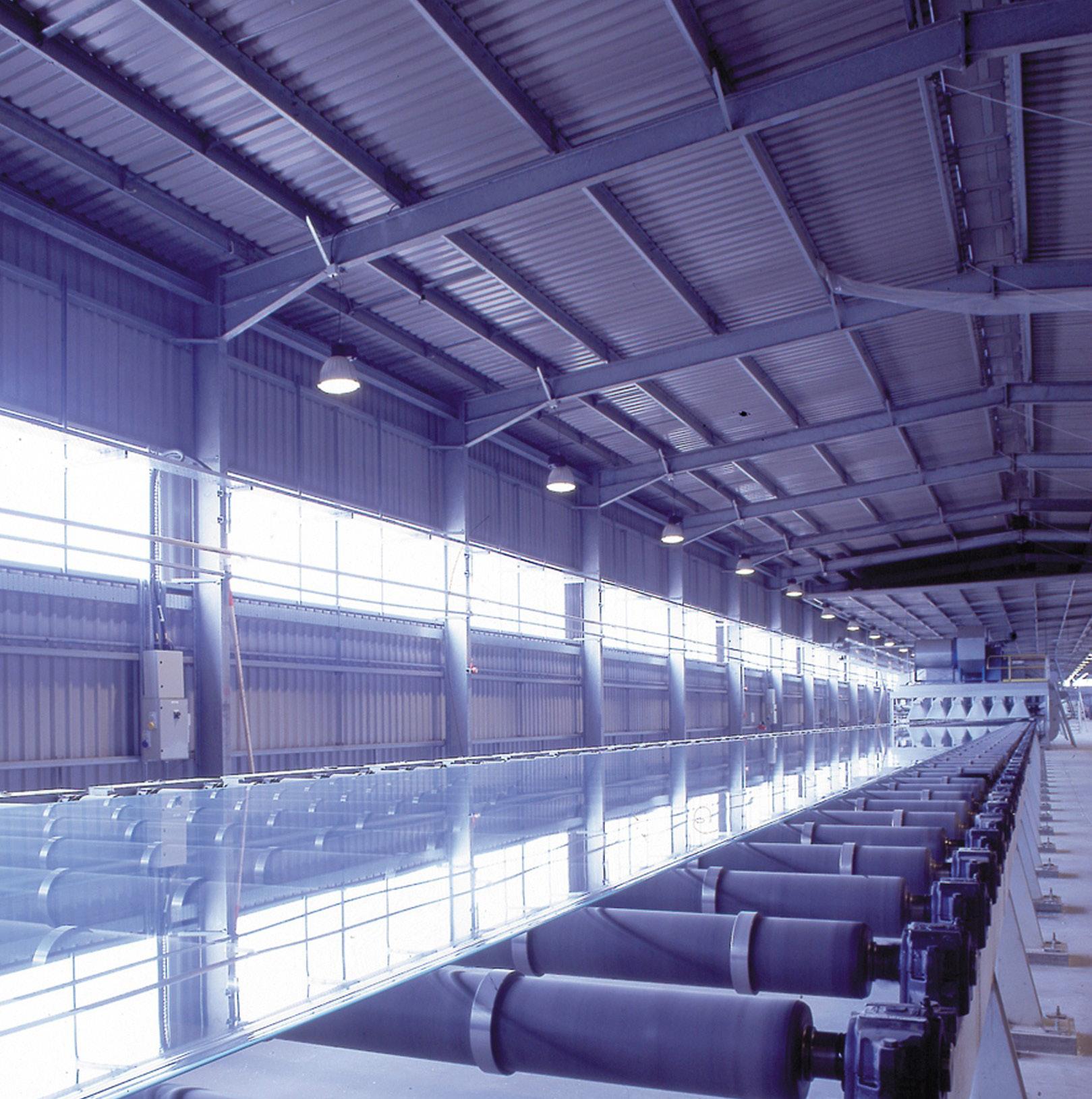
17 minute read
ACHIEVING A VIRTUOUS CIRCLE: DRIVING CIRCULARITY
Achieving a virtuous circle: Driving circularity in the glass industry
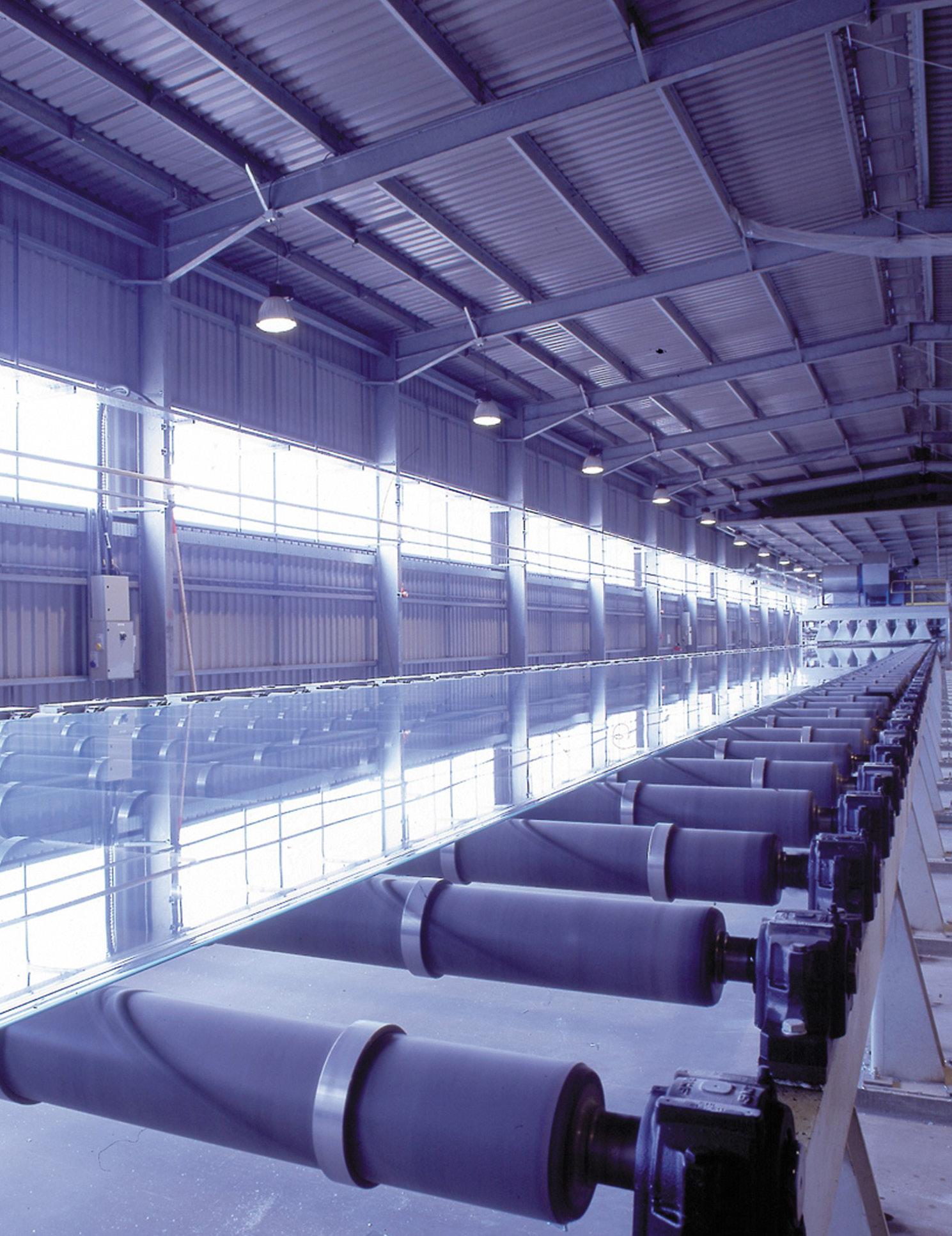
Advertisement
Graham Coult, Eckersley O’Callaghan, Technical Director and Rebecca Hartwell, Cambridge University, Research Partner
Float line The cullet producer carries the cullet to the float line, where it will be purchased by the glass manufacturer after being scanned for quality control. © Saint Gobain Glass UK
Glass has the potential to be endlessly recycled without degrading in quality. Yet it’s estimated that less than 10% of flat glass is recovered from buildings in the UK. What can be done to get more recycled glass back into the supply chain so that this dismal statistic can be improved?
That’s the task we at Eckersley O’Callaghan set ourselves two years ago after joining up to Engineers Declare. By signing up to the agreement, we had a duty to think about circularity. We’re in an ideal position to understand the problem and influence change through our close links not only with our network of construction industry colleagues and clients, but with the people who make glass, and who make things out of glass. After two years of talking to the whole supply chain from the raw material suppliers through to glass consumers, from building developers to demolition companies, we are ready to share our insights, ahead of a soon-to-be-launched regional pilot project to test a more circular approach for flat glass.
We believe there is the potential to reduce the annual emissions of the UK flat glass valuechain by up to 16%1 by recycling end-of-life flat glass back into the chain of production.
Before considering how to deliver greater circularity, our research needed to understand not only the processes of flat glass production, but those of the wider glass industry as well. We then analysed the efficiency of existing and potential recovery routes for flat glass with their implications for materials, energy use and emissions.
Glass is classified as one of the eight energyintensive sectors in the UK, accounting for 0.5% of total UK energy consumption2 and 0.5 - 1.0% of total UK greenhouse gas emissions in 20193. A total of 3.5 million tonnes4 of glass is produced annually in the UK. Container glass accounts for approximately 60% of production, flat glass for 22%, and glass wool for 10%.
During the production process, glass waste of sufficient quality to be returned to fabrication, known as cullet, is added to the melt of the raw materials used to produce glass, typically at a level of 10-25%. This has several benefits. Firstly, it improves efficiency by reducing the demand for primary raw materials - the use of 1 tonne of cullet saves 1.2 tonnes of raw materials. Secondly, it reduces energy demands in the melting phase, leading to a cut in energy consumption of 2.5 – 3.0% for every 10% increase in cullet5. Thirdly, this has a corresponding reduction in both combustion and process emissions. An oft-quoted statistic is that for every tonne of glass included in the glass melt, 580kg of CO2 is saved (although this figure varies according to many variables).
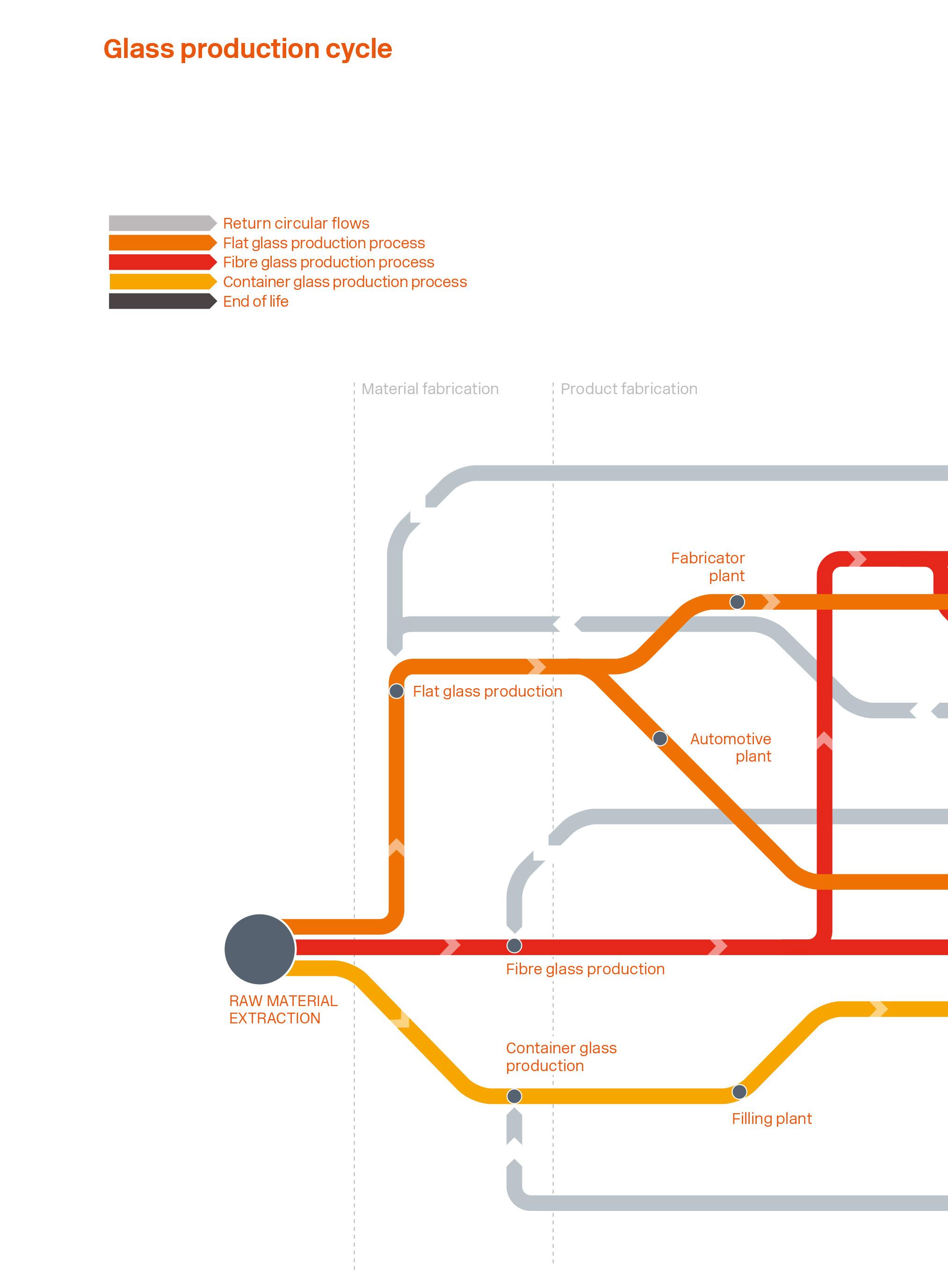
Cullet can be one of three types – internal glass produced during the manufacturing process; off-cuts of certifiable quality returned by fabricators; and post-consumer glass. Currently, the market for post-consumer cullet isn’t sufficiently developed, with the result that 90-95% of post-consumer glass ends up being downgraded either for end of life uses such as aggregates or additives for paint, or worse still, as landfill. We need to change perceptions so that instead of consigning this cullet to be waste, it is instead considered as material stock for recovery in a closed-loop process. The potential benefits are significant - our research indicates that in the extremis case the
The Glass Production Cycle is a product of the research we have conducted with the links we have identified for each strand of the glass supply chain, from production through to disposal and recycling, while identifying the potential for the application of circular economy principles. © Eckersley O’Callaghan
replacement of 100% primary raw materials with 100% post-consumer cullet gives a total energy saving of 27%, with a reduction in total emissions of 41%1 from raw material sourcing through to the production of uncoated flat glass product.
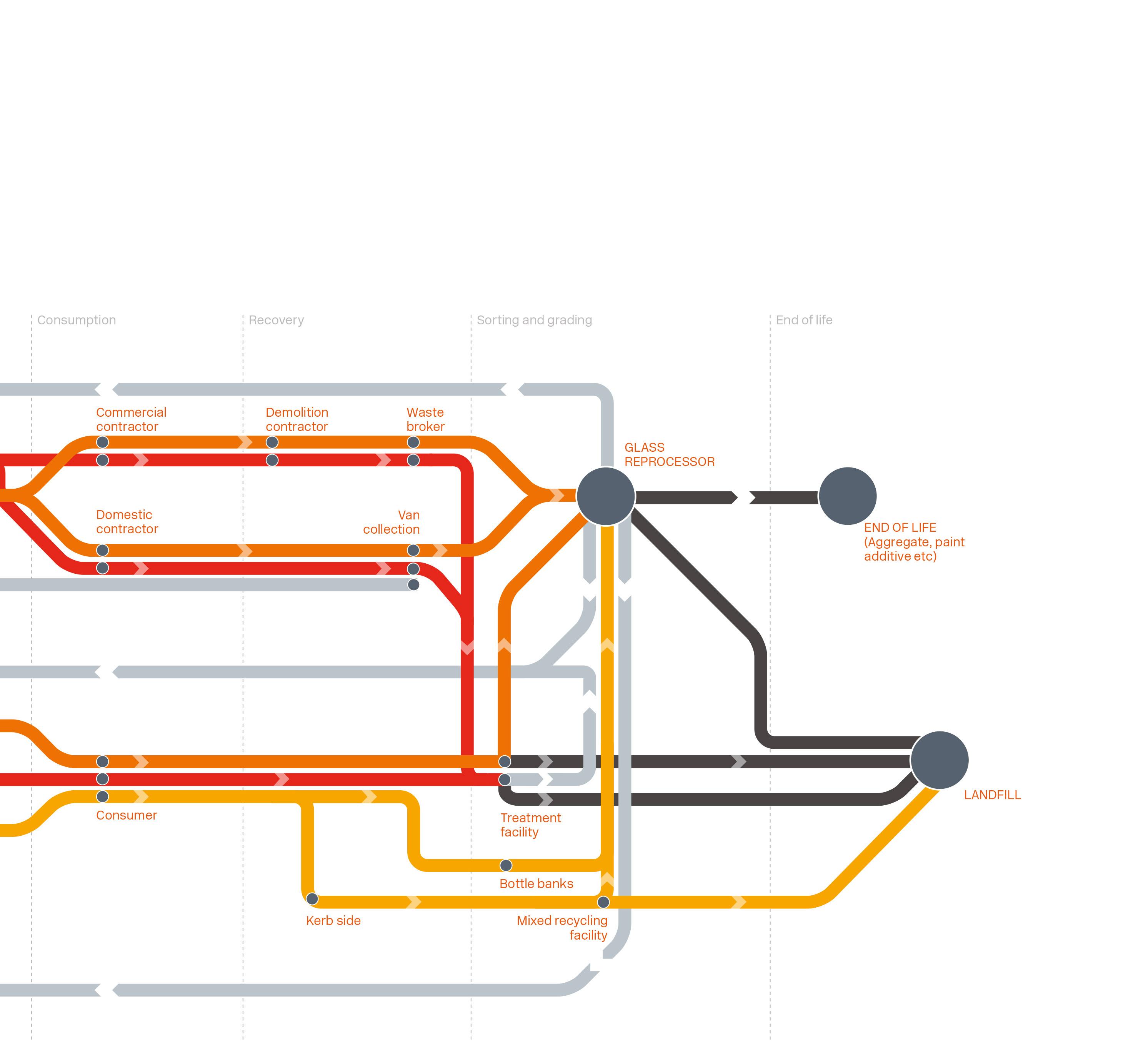
While the use of 100% cullet has been shown to be possible, in the short term the emphasis should be on redirecting flat glass waste to the higher value secondary uses including: container, flat or glass wool, and subsequently building up the supply chain for the longer-term goals. The existing ~10% rate of recycling building glass back into production means that an estimated 180,000 tonnes of embodied carbon are being downgraded each year as a result of the glass that isn’t recycled. This is seen as a conservative estimate, and the figure could be as high as 700,000 - 900,000 tonnes.
It's a very different story elsewhere in the glass industry. There is a well-established take-back infrastructure for container glass recycling, driven by packaging industry legislation and the ease of kerbside recycling. This reached a record recycling rate of 76.5%6 in 2019, which sits within the average rate for Europe. In this sector, manufacturers are also looking to decarbonise the production process with increased use of cullet, with new container glass production containing 50-52% post-consumer cullet from UK sources 7 , 8. This rate of recycling is assisted by container glass manufacturers being able to tolerate higher levels of contaminants in the raw materials. The glass wool sector uses up to 80% of cullet.
Our transformation of the 1968 listed building at UNESCO's headquarters forms a pilot recycling project in Paris audited and approved by glass manufacturers for certain recovery protocols. © Eckersley O’Callaghan
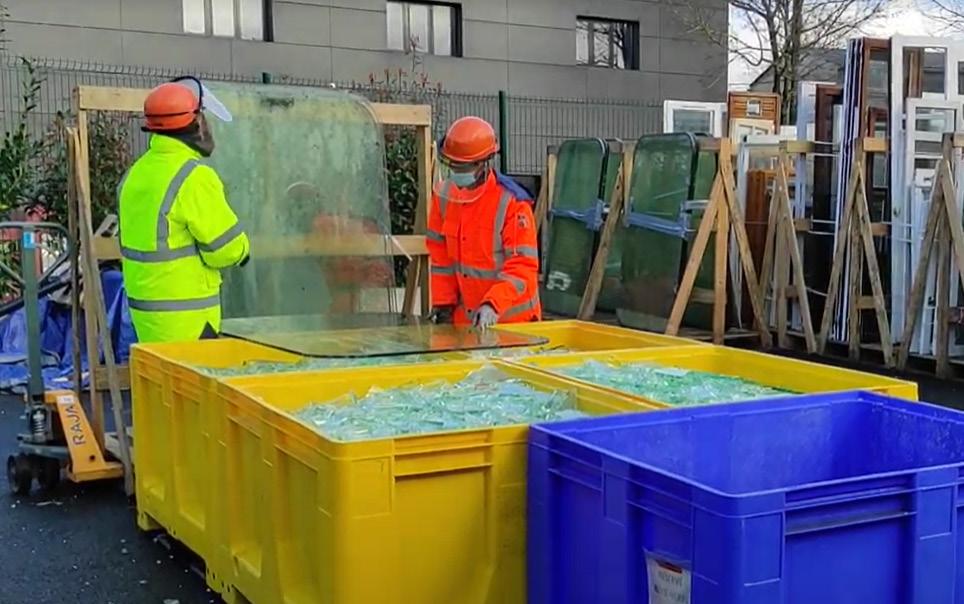
UNESCO's facade glazing panels are knocked out from frames to provide high quality cullet with low contamination risk. © Eckersley O’Callaghan

carbon neutrality by 2050, led by British Glass and the Department for Business, Energy & Industrial Strategy, is primarily focused on furnace technology and fuel-switching. Our complementary initiative focuses on reducing energy consumption and emissions through greater use of post-consumer cullet. This will require the action and participation not only of the glass industry but the broader building supply chain.
So what are the barriers to increasing the use of post-consumer cullet for producing new flat glass? A key impediment is the lack of supply due to so little glass being recovered when buildings are redeveloped, in contrast to far higher value materials such as aluminium, copper and steel. Instead, glass is knocked out and crushed, much of it ending up in landfill where it incurs a rate of just £3.10 per tonne as a lower rated material compared with £96.70 per tonne for standard rated materials (at 2021 prices).
We spoke to demolition companies and found them open to change but ultimately governed by the fast pace of their contracts, which results in only high value and easily retrievable materials being recovered. Glass recovery may lead to a slower demolition process. There is a lack of understanding of the options that could offset any additional associated costs on-site. Small pilot projects in France suggest that cullet can cost half the price that flat glass manufacturers would pay for raw materials, so there is commercial potential, especially if the glass goes straight to the manufacturers rather than through multiple intermediaries.
We’ve been talking to leading flat glass manufacturers in the UK, to try to understand their approach and what’s preventing them from using more cullet, given the known savings in raw materials and energy costs. Currently flat glass cullet that is collected is predominantly sent to container lines instead. Aside from supply, the key concern for flat glass manufacturers is fear of contamination – how to make sure that any post-consumer glass they’d be receiving back into the supply chain would be free from contaminants such as glass-ceramics, organic materials and metals.
This reticence is understandable. In an industry where the margins are so minimal, having to stop production to deal with contamination issues in the float tank has major commercial implications. The stakes are much higher regarding contamination in the flat glass industry compared with container glass – one critical defect in a jumbo sheet could result in 350kg of waste compared to 400g for a glass bottle.
The challenge is to find a way of minimising the risk of contamination. A unified set of specified grades of cullet that is agreed by flat glass manufacturers and reprocessors will be a major goal. There’s a great deal of work to be done here to establish these assurances of high purity, and in doing so provide greater certainty that there will be a market for the cullet after the cost outlay of glass recovery. Nonetheless, we feel there is the potential to create unified specification grades for the maximum level of contaminants that would enable the market to operate more effectively.
Glass recovery from site is not a significant technological challenge, more a matter of logistics and quality control, and something that can certainly be overcome. Indeed, those who understand this and can provide efficient construction methods will stand to gain.
The original windows at Panther House in London comprise of small glass panels in iron frames which will have a complicated and unlikely recovery process after demolition has taken place. © Eckersley O’Callaghan

These internal glass partitions in the offices of Lafayette Anticipations in Paris, are an ideal building component for recycling as they are easy to process. © Eckersley O’Callaghan (WRAP) introduced some quality protocols for glass recovery from site back in 2008 but it was too early for the industry. Further work was carried out in the Buildings as a Material Bank (BAMB) project in 2020. This needs to be revisited to draw up on-site recovery standards for recycling building glass into cullet.
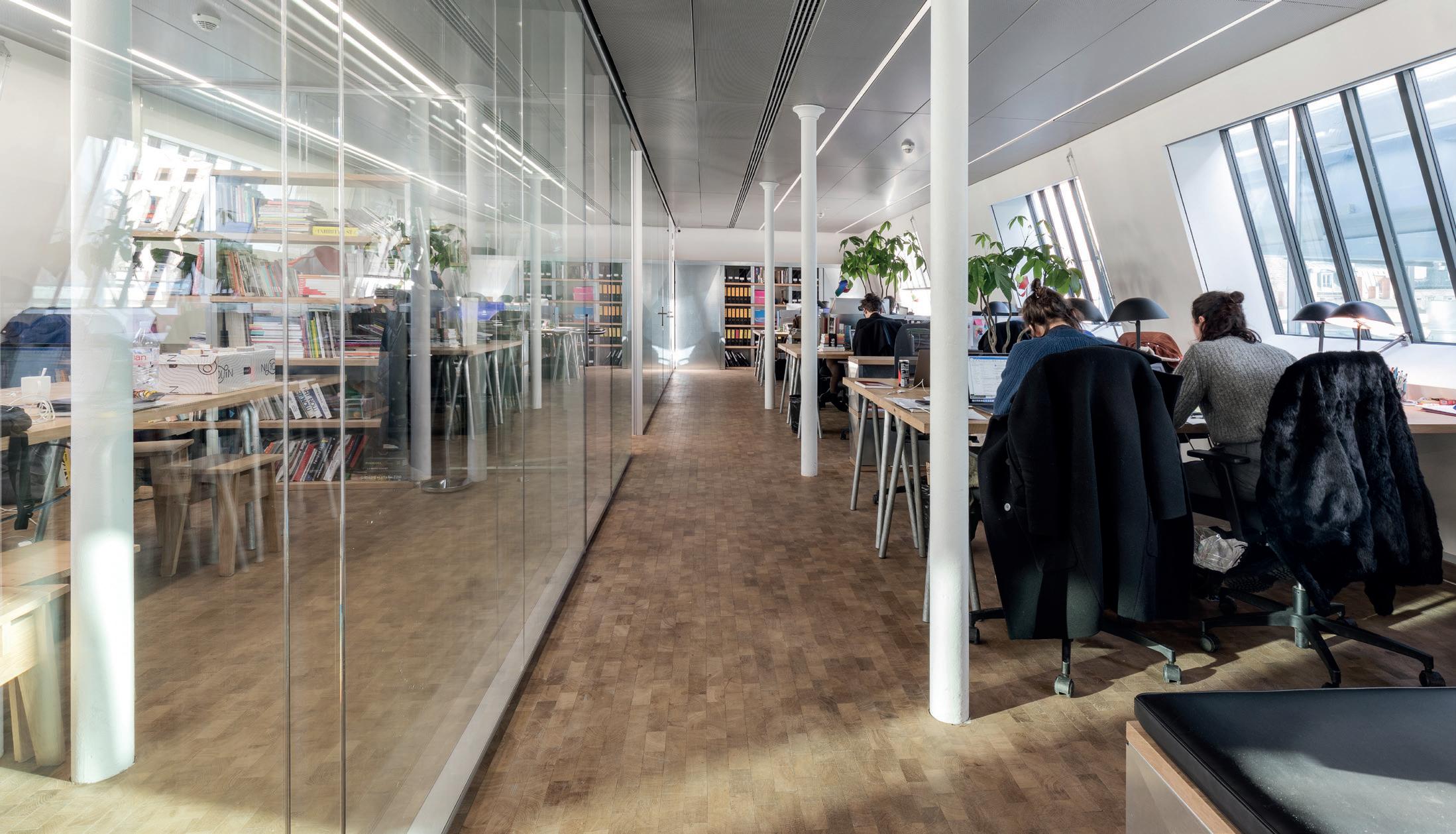
Alternative mechanisms for collection that sort flat glass cullet more effectively should be investigated. We think it would be beneficial to consider grading post-consumer flat glass cullet to then distribute to relevant glass markets based on quality. Improved scanning technology to identify contaminants could also help.
We can learn from a pilot recycling project at the UNESCO building in France. For this, flat glass manufacturers have audited and approved certain recovery protocols so that the demolition contractors have to deliver the framed glazing panels into stillages. The panels are then transported to a cullet factory where the glass can be simply knocked out from the uPVC or aluminium frames to provide high quality cullet with a low risk of contamination. The cullet producer then organises collection of the cullet by the glass manufacturer. The total amount of cullet produced for recycling on this project is estimated at 113 tonnes. Based on the
St Helens recovery loop is a Pilot project to enhance the waste strategy in the area by reducing the amount of glass going into landfill and increasing recovery of window glass at quality sufficient to produce new glass. © Eckersley O’Callaghan
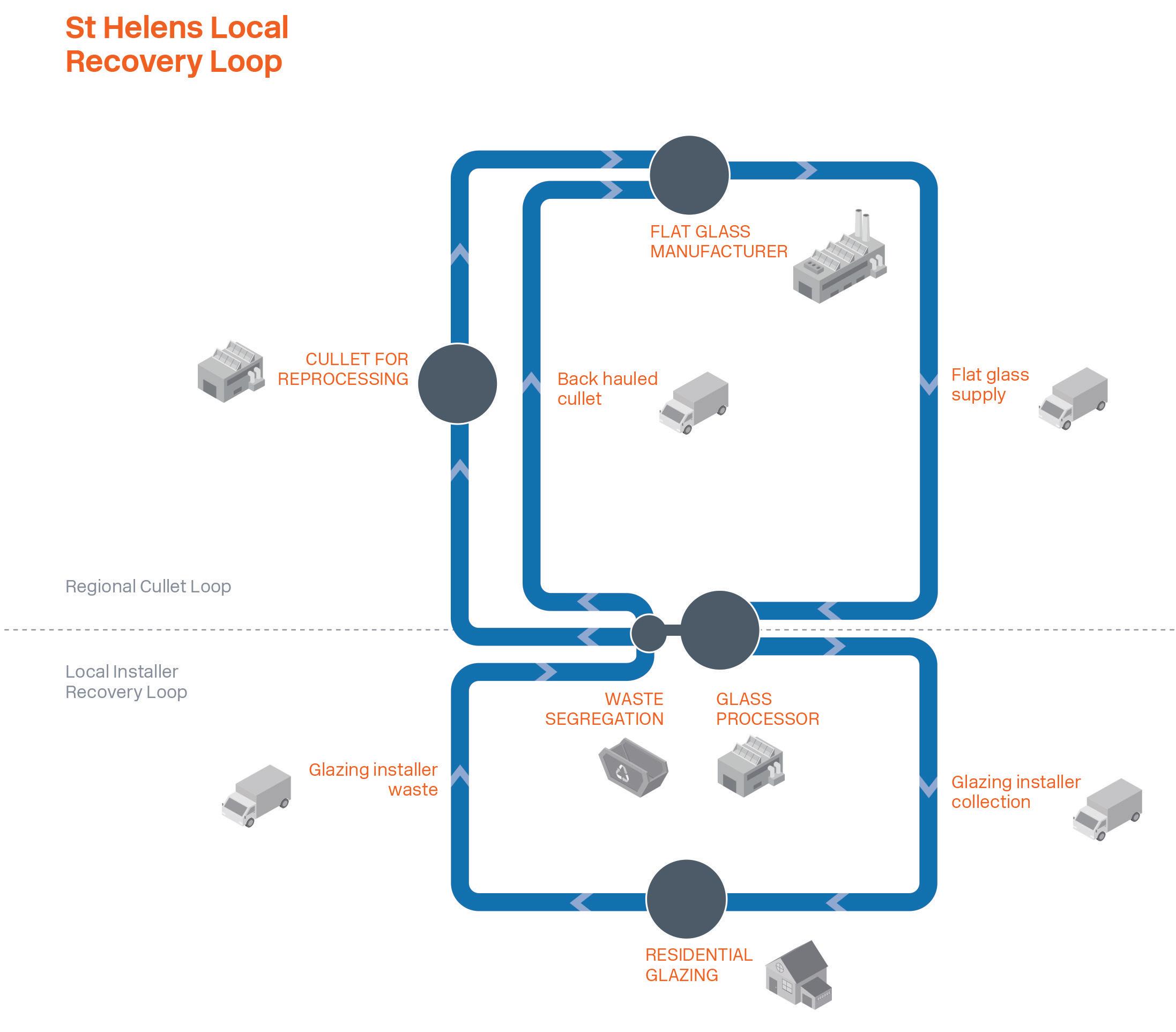
assumption that 1 tonne of glass saves 580kg of CO2, the cullet recycling should avoid 66 tonnes of CO2 emissions..
So, what else can be done to encourage change? So far there just hasn’t been the collective thinking that’s needed to drive a more circular approach from developers right through to the glass industry. Until we get this, people will fight against change and continue to benefit from the status quo of putting waste glass in the ground. However, during the latter period of our research, we’ve noticed a sea change in approach. Attitudes are starting to change – we’ve noticed that the idea of using more post-consumer cullet is starting to be viewed more favourably. We can see a way to explore simple opportunities in the domestic market but the commercial side will require significant effort to embrace the change.
Everyone has to play their part. We need owners and developers to make the commitment to recover the glass from their buildings and prioritise it for high-value recovery options. The demolition contractors need to be able to better understand the costs of recovery. So far this isn’t happening – our research found less than a handful of projects in the UK where developers had sought a market for the recovered glass. We need architects to specify that all the glass in the building they’re retrofitting should be recovered where practical. The recovery of internal glass partitions, for example, is much easier to process than a small panel in a filigree iron frame. How do we get glass recycling on the agenda of contractors and their coordinated engagement? Could they work together to establish recycling plants at locations of easy access?
There needs to be a carrot and stick approach. We’d like to explore the use of planning guidance to encourage glass recovery by mandating glass recovery from commercial demolition where practical. We’d like to see the requirement for a full assessment of the potential for glass recycling as part of the demolition application – buildings with extensive glazing are likely to be more suitable candidates than those with small pockets of glass. A predemolition audit should cover this in greater detail and should be verifiable. Perhaps there could be the potential for offsetting glass that
isn’t recycled in some other way that would still benefit the recycling process. Perhaps there is scope to encourage glass recycling more strongly through the BREEAM assessment system, where we are working with the Technical Working Group to develop the next guidance.
We believe the domestic market – which is considerably larger than the commercial market – presents more straightforward opportunities for circularity for relatively modest investment.
We are developing a pilot project for St Helens – fittingly where Pilkington was first established – in collaboration with Arup, British Glass, Diageo, Glass and Glazing Federation, Glass Futures, Pilkington - NSG Group, Saint Gobain, The Glass Company and St Helens Borough Council. This was initiated at COP26 and we hope to launch it this spring. The aim is to enhance the waste strategy in the pilot area by reducing the amount of glass going to landfill and increasing the recovery of window glass at a quality that can be used to produce new glass. In doing so, this will reduce both energy use and carbon footprint.
Leading glass manufacturer Saint Gobain’s Eggborough factory. © Saint Gobain Glass UK Glass waste of sufficient quality to be returned to fabrication is known as cullet where it is added to the melt of raw materials used to produce glass. © Saint Gobain Glass UK
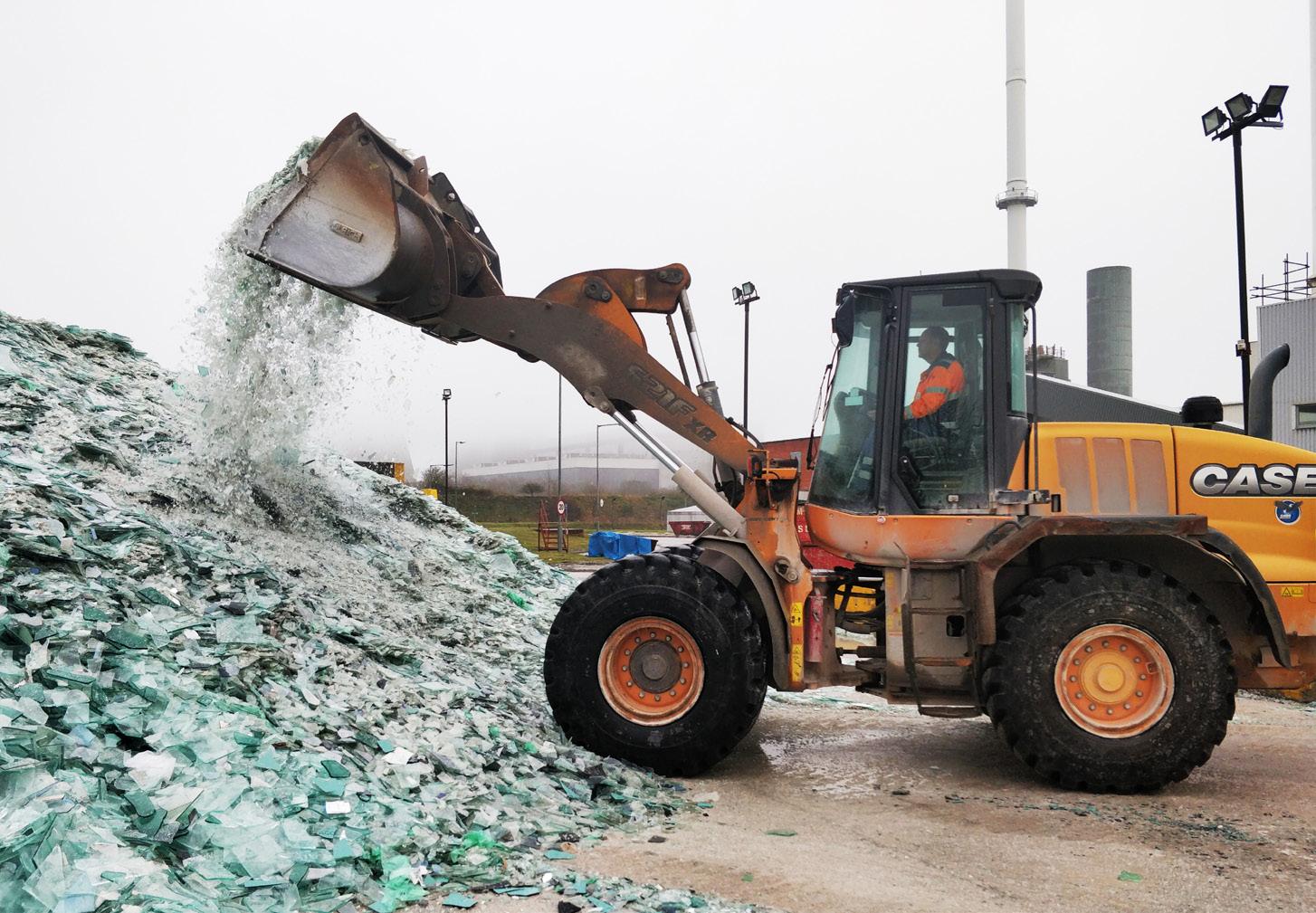
We are optimistic that with the right will and organisation this can succeed. Our approach is to work with installers to dispose of insulated glazing units or framed glazing at a network of local recovery plants in a way that will allow recycling through appropriate segregation and storage. This cullet can then be sold on the open market, whether for use in container glass or in flat glass manufacture - either destination means a reduction in raw materials and energy used. The cullet will either go straight back to the glass manufacture or via a bulking station
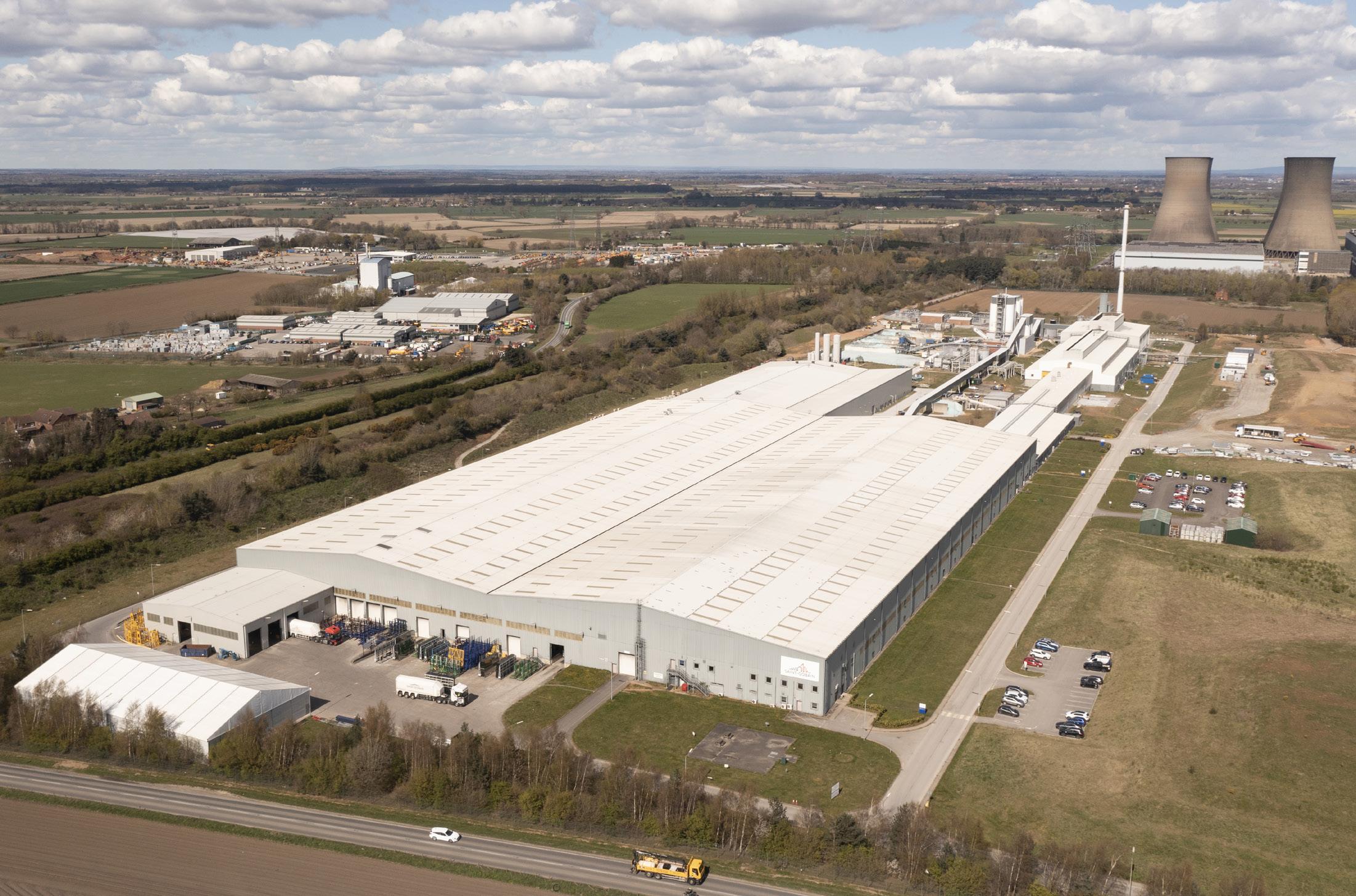
and reprocessor. While such an approach has already been shown to be effective at a small scale, this level of intervention to stimulate the market is unprecedented.
We see a role for glass industry organisations such as British Glass and the Glass and Glazing Federation in promoting the benefits of the initiative throughout the industry. In other established programmes such as Vlakglas Recycling in the Netherlands, the insulated glazing unit (IGU) manufacturer supports the glass processing required for recycling through a levy on the price of glass per square metre of IGU to help fund the recovery for the cullet.
During the pilot study, cullet volumes and quality will be monitored – including contaminant levels before and after reprocessing. Transportation distances will be tracked to monitor associated costs and carbon expenditure. The results should equip us with sufficient knowledge on costs, logistics and carbon reduction to demonstrate the efficacy of the establishment of flat glass take-back infrastructure in the UK. It will also enable us to understand what it takes from a local perspective to develop recycling networks of this nature.
The aim is to learn enough from this exemplar project to produce a scalable business case for wider application to help drive a market for flat glass cullet. There is potential to roll it out with local fabricators across Merseyside and beyond with a view to securing a national approach.
We would also look to identify upcoming regional refurbishment and demolition projects from commercial buildings to act as exemplars, and to understand the changes and opportunities for driving recycling in the commercial sector.
After two years of research, we have gained valuable insights into the challenges of recycling glass back into the manufacturing process. There’s the potential to learn a great deal more as we drive this project forward, but we can’t do it alone. We need collective action.
This is a call to arms to both the glass world and the wider construction industry. We need to raise awareness of what can be done to drive greater circularity by joining together across the sector in a spirit of cross-disciplinary innovation. Only then can we bring about the muchneeded changes required.
1 Rebecca Hartwell, Graham Coult, Mauro Overend; Mapping the flat glass value-chain: A material flow analysis and energy balance of UK production; 07 March 2022; PREPRINT (Version 1) available at Research Square; https://doi.org/10.21203/ rs.3.rs-1401635/v1
2 WSP Parson Brinkerhoff; and DNV GL, “Industrial Decarbonisation & Energy Efficiency Roadmaps to 2050: Cross Sector Summary,” 2015.
3 R. Ireson et al., “Alternative Fuel Switching Technologies for the Glass Sector,” 2019. [Online].
4 Glass Sector Net Zero Strategy 2050, British Glass 5 R. Beerkens, G. Kers, and E. Van Santen, “Recycling of post-consumer glass: Energy savings, CO2 emission reduction, effects on glass quality and glass melting,” in Ceramic Engineering and Science Proceedings, 2011, vol. 32, no. 1, doi: 10.1002/9781118095348.ch16.
6 FEVE, “Latest Glass Packaging Recycling Rate Steady at 76%,” 2018. https://feve.org/glass_recycling_ stats_2018/ (accessed Dec. 03, 2021).
7 FEVE, “Close the glass loop: The action plan for the UK,” no. June, 2020.
8 P. Lee, N. Bell, T. Garcia, O. Lee, J. Harding, and K. Baker, “Recycling DRS in Scotland,” 2019.
Graham Coult, Eckersley O'Callaghan, Technical Director
With 20 years’ experience as a structural and facade engineer, Graham has a particular passion in the development of structural glass design using sophisticated analysis and modelling tools. Graham's technical expertise in pioneering glass engineering has been instrumental in delivering the practice’s many challenging and awardwinning glass projects, notably for Apple. As Technical Director at Eckersley O'Callaghan, Graham is responsible for the strategic operations across the company. This includes defining design processes and project delivery for project excellence. He also leads our R&D programme driven by a pursuit to explore the innovative use of material in design.
Rebecca Hartwell, Cambridge University, Research Partner
Rebecca is a PhD candidate in the Glass and Façade Technology research group at Cambridge University under the supervision of Professor Mauro Overend (TU Delft). She previously graduated in Material Science and Engineering from the University of Manchester which included a 1-year industry placement at Siemens Magnet Technology. Subsequently, Rebecca worked as a research assistant at the International Centre for Advanced Materials, to develop research in understanding the role of microstructure in the failure of insect cuticle using X-Ray Computed Tomography. Her current PhD research is developing the knowledge, tools, and technologies to promote the effective reuse and high-value recycling of building envelopes.
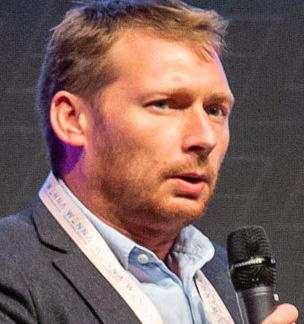
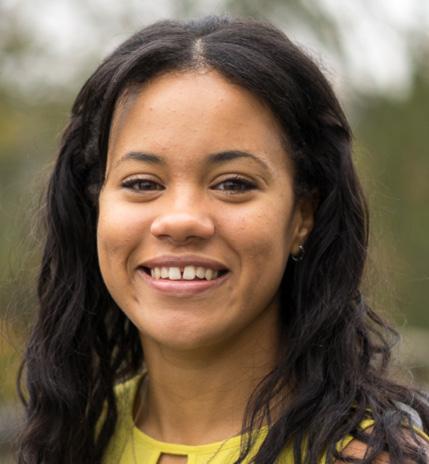
