PVS a very brilliant company in its area, capable of building up positive relationships. To get to know the group’s approach to the market better, we asked a few questions to three key Sales & Business Development Managers: Stefano Moltani, Chiara Mariani and Manfredi Musmarra.
Stefano Moltani, can you describe the added value and skills that have built PVS Group identity so far?
Moltani: “In these intense ten years’ activity, the company could meet plenty of customers’ requirements, always working hard to find solutions, supporting the needs aimed at finalizing the project ‘goals’ in terms
of timing and quality. Based on the previous experiences of the founding members – Rodolfo Russo, Antonino Manoli, Antonio Santisi – the company took its first steps in the field of consultancy and qualification services for API and HPAPI production plants and the related automation (DCS, SCADA, PLC/HMI, recording systems…), both for green field projects and revamping projects, as well as for routine maintenance activities. Good results enabled PVS to introduce many resources: this has progressively led us to operate within the entire pharma supply chain, thus gaining more and more expertise and opportunities to deal with new challenges. I’d say our cutting edges are flexibility, dynamism and
whereas today PVS staff is about to reach 50 units and our tool park has expanded in terms of types and quantities. With the present technical and instrumental force, we are able to manage complex qualification projects, reaching a meaningful share of the services provided throughout the country and significantly increasing our customer portfolio.
This is a source of satisfaction for us and the feedback we got, pushes us to commit even more. Looking back on our journey, the results were many, even on a corporate level. Over the years, we opened three head offices: in Paderno Dugnano
reliability. Of course, quality remains an essential element in our business”.
What have been the main results achieved in these first ten years and what are the next steps?
Moltani: “In the first year of operation, resources and tools were less,
Stefano Moltani: “Today PVS staff is about to reach 50 units and our tool park has expanded in terms of types and quantities. With the present technical and instrumental force, we are able to manage complex qualification projects”
(MI), Vicenza e Latina. Starting from the first small rented office, today we own the 600 m 2 headquarters in Paderno Dugnano.
An important result also from a financial perspective, which speaks of our commitment and desire to create a serene and collaborative environment.
Over the years, expert professionals and people of value have grown up here: they are still an integral part of the company today and a driving force for new colleagues in terms of responsibility, skills and maturity”.
PVS Group Sales & Business Development Managers: from the left, Manfredi Musmarra, Chiara Mariani and Stefano Moltani
PVS has been cooperating for many years with chemical and pharma industries offering GMP services, and the appreciation our group of technicians has always received turned our interventions from merely technical services into consulting opportunities
Chiara Mariani, what about PVS team’s approach to the customer and to the market?
Mariani: “PVS corporate spirit is based on values we strongly believe in, that we like to bring about and highlight in the relationships with our customers: sharing, commitment and reliability. This because we think an honest and constructive discussion is the basis of every peaceful professional relationship. In the company, we are used to speaking directly, to talk about experiences, problems and daily activities in our environment. We try to recreate this mood at customers’. They perceive and appreciate it. Our customers trust us and this is the greatest goal we aim at. On an operational level, we assign a dedicated technical contact person for each activity and for each customer, and in case of particularly complex projects, we also hold periodic meetings internally to analyze the work in progress. We assess together every single client according to their features, making sure they feel understood and involved in achieving their goals”.
How do you approach sector events?
Mariani: “From a commercial point of view, sector events are an important strategic action in terms of position-
ing and communication. From a relationship point of view, in our opinion, they are an opportunity to meet our customers and discuss with them. PVS is keen on having a strong presence on the most important events in which its operational field is the protagonist (association conferences, trade fair congresses, scientific seminars, etc.), also through sponsorships or its own stand, which becomes a point of reference for business meet-
Chiara Mariani: “Our customers trust us and this is the greatest goal we aim at”
ings or, as it often happens, an opportunity to exchange greetings and insights in a more informal environment. Yet, that is not all. Because in our opinion, it is essential to conduct the game firsthand. That is why PVS has been promoting its Compliance Day for years, a free seminar aimed at our customers, which is held annually. The topics range from risk-based approaches in qualification and commissioning to value-added services for the life sciences industry, and much more, with programs that are updated depending on the latest topics. Teachers are selected among our project managers – people with high technical skills, who face challenges
in the field every day, and who therefore have a lot to tell – and some key figures among our partner companies, including Endress+Hauser and QualiWare. This year the Compliance Day will be held in Aprilia (LT) on October 3rd: of course, you are all invited!”.
Manfredi Musmarra, Let’s talk about SolTech: which were the premises and what about its goals?
Musmarra: “It was a natural evolution of what happened over time from the collaboration with our customers and partners. PVS has been cooperating for many years with chemical and pharma industries offering GMP services, and the appreciation our group of technicians has always received turned our interventions from merely technical services into consulting opportunities. All this meant a new awareness of our potential. Customers have recognized our great reliability and, more and more often, they have involved us in the choice of solutions technologically suited to their context, looking for alternative solutions and project management. Thus over the years, we have carved out a position in our sector, not just as PVS, but as a group of companies capable of expressing added value in the field of highly specialized engineering, design and consultancy services in the GMP field. Relying upon customer trust and upon our top technical level, our Group aimed at a further goal and we created a new subject to implement the services we wanted and were able to offer the market. SolTech was born from this initial thrust, to expand our service range, offering customers the chance to contact a company focusing on innovative technological products and solutions, suitable for the many and varied Italian and foreign manufacturers”.
What solutions does SolTech implement and for which pharmaceutical applications?
Musmarra: “We are very well introduced in the market of specialized products and systems for the pharmaceutical world. This does not mean we only offer innovative solutions, but we can also select already present products and services, or in any case those that are most suitable to the real customers’ needs. In fact, the choice of the best technologies to integrate into projects often requires a deep knowledge of the products available on the market and an essential verification of their real applicability to production processes. By the way, SolTech offers disposable products, process and laboratory equipment, automation systems (based both on architectures already present on the market and which can be created with alternative products suitable for every budget). For instance the latest idea was designed and developed for MKT calculation, for the purpose of integrating this functionality on systems where it is not present, and combining the system’s solidity with the cost-effectiveness that this introduction requires. The search for quality products, with an essential green vocation, has also led us to select a wide range of disposable products - full-body suits, in particular - which also features an ISCC+ certification, essential to certify the real participation in the chain of modern products recycling. Lately, turnkey activities are playing an increasingly higher importance in our business. The interventions on the re-
PVS Group has been organizing for several years, in collaboration with partner companies, an in-depth day on the technological challenges of the life science sector.
Next meeting: Compliance Day in Aprilia, 3 October 2024
cording of environmental parameters in laboratories and warehouses have become very relevant, allowing us to provide the complete range of services, thanks to the total management of the project: from the study and regulatory compliance phase, up to the supply and creation of tailor-made products, field installation and, obviously, plant qualification and validation of the systems connected to it”.
Are you thinking about expanding the range of partner brands?
Musmarra: “Certainly we are. Representing for our customers a reliable and competent partner means committing to always being informed about what is designed and is available on the market. Throughout this year, we aim at expanding our collaborations with other manufacturers. The automation market in general is our benchmark market: many of us come from this world and, with the latest additions to the group of specialized personnel, we foresee further developments also for more complex and highly customized projects”.
How does the synergy with the PVS group occur?
Musmarra: “Synergy is our strength. We have always relied upon the collaboration among the engineers from
Manfredi Musmarra: “SolTech integra la proposta di PVS Group, proponendo prodotti monouso, apparecchiature di processo e per i laboratori, oltre a sistemi di automazione”
Manfredi Musmarra: “SolTech offers disposable products, process and laboratory equipment, automation systems: based both on architectures already present on the market and which can be created with alternative products suitable for every budget”
Process Service, a company specializing in the production of chemical-pharmaceutical plants, and PVS technicians and consultants in Italy and abroad. Thus we can complete our proposal relying on process experts, specialised technicians, GMP consultants, as well as consultants for very special plants – I’m thinking of our in-house section dealing with TOC – as well as automation experts to develop bigger projects. This synergy among our colleagues’ skills and experiences is very important for us. This enables us to be a group of consultants with a broad spectrum of knowledge, capable of facing complex problems thanks to the presence in the group of people with expertise on very specific technical topics. This approach makes us a key partner: a consultant with a vision that doesn’t focus only on single issues, but considers the general context”. l
Flexibility, robotics and waste minimisation for a more sustainable and time-saving production of drugs.
Achema 2024, the World Forum for the Process Industries that unites manufacturers and service providers from over 50 countries, is fast approaching. Steriline, the European manufacturer of standard and robotic lines for the aseptic processing of injectable drugs, will exhibit at stand E95, hall 3.1
could cause a fall in revenue for pharmaceutical manufacturers, which are under additional pressure because of fixed sales prices for drugs (i.e. in the EU).
Technologies and solutions that facilitate the maximisation of profit are thus under intense scrutiny by pharmaceutical produc-
(Frankfurt Fair), showcasing the new technologies developed to upgrade its zero-loss philosophy, to better meet the sustainability needs of the pharmaceutical industry.
The market for pharmaceutical packaging will grow by 8.24% worldwide and the market for pharmaceutical packaging machines by 7.5% per year until 2028. At the same time, the rising costs for filling, packaging and labelling medicines, added to the increased energy costs,
to easily change the production cycles and vary containers and capacities) with zero-loss philosophy 2.0, a methodology first developed five years ago and now improved to further save time and speed up production. Steriline’s zero-loss philosophy 2.0 detects inaccuracies in filling and stoppering processes directly in their respective stations and, if necessary, it reprocesses any non-compliant pieces. The filling station is equipped with high-precision weighing cells that measure the filling levels and, through sophis-
ers, who are particularly focused on production flexibility, robotics implementation and sustainability, especially in terms of recycling and reducing consumption and waste.
At Achema 2024, Steriline will showcase a Robotic Vial Filling Machine (RVFM5) that merges these qualities for the primary packaging of injectable drugs. Equipped with 5 filling needles, it integrates robotics (which allows
ticated software that relies on the received feedback, the station controls pump operation to deliver accurate filling (±0.5 % or better, depending on filling volume vs. output requirement). At the stoppering station, the technology relies on pressure sensors that can distinguish an appropriately executed sealing process from an incorrect one. Both checks potentially avoid any waste due to non-compliant filling or missing components.
“Innovation and sustainability
are certainly among the challeng es of the pharmaceutical indus try,” states Federico Fumagalli, Chief Commercial Officer of Ster iline. “United, these themes lead to a win-win combination: a low er impact on our planet (in terms of resources) combined with a reduction in production costs, a panacea for business and operat ing margins. The zero-loss philos ophy, which we continue to im prove thanks to research in our laboratories, embraces this syn ergy and aims to minimise waste in favour of more efficient pro duction.”
The RVFM5 will also be equipped with a new technology for the monitoring of viable and non-vi able particles provided by Particle Measuring Systems. “Continuous microbial monitoring by active air sampling is achieved using the BioCapt® Single-Use Impactor, making it possible to reduce the amount of agar plates for air mon itoring by at least 50% on filling lines such as Steriline’s,” states Frank Panofen, Vice President & GM of the Life Sciences Division at Particle Measuring Systems. Finally, visitors will also have the exclusive opportunity to discover the new launches of rapid trans fer solutions from Getinge. Posi tioned as a step forward in aseptic transfer, they represent Getinge’s commitment to addressing cus tomer challenges related to con tamination risk, production effi ciency and resource utilisation. Attendees can discover firsthand how these innovative solutions contribute to operational integ rity, production processes and re source management.
Exhibits at Achema: Hall 3.1, stand E95
S4S revolutionizes pharmaceutical manufacturing with state-of-the- art contamination control solutions. Our technologies ensure sterile environments, reduce contamination risks, and meet the highest standards.industry
We bridge operational excellence and sustainability, ensuring your pharmaceutical manufacturing is safe, compliant, and environmentally responsible.
Antares Vision Group, a leading player for traceability and visual inspection solutions, will present its latest technological developments for the life science sector at Achema. Among other solutions, at Stand B4, Hall 3.0 the company will debut its first automatic inspection machine for
blow-fill-seal (BFS) cards. Providing 100% inspection, the VRI VI for BFS Cards can provide seamless quality assurance at speeds of up to 100 pieces per minute.
BFS containers are among the most prominent packaging type for pharmaceuticals; however, their inspection presents a set of unique challenges due to characteristics such
as surface uniformity, complexity of shape, variable transparency and opacity, and small dimensions. Antares Vision Group’s BFS card machine performs cosmetic inspection, particles detection (reflecting & non-reflecting), fill level check (short wave infra-red) and tab OCR/ OCV verification. When necessary, the unit can employ advanced algorithms capable of effectively detecting foreign particles in containers at low fill levels, which pose additional challenges given their aversion to spin-centric detection techniques.
Leak Detection Capabilities
Also in Frankfurt, Antares Vision Group will emphasize its prowess in leak detection. For example, the company’s container closure integrity testing (CCIT) plays a critical role in maintaining the sterility and stability of sterile products, and is essential for preserving critical headspace gas conditions – including those common to freezedried products.
The company’s solutions set in this niche includes Head-Space Gas Analysis (HSGA), a rapid, reliable, and non-destructive analytical method suitable for monitoring gas concentration and pressure measures in sealed containers. HSGA can be used to detect primary container leaks, or as a process analytical technology (PAT) to control facets of the upstream process (e.g. humidity excess).
Antares Vision Group provides visual inspection, CCIT and combined VI & CCIT machines that are specially designed for small- to large-volume BFS containers, as well as solutions for other container types.
AI-enabled solutions for Blister Filling Control
At Achema, Antares Vision Group also will showcase a completely redesigned solution for inspecting pharmaceutical blisters. Equipped with artificial intelligence features, the Blister Filling Control (BFC) module can be easily integrated into common blister production and sealing lines. The system’s features provide enhanced inspection of various oral solid dose products housed in blisters – including scenarios where low contrasts (such as white pills in white packaging) present inherent challenges. The BFC unit also facilitates and expedites new product recipe setup.
Antares Vision Group also will display its new range of checkweighers designed for maximized efficiency and seamless line integration. The machines perform accurate weight
control at speeds up to 350 ppm, and feature a top-bottom gripping system with stabilization conveyor. The range is fully compliant with 21 CFR Part 11, and can be equipped with various ejection systems as determined by product weight.
Traceability, inspection for quality control and integrated data management
Other solutions presented by Antares Vision Group at Achema include:
• Serialization and aggregation technology: Antares Vision Group’s proven modular solutions for managing track & trace compliance with seamless integration on any third-party equipment, as well as standalone modules covering Levels 1-4 hardware and software for EU-FMD, DSCSA and other regulatory requirements.
• Smart Clearance: a solution environment designed to automate the mandatory line clearance process through integrated cameras powered by artificial intelligence, toward the goal of improving plant efficiency and productivity.
• Layout Inspection for stick packs: a system that verifies the correctness of printed information (including variable data or barcodes)
designed for inline installation on stick pack filling machines.
Antares Vision Group systems are part of DIAMIND, the integrated ecosystem of solutions connecting physical products with digital identities and operating at line, factory, warehouse, enterprise, and supply chain level to guarantee product quality and end-to-end traceability through integrated and cloud data management. l
Exhibits at Achema: Hall 3.0, Booth B4
As a one stop solutions supplier, Romaco will be taking advantage of this year’s Achema to present its broad portfolio of machinery. From powder processing to the finished pallet, the manufacturer’s technologies cover the entire process chain in the pharmaceutical, nutraceutical, food and chemical industries. The all-in-one machinery supplier strictly focuses on aspects of sustainable product development. Romaco’s energy efficient technologies make sparing use of resources and improve the carbon footprint of its machines while cutting the manufacturing costs for users. The company’s success in meeting climate change objectives is audited by independent organizations. Romaco recently earned a silver medal in the EcoVadis Sustainability Rating and, with a total score of 67, is among the 11% top-rated businesses. In addition, the SBTi (Science Based Targets initiative) has confirmed the achievement of Romaco’s targets for reducing Scope 1 and 2 greenhouse gas emissions in 2023. In 2024, Romaco also became a member of the UNGC (United Nations Global Compact).
The containment version of Romaco Kilian’s KTP 420X C rotary tablet press fulfills all requirements for processing active pharmaceutical ingredients up to OEB Level 3 with medium toxicological potency. This includes numer-
ous medications, for example for treating hypertension, ventricular ulcers or bronchial asthma. The containment tablet press is configured with a Restricted Access Barrier System (RABS) featuring glove ports to protect the operator as well as a Rapid Transfer Port (RTP) for contamination-free material transfer. Negative pressure in the compaction area and electric door locks as well as dust-tight docking systems and a dust-tight tablet chute moreover ensure GMP compliance. The efficient implementation of high-quality containment processes is additionally supported by the proven hygienic design of the KTP 420X C. The hermetical separation between the compaction and technical areas prevents tablet dust from en-
tering the mechanical compartment. The compaction area itself is designed as a deep-drawn, single-piece run-off containment with polished surfaces and large radii, so that far less effort is necessary for cleaning. Protective clothing is only required for cleaning the press and is not essential during production. The very good OEE and extremely low TCO are key characteristics of the Romaco Kilian KTP 420X C. With a maximum output of 475,200 tablets per hour, the technology is classed as a high-speed press for containment applications.
All in all, Romaco will be exhibiting six different machines in the areas of granulation, tableting, film coating, blister packaging and aseptic liquid filling. Among them is the Kilian KTP 1X R&D tablet press for laboratory use. The compact TPR 25 Pilot mobile tablet coater is the latest addition to Tecpharm’s Optima product family and covers an extremely wide batch size range from 5 to 100 percent. The Innojet VENTILUS® Pilot fluid bed processor is another mobile all-rounder for pilot scale applications that impresses with excellent results in terms of flow properties as well as powder and granulate compressibility. Romaco Noack’s new Unity 600 blister packaging line combines high efficiency with a sustainable system concept. This double-lane, highspeed line achieves a maximum output of 600 blisters and 350 cartons per minute. The Macofar Oftalmica was specially developed for filling additive-free ophthalmic products but can also handle nasal sprays and injectables.
Exhibits at Achema: Hall 3.0, Booth B49
MG2 Srl (based in Bologna, Italy) and Qualicaps Co. Ltd (based in Nara, Japan), two companies that have made the history of pharmaceutical technology and still represent the best of quality in their sector, announce the conclusion of a distribution agreement. Indeed, the two brands share a long history that sees both enter the market in the mid-60s and today they are synonymous of product reliability and quality.
“We are proud of the esteem and the trust shown towards MG2 by Qualicaps, a company that can boast a unique expertise in the supply of solutions for pharmaceutical production into capsules. This collaboration will allow us to further increase the value of our products and services range,” says Manuela Gamberini,
General Director of MG2.
“Qualicaps is excited to enter this collaboration with MG2, a company renowned for its excellence in pharmaceutical equipment. This represents a major advancement for both organizations, enabling us to join our collective expertise and capabilities to provide liquid filling solutions to a broader customer base,” adds Seiichiro Matsumura, President of Qualicaps in Japan.
From now on, indeed, MG2 machines equipped with liquid filling unit can benefit from an additional strength: the integration with Qualicaps sealing machines.
More in detail, the agreement between MG2 and Qualicaps consists in the distribution by the Italian company of the Qualicaps sealing machine
> estrusori > dosatori > componenti > trasporto pneumatico > sistemi completi
+ Dosatori ad alta precisione per un dosaggio ottimale degli ingredienti
+ Cambio rapido tra configurazione a vite singola e a vite doppia
+ Un unico riduttore di velocità offre una gamma completa di portate per tutti i modelli
+ Ingombri ridotti ideale per sistemi multi componente
+ Inclinazione dosatore di 2 gradi per un migliore drenaggio nel WIP
+ Facile da smontare e pulire
Montenegro S.r.l. Via Volturno, 37 20861 Brugherio (MB)
Tel: +39 039 883107
Fax: +39 039 880023
info@montenegrosrl.it
model S-125 that adds the celebrated quality and reliability of the Japanese technology to the undisputed know-how of the made in Italy product of MG2.
Exhibits at Achema: Hall 3.1, Booth F47
I nuovi dosatori farmaceutici Coperion K-Tron sono ideali sia per applicazioni a batch che continue. Il concetto generale è impostato specificamente per una rapida pulizia e smontaggio, richiede solo pochi secondi disconnettere la tramoggia semisferica, l’agitatore, le viti di estrazione e la tramoggia di stoccaggio dal riduttore. www.coperion.com/it/dosatori-farmaceutici
At Achema 2024 Marchesini Group celebrates its 50th anniversary and showcases a wide selection of machines and production lines for the pharmaceutical industry.
One of the most anticipated events for chemical, pharmaceutical, and biotechnological companies worldwide is returning: Achema 2024. This edition will be a special occasion for Marchesini Group, as it celebrates its 50th anniversary this year. In addition to showcasing a wide selection of machines and production lines for the pharmaceutical industry, the Group will invite visitors to join the celebrations and reflect on the future together, sharing new ideas and projects.
The G3 stand – Hall 3.1 will host several solutions produced by various Group divisions, including an absolute novelty designed to enhance the performance of companies specialised in the production of injectable sterile medicines. It is a line under isolator for sterile filling, capping, and coding of vials of various sizes, designed to be extremely fast: the line can produce up to 500 pieces per minute with 100% IPC. The line will be unveiled to the public on the first day of the event, June 10th, with an official presentation to the press and industry
experts scheduled for 12 o’clock. In addition to this innovation developed by the Aseptic division, the Group will also exhibit several machines produced by the Pharma Process and Pharma Laboratory divisions, perfectly compliant with the rigorous Good Manufacturing Practice (GMP) standards. The stand will also feature two monoblocks, one for packaging solid products and one for powdered products: the first consists of a blister machine, equipped with the SEA Vision Line Clearance system, and a cartoner with an integrated Track & Trace module; the second is a compact solution for powder filling with 100% weight control, developed by M.A.R, the latest brand to join the Group.
New additions from the Pharma Packaging division showcased at the stand include a line for packaging and labeling injection pens, featuring a robotic island that precisely and flexibly positions the pens inside a paper tray. This tray, internally designed by the R&D department, features a functional design that enables significant savings in paper and glue (-50% compared to traditional models on the market).
Finally, there will be a corner dedicated to the Digital area featuring the latest innovations in digital transformation and artificial intelligence, includ-
ing the “Morpheus” predictive maintenance solution, augmented reality format changeover, and the latest tech nologies related to robotic applications.
A constant focus on the future Marchesini Group closed 2023 with 591 million in revenue, marking a +15% in crease compared to 2022. In 2024, the Group plans to consolidate its strategic assets, maintaining the same trend as the previous year and aiming for further growth. “To achieve these objectives and best prepare for the challenges that lie ahead, we will continue to invest in robotics, vision systems, and artificial intelligence,” comments Pietro Cassani, CEO of Marchesini Group. “Building the future together also means focusing on youth and education, continuing to travel and export ideas and innovations worldwide. In recent months, we have opened new branches in South Ameri ca, Asia, and North Africa, ensuring an even more impactful presence in over 116 countries worldwide. Our 100% made in Italy production remains en tirely in Italy, where we are strengthen ing production by initiating expansion works at some of our facilities in Tuscany, Lombardy, and Emilia-Romagna”.
Exhibits at Achema: Hall 3.1, Booth G3
At Achema, Syntegon presents an exemplary OSD production line, which shows all possibilities: from laboratory to big batch production or continuous manufacturing.
At Achema, Syntegon presents its comprehensive portfolio for the development and production of oral solid dosage (OSD) forms. “We are currently seeing two trends that offer pharmaceutical companies different advantages: on the one hand, production in ever larger batches and, on the other hand, continuous manufacturing,” says Fritz-Martin Scholz, Product Manager at Syntegon. “We are continuing to develop our existing portfolio in both directions and can therefore identify and implement the best solution for our customers’ applications.” An exemplary OSD production line and further exhibits give trade show visitors the opportunity to see this wide range of possibilities.
Gentlewing: effective mixing and granulation
With the Gentlewing impeller from the Syntegon subsidiary Hüttlin, the company presents a solution that meets the need for flexible batch production. Its unique geometry enables the innovative mixing tool to achieve fill levels of between 20 and 80 percent and is a core component of the Hüttlin highshear mixer technology. “The Gentlewing achieves optimum granulates with high yields in all versions,” Scholz emphasizes. This makes it possible to produce batches of between 0.1 and 720 kg, from R&D to pilot and production scale. The technology is available in top or bottom drive executions.
Pharmaceutical companies also require a high degree of flexibility in terms of process and batch sizes when it comes to fluid bed technology. The HDGC fluid bed system enables the highly efficient drying, granulation, and coating of powders, granulates, and pellets in just one product container – from laboratory scale to batch sizes of more than 1,200 kg. Thanks to the special air flow of the Hüttlin Diskjet, the system ensures optimum use of process air. This results in homogeneous fluidization, shorter process times, and a low filter load. During granulation and coating, a special three-component nozzle provides higher spray rates and an optimized yield without interrupting the process.
Xelum: continuous manufacturing at all scales
In addition to batch production, continuous manufacturing is a time- and cost-efficient alternative. With the Xelum platform, Syntegon offers a flexible solution for both continuous direct compression and continuous fluid bed granulation. Xelum doses and mixes active ingredients and excipients as individual X-keys (packages), which run
continuously through the process chain and are continuously removed from the system, for example as tablets from the integrated TPR tablet press. “Xelum ensures shorter time to market for new formulations,” Scholz explains. This is further supported by the simple scale-out: “The process parameters of the Xelum R&D can be transferred directly to the production system – for a faster production start and significantly lower development costs.”
TPR 500: production-scale tablet compression
Flexibility in tablet shapes and batch sizes as well as robust manufacturing processes are the main requirements for tablet presses. The TPR 500 on show at Achema can produce more than 400,000 tablets per hour in a wide variety of sizes and shapes. “Our customers appreciate the broad range of mixtures and granulates that can be processed, as well as the ergonomic and user-friendly design of the press,” Matthias Moessinger, Product Manager at Syntegon, underlines. The modular powder feed system can be adapted to any powder characteristic. All filling and machine parameters that are important for product quality are continuously monitored and documented in accordance with GMP and GDP.
Exhibits at Achema: Hall 3.1, Booth C71
Interview with Simonetta Ghisi, CEO at Texpack, leading manufacturer of industrial gaskets:
“There are many achievements we are proud of. Yet we cannot stop to look back and enjoy our previous results: every year we are ready for new challenges”.by Alessandro Bignami
There is never a time to sit down and look back to observe and enjoy your good results. Every year actually brings new challenges, often raising the bar of difficulties to be overcome. Yet, this awareness does not deprive Simonetta Ghisi, Texpack CEO, of the deep pride for the 30 years history of the company, founded and led together with her husband, Giorgio Lanza, until he passed away in 2020, when the pandemic was beginning. Texpack, headquartered in Adro (BS), is a manufacturer of packings, tapes, twisted ropes, cloths and sleeves, for thermal insulation with dynamic use, of pumps and
valves. It produces and markets industrial gaskets of different types and sizes, offering a complete range of sealing systems and products for high temperatures, as well as a range of products for the maintenance of fireplaces and stoves dedicated to the consumer market. With Simonetta Ghisi, now alone at the helm of Texpack, though supported by her sons Camilla and Antonio, we had the opportunity to take stock on the company’s thirtieth anniversary, a period during which Texpack faced and overcame many challenges.
Simonetta Ghisi, you’ve just celebrated your first 30 years.
“Texpack took its first steps in-between the end of 1993, when it start-
ed as an individual business, and the early 1994, when the LLC was opened. That is why, after a first celebration before Christmas, this year we’ll still have a moment of celebration”.
What are you most proud of during this long journey?
“Looking back, first of all I’m proud of how we succeeded in overcoming the initial difficulties. Those were engaging and complex years, during which we faced the challenge of the transition from asbestos to substitute materials. Since then, the company has gone on growing and strengthening and I’m proud of the various goals we achieved.
Yet I immediately realized there isn’t definitely a time to sit down and enjoy your results. Every year there’s a new obstacle to overcome, a new problem to be solved. Just think of the latest period: the pandemic, the shortage of raw materials, the breakdown of supply chains, inflation and now the wars on Europe’s borders. To cut a long story short, for those who do business there is no ‘comfort zone’, even when one might deserve it.
We must always be ready to get back into the game, to adapt to different, ever-changing situations, for the purpose of evolving the company. First, there were two of us at the helm, my husband, Giorgio Lanza, and me. Today I’m alone, supported by my daughter Camilla and my son Antonio Lanza, who are training and still have
a lot of experience to gain. In recent years my responsibility has therefore increased, but for a long time, at least, I have been surrounded by a close-knit and qualified team. We must keep on this path and expand to new professionals to make the company’s organization even more efficient. Changes are increasingly faster and, compared to the first stages of our history, the way of working is decidedly different”.
Are you working on innovative products?
“Our sector is not so sensitive to innovations or latest trends. Once a process works well, it is not likely to be modified to adopt a new kind of gasket. Innovation is made moreover in case of special and unique applications, that cannot be standardized as you can do with catalog products. If we really want to talk about trends, I remark that, with international conflicts and attacks on commercial ships in the Red Sea, the choice of made in Italy is becoming increasingly strategic, as well as prestigious and safe.
And this clearly benefits us in the competition with products imported from Asia”.
Have you installed new machines in the production area?
“In recent years we have invested very much in innovative technologies, thanks in particular to the benefits of the Industry 4.0 plan. One of the latest addition is the plate cutting machine, that enabled us to further improve gasket production. At first, we purchased it mainly to meet the need of limited and urgent quantities. But the use of the new cutting machine now is increasing and is going to support our total production structurally. We are also investing on the head office, to equip it with an entrance and a sign to be better identified and on the participation to international exhibitions in different sectors”.
What about next months in your opinion?
“2024 started at a rather slow pace. The serious international situation is obviously making itself felt. The embargo against Russia has caused a shortage of some raw materials which will take years to compensate with valuable alternatives. However I think it is an adjustment phase after the decline at the end of 2023, that should
prelude a recovery in the second half of 2024. These are cycles of slowdown and acceleration that have characterized the economy for some years”.
Has the problem of supplying raw materials completely disappeared?
“The situation has improved, also because demand has calmed down after the post-Covid rebound. International conflicts and in particular the Red Sea questions risk having serious repercussions in the coming months, increasing delays and costs of raw materials. It is also the price that Europe pays after having relocated many productions and made its economy too dependent on other continents”. l
Needles
New tools adapted to the needs of pharma and biotech sectors
Aseptconn is a leading supplier of components, products, software and systems for the pharmaceutical, biopharmaceutical and other critical industries.
Aseptconn is a leading supplier of components, products, software and systems for the liquid sterile technology as it is used primarily in the pharmaceutical, biopharmaceutical and other critical industries. The innovative products, combined with expert advice, help to improve the customers’ processes in the long term. Aseptconn’s mission is to respond quickly and efficiently to the needs of the customers. It is also committed to driving innovation in the pharmaceutical and biotech sectors by offering new tools adapted to the needs of all the partners. Some examples…
Hoses and connections for pharma, biotech, cosmetics, food, beverage and chemical industry
Aseptconn offers a wide range of hoses specially designed for the pharmaceutical, biotech, cosmetic, food, beverage and chemical industries.
The company also ensures their
pipings can be coloured according to the status or the fluid streams stored into the background. Further you can automatically generate the data for IQ and OQ in minutes. Save a lot of time and money!
Filling needles for pharmaceutical sterile aseptic machines
proper use through training in the correct assembly practices of Aseptcor® hoses and reusable Aseptlock® hygienic connections. Hose connections, also referred to as hose fittings, hose barbs or hose couplings, are specialized components utilized in various industrial applications to connect two hoses or pipelines together. Their purpose is to safely transport liquids, gases, or solids from one point to another. It is vitally important that these connections are completely sealed to prevent leaks, contaminations, and pressure losses.
The Aseptsoft add-on developed by Aseptconn was designed to increase efficiency in pharmaceutical process design many times over. Aseptsoft is a software Plugin created by Aseptconn to help the process developers to design dynamic P&ID’s. Components and
Computational Fluid Dynamics is the best tool that could predict the parameters for different physical and chemical processes. It assists the designing of the systems by eliminating the needs to build expensive prototypes and to perform complex experiments. Properly set by Aseptconn’s experts, CFD will predict the temperatures, pressures, flow velocities, concen trations, shear stress, etc. for all the system points. The under standing of the processes gained in this way can help to speed up processes development, re duce costs and make the systems more reliable. In the mixing pro cesses, the wide range of exist ing substances, different physical and chemical properties, with dif ferent tank and agitator design, leads to practically infinite possi bilities, situations and mixing re sults. Aseptconn solves and inter prets these with you.
The services: CFD SimulationsFlow Dynamics, Mixing processes, Sterilization processes; Flow cal culations and design; Pharma Pro cess design.
In specialized fields such as biotechnology, pharmaceuticals, cosmetics and food production, the reliability of every individual process step is paramount. Within this framework, filling needles play a pivotal role. They are specially designed instruments used in various industries to precisely dose liquids or semi-liquid products and fill them into containers, ampoules or other packaging. These needles are more than simple chan
Fine chemical plants
High purity products
Bulk APIs Productions
Sterile production lines (bulk, filling and lyophilizations)
Biopharmaceutical plants (fermentations, DSP, mAbs)
High Potent APIs (HP API) Productions
Utilities and clean utilities systems design
R&D and QC laboratories
BEA Technologies has increased its presence as a qualified supplier to many chemical and pharmaceutical companies pointing to a wide range of filter elements and the flexibility to develop dedicated solutions to solve some specific customer’s requirements.
BEA Technologies is an Italian company, with a worldwide network of distribution, specializing in the design and construction of filters and automatic filtration systems. Constant research in the field
ting edge solutions to clients since 1961. Design, production, distribution and after-sales services meet the ISO-9001 requirements. Pressure vessels are manufactured in accordance with ASME and certified for the European PED marking. We met
Who is BEA Technologies and what do you do?
“BEA Technologies was founded in 1961 and it is a company focused in filtration and purification of water, liquids, compressed air and gases. Throughout more than 50 years of supplying products and services to our customers we have elaborated our business model which is based on innovative product lines and solutions to solve the filtration and purification problems of our customers.
One of the most important factors that we care about is to reduce the cost of filtration on plants and equipment to create a real value and payback for our customers. Our target is to become the perfect partner counting on specific people in our team which can provide high valuable expertise and know-how in filtration and purification”.
Who are your main clients?
“We are present to offer our filtration solutions to many industrial sectors, as chemical, pharmaceutical, medical, mechanical and energy producing companies. Specifically throughout the last 20 years we have increased our presence as a qualified supplier to many chemical and pharmaceutical companies pointing to a wide range of filter elements and the flexibility to develop dedicated solutions to solve some specific customer’s requirements”.
Which are the range of products that you offer for the pharmaceutical industry?
“We are offering a wide range of filter elements incorporating different polymeric materials and membranes (Nylon, PES, PVDF, PTFE) to be installed in many types of different housings and a series of high performance Magnexflo filtration systems which are characterized by the feature to install regenerable and cleanable polymeric filter elements to reduce the cost of filtration and meet the request about more sustainable processes. In BEA Technologies lines of products are present ‘Positive charged’ Nylon 66 membrane filters specifically dedicated to the retention of endotoxins from different products and water solutions, we ha PES membrane filter elements for the sterile filtration of solutions including the filters rated to 0,1 micron able to retain mycoplasma.
We can provide a line of filter cartridges with PVDF membrane to process liquids and solutions where it is requested the minimum level of adsorption of specific substances and
stabilizers. We are implementing our range of filter capsules, including capsules for pre-filtration and final – sterile filtration, to be able to satisfy the increasing request for single-use systems for the new production processes of pharma companies. Moreover we can provide a wide range of metallic filter elements incorporating sintered fibers, sintered powder and pleated wire mesh for the processes which require resistance to aggressive solvents, high temperature, vacuum or high pressure as some applications in fermentation processes”.
What are the specific solutions you elaborated for the pharmaceutical industry?
“We have elaborated two specific solutions for the pharmaceutical industry. The first is the line of ‘Animal-Free’ filter element series that we have studied and realized to satisfy the request of a customer which has to comply with specification of production imposing to use all materials Animal-Free including the filter elements which are to become in contact with the product to be filtered.
The realization of ‘Animal-Free’ filters has required a deep research in the various component and stabilizers used in the production of polymers because some an -
imal fats are added in the composition of polymers aa ‘fluidifying agents’ to make easier the following moulding of polymers. Finally it was possible to select some polymers that were “animal-free” for the construction of BEAPURE line of Animal-Free filters. BEAPURE filter elements have proved of full satisfaction to the customer which is exporting its products worldwide”.
What are the specific solutions you elaborated for the chemical industry?
“The second product that required the study and elaboration of large surface filter elements highly regen-
Membrane filters with capsules for chemical and pharmaceutical applications
erable was the Magnexflo automatic filtration system used for the purification of chemical products, gelatines and generally viscous products and solutions. The characteristic to install highly regenerable filter elements has got Magnexflo to be listed as ‘Innovation product’. Magnexflo is a modular filtration system that can assemble different filtration stages
Roberto Bea: “One of the most important factors that we care about is to reduce the cost of filtration on plants and equipment to create a real value and payback for our customers”
in one fully mounted package controlled by PLC or DCS. Installed software is controlling the various steps of filtration and deciding when to start the regeneration cycle using the CIP unit connected”.
What kind of challenge do you have to face every day and what are the decisive factors for the success of the company?
“The cost of filtration is one of the most important factors evaluated by managers of supply chains and we claim to be able to match the challenge about cost of filtration but maintaining always a high level of
performance because we are committed to reach and maintain the full satisfaction of the customer”.
Today there is much talk of Industry 4.0 as a strategic factor; in your opinion, what are the most important aspects of the ongoing technological revolution?
“In BEA Technologies we are imple menting the digitalization and the Industry 4.0, in fact we have bought a new generation of pleating and production machines and equipment which can be digitally connected to our mainframe to transmit real time data about production rate so that we can control the production schedule and the timeframe to com plete specific operations which prod ucts are marked with a ‘bar code’ to maintain the traceability through production and stocks. Moreover we have recently installed two ‘auto matic warehouses’ one dedicated to semi-finished products ready for fi nal assembly and the other in a ware house where the finished packed fil ter elements, marked with ‘label and barcode’ are finally loaded to be ful ly traceable and linked to the trans portation documents going to cus tomers”.
How does BEA Technologies relate to sustainability, circular economy and innovation?
“Our organization and R&D team are studying the solutions that can be incorporated in the filtration prod ucts to match some of the require ments of sustainability and circular economy. Actually the Focus is on the use of materials that can be re cyclable or partially recyclable after the filtration”.
Exhibits at Achema: Hall 5.0, Booth B18
Which with the EMSuite system achieves new safety standards.by Alessandra Ferrari*
In the dynamic world of pharmaceuticals and biotechnology, the reliability and precision of a continuous monitoring system and alarm management are of crucial importance.
Ellab places itself at the forefront of this challenge with reliable and innovative monitoring solutions, guaranteeing the safety of the most critical environments and valuable products. The future of continuous monitoring is here, and it is cast with four fundamental principles in mind:
1. For the customer, the protection of their assets is crucial and must
never be compromised.
2. Alarms and corrective actions must be clear, adequate and manageable so that actions can be taken quickly and appropriately.
3. Data integrity must be absolute, without loss, alteration or vulnerability
4. The customer must always be ready for inspections and audits with a complete overview and documentation at hand.
With these fundamental principles, Ellab has developed the TrackView Pro monitoring system with EMSuite software, so that the user can take en-
vironmental monitoring of the most critical environments to a completely new and, above all, reliable level.
Uncompromised Asset Protection: protecting assets with a fail-safe system
Losing a product batch due to faulty monitoring is unacceptable. Customers’ products should be safely stored within appropriate conditions 24/7, and if these conditions are breached, the manufacturer must be informed immediately to safeguard the assets.
Ellab’s new Continuous Monitoring Solution comes with a row of failsafes, to make sure that environments, products and samples are safe, even in case of unexpected events. The system is designed to ensure continuous operation, with a dual power supply and a built-in backup memory that ensures continuous data recording even in the event of a network interruption or power failure.
• There are no gaps in your monitoring data, so you won’t miss any alarms if the thresholds are exceeded.
• Alerts are sent out to relevant team members via email, SMS, phone call and/or mobile app notification.
• Thanks to intelligent alarms and ‘action cards’, your staff receive clear
The Danish Ellab A/S Group is based also in Italy through its Ellab Italia branch, which is headquartered in Pero, near Milan. Since 1977, the latter has been providing accredited validation, monitoring and calibration solutions and services (ISO17025) and instruments for the measurement and monitoring of temperature, pressure, relative humidity and HVAC parameters. Quality, flexibility and efficiency are the distinctive features that make Ellab a benchmark firm for pharmaceutical, biotechnology, cosmetics, food and hospital companies. Ellab has always communicated with customers with the aim of providing them with a 360-degree service that helps them to successfully overcome the challenges of the various applications: sterilization, freeze-drying, environmental simulation climatic chambers, depyrogenation, warehouse mapping, pasteurization, CTU Mapping and many others. Ellab is a reliable partner to meet the complex requirements of regulated environments, verify the correctness of the documentation required by the authorities and obtain compliance with GxP regulations.
and precise operating procedures to promptly address the situation and intervene immediately to avoid any potential damage or losses.
Simplified management with innovative solutions
With TrackView Pro and EMSuite, the pharmaceutical and biotechnology industry will have a continuous monitoring solution designed for the rigorous conditions of this industry, ensuring compliance with FDA and GAMP guidelines and the process requirements of the individual company. Thanks to an intuitive user interface it is possible to constantly and reliably have under control: refrigerators and freezers; liquid nitrogen tanks (LN2); blood banks; warehouses and depots; laboratories and research facilities; clean rooms; stability chambers and incubators. Thanks to Ellab's wide range of sensors and devices, temperatures, humidity, pressure, CO2 levels and other critical parameters can be precisely monitored. Regardless of the size or complexity of the plant, Ellab offers the ideal solution
• Easily generated into reports for audits and inspections.
• Only available for chosen users.
• Safely documented through audit trails.
• Automatically and continuously logged without room for human error.
• Always ready for possible inspections.
The TrackView Pro monitoring system with EMSuite software allows the user to take monitoring of the most critical environments to a new level
to ensure process safety, guaranteeing compliance with regulations and internal requirements, the view of detailed reports and the efficient management of alarms. Furthermore, with a dedicated customer service, the customer is always supported by a group of experts ready to help him in case of questions or problems.
All your data will be reliably stored, transmitted, and received, safe from network failures, loss, alterations, or misuse. You get to stay compliant and without worry, as your data is:
• Protected and supported by 2-way communication.
• Securely encrypted.
• Completely without gaps.
Thanks to the wide range of Ellab sensors and devices, you can precisely monitor temperature, humidity, pressure, CO2 levels and other critical parameters
Ellab's continuous monitoring system allows you to always be one step ahead. With reliable data and automatic reporting, the biopharmaceutical manufacturer is ready to face inspections and audits without stress or worry. Ellab constantly invests in research and development to develop new technologies and improve product performance. Furthermore, it collaborates with organizations and academic institutions around the world to stay updated on the latest trends and developments in the environmental monitoring sector. With Ellab's comprehensive and reliable monitoring solutions, you can improve the safety and efficiency of your operations, ensuring regulatory compliance and living with peace of mind knowing that your processes are always under control. Joining Ellab in embracing the future of environmental monitoring means experiencing the difference it can make for your organization. With Ellab's continuous monitoring system, you are always one step ahead. l
At Achema Endress+Hauser will provide a comprehensive overview of measurement technology and industry solutions for the chemical and life sciences industry.
Cost savings, increased efficiency, sustainability and risk minimization – how do you overcome the major challenges facing the process industry? According to the motto "Sustainable Partner, Sustainable Success", Endress+Hauser will provide a comprehensive overview of state-of-the-art measurement technology for the chemical and life sciences industry and present practical industry solutions at ACHEMA 2024.
Plant and supply security, maintaining competitiveness when switching to new energy sources, digitalization pressure and faster product development times – the list of challenges is long.
"This makes it all the more important for the process industry to bring innovation and practice together and show how measurement technology can help to comply with the strictest safety standards while increasing efficiency and profitability," says Andreas Leppert, Industry Manager Chemical & Oil at Endress+Hauser Germany. The focus here is on supporting the optimization of CO2 emissions as well as progressive digitalization, which must also play a much greater role in plant operation.
Malfunctions in process plants can have serious consequences for the environment, people and machinery. The more complex the plant, the greater the risk of safety-relevant malfunctions. In the chemical & oil and life sciences sectors in particular, the process environment also harbors considerable risks: For example, the measurement technology used must not only withstand extreme corrosion or temperature, it must also guarantee safety in potentially explosive areas.
At ACHEMA, Endress+Hauser will be
presenting SIL-certified measuring devices and intelligent testing concepts that systematically reduce safety risks. This also includes the pioneering Heartbeat Technology diagnostic and testing concept. "Our measuring devices think for themselves, monitor themselves and help to rectify malfunctions in record time with precise instructions. In this way, we create the basis for turning data and documents into economic success by reliably and safely achieving maximum system performance," says Andreas Leppert.
At the fair, Endress+Hauser is also focusing on the topic of sustainability. As a partner to the process industry, the company helps its customers to become climate-neutral and offers the necessary measurement technology, solutions and services. The transparent recording of captured CO2, as well as the direct and indirect reduction and avoidance of CO2 through the optimization of measurement technology play a key role in this. The basis for decarbonization is dig-
italization: without valid data, many applications in the field of decarbonization cannot be used and monitored sustainably. At the trade show, Endress+Hauser will be showcasing modern solutions for the process and automation industry that will be decisive for future developments. The possibilities for digitalization with software solutions from Endress+Hauser form the basis for sustainable action.
Increase efficiency
However, digitalization not only contributes to greater sustainability, but also promotes increased efficiency. This requires intelligent, seamlessly networked measurement technology: "The networking of field devices offers great potential for improving system performance. However, 97% of field data has so far remained unused," says Andreas Leppert.
Thanks to Ethernet Advanced Physical Layer (APL), it is now possible for devices in the process industry to communicate with each other at high speed and over distances of up to 1,000 m. "We want to show on site that Ethernet APL is a key technology that closes the gap in the automation pyramid towards the field level and thus opens doors for more efficient processes," continues Leppert.
At the trade show, Endress+Hauser will also be demonstrating how existing data streams can be optimally utilized using digital twins. In addition, a variety of inline calibration services offer customers support in always keeping their systems in top condition, thus reducing the need for maintenance, and extending calibration intervals in the future.
Digital interfaces enable seamless integration of the calibration data into the production or process control system, which enables real-time monitoring and adjustment of the measuring devices. This increases efficiency, re-
duces production downtime, and improves the accuracy of measurements. "We not only want to show what is possible in the future with the help of digitalization, but also what action can be taken now to make the industry safer – and therefore more efficient and sustainable," says Dr. Markus Heiny, Industry Manager Life Sciences at Endress+Hauser Germany.
Endress+Hauser offers the complete range of services for process automation – from comprehensive field instrumentation to automation solutions and attractive life cycle management. The company will also be presenting its "My Endress+Hauser" platform at the trade show so that customers do not lose track of their prices, transactions and data and instead manage them sensibly.
The new functionalities transform the tool into an intelligent and powerful cooperation platform that connects customers directly with Endress+Hauser and its network of sales representatives. A personalized area also makes it possible to trade within minutes, buy products, order spare parts and access key contacts anywhere, anytime. l
Exhibits at Achema: Hall 11.1, Booth C27
Endress+Hauser Italy celebrates 50 years
Endress+Hauser has established itself as a major player in the Italian industrial landscape since 1974. “We can look back on five exciting decades, during which the requirements of the market have steadily changed. But one thing has not changed: we have consistently supported our customers with innovative solutions – and we will continue to be a reliable partner in the future,” says Ivano Mazzoletti, managing director of Endress+Hauser Italy and corporate sales director for Central Europe.
Endress+Hauser has maintained a presence in Italy with its own sales center since 1974, a period in which it recorded continuous growth. A key milestone was the diversification of the business and the industry-based alignment of the sales organization. The sales center has achieved notable results with products for gas analysis since 2017. In addition, the service and solutions business has enjoyed above-average growth and heavily expanded its customer training and calibration service offerings.
Ivano Mazzoletti expressed his appreciation on the occasion of the anniversary celebration to the employees, all of whom were invited to the event. “The fruits of our activities are of course our products. But it’s our employees who help bring them to maturity through their hard work and enthusiasm.”
Endress+Hauser Italy currently has around 240 employees, primarily in the food, water & wastewater and chemical industries. The headquarters is located near Milan in Cernusco sul Naviglio, with additional sales offices in Venice, Turin, Modena, Macerata and Rome. Close partnerships are also maintained with sales representatives in southern Italy, Sardinia and Sicily.
At Achema Stäubli Robotics comes prepared with a robust portfolio of pharmaceutical robots designed to address
the requirements of each GMP
clean air grade.
Achema is coming to Frankfurt am Main showcasing process solutions for chemical, pharmaceutical, and biotech research and manufacturing. As organizations prepare for automation upgrades, Stäubli Robotics, a leader in industrial automation, comes prepared with a robust portfolio of pharmaceutical robots designed to address the requirements of each GMP clean air grade.
Robots in the pharmaceutical industry must meet strict criteria beyond the requirements of most other indus-
tries. The focus is on cleanability and compatibility with decontamination media and processes as defined by GMP grades. Stäubli Robotics brings leading-edge automation solutions to each area of production with robots engineered to meet the requirements of isolators, RABs, and freeze dryers in Grade A/B areas as well as less restricted Grade C/D areas.
Achema attendees will have the opportunity to discover Stäubli’s complete pharma offering, comprised of three distinct robot ranges – the newest, accessPharma, for non-asep-
tic applications; Stericlean for aseptic applications; and Stericlean+ for use in isolators – covering the full spectrum of requirements. At Booth 3.1. J72, Stäubli will exhibit three next-level pharma robots, representing each product range: a TX2-90 accessPharma, a TX2-60 Stericlean, and a TX2-60 Stericlean+.
Grade A/B to C/D: product evolution for changing industry demands Stäubli has been a partner to the pharmaceutical industry for dec-
ades. Its groundbreaking Stericlean series, launched in 2008, was the world’s first robot designed to operate in areas with rigorous cleaning procedures. They have since been deployed in pharmaceutical and biotech labs and production facilities worldwide, where they bring new levels of efficiency to material handling, fill-finish, and many other applications.
The current era, defined by new market challenges and stricter regulations such as the revised GMP Annex 1, requires solutions that can stand up to heightened regulatory scrutiny while elevating efficiency and increasing output. Building on the long success of the acclaimed Stericlean, Stäubli worked with OEMs, system integrators, and customers in the pharmaceutical space to expand and adapt its robots to handle more applications and meet changing compliance and commercial needs. The result is Stericlean+, which debuted in 2022 with the flagship TX2-60. Stericlean+ is a breakthrough in the automation of highly aseptic processes, featuring higher cleanability, a new FDA-compliant surface coating and joint sealings, and other enhanced hygienic design features aimed at delivering unprecedented levels of product and patient safe-
ty. The entire outer surface is capable of withstanding intensive cleaning and decontamination with VHP (H2O2) in isolators.
Together, Stericlean and Stericlean+ cover all requirements in Grade A/B production areas, meeting the highest hygiene and cleanliness standards in isolators, RABs, freeze dryers, and autoclaves. They are also used in cell & gene therapy (CGT), biotherapy, API research and production, lab automation, auxiliary processes, and other areas within pharmaceuticals.
Bringing optimal automation to the Grade C environment
The newest pharma offering from Stäubli, accessPharma, focuses on the Grade C environment, coming full circle with fast, reliable automation solutions for non-aseptic areas. The accessPharma series is designed for inspection and secondary packaging applications in Grade
C/D areas, where cleaning is generally handled with isopropyl alcohol or ethanol alcoholic wipes. The robots feature a new isopropyl alcohol- and ethanol-resistant coating, as well as hygienic screws.
Automation upgrades in Grade C areas can help organizations cope with labor shortages and relieve workers of the physical demands of loading and unloading machines. They also support regulatory compliance and help ensure consistent workflow and throughput.
Stericlean+ demos and exhibits bring aseptic automation upgrades to life
Minimizing human intervention is always a major theme in pharmaceutical industry automation. The revised Annex 1 specifically emphasizes the need to reduce human intervention in aseptic processes and increase automation to lower the risk of contamination while scaling production.
Grade A/B (ISO 5): existing pharmaceutical production lines reveal key trends in automation
Final packaging Grade D/E and NCA (ISO 8)
Grade A (ISO 5) robotics in containment isolators
TX2-60
Stericlean+: for use in isolators in Grade A highly aseptic areas
TX2-90
Stericlean: Stericlean series for aseptic applications in Grade A/B areas meeting hygienic and cleanliness standards
Automation and robots have long been the norm in Grade A/B areas, where product containers remain open, and the risk of contamination is high. However, open systems that allow manual fault intervention via glove ports continue to pose risks. Annex 1 discourages the use of glove ports, accelerating the trend toward closed automated systems with gloveless isolators. In such systems, the same robots that perform process tasks can handle fault interventions with the use of
telemanipulation, thereby eliminating the risks.
In an interactive exhibit at Achema, attendees will have the opportunity to test Stäubli’s telemanipulation functionality hands-on, moving a TX2-60 Stericlean+ robot with an optional hollow wrist using a joystick rather than gloved hands – a technological advancement that promises to propel the industry forward in its evolution.
Automating the gap between fillfinish and freeze dryer
A look at the set-up of pharmaceutical production lines, particularly fill-finish machines and freeze dryers, can reveal key trends in automation. In new plants, these stations are usually arranged close to one another. This is not always the case at existing plants that require automation upgrades; therefore, automating transportation from the end of the fill-finish line to the freeze dryer is currently a major focus of automation upgrades. Traditionally, product containers are moved between filling and freeze drying stations either by conveyors or humans. But a more efficient and safer alternative is on the horizon: automated guided vehicles (AGVs) adapted to the aseptic requirements of Grade A/B environments. Serving as a link between these cells,
TX2-40 accessPharma: for inspection and secondary and packaging applications in Grade C/D areas
a mobile solution could be the key to meeting aseptic process requirements while increasing production. According to Rudolf M. Weiss, Global Head of Life Sciences & Food at Stäubli Robotics, “We continuously develop robotic solutions for all applications and cleanroom levels in the life science sector, but the spotlight will be on hygienic design mobile robots for highly demanding mobile applications in Grade A/B environments, where rigorous cleaning requirements apply.”
Stäubli’s pharma robots are already a major asset on fill-finish lines. Achema attendees can witness this for themselves at Stäubli’s freeze dryer loading/unloading demo cell, developed in partnership with Spanish company Telstar, a specialist in pharmaceutical process equipment. The demo features a stationary Grade A-compliant TX2-90 Stericlean+ robot loading trays into a “pizza door” freeze dryer and handling auxiliary tasks such as picking up clips and linking the trays to each other. l
Exhibits at Achema: Booth J72, Hall 3.1
Even after the Corona pandemic has subsided, the demand for pharmaceuticals is increasing. But the requirements are changing - and this has an impact on production equipment. Machines for packaging medicines are not exempt from this. And their manufacturers are only spurred on by this.
by Armin Scheuermann*B*Chemical
engineer and freelance trade journalistiopharmaceuticals are the real mimosas: heat, moisture, oxygen ingress or simply just the wrong light can cause the sensitive drugs, which are made from living organisms or cells, to lose their effect. This became particularly clear in the Covid pandemic: the new mRNA vaccines from Biontech-Pfizer and Moderna require sophisticated packaging and logistics concepts to ensure storage temperatures between -60 and -80°C, for example. And although manufacturers are working feverishly and also successfully on less sensitive active ingredientspackaging remains an essential element in the fight against past and future pandemics. The example of vaccines only high-
lights the importance of pharmaceutical packaging. Every second new drug approved in the EU is now produced using genetic engineering, is particularly sensitive to environmental influences and must be packaged accordingly. In addition, there are increasing regulatory requirements for production technology, such as An-
nex 1 to Good Manufacturing Practice (GMP guidelines), which was finalised in 2022: this will newly regulate the sterile production and the filling and packaging of medicinal products - with the aim of reducing contamination risks for the medicine.
Pharmaceutical market growing, machine market even stronger No wonder, then, that the market for pharmaceutical packaging machines is growing disproportionately - even more strongly than the pharmaceutical market as a whole. Market researchers from Evaluate Pharma, for example, expect the global pharmaceutical industry to grow by 6 % annually to 1.6 trillion US dollars between 2022 and 2028. In parallel, the market for pharmaceutical packaging will grow by 8.24 % and that for pharmaceutical packaging machines by 7.5 % per year - according to the expectations of the market research company Mordor Intelligence.
At the same time, the rising costs for filling, packaging and labelling medicines are being met by declining revenues for pharmaceutical manufacturers. After the vaccine boom of the Corona years, the pharmaceutical industry is not only struggling with de-
There are increasing regulatory requirements for production technology, such as Annex 1 to Good Manufacturing Practice (GMP guidelines), which was finalised in 2022
clining sales, but also with the cost explosion due to the energy crisis. On the stock exchanges, the market value of biotech companies has halved, while at the same time the prices for inputs - including chemical precursors - have risen significantly in 2022. The pharmaceutical industry has come under particular pressure here becauseas in the EU, for example - it has to sell
some of its products at a fixed price. These and other trends are now also reflected in the enquiries and specifications for packaging machines: whereas in the past, for example, filling and sealing machines with high output and lines designed specifically for one drug were demanded, today the desire for flexible lines that can be quickly - and if possible automatically - converted to new products and other packaging formats dominates. The trend towards smaller batches plays just as much a role here as easier handling. It is noticeable that the desire for flexible production processes is no longer only expressed by contract manufacturers, so-called CMOs, but also by original manufacturers.
After the vaccine boom of the Corona years, the pharmaceutical industry is not only struggling with declining sales, but also with the cost explosion due to the energy crisis
Flexible filling and packaging processes required
This development is clearly illustrated by the example of injectable preparations, the so-called injectables. Already in the years before the pandemic, machine manufacturers had registered a strongly growing demand for readyto-fill syringes. The enormous demand for vaccines in the Corona years 2020 to 2022 had recently caused a revival of bulk packaging such as vials, but in the meantime the share of “ready-touse” (RTU) syringes is rising again significantly. With RTU syringes, for example, the medicine is filled directly into a sterilised syringe. This not only reduces the risk of contamination during preparation and administration, but also avoids dosing errors. The customer’s desire to find better packaging solutions for less money is therefore driving the machine manufacturers. And one keyword runs through the description of most new developments: Flexibility. Syntegon, for example, has developed the Versynta flexible filling system as a platform with which biopharmaceuticals can be filled both in RTU syringes and in bulk pack-
aging in the isolator. To significantly reduce project times, supplier Groninger also relies on flexibility with the Flexfill concept, but combines it with standardised modules that are also housed in the isolator or RABS. Bausch+Ströbel also relies on modularisation and has radically reduced the number of format parts in the new CombiSys line. This makes it comparatively easy to convert the machine from vials to RTU packaging, for example.
New transport systems and digital technologies
Bausch+Ströbel kills two birds with one stone with a new magnetic transport system that moves the packaging material through the machine: In contrast to common drives, a fixed cycle time is no longer required, which increases flexibility. At the same time, the magnetic drive makes wipers and bellows seals unnecessary, thus eliminating a cause of contamination in the
sterile area. Optima has also addressed the transport of packaging materials in the machine: With the new FillCell formatless transport system, the main aim is to increase product yield. Especially with expensive active ingredients, it is important to avoid losses during machine start-up.
Machine manufacturers are taking this requirement into account with new dosing and filling systems, but also optimised transport, monitoring and labelling solutions. Digital technologies are playing an increasingly important role here: this begins with training operators with virtual reality goggles on digitised equipment, extends to the seamless recording of production parameters in the production process, and ends with the evaluation and visualisation of key figures such as Overall Equipment Effectiveness (OEE), which are becoming more and more important in the growing competition of the pharmaceutical industry.
The Körber Group, for example, has dedicated itself to this topic, using its Manufacturing Execution System (MES) to analyse the operational efficiency of biopharmaceutical manufacturing processes on the basis of different and previously unnetworked data. Among other things, this should enable biopharmaceutical manufacturers to significantly accelerate their timeto-market. Uhlmann Pac-Systeme networks machines and entire plants of any manufacturer via interfaces with a
new software (Pexcite), thus enabling centralised monitoring and control. In addition to looking at line efficiency and planning set-up times, this also makes it easier to comply with regulatory obligations.
Robots in glove-free isolator, scalable parenterals production
The automation strategy of many manufacturers now includes the use of robots - not only at the end of the line, for example to stack packaged medicines on pallets, but already in the sterile isolator. Machine developers are benefiting from the fact that, on the one hand, the range of cleanroom-suitable robots is steadily growing, while at the same time the costs for robotics are continually falling. In this way, automated solutions are increasingly replacing the otherwise necessary gloved interventions on the isolator. This is because in the demanding sterile production of high-quality medicines, human intervention is increasingly being perceived as a nuisance and is being replaced by technical solutions.
At the machine manufacturer IMA, the gloveless aseptic process in the isolator is being promoted under the name “Injecta”. But the machine manufacturers already mentioned are also pursuing the trend towards aseptic filling without human intervention with their own solutions. The development is consistently implementing the requirements of the new GMP Annex 1. In many places,
this also includes dispensing with the time-consuming sterilisation of the primary packaging material by using sterile packaging materials.
In general, the packaging of sterile preparations for injection and infusion (parenterals) is very demanding, and the machine technology is expensive. This becomes a problem especially when the success of a drug and its required quantity are not yet known. The folding box manufacturer Faller Packaging has developed a scalable solution to this problem together with the machine manufacturer Schubert-Pharma: This starts with the initially manual loading of pre-prepared folding box packaging. As soon as demand increases, cobots are used until the process is finally switched to a fully automatic top-loading machine.
Sustainability becomes important But it is not only the development of the processes around the primary packaging of medicines that follows the new requirements of the pharmacists. Developments in secondary packaging in folding boxes, trays and cartons are not standing still either. In addition to flexibility and product safety, important trends here are resource optimisation and low CO2 emissions. This is because the topic of sustainability is also increasingly finding its way into companies in the pharmaceutical industry via CSR and ESG criteria.
In order to improve the recyclability
The automation strategy of many manufacturers now includes the use of robots - not only at the end of the line, for example to stack packaged medicines on pallets, but already in the sterile isolator
of packaging, Uhlmann, for example, is increasingly relying on packaging made of monomaterial. With the Parenteral Tray Center, the manufacturer has recently also introduced a flexible “direct-in-carton” solution that can pack ampoules, vials and syringes both in cardboard trays made of monomaterial and in conventional plastic clamp blisters. Recyclable packaging places new demands on machine manufacturers. Close coordination between machine and packaging supplier is therefore important. At Faller Packaging, for example, the approach is called 3R: Redesign, Reduce, Recycle: in addition to the use of new recyclable mono-materials, this also includes testing existing products and processes with the aim of minimising the use of raw materials and energy.
But labelling technology is also evolving. While in the past decade this was mainly characterised by the fight against counterfeit medicines, other requirements are now coming to the fore with regard to biopharmaceuticals. One trend here is the development of new labelling solutions with sensor functions. The so-called “smart labels” use printable indicators that can be used to monitor the correct storage of a medicine or the correct application temperature. If the heat or UV light exposure of the medicine exceeds a defined value, the indicator on the packaging changes colour. Another piece of the mosaic to be able to safely control biopharmaceutical mimosas in everyday life. l
(text courtesy of Achema Press Office)
RIVISTA DELL’
MANAGING DIRECTOR: Simone Ghioldi
EDITORIAL BOARD: Alessandro Bignami (a.bignami@interprogettied.com), Eva De Vecchis (e.devecchis@interprogettied.com)
GRAPHIC LAYOUT: Studio Grafico Page Vincenzo De Rosa, Rossella Rossi - www.studiopage.it
COLLABORATORS: Alessandra Ferrari, Marzia Savino, Armin Scheuermann
TRANSLATIONS: Elena Marzorati
INTERPROGETTI EDITORI S.R.L. via Roggia Borromea, 16 - 22060 Carugo (CO) Editorial, sales and subscription offices Tel./fax +39 031 3665163 www.interprogettied.com
SALES DIRECTOR: Marika Poltresi
SALES: Simone Ghioldi (vendite@interprogettied.com)
ADMINISTRATION: amministrazione@interprogettied.com
SALES OFFICE: Raffaella Sepe (raffaella@interprogettied.com)
© Copyright Interprogetti Editori Srl
The columns and news are realised by the editorial team. All rights reserved – All reproduction, even partial, of published material without the publisher’s consent is strictly prohibited.
SUBSCRIPTION RATES:
Italy: ordinary mail delivery EUR 45.00, COD delivery EUR 48.00
International: ordinary mail delivery EUR 60.00, express delivery within Europe EUR 70.00 Express delivery to Africa, America, Asia: EUR 85.00
Express delivery to Oceania: EUR 100.00
Single copy: EUR 10.00
The VAT on subscription prices as well as on the price of single copies is paid by the publisher pursuant to article 74, sub-section 1, point C of the Italian DPR n. 633 of 26th Oct 1972 and subsequent amendments and additions. It is therefore not possible to issue invoices.
Registered at the Court of Milan on 7 May 2010 no. 259
Managing Director: Simone Ghioldi
Printed on May 28th, 2024 at Litogi, Milano
Information to be given to the data subject - art. 13, legislative decree 30th June 2003, no. 196. Personal data are processed, with or without the help of electronic means, by Interprogetti Editori S.r.l. - vis Maggiolino, 34 F - 23849 Rogeno (LC), Italy, to send you the magazine requested and for the operations connected. The processing of data will be carried out by the persons who have been committed by the controller the task of performing the processing operations connected with recording, modification, processing of personal data and printing, fulfilment and delivery of magazines, commercial and fiscal issues, accounting and call center activity. With reference to art. 7, Italian legislative decree 196/2003, you have the right to access to your data, modify, update or cancel data or to object to their processing for direct marketing purposes, by writing to the controller, and ask for the list of data processors.
Publisher’s information to public – art. 13, legislative decree 30th June 2003, no. 196. With reference to Italian Personal Data Protection Code and art. 2, point 2 of Code of Conduct for the processing of personal data in the exercise of journalistic activities, Interprogetti Editori S.r.l. informs that the place where personal data, images and photos are kept is Rogeno (Italy). Data can be used by journalists, free-lance journalists, persons in the role of trainee journalists and persons who carry out processing for the publication or occasional circulation of essays, articles and other intellectual works for the purpose of the exercise of their journalistic or similar activities. The processing of data will be carried out by the persons mentioned above and by persons in charge of printing and publishing activities. With reference to art. 7, Italian legislative decree 196/2003, you have the right of access to your data, modify, update or cancel data or to object to their, by writing to Interprogetti Srl, and ask for the list of data processors. It is understood that the provisions concerning professional secrecy in the journalistic profession shall be left unprejudiced as related to the source of the information if a data subject requests to be informed of the source of the personal data processed by journalists.