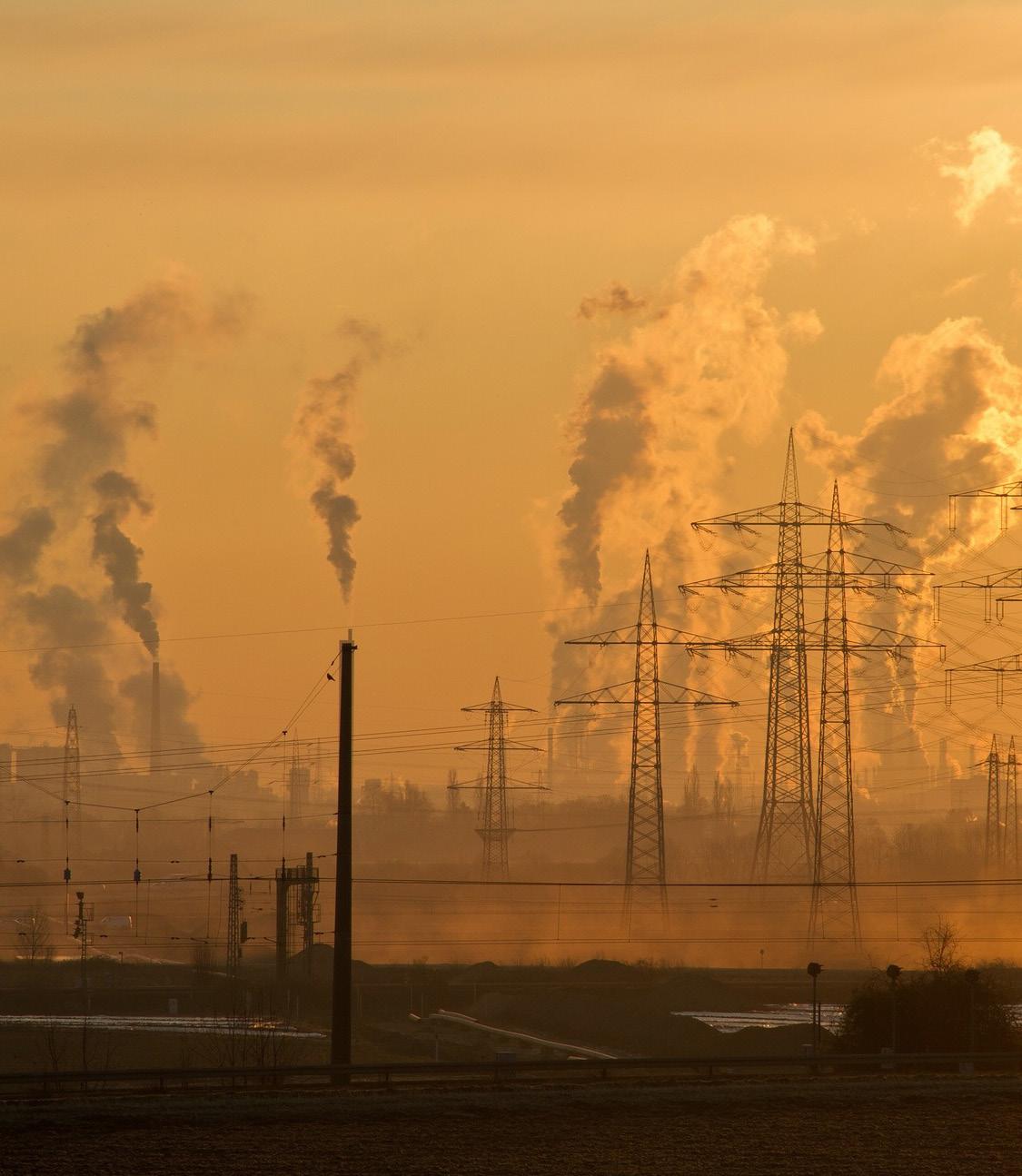
17 minute read
REDUCING THE CARBON IMPACT OF FAÇADES: IS INNOVATION WHAT WE NEED? Helen Sanders - General Manager, Technoform North America
Reducing the carbon impact of façades:
Is innovation what we need?
Advertisement
Helen Sanders, PhD; Technoform
In his new book, “How to Avoid a Climate Disaster,” Bill Gates articulates the need to move from the current 51 billion tons/ year of global carbon emissions to net zero by 2050, the significant challenges it presents and the sobering consequences of not taking action [1]. He identifies construction, with high carbon intensive concrete and steel, as a key challenge area. He also mentions glass and aluminum, the main components of façades.
Annually, carbon emissions from building materials and construction (embodied carbon) comprise 11% of global greenhouse gas emissions, and carbon emissions from operating buildings (operational carbon) comprise 28% [2] (Figure 1). Since emissions related to construction occur at the beginning of a building’s lifecycle, the impact of its embodied carbon on near-term emissions is more significant than the 11% figure implies. The timing of these emissions matters because:
• Carbon emissions need to be curbed quickly: The United Nation’s International
Panel on Climate Change (IPCC) predicts that the rate of carbon emissions needs to have reduced to zero by around 2055 to maintain global warming to 1.5oC and prevent a climate catastrophe [3]. • The rate of building construction is accelerating: Globally, the equivalent of one New York City is being built every 35 days. According to the founder/CEO of
Architecture 2030, Ed Mazria, the global building floor area is estimated to grow by 40% in the next 15 years. This is the equivalent of replicating all the buildings already standing in the entire western hemisphere [4]! • Continued greening of electrical grids over time can reduce the emissions from building operations through its lifetime, but its embodied carbon is already emitted and contributing to warming.
Do we need more innovation in façades?
Gates states, “We need lots of breakthrough science and engineering” to get to net zero. While this is also true for façades, some changes to “business-as-usual” design and construction can be made that do not necessarily require “breakthrough science,” and could make a big impact in carbon emissions immediately. Consider operational carbon – that is, improving building energy efficiency. One major step would be to ensure that the already existing and proven high-performance façade technologies, and best practices in design, testing and installation, are fully adopted globally. Figures 2, 3 and 4 show examples of advanced thermal break technologies for aluminum fenestration, insulating glass and opaque cladding attachment and their use in buildings. Many of these product technologies have been proven over decades of use in advanced geographic markets but have not yet been adopted as business-as-usual globally. Achieving economies of scale typically reduces costs, further driving adoption, which is especially needed to enable widespread use in emerging markets.
In the U.S., the adoption of new façade technologies is slow. The current business-asusual façades do not come close to using the highest performing fenestration and façade systems available. This is primarily because building codes do not force their use, the cost of energy is so low that the simplistic payback calculations based on energy alone do not add up, and façade performance can be traded off with higher performing HVAC systems. The design-bid-build process, in which three equivalents are typically required, combined with low-bid wins also constrains adoption of new products. This remains true until more than one manufacturer can supply a solution and the cost is more comparable to the businessas-usual lower performance solutions. This also lowers incentives for manufacturers to innovate. In addition, according to the Façade Tectonics Institute, building energy simulation and thermal modeling tools in widespread use are not sophisticated enough to accurately address thermal bridging issues [5]. As a result, we think façades perform better than they do. This means that with our code standard compliance tools we cannot show a cost-benefit for new technologies that address those parasitic losses.
Innovation in simulation tools and in code and policy incentive infrastructure for construction is needed urgently. This will drive the mass adoption of already developed innovations, lower their costs further and positively reinforce supply chain investment in additional innovation.
To build or not to build
Turning now to the need for embodied carbon reduction. When thinking about either embodied carbon or operational carbon, the most sustainable building is the one that is not built.
Because it is difficult to imagine a global moratorium on construction, assessing the ability to re-use or re-purpose existing structures rather than demolishing is an important first consideration. If new construction is necessary, we must change the design approach and decision-making process to focus on extending a building’s service life and minimizing the structure’s size. Size impacts both embodied and operational carbon.
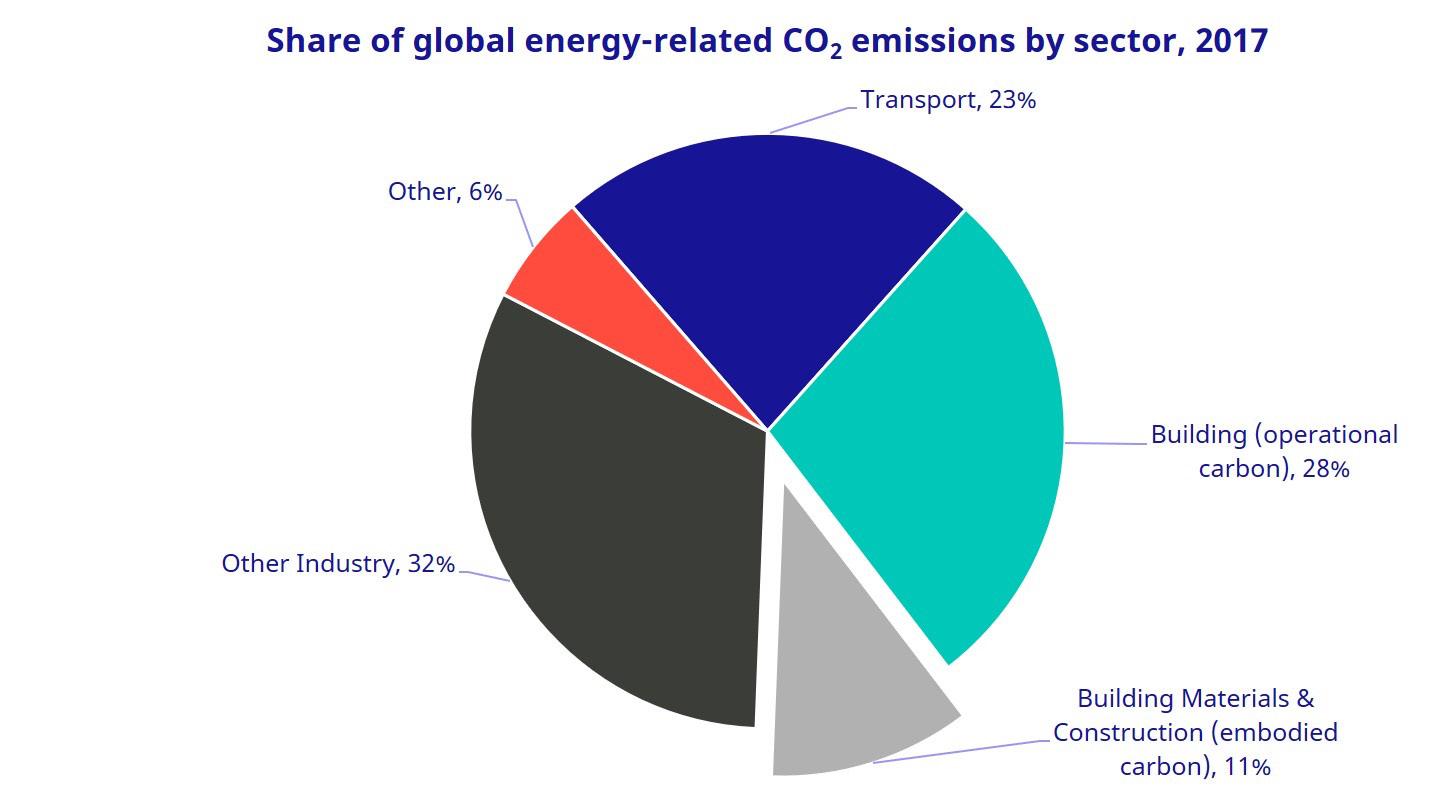
Figure 1: The breakdown in carbon emissions globally according to the UN Global Status Report 2017 [2]
Making it last
Making a building last longer is key to minimizing embodied carbon. Simplistically, doubling lifetimes could halve embodied carbon. This means maximizing the service life of a building’s components and providing paths for easy service, maintenance and upgrades to improve operational performance as technologies become available.
Typically, North American buildings have an assumed service life of up to 50 years [6]. What would the design of a 200-year building look like in terms of component lifetime, maintenance, service and upgradeability requirements? Typically, façade systems are not designed with these requirements mind. For example, by preventing access to the “chicken head” – the upturned leg and gaskets on the stack horizontal on a unitized wall system – curtainwall systems are not designed for serviceability nor are they easily upgradeable. Addressing serviceability and upgradeability in curtainwall and other façade systems is a key innovation area for the glazing industry to address.
Also, consider the introduction of insulating glass to façades in the past 50 years which replaced single-pane glazing. Mic Patterson of the Façade Tectonics Institute has observed that a carbon intensive material capable of lasting centuries has been turned into a material that now lasts just a few decades (Figure 5). While this has delivered substantial improvements in building energy efficiency as well as in occupant thermal comfort, the impact on embodied carbon only recently has been considered.
The Bullitt Center in Seattle, designed by the Miller Hull Partnership, LLP, and completed in 2013, was ahead of its time in the U.S. Dubbed the “World’s Greenest Commercial Building,” it was designed to have a 250-year lifetime, to have the highest thermal performance, and with many other sustainable features meeting the challenging Living Building Challenge standard (Figures 6a and 6b). The façade incorporates an insulating glass unit (IGU) with a plastic hybrid stainless steel (PHSS) spacer in a triple-pane configuration and dual-seal silicone edge bond. These components, along with operable fenestration with wide complex thermal breaks, contribute to the façade’s thermal performance and longevity. To achieve our carbon reduction goals this type of design needs to become the norm, not the exception.
Designing insulating glass for lifetime The edge bond system of an IGU is critical to its lifetime. Typically, the edge bond system
Figures 2a, b, c: (a) High-performance aluminum fenestration system with (i) complex polyamide thermal break technology that manages conduction, convection, and radiation and (ii) a plastic hybrid stainless steel warm-edge spacer. These product technologies have over 40- and 20-year track records, respectively, and have been used in many large-scale buildings including (b) the LEED® Gold certified Leeza Soho building in Beijing and (c) the 465 N. Park Tower, Chicago.
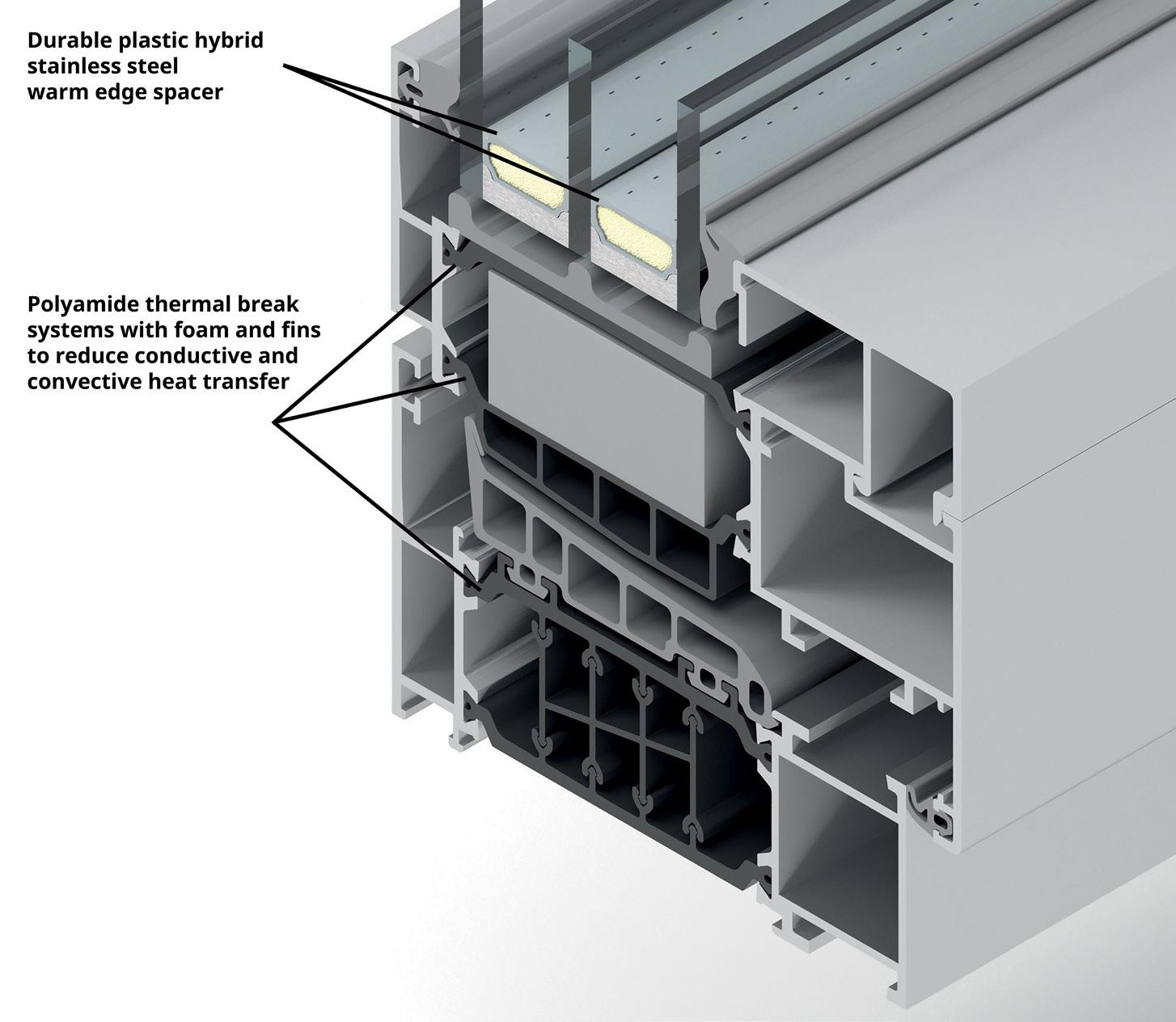
Figure 2c-i – Pappageorge Haymes Partners, Darris Lee Harris Figure 2c-ii – PDET Photography
Figure 2b – courtesy of Hufton+Crow
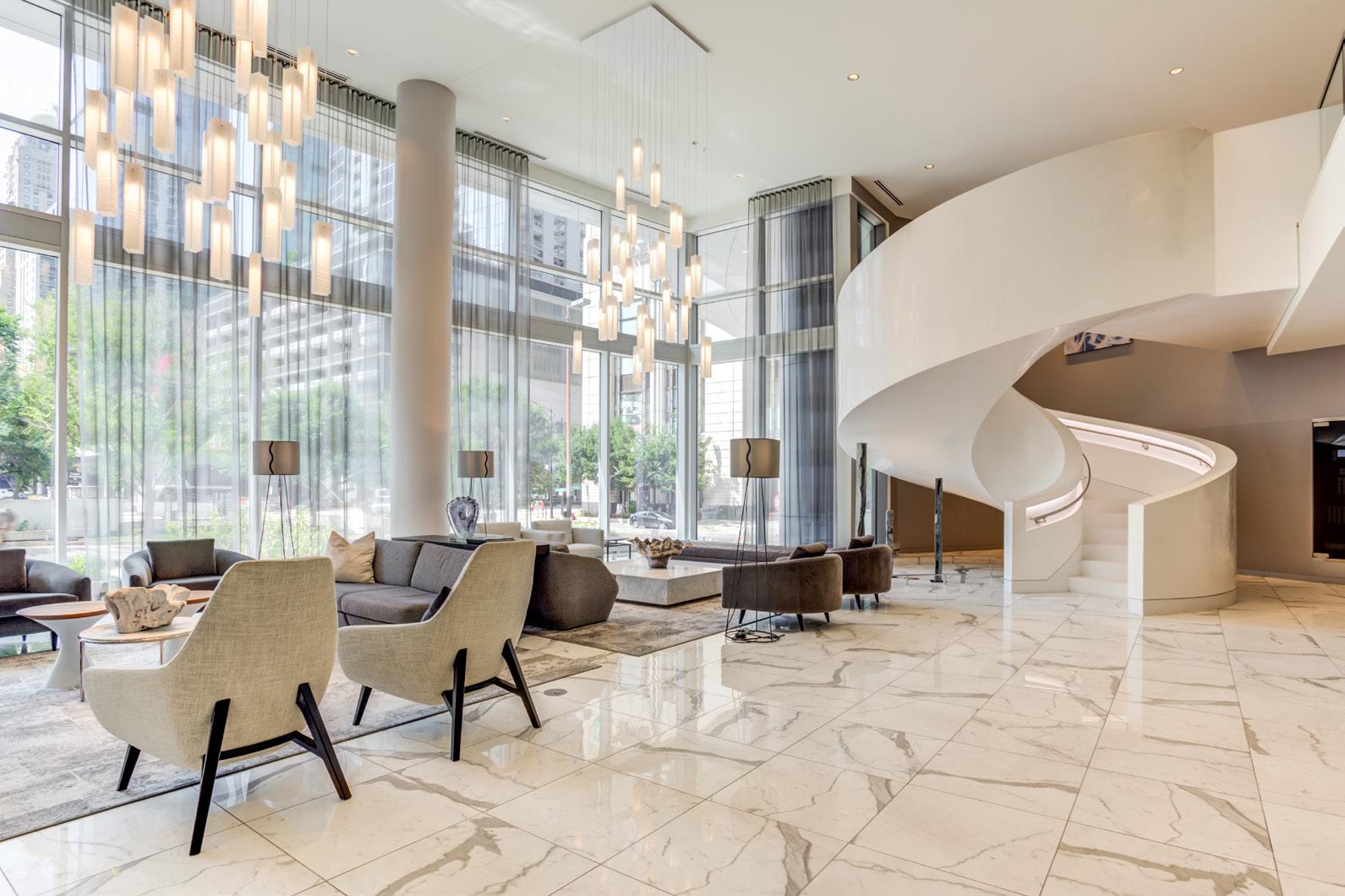
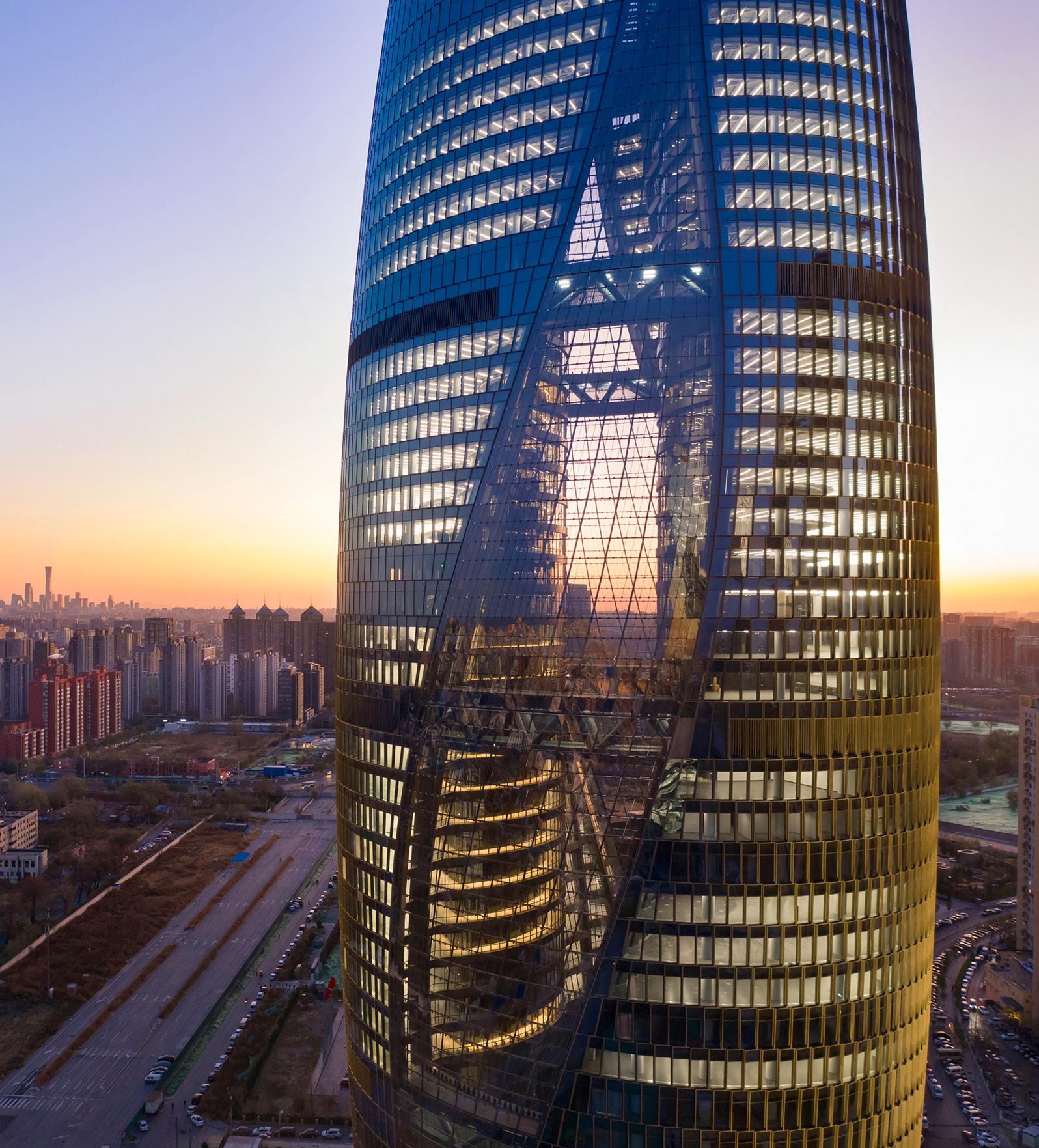
Figures 3a, b: Polyamide pressure plates replace aluminum pressure plates in curtainwall, improving thermal performance by up to 20%. Georgia State University College of Law, Atlanta, features a curtainwall with polyamide thermal breaks and polyamide pressure plates.
3a – courtesy of YKK AP
3b – © Chuck Choi Architectural Photography comprises a spacer to create an insulating cavity between the two panes, which also contains desiccant plus a primary sealant and a secondary structural sealant. While awaiting the commercialization of a breakthrough technology that can deliver the thermal performance of insulating glass with the service life of monolithic glass, the most important focus now is on ensuring that the insulating glass produced in the meantime has as long a service life as possible.
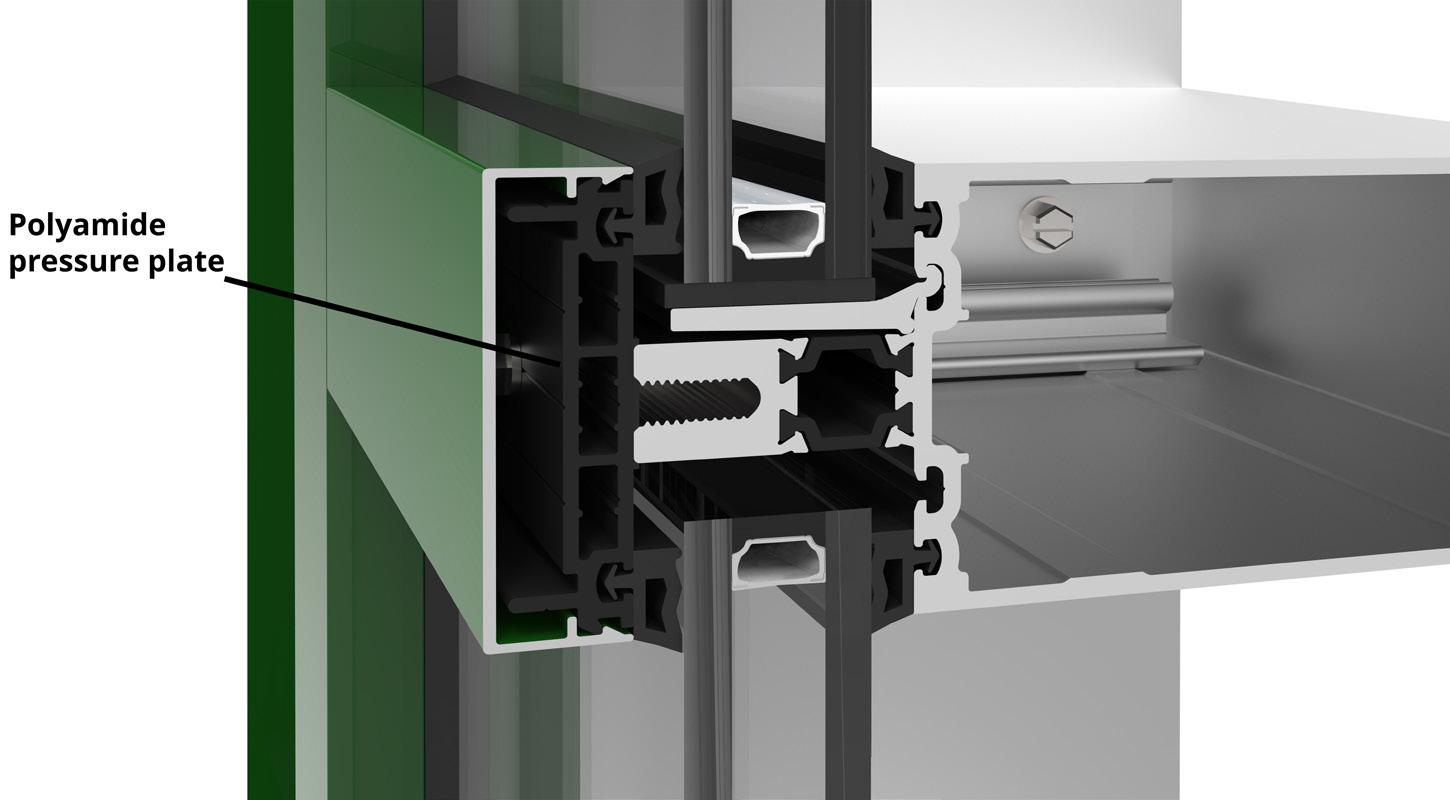
It is important to retain perspective on the balance of operational and embodied carbon. While it is important to improve fenestration thermal performance, it is crucial to avoid trading small incremental gains in fenestration
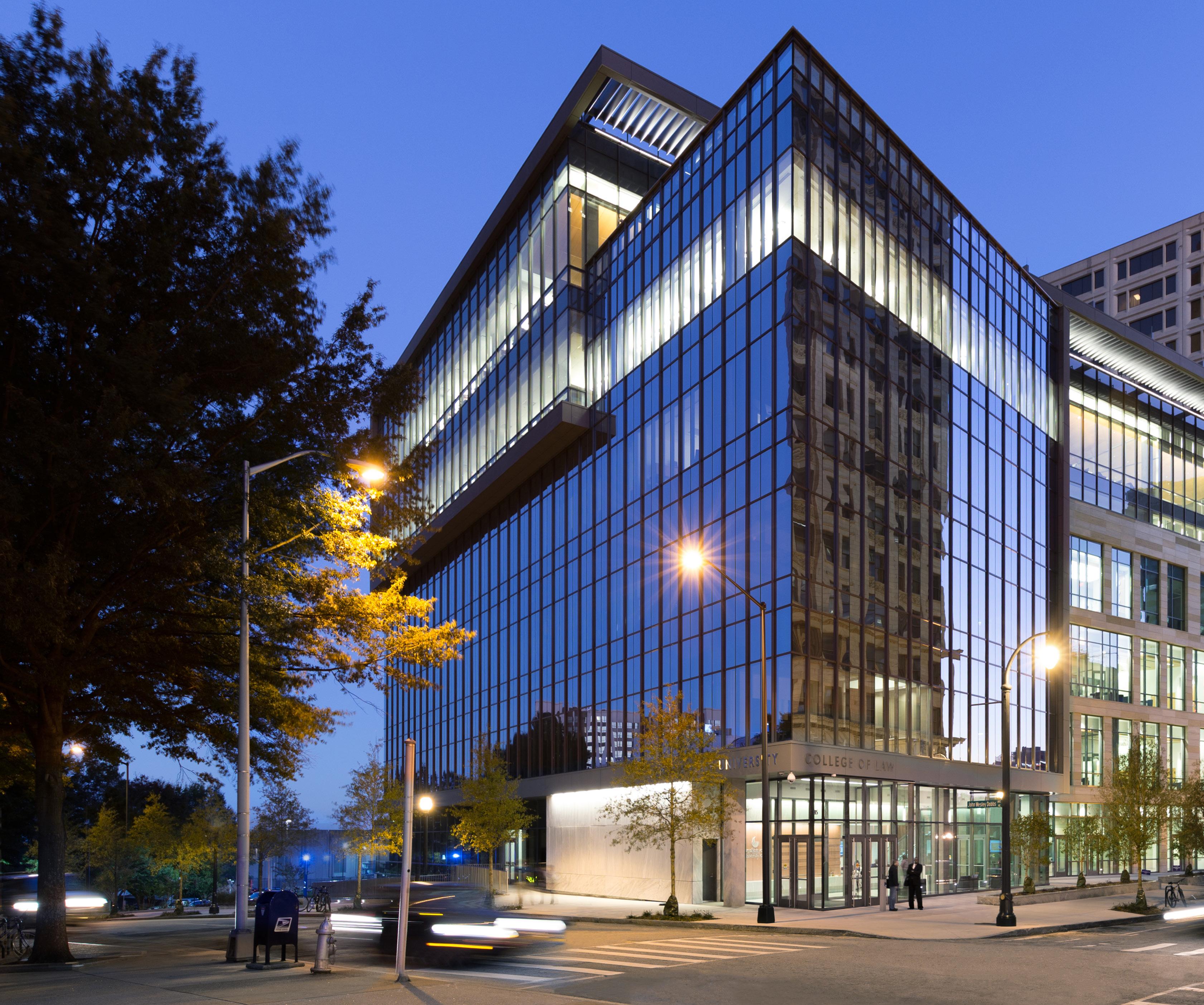
assembly thermal performance for higher IGU service life risk. For example, the embodied carbon impact of having to replace IGUs after 15 years rather than 30 years is much greater than the operational carbon saved by a minor increase in fenestration thermal performance. Depending on the building massing, changes in fenestration thermal performance contribute proportionately less to the overall building energy performance. Even from an operational carbon perspective, IGU thermal performance is only as good as its ability to maintain that performance over its lifetime.
Ideally, implementing solutions with improved thermal performance as well as long service life is the most desired outcome. This is where careful edge seal design, manufacturing and installation is critical.
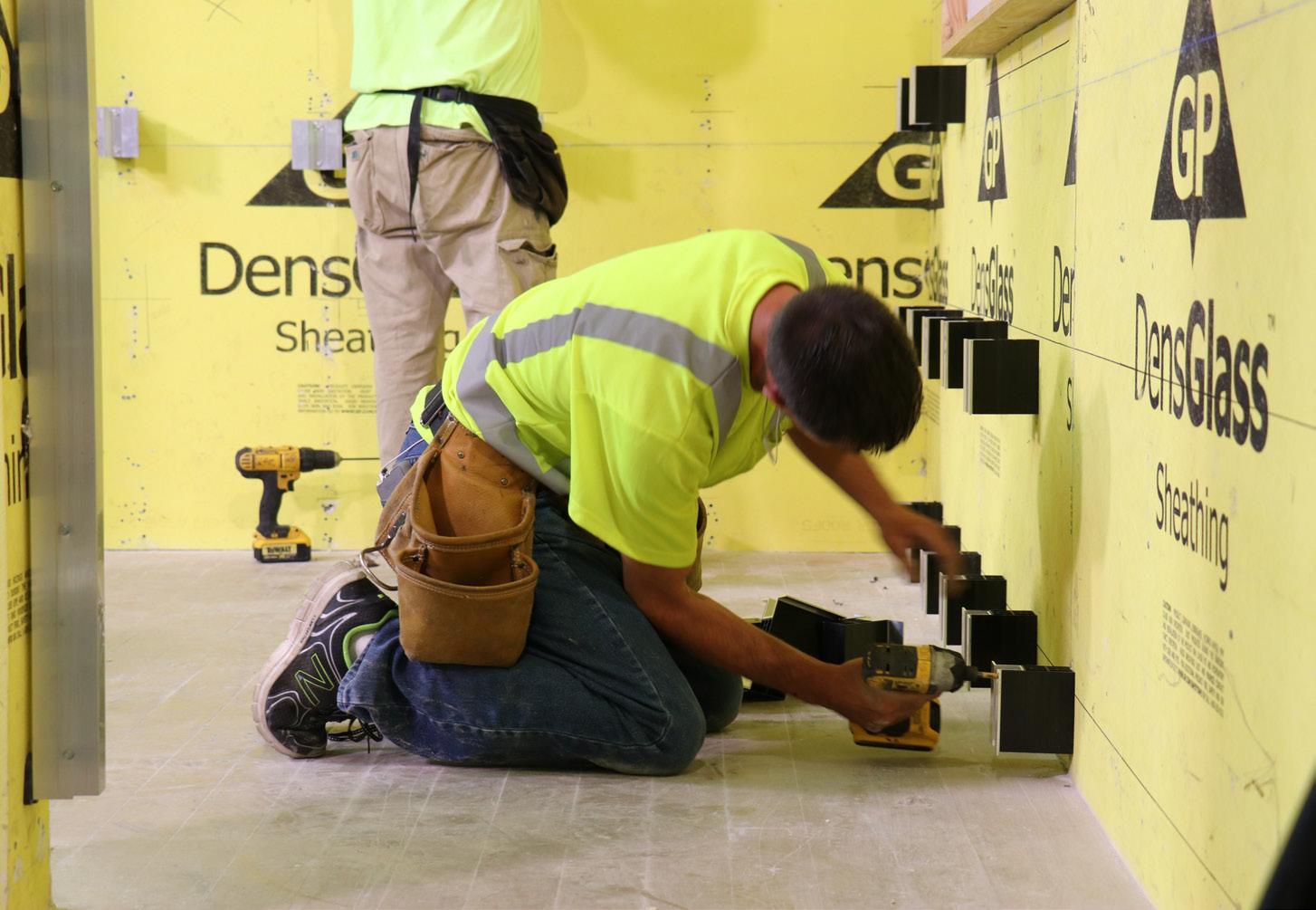
Typically, service life of 25+ years is expected for an IGU if the edge bond is carefully designed, well manufactured and installed. Shortened lifetimes (Figure 7) [7] resulting from premature seal failure can be the result of: • Not designing the edge bond for the specific application or not designing it to resist the expected climate loads • Component versus system thinking – Using spacer and sealant components that do not work effectively together as a system or not incorporating high-quality materials, or enough of such materials • Poor manufacturing workmanship or factory process control • Poor installation, which does not effectively manage water or material incompatibilities, nor support the glass edges
What do we mean by carefully designed?
The edge bond of an IGU is not a collection of individual components, rather it should be considered a system in which the components interact to deliver performance. They must be carefully combined in type and quantity appropriate to the application.
Components of a proven edge seal – spacer or sealants – should not be swapped without appropriate testing and evaluation to confirm equivalency in durability and service life performance. Consider that the typical secondary sealant system used in commercial systems is silicone. It is used because of its structural strength, its UV stability and its ability to resist liquid water. However, it has high moisture vapor and gas permeation rates. Therefore, unlike other secondary sealant options, it cannot be relied on to create a back-up diffusion barrier to the primary seal. This means that the primary seal, comprised of the spacer and primary sealant (typically polyisobutylene, PIB), must have excellent vapor and gas barrier properties, and be fabricated with no defects.
The excellent barrier properties that solid metals provide is a key reason why aluminum, stainless steel and PHSS warm-edge box spacer have become the benchmark for durability in
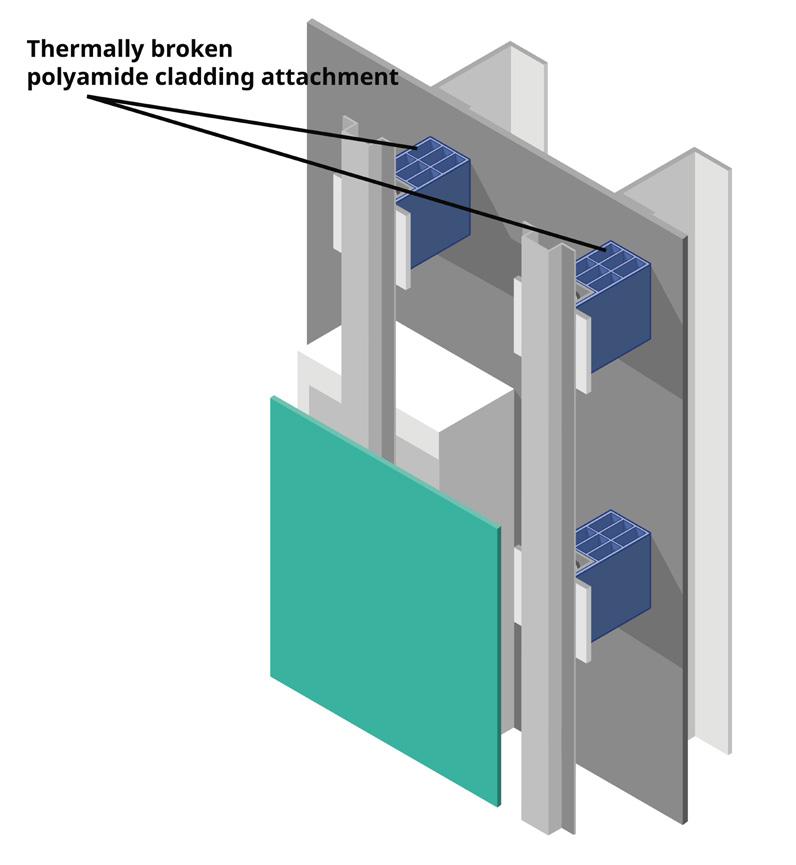
Figures 4a, b: (a) A thermally broken cladding attachment using glass-filled polyamide replaces low-performance continuous aluminum z-girts, which can degrade opaque panel performance by up to 50%. (b) How thermally broken cladding clips attach to the façade structure. Credit: courtesy of Technoform
Figure 5: Single-pane glass lasts many hundreds of years compared to insulating glass. Credit: Evie Fjord on Unsplash
dual-seal silicone systems. The other reason is the excellent adhesion of aluminum and stainless steel to silicone and to the other typical IGU sealants. The transition from aluminum to stainless steel to hybrid spacer delivers increasingly higher thermal performance without loss of durability performance.
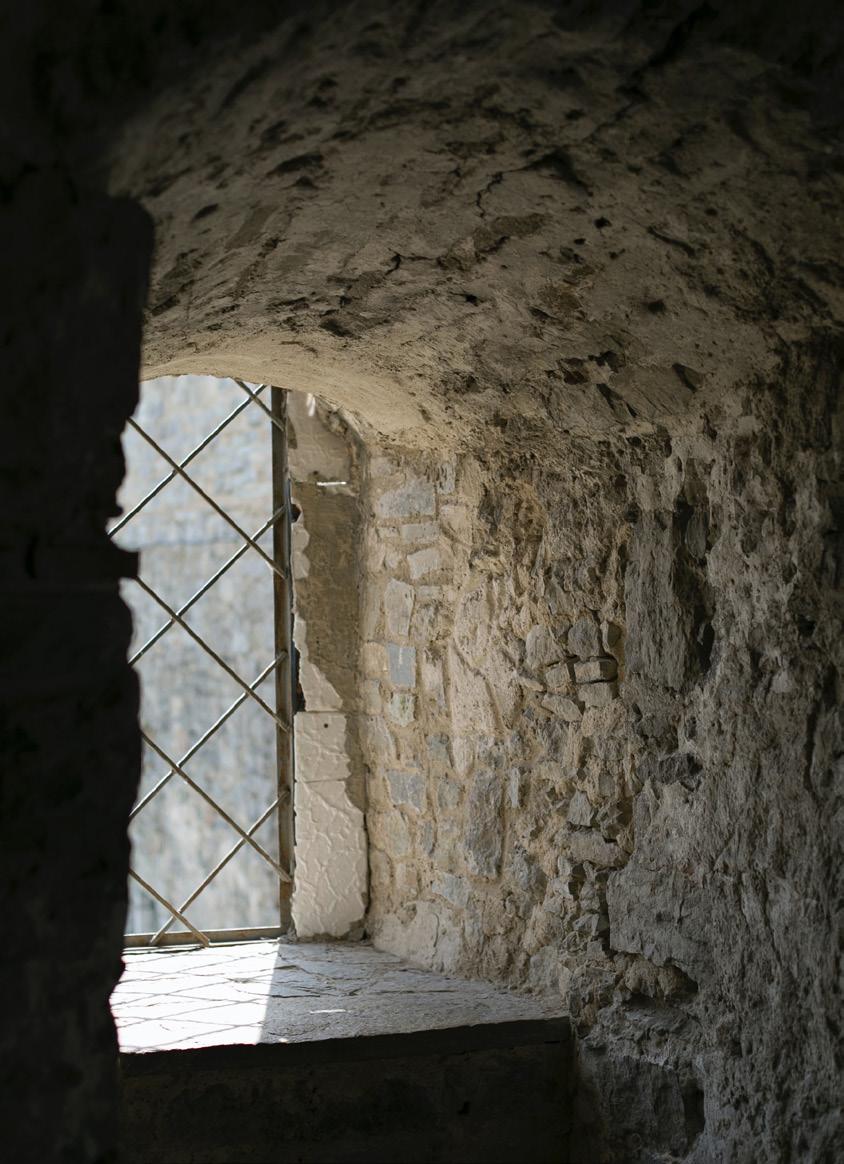
Adhesion to the spacer is very important. It holds the spacer in place, preventing movement into the cavity – which is especially important for non-rigid bar, flexible spacer systems made from foam and butyl matrix. Good adhesion prevents water accumulation at the primary seal, which would cause PIB degradation and premature seal failure. Importantly, good adhesion of the secondary seal to the back of the spacer also prevents over-extension of the PIB. The three-sided bond created between the sealant, the two glass surfaces, and the spacer is significantly stiffer than a two-sided bond created where there is only adhesion between the sealant and the two glass surfaces [8]. As a result, under climate load, the stiffer edge bond suffers smaller PIB extension, reducing vapor and gas transmission. This is expected to correlate with longer lifetime.
Desiccant carrying capacity is also important for lifetime. All other factors being the same, more should be better. The path length (or depth) of sealant is also critical. Typically, spacer and sealant manufacturers provide guidance on minimum sealant depths for spacer types and/ or barrier film types. Fabricators qualify their IGUs through standardized durability tests with a given spacer, sealant type and quantity. As an aside - it is important that thermal performance modeling should be done using the correct sealant height required for delivering durable performance (and for meeting any structural design requirements). More sealant typically reduces thermal performance.
Returning to our dual-seal silicone edge bond example, substituting a different spacer component into this edge bond system that does not have the same moisture vapor barrier or desiccant carrying capacity without testing and evaluation would be a mistake. The Insulating Glass Certification Council (IGCC), which runs a certification program for insulating glass fabricators in North America, categorizes spacers into similar types, according to vapor barrier type (metal or multi-layer plastic foil) and whether it is single or multicomponent. IGCC allows fabricators to substitute stainless steel box spacers with PHSS spacers without immediately retesting their IGUs because both have the same solid metal vapor barrier and desiccant carrying capacity. Substitution of metal box spacer with spacer that have a metallized plastic foil barrier is not allowed without testing because of the difference in barrier properties and adhesion.
Testing and certification
It is important to evaluate the durability performance of an edge bond system using standardized weathering tests (e.g. ASTM E2190 and EN 1279), understand the margin by which the system meets the standard (the larger margin the better), and the extent to which this performance can be replicated in production day after day. It is not enough to just pass these tests once with a laboratorymade unit. Design teams must expect that a fabricator’s IGUs made on their production lines meet these requirements on a regular basis. This is where IGU certification programs are useful to specify. Programs that require fabricators to produce IGUs on their production lines annually, in the presence of a third-party auditor, and to demonstrate these units meet the requirements of standardized weathering tests, give the best indication of quality.
In addition, meeting the requirements of these weathering standards may not be sufficient to confirm application-specific performance. IGUs designed for commercial applications destined for the 50th floor of a tower are tested to the same weathering standard as residential style IGUs destined for small windows in single family homes.
We must design for climate stress
When installed, changes in external weather conditions cause temperature and pressure changes in the cavity of the IGU. This, in turn, creates a tensile load on the edge bond. Typically, the lites of the IGU deflect and/or the edge seals stretch to increase the cavity volume in response to increased temperature or increased altitude. The smaller or stiffer the unit, the less deflection can occur in the glass, and the more load is exerted on the edge seal, creating larger PIB extension. The larger the PIB extension, the greater the area for water vapor and gas transmission, potentially impacting lifetime.
The globally used standardized IGU durability tests (ASTM E2190, EN 1279-2) exert an edge force of 0.69 to 0.72 N/mm. A 25-year field
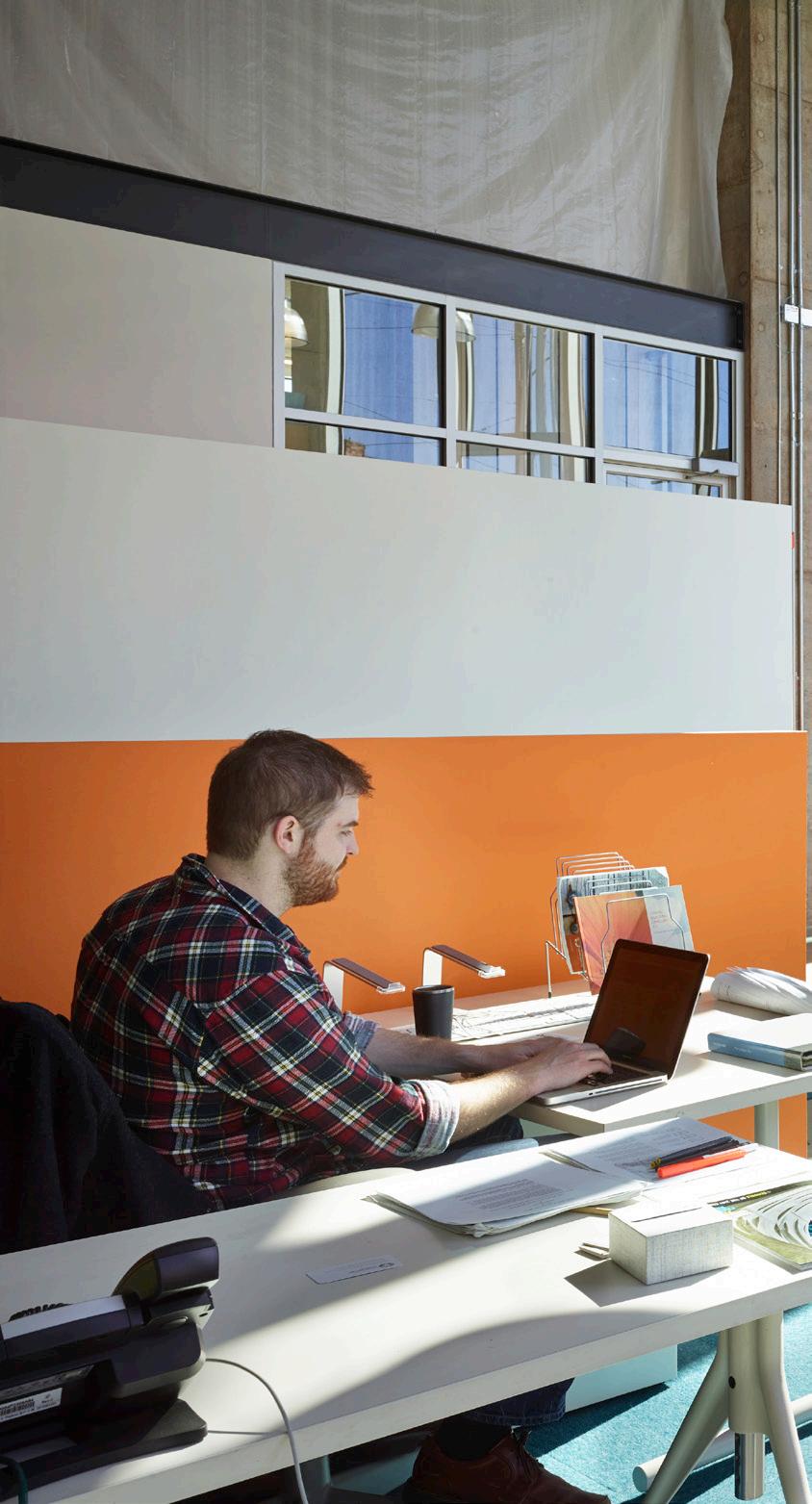
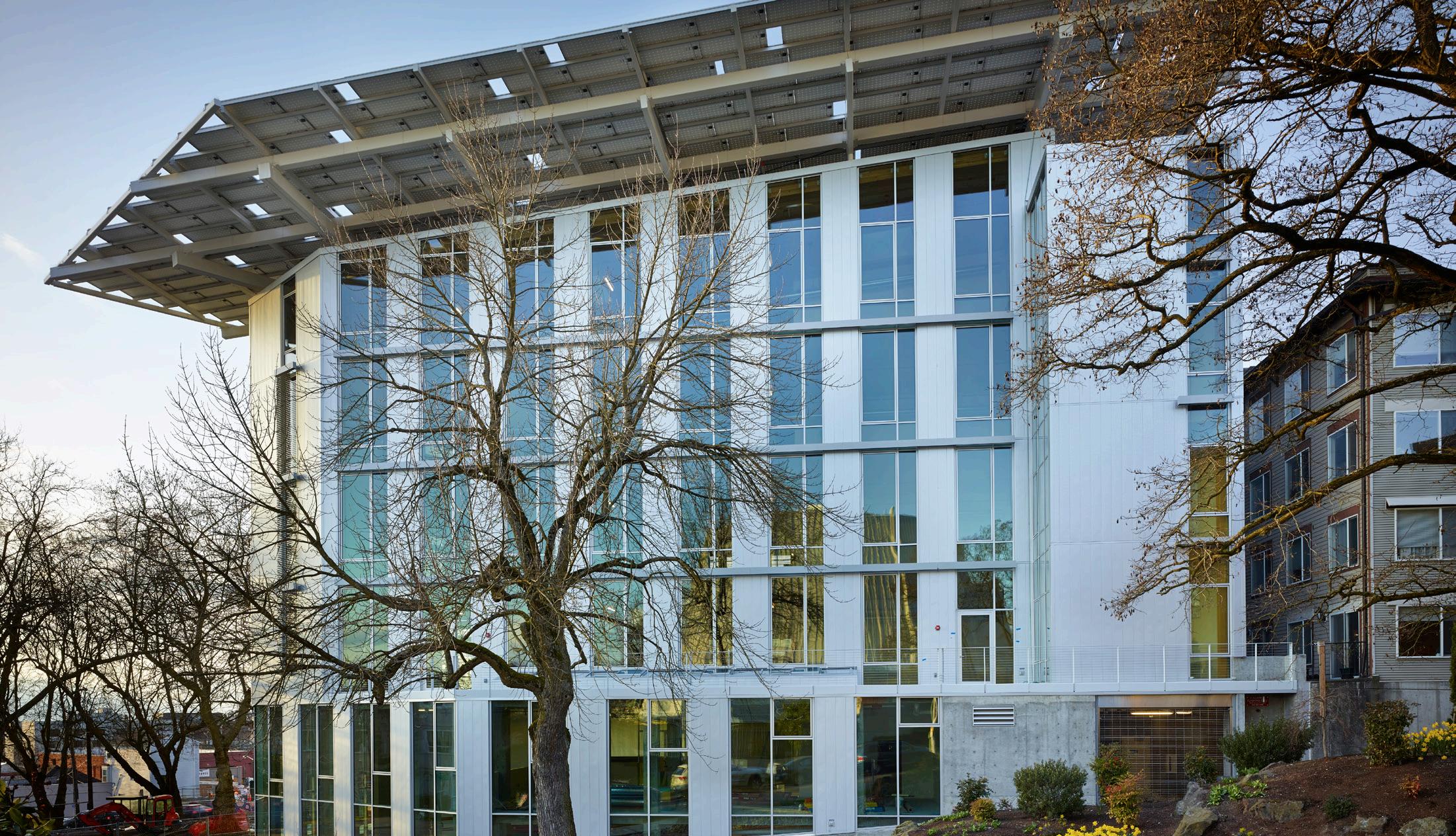
Figures 6a, b: The Bullitt Center, Seattle, was designed by The Miller Hull Partnership with a 250-year design lifetime, utilizing plastic hybrid stainless steel spacer and complex thermal break technology. Credit: ©Benjamin Benschneider, courtesy of Technoform correlation study completed in North America by the Insulating Glass Manufacturers Alliance (IGMA) [9] demonstrated a correlation between the performance of units in the precursor test to ASTM E2190 (E773/E774) to lifetime. IGMA reported a 3.6% failure rate at 25 years for the performance that now correlates to the ASTM E2190 standard. Based on this, one could consider that IGUs that meet the standard test requirements are qualified for serviceability based on not exceeding this edge force when installed.
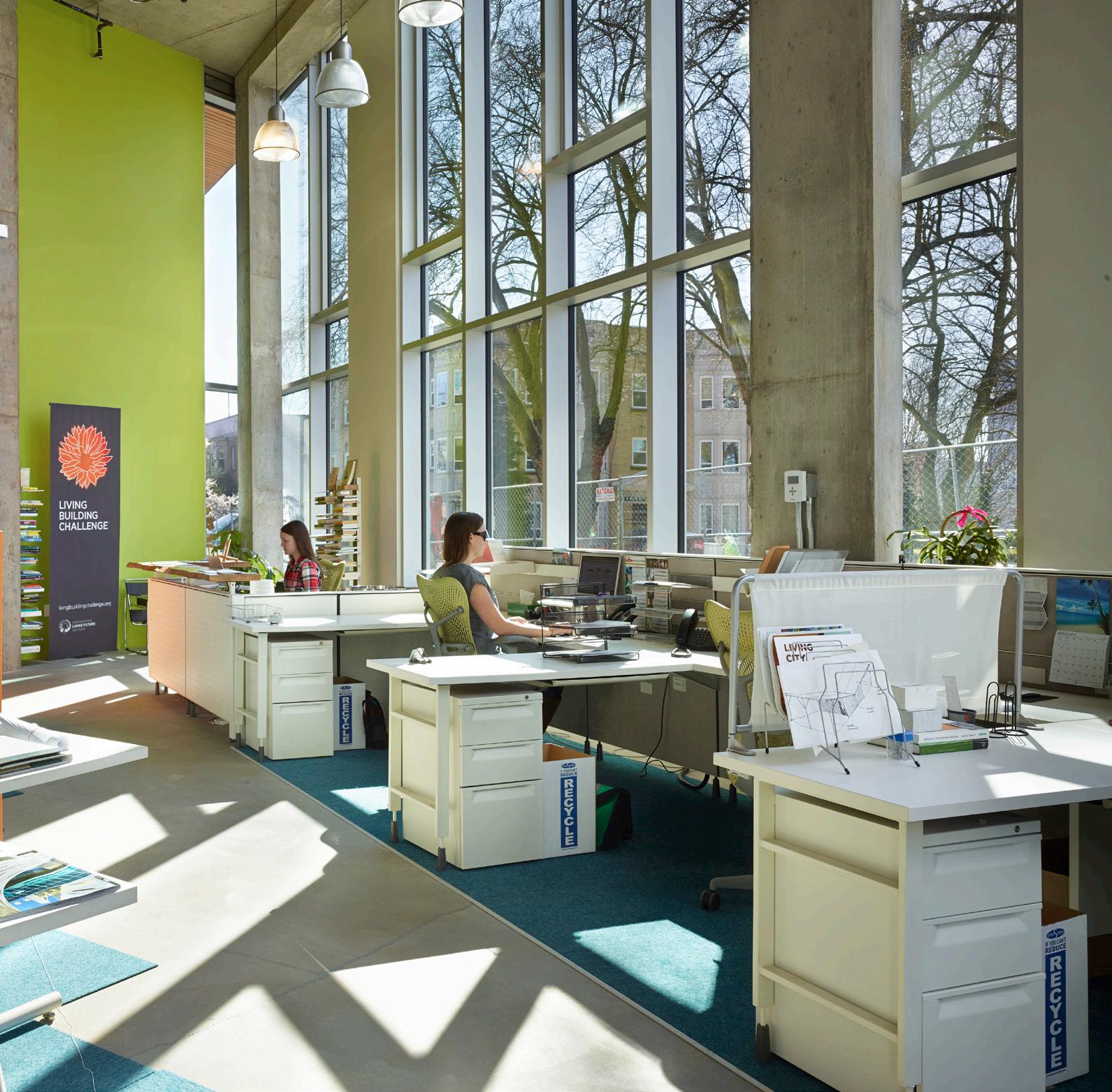
Unfortunately, IGUs are not typically designed with project specific serviceability in mind. The edge bond sealant height is defined based on what passes the IGU durability tests. Then, the IGU glass thicknesses are defined based on the requirements of wind and snow loads, and impact resistance for the largest unit in the project. The definition of the cavity size and number is based on thermal and acoustical requirements. Finally, this configuration is used on all units in the project, no matter what size. This leads to potential serviceability risk for smaller stiffer units, especially in high temperature applications and in wide cavity or multi-cavity configurations.
In structural applications, silicone contact width is calculated, but only to ensure the
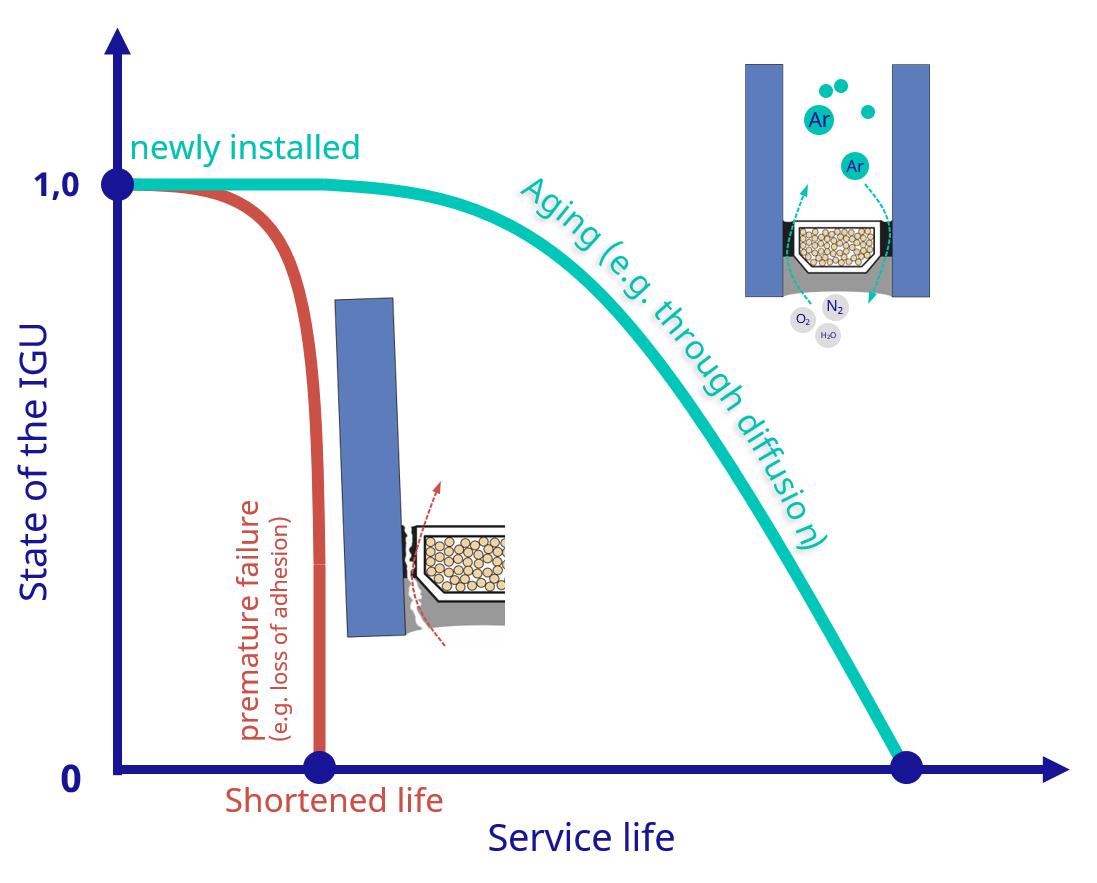
Figure 7: Service life of IGUs [7]. Credit: courtesy of Technoform
glass does not fall off the building, rather than the extent to which it controls PIB elongation. According to the work by Simpson Gumpertz & Heger Inc. in collaboration with Technoform [8], if it were sized for elongation to match standardized testing, more contact width typically would be required. Developing and promulgating industry standards for edge bond serviceability design and widespread adoption is an “innovation” that could make an immediate difference in IGU service lifetime.
Conclusion – to innovate or not?
There is certainly more innovation needed to reduce the carbon impact of façades – more upgradeable and serviceable curtainwall and window systems; step changes in spandrel panel thermal performance and in IGU lifetime; a lower carbon process for float glass – to name a few. However, proven technologies already are available that can meaningfully improve façade thermal and solar control performance. They just need to be used in every building. This requires innovation in codes, public policy, payback methodologies and simulation tools [10].
Lifetime serviceability and maintainability are key to managing embodied carbon. For insulating glass, optimizing lifetime is critical because of the embodied carbon in the glass. Careful edge bond system design, manufacturing and installation all play roles. When pushing the boundaries of thermal performance, it is important to assess the implications for lifetime.
References:
[1] Bill Gates; “How to Avoid a Climate Disaster: The Solutions We Have and the Breakthroughs We Need;” Feb. 2021; https://www. penguinrandomhouse.com/books/633968/ how-to-avoid-a-climate-disaster-by-bill-gates
[2] United Nations Environment and the International Energy Agency; Global Status Report; 2017; https://www.worldgbc.org/newsmedia/global-status-report-2017
[3] United Nations International Panel on Climate Change; Special Report on Global Warming of 1.5oC; Oct. 2018; https://www.ipcc.ch/sr15
[4] Ed Mazria of Architecture 2030; “To Net Zero Carbon and Beyond: Framing the Challenge,” presentation at Carbon Smart Building Day; Sept. 2018; https://www.youtube.com/watch?v=Bzkd3s6_tg
[5] Façade Tectonics Institute; response to U.S. Department of Energy’s Building Technology Office request for information; July 2020. https:// s3.us-east-2.amazonaws.com/facadetectonicscraft-assets/files/DOE-BTO-feedback-from-FTIwindows-final.pdf
[6] RDH Building Science, Inc.; “How Long Do Buildings Last” blog; Jan. 2015; https://www.rdh. com/blog/long-buildings-last
[7] F. Feldmeier & R. Heinrich, B. Hepp, J. Schmid, W. Stiell; Alterungsverhalten von MehrscheibenIsolierglas, Fraunhofer IRB Verlag; 1984 [8] Adam Nizich of Simpson Gumpertz & Heger Inc., Helen Sanders of Technoform, K. Burkhart of Simpson Gumpertz & Heger Inc; “A Strain-Normalized Serviceability Limit State for Secondary Seal of Insulating Glass Units with Rigid Spacers;” accepted for publication by ASTM C24 Committee on Building Seals and Sealants, 2021. Pending publication.
[9] Insulating Glass Manufacturers Alliance; IGMA TR-4000-08, “25 Year Field Correlation Study Report, 1980 to 2005;” 2008; https:// store.fgiaonline.org/pubstore/ProductResults. asp?cat=0&src=TR-4000
[10] Helen Sanders of Technoform; USGNN Insights and Inspirations blog, “Transform or Fail: 2030 Goals are Unattainable Without a Step Change in Building Energy Codes;” Feb. 2021; https://www.usglassmag.com/ insights/2021/02/transform-or-fail-2030-goalsare-unattainable-without-a-step-change-inbuilding-energy-codes
Helen Sanders, PhD, is a general manager at Technoform North America. She has 25 years of experience in glass technology and manufacturing, with expertise in functional coatings, insulating glass and thermal zone technologies for fenestration. She is the president of the Façade Tectonics Institute and a board member of the Fenestration and Glazing Industry Alliance (FGIA). She has a master’s degree in natural sciences and a doctorate in surface science from the University of Cambridge, England. She can be reached at helen.sanders@ technoform.com.
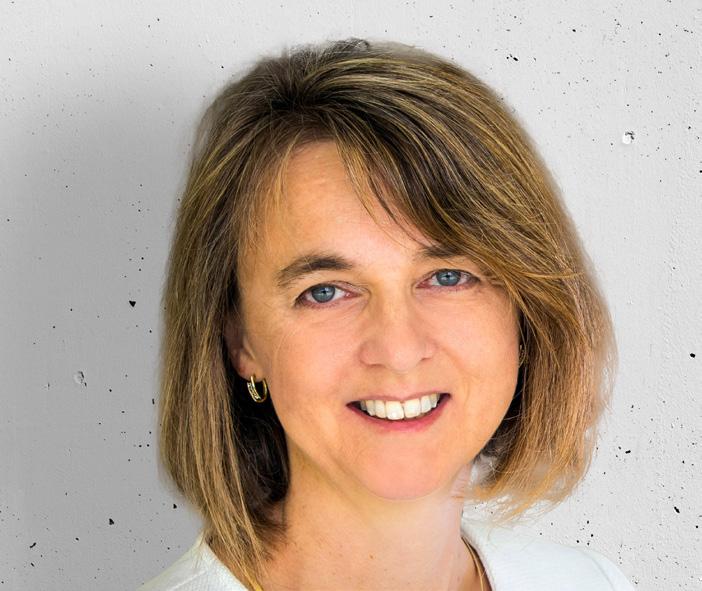