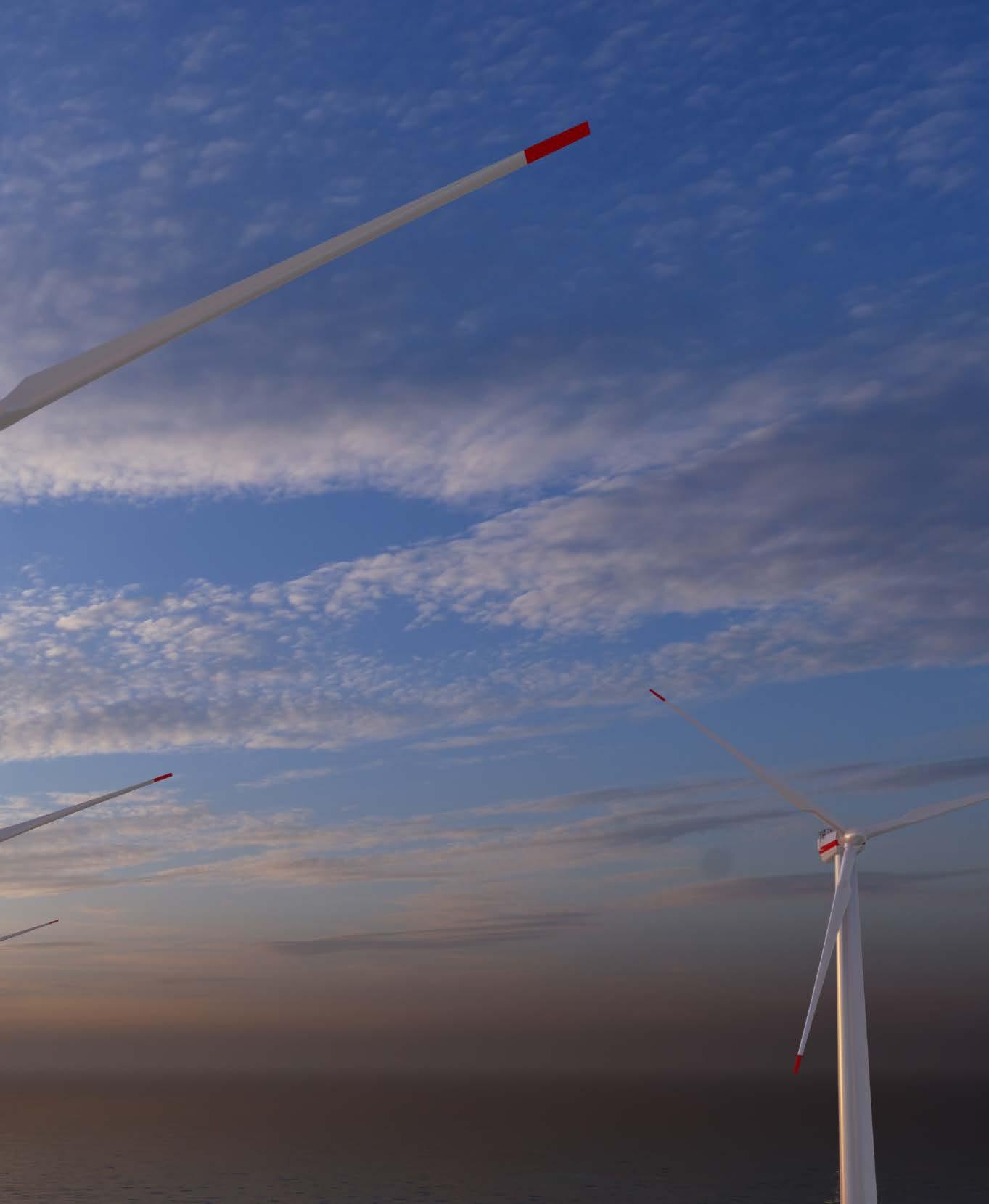
2 minute read
Reducing operation and maintenance costs of offshore wind turbines
copyright European Union, 1994-2023
Researchers have developed a high-accuracy, real-time, unattended, fast-response solution based on ultrasounds to monitor corrosion – an issue facing offshore structures.
Offshore wind is a fast-growing renewable energy source. In 2021, installed offshore wind capacity was 14.6 GW1 in the EU, a number set to increase by at least 25 times in 2030. Its deployment, therefore, plays a key role in achieving the European Union’s long-term climate and energy objectives2. However, the operation and maintenance (O&M) of offshore wind turbines is a challenging
1 https://energy.ec.europa.eu/topics/renewable-energy/offshore-renewable-energy_ en#:~:text=The%20installed%20offshore%20wind%20capacity,the%205%20EU%20sea%20basins 2 https://cordis.europa.eu/programme/id/H2020-EU.3.3 and costly process. This is a result of environmental conditions that cause high levels of corrosion and the lack of easy access to these turbines. “Addressing this, the EU-funded WATEREYE3 project set out to reduce O&M costs by designing an integrated solution that will enable wind farm operators to accurately predict future maintenance needs in real time in an unattended manner,” notes Ainhoa Cortés, project coordinator.
3 https://watereye-project.eu/about/
A closer look at the WATEREYE monitoring system

“We aimed to design a smart corrosion monitoring system to cover two fundamental areas: the splash zone and the atmospheric zone of an offshore wind turbine,” explains Cortés. The idea of the system is to monitor primarily the corrosion of the outer side of the wind turbine structure from the inner surface. “To cover large structures, a mobile platform based on a drone was proposed. This way, a smart ultrasound system is embedded into the drone allowing for the measurement of a high number of critical points per year,” adds Cortés. The splash zone, however, is different because this is a restricted area that is impossible to access with a drone. To monitor it, the project used a matrix of smart sensors that were fixed to measure the most critical points. “This way, the WATEREYE solution measures the wall thickness and relates the loss of thickness with the corrosion level,” confirms Cortés. The ultrasound data is sent wirelessly to the base station located inside the wind turbine. “We developed the algorithms, models and software tools to process the acquired data for a range of tasks,” adds Cortés.
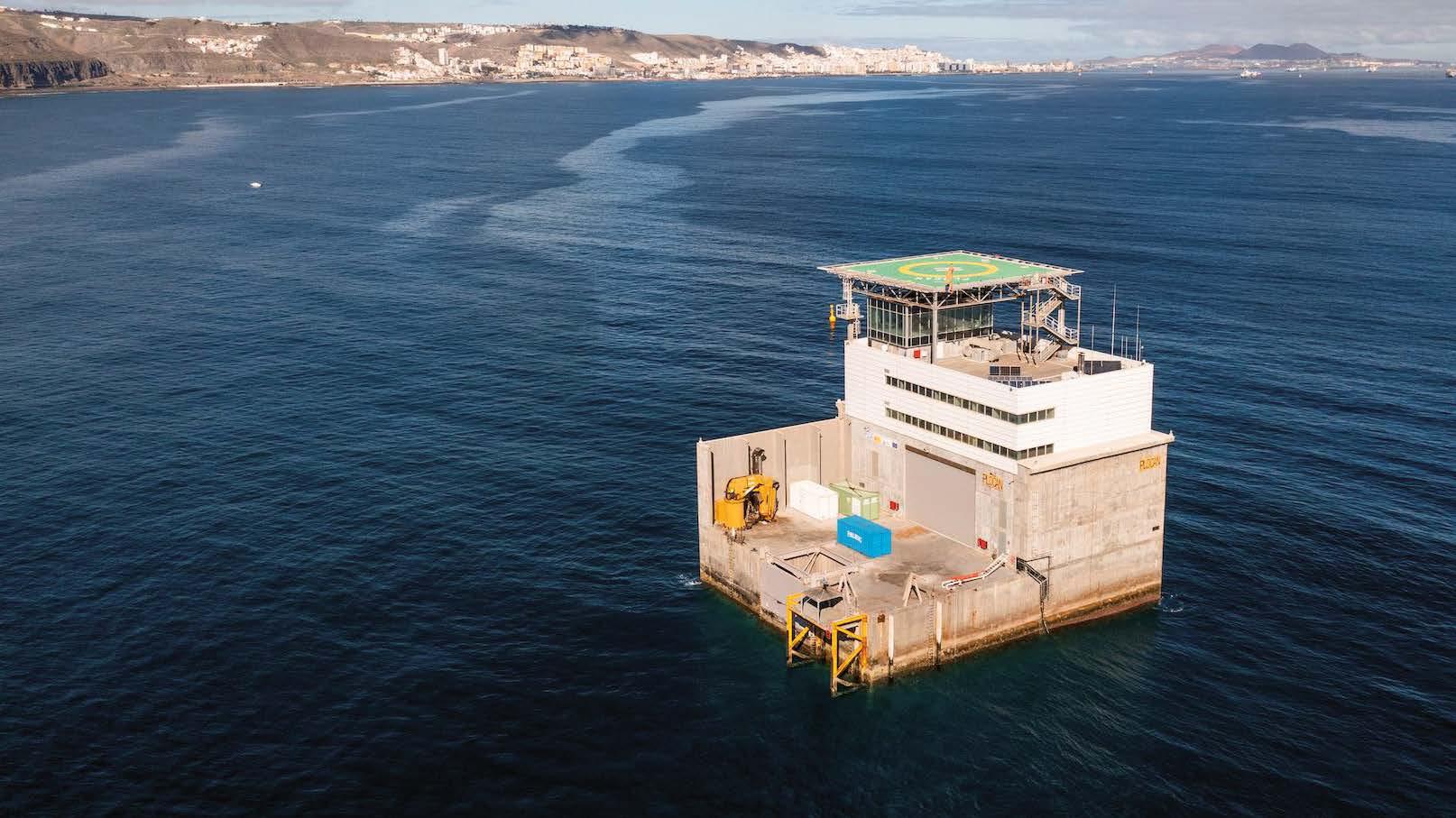
Overcoming current limitations of operation and maintenance efficiency
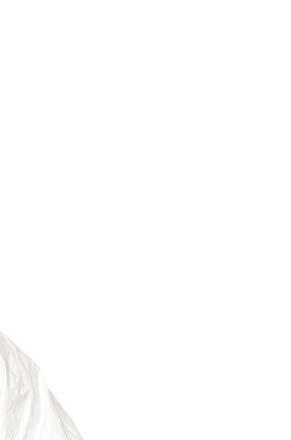
The WATEREYE solution was tested in a real environment at the offshore platform of PLOCAN4, where its functionality was successfully validated. “Mainly, the physical system: ultrasound measures and corrosion detection, drone positioning and wireless communications,” reports Cortés. Project results showed that the monitoring solution can detect the corrosion of large structures with high accuracy through a low-cost, low-weight and low-power consumption monitoring system. “We have designed a highaccuracy, unattended, fast-response and non-invasive ultrasound smart sensor and characterised the monitoring system to be flexible enough regarding the type of corrosion and the target thickness,” outlines Cortés.
The project has also successfully enhanced the calibration methods and communications protocols of the radio frequency technologies with the aim of transmitting the measures wirelessly
4 https://plocan.eu/en with high reliability inside a metallic offshore tower. “We have also achieved a precise positioning of the drone inside the wind turbine and developed mathematical models to detect the corrosion degradation rate and predict the type of degradation and failure mechanisms that a given coating/steel material combination will suffer from, in a given environment,” confirms Cortés. As for the next step, “it would be to analyse in depth pitting corrosion, and the idea is to enhance the developed ultrasound solution to quantify the pit size,” concludes Cortés. ‹
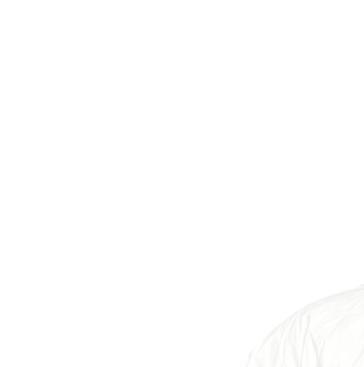
Cavitation
Erosion
Corrosion
Engineering made in Germany - since 1960
Ultra wear resistant elastomeric coatings repair compounds
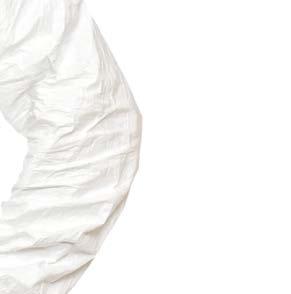
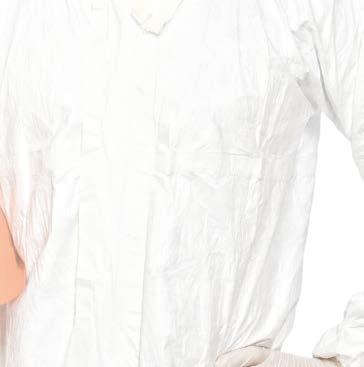

