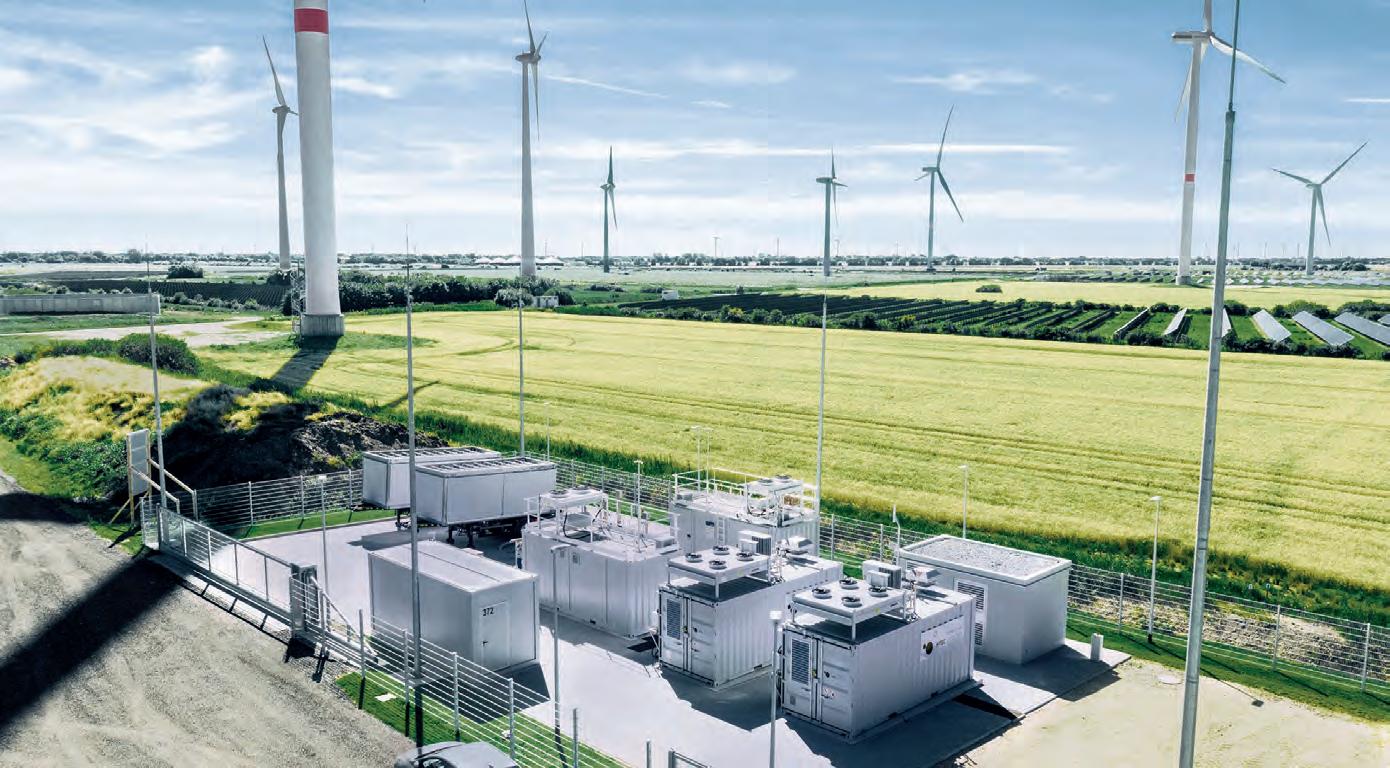
4 minute read
The shift from CO2
For the chemical industry, the energy transformation is a significant challenge that must be dealt with as rapidly as possible. The shift to renewable raw materials and energy sources thus calls for extensive changes to existing processes. But it also opens up avenues for avoiding, capturing and storing CO2.
by Florian Kraftschik* and Frederik Effenberger**
Advertisement
The energy transformation has a clear goal in the industrial sector: shifting the energy supply to a sustainable basis through renewable sources. The idea is to reduce or completely do away with anthropogenic CO2 emissions created by fossil energy sources. Many of the technologies for industrial decarbonization place high and very specific demands on process measurement technology. This article offers an overview of how Endress+Hauser can make a contribution as a partner for the process industry.
The chemical industry must deal the energy transformation as rapidly as possible
For the chemical industry, the energy transformation is a significant challenge that must be dealt with as rapidly as possible. The complexity of this task stems from the fact that while fossil-based raw materials must be replaced since they are the underlying cause of carbon dioxide emissions that are harmful to our climate, CO2 is a necessary raw material for diverse processes in the chemical industry. To date, however, CO2 has been generated as a byproduct, which in a future decarbonized world will no longer be possible in a conventional way.
The shift to renewable raw materials and energy sources thus calls for extensive changes to existing processes. But it also opens up avenues for avoiding, capturing and storing CO2. In order to provide a better description of the various strategies and approaches for reaching the climate goals, and to discuss the corresponding challenges and solutions, this article breaks them down into three main issues:
The first issue is the electrification of processes to avoid emissions and increase the efficiency of existing plants with the aim of reducing emissions wherever they are (still) unavoidable.
The second issue relates to the shift to alternative energy sources, particularly green hydrogen. As well as the manufacture, transport, utilization and storage of H2, other topics that fall into this category include power-to-chemical (P2C) approaches or green steel.
The third area revolves around CO2 as a raw material, which should be viewed as an emission or as a captured product. This topic also includes key terms such as carbon capture (CC) or direct air capture (DAC), as well as the issue of CO2 storage and transport.
Electrification of processes and efficiency improvements
The first promising measure, where implementation is possible, is to convert the chemical industry processes directly to renewable, ze- ro-emission electricity generated from wind, water and solar sources. This is certainly one of the biggest and likely easiest adjustments in the process industry. In many cases these adjustments can be made without drastically impacting processes. One example is steam generation, which can be easily electrified and where no changes to the heat network or the instrumentation for measuring and balancing the generation, distribution and consumption of heat are necessary.
For processes that cannot immediately be converted to zero-emission sources, there is often greater potential for emissions savings that can be realized by optimizing and improving plant efficiency. The optimization measures require measurement and balancing of energy consumption. This can be accomplished with Endress+Hauser’s broad field instrument portfolio, which can be used to monitor all parameters in the
A close-meshed network of measuring instruments and energy computers records the quantities of heat flowing through the Endress+Hauser steam lines core processes, as well as in auxiliary systems such as steam, cooling or CIP/SIP. The portfolio features a wide range of measurement parameters such as pressure, flow, material moisture, liquid analysis, level, optical analysis, system components and temperature. As well as services for monitoring CO2 emissions, Endress+Hauser offers digitalization services through Netilion, an IIoT ecosystem that creates transparency in terms of plant assets and provides a basis for plant optimization.
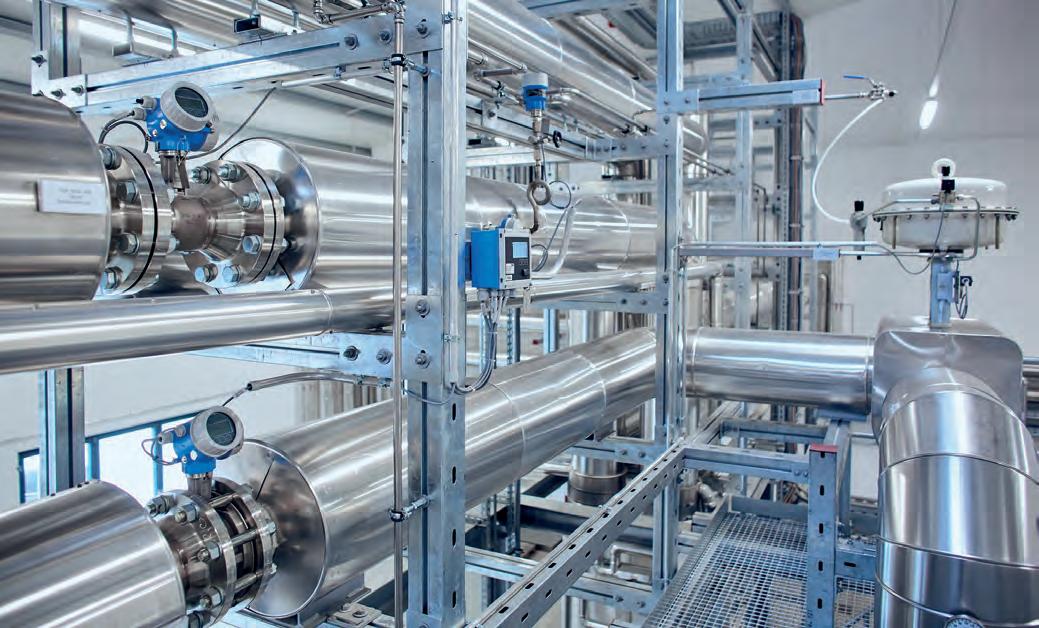
Hydrogen as a storage medium
The second issue related to industrial decarbonization is the conversion to alternative energy sources. Sufficient availability of renewable energy is crucial for reducing emissions through electrification. The sun does not shine everywhere, nor at all times, to the same extent. And wind energy is also subject to large fluctuations. While regenerative energy is the foundation of electrification, a key factor for a successful energy transformation is storage technologies that can balance out these fluctuations. One medium that can store excess solar and wind energy is hydrogen. The conversion of electricity to hydrogen loses some energy, but hydrogen stores well and can be converted back to electricity with relative ease if required. Storing energy in hydrogen is known by the term power-to-chemicals (P2C).
In chemical plants, however, there are processes that require so much energy in total that their energy requirements cannot be fully covered by regularly feeding the grid with renewable electricity. These processes can be completely converted to hydrogen, which is delivered to the plant via a transport network.

Endress+Hauser: measurement technology for the energy transformation
Measurement devices and solutions play an important role in the overall energy transformation. Today, core processes and auxiliary systems such as heating, cooling and CIP/SIP systems are already equipped with a close-meshed network of measurement instruments in order to capture measurement values and other data for process monitoring and control and to communicate the information to the control system. For the energy transformation, plant operators will also require precise measurement values regarding energy input and usage, the exact distribution and the energy balance across the entire plant. The level of CO2 emitted into the environment must be precisely tracked as well. Given that the exact amount of energy has to be reliably monitored, the demands on the instrumentation are high in terms of measurement accuracy and long-term stability.
After all, only those who know where the energy is being used are in a position to affect energy savings or shift to other sources.
The demands on the instrumentation are unique, however, particularly when the devices come into direct contact with hydrogen. For measuring pressure in electrolyzers, for example, Endress+Hauser offers a pressure measurement cell with a gold-coated membrane that provides effective protection against the diffusion of the very small H2 molecules through the membrane. If the gas