
9 minute read
Ilmac 2023 inspires the future of chemistry and life sciences
Around 400 leading suppliers in the industry will come together in Basel to present their solutions, innovations and new products to the around 10,000 expected trade visitors from Switzerland, Austria and Germany.
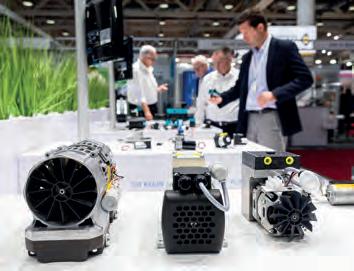
Advertisement
Ilmac is bringing the chemical and life science industries together once again at the key location of Basel from 26-28 September 2023. Trade visitors from Switzerland, Austria and Germany can expect to touch base with reputable companies from over 20 countries. At this year’s event, the most important industry meeting place will present promising new live formats and enhanced digital offerings.
This autumn, leading suppliers in the industry, such as Agilent, Endress+Hauser, Integra, Mettler Toledo, Metrohm, Siemens and Skan, as well as innovative start-ups, will come together at Ilmac in Basel to present their solutions, innovations and new products to the around 10,000 expected trade visitors from Switzerland, Austria and Germany. The organizers expect around 400 exhibitors to attend. New additions such as the Startup Area, the “Lab of the Future”, the “Job Connect” area and the Speakers’ Corner will complement well-established formats such as the Ilmac Conference and Pharma Logistics Days, which are taking place in parallel for the third time, making Ilmac a highly efficient knowledge and networking platform for the chemical and life science industry. “Basel is a world-leading hub for the life sciences. Our aim is to actively contribute to the growth and advancement of the location by offering the industrial sector the Ilmac platform, which will generate the necessary inspiration to improve and continuously innovate the healthcare ecosystem,” says Roman Imgrüth, CEO of MCH Exhibition & Events.

Ilmac Conference – the latest research and business insights
The program of the scientifically driven “Ilmac Conference” will help prepare participants for the future. The three-day congress facilitates efficient knowledge sharing, covers a wide variety of topics and boasts top-class speakers.
This year’s focus lies on important industry topics such as “Lab Digitisation”, “Chemical Technologies” and “New Biotech Methods”. The “Ilmac Conference” is organised in cooperation with the Swiss Chemical Society, the Swiss Biotech Association and the Swiss Association of Graduate Chemists FH (SVC). “As a partner of Ilmac, SCS has been accompanying and supporting the event for over 60 years. The city of Basel, a key location for laboratory-based research in Switzerland, offers the ideal conditions for a successful trade fair,” says David Spichiger, Executive Director of the Swiss Chemical Society.
Smart and sustainable: the laboratory of the future
Laboratory facilities are in a phase of transformation. In light of increasing digitisation, various processes and structures of the future laboratory will be subject to comprehensive re-examination. The Lab of the Future allows Il- mac participants to interactively experience a future laboratory, using augmented and virtual reality. “As a partner of Ilmac, we’re letting this year’s participants delve into the laboratory of the future. Inspired by the collaboration in the Basel Life Science Cluster, we’re showing the benefits, technological advances and sustainability of a digital, integrated laboratory,” says Dr Sadiya Raja, Arcondis. Laboratory buildings consume up to 10 times more energy than other buildings. Green Lab, a cluster run by the Green Building Schweiz association, initiates and moderates the collaboration between all participants and supports the dissemination of technical innovations as well as the use of new or little-known business models for Green Labs which are safe, sustainable and competitive. The Green Lab Symposium is the only laboratory symposium in Switzerland. It hosts workshops that let participants exchange best-practice examples, bring together experts from a wide variety of disciplines and help search for solutions in individual projects.
The pulse of pharmaceutical logistics
The chemical and life science industry has very high and very specific demands when it comes to the transport of goods. At the Pharma Logistics Days in Hall 2.0, companies can find trends, innovations and the right partners for their transport challenges. Over the course of two days, around 40 of the leading logistics service providers will present new solutions and innovative services.

Solvay to produce green hydrogen for its Peroxides activity in Rosignano
Ilham Kadri, CEO of Solvay
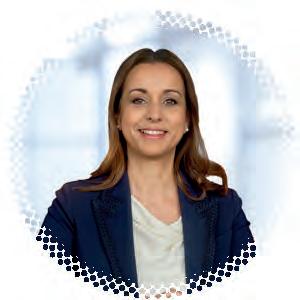
Solvay and Sapio are partnering in the joint development of the Hydrogen Valley Rosignano Project, a largescale hydrogen production plant with locally-sourced green energy in Rosignano, Italy. Led by two technology leaders in the hydrogen economy, this project will further enable the decarbonisation of Solvay’s activities in Rosignano, leading to a
15% reduction of CO2 emissions for Peroxides related operations. The green hydrogen production plant will be built by mid-2026 on a former industrial area within Solvay’s Rosignano facility and will be powered by green electricity through the construction of a dedicated 9.5 MW photovoltaic installation.
It will have a capacity of 756 tons of green hydrogen per year, which will be used for the production of peroxides on site.
“We are very proud of this project at our Rosignano facility. Hydrogen is a key enabler for a modern, resource-efficient and competitive economy, and we are proud to be one of the first players to take on this opportunity. It will help us reach our important ambition towards carbon neutrality before 2050,” said Ilham Kadri, CEO of Solvay. “This project is the first example of green hydrogen peroxide production at such a scale in Europe. Moreover, this investment will be an important stimulus to the local and regional economy.”
Forerunner and innovator for the national circular economy for 60 years
Itelyum, a group specialised in the management, recycling and valorisation of industrial waste, controlled by Stirling Square and owned by DBAG, celebrated 60 years in business and results as a sustainability game changer.
“Six decades of activity as an absolute forerunner of the times, always at the forefront of the circular economy and sustainable development,” said Itelyum CEO Marco Codognola. “Every year Itelyum takes a step forward on the road to decarbonisation, also thanks to the range of regenerated products that allow significant savings in CO2 emissions. And also: one million eight hundred thousand tonnes of special waste per year treated, achieving circularity indices close to 85%, through the regeneration of exhausted oils, the purification of solvents and the all-round management of special waste, both hazardous and not, also growing in the port sector and in water treatment”.
This morning at Villa Necchi Campiglio, in Milan, after the speeches by Deputy Minister Vannia Gava and Lombardy Region Environment Councillor Giorgio Maione, the years that have built a company history characterised by a pioneering and visionary spirit were retraced: from the beginnings at Viscolube onwards, it has always looked ahead, with the ability to produce change in regenerative processes.
“We have consolidated a business based,” says Itelyum President Antonio Lazzarinetti, “on offering sustainable solutions that generate economic, social and environmental value for our people, our customers and the territories in which we operate. Our story began in 1963 in via Tavernelle in Pieve Fissiraga with 50 employees and today continues with Itelyum present throughout the country, gen- erating 600 million in revenues, through 32 operating sites, 1,300 people and highly specialised technology, unique in Italy”.
Today, the Itelyum Group brings with it, through its Research and Development activities, a further step towards the evolution of material processing as a response to non-renewable sources and the protection of the natural heritage.
Projects that herald an epochal change in the sector:
1) Rare earths. A multifunctional pilot plant for the recovery of WEEE of various types is in operation.
2) Silver recovery from photovoltaic panels. If the efficiency of the panels is greater than 20%, they are regenerated and sent for reuse, while the fraction of panels that does not pass this test is sent for recycling. In the latter case, they are disassembled for aluminium recovery and through a state-of-the-art process the crushed residual fraction is obtained, which is rich in silicon and silver.
3) Plasbreaker: lubricating bases from mixed waste plastics (plasmix). The aim of Plasbreaker is to convert plasmix into value-added products such as lubricants and hydrogen. This treatment also involves the use of used oil that cannot be regenerated and therefore cannot otherwise be recycled, with a consequent additional environmental benefit.
4) Biolubricants from used vegetable oils and the vegetable fraction of used mineral oil. The aim of this project, called BIOLUBE Itelyum, is an innovative process that is able to obtain biolubricants from waste materials such as used vegetable oils (UCO) and the soaps contained in bitumen residues from the regeneration of used mineral oils.
Bormioli Pharma reaffirms its commitment to environmental and social sustainability
Pharma, a leading international manufacturer of pharmaceutical packaging and medical devices, presented the second edition of its Sustainability Report. This edition aims to reaffirm and consolidate the company’s commitment to environmental and social responsibility, protecting the wellbeing of people and the environment, in line with its mission to “Make health a positive practice, accessible to everyone, kind to the planet’”.
Of the main targets, the 30% CO2 reduction by 2030 (compared to the 2021 baseline) has been confirmed, and new ones have been introduced, such as the commitment to carry out an initial LCA analysis on a glass product by the end of this year and to complete the assessment of “Scope 3” emissions - i.e. those related to but not directly attributable to the Group’s business, such as those arising from employee mobility, supply chain operations and the use of manufactured goods - by 2025. The “50in5” target of increasing the share of sustainable raw materials in production processes has also been confirmed: this is a goal that the company has already come a long way towards, reaching 39% in 2022, versus a target of 50% by 2025. The goal of reducing water consumption, to be achieved by 2030, has been made more challenging and raised from -30% to -41% compared to the consumption recorded in 2021, demonstrating how the company has already embarked on a virtuous path and wants to commit itself further in this direction. This revision is in fact supported by already achieving a 35% reduction in 2022.
“From the war in Ukraine to rising energy prices, 2022 was a year marked by a series of huge geopolitical and macroeconomic events. Despite this, Bormioli
Pharma has always guaranteed production continuity, confirming its solid position as a partner of excellence for the international pharmaceutical industry”, commented Andrea Lodetti, CEO of Bormioli Pharma.
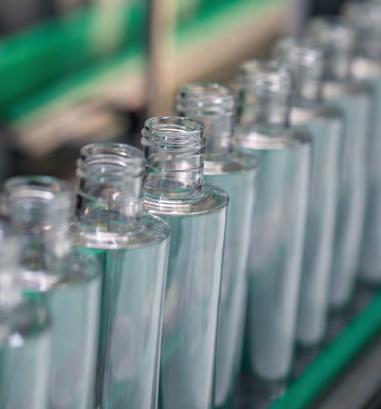
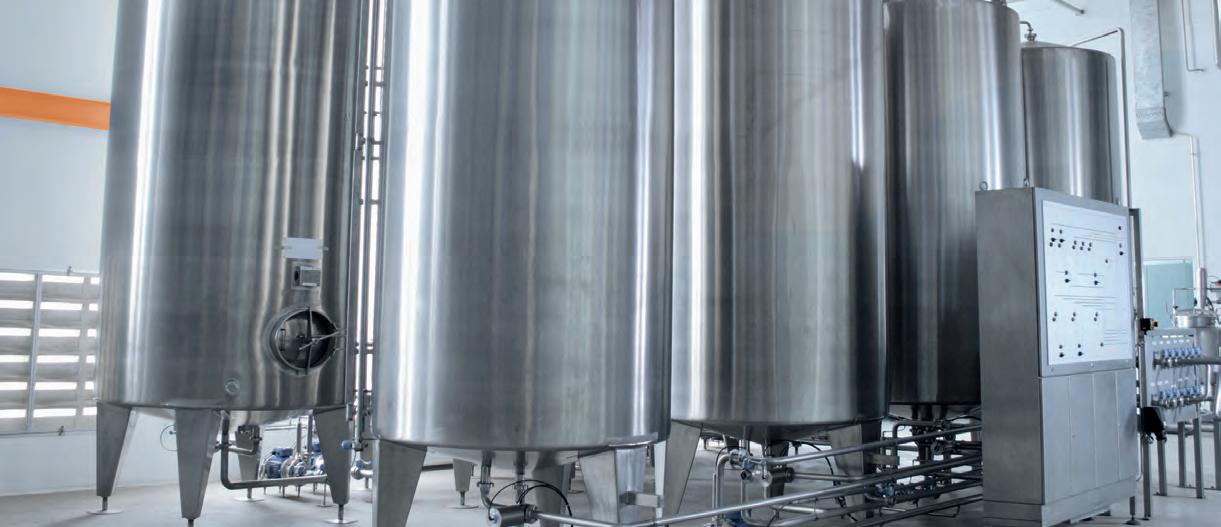
Continuous Process Monitoring of TOC
This Compact Version is ideal for installations in common mounting spaces on water puri cation or distribution skids. Clearly arranged components and menu-based operation via transmitter makes the analyzer fast and straightforward to handle. Removable stainless steel cover available.
Swan Analytical Instruments ∙ CH-8340 Hinwil www.swaninstruments.ch · swan@swan.ch
Robotic solution to process small batches of single-dose PFSs for veterinary vaccines
Steriline delivered to FATRO an extremely compact robotic filling machine, to produce small batches of veterinary vaccines in single-dose pre-filled syringes.
Steriline, an Italian manufacturer of robotic and standard fill/ finish lines for the aseptic processing of injectable drugs, delivered to FATRO an extremely compact robotic filling machine, to produce small batches of veterinary vaccines in single-dose pre-filled syringes (PFSs).
FATRO, founded in 1947 by the pharmacist and veterinarian Gualtiero Zaini and his son Corrado Zaini (a chemist), develops and produces medicines and vaccines for animals. Today, it is a flagship of the Italian Veterinary Pharmaceutical Industry, exporting its products to more than 90 countries according to an internation- al expansion plan that adapts the strategies to the different local realities. In order to enter into the veterinary segment market that requires single-dose formats, FATRO decided to introduce into its fleet of machines a lean solution, equipped with only a few components, that processes small batches of single-dose PFSs. The machine was supposed to occupy as little space as possible, to reduce the management costs of the grade B area the equipment would have to be housed in.
Steriline proposed an extremely compact and flexible filling solution: a Robotic Nest Filling Machine (RNFM2) designed to manage 0.5 ml PFSs with a production capacity of up to 2,900 pieces/ hour.
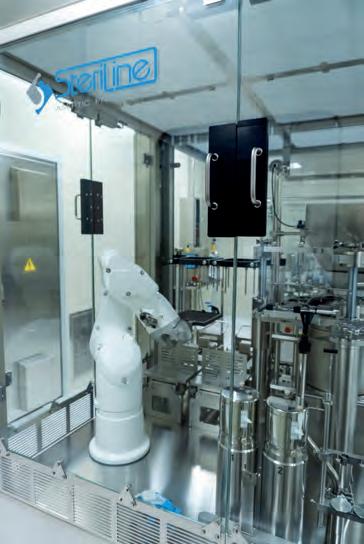
With two manual loading and unloading stations, where an operator inserts tubs previously peeled under a Laminar Air Flow, the stand-alone solution is equipped with a robotic arm that picks up the nest in the tub containing the empty PFSs and positions it under the two filling heads connected to peristaltic pumps. Simultaneously to the filling process, two stoppering heads seal the filled PFSs. Once both processes are completed, the robotic arm repositions the nest in the tub at the exit station, ready for the operator to withdraw and transfer to the secondary packaging process. The whole process therefore requires a very small action area, which translates into the very limited machine footprint (1.250 m x 1.250 m) under the open Restricted Access Barrier System (oRABS).
“We are very happy to have acquired this machine from a company we have been partners with for a decade. Thanks to the Robotic Nest Filling Machine, we can now satisfy market demands and be closer to our customers’ needs,” says Dr Francesco Meliota, FATRO Vice President.
The whole project, from the order to the product set-up, took one year. The Factory Acceptance Test (FAT) was completed in September 2022 without requiring any customer service intervention.
Filippo Parini, Area Sales Manager at Steriline, states: “I am happy that FATRO chose Steriline expertise and competences despite the many competitors in the Bologna area. Fatro was really satisfied with Steriline capabilities and technologies and invited us to propose our solutions for other applications. I am convinced that this is the beginning of an even stronger partnership.”
Complete lines for the aseptic processing of injectable products
Steriline is a well-established European manufacturer, highly specialised in the production of complete lines for the aseptic processing of injectable products, supplying pharmaceutical companies worldwide.
Steriline was founded in 1989 in the Lake Como area (Italy), where its headquarters and manufacturing facilities are still based. With operations in over 50 countries around the world, Steriline has a network of over 220 people, including direct employees and external partners, in addition to 40 local sales representatives. Exports represent more than 90% of Steriline’s turnover, with over 1,800 machines installed throughout Asia, Europe and the U.S.A.
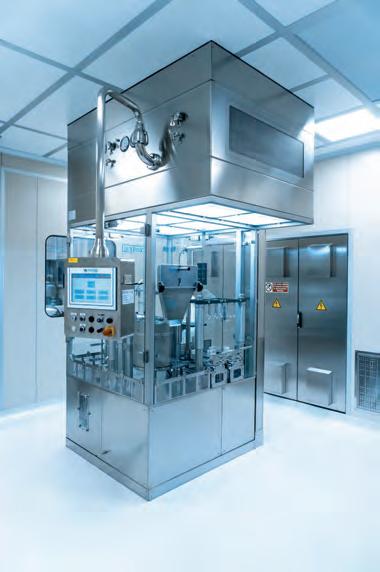
