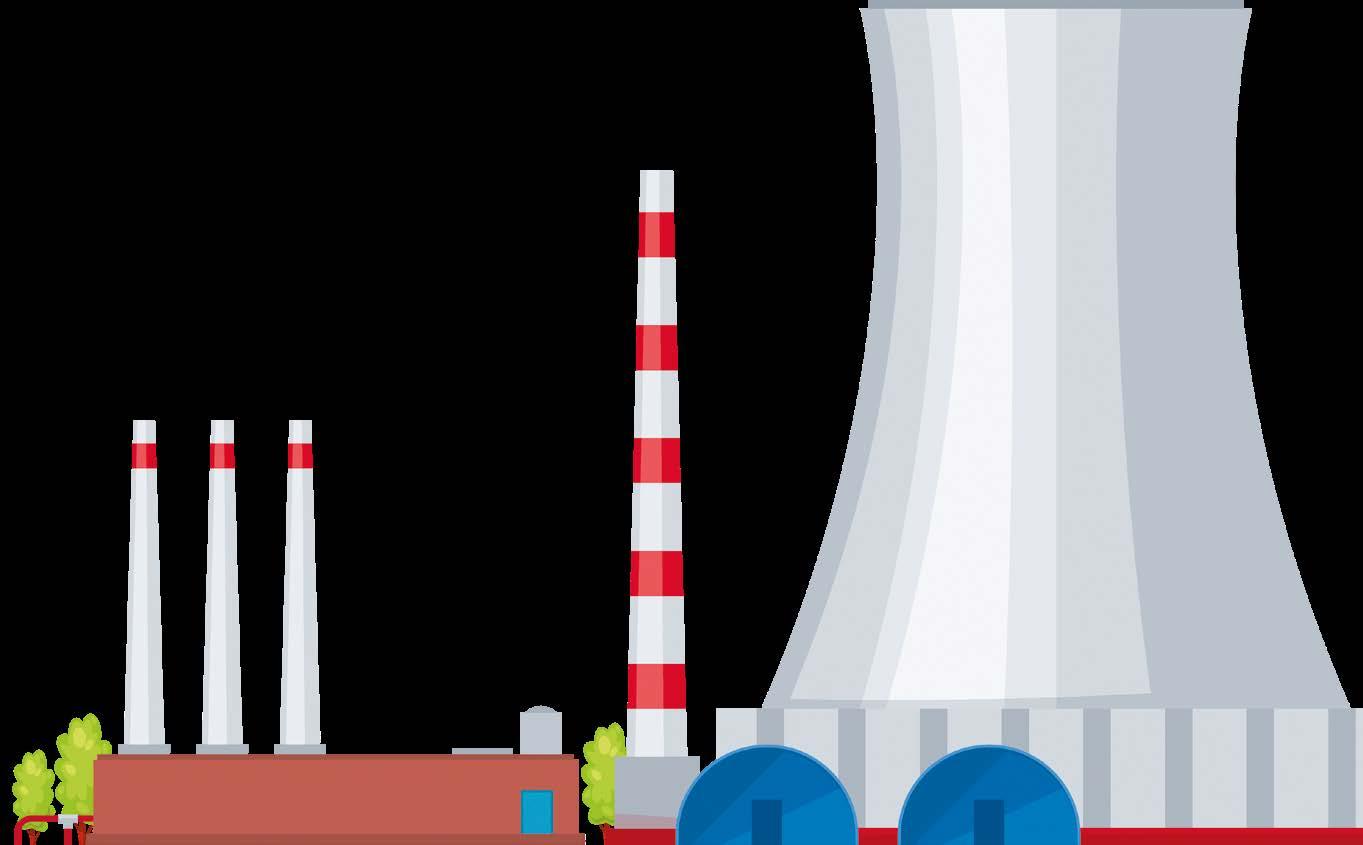
8 minute read
Micro-cracks caused by corrosion under insulation in France’s nuclear power plants
by Monica Fumagalli, ipcm®
The electricity supply of France, the world’s fifth-largest economic power, is being severely challenged by corrosion damage in the pipes of the primary and auxiliary cooling circuits of numerous nuclear reactors.
Anow famous report released a few years ago by NACE International1 estimated that the global cost of corrosion is equivalent to over 3% of world GDP. As is easy to deduce, maintenance and repair of damage caused by this relentless phenomenon have always played a major role in the management of assets, as it can have major economic consequences and even lead to emergency situations in terms of energy resources, such as, for example, the interruption of electricity and gas supply.
In addition to this, when it comes to nuclear energy, one of the most serious effects can be a leak in pipes, with a high risk of radioactive substances escaping. For more than a year now, this issue has been particularly topical in France, as periodic inspections have revealed micro-cracks in the primary and auxiliary cooling circuit piping of some reactors caused by corrosion under insulation, which has led to the closure of the affected power plants for repairs with well-known repercussions on the French government’s energy policy.
The current situation
In February, EDF - Électricité de France S.A., France’s leading energy producer and distributor, released some data on its electricity production in 2022, including almost 18 billion of Euros
The resulting interruptions meant that last year France became a net importer of electricity for the first time in decades. Now, what is causing the French nuclear power plants’ corrosion problems?
The origin of these problems
Caused by moisture accumulating under thermal insulation, corrosion under insulation can sometimes take the form of stress corrosion. This occurs due to the combined action of corrosion and prolonged tensile stress that causes the sudden and unexpected fracture of metallic materials and is characterised by rapid propagation due to these two factors’ interaction. At the end of 2021, stress corrosion cracking was discovered affecting the primary circuits of some of EDF’s nuclear reactors, which led to their prolonged shutdown for necessary repairs. Inspections carried out on nuclear reactors showed that almost one third of the French nuclear fleet was affected by corrosion issues and, as one of France’s best-known business and financial newspapers pointed out, by May 2022 the situation was so dramatic that not a week went by without “corrosion sous contrainte” being mentioned in media reports3
Inside a reactor
Nuclear power plants produce electricity using the heat generated
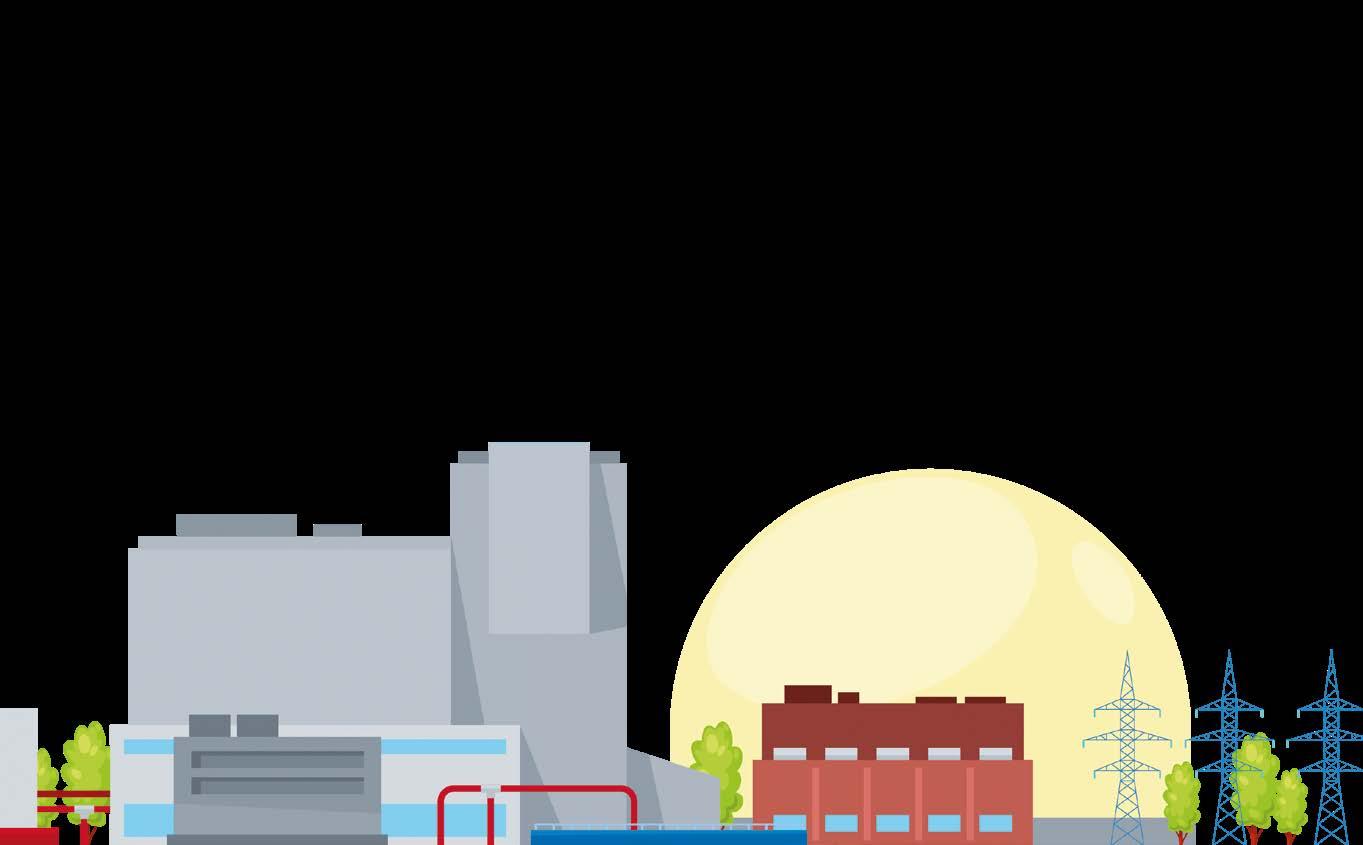
This cycle takes place in the so-called “primary circuit”. This, however, is not a completely closed loop: emergency circuits are connected to it for safety. In an emergency, this system allows water to be sent from a tank to cool the reactor. At the same time, since neutrons, uranium, and fission products are radioactive and therefore potentially harmful to living beings, the reactor is enclosed in steel and lead tanks to shield radiation and then protected with a double concrete casing.
Sixteen reactors, one common defect
The inspections carried out by EDF found that most of the micro-cracks caused by stress corrosion were located on the steel pipes (with a diameter of 25 to 30 cm and a thickness of 3 cm) that make up the “auxiliary circuits” connected to the reactors’ primary circuit, in which water circulates at around 330 °C. At the end of 2021, anomalies were found very close to their connection with the primary circuit, at a point where the pipes form a curve. Micro-cracks up to 5 mm caused by stress corrosion were found along the welds of these angle pipes. Since the thickness of steel pipes is 3 cm, there was no risk of leakage, but it was still necessary to take action to prevent these cracks from widening. Experts agreed that the problem stemmed from the shape of the angle pipes themselves, which can generate enough temperature changes to put a strain on steel. This defect concerns all the 16 most recently-built reactors. Repairing them is possible, but it is necessary to stop each reactor, replace the damaged part of the pipework, and reweld it, obviously while paying the utmost attention to radioactivity.
First signs of corrosion: the Civaux nuclear power plant
According to an official statement by EDF4, on 15 December 2021, during the second ten-year inspection carried out with nondestructive methods on reactor No. 1 in Civaux (New Aquitaine), one of the newest ones in the French nuclear fleet, damage was found in the stainless steel of a part of the piping of the safety injection system (the so-called “RIS”).
Ultrasonic tests on this circuit revealed faults at two welds located upstream and downstream of one bend of the 4 lines constituting the safety injection circuit. No defects had been found during the first inspection in 2011. EDF therefore proceeded to section the affected parts of the pipeline. Laboratory tests confirmed that the defects observed on the Civaux 1 reactor were linked to a degradation phenomenon that simultaneously involves the material and its intrinsic characteristics, i.e. the mechanical stresses to which it is subjected and the nature of the fluid circulating in it.
4 https://www.edf.fr/sites/groupe/files/contrib/groupe-edf/ producteur-industriel/carte-des-implantations/centrale-chooz/ actualites/2022/JANVIER/edf_note_info_ris_14janv2022.pdf
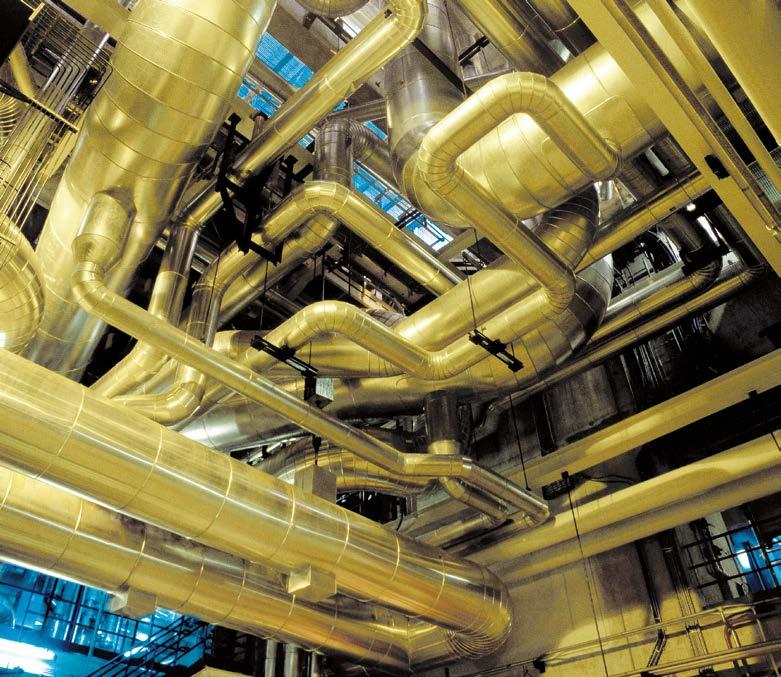
This is known as “corrosion under insulation” and it can be detected by carrying out specific ultrasonic tests, such as those carried out preemptively by EDF during inspections of its reactors. Other checks were then carried out on the same structures at reactor No. 2 of the Civaux nuclear power plant and they revealed similar anomalies.
The 4 reactors of the Civaux and Chooz (Ardennes) power plants use the same technology and form the N4 series of the French nuclear fleet. Therefore, as a precautionary measure, EDF decided to shut down the 2 reactors at the Chooz power plant in order to carry out these same checks. In the course of these inspections, a fault was detected on a section of the pipework in reactor No. 2 at Chooz B. Assessments are going to be extended to other areas. EDF concluded its report by stating that “solutions are being assessed for the replacement or repair of the affected portions of the pipeline. They will be implemented on a case-by-case basis, depending on the results of the inspections, in order to ensure the safety of all facilities,” and by communicating the duration of service interruptions due to repair work. Since these initial findings, other similar faults have been found in further reactors of the French nuclear fleet. The most recent one was at the Penly plant (Seine-Maritime), which was due to come back on line in May.
The last inspection: the Penly nuclear power plant
On 24 February this year, EDF announced that checks were being carried out on the welds of a pipe of the Penly 1 reactor, which had been repaired in January. This inspection quickly led to the discovery of a very large crack. According to the “Transitions & Energies” magazine5, the discovery of this further defect shows that the maintenance problems of the 56 reactors of the French
5 https://www.transitionsenergies.com/reacteurs-nucleaires-francais-pas-seulement-affectes-parcorrosion-sous-contrainte/ nuclear fleet go far beyond the stress corrosion issues detected in 2021, probably caused by a design flaw in the most recent reactors, which in turn leads to physical stresses on the materials causing cracks. In Penly, early indications are that the weak point would be some welds on the emergency cooling circuit that were “repaired” or “touched up” during the construction of the plant. A note released by the French Nuclear Safety Authority (ASN)6 stated that this significant corrosion defect consisted of a large crack with a length of 155 mm, i.e. one quarter of the pipe’s circumference, and a maximum depth of 23 mm, compared to a total pipe thickness of 27 mm. This resulted in the closure of the power plant for the necessary repairs and in the decision to change all the affected circuits at the same level as Penly (N4) and its predecessor, the 1,300-MW P’4-series reactor, by the end of 2023.
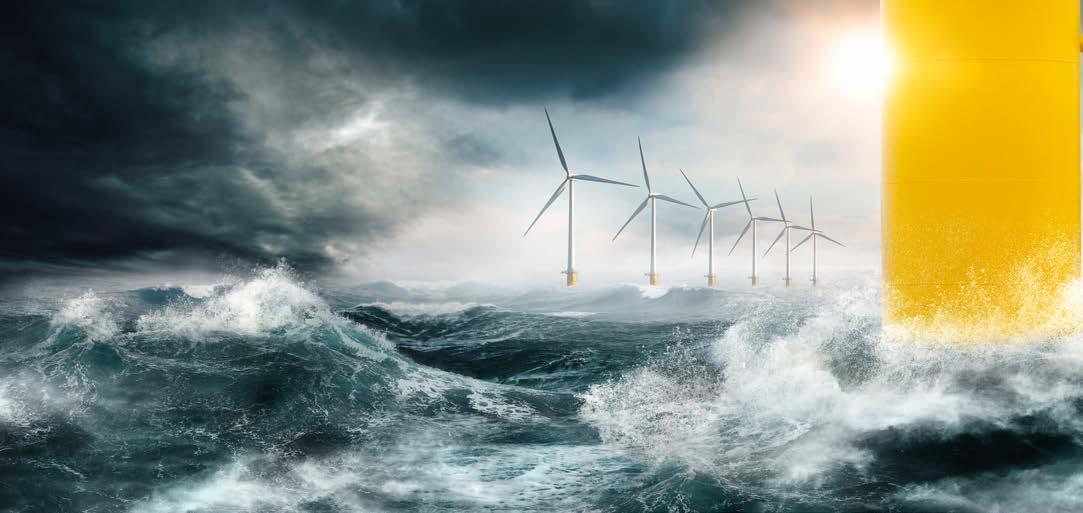
Conclusions
EDF pointed out that the occurrence of stress corrosion cracking is related to several factors – above all, the auxiliary circuit lines’ geometry and, secondly, the state of the welds and the mechanical stresses that this generates on the material. We can therefore conclude that, while it is true that the preparation of substrates, the choice of the most appropriate corrosion protection coatings, and the correct inspections are key to prevent corrosion, the ability to take into account already during the design phase the consequences that a given structure may have on the system’s circuits, including the stagnation of humidity that weakens the material and the mechanical stresses to which the entire system is subjected, is also essential to guarantee proper functioning and avoid service interruptions with serious consequences for an entire community and the economy of a country. ‹
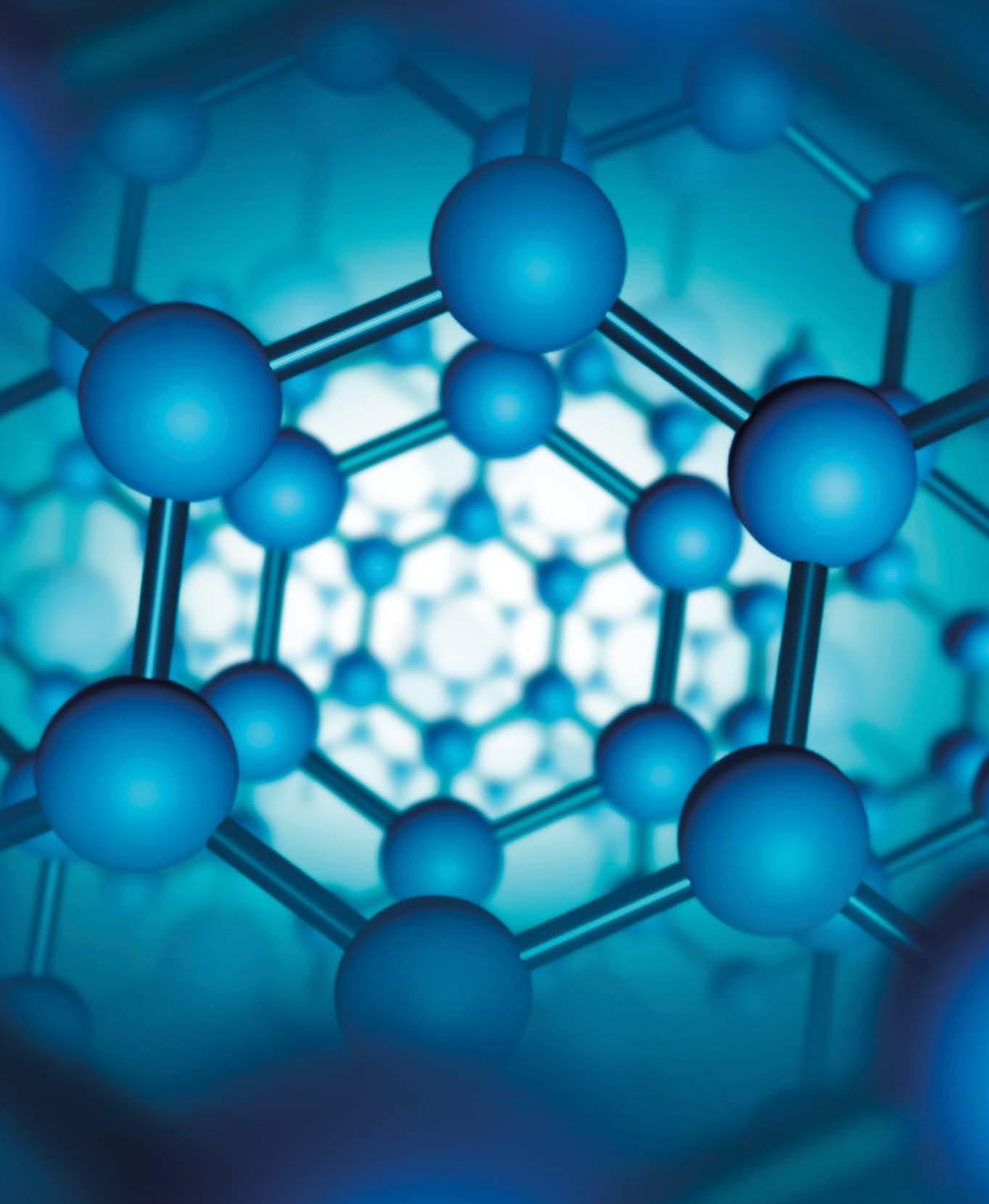
Corrosion is a costly issue that significantly impacts naval and marine infrastructure, bridges, buildings, pipelines, and many other industries. To help combat this problem, corrosion protective coatings can extend the life of existing infrastructure and equipment.
“The economic cost of corrosion is significant. According to a United States Congressional Briefing on May 31, 2012, corrosionrelated costs amounted to US$452 billion per year in the US, including US $22 billion for the Department of Defense. The global anti-corrosion coating market was estimated to be $27.4 Billion in 2019 and expected to grow to 63.7 Billion by 2030 according to Business Wire.” said Greg Fenton, CEO of Zentek. “To help address this issue, corrosion protective coatings are used to extend the life of existing infrastructure and equipment, generally providing a high return on investment. With ZenARMOR™, our team has developed a nanomaterial-based technology that has the potential to further enhance this return on investment by not only improving the performance of existing corrosion protection solutions but doing so in a way that reduces environmental impact.”
Third-party testing
The company is collaborating with Quantum Chemical, a division of Quantum Technical Services Ltd., a manufacturer of highperformance primers and coatings. Testing by Quantum Chemical of ZenARMOR™ in an epoxy system following ASTM B-117 Salt Spray Testing demonstrated excellent corrosion resistance with no blisters or any other signs of corrosion after 1,500 hours with the addition of a very low dose of ZenARMOR™ versus the same corrosion protection epoxy without ZenARMOR™ which started breaking down at the 1000-hour mark. ZenARMOR™ is also comprised of fewer active ingredients compared to other products in the market, which management believes potentially has environmental benefits versus other corrosion protection products. Testing is ongoing and the company will report on further significant testing milestones. Tony Lagrange, founder, and owner of Quantum Chemical since 1995 commented: “these initial results of ZenARMOR™ after 1,500 hours of salt spray testing is impressive. Corrosion is a significant problem, and we are excited to be part of the Zentek testing and optimizing strategy for the ISC challenge and to help address this global corrosion problem. We are also leaders in the development of intumescent coating and paint products. We have significant inhouse testing infrastructure equipment for intumescent coatings optimization. We are well positioned to work with Zentek on both corrosion and intumescent coating technologies that can improve performance and safety while reducing environmental impact.”
Next step: innovative solutions Canada testing stream – Military call for prototypes
The company also reports that a proposal for its ZenARMOR™ corrosion protection self-healing coating was submitted to the Innovative Solutions Canada (ISC) testing stream – Military Call for Prototypes. The company is pleased to announce that it has been advised that the ZenARMOR™ proposal has met the mandatory and technical evaluation criteria of the Military Call for Prototypes, Military Component, and is considered conditionally qualified, pending further steps such as matching our innovation with a Government of Canada Organization (GCO) interested in testing ZenARMOR™. The company and the ISC program have begun to socialize ZenARMOR™ to GCOs, exploring opportunities for partnership and testing. Conditionally qualified innovations are now listed on the ISC website.
Intellectual property
The company has filed a provisional patent with the United States Patent and Trademark Office for the ZenARMOR™ corrosion protection technology and has also filed a trademark for ZenARMOR™.
About Zentek Ltd.
Zentek is an IP development and commercialization company focused on the research, development and commercialization of novel products using graphene and nanomaterials for use in the healthcare industry and beyond.
Zentek’s patented ZenGUARD™ coating is shown to have 99% antimicrobial activity and to significantly increase the bacterial and viral filtration efficiency of both surgical masks and HVAC systems. Zentek’s ZenGUARD™ production facility is located in Guelph, Ontario. ‹