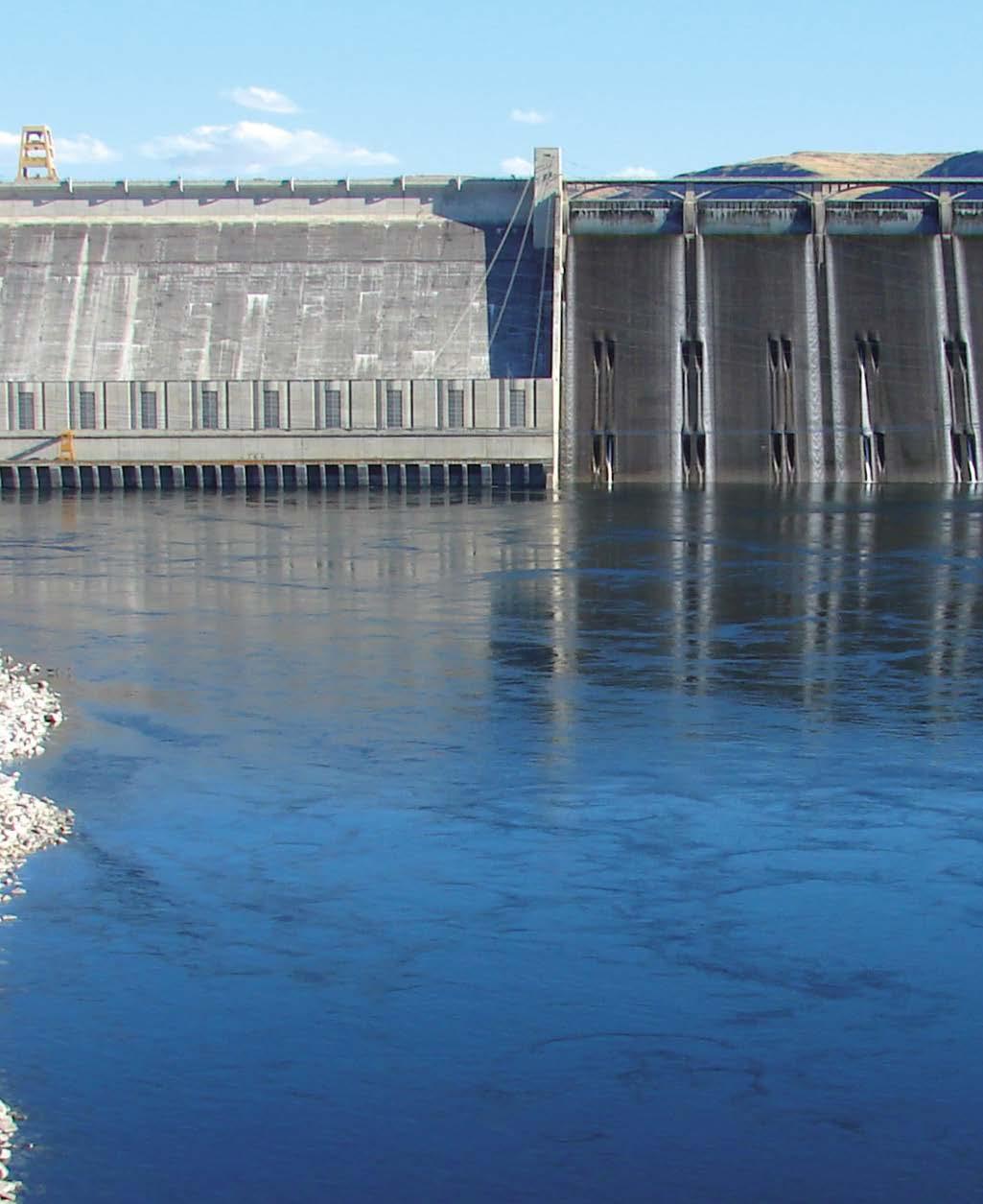
10 minute read
The hydropower industry and epoxy coatings
by Alexander Ruiz Belzona – Miami Lakes (FL) – United States aruiz@belzona.com
Hydropower is a renewable energy source that has been harnessed for thousands of years. Today, it is one of the most important sources of electricity in the world, and its use is only expected to grow in the future. One of the key components of the hydropower industry is the use of epoxy coatings, which are used to protect the machinery and infrastructure used in hydropower operations. In this blog post, we will explore the role that epoxy coatings play in the hydropower industry and the benefits they provide.
Epoxy coatings are a popular choice for use in the hydropower industry because of the many benefits they provide. One of the primary benefits of epoxy coatings is their ability to protect machinery and infrastructure from corrosion.
Corrosion is a major problem in hydropower operations because the equipment used is often exposed to water and other corrosive substances. Epoxy coatings provide a protective barrier that prevents corrosion from occurring, which helps to extend the life of the equipment and reduce maintenance costs.
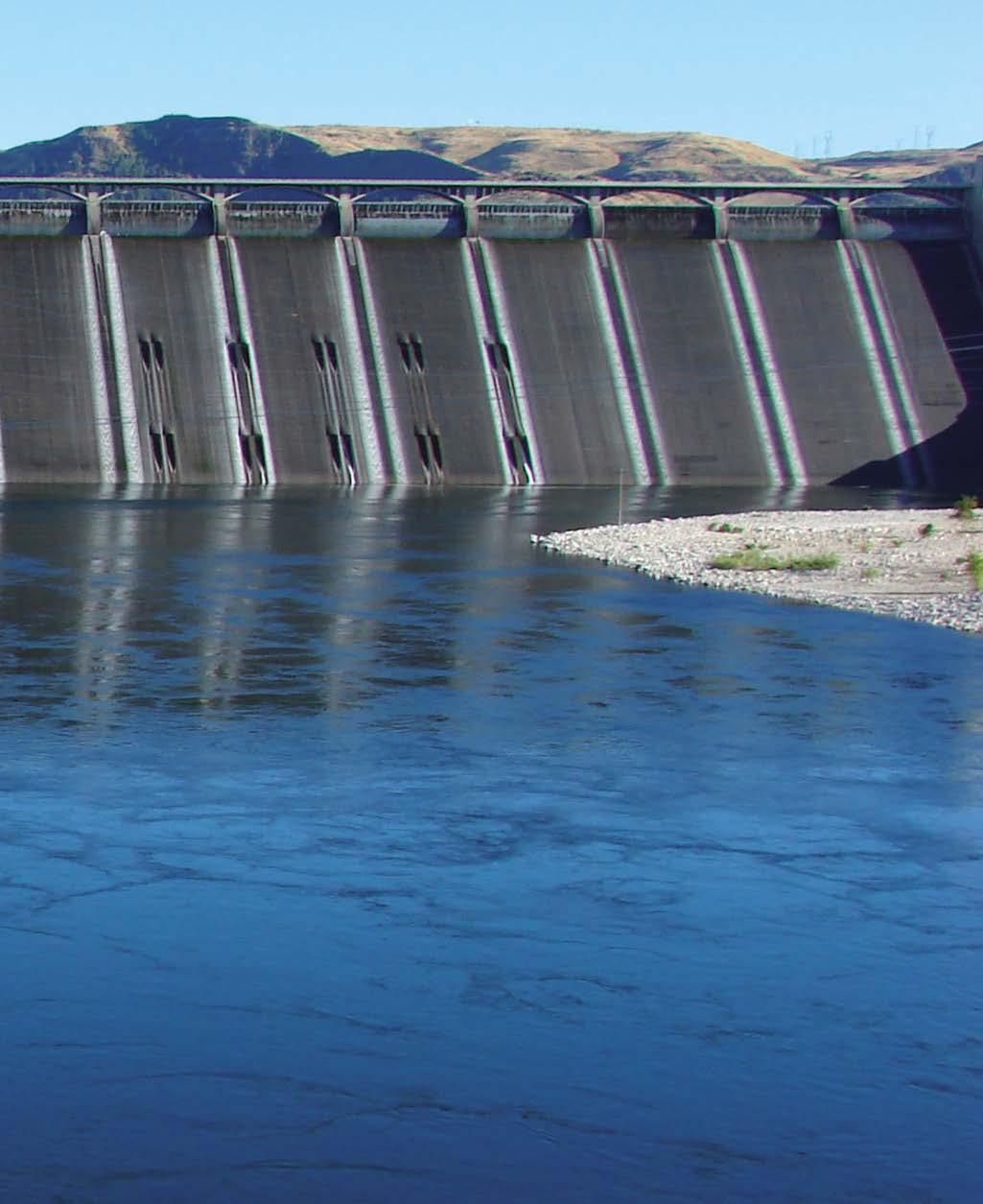
Another benefit of epoxy coatings in hydropower operations is their ability to provide a smooth surface for water to flow over. This is particularly important in turbines, where a smooth surface is essential for optimal operation. The use of epoxy coatings can help to reduce friction and improve the efficiency of the turbine, which can lead to increased power generation and lower operating costs.
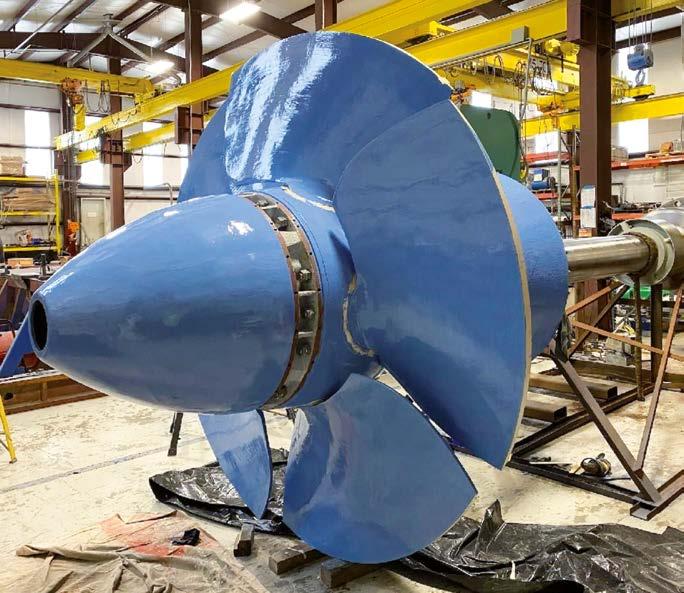
Finally, epoxy coatings are also resistant to high temperatures and can withstand exposure to UV radiation. This makes them an ideal choice for use in the harsh environments found in hydropower operations, where machinery and infrastructure are often exposed to extreme temperatures and intense sunlight.
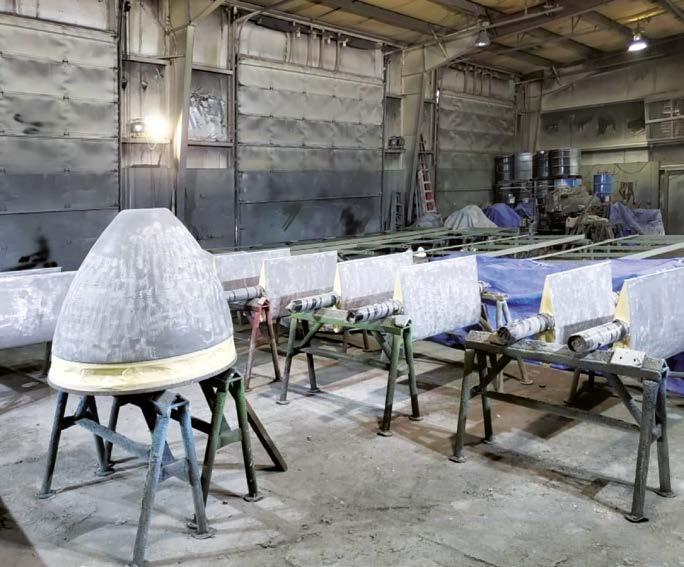
Hydropower industry case study
Belzona had the opportunity to improve the condition of a 60-year-old Kaplan hydropower unit that was showing signs of wear and was due for a full mechanical overhaul. Operators at the Hydropower Plant grit blasted and cleansed the unit with solvent. Belzona 1111 (Super Metal) was used to smooth over the wear and cavitation in a full skim coat. Once cured, the Belzona 1111 (Super Metal) was sanded down to the required profile, and frost blasted. Two full coats of Belzona 1341 (Super Metal Glide) were applied. The coating can provide increased efficiency on new and refurbished equipment while also providing full corrosion and erosion protection while immersed.
Surviving 60 years with minimal wear is impressive. However, by using Belzona 1341 (Super Metal Glide), the unit can continue to operate for many more years, providing reliable service and cost savings over the long term.
The use of this product can improve the unit's resistance to wear and tear and can also provide an additional layer of protection against environmental factors such as moisture and chemicals.
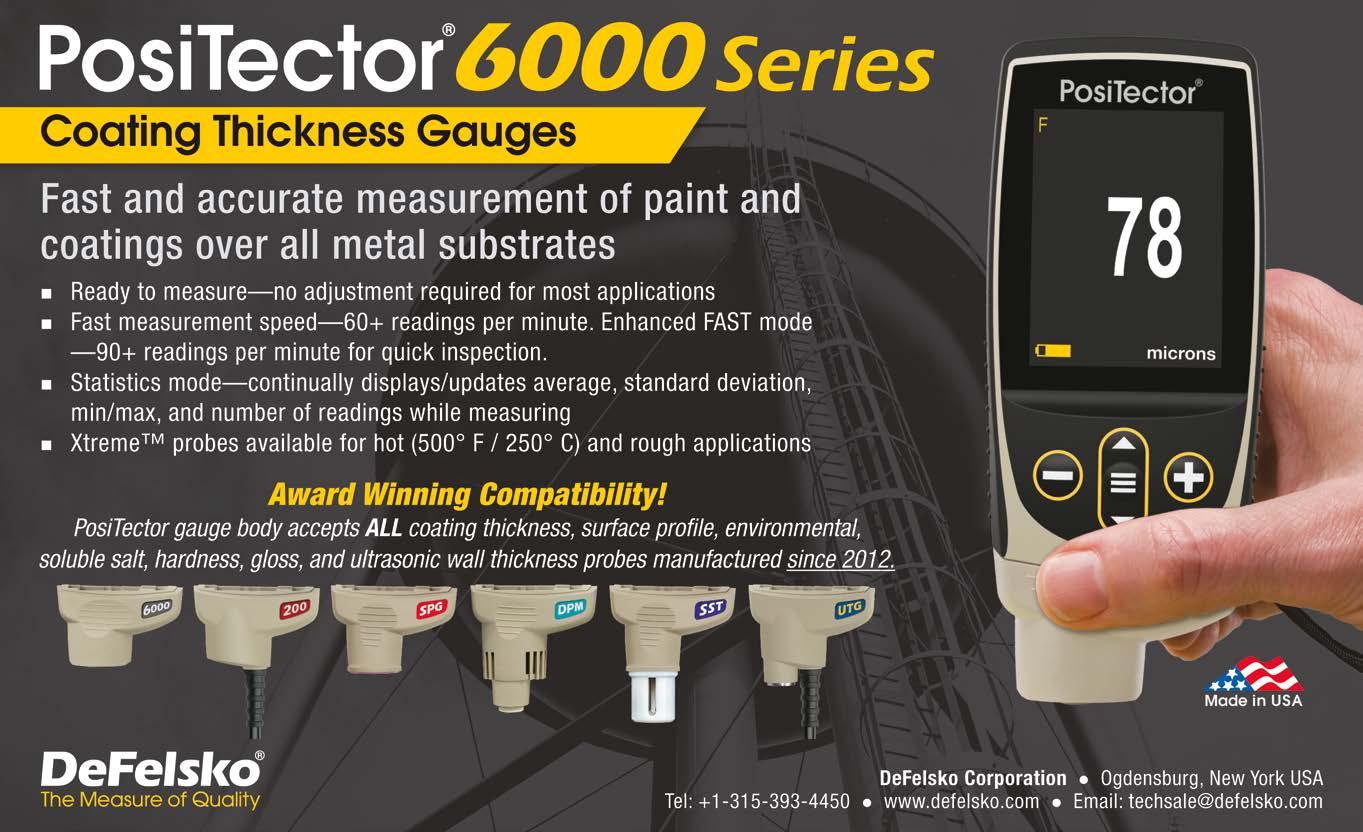
The future of epoxy coatings in the hydropower industry
As the demand for renewable energy sources continues to grow, so too does the necessity for hydropower. This is expected to drive an increase in the use of epoxy coatings in the hydropower industry, as more and more equipment is needed to meet the growing demand for electricity. In addition, advances in epoxy coating technology are likely to make them even more effective at protecting machinery and infrastructure from corrosion and other forms of damage.
One area of particular interest is the development of epoxy coatings that are more environmentally friendly. As the world becomes increasingly concerned about the impact of industrial processes on the environment, there is a growing demand for coatings that are engineered with plant-derived ingredients. The Belzona Research and Development Team are currently in the process of formulating products made from bio-based materials that are produced from sustainable plant-based feedstocks, rather than the traditional fossil-fuel based ingredients.
Conclusion
Epoxy coatings play a critical role in the hydropower industry, providing protection against corrosion, improving efficiency, and withstanding the harsh environments found in hydropower operations. As the demand for renewable energy continues to grow, the use of epoxy coatings in the hydropower industry is expected to increase, and advances in technology are likely to make them even more effective. By working together, the hydropower industry and coating manufacturers can help to develop coatings that are both effective and environmentally conscious, ensuring a sustainable future for the industry and for the planet. ‹
edited by MontiPower Hennef, Germany - info@montipower.com
The Bristle Blaster® is considered as a substitute for grit blasting and this is certainly true when it is used over small areas. However, it cannot be considered a substitute for grit blasting over larger areas where it cannot compete on production rates for OEM or outdoor work when access is possible.
Its main advantage for small areas is that no heavy equipment needs to be mobilized, there is little dust contamination produced in the work area and therefore the clean-up regimes are not as arduous. It is however much more advantageous than hand tools such as grinders and needle guns.
The benefits of the Bristle Blaster’s use are the following:
Corrosion, mill scale and coating removal similar to ISO 8501-1 Sa 2.5
Surface texture/anchor profile 40120μm Rz (1.6-4.7 mils)
Environmentally friendly / grit-free process
Improved surface integrity
Negligible heat generation
Simple and economical compared to grit blasting in the field.
Currently, when undertaking pipework paint preparation, corrosion removal and coating damage assessment work, the utility network services utilise grit blasting. This can be cumbersome, produces waste and required a two-person team to undertake safely. The use of the Bristle Blaster® for the above activities is cheaper, produces little waste and can achieve the same results as grit blasting for small surface areas.
The unit can be purchased in either 110v or pneumatic versions with the 110v version easily run from the team vehicle power source, or, coupled with the V2G mobile power supply, could allow for work in remote locations, without requirement for vehicle access.
Tests’ results for 3 different surface prep methods
A well-known European utility company did some research. Research was completed on coating adhesion and cyclic corrosion tests for three different surface prep methods used power wire brushing, grit blasting and bristle blasting. Power wire brushes can deliver SSPC SP 11 bare metal finishes, however, surface conditions ultimately lead to adhesion failure of the coatings due to poor anchor profiles. In contrast, bristle blasting removes coatings and affords an anchor pattern giving surface profiles similar to grit blasting. The difference between wire brushing and bristle blasting is that score markings & striations are eliminated, as bristle tips retract after impacting target surface. Corrosion tests were made under laboratory conditions after applying different coating systems on test specimens. Pull-off tests showed improved corrosion resistance for bristle blasting due to higher adhesion of coating systems. Surfaces machined by the power wire brushing were still corroded and therefore due to disbondment. That is, bristle blasting clearly outperformed power tool techniques, and is at least equivalent to and even can exceed the cleaning that is achieved by white metal blast cleaning SP 5 or ISO8501-1 Sa 2,5.
Health, safety & environment
Grit blasting process can produce hazardous dust and debris and must be performed by an individual that is confined or encapsulated in a control-suit, which both filters dust and supplies fresh air from a remote source. Furthermore, the noise level emitted by such equipment varies from 112-119 dB(A).
The equipment/apparatus used for carrying out grit blast operations is complex, costly, and requires considerable set-up and demobilisation time. Power wire brushing removes burrs and cleans impurities off various surfaces. The pipeline operator typically sees cup wire brush attachments utilised with angle grinders such as Makita GA4530. Cleaning and deburring with a wire brush remains by and large an intensely manual process, and produces a vibration magnitude of 7.5 m/s2. Choosing the right brush for the job and using the right technique can have a dramatic impact on throughput.
The grinders produce a Sound Pressure Level of 85 dB(A).
The wire bristle impact or bristle blasting process for surface preparation utilises a rotary disk which operates at a spindle speed of approximately 2,500 rpm. Noise levels emitted by this equipment are the same (83.5 dB(A)) for both the pneumatic and electric versions.
The compact 2.3kg tool is operated by grasping both the control handle and the main body of the tool, and directly exerting the working surface of the tool against the surface to be prepared.
The user-applied force required for this operation are far below that required for grit blasting and power wire brushing operations. The electric tool produces a vibration magnitude of 3.1 m/s2, and can be used for up to five hours before the action level is reached.
The Bristle Blaster tools
The Bristle Blaster® has been developed and significantly enhanced over the years. Today, a wide range of Bristle Blaster® tools are available, including:
Bristle Blaster® Pneumatic, which has ATEX approval for use in Zone 2 as tested by Gexcon from Bergen with air-cooling.
Bristle Blaster® Electric Single, 110V and 240V units for standard electric power sources
Bristle Blaster® Cordless, electric battery operated for use in remote locations and for rope-access work
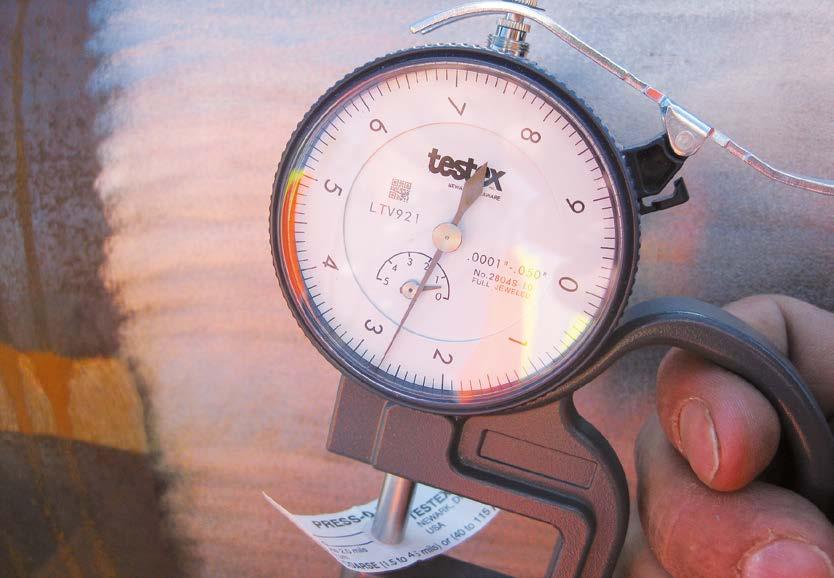
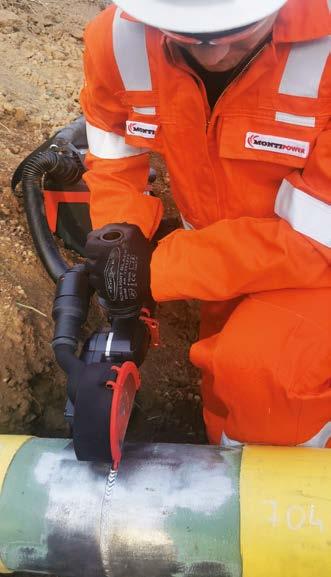
Bristle Blaster® Double, 110V and 240V, fits 2 x 23mm Bristle Blaster belts for Double the bristle blasting area
Bristle Blaster® Axial – specially designed for difficult-to-reach areas such as weld seams, corners, flanges and more
Bristle Blaster® Subsea – for underwater surface preparation.
A Bristle Blaster® belt consists of spring steel wire bristle tips that are bent forward and dynamically tuned to the hand-held power tool. The bristle tips are specially designed and sharpened to strike the corroded surface with kinetic energy that is equivalent to conventional blasting processes that use grit blast media.
Immediately after the bristle tips strike the corroded steel surface, they retract from the substrate, which results in the removal of mill scale, rust, and existing paints and creates a new surface profile where the peaks and the valleys form a continuous pattern with no smooth, unprofiled areas. Consequently, surfaces that have been treated by bristle blasting have a texture and visual cleanliness that mimic those obtained by conventional grit blasting processes.
The tools should be used with the accelerator bar when higher surface profiles depths are required or without the accelerator bar when lower surface profile depths are specified or for softer ferrous and non-ferrous substrates, including composites and aluminium. The Bristle Blaster® with the accelerator bar should regularly achieve surface profiles >75 micron (3 mil), while without the accelerator bar surface profiles of circa 25 micron (1 mil) is the norm.
Standard pneumatic and electric variomatic (also cordless) drive units without the accelerator bar are available as MBX®. MBX® stands for metal blasting and bristle blasting for steel substrates. The MBX® wire bristle tips are shorter than the Bristle Blaster® wires. The MBX carbon brush bristle tips are hardened. The MBX® bristles are available with a knee like the Bristle Blaster belts, but also without the knee as a straight variant for finer homogeneous surface profile grades. The MBX® comes in course, medium and fine variants similar to sanding machines.
The advantages of the bristle blasting processes
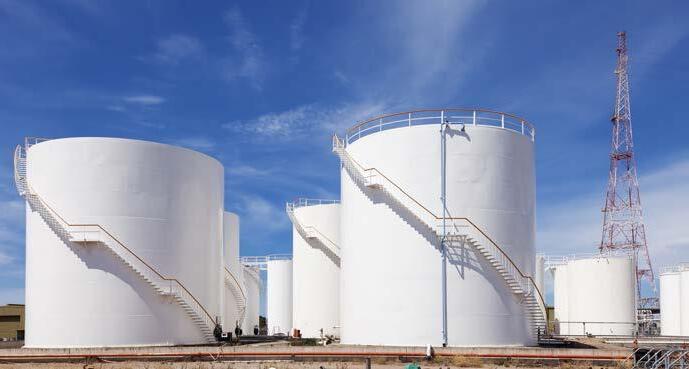
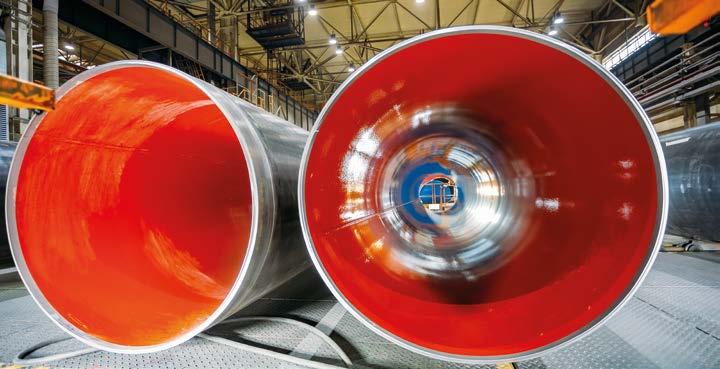
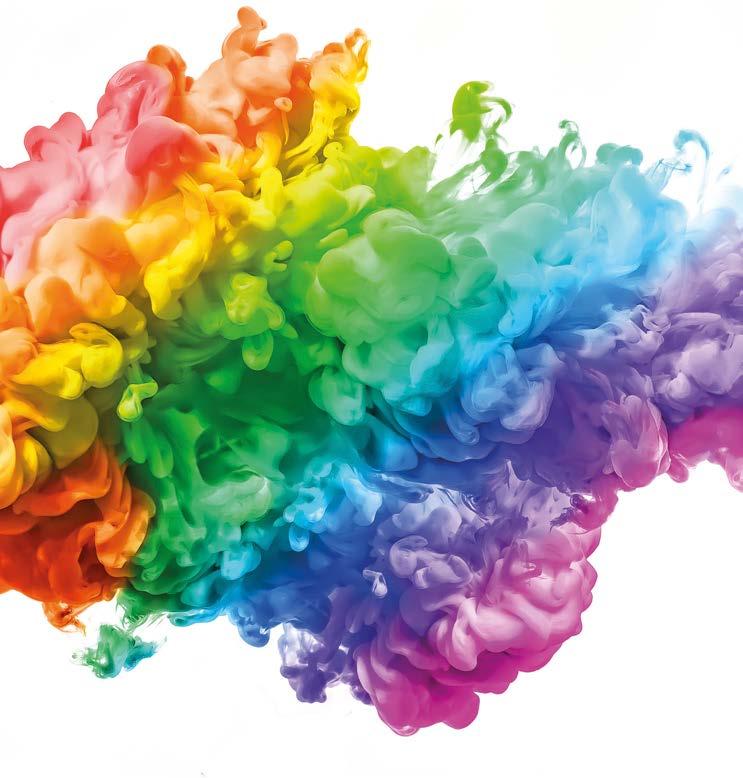
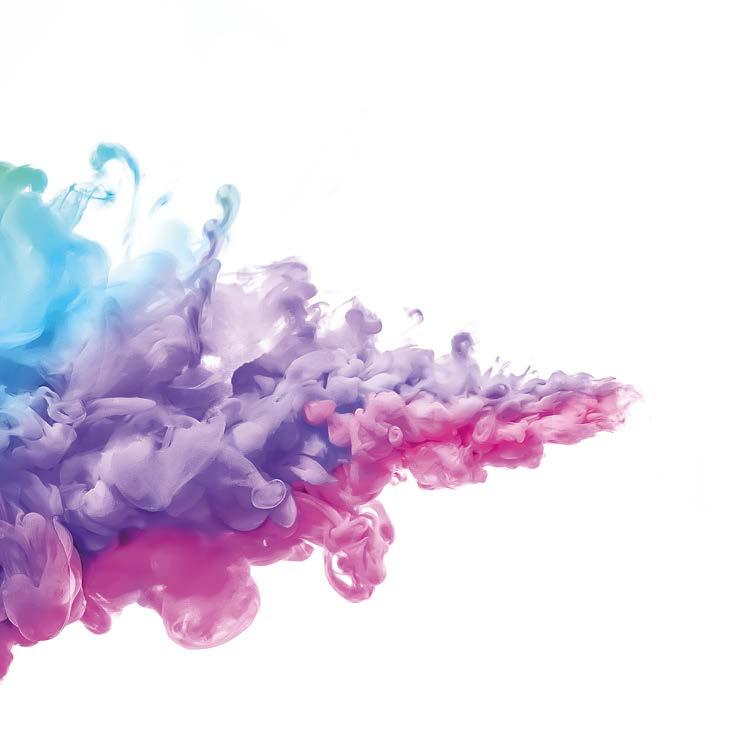
Bristle blasting simplifies the surface preparation operation and reduces costs through the elimination of expensive equipment, media and extensive environmental and safety measures. Although the bristle blasting process is ideally suited for spot repair applications, it can also be readily applied to larger surface areas where the use of other metal cleaning processes may be prohibitive.
For any coating job, it is recommended to make an assessment of the correct tool and bristle for the surface desired and the application at hand. This is particularly true for difficult to prepare areas such as corners, edges, and weld seams. For flat surfaces, the Bristle Blaster® Double or Prepper® Quattro can bring significant efficiency gains in terms of time and costs. An assessment of the operating area will also need to be considered, though the Bristle Blaster® or MBX® is specially designed for a wide range of environments:
Bristle blasting does not use or produce hazardous materials
– steel bridges can be bristle blasted safely while passenger trains continue to operate
Bristle blasting is a green alternative with low vibration levels and sound pressure – pipelines in environmentally protected areas can be safely prepared with the Bristle Blaster and the consumed belts can be recycled
Bristle blasting is a cost-efficient alternative – set-up is quick and easy and there is no need for enclosures, grit-recovery, breathing apparatus or complex equipment
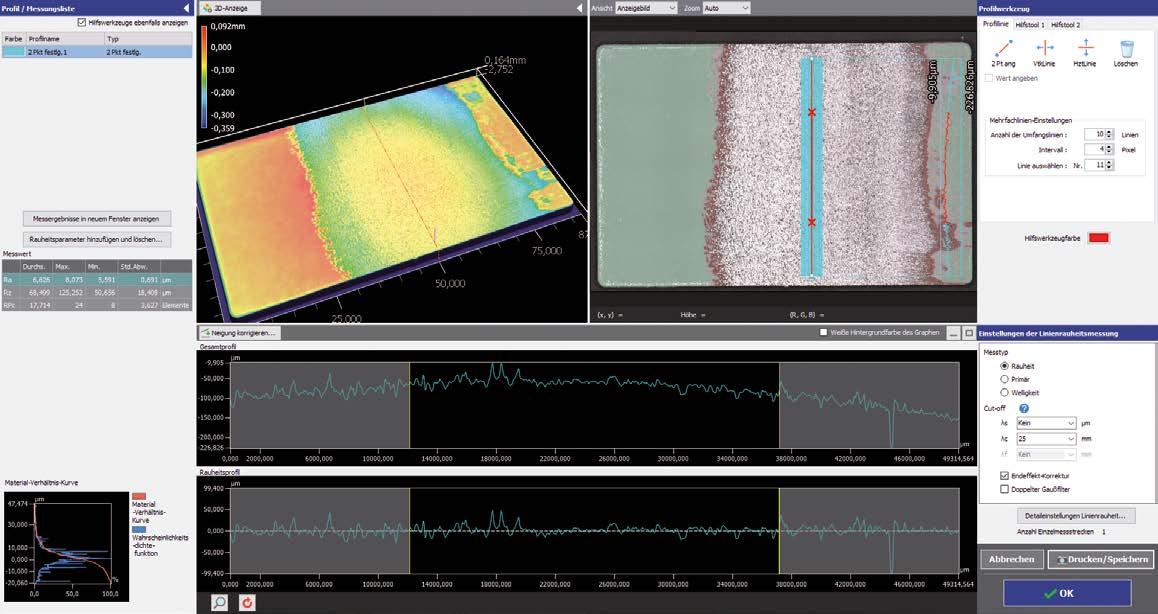

Bristle blasters are extremely portable and extremely lightweight – weighing as little as 1.1kg and vacuum control units (also cordless) can be easily connected
New features are always being introduced – such as dead man’s switch, safety caps, and rope access fittings – continually making bristle blasters even safer and more convenient on the job.
Bristles are available in carbon steel and stainless steel, with belts available in a range of sizes from 43mm, 23mm, 11mm and half 11mm bristles. Zapper wheels in silicone at 1300RPM as cordless units or yellow wheel erasers (up to 3500RPM) are also available for edge feathering of thick polyethylene, polypropylene or removal of glue and glued foils/stickers.
Monti surface preparation equipment is also available for use with drones, magnetic wall crawlers or walk-behind solutions, ideal for decks and floors.
For best use of the tool(s), it is highly recommended that the user is trained by qualified individuals. Understanding the proper technique and approaches to different applications are important for best results and in ensuring efficient use of the tools and belts to ensure the best possible coating and sealant bond.
Advantages of the bristle blasting method:
No special skills required (training recommended for best use)
Minimal safety and hazmat requirements when compared to abrasive blasting
Much smaller environmental footprint when compared to abrasive blasting
Cleanliness grades similar to ISO 8501-1 Sa2.5 /SSPC-VIS1 SP 10/Nace No.2
Complimentary to abrasive blast cleaning for critical areas such as weld seams and hard to reach areas.
Low noise, low vibration and low rotational speeds of approximately 2500 RPM
Versatile with different tool configurations and different sized belts for different applications
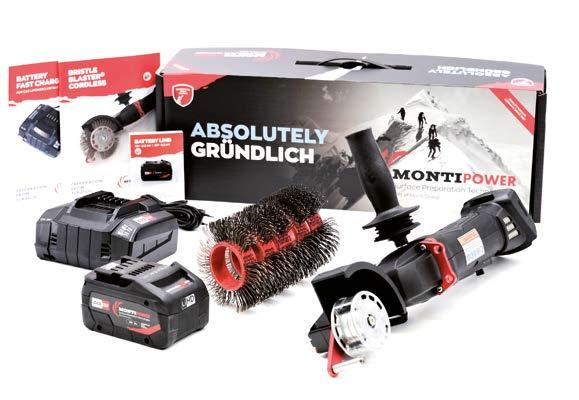
Efficient surface profiling solutions in combination with other methods such as induction coating removal or water jetting
Bristles can be resharpened for longer use, and bristles can be recycled
Removes mill scale
Bristle Blaster Axial drive units are specially designed for difficult to reach areas
Bristle Blaster Pneumatic units are ATEX approved for surface preparation in potentially explosive environments
No burnishing, polishing or smearing effect.
Disadvantages of the bristle blasting method:
Less efficient at removing thick-pack rust
Less efficient than abrasive blast cleaning for large surfaces
Bristles can create cold sparks with metal contact.
Whether removing, cleaning or profiling, the Bristle Blaster is a powerful technology ideally suited to a wide range of fabricating and infrastructure-support operations such as onshore/offshore well drilling installations, bridge refurbishment, the fabrication and repair of naval / marine vessels and industrial maintenance applications. ‹
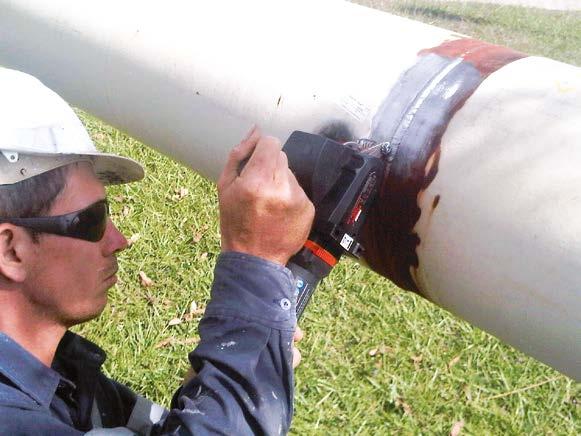