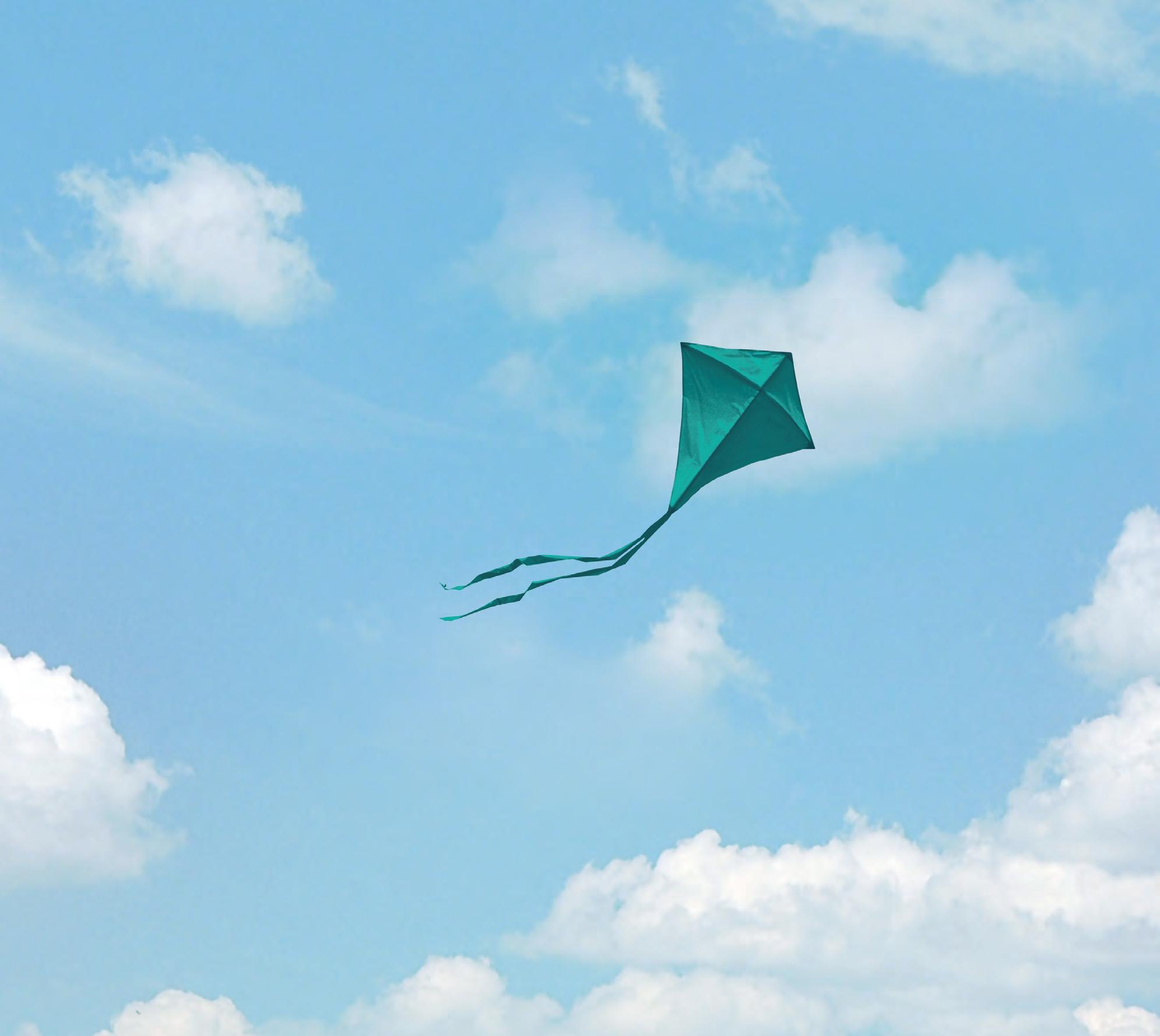
3 minute read
ITELYUM: il nome dell’economia circolare.
Tecnologia, esperienza e innovazione per la rigenerazione degli oli lubrificanti, la purificazione dei solventi e i servizi ambientali per l’industria.
29 siti operativi e più di 1.200 persone: soluzioni sostenibili per circa 35.000 clienti in più di 60 Paesi nel mondo.
Advertisement
The focus on a value contribution to solving the climate problem and sustainable management is also important for plant engineering for another reason: attracting talent through employer branding (Photo © shutterstock Gorodenkoff, by Achema Press Office)
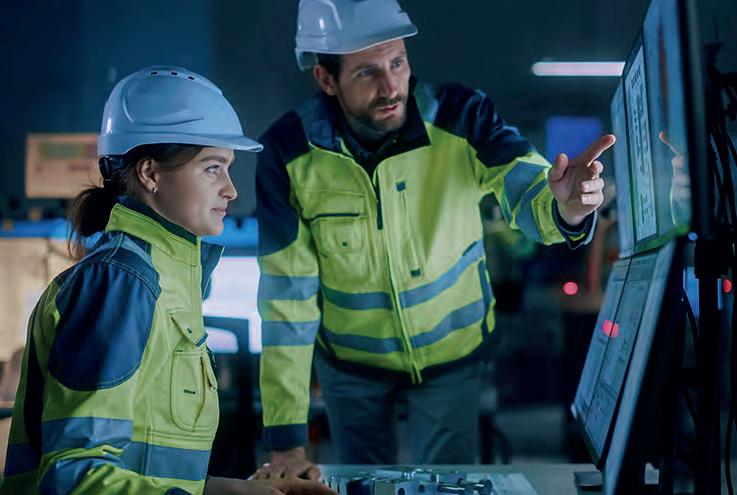
Mammoth task of decarbonisation changes chemical plant engineering
However, it is clear that the mammoth task of decarbonisation is also changing chemical plant construction itself. In recent years, the flood of projects and rising prices have already led to a paradigm shift in contract design. While clients were able to commit their contractors to fixed-price contracts a few years ago, the wind has now shifted in favour of EPC providers: chemical plant builder Worley, for example, reports that the share of fixedprice contracts (lump sum turn key) in turnover has fallen to 1%. The company now bills 80% of its contracts on a reimbursable basis.
In the future market of hydrogen, manufacturers of electrolysis plants are planning to massively expand their capacities. The chemical plant construction sector will be investing massively in its own technology and corporate development in the coming years.

And because investors are increasingly attaching importance to sustainable business models, companies in the chemical plant engineering sector must themselves operate according to ESG criteria. This is why almost every annual report in the industry recently contains a reference to progress in the areas of environmental, social and responsible corporate governance. The focus on a value contribution to solving the climate problem and sustainable management is also important for plant engineering for another reason: attracting talent through employer branding. After all, one of the biggest challenges currently facing the industry is the lack of qualified specialists.
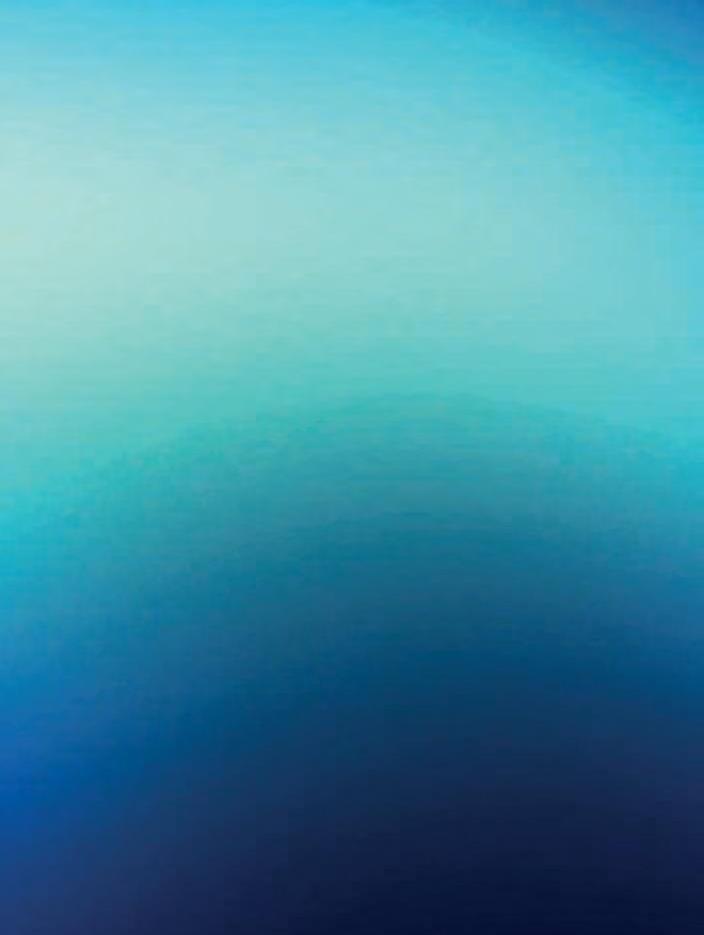
Automation of the engineering processes and the construction site
Because not only personnel but also other resources important for chem ical plant construction will remain scarce in the coming years, the in dustry is focusing on increasing pro ductivity: digitalisation and auto mation of engineering processes and artificial intelligence are just some of the levers with which the industry is tackling the issue. Conclusion: with its solutions ex pertise, the global chemical plant engineering industry is an impor tant enabler for the decarbonisation of chemistry and the energy trans formation of the economy. The industry is tackling the chal lenge of scarce human and engi neering resources through digital isation and investment in its own business.
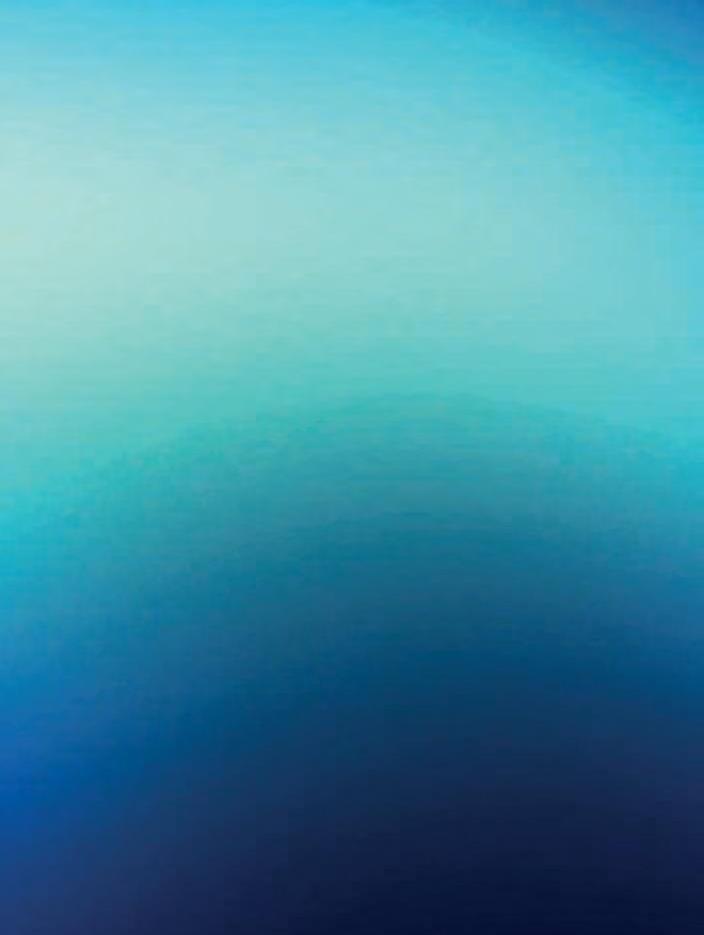
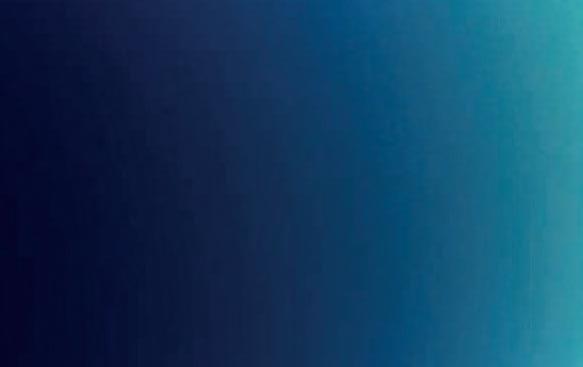
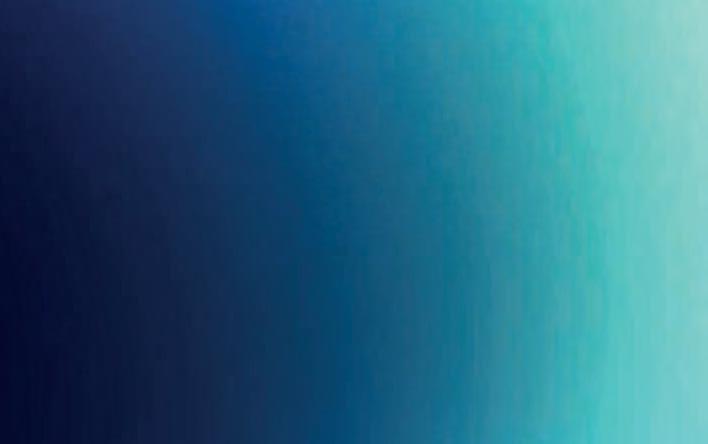

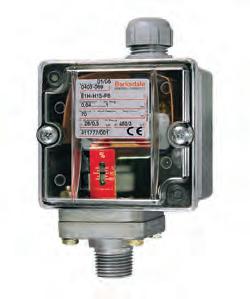
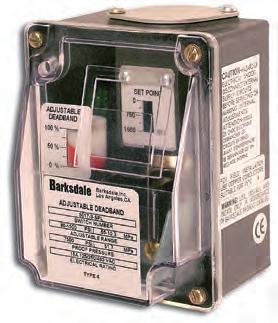
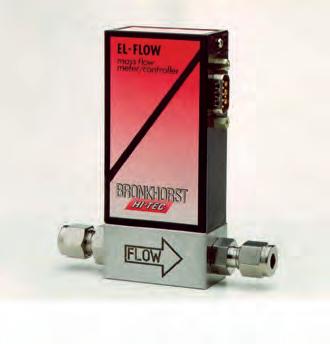
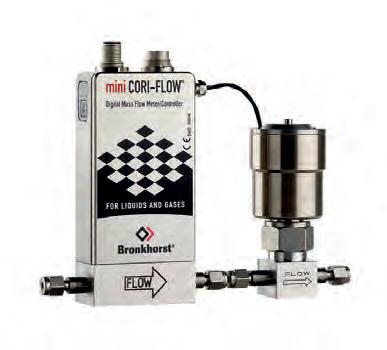
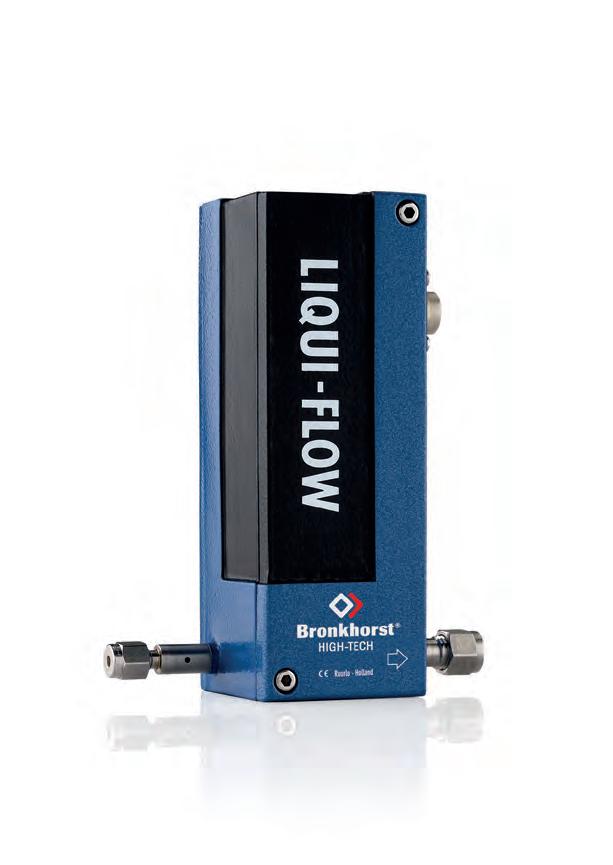
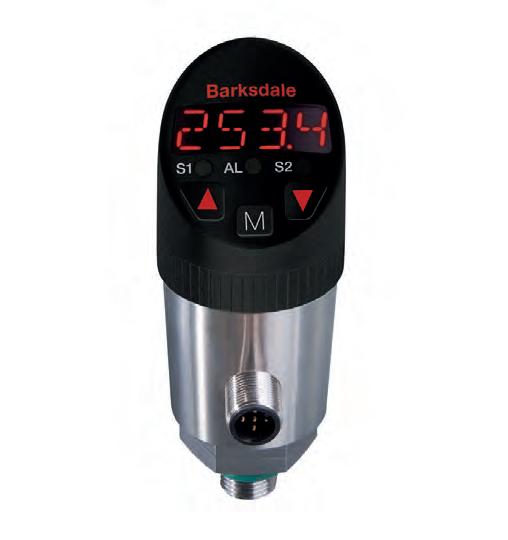
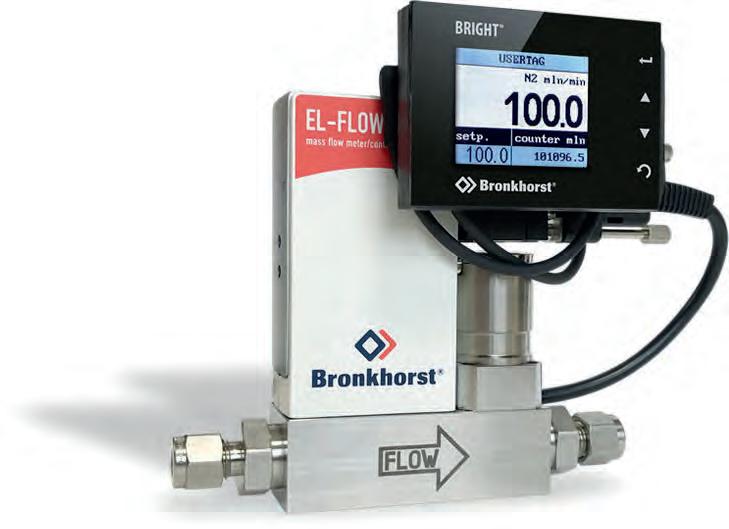
Less is More
An innovative rotating cleaning nozzle with a special flat fan design developed by Lechler, saves time and money through uniform coverage when cleaning tanks. In a series of tests, it was capable of reducing the cleaning time by 40% and fresh water consumption by 30% in comparison to conventional spray balls.
re are mechanics, chemistry, time and temperature (Sinner Circle).
Predictable return on investment
The cost associated with this nozzle is paid off quickly, especially when you compare the significant reduction in lower operating costs. More efficient cleaning systems will also
Reliable cleaning processes reduce the risk of claims
Hygiene is absolutely essential to ensure the quality and uniformity of goods that are manufactured, filled and packaged. Industrial cleaning processes such as Cleaning in Place (CIP) provide a long-term contribution in maintaining the required hygiene levels and protecting manufacturers against expensive claims which can damage their reputation. The required cleaning jobs must be performed quickly and more or less in between production. Longer downtimes result in higher costs.
With modern cleaning processes, the focus is no longer on effectiveness but efficiency. Optimally matched factors achieve the desired cleaning result with the economical use of resources. The main four factors he- become increasing important in production plant as well in the future. The goal is to show how the cleaning result is affected by gradually increasing the operating pressure and the size of the tank. The results will be used by Lechler for further optimization of the rotating cleaning nozzle. In order to increase process reliability even further, the rotating cleaning nozzle can also be optionally combined with a rotation monitoring sensor.

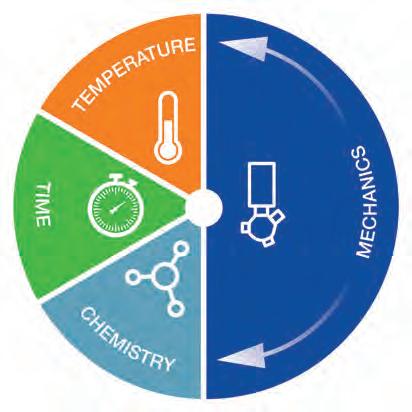
Renowned plant manufacturers have placed their trust in the nozzle technology and know-how of Lechler company for many years now. Reduction in the costs for energy, natural resources and additives is an important argument in the industry.
Lechler never focuses on just the individual nozzles but always on the overall process.
Different type of materials, certifications, flow rates, diameters of coverage, impact forces and efficiency classes. Lechler’s tank cleaning satisfy all needs of processes.
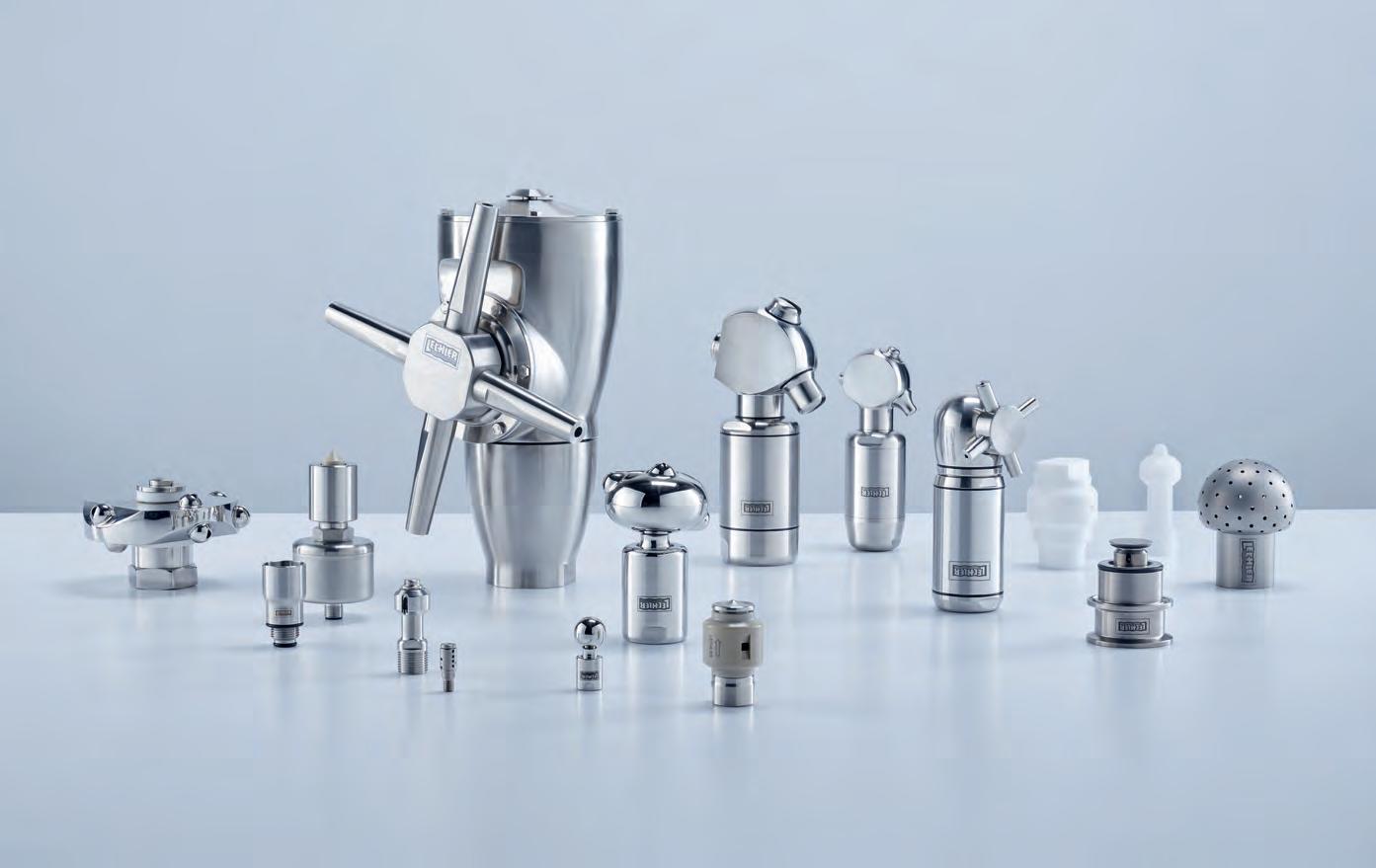
Discover yourself advantages.