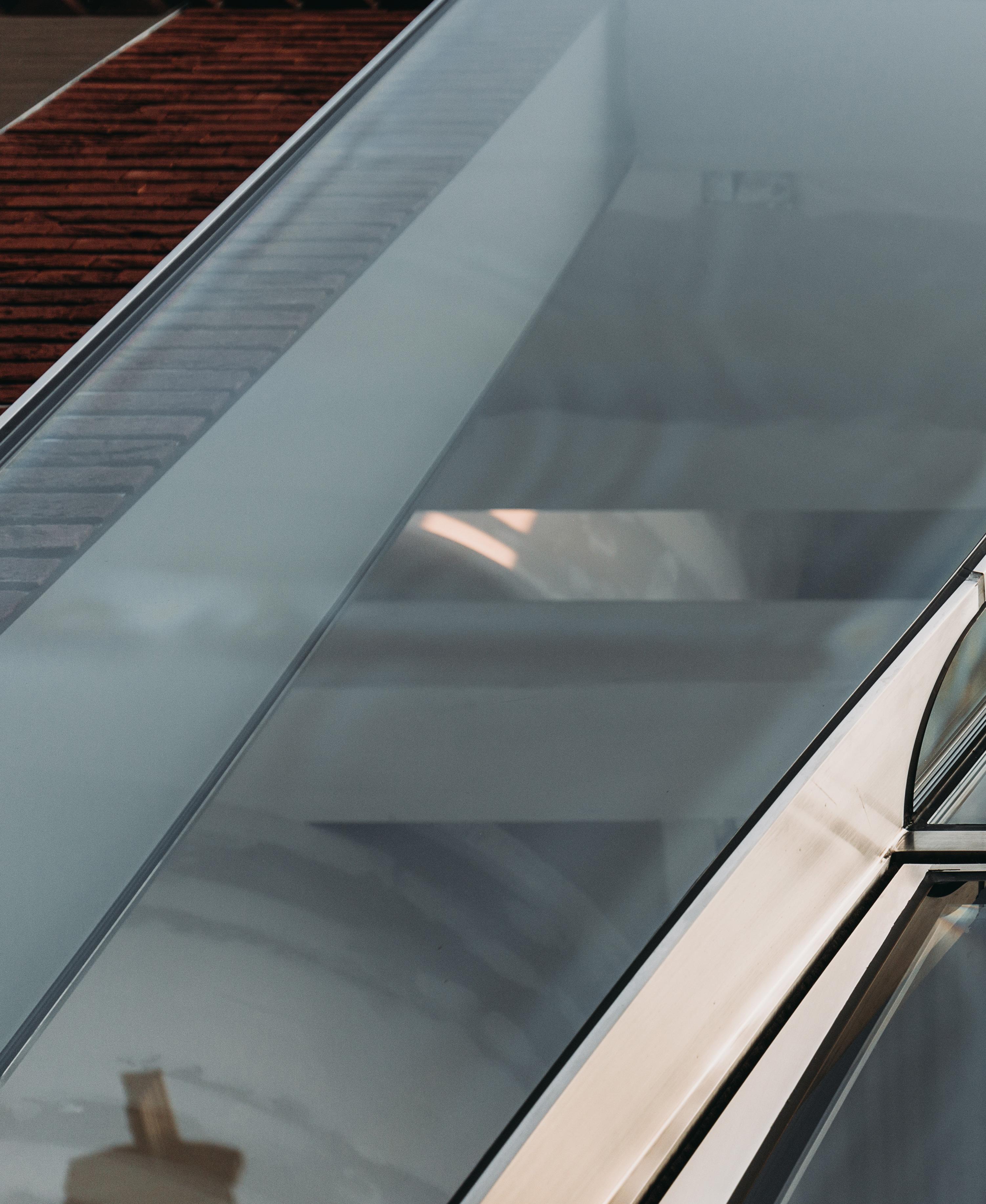
14 minute read
THE LOOKING GLASS: A WATCHMAKER’S CHALLENGE Iris Rombouts - Project Manager and Structural Engineer, Octatube and Chris Noteboom - Senior Structural Engineer, Arup
The Looking Glass: a watchmakers challenge
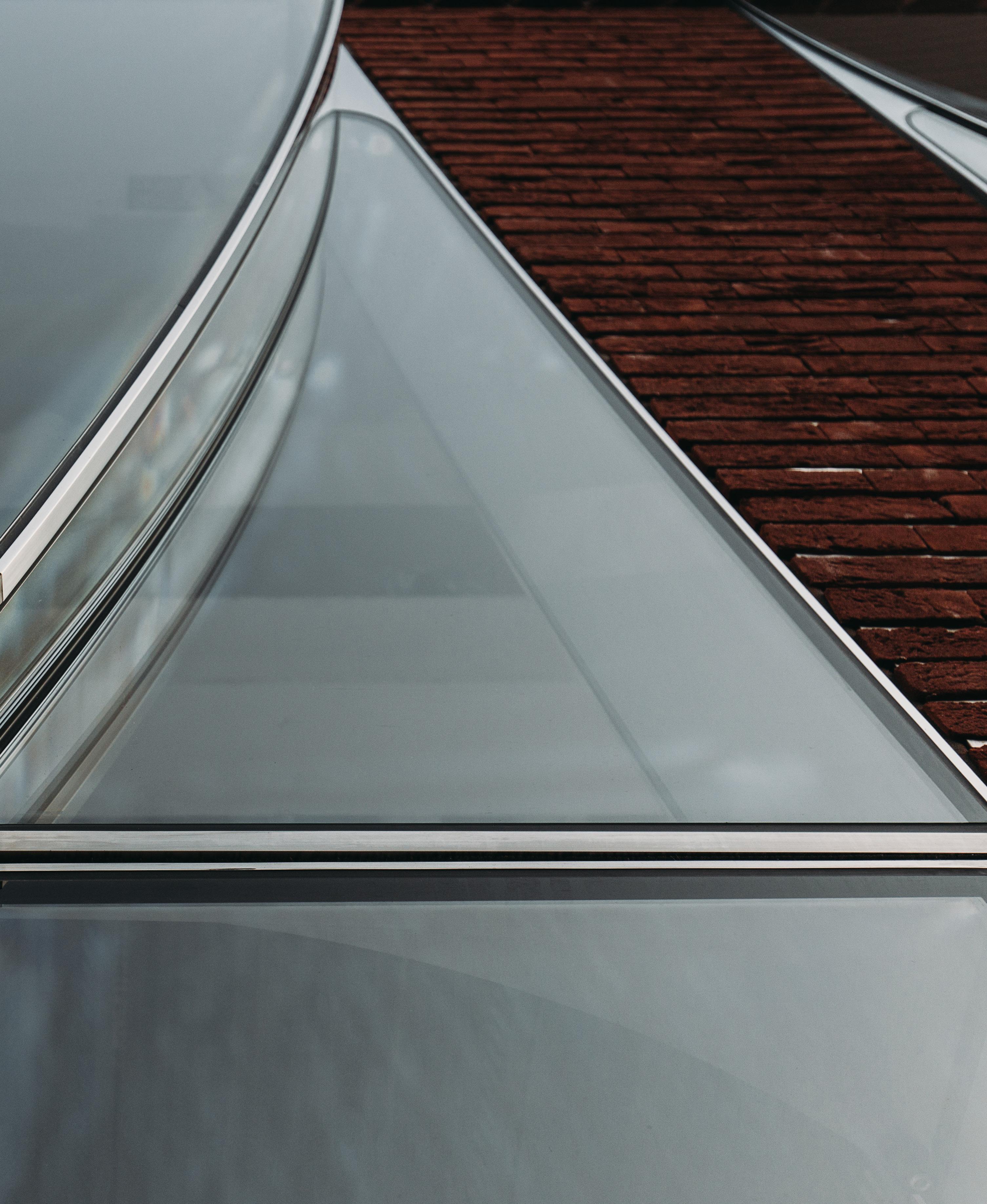
Advertisement
Iris Rombouts, project manager and structural engineer at Octatube Chris Noteboom, senior structural engineer at Arup
On the famous and most exclusive shopping street in Amsterdam, the P.C. Hooftstraat, a new design jewel brightens the day. The façade of number 138, features three curved glass boxes descending from the upper floors, resembling the flow of billowing/frisky fabrics. The glass boxes start flush with the adjacent buildings and cantilever outward while moving upward.
This gradual movement emanates a fluidity you wouldn’t associate with glass.
The 19th century street, filled with traditional town houses, has grown into a place where heritage and design meet each other. The recent, most remarkable developments in the P.C. Hooftstraat have taken place at eyelevel, with contemporary, fresh take on the streets facades. This latest showstopping addition is aptly named the ‘The Looking Glass’.
For this façade, developer Warenar Real Estate brought together a team of specialists of UNStudio, Arup and Octatube. Octatube was invited as a Design & Build partner to do the pre-engineering, technical design, production and assembly.
Geometry
The ground, first and second floor parts of The Looking Glass façade are split in three, in line with the historic identity of the street and thus three horizontal strips of façade can be distinguished. This trichotomy in the façade is not only architectural, but was also used as guiding principle for structure and construction.

The glass parts of the façade consist of three steel and glass boxes covering both ground floor as well as the first floor, with a total height of 8.2 meter and width of 1.8 meter. These boxes have a twisted geometry and make the design of the façade special and distinctive. The boxes have precisely detailed glass connections and custom non-orthogonal steel and glass doors. They start flush with the brick façade but rising up they lean and cantilever outwards (250mm) to become more visible from a distance. Four 3d curves define the main geometry. Two of them define the inside edges of the glass box. They are relatively simple as they are planar and only bend in the plane of the façade. The two front curves are more complex, starting narrow at the bottom to provide space for doors and then bend outwards in the plane of the façade and out of the facade.
During the design process of The Looking Glass, all possible ideas to get the required shape were investigated, such as conventional methods of slumped annealed and chemically toughened. Or simplifying geometry to fit within a cylindrical shape which will be then possible to bend during tempering. There were also experiments with an idea of cold bending techniques during the lamination with potentially additional cold bending on site. Similar concepts are used in the Van Gogh Museum in Amsterdam. Due to the complexity of the geometry, desired visual quality, tight tolerances and the proposed detailing, slumped annealed glass was recommended. Visible clamp plates on the outside were architecturally undesirable which in turn meant on site cold bending was not an option. Cold bending during lamination was considered as too specialized with commercial disadvantages and therefore hot bended glass was chosen.
Detail of modern stained glass window
How adjacents facades fit together
Curved glass
The boxes feature several curved, unique glass panels. Initially, the design included twisted glass elements above the doorways, with a minimum radius less than 0.5 m, thus highly curved. However, while these elements are theoretically possible to produce, they would pose a significant risk to the project program and also a significant increase in costs. The geometry was modified in such way that only single-curved glass elements were needed. The doors were made flat and the twisted element above was replaced by one flat element and one curved element. An almost invisible glass division was introduced on the second floor. This ‘cut’ reduced the height of the panels with 3 meters: from more than 8 meters to more than 5 meters. In addition, production tolerances were reduced and minimalist detailing improved. Another advantage of the ‘cut’ was that the top part of the glass boxes now consists only of flat elements. The largest glass elements are the front panels of 6 meter in height, starting narrow at the bottom and become wider as they go upwards and protrude. They contribute their weight to the narrow base beneath.

The three glass boxes consist of panels of laminated, annealed low-iron glass with curved and straight lines. The choice for low-iron glass was dictated by the wishes of the client wanting the façade to be as transparent as possible. Not choosing low-iron glass would have given a greenish glow, detracting visual
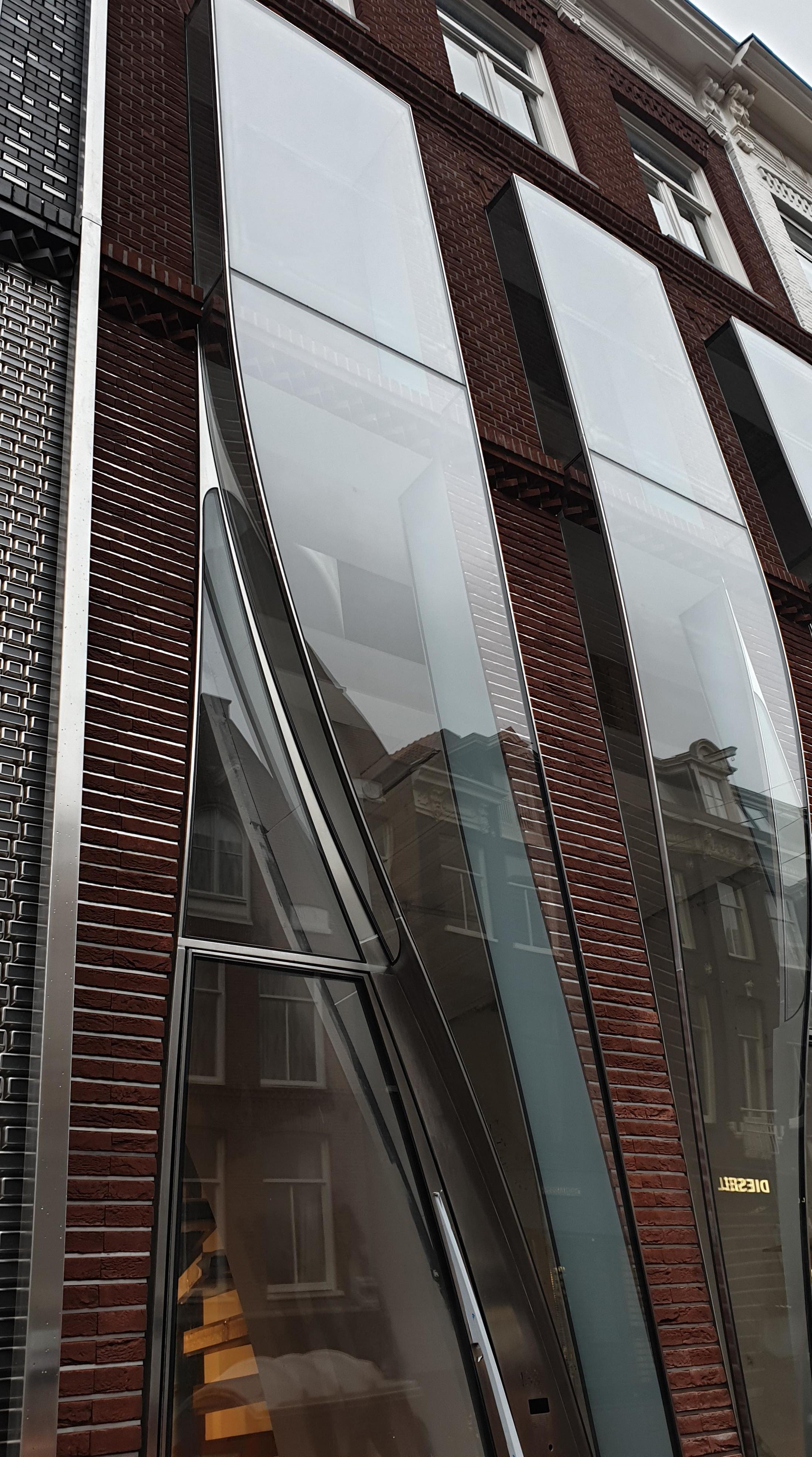
Section detail in design phase
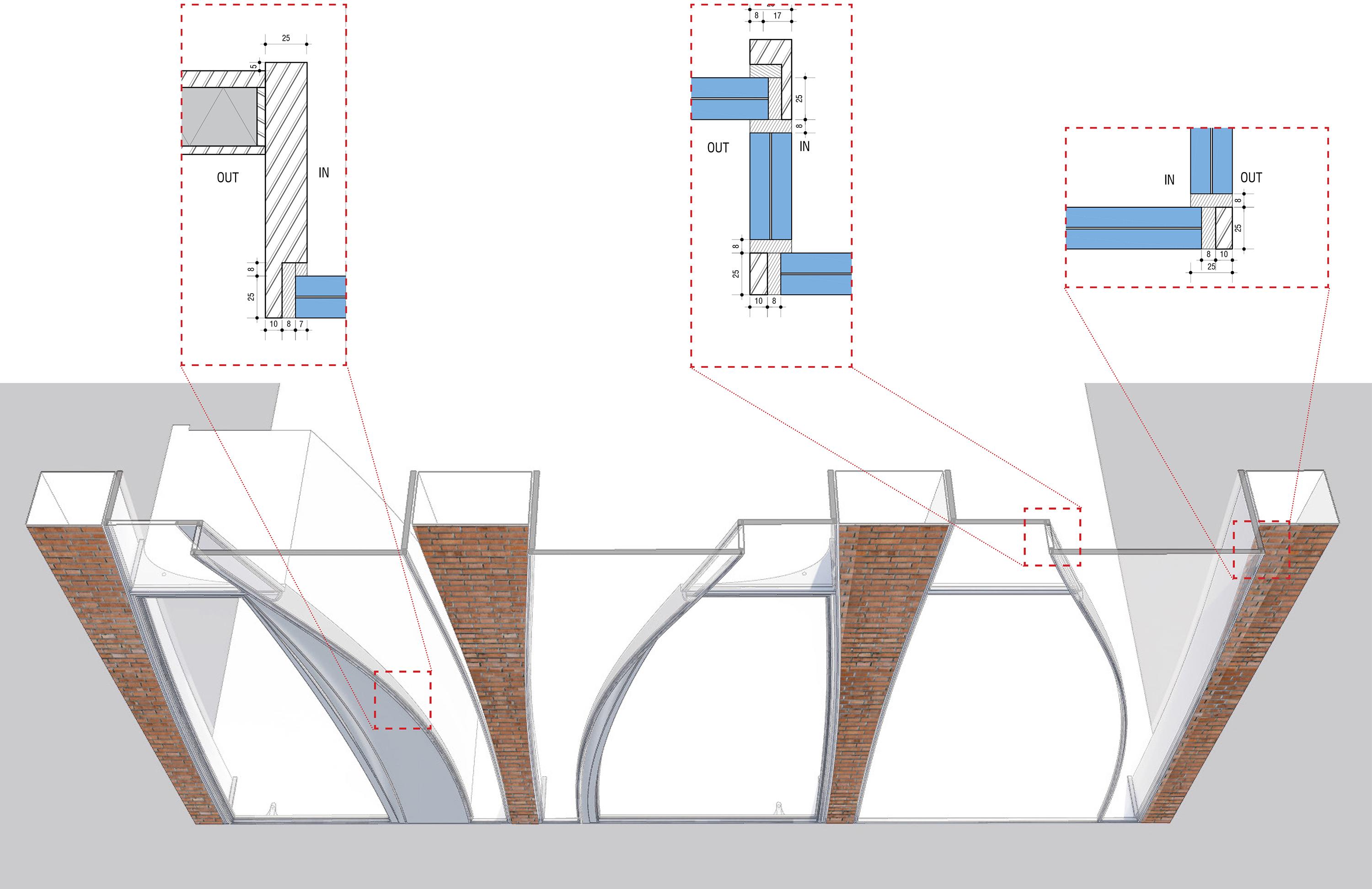
quality. Arguments to choose for laminated glass where the minimal dimensional tolerances, strength and rigidity. Burglary resistance and throughfall safety were aspects as well. Annealed glass was required due to manufacturing method and aesthetically desired, some changes were needed to decrease the maximum temperature difference between the clear outside and shade inside glass. The risk of thermal breakage of the annealed side panes is reduced by gluing stainless steel plates to the glass elements, acting as cooling ribs and changing the color of the pre-smearing to light gray. On some of the stainless steel plates two studs are welded making the connection to the main structural steel.
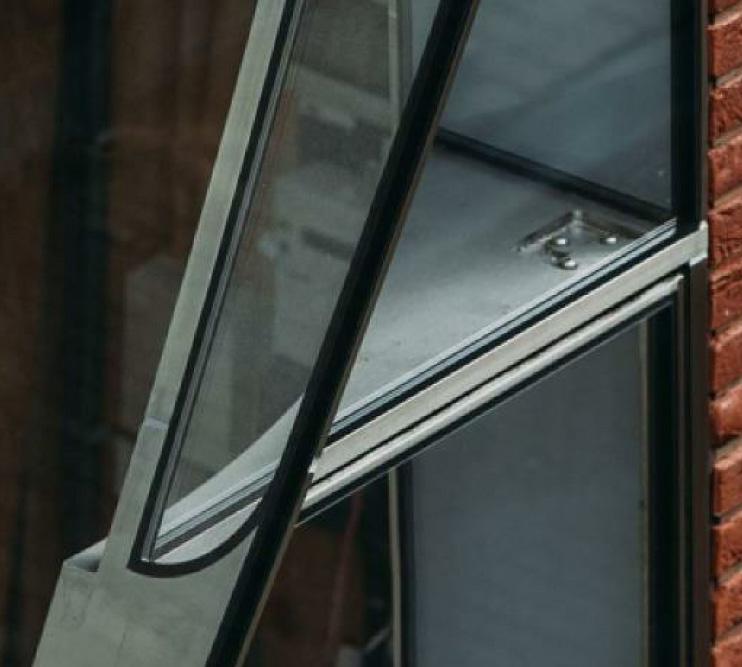
The summer in Amsterdam in 2019 was a hot one. When an air temperature around 40 degrees was measured, temperature measurements on the glass where carried out to compare calculations with reality. All measured values where within the calculations, given confidence for the rest of the year relating to the risk on thermal breakage.
A detail photo of the top door connection
Curved glass Detail of one of the custom-made doors
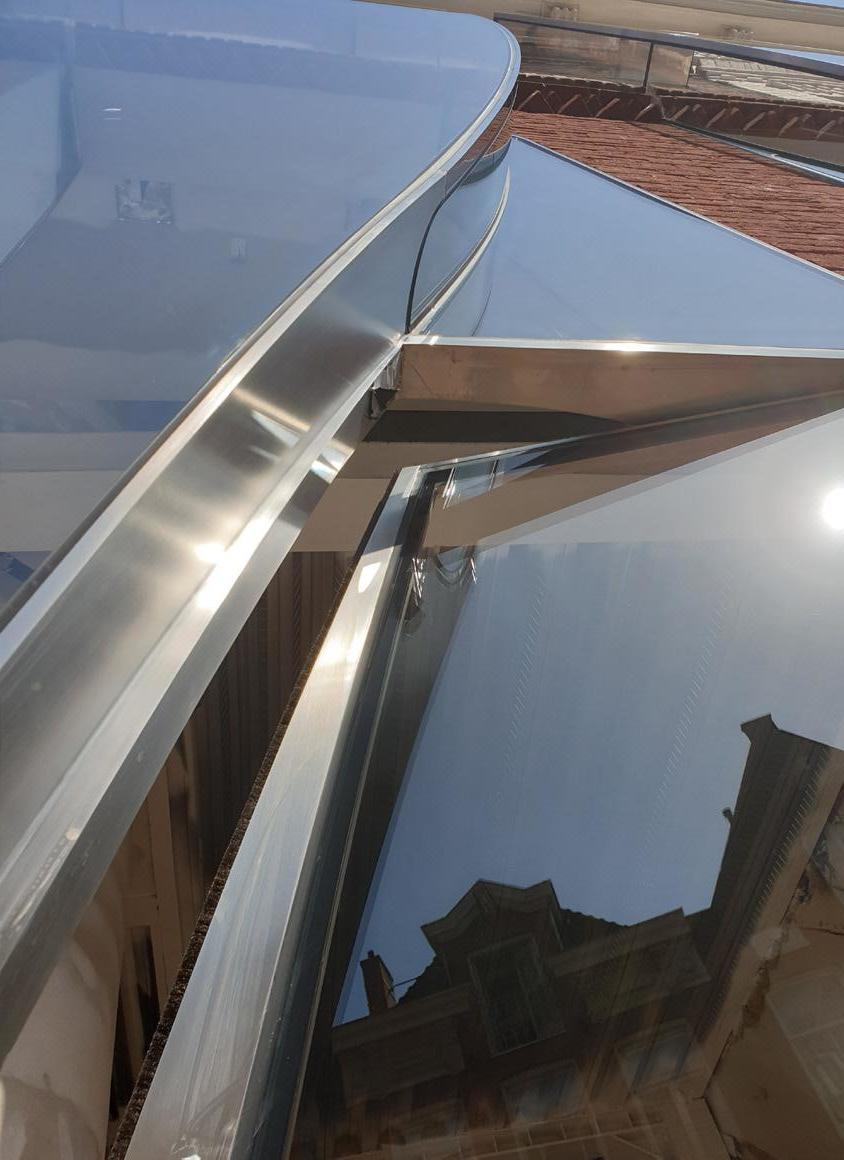
Picture frame
A so called picture frame concept has been applied, allowing to pre-assemble the glass boxes. The frame is made of rectangular hollow sections, measuring 120x60x8 mm. The glass is connected (by silicone) to this steel frame and the steel frame is connected to the brackets. The supports and brackets for the doors are also connected to this frame. After positioning the frame at the construction site and connecting the brackets, a few extra connections in between ‘picture frames’ were made as well, to specifically increase stiffness for the door connections with long brackets.
Modern stained glass windows
Slender stainless steel elements wrap all around the glass define the shape of the glass boxes and provide extra stiffness around door openings. They are also used for connections. The risk of thermal breakage of the annealed curved glass panels that are partially inside and partially outside is minimized by gluing stainless steel plates to the glass elements, acting as cooling ribs.
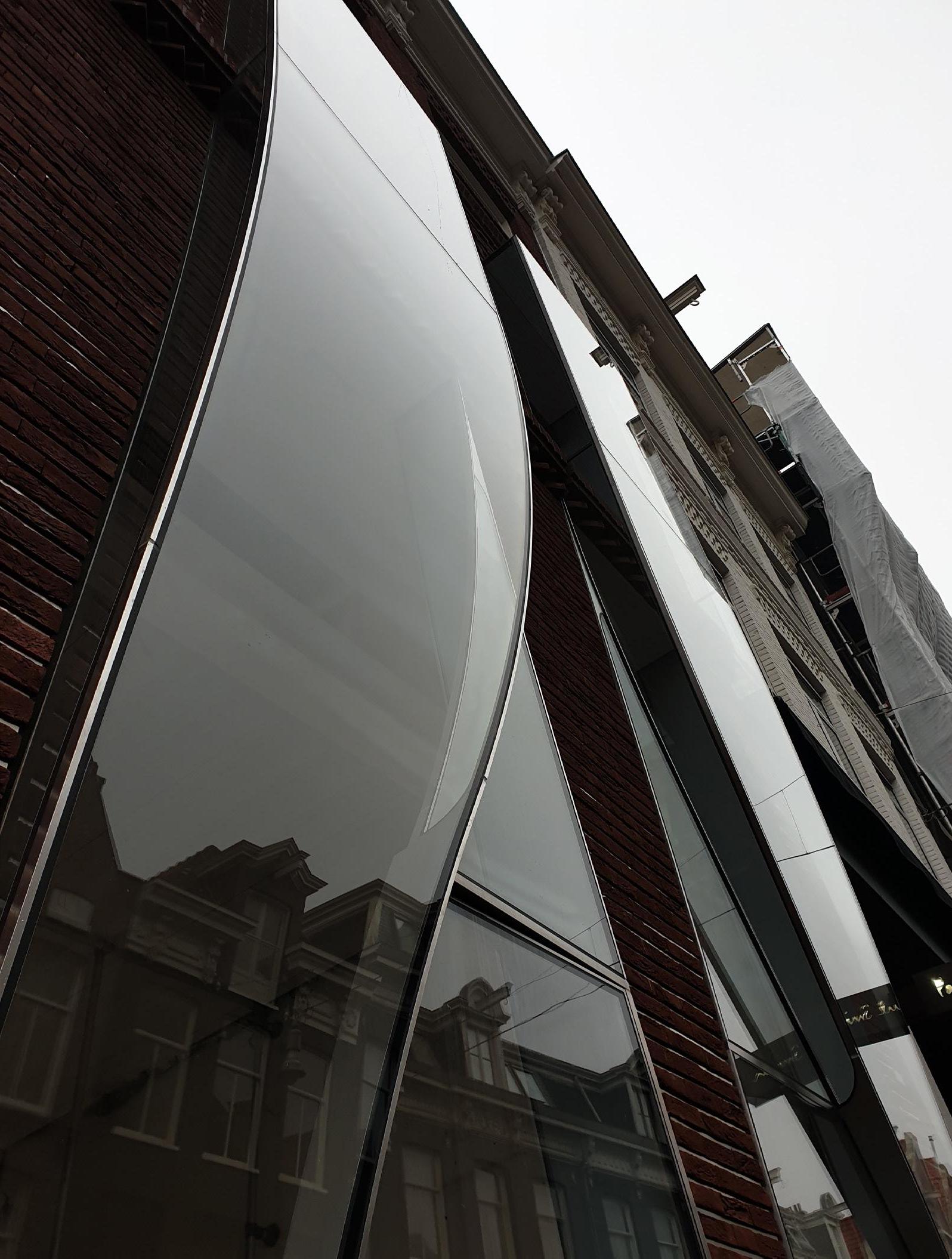
A lot of moulds were needed to produce the stainless steel elements. To be able to make the stainless steel edge, the steel was cut out in a curved way and then rolled so that it could be made double-curved. The resulting profiles were placed next to the glass, curved as well, within a millimeter of accuracy in the corner detail. The edge between the glass and the stainless steel was structurally cemented.
The stainless steel and glass boxes are connected to the picture frame, fully assembled in the factory of Octatube in Delft (Netherlands). A modern version of stained glass windows, but now curved and with stainless steel and structural silicone.
Custom made doors
The façade contains two oversized structurally bonded doors made of laminated heatstrengthened glass with structurally bonded stainless steel framing. They are integrated into the main frame of stainless steel elements that support the glass façade. The glass box on the right has fixed glass elements but with a similar geometry as the doors. The glass box in the middle has the same stainless steel sections bonded to the static glass elements, but also features an extra stainless steel door frame with structurally bonded door. The glass box at the left features a smaller door to provide space for the door hardware to accommodate the facilities of the top floor apartment, such as an intercom and mail box. To meet the building regulation, the curves of the façade were optimized for the required minimum free width
Drawing of all glass side elements on temporary supporting structure with temporary supports to the main steel structure
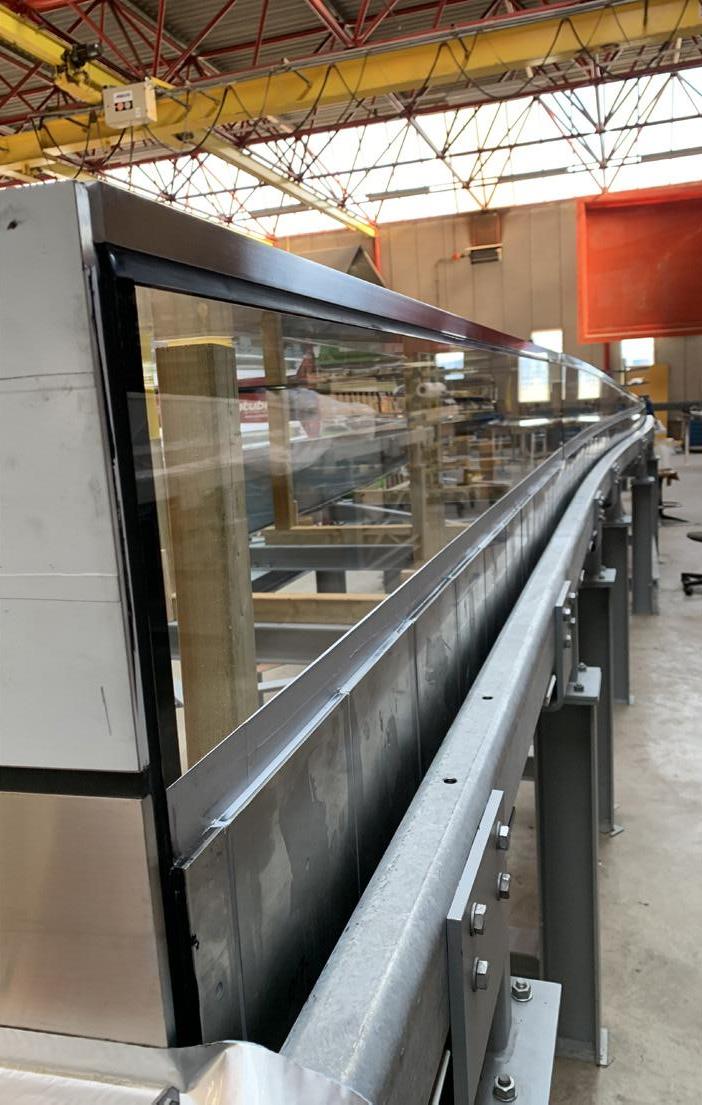
Drawing of temporary supporting structure with all glass panes applied with highlighted front element Curved side of a glass box with stainless steel cooling ribs
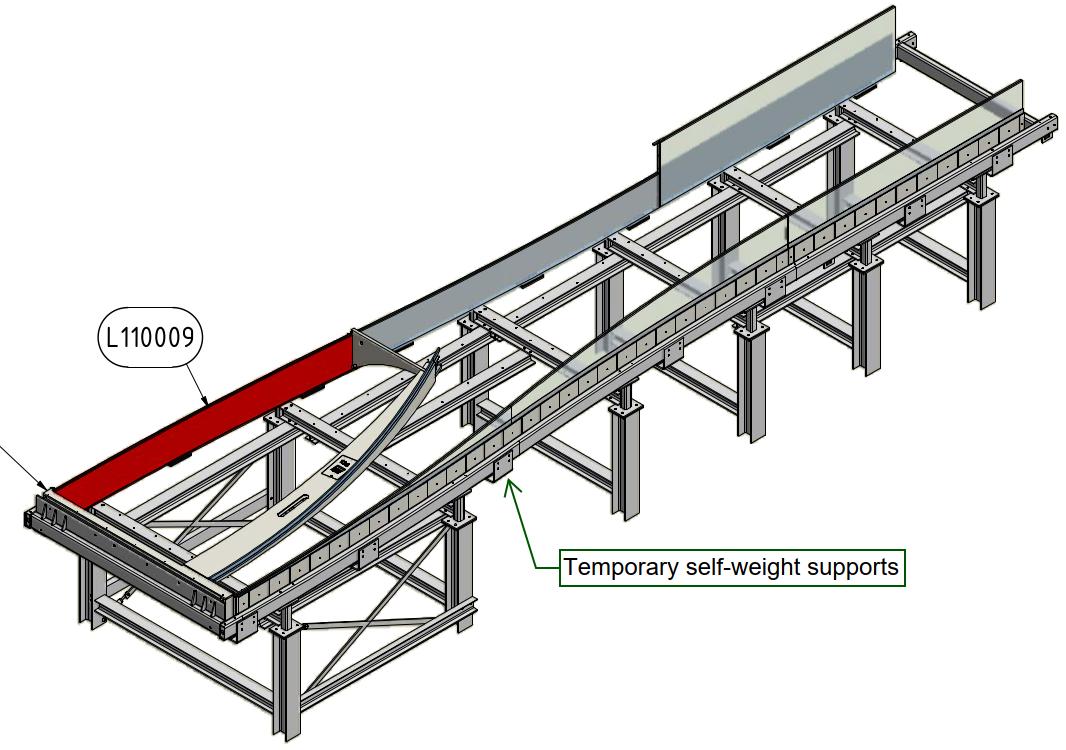
Wrapped up for protection during transport
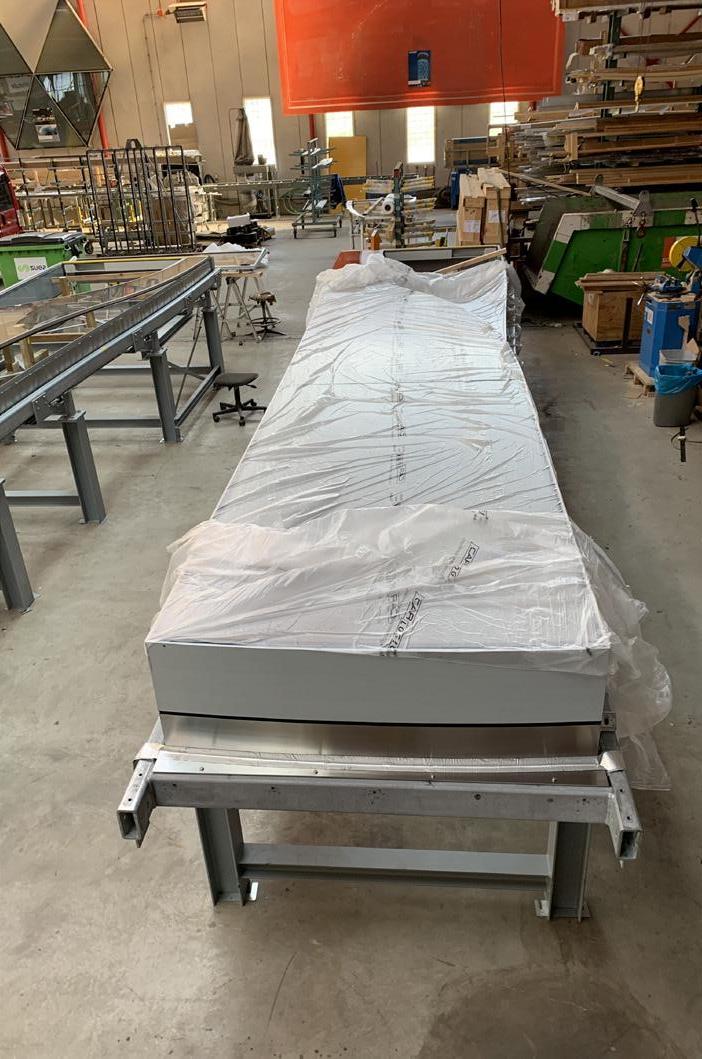
and height to enter the store and apartment. The shop door measures 2.9 m high and 1.5 m width in closed position.
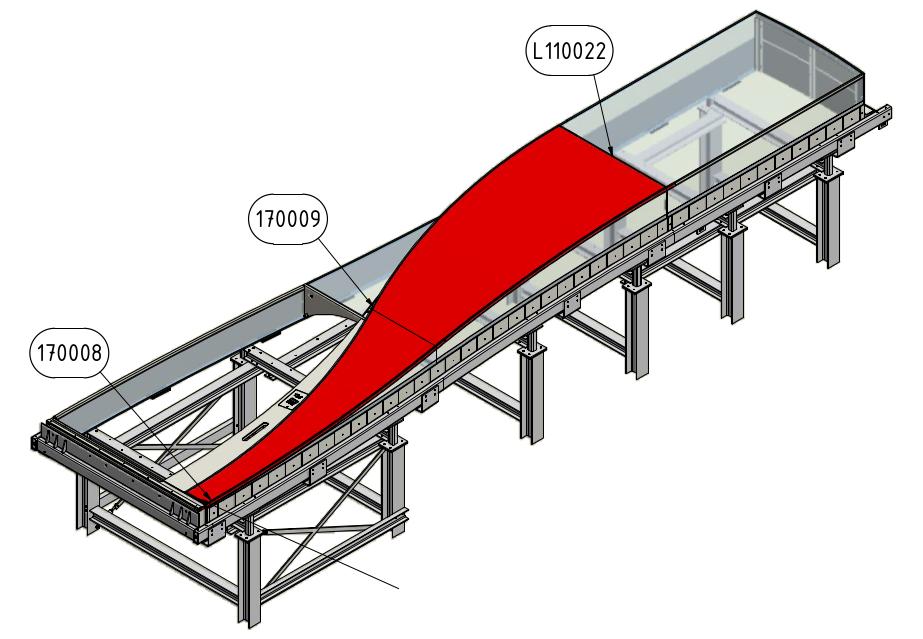
As minimalistic detailing was pursued by the design team, the door frame and all its hardware was integrated into the load-bearing stainless steel frame. Also, the top pivot is hidden in the 25mm thick horizontal plate which is connected through a glass joint of 10 mm to the main steel. All structural stainless steel elements were produced within a tolerance of 2 mm so the door can open and close smoothly. All the stainless steel parts have a very fine grade finish without a shining look. To reach a high level of visual quality using structural bonded connections, all joints were pre-smeared with an overlap to contain a visual smooth line of silicone.
An important part of the hardware design is the custom-made door handle on both door leaves. The door handle is curved and varies in section size from start to end in fluent lines. It is custom-designed and produced for this project.
Structural silicon
The three glass boxes are entirely held together by structural sealant. Connections between curved glass elements are all glued in combination with stainless steel elements for edge protection and emphasis on the curved geometry. No bolts were used.
Pre-assembled horizontally
Narrow part at the bottom of the large front panel

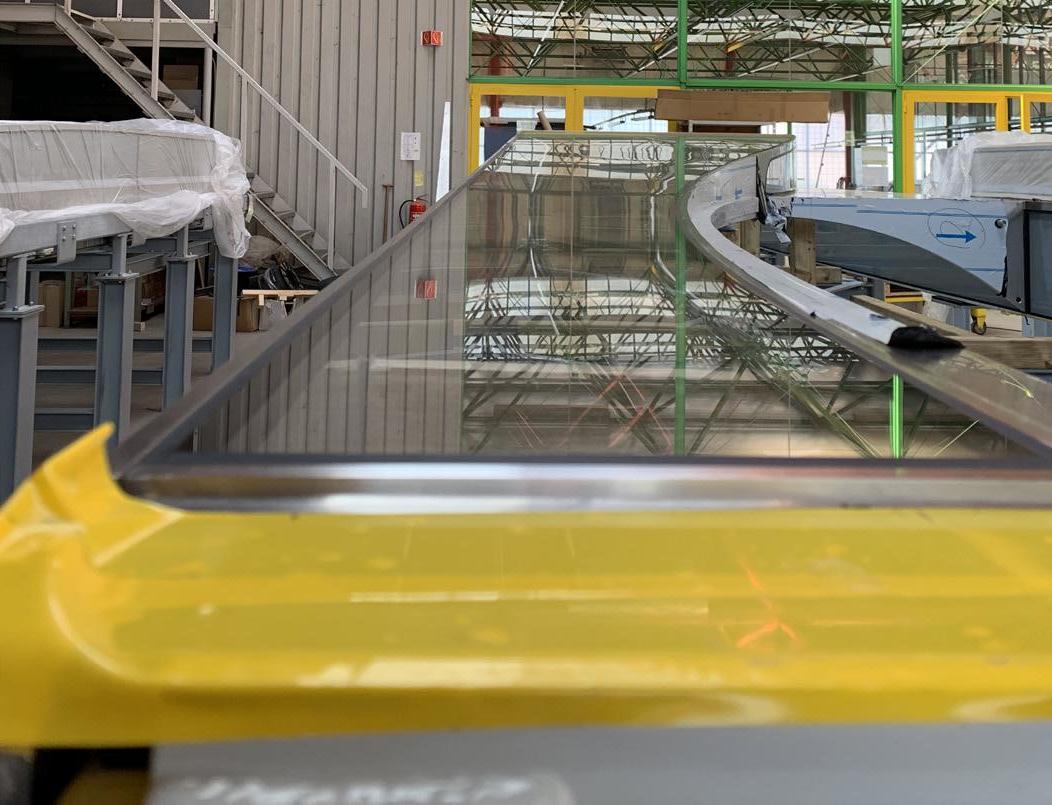
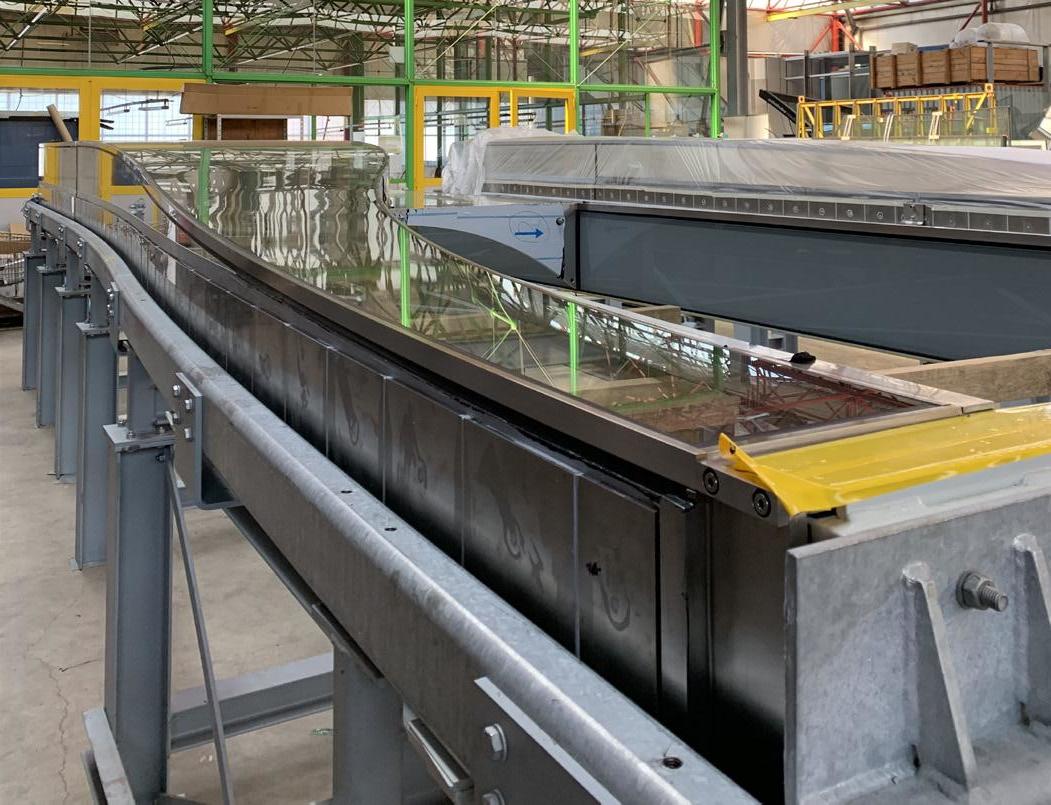
Assembly structure on site in horizontal position

The glass boxes are only supported vertically at the bottom. Horizontal supports in and out of the plane of the façade were designed at the first and second floor, matching the glass divisions. The upper panel slightly cantilevers outward, creating a tensile load on the silicone bonding. The glass-glass corners with sealant in between produced black edges. One of the reasons the architect wanted to frame the glass entirely with stainless steel.
A lot of temporary elements made out of POM were made to keep the glass and stainless steel in the right place and at the correct distance for structural gluing. All structural joints were glued in multiple steps: first create structural connections at a recessed location, then remove the temporary POM elements and glue the visible part of the joint in one go.
Due to the minimalistic detailing, desired quality and geometrically complex glass shape, all three glass boxes are preassembled in the factory of Octatube in Delft (Netherlands). By doing this, all glued details were applied under well monitored conditions.
Since each glass box has a width of 1.8 m and height of 8.2 m, it was no option to preassemble the units vertically. The glass boxes were therefore pre-assembled horizontally and rotated 90 degrees vertically on site. This resulted in extra analyses of stiffness of dead load supports. The two doors were separately produced and brought to site in a later stadium.
Auxiliary frame
Octatube designed a custom steel auxiliary frame that functioned as a stiff mould around the glass boxes, making sure that the structural sealant and glass didn’t experience too heavy loads during transport and hoisting. The structure surrounds the glass boxes on all sides and is mechanically linked to the picture frame of the glass boxes.
After assembly in the workshop in Delft, the boxes were carefully packed with thick white plastic as an extra protection during transport, hoisting and application of the masonry in a later stage.
The glass boxes were transported horizontally in their auxiliary frames to the P.C. Hooftstraat. On site they were rotated and vertically mounted into the façade: one of the most spectacular challenges of this project. Two cranes handled the rotation of all three boxes with an elaborate pulley mechanism at the top and bottom of each box. The rotating had to be done slowly to gradually control the self-weight of the glass box: going from a horizontal load to a vertical load before being mounted in the superstructure.
Glass box with assembly structure in 30 degrees position

All glass boxes installed with two assembly structures still in attached Glass box with assembly structure in 60 degrees position
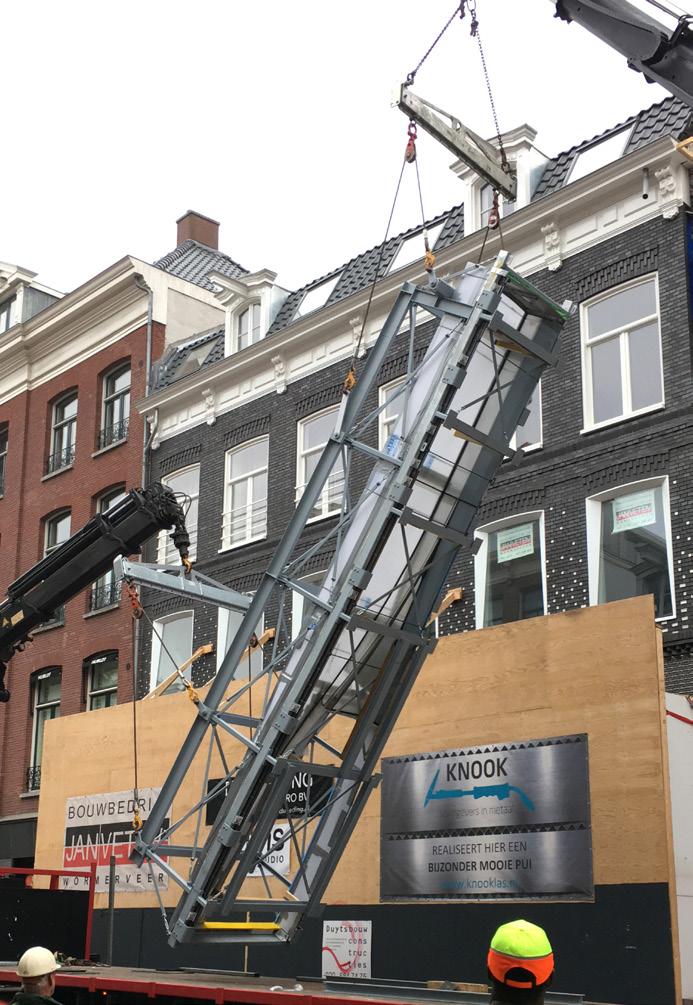
All glass boxes installed, still protected

The rotation of the boxes only took a few minutes. For every box the total installation time including rotation, lifting and connecting to the main structure was just 1 hour. Once the glass boxes were connected to these brackets, the auxiliary frame was removed. After months of preparation, the entire assembly was done in just 1.5 days.
In many ways ‘The Looking Glass’ was a job for a Swiss watchmaker. It all came down to the exact millimeters – from the silicone bonding to the glass and steel connections as well as the steel frame and the rotation on site. Frequent collaboration throughout the whole project between all parties resulted in successful delivery with no glass breakage during the construction phase. One of those projects that showcase how teamwork, diligence and courage can lead to a showstopping result. It took years to design, months to assemble in factory, but only 2 days to construct on site.

For more information, please read the Challenging Glass Paper written by Iris Rombouts (Octatube) and Chris Noteboom (Arup). This article is an abstract of this paper.
Iris Rombouts is project manager and
structural engineer at Octatube, a Dutch based Design and Build company specializing in bespoke building structures with an emphasis on advanced applications of glass and steel. She has a fascination for glass calculations and complex structural designs and is therefore involved in the company for 6 years. She started as a structural engineer but grew into a combination with also the project managers role and has done many projects for Octatube. For example a waving canopy in Tilburg, a complex gridshell roof over a monumental courtyard in The Hague, a full glass façade with hanging fins and a standing façade in Dublin and so on. For the PC Hooftstraat facade, she was the structural engineer and the project manager.
Chris Noteboom is structural engineer at Arup and lectures at the TU Delft
about structural glass. He is specialized in complex glass, steel and timber structures. In Arup he is part of the Arup Glass Network that spreads all across the world to share knowledge and advise on projects. Before Arup he worked at Octatube, a specialized façade contractor in the Netherlands. Past glass projects Chris worked on include the Markthal Rotterdam and the New Entrance of the Van Gogh Museum in Amsterdam. For the PC Hooftstraat facade, he was involved from the first sketches to the final construction and acted within Arup as structural engineer and project manager.
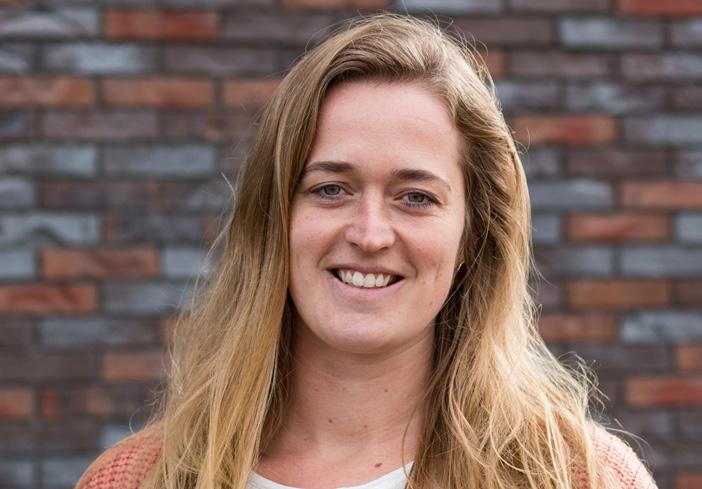

