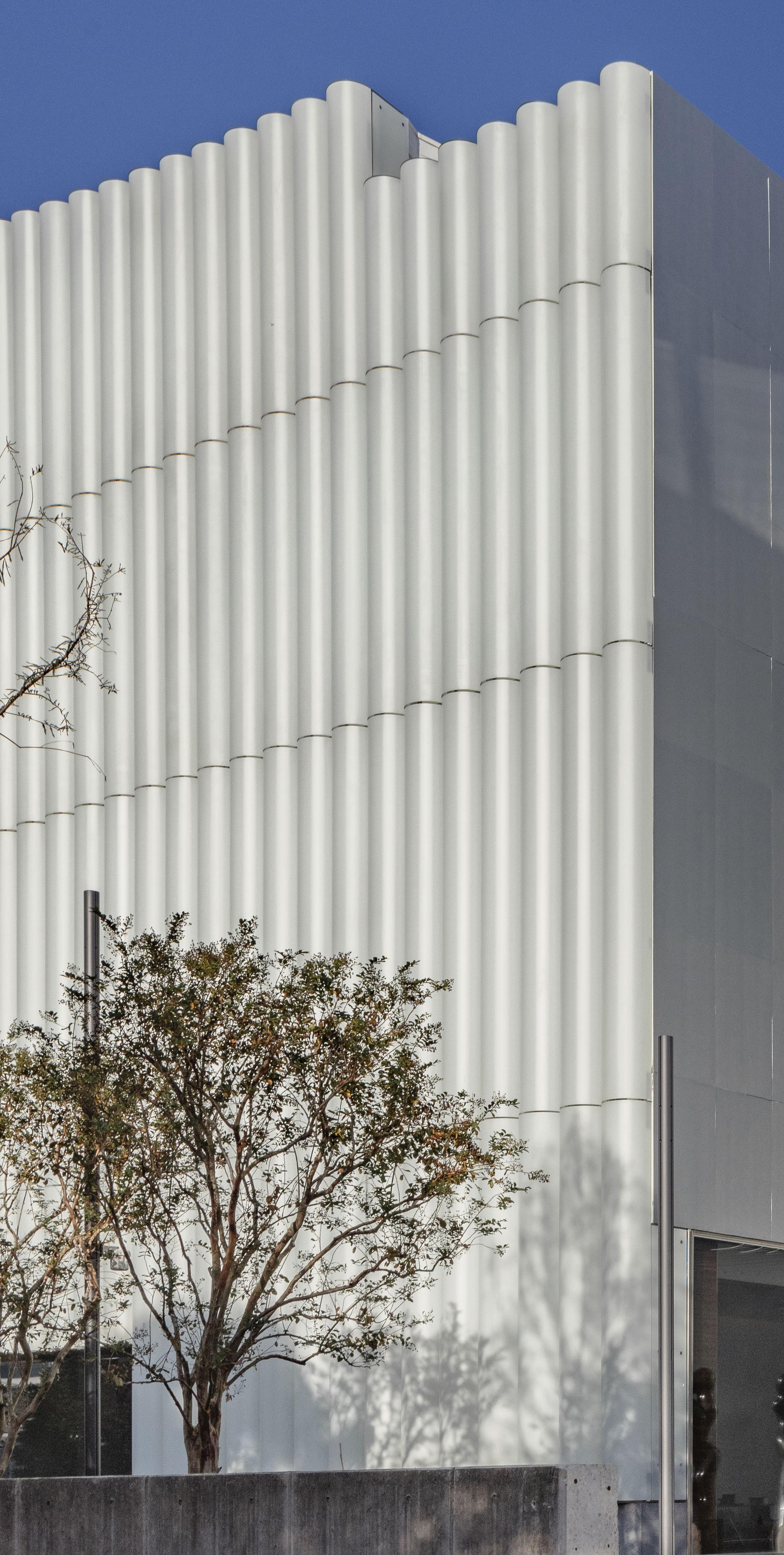
12 minute read
MUSEUM OF FINE ARTS IN HOUSTON: FAÇADE WITH 1,100 HOT-BENT GLASS TUBES PLAYS WITH DAYLIGHT Jürgen Wax – CEO and Stefan Zimmermann - Senior Branch Manager, Josef Gartner GmbH
Museum of Fine Arts in Houston
Façade with 1,100 hot-bent glass tubes plays with daylight
Advertisement
Jürgen Wax (CEO Josef Gartner GmbH) Stefan Zimmermann (Senior Branch Manager, Josef Gartner GmbH, Branch Würzburg)
Photo: Richard Barnes

In November 2020, the Museum of Fine Arts in Houston was officially opened to the public. A state-of-the art glass façade provides precise daylight control for the newest building on the museum’s campus.
The Nancy and Rich Kinder Building has been clad with 6-metre-long hot bent glass tubes. These wave-shape half tubes made of translucent laminated safety glass characterise the appearance of the museum. Above all, they generate diffuse and shadow-free light for the works of art and reduce the amount of energy entering the building. This effect is intensified by the curved roof featuring vertical glazing with natural light slipping through the atrium into the central exhibition rooms.
The American architect Steven Holl had set highly demanding lighting requirements for the façade to avoid artificial light as far as possible and to allow for homogenous illumination of the exhibition rooms with natural daylight. Façade specialist Josef Gartner GmbH, member of the Permasteelisa Group, was able to demonstrate in a range of testings the requested light transmission and structural characteristics of the curtain-type tubular glass façade. To fully respect the architectural intent, fixings were made invisible from the outside and horizontal and vertical joints minimized. The wind loads vary considerably and the space between the glass tubes and the load-bearing external walls should be accessible at all times for maintenance and cleaning work.
From the outside, the building is almost completely wrapped in translucent glass (“Cool Jacket”). The twelve areas clad with semicircular glass tubes are separated by seven entrance and access areas, which are cut into the building complex to create interior courtyards. The roof of the building consists of a geometric free form featuring a variety of irregular concave segments. The transitions of these segments are closed by curved vertical glazing (“clerestory”). Photo: Richard Barnes

Kinder Building by Steven Holl featuring undulating glass tube façades and curved skylights
The 25-metre-high Kinder Building is one of the three new buildings on the Museum of Fine Arts campus, which, together with the redevelopment of the Sarofim Campus, will cover a total area of more than 60,000 square metres. With its vertical tubular glass cladding the trapezoidal concrete building, provides a complementary contrast to the Law Building designed by Mies van der Rohe in 1958 and
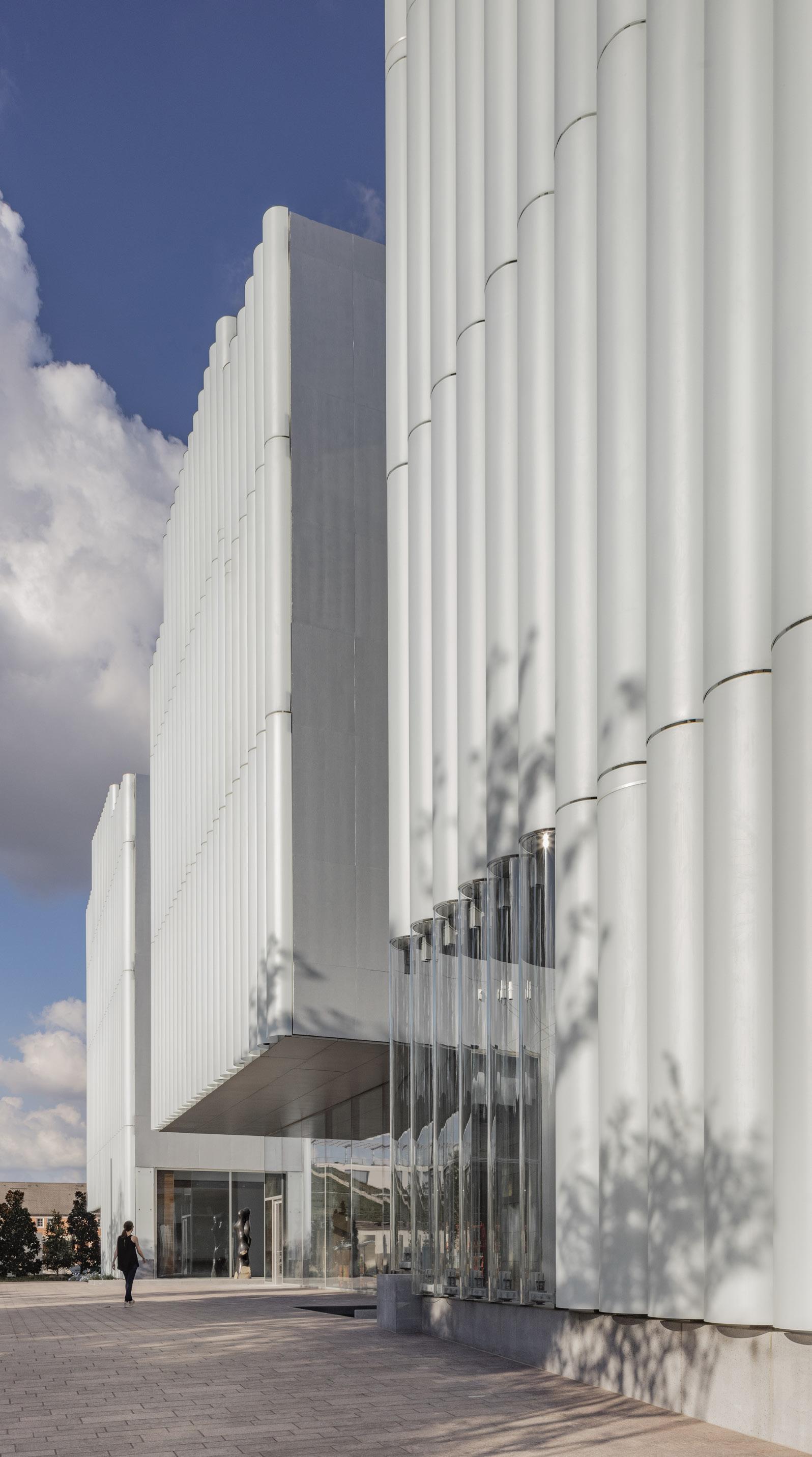
Photo: Richard Barnes
1974 and to the stone façade of the Beck Building constructed in 2000. The building is accessed via seven entrance areas, which slice the perimeter in the form of courtyards with gardens, thus linking the building with the surroundings. With the courtyards and the glass façade, Steven Holl wants to foster the exchange between the museum and the surrounding park landscape. The rooftop is modelled on the billowing clouds of the Texas sky. The many irregular concave roof segments are followed by curved translucent vertical skylights.
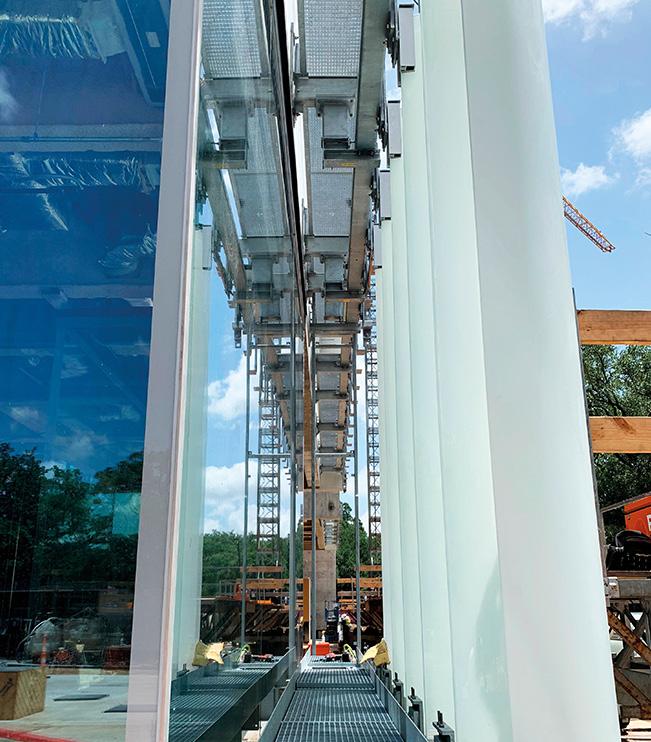
On a total area of 17,000 square metres, the Kinder Building offers an exhibition area of around 9,300 square metres as well as a theatre with 215 seats, a restaurant, and a café. On two floors, circling a light-flooded atrium, the Museum of Fine Arts intends to comprehensively present its prestigious international art collections of the 20th and 21st centuries for the first time. One focus is put on American painting of the post-war period. Several sculptures in front of the building also take up the central theme of light, such as two tunnels with light installations or six reflective water surfaces on the building.
Photo: Knippers Helbig
Photo: Richard Barnes
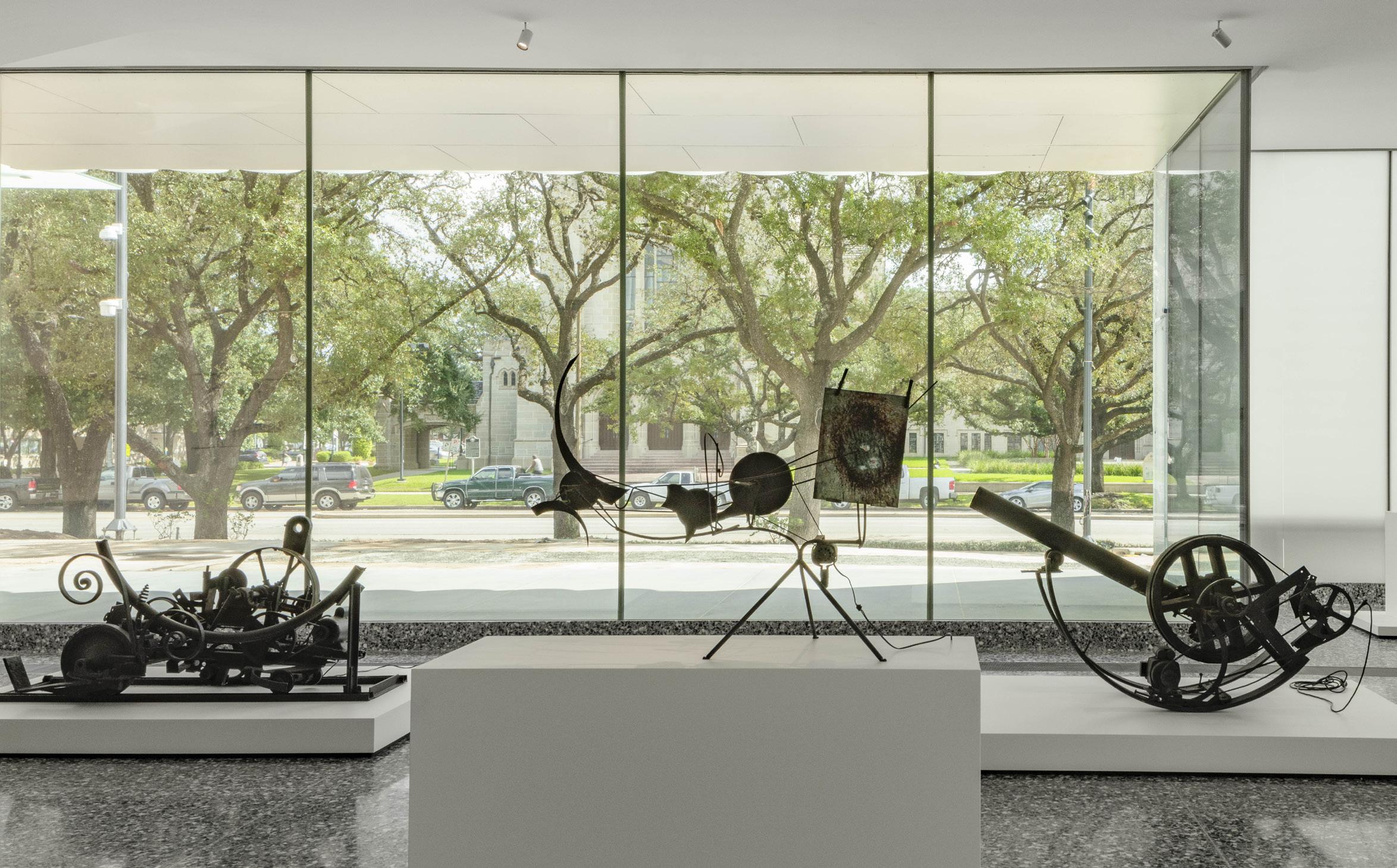
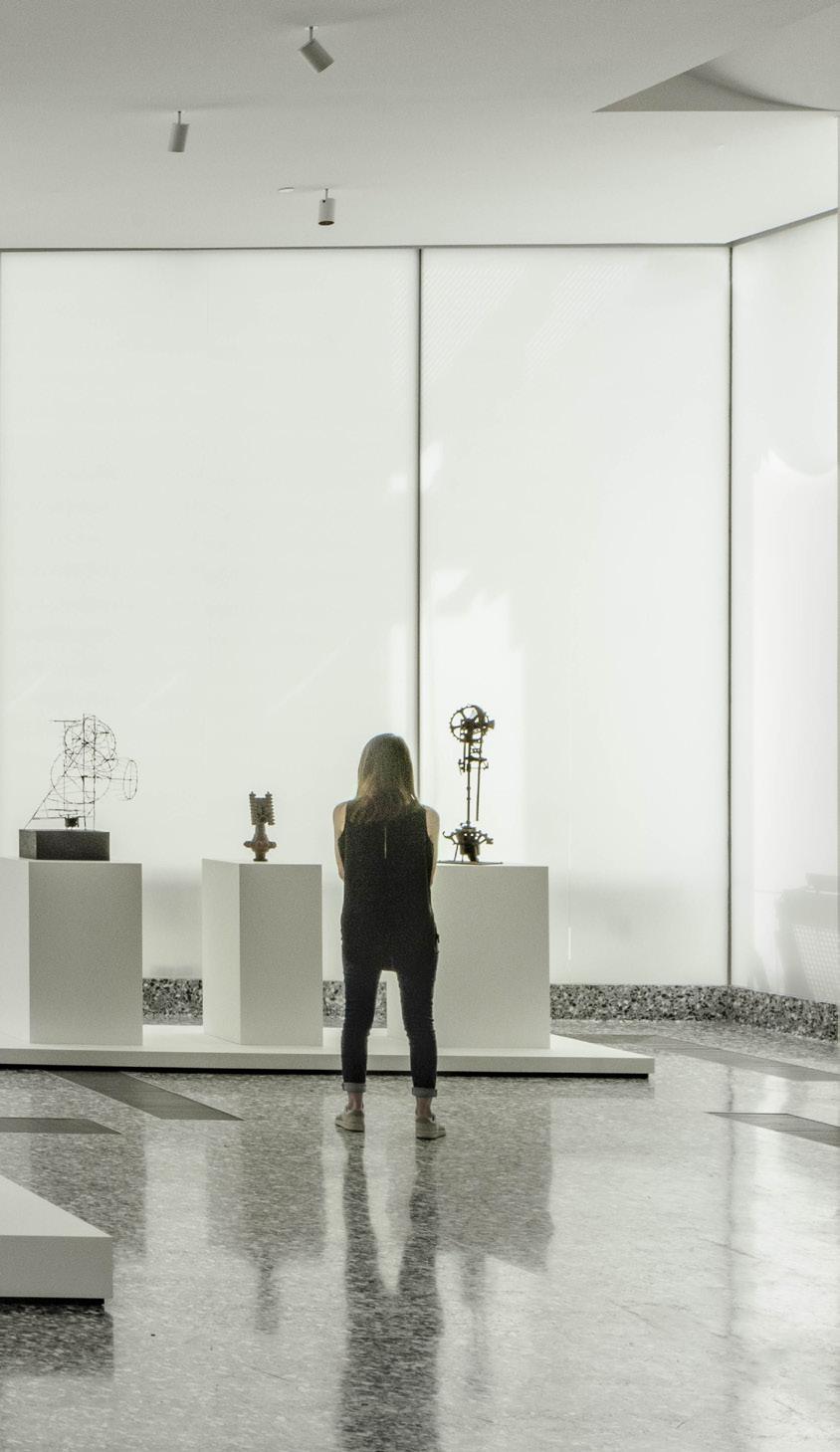


Photo: Sean Fleming / smfleming.com Photo: Richard Barnes
Numerous mock-ups and tests for structural analysis and lighting control of the glass tubes
The so-called Cool Jacket façade (4,700 square metres) consists of 1,100 translucent glass tubes, up to 6 metres tall, which were manufactured in a tight radius of 330 mm using the force of gravity bending process. Since little experience is available for such types of façade, numerous mock-ups and test setups were required for the glass tubes, in order to achieve the function as requested by clients and architects. Depending on the season and weather conditions, the sunlight changes a lot in Houston. The geometry of the building added to the challenge of exactly calculating the individual museum areas.
Glasses with different diameters, translucent interlayers and etching degrees were produced as mock-ups. As the wind loads on the façade vary from 40 psf to 100 psf, glass thicknesses of 2 x 8 mm and 2 x 10 mm were used in accordance with the structural requirements and the span width. Based on the mockups and the lighting values, tubes with 180° circle segments and a radius of 381 mm were selected. The two low-iron glasses were laminated with four translucent PVB films (each 0.38 mm thick). The surface of the outer glass pane has undergone etching. In particular, the infrared radiation of sunlight is absorbed by the glasses and dissipated via a rear ventilation system.
The narrow bending radius and the length of the glass tubes could only be produced by force of gravity bending. The two glasses were first cut and then bent pairwise on steel templates in the bending furnace. In the autoclave, they were laminated with the PVB films.
In order to accurately calculate the amount of daylight in the museum’s exhibition areas,
Project Data:
Owner
Museum of Fine Arts, Houston, TX
Architect
Steven Holl Architects, New York, NY
Client
McCarthy Building Companies, Houston, TX
Façade Consultant
Knippers Helbig, Stuttgart a mock-up on a scale of 1:2 was built. For visual assessment, a large scale mock-up with 6-metre-tall glass tubes was built in Houston in 2016. The internal stresses in the curved glass were then measured using a large scale 4-point bending test and the maximum surface and edge stresses were determined.
Over a period of five months, the temperatures of the glass and in particular the temperature differences between the inner and outer surfaces were measured at 90 measuring points on the large-scale mock-up. Ultimately, these individual tests were decisive for the planning of the tubular glass façade, as simulations often proved to be too inaccurate for precise daylight control. A decisive criterion has been the uniform glass quality, for which comprehensive quality controls with regular checks have been developed.
The dead weight of the glass tubes is carried by steel support brackets. For the absorption of horizontal loads, aluminium extrusions are bonded to the glass tubes in the corners, which are bolted to the steel support brackets. The brackets transfer the load into a hot-dip galvanised steel substructure, which forms a space between the steel concrete wall and the glass tube façade that can be walked on for maintenance and cleaning purposes.
Roof glazing and inner courtyard façades
The curved vertical roof glazing has a total area of approx. 500 square metres and connects the individual segments of the roof surface, which are arranged at different heights. The substructure of the glazing consists of helix shape-bent upper and lower aluminium profiles and features interposed vertical posts. This creates a geometric freeform surface into which the flat glass is cold-bent.
The inner courtyards are clad with 23-metrehigh stick-system façades made of steel. The 2,300 square metres of courtyard facades were glazed directly onto the steel construction (welded from T-profiles) via an EPDM support gasket.
Different glass build-ups were used for both the roof and the inner courtyards. Depending on the use of the rooms behind, partly transparent and partly translucent glazing was installed to allow for precise control of the incidence of daylight.
As a facade specialist, Josef Gartner GmbH creates engineering solutions in aluminum, steel and glass, helping the world’s best architects and aspiring builders realize their ambitious ideas.
For the past 150 years, Gartner has shaped the skyline of metropolises all over the world - from the Elbphilharmonie in Hamburg to the Academy Museum of Motion Pictures in Los Angeles, California. For large-scale and complex construction projects, Gartner is the first choice for high performance façades, characterized by innovative German engineering, technical precision, and the highest quality.
With its headquarters in Gundelfingen, Germany, the company was founded in 1868 as a family business, and in 2001 Gartner became a member of the Permasteelisa Group. As part of the Permasteelisa Group, Gartner profits from a worldwide network of specialists and has a strong presence in various markets with wholly-owned subsidiaries or offices.
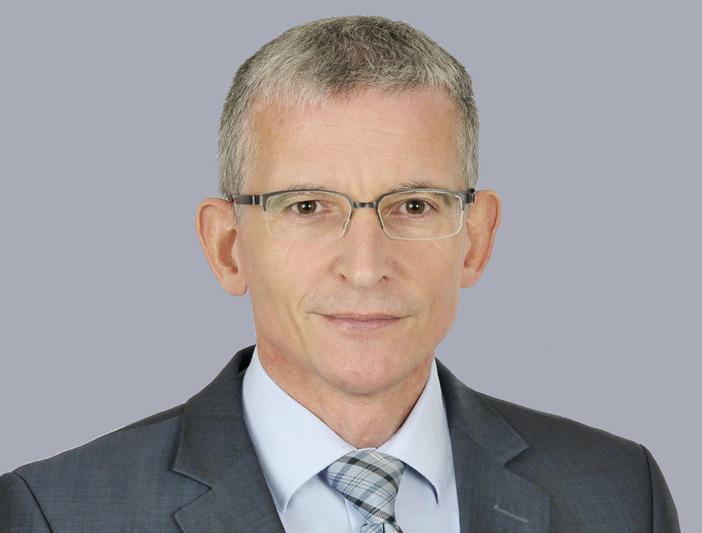
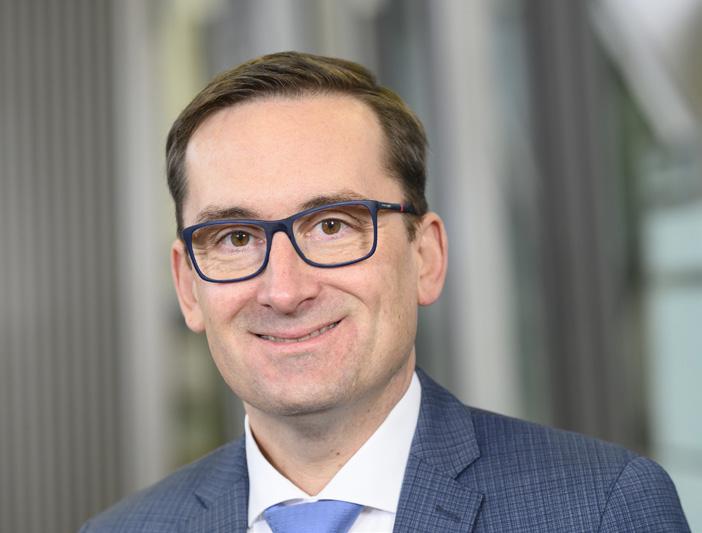
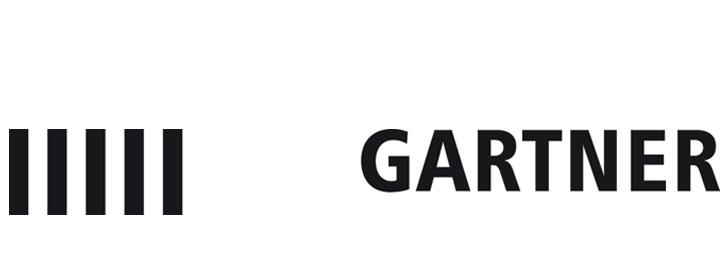
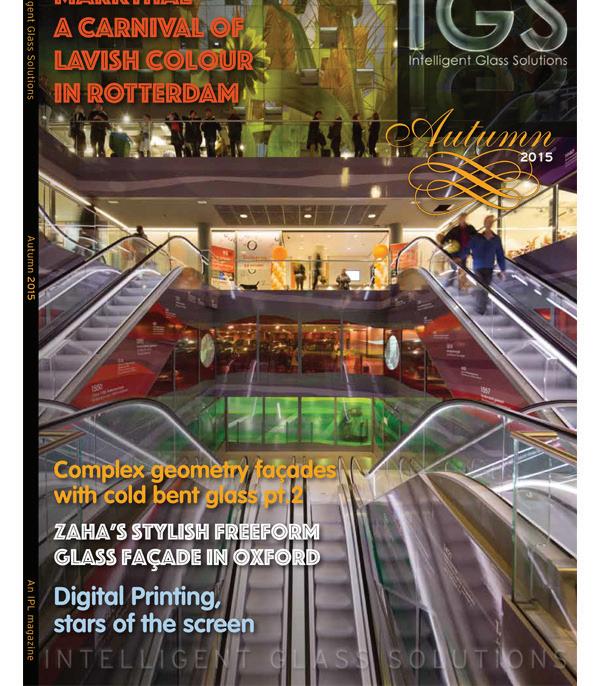

2019Out with the old Helloooooo2020 This is what tomorrow looks like Trends gaining tractionIntelligent Glass Solutions Winter 2019 INTELLIGENT GLASS SOLUTIONS Winter 2019 www.igsmag.com Our subscribers are a key part of our family Annual subscription is available at: £59 (postage within UK) £70 (postage within Ireland and mainland Europe) £96 (postage to rest of the world) Individual copies are available at £40 per copySubscriptions
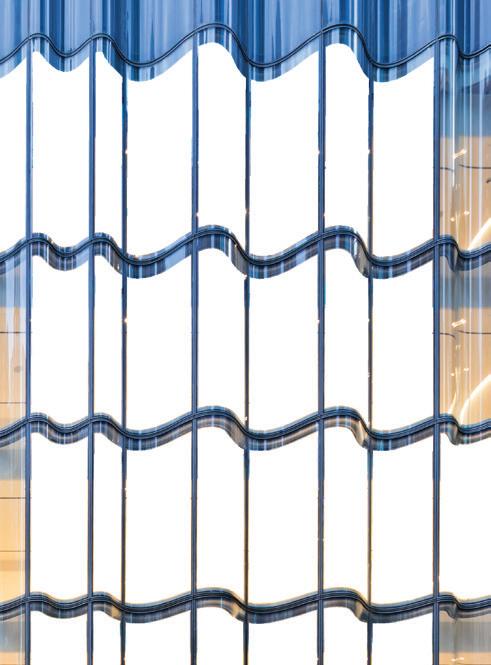
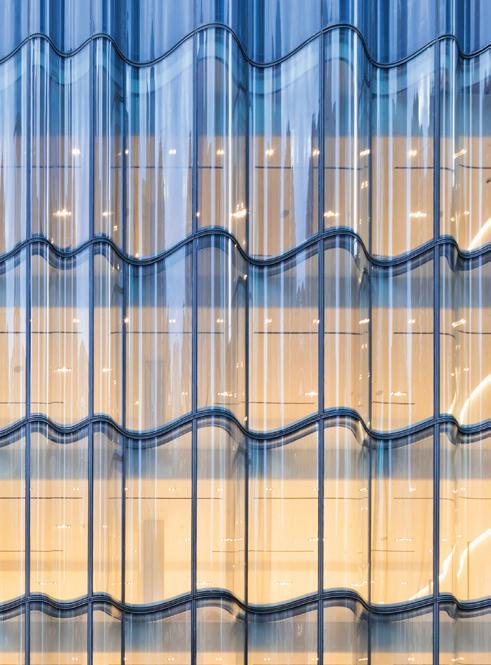

28/11/2019 20:46
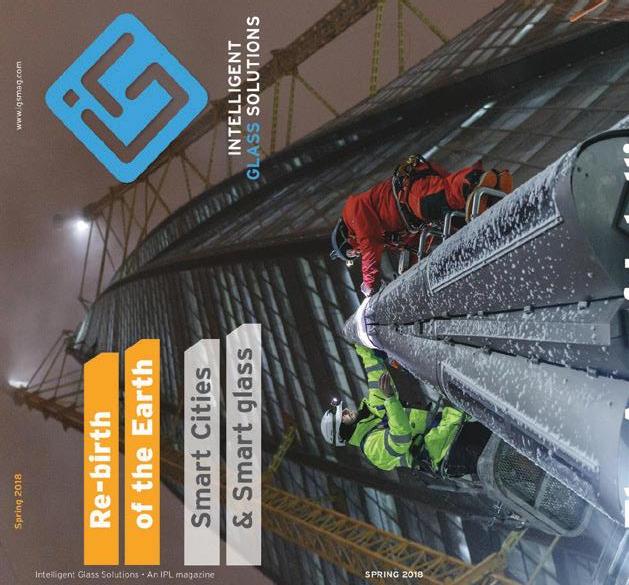

Name ................................................................................................................................. Company....................................................................................................................... Address...........................................................................................................................
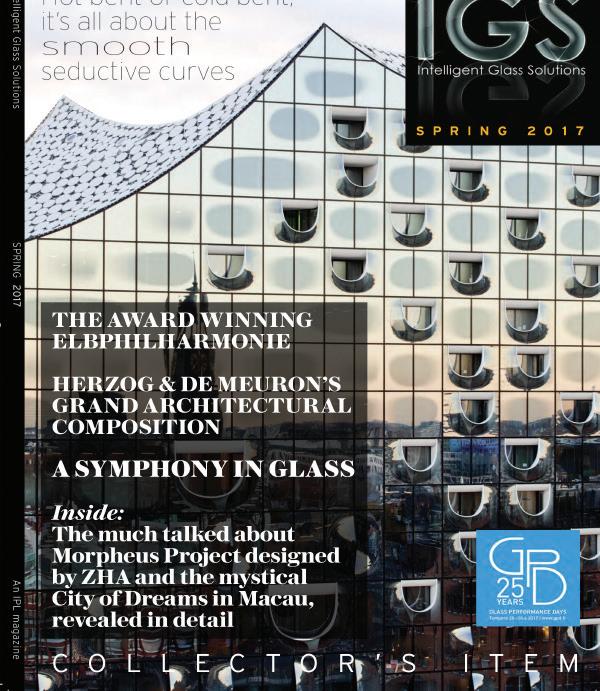
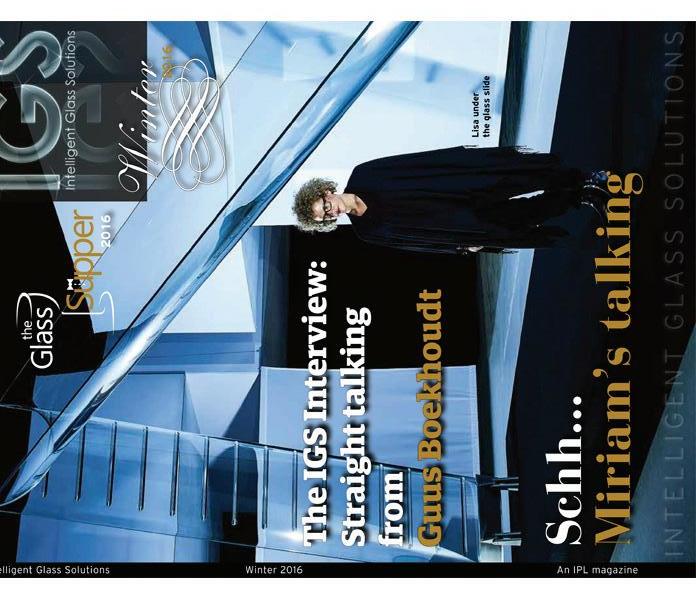
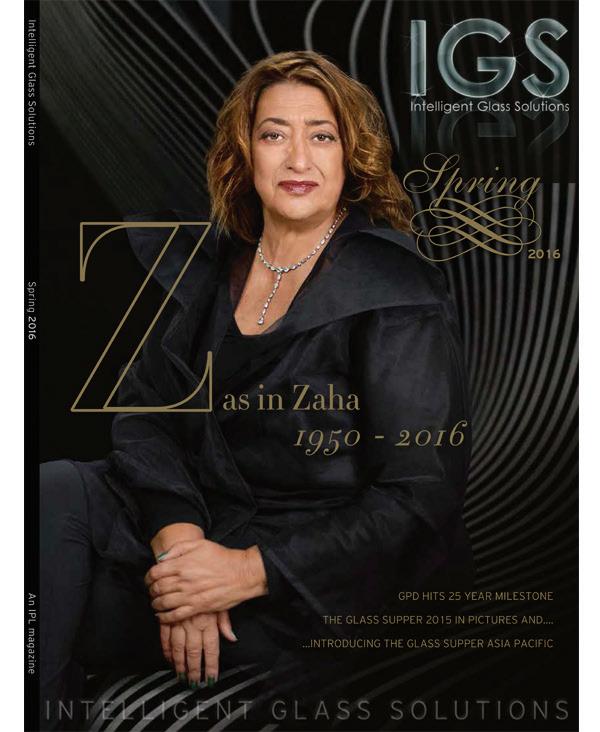
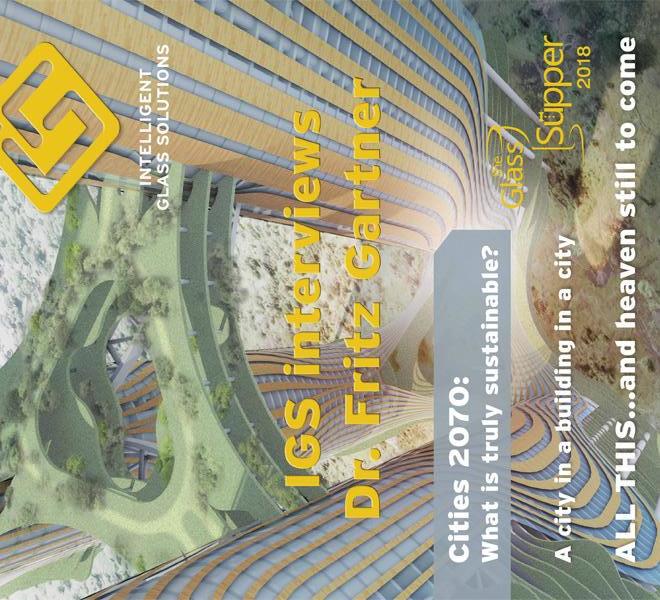
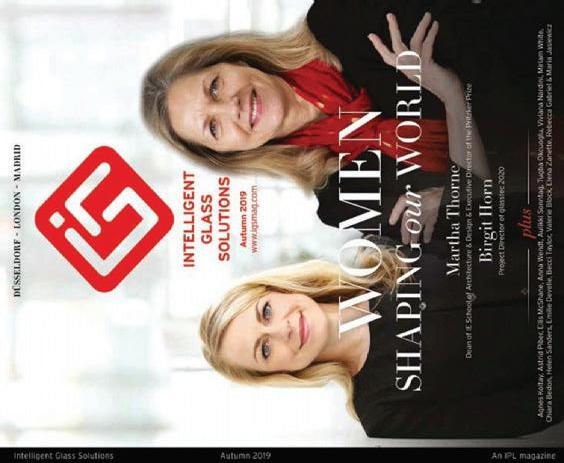
.................................................................................................................................................. Tel.......................................................................................................................................... Fax........................................................................................................................................ Email..................................................................................................................................


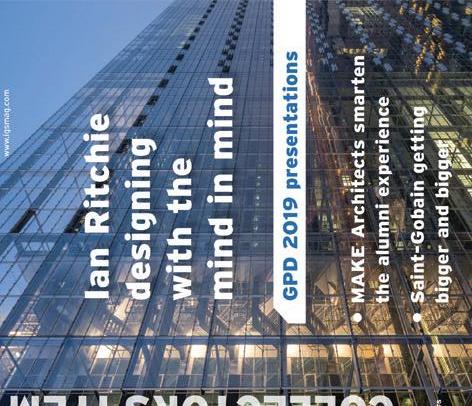
Please contact me by Tel to discuss subscription options ¨ Please send me a subscription form by fax or email ¨ (Tick as appropriate)
Post this form to:
Nick Beaumont, Intelligent Publications Limited, 3rd Floor Omnibus House, 39-41 North Road, London N7 9DP, United Kingdom. Or Telephone: +44 207 607 9907
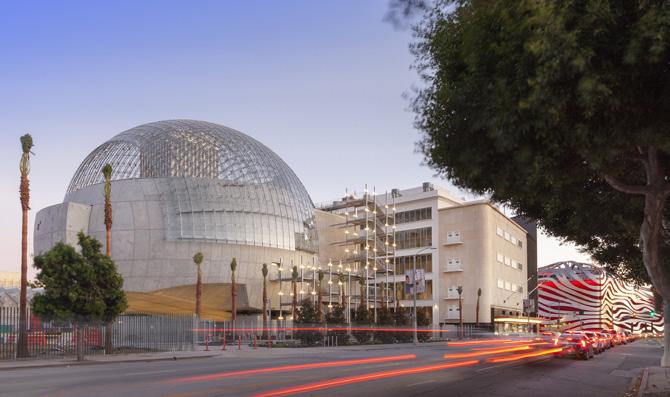
Reprints
Whenever your company products or services are mentioned in IGS, whether it’s an article, case study or new innovation we can produce a tailor-made reprint for you to use in your future marketing and promotional campaigns. Reprints can vary from a single page to multiple page brochures.
To order your reprints simply contact us at the following email address:
nick@intelligentpublications.com
or go to igsmag.com
TRANSPARENT ARCHITECTURAL STRUCTURES EXECUTIVE BOARDROOM COMMENTARY
(fig 8. 1 Triton Square) © DBOX for Arup EXECUTIVE BOARDROOM COMMENTARY
“What should our designs try to achieve? We must take a critical look at the brief, make it more comprehensive. We must look beyond the narrow object and ask ourselves: What will be the ecological consequences? Ove Arup in 1972
Nearly 50 years later, as an industry, are we yet to fully understand what the ecological consequences of our actions are? It can be challenging to relate the UN Sustainable Development Goals to a façade panel and understand how, in this assembly of metal, glass and gaskets, we can make the significant contributions that are needed now. Still more challenging to plan how we are going to decarbonise the making of the built environment over the next few years while transitioning to a circular or doughnut economy. (fig 1. Opportunities in the circular lifecycle beyond carbon targets)
EXECUTIVE BOARDROOM COMMENTARY
The Consequences of Carbon
- what is responsible innovation? EXECUTIVE BOARDROOM COMMENTARY
24 intelligent glass solutions | spring 2021
Buildings as Safety Bubbles
intelligent glass solutions | spring 2021
Anna Wendt
Throughout the past 12 months the physical boundaries created by our built environment have become ever more noticeable and increasingly important to us. Safety concerns throughout lockdowns due to the global COVID pandemic have raised awareness as to the barrier between the conditioned and unconditioned environment. The political unrest and protests in various parts of the world have further highlighted the physical safety net that our buildings provide, and just how vulnerable they can be to unexpected events of attack.
The size of our individual worlds has been TRANSPARENT ARCHITECTURAL STRUCTURES somewhat reduced and focused towards our more immediate surroundings – particularly
42 intelligent glass solutions | spring 2021
Design & Engineering of the iconic spherical shell of the Academy Museum
of Motion Pictures, LA
the buildings which we inhabit. For many, the boundaries of home and work have been blurred and the functionality of our homes has been stretched and put to the test as we attempt to live, work and play within the confines of our homes. The safety and security that we feel within our buildings has become increasingly important whether it be our own home or a building we are visiting. The perceived threats, from the external environment, onto our wellbeing are all the more apparent and as building designers we need to respond to this.
This article considers the role of the façade in responding to the increased requirements we are placing on our buildings and the protective, yet flexible, safety barrier we want it to provide.
intelligent glass solutions | spring 2021 43
Completed glass dome in December 2019. Image: Patrick Price.
60 intelligent glass solutions | spring 2021 intelligent glass solutions | spring 2021 61