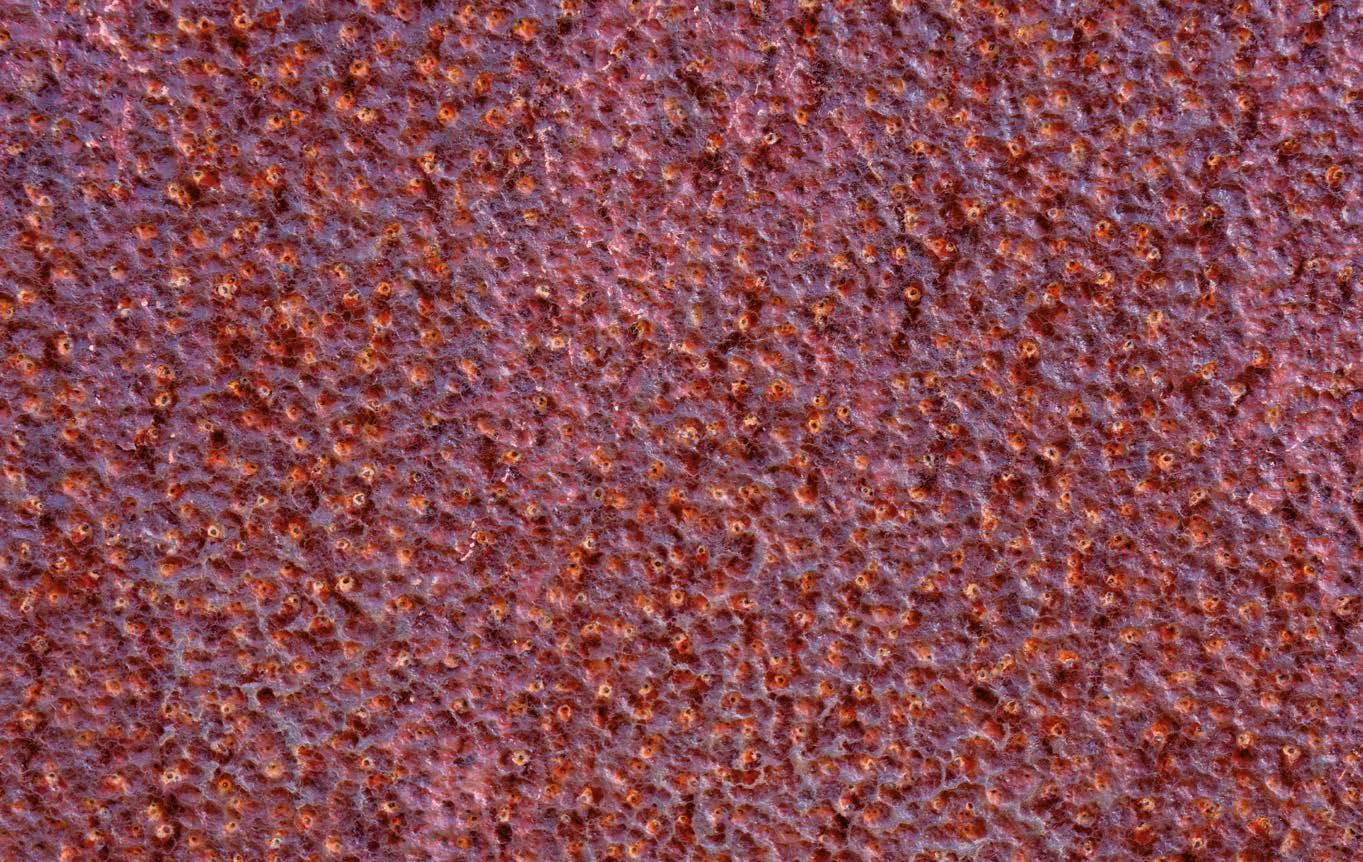
6 minute read
Local intensification of general corrosion attack in quenched and tempered steel: the role of inclusions
by Francesco Andreatta* and Matteo Zanocco University of Udine, Polytechnic department of engineering and architecture - Udine, Italy
Stefano Virgilio
Wärtsilä Italia S.p.A. - San Dorligo della Valle (Trieste), Italy
*Corresponding author: francesco.andreatta@uniud.it
Inclusions in 42CrMo4 QT steel
The 42CrMo4 QT is typically employed in the oil&gas, offshore and marine industry due to its high mechanical strength combined with good toughness in the quenched and tempered condition (QT) [1–4] which was processed with the intent of having fewer and smaller inclusions, was compared with regular grade SS304. Transmission electron microscopy (TEM). Inclusions are unavoidable in steels and can be produced during steel deoxidation or during the cooling of the melt in the steelmaking process [5–8]. Typical inclusions include alumina, silica, manganese sulphide or complex oxy-sulphide inclusions in the case of Ca treated steels [6–8]. In particular, Ca treatment of 42CrMo4 steel improves its fatigue resistance trough the formation of globular inclusions consisting of a core of alumina and a (Ca,Mn)S outer shell [7].
The inclusions in 42CrMo4 QT steel (composition given in Table 1) were characterized by means of field emission – scanning electron microscope (FE-SEM). Figure 1 shows an example of a typical oxysulphide inclusion with size of about 5 μm.
As it can be seen in the elemental maps obtained by energy dispersive x-ray spectroscopy (EDXS), the core of the inclusion consists of alumina. The outer part of the inclusion exhibits the signals of Mn, S and Ca.
This is related to the nucleation of MnS on the alumina core promoted by the Ca treatment of the steel. As a result, the MnS outer part of the inclusions contains Ca. A narrow gap can be appreciated at the periphery of the globular inclusion.
Topography and surface potential of the inclusions
Non-metallic inclusions like the one shown in Fig. 1 can cause localized attack in the form of pitting [9–12]. In order to evaluate the role of the inclusions in the initiation of pitting corrosion, the microstructure of 42CrMo4 QT steel was investigated by means of an atomic force microscope. This technique was used to evaluate the topography at inclusion sites. Figure 2A shows the topographic map of a core-shell oxy-sulphide inclusion similar to that shown in Fig. 1.
The narrow gap between the inclusion and the surrounding steel matrix is clearly visible in the topographic map. Figure 2B shows the surface potential map (Volta potential) for the same region containing the inclusion. The outer shell of the inclusion appears brighter than the surrounding matrix. The potential difference between the shell of the inclusion and the matrix is about 70 mV. This indicates that the shell of the inclusion is more noble than the matrix and would be the cathode in the local galvanic couple with the steel matrix in the presence of an aggressive electrolyte. The core of the inclusion exhibits similar contrast to that of the matrix suggesting that the core of the inclusion would establish a weak galvanic couple with the surrounding steel.
The existence of a Volta potential difference between inclusions and steel matrix (as shown in Fig. 2B) has been often correlated in literature to localized attack in the form of pitting [11, 13, 14]. Besides, this is associated to a deep and narrow gap at the periphery of the inclusion that could provide conditions favourable to crevice corrosion.
The existence of such gaps is well known in literature and is the result of the different thermal expansion coefficient and deformability of the inclusions with respect to the matrix [9, 11]. This leads to the formation of the gaps during thermo-mechanical processing of the high strength steel.
Localized corrosion at the inclusions
Galvanostatic polarization measurements (current density of 1 mA/cm2 for 1 h) were carried out in order to evaluate the onset of localized attack in the 42CrMo4 QT steel. These measurements were carried out in 0.1M NaCl solution with 3 g/l Na2SO4. After the electrochemical test, the surface of the samples was inspected by FE-SEM in order to evaluate the morphology of attack.
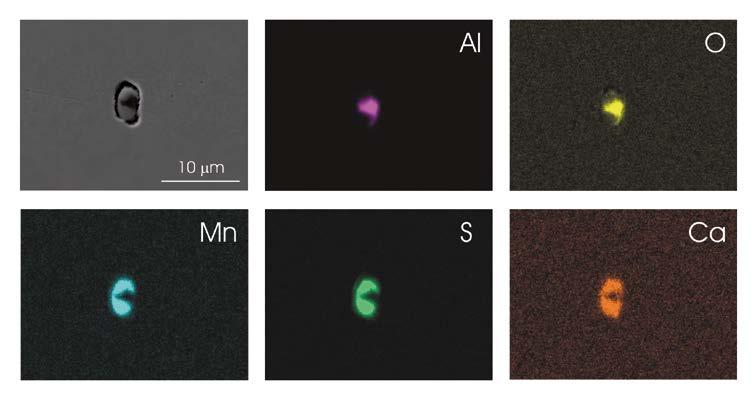
Figure 3 shows an example of the appearance of the surface of the 42CrMo4 QT steel after the galvanostatic polarization test. The steel surface displays several pits (indicated by the arrows).
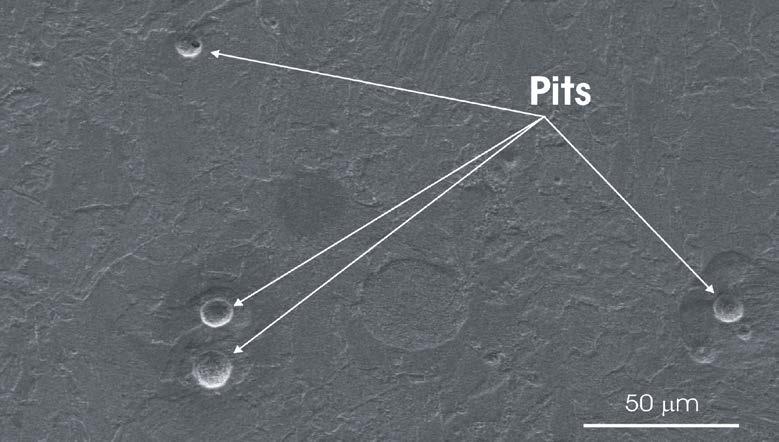
Moreover, the steel matrix exhibits general corrosion due to the attack of the tempered bainite in the matrix. The intensification of the attack in the form of pitting revealed in the galvanostatic polarization measurements was further investigated combining immersion tests with FE-SEM characterization. The surface of 42CrMo4 QT steel was initially characterised by means of FE-SEM to locate the inclusions and to obtain their chemical composition. Successively, the samples were immersed in 0.1M NaCl solution + 3 g/l Na2SO4 and inspected at different immersion times to observe the morphology of attack. Figure 4 reports FE-SEM images of a region containing an oxy-sulphide inclusion similar to that shown in Fig. 1 before and after the immersion for 3 h in the testing electrolyte. Before immersion, the composite structure of the inclusion and the gap at its periphery can be clearly recognized. After 3 h immersion, a large pit was formed at the site of the inclusion, which is no longer visible.
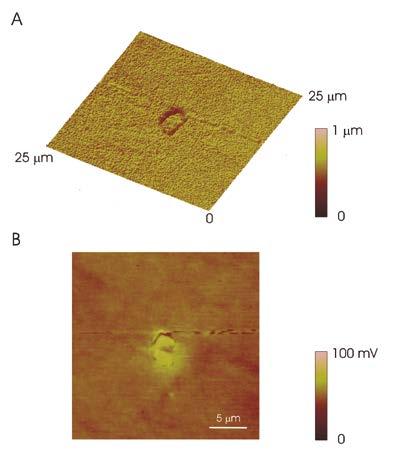
This clearly demonstrate that the localized attack shown in Fig. 3 preferentially initiates at the oxy-sulphide inclusions sites in 42CrMo4 QT steel. The fast initiation of the attack is due to the potential difference between the inclusion and the steel matrix, which is mainly due to the Ca-rich MnS shell with cathodic behaviour relative to the steel matrix. This can be considered the driving force for the intensification of the attack at the inclusions. Besides, the steel matrix surrounding the particle is generally attacked in line with the morphology observed after galvanostatic polarization (Fig. 3). This is related to the low corrosion resistance of the tempered bainite in the testing electrolyte. The role of the gap at the periphery of the inclusion should be also considered. As considered above in the discussion of the AFM topographic image (Fig. 2A), the gap can promote crevice corrosion, which most likely is responsible for the detachment of the inclusion from the steel matrix. Therefore, the morphology of attack shown in Fig. 4 suggest a synergistic effect between the
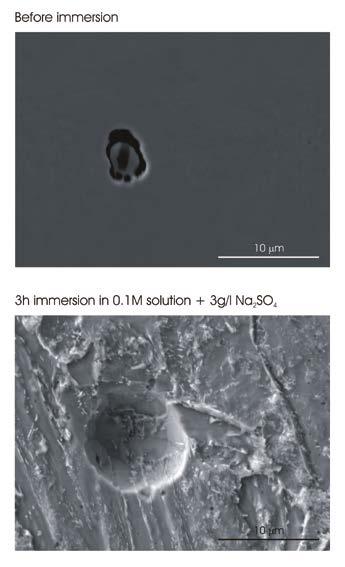
References galvanic coupling between the inclusion and the matrix and the crevice corrosion related to the gap at its periphery.
Conclusions
The localized attack of 42CrMo4 QT steel takes place at the sites of complex oxysulphide inclusions. The driving force for the onset of the attack is related to potential differences between the inclusions and the surrounding steel matrix leading to galvanic coupling with the steel matrix in the presence of an aggressive electrolyte. The general corrosion mechanism is coupled with non-uniform morphologies at narrow and deep gaps at the periphery of the inclusions during thermo-mechanical processing of the steel likely associated to the galvanic coupling. Marked uniform corrosion of the 42CrMo4 QT steel was noticed in 0.1M NaCl solution with 3 g/l Na2SO4, as expected, alongside with more localized effects at the inclusion sites. Results of this work highlight the importance of quality control in the production of high strength steels in order to improve their durability. ‹
1. Jun, J.; Holguin, K.; Frankel, G.S. Pitting Corrosion of Very Clean Type 304 Stainless Steel. Corrosion 2014, 70, 146–155, doi:10.5006/0995.
2. Zhu, M.; Deng, Z. Evolution and Control of Non-Metallic Inclusions in Steel During Secondary Refining Process. Jinshu Xuebao/Acta Metall. Sin. 2022, 58, 28–44, doi:10.11900/0412.1961.2021.00227.
3. Behrens, B.A.; Brunotte, K.; Petersen, T.; Diefenbach, J. Mechanical and Thermal Influences on Microstructural and Mechanical Properties during Process-Integrated Thermomechanically Controlled Forging of Tempering Steel AISI 4140. Materials (Basel). 2020, 13, 1–13, doi:10.3390/ma13245772.
4. Malau, V.; Fauzi, W.I. Effects of Heat Treatments on Mechanical Properties, Specific Wear and Corrosion Rate of HQ 809 Steel for Machinery Components Application. Proc. - 2018 4th Int. Conf. Sci. Technol. ICST 2018 2018, doi:10.1109/ICSTC.2018.8528600.
5. Wagner, R.; Schmiedel, A.; Dudczig, S.; Aneziris, C.G.; Volkova, O.; Biermann, H.; Weidner, A. Tailoring Nonmetallic Inclusions in 42CrMo4 as a Preparative Tool for Active and Reactive Steel Melt Filtration. Adv. Eng. Mater. 2022, 24, doi:10.1002/adem.202100640.
6. Weidner, A.; Krewerth, D.; Witschel, B.; Emmel, M.; Schmidt, A.; Gleinig, J.; Volkova, O.; Aneziris, C.G.; Biermann, H. Microstructure of Non-Metallic Inclusions Identified in Cast Steel 42CrMo4 after Metal Melt Filtration by Novel Foam Filters. Steel Res. Int. 2016, 87, 1038–1053, doi:10.1002/srin.201500462.
7. Zhang, L.; Thomas, B.G. State of the Art in the Control of Inclusions during Steel Ingot Casting. Metall. Mater. Trans. B Process Metall. Mater. Process. Sci. 2006, 37, 733–761, doi:10.1007/s11663-0060057-0.
8. Abraham, S.; Bodnar, R.; Raines, J.; Wang, Y. Inclusion Engineering and Metallurgy of Calcium Treatment. J. Iron Steel Res. Int. 2018, 25, 133–145, doi:10.1007/s42243-018-0017-3.
9. Liu, P.; Zhang, Q.H.; Watanabe, Y.; Shoji, T.; Cao, F.H. A Critical Review of the Recent Advances in Inclusion-Triggered Localized Corrosion in Steel. npj Mater. Degrad. 2022, 6, 1–17, doi:10.1038/ s41529-022-00294-6.
10. Li, Y.; Liu, J.; Deng, Y.; Han, X.; Hu, W.; Zhong, C. Ex Situ Characterization of Metallurgical Inclusions in X100 Pipeline Steel before and after Immersion in a Neutral PH Bicarbonate Solution. J. Alloys Compd. 2016, 673, 28–37, doi:10.1016/j.jallcom.2016.02.224.
11. Liu, C.; Yuan, H.; Li, X.; Che, Z.; Yang, S.; Du, C. Initiation Mechanism of Localized Corrosion Induced by Al2O3-MnS Composite Inclusion in Low-Alloy Structural Steel. Metals (Basel). 2022, 12, 1–10, doi:10.3390/met12040587.
12. Liu, C.; Revilla, R.I.; Zhang, D.; Liu, Z.; Lutz, A.; Zhang, F.; Zhao, T.; Ma, H.; Li, X.; Terryn, H. Role of Al2O3 Inclusions on the Localized Corrosion of Q460NH Weathering Steel in Marine Environment. Corros. Sci. 2018, 138, 96–104, doi:10.1016/j.corsci.2018.04.007.
13. Liu, C.; Revilla, R.I.; Liu, Z.; Zhang, D.; Li, X.; Terryn, H. Effect of Inclusions Modified by Rare Earth Elements (Ce, La) on Localized Marine Corrosion in Q460NH Weathering Steel. Corros. Sci. 2017,