
5 minute read
An intelligent and integrated ecosystem with technological innovations
Life science: traceability, quality control, and data management, from the product to the supply chain
Diamind Line is a suite that manages inspection systems and machines for packaging and production lines to control the quality of products, packaging, containers, and labelling, and track and trace machines and systems for digital identity management through serialization and aggregation on production lines.
Advertisement
• Traceability: Advanced solutions for serialization and aggregation (of bottles and cartons)
• Traceability, quality control, and product authentication: A “digital fingerprint” solution born from the partnership with Edgyn, integrated with traceability and weight control
• Blister quality control: A combination of laser technology and traditional vision systems; performs three-dimen- sional inspection, powered with Artificial Intelligence
• Stick pack quality control
• Weight control: A checkweigher for small, medium, and large cartons, a first for Antares Vision Group in the Life Science business area
• Automatic visual inspection & high voltage leak detection
• Automatic visual inspection for liquids in glass vials
• Automatic visual inspection for prefilled syringes (conference)
• Automatic visual inspection for blowfill-seal (BFS) cards (conference).
Diamind Factory is a software suite that manages the entire production site.
• Monitoring and optimizing processes
• Production efficiency and quality improvement
• Optimizing planning and factory maintenance
• Enabling sustainability
• Line clearance: Digitization of line clearance procedures, enhanced with Artificial Intelligence.
Diamind Enterprise and Diamind Supply Chain: Respectively, these are software suites that address regulatory compliance management at the enterprise level, including track and trace management of serialized and non-serialized products and assets, and end-toend supply chain visibility and management, from raw materials through trading partners to the end user.
• Quality: Collecting of inspection and quality control data
• Efficiency: Data analysis to improve production processes
• Sustainability: Collecting of data relating to the environmental impact at all stages of supply chain
• Regulatory compliance: Ongoing compliance with current and emerging regulations
• Visibility: A global view of the entire product lifecycle, from raw materials to the patient.
Food & beverage: product quality and consumer safety with the best inspection technologies
Antares Vision Group provides solutions products and packaging and consum er safety.
Diamind Line:
• Detection of foreign bodies in pack aged foods and beverages with mi crowave technology: A new techno logical application that revolutioniz es inspection for quality control by overcoming the limitations of current technologies (e.g., X-rays and metal detectors)
• IR spectroscopy for leak checks (food industry): On the line, checks 100% of production for the presence of mi cro-holes in packaging and seals
• Check for the presence of micro-holes, foreign bodies, weight control, seals, and labels: A standalone machine combining several inspections to en sure product quality and safety
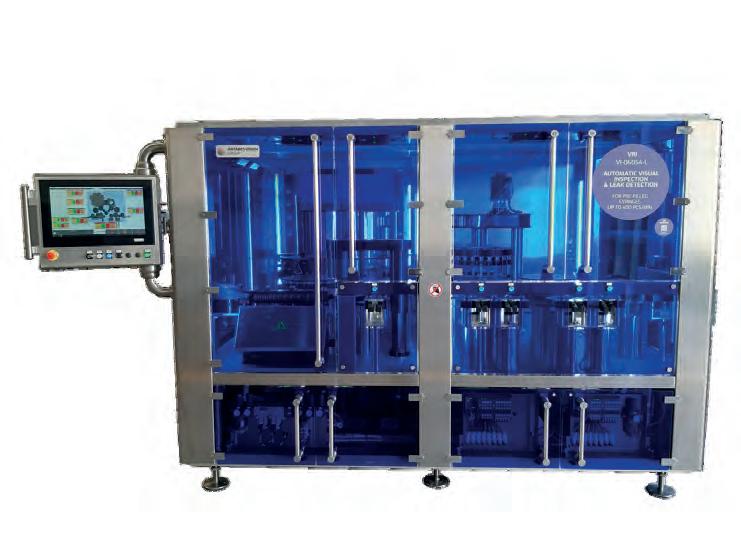
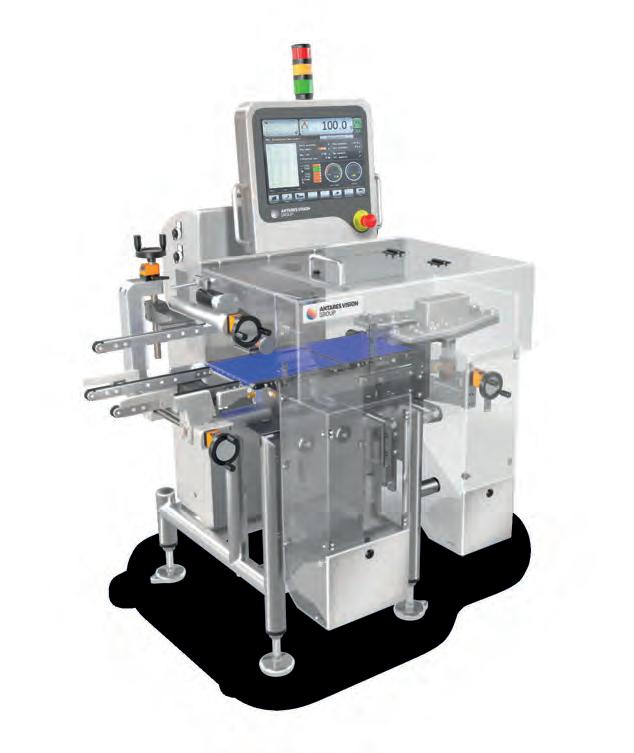
• Inspection of tethered caps.
Diamind Factory:
• Monitoring and optimizing processes
• Production efficiency and quality improvement
• Optimizing planning and factory maintenance
• Enabling sustainability.
Diamind Enterprise and Diamind Supply Chain
Sustainability: Collecting of data re lating to the environmental impact at all stages of supply chain
• Regulatory compliance: Ongoing compliance with current and emerging regulations
• Visibility: A global view of the entire product lifecycle, from raw materials to the final consumer.
Cosmetics: unique digital identities for traceability to fight parallel markets and counterfeits and to foster customer engagement
Antares Vision Group offers the cosmetics industry complete hardware and software solutions designed to ensure the quality and integrity of products from production to market, to help fight counterfeits and deter parallel markets, and to protect consumers.
• End-to-end traceability of products: Advanced solutions for serialization and aggregation
• Creation of a unique digital identity for each product: In line with the Digital Product Passport proposed by the European Commission
• Digitization of the supply chain
• Customer engagement. l
Components
The specialized know-how gained over the years of experience in solid handling, together with the innovative spirit, allows CO.RA. to provide its experience far beyond the supply of a simple plant.
During almost 40 years of experience in terms of pharmaceutical, chemical and cosmetics processes, the attention of CO.RA. to taking care of the details of each component or plant considers as a strong point the presence of technical support and specific consultancy for its customers, of which CO.RA. can boast.
The company takes care of the production process by listening to customer needs, the heart of the development of an effective technical solution, the goal is to contribute to the achievement of your production objectives, for this reason CO.RA. is interested in knowing the characteristics of customer products, carrying out the tests to verify the behavior of the product in contact with CO.RA. machines and customize them to such an extent as to make them perfectly suited to production needs.
On each systems designed and manufacturer inside the production site, it’s possible to use all kind of CO.RA. valves thanks to the versatilities of the range of products.
An example of an integrated System is the Drum Dosing System that can be divided in two categories: Continuous Liner Discharging System and Inflatable / Deflatable ring Dosing System. The operating cycle of the sys- tem is divided into two distinct phases: gross dosing and small dosing. During the first phase the butterfly opens to allow the quick discharge of 95% of the product to be dosed until the heavy weight limit is reached.

The Continuous Liner Discharging System allows the operator to create a polyethylene continuous liner bag inside a container for the continuous discharging of a product. The product is discharged into the polyethylene liner bag and once the necessary weight is reached, the system allows the operator to cut and pack the bags in a closed cycle.
An empty container is placed on the base of the scale, the liner is pulled until it touches the bottom of the container and the end is closed by means of a clip in order to form the “bag bottom”. At this point it is necessary to push the start button on the dosing terminal, and once the product has been discharged, a clip is placed to close the bag and another clip 10 cm above that one in order to create the necessary space to cut the bag. Finally, it is necessary to remove the container from the base and repeat the cycle described above.
The Inflatable / Deflatable ring Dosing System allows the operator to lock the bag (already placed inside the container) and to perform the unloading of the product as long as the weight is not reached. Once the weight is reached the operator by the control panel unlocks the bag and the operator can proceed to close it. The working cycle of this system is similar to the Continuous Liner Discharging System, but the closing of the bag is done manually by the operator once it has finished unloading. On this type of system, a dust suction system can be installed which further reduces operator contact with the product.
The terminal of CO.RA. systems are provided with a high tech digital devices on which possible also customize software to control process in relation to customer’s process needs. Inside Control panel, CO.RA. usually supplies in default a module for a remote assistance thanks to which is possible connect the system installed on customer site, directly to the software engineer, in order to have assistance.
Linked to the supply CO.RA. also offers a 360° support which consists of a wide range of services such as:
• Analysis and Verification of P&ID and Customer Technical Specifications;
• Meeting and technical inspections to define the project;
• Design and proposal of a Customized Technical Solution;
• Drafting of Specifications and Documents necessary for the realization of the project;
• Carrying out of Checks and Tests at CO.RA. Technology Center with customer products;
• Project validation (DQ), FAT at CO.RA. or in Smart Services;
• Installation and SAT at the customer’s site;
• IQ, OQ and PQ validation tests, Use and Maintenance Manuals complete with certifications;
• Process and systems engineering;
• Possibility of issuing GAMP5 (title CFR 21 part 11);
• Technical Training for staff training on site or in SMART mode;
• Modification of modification requirements;
• Technical support for drafting SOP;
• Technical assistance on site or in SMART mode;
• Scheduled maintenance;
• Revamping of CO.RA. products;
• Management of complaints and reports of anomalies.