

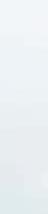
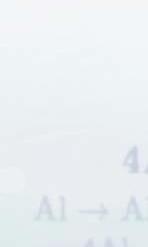


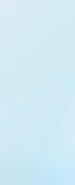
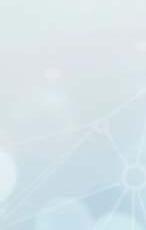

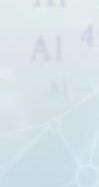
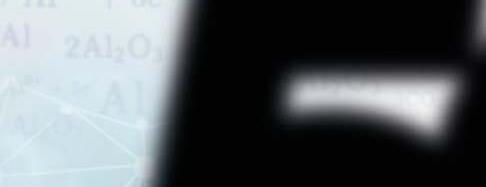
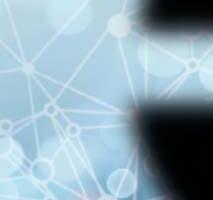
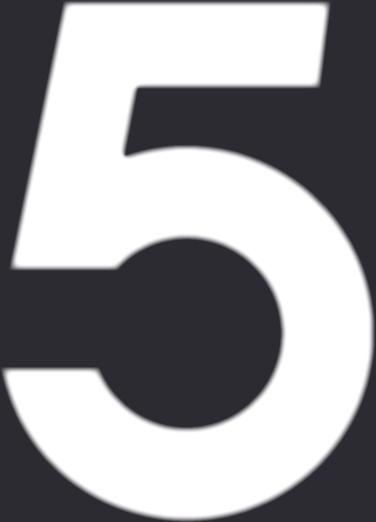


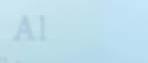


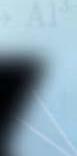

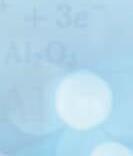



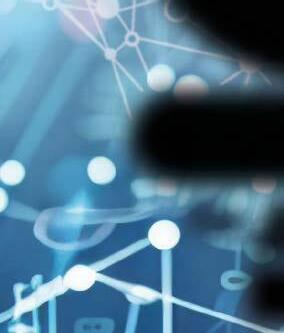

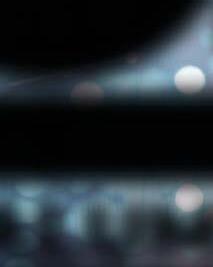






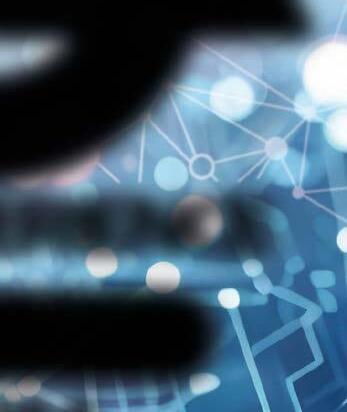


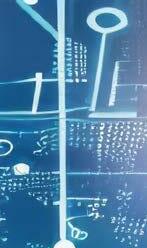
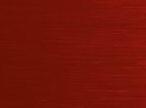

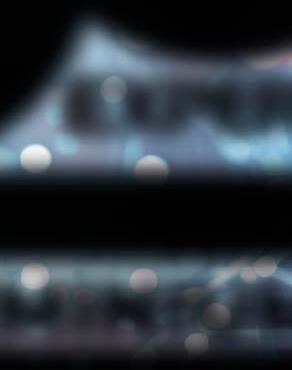










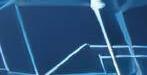
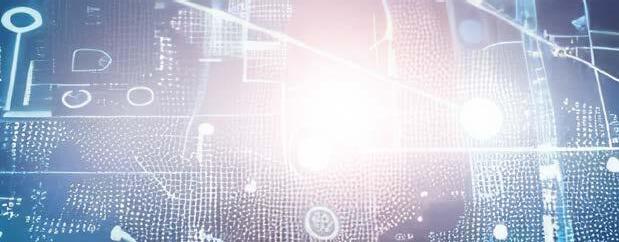
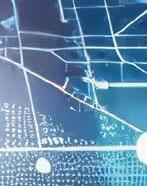

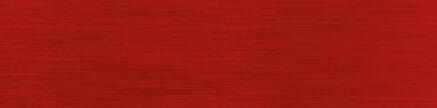

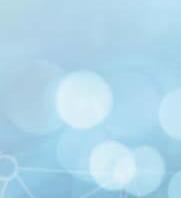
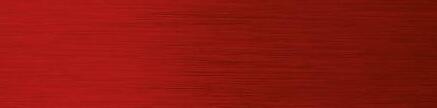

A new line of nanotechnology conversions for corrosion classes C3H - C4H - C5M
DOLLCOAT RS 103 is the first product in a new family of surface conversions for high-performance processes. It gives pre-treated surfaces extremely high-quality protection and corrosion resistance, whatever the nature of the paints used.
MAIN FEATURES
Multimetal no rinse product to be used at room temperature.
Applicable with nebulisation modules, through traditional recirculating or immersion nozzles.
Excellent pre-cataphoresis treatment.
REGISTRATI ORA
ESPOSIZIONE
CONFERENZA
TECHFOCUS
Esplora le più recenti tendenze e tecnologie nel mondo della pittura e dei rivestimenti, mentre stringi preziose connessioni con i leader del settore.
Paint & Coatings: il luogo dove l’ispirazione, l’apprendimento e le opportunità di networking si incontrano per trasformare il tuo business!
Unisciti a Noi per l’Aperitivo di Paint & Coatings!
Quando
Il primo giorno dell’evento, 22 ottobre 2024
Ora Dalle 17:00
Dove
NH Milano Congress Centre
POLYMER ACADEMY
sponsorizzato da
26
HIGHLIGHT OF THE MONTH
La nuova strategia di Eisenmann: ampio portfolio tecnologico, soluzioni personalizzate e presenza internazionale
66
FOCUS ON TECHNOLOGY
Vernici in polvere metallizzate e ad effetto per le superfici tridimensionali di rivestimento di Emboss
ADVANCEMENTS
46
Maggiore adesione della vernice e possibili risparmi grazie ad un nuovo processo di verniciatura di alta qualità
76
RESEARCH BREAKTHROUGH
Rivestimento antiaderente ultrasottile, duro e sostenibile rivoluziona i processi di formatura nello stampaggio a iniezione e nella pressofusione
Elevato tasso di recupero con la tecnologia a membrana ultrafiltrante nei processi di elettroforesi
Automazione e qualità elevata: Pulsar migliora il proprio processo di verniciatura con l’installazione di un nuovo robot antropomorfo
Le vernici in polvere a bassa temperatura di KABE-Farben: qualità per applicazioni architettoniche
62 SUCCESS STORIES
La collaborazione tra DHK, ALIT Technologies e Alufinish inaugura una nuova era per la protezione delle superfici metalliche
88
ROAD TO 2050
EcoAl® di Alsan - passivazione esente cromo nei processi di pretrattamento per la verniciatura a polvere
FOCUS ON TECHNOLOGY
Azeta si conferma azienda pioniera nella verniciatura dell’alluminio grazie a una nuova linea verticale combinata con un innovativo sistema di alimentazione polveri IPS
HIGHLIGHT OF THE MONTH
ST Powder Coatings presenta la nuova serie Green Oasis Range, l’oasi ecosostenibile del futuro
The HP series is specifically designed to uniform the thickness of powder applied on all parts of the painted support.
CARATTERISTICHE
La serie HP è pensata specificatamente per uniformare lo spessore di polvere applicata su tutte le parti del supporto verniciato.
Pulverit S.p.A. Italia
Via Carlo Reale, 15/4
20157 Milano-Italy
Tel +39 02 376751
email: pulverit@pulverit.it
Reduction between 15% and 30% of the powder required to paint the support. The HP series considerably reduces the “orange peel” effect due to the accumulation of powder in the parts adjacent to the critical points and minimizes the accumulation effect on the edges.
CARATTERISTICHE
Riduzione tra il 15 % e il 30% della polvere necessaria a verniciare il supporto. La serie HP riduce notevolmente l’effetto “buccia di arancia”
dovuto all’accumulo di polvere nelle parti adiacenti ai punti critici e minimizza l’effetto di accumulo sui bordi.
Pulverit Polska Sp. z o.o. ul. Strefowa 16
43100 Tychy-Polska
Tel. +48 32 329 14 11
email: biuro@pulverit.pl
Pulverit Deutschland GmbH Im Wert 3
73563 Mögglingen- Deutschland
telef.: +49 7174 7193000 email: info@pulverit.de
Pulverit Iberia s.l.u. c/ Caravis, 28, 1º 3ª 50197 Zaragoza Tel. +34 607163259
email: iberia@pulverit.it
108
112
114
90
ADVANCEMENTS
Evoluzione del design: la tecnologia
PVD di Kenosistec per finiture eleganti, durature e sostenibili
ROAD TO 2050
116
Cucchiaini per gelato e tee da golf: completamente assorbiti dalla natura
FOCUS ON TECHNOLOGY
Luxe Perfil: gli esperti nell’impossibile si affidano alle prestazioni del nuovo prodotto di pretrattamento
PrimeCoat® A109
ADVANCEMENTS
EcodePure è la via verso il riciclo dell'acqua e lo scarico zero
SUCCESS STORIES
ItalMesh riveste il nuovo Burger King di Rovereto con i suoi pannelli in alluminio forato e verniciato
SUCCESS STORIES
RIPOL a Bayreuth: innovazione e design avanguardista
102
FOCUS ON TECHNOLOGY
Alzare l’asticella della qualità: il nuovo impianto di Sirio Galv per la verniciatura a liquido di complementi d’arredo e illuminazione di alta fascia
146
SUCCESS STORIES
Delco Trailers rivoluziona il processo di finitura dei rimorchi con una nuova linea di verniciatura automatica
122
SUCCESS STORIES
PAN-DUR vernicia i sistemi di refrigerazione con EcoPaintJet di Dürr, senza necessità di mascheratura
126
ROAD TO 2050
In anticipo sulla regolamentazione per rivestimenti più ecologici
130 HIGHLIGHT OF THE MONTH
L’evoluzione di Vernici Caldart: una storia di successo italiana attraverso cinquant’anni di innovazione
134 ANALYSIS
La scelta: la transizione verde e l’effetto green HangOn
142 HIGHLIGHT OF THE MONTH
Defil Srl: innovazione nel settore della filtrazione industriale
150
ROAD TO 2050
Olea FP: un’opzione naturale e sostenibile per l’industria delle vernici e dei rivestimenti – Dal flusso degli scarti alle polveri funzionali ad alte prestazioni
154
UCIF INFORMS
La Cybersecurity aziendale: un impegno condiviso per la sicurezza digitale
156
160
COLOUR STUDY
Il fascino travolgente del rosa
MEETING THE INDUSTRY
The strength of Europolveri products does not derive from the sole mixture of carefully selected raw materials, but rather from the people who study, model and formulate powder coatings thanks to more than 40 years of experience, and provide customers with the best solutions on the market A clear corporate philosophy and a shared vision have allowed to supply a vast range of products for three generations With more than 1000 products available in stock and over 40,000 already formulated, Europolveri offers infinite solutions to customer requests
Request the English version at info@ipcm.it
Alessia Venturi Editor-in-chief Direttore Responsabile
Vi siete mai chiesti qual è la differenza tra progettualità e progettazione, tra un progetto e il suo sviluppo?
È la stessa che intercorre fra sogno e realtà.
Il sogno, come la progettualità, è la fase creativa, fantasiosa, ricca di dettagli e di ispirazione, con tratti irrealizzabili ma visionari. È la relazione esistente tra il soggetto e la propria realtà, tra il progettista e la tematica da affrontare.
La realtà, come la progettazione, è la fase costruttiva, la realizzazione dell’idea – o del sogno, per l’appunto - con colori meno vividi, con il sacrificio di qualche dettaglio e con il compromesso necessario fra ciò che è realizzabile e ciò che non lo è.
Nell’ambito dell’architettura e del design, la progettualità si riferisce dunque al pensiero creativo che sta dietro a un progetto, all’approccio visionario che guida la successiva realizzazione. La progettazione, invece fa riferimento al processo tecnico attraverso il quale si trasforma un’idea in un prodotto tangibile, come un edificio o un oggetto di design.
Colmare la distanza fra progetto e sviluppo significa disporre di tutte le tecnologie e di tutti i materiali, incluse le finiture, necessari alla trasposizione di un’idea nella realtà.
È proprio questa la fase più difficile per i progettisti, che a volte sono a digiuno delle necessarie informazioni tecniche sui materiali e sulle loro performance. È qui che entra in gioco il CMF (Colori Materiali Finiture), un’area progettuale che lavora sull’identità cromatica, tattile, decorativa di prodotti e ambienti: negli anni, gli esperti di CMF hanno lavorato, da una parte con i progettisti e, dall’altra, con i produttori di materiali e finiture, per promuovere la reciproca informazione, formazione e collaborazione per avvicinare il mondo progettuale – notoriamente portato ad abbattere i limiti – con il mondo industriale – che con i limiti tecnici e scientifici si scontra ogni giorno. ipcm®, sin dalla sua nascita nel 2010, ha avuto il settore dell’architettura metallica, inclusi architetti e designer, fra i suoi target preferenziali, conducendo un lavoro di informazione puntuale su tutto quello che è innovazione nel mondo dei materiali per la finitura delle superfici, ciò che costituisce la pelle di un prodotto, l’interfaccia fra esso e l’ambiente. Questo numero speciale Alluminio di ipcm® propone una serie di articoli e di casi di successo sui picchi di innovazione raggiunti nel settore del trattamento delle superfici in alluminio, il materiale sempre più diffuso in architettura – e non solo.
Come negli anni passati, ipcm® è media partner della più importante piattaforma dedicata all’industria dell’alluminio, la fiera internazionale ALUMINIUM di Düsseldorf.
Ci vediamo fra gli stand per discutere gli argomenti, le tendenze e gli sviluppi più significativi del settore.
Gianmaria Guidi, Germedia Srl – Brescia, Italia gianmaria.guidi@germedia.it
Purtroppo - e sempre più spesso nel settore dei trattamenti di verniciatura - è possibile verificare come per la nostra società non sia stato possibile anticipare ed evitare la perdita dei livelli di conoscenza, abilità e competenza. Kaufman nel 1974 definiva questo fenomeno l’obsolescenza delle competenze, riferendosi alla mancanza di conoscenze o abilità aggiornate necessarie a un lavoratore per continuare a svolgere perfettamente la sua attività professionale attuale o futura. Sempre più spesso durante le attività professionali, si affrontano grosse problematiche che derivano proprio dalla mancata compensazione delle fisiologiche asimmetrie informative tra parti contrattuali, che attualmente non riescono più ad essere adeguatamente compensate per mancanza
di competenze tecniche specifiche. Negli ultimi decenni, le dinamiche di mercato hanno favorito aspetti economici e finanziari a discapito degli investimenti in formazione tecnica, dando per scontato che gli aspetti tecnici alla base del settore fossero ormai assunti radicati nella consapevolezza comune. Il caso di seguito descritto cerca di rifocalizzare l’attenzione sul metodo di calcolo che definisce l’incidenza economica dei prodotti vernicianti in un progetto di verniciatura.
Criteri di calcolo per la resa pratica
Ogni progetto di verniciatura richiede un’approfondita analisi di fattibilità, che certamente deve considerare vari fattori e vincoli, come i vincoli
temporali, tecnologici, normativi e, non ultimi per importanza, i vincoli economici. Nel presente articolo verrà analizzato, in particolare, l’aspetto relativo al calcolo della resa dei prodotti vernicianti, quale voce di costo direttamente incidente sul fattore economico del progetto di verniciatura. Al fine di concretizzare la prestazione del trattamento di verniciatura e raggiungere la durabilità attesa definita in fase progettuale, è necessario ottenere e mantenere gli spessori secchi dei rivestimenti (Dry-Film Thickness, DFT) come stabilito inizialmente. Questo assicura che il rivestimento funzioni da barriera protettiva, impedendo agli agenti corrosivi come acqua, sali e ossigeno di raggiungere la superficie del metallo. Un DFT insufficiente può lasciare zone vulnerabili, esponendo il metallo alla corrosione, mentre un DFT adeguato aumenterà la resistenza del rivestimento alle sollecitazioni meccaniche e chimiche, prolungando la vita utile della protezione e riducendo la necessità di manutenzione e riparazioni frequenti. Un buon progetto di verniciatura deve utilizzare la terminologia adeguata a definire i DFT desiderati, considerando anche che, nell’ambito dei trattamenti di verniciatura, le grandezze nominali espresse si traducono in misure effettive condizionate da ampie tolleranze, assolutamente necessarie e imprescindibili.
Terminologia e definizioni: discriminanti economiche
Esistono normative internazionali per determinare gli spessori secchi o umidi di un rivestimento. In questo articolo ci concentreremo sugli spessori secchi, quale parametro oggettivo per la valutazione qualitativa finale del ciclo applicato. L'opera di verniciatura può essere suddivisa in due macro-fasi principali: la fase progettuale e la fase esecutiva. Nella fase progettuale, il progettista stabilisce lo spessore nominale del trattamento
di verniciatura (Nominal Dry-Film Thickness, NDFT), definisce il piano di campionamento e le tolleranze di misura (per esempio, +/- 20%).
Durante la fase esecutiva, l’applicatore si occupa di applicare il rivestimento, cercando di rispettare e mantenere gli standard prefissati. In questa fase, l'applicatore misura inizialmente lo spessore umido applicato (Wet-Film Thickness, WFT) e, dopo la polimerizzazione, verifica lo spessore secco finale raggiunto (Dry-Film Thickness, DFT).
È importante evidenziare che la terminologia e gli acronimi utilizzati per definire le grandezze desiderate non sono universali, ma dipendono strettamente dalle normative tecniche adottate dal progettista. Per esempio, nelle normative ISO 2808 e ISO 19840, l’acronimo DFT può riferirsi a due misurazioni diverse, una delle quali esclude la rugosità superficiale derivante dalla granigliatura. Queste differenze sono di fondamentale importanza nel calcolo della resa di un trattamento di verniciatura.
Calcolo della resa: aspetti pratici
A fronte delle indicazioni ricevute riguardo all’NDFT, l'applicatore dovrà necessariamente calcolare la resa dei prodotti vernicianti che compongono il trattamento di verniciatura, tenendo in considerazione almeno i seguenti aspetti:
La resa teorica di un prodotto verniciante, basata sul suo residuo secco in volume (RSV), deve essere attentamente valutata (fig. 1). Inoltre, è necessario considerare l'eventuale diluizione necessaria per l’applicazione del prodotto, la quale aumenta il contenuto di sostanze organiche volatili e riduce il valore del RSV, con un conseguente impatto diretto sullo spessore del film secco finale.
Il fattore di correzione per le superfici granigliate, il quale tiene conto del fatto che una parte del prodotto verniciante si deposita all'interno delle irregolarità della superficie, creando un cosiddetto "volume morto" (fig. 2). Questo volume, pur essendo riempito dal prodotto, non contribuisce alla protezione effettiva del substrato, poiché non aumenta lo spessore del film secco che copre le aree esposte. Pertanto, è fondamentale considerare questo fattore di correzione durante il calcolo della resa del prodotto, poiché esso incide direttamente sull'efficacia della protezione fornita dal trattamento di verniciatura. Ignorare il volume morto potrebbe portare a una sottostima della quantità di vernice necessaria per ottenere la protezione desiderata.
Il fattore di sovraconsumo necessario (SCN) rappresenta la quantità di prodotto verniciante che, pur non disperdendosi nell’ambiente, si deposita sulla superficie per garantire il rispetto dei valori di NDFT richiesti (fig. 3). Questo sovraconsumo non è dovuto all’imperizia degli applicatori, ma è una discontinuità inevitabile nel processo di verniciatura. Qualsiasi metodo di applicazione impiegato genera inevitabilmente variazioni nello spessore del film organico sulla superficie. Pertanto, per assicurare il rispetto del valore minimo di DFT previsto dal piano di campionamento, è necessario applicare un volume maggiore di prodotto verniciante.
Il fattore di perdita dovuto alla geometria dell’oggetto influisce principalmente sulle applicazioni a spruzzo, ma va considerato che, in misura minore, può incidere anche sulle applicazioni a pennello o a rullo, a seconda della complessità della geometria dell’oggetto da rivestire.
Il fattore di perdita dovuto all’overspray incide sulle applicazioni a spruzzo e può essere influenzato da vari elementi, come la distanza dalla superficie, la complessità della geometria del pezzo, la presenza di correnti d’aria, il tipo di atomizzazione utilizzato e la pressione di erogazione impostata dall’operatore.
Impatti economici e stime preventive
Ogni stima preventiva non può essere esatta e sarà eventualmente confermata o smentita al termine dei lavori. Tuttavia, poiché nella fase di preventivazione è necessario calcolare l’impatto economico derivante dal consumo di prodotti vernicianti, è utile ricorrere a formule computazionali che impiegano coefficienti di correzione teorici. La costanza dell’applicatore nell’uso di tali formule e la verifica finale dei coefficienti teorici inizialmente applicati permetteranno all’impresa di contenere i margini di errore, consolidando così la propria posizione nel mercato con una competitività qualitativo-economica di alto livello.
Calcolo della resa teorica
Il calcolo della resa teorica dei prodotti vernicianti, espressa in metri quadrati (m2) per litro (l) applicato viene generalmente determinato utilizzando la seguente formula:
Mentre la resa espressa in litri per metro quadrato applicato viene determinata utilizzando la seguente formula:
Dove:
RT = Resa Teorica
RSV = Residuo Secco in Volume, percentuale di prodotto che rimane sulla superficie dopo l’evaporazione del solvente
DFT = Dry Film Thickness, spessore richiesto espresso in micron.
La formula assume condizioni ideali e non tiene conto di fattori come sovraconsumo, volume morto, o perdite dovute a overspray che possono ridurre la resa effettiva
Coefficiente di correzione per volume morto o “dead volume” Il coefficiente di correzione per il volume morto, noto anche come "dead volume”, raffigurato in fig. 2 è essenziale per compensare la perdita di prodotto verniciante che si deposita nelle irregolarità della superficie e non contribuisce alla protezione effettiva. Questo coefficiente aiuta a stimare la quantità effettiva di vernice necessaria per ottenere il risultato desiderato.
For decades, Radial has been designing, building and installing tailor-made coating plants for metals, plastics and wood. Our systems are the ideal choice for those who desire a cutting-edge turnkey solution.
La normativa ISO 19840, in accordo con le indicazioni della ISO 8503-1, fornisce una guida su come applicare questo coefficiente. La tabella 1, messa a disposizione da tali normative, semplifica l'applicazione pratica di questo coefficiente, consentendo di adattare il calcolo della resa del prodotto tenendo conto delle discontinuità superficiali e delle perdite associate.
Profilo superficiale conforme a ISO 8503-1
di correzione µm
questo articolo, si forniscono indicazioni specifiche in base alla geometria della struttura da trattare, lasciando al lettore il compito di adattare il coefficiente in base alle proprie esperienze pregresse e future. Questo fattore riflette l’effettivo deposito di prodotto verniciante sulla superficie trattata e, sebbene sia correlato alla geometria, non implica direttamente la "perdita" di materiale, che sarà trattata separatamente secondo il criterio geometrico delle strutture. Per distinguere i due coefficienti, si utilizza l'acronimo SCN seguito dal tipo di geometria.
SCN per geometria lineare:
Per geometria lineare si intendono lamiere, profili e strutture tubolari di grandi dimensioni e a superficie piana, in cui l’applicazione della vernice a spruzzo non comporta frequenti cambi di direzione. Questo tipo di applicazione consente all’operatore di mantenere una posizione costante di erogazione su almeno il 90% della superficie da trattare. La tecnica stripe coat non è obbligatoria e, se utilizzata, deve essere limitata al massimo al 5% della superficie totale.
Pertanto, in caso di superficie granigliata, una volta stabilito il tipo di rugosità indicato, l’NDFT del primo strato andrà maggiorato del valore di correzione.
Coefficiente di correzione per SCN
Poiché questo articolo introduce un nuovo fattore volto a bilanciare gli interessi di tutte le parti coinvolte nelle opere di verniciatura, le seguenti considerazioni saranno basate su dati empirici raccolti sperimentalmente durante le attività ispettive (fig. 3). È importante notare che questo fattore è influenzato da molteplici condizioni, come il tipo di applicazione, la complessità della geometria dell'oggetto, la metodologia utilizzata e le tolleranze indicate nel piano di campionamento del DFT finale. In
SCN per geometria complessa:
Per geometria complessa si intendono lamiere, profili e tubolari assemblati per formare strutture complesse. In tali casi, l’applicazione a spruzzo della vernice richiede numerosi cambi di direzione, impedendo all’applicatore di mantenere una posizione di erogazione costante su oltre il 50% della superficie da trattare. La stripe coat (applicazione a strisce) è necessaria, ma deve coprire al massimo il 15% delle superfici.
SCN per geometria intricata:
Per geometria intricata si intendono lamiere, profili e tubolari assemblati per formare strutture intricate. In tali casi, l'applicazione a spruzzo della vernice richiede numerosi e frequenti cambi di direzione, impedendo
all'applicatore di mantenere una posizione di erogazione costante sulla superficie da trattare. Di conseguenza, è necessaria l'applicazione della stripe coat, che deve coprire oltre il 15% delle superfici. Nella tabella 2 si forniscono anche valori relativi alle applicazioni a rullo e pennello.
Tipo di superficie
Coefficiente di correzione per perdita effettiva di prodotto verniciante
La perdita effettiva di prodotto verniciante deve essere correlata all’efficienza di trasferimento (ET), che rappresenta la quantità di vernice applicata che effettivamente raggiunge la superficie da rivestire (figg. 4 e 5). Due fattori principali influenzano questa efficienza: la geometria dell'oggetto e il tipo di metodo applicativo utilizzato. Sulla base delle definizioni precedenti riguardanti la geometria, si utilizza il termine "perdita" al posto dell'acronimo SNC per differenziare i coefficienti di correzione relativi (tabella 3).
with a complete service that includes system design manufacturing, installation, technical support and chemicals
Perdita per geometria lineare: Ci si riferisce a lamiere, profili e strutture tubolari ampie e piane, dove l'applicazione a spruzzo di un prodotto verniciante non richiede frequenti cambi di direzione, consentendo all'operatore di mantenere una posizione di erogazione costante su almeno il 90% della superficie da trattare. In queste condizioni, quasi tutto il quantitativo di prodotto verniciante applicato si deposita sulla superficie. Tuttavia, fattori come il tipo di atomizzazione scelto, la distanza dalla superficie, la geometria del pezzo, la presenza di correnti d'aria e la pressione di erogazione impostata dall'operatore possono influenzare il risultato finale.
SPRAY BOOTHS WATER SLUDGE REMOVAL
RESIN DEMINERALIZATION SYSTEMS
REMEDIATION OF CONTAMINATED SITES
BIOLOGICAL SYSTEMS
BATCH TREATMENTS
PHYSICAL-CHEMICAL SYSTEMS
ADSORPTION FILTRATION
REVERSE OSMOSIS
MEMBRANE SYSTEMS
EVAPORATORS
BIOGAS BIOMASS SYSTEMS
OIL SEPARATORS
DESANDERS
DESALINATION SYSTEMS
PYROCHAR
OTHER SYSTEMS
CHEMICALS
Perdita per geometria complessa:
Si fa riferimento a lamiere, profili e tubolari assemblati in strutture complesse, dove l'applicazione a spruzzo di un prodotto verniciante richiede frequenti cambi di direzione, impedendo all'operatore di mantenere una posizione di erogazione costante per almeno il 50% della superficie da trattare. In queste circostanze, una parte del prodotto verniciante non si deposita sulla superficie a causa della geometria del pezzo, che facilita la dispersione del materiale applicato. Fattori aggiuntivi, come il tipo di atomizzazione scelto, la presenza di correnti d'aria e la pressione di erogazione impostata dall'operatore, possono aggravare ulteriormente questa dispersione.
Perdita per geometria intricata: Si tratta di lamiere, profili e tubolari assemblati in strutture molto complesse, dove l'applicazione a spruzzo di un prodotto verniciante richiede all’applicatore continui cambi di direzione, impedendo all'operatore di mantenere una distanza costante dalla superficie da trattare. In queste situazioni, una parte significativa del prodotto verniciante applicato non si deposita correttamente sulla superficie a causa della complessità geometrica del pezzo, che contribuisce alla dispersione di gran parte del prodotto. Fattori aggiuntivi come il tipo di atomizzazione utilizzato, la presenza di correnti d'aria e la pressione di erogazione impostata dall'operatore possono ulteriormente accentuare questa dispersione.
Schema di calcolo suggerito
Per calcoli computazionali relativi a un progetto di verniciatura a spruzzo su geometrie lineari, utilizzando un profilo di sabbiatura "coarse" per
Schema adeguamento NDFT di progetto Valori in µm
NDFT da progetto 200
Fattore di correzione per Dead Volume (solo per primer) + 40
Fattore di correzione SCN (geometria lineare =15%) + 30
Fattore di perdita effettiva (geometria lineare =10%) + 20
Totale NDFT ricorretto dai coefficienti = 290
Analisi resa teorica e pratica
teorica
Incremento sul consumo teorico + 44.8%
raggiungere un NDFT di 200 micron, con un prodotto verniciante (PV) avente l'80% di RSV, si propone il seguente schema di calcolo nei due esempi in questa pagina.
Conclusioni
Per garantire la durabilità di un'opera di verniciatura, è essenziale condurre un'accurata analisi economica preliminare. Le variabili del progetto e i relativi coefficienti di correzione devono essere discussi e concordati in specifici incontri tra il committente e l'esecutore. Fattori correttivi come il sovraconsumo necessario, se non adeguatamente considerati, possono avere conseguenze economiche rilevanti. Questi costi non possono essere trascurati nella fase progettuale, né interamente attribuiti agli applicatori, presupponendo abilità esecutive irrealistiche. Per rispettare gli standard di prestazione del trattamento, tutte le parti contrattuali devono considerare e condividere in modo concreto i fattori di correzione menzionati.
L’autore
Il Dott. Gianmaria Guidi vanta un’esperienza trentennale nel settore della verniciatura industriale ed anticorrosiva. Negli anni, si è specializzato nella gestione dei contenziosi tecnico legali ed è regolarmente iscritto all’Albo dei Consulenti Tecnici d’Ufficio (C.T.U.) del Ministero della Giustizia, valorizzando ulteriormente le precedenti qualifiche NACE e FROSIO.
Tutto quanto esposto e riportato, a beneficio del settore.
ESEMPIO 2
Schema adeguamento NDFT di progetto Valori in µm
NDFT da progetto 200
Fattore di correzione per Dead Volume (solo per primer) + 40
Fattore di correzione SCN (geometria intricata =40%) + 80
Fattore di perdita effettiva (geometria intricata =50%) + 100
Totale NDFT ricorretto dai coefficienti = 420
Analisi resa teorica e pratica
Resa teorica in m2/l 4.0 m2/l
Let‘s talk about powder coating. A technology that is proven since decades and actually, it‘s just getting started with FLOWSENSE. FLOWSENSE? It‘s a software masterpiece and a bunch of small sensors that do big things: Consistent powder output from the first to the last workpiece. Reliability, measured in real time. Put quality on repeat!
Le nuove filiali ALIT-Service in Serbia e Portogallo avvicineranno i servizi di sverniciatura di alta qualità ai clienti.
L’azienda di sverniciatura chimica ALIT Technologies ha recentemente annunciato con orgoglio l’apertura delle sue prime due filiali internazionali in Portogallo e Serbia, con il marchio ALIT-Service. L’espansione testimonia l’inizio di un nuovo capitolo per l’azienda italiana, che mira a estendere i propri servizi di sverniciatura conto terzi anche in nuovi mercati globali.
“ALIT-Service rappresenta un’iniziativa innovativa e strategica, destinata a trasformare il panorama della sverniciatura industriale. Ciò che rende unico il nostro servizio è il suo approccio audace e personalizzato, utilizzando esclusivamente prodotti di alta qualità per soddisfare le diverse esigenze dei clienti in tutto il mondo”, ha affermato Loris Rossi, amministratore di ALIT Technologies.
Con l’introduzione di ALIT-Service, l’azienda amplia ulteriormente la sua già vasta gamma di offerte, al fine di avvicinare i suoi servizi di alta qualità ai propri clienti. Le nuove aperture intendono infatti colmare le lacune geografiche e soddisfare la crescente domanda di servizi di
sverniciatura in regioni non ancora coperte dai distributori. Tuttavia, le nuove filiali in Portogallo e Serbia sono solo l’inizio di un ambizioso progetto di espansione: ALIT Technologies prevede di aprire molte altre sedi strategiche in tutto il mondo. Secondo l’azienda, la sua espansione non è solo un segno di ambizione, ma anche un impegno concreto a sostenere la crescita economica e lo sviluppo sostenibile nelle comunità locali, creando nuovi posti di lavoro e fornendo servizi sempre più richiesti.
“Con questa iniziativa rivoluzionaria, ALIT Technologies abbraccia il cambiamento, ridefinisce gli standard del settore e apre le porte a un nuovo ed entusiasmante capitolo di successo globale, dimostrando la nostra visione di un futuro in cui innovazione ed eccellenza sono pilastri fondamentali”, ha concluso Rossi.
Per maggiori informazioni: www.alit-tech.com
L’acquisizione di Monarch Chemicals rafforzerà la posizione di Brenntag sul mercato mondiale.
Brenntag ha recentemente acquisito Monarch Group Holdings, uno dei principali distributori del Regno Unito di prodotti chimici per svariate industrie, tra cui vernici e rivestimenti.
“Il team di Monarch ha costruito un’ottima offerta di prodotti e servizi per la sua ampia base di clienti e partner di fornitura, e non vediamo l’ora di crescere ed espandere questa offerta insieme. Con questa operazione Brenntag acquisisce competenze, infrastrutture e capacità di miscelazione di liquidi e polveri. Con la nostra strategia di acquisizione, espandiamo le nostre operazioni di servizio dell’ultimo miglio per offrire ai clienti un portafoglio più ampio di prodotti e servizi a valore aggiunto, con il supporto dei nostri servizi di supply chain regionali all’interno della nostra rete globale. Grazie a questa offerta ampliata, tutti i nostri clienti nel Regno Unito potranno trarre vantaggio in futuro”, ha commentato Russel Argo, Regional President Brenntag Essentials EMEA. “Siamo molto orgogliosi del livello di servizio e di assistenza che possiamo offrire ai nostri partner di fornitura e ai nostri clienti. La nostra indipendenza ci ha reso flessibili, ma l’ingresso in Brenntag, un distributore veramente globale, ci darà l'ampiezza e la rete necessarie a far crescere la nostra attività e servire meglio i nostri clienti con una gamma più ampia di prodotti e servizi”, ha commentato Jon Hill, amministratore delegato di Monarch.
Per maggiori informazioni: www.brenntag.com
Eurotherm solves every problem concerning painting processes, creating complete lines for the entire process.
Our structure is organized and flexible and able to satisfy the most demanding requests.
Customers who turn to Eurotherm are customers who, despite knowing the “painting process”, want to improve production by adopting highly customized technical solutions.
95 Employees 205 Plants realized in 2023
1: 4.700 m² of offices, metal work production and painting.
2: 5.300 m² for production, preassembling, warehouse and logistics.
Eurotherm S.p.A.
T +39 011 98 23 500 | M info@eurotherm.eu
Eurotherm France S.A.S.
T +33 6 76 72 48 65 | M france@eurotherm.eu
Eurotherm Oberflächentechnik GmbH
T +49 7571 92795 10 | M germany@eurotherm.eu
Eurotherm Benelux Srl
T +33 6 47 44 96 27 | M dekergorlay@eurotherm.eu
Il prossimo impianto di verniciatura di Dürr consentirà ad Airbus di verniciare il serbatoio centrale posteriore dell’aereo A321XLR con una maggiore efficienza energetica e minori emissioni di carbonio.
La società di ingegneria tedesca Dürr ha intrapreso il suo progetto singolo più significativo fino ad oggi per la divisione del Gruppo Airbus, Premium AEROTEC. Il progetto prevede la costruzione di un impianto di verniciatura all’avanguardia ad Augsburg (Germania) per il rivestimento del nuovo serbatoio centrale posteriore dell’Airbus A321XLR, fondamentale per la capacità di lungo raggio dell’aereo, che ne estende la portata di 8.700 chilometri.
L’impianto di verniciatura sarà un sistema chiavi in mano, che incorporerà tecnologie all’avanguardia per migliorare l’efficienza energetica e ridurre le emissioni. In particolare, sarà dotato di un sistema di depurazione dei gas di scarico completamente elettrico, una novità assoluta per le strutture di Premium AEROTEC. Questo sistema, basato sull’ossidazione termica rigenerativa, promette di ridurre significativamente le emissioni di CO2
Protezione avanzata delle superfici ed efficienza energetica Il progetto coprirà l’intero processo di verniciatura, dal pretrattamento alla sigillatura e alla verniciatura. Il nuovo impianto di verniciatura comprenderà cabine per la sigillatura, la pulizia e la verniciatura, nonché aree per il controllo delle superfici e delle perdite. Gli elevati standard di resistenza alla corrosione e di diffusione garantiranno che le superfici dei serbatoi resistano a condizioni estreme senza corrodersi.
Il serbatoio del carburante integrato nella fusoliera dell'Airbus A321XLR è il componente chiave per trasformare i precedenti aeromobili a corto e medio raggio nella nuova versione a lungo raggio.
Inoltre, per raggiungere questi standard elevati mantenendo l’efficienza energetica, Dürr sta implementando un sistema di canalizzazione dell’aria specifico per ogni componente per ridurre la quantità d’aria necessaria per il condizionamento, riducendo così il consumo energetico. I sistemi di recupero dell’energia ricicleranno inoltre fino al 65% dell’energia proveniente dall’aria di scarico, aumentando ulteriormente l’efficienza. Rimozione sostenibile degli inquinanti
L’impegno di Premium AEROTEC per la sostenibilità è sottolineato dall’adozione del sistema di purificazione dei gas di scarico completamente elettrico Oxi.X RV di Dürr, che funziona senza fiamma libera, con emissioni di ossidi di azoto molto ridotte. Inoltre, è progettato per funzionare con elettricità green, eliminando ulteriori emissioni di CO2 Il sistema Oxi.X RV di Dürr comprende anche un’unità Sorpt.X CD che concentra i flussi d’aria di scarico per migliorare l’efficienza economica, riducendo il volume e aumentando la concentrazione di solvente. Ciò consente all’unità Oxi.X RV a valle di essere più piccola e di funzionare senza energia di riscaldamento aggiuntiva, ottimizzando il rapporto costibenefici.
Per maggiori informazioni: www.durr.com
L'aria di scarico viene depurata ricorrendo ad un Oxi.X RV senza fiamma secondo il principio dell'ossidazione termica rigenerativa (RTO).
I prodotti all’acqua Lechler Tech conformi ai CAM offrono elevate prestazioni, riducono l’impatto ambientale grazie a basse emissioni di VOC e garantiscono finiture di qualità nel rispetto delle normative europee.
Lechler Tech propone soluzioni che soddisfano le esigenze dei clienti senza compromettere la salute del pianeta. Scegliere prodotti all’acqua conformi ai CAM è un passo importante verso un futuro più consapevole. Di seguito, alcune caratteristiche e benefici dei prodotti all’acqua Lechler Tech conformi ai CAM:
Riduzione delle emissioni di COV: i prodotti all’acqua hanno una minore emissione di Composti Organici Volatili (COV), contribuendo a migliorare la qualità dell’aria e riducendo l’impatto sull’ambiente.
Sicurezza: i prodotti all’acqua sono generalmente meno tossici e più sicuri da manipolare rispetto a quelli a base di solventi, proteggendo la salute degli operatori e degli utilizzatori finali.
Prestazioni elevate: oltre a garantire un ridotto impatto ambientale, i prodotti Lechler Tech mantengono elevate prestazioni in termini di durata, resistenza e qualità della finitura.
Conformità normativa: essere conformi ai CAM significa rispettare le normative europee vigenti in materia di costruzioni (Green Public
Procurement), facilitando l’accesso a bandi e gare d’appalto.
Rispondenza ai protocolli internazionali Bream/LEED/Well: attraverso la conformità CAM è possibile avere accesso agli accrediti per LEED/Bream/ Well.
I prodotti water-based hanno superato il test 16516 di basse emissioni COV richiesto da IAC GOLD, in accordo con la ISO 16000/EN e sono stati approvati CAM: la conformità ai CAM permette di offrire prodotti totalmente esenti da METALLI PESANTI, a basso o assente VOC EMISSION e con VOC CONTENT controllato.
I prodotti Lechler Tech all’acqua consentono di ottenere finiture di alta qualità su una vasta gamma di supporti metallici e plastici. Questi prodotti offrono una versatilità notevole, permettendo di creare finiture lucide, opache, con colori pastello e anche effetti metallizzati/micalizzati e texture.
Per maggiori informazioni: www.lechler.eu
Il rivestimento Redox One Coat di AkzoNobel è una vernice in polvere che proteggere le superfici metalliche dalla corrosione e dai raggi ultravioletti.
Il produttore ceco di sistemi di scaffalatura
Trestles ha recentemente annunciato di essersi rivolto ad AkzoNobel per ottenere una finitura duratura e di qualità. Il produttore internazionale di vernici e rivestimenti ha infatti fornito Redox One Coat, un prodotto verniciante in polvere sviluppato specificamente per proteggere le superfici metalliche dalla corrosione e dai danni provocati dai raggi ultravioletti, ottimizzando al contempo i tempi di produzione e riducendo i costi.
“Ci sono molte aziende con cui siamo in competizione, in particolare nel settore dei cancelli e delle recinzioni, e la maggior parte di loro ha maturato più esperienza di noi. Per distinguerci dalla concorrenza, dobbiamo quindi avere la migliore qualità. Abbiamo
scelto Redox One Coat perché è una soluzione flessibile, che può essere applicata sia sull’acciaio inossidabile che sull’acciaio zincato.
Adesso siamo dunque in grado di fornire la qualità che i nostri clienti cercano, al prezzo che sono disposti a pagare”, ha dichiarato Daniel Molnár, il responsabile acquisti di Trestles.
Interpon Redox One Coat consente a Trestles di raggiungere una protezione dalla corrosione certificata fino alla classe C4M e un’elevata resistenza ai raggi ultravioletti con un’unica mano e un pretrattamento chimico di base, mentre i rivestimenti in polvere tradizionali richiedono solitamente uno strato di primer per la protezione dalla corrosione seguito dalla finitura per fornire brillantezza e protezione UV.
“Nei test di nebbia salina, Interpon Redox
One Coat ha ottenuto i risultati migliori nel proteggere i nostri prodotti dalla corrosione. La abbiamo testata anche su diverse superfici in acciaio, così come su alcuni prodotti Beta che abbiamo attualmente in prova, con risultati eccellenti. Volevamo essere certi che il prodotto funzionasse, anche in condizioni di pioggia o neve. Da quando utilizziamo Redox One Coat, non abbiamo ricevuto reclami” ha continuato Molnár. “Inoltre, stiamo cercando di aumentare la nostra produzione e Interpon Redox OneCoat ci aiuterà. Un’applicazione monostrato avrà un impatto positivo sulla riduzione dei tempi e dei costi, aiutandoci a rimanere competitivi. AkzoNobel non solo ha i prodotti e i colori di cui abbiamo bisogno, ma il suo personale è anche molto cordiale e flessibile: il supporto tecnico che fornisce è sicuramente uno dei motivi per cui continuiamo a essere uno dei produttori più importanti dell’intera Unione Europea”.
Per maggiori informazioni: www.interpon.com/us/en
BYK-Gardner ha nominato il suo nuovo presidente e amministratore delegato, il dott. Jörg Krames.
BYK-Gardner – parte del Gruppo ALTANA – ha accolto il suo nuovo amministratore delegato: Jörg Krames. In qualità di ingegnere meccanico con un dottorato in ingegneria chimica, Krames assume la direzione globale del produttore internazionale di strumenti per la misurazione con sede a Geretsried (Alta Baviera - Germania), dei suoi rappresentanti esteri e di circa 350 dipendenti.
Gli strumenti di prova e misurazione dell’azienda valutano oggettivamente la qualità del colore, la brillantezza e l’aspetto, nonché le proprietà fisiche di prodotti vernicianti e in plastica. L’anno scorso, BYK-Gardner ha acquisito strumenti per la misurazione non distruttiva e ad alta precisione dello spessore del rivestimento.
Krames ha trascorso in precedenza quindici anni presso ECKART, anch’essa parte del Gruppo ALTANA, come Vice President Global Key Account e responsabile della divisione Management Coatings. In precedenza, ha lavorato per BASF Coatings come Director Key Account in Giappone e Germania per case automobilistiche come Toyota e Volkswagen.
I suoi obiettivi principali sono promuovere la percezione di BYK-Gardner come fornitore di strumenti di misurazione premium e la digitalizzazione dei processi aziendali. Inoltre, in ottica di ricambio generazionale, anche i progetti di trasformazione e lo sviluppo continuo dei dipendenti sono tra i punti focali della sua strategia aziendale.
“Siamo lieti di aver trovato in Jörg Krames un amministratore delegato al nostro interno che non solo vanta un’eccellente competenza professionale, ma che conosce anche molto bene il Gruppo ALTANA”, ha affermato Jörg Hinnerwisch, membro della direzione di BYK e del consiglio di amministrazione di ALTANA. “Con la sua spiccata attenzione ai clienti, alla tecnologia e all’innovazione, Krames continua a guidare BYK-Gardner sulla strada del successo”.
Per maggiori informazioni: www.byk-instruments.com
La nuova gamma di rivestimenti protettivi di HMG combina le prestazioni dei rivestimenti a base di solventi con i vantaggi ambientali dei prodotti a base d’acqua, permettendo agli utenti di ridurre le emissioni di VOC senza compromettere le prestazioni.
HMG Paints ha recentemente lanciato Hydrosol, una nuova gamma di rivestimenti ibridi progettati per il mercato della fabbricazione dei metalli.
Il primo prodotto di questa gamma è Hydrosol QD Primer, un primer alchidico ad essiccazione rapida, progettato per la massima versatilità ed efficienza. Infatti, migliora l’adesione e la resistenza all’umidità, offrendo una buona protezione contro la corrosione grazie all’incorporazione di Fosfato di Zinco modificato. Questo primer è ideale per strutture, telai e manufatti in acciaio ed è applicabile a rullo o con spruzzatura airless o convenzionale.
Inoltre, i primi utilizzatori che stanno adottando Hydrosol QD Primer stanno riscontrando numerosi vantaggi, tra cui una maggiore copertura rispetto ai prodotti concorrenti e una maggiore efficienza nell’applicazione. Questo è dovuto al contenuto di solidi in volume di Hydrosol QD Primer, che si attesta al 55% rispetto al circa 40% dei prodotti concorrenti. “Il nostro nuovo Hydrosol QD Primer rappresenta un avanzamento significativo nelle vernici protettive e testimonia il lavoro svolto dal nostro team di Ricerca e Sviluppo per portare innovazioni sul mercato. Questo prodotto non solo soddisfa gli elevati standard di prestazione che i nostri clienti si aspettano da noi, ma si allinea anche con il nostro impegno verso la sostenibilità ambientale. È il primo pezzo del puzzle della nostra gamma Hydrosol, con una varietà di prodotti entusiasmanti che si aggiungeranno presto a questa gamma,” ha dichiarato Paddy Dyson, Marketing Manager di HMG Paints.
Il secondo prodotto a essere lanciato sarà Hydrosol Compliant DTM, un Direct-to-Metal che può essere applicato direttamente su superfici metalliche nude o già primerizzate. Questa tecnologia è conforme al PG6/23 11 ed è ideale come finitura primer a mano unica per contenitori, cassoni, contenitori, attrezzature agricole e macchinari da costruzione. Ha emissioni di COV inferiori rispetto ai prodotti equivalenti a base solvente ed è disponibile in un’ampia gamma di colori, inclusi RAL e BS.
Per maggiori informazioni: www.hmgpaint.com
Il nuovo dispenser automatico X-SMART PRO di Fast & Fluid Management combina ripetibilità e durabilità.
Fast & Fluid Management ha recentemente presentato il nuovo dispenser automatico X-SMART PRO, specificamente progettato per offrire una ripetibilità senza pari e una struttura robusta, adatta anche agli ambienti più difficili. Sfruttando un'avanzata tecnologia di pompa a pistoni, assicura l'erogazione precisa del colore, fondamentale per ottenere i risultati costanti richiesti in vari settori.
Il dispenser automatico di vernice migliora la precedente serie X-SMART con un involucro in metallo resistente e una nuova spazzola, che garantisce operazioni di pulizia ottimali. Inoltre, introduce ulteriori caratteristiche, tra cui un sensore della porta anteriore che garantisce la sicurezza degli operatori senza compromettere la funzionalità.
“Nel rapido mercato della tintometria industriale, precisione e durabilità non sono solo semplici requisiti, ma la base su cui le aziende possono costruire la propria reputazione. Per questo motivo, riconoscendo le sfide che devono affrontare i nostri clienti in tutto il mondo, il dispenser automatico X-SMART PRO è stato progettato per offrire velocità e robustezza, fondamentali per mantenere un funzionamento continuo e affidabile. Grazie alla sua struttura in acciaio, è capace di supportare un uso intenso, rendendolo una soluzione ideale per le aziende che vogliono ridurre i tempi di inattività e migliorare l'efficienza operativa”, ha dichiarato l'azienda.
Per maggiori informazioni: https://emea.fast-fluid.com
Da Torino a Cassino: lo sgrassante CONDORINE SG 576 N sviluppato da Condoroil Chemical, già introdotto nella linea di lavaggio dei paraurti dello stabilimento Stellantis di Torino Mirafiori, è oggi stato implementato anche nella linea produttiva di Cassino, con un notevole risparmio dal punto di vista energetico e del consumo idrico.
Risparmio energetico, ecologia e basso impatto ambientale, sono, da sempre, prerogative del Gruppo Stellantis. Partendo da questi presupposti, circa un anno fa, Condoroil Chemical ha iniziato i test dello sgrassante CONDORINE SG 576 N da integrare nel processo di lavaggio finale della componentistica in plastica.
Caratteristiche del prodotto
CONDORINE SG 576 N è un detergente a bassa quantità di schiuma monocomponente, attivo anche a temperatura ambiente; il suo utilizzo permette quindi notevoli risparmi energetici e minore consumo d’acqua rispetto ai prodotti tradizionali. La quasi totale assenza
di schiuma e le innovative peculiarità della formulazione permettono inoltre di ridurre l’effetto dei trascinamenti, minimizzando quindi il progressivo inquinamento dei risciacqui post lavaggio.
Un progetto di successo
Il progetto è nato in collaborazione con il team Painting Process Engineering PPE Materials Approval Torino-Mirafiori, dove il prodotto è utilizzato nel processo di lavaggio della linea di produzione dei paraurti, confermando l’esito positivo dei test preliminari effettuati: sono stati soddisfatti, fin da subito, tutti i requisiti qualitativi richiesti da Stellantis per l’omologazione del prodotto, e i notevoli
risparmi ipotizzati in fase di progettazione. Il cliente ha potuto infatti rilevare:
la perfetta pulizia dei componenti trattati; il notevole risparmio energetico dovuto all’applicazione a temperatura ambiente; il minor consumo di prodotto; il minor consumo d’acqua, anche per il risciacquo dei componenti. Si è osservata una riduzione dell’80% del consumo di acqua demineralizzata nella fase di risciacquo finale (da 500 L/h a 100 L/h).
Da Torino a Cassino: l’implementazione di CONDORINE SG 576 N Successivamente CONDORINE SG 576 N è stato proposto all’Unit Plastic del reparto produzione e verniciatura paraurti dello stabilimento Stellantis di Cassino (Frosinone), dove era utilizzata una soluzione bicomponente che richiedeva una temperatura di lavoro di almeno 55 °C (come quasi tutti gli attuali sgrassanti per la plastica). Ora, lavorando a temperatura ambiente, hanno ottenuto notevoli risparmi senza alcun compromesso sulla qualità dei risultati. L’implementazione di questo prodotto nello stabilimento di Cassino è stata possibile grazie al team di Process Improvement, che ha svolto un ruolo fondamentale nelle prime fasi di avviamento e continua a seguire con attenzione il regolare processo produttivo.
Per maggiori informazioni: www.condoroil.com
Moreno Zuccarelli, Sales Manager
Verniciatura Industriale di Condoroil, e Achille Di Sano, responsabile produzione e verniciatura paraurti STELLANTIS Alfa Romeo Cassino.
Your
Il nuovo stabilimento di Gossau è dotato di aree di produzione più ampie, laboratori di prova avanzati e sistemi ecosostenibili, che consentono a Gema di potenziare e aumentare la capacità produttiva.
Il fornitore di apparecchiature per l’applicazione di vernici in polvere Gema si è recentemente trasferito nel nuovo stabilimento di Gossau (Svizzera). Questa mossa sottolinea l›impegno dell›azienda nel migliorare e incrementare la propria capacità produttiva.
La nuova struttura di Gossau vanta ampi spazi per uffici, sale riunioni all’avanguardia e moderne infrastrutture tecnologiche. È dotata di un magazzino automatico verticale e aree di produzione ampliate, che migliorano l’efficienza operativa.
Inoltre, la struttura include un sofisticato laboratorio di test e applicazioni per i clienti con linee di rivestimento avanzate.
La nuova sede di Gema è dotata di impianti fotovoltaici per la produzione di energia e di un sistema di pompe geotermiche per il riscaldamento, che mettono in mostra l’impegno dell’azienda verso pratiche rispettose dell’ambiente.
For further information: www.gemapowdercoating.com/en/
Leading companies rely on vacuum distillation systems for the sustainable treatment of industrial wastewater.
Do you want to benefit from a zero liquid discharge production with VACUDEST aswell?
Just contact our Experts!
KANSAI HELIOS Italia e Weilburger Coatings Italia insieme per cogliere nuovi successi.
Aseguito dell’annuncio di KANSAI HELIOS di aver completato con successo l’acquisizione di Weilburger Coatings lo scorso maggio, Weilburger Coatings Italia e KANSAI HELIOS Italy hanno iniziato a definire e sviluppare le prime sinergie. Si tratta, infatti, di una integrazione strategica che non solo espande le capacità produttive di KANSAI HELIOS in Italia, ma ne rafforza anche la posizione sul mercato in qualità di fornitore di sistemi. Grazie alla produzione locale di vernici industriali liquide e in polvere, le competenze e la gamma di servizi dell’azienda sono ora più che mai ampie e competitive. Inoltre, la posizione strategica delle unità produttive e il potenziamento delle strutture di stoccaggio situate a Bergamo, garantiscono maggiore flessibilità ed efficienza alle forniture. D’ora in poi, KANSAI HELIOS Italia e Weilburger Coatings Italia potranno offrire al mercato italiano il valore aggiunto di un approccio unificato, con una combinazione vincente di competenze e punti di forza. Negli ultimi anni KANSAI HELIOS Italia ha registrato una crescita significativa grazie a investimenti strategici e continue migliorie dei propri stabilimenti di Riese Pio X (Treviso) e Tezze sul Brenta (Vicenza) per la produzione di vernici in polvere. L’azienda ha ampliato le proprie capacità produttive, installando nuove linee di produzione e aggiornando le strutture esistenti con attrezzature all’avanguardia. Sono in fase di implementazione sistemi avanzati per eliminare l’utilizzo della carta nel processo produttivo e garantire la completa tracciabilità del prodotto, migliorando sia l’efficienza che la sostenibilità. Innovazione e sostenibilità sono i due cardini a partire dai quali KANSAI HELIOS Italy sta sviluppando nuove linee di prodotti. In particolare, le sue nuove polveri e formulazioni a bassa temperatura di polimerizzazione sono realizzate con l’utilizzo di materie prime riciclate o naturali. Parallelamente alla qualità e sostenibilità dei prodotti, fornire servizi di alto livello ai propri clienti rimane tra gli obiettivi principali dell’azienda. Il suo impegno è volto a garantire la massima disponibilità del prodotto, tempi di consegna brevi e assistenza tecnica continua. Con 22 diverse attestazioni di qualità, KANSAI HELIOS Italy è certamente il partner ideale per il settore. A sua volta, negli ultimi anni Weilburger Coatings Italia ha fatto passi da gigante, grazie a investimenti strategici e miglioramenti continui. L’azienda è specializzata in rivestimenti liquidi industriali, con un sito produttivo all’avanguardia situato a Sotto Il Monte, Bergamo. Le infrastrutture sono state rinnovate e ampliate: in particolare, l’implementazione di nuovi magazzini ha migliorato sia le capacità di stoccaggio, che quelle logistiche.
Questi sviluppi supportano l’obiettivo strategico di servire svariati settori di mercato, tra cui casalinghi, stufe e apparecchi di riscaldamento, veicoli ferroviari, l’industria dell’occhialeria, piccoli articoli e cerniere, imballaggi e contenitori in alluminio, e il settore coil e foil. L’attività di Weilburger Coatings Italia è basata su di un impegno costante all’innovazione, qualità e sostenibilità, testimoniate da certificazioni come ISO 9001-2015, ISO 14001-2015 e ISO 45001-2018.
Con l’acquisizione di Weilburger Coatings Italia, KANSAI HELIOS consegue un’espansione significativa in Italia. Inoltre, l’allineamento strategico delle
due aziende amplierà le capacità produttive e, soprattutto, rafforzerà la posizione di fornitore di sistemi dell’azienda. Ora, con due hub centrali, KANSAI HELIOS è in grado di offrire una gamma completa di rivestimenti industriali: il sito di Bergamo per i rivestimenti liquidi e i siti di Treviso e Vicenza per i rivestimenti in polvere, i rivestimenti destinati all’architettura e quelli per la verniciatura di auto.
Bine Pangršič, amministratore delegato di KANSAI HELIOS Italia, dichiara: “Vogliamo sfruttare appieno la competenza del team Weilburger Coatings per migliorare ulteriormente la soddisfazione dei nostri clienti e affidare con fiducia la nostra attività di rivestimenti industriali nelle mani dei nostri colleghi di Bergamo. Weilburger Coatings Italia diventerà, quindi, il fulcro per la produzione di rivestimenti liquidi industriali in Italia, anche per i prodotti KANSAI HELIOS, che naturalmente saranno mantenuti. Weilburger Coatings Italia assumerà solo la funzione commerciale e agirà come partner locale di servizi. Nel settore dei rivestimenti liquidi,
gli esperti di Weilburger Coatings Italia lavoreranno fianco a fianco con i rappresentanti di vendita di KANSAI HELIOS, che si trasferiranno a Bergamo. Ciò significa garantire ai nostri clienti continuità nei contatti”. Unendo le forze e concentrandosi sulle rispettive attività principali, KANSAI HELIOS Italy e Weilburger Coatings Italia sono pronte a migliorare prodotti e servizi, sfruttando le sinergie e massimizzando l’efficienza. L’integrazione del sito produttivo di Bergamo nella rete KANSAI HELIOS offre, ad esempio, maggiori volumi di stoccaggio e una migliore posizione strategica, consentendo il trasferimento delle merci dall’hub di Piacenza direttamente a Bergamo. Di conseguenza, gli uffici di Piacenza verranno chiusi.
Zoran Boras, Amministratore Delegato di Weilburger Coatings Italia, aggiunge: “Le posizioni strategiche delle nostre unità produttive e i magazzini ben sviluppati in tutti i siti forniscono una solida base per la crescita futura. Questa configurazione ci consente di offrire una maggiore flessibilità e maggiori capacità di stoccaggio a lungo termine, con l’opportunità di un’ulteriore espansione in futuro. Il trasferimento sarà completato entro marzo 2025, senza avere impatti sulle attività quotidiane e sulle consegne. Inoltre, la vicinanza dei magazzini agli impianti di produzione offre una logistica senza interruzioni e tempi di risposta più rapidi”.
L’ampliamento di capacità produttive e di stoccaggio, e le offerte di servizi migliorate, vanno a rafforzare la posizione dell’azienda come fornitore di sistemi completi, allineato ai desideri e alle esigenze dei clienti. L’Italia rimane uno dei mercati strategici per il Gruppo KANSAI HELIOS e questa acquisizione amplia ulteriormente l’offerta e rafforza la sua posizione di fornitore di sistemi. Unendo le forze con Weilburger Coatings, KANSAI HELIOS è ora più forte che mai sul mercato italiano, fornendo una solida piattaforma per l’innovazione e la crescita.
KANSAI HELIOS Italia e Weilburger Coatings Italia
Le due aziende sono uno dei principali fornitori di sistemi di rivestimento integrati, tra cui tecnologie liquide, in polvere, di cataforesi, gelcoat, nonché adesivi e sigillanti. Insieme gestiscono tre siti produttivi in Italia. Per i rivestimenti in polvere uno a Riese Pio X (Treviso), con una produzione di circa 7500 tonnellate di rivestimenti in polvere termoindurenti e uno a Tezze sul Brenta (Vicenza) con una produzione di circa 2500 tonnellate di polveri termoplastiche. La produzione di vernici liquide è localizzata a Sotto Il Monte, Bergamo, dove vengono prodotte circa 2500 tonnellate di rivestimenti. Entrambe le aziende sono membri di KANSAI HELIOS, che fa parte di KANSAI PAINT, uno dei principali produttori mondiali di pitture, vernici e rivestimenti.
Per maggiori informazioni: www.kansai-helios.it e www.weilburger.it
Da un’intervista con Matthias Haarer, Managing Director di Eisenmann GmbH – Böblingen, Germania
Alessia Venturi, direttore responsabile delle riviste ipcm®, ha intervistato Matthias Haarer, Managing Director di Eisenmann GmbH, da sempre sinonimo di soluzioni efficienti, personalizzate e di alta qualità nel settore della verniciatura industriale.
Eisenmann è un’azienda in rapida crescita. Sin dalla sua fondazione nell’ottobre 2020, il numero di dipendenti presso la sede centrale di Böblingen (Germania) è cresciuto da 100 a 190. Inoltre, ci sono 40 dipendenti nelle sue succursali di Puebla (Messico) e Carolina del Sud (Stati Uniti).
Nella sede centrale di Böblingen, l’azienda riunisce tutte le sue competenze chiave: ricerca e sviluppo, ingegneria, project management, controllo qualità, assistenza e vendita. Eisenmann gestisce anche un centro tecnico di 8.000 m² per il pre-assemblaggio, la logistica, lo stoccaggio dei ricambi e la ricerca e sviluppo. Attraverso partner commerciali (licenziatari) in Cina, India e Spagna, e filiali in Turchia, Italia, USA, Messico e Arabia Saudita, l’azienda tedesca intrattiene relazioni commerciali affidabili in questi mercati. Eisenmann GmbH prevede di raggiungere una performance operativa globale di oltre 100 milioni di euro nel 2024, contando su un ampio portfolio prodotti e su una base clienti in diversi segmenti industriali, dai settori dell’automotive (storicamente il core business dell’azienda) e dei cerchi in lega, alle macchine agricole e da costruzione, fino alla general industry per quanto riguarda la verniciatura dei metalli e delle materie plastiche con tecniche applicative a immersione, a polvere e a liquido.
Sig. Haarer, può fornire ai nostri lettori un quadro sintetico di Eisenmann GmbH?
“Eisenmann GmbH, fondata nel 2020, si concentra sullo sviluppo continuo e di successo della sua unità aziendale Paint & Assembly Systems, con oltre 1.000 brevetti che comprendono tutti i prodotti chiave, come E-Shuttle 200 & 300, Vario-Shuttle XL, Vario-Loc, Vario-Mover (AGV), E-Cube e oltre 2.000 impianti di verniciatura installati in tutto il mondo, di cui circa 90 sono attribuibili al settore dei cerchi in lega, un campo in cui Eisenmann è stata pioniere.”
Il sistema di separazione a secco modulare ed efficiente dal punto di vista energetico E-Cube.
Cosa rappresenta oggi Eisenmann?
“Il marchio Eisenmann rappresenta soluzioni personalizzate, efficienti e di alta qualità nel settore della verniciatura industriale. Offriamo, su scala globale, un portfolio ampio e collaudato di impianti di verniciatura per
l’industria del metallo, dell’auto e dei cerchi in lega, inclusa la tecnologia di trasporto per l’assemblaggio finale.
Avere oltre 2.000 impianti di verniciatura installati in tutto il mondo significa che oltre 60 milioni di carrozzerie sono state trattate nell’area
PT-ED con tecnologie brevettate Eisenmann, come i sistemi di trasporto per la verniciatura a immersione della serie E-Shuttle o il sistema a immersione rotante per carichi utili più elevati VarioShuttle XL. Grazie alla nuova strategia aziendale, possiamo supportare i nostri clienti in tutto il mondo con un’assistenza e una gestione dei ricambi affidabili (24 ore su 24, 7 giorni su 7). L’obiettivo è garantire che gli impianti mantengano il loro valore il più a lungo possibile, così che i nostri clienti possano raggiungere in modo affidabile i loro obiettivi di produzione individuali e la massima qualità. La nostra competenza comprende anche l’analisi delle misure di modernizzazione e la creazione di concept retrofit innovativi e sostenibili per gli impianti esistenti.”
Cosa significa personalizzare un impianto di verniciatura?
“Le esigenze dei clienti sono estremamente variabili, anche all’interno
dello stesso settore industriale. Ogni impianto di verniciatura si basa su una pianificazione e una progettazione individuali, è personalizzato secondo le esigenze del cliente e, di conseguenza, è unico. Variano per la complessa interazione tra le fasi di processo e i sistemi di trasporto ad esse adattati. Tutti i nostri prodotti e le nostre soluzioni si basano sull’esperienza acquisita in un’ampia gamma di progetti in diversi settori industriali in tutto il mondo, ed è su questa esperienza che continueremo a concentrarci in futuro.”
Cultura aziendale: come si può definire quella di Eisenmann?
“Trasparenza e responsabilità aziendale, apprezzamento e tolleranza, impegno e autenticità nella pratica, audacia, apertura al nuovo, consapevolezza delle risorse e sostenibilità in primo piano: questi sono i valori aziendali di Eisenmann. Oggi, più di 230 dipendenti lavorano ogni giorno per garantire il successo dei nostri clienti. Progettisti altamente specializzati combinano la loro pluriennale esperienza ingegneristica con idee fresche di giovani talenti altamente qualificati. Di conseguenza, la nostra gamma di prodotti e servizi è in continua evoluzione. Le nostre
attività sono caratterizzate da agilità e capacità di innovazione, oltre che da affidabilità e ambiziosa collaborazione all’interno del team. Inoltre, vivere i nostri valori nel nostro ambiente lavorativo contribuisce anche alla soddisfazione dei clienti e a creare un buon clima di lavoro. Lavoriamo insieme in modo costruttivo, manteniamo le promesse e rispettiamo le scadenze. Questo ha portato a un alto livello di lealtà tra i nostri dipendenti e a relazioni di fiducia con i nostri partner e fornitori. È qualcosa di cui siamo orgogliosi.”
Puoi descrivere brevemente il portfolio prodotti e servizi di Eisenmann?
“Le nostre tecnologie forniscono standard qualitativi costanti lungo tutto il processo, dal pretrattamento all’assemblaggio finale. Ciò che ci distingue è il nostro approccio orientato alla soluzione e incentrato sul cliente, sempre tarato sulle mutevoli esigenze del mercato. Il nostro obiettivo è sviluppare concept di impianti rilevanti e duraturi che possano essere integrati ottimamente all’interno di processi
esistenti e portino ai nostri clienti nuove potenzialità nella verniciatura.
Il nostro portfolio prodotti comprende:
Convogliatori aerei per il pretrattamento e la verniciatura per immersione mediante cataforesi (PT/E-Coat), ad esempio VarioShuttle XL, E-Shuttle 200 e E-Shuttle 300;
Convogliatori aerei per l’intero processo di verniciatura, come VarioMover (AGVveicolo a guida automatica), VarioLoc, sistemi monorotaia, sistemi di traporto tradizionali con skid, sistemi Power & Free per diversi carichi utili (Power & Free invertiti, trasportatori circolari e a fuso) per un utilizzo efficace e personalizzato nella general industry, nell’industria metallurgica e nel settore automotive;
Diversi sistemi di asciugatura (più compatti e a risparmio di risorse: E-SmartOven);
E-Cube, RE-Cube/sistema di separazione a secco per la raccolta e lo smaltimento dell’overspray;
Soluzioni e tecnologie applicative per la movimentazione automatizzata.
La nuova unità aziendale Robotics si aggiunge a questa vasta gamma di tecnologie.”
In che cosa consiste la nuova unità aziendale Robotics?
“Ci sono grandi aspettative sulla qualità e sulla quantità dei prodotti, così come sui processi produttivi e sugli aspetti sanitari: precisione, accuratezza di posizionamento, efficacia, velocità ed ergonomia stanno diventando sempre più importanti. Una combinazione intelligente e una cooperazione sicura tra uomo e macchina sono oggi indispensabili e comuni. Per questo motivo stiamo lavorando su concept affidabili per nuovi sistemi e, cosa molto importante, su idee per l’adeguamento o la conversione di impianti di verniciatura esistenti. Basandoci su un’architettura software standardizzata con concetti operativi uniformi, consentiamo l’utilizzo di robot e tecnologie applicative dei principali produttori.
La nostra esperienza copre tutte le tecnologie di processo e di applicazione per:
Sigillatura sottoscocca;
Sigillatura degli interni;
Isolante spray;
Protezione delle cavità;
Gestione dei materiali.”
Qual è l’obiettivo di Eisenmann nello sviluppo di nuove tecnologie?
“La sostenibilità economica ed ecologica, così come l’attenzione all’efficienza energetica, sono fattori cruciali per tutti gli sviluppi. Oltre a questo, vogliamo offrire flessibilità, facilità d’uso e facile integrazione dei diversi sistemi.
Per questo abbiamo fondato la nuova un’unità aziendale Robotics. Gli impianti di verniciatura automotive sono enormi, ricchi di tecnologie di verniciatura e ad alto consumo di energia e di risorse. Dal punto di vista energetico, la fase di verniciatura è la più intensa dell’intero processo di produzione di una scocca.
Tra le varie tecnologie che abbiamo sviluppato a questo proposito, vale la pena menzionare il nuovo sistema di separazione a secco RE-Cube, che utilizza la pirolisi per una separazione a
secco dell’overspray a costi e consumi energetici contenuti.
Il passaggio dalla separazione a umido a quella a secco dell’overspray era già stato favorito da questioni energetiche. Ora che la separazione a secco è ben collaudata e ampiamente utilizzata, abbiamo sviluppato il nuovo sistema RE-Cube partendo dall’esperienza acquisita con la seconda generazione della nostra tecnologia proprietaria E-Cube. RE-Cube sta per REcycling Cube e questo è il punto chiave, trattandosi di un cubo con un guscio di lamiera dove solo le parti filtranti all’interno del cubo sono fatte di cartone. L’idea alla base è quella di pirolizzare il cubo di cartone in un forno di pirolisi a 450 °C, utilizzando il calore generato da questo processo per altre aree dell’impianto di verniciatura, ad esempio per riscaldare i forni o le vasche di PT. Si tratta di un processo neutro dal punto di vista delle emissioni di CO2, poiché si elimina la necessità di logistica e trasporto e si bilancia la CO2 emessa durante la pirolisi con quella risparmiata per riscaldare altre fasi del
processo di verniciatura. È economia circolare al suo meglio!”.
Ha menzionato ATLAS, il concept di sostenibilità di Eisenmann per migliorare il bilancio energetico e delle risorse. Può spiegare nel dettaglio questo approccio?
“Un impianto di verniciatura consuma molte risorse, siamo consapevoli delle nostre responsabilità e cerchiamo di progettare i nostri prodotti in modo da ridurre le emissioni nocive e risparmiare risorse come l’elettricità e l’acqua.
Tutte le idee chiave e gli approcci tecnici che possono migliorare il bilancio energetico e delle risorse si basano sul concetto saldamente ancorato di sostenibilità ATLAS e osservato dai nostri dipendenti.
ATLAS è l’acronimo di Advanced Technology for Low-emission Application and Sustainability. Non vogliamo limitarci a uno slogan per la sostenibilità, vogliamo davvero vivere questo programma in termini di categorie di prodotti. Un esempio semplice
è la tecnologia di essiccazione in un impianto di verniciatura per auto. Abbiamo sviluppato forni smart altamente efficienti, capaci di adattare il processo di asciugatura al tipo di scocca in ingresso. Chiamiamo questi forni “smart” perché, in combinazione con le nostre tecnologie di trasporto intelligenti, come il VarioLoc o il Vario Mover (il nostro sistema AGV), hanno l’intelligenza di indirizzare l’aria calda in modo individuale e preciso ai rispettivi componenti della scocca grazie a un controllo ottimizzato degli ugelli orientabili. Ci sono molti altri esempi di tecnologie sviluppate da Eisenmann che rispettano l’approccio ATLAS. Nell’area PT/ ED con il brevettato Vario-Shuttle XL, un sistema di trasporto rotante per la verniciatura a immersione, è possibile verniciare anche scocche pesanti fino a 2.000 kg con flessibilità, manovrabilità ed efficienza sempre elevate. Questo soddisfa una nuova richiesta comune dei nostri clienti, che producono scocche sempre più grandi, in linea con la tendenza dei SUV e della mobilità elettrica. È curioso, ma le scocche delle auto elettriche sono talvolta più pesanti di quelle delle auto tradizionali!
In sintesi, ATLAS non è solo teoria messa su una pagina web: è un concetto, lo viviamo e i nostri prodotti lo realizzano”.
Come ultima domanda, può illustrare brevemente quali sono le prospettive dell’azienda?
“Eisenmann sta progettando una nuova struttura e nel 2026 si trasferirà
in una sede propria nella vicina città di Gärtringen. Questo passo sottolinea la crescita stabile di Eisenmann GmbH.
Un nuovo edificio ci offre la massima flessibilità in termini di costruzione moderna ed efficiente dal punto di vista energetico. Torniamo al concetto di ATLAS: l’uso attento di preziose risorse naturali non determina solo le nostre azioni nello sviluppo delle nostre tecnologie, per noi è importante realizzare con coerenza questi obiettivi anche nella progettazione di un ambiente di lavoro moderno, che soddisfi in modo ottimale le nostre esigenze e fornisca anche un quadro di presentazione adeguato per i progetti di investimento dei nostri clienti.
Stiamo costruendo una nuova sala di pre-assemblaggio di circa 7.000 m² che ospiterà la logistica, i dispositivi e le attrezzature di prova, l’area di ricerca e sviluppo e il pre-assemblaggio dei nostri prodotti proprietari. Oltre alla sala di preassemblaggio, un nuovo edificio di circa 3.500 m² ospiterà da 250 a 300 dipendenti.
Come ho detto, questo passo sottolinea in qualche modo lo sviluppo positivo della nostra nuova azienda. A volte, dobbiamo ricordare a noi stessi che non sono solo quattro anni che siamo tornati in attività, non siamo partiti da zero. Con una nuova sede uniamo l’eredità e il futuro. L’investimento per il nuovo edificio ammonterà a 20-30 milioni di euro. La nuova sede di Gärtringen offrirà anche la possibilità di espansione futura. Vorremmo continuare a svilupparci come datore di lavoro interessante nella regione e creare ulteriori posti di lavoro.”
via E De Nicola, 18 - I-20090 Cesano Boscone (MI) Italy - tel +39 0255210608 www.ravarinicastoldi.it - dive@ravarinicastoldi.it
Kevin Biller kbiller@chemquest.com
Caro Joe, cosa fa sì che una polvere fluidifichi meglio di un’altra?
Jason Smith Denver, Pennsylvania
Ciao Jason, questa è un’ottima domanda. Affinché una vernice in polvere funzioni bene, molte proprietà fisiche e chimiche devono essere allineate. Le prestazioni di fluidizzazione sono una delle caratteristiche fisiche necessarie per applicare con successo una vernice in polvere. La fluidizzazione consiste nell’incorporare un volume d’aria in una data quantità di polvere per prepararla al trasporto dalla tramoggia alla pistola di applicazione. Questa miscela di aria e particelle non solo facilita il trasporto del materiale, bensì migliora anche la distribuzione della carica elettrostatica alle singole particelle in uscita dalla pistola. La distribuzione dimensionale delle particelle (DDP) è il fattore primario che influenza la fluidizzazione. Le vernici in polvere sono composte da una gamma di particelle di dimensioni diverse – da circa 1,0 micron fino a circa 100 micron. La miglior fluidizzazione si verifica al centro del range, tipicamente 20-60 micron. Le particelle fini (<10 micron) tendo ad agglomerarsi compromettendo la fluidizzazione. Le particelle grossolane (>100 micron) sono difficili da fluidificare per via della loro massa relativamente elevata. Quindi, le vernici in polvere con la migliore fluidizzazione hanno una distribuzione dimensionale delle particelle ristretta, ovvero con un livello minimo di particelle fini e grossolane. Se si utilizza un sistema di recupero e riciclo dell’overspray, questo può influenzare la fluidizzazione. Le particelle più adatte vengono
preferibilmente depositate sul manufatto che si vernicia e di conseguenza le particelle fini e grossolane sono quelle che compongono l’overspray. Reintrodurre l’overspray nella polvere fresca influenzerà il processo di fluidizzazione. Come evitare questo problema? La miglior strategia è utilizzare vernici in polvere di alta qualità da produttori affidabili. I fornitori più affidabili utilizzano processi di macinazione ben controllati, che generano DDP relativamente ristrette. Le DDP ristrette offrono un’elevata efficienza di trasferimento al primo passaggio e quindi un overpsray minore. Un fattore secondario che influenza negativamente la fluidizzazione è l’umidità. La polvere “umida” è molto difficile da fluidificare e da trasportare all’interno del sistema di applicazione. Elevati livelli di umidità sono solitamente causati da stoccaggio e movimentazione scorretti delle scorte di polvere. Le vernici in polvere andrebbero stoccate in ambienti con aria condizionata e andrebbero evitati contenitori/sacchi aperti. Inoltre, bisogna evitare di introdurre polvere “fredda” in un ambiente più caldo e più umido. La polvere fredda agirà da essiccante e assorbirà l’umidità dell’ambiente. È consigliabile, quando si sposta la polvere dal magazzino all’area applicativa, consentirle di acclimatarsi all’ambiente applicativo prima di aprire la confezione. Grazie per la tua domanda. Cordiali saluti, Joe
Ciao Joe, stiamo pianificando di utilizzare tubi quadrati in acciaio inox 304 laminato a freddo per gli alloggiamenti dei nostri strumenti, ma questi tubi sono leggermente ossidati e vaiolati. Stiamo cercando di offrire al cliente una finitura che sembri professionale e che impedisca all’acciaio di ritornare nelle condizioni in cui lo abbiamo ricevuto. Abbiamo ipotizzato di verniciare a liquido, a polvere, lucidare o applicare un rivestimento galvanico sull’alloggiamento, ma credo che la verniciatura a polvere sia il modo più conveniente per proteggerlo. L’ambiente in cui si troverà lo strumento varierà da -40°C to +100°C e sarà occasionalmente polveroso, oleoso e vicino all’acqua di mare (non a contatto). Dato che i tubi sono in acciaio 304SST so che l’adesione è un grosso problema. Puoi consigliarmi il modo migliore per preparare la superficie di un materiale 304SST? Apprezzerei molto dei dettagli sul tipo di sgrassante, sul tipo di graniglia metallica (non ferrosa) o di prodotto chimico (tipo silano) e sul tipo di primer, in modo che l’irraggiamento UV e la corrosione da acqua di mare non danneggino l’alloggiamento per almeno 10 anni. Aspetto una tua risposta.
Christopher Filoon, Pennsylvania
Ciao Christopher, questa è un’ottima domanda ed è molto saggio esaminare tutte le opzioni che hai citato prima di impegnarsi con un nuovo processo. Le vernici in polvere costituiscono un’ottima finitura per l’acciaio inossidabile se il processo è studiato e mantenuto correttamente. Il segreto sta nella pulizia e nel pretrattamento del metallo prima dell’applicazione della polvere. Il processo che dovresti considerare inizia con la granigliatura. Una graniglia di alta qualità come l’ossido di alluminio sarà sufficiente. Dopo la granigliatura effettua una fase di sgrassaggio alcalino ben controllata per rimuovere ogni residuo di olio, fluidi di lavorazione e contaminanti derivanti dalla manipolazione. È importante anche mantenere pulita la graniglia.
Successivamente ti suggerisco una fase di passivazione per rimuovere eventuali residui ferrosi sulla superficie inossidabile, nonché eventuali residui di solfuri. Tracce di entrambi i contaminanti possono fungere da siti di innesco della corrosione. La passivazione dell’acciaio inossidabile in genere comporta l’immersione del componente in un bagno di acido nitrico, sebbene si possano utilizzare anche soluzioni di acido nitrico/bicromato di sodio o acido citrico. La concentrazione di acido può variare tra il 20 e il 50% in volume. La norma ASTM A380 descrive le pratiche standard per la passivazione dell’acciaio inossidabile.
Dopo aver accuratamente asciugato i manufatti, è importante verniciare a polvere il prima possibile la superficie passivata. Le superfici pretrattate chimicamente hanno una durata limitata prima che inizino a degradarsi. Utilizzare una vernice in polvere di alta qualità evita la necessità del primer. Per soddisfare la durabilità richiesta negli ambienti da te descritti è necessario applicare la polvere con lo spessore specificato dal fornitore della vernice; 65-80 micron sono solitamente sufficienti per un’applicazione per ambiente esterno. È anche fondamentale assicurarsi che i manufatti verniciati polimerizzino con temperatura e tempo sufficienti. Quando un produttore di polvere menziona la cottura raccomandata, il tempo si calcola dal momento in cui il manufatto ha raggiunto la temperatura
indicata. È quindi importante considerare il tempo di riscaldamento necessario per raggiungere tale temperatura.
Per quanto riguarda la garanzia di prestazioni accettabili, possono raccomandare un paio di test pratici. Ti suggerisco di preparare alcuni pezzi di prova sottoposti all’intero ciclo lavaggio/passivazione/ verniciatura/polimerizzazione e di sottoporli ai seguenti test:
1. Test di adesione cross cut: incidi nel rivestimento una “X” di 40x40 mm con una lama affilata. Applica un nastro resistente come 3M 2517 o Permacel #99 e tira con decisione. La vernice non dovrebbe mostrare alcuna perdita di adesione. Un test simile si può effettuare con un quadrettatore, come descritto dalla norma ASTM D3359. Questo strumento incide una serie di tagli perpendicolari che formano una griglia. Tuttavia anche la semplice incisione a “X” è solitamente sufficiente per determinare se l’adesione è accettabile.
2. Test di adesione con immersione in acqua calda: posiziona i campioni verniciati valutati nel test di adesione di cui sopra in acqua a 75 °C per 24 ore. Rimuovili e lasciali asciugare, dopodiché ricontrolla l’adesione con il nastro. La vernice dovrebbe mostrare poca o nessuna perdita di adesione.
3. Confermerei i risultati di questi testi con un test in nebbia salina per 500 ore (ASTM B-117). Posiziona i campioni incisi nella camera di corrosione e valutali ogni 250 ore. La maggior parte delle vernici in polvere supera il test di resistenza in nebbia salina per 1.000 ore; 500 ore è ciò che considero un punto di riferimento minimo.
Buona fortuna nell’individuazione di una tecnologia di finitura che ti possa offrire il giusto equilibrio costi/ prestazioni.
Cordiali saluti, Joe
Ilaria Paolomelo ipcm®
Pulsar, un’azienda polacca specializzata nella produzione di dispositivi di sicurezza e accessori per sistemi di allarme, ha riscontrato in passato problemi legati alla qualità finale della verniciatura dei suoi prodotti. Per risolvere queste criticità, ha deciso di passare da un sistema di applicazione manuale a uno automatico, affidandosi a Lesta. Il robot di verniciatura fornito dall’azienda italiana ha permesso a Pulsar di ottenere una finitura uniforme, migliorare la ripetibilità del processo e ridurre al minimo i ritocchi manuali – un cambiamento che ha incrementato significativamente la produttività, consentendo all’azienda di gestire una produzione giornaliera fino a 2.000 set di prodotti, con un aumento della capacità del 400%.
Nel contesto industriale moderno, la verniciatura rappresenta una fase cruciale che incide non solo sull’aspetto estetico di un prodotto, ma anche sulla sua protezione e durabilità nel tempo. Spesso, quando le aziende hanno la necessità di installare un nuovo sistema di verniciatura, si trovano di fronte a una scelta fondamentale tra due modalità di applicazione dei prodotti vernicianti: quella manuale e quella automatica. Ciascuna presenta vantaggi specifici, ma anche sfide che possono avere un impatto significativo sull’efficienza e sulla qualità complessiva del prodotto finito.
La verniciatura manuale, pur offrendo un elevato grado di controllo e adattabilità, è legata fortemente all’abilità e all’esperienza dell’operatore. Questa modalità permette di intervenire su dettagli complessi e di gestire in maniera flessibile variabili imprevedibili, come superfici irregolari o condizioni ambientali mutevoli. Tuttavia, il processo manuale può
Da sinistra: l’entrata dei componenti nel tunnel di pretrattamento; il processo di nebulizzazione; i componenti a seguito del pretrattamento.
presentare limitazioni in termini di uniformità e ripetibilità dei risultati, aumentando il rischio di difetti e variabilità nella qualità della finitura.
Dall’altro lato, i sistemi automatici sono progettati per operare con alta efficienza, assicurare maggiore precisione e ripetibilità dei risultati, ridurre i tempi di lavorazione e minimizzare l’errore umano. Per tale motivo, essi sono particolarmente vantaggiosi in ambienti di produzione su larga scala, dove la costanza dei risultati e la velocità sono essenziali per mantenere la competitività e soddisfare le esigenze qualitative.
Pulsar ha affrontato direttamente questa decisione. Fino al 2017, l’azienda operava con un impianto di verniciatura manuale dotato di due cabine, ma nonostante l’efficienza dell’impianto, la qualità dei risultati non era all’altezza delle aspettative: problemi legati all’uniformità della finitura e alla qualità complessiva stavano compromettendo l’efficienza operativa e la capacità di rispettare gli standard elevati richiesti dai loro clienti. Per risolvere queste criticità, Pulsar ha scelto di automatizzare la fase di applicazione della vernice, affidandosi a Lesta, azienda di Dairago (Milano), che ha fornito un nuovo robot di verniciatura antropomorfo a sei assi. Questo robot, installato all’interno di un’unica cabina di verniciatura, lavora in sinergia con i reciprocatori. Il robot si occupa di applicare la vernice nelle aree più difficili da raggiungere, come le aree cave dei componenti, mentre i due reciprocatori, ciascuno dotato di tre pistole, rivestono le superfici più piane. Questa innovazione ha permesso all’azienda polacca di superare le
limitazioni del processo manuale, raggiungendo livelli di qualità superiori e garantendo una maggiore costanza in termini di finitura.
Pulsar: innovazione e qualità nella produzione di accessori per sicurezza e videosorveglianza Dal 1994, Pulsar (Lapczyca, Polonia) si è affermata come leader nel settore della produzione di accessori per sistemi di allarme, controllo d’accesso e videosorveglianza. La gamma di prodotti offerti da Pulsar è ampia e diversificata e comprende contenitori, alimentatori, dispositivi PoE, sistemi antincendio, trasformatori e accumulatori di corrente. L’azienda polacca ha rapidamente esteso la sua influenza ai mercati europei e asiatici, consolidando la sua posizione grazie a un costante impegno verso l’eccellenza. “Grazie a una strategia incentrata sulla qualità e sull’innovazione, siamo riusciti ad espanderci in nuovi mercati e a mantenere una posizione di leadership,” afferma Krzysztof Tatara, CEO di Pulsar.
Oggi, con oltre 200 dipendenti e una sede produttiva di 8.000 m², Pulsar si distingue come un’azienda moderna e dinamica, capace di rispondere con flessibilità alle esigenze del mercato globale. Il successo dell’azienda è il risultato di un ciclo produttivo attentamente curato, in cui ogni fase è progettata per garantire standard qualitativi elevati.
“Pulsar utilizza solo materiali di altissima qualità e sottopone ogni prodotto a rigorosi controlli durante tutte le fasi della produzione, che spazia dalla
lavorazione della lamiera alla verniciatura, dalla produzione e installazione di componenti elettrici all’assemblaggio finale”, continua Tatara. “La verniciatura è una delle fasi più importanti del nostro processo produttivo, poiché conferisce ad ogni componente metallico una protezione essenziale. Infatti, il ciclo di finitura ha per Pulsar prima di tutto un ruolo funzionale e poi estetico”.
Il ciclo di verniciatura e la particolarità della cabina
Il processo di verniciatura è progettato per garantire la massima qualità e durabilità del prodotto finito, mantenendo al contempo un’elevata efficienza produttiva. “I componenti, dopo essere stati caricati manualmente dall’operatore sul trasportatore monorotaia entrano nel tunnel di pretrattamento e sottoposti ad una fase di sgrassaggio, necessaria per rimuovere oli e residui superficiali derivanti dalle fasi di lavorazione precedenti, combinata con una passivazione con sali di ferro per conferire uno strato protettivo; una fase di risciacquo con acqua di rete e un ulteriore risciacquo con acqua demi. Questi passaggi sono sufficienti per i prodotti di Pulsar, destinati all’uso interno come i sistemi di sicurezza per abitazioni, che non richiedono protezione avanzata contro la corrosione”, afferma Łukasz Szczepanik, Sales Manager di Indufinish, società di ingegneria che ha fornito l’impianto di verniciatura.
“Inoltre, la particolarità del tunnel di pretrattamento risiede nell’uso di
vasche realizzate in polipropilene, che garantisce numerosi vantaggi rispetto all’acciaio. Esso si distingue per la sua elevata resistenza alla corrosione, un fattore determinante in ambienti industriali dove umidità e prodotti chimici possono facilmente deteriorare l’acciaio. Il miglior isolamento termico offerto dal polipropilene, infine, contribuisce a una maggiore efficienza energetica dell’impianto, mantenendo temperature stabili e riducendo le dispersioni di calore”, continua Szczepanik.
Dopo il pretrattamento, l’operatore scarica i pezzi, i quali vengono sottoposti al processo di mascheratura, necessaria per evitare che determinate parti perdano la propria conduttività; sono quindi posizionati su appositi carrelli e trasportati verso la nuova zona dedicata all’applicazione della verniciatura. “La precisione con la quale i prodotti vengono agganciati è cruciale poiché anche uno spostamento di pochi mm può influire sulla qualità finale della finitura. Per questo motivo, l’operatore utilizza dei tracker laser per posizionare i componenti correttamente sui ganci di appensione”, prosegue Szczepanik. Il sistema, dotato di una barriera laser per il rilevamento automatico delle sagome dei prodotti, ottimizza la fase di applicazione della vernice.
I componenti vengono trasportati all’interno della cabina di verniciatura a una velocità di 1 metro al minuto, dove il processo di applicazione del rivestimento è suddiviso in due fasi. Inizialmente, il robot antropomorfo a sei assi fornito da Lesta si occupa di applicare il rivestimento nelle aree cave e difficilmente raggiungibili, sfruttando la sua tecnologia avanzata per
verniciare le superfici concave. Successivamente, sei pistole montate sui reciprocatori, fornite da PUT Wagner-Service Polska, applicano la polvere sulle superfici esterne dei componenti, che sono per lo più piane. “La particolarità di questa installazione,” spiega il Sales Manager di Indufinish, “è che, all'interno di un'unica cabina, convivono sia il robot che i reciprocatori. A differenza di altri sistemi in cui il robot svolge solo una funzione di pre-ritocco, qui è parte integrante della fase di applicazione.”
Se necessario, viene eseguito un ritocco manuale ma, grazie alla programmazione avanzata dei robot, questa operazione è ormai rara. “La cabina di verniciatura è progettata per consentire rapidi cambi di colore grazie all’utilizzo di un ciclone che facilita il riutilizzo delle polveri residue. In Pulsar abbiamo una media di cinque cambi colore a settimana in quanto l’80% della produzione è verniciata di bianco, mentre il restante 20% di nero, grigio e rosso”, spiega Tatara. Al termine della fase di applicazione, i prodotti entrano nel forno di polimerizzazione per circa 20 minuti e dopo il raffreddamento, l’operatore li scarica dai ganci, toglie eventuali mascherature, si occupa del controllo qualità e prepara i prodotti per la spedizione. Nonostante le dimensioni compatte dell’impianto di verniciatura, Pulsar è in grado di trattare fino a 2.000 set di prodotti, ciascuno composto da due pezzi, in una giornata lavorativa di 16 ore. In alcune circostanze, l’impianto può gestire fino a 5.000 set di prodotti più piccoli.
Le ragioni di una scelta
Pulsar ha recentemente intrapreso un importante rinnovamento del proprio impianto di verniciatura. Nonostante l’impianto fosse stato installato nel 2017, le sfide legate alla
APPROVED www.lechler.eu
LECHLER TECH WATER-BASED PRODUCTS: HIGH QUALITY FINISHES ON A WIDE RANGE OF METAL AND PLASTIC SUBSTRATES.
Dopo la fase di applicazione, i componenti transitano in un polmone di accumulo prima di entrare nel forno di polimerizzazione (a sinistra) e un dettaglio dei componenti in uscita dal forno di polimerizzazione.
qualità del rivestimento sono emerse con il tempo. “Il sistema manuale che avevamo in uso, sebbene inizialmente efficace, iniziava a mostrare i suoi limiti,” ha spiegato il CEO di Pulsar. “Le differenze tra gli operatori, specialmente durante i turni, causavano variazioni indesiderate nella qualità del prodotto finale. Non potevamo permettere che questo influenzasse la nostra reputazione. Da qui, la scelta di fare un salto tecnologico: su consiglio di Indufinish, a cui ci eravamo già rivolti per l’installazione dell’impianto di verniciatura, abbiamo deciso di investire in un robot di verniciatura automatizzato non solo per migliorare la qualità del rivestimento, ma anche per incrementare la nostra capacità produttiva. Oggi, grazie a questa tecnologia, la nostra produzione è aumentata di oltre il 400%”.
Conclusioni
“Dopo una visita presso l’impianto per analizzare le problematiche, è stato subito evidente che una parte significativa delle operazioni manuali poteva essere ottimizzata tramite l’uso di un robot di verniciatura. Ho suggerito a Pulsar che l’automazione avrebbe potuto sostituire molte delle operazioni manuali, migliorando così l’efficienza e la qualità del processo di verniciatura”, afferma il Sales Manager di Indufinish. “Organizzammo
quindi un incontro con Igor Kania, rappresentante per il mercato polacco di Lesta, e già nel corso di quel primo incontro fu subito evidente che il robot avrebbe potuto risolvere i problemi riscontrati”. L’implementazione del robot, inizialmente non prevista, è diventata la chiave per risolvere le problematiche di qualità e rendere il processo di produzione più fluido e meno dipendente dal lavoro manuale. La scelta di integrare il robot non ha solo ottimizzato i processi produttivi, ma ha anche migliorato le condizioni di lavoro all’interno dell’azienda. “Ridurre l’esposizione dei nostri dipendenti alle polveri era una priorità,” ha sottolineato Tatara. “Ora, i nostri addetti si occupano principalmente della programmazione del robot più che della verniciatura, il che rende il loro lavoro meno gravoso”.
Il CEO ha inoltre espresso grande soddisfazione per la tecnologia avanzata di Lesta e il continuo supporto di Indufinish: “Non possiamo che essere entusiasti della nostra collaborazione con Lesta e Indufinish.
La tecnologia fornita da Lesta si è dimostrata all’altezza delle nostre aspettative, e il supporto costante di Indufinish è stato fondamentale per affrontare e risolvere ogni sfida che si è presentata lungo il cammino. Siamo estremamente soddisfatti dei risultati ottenuti e siamo certi che questa collaborazione con Lesta e Indufinish ci permetterà di continuare a crescere e a soddisfare le esigenze dei nostri clienti”.
Federica Alberti
SG Projects – Voghera (Italia) federica.alberti@sgprojects.it
SG Projects è l’azienda partner di Solecta che si occupa della distribuzione dei loro prodotti e vernici in Italia, garantendo un supporto continuo ai clienti e rappresentando un intermediario rapido, pronto a risolvere velocemente qualsiasi problematica che possa sorgere sulle linee di ultrafiltrazione. Di seguito è presentata una panoramica dei vantaggi offerti dalle membrane ad ultrafiltrazione per i processi di elettroforesi e una guida rapida per eseguire operazioni manutentive efficaci.
Il cuore di un processo di verniciatura industriale è il bagno cataforetico, dove uno strato viene depositato per elettrodeposizione sui pezzi da verniciare. Al termine di questa fase, i pezzi verniciati sono risciacquati con ultrafiltrato (la parte liquida del bagno di verniciatura, purificata dai pigmenti attraverso un processo simile alla osmosi inversa ma con un diverso cut-off).
L’ultrafiltrazione è un processo a membrana azionato dalla pressione, in grado di separare i componenti della soluzione in base alle dimensioni e alla forma delle molecole. Applicando una differenza di pressione lungo una membrana di ultrafiltrazione, il solvente e le specie di soluto di piccole dimensioni passano attraverso la membrana e vengono raccolti come permeato, mentre le specie di soluto più grandi vengono trattenute dalla membrana e recuperate come concentrato. Negli impianti di cataforesi, il permeato dell’ultrafiltrazione contiene acqua e solubilizzante per vernici. Il permeato è utilizzato nella sezione di risciacquo della linea di verniciatura. Questo metodo di recupero fornisce un sistema di risciacquo a ciclo chiuso per il recupero del contenuto solido di una vernice (drag-out). Inoltre, il permeato può essere deviato verso lo scarico per ridurre la conduttività della vernice. Il grado di recupero della vernice dipende dalla quantità di acqua di risciacquo fornita al bagno di verniciatura a immersione. Questa quantità corrisponde alla quantità di filtrato. La capacità del filtrato riferita alla superficie della cartuccia a membrana ad una certa capacità di ricircolo
della vernice è la “capacità specifica del filtrato”, che dipende dal tipo di vernice utilizzata e deve essere determinata caso per caso mediante misurazione.
La capacità specifica del filtrato è influenzata anche dal sistema di ricircolo della vernice, ovvero dalla:
Pressione
Temperatura
Concentrazione di solidi
Flusso trasversale
Trascinamento dal pretrattamento
È necessario adattare il materiale di reintegro all'uso dell'ultrafiltrazione. Per essere più precisi, nel processo di verniciatura è necessario risciacquare prima la superficie delle parti rivestite con acqua e successivamente risciacquare con acqua pura. Le acque reflue contengono principalmente sostanze chimiche nocive come resina epossidica, vernice, olio vegetale, acido carbossilico, butanolo e pigmenti. Quando il pezzo verniciato è estratto dalla vasca di elettroforesi, è necessario utilizzare acqua per lavare via la vernice liquida residua sulla superficie, producendo così acque reflue contenenti vernice elettroforetica. La vernice elettroforetica presente nelle acque reflue rappresenta il 30% della vernice utilizzata. L’adozione di un dispositivo a membrana di ultrafiltrazione creerà un percorso di circolazione chiuso, consentendo di riutilizzare sia la vernice che l’acqua.
Un semplice schema rappresentate un processo di elettroforesi con membrane ad ultrafiltrazione.
I vantaggi delle tecnologie di ultrafiltrazione
L’ultrafiltrazione può offrire vantaggi significativi in termini di recupero della vernice, controllo dei parametri chimici della verniciatura e bilanciamento della conducibilità nella vasca. Con il procedere del processo di elettroforesi, il contenuto di acqua, co-solventi e ioni inorganici nella soluzione di elettroforesi nella vasca metallica aumenta, incidendo sulla qualità del processo di verniciatura. La tecnologia di ultrafiltrazione è in grado di trattenere i polimeri e i pigmenti, rimuovere l’acqua in eccesso e altre impurità nella soluzione di elettroforesi, prolungare la durata della soluzione di rivestimento e migliorare la qualità della vernice.
La tecnologia delle membrane di ultrafiltrazione offre quindi i seguenti vantaggi per il trattamento delle acque reflue derivanti dal processo di verniciatura per elettroforesi:
Ha un buon effetto di ritenzione, fornendo un filtrato pulito e trasparente dopo il trattamento;
Il controllo automatico del sistema è semplice e facile da usare, in modo da garantire la sicurezza durante le operazioni;
L’apparecchiatura, di ingombro ridotto, ha una struttura robusta e un basso consumo energetico;
La grande portata d’acqua è adatta al recupero della vernice elettroforetica catodica e anodica;
Possiede una buona capacità di resistenza alla contaminazione e il funzionamento a lungo termine non influisce sulla produzione di acqua. Di fatto, la tecnologia delle membrane di ultrafiltrazione ha svolto un ruolo importante nel processo di verniciatura per elettroforesi di scocche, accessori per bagagli, elettrodomestici e diversi componenti
metallici per molti altri settori industriali. Il tasso di recupero è aumentato significativamente e il costo di lavorazione è stato ridotto del 30%.
La manutenzione delle membrane di ultrafiltrazione
Dopo diverse ore di funzionamento, il processo di elettroforesi può subire una diminuzione della velocità di flusso. Pertanto, potrebbe essere necessaria una procedura di recupero. Diversi fattori, legati al normale funzionamento dell’impianto di elettroforesi, possono influenzare il flusso del permeato attraverso le membrane di ultrafiltrazione, come il tipo di vernice impiegata, la percentuale di solidi, la temperatura operativa, la conducibilità e il pH dei serbatoi, il flusso di vernice e la pressione di ingresso alle membrane, nonché la contaminazione da caduta e trascinamento dal tunnel di pretrattamento, solo per citarne alcuni. Dopo l’avvio, il flusso di ultrafiltrazione diminuirà fino a raggiungere un flusso stazionario entro alcuni giorni; questo flusso stazionario sarà considerato come base di riferimento per il sistema. Tuttavia, quando il flusso scende a circa il 70% del valore stazionario, è il momento di procedere alla pulizia. Un ritardo nella pulizia può portare a incrostazioni irreversibili. È importante mantenere la portata raccomandata per il proprio sistema. Per la vernice, si consiglia di mantenere un differenziale di pressione di 2,0 - 2,3 bar, con una pressione minima in uscita di 0,7 bar. Considerando il numero di variabili che influenzano il corretto funzionamento del sistema di ultrafiltrazione, è fondamentale tenere un registro dettagliato e aggiornarlo regolarmente. Questo permetterà di evitare potenziali problemi e di determinare con maggiore precisione la causa del calo di flusso, così da eliminarla come problema potenziale o ricorrente.
Di seguito le problematiche più comuni e le relative soluzioni:
Arresti
Quando si verifica un arresto non programmato, la vernice non deve rimanere inattiva nel sistema di ultrafiltrazione: se lasciata inattiva per troppo tempo, le membrane possono sporcarsi in modo irreversibile. Pertanto, durante gli arresti, è necessario drenare e risciacquare immediatamente il sistema con acqua fresca demineralizzata o da osmosi inversa (o permeato, se disponibile) e avviare una procedura di pulizia chimica prima di fermare il sistema.
Aggiunte alla vernice
Inoltre, quando si aggiungono resina, pigmenti, solventi o solubilizzanti alla vernice, questi devono essere aggiunti lentamente e secondo le raccomandazioni del fornitore. Inoltre, le aggiunte non devono essere effettuate in prossimità dell’ingresso della pompa di ultrafiltrazione.
Un esempio di tecnologie ad ultrafiltrazione.
• ZERO EMISSIONS
• EASY MAINTENANCE
• FULLY AUTOMATIC
Sedimenti e agglomerati
Un esempio di sistema di ultrafiltrazione e uno schema del processo.
Le vernici contengono sempre una piccola percentuale di particelle di vernice destabilizzate, che possono causare la formazione di sedimenti o agglomerati nelle aree del sistema con flusso nullo. Poiché circa 10 g di agglomerati possono danneggiare un elemento da 8”, è fondamentale eseguire tutte le procedure di prefiltrazione necessarie per evitare che sedimenti e/o agglomerati raggiungano i moduli di ultrafiltrazione.
Incrostazioni di vernice
Uno dei principali motivi di prestazioni insoddisfacenti e di diminuzione del flusso è legato alle incrostazioni di vernice. Il fouling della vernice si verifica quando la stabilità o la solubilità della vernice consente l’agglomerazione delle particelle di vernice, causando l’ostruzione della superficie della membrana con questi agglomerati “gommosi”. Di conseguenza, il permeato attraversa la membrana con maggiore difficoltà.
Stabilità della vernice
Una buona vernice è costituita da particelle di vernice disperse che presentano cariche elettriche ottimali per respingere ogni particella dalle
altre, inibendo la formazione di agglomerati. La vernice instabile può perdere queste cariche elettriche a causa di una o più delle seguenti condizioni:
Livelli inadeguati di solubilizzante che causano un’alterazione del pH della vernice;
Contaminanti (come il ferro) che reagiscono con il solubilizzante o la vernice;
Batteri che consumano il solubilizzante o disturbano in altro modo la solubilità della vernice;
Portate troppo basse per spazzare via lo strato di incrostazioni sulla superficie della membrana;
Portate molto basse che provocano sedimentazione, perdita di carica elettrica e agglomerazione;
Materiale di alimentazione di reintegro introdotto in modo improprio;
Introduzione di aria occlusa nella vernice, attraverso il vortice della pompa, ecc...
Dosing and nebulization system for the conversion coating of metal and aluminium parts
Drizzling consists of a dosing panel for automatically managing the demineralized water coming from a feed tank and the amount of passivating chemical product, in order to apply an optimally concentrated solution on the material to be treated. The use of special atomizing nozzles and compressed air enables it to produce and evenly distribute a light mist of chrome-free solution.
Electric circuit fully insulated from liquids for greater safety The solution that is sprayed is always fresh and dosed in-line
Suitable to treat different types of metal components
Andreas Michalske
VENJAKOB Maschinenbau GmbH & Co.KG, Rheda-Wiedenbrück- Germania andreas.michalske@venjakob.de
Le moderne raccorderie combinano forma, funzionalità e design. La sfida dei produttori è soddisfare le preferenze individuali relative a colore e design e al contempo garantire durabilità e resistenza all’abrasione. Prima o poi la finitura potrebbe subire danni in alcune aree, specialmente in caso di utilizzo intensivo. Insieme a tre partner tecnologici, Venjakob - specializzata in linee di finitura personalizzate - fornisce una soluzione che offre notevoli vantaggi economici ed ecologici.
Ovunque vi sia richiesta di rubinetterie e pezzi cromati con una superficie elegante colorata, metallizzata o liscia, il rivestimento gioca un ruolo fondamentale. A seconda del materiale da rivestire, il processo può essere molto complesso e dispendioso in termini di risorse. Gli accessori, per esempio nei bagni e nelle cucine, sono
soggetti ad uso intensivo e devono quindi essere robusti e resistenti alla corrosione.
“La sola metallizzazione non è sufficiente per ottenere un’adesione del rivestimento di lunga durata”, afferma Andreas Michalske, Sales Engineer di Venjakob.
Finiture superficiali innovative e resistenti per componenti in metallo e plastica senza l’uso di metalli pesanti grazie al processo HEC. Questo processo ecologico offre proprietà tecniche migliorate, supera i rigidi requisiti di settore e offre un aspetto accattivante, con una scelta quasi illimitata di colori e livelli di brillantezza.
Venjakob ha presentato il suo processo di verniciatura brevettato durante PaintExpo 2024 a Karlsuhe/Germania, la fiera leader per le tecnologie di verniciatura.
Fino al 70% di risparmio senza alcuna perdita di qualità Per l’industria dei raccordi, il processo di verniciatura di alta qualità (HEC) potrebbe essere la soluzione a molte sfide. Esso include uno speciale pretrattamento in un sistema ad alto vuoto. Alla superficie dei componenti metallici e plastici viene applicato uno strato funzionale antistatico con una maggiore tensione superficiale. Questo semplifica il successivo processo di verniciatura. Il pre-lavaggio della superficie con aria ionizzata è sufficiente. “Nel successivo processo di verniciatura possiamo gestire spessori compresi tra 12 e 25 µm. Il consumo di vernice è ridotto fino al 70%. I componenti trattati in questo modo hanno un aspetto qualitativamente elevato e superano tutti i test”, spiega Michalske. È importante sapere che l’industria dei raccordi pone requisiti più elevati rispetto, per esempio, all’industria automobilistica. Esiste il cosiddetto test di ebollizione: i componenti vengono posti in un liquido in ebollizione per verificare quanto a lungo rimangono intatti o non rilasciano alcuna sostanza dannosa. Nel settore auto i componenti “bollono” per un’ora. Nel settore tedesco della raccorderia, per 100 ore.
Meno sforzi per risultati migliori
Il processo di rivestimento di alta qualità si completa in soli pochi passi. I componenti sono pretrattati con uno speciale processo in alto vuoto e con un plasma sottovuoto appositamente generato. Successivamente passano al sistema di verniciatura. Il pretrattamento in alto vuoto sostituisce la passivazione e la fosfatazione, riducendo quindi il numero delle fasi necessarie. Non vi è alcun accumulo sui bordi durante il successivo processo di verniciatura. Questo processo offre molti altri vantaggi e può anche essere integrato nei processi in serie esistenti.
Chi è Venjakob
Venjakob, fondata nel 1963 e alla terza generazione di conduzione familiare, è tra i leader mondiali nella produzione di linee di finitura. L’azienda sviluppa soluzioni individuali per l’intera linea produttiva, incluse soluzioni di pretrattamento, verniciatura, asciugatura e tecnologie di essiccazione, nonché impianti di purificazione dell’aria di scarico. Il tutto da un’unica fonte e personalizzato secondo le esigenze degli utilizzatori provenienti da una vasta gamma di settori. Venjakob ha sede a Rheda-Wiedenbrück, in Germania, e conta 380 dipendenti in tutto il mondo. Tra gli stabilimenti produttivi troviamo Venjakob Umwelttechnik GmbH & Co. KG a Sarstedt, in Germania e Nutro Inc. a Strongsville, Ohio, USA.
• Ispezionato, testato e comprovato a livello industriale
• Conforme agli standard dei settori raccorderia, hardware e automotive
• Sistema monostrato, senza promotori di adesione o primer aggiuntivi
• Può essere integrato in processi in serie esistenti
• Non sono necessarie condizioni di camera bianca
• Risparmio di vernice fino al 70%
• Nessun costo di smaltimento
• Sostituisce passivazione e fosfatazione
• Non sono necessarie sostanze chimiche aggiuntive né acqua
• A basso impatto ambientale, privo di cromo e metalli pesanti
50
60 HIGHLIGHT OF THE MONTH
Le vernici in polvere a bassa temperatura di KABE-Farben: qualità per applicazioni architettoniche
62 SUCCESS STORIES
La collaborazione tra DHK, ALIT Technologies e Alufinish inaugura una nuova era per la protezione delle superfici metalliche
66 FOCUS ON TECHNOLOGY
Vernici in polvere metallizzate e ad effetto per le superfici tridimensionali di rivestimento di Emboss
72 ROAD TO 2050
EcoAl® di Alsan - passivazione esente cromo nei processi di pretrattamento per la verniciatura a polvere
76 RESEARCH BREAKTHROUGH
Rivestimento antiaderente ultrasottile, duro e sostenibile rivoluziona i processi di formatura nello stampaggio a iniezione e nella pressofusione
80 FOCUS ON TECHNOLOGY
Azeta si conferma azienda pioniera nella verniciatura dell’alluminio grazie a una nuova linea verticale combinata con un innovativo sistema di alimentazione polveri IPS
HIGHLIGHT OF THE MONTH
ST Powder Coatings presenta la nuova serie Green Oasis Range, l’oasi ecosostenibile del futuro
Evoluzione del design: la tecnologia PVD di Kenosistec per finiture eleganti,durature e sostenibili
FOCUS ON TECHNOLOGY
Luxe Perfil: gli esperti nell’impossibile si affidano alle prestazioni del nuovo prodotto di pretrattamento PrimeCoat® A109
FOCUS ON TECHNOLOGY
Alzare l’asticella della qualità: il nuovo impianto di Sirio Galv per la verniciatura a liquido di complementi d’arredo e illuminazione di alta fascia
EcodePure è la via verso il riciclo dell'acqua e lo scarico zero
SUCCESS STORIES
ItalMesh riveste il nuovo Burger King di Rovereto con i suoi pannelli in alluminio forato e verniciato
SUCCESS STORIES
RIPOL a Bayreuth: innovazione e design avanguardista
AkzoNobel rafforza il suo impegno per ridurre l’impronta di carbonio con una gamma di vernici in polvere a basso consumo energetico e superdurevoli.
Il settore architettura può ora contare su un rivestimento in polvere superdurabile a bassa temperatura sviluppato da AkzoNobel, che aiuta a proteggere gli edifici anche negli ambienti più difficili. Dopo il lancio, nel 2023, della versione con durabilità standard, la nuova gamma Interpon D2525 Low-E è stata specificamente progettata per resistere in condizioni ambientali più estreme. Supportata da una Dichiarazione Ambientale di Prodotto (EPD) contribuisce a migliorare la longevità anche in ambienti standard. Utilizzando la tecnologia pionieristica introdotta da AkzoNobel in occasione del lancio della versione standard, la nuova gamma può essere polimerizzata a temperature più basse (150 °C), pur offrendo gli alti livelli di qualità e prestazioni richiesti dai clienti nei settori dell›edilizia e delle costruzioni.
“Quest’ultima innovazione conferma il nostro impegno nell’ascoltare i clienti e fornire loro sempre nuovi vantaggi - come una maggiore durabilità e la polimerizzazione a bassa temperatura - senza compromettere l’estetica”, afferma Bob Dirks, Global Segment Manager per l’Architettura nella divisione Vernici in Polvere di AkzoNobel.
“Supporta inoltre la necessità di una responsabilità collettiva verso un futuro più sostenibile e sottolinea il nostro impegno per la sostenibilità lungo tutta la catena del valore.”
L’Interpon D2525 Low-E può essere polimerizzata a una temperatura
più bassa (150 °C invece di una temperatura standard compresa tra 180 °C e 200 °C) per ridurre il consumo energetico fino al 20%, oppure può essere polimerizzata fino al 25% più velocemente rispetto alle vernici convenzionali, consentendo di rivestire più prodotti in meno tempo e migliorare l›efficienza della linea di rivestimento.
Oltre a supportare i clienti nella riduzione delle loro emissioni di carbonio, aiuterà AkzoNobel a raggiungere il proprio obiettivo di riduzione del 50% delle emissioni di carbonio, lungo la catena del valore, entro il 2030. È ideale per qualsiasi superficie metallica architettonica o industriale, sia esterna che interna, e le caratteristiche principali includono eccellenti livelli di durabilità sia in termini di prestazioni che di integrità del colore. I clienti Interpon possono anche richiedere assistenza per il calcolo dei benefici derivanti dall’uso dei prodotti Low-E, in termini di risparmio energetico, emissioni di carbonio o di aumento della produttività.
Le vernici in polvere Interpon sono presenti su alcuni degli edifici più famosi al mondo, tra cui The Shard e l’Abbazia di Westminster a Londra, Regno Unito; lo stadio Bird’s Nest a Pechino, Cina e la Sagrada Familia a Barcellona, Spagna.
Per maggiori informazioni: www.interpon.com/gl/en/products/architectural/interpon-d-low-e
GSB International Association parteciperà alla prossima edizione di ALUMINIUM (stand 3F70-03), che si terrà dall’8 al 10 ottobre 2024 a Düsseldorf.
La garanzia della qualità dei rivestimenti è di grande importanza per l’industria dell’alluminio perché, indipendentemente dal prodotto, è la superficie a catturare sempre l’attenzione. Si presta quindi particolare attenzione alla garanzia della qualità ogni volta che una superficie è esposta a influenze esterne ma deve mantenere un aspetto ragguardevole per lungo tempo – come avviene per le facciate.
Gli edifici sono in genere costruiti per essere utilizzati per molti decenni e, a seconda della loro posizione, sono esposti a varie influenze ambientali. Sulle coste, l’acqua salata del mare può aumentare la corrosività dell’ambiente, mentre le regioni con molte ore di sole all’anno hanno alti livelli di intensità UV.
Ma anche l’utilizzo che si fa degli edifici ha un ruolo: le piscine, per esempio, sono pulite con detergenti aggressivi. L’elenco dei possibili fattori di stress potrebbe continuare all’infinito…
Con il suo sistema di garanzia della qualità per il rivestimento dell’alluminio nel settore architettonico, GSB International – associazione leader nella qualità per i rivestimenti superficiali nei settori dell’alluminio e dell’acciaio – tiene conto di queste influenze esterne e garantisce così ad architetti, costruttori e progettisti un’esperienza lavorativa senza stress.
Chiunque sia interessato alla garanzia di qualità o abbia domande dettagliate sui rivestimenti può incontrare gli esperti di GSB alla fiera ALUMINIUM 2024 di Düsseldorf. Allo stand 3F70-03, l’associazione non vede l’ora di intrattenere grandi conversazioni sui rivestimenti e non solo: ci sarà infatti anche un impianto di verniciatura a polvere, per consentire a tutti i visitatori di sperimentare questo processo in prima persona.
Per maggiori informazioni: www.gsb-international.de
PRATIC ha scelto di affidarsi alla competenza di IMEL per installare un nuovo impianto di verniciatura all’avanguardia che garantisce performance qualitative elevate ai rivestimenti in polvere di pergole e tende da sole in alluminio.
PRATIC S.p.A., parte del gruppo STELLAGROUP, leader mondiale nella produzione di pergole e tende dal design e dall’architettura raffinati, ha implementato presso la sua sede produttiva di Fagagna (Udine) un avanzato impianto di verniciatura a polveri, realizzato da IMEL S.p.A..L’impianto è stato progettato per garantire elevate prestazioni in termini di resistenza, offrendo una notevole versatilità nei cicli di pretrattamento e verniciatura, con un alto grado di automazione. Il sistema è ottimizzato per il risparmio energetico ed integra un sofisticato impianto di depurazione che permette il recupero degli scarichi reflui. La linea si distingue per l’uso di apparecchiature di alta qualità, un design compatto che ottimizza gli spazi, e l’attenzione ai dettagli, tratti distintivi dei progetti di PRATIC. L’impianto comprende un tunnel di pretrattamento a camere separate, realizzato interamente in INOX AISI 316, che permette il trattamento localizzato e riduce al minimo la contaminazione dei bagni, rendendolo idoneo all’utilizzo di qualsiasi agente chimico. I forni di asciugatura e polimerizzazione delle polveri, posti uno accanto all’altro, sono isolati adeguatamente e dotati di porte che garantiscono un ottimale mantenimento termico, contribuendo così a ridurre i consumi di combustibile. L’impianto è inoltre dotato di due cabine Magic Cylinder di Gema, ciascuna equipaggiata con 14 pistole alimentate da un sistema di spruzzatura che utilizza pompe in fase densa e un sistema di cambio colore rapido. Elemento chiave dell’impianto è la sua eco-compatibilità: il 97% delle acque reflue viene recuperato grazie a un complesso sistema di
depurazione basato sull’evaporazione per ricompressione meccanica. Questo innovativo processo consente il riutilizzo dell’acqua negli stadi di pretrattamento, mantenendo i bagni in condizioni ottimali e riducendo il consumo di risorse idriche, con uno scarico quasi nullo nella rete fognaria. Grazie all’alto livello di automazione e all’integrazione di alcuni moduli della piattaforma i4paintshop®, l’impianto è in grado di gestire automaticamente diversi cicli di verniciatura, in base al codice dei pezzi e alle priorità assegnate. Il sistema garantisce una gestione automatica dei flussi di dati, completa tracciabilità dei processi, monitoraggio costante dei consumi energetici e un’efficiente programmazione della manutenzione. Inoltre, grazie alla lettura digitale dei dati di ogni componente dell’impianto, è possibile gestire in maniera ottimale la qualità e ridurre gli scarti, in conformità alle normative Qualicoat. Le elevate prestazioni di verniciatura e il rigoroso controllo del processo hanno permesso a PRATIC di ottenere la prestigiosa certificazione QUALICOAT SEASIDE, che attesta il rispetto delle normative internazionali più stringenti in termini di qualità del trattamento dell’alluminio e della verniciatura. Questa certificazione garantisce a PRATIC il massimo livello di adesione della vernice e una resistenza eccellente alla corrosione causata dagli agenti atmosferici. Grazie a questa collaborazione, IMEL ha superato una nuova sfida nei trattamenti di verniciatura industriale di alta gamma, dimostrando la propria competenza e capacità innovativa.
Per maggiori informazioni: www.imelspa.com
New TIXO Clear and TIXO Filler. Superior quality for carbon fiber surfaces.
The Tixo line redefines the finishing of carbon surfaces, both glossy and matte. Specifically designed for this material, TIXO products offer extraordinary thixotropy and fullness, allowing for the application of considerable thicknesses with excellent levelling and impeccable aesthetic appearance. Thanks to their high resistance, these UHS paints reduce the number of coats required, ensuring faster and more efficient processing. The exceptional gloss and scratch resistance of TIXO paints elevate quality standards to a superior level.
Discover all Vernici Caldart products designed for Automotive on our website.
Le tendenze cromatiche 2024-2025 sono state presentate da Axalta nel suo ultimo Vibes Colour Journal: natura e aspirazioni tecnologiche si uniscono sotto il nome di Architectural Fusion.
Axalta Coatings ha lanciato l’ultima edizione di Vibes, la rivista con cui l’azienda offre annualmente ad architetti e designer una guida alle ultime tendenze, esplorando colori e texture nell’ambiente costruito. Gli ultimi trend sono stati raccolti sotto il tema ‘Architectural Fusion’, fondendo l’essenza della natura con le aspirazioni tecnologiche e la profondità emotiva.
Le nuove tendenze colore di Axalta catturano il legame con la natura e allo stesso tempo abbracciano un futuro guidato dalla tecnologia, aiutando architetti e designer nei loro sforzi creativi. Questa dualità ispira
la creatività ed evoca una miscela di calma e nuovi inizi.
Inoltre, i casi studio presentati sulla rivista dimostrano che i materiali da costruzione verniciati con i prodotti Axalta sono variegati come le moderne società globali. Il portfolio tecnologico di Axalta affronta la natura di questi materiali diversi, come i substrati metallici, combinandoli con un’esperienza cromatica esaltante.
“Nel presentare l’ultima edizione di Vibes, siamo entusiasti di mostrare la vibrante intersezione tra colore, creatività e innovazione nella progettazione architettonica. I nostri temi curati - Earth Unity, Human Evoke, Tech Vision e Vivid Vibe - riflettono una miscela armoniosa di natura, tecnologia e connessione umana, offrendo ai progettisti una tavolozza di colori e finiture di grande ispirazione. Ogni pagina di Vibes è una testimonianza dell’impegno di Axalta nel superare i confini del design, nel promuovere una connessione più profonda con il nostro ambiente e nell’abbracciare le infinite possibilità del futuro,” ha dichiarato Sally Put, Direttrice della rivista e Global Marketing Communications Manager di Axalta EMEA.
Vibes 2024-25 analizza le seguenti tendenze cromatiche:
Earth Unity: Il legame dell’umanità con la natura e l’universo. Tonalità come il cristallo ametista, l’ocra, la pietra e l’argilla ricordano le foreste e i frutti di bosco.
Human Evoke: Enfatizza le connessioni emotive. I toni più chiari ricordano i motivi delle conchiglie, con accenni di pietra, metalli preziosi e rosso emotivo.
Tech Vision: Ambizioso e curioso, appassionato di tecnologia. I colori includono giallo paglierino, rosa, verde, blu e viola, che riflettono l’innovazione e l’esplorazione scientifica.
Vivid Vibe: una tavolozza che celebra la creatività speranzosa. Riconosce il mondo così com’è e s’impegna per un futuro più luminoso. Immaginate colori che evocano ricordi, stimolano l’immaginazione e ispirano la creatività nel design.
Per maggiori informazioni: www.axalta.com/colourdesign_global/en_US/vibes-colourjournal.html
Il certificato QUALICOAT garantisce che i prodotti di WEG Messico soddisfano i più alti standard di qualità.
La filiale messicana del produttore internazionale di equipaggiamenti elettrici WEG ha recentemente ottenuto il certificato di qualità QUALICOAT, a seguito di ispezioni condotte da esperti e test eseguiti da laboratori accreditati secondo gli standard ISO 17025. Il sigillo di qualità QUALICOAT è uno schema di certificazione di prodotto sviluppato dall’omonima organizzazione globale con sede a Zurigo (Svizzera) e specializzata nella certificazione della qualità della verniciatura e del rivestimento dell’alluminio e delle sue leghe per applicazioni architettoniche. L’organizzazione definisce requisiti di qualità completi e ne monitora la conformità da parte degli stabilimenti autorizzati in tutto il mondo, garantendo che i prodotti soddisfino i più elevati standard di qualità e fornendo agli acquirenti la garanzia che riceveranno un prodotto di alta qualità.
Per maggiori informazioni: www.weg.net
WE TURN YOUR FORMULATIONS INTO OUTPERFORMULATIONS.
LIl gruppo internazionale tecnologico ANDRITZ, specializzato nella produzione di impianti, apparecchiature, sistemi, servizi e soluzioni digitali innovativi per un’ampia gamma di settori e mercati, ha completato con successo la consegna, l’installazione e l’avviamento della nuova linea di trattamento superficiale in continuo e dell’impianto integrato di trattamento delle acque reflue presso AMAG rolling GmbH di Ranshofen, in Austria. eseguire trattamenti superficiali di alta qualità per un’ampia gamma di coil in alluminio laminati a caldo e a freddo fino a 5 mm di spessore.
a moderna linea con riscaldamento esclusivamente elettrico e digitalizzazione avanzata rafforza la posizione di AMAG come uno dei principali specialisti in superfici di alluminio di alta qualità e supporta gli obiettivi di sostenibilità dell’azienda.
L’impianto lungo 115 m è stato costruito su un’area greenfield. I dispostivi ANDRITZ - in particolare l’impianto di decapaggio a spruzzo ad alta efficienza - consentono ad AMAG di
La nuova linea ANDRITZ per coil di alluminio presso AMAG è riscaldata con energia sostenibile ed è caratterizzata da una digitalizzazione avanzata per elevati livelli di qualità e produttività.
Il riscaldamento elettrico con energia sostenibile e l’integrazione di un impianto all’avanguardia per il trattamento delle acque reflue contribuiscono a una produzione ecocompatibile. Soluzioni digitali avanzate e moderni metodi di analisi dei dati vengono utilizzati per aumentare la qualità e la produttività del trattamento superficiale. Un sistema di trasporto autonomo dei coil, anch’esso alimentato elettricamente, migliora l’efficienza dell’intero processo produttivo. “Realizzare questo progetto insieme ad ANDRITZ è stata un’ottima decisione”, afferma Florian Stadler, amministratore delegato di AMAG rolling GmbH. “La collaborazione tra i nostri team è stata ancora una volta eccellente, come nei progetti precedenti, determinando la conclusione tempestiva del collaudo. Con questa nuova linea possiamo migliorare ulteriormente la qualità dei nostri prodotti e, allo stesso tempo, compiere un altro passo verso la decarbonizzazione”.
ANDRITZ GROUP
Il gruppo internazionale ad elevata tecnologia ANDRITZ offre un vasto portfolio di impianti, apparecchiature, sistemi, servizi e soluzioni digitali innovativi per un’ampia gamma di settori e mercati.
La sostenibilità è parte integrante della strategia e della cultura aziendali.
Con il suo ampio portfolio di prodotti e soluzioni green, ANDRITZ mira a dare il massimo contributo possibile a un futuro sostenibile e ad aiutare i propri clienti a raggiungere gli obiettivi di sostenibilità. ANDRITZ è leader globale di mercato in tutte e 4 le sue aree di business: cellulosa e carta, metalli, energia idroelettrica e ambiente ed energia. La leadership tecnologica e la presenza globale sono i capisaldi della strategia del gruppo, che si concentra su una crescita proficua a lungo termine. Il gruppo quotato in borsa ha circa 30 mila dipendenti e oltre 280 sedi in più di 80 Paesi.
ANDRITZ METALS
Tramite Schuler Group, ANDRITZ Metals è uno dei principali fornitori mondiali di tecnologie, impianti e soluzioni digitali nella formatura dei metalli. Il portfolio prodotti comprende anche soluzioni di automazione e software, knowhow di processo e assistenza. Nel segmento della lavorazione dei metalli, l’azienda offre soluzioni innovative, sostenibili e leader di mercato per la produzione e la lavorazione di prodotti piani, per impianti di saldatura e forni con le sue soluzioni di bruciatori, nonché servizi per l’industria della lavorazione dei metalli.
Per maggiori informazioni: www.andritz.com
Europolveri mette a frutto la sua quarantennale esperienza per proporre tre serie di vernici in polvere specificatamente sviluppate per le applicazioni dell’alluminio nei settori dell’architettura e del design.
Nel corso degli anni, i trattamenti di verniciatura a polvere hanno acquisito sempre più importanza.
©
Rappresentano infatti ormai una scelta fondamentale per architetti e progettisti alla ricerca di finiture performanti e accattivanti per elementi architettonici, mobili e oggetti d’arredo e di design. In questo contesto, le vernici in polvere offrono la possibilità di scegliere tra una vasta gamma di prodotti con un livello di specializzazione sempre maggiore, diventando un elemento fondamentale per il risultato finale di un progetto, non solo in termini estetici formali ma anche per quanto riguarda funzionalità e durata. Da oltre quarant’anni le vernici in polvere Europolveri, grazie alla loro tecnologia, applicabilità, specificità e varietà, rappresentano un punto di riferimento per il trattamento superficiale di molteplici tipologie di oggetti. La serie ArchitecturalPlus –certificata Qualicoat (classe 1 e 2) e GSB – è composta da prodotti specificatamente sviluppati per il mondo dell’architettura e formulati per esaltare gli effetti delle vernici in polvere su componenti in alluminio per porte, finestre, infissi e facciate continue. Include un’ampia gamma di colori con finitura liscia, raggrinzita e testurizzata, in base alle specifiche esigenze dei clienti.
La gamma ArchitecturalFlex rappresenta l’ultima novità proposta da Europolveri, una soluzione per il coil coating che risponde alle specifiche richieste di resistenza alla piega e applicazione a basso spessore.
La serie ArchitecturalLignum, composta da prodotti per sublimazione e polvere su polvere, offre al cliente la possibilità di riprodurre le calde finiture del legno anche su pannellature e profili in alluminio.
Per maggiori informazioni: www.europolveri.it
ESTAL ha analizzato la nuova Direttiva sulle Emissioni Industriali (IED), entrata in vigore lo scorso agosto, che introduce cambiamenti significativi nel campo del trattamento delle superfici dei metalli per ridurre le emissioni industriali.
ESTAL, l’Associazione Europea per il Trattamento delle Superfici in Alluminio, che mira a promuovere gli interessi dei suoi associati - oltre 400 aziende di anodizzazione e verniciatura in tutta Europaha analizzato la pubblicazione dell’ultima Direttiva Europea sulle emissioni industriali ((IED, Industrial Emissions Directive).
Questa nuova Direttiva è stata pubblicata sulla Gazzetta Ufficiale dell’Unione Europea il 15 luglio ed è entrata in vigore il 4 agosto 2024. Consiste in una serie di modifiche alla precedente Direttiva IED 2010/75/ UE, per la quale è ora disponibile un testo consolidato1
La revisione introduce diversi cambiamenti volti a ridurre le emissioni industriali, due dei quali sono molto importanti per ESTAL. In primo luogo, le autorità competenti sono ora tenute a stabilire i valori limite di emissione più rigorosi possibili utilizzando le Migliori Tecniche Disponibili (BAT, Best Available Techniques) dai Livelli di Emissione Associati alle BAT (BAT-AELS), mentre in passato si trattava solo di non superarli. In secondo luogo, quando i processi industriali sono omogenei in tutta l’UE, i permessi devono includere valori limite prestazionali quantitativi vincolanti per il consumo di acqua, la produzione di rifiuti, l’efficienza delle risorse e dell’energia, ove opportuno. Nel caso in cui i processi non siano
1 https://eur-lex.europa.eu/legal-content/EN/ALL/?uri=CELEX:02010L0075-20240804
omogenei, i nuovi Sistemi di Gestione Ambientale dovranno includere parametri di riferimento indicativi su questi aspetti.
Il Documento di Riferimento sulle Migliori Tecniche Disponibili per il Trattamento delle Superfici Metalliche e Plastiche (STM BREF), che stabilirà la base per il rilascio dei permessi per i membri delle Associazioni Nazionali coinvolte in ESTAL, sarà tra i primi ad essere pubblicato sotto la nuova Direttiva. Ciò significa che l’STM BREF, attualmente in fase di revisione, sarà implementato con questi requisiti, più severi rispetto a quelli dei precedenti BREF pubblicati sotto la Direttiva originale del 2010. Il Gruppo di Lavoro STM BREF di ESTAL è stato coinvolto nel processo di revisione, iniziato due anni fa.
Poiché il trattamento superficiale delle linee di anodizzazione in serie o delle linee di conversione chimica in serie è difficile da calcolare e i processi non sono omogenei, ESTAL ritiene non fattibile definire i requisiti quantitativi per l’efficienza delle risorse. Tuttavia, considera opportuno richiedere a ciascuna linea di conversione e anodizzazione di sviluppare un proprio piano di miglioramento, adattato alla situazione specifica, in modo che tutti gli impianti contribuiscano all’obiettivo di proteggere l’ambiente.
Per maggiori informazioni: www.estal.org
Sometimes it is what is on the outside that counts. Our zinc flake systems are suitable for all screws and bolts and hug every thread perfectly. Premium quality that protects against corrosion, sets defined coefficients of friction and withstands a range of mechanical stresses. However, we are not satisfied with the best and are constantly on the lookout for new solutions and innovations – for every problem, for every challenge.
High cathodic corrosion protection
Complex fastenings no problem
Cross-linking at low curing temperature
HIGHLIGHT OF THE MONTH
A cura di KARL BUBENHOFER AG
Gossau SG, Svizzera pulver@kabe-farben.ch
Nell’ambito dei suoi continui sforzi R&D, KABE-Farben ha recentemente introdotto POLYFLEX® PES-140-SD-NT: una serie completa di vernici in polvere a bassa temperatura di polimerizzazione e altamente resistenti alle intemperie, progettate per applicazioni architettoniche.
Da quasi 50 anni, KABE-Farben è sinonimo di qualità e innovazione tecnologica nel campo delle vernici in polvere. I rivestimenti certificati Qualicoat di KABE-Farben stabiliscono parametri di riferimento e riflettono la sua continua ricerca delle massime prestazioni.
Lavoro pionieristico nella polimerizzazione a bassa temperatura per applicazioni certificate su facciate
Quasi 15 anni fa, l’azienda ha raggiunto un traguardo significativo: ha infatti ridefinito gli standard del settore con il suo primo sistema di verniciatura a polvere a bassa temperatura di polimerizzazione per facciate, certificato secondo Qualicoat Classe 1. Il sistema POLYFLEX® PES-165-NT (numero di approvazione P-0937) continua a stupire con una straordinaria finestra di polimerizzazione, a partire da 10 minuti a 160 °C, e la sua capacità di cottura rapida a temperature più elevate. Questa innovazione sottolinea l’attenzione precoce dell’azienda per lo sviluppo in nuove aree tecnologiche, massimizzando sia la qualità che l’efficienza dei prodotti.
Sviluppo continuo per le massime esigenze
Negli ultimi anni, KABE-Farben ha continuato a investire nello sviluppo di vernici in polvere poliestere a bassa temperatura, specificamente per le facciate. La gamma è stata notevolmente ampliata con vari livelli di brillantezza e tipi di superficie con proprietà di polimerizzazione a bassa temperatura. Sono particolarmente degne di nota le versioni per substrati degassanti. Pertanto, l’azienda offre non solo soluzioni su misura per i complessi requisiti dei moderni progetti architettonici, ma anche funzionalità per un’elevata sicurezza applicativa in altri settori.
Stabilire nuovi standard Qualicoat Classe 2
Quest’anno, KABE-Farben presenta con orgoglio POLYFLEX® PES-140-SDNT, una serie completa di vernici in polvere a bassa temperatura altamente resistenti alle intemperie per applicazioni architettoniche (ma non solo), tutte certificate Qualicoat Classe 2. Rispetto alla qualità standard per le facciate, Qualicoat Classe 2 è caratterizzata da una maggiore resistenza ai raggi ultravioletti e alle intemperie, con conseguente maggiore durata e sostenibilità. La linea include prodotti adatti a molteplici superfici, tra cui finiture lisce con diversi livelli di brillantezza e finiture finemente strutturate. Le finestre di polimerizzazione partono da 10 minuti a una temperatura del substrato di 160 °C – un unicum del mercato. A temperature più elevate, queste vernici in polvere presentano inoltre tempi di polimerizzazione molto brevi.
Questi innovativi rivestimenti in polvere poliestere offrono non solo
un’eccellente resistenza ai raggi UV e alle intemperie, ma anche eccezionali proprietà di lavorazione, buona stabilità allo stoccaggio e caratteristiche superficiali superiori. L’azienda è particolarmente orgogliosa del suo esclusivo sistema liscio e opaco POLYFLEX®
PES-140-SD-NT-GU Corona Matt, con un livello di circa 10 unità di brillantezza (60°), certificato Classe 2. Questo innovativo e unico sistema offre non solo un’estetica eccezionale, ma può anche essere polimerizzato a 160 °C.
Per tutte le superfici menzionate, sono disponibili anche varianti effetto perlato con un’eccellente durata e che offrono ulteriori opzioni estetiche e migliorano l’impatto visivo di qualsiasi progetto.
Soluzioni di verniciatura a polvere orientate al futuro
KABE-Farben è sinonimo di progresso tecnologico e massima qualità nei rivestimenti in polvere. La sua continua forza innovativa e l’impegno per prodotti eccellenti la rendono il partner ideale per applicazioni architettoniche esigenti, ma non solo. Fidatevi dell’esperienza del suo team e lasciatevi ispirare dalle sue vernici in polvere a bassa temperatura e altamente resistenti alle intemperie, per risultati che stupiscono. L’azienda offre da molti anni anche un ampio portfolio a bassa temperatura per applicazioni interne.
Nella gamma di prodotti KABE-Farben è possibile trovare le seguenti vernici in polvere a bassa temperatura certificate Qualicoat:
Classe 1 – Qualità standard per facciate
- POLYFLEX® PES-165-NT smooth Corona silk gloss – Numero di approvazione P-0937
- POLYFLEX® PES-165-NT smooth Corona silk matt – Numero di approvazione P-1979
Classe 2 – Qualità per facciate altamente resistenti alle intemperie
- POLYFLEX® PES-140-SD-NT smooth Corona silk gloss – Numero di approvazione P-2079
- POLYFLEX® PES-140-SD-NT smooth Corona Satin matt – Numero di approvazione P-2078
- POLYFLEX® PES-140-SD-NT-GU smooth Corona matt – Numero di approvazione P-2053
- POLYFLEX® PES-140-SD-NT fine structure Corona silk matt/matt –Numero di approvazione P-2056.
La società di design DHK ha realizzato un nuovo impianto per il pretrattamento di componenti in alluminio dotato del sistema DRIZZLING di ALIT Technologies Spa, che atomizza una soluzione passivante preparata in tempo reale in base al rapporto di diluizione impostato tramite pannello di controllo.
L’azienda belga DHK produce e commercializza coperture per terrazze, pergole personalizzate, tettoie, davanzali e soglie in alluminio, oltre a fornire profili in alluminio, pannelli sandwich, profili in acciaio, PVC, policarbonato e un vasto portfolio di accessori per la realizzazione di strutture ad uso architettonico.
DHK è presente con i suoi punti vendita a Genk e a Chatelineau (Belgio) ed anche in Lussemburgo. Nel sito di Chatelineau l’azienda dispone di una nuova e moderna linea di verniciatura, dove viene effettuato il
pretrattamento e la verniciatura a polvere delle superfici metalliche che immette nel mercato. L’alluminio, in particolare, rappresenta il materiale per eccellenza che DHK propone sul mercato. Questo perché tale materiale offre una serie di vantaggi che lo rendono perfetto per l’architettura di strutture esterne non sottoposte a carichi pesanti. È leggero, assolutamente riciclabile, di facile lavorazione e con ottime caratteristiche di resistenza alla corrosione se opportunamente pretrattato.
Il pretrattamento delle superfici in alluminio
Pretrattare la superficie di alluminio significa effettuare su di essa una serie di trattamenti chimici che la trasformano e la rendono una base ideale per l’ancoraggio dello strato di vernice che sarà applicato su di essa. L’insieme dei trattamenti chimici effettuati, sommati alla vernice applicata sulla superficie, renderanno il manufatto finito assolutamente resistente alla corrosione atmosferica e quindi utilizzabile nel settore architettonico. Sia i trattamenti chimici che l’applicazione della vernice in polvere sono esattamente ciò che avviene nella moderna linea di pretrattamento e verniciatura di DHK. In questa linea, i manufatti in alluminio sono agganciati a un convogliatore aereo, passano attraverso un tunnel a spruzzo dove sono prima sgrassati e decapati, poi passivati ed infine trasferiti nella zona per l’applicazione della vernice.
“Inizialmente, i manufatti in alluminio sono sgrassati e decapati a spruzzo grazie all’effetto combinato del decapante acido ALFIDEOX 82/3 e dell’additivo sgrassante ALFISID 14. Nei settori successivi del tunnel, i materiali sono poi risciacquati con acqua di rete e successivamente con acqua demineralizzata. A questo punto, la superficie di alluminio è perfettamente priva di oli e grassi: è disossidata e quindi pronta e perfettamente reattiva per il successivo trattamento di passivazione, un passaggio fondamentale durante il quale dei promotori di adesione a base polimerica e degli inibitori di corrosione a base titanio sono ancorati chimicamente alla superficie. Il prodotto utilizzato in questo caso è ALFICOAT 748, una soluzione omologata QUALICOAT e GSB che ha superato i più rigidi test del settore, incluso il test di esposizione all’aperto per 10 anni. Questo prodotto è storicamente applicato a immersione o mediante spruzzo tradizionale, ma DHK impiega una tecnologia applicativa assolutamente innovativa ed efficace”, ha spiegato Ludwig Liesens, il responsabile della divisione Pretrattamento di Alufinish GmbH – l’azienda che fornisce i prodotti utilizzati in questa fase. L’ingresso
pannello di controllo del sistema DRIZZLING fornito da ALIT Technologies Spa e un ugello atomizzatore.
Il sistema DRIZZLING di ALIT Technologies Spa
Nell’impianto di pretrattamento è stata installato il sistema DRIZZLING, che permette di atomizzare sui manufatti in alluminio una soluzione di ALFICOAT 748 preparata in tempo reale, secondo un rapporto di diluizione programmabile a pannello. La tecnologia DRIZZLING miscela istantaneamente in linea il prodotto chimico e l’acqua demineralizzata, nebulizzando tale miscela per creare una nebbia che si deposita sulla superficie in alluminio, passivandola. “L’enorme vantaggio di DRIZZLING è che la soluzione chimica è sempre fresca, appena preparata e quindi estremamente reattiva e priva di contaminanti provenienti dai trascinamenti delle fasi precedenti. Grazie a DRIZZLING non serve più la tradizionale vasca di passivazione, e non servono più le pompe di spruzzatura ad alto consumo energetico. La soluzione è preparata all’istante e atomizzata sulla superficie, non è più necessario effettuare analisi chimiche sul liquido in vasca, proprio perché non esiste più la vasca. La semplificazione gestionale è insomma notevole, e gli spazi di installazione sono inferiori rispetto a quelli della tradizionale tecnologia a spruzzo”, ha aggiunto Liesens. “L’installazione è
stata velocissima: all’interno del tunnel sono state montate le due rampe, una contrapposta all’altra, mentre fuori dal tunnel è stato posato il quadro di miscelazione e comando. Il tutto è arrivato in configurazione plug and play, ed in poche ore il sistema era già pronto per essere utilizzato. I tecnici di ALIT Technologies hanno assistito il cliente durante la fase di avvio e nella formazione del personale preposto”.
Eccellente passivazione, con consumi ridotti “Sono presenti due rampe, per un totale di otto ugelli atomizzatori. Il flusso di soluzione è di circa 160 litri/ora con un consumo di prodotto chimico ALFICOAT 748 di circa 0.5Kg/ora. La qualità della passivazione è ottima: il deposito di titanio è regolarmente verificato e rientra perfettamente nei range prestabiliti dal fornitore Alufinish GmbH. Il connubio tra prodotto chimico di Alufinish GmbH e il sistema applicativo Drizzling di ALIT TECHNOLOGIES Spa è perfetto e sarà presto replicato in altri impianti di pretrattamento per l’alluminio. Ringrazio Thibaut Braibant e Jean-Marie Jenicot di DHK per la fiducia che ci hanno dimostrato”, ha concluso Liesens.
Alessia Venturi ipcm®
La vernice in polvere, con le sue evoluzioni a livello di effetti cromatici, decorativi, estetici, ad imitazione delle superfici naturali e con il miglioramento delle performance sia estetiche sia funzionali, rappresenta con sempre maggior frequenza la scelta preferita da architetti e progettisti per la finitura di elementi di architettura, come i cladding metallici. Ciò accade grazie allo spirito collaborativo e alla sperimentazione congiunta fra produttori di pannelli metallici e produttori di vernici in polvere. In questo articolo raccontiamo il sodalizio professionale fra Emboss Panels, specializzata nella produzione di pannelli metallici con effetto tridimensionale, e TIGER Coatings che le fornisce vernici in polvere ad effetto, opache e super opache, metallizzate e simil-anodizzate per impreziosire le superfici scolpite dei pannelli proposti dall’azienda veneta.
Il cladding è una sorta di pelle che protegge, decora ed esalta il materiale sottostante e le sue forme. Con il cladding si può accentuare la modernità di un edificio o di un interno; si può arginare, contenere e schermare la luce per creare effetti visivi; si può proteggere un’area o isolarla termicamente e acusticamente; infine, si può esaltare l’estetica e la bellezza, promuovere la sostenibilità e la durabilità nel tempo di una struttura o di un componente.
Grazie alla sua versatilità di forme, materiali (può essere realizzato in legno, metallo o compositi), e finiture, il cladding rappresenta uno degli strumenti più potenti nelle mani di architetti e progettisti per dare vita a strutture esclusive, distintive e con un’anima.
“Superfici scolpite per l’architettura”: questa è la definizione evocativa che Emboss, azienda di Tezze sul Brenta (Vicenza) nata nel 2018 e produttrice di pannelli decorativi per l’architettura e l’interior design, dà del proprio prodotto.
Emboss rappresenta l’unione di anime diverse che creno una soluzione ricercata ed esclusiva per il rivestimento di esterni ed interni: designer
e artigiani lavorano insieme per realizzare pannelli metallici con effetti decorativi di grande impatto. Emboss fornisce architetti, progettisti, installatori, distributori e utilizzatori finali che vogliono personalizzare i propri progetti con pannelli dall’aspetto esclusivo e attraente. Grazie a un processo di produzione innovativo che consente di deformare le lamiere metalliche, offre superfici tridimensionali con effetti vibranti e multiformi. “L’azienda nasce con una forte impronta tecnica” esordisce Cesare Zilio, ingegnere e fondatore di Emboss “dal momento che inizialmente era uno studio di progettazione specializzato nell’ambito del rivestimento metallico di facciata. Nel corso degli anni Emboss si è sempre più curata dell’aspetto produttivo delle lastre metalliche di rivestimento, sviluppando il concetto di lastre con effetto tridimensionale. La sperimentazione di varie tecniche di produzione ha portato l’azienda a definire un processo efficiente e innovativo di produzione di pannelli metallici 3D utilizzati per il rivestimento di facciata, il rivestimento di interni e di controsoffitti”.
Se l’attribuzione meccanica di effetti 3D attraverso la deformazione della lamiera già rende i pannelli metallici di Emboss una soluzione
estremamente attrattiva, unica ed esclusiva per il cladding architettonico, le vernici contribuiscono ad esaltare questi effetti.
“La finitura deve valorizzare quello che Emboss attribuisce in più alla semplice lastra metallica e deve essere quanto più possibile liscia, poiché la texture materica è già insita nella tridimensionalità che diamo al metallo” spiega Zilio. “Prediligiamo la verniciatura a polvere e in particolare abbiamo scelto di collaborare con uno dei leader di settore, -TIGER
Coatings -non solo per la qualità delle loro polveri ma anche per il servizio tecnico, l’assistenza del laboratorio per prove e validazioni, la disponibilità a sperimentare e a formulare prodotti con colori ed effetti personalizzati”.
“Le superfici scolpite di Emboss sono decorazioni create con una tecnica produttiva esclusiva: ogni modello è accuratamente disegnato e riprodotto meccanicamente con un sistema di deformazione plastica che combina artigianalità e industrializzazione. Questo processo di produzione offre numerose opportunità: è possibile lavorare lamiere metalliche solide, perforate o espanse in alluminio, acciaio zincato, acciaio
inox, ottone, rame e zinco titanio (una lega che, sotto l’azione degli agenti atmosferici, si ricopre superficialmente di un sottile strato autoprotettivo che dona un naturale invecchiamento e un gradevole aspetto estetico al materiale N.d.R.)” prosegue Zilio.
“Pur essendo giovani riusciamo a fornire un pannello finito, pronto per essere installato, non semplicemente stampato e verniciato ma - se necessario – anche piegato e intelaiato. La condizione ideale per l’impiego dei pannelli tridimensionali Emboss è che siano specificati dal progettista: concepire un progetto sin dall’inizio con questo tipo di rivestimento, consente di ottimizzare sia la resa estetica sia i costi di produzione in termini di divisione lastre, modulo della sottostruttura, finiture e così via”. Emboss propone diversi pattern standard ma anche la possibilità di personalizzare gli effetti per attribuire originalità ed esclusività ad ogni progetto.
“Abbiamo dei pattern a catalogo: Bumps presenta un effetto organico acqueo; Carapax, un effetto organico simile al precedente ma con una trama più fitta; Branch con un disegno di ramificazioni che propongono una logica della continuità della trama tra i vari pannelli di rivestimento,
Line un rigato lineare elegante; Quilt che presenta un effetto morbido, trapuntato, infine Sand che presenta un effetto a onde che ricorda le dune di sabbia. Un’altra cosa molto importante è il tema della customizzazione. Diamo la possibilità ai clienti di creare un disegno personalizzato è ciò valorizza molto la nostra offerta” sottolinea Cesare Zilio. “La forza di Emboss è quella di avere indagato delle tecnologie produttive snelle, per riuscire a proporre queste soluzioni su misura a costi interessanti e anche per piccoli lotti”. Tutti i pannelli Emboss possono essere realizzati con lamiera piena o forata e decorati con diverse tecnologie, dall’anodizzazione alla verniciatura a polvere o liquido, dall’elettro-colorazione alla lucidatura e satinatura.
Grazie a queste molteplici combinazioni di substrato, effetti, decorazioni e funzionalità del rivestimento, i pannelli Emboss rappresentano una soluzione decorativa molto versatile: possono essere usati sia per applicazioni di architettura esterna come rivestimenti di facciata e coperture, sia per gli interni, ad esempio per controsoffitti o rivestimenti murali. I pannelli di lamiera piena sono di norma utilizzati per coperture complete, mentre con quelli in lamiera forata o espansa si possono creare trasparenze e giochi di pieni e vuoti adatti per schermature solari e sistemi di ventilazione.
La verniciatura a polvere: un moltiplicatore di effetti decorativi
“Lavorare tutti i tipi di lastra metallica ci apre la possibilità di utilizzare svariate finiture superficiali per accentuare di volta in volta l’effetto tridimensionale desiderato nel contesto progettuale specifico. Spaziamo quindi dall’acciaio lucido all’acciaio satinato, dall’alluminio pre-anodizzato all’alluminio verniciato, che costituisce una grossa parte della nostra produzione. Per i prodotti Emboss la verniciatura costituisce una finitura molto flessibile e utile, perché ci consente di offrire al cliente un ventaglio di cromie, livelli di brillantezza, effetti speciali molto ampio. L’unico limite della finitura verniciata è che diminuisce la brillantezza della superficie metallica, perché con una superficie verniciata non è possibile mantenere l’effettospecchio – importante per alcuni dei pattern proposti. Tuttavia con la sperimentazione e il supporto tecnico di TIGER arriviamo a degli ottimi compromessi fra colore, effetto e brillantezza finale” spiega Cesare Zilio.
“Lavorando nel settore del metallo, conoscevo TIGER e la qualità della loro proposta di mercato ancora prima della nascita di Emboss nel 2018. La collaborazione in termini più legati all’utilizzo dei prodotti vernicianti TIGER e alla ricerca congiunta delle finiture migliori per i nostri pannelli 3D è iniziata circa due anni fa. Oggi la nostra partnership è esclusiva, sia per le finiture standard con colori RAL sia per le finiture ad effetto speciale, fra le quali ad esempio quelle della Serie 68 di TIGER Drylac® specifica per esterni, per noi
particolarmente interessante per l’effetto super opaco. Lavoriamo anche con la Serie 3DMetallics, tutti in classe 2 Superdurabile. Infine TIGER ci supporta anche nello sviluppo di finiture personalizzate ed esclusive, ad esempio con colori NCS, che – una volta approvate della committenza –sono poi prodotte in piccoli lotti. Emboss non è specialista delle polveri, al tempo stesso riceviamo richieste di finiture disparate, perché il prodotto in sé è già particolare quindi anche i requisiti di finitura lo sono”. “Per l’applicazione delle polveri sui pannelli per il cladding esterno e per facciate ci affidiamo alla competenza di Pintarelli Verniciature di Trento e ai loro cicli di pre-trattamento e verniciatura certificati, mentre per le applicazioni da interno ci appoggiamo anche ad altri fornitori. Emboss fornisce sempre ai terzisti il codice della polvere da utilizzare (colore e classe chimica), talvolta acquistiamo anche direttamente le polveri da TIGER”.
TIGER Drylac® Serie 68 e 3D Metallics
“I colori simil-anodizzati matte e flat matte della Serie 68 di TIGER Drylac® sono particolarmente valorizzanti per i prodotti Emboss perché mettono in risalto i giochi di luci e ombre che si creano con i nostri pattern tridimensionali” commenta Cesare Zilio. “Sottolineano la bombatura della lastra, accentuando la tridimensionalità dell’effetto. Inoltre, la formulazione superdurabile e altamente resistente agli agenti atmosferici le rende ideali per la finitura dei cladding destinati ad applicazioni in esterno”. La Series 68 di TIGER Drylac® fornisce numerose tonalità per finiture lisce con estetica opaca o super-opaca e la loro applicazione non è limitata all’alluminio, si possono applicare anche su acciaio e acciaio zincato. Offrono elevata costanza e omogeneità di colore fra i vari lotti, e sono superdurabili con certificazioni GSB e/o QUALICOAT con resistenze fino a 10 anni Florida. La Serie 68 3D Metallics di TIGER Drylac®, anch’essa
poliestere in qualità superdurabile GSB Florida 3 anni e/o QUALICOAT class 2, combina le prestazioni e l’applicazione in mano unica della Serie68 con la brillantezza e la profondità di effetto tipici delle vernici liquide metallizzate, trasformando ogni pannello in un elemento esclusivo.
La finitura a polvere: ineguagliabile per versatilità “Di recente abbiamo iniziato a valutare anche l’utilizzo di vernici liquide, in particolare di un trasparente pigmentato da applicare a all’alluminio pre-anodizzato con finitura a specchio” conclude Cesare Zilio. “Questo ci permetterebbe di conservare un’estetica lucida combinata con il colore, un effetto particolare non ottenibile con le polveri. Tuttavia i vantaggi dell’impiego delle vernici in polvere, quali il grado di personalizzazione, l’omogeneità, la ripetibilità della finitura e dei colori, la loro sostenibilità intrinseca e il processo applicativo a mano unica, restano ineguagliabili e rendono questa soluzione quella che preferiamo”.
© ipcm
The system with OptiSpray All-in-One pump technology and double OptiSpeeder powder hoppers (DualSpeeder) enables the handling and preparation of two independent colours one after the other for ultra-fast colour changes or in parallel for simultaneous coating from both OptiSpeeder powder hoppers.
In un’epoca caratterizzata da una crescente consapevolezza ambientale e da preoccupazioni per la sostenibilità, le industrie sono alla continua ricerca di metodi innovativi per ridurre la loro impronta di carbonio. Uno di questi progressi che ha guadagnato terreno è il passaggio alla passivazione esente cromo nel processo di pretrattamento per la verniciatura a polvere.
©
Figura 1 - EcoAl® 20 è una passivazione a base di titanio esente cromo che crea uno strato protettivo sulla superficie metallica, offrendo un’ottima resistenza alla corrosione e favorendo l’adesione.
©
Itrattamenti a base di cromo sono stati a lungo un punto fermo nel settore industriale per la passivazione delle superfici metalliche prima della verniciatura. I composti di cromo (VI), in particolare i cromati esavalenti, sono stati favoriti grazie alla loro resistenza alla corrosione e alle loro proprietà di promozione dell’adesione. Tuttavia, i rischi per l’ambiente e la salute associati al cromo esavalente hanno portato all’emanazione di normative rigorose e a una spinta collettiva per trovare alternative più sostenibili. In risposta ai limiti e ai rischi dei metodi tradizionali a base di cromo, la passivazione esente cromo è emersa come un’alternativa più sicura ed ecologicamente responsabile. L’obiettivo principale di questo approccio è garantire una finitura superficiale di alta qualità riducendo al minimo l’impatto ambientale.
Benefici della passivazione priva di cromo
Attenzione all’ambiente: la passivazione senza cromo riduce sostanzialmente il rilascio di sostanze tossiche nell’ambiente, contribuendo alla conservazione degli ecosistemi e riducendo al minimo l’inquinamento. Ciò è in linea con gli obiettivi generali delle pratiche industriali sostenibili.
Protezione della salute umana: l’eliminazione del cromo esavalente dal processo salvaguarda la salute dei lavoratori
coinvolti nei processi di trattamento e verniciatura, riducendo il rischio di malattie legate all’esposizione.
Conformità normativa: Il regolamento REACH inasprisce le normative sulle sostanze pericolose. Le alternative prive di cromo soddisfano tutti i requisiti REACH.
Efficienza delle risorse: i processi di passivazione senza cromo richiedono un consumo energetico inferiore e un minor numero di sostanze chimiche, con conseguente aumento dell'efficienza e riduzione dei costi operativi e dell'impronta di carbonio.
Prestazioni e qualità: contrariamente a quanto si pensa, la passivazione senza cromo non compromette la qualità della superficie trattata. Le alternative prive di cromo offrono proprietà di resistenza alla corrosione e di adesione comparabili, garantendo una finitura di alta qualità per la verniciatura a polvere.
Innovazione e reputazione: l’adozione di pratiche ecologiche come la passivazione senza cromo può migliorare la reputazione di un’azienda e promuovere l’innovazione. Le aziende che danno priorità alla sostenibilità hanno maggiori probabilità di attrarre clienti e partner attenti all’ambiente (Figura 1).
La passivazione esente cromo di Alsan: EcoAI®20 EcoAl® 20 è una passivazione esente cromo a base di titanio che combina composti di titanio e polimeri selezionati per creare uno strato protettivo sulla superficie del metallo con un’eccellente resistenza alla corrosione e promozione dell’adesione. EcoAl® 20 può essere applicato per immersione, a cascata o a spruzzo. Lo strato di conversione ottenuto con EcoAl® 20 consente di ottenere eccellenti risultati di adesione e resistenza alla corrosione con tutti i tipi di vernici e, in particolare, garantisce una grande protezione anticorrosiva filiforme. Con EcoAl® 20 è possibile ottenere rapidamente strati di conversione adeguati, solo con un breve tempo di contatto (circa 10-60 secondi), in base al metodo applicativo. La tecnologia EcoAl® 20 è facilmente adattabile a ogni linea di processo, includendo anche un sistema completamente automatizzato che garantisce il controllo di ogni parametro di lavoro. Nella figura 2 sono mostrati alcuni esempi di implementazione di EcoAl® 20. EcoAl® 20 è stato approvato per la prima volta da QUALICOAT nel 2003 (A-013). Da allora, è stato adottato con successo in tutto il mondo sia in linee orizzontali che verticali. Ecoal® 20 è il pretrattamento esente cromo approvato da Qualicoat, leader nei mercati spagnolo, marocchino e messicano. Si stima che, con la certificazione QUALICOAT, oltre 120.000.000 m2 di alluminio estruso sono trattati annualmente con EcoAl® 20 in tutto il mondo. EcoAl® 20 ha recentemente ottenuto il prestigioso riconoscimento della licenza
Turn key solutions for industrial wastewater treatment
Design and manufacturing of plants and chemicals for industrial wastewater treatment
Chemical-physical plants
Sludge treatment and compactor systems
Ion exchange demineralization systems and reverse osmosis systems
Oil separators
Filtering systems
Batch type systems
Flotation units
Chemicals and spare parts for water treatment
Technical service, support and maintenance of wastewater treatment plants
Beware of imitations, buy the original!
GSB International, che ne certifica la conformità ai severi standard di qualità GSB AL 631-2 per i prodotti chimici utilizzati nel pretrattamento dell’alluminio (Figura 3).
Conclusioni
L’adozione della passivazione senza cromo EcoAl® nella fase di pretrattamento previa verniciatura a polvere è un passo significativo verso l’eccellenza ecologica nel settore dell’alluminio. Rinunciando all’uso dei pericolosi composti di cromo esavalente, le aziende possono migliorare la loro gestione ambientale e contribuire alla diffusione di processi produttivi più puliti e sicuri. Il passaggio ad alternative prive di cromo è una testimonianza dello spirito innovativo delle industrie che cercano di bilanciare qualità, prestazioni e sostenibilità nelle loro attività. Nell’anno del 50° anniversario di Alsan, l’azienda riafferma più che mai il suo impegno per la sostenibilità e il rispetto dell’ambiente, pilastri essenziali per garantire il futuro del nostro pianeta e l’eredità delle
generazioni future. La sua dedizione alla qualità e all’eccellenza si riflette nel continuo sviluppo di prodotti, come EcoAl® 20, progettati per rispondere alle sfide ambientali più impegnative. Nel corso dei decenni, Alsan si è assunta in modo proattivo la responsabilità di creare soluzioni sostenibili che non solo soddisfano gli standard di qualità odierni, ma costituiscono anche un punto di riferimento per il futuro. Ogni miglioramento apportato ai suoi prodotti riflette la sua visione a lungo termine, incentrata sulla sostenibilità dell’industria dell’alluminio. Questo impegno è stato evidenziato dalla decisione strategica dell’azienda, quattro anni fa, di stabilire un proprio consulente tecnico e un magazzino in Polonia, migliorando la capacità di servire e rispondere al mercato europeo con agilità e competenza (Figura 4). Questo spostamento ha permesso di stringere legami più stretti con i clienti e i partner di Alsan, promuovendo pratiche che rispettano e valorizzano il nostro ambiente, garantendo così un’eredità duratura per le generazioni future.
Figura 3 - EcoAl® 20 è stata inizialmente approvata da QUALICOAT nel 2003 e ha recentemente ottenuto ulteriore riconoscimento, acquisendo la prestigiosa licenza da GSB International.
Figura 4 - Si stima che, con la certificazione QUALICOAT, oltre 120.000.000 m² di alluminio estruso vengano trattati con EcoAl® 20 ogni anno in tutto il mondo.
Klaus Vissing
Fraunhofer Institute for Manufacturing Technology and Advanced Materials IFAM – Brema, Germania klaus.vissing@ifam.fraunhofer.de
Il nuovo rivestimento UltraPLAS sviluppato dai ricercatori del Fraunhofer si è dimostrato una soluzione rivoluzionaria alle sfide dei processi di formatura primaria. Questo rivestimento avanzato e facile da pulire viene applicato come strato gradiente utilizzando un processo a plasma freddo ed è adatto a materiali come acciaio per utensili, acciaio inossidabile e alluminio. Le esclusive proprietà fisiche di UltraPLAS consentono uno stampaggio perfetto anche di superfici riflettenti su scala nanometrica. Riducendo il numero di fasi post-produzione e rinunciando agli agenti distaccanti, l’applicazione è classificata come molto economica.
Come si possono rivestire le superfici di utensili sofisticati e di alta qualità in modo tale da migliorarne la produzione e da ridurre o semplificare notevolmente i processi di pulizia? I ricercatori
del Fraunhofer Institute for Manufacturing Technology and Advanced Materials IFAM hanno indagato sulla questione insieme ai partner dei progetti “GlossyCast” e “UltraTrenn”, finanziati dall’Industrielle
Gemeinschaftsforschung IGF. Lo scopo dei progetti di ricerca era ridurre le forze di sformatura e la formazione di depositi, resistendo alle sollecitazioni specifiche della pressofusione di zinco ad alta pressione e dello stampaggio a iniezione delle materie plastiche. Nello specifico, lo stampaggio a iniezione di componenti tecnici in plastica richiede soluzioni per ridurre le forze di sformatura e la formazione di depositi. Questo vale per la produzione di componenti con superfici a elevata brillantezza o microstrutture altamente definite come lenti di plastica, motivi ornamentali o connettori con elevata accuratezza dimensionale. Similmente, nella pressofusione ad alta pressione di zinco, i depositi sulla superficie dello stampo, nonché i depositi di distaccanti e lubrificanti, inibiscono la produzione di colate di zinco lucide e di alta qualità. Ciò comporta considerevoli costi di post-lavorazione dei componenti. Indipendentemente da ciò, la sola applicazione dell’agente distaccante può rappresentare fino al 20% del tempo ciclo: se l’agente distaccante non fosse più necessario il risparmio potenziale sarebbe considerevole.
UltraPLAS conferisce al rivestimento proprietà eccezionali
Per soddisfare i requisiti sopracitati – ovvero superfici ottiche ultra-lisce (Ra < 25 nm) – il rivestimento deve essere liscio e privo di struttura. Per ottenere ciò è stato utilizzato il processo a plasma freddo, il cosiddetto processo PE-CVD (deposizione chimica da fase vapore potenziata al plasma). Formando uno strato gradiente, questo processo permette da un lato un’eccellente adesione dello strato al componente e dall’altro eccezionali proprietà antiaderenti e proprietà fisiche del prodotto. Il rivestimento realizzato in questo modo è caratterizzato, per esempio, da un elevato modulo di elasticità (28-32 GPa) e da elevata densità (1,5 g/cm³). Ciò si traduce in un intervallo di durezza Mohs di 5,5, come il vetro o lo smalto. Questo grazie ai ricercatori del Fraunhofer che sono riusciti a produrre il rivestimento UltraPLAS con uno spessore particolarmente sottile, inferiore a 100 nm. Ciò si è persino rivelato necessario nel progetto GlossyCast per fornire un buon effetto antiaderente. Inoltre, gli strati sottili e privi di struttura consentono di riprodurre perfettamente sia le strutture superficiali su scala nanometrica, ad esempio per il processo di nanoimpronta, sia le superfici lucide a specchio.
Qualità sostenibile e produzione economica garantite
Ampie prove pratiche effettuate presso varie aziende industriali hanno dimostrato che le forze di sformatura e la formazione di depositi sono state ridotte.
Foto di apertura: UltraPLAS consente una perfetta riproduzione di superfici a specchio. Utensile con rivestimento antiaderente (a sinistra) con elemento stampato a iniezione.
LOCAL ASSISTANCE SELF-LEARNING ROBOT
1 OPERATOR REQUIRED
È stato anche dimostrato che la riduzione delle forze di adesione riduce le forze di sformatura totali. Di conseguenza, la temperatura di sformatura può essere aumentata e la quantità di attrito ridotta. Contrariamente allo stato dell’arte, i rivestimenti possono essere rimossi sia efficacemente sia delicatamente utilizzando la tecnologia al plasma cosi da poter, se necessario, applicare un nuovo rivestimento numerose volte, senza alcuna perdita di qualità. Questo è particolarmente interessante per le superfici ad elevata brillantezza, poiché elimina la necessità di una lucidatura dispendiosa in termini di tempo o di lavorazioni meccaniche di altissima precisione. È stato anche dimostrato che la produzione diretta di superfici pressofuse in zinco di alta qualità utilizzando la tecnologia di pressofusione può aumentare in modo rilevante l’efficienza economica. Migliorando in modo significativo la qualità superficiale dei componenti pressofusi, le costose e dispendiose fasi di post-produzione come granigliatura, molatura e lucidatura posso essere semplificate o evitate. Lo sviluppo del rivestimento distaccante ultra-durevole UltraPLAS per le pressofusioni di zinco rappresenta un notevole progresso nel settore della fonderia. La possibilità di eliminare gli agenti distaccanti apre a un nuovo potenziale per migliorare la
qualità della pressofusione, riducendo i costi di produzione e rendendo il processo più ecologico. Poiché le pressofusioni sono prodotte senza agenti distaccanti, si riduce il tempo di pretrattamento per la galvanica e, di conseguenza, si riduce il consumo di materiali. I componenti prodotti hanno il grado di ruvidità desiderato. Grazie alla superficie più liscia, si può evitare il rivestimento galvanico di rame lucido, risparmiando così in materiali, tempo e acque reflue. Anche la riduzione del 50% dello spessore dello strato di rame (cianuro) e nichel lucido ha portato a ulteriori risparmi in materiali e tempo.
Informazioni sul processo di sviluppo
Lo sviluppo di UltraPLAS è stato preceduto dallo sviluppo del rivestimento antiaderente PLASLON, caratterizzato da elevata durezza (Mohs 4.5 - 5.5) e da eccellente resistenza al calore (fino a 230 °C). Queste proprietà hanno reso PLASLON un popolare rivestimento per pentole privo di PFAS semplice da pulire. Grazie all’innovazione continua e allo sviluppo di prodotti come UltraPLAS e PLASLON, Fraunhofer contribuisce in modo significativo al miglioramento dei processi produttivi e promuove la sostenibilità nell’industria.
I seguenti progetti sono stati finanziati dal Ministero Federale dell’Economia e della Protezione del Clima nell’ambito del programma per la promozione del finanziamento industriale congiunto (IGF) su decisione del Bundestag tedesco.
GlossyCast
• Riferimento finanziamento IGF 22003 N
• Innovazione nella pressofusione di zinco – Produzione di superfici pressofuse a specchio senza agenti distaccanti
• Durata: 01.02.2021 - 31.01.2024
• Partner del progetto: Fraunhofer Institute for Manufacturing Technology and Advanced Materials IFAM, fem Research Institute
UltraTrenn
• Riferimento finanziamento: IGF 22597 N
• Rivestimenti distaccanti ultrasottili con spessori inferiori a 100 nm per sformatura e post-lavorazione affidabili di componenti micro-stampati
• Durata: 01.10.2022 - 30.09.2024
• Partner del progetto: Fraunhofer Institute for Manufacturing Technology and Advanced Materials IFAM, University of Paderborn.
CHEMTEC’S technologies are designed to have a very limited environmental impact, to reduce consumption of resources and for a greater operational simplicity.
CHEMTEC develops customized solutions that aim to maximize the customer’s satisfaction.
NANOTECHNOLOGICAL CONVERSION COATING
WATER PURIFICATION AND RECIRCULATION
ONE STEP METAL PRETREATMENT
PAINT STRIPPERS
DISCOVER MORE ON WWW.CHEMTEC.IT
Monica Fumagalli ipcm®
Azeta Srl di Muro Leccese, nel Salento pugliese, è stata una delle prime aziende del territorio a specializzarsi nella lavorazione e nel trattamento superficiale dell’alluminio e la prima a brevettare, negli anni Novanta, il rivestimento effetto legno applicato con ciclo liquido su polvere su questo materiale. E’ anche la prima realtà in Italia nel settore dell’alluminio ad avere recentemente installato un impianto automatico in verticale di Euroimpianti per la verniciatura a polveri dei profili abbinato all’ultimo dispositivo per l’alimentazione e il controllo delle polveri di Wagner, il sistema IPS, con l’obiettivo di aumentare la propria capacità produttiva e ridistribuire la manodopera in modo più efficace.
In Italia la prima testimonianza dell’utilizzo dell’alluminio in edilizia risale al 1897, quando l’architetto Raffaele Ingami costruì la cupola della chiesa romana di San Gioacchino ai Prati di Castello inserendo per la prima volta questo materiale per il suo rivestimento.
Il Gruppo Ruggeri è specializzato nella fusione, estrusione e verniciatura dei profilati in alluminio, in particolare per il settore serramentistico.
Mancano solo pochissimi anni all’inizio del XX secolo, che sarà poi definito “il secolo dell’alluminio”, per l’importanza crescente che questo metallo avrà nelle più svariate applicazioni, grazie alle sue caratteristiche di leggerezza, duttilità, lucentezza e resistenza alla corrosione e, in anni più recenti, alla possibilità del suo riciclo totale. Nell’arco di pochi decenni l’alluminio passò infatti dall’uso esclusivo legato alla produzione orafa a un utilizzo ampiamente diffuso sia in edilizia, per la copertura degli edifici, sia nell’industria metallurgica bellica al servizio del primo conflitto mondiale e nella nascente industria aereonautica: dal 1908 la struttura rigida dei dirigibili Zeppelin era costruita in questo materiale, così come alcune parti dell’aereo Spirit of St. Louis di Charles Lindbergh che compì il primo volo transatlantico nel 19271
Proprio dallo sviluppo di queste soluzioni innovative per i settori aereonautico, prima, e automobilistico, poi, i progettisti presero spunto e ispirazione per utilizzare l’alluminio anche in architettura; un impiego già ampiamente diffuso oltreoceano dove i grattacieli e le case unifamiliari americani - dal Chrysler Building alla sperimentale Aluminaire House, la prima casa costruita totalmente in metallo - diventarono modelli di riferimento anche per l’edilizia italiana, in cui l’alluminio entra finalmente a pieno titolo negli anni Cinquanta. Solo negli anni Settanta però, a seguito della crisi energetica e alla maggiore richiesta di isolamento termico delle abitazioni, l’alluminio inizia a diffondersi nel mondo della serramentistica - in precedenza ad appannaggio esclusivo del legno - diventando elemento costitutivo della controfinestra, una seconda intelaiatura aggiunta per migliorare l’isolamento termico del serramento in legno già installato. Grazie al rapido sviluppo tecnologico del settore, iniziarono presto a diffondersi anche particolari trattamenti superficiali in grado di conferire al profilo in alluminio maggiore resistenza agli agenti atmosferici ed effetti estetici accattivanti, come l’anodizzazione, la verniciatura a polvere e la decorazione per sublimazione. “Con la mia attività sono stato tra i primi imprenditori a introdurre i profilati di alluminio nel Sud Italia proprio negli anni in cui le qualità di questo materiale iniziavano ad essere riconosciute anche nel settore dei serramenti” – ci racconta gli albori di Azeta Srl Salvatore Ruggeri, suo fondatore e attuale presidente del gruppo che da qui ha preso avvio, oltre che volto noto non solo dell’imprenditoria, ma anche della politica italiana per il suo passato da parlamentare. “Ci siamo quindi specializzati nella lavorazione e nel trattamento superficiale dell’alluminio, tanto che nel 1995 abbiamo installato il primo
1 https://dsdra.web.uniroma1.it/sites/default/files/Materiali%20e%20 strutture%2012.pdf
Da sinistra a destra:
Ciascuna cabina
è attrezzata con 4 reciprocatori contrapposti.
Il trasportatore monorotaia in primo piano e, sullo sfondo, il forno di asciugatura e polimerizzazione.
L’impianto per la pulizia dei ganci senza l’utilizzo di prodotti chimici.
impianto di verniciatura in grado di applicare rivestimenti effetto legno con un ciclo liquido su polvere da noi brevettato: oggi siamo uno degli hub dell’alluminio del Sud Italia più conosciuti e premiati a livello nazionale. Per quanto riguarda il trattamento superficiale degli estrusi, lavoriamo con un impianto di verniciatura orizzontale, ma, spinti dalla necessità di implementare e automatizzare il più possibile la produzione, abbiamo recentemente deciso di sperimentare una nuova tipologia di impianto, un modello per la verniciatura a polvere in verticale dei profili, progettato e installato alla fine del 2023 da Euroimpianti di Valeggio sul Mincio (Verona), combinato con il sistema di ultima generazione per l’alimentazione e gestione delle polveri di Wagner, la centrale IPS”.
Il Gruppo Ruggeri: la filiera completa dell’alluminio Nato agli inizi degli anni Settanta per l’iniziativa imprenditoriale del suo attuale presidente, il Gruppo Ruggeri, che da lui prende il nome, è attualmente una realtà consolidata costituita da 4 aziende, ciascuna specializzata in una fase di lavorazione cruciale della filiera degli estrusi. “Quando ricordo il periodo in cui ho avviato la mia attività – racconta Ruggeri – non posso negare che le difficoltà sono state tante, ma i successi e le soddisfazioni le hanno presto superate: ho iniziato vendendo sagomati in ferro e, quando i primi profili in alluminio con effetti particolari hanno cominciato a circolare, me ne sono interessato, comprendendo da subito il notevole potenziale di questo materiale. Nel 1975, con altri due soci, abbiamo fondato la società Azeta Metalli Sas, lanciando il profilo in alluminio verniciato, che non esisteva sul mercato del tempo e riscontrando un sempre maggiore successo: abbiamo così brevettato Woodall, il primo processo di applicazione liquido su polvere per ottenere
l’effetto legno su alluminio, poi diffusosi anche nel Nord Italia con la diversa applicazione di polvere su polvere. Nel 1999 iniziammo a riscontrare la necessità di produrre da soli i profilati, creando un nuovo stabilimento di estrusione e implementando contemporaneamente l’attività di verniciatura grazie alla costruzione di un ulteriore nuovo capannone. In questo periodo i volumi di produzione raggiungevano ormai le 500 t/mese ed erano in continuo aumento; nel 2006 abbiamo infine aperto la nostra fonderia, completando in questo modo la filiera dell’alluminio”. Oggi il Gruppo Ruggeri, che offre lavoro a oltre 170 persone, è quindi costituito da: Ruggeri Service Spa, la fonderia che produce billette da estrusione; TO.MA. Spa, specializzata nell’estrusione dell’alluminio, realizza estrusi per serramenti, l’architettura in generale e l’industria; Azeta Color Srl propone centinaia di soluzioni per la finitura dell’alluminio sia a liquido sia a polvere, dai colori RAL alla verniciatura ad effetto legno con i processi Woodall, già citato, Lignall, PAZ (polvere su polvere) e di sublimazione; e, infine, Azeta Metalli SAS, che commercializza e distribuisce i profilati e le lamiere in alluminio, gli accessori per serramenti e le macchine e le attrezzature per la lavorazione dell’alluminio. “Le aziende del Gruppo Ruggeri rappresentano pertanto la filiera completa della trasformazione, lavorazione e commercializzazione degli estrusi in alluminio – conferma Ruggeri - rispettando i più elevati standard qualitativi di prodotto e nel pieno rispetto del territorio e dell’ambiente, basti pensare che siamo attualmente in grado di produrre billette su richiesta in lega 6060 aventi un contenuto di materiale recuperato pari all’87% e questo ci permette di porci in classe A per contenuto di riciclato/recuperato, secondo i parametri della certificazione REMADE2”.
2 https://www.remadeinitaly.it/
Woodall: il primo effetto legno su alluminio
Probabilmente a causa della lunga tradizione serramentistica legata alla lavorazione e alla verniciatura del legno, l’alluminio ha tardato ad essere riconosciuto in Italia come valida alternativa agli elementi costruiti con questo materiale naturale. E, forse proprio per questa ragione, è alla base del successo di Woodall, il processo brevettato nel 1995 con cui Azeta ha avuto l’intuizione di mutuare le caratteristiche di resistenza e durata del metallo con la resa estetica calda e naturale del legno, che si abbina bene a diversi stili architettonici, specialmente nelle abitazioni dove il legno è un elemento centrale.
“Ulteriori vantaggi dell’elemento in alluminio verniciato rispetto al legno – sottolinea Ruggeri –sono: la manutenzione inferiore richiesta grazie alle sue performance di resistenza anticorrosiva; l’isolamento termico migliorato ottenuto grazie a tecniche, come il taglio termico, che migliora l’isolamento ed evita le dispersioni di calore; la leggerezza che facilita l’installazione e riduce il carico complessivo sulle strutture architettoniche e - ultimo ma non meno importante - il rispetto dell’ambiente, essendo l’alluminio riciclabile al 100%”.
Il primo impianto di verniciatura dei profili verticale
La continua crescita produttiva e le nuove esigenze del mercato hanno convinto il management del Gruppo Ruggeri ad avviare un progetto di implementazione che ha coinvolto la fonderia, la cui superficie verrà raddoppiata, il reparto di verniciatura con l’integrazione del nuovo impianto di verniciatura verticale dei profili, e la divisione imballaggio. La conclusione dei lavori è prevista tra gennaio e febbraio 2026.
“L’impianto studiato e installato da Euroimpianti – precisa Fabrizio Ruggeri, il figlio di Salvatore che sta affiancando il padre alla guida dell’azienda – è il primo integrato in stabilimento per la verniciatura verticale dei profili. Abbiamo sempre lavorato con impianti di verniciatura orizzontali, ma questo sistema verticale ha mostrato da subito notevoli vantaggi rispetto agli altri. Prima di confermare la scelta dell’azienda veneta come fornitrice di questa tecnologia, abbiamo valutato altre opzioni, ma la soluzione di Euroimpianti ci ha convinto principalmente per le elevate performance di automazione che ci consentono di ridistribuire in altri reparti la manodopera prima assegnata all’impianto e per l’aumentata capacità dei volumi verniciati, corrispondenti a circa 15 t/giorno, che ci permettono – finalmente – di rispondere alle esigenze di un mercato che richiede quantità sempre più elevate. Un ulteriore vantaggio della verniciatura in verticale è legato
al posizionamento dei profili più pesanti che, stazionando in verticale, non presentano il rischio di curvatura, come invece può verificarsi nell’impianto orizzontale: questo ci consente una notevole riduzione degli scarti”.
Principali caratteristiche dell’impianto di verniciatura
“Ogni impianto studiato da Euroimpianti” – spiega Gianluca Baruffaldi, CEO del Gruppo Euroimpianti – “è configurato e personalizzato in base alla quantità di profili di alluminio da verniciare e alle esigenze particolari del flusso dei materiali all’interno del processo produttivo. L’impianto installato in Azeta rappresenta lo stato dell’arte della tecnologia impiantistica, estremamente affidabile e dall’elevata capacità produttiva, oggetto di uno studio ad hoc in termini di risparmio energetico e termico. Si compone di un tunnel di pretrattamento a 10 stadi. Ogni dettaglio del tunnel - lunghezza degli stadi, vasche e interassi - è progettato secondo i dettami richiesti dai cicli di trattamento chimico Qualicoat e AAMA. L’ultimo stadio di passivazione è dotato del sistema Nebula, che garantisce che il pezzo da trattare sia nebulizzato con una soluzione dalle qualità chimiche costanti e con ridotto consumo di acqua. Il dispositivo è dotato di un sistema di dosaggio, miscelazione e controllo del prodotto chimico, di un sistema operativo con pannello di comando touch-screen e di rampe con ugelli atomizzatori. Dopo il pretrattamento, i profili sono condotti dal trasportatore monorotaia nel forno di asciugatura studiato in modo tale che sia possibile recuperare il calore dai pezzi in fase di raffreddamento”.
Una cabina a forma di diamante
Le due cabine di verniciatura appartengono alla serie Diamond, il cui nome si ispira alla forma di diamante della struttura. “Ciò che contraddistingue questa cabina di applicazione”, interviene Antonio Cimenes, agente di vendita dell’azienda veneta, “è senza dubbio la sua geometria: grazie alla perfetta simmetria dei componenti di cui è composta, si possono verniciare profili di qualsiasi forma e sezione con le massime prestazioni: è infatti composta da una struttura di metallo verniciata a polvere che funge da supporto e contenimento per una serie di teli dielettrici simmetricamente contrapposti. 4 reciprocatori per lato, speciali corpi pistola angolari e un percorso lineare del trasportatore durante la fase di verniciatura garantiscono flessibilità e controllo dei parametri di applicazione. I teli laterali che delimitano l’area applicativa presentano una movimentazione rotatoria comandata dal software che favorisce il recupero della polvere e agevola e velocizza le
operazioni di cambio colore. La pulizia all’interno della cabina avviene in modo completamente automatico grazie al sistema di aspirazione e recupero polveri composto da un ciclone separatore ad alta efficienza e da un filtro autopulente dotato di cartucce che intercetta la polvere non separata dal ciclone. Anche il pavimento è composto da un telo dielettrico rotante a pulizia automatica. Infine, la linea è attrezzata con un dispositivo che permette la pulizia dei ganci senza l’utilizzo di prodotti chimici”.
Tra i principali fornitori di polveri a cui Azeta si rivolge vi è Pulverit Spa, la cui storia ha preso avvio nello stesso periodo della società leccese.
Impianto verticale e sistema di gestione polveri IPS: il binomio vincente
“Questo è il primo impianto di verniciatura verticale che adotta l’innovativo sistema IPS di Wagner per la gestione della polvere nel settore italiano dell’alluminio”, precisa Michele De Cesaris, Area Manager Powder Coating di Wagner. “Abbiamo però fornito ad Azeta anche la nostra classica centrale polveri SuperCenter EVO, la prima studiata per essere in linea con i parametri Industry 4.0 e già rodata con innumerevoli impianti di verniciatura verticale: il Supercenter EVO e la centrale IPS lavorano perfettamente con ciascuna delle 2 cabine”. Sono stati invece rilevati i notevoli vantaggi che questo binomio comporta: “Il centro polveri IPS consente infatti di incrementare la produttività, mantenere standard qualitativi elevati, operare in modo semplice e diminuire costantemente i tempi di cambio colore. Il sistema di feeding della polvere è rivoluzionario, in quanto parte dal concetto di lavorare con il contenitore in pressione, senza utilizzo di pompe (Venturi o pinch), rispondendo appieno
© ipcm
L’impianto chimico-fisico per il trattamento delle acque reflue di pretrattamento.
consente la preparazione della stessa mediante setaccio a ultrasuoni, vibrazione e fluidizzazione, oltre a presentare particolari accorgimenti tecnici per il dosaggio preciso delle pistole. I sensori integrati di peso, portata, pressione e livello, nonché il cambio colore completamente automatico consentono un’elevata produttività ed efficienza economica, in quanto l’applicazione è costante nel tempo - oltre le 2.000 ore senza aggiustamenti dei parametri applicativi e quindi senza manutenzione ordinaria”. Grazie a questo nuovo centro polvere, Azeta può infatti gestire meglio il consumo di vernice e il layout del ventaglio di spruzzatura, migliorando le performance del rivestimento, che è l’aspetto che più interessa la società pugliese. “IPS presenta inoltre il massimo livello di automazione del cambio colore che non richiede presidio umano, con un controllo centralizzato di tutte le fasi del processo e la rilevazione dei consumi della polvere in tempo reale”.
L’impianto chimico-fisico per il trattamento delle acque reflue
La linea è inoltre dotata di un impianto di trattamento per le acque reflue del tunnel di pretrattamento sviluppato da Saita Srl di Limena (Padova). “Il sistema di trattamento acque che abbiamo installato presso Azeta –interviene Carlo Enrico Martini, Sales Manager di Saita - è un impianto tradizionale di tipo chimico-fisico con capacità pari a 2.000 l/ora, in cui le acque diluite scaricate dagli stadi di lavaggio sono trattate in continuo, mentre i reflui concentrati sono stoccati in un serbatoio di bilanciamento e dosati nello stesso impianto di depurazione. L’acqua demineralizzata viene prodotta e recuperata a circuito chiuso nelle vasche del tunnel di
lavaggio da un demineralizzatore con resine a scambio ionico in doppia linea con capacità di 10.000 l/ora”.
Conclusioni
“Grazie a questa nuova linea di verniciatura avremo la possibilità di consolidarci come gammisti e di diventare sempre più protagonisti nel settore dei profili in alluminio verniciati, aumentando la nostra capacità produttiva e la qualità finale del rivestimento” – conclude Salvatore Ruggeri. “Anche se l’investimento è stato importante è il risultato quello che conta: restiamo soddisfatti dei partner che abbiamo scelto, perché i team di Euroimpianti e Wagner hanno dimostrato non solo competenza, ma anche una notevole capacità di adattarsi alle nostre esigenze e di venirci incontro, anche quando non era scontato lo facessero, come nel caso della doppia centrale che Wagner ci ha fornito per evitare che potessero insorgere problematiche di produzione con un sistema mai testato prima con questa tecnologia di verniciatura in verticale. Oggi abbiamo triplicato la nostra capacità produttiva, riducendo il numero di turni e ricollocando i nostri collaboratori in altre aree dello stabilimento con mansioni diverse”. In questo modo Azeta confermerà il proprio ruolo strategico nel settore dei rivestimenti per l’alluminio: “L’effetto legno ha ormai un proprio vasto mercato di rilievo: attualmente stiamo sviluppando un rivestimento con lo stesso effetto anche su PVC. Siamo alla continua ricerca di soluzioni per soddisfare la richiesta di profilati dagli effetti più particolari: la nostra storia è partita da lì e continueremo a perseguire questa strada perché siamo convinti che anche il futuro di Azeta si baserà su questo approccio pionieristico”.
HIGHLIGHT OF THE MONTH
Enrico Dall’Igna
ST Powder Coatings S.p.A. - Montecchio Maggiore (VI) enrico.dalligna@stpowdercoatings.com
Con l’obiettivo di promuovere la sostenibilità, St Powder Coatings ha lanciato Green Oasis: la nuova gamma di vernici in polvere è formulata con resine poliesteri contenenti una combinazione di materie prime riciclate e/o con una parte dei componenti derivanti da fonti rinnovabili.
Il numero di consumatori e di aziende che attribuiscono una grande importanza alla compatibilità ambientale è sempre in costante aumento. Di conseguenza, per i loro progetti molti scelgono le vernici in polvere, perché queste soluzioni che non generano emissioni sono considerate ecologiche. Tuttavia, ciò non è propriamente esatto: le vernici in polvere convenzionali sono composte per oltre il 50% da resine ottenute da petrolio e gas naturale derivante da giacimenti sotterranei. È proprio per questo che ST Powder Coatings si propone di selezionare costantemente opzioni di prodotto e manifatturiere utili a ridurre
l’impatto negativo sull’ambiente. Il nostro tempo richiede infatti soluzioni innovative per garantire la vivibilità del pianeta e preservarlo per le generazioni future.
L’obiettivo deve essere quello di ridurre al minimo le emissioni nocive per l’ambiente, senza però compromettere la qualità, la competitività e gli standard del prodotto finito. L’azienda si chiede dunque: può ottimizzare i processi produttivi e ridurre l’impatto ambientale, mantenendo o migliorando la qualità e riducendo allo stesso tempo la propria impronta di carbonio?
La nuova serie di vernici in polvere
Green Oasis
Il laboratorio di ricerca e sviluppo di ST Powder Coatings si è sempre concentrato su innovazioni tecniche che non sono solamente belle da vedere, ma che portano benefici alle persone e all’ambiente, offrendo un valore aggiunto. Questi sforzi hanno portato alla creazione di una prima serie di vernici in polvere con materie prime con componenti derivanti da fonti rinnovabili già nel 2012 – una novità assoluta all’epoca. Sulla base dell’esperienza acquisita, l’azienda è oggi in grado di presentare la nuova serie di vernici in polvere Green Oasis, disponibile in tre configurazioni, di cui 2, la serie R e PLUS saranno presto disponibili sul mercato:
SERIE P: a base di resine poliesteri contenenti materiali riciclati;
SERIE R: a base di resine poliesteri con parte dei componenti derivanti da fonti rinnovabili;
SERIE PLUS: a base di resine poliesteri contenenti una combinazione di materie prime riciclate e con una parte dei componenti derivanti da fonti rinnovabili.
Alcune varianti di queste vernici in polvere sono disponibili a bassa temperatura di polimerizzazione, per ridurre ulteriormente l‘impatto ambientale diminuendo il consumo energetico.
Green Oasis SERIE P
La serie P Green Oasis utilizza nel suo ciclo produttivo componenti a base di PET riciclato. Il PET riciclato (rPET o poliestere riciclato) è un materiale ottenuto
dal riciclaggio di materiali di scarto. Proviene per lo più dal riciclaggio delle bottiglie in PET e, in misura minore, dai rifiuti industriali di poliestere o di abbigliamento.
Nell‘ottica di un’economia circolare realmente funzionante, ST Powder Coatings ha sviluppato un processo solido ed affidabile per la produzione di vernici in polvere a partire da questo polimero riciclato, mantenendone inalterata l’altissima qualità che le contraddistingue.
Green Oasis SERIE R
La serie R Green Oasis utilizza innovative resine poliesteri sintetizzate non solo con gas tradizionale da giacimento ma, soprattutto, con biogas ecologico: ciò significa che le fonti della materia prima essenziale per la produzione delle vernici in polvere possono essere rifiuti alimentari, agricoli e forestali. In questo modo si trasformano gli scarti in una materia prima di alta qualità. Alta qualità che può essere ritrovata inalterata nella nuova gamma di vernici in polvere.
Green Oasis SERIE PLUS
La serie PLUS Green Oasis combina in un‘unica soluzione i vantaggi delle serie R e P. La serie PLUS porta ai valori massimi il tenore di materie prime derivanti da fonti rinnovabili e da riciclo, offrendo il miglior contributo in termini di riduzione dell‘impronta ecologica.
SPECIAL ISSUE ON METAL ARCHITECTURE AND DESIGN
A cura di Kenosistec Srl
Casarile (MI), Italia antonio.angolemme@kenosistec.it
La tecnologia PVD si posiziona al centro della scena nel mondo delle finiture per il settore del design con le sue eccezionali proprietà estetiche, funzionali e sostenibili. Attraverso la capacità di personalizzare gli impianti e soddisfare le esigenze specifiche dei clienti, Kenosistec offre ai designer l’opportunità di creare prodotti distintivi, duraturi e rispettosi dell’ambiente.
Il Physical Vapor Deposition (PVD) è una tecnica di ingegneria superficiale biocompatibile che consente di depositare sottili strati di materiale su diversi supporti come metallo e leghe, plastica, vetro, ceramica, polimeri e materiali per semiconduttori. Il PVD forma un rivestimento con proprietà specifiche che migliorano sia l’estetica sia le proprietà funzionali dei prodotti: questa tecnica di vaporizzazione permette infatti di ottenere rivestimenti resistenti all’abrasione e agli shock termici, garantendo quindi una lunga durata. Nel settore del design, dove estetica e funzionalità devono andare di pari passo, il PVD si distingue dunque come una risorsa fondamentale
– che offre possibilità creative quasi illimitate. Grazie alla sua versatilità, questa tecnologia trova infatti molteplici applicazioni: dalla rubinetteria agli accessori d’arredo, dalla gioielleria e posateria all’orologeria, fino al packaging.
Kenosistec Srl ha sviluppato soluzioni avanzate per soddisfare le esigenze del mercato del design, contribuendo all’adozione sempre più diffusa del PVD. “Il Physical Vapor Deposition in questo settore apre nuove possibilità per creare opere personalizzate, con la possibilità di ottenere varie finiture e colori. Si tratta di un processo di rivestimento particolarmente apprezzato per la sua versatilità: le finiture PVD possono essere
depositate su una vasta gamma di substrati differenti, a differenza di altri metodi di deposizione. Questo lo rende una scelta ottimale per coloro che cercano versatilità, qualità e precisione”, spiega Antonio Angolemme, Head of Sales di Kenosistec.
I vantaggi del PVD per la qualità della finitura
Una delle ragioni principali per l’uso crescente del PVD nel settore del design è l’eccezionale qualità della finitura che permette di ottenere. I rivestimenti PVD sono infatti resistenti ai graffi, all’usura e alla corrosione, rendendo i prodotti durevoli anche in ambienti applicativi come quelli della rubinetteria, dove il contatto con acqua e sostanze chimiche può causare deterioramento. Inoltre, questa tecnica di rivestimento consente di utilizzare una vasta gamma di colori, permettendo così ai designer e agli architetti di seguire i trend di mercato.
“Finiture come oro, bronzo, nero e cioccolato sono attualmente molto popolari nel settore dell’arredo, ma le possibilità cromatiche sono pressoché infinite. Ciò rende il PVD una scelta privilegiata per soluzioni distintive e personalizzate. Grazie a questa tecnologia è infatti possibile anche effettuare produzioni con colori progettati ad-hoc, ideali per oggetti dal carattere esclusivo”, aggiunge Angolemme. “Le finiture ottenute con il PVD sono brillanti e uniformi e conferiscono ai prodotti un aspetto raffinato e di alta qualità”.
Una soluzione ecosostenibile
Oltre ai benefici estetici e funzionali, il PVD si distingue anche per il suo ridotto impatto ambientale.
A differenza di altri processi di rivestimento che possono generare scarti tossici o richiedere l’uso di prodotti chimici inquinanti, questo processo è considerato ‘green’ e pulito poiché non utilizza solventi, non rilascia sostanza nocive al termine del ciclo e consente di depositare anche a basse temperature, contribuendo a ridurre il consumo energetico e le emissioni di gas serra. Grazie al controllo preciso dello spessore, permette anche di minimizzare il consumo dei materiali di rivestimento, contribuendo a una maggiore efficienza produttiva.
Grazie alla lunga durata dei rivestimenti PVD, i prodotti finiti con questa tecnologia necessitano infine di meno sostituzioni, riducendo così i rifiuti
e il consumo di risorse nel tempo. Questo approccio sostenibile è conforme alle normative europee REACH e RoHS, rendendo il PVD una scelta sicura e responsabile per le aziende che vogliono ridurre il loro impatto ambientale.
Kenosistec: innovazione e leadership nella tecnologia PVD Fondata nel 2005, Kenosistec è diventata un leader nel panorama tecnologico italiano, specializzandosi nella produzione di sistemi PVD personalizzati. Parte del Gruppo Angelantoni Industrie, l’azienda ha consolidato la sua posizione grazie alla sua capacità di offrire soluzioni su misura per settori che spaziano dall’occhialeria, all’automotive, fino ai materiali per l’architettura e gli accessori per l’arredamento.
THE
BECOMES
We supply you with individualized
“È proprio nel settore del design e dell’arredo che Kenosistec gioca un ruolo chiave, grazie alla versatilità del PVD, che è ampiamente utilizzato anche nella produzione di maniglie, piedini di mobili, lavelli, miscelatori, elettrodomestici, rubinetti, docce, accessori come porta-salviette e sistemi di illuminazione”, afferma Angolemme. “Le nostre innovazioni tecnologiche Hi.P.Po. e CHROME+ guidano questa evoluzione, offrendo soluzioni che non solo soddisfano le esigenze attuali del mercato, ma che sono anche pronte a rispondere alle sfide future”.
Il contributo della tecnologia Hi.P.Po
Una delle innovazioni più significative di Kenosistec a supporto del settore è la tecnologia Hi.P.Po. (High Productive Powered Sputtering Cathode), una sorgente di sputtering di nuova generazione progettata per la produzione su larga scala. Rispetto ai catodi planari tradizionali, Hi.P.Po. offre un tasso di deposizione superiore di 10 volte, una maggiore uniformità delle finiture e un consumo energetico ridotto di oltre un terzo. La tecnologia consente inoltre di depositare materiali come nitruri e carburi, offrendo una vasta gamma di colori e finiture – rispondendo così alle esigenze del design moderno.
CHROME+: la cromatura su plastica
CHROME+ è un altro esempio dell’innovazione di Kenosistec. Questa tecnologia bi-strato brevettata, unica nel suo genere, permette la cromatura su plastica senza l’uso di processi galvanici. Offre finiture lucide e satinate che soddisfano i rigorosi standard del settore automotive e possono essere applicate anche in ambiti come gli elettrodomestici e gli accessori d’arredo.
Lo stabilimento di Casarile:
Coating Service multifunzione interno
Dopo anni di sviluppo di finiture in PVD per supportare i nostri partner e aiutarli a rimanere competitivi, abbiamo ampliato i nostri servizi per offrire trattamenti direttamente al settore. Tuttavia, il nostro obiettivo principale rimane quello di educare il mercato e promuovere il PVD come attore chiave nella finitura superficiale. "Stiamo lavorando a stretto contatto con un settore disposto a innovare, sviluppare o espandere le sue soluzioni di finitura. Il nostro Coating Center svilupperà anche nuove soluzioni, introdurrà nuovi prodotti, ridurrà il time to market e tutto ciò di cui il settore ha bisogno per approfondire e migliorare le sue competenze nel PVD". La tecnologia PVD è in continua espansione: dai nuovi traguardi nel settore delle finiture in mercati ad ora inesplorati, a nuove tecnologie – quali l’Hipims – per rispondere alle crescenti esigenze di produzione, ma quello che fa davvero la differenza è il processo adottato. Attraverso lo studio di processo è possibile ottenere efficienza e ripetibilità perfette, oltre che conferire alcune proprietà speciali al substrato.
Kenosistec offre soluzioni di supporto e guida per i clienti che si approcciano a questa tecnologia, contribuendo alla realizzazione di un metodo: il Cleaning Coating Testing per esempio è il servizio chiavi in
mano offerto dall’azienda, che si occupa dello studio preliminare per verificare la fattibilità del processo, della progettazione e produzione dell’impianto di PVD e infine dell’installazione e della messa in funzione della macchina, garantendo l’assistenza per tutto il ciclo di vita del sistema.
Kenosistec può essere considerata la soluzione ideale anche per chi vuole muovere i primi passi nel mondo del PVD, ma non ha la possibilità di acquisire un impianto di produzione. L’azienda offre infatti un servizio di coating in conto terzi flessibile e altamente specializzato, che garantisce eccellente qualità e supporto tecnico in ogni fase del processo. Questo servizio che permette ottenere una finitura PVD per testare la reazione del mercato prima di acquisire un impianto, ma è anche adatto per chi ha già un impianto e sta affrontando una crescita improvvisa o temporanea dei volumi.
Il futuro del design passa per il PVD, e Kenosistec è all’avanguardia in questo percorso, offrendo servizi e tecnologie che permettono di creare prodotti belli, durevoli e rispettosi dell’ambiente. Con l’espansione delle applicazioni del PVD e il continuo sviluppo di nuove soluzioni, le possibilità per il settore del design sono pressoché infinite, e Kenosistec è pronta a sfruttarle al massimo.
gli esperti nell’impossibile si affidano alle prestazioni
Alessia Venturi ipcm®
Nel settore dell’architettura metallica ogni progetto richiede una soluzione unica. Tuttavia, la base di partenza necessaria per qualsiasi progetto è la qualità dei manufatti e delle strutture che lo comporranno. Questa qualità si misura sostanzialmente nella loro durabilità in esterno, nella loro resistenza alla corrosione e alle intemperie, entrambe caratteristiche garantite dal ciclo di finitura. Luxe Perfil, leader europeo nel settore del coil coating in alluminio ha scelto un prodotto molto innovativo e unico sul mercato, il PrimeCoat® A109 di DN Chemicals, per soddisfare le specifiche di qualità dei propri prodotti per architettura.
Quella dell’alluminio per impiego architettonico è un’industria molto vivace e dinamica, con requisiti sempre nuovi e più complessi, non solo dal punto di vista progettuale ma anche prestazionale. Rispondere in maniera puntuale a queste esigenze, anticipandole, è la specialità di Luxe Perfil, gruppo italo-spagnolo specialista dell’alluminio che produce profili, porte, pergole bioclimatiche, avvolgibili e zanzariere destinati a progetti di edilizia commerciale e privata in oltre 40 paesi nel mondo.
È risaputo che la finitura costituisce parte integrante della qualità di un progetto architettonico, poiché ne è la prima barriera, la prima protezione verso tutto ciò che circonda e influisce su questo progetto: agenti atmosferici e ambientali, sollecitazioni meccaniche e chimiche, cicli di pulizia, impatto umano.
È anche risaputo che le prestazioni della vernice, qualsiasi vernice, da sole non sono sufficienti a dare questa qualità di prestazioni: si tratta sempre di un gioco di squadra fra pre-trattamento e verniciatura. Dove la vernice non arriva – o non può arrivare per limiti chimici o applicativi – il pre-trattamento è pronto a spingere in alto le sue prestazioni e, insieme ad essa, a raggiungere la conformità alle specifiche. È quanto è accaduto in Luxe Perfil di Chiva (Valencia), e Alucofer di Robledo (Albacete), appartenenti allo stesso gruppo specialista nella produzione, finitura e trasformazione dell’alluminio.
La collaborazione con DN Chemicals di Milano – già fornitore della terza consociata del Gruppo, l’italiana Luxe Coat – per la sperimentazione, prima, e l’industrializzazione poi di un prodotto di conversione esente cromo no-rinse altamente innovativo, ha consentito a Luxe Perfil di raggiungere una resistenza alla corrosione mai raggiunta prima dai suoi coil verniciati a liquido o a polvere. L’azienda spagnola è anche riuscita a ridurre i costi e i tempi di produzione, dal momento che il prodotto fornito da DN Chemicals consente di saltare la fase di applicazione di un primer tradizionale.
Esperti nell’impossibile
Con 30 anni di esperienza, 320 collaboratori, 130.000 m2 di installazioni in Spagna e Italia, 50.000 tonnellate all’anno di capacità produttiva di nastro in alluminio verniciato e 10.000 tonnellate di profili estrusi e verniciati, Luxe Perfil si definisce “esperta nell’impossibile”.
“Luxe Perfil è un gruppo a cui appartengono 3 aziende specializzate nella lavorazione dell’alluminio, di cui due in Spagna - Luxe Perfil e Alucofer – e una in Italia – Luxe Coat di L’Aquila” racconta Giuseppe Procopi, Direttore Generale del gruppo. “Le attività produttive iniziarono quasi 30 anni fa con la realizzazione di avvolgibili su misura. Grazie a un’intuizione del titolare per rispondere alle tendenze del mercato, negli anni sono stati via via integrati altri processi produttivi legati all’industria dell’alluminio fino ad oggi: con 4 linee di coil coating, di cui 3 a liquido e una ibrida liquido/polvere, 4 linee di taglio, fonderia, pressa di estrusione, 15 linee di profilatura per avvolgibili e 2 per cassonetti, due impianti di verniciatura a polvere orizzontale e uno verticale per gli estrusi fino a 8,5 m, 1 laminatoio, 2 colate continue, 1 tensospianatrice, oggi il gruppo Luxe Perfil ha integrato verticalmente
Dall'alto:
La linea di coil fino a una larghezza di 1550 mm, con uno spessore massimo di 3,05 mm, in due finiture: liquida e in polvere.
Uno dei due chemcoater che applicano il prodotto no-rinse esente crcomo PrimeCoat® A109 sui coil di Luxe Perfil.
La testa di verniciatura a liquido dei coil.
in azienda l’intera filiera dell’alluminio, riducendo i tempi di produzione e aumentando la qualità. La prima linea di coil coating fu installata qui a Valencia, a seguito del consumo di coil verniciato continuamente in crescita. Oggi nello stabilimento di Chiva abbiamo 3 linee di coil coating. In seguito con l’incremento importante della richiesta di avvolgibili su misura, si decise di investire anche negli estrusi, perché nessun fornitore riusciva a stare al passo con la nostra richiesta. 20 anni fa a Robledo nasceva Alucofer, dove abbiamo installato la prima pressa di estrusione e una linea di verniciatura orizzontale a cui, qualche anno fa, abbiamo affiancato una linea verticale, unica in Europa a verniciare fino a oltre 8,5 m di lunghezza, e una linea di verniciatura coil a liquido per piccoli lotti (60 cm di larghezza), la cui incidenza sul volume totale di avvolgibili era in grande crescita. In Alucofer abbiamo avviato anche la produzione di profili PVC con 6 linee di estrusione,
nonché la fonderia per le billette da estrusione e la pressofusione per l’accessoristica, che è poi verniciata a polveri su una delle linee orizzontali. Completa la dotazione impiantistica per la finitura degli estrusi una linea di sublimazione.”
“L’obiettivo di questo sviluppo tecnologico e di questa espansione dell’area produttiva era quello di offrire un ventaglio di prodotti sempre più ampio, puntando a essere fornitori unici dei nostri clienti, facilitando la gestione dell’approvvigionamento da parte dei clienti esteri. Nel frattempo il mercato della tapparella si è evoluto, specializzandosi nella produzione di elementi oscuranti e di schermatura come le zanzariere e le pergole bioclimatiche - quest’ultime oggi sono tra i nostri prodotti principali. Abbiamo una tipologia di clientela variegata, che riceve un servizio rapido, completo e un grande supporto tecnico, potendo contare sulla nostra struttura solida ad elevata produttività”.
Il laboratorio di controllo qualità di Luxe Perfil a Chiva (Valencia).
Prova di qualità sulle vernici applicate da Luxe Perfil.
La finitura: una gamma infinita di possibilità e altrettante richieste di performance
Da Doha a Saransk da Bruxelles a Roma fino a Montreal, i prodotti Luxe Perfil hanno contribuito alla realizzazione di progetti architettonici iconici.
“In Luxe Perfil siamo coscienti dell’importanza di contare sulle finiture migliori disponibili sul mercato affinché i nostri prodotti abbiano una qualità indiscutibile, non solo dal punto di vista estetico ma anche dal punto di vista delle prestazioni in esterno. Seguendo progetti in oltre 40 paesi nel mondo, gli ambienti in cui sono inseriti i nostri prodotti sono i più diversi. Per quanto riguarda la scelta delle finiture, nel settore Building sono normalmente gli architetti a dare indicazioni precise già nei progetti. In molte occasioni, forti della nostra esperienza pluriennale, abbiamo sviluppato noi stessi colori ed effetti diversi, con l’obiettivo di migliorare l’impatto estetico dei nostri prodotti. Portiamo avanti uno sforzo di ricerca e sviluppo interno per soddisfare e anticipare le esigenze che percepiamo nel mercato” commenta Procopi. “Nel settore Coil siamo tra i pochi in Europa in grado di verniciare fino a una larghezza di 1.550 mm, con uno spessore massimo di 3,05 mm, in due finiture: liquida e in polvere. Oggi proponiamo finiture in tutta la carta RAL, colori ad effetto, texture e livelli di brillantezza diversi, nonché l’effetto legno”.
“Come dicevo prima, di fondamentale importanza è soddisfare le performance richieste che, nel settore delle tapparelle e della protezione solare, sono sempre in crescita: resistenza chimica ai prodotti di pulizia e meccanica ai cicli di apertura e chiusura della tapparella, resistenza alla corrosione, agli UV, agli agenti atmosferici, sono i parametri principali di misura della qualità. Dobbiamo considerare che la tapparella è il primo elemento esposto all’esterno di un serramento ed è soggetta ad un rischio di corrosione maggiore rispetto alla finestra vera e propria, anche perché la tapparella può rimanere chiusa per molto tempo, oltre ad essere un elemento dinamico. Talvolta le richieste dei clienti in tema di resistenza alla corrosione sono così alte che i fornitori di vernici non sono in grado di soddisfarli, quindi il ruolo del pre-trattamento che noi effettuiamo sui nostri coil diventa strategico ai fini della conformità.
“Abbiamo risolto il problema di innalzamento delle prestazioni attraverso la collaborazione con DN Chemicals, iniziata quando abbiamo aperto Luxe Coat in Italia e abbiamo iniziato a fare prove di applicazione con risultati ottimi1. Dopo aver testato DN per diversi anni e sulla base di progetti di sperimentazione comuni, abbiamo deciso di contattarli anche per Luxe Perfil. I loro prodotti di pretrattamento, che impieghiamo su tutte le linee coil sia in Luxe Perfil sia in Alucofer (oltre che presso l’italiana Luxe Coat) ci danno garanzia di performance elevate soprattutto in tema di resistenza alla corrosione che altri fornitori non ci assicurano”.
1 Giorgia Ricchiuti, “Passaggio in due fasi dalla cromatazione a un ciclo esente cromo su una linea di verniciatura coils in alluminio” da ipcm® n. 75, Vol. XIII, Maggio-Giugno 2022, pagg. 94-99)
Un pre-trattamento robusto
“A Luxe Coat forniamo un ciclo di pre-trattamento esente cromo ormai consolidato” interviene André Bernasconi, General Manager di DN Chemicals di Milano. “L’elemento di novità è che Luxe Coat ha installato il primo impianto al mondo di nebulizzazione per il pretrattamento del coil per architettura ad alto spessore, da 1,2 mm fino a 3 mm, per facciate continue. In Luxe Perfil e in Alucofer, invece, il processo avviene tramite Chem Coater (un’apposita macchina per l’applicazione di prodotti no-rinse come se fossero una vernice) che applica un prodotto innovativo formulato con un particolare polimero fondamentale per la protezione anticorrosiva ma anche per attribuire al coil verniciato quella flessibilità necessaria alla fase di postformatura.
Le prestazioni del prodotto PrimeCoat® A109 sono analoghe a quelle garantite da un esente-cromo, pur non presentando in formulazione alcun altro metallo. Si tratta di una resistenza dalle 1000 alle 1500 ore in nebbia salinoacetica a seconda del tipo di lega di alluminio trattata.
Un ulteriore vantaggio di questo prodotto è che si può evitare l’applicazione di un primer tradizionale, con evidenti risparmi economici e velocità produttiva”.
“Per lo sgrassaggio alcalino Luxe Perfil usa DenClean 418 AS e il disossidante DenAcid 774 per la mordenzatura.
La linea coil in Alucofer usa lo stesso sgrassante alcalino e la stessa conversione con PrimeCoat® A109, ma non presenta la fase di neutralizzazione acida” prosegue Gherardo Minotti, Business Development di DN Chemicals. “In entrambi gli stabilimenti hanno installato un sistema di depurazione delle acque sviluppato in collaborazione con noi. Quando abbiamo approcciato Luxe Perfil, dopo una lunga collaborazione con Luxe Coat, abbiamo individuato delle necessità di ammodernamento della fase di pretrattamento, quindi ci siamo presentati come fornitori sia di prodotti consolidati sia di innovazione”. “L’analisi elettrochimica delle prestazioni di PrimeCoat® A109 è molto interessante, perché dimostra contestualmente sia il livello di protezione dal punto di vista elettrochimico, quindi dalla corrosione, sia la bassissima permeabilità dell’acqua, che dà buoni presupposti per non avere problemi di corrosione del substrato esposto alle intemperie”.
Un cambiamento molto positivo “Grazie all’integrazione di questi prodotti, oltre alle prestazioni abbiamo migliorato notevolmente anche il nostro processo produttivo, che è diventato più
stabile. Siamo davvero molto soddisfatti” commenta Procopi. “Tendenzialmente, cambiamo fornitore con estrema difficoltà. In Luxe Coat è stato facile introdurre le tecnologie di DN Chemicals perché l’azienda partiva da zero, ma in Luxe Perfil tendiamo a essere molto fedeli nel tempo, a meno che delle mancanze da parte del fornitore stesso non ci costringano a cambiare. Nel caso di DN Chemicals non è stato così: dopo un anno di test, sono stati molto attenti e bravi a proporsi in modo che non potessimo ignorarli”.
“Il prodotto di conversione è stato testato prima su lamierini in laboratorio, poi con una prova di mezza giornata e poi con 2 prove di un mese ciascuna, una nel 2022 e una nel 2023. Forniamo il prodotto dalla primavera del 2024” chiosa André Bernasconi. “Si è trattato di un bel progetto, che ha richiesto tempo ma è andato a buon fine, quindi è motivo di soddisfazione anche per noi in DN Chemicals”.
“Spesso accade di intraprendere buoni progetti ma che non si riesca a trovare il fornitore in grado di mettere in pratica quello che tu hai mente. Con DN Chemicals si è trattato di testare e poi introdurre un prodotto che loro stavano già sviluppando: ci siamo trovati entrambi nel momento giusto per sviluppare un prodotto che non esisteva sul mercato!” conclude Giuseppe Procopi.
Bringing your surface to perfection. Verind offers painting solutions from manual to automatic application, high-quality and easy to integrate.
1 Sgrassaggio (6m3 50°C) con Denclean 418 AS
2 Lavaggio (2m3) a temperatura ambiente
3 Mordenzatura acida (2m3) a temperatura ambiente con Denacid 774
4 Lavaggio (2m3)a temperatura ambiente con conducibilità < 200 microS
5 Lavaggio (2m3) a ambiente con conducibilità < 50 microS
6 Conversione applicata con ChemCoater PrimeCoat A109 Chrome-Free
Velocità della linea 40 -50 m/min
PrimeCoat® A109 è un pretrattamento esente cromo a base acqua specificatamente sviluppato per migliorare l’adesione della vernice e le proprietà di legame con la superficie metallica. L'acciaio rivestito con una lega di alluminio e zinco, pretrattato con PrimeCoat® A109, fornisce un'eccellente adesione durevole per le vernici in coil-coating e buone proprietà adesive. Le proprietà adesive di PrimeCoat® A109 sono state testate in combinazione con diversi rivestimenti monostrato e primer/topcoat dopo l'esposizione a condizioni di umidità, come test di umidità e immersione in acqua bollente. Quando viene utilizzato un sistema appropriato di primer e topcoat, il pretrattamento PrimeCoat® A109 offrirà una buona resistenza alla corrosione, paragonabile a un pretrattamento convenzionale senza risciacquo con cromato. Non ha pittogrammi di pericolo in etichetta.
DN Chemicals provvede regolarmente a monitorare la qualità del processo con:
• Prove di adesione T-bend, adhesion after boiling, impact test
• Prove di resistenza alla corrosione in camera di nebbia salina acetica ASTM B117
• Prove di resistenza alla corrosione per via elettrochimica EIS – ACET
Risultati ACET Test
Max Z ( Ω*cm2) Min Z ( Ω*cm2)
I valori di Max Z e Min Z rappresentano il valore massimo e minimo di impedenza registrati da inizio a fine test. Il valore di delta z rappresenta di quanto si è degradato il campione da inizio a fine test. Un valore basso indica un basso degrado. Ciò è confermato dal diagramma di bode qui di seguito che riporta le impedenze registrate durante la prova: sono 7 rette sovrapposte e questo significa degrado molto basso.
Il water uptake dà una indicazione sulle proprietà idrofobiche del rivestimento: in questo caso il valore è basso e quindi il rivestimento ha ottime proprietà idrofobiche (vedere immagine).
Trattamento acque
I prodotti forniti per l’impianto di depurazione sono:
• Denflok 7315 coaugulante primario
• Denflok 7504 polielettrolita
• Dencide 7702 sanificante antibatterico
• Dencal 6304 OS trattamento membrane osmosi.
Ilaria Paolomelo ipcm®
Nel mondo dell’arredamento e dell’illuminazione di lusso, la qualità e l’estetica sono fattori determinanti. Sirio Galv, da sempre sinonimo di eccellenza nel trattamento galvanico e nella verniciatura, ha recentemente compiuto un passo significativo verso l’innalzamento degli standard qualitativi con l’installazione di un nuovo impianto di verniciatura a liquido progettato e installato da Verona Impianti 2002. La nuova linea, oltre a garantire finiture di eccellente qualità, ha giocato un ruolo fondamentale nel supportare la politica ambientale di Sirio Galv, orientata alla riduzione dei consumi e all’efficienza energetica.
Nel cuore del Veneto si estende un’area rinomata a livello internazionale per la sua tradizione nell’industria dell’illuminazione. Questo polo produttivo, formalmente costituito nel 2008 come Distretto Veneto dei Sistemi per l’Illuminazione (oggi Luci in Veneto), rappresenta una significativa aggregazione di imprese del settore, promossa dal Comune di Piombino Dese (PD). Fin dalla seconda metà degli anni 2000, il Distretto si è affermato come un centro di eccellenza, capace di integrare l’intera filiera dell’illuminotecnica, dalla produzione e assemblaggio di apparecchiature per l’illuminazione fino alla commercializzazione dei prodotti finiti. A pochi chilometri da Piombino Dese, più precisamente a
Camposampiero (PD), sorge la sede di Sirio Galv, azienda specializzata nel trattamento galvanico e nella verniciatura industriale di complementi d’arredo e di design di alta gamma. Fondata nel 1996 da Claudio Vaccarin, Sirio Galv si è affermata come partner strategico per le imprese del settore illuminotecnico e dell’arredamento, grazie all’eccellenza qualitativa e all’adozione di tecnologie all’avanguardia. Tra i suoi più recenti investimenti, spicca l’installazione di un nuovo impianto di verniciatura a liquido progettato da Verona Impianti 2002 (Colognola ai Colli, VR), che consente all’azienda di affrontare le sfide di un mercato in continua evoluzione con maggiore efficienza, mantenendo standard elevati di qualità e sostenibilità ambientale.
Da sinistra: la zona di carico dell’impianto di verniciatura; asciugatura manuale con soffiaggio ad aria compressa; L’entrata del forno di asciugatura/cottura.
Sirio Galv: eccellenza artigianale e innovazione tecnologica
Sirio Galv è nata dall’intraprendenza di Claudio Vaccarin, imprenditore che ha iniziato la sua carriera da giovane come operatore nei trattamenti galvanici, sviluppando rapidamente una profonda conoscenza del settore. Affascinato dalla precisione e dalla disciplina richieste per realizzare finiture di alta qualità in cromo, nichel o oro, Vaccarin decise 28 anni fa di fondare la sua azienda, offrendo trattamenti galvanici e verniciatura prima al settore dell’illuminazione e poi anche a quello dell’arredamento. “Quando il settore dell’illuminazione ha subito una contrazione a causa della delocalizzazione produttiva, Sirio Galv è stata in grado di reinventarsi, puntando sull’arredamento e ampliando la propria gamma con soluzioni tecniche avanzate, senza mai rinunciare alla tradizione artigianale che ci contraddistingue”, afferma Claudio Vaccarin, titolare dell’azienda padovana.
Oggi, Sirio Galv si distingue per la sua flessibilità produttiva, grazie a tre impianti galvanici altamente specializzati. Due di questi sono semiautomatici e studiati per garantire una qualità impeccabile su piccole e medie produzioni, mentre il terzo è un impianto manuale, pensato per la lavorazione di pezzi fuori misura o per finiture particolari e quindi per soddisfare anche le richieste di personalizzazione più complesse. Con un team di oltre 25 professionisti, l’azienda offre trattamenti galvanici e
verniciature di precisione in cromo, nichel, oro e altre finiture custom, combinando tecnologia avanzata e competenza per risultati estetici e funzionali d’eccellenza.
“La nostra crescita e il nostro successo sono il risultato di un impegno costante verso l’innovazione: dall’ottimizzazione dei processi di verniciatura all’adozione di soluzioni sempre più efficienti e sostenibili, abbiamo saputo interpretare ogni cambiamento del mercato come un’opportunità di sviluppo”, continua Vaccarin.
Un metodo produttivo accurato – dalla preparazione del supporto alla verniciatura
Il metodo produttivo di Sirio Galv è caratterizzato da un’approfondita attenzione ai dettagli e una cura maniacale per la qualità, che si riflette in ogni fase del processo, dalla pulitura iniziale alla verniciatura finale. “Ogni pezzo che arriva in azienda attraversa un ciclo produttivo studiato per garantire i massimi standard di precisione e perfezione estetica”, afferma Claudio Vaccarin.
La prima fase – per i clienti che lo richiedono – è dedicata alla pulitura robotizzata necessaria a rimuovere imperfezioni e residui di lavorazione e assicurare che la superficie sia pronta per il processo successivo.
I componenti sono poi sottoposti alla fase di preparazione al trattamento galvanico che prevede sgrassaggio e lavaggio con ultrasuoni allo scopo
di eliminare qualsiasi tipologia di oli, paste e altri residui derivanti dalle lavorazioni precedenti. “A questo punto, i componenti vengono trattati con uno strato di nichel, base essenziale per garantire l’adesione delle successive finiture. A seconda delle richieste del cliente, Sirio Galv applica finiture di diverso colore, tra cui oro, rame e nero, garantendo uniformità e durabilità grazie a un ciclo di immersione in bagni galvanici controllato con estrema precisione”, continua Vaccarin. Una volta completato il processo galvanico, i pezzi passano alla fase di verniciatura. “I componenti trattati da Sirio Galv sono componenti destinati all’arredamento di interni e quindi richiedono finiture che puntano principalmente sull’aspetto estetico, più che alla protezione dalla corrosione. Quest’ultima è infatti garantita dallo strato galvanico, mentre la verniciatura svolge un ruolo essenzialmente estetico per conferire maggiore bellezza e uniformità al prodotto. In questo settore, dove estetica e funzionalità devono coesistere in perfetta armonia, ogni pezzo deve essere impeccabile”, sottolinea Marta Vaccarin, figlia del fondatore Claudio e seconda generazione a capo dell’azienda.
Le tendenze di un mercato in evoluzione
“Parlando di estetica, per il successo di un’azienda è essenziale che i componenti non siano solo impeccabili dal punto di vista della qualità
della finitura, ma che si possano anche adattare alle più svariate richieste dei clienti,” spiega Marta Vaccarin. “Le tendenze e le richieste dei settori a cui ci rivolgiamo cambiano costantemente, e ci troviamo a rispondere a una varietà di esigenze, offrendo una gamma ampia di finiture e colori, con un catalogo che conta circa un centinaio di vernici”.
Ogni progetto parte con una fase di campionatura durante la quale il cliente approva una serie di test su pezzi prototipo, garantendo così che ogni finitura, che sia lucida, semi-opaca o pigmentata, soddisfi perfettamente le aspettative.
“Attualmente stiamo osservando un notevole ritorno del cromo lucido, una tendenza che segna una svolta rispetto al decennio precedente, dominato da finiture opache e colorate”, continua Vaccarin.
Il ciclo di verniciatura e le caratteristiche tecniche del nuovo impianto
Per riuscire ad essere competitivo in un mercato di alta fascia, Sirio Galv ha scelto di affidarsi a partner di eccellenza come Verona Impianti 2002, per la realizzazione del nuovo impianto di verniciatura, e come Lechler (CO) per la fornitura dei prodotti vernicianti.
“Il carico e scarico dei componenti avviene manualmente e, per motivi logistici, le due aree non sono collocate nella stessa zona, come avviene
solitamente negli impianti di verniciatura. Abbiamo progettato la zona di carico in modo che fosse adiacente alle vasche di galvanica, mentre la zona di scarico è situata vicino all’area di controllo qualità, prima dell’imballaggio e della spedizione”, spiega l’Ing. Albino Tamellin, titolare e fondatore di Verona Impianti 2002. Dopo essere stati caricati, i componenti sono prima asciugati manualmente con soffiaggio ad aria compressa, poi convogliati, attraverso trasportatore monorotaia, nel forno di asciugatura dove permangono per circa 20 minuti ed infine lungo un polmone di accumulo e sottoposti a raffreddamento forzato. “Il trasportatore è dotato anche di un canalino parasporco essenziale per evitare che gli oli di lubrificazione della catena possano in qualche modo contaminare e sporcare i componenti da verniciare appesi”, continua Tamellin. “Successivamente, i pezzi entrano nella cabina a temperatura controllata (26° C) dedicata all’applicazione del rivestimento. “Quest’ultima, effettuata manualmente dall’operatore mediante pistola fornita da Wagner (Valmadrera, LC), rappresenta un elemento distintivo che conferisce un valore artigianale unico ai prodotti di Sirio Galv. Dal momento che lavoriamo su piccole serie, pezzi singoli o con una geometria complessa, l’applicazione manuale ci consente di raggiungere zone difficili da verniciare e di ottenere finiture perfette su ogni componente”, continua Claudio Vaccarin. “Il numero di strati di prodotto verniciante da applicare varia in base alle richieste del
cliente. Solitamente per i nostri prodotti prevediamo una finitura bagnato su bagnato o, alternativamente, l’applicazione di una prima mano di topcoat con la cottura in forno a 140 °C per 25 minuti e poi un’ulteriore applicazione del medesimo topcoat, seguita dall’essiccazione in forno”. Infine ogni componente è controllato singolarmente prima dell’imballaggio per assicurare che rispetti gli standard qualitativi richiesti da un mercato di fascia alta, dove l’attenzione ai dettagli non perdona imperfezioni. “Una delle prime richieste ricevute durante la fase di progettazione dell’impianto riguardava la sostenibilità e la riduzione dei consumi. Per rispondere a queste esigenze, abbiamo dedicato particolare attenzione alla riduzione dei consumi e all’efficienza energetica. A tal proposito, abbiamo progettato un forno con un isolamento termico che supera le esigenze di temperatura di essiccazione dei prodotti vernicianti utilizzati da Sirio Galv. Inoltre, per assicurare una qualità impeccabile dei prodotti finiti, abbiamo progettato un sistema di filtrazione che copre tutta l’area di ricircolo dell’aria all’interno del forno nonché adottato misure per trattenere qualsiasi particella o residuo che potrebbe provenire da diverse aree, come il generatore di calore. Durante i cicli di riscaldamento, le parti del generatore che non possono essere verniciate tendono a sviluppare piccole tracce di ossido, che potrebbero diffondersi nel forno; attraverso filtri metallici adatti alle alte temperature, otteniamo una
Sirio Galv è specializzata nel trattamento galvanico e nella verniciatura industriale di complementi d’arredo e di design di alta gamma.
filtrazione del flusso completa, ricircolando aria completamente pulita, proprio come avviene nel settore carrozzeria”, afferma Pietro Tamellin di Verona Impianti 2002.
I fattori determinanti nella scelta dell’impianto: la collaborazione con Verona Impianti 2002
Quando Sirio Galv ha deciso di aggiornare il proprio impianto di verniciatura, la scelta è stata guidata da esigenze specifiche e dalla necessità di rispondere a nuove sfide di mercato. Il precedente impianto, installato nel 1996 e progettato per lavorare su componenti di lampadari e pezzi di piccole dimensioni, non era più adeguato alle nuove richieste del mercato dell’arredamento e del design di alta gamma. Con oltre 20 anni di servizio, l’impianto era ormai obsoleto e non in grado di soddisfare le attuali esigenze di efficienza e qualità.
Per affrontare questa transizione, Sirio Galv ha consultato alcuni dei suoi partner e fornitori nel settore della verniciatura industriale, chiedendo loro di raccomandare aziende specializzate nella produzione di impianti di verniciatura all’avanguardia. Dopo un’attenta valutazione e diverse consultazioni, l’azienda ha trovato in Verona Impianti 2002 il partner ideale. La sintonia immediata e la comprensione delle esigenze specifiche di Sirio Galv hanno reso Verona Impianti 2002 la scelta naturale. “Avevamo due requisiti principali: sostituire il precedente impianto con uno di nuova generazione che fosse allineato ai nostri standard di consumi, emissioni e sostenibilità, e risolvere un problema di inquinamento da pollini. Essendo situati a ridosso della campagna, ci siamo spesso trovati a dover affrontare la sfida dei pollini, che, essendo molto leggeri, tendevano a depositarsi sui componenti freschi di verniciatura. Questo problema ci costringeva a riverniciare i pezzi per eliminare i difetti causati da questi contaminanti. Con il nuovo impianto, abbiamo finalmente risolto questi problemi: il sistema è completamente pressurizzato e ogni punto di accesso è dotato di lame d’aria che impediscono l’ingresso di polvere e pulviscolo”, afferma Vaccarin.
Inoltre, Sirio Galv ha sempre dimostrato un forte impegno verso la sostenibilità e la riduzione dei consumi, e dal 1996 opera secondo la filosofia dello “scarico zero”. Le acque utilizzate nei processi produttivi vengono trattate internamente e riutilizzate, mentre l’energia elettrica necessaria viene prodotta tramite un cogeneratore. “I motori della linea di verniciatura sono inoltre regolati tramite inverter per ottimizzare i consumi elettrici e mantenere un perfetto bilanciamento della pressurizzazione”, dice Tamellin. Recentemente, l’azienda ha anche installato un impianto fotovoltaico che alimenta delle pompe di calore, permettendo così un ulteriore risparmio in termini di utilizzo di gas. “La sostenibilità ambientale non riguarda soltanto la riduzione dei consumi, ma anche delle emissioni di COV. Nonostante l’uso di vernici liquide a base solvente, abbiamo sempre prestato grande attenzione a ciò che veniva immesso in atmosfera, ma desideravamo ridurre ulteriormente la nostra impronta ecologica. Insieme al team di Verona Impianti, abbiamo lavorato in sinergia per ottenere risultati più sostenibili. Oggi, le emissioni sono scese molto rispetto ai valori molto più elevati del passato,” continua Vaccarin, evidenziando il successo del progetto.
Infine, riflettendo sull’installazione del nuovo impianto, il titolare di Sirio Galv ha sottolineato: “Lo spazio ristretto che avevamo a disposizione nel nostro stabilimento per l’installazione era davvero limitato. Le vasche di galvanica ci vincolavano in larghezza e il muro del capannone in lunghezza. Tuttavia, nonostante queste difficoltà, siamo riusciti a inserire tutte le tecnologie necessarie nell’area disponibile, e l’impianto ci è stato consegnato in tempi brevissimi, proprio durante il periodo estivo, il che ci ha permesso di non ritardare le consegne delle commesse in ordine. Siamo estremamente soddisfatti, non solo della collaborazione con il team di Verona Impianti, ma anche del sistema che hanno fornito. È affidabile e risponde a tutte le nostre esigenze. Non abbiamo mai avuto un fermo per guasti, e questo ci ha permesso di proseguire con la produzione senza interruzioni”.
Jesús Galindo
ALSAN - Álvarez Schaer - Paterna (Valencia), Spagna marketing@alsan.es
La depurazione delle acque di scarico costituisce un elemento chiave negli impianti di verniciatura a polvere e di ossidazione anodica. Il suo corretto funzionamento è essenziale per garantire che i reflui finali rispettino in modo soddisfacente la normativa. Il rispetto di parametri di scarico sempre più restrittivi, insieme alla crescente scarsità di acqua, ha portato Alsan a condurre studi sul riutilizzo di questa preziosa risorsa.
In un processo di depurazione convenzionale, come il sistema
AludePure di ALSAN, la precipitazione di solfati, fluoruri, alluminio e altri metalli è ottenuta attraverso l'uso di calce e HCl, che agiscono anche come regolatori di pH. Tuttavia, alcuni parametri di scarico come la conducibilità e la concentrazione di solfati, risultano in alcuni casi difficili da soddisfare con questo trattamento classico. L'azienda ha cercato di migliorare la precipitazione o la rimozione dei contaminanti, garantendo che le acque risultanti presentino una conducibilità molto
bassa e una bassa concentrazione di contaminanti. Queste acque non solo soddisfano i limiti di scarico, ma sono anche adatte al riutilizzo, riducendo così il consumo complessivo.
EcodePure è il nuovo processo di depurazione sviluppato da ALSAN ed è facilmente implementabile in un sistema AludePure preesistente (figg. 1-3). La differenza principale sta nell'impiego di additivi appositamente sviluppati, studiati per far precipitare solfati, alluminio e fluoruri a valori molto più bassi di quelli normalmente raggiunti dai
processi convenzionali. Come spiegato più avanti, lo schema per il trattamento e il riutilizzo delle acque reflue varia a seconda del tipo di linea di produzione, con una depurazione separata degli effluenti acidi e alcalini che è fondamentale.
Gli effluenti alcalini seguiranno il processo di trattamento standard, basato sulla neutralizzazione e sulla precipitazione dell'alluminio disciolto sotto forma di allumina. Gli effluenti acidi saranno sottoposti al nuovo processo di purificazione che riduce efficacemente le concentrazioni di contaminanti al di sotto dei limiti di scarico più esigenti. È importante sottolineare che l'intero contenuto di fluoruri e solfati si trova nell'effluente acido. Questi due parametri: solfati, fluoruri e conducibilità, risultano essere i più difficili da soddisfare attualmente con i processi standard di trattamento delle acque basati sulla precipitazione degli inquinanti con la calce (Tabella 1).
Parametro di scarico Limite di scarico
Solfati (ppm)
Fluoruri (ppm)
Conduttività (μS/cm)
Valori ottenuti con calce
Valori ottenuti con EcodePure
1500 1500-3000 < 250
10 20-30 < 10
3000 4000-15000 < 2000
A seconda del tipo di trattamento, ovvero un pretrattamento alla verniciatura con acido, un doppio pretrattamento o una linea di ossidazione anodica, il diagramma di depurazione e la percentuale di acqua riciclata saranno diversi. ALSAN presenta la soluzione chiave per le linee di verniciatura a polvere attraverso il sistema EcodePure PC e per il trattamento delle acque reflue di anodizzazione attraverso il sistema EcodePure AN. Segue una breve descrizione dello sviluppo e del funzionamento di ciascuna di queste soluzioni.
Dall'alto:
Figura 1 - Il nuovo processo di depurazione EcodePure sviluppato da ALSAN è facilmente implementabile in un sistema AludePure esistente.
Figure 2 e 3 - Alcune apparecchiature del sistema AludePure.
Figura 4 - Processo EcodePure PC per sistemi di pretrattamento acido per la verniciatura a polvere.
Figura 5 – Processo EcodePure PC per impianti di verniciatura a polvere con doppio pretrattamento.
6 – Processo EcodePure AN per linee di ossidazione anodica.
EcodePure PC: linea di pretrattamento acido per verniciatura a polvere
Questa linea rappresenta lo scenario più semplice, poiché tutte le acque reflue generate sono interamente acide, per cui non è necessario separare gli effluenti prima del trattamento. Questo effluente acido è sottoposto al nuovo processo di trattamento delle acque, EcodePure PC, dove in una prima fase è neutralizzato con calce e additivi per la precipitazione di solfati e fluoruri. Una volta separato il precipitato, l'effluente è neutralizzato con CO2 e filtrato, rendendolo pronto per coprire il fabbisogno di acqua nei risciacqui della linea. In questo caso, il 100% dell'acqua impiegata nella linea è riutilizzata. L'uso di CO2 come reagente nella fase di neutralizzazione è essenziale perché permette di diminuire il pH e ridurre il contenuto di calcio. L'uso di HCl, che è il reagente più comune per la regolazione del pH negli impianti di trattamento delle acque, è fortemente sconsigliato se si desidera riutilizzare l'acqua, poiché introdurrebbe cloruri nell'acqua di processo, portando a vaiolatura nel materiale. Uno schema del processo di trattamento dell'acqua è illustrato nella Figura 4
ALSAN ha testato il sistema EcodePure PC con un campione di un suo cliente che utilizza il suo prodotto per l'attacco acido, ALCID 2005RH, nonché il suo prodotto senza cromo Ecoal® 20AH1 nella sua linea di produzione. Le acque reflue prodotte nella linea sono quindi esclusivamente acide e, dopo essere stata sottoposta al processo EcodePure e alla successiva neutralizzazione, l'acqua risultante presenta una conducibilità, una concentrazione di solfati e fluoruri sufficientemente bassa da poter essere riutilizzata nel processo. I parametri di quest'acqua prima e dopo il trattamento sono riportati nella Tabella 2
Parametri di scarico
Ingresso nell'impianto di trattamento rifiuti
Dopo il trattamento con EcodePure
5.8
6.8
EcodePure PC: impianto di verniciatura a polvere con doppio pretrattamento
In questo tipo di linea, gli effluenti saranno separati in flussi acidi e alcalini e trattati in modo indipendente. Da un lato, gli effluenti acidi saranno trattati come spiegato nel caso precedente, ottenendo un
flusso con bassa conducibilità e contenuto minimo di inquinanti. Quest'acqua, che dopo il processo EcodePure PC ha un pH alcalino, è riutilizzabile nei risciacqui alcalini della linea senza bisogno di regolare il pH, oppure può essere neutralizzata e inviata ai risciacqui acidi o alcalini. L'impiego di CO2 sarà studiato per ogni caso. Gli effluenti alcalini, invece, saranno trattati nel modo convenzionale per far precipitare l'alluminio e regolare il pH entro gli standard di scarico. Nel caso dell’impianto di verniciatura a polvere, gli effluenti alcalini provengono da risciacqui solo leggermente concentrati e con basse quantità di solfati e fluoruri, pertanto il rispetto dei parametri di scarico non rappresenta un problema. Una rappresentazione schematica del sistema EcodePure PC per le linee di pretrattamento doppie è presentata nella Figura 5.
L'utilizzo di EcodePure PC nei sistemi pretrattamento consente di riutilizzare dal 50% al 100% del consumo attuale di acqua, fornendo una soluzione necessaria e in linea con la protezione dell'ambiente.
EcodePure AN: linee di ossidazione anodica
Come negli impianti di verniciatura con doppio pretrattamento, la separazione degli effluenti acidi e alcalini è fondamentale nelle linee di ossidazione anodica. Tuttavia, in questo caso, gli effluenti alcalini rappresentano generalmente una percentuale inferiore del volume totale delle acque reflue, circa il 20-30% a seconda della linea. Di conseguenza, sottoponendo gli effluenti acidi al processo EcodePure AN e dopo la neutralizzazione, il volume di acqua riciclata raggiungerà il 65-75% dell'acqua di processo (Figura 6).
L'effluente alcalino, tipicamente molto concentrato, può presentare un'elevata conducibilità anche dopo il trattamento convenzionale, per cui in questi casi sarà necessario un impianto di osmosi inversa per l'effluente alcalino già trattato. È da notare che questo effluente alcalino trattato contiene principalmente cloruro di sodio, in modo da essere adatto al sistema di osmosi inversa. L'acqua osmotizzata risultante può essere reintrodotta nell’impianto, aumentando così la percentuale di acqua riciclata al 90% e lasciando un rifiuto dall'osmosi, corrispondente al 10% dell'acqua totale utilizzata, che può essere gestito o evaporato, raggiungendo in entrambi i casi lo scarico zero.
In conclusione, il nuovo sistema EcodePure permette, grazie all'utilizzo di additivi appositamente studiati, la precipitazione completa di metalli, solfati e fluoruri a valori inferiori a quelli stabiliti dai limiti di scarico e il riutilizzo di una percentuale di acqua compresa tra il 50 e il 90%.
Una soluzione consigliata a tutte quelle aziende che decidono di fare un passo avanti nel loro impegno di gestione ambientale e di cura delle risorse naturali del nostro pianeta.
Il Team ItalMesh ha ingegnerizzato e realizzato il rivestimento esterno dell’edificio, sede del nuovo punto vendita di Burger King a Rovereto, inaugurato nel 2023.
ItalMesh è un’azienda italiana specializzata nella realizzazione di progetti architettonici con l’utilizzo di reti metalliche stirate e pannelli forati, affermata sul mercato nazionale e internazionale.
I prodotti realizzati da ItalMesh possono essere utilizzati sia per rivestire elementi per architettura da esterno, come facciate, frangisole, balaustre e recinzioni, sia per interni, come controsoffitti ed altri elementi di Interior design. L’alta tecnologia, la qualità dei materiali e della lavorazione, unite alle infinite combinazioni di forme e colori, permettono di fondere perfettamente l’estetica e la funzionalità, rendendo le realizzazioni ItalMesh versatili e sempre innovative.
Ne è un esempio il cladding studiato e realizzato per rivestire un nuovo punto vendita italiano di Burger King, la rinomata catena di Fast Food americana che a Rovereto, nella provincia autonoma di Trento, ha inaugurato uno dei suoi 250 ristoranti distribuiti lungo tutta la Penisola. Per questo progetto, sviluppato in collaborazione con lo StudioA22 Architettura e Design con sede nella stessa città roveretana, sono stati utilizzati circa 1250 m2 di lamiera in alluminio forata e verniciata con un prodotto altamente duraturo di polvere bianca che, in base al riflesso della luce solare e alla posizione dell’osservatore, dona profondità e movimento alla struttura.
ItalMesh ha realizzato tutti gli inserti e i profili in colore rosso, creando così un forte contrasto con il bianco lucido delle pareti.
Il risultato è un edificio discreto, che si integra perfettamente nel paesaggio trentino, ma con un profilo inconfondibile che lo associa immediatamente al Fast Food americano, a cui l’involucro esterno dà tono e carattere.
ItalMesh: la forza del rivestimento
L’azienda, che ha la propria sede a Montirone, in provincia di Brescia, offre al mercato più di 300 modelli di reti stirate e pannelli forati personalizzabili realizzati in diversi materiali e con differenti spessori. “Effettuiamo i trattamenti superficiali dei nostri prodotti tramite verniciatura con polveri termoindurenti atossiche con grado elevato di resistenza ai raggi UV e alla corrosione, o ossidazione anodica” – sottolinea Luca Baronchelli, Export Manager di ItalMesh. “Queste finiture presentano numerosi vantaggi, come l’auto-pulizia del
materiale e la possibilità di mantenere inalterate nel tempo le sue caratteristiche funzionali ed estetiche. Le finiture sono concepite non solo per offrire speciali effetti estetici che impreziosiscono ogni progetto, ma anche come rivestimento protettivo che permette alta resistenza alle condizioni climatiche più estreme. ItalMesh all’interno del suo stabilimento dispone di tre impianti di verniciatura di ultima generazione, muniti di robot antropomorfi, cambio colore automatico e controllo del processo costante”. Caratterizzata da una forte vocazione alla sostenibilità e all’automazione e sostenuta da un team tecnico esperto e consolidato, che segue e supporta il cliente nella realizzazione del progetto attraverso tutte le fasi - dal concept alla progettazione, ingegnerizzazione, realizzazione e installazione – la società ha raggiunto un’importante affermazione internazionale, penetrando con i propri prodotti innovativi in mercati distribuiti a livello globale, dal Canada all’Australia, dagli Stati Uniti alla Nuova Zelanda, passando per i più esigenti Paesi mediorientali.
Un nuovo approccio alla sostenibilità L’azienda bresciana sostiene da sempre l’utilizzo di tecnologie ecosostenibili a basso impatto ambientale. “La nostra produzione è da sempre attenta all’impatto ecosostenibile delle nostre lavorazioni” – spiega Baronchelli – “ricicliamo i rifiuti, recuperiamo le materie prime, cerchiamo di abbattere il consumo delle risorse energetiche grazie all’impianto fotovoltaico che copre il 90% del fabbisogno dello stabilimento e ci impegniamo a sviluppare i nostri prodotti con un occhio di riguardo al loro impatto ambientale. Ne è un esempio il nostro progetto Zero Gravity Eden (che sarà l’argomento di un articolo più approfondito in pubblicazione su uno dei prossimi fascicoli della nostra rivista, NdR), nato dalla nostra convinzione che l’utilizzo di tecnologie vegetali verticali in edilizia rappresenti una soluzione sostenibile per migliorare sia l’ambiente urbano sia quello industriale. Questo nuovo progetto si basa su una nuova concezione architettonica del mondo che ha spinto ItalMesh a creare reti in metallo stirato e verniciato in cui possano vivere e svilupparsi i vegetali, dando così vita a pareti verdi in grado di far crescere un vero e proprio giardino verticale pensato per ricoprire le facciate di qualsiasi struttura”. Il percorso di crescita di ItalMesh è basato sulla sapiente combinazione di un’esperienza ultratrentennale nel settore e sulla capacità di anticipare le richieste del mercato con progetti innovativi e lungimiranti per “vestire su misura” qualsiasi tipologia di involucro architettonico con soluzioni funzionali, durature, accattivanti dal punto di vista estetico ed ecosostenibili.
Per maggiori informazioni: www.italmesh.com
L’arte della verniciatura in polvere si fonde con l’innovazione nel prestigioso Centro di Ricerca Africano dell’Università Tedesca a Bayreuth, Germania.
Da sempre all’avanguardia nel settore della verniciatura in polvere, RIPOL si impegna a fornire soluzioni che combinino estetica e funzionalità con un occhio di riguardo per l’ambiente. Il nostro contributo al Centro di Ricerca Africano dell’Istituto di Studi Africani (IAS) dell’Università di Bayreuth ne è un chiaro esempio, in cui la nostra tecnologia si fonde con l’innovazione per creare un’architettura che lasci il segno.
Innovazione architettonica
Sul campus universitario di Bayreuth, in Germania, prende forma un progetto architettonico innovativo destinato a diventare un punto di riferimento per l’innovazione e la ricerca in Africa. La posa della prima pietra, tenutasi il 24 marzo 2023, ha segnato l’inizio di un viaggio verso la realizzazione di un centro all’avanguardia, il cui completamento è previsto per la fine del 2024.
Sostenibilità, estetica e tecnologia in perfetta armonia
La scelta dei materiali è stata centrale in tutto il progetto. Sostenibilità, estetica e tecnologia sono stati i pilastri portanti fin dalla fase di costruzione, bilanciando funzionalità e stile senza compromettere l’utilizzo di materiali ricercati. La facciata del centro è una combinazione armoniosa di funzionali montanti metallici verticali che ottimizzano l’efficienza energetica e conferiscono all’edificio un aspetto distintivo.
Palette di colori: un omaggio agli studi africani a Bayreuth
La scelta dei colori per la facciata - dai toni vivaci del giallo ai caldi marroni e rossi, identificati dai codici NCS S 1070-Y10R, NCS S 2060-Y30R, NCS S 4050-Y40R, NCS S 4550-Y80R - è stata influenzata dalla varietà cromatica, spesso presente nell’arte Africana e anche nel logo dell’Istituto di Studi Africani. L’effetto ondulato creato dall’applicazione di questi colori sulla facciata aggiunge eleganza e modernità all’infrastruttura e si integra perfettamente con l’estetica degli edifici circostanti.
Eccellenza tecnica nella verniciatura: la Serie RIPOL 52L
Nel processo di verniciatura dei frangisole, è stata selezionata la serie 52L Poliestere per architettura liscio opaco di RIPOL, una soluzione di rivestimento in polvere progettata per soddisfare i requisiti e le prestazioni delle specifiche GSB e QUALICOAT del settore architettura. Questi prodotti sono formulati per resistere a severe condizioni chimiche e meccaniche e hanno superato con successo test di laboratorio che ne hanno confermato le proprietà tecniche. Si caratterizzano per una eccellente resistenza agli agenti atmosferici, una buona resistenza alla nebbia salina e all’umidità e un’ottima ritenzione del colore e della brillantezza.
Impegno per la qualità e l’ambiente
Le vernici in polvere utilizzate sono prodotte e testate in conformità con i sistemi di qualità ISO 9001 per garantire prestazioni superiori e costanza dei lotti. Adatte ad applicazioni su alluminio, acciaio e acciaio zincato, la serie 52L, come tutti i prodotti RIPOL, è rispettosa dell’ambiente. Le vernici in polvere RIPOL non contengono solventi e non rilasciano Composti Organici Volatili (COV) nell’ambiente. L’eventuale polvere di ricircolo può essere recuperata come polvere vergine utilizzando attrezzature idonee, con uno spreco minimo. Lo smaltimento è facile e sicuro. Tutti i prodotti RIPOL sono privi di metalli pesanti. Con questo progetto, RIPOL è orgogliosa di riaffermare il suo impegno verso l’innovazione eco-compatibile, proponendo una soluzione ideale per le strutture che mirano all’eccellenza nel settore dell’architettura sostenibile e contribuiscono attivamente alla costruzione di un futuro più verde.
Per maggiori informazioni: www.ripol.com
Dr. Timo Porsch
Managing Director di periplast GmbH & Co. KG - WuppertaL, Germania t.porsch@periplast.de
Frank Siegel
Direttore Vendite del segmento verniciatura piccoli componenti di Walther Trowal GmbH & Co. KG - Haan, Germania f.siegel@walther-trowal.de
La verniciatrice a tamburo Rotamat apre la strada alla produzione di beni usa e getta ecologici.
Ogni anno solo in Europa vengono prodotti miliardi di cucchiaini da gelato in plastica, la maggior parte dei quali gettata via con noncuranza nell’ambiente. periplas produce cucchiaini in materiale granulare biodegradabile – sviluppato internamente – che si dissolve completamente se esposto all’umidità. Per evitare che la dissoluzione avvenga troppo velocemente, i cucchiaini vengono rivestiti con un sottile film protettivo in un’unità di verniciatura Rotamat.
Attualmente la produzione annuale globale di materiali plastici ammonta a circa 400 milioni di tonnellate. Circa il 50% di questa sbalorditiva quantità è utilizzata per packaging e beni usa e getta, utilizzati per un tempo limitato. Solo il 15% di questi prodotti viene riciclato e oltre il 30% disperso con noncuranza nell’ambiente.
Per esempio, i cucchiaini per il gelato vengono utilizzati per circa mezz’ora. Successivamente diventano spazzatura… o, peggio ancora, vengono
© periplast © periplast
La verniciatura con Rotamat garantisce la dissoluzione dei cucchiaini solo dopo il loro utilizzo. periplast fornisce articoli usa e getta in svariati colori.
gettati a terra. Ogni cucchiaino pesa solo pochi grammi, ma solo in Germania se ne utilizzano ogni anno circa 360 milioni, numero che in Europa raggiunge i diversi miliardi. Per questo motivo periplas ha cercato una soluzione che consentisse di produrre a basso costo cucchiaini che si dissolvessero dopo l’uso.
Un materiale che si ricicla da solo
La soluzione è il materiale granulare “periamyl”, sviluppato da periplast e in attesa di brevetto. È un polimero naturale al 100% costituito da amido di mais – una materia prima che cresce in natura. Quando raggiunge l’ambiente, degrada praticamente in qualsiasi condizione. Può essere riprodotto naturalmente e a costi molto ragionevoli. periplast produce i granuli presso il suo stabilimento di Wuppertal. Un altro significativo vantaggio di peryamil è che si può facilmente modellare con il calore. Questo permette di produrre in modo economico articoli usa e getta con le tradizionali apparecchiature di stampaggio a iniezione – creando così le condizioni ideali per la produzione a basso costo di beni usa e getta su scala industriale. Consente, per esempio, la produzione di posate usa e getta o tee da golf dall’aspetto plastico ma in realtà in materiale che cresce in natura al 100% e disponibile in abbondanza. Cosa più importante, il materiale degrada molto velocemente, anche in acqua salata.
Progetto iniziale “cucchiaini per gelato”
La prima applicazione a livello industriale di questo tipo di materiale sono i cucchiaini per il gelato. Una volta buttati via, i batteri presenti nell’ambiente ne garantiscono la dissoluzione in circa 20 settimane. Tuttavia, per assicurarsi che i cucchiaini non si sciolgano durante l’utilizzo, ovvero mentre si mangia il gelato, questi devono essere rivestiti con un materiale impermeabile. È entrata quindi in gioco Walther Trowal: da molti anni periplast utilizza le sue apparecchiature per la verniciatura in massa di componenti metallici. Grazie a questa collaborazione di lunga data le due aziende si sono ritrovare a discutere sul rivestimento dei cucchiaini per gelato…per Walther Trowal una nuovissima applicazione delle sue unità di verniciatura Rotamat.
Grazie a dei trial di lavorazione presso il Test & Training Center di Walther Trowal ad Haan, è stato sviluppato un rivestimento costituito da una soluzione ceramica multicomponente. Questo forma un biossido di silicio sulla superficie dei cucchiaini, stabile a lungo e anche insapore.
La versione standard della verniciatrice Rotamat R 80 ha soddisfatto immediatamente tutte le richieste di periplast, senza la necessità di modifiche tecniche.
Lo spessore del rivestimento ceramico è tale da rimanere assolutamente stabile durante l’utilizzo. Tuttavia, dopo poche ore il rivestimento viene infiltrato dall’acqua, per esempio attraverso i bordi del cucchiaio. Ciò
provoca l’espansione del materiale di base in modo tale che il rivestimento, composto sostanzialmente da sabbia, si scinda: il processo di dissoluzione inizia.
Per il progetto è stato molto importante riuscire ad ottenere il rivestimento con una macchina standard di Walther Trowal, che non ha richiesto alcuna modifica tecnica. Al momento periplast utilizza la Rotamat R 80 per rivestire lotti di circa 4.000 cucchiaini. Il peso di un lotto di questa dimensione consente il carico e scarico manuale senza eccessivo stress per l’operatore.
L’operazione di verniciatura vera e propria è completamente automatica. Gli operatori che gestiscono le macchine di stampaggio sono le stesse che caricano e scarico l’unità Rotamat e che monitorano l’intero processo. Non è quindi necessario personale aggiuntivo. La macchina è stata commissionata nel 2023 e ha sempre funzionato senza problemi. La manutenzione è limitata all’occasionale pulizia del tamburo e al cambio periodico dei filtri aria.
Oltre ai cucchiaini da gelato sono disponibili anche set completi di posate usa e getta in periamyl, in lotti da 10.000 pezzi. Come ai cucchiaini, anche a questi set viene applicato il rivestimento ceramico protettivo con Rotamat. Oltre alla loro compatibilità ecologica e sostenibilità, offrono un ulteriore vantaggio: i bordi affilati che si ottengono con il rivestimento ceramico consentono di tagliare facilmente una bistecca.
Un altro articolo con un enorme potenziale di mercato sono i tee da golf. Solo in Europa ne vengono utilizzati e gettati via ogni anno 1,4 miliardi di pezzi. Se anche solo il 10% dei tee in plastica fosse disperso nell’ambiente, nel giro di pochi decenni il terreno dei campi da golf sarebbe invaso da enormi quantità di plastica. I tee in periamyl, invece, si dissolverebbero molto rapidamente.
La verniciatrice Rotamat
Il sistema Rotamat rappresenta una soluzione economica per la verniciatura in massa di piccoli componenti come O-ring, manopole, molle e viti. Permette il trattamento di un’ampia gamma di componenti in metallo, legno, gomma e tutti i tipi di plastica. Componenti per l’industria cosmetica e automobilistica, per componenti per articoli da scrittura, per giocattoli, per l’industria tessile, nonché guarnizioni e silenziatori (elementi di ammortizzazione). I prodotti vernicianti possono essere a solvente o all’acqua. I sistemi Rotamat sono utilizzati per rivestimenti decorativi
Se esposti all’acqua, i cucchiaini si sciolgono quasi completamente in 6 settimane.
con numerose vernici ornamentali all’acqua e a solvente, ma anche per verniciare con rivestimenti anti-attrito, materiali leganti, isolanti o anticorrosione.
Nelle unità Rotamat i lotti di piccoli componenti sono verniciati in una camera a spruzzo rotante e chiusa (tamburo). Le pistole automatiche applicano uniformemente il materiale verniciante sui manufatti, che ruotano continuamente l’uno sull’altro. Il risultato sono superfici verniciate in modo preciso, con uno spessore del rivestimento uniforme e con un’eccellente aspettativa di vita del materiale verniciante applicato. Anche i componenti molto fragili o con geometrie complesse escono dall’unità con un rivestimento molto omogeneo, completamente asciutto e senza appiccicarsi tra loro. Una volta usciti dalla Rotamat i manufatti possono passare subito al processo di lavorazione successivo o alla fase di assemblaggio.
Il processo di verniciatura è completamente automatico. L’operatore deve solo caricare nuovi lotti di componenti grezzi e scaricare i lotti dei componenti finiti. Il costoso posizionamento dei componenti su telai speciali - necessario con i sistemi di verniciatura tradizionali- è stato completamente eliminato.
Chi è periplast
Dal 1978 periplast GmbH & Co. KG di Wuppertal (Germania) è specializzata nella produzione di componenti in plastica con stampaggio a iniezione ad alta precisione. Sin dalla sua fondazione, l’azienda di medie dimensioni a conduzione familiare produce bobine per filati e filo.
Rotoli, pannelli e celle in fibra di vetro
Celle filtranti per alte temperature
Rotoli e pannelli in fibra sintetica
Accumulatore vernice “Columbus”
Filtri “Andreae”
Cartucce filtranti
Filtri assoluti
Applicazioni speciali
Rolls, panels and cells of glass fiber
Filtering cells for high temperatures
Rolls and panels of synthetic fiber
Paint accumulator “Columbus” “Andreae” filters
Filtering cartridges
Absolute filters
Special application
©
Test: dopo essere stati esposti al terreno per 21 settimane (parte destra dell’immagine) i cucchiaini si sono sciolti completamente.
Se esposti al terreno, i tee da golf si sciolgono dopo poche settimane.
Alcuni anni fa è stata costituita una seconda sede produttiva in Romania, per servire meglio la clientela di quest’area geografica. Dal 2010 – presso la sede centrale di Wuppertal – periplast sviluppa prodotti in bioplastica, velocemente biodegradabili e che non richiedono materie prime fossili. L’amministratore delegato Dr. Timo Porsch, laureato in chimica, lavora in azienda dal 2015.
Walther Trowal – Tecnologie per la finitura superficiale dall’inventore del processo “Trowalizing”
Dal 1931 Walther Trowal sviluppa e produce sistemi per la finitura delle superfici. Concentrandosi inizialmente solo sulla finitura in massa – il termine “Trowalizing” ha origine dall’indirizzo telegrafico aziendale “Trommel Walther” – Walther Trowal ha costantemente ampliato il suo portfolio prodotti. Nel tempo l’azienda ha sviluppato una vasta gamma di macchinari e sistemi per la finitura in massa, la granigliatura e la verniciatura di piccoli componenti prodotti in serie.
Con l’invenzione di nuovi sistemi come la finitura a trascinamento e lo sviluppo di speciali metodi di finitura per i componenti stampati in 3D, l’azienda ha ripetutamente mostrato le sue capacità di innovazione.
Walther Trowal sviluppa e implementa soluzioni complete per il trattamento delle superfici, che possono essere facilmente integrate nei sistemi produttivi interconnessi dei clienti. Ciò include l’intera tecnologia di processo, perfettamente adattata alle esigenze di finitura superficiale dei manufatti: le apparecchiature e i relativi prodotti di consumo si completano sempre a vicenda in modo ottimale.
Ogni singolo manufatto e ogni singolo processo produttivo devono soddisfare speciali requisiti tecnici. Questo è il motivo per cui esperti ingegneri di processo nel laboratorio di prova, in stretta collaborazione con i clienti, sviluppano la tecnologia di processo ottimale per la finitura richiesta. Il risultato: superfici che soddisfano esattamente le specifiche richieste…con tempi di lavorazione brevi e risultati altamente omogenei e ripetibili.
Walther Trowal è uno dei pochi produttori che sviluppa e produce internamente tutte le macchine e i prodotti di consumo per la finitura in massa, inclusi i prodotti plastici e ceramici per la levigatura e la lucidatura, nonché i composti. La gamma di attrezzature dell’azienda include anche tutti i tipi di attrezzature periferiche per movimentare i manufatti quali sollevatori e ribaltatori, nastri trasportatori e rulliere, oltre a speciali essiccatoi per le applicazioni in massa e, ultimo ma non per importanza, sistemi per la pulizia a il riciclo delle acque di processo.
Con il suo programma di scambio di componenti soggetti a usura come i tamburi, che fanno parte di un programma di riciclo continuo, Walther Trowal conserva risorse preziose, contribuendo in modo significativo alla sostenibilità della produzione industriale. Un rapido servizio tecnico e un servizio globale di riparazione e manutenzione garantiscono un’elevata operatività dei nostri macchinari.
Walther Trowal serve clienti provenienti da un’ampia varietà di settori diversi in tutto il mondo, tra i quali automotive, aerospaziale, ingegneria medica e energia eolica.
PAN-DUR produce vetrate isolanti per sistemi di refrigerazione commerciale. L’azienda ha recentemente iniziato a utilizzare EcoPaintJet di Dürr. L’applicazione di vernice ad alta definizione dei bordi e senza overspray con EcoPaintJet consente a PAN-DUR di aumentare la flessibilità e la velocità produttiva, riducendo i costi di verniciatura.
EcoPaintJet, inizialmente introdotto per applicare la vernice senza overspray nella verniciatura dei veicoli industriali, sta ora apportando benefici ad altri settori. PAN-DUR isola le vetrate dei sistemi di refrigerazione commerciale che produce e da diversi mesi utilizza l’innovativo sistema applicativo di Dürr per verniciare le superfici in vetro. Questa tecnologia consente di risparmiare tempo e materiali eliminando la necessità di più stencil nella serigrafia.
Conosciamo tutti le grandi unità di refrigerazione dei supermercati: scaffali a parete, vetrine o banconi, dietro i cui pannelli in vetro o plastica è conservata una vasta gamma di prodotti alimentari.
PAN-DUR utilizza un vetro di sicurezza rinforzato (ESG - Enhanced Safety Glass) per i suoi componenti in vetro.
Per nascondere le antiestetiche giunzioni sigillate sui bordi del vetro e la tecnologia di refrigerazione vi vengono applicate delle strisce decorative opache. Fino ad oggi PAN-DUR utilizzava a questo scopo la serigrafia, che richiedeva però uno stencil o template per ogni colore, misura o variazione nel design.
Maggiore flessibilità, minori costi
L’applicazione di vernice ad alta definizione dei bordi e senza overspray con EcoPaintJet consente a PAN-DUR di evitare il complesso processo serigrafico, aumentando la flessibilità e la velocità produttiva e riducendo i costi di verniciatura. Ogni contorno viene semplicemente programmato e applicato nel colore desiderato all’area predefinita corrispondente, senza dover prima mascherare le superfici in vetro, eliminando la complessa e costosa produzione di template singoli, nonché la necessità di trovare lo spazio per conservarli.
Un unico riferimento per l’intera gamma di tecnologia di processo
Dürr ha fornito a PAN-DUR non solo l’applicatore, bensì tutta la tecnologia di processo, dal sistema di estrazione della vernice dai contenitori fino al sistema di alimentazione della stessa all’applicatore. Tra i componenti installati, il sistema di cambio colore e dosaggio Fluid Board, il sistema di pulizia dell’applicatore e l’unità di controllo EcoAUC. PAN-DUR ha sviluppato un portale multi-asse su cui montare la testa di
WATER RECOVERY
MINIMIZATION OF WASTE
TO BE DISPOSED OF REUSE OF DISTILLATE
DISPOSAL COST REDUCTION
ZLD: ZERO LIQUID DISCHARGE
Con EcoPaintJet sono possibili anche altre applicazioni industriali, per esempio nel settore del legno, nella produzione di finestre e cucine e nella verniciatura di veicoli ferroviari.
applicazione girevole e regolabile in altezza di EcoPaintJet, integrando senza problemi la tecnologia di processo. “Abbiamo collegato la tecnologia di Dürr alle nostre interfacce di sistema. L’implementazione non avrebbe potuto filare più liscia di così”, ha spiegato Jens Verhoef, responsabile sviluppo della tecnologia elettrica e di automazione presso PAN-DUR. La più grande sfida è stata trovare la giusta vernice da utilizzare sulle superfici in vetro. Anche l’azienda specialista in vernici Votteler, partner di lunga data di PAN-DUR, è stata coinvolta nello sviluppo. Il project manager Uwe Schmidt spiega: “Verniciare le superfici in vetro è molto complicato. Sono necessarie vernici appositamente sviluppate, le cui proprietà reologiche, di copertura e di distribuzione delle particelle siano perfettamente adattate al sistema. Questo sistema di verniciatura si può utilizzare anche su altri substrati. Abbiamo quindi dovuto fare un po’ di pratica prima di trovare la vernice giusta”.
Altri possibili utilizzi industriali
Con EcoPaintJet sono possibili anche altre applicazioni industriali, per esempio nel settore del legno, nella produzione di finestre e cucine e nella verniciatura di veicoli ferroviari. “Ovunque si potrebbe aver bisogno di applicare strisce dritte su superfici piane e questo tipo di verniciatura richiede ancora la mascheratura. Stiamo ricevendo molte richieste da svariati settori”, afferma Fabian Schilt, responsabile del team vendite industriali europee di Dürr. Un ulteriore vantaggio che rende l’intero sistema molto interessante per altri utilizzi è che tutti i suoi componenti sono di facile integrazione nei sistemi produttivi esistenti.
Per maggiori informazioni: www.durr.com
A cura di NOF METAL COATINGS EUROPE SA Creil, Francia inforfr@nofmetalcoatings.eu
NOF Metal Coatings presenta la gamma di finiture prive di PFAS.
IPFAS, o sostanze poli- (o per-) fluoroalchiliche, ampiamente utilizzate in diversi settori industriali, sono ora oggetto di un esame sempre più approfondito a causa della loro presenza duratura nell’ambiente. Un eventuale divieto europeo sui PFAS basati sul REACh potrebbe entrare in vigore già nel 2027 per specifici segmenti industriali.
A parte il PTFE, un fluoropolimero attualmente classificato come
“polimero a basso rischio” dall’Organizzazione per la Cooperazione e lo Sviluppo Economico (OCSE), nei prodotti di NOF Metal Coatings Group non sono utilizzati altri PFAS.
Indipendentemente dalle potenziali restrizioni imposte dalle autorità ambientali sul PTFE, l’azienda ha colto questa nuova normativa come un’opportunità per sviluppare una nuova generazione di topcoat privi di PFAS, disponibili in tutto il mondo.
Serie PLUS® senza PFAS
Gli obiettivi ambiziosi di questi sviluppi mirano a offrire ai clienti una nuova gamma di prodotti più rispettosi dell’ambiente, garantendo al contempo le stesse prestazioni tribologiche dell’attuale gamma PLUS®, la gamma di finiture più conosciuta:
PLUS® XL 2 Silver: COF 0,06 – 0,09 (ISO 16047)
PLUS® VLh 2 Silver: COF 0,09 – 0,14 (ISO 16047)
PLUS® ML 2 Silver: COF 0,10 – 0,16 (ISO 16047).
Applicate sui basecoat di zinco lamellare a base acquosa GEOMET® di NOF Metal Coatings Group, le alternative PFAS-free al PLUS® XL, PLUS® VLh e PLUS® ML soddisfano o superano i requisiti e le specifiche OEM globali, fornendo al contempo eccezionali proprietà tribologiche, tra cui:
Serraggio multiplo e serraggio ad alta velocità;
Compatibilità con vari substrati di accoppiamento (e-coat, alluminio, zinco e acciaio);
Evitano l’effetto stick slip;
Tenuta ai test di deserraggio (anche ad alta temperatura – PLUS® VLh 2 Silver e PLUS® ML 2 Silver).
Dall'alto:
PLUS® XL 2 Silver coefficiente di attrito secondo diversi standard.
PLUS® VLh 2 Silver applicato su E-coat (MBN 10544).
Total Finishing S stems is a leading designer and integrator of high-q alit and comple ind strial finishing s stems. Whether o need an in-depth process anal sis or req ire finishing eq ipment and components, o r eq ipment e ceeds e pecta ons and o r inno a on and a toma on is ind str leading.
Miglioramento estetico dei pezzi verniciati
Per offrire ai clienti i migliori prodotti sul mercato, NOF Metal Coatings Group ha colto questa opportunità per valorizzare l’estetica dei prodotti di questa nuova gamma aggiungendo pigmenti di alluminio, ottenendo così un colore argento uniforme. Questa valorizzazione migliorerà l’aspetto visivo degli assemblaggi in cui gli elementi di fissaggio sono visibili ai clienti. Oltre all’estetica migliorata grazie alla presenza di pigmenti di alluminio nel rivestimento, tutti e tre i nuovi topcoat PFAS-free includeranno pigmenti fluorescenti per facilitare l’identificazione positiva - una caratteristica esclusiva dei topcoat del Gruppo NOF Metal Coatings.
In cammino verso un futuro più verde
Nel frattempo, nei laboratori di ricerca e sviluppo dell’azienda, il team di NOF Metal Coatings Group continuano a lavorare su rivestimenti privi di PFAS e sistemi GEOBLACK®, con l’aggiunta di topcoat neri alla gamma PLUS® PFAS-free, per essere pronti prima della fine dell’anno.
Dall'alto:
PLUS® VLh 2 Silver applicato su alluminio (MBN 10544).
PLUS® ML 2 Silver test stick-slip a 300 giri/ min. su E-coat (vite flangiata M10).
Our 70 years experience in Surface Treatment is ready for the E-Mobility market.
Research, innovation, development.
In 70 years, our vision towards the future has never stopped. Today, Tecnofirma provides quality to the electric market which is the most evolving technology in the automotive industry. Our impregnation, cleaning and painting plants are the result of the constant commitment to offer cutting-edge solutions and products anytime, anywhere.
Da un’intervista con Gianluca Zanardo e Cristian Sala Vernici Caldart – Bellusco (MB), Italia gianluca.zanardo@vernicicaldart.it; cristian.sala@vernicicaldart.it
Da piccola azienda specializzata in vernici per cartoline, Vernici Caldart ha attraversato un percorso caratterizzato da ricerca e innovazione che le ha permesso di espandersi in tutto il mondo, divenendo un punto di riferimento per molteplici settori industriali.
L’industria chimica italiana è uno dei pilastri dell’economia del Paese e rappresenta un settore altamente competitivo e tecnologicamente avanzato. In questo contesto si colloca Vernici Caldart, un’azienda specializzata nella produzione di vernici industriali
liquide. Fondata oltre cinquanta anni fa, Vernici Caldart ha saputo crescere e innovare, conquistando una posizione di rilievo a livello nazionale e internazionale.
L’azienda si è evoluta grazie alla continua ricerca di soluzioni avanzate e
personalizzate per i suoi clienti, distinguendosi nella produzione di vernici di elevata qualità per diversi settori, tra cui occhialeria, automotive, general industry, cosmetica, packaging e metallizzazione. Grazie a un know-how consolidato e alla presenza di laboratori di ricerca, Vernici Caldart è inoltre in grado di sviluppare vernici ad alte prestazioni per ogni tipo di materiale, tra cui metallo, plastica e vetro. Abbiamo intervistato Gianluca Zanardo e Cristian Sala, amministratori e rispettivamente International Sales Director e Direttore Commerciale Italia, per comprendere meglio le caratteristiche vincenti di Vernici Caldart e la sua evoluzione.
Ci potete descrivere brevemente la storia di Vernici Caldart?
Gianluca Zanardo: “L’azienda fu fondata nel 1976 da Carlo Caldart, imprenditore di origini bellunesi. Inizialmente dedicata alla produzione di vernici per cartoline, era descritta sulle Pagine Gialle come ‘produttrice di vernici speciali’. Proprio questa caratteristica attirò l’attenzione di un’azienda leader del settore dell’occhialeria nei primi anni ‘80, che cercava un fornitore in grado di produrre vernici per i suoi prodotti. Alla domanda ‘Producete vernici per occhiali?’, il nostro fondatore rispose: ‘No, ma ci possiamo provare’, frase che ancora oggi rappresenta il nostro spirito aziendale. La storia di Vernici Caldart è stata, e continuerà ad essere, caratterizzata da una costante ricerca e sviluppo, sempre orientata a soddisfare le esigenze dei nostri clienti”.
Com’è strutturata oggi Vernici Caldart?
GZ: “All’interno dell’azienda si sono oggi sviluppate aree di eccellenza specifiche, come i nostri laboratori di ricerca e sviluppo e di controllo qualità. Grazie alle competenze del nostro servizio tecnico, all’utilizzo di materie prime di elevata qualità e a processi produttivi all’avanguardia, sviluppiamo prodotti vernicianti ad alte prestazioni impiegati in molteplici mercati. Tutto ciò combinando una qualità estetica unica e in grado di valorizzare le
superfici con le caratteristiche tecniche richieste da ciascun utilizzo finale”.
Cristian Sala: “Oltre alla sede storica di Bellusco (MB) – che si occupa di ricerca sviluppo, produzione e spedizione per conto delle divisioni dedicate al mercato dell’occhialeria e dell’industria cosmetica – disponiamo anche dello stabilimento di Pojana Maggiore (VI), dedicato alla divisione Industry / Car Refinish. Gestiamo inoltre un deposito in Puglia e uno in Sicilia, e possiamo contare su una rete di agenti e rivenditori che coprono capillarmente il territorio italiano, rappresentante circa il 75% del nostro fatturato annuale. Per quanto riguarda l’estero invece, siamo attivi in Francia, Spagna, Polonia, Turchia, USA, Brasile, Argentina, Tailandia e Cina”.
Quali sono i vostri settori di riferimento?
CS: “Siamo specializzati nella produzione di vernici e sistemi tintometrici polivalenti –costituiti da leganti e paste coloranti a base solvente e acqua – per l’industria generale, ma siamo anche rinomati per l’eccellenza nel settore dell’occhialeria. Ad oggi siamo infatti i
primi produttori mondiali di vernici per occhiali in plastica e metallo, oltre che di vernici per dispositivi di protezione individuale ad uso professionale e sportivo, come maschere e caschi da sci e motocross in PVC e poliuretano. Le nostre vernici sono utilizzate anche nei settori della cosmetica, del beverage, degli accessori di moda, della componentistica auto e dei complementi d’arredo e illuminazione. Inoltre, la nostra tecnologia è utilizzata nel campo della bigiotteria e per piccoli accessori come fermacapelli, spille e fibbie, oltre che per realizzare la finitura perfetta per contenitori, tappi, flaconi e bottiglie di vario tipo”.
CS: “Siamo anche leader nella produzione di vernici utilizzate nei cicli e nei processi di metallizzazione, sputtering e PVD, una tecnologia a basso impatto ambientale che si sta espandendo molto rapidamente. Grazie alle sue particolari caratteristiche, questa tecnologia è infatti in grado di sostituire i cicli tradizionali di rivestimento galvanico e riesce ad essere molto performante su diverse tipologie di supporto, dai materiali plastici come ABS e PP ai supporti metallici, fino a quelli in vetro. Un’altra soluzione
ampiamente richiesta è la nostra serie EFT di vernici ad effetto cromo –prodotti monocomponenti e bicomponenti ad adesione diretta su plastica e metallo disponibili in un'ampia gamma di colori come grigio, argento, blu, rosso, verde, oro e rosato. Questo portfolio rappresenta una valida alternativa nella creazione di superfici ed effetti visivi di alta qualità e a bassissimo impatto ambientale, poiché riproducono fedelmente gli effetti cromo, argento, rame, bronzo, nickel e titanio”.
E gli elementi distintivi della vostra offerta?
GZ: “Uniamo quotidianamente l’impulso creativo alla capacità di interpretare le ultime tendenze, investendo nella tecnologia che ci consente di produrre vernici industriali di alta qualità a costi competitivi e con un servizio clienti efficiente. Riponiamo anche la massima attenzione al rispetto e alla tutela della salute degli utilizzatori e dell’ambiente”.
CS: “La nostra produzione si fonda sulla ricerca e sullo sviluppo di prodotti nel pieno rispetto delle norme vigenti in materia di tutela dell’ambiente e della salute. Al fine di soddisfare le aspettative dei clienti e delle parti interessate, noi di Vernici Caldart abbiamo infatti implementato un sistema di gestione della qualità, uniformandoci ai requisiti della normativa UNI EN ISO 9001:2015. Inoltre, fin dall’inizio della nostra storia aziendale, siamo stati caratterizzati dall’estrema flessibilità produttiva: sviluppiamo nuovi prodotti vernicianti in continuazione, perché cerchiamo di personalizzare la produzione a seconda delle specifiche esigenze di ciascun cliente. Infatti, di recente abbiamo ampliato lo spazio dedicato ai laboratori di ricerca e sviluppo e assunto nuovo personale, per far evolvere la struttura sia a livello produttivo che manageriale”.
GZ: “Il nostro stabilimento di Pojana Maggiore, situato in Veneto, rappresenta un asset fondamentale per la nostra flessibilità operativa.
Specializzato nella produzione di prodotti per la macinazione, paste e sistemi tintometrici, utilizza tecnologie moderne conformi ai principi dell’Industria 4.0. Recentemente, il sito è stato ampliato con l’aggiunta di nuovi magazzini e un reparto produttivo all’avanguardia, permettendoci di ottimizzare la produzione di lotti di vernice, migliorando la capacità di adattamento ai volumi e alle richieste personalizzate. Questo ci consente di garantire un servizio rapido e di offrire soluzioni vernicianti su misura. A supporto, abbiamo inoltre creato un centro tecnico con un’area formativa strategica per trasmettere competenze ai clienti tramite sessioni di formazione specializzata”.
L’ampliamento del vostro portfolio di prodotti e di servizi offerti è quindi il motore che ha trainato la vostra crescita?
CS: “Parallelamente, abbiamo sviluppato una struttura aziendale solida che ci ha permesso di espandere la nostra rete commerciale e distributiva, investendo significativamente anche nella formazione interna. La reputazione dei nostri prodotti, diffusa attraverso il passaparola sulla loro qualità e performance, ha contribuito ulteriormente alla nostra crescita. Nel 2005, il fatturato superava i cinque milioni di euro, e da allora è cresciuto costantemente, raggiungendo i sedici milioni nel 2017 e toccando i trenta milioni nel 2023, anno in cui è stato avviato il closing con il fondo Itago SGR S.p.A.”.
Potete entrare più nel dettaglio riguardo a questa acquisizione e ciò che comporta per l’azienda?
CS: “Prima dell’ingresso del fondo Itago SGR, Vernici Caldart aveva registrato il suo record storico di fatturato, pari a trenta milioni di euro. Tuttavia, all’interno della famiglia Caldart emergeva il timore che la
mancanza di un passaggio generazionale potesse portare a una fase di stagnazione. L’offerta del fondo Itago SGR ha quindi rappresentato non solo un’opportunità di capital gain per la famiglia, ma anche una strategia per assicurare la continuità e il futuro potenziale di crescita dell’azienda".
GZ: “Il fondo ha manifestato interesse per l’acquisizione all’inizio del 2023, riconoscendo il nostro costante trend di crescita e il significativo potenziale dell’azienda. Dopo un’analisi approfondita dei nostri business plan, ha condiviso le strategie pianificate e deciso di co-investire nella società, supportandoci nello sviluppo e nella strutturazione aziendale. Con il closing finalizzato a maggio 2024, sia io [Gianluca Zanardo, ndr] che Cristian Sala siamo stati nominati amministratori e coinvolti nell’azionariato, avviando un piano di crescita che prevede l’espansione del personale tecnico, amministrativo e commerciale per sostenere questa nuova fase di sviluppo".
CS: “In sintesi, i cambiamenti interesseranno unicamente gli aspetti organizzativi interni, poiché il fondo ha riconosciuto la nostra competenza manageriale, assicurandoci totale autonomia nella gestione operativa”.
Per concludere, cosa prevedete quindi per il futuro di Vernici Caldart?
CS: “Vogliamo assolutamente mantenere la nostra posizione di partner flessibile e affidabile per l’industria, capace di offrire soluzioni innovative e di alta qualità grazie alla nostra ampia gamma di prodotti e all’attenzione alla ricerca, al fine di consentire ai clienti di beneficiare di un servizio altamente specializzato e vernici personalizzate per ogni esigenza produttiva”.
GZ: “Ci impegniamo anche verso una continua innovazione del prodotto e l’evoluzione tecnologica, ponendo l’attenzione sulle normative di legge in costante mutamento, nel rispetto della salute degli utilizzatori e dell’ambiente. Altri punti importanti per noi sono lo sviluppo, l’ottimizzazione dei processi e del know-how. Inoltre, il mercato ci sta ricercando anche per altri settori in cui non siamo attualmente interamente esposti, perché consapevole delle nostre competenze. Stiamo infatti assistendo ad un aumento di fatturato proveniente dal settore automotive, che vorremmo incrementare ulteriormente. Stiamo investendo in modo significativo per ampliare la produzione di vernici liquide a base acqua e a essiccazione UV, rispondendo alla crescente richiesta di soluzioni eco-sostenibili da parte dell’industria. Questo impegno riflette la nostra forte sensibilità verso le tematiche ambientali e il nostro ruolo proattivo nel guidare il cambiamento verso processi produttivi più sostenibili, senza mai compromettere la qualità e l’innovazione”.
Adriano Antonelli
Tecno Supply - Ibix Srl, Lugo (Ravenna) – Italia adriano.antonelli@tecnosupply.com
Oggi più che mai la questione del risparmio energetico ottenibile grazie al massimo efficientamento del processo produttivo, in generale, e del reparto di verniciatura, in particolare, è all’ordine del giorno: in questa analisi dettagliata Adriano Antonelli, responsabile commerciale di Ibix Srl – Tecno Supply, ci spiega come, attraverso uno studio attento dei sistemi di appensione dei pezzi, sia possibile ridurre le risorse energetiche impiegate durante il processo di verniciatura, abbattendo i costi e aumentando l’efficienza della linea.
Si sta concludendo un’epoca di equilibri e contrappesi che ha permesso all’economia internazionale di operare in un tessuto socio-economico stabile, garantendo le condizioni per una crescita costante e progressiva sul lungo periodo. Soprattutto l’Europa ha potuto godere di materie prime come gas naturale e petrolio a prezzi competitivi dalla Russia e dai Paesi nord-africani. L’assenza di turbolenze ha consentito l’approvvigionamento economico, senza la necessità di aperture da parte di nuovi fornitori e infrastrutture. Il mercato cinese ha permesso di acquistare molti prodotti come se ci trovassimo in una
condizione deflattiva. Prodotti a basso valore aggiunto nel campo tessile e della componentistica, per esempio, sono stati delocalizzati sfruttando la manodopera e normative poco stringenti rispetto a quelle dell’UE. La supremazia americana e la sua politica internazionale ha permesso un equilibrio nelle zone più instabili evitando possibili interventi militari. La problematica climatica, anche se già in essere, non era un argomento così forte e impellente nell’opinione pubblica e non poteva in nessun modo influenzare a livello normativo e, dunque, a cascata, la vita dei cittadini e i processi aziendali.
Tutto ciò sembra che si sia sgretolato in pochi anni. Il mercato cinese ha una crescita considerata debole: la politica cinese internazionale aggressiva attuata attraverso gli aiuti di stato, ha inondato i mercati europei con i suoi prodotti. Purtroppo, non si tratta più di prodotti di fascia bassa ma soprattutto di beni con valore aggiunto come i pannelli solari e, in un prossimo futuro, le auto elettriche, che sono due esempi significativi di come la vendita sottocosto, sostenuta dal contributo statale, stia distruggendo tessuti nazionali industriali europei storici e strategici. La politica americana sembra ormai cambiata e sta virando verso una maggiore attenzione ai propri confini nazionali rispetto a quelli internazionali. Uno slogan del precedente Presidente “American First” ha fatto da spartiacque con il passato. Non più investimenti per poter essere gli sceriffi internazionali, ma progetti per sostenere la propria economia e gli affari interni. Il ritiro di truppe da Paesi da stabilizzare e soprattutto da progetti di cooperazione internazionali sono le conseguenze delle scelte delle nuove amministrazioni. La mancata desistenza da interventi militari ha provocato l’inizio di micro-guerre in aeree strategiche come quella russo-ucraina e mediorientale. Le sanzioni inflitte ad alcuni Paesi e l’instabilità governativa hanno ridotto la fornitura delle materie prime, così importanti per la nostra economia. La questione climatica e le scelte consequenziali della politica stanno portando ad alcune normative a volte discutibili. Imporre entro una determinata data l’utilizzo dell’auto elettrica, senza la possibilità di sviluppare tecnologie alternative per poter raggiungere lo stesso obiettivo – ossia quello della riduzione delle emissioni - potrebbe voler dire consegnarsi totalmente per i prossimi decenni al mercato cinese, in posizione molto più avanzata rispetto a quello occidentale. Questo provocherebbe la perdita di posti di lavoro e competenze in molti aspetti e in determinati segmenti di mercato. Alcuni
allarmi in essere stanno innervosendo i mercati finanziari: sembra che il rischio di recessione sia alle porte. Fino a poco tempo fa, per esempio, si sarebbe pronosticato un atterraggio morbido (soft landing) dell’economia americana, mantenendo il costo del denaro pressoché stabile, con un mercato del lavoro forte e ai massimi livelli. Questo dato però è stato disatteso dalle ultime rilevazioni e la riduzione percentuale del monte acquisti dei buyer a stelle e strisce nell’ultimo trimestre sono segnali che hanno innervosito le Borse.
Il cambiamento climatico impone, però, ulteriori azioni correttive nelle nostre aziende. La riduzione delle emissioni, l’efficientamento della produzione e la necessità di una transizione sono azioni ormai impellenti. Questo viene richiesto dalle normative, dal mercato, dai clienti e dalla possibilità di incrementare i profitti. I futuri partner saranno selezionati in base a chi potrà garantire un passaporto di efficienza ambientale. L’efficienza energetica è un tema che va oltre la pura questione ambientale, perché – prima di tutto - è entrato in modo preponderante nelle normative europee e nazionali. Per esempio, da non sottovalutare e da studiare in modo dettagliato è il Piano di Transizione 5.0 recentemente diffuso. Il programma mira a sostenere gli investimenti nella transizione green attraverso i crediti d’imposta. Sarà premiato chi riuscirà nell’intento di ridurre i consumi energetici delle proprie unità produttive. Inoltre, saranno sostenuti gli investimenti per l’autoproduzione di energia da fonti rinnovabili e la formazione del personale finalizzata al consolidamento delle conoscenze e delle tecnologie in ambito green. Il Decreto ha l’intento di aiutare le aziende nelle sfide della digitalizzazione e dell’ecocompatibilità in cui probabilmente si ridisegneranno gli equilibri economici internazionali. Inoltre, il credito d’imposta verrà riconosciuto agli investimenti in strutture produttive sul territorio nazionale che
saranno innovative nell’ambito della riduzione delle risorse energetiche.
La massima efficienza in verniciatura
Analizziamo quest’ultimo aspetto, partendo da come è possibile essere efficienti e sostenibili nel reparto di verniciatura. L’obiettivo è incrementare la densità e, dunque, riuscire a riempire la linea produttiva. Ma, prima di
affrontare le soluzioni per poter aumentare l’efficienza del processo di verniciatura, andiamo a verificare i consumi e i valori della CO2 nei processi di trattamento superficiale, anche se in questo articolo possiamo farlo solo in modo generico e indicativo.
La linea di verniciatura emette CO2 a causa del consumo di energia nei vari processi di pretrattamento, verniciatura, cottura, etc… La fonte può essere elettrica, una combinazione
di elettricità e gas, gasolio o GPL. A seconda della combinazione e del modo in cui l’energia viene prodotta, l’impronta sull’ambiente cambia in modo determinante. L’elettricità alimentata dal carbone, per esempio, produce emissioni di CO2 oltre 30 volte superiori a quelle dell’energia idroelettrica. Le vernici in polvere possono avere un peso determinante nel calcolo della CO2 prodotta dal ciclo produttivo, a seconda della densità di appensione (fig. 1). Infine, l’appensione con ganci e attrezzature può determinare calcoli di emissioni completamente diversi. L’utilizzo di appropriate attrezzature può cambiare l’efficienza e, quindi, il risultato finale.
Il
Che cos’è dunque il Green Effect HangOn?
Grazie ad una soluzione di appensione intelligente che possa consentire la massima densità, si raggiungerebbe l’obiettivo di riempire la linea e incrementare la quantità di pezzi che si possono rivestire in un unico ciclo produttivo. É necessario tenere in considerazione che l’80-90% del consumo energetico in un ciclo di rivestimento è costante, indipendentemente dalla quantità di merce rivestita. Dunque, aumentare la densità di appensione permette di ridurre i consumi di CO2 per prodotto verniciato, quindi, i costi e, di conseguenza, di aumentare i profitti.
Quali tipologie di appensione possono essere approcciate per determinare una transizione green nel proprio ciclo di verniciatura? Un esempio è il nuovo sistema HQW D, un telaio ad albero con diametro di 2 mm, che presenta punti di appensione fissi (fig. 2). La gamma è ampia, perciò è possibile scegliere il passo che si desidera. Per avere un telaio compatto, anche nella confezione, come, per esempio, una scatola di ganci, l’appensione superiore dovrà essere effettuata aggiungendo un proprio gancio alla sommità. Il telaio è pensato per essere utilizzato nel momento in cui si presenti una necessità improvvisa e per evitare l’appensione gancio su gancio. Questo è un punto fondamentale perché l’appensione a
“catenella” permette, oltre a un tempo di appensione maggiore, un numero di pezzi notevolmente minore rispetto alla soluzione HQW D. Sul sito www.hangon.it è possibile visualizzare, oltre ai fogli di calcolo, che consentono di testare i risparmi che si possono ottenere inserendo i propri dati, anche i video, che offrono un’idea dell’applicazione. Il costo, che per ogni punto di appensione è paragonabile a quello del gancio singolo (e quindi il totale è inferiore a 1 euro), non pone il problema della rigenerazione. Il nuovo sistema HQW S (fig. 3), invece, è completo di gancio superiore orientato sia a 0 che a 90° e i ganci hanno una distanza variabile. Questo tipo di telaio economico permette di evitare appensioni improvvisate con ganci che determinano una perdita di densità e di efficienza. Il gancio con diametro di 2 mm e il rinforzo per tutta la lunghezza del telaio garantiscono stabilità nell’appensione. Un’ulteriore soluzione che permette la massima flessibilità è il sistema Flexi Frame (fig. 4). L’ idea è quella di avere un telaio completamente smontabile e stoccabile a scaffale. Il telaio è formato da una barra a “T” dove sono posizionate due spalle orizzontali porta-barre. All’interno possono essere alloggiate le barre HQL, HCL BHL, H11B e HQS.
Il telaio è stato pensato per essere sempre disponibile a stock e utilizzato al momento di necessità urgente.
I vantaggi sono molteplici:
risparmio dello spazio in magazzino e riduzione dei problemi di immagazzinamento;
minori costi di trasporto anche se ‘una tantum’;
facilità di movimentazione;
flessibilità e compattezza;
self-locking;
possibilità di personalizzazione secondo necessità;
costo basso.
L’ultimo arrivato: il telaio HQS
Il telaio HQS (fig. 5) è caratterizzato da lamelle metalliche per poter appendere dai singoli pezzi fino ai profili. Il gancio centrale da 4 o da 5 mm permette una resistenza del telaio nel suo complesso fino a 100 kg. Questo telaio è stato da poco lanciato sul mercato con varie tipologie di ganci, grazie ai quali ogni cliente potrà avere a disposizione la configurazione più adatta al proprio utilizzo specifico. La lunghezza dell’albero può arrivare fino a 2400 mm, lo spessore della lamiera è di 1 mm e l’altezza di 18 mm. È possibile, inoltre, realizzare diverse configurazioni: lamelle solo da una parte (dunque tranciate), a zig zag o piegate da 0 a 180°. Pensato per evitare l’appensione singola, questo telaio prodotto in modo automatico permette un costo contenuto, al pari del singolo gancio. Le nuove configurazione proposte permetteranno all’utilizzatore di trovare la forma del gancio adeguata al pezzo da appendere. Un’altra novità è l’adattatore che permette di allungare il telaio HQS utilizzando ganci standard o disponibili al momento. Il telaio HQS ha numerose applicazioni, dall’appensione di minuteria o pezzi più o meno pesanti fino all’appensione di profili.
electrostatic systems for liquid painting
electrostatic systems and spraying booths for powder coating
pneumatic systems for high-, medium-, and low-pressure painting
robot and reciprocators IR and UV drying systems
Caratteristiche delle barre
La barra HQL (fig. 6) è prodotta in modo completamente automatico, riducendo i costi senza la preoccupazione di gestirne la rigenerazione. Il gancio con diametro di 1 mm viene inserito nella barra in modo doppio, per appendere i pezzi simmetricamente. Per esempio, nella barra HQL 800X33 sono agganciati 46 ganci per una lunghezza di 800 mm. La barra può essere inserita nel sistema universale HCF. In questo modo il sistema è modulare ed è possibile inserire le barre in base alla lunghezza del pezzo. Il cappuccio HQL
G6 permette inoltre una perfetta elettrostaticità. Oggi è disponibile anche la barra con gancio da 1,5 mm, sempre in acciaio armonico, per pezzi con pesi importanti nel campo della minuteria. Nella gamma sono disponibili anche configurazioni particolari, come, per esempio, quelle a tripla piega, perché i pezzi leggeri potrebbero volare via durante il pretrattamento: la tripla piega permette, infatti, un ancoraggio più sicuro. Sono disponibili anche le barre HQL con appensione solo da una parte, nel caso sia necessario appendere solo da un lato ed evitare ombreggiature e problematiche di ogni sorta.
I vantaggi dell’utilizzo di questa barra sono molteplici:
risparmio di tempo: si può essere fino a 30 volte più veloci rispetto all’utilizzo di un singolo gancio;
segno minimo dei ganci;
materiale in acciaio armonico;
possibile fornitura di barre con configurazione di ganci speciali;
imballaggio intelligente per ridurre i costi di trasporto.
Una versione più robusta della barra sopra citata è l’HQC. La barra alloggia ganci con un diametro di 1,5 mm, ma solo da un lato, e ha un innesto che permette di inserirli in un gancio centrale con diametro da 10 mm. Il portabarra R 58 permette la stabilità della barra e la possibilità di estrarla in modo semplice, anche grazie al cappuccio BH G 20. Il telaio risulta economico e flessibile, dato che è possibile saltare i livelli. I ganci hanno una distanza di 50, 75 e 100 mm. Anche questa tipologia di barra è stata pensata per evitare di utilizzare il singolo gancio. In questo modo si potrebbero ridurre in modo drastico i tempi di appensione da parte dell’operatore: infatti, con il telaio pronto all’uso, si evita la gestione dei ganci singoli. Inoltre, il telaio permette una facile pre-appensione fuori linea. Il vantaggio del telaio è quello di poter essere utilizzato per molteplici configurazioni di pezzi da appendere. La tecnologia di produzione della barra ha permesso di avere un costo simile a quella del gancio e questo permette di evitare l’eventuale aggravio di costi nell’acquisto del telaio rispetto al gancio standard. Inoltre, per rendere il telaio più versatile, è stato lanciato il nuovo adattatore metallico che permette di inserire anche la barra H11B. In questo modo, utilizzando lo stesso gancio centrale, è possibile alloggiare una barra che permette di inserire un gancio fino a 4 mm di diametro e ottenere una flessibilità orizzontale. La barra H11B è una barra punzonata dove il gancio alloggia all’interno: in questo modo il punto di contatto resta pulito e protetto ed è possibile cambiare in modo flessibile il gancio di appensione quando necessario. Con la stessa barra si possono utilizzare ganci standard o ganci gemelli, che riescono a inserirsi tra le due punzonature e a rimanere fissi. Per quanto riguarda i ganci gemelli, è
possibile piegare qualsiasi configurazione e, dunque, offrire una maggiore flessibilità. La barra risulta resistente ed è stato stimato e pubblicato da HangOn quanto una barra può sostenere, a seconda della lunghezza.
Questa tipologia di appensione è stata pensata anche nella versione più robusta H2B, H25B e H3B. In questo modo le barre possono alloggiare ganci fino a 10 mm di diametro. All’estremità di queste barre, possono essere saldati dei ganci per la costruzione di un telaio a “T”. Questo permette la stabilità dei pezzi e la modularità di inserire il gancio dove necessita, senza perdere la conducibilità.
La barra HCL presenta alloggiamenti dove è possibile inserire molle, ganci formati con il tondino o con la lamiera. L’estremità è protetta con un cappuccio di silicone che permette la facile estrazione e garantisce la conducibilità.
La barra può avere alloggiamenti sia singoli che doppi per aumentare la densità di appensione. Il sistema risulta estremamente flessibile e
permette una riduzione della proliferazione dei telai costruiti per ogni pezzo da verniciare. Gli accessori possono essere costruiti “ad hoc” a seconda dei pezzi. All’interno del porta-gancio possono essere alloggiate 2 molle con un’uscita a 4 estremità. La barra può essere utilizzata anche per la verniciatura in cataforesi grazie ad un sistema di cappucci che permette la protezione delle estremità ed evita che la vernice cataforetica risalga.
La flessibilità dei telai universali HCF permette dunque di avere bilancelle con le barre intercambiabili, e, in alcuni casi, barre con accessori inseribili, a seconda del pezzo da appendere. Tutto ciò comporta una riduzione significativa del parco telai necessario per i differenti articoli, una riduzione degli spazi occupati per lo stoccaggio e una riduzione delle problematiche per la loro movimentazione. Il telaio universale può essere utilizzato anche per cataforesi. La struttura rimane tale ma cambiano le barre e gli accessori per permettere
Figura 7 - Nei casi in cui non sono utilizzate vernici metallizzate e dove è permesso avere un “tassello” non verniciato in una delle due facce del pezzo metallico, è possibili utilizzare il magnete.
Figura 8 - Oltre alla gamma HangOn prodotta in modo automatico e standardizzato, è possibile costruire telai, ganci e sistemi ad hoc, secondo le necessità del cliente.
la massima conducibilità. Nella gamma sono disponibili barre già saldate con ganci quadro; questo permette di avere il minimo contatto. Per avere una maggiore flessibilità, sono disponibili dei porta-ganci dove è possibile inserire accessori quadro e, nella parte superiore, i cappucci di protezione.
Caratteristiche dei magneti
Un’altra applicazione interessante di appensione è l’utilizzo di magneti (fig. 7). Nei casi in cui non si utilizzino vernici metallizzate e dove è permesso avere un “tassello” non verniciato in una delle due facce del pezzo metallico, è possibili utilizzare il magnete per l’appensione. Questo sistema permette di essere veloci in questa delicata fase preparatoria e risolvere le problematiche operative, soprattutto quando non ci sono fori. Nella gamma ci sono molteplici magneti, a seconda dei pesi che si devono sostenere. Il magnete è sempre coperto da una mascheratura in silicone per evitare che si sporchi.
Oltre alla gamma HangOn prodotta in modo automatico e standardizzato, è possibile costruire telai, ganci e sistemi ad hoc, secondo le necessità del cliente (fig. 8). Le soluzioni di appensione e mascheratura in un’unica soluzione permettono di ridurre i tempi ed evitare manipolazioni eccessive del prodotto. In questo modo si raggiungono gli obiettivi di qualità richiesti, senza tralasciare la densità e la velocità di appensione.
Caratteristiche dei carrelli
La costruzione di carrelli permette la possibilità di gestire il processo del trattamento (fig. 9). Questo aspetto è divenuto fondamentale per ridurre
Figura 9 - I carrelli HangOn sono modulari e flessibili: sono, infatti, componibili in base alla tipologia di telaio utilizzato.
i tempi e aumentare la densità. Un’appensione in linea potrebbe risultare poco efficiente in termini di densità, perché nei tempi di movimentazione dell’impianto non si riuscirebbe a riempire in modo adeguato l’ipotetico m3. I carrelli possono permettere una pre-appensione e movimentazione adeguate all’interno dell’azienda. I carrelli HangOn sono stati studiati per essere modulari e flessibili: sono, infatti, componibili in base alla tipologia di telaio utilizzato. Nel caso in cui dovessero essere sostituiti e avere attacchi o dimensioni diversi, il carrello si adatta alle varie esigenze. Ha così una duplice funzione: quella di permettere una pre-appensione e portare tutte le bilancelle sulla linea di verniciatura e quella di stoccare in modo ordinato i telai non utilizzati. A partire dai componenti è possibile studiare carrelli speciali, in base alle varie esigenze.
Un nuovo strumento di calcolo
Uno strumento utile è il nuovo software di calcolo CCC presente sul sito www.hangon.it per tramutare le idee in numeri e confrontare due sistemi di appensione. É possibile inserire qui i dati commerciali - dal costo delle vernici in polvere alle persone utilizzate in linea, al costo dell’impianto, alle tempistiche del processo - e visualizzare e confrontare i costi di appensione.
La struttura Italiana distributiva e tecnica di Tecno Supply divisione Ibix è caratterizzata da una capillare presenza sul territorio nazionale che le permette un’assistenza puntuale e un supporto immediato per tutte le questioni tecniche e commerciali che dovessero sorgere presso chi vernicia.
Lavaggio Industriale
Lavaggio di precisione
Sgrassanti interoperazionali
Miscele di tensioattivi
Protezione temporanea
Galvanica Funzionale
Zinco e leghe di zinco
Passivanti e Sigillanti
Rivestimenti resistenti all'usura
Pretrattamento
SurTec Italia Sas di Externa Holding Srl
Via Boito, 251 Tel.: +39 059 8579901
41019 Soliera (MO) E-Mail: info-it@surtec.com Italia Web:www.SurTec.com
Pretrattamento metalli alla verniciatura
Processi di conversione esenti
Cromo e Fosfati
Fosfatanti a bassa temperatura
Passivanti per acciaio zincato a caldo
Passivazione conduttiva su
Alluminio TCP
Galvanica Decorativa
Rame, Nichel e Cromo
Deposizione su plastica (POP)
Stagno e leghe di Stagno
Pretrattamento
Da un’intervista con Alfredo Pellegrino
Defil Srl - Sesto San Giovanni (Milano), Italia
Defil Srl, azienda specializzata nel settore della filtrazione, depolverazione e trattamento dell’aria per impianti civili e industriali dal 1985, negli ultimi due anni ha investito in nuovi macchinari per la produzione dei filtri, tra cui recentemente un nuovo pieghettatore elettronico 4.0 con abbinato un nuovo tagliere longitudinale, migliorando così i propri standard qualitativi e riducendo i tempi di lavorazione, garantendo al contempo una riduzione degli sprechi delle materie prime.
Il settore della filtrazione per la verniciatura industriale è in forte espansione, alimentato dalla crescente richiesta di soluzioni sostenibili che ottimizzino l’efficienza produttiva e riducano l’impatto ambientale. In questo contesto, Defil Srl di Sesto San Giovanni, Milano, si distingue come un importante player sul mercato. Fondata da Nicola Pellegrino nel 1985, l’azienda ha inizialmente concentrato le proprie attività sulla distribuzione e commercializzazione di diversi sistemi filtranti, che spaziano dai semplici materassini per le cabine di verniciatura a gruppi filtranti completi.
Nel corso degli anni Defil ha saputo evolvere, anche grazie alla professionalità del proprio staff e dei partner, puntando sempre su innovazione e qualità, passando da ditta commerciale a produttore di filtri a proprio marchio o, su richiesta, a marchio della propria clientela. “Oggi, Defil offre soluzioni di filtrazione su misura per una vasta gamma di
settori, tra cui verniciatura, automotive, farmaceutico/chimico, alimentare, cosmetico, energetico e condizionamento (questi sono solo alcuni dei settori in cui è possibile trovare prodotti Defil). Operiamo sia sul mercato nazionale che internazionale, con una forte presenza in Spagna, Francia, Portogallo e Russia, dove collaboriamo con distributori locali per espandere la nostra rete commerciale,” spiega Alfredo Pellegrino, Responsabile commerciale di Defil.
Investimenti in ottica 4.0: la nuova pieghettatrice elettronica
L’integrazione di tecnologie 4.0 sta trasformando la produzione industriale, rendendo i processi più efficienti e personalizzabili. Defil, con un focus costante sull’innovazione, ha recentemente compiuto un importante passo in avanti in questa direzione, dotandosi di una nuova
pieghettatrice elettronica con relativa taglierina accoppiata.
“Abbiamo acquistato questa macchina per la realizzazione dei pieghettati delle cartucce filtranti, consentendoci di offrire una maggiore flessibilità nella produzione di filtri e ridurre significativamente i tempi di lavorazione. Si tratta di un sistema versatile, che ci consente di produrre componenti con altezze e spessori variabili. Grazie alla tecnologia 4.0, possiamo cambiare velocemente le ricette di produzione, e controllare in tempo reale lo scarico delle materie prime, consentendoci così di ridurre i tempi di pieghettatura/taglio dei setti filtranti e, di conseguenza, migliorare la qualità del processo, in alcuni casi azzerando gli scarti dei setti filtranti,” spiega Alfredo Pellegrino.
“In passato, per delle specifiche produzioni ci affidavamo a dei partner esterni che eseguivano delle lavorazioni su nostri disegni ed esclusivamente con nostre materie prime: stiamo cercando di limitare al massimo queste procedure, per abbattere i costi e aumentare la nostra competitività,” spiega Paola Pellegrino, Responsabile Qualità e Acquisti materie prime di Defil.
Qualità del prodotto
“La nostra società è molto attenta a ottenere una qualità produttiva
Le bobine di alimentazione della pieghettatrice (foto di sinistra) e i setti all’interno della pieghettatrice.
Il touch-screen della nuova pieghettatrice 4.0 e le strutture metalliche che contengono i setti filtranti.
di buon livello, con l’obbiettivo di soddisfare al meglio le esigenze e le richieste dei propri clienti. Tutto questo è possibile partendo dall’acquisto di materie prime da case madri europee, ottimizzando i prodotti presenti a magazzino, e dalla preparazione tecnica professionale del personale,” aggiunge Paola Pellegrino.
Filtri su misura per il mercato della verniciatura
Uno dei settori principali per Defil è la verniciatura industriale, che rappresenta circa un terzo del fatturato aziendale.
“Abbiamo sviluppato una gamma di prodotti avanzati sia per la verniciatura a polvere che a liquido. Per la verniciatura a polvere, offriamo una selezione di filtri a cartuccia, filtri a maniche progettati e costruiti con diversi setti filtranti ed esecuzioni per garantire elevate prestazioni e in grado di risolvere le varie problematiche riscontrate dalle ditte che richiedono i nostri filtri,” spiega Alfredo Pellegrino.
“Nel settore della verniciatura liquida spiccano il Max Paint filter, che è uno speciale materassino filtrante a forma alveolare, ad alte prestazioni, di cui
Defil è rivenditore esclusivo per il mercato italiano. Un altro prodotto di forte utilizzo sono gli accumulatori di vernice: filtri a secco progettati per cabine di verniciatura manuali o robotizzate, che sfruttano il principio di
separazione per inerzia, garantendo quindi un’efficace cattura dell’overspray e ottimi risultati applicativi. Inoltre, a catalogo disponiamo di filtri
Paint Stop, filtri originali Andreae, di cui Defil è rivenditore ufficiale per l’Italia e filtri in fibra di vetro, ideali per catturare particelle fini e garantire la purezza dell’aria. Grazie alla disposizione variabile delle fibre e alla loro densità, questi prodotti offrono un’elevata capacità di accumulo delle polveri e un minor rischio di rilascio, ottimizzando i processi produttivi,” continua Alfredo Pellegrino.
Nel corso degli anni Defil ha ampliato i filtri per la verniciatura, offrendo anche sacchi filtranti per la cataforesi, cartucce per liquido, lastre in setto poroso e sistemi di pulizia come tubi Venturi e ugelli rotanti.
“Grazie all’esperienza maturata in quasi quarant’anni di storia, Defil è in grado di offrire un prezioso know-how per quanto riguarda la filtrazione nei vari processi produttivi, la protezione ambientale sul posto di lavoro e l’abbattimento dell’inquinamento atmosferico,” interviene Paola Pellegrino.
Progetti futuri e conclusioni
Con un occhio sempre rivolto all’innovazione tecnologica e alla sostenibilità, Defil si conferma come partner d’eccellenza per chi cerca
soluzioni all’avanguardia nella filtrazione industriale. “Abbiamo in programma di automatizzare il processo di taglio dei pannelli per la costruzione delle celle filtranti, attualmente manuale, per raggiungere una produzione completamente digitalizzata e integrata. Inoltre, stiamo valutando l’espansione della nostra offerta con lo stampaggio interno dei componenti metallici, che ci consentirebbe di incrementare ulteriormente l’autonomia e diversificare i nostri prodotti,” chiosa Alfredo Pellegrino.
Simona Pellegrino, Amministratore Delegato di Defil, conclude esprimendo grande soddisfazione per l’acquisto della nuova pieghettatrice elettronica: “siamo più che soddisfatti del recente investimento, che ci consente di posizionarci meglio sul mercato nazionale e internazionale. Defil rappresenta ormai un punto di riferimento nel settore, grazie alla nostra capacità di innovare costantemente e adattarci alle esigenze di un mercato in continua evoluzione. Gli investimenti in tecnologie 4.0 e il continuo impegno nello sviluppo dei processi produttivi ci hanno permesso di migliorare la qualità dei nostri filtri e di rafforzare la nostra presenza internazionale. Con uno sguardo rivolto a un futuro sempre più automatizzato e sostenibile, siamo pronti a consolidare la nostra posizione, continuando a offrire soluzioni all’avanguardia.”
Delco Trailers, specializzata nella produzione di rimorchi, ha intrapreso un ambizioso progetto di automazione del proprio processo produttivo, implementando una nuova linea di verniciatura completamente automatizzata. Per questa importante iniziativa, l’azienda ha scelto Total Finishing Systems come partner strategico. L’obiettivo? Garantire finiture impeccabili e aumentare la capacità produttiva, arrivando a verniciare fino a 500 rimorchi a settimana.
“Quando si guarda un rimorchio, la prima cosa che salta all’occhio è la finitura”.
Questa affermazione di William Dyck, COO di Delco Trailers, racchiude perfettamente la sfida che l’azienda sta affrontando negli ultimi anni. Delco, con sede a Brookston, Texas, ha intrapreso un ambizioso percorso di automazione del proprio reparto produttivo, investendo in una nuova linea di verniciatura completamente automatizzata. Per portare a termine questo progetto, si è affidata a Total Finishing Systems (Montclair, California), leader americano specializzato nella fornitura di
soluzioni di verniciatura chiavi in mano. L’obiettivo di Delco Trailers è ambizioso e chiaro: raggiungere i più alti standard di finitura, garantendo prodotti esteticamente impeccabili grazie a un controllo meticoloso in ogni fase del processo. Tuttavia, l’installazione della nuova linea di verniciatura non ha solo migliorato la qualità del rivestimento, ma ha anche risposto alla necessità di incrementare significativamente la produttività. “Delco puntava a verniciare circa 500 rimorchi a settimana, un traguardo ambizioso che richiedeva un potenziamento della capacità produttiva”, afferma Ty Crowder, Presidente di Total Finishing Systems.
“Con il nuovo sistema, siamo riusciti a raggiungere questo obiettivo”.
L’impegno di Delco nella ricerca di soluzioni innovative e l’attenzione ai dettagli garantiscono che ogni rimorchio prodotto sia non solo esteticamente perfetto, ma anche progettato per resistere alle sfide più impegnative. A tal proposito, Dyck ha sottolineato: “Ogni rimorchio è costruito interamente in acciaio, il che assicura resistenza e durabilità anche nelle condizioni più difficili”. Questo progetto rappresenta un passo fondamentale per Delco Trailers, rafforzando ulteriormente la sua reputazione come produttore di rimorchi di alta qualità nel mercato americano.
L’impianto di verniciatura
La linea di verniciatura fornita da Total Finishing Systems è un impianto altamente sofisticato, equipaggiato con tecnologie all’avanguardia e un complesso sistema di trasporto che si dirama in più direzioni per garantire la massima flessibilità operativa.
L’impianto presenta 27 zone di carico e 27 zone di scarico automatizzato per assicurare un flusso continuo e organizzato delle operazioni. “Prima dell’implementazione della nuova linea, gli operatori dovevano spostare manualmente o con l’aiuto di muletti i rimorchi dall’area di saldatura a quella di stoccaggio e successivamente alla linea di verniciatura. Ora, grazie al nuovo sistema automatizzato, i componenti sono automaticamente trasportati tramite carroponte dal reparto di saldatura
a quello della verniciatura, riducendo significativamente l’impiego di manodopera, accelerando le tempistiche e aumentando notevolmente la produttività.
“I componenti vengono quindi sottoposti inizialmente a un pretrattamento meccanico tramite granigliatura. Questo processo avviene in due aree dedicate: una per la granigliatura manuale e l’altra per quella automatica”, spiega Fabian Cardenas, General Manager di TFS. “Successivamente, il convogliatore power&free, che si estende per oltre 2900 metri (9500 ft) di lunghezza si biforca: i componenti che seguono la linea primaria passano attraverso un tunnel di pretrattamento a tre stadi e successivamente nel forno di asciugatura; quelli che seguono la linea secondaria, invece, vengono sottoposti a soffiaggio, lavaggio manuale e poi asciugatura”, continua Cardenas.
Nella fase successiva, i componenti vengono trasportati nelle cabine di applicazione dei prodotti vernicianti. Anche in questo caso, il convogliatore si dirama per dirigere i pezzi verso la cabina corretta. Su entrambe le linee di trasporto sono presenti due cabine adiacenti dedicate rispettivamente all’applicazione del primer e due cabine per l’applicazione del rivestimento in polvere. Ogni cabina, lunga 48 metri (160 ft) è dotata di sistema di recupero polveri comprensivo di ciclone. A seguito dell’applicazione, i componenti passano nei due forni di polimerizzazione, anch’essi disposti in modo adiacente. Infine, le due linee si riuniscono in un’unica catena, convogliando i componenti fino all’area di scarico.
Il layout dell'impianto di verniciatura: sono ben visibili le 27 zone automatiche di carico/scarico.
Soddisfare le esigenze
“Quando Delco Trailers ha deciso di adottare un nuovo sistema di finitura, avevano già chiaro il tipo di soluzione necessaria e siamo entusiasti che abbiano trovato in Total Finishing Systems il partner perfetto per questa realizzazione,” afferma il General Manager di TFS. “Dopo il nostro incontro alla fiera Fabtech a Chicago nel 2021, Delco cercava un fornitore capace di offrire un sistema di verniciatura complesso e chiavi in mano, in grado di gestire componenti pesanti e lunghi fino a 15 metri (52 ft) e di raggiungere una capacità produttiva di circa 500 rimorchi a settimana”.
“Un fattore determinante nella scelta è stata la nostra capacità di progettare un layout innovativo e su misura. Il design del sistema è stato completamente personalizzato per rispondere alle precise esigenze del cliente, che aveva una visione dettagliata su come organizzare la produzione”.
Un altro aspetto cruciale è stato lo spazio limitato. “Nonostante le dimensioni imponenti del sistema, lo spazio a disposizione era ridotto.
Abbiamo dovuto sfruttare ogni metro quadrato disponibile con grande attenzione,” continua Crowder. “Inoltre, il controllo dei costi
è stato essenziale. Abbiamo lavorato per fornire al cliente le migliori tecnologie possibili senza superare il budget, realizzando un sistema che soddisfacesse pienamente le sue aspettative”.
Oltre a questo importante investimento tecnologico, Delco sta perfezionando i suoi processi produttivi interni per ottimizzare l’organizzazione aziendale. L’azienda mira a migliorare la gestione delle previsioni e ridurre l’inventario dei materiali, potenziando al contempo le procedure di magazzino per tracciare più efficacemente i componenti.
La collaborazione strategica con un pool di aziende
Quando Delco Trailers ha deciso di implementare un nuovo sistema di finitura, i requisiti erano chiari: un impianto altamente personalizzato e complesso. “Siamo orgogliosi che abbiano scelto Total Finishing Systems come partner ideale per realizzare questo ambizioso progetto”, afferma il General Manager di Total Finishing Systems.
Il progetto ha richiesto un’attenta analisi e uno studio approfondito per progettare un layout di tale complessità. “La collaborazione con i nostri partner è stata fondamentale: Erzinger (Joinville, Brasile) ha fornito le
cabine e il sistema di recupero della polvere, mentre Railtechniek (Tiel, Paesi Bassi) ha realizzato il trasportatore birotaia. Total Finishing Systems si è occupata della progettazione dei tunnel di pretrattamento e dei forni di asciugatura e polimerizzazione, oltre all’integrazione di tutte le tecnologie lungo la linea”, afferma Crowder. “Ogni fase del progetto ha richiesto grande attenzione ai dettagli e una preparazione meticolosa per garantire che tutte le esigenze del cliente fossero pienamente soddisfatte,” conclude Fabian. “Siamo entusiasti dei risultati ottenuti finora, avendo già consegnato il 95% dell’impianto, e continuiamo a lavorare per perfezionare il sistema fino alla sua completa operatività”.
I componenti in entrata nel forno di polimerizzazione e un rimorchio verniciato.
Kathrin Schilling
Fondatore & Direttore di BioPowder - Birkirkara, Malta
In tutto il mondo e in tutti i settori, le aziende sono chiamate ad essere più sostenibili, verdi e pulite. Di conseguenza, è sempre più importante bilanciare le considerazioni economiche, sociali e ambientali per garantire una migliore qualità della vita per le generazioni presenti e future.
Con la spinta verso la sostenibilità, l’industria dei rivestimenti potrebbe trovarsi ad affrontare tante sfide per via dell’impatto sull’ambiente e sulla salute di alcune sostanze chimiche comunemente utilizzate nei suoi prodotti. Tuttavia il mercato offre oggi delle alternative naturali e sostenibili che possono addirittura migliorare le proprietà fisiche e meccaniche delle formulazioni. Tra queste alternative troviamo leganti biologici, texturizzanti biodegradabili, contenuto riciclato e pigmenti naturali.
L’incredibilmente utile oliva
Una materia prima circolare che ultimamente ha guadagnato maggiori attenzioni è il nocciolo di oliva, un sottoprodotto del frantoio. La produzione di olio consiste nella compressione dell’intera oliva, che produce un residuo solido di polpa, buccia e frammenti di nocciolo. In passato i noccioli di oliva grezzi erano utilizzati principalmente per la combustione. In alcuni paesi sono ancora considerati prodotti di scarto e non fanno ancora parte di alcuna catena di riciclo. Secondo l’International Olive Council1, la produzione globale di olio di oliva per il raccolto del 2021/22 è stimata in 3,10 milioni di tonnellate, il 2,9% in più rispetto all’anno precedente. Esiste quindi una grande quantità di sansa con i relativi problemi di smaltimento per via del suo contenuto di grassi e di composti polifenolici. Fortunatamente sono emerse nuove tecnologie per recuperare questo scarto e scomporlo nei suoi diversi componenti. Degli speciali macchinari lavorano la sansa in ambiente umido e i frammenti dei noccioli vengono separati dalla polpa e dal guscio tramite un processo di centrifuga. I frammenti sono poi puliti meccanicamente, asciugati e setacciati in base alle dimensioni delle particelle. Grazie a questo procedimento complesso BioPowder (www.bio-powder.com) recupera dei granuli marrone chiaro privi di polvere/polpa e quasi inodori. Dopodiché li lavora ulteriormente fino ad ottenere polveri micronizzate di
1 International Olive Council, The World of Olive Oil, 13 Jan 2022
prima qualità e con diverse opzioni di funzionalizzazione della superficie. Commercializzati con il marchio Olea FP (Functional Powders), sono additivi completamente circolari con tutte le proprietà desiderabili per le moderne formulazioni di rivestimenti.
Benefici tecnici delle polveri micronizzate ad alte prestazioni ricavate da noccioli di oliva riciclati
Per vernici, pavimentazioni e altri sistemi di rivestimento, Olea FP offrono un’eccezionale gamma di opportunità grazie alle seguenti proprietà meccaniche:
Elevata durezza >3.5 sulla scala di Mohs
Olea FP hanno un elevato livello di durezza, che le rende adatte all’utilizzo nei rivestimenti che richiedono elevata robustezza, stabilità e resistenza all’abrasione. Ciò si traduce in una lunga vita utile dei rivestimenti funzionali per aree esterne e a traffico intenso.
Bassa capacità di legarsi a olio e acqua
Grazie alla loro scarsa capacità di legarsi a olio e acqua, Olea FP forniscono stabilità delle particelle senza rischio di espansione o rigonfiamento. Questa caratteristica facilita la loro incorporazione nelle formulazioni sia a base acqua che a solvente, migliora la durabilità dei rivestimenti e riduce la probabilità di crepe e sfaldature.
Bassa densità
Con la loro bassa densità Olea FP sono ideali per l’utilizzo nei materiali leggeri. Questa caratteristica può anche offrire un potenziale di risparmio riducendo la quantità necessaria per i lotti volumetrici.
Forma delle particelle compatta
La forma compatta delle particelle di Olea FP consente un’elevata possibilità e facilità di incorporazione nei rivestimenti. L’effetto è solitamente una buona dispersibilità, la quale produce una texture liscia.
Superficie reattiva delle particelle
La reattività superficiale di Olea FP può essere sfruttata oppure inibita attraverso la funzionalizzazione. Questa caratteristica permette di
produrre rivestimenti con proprietà personalizzate, quali una miglior adesione oppure la resistenza all’acqua.
Resistenza termica e proprietà isolanti
Olea FP hanno resistenza termica e proprietà isolanti. Questo è particolarmente importante per i rivestimenti industriali, per esempio per l’utilizzo in condotte o serbatoi di stoccaggio, nei quali la resistenza al calore e l’isolamento sono fondamentali.
Effetti dimostrati di Olea FP nelle formulazioni
Riduzione della brillantezza
Uno dei modi con cui Olea FP possono migliorare le formulazioni è riducendo la loro brillantezza. Le polveri micronizzate si sono dimostrate efficaci come agenti opacizzanti, tra gli altri nei seguenti modi:
Come pigmenti naturali in una matrice PU-acrilato: Olea FP sono state aggiunte ad una matrice PU-acrilata per modificare il colore e la brillantezza del rivestimento. L’aggiunta della polvere ha determinato un cambiamento del colore verso lo spettro rosso/giallo e una graduale opacizzazione della vernice. La brillantezza complessiva della vernice è stata ridotta a quasi il 50%, producendo una finitura sempre più opaca.
In sostituzione alle polveri opacizzanti in polietilene nella formulazione di vernici acriliche: una quantità di Olea FP funzionalizzate (idrofobe) è stata aggiunta con una concentrazione del 10%. Lo studio comparativo ha mostrato una brillantezza ridotta a tutti gli angoli di incidenza; l’intervallo
© BioPowder
dimensionale delle particelle più efficace è 0-100 μm.
Nel complesso, gli studi condotti dimostrano l’efficacia di Olea FP come agente opacizzante in diversi tipi di vernice, incluse le vernici epossidiche e acriliche. Riducendone la brillantezza, Olea FP aiutano a conferire una finitura opaca, auspicabile in molti tipi di applicazione come automotive o arredamento. Inoltre, il loro utilizzo in sostituzione degli agenti opacizzanti tradizionali come la polvere in polietilene può ridurre l’impatto ambientale del processo di produzione delle vernici.
Rinforzo e maggiore resistenza all’abrasione
L’elevata durezza di Olea FP le rende ideali per l’uso come agenti rinforzati nei rivestimenti. Aggiungendo quantità variabili di Olea FP, i produttori possono migliorare la resistenza dei rivestimenti all’usura, dovuta per esempio all’impatto e all’abrasione. Questa caratteristica è particolarmente utile nelle applicazioni in cui il rivestimento è soggetto a elevate sollecitazioni, come nei contesti marini o industriali. Nell’ambito dello studio completo sono stati effettuati i seguenti test:
test di indentazione: in un rivestimento PU-acrilato rinforzato con particelle di Olea FP, si è scoperto che delle quantità di polvere di noccioli di oliva pari ad almeno il 5% possono aumentare la durezza di una vernice fino al 20%.
test di Taber: la formulazione PU-acrilata di cui sopra, con percentuali variabili di Olea FP, è stata sottoposta ad abrasimetro Taber. Questo ha applicato una pressione sulla superficie, che ha rimosso gradualmente
BioPowder ottiene una fornitura costante di noccioli di oliva di alta qualità da frantoi selezionati con cura e li trasforma in granuli, polvere o farina con una specifica precisione nella gamma del micron.
lo strato di vernice. È stato verificato che l’utilizzo di polvere di noccioli di oliva ha ridotto la perdita di massa fino al 50% in meno di 600 cicli. Questi risultati dimostrano che la polvere di nocciolo di oliva migliora la resistenza all’abrasione e la durezza delle formulazioni. Di conseguenza, Olea FP posso contribuire ad estendere la vita utile dei rivestimenti, aumentandone l’efficienza. Inoltre, la leggerezza della polvere la rende un’opzione interessante per rivestimenti leggeri, nelle applicazioni in cui conta ogni singolo grammo.
Particelle naturali per texture ed effetti superficiali
Oltre all’utilizzo come opacizzante e rinforzante, Olea FP sono anche un’eccellente opzione per creare texture superficiali esclusive. I produttori alla ricerca di alternative bio possono prendere in considerazione Olea FP per i seguenti utilizzi:
riempitivo funzionale e agente di viscosità: incorporare la polvere di nocciolo di oliva nelle formulazioni epossidiche, acriliche e altre, consente regolazioni di viscosità e reologia migliorando al contempo la resistenza complessiva.
texture superficiale: le particelle di nocciolo di oliva possono essere sparse sulla superficie dei rivestimenti per creare un effetto decorativo e/o antiscivolo. Le particelle di Olea FP sono disponibili in una gamma da <50μm fino a 4mm, offrendo un’ampia gamma di texture.
particelle decorative e vettori di pigmento: oltre ad essere adatte agli effetti decorativi, le particelle Olea FP sono dei potenti vettori di pigmento. I test hanno dimostrato elevati livelli di efficacia con pigmenti provenienti da fonti sia naturali sia sintetiche. In risposta all’elevata richiesta di texture completamente naturali, per esempio alternative alle particelle di quarzo o polimeriche, BioPowder ha recentemente lanciato la sua gamma di particelle colorate con il brand Olea Colors.
In sintesi, l’utilizzo di Olea FP nei rivestimenti comporta numerosi vantaggi. Come materiale compostabile, costituisce un’alternativa ecologica alle particelle opacizzanti tradizionali. La sua resistenza e il suo basso peso lo rendono un’interessante opzione per il rinforzo, mentre la sua gamma dimensionale personalizzabile offre versatili opportunità di texturizzazione della superficie. I produttori dovrebbero idealmente sfruttare entrambi questi vantaggi per creare rivestimenti accattivanti da fonti rinnovabili.
Polveri funzionali biologiche: innovazione green con un’impronta di carbonio ottimizzata
La necessità da parte delle aziende di adottare la sostenibilità lungo tutta la catena del valore è diventata senza dubbio imperativa. Ma cosa serve per essere veramente ecocompatibili e per fissare nuovi standard di produzione responsabile? Nello specifico, cosa fa sì che un rivestimento si distingua come sostenibile? La risposta risiede nell’impronta di carbonio
© BioPowder
© BioPowder
Il linoleum rinforzato ‘naturazzO’ di BioPowder è una resistente pavimentazione che contiene fino al 40% di riempitivi compositi Olea FP. Si è dimostrato efficiente per le superfici industriali ad elevato carico.
Con le particelle naturali di BioPowder i produttori possono creare esclusive texture superficiali. I sistemi raccomandati per l’incorporazione delle particelle sono le resine epossidiche, poliuretaniche e poliaspartiche.
e quindi in una valutazione completa del ciclo di vita di tutti i materiali utilizzati in una formulazione.
Misurare la produzione di CO2 in tutte le fasi della filiera produttiva è diventato un punto di riferimento riconosciuto. A questo proposito, BioPowder si è impegnata in pratiche snelle, profondamente radicate nell’ecosistema circolare dei sottoprodotti dell’oliva. Di conseguenza, le particelle di nocciolo di oliva hanno un’impronta di carbonio ottimizzata: sono prodotte al 100% meccanicamente, con l’elettricità come principale risorsa. L’utilizzo di acqua è minimo e la produzione non genera alcun rifiuto. Ancora più importante, gli ulivi sono tra le piante che assorbono le maggiori quantità di CO2. Evidenze scientifiche dimostrano che vengono prodotti circa 1,5 kg di CO2 per ogni litro di olio extra vergine. Tuttavia, un uliveto può assorbire fino a 10 kg di CO2 coltivando la stessa quantità di olive2. In conclusione si può affermare che le polveri di nocciolo di oliva stanno indubbiamente creando opportunità per innovazioni efficienti in termini di CO2 nel settore delle vernici e dei rivestimenti. Il team di BioPowder supporta i produttori di rivestimenti in tutte le fasi di ricerca e sviluppo e di produzione e non vede l’ora di trovare nuovi partner di progetto.
2 International Olive Council, Application for the Calculation of CO2 Balance in Olive Farming, 27 Jul 2016
BioPowder è un produttore e fornitore di polveri di noccioli di frutta di alta qualità e di abrasivi biologici privi di additivi chimici. Derivati dai flussi collaterali di lavorazione alimentare, i prodotti dell’azienda supportano un’economia circolare e permettono ai produttori di ridurre il loro impatto ambientale. Fondata nel 2017 e con sede a Malta, l’azienda si rifornisce dalla regione del Mediterraneo e gestisce la produzione nel sud della Spagna. BioPowder fa parte di una filiera sostenibile che crede fortemente nella lavorazione dei sottoprodotti agricoli (non colture), nell’approvvigionamento locale o regionale e nella garanzia che le sue attività non interrompano la filiera alimentare.
Manuela Casali
UCIF – Unione Costruttori Impianti di Finitura, Milano, Italia info@ucif.net
La cybersecurity, da competenza esclusiva della divisione IT, sta oggi coinvolgendo apparati sempre più ampi della struttura aziendale, arrivando a interessare in prima persona tutti i collaboratori, indipendentemente dal ruolo che ricoprono.
In un mondo sempre più digitale, la cybersecurity aziendale non è più una responsabilità esclusiva del dipartimento IT. Oggi, ogni dipendente gioca un ruolo cruciale nella protezione delle informazioni e delle risorse dell’azienda. La crescente complessità delle minacce informatiche rende essenziale che tutti, indipendentemente dalla posizione occupata in azienda, prestino attenzione ai potenziali attacchi informatici, anche quelli provenienti da fonti inaspettate.
La maggior parte degli attacchi informatici non inizia con un sofisticato hacking dei sistemi, ma con qualcosa di molto più semplice: un’email di phishing, un link sospetto, o una chiavetta USB lasciata incustodita. Questi vettori di attacco sfruttano la fiducia e la disattenzione dei dipendenti, trasformandoli in porte d’ingresso per cybercriminali. Questo significa che anche il miglior sistema di sicurezza può essere vulnerabile se le persone non sono adeguatamente formate e consapevoli dei rischi.
Un aspetto spesso sottovalutato è la provenienza delle minacce. Non solo hacker professionisti o gruppi organizzati possono rappresentare un rischio, ma anche ex-dipendenti, fornitori esterni e persino errori accidentali da parte del personale interno possono compromettere la sicurezza aziendale. È importante che tutti siano consapevoli di queste potenziali fonti di rischio e siano in grado di riconoscere comportamenti sospetti o inusuali. La formazione è la prima linea di difesa contro le minacce informatiche. Corsi regolari di aggiornamento sulla cybersecurity aiutano i dipendenti a riconoscere e rispondere correttamente alle minacce. La formazione non deve limitarsi a sessioni teoriche, ma includere simulazioni pratiche, come test di phishing, per preparare il personale a reagire in situazioni reali. Inoltre, la cultura della sicurezza deve essere promossa a tutti i livelli dell’organizzazione. I dipendenti devono sentirsi responsabilizzati e parte
attiva nella protezione delle risorse aziendali, comprendendo l’impatto che un singolo errore può avere sull’intera azienda. Oltre alla formazione, la prevenzione è fondamentale. Le aziende devono adottare misure proattive come l’aggiornamento costante dei sistemi, l’implementazione di software di sicurezza avanzati, e la verifica periodica delle vulnerabilità. È essenziale anche stabilire procedure chiare per la gestione degli incidenti, in modo che, in caso di attacco, l’azienda possa rispondere rapidamente e limitare i danni. La cybersecurity aziendale è una sfida che richiede la partecipazione attiva di tutti i membri dell’organizzazione. Solo attraverso una combinazione di formazione, consapevolezza e misure preventive, le aziende possono proteggersi efficacemente dalle minacce informatiche. In un’epoca in cui le informazioni sono uno degli asset più preziosi, la sicurezza digitale deve essere una priorità condivisa da tutti. Le norme relative alla cybersecurity variano a seconda della giurisdizione e del settore. Tuttavia, ci sono alcune normative internazionali e locali che sono fondamentali per le aziende e le organizzazioni. Di seguito sono elencate alcune delle principali norme internazionali attualmente in vigore, quali ad esempio il GDPR, che si applica a tutte le organizzazioni che trattano dati personali di cittadini dell’UE, indipendentemente dalla loro ubicazione; l’ISO/IEC 27001, standard internazionale che specifica i requisiti per un sistema di gestione della sicurezza delle informazioni o ancora il Cybersecurity Act, entrato in vigore in UE nel 2019 e che stabilisce un quadro per la certificazione della cybersecurity all’interno dell’Unione Europea.
UCIF attraverso la collaborazione con ANIMA Confindustria propone a attua incontri di aggiornamento e formazione sul tema, per aiutare i propri Associati ad essere sempre informati sulle nuove problematiche o su come poter gestire al meglio le proprie attività.
Ilaria Paolomelo ipcm®
Associato spesso a sentimenti di dolcezza, amore e femminilità, il rosa ha una storia ricca e variegata che abbraccia arte, letteratura, natura, cinema e cultura di massa. In questo articolo, esploreremo le origini del colore rosa, il suo significato, e come è stato utilizzato nel corso dei secoli.
Il rosa, un colore ricco di storia e simbolismo, ha attraversato secoli di trasformazioni culturali e artistiche, trovando un ruolo significativo nel cinema, nella moda e nella psicologia.
Originariamente raro e prezioso nell’antichità, il rosa ha visto la sua evoluzione dal Rinascimento fino al XVIII secolo, diventando simbolo di eleganza e potere grazie a figure come Madame de Pompadour. Nel XX secolo, ha assunto connotazioni di femminilità e delicatezza, sebbene in passato fosse considerato anche un colore maschile. In psicologia, il rosa è associato a tranquillità, compassione, ottimismo e creatività, dimostrando il suo potere calmante e il suo impatto positivo sul nostro stato d’animo.
Dai film iconici come “Colazione da Tiffany” e “Mean Girls” alla cultura pop e alle campagne di sensibilizzazione come il “Pink Ribbon”, il rosa continua a influenzare e ispirare, rimanendo un colore centrale nelle tendenze culturali e sociali di oggi.
Il rosa nella storia
Il rosa, ottenuto mescolando il rosso con il bianco, è un colore che ha attraversato secoli di trasformazioni culturali e artistiche. Nell’antichità, il rosa era difficile da ottenere e, di conseguenza, raro e prezioso. In campo artistico, i primi usi di tale colore si possono riscontrare nell’antica Roma, dove veniva impiegato per affreschi e decorazioni ceramiche. Con l’avanzare dei secoli, durante il Rinascimento, il rosa divenne più accessibile grazie ai progressi nella produzione di pigmenti e venne utilizzato nei dipinti religiosi per rappresentare la pelle umana e le vesti sacre. La parola “rosa” apparve per la prima volta nel XVII secolo, ma il colore si diffuse ampiamente nel XVIII secolo. Proprio in questo periodo, Madame de Pompadour, amante del re Luigi XV, è celebre per aver elevato il rosa a simbolo di moda e prestigio, tanto che una tonalità di porcellana rosa fu battezzata “Rosa Pompadour” da La Manufacture nationale de Sèvres, una delle più celebri manifatture di porcellana in Europa fondata nel 1740 a Sèvres, in Francia, per volontà del sovrano. Durante questo periodo, il rosa era indossato da uomini e donne e considerato un colore elegante e potente. Tuttavia, il significato del rosa è cambiato nel tempo. In Occidente, il rosa è ora tradizionalmente associato alla femminilità, alla dolcezza e all’innocenza, un’associazione che si è consolidata solo nel XX secolo. Prima del XIX secolo, il rosa era spesso considerato un colore maschile,
soprattutto per i bambini. In molte culture asiatiche, invece, il rosa è simbolo di buona fortuna e felicità. Oggi, il rosa è anche associato alla tranquillità e alla serenità: studi psicologici hanno infatti dimostrato che questa tonalità può avere un effetto calmante e ridurre i livelli di aggressività, motivo per cui viene utilizzato in ambienti come gli ospedali, le carceri e le scuole per conferire un’atmosfera di calma.
L’origine della parola “rosa”
La parola “rosa” deriva dal latino ed indica sia il colore che l’omonimo fiore. Ma l’origine della parola latina è ancora più antica e si può far risalire al greco antico “rhodon”1 (ῥόδον). Questo termine greco, a sua volta, ha probabili radici nelle lingue del Vicino Oriente, come il persiano antico “vrda-” o l’aramaico “warda”, che hanno rispettivamente il significato di spina e rosa canina.
Il fiore della rosa ha avuto una notevole importanza simbolica e culturale nelle civiltà antiche, il che ha portato il termine a diffondersi ampiamente.
In molte culture, la rosa è stata associata all’amore, alla bellezza e alla passione, e queste connotazioni si sono riflesse anche nel linguaggio: ad esempio, nella mitologia greca, la rosa era associata ad Afrodite, la dea dell’amore, e in epoca romana, a Venere.
1 https://it.wikipedia.org/wiki/Rosa_(colore)
Il rosa nella letteratura e nell’arte
Il colore rosa ha avuto un ruolo significativo sia nella letteratura che nell’arte, assumendo significati e connotazioni diverse a seconda del contesto storico e culturale.
Nella letteratura, il rosa è tradizionalmente associato alla delicatezza e alla sensibilità. In molte opere di Jane Austen, ad esempio, i personaggi femminili sono spesso descritti con abiti rosa, che simboleggiano purezza e romanticismo. Tuttavia, il significato del rosa non è statico: nel romanzo “Cattive Ragazze” di Joyce Carol Oates, questo colore viene utilizzato per rappresentare la ribellione e la forza interiore, associandosi a personaggi femminili forti e indipendenti.
Anche nell’arte, il rosa ha subito trasformazioni significative nel tempo.
Durante il periodo Rococò, rappresentava eleganza e raffinatezza, come dimostrano le opere di François Boucher e Jean-Honoré Fragonard. Nel XX secolo, artisti come Pablo Picasso e Mark Rothko hanno impiegato il rosa in modi innovativi per esplorare emozioni e introspezione. Picasso, in particolare, ha avuto un “periodo rosa” in cui le sue opere esprimevano serenità e calore. Nel periodo postmoderno, artisti come Jeff Koons hanno utilizzato il rosa per esplorare la cultura di massa e il kitsch, spesso per commentare la commercializzazione della bellezza e la superficialità della cultura popolare.
Il rosa in natura
Il rosa in natura si manifesta in diverse forme, dai fiori ai paesaggi. Uno degli esempi più celebri sono i fiori di ciliegio, o “sakura”, in Giappone. Questi fiori colorano i paesaggi con delicate sfumature rosa e rappresentano simboli culturali profondi. La loro fioritura, celebrata durante l’Hanami, simboleggia la bellezza effimera della vita e l’importanza di apprezzare i momenti fugaci.
I fenicotteri, invece, sono famosi per il loro piumaggio rosa brillante, dovuto alla loro dieta. Questi uccelli, a differenza di ciò che si potrebbe pensare, non nascono rosa, bensì con piume grigie o bianche. Nel corso della loro vita assumono questa colorazione mangiando crostacei e alghe ricchi di carotenoidi, pigmenti organici che, una volta digeriti, vengono metabolizzati e depositati nelle piume, nel becco e nella pelle. Così, il colore rosa diventa un indicatore visivo della salute e della dieta del fenicottero: più ricca è la dieta di carotenoidi, più brillante sarà il loro piumaggio.
Infine, la natura ci dona anche splendidi paesaggi sfruttando le nuance di tale colore. Definita come “i Caraibi del Mediterraneo”, la spiaggia di Elafonissi, situata nella costa sud-occidentale di Creta, è una delle mete estive più ambite della Grecia. Questa spiaggia è famosa in tutto il mondo per la sabbia rosa, formata da foraminiferi e conchiglie rosa e rosse che si polverizzano a contatto con l’acqua del mare. Anche la spiaggia rosa di Budelli, situata nell’Arcipelago di La Maddalena in Sardegna, è celebre per la sua sabbia rosa, composta da gusci calcarei di un organismo unicellulare, il Miniacina miniacea, e frammenti di corallo.
Una vera e propria pink-mania
Il colore rosa ha avuto un impatto fondamentale nel cinema e nella cultura di massa, evocando atmosfere particolari e caratterizzando i personaggi con il suo simbolismo di eleganza, ribellione e potere. Questa tinta ha trovato ampio spazio in film iconici e ha lasciato un’impronta significativa sulla moda e sulle tendenze sociali.
Nel film Colazione da Tiffany, il rosa è utilizzato per esaltare l’eleganza, la vivacità, la raffinatezza e il glamour di Holly Golightly, celebre personaggio interpretato da Audrey Hepburn. Allo stesso modo, in Grease, il gruppo delle “Pink Ladies” adotta il rosa come simbolo di amicizia e ribellione adolescenziale, creando un’icona duratura della moda e della cultura pop degli anni ‘70.
Il rosa ha continuato a essere un colore distintivo nella cultura popolare con film come Mean Girls, dove il famoso slogan “On Wednesdays we wear pink” diventa un simbolo di conformità e appartenenza a un gruppo sociale. Questo utilizzo del rosa per rappresentare il potere e la dinamica sociale tra adolescenti ha consolidato il suo ruolo nella cultura giovanile. Oltre al cinema, il rosa è profondamente radicato nella cultura di massa contemporanea. È il colore distintivo di molti marchi e prodotti, tra cui le iconiche gomme da masticare Big Bubble, il logo di Victoria’s Secret e il packaging di Barbie. Lanciata nel 1959 da Mattel, Barbie inizialmente non aveva il rosa come colore predominante, ma negli anni ‘60 e ‘70 il rosa è emerso come elemento chiave nel branding della bambola più famosa al mondo, rafforzato negli anni ‘80 e ‘90 attraverso strategie di marketing. Oggi, il rosa Barbie è diventato un simbolo iconico e onnipresente nella
cultura pop, conferendo al brand e a coloro che indossano tale nuance un forte senso di femminilità e glamour.
Questo successo è stato ulteriormente amplificato dal film Barbie, diretto da Greta Gerwig e interpretato da Margot Robbie e Ryan Gosling, che ha ottenuto un clamoroso successo al botteghino, incassando oltre 1,4 miliardi di dollari a livello globale e diventando uno dei maggiori successi cinematografici del 2023 oltre che il film di maggior incasso mai prodotto da Warner Bros.
La pellicola non solo ha riportato in auge il personaggio di Barbie, ma ha anche dimostrato la capacità del cinema di influenzare le tendenze culturali e commerciali. Il predominante rosa acceso dell’ambientazione e dei costumi ha risvegliato e amplificato il fascino del colore, portando a un rinnovato interesse per questa tonalità nella moda e nelle decorazioni. Ne è un esempio concreto il modello di sandali Arizona color rosa cipria prodotto dall’azienda tedesca Birkenstock: secondo la piattaforma di shopping online Lyst, a solo una settimana dall’uscita del film, le ricerche online per le Birkenstock rosa sono aumentate del 110%2
La rappresentazione del mondo di Barbie ha alimentato un’ondata di nostalgia e stimolato discussioni su temi di femminilità e identità di genere, suggerendo che il rosa continuerà a essere un elemento centrale nella cultura pop.
Ma il rosa è legato anche a tematiche più serie e importanti che pongono quasi sempre al centro le donne.
2 https://forbes.it/2023/08/02/birkenstock-sbarco-borsa-settembre-l-catterton-8-miliardi/
Il “Pink Ribbon”, simbolo internazionale della lotta contro il cancro al seno, è molto più di un semplice nastrino rosa. Esso rappresenta solidarietà e speranza per milioni di persone in tutto il mondo, contribuendo a sensibilizzare l’opinione pubblica e a raccogliere fondi per la ricerca e il trattamento di questa malattia oncologica.
Inoltre, il rosa ha trovato una forte applicazione anche in movimenti sociali e politici. Il “Pink Protest” è un’iniziativa che utilizza il colore per sostenere i diritti delle donne e delle minoranze, dimostrando come il rosa possa essere un potente strumento di advocacy e attivismo.
Da sinistra a destra:
- La fioritura dei fiori di ciliegio in Giappone.
- La celebre spiaggia rosa di Budelli, Sardegna.
- Il brand Barbie ha fatto del rosa il suo colore predominante.
Lo scorso sabato 7 settembre, il team di ipcm® ha avuto il piacere di partecipare al 40° anniversario di Idrotecnica. L’evento è stato un’importante occasione per ripercorrere la storia dell’azienda specializzata nella produzione di sistemi per il trattamento delle acque e celebrare i numerosi successi raggiunti in quattro decenni di attività.
Lo scorso sabato 7 settembre, presso la sede di Idrotecnica a Genova, si è celebrato il 40° anniversario dell’azienda specializzata nella progettazione, produzione e installazione di sistemi di purificazione e demineralizzazione delle acque per diversi settori industriali, tra cui cosmetica, farmaceutica, laboratori di ricerca e verniciatura. Questo evento non è stato solo un’occasione per festeggiare, ma anche per ripercorrere i quattro decenni di successi e innovazioni che hanno reso Idrotecnica una realtà solida e ben riconosciuta a livello globale. All’interno del reparto di produzione aziendale,
i partecipanti hanno avuto l’opportunità di prendere parte a una visita guidata, dove erano esposti i primi impianti di trattamento acque forniti da Idrotecnica negli anni ‘90, accanto ai più moderni e avanzati sistemi attualmente in uso. Questa esposizione ha offerto uno spaccato dell’evoluzione tecnologica dell’azienda, mettendo in luce il suo impegno costante verso l’innovazione. Uno dei momenti più significativi della giornata è stato il discorso del CEO Federico Marcenaro, che ha ricordato con emozione la fondazione dell’azienda da parte di suo padre Alessio, sottolineando come la passione, l’impegno e la continua ricerca
dell’eccellenza abbiano guidato Idrotecnica nel suo percorso di crescita. “Sono stati 40 anni intensi, ricchi di sfide e successi, e guardiamo al futuro con lo stesso entusiasmo, determinazione, apertura, professionalità e soprattutto con l’umiltà che ci ha contraddistinto sin dall’inizio,” ha affermato Marcenaro. Durante il suo intervento, ha voluto esprimere profonda gratitudine a tutti coloro che hanno contribuito al successo dell’azienda: collaboratori, partner, fornitori e clienti, il cui supporto è stato fondamentale per il raggiungimento degli ambiziosi traguardi aziendali. Un ringraziamento speciale è stato riservato alla sua famiglia, che ha sempre sostenuto e accompagnato l’azienda nel suo percorso. Marcenaro ha posto l’accento sull’importanza dell’innovazione e della qualità, valori che continuano a guidare Idrotecnica nell’affrontare le sfide del mercato globale.
L’evento ha offerto anche uno sguardo verso il futuro, con Marcenaro che ha anticipato alcune delle opportunità e delle sfide che attendono l’azienda nei prossimi anni, affermando che Idrotecnica continuerà a investire in ricerca e sviluppo per rimanere all’avanguardia nel settore, rispondendo alle esigenze di mercati in continua evoluzione e sempre più esigenti.
La giornata si è conclusa in un clima di festa e convivialità, con un brindisi e un pranzo che ha coinvolto tutti i presenti.
“Questo 40° anniversario non rappresenta solo un importante traguardo storico, ma anche un nuovo punto di partenza per affrontare con successo le sfide future e continuare a scrivere la storia di Idrotecnica nei decenni a venire”, ha concluso il CEO.
Helios Quartz ha festeggiato 85 anni di attività inaugurando un nuovo magazzino e accogliendo oltre 150 ospiti per rendere omaggio ai propri dipendenti e alle loro famiglie.
Il 12 settembre Helios Quartz ha celebrato un traguardo importante: 85 anni di storia. La storica azienda italiana, con sede a Cambiago, rinomata per la lavorazione del vetro di quarzo e la produzione di lampade IR e UV, ha organizzato un evento esclusivo nella sua nuova struttura, accogliendo oltre 150 ospiti per un momento di festa e riflessione. L’evento, riservato esclusivamente ai dipendenti e alle loro famiglie, ha creato un’atmosfera calorosa e coinvolgente, dove l’orgoglio per il percorso compiuto si è fuso con la speranza e l’entusiasmo per le sfide future.
Sotto la guida del CEO Armando Giro dal 2016, che ha raccolto l’eredità paterna con la stessa visione e determinazione, Helios Quartz continua a consolidare il suo ruolo di riferimento nel settore. Durante la serata, il CEO ha voluto omaggiare il percorso dell’azienda, rendendo merito non solo ai risultati raggiunti, ma soprattutto alle persone che ne hanno fatto parte e che hanno contribuito a farla crescere.
Particolarmente toccante è stato il riconoscimento riservato a Enrico Giro, padre dell’attuale CEO, figura chiave nello sviluppo dell’azienda, e ai dipendenti, considerati il cuore pulsante di Helios Quartz. Giro ha espresso calore e gratitudine sottolineando quanto la dedizione e il lavoro di squadra abbiano contribuito a costruire il successo dell’azienda, unendo passato e presente con lo sguardo rivolto al futuro.
Il CEO ha chiuso la serata con un messaggio positivo: “Il futuro di Helios Quartz è brillante e sono veramente entusiasta di condividerlo con tutti voi”.
Chi è Helios Quartz
Fondata nel 1940, Helios Quartz è nata come azienda a conduzione familiare ed è oggi un gruppo internazionale con due stabilimenti produttivi, in Italia e in Svizzera, e uffici commerciali negli USA, in Cina e in Asia. L’azienda è oggi un importante fornitore internazionale per la lavorazione del vetro di quarzo e la produzione di lampade IR e UV, e produce anche apparecchiature dedicate per applicazioni industriali, scientifiche e mediche. Oltre 70 anni di esperienza in diversi settori hanno permesso a Helios Quartz di acquisire un know-how tecnologico avanzato, una profonda conoscenza dei processi produttivi e solide competenze in molti settori di diverse applicazioni: le aziende Helios Quartz sono in grado di soddisfare ogni richiesta, studiando soluzioni per le applicazioni più specifiche e complesse, anche grazie a un centro di collaudo all’avanguardia situato nello stabilimento produttivo di Cambiago.
La prossima edizione di Paint & Coatings Italy si terrà dal 22 al 23 ottobre a Milano.
Paint & Coatings Italy ritorna per la sua terza edizione, che si terrà il 22 e il 23 ottobre presso l’NH Milano Congress Centre di Assago. Supportato da AssICC e ASSOVERNICI, Paint & Coatings Italy è stato sviluppato pensando agli operatori del settore. L’evento è ricco di contenuti che coprono una vasta gamma di argomenti, combinati con un’area espositiva che presenta i principali fornitori attivi nel tuo settore. Qualunque sia la propria esperienza, l’evento offre competenze, intuizioni creative, conoscenze, servizi, strumenti e contatti professionali mirati.
P&C Italy è l’opportunità per dare una nuova luce di colori al business del settore. L’evento, noto per la sua capacità di riunire esperti, innovatori e aziende leader, offrirà una piattaforma ideale per discutere delle ultime tendenze, innovazioni tecnologiche e opportunità di networking.
L’esposizione sarà la più grande di sempre, con un incremento significativo nel numero di espositori a disposizione, migliaia di prodotti da scoprire e un maggior numero di esperti del settore pronti a condividere le loro conoscenze.
In parallelo all’area espositiva, ci sarà un programma di contenuti completo che offre un’opportunità unica per scoprire nuove soluzioni, formare collaborazioni strategiche e rimanere aggiornati sugli sviluppi del settore.
La Conferenza di P&C Italy vedrà esperti e aziende del settore chimico
e dei materiali discutere di argomenti attuali e rilevanti. L’obiettivo principale è esplorare soluzioni innovative e sostenibili che rispondano alle crescenti esigenze ambientali e alle normative vigenti.
Supportata da AssICC, la conferenza affronterà vari argomenti normativi, presentando aggiornamenti sull’etichettatura e la notifica PCN secondo le recenti regolamentazioni CLP. Ulteriori contenuti copriranno l’importanza dei controlli REACH e CLP per garantire la conformità alle normative europee.
Un momento saliente sarà la sessione dedicata alla certificazione dei verniciatori e allo stato dell’arte in Italia, seguita da una presentazione sull’uso della Dichiarazione Ambientale di Prodotto (EPD) per comunicare gli impatti ambientali lungo il ciclo di vita dei prodotti.
ERMA, l’European Resin Manufacturer Association, avrà un ruolo cruciale nel guidare le discussioni sulla sostenibilità, fornendo sia un quadro normativo che strategie pratiche per aiutare le aziende a diventare più responsabili dal punto di vista ambientale. Il programma completo è disponibile sul sito: www.paint-coatings.it/la-conferenza/.
Dato il successo della Polymer Academy della scorsa edizione, P&C Italy si concentrerà nuovamente sui leganti polimerici, coinvolgendo i principali produttori di resine. Questo Congresso evidenzia come l’innovazione e la sostenibilità siano al centro del progresso nel settore dei rivestimenti e dei polimeri, con un forte focus sulla qualità e l’efficienza dei processi produttivi.
Inedita per il 2024, è la Additives Academy, condotta dai principali produttori di additivi per il settore. Il Convegno dedicato tratta soluzioni innovative e sostenibili per vernici e rivestimenti. Gli argomenti principali includono l’uso di additivi antimicrobici, rivestimenti marini sostenibili, agenti umettanti esenti da PFAS, e additivi a base di cera. Si discute anche di miglioramenti nelle prestazioni dei rivestimenti con additivi intelligenti, sostituti del PFAS, cere biodegradabili, e addensanti avanzati. Infine, vengono esplorate le sfide e le opportunità nella formulazione di vernici eco-sostenibili, con un focus su additivi naturali, cristalli bidimensionali e il riciclo di pigmenti.
Non resta che segnare in agenda questo appuntamento imperdibile: Paint & Coatings Italy torna all’NH Milano Congress Centre di Assago, pronto a consolidare la sua reputazione di evento di punta nel panorama nazionale delle vernici e dei rivestimenti. E, infine, si ricorda che pranzo e caffè sono offerti a tutti i visitatori che arrivano onsite prima delle 10.
Per maggiori informazioni: www.paint-coatings.it
Per molti settori industriali, l’alluminio - il “metallo magico” - è e continua a essere il materiale preferito per prodotti sostenibili e tecnicamente imbattibili. Durante ALUMINIUM 2024, la principale fiera mondiale che si terrà a Düsseldorf dall’8 al 10 ottobre, quasi 800 espositori provenienti da 50 nazioni mostreranno il potenziale di questo metallo leggero e come l’industria dell’alluminio sta affrontando le sfide attuali e si sta preparando al futuro.
Ogni due anni, la più grande vetrina dell’industria dell’alluminio riunisce produttori, operatori e fornitori di tecnologie dell’intera catena del valore: dalla produzione di materie prime e dai segmenti della produzione primaria, dalla progettazione di macchine e impianti, alle tecnologie di processo e ai prodotti semilavorati, ai prodotti finiti e, non da ultimo, alle tecnologie di riciclo mirato. Qui verranno presentate le soluzioni innovative ottenute utilizzando l’alluminio nell’automotive, nell’ingegneria meccanica e in quella edile, nell’aerospace, nell’elettronica, nel packaging e nei trasporti.
Ogni due anni ALUMINIUM rappresenta il punto di incontro e la vetrina più importante per i grandi gruppi internazionali. Inoltre, molte PMI e start-up sfruttano questa importante fiera internazionale per fare il loro ingresso sul mercato, scambiare idee con i clienti e fare network con altre realtà del settore. Per tutti loro, ALUMINIUM funge sia da barometro del mercato sia da motore di innovazione. Quest’anno, 780 aziende espositrici dell’intera catena del valore dell’alluminio si presenteranno nei 5 padiglioni. Le hall 1 e 4 saranno dedicate ai prodotti semilavorati, mentre la hall 5 si concentrerà sulla costruzione dei forni, sulla lavorazione dei metalli e sulle tecnologie di giunzione e automazione. La hall 3 avrà come protagoniste le tecnologie di trattamento superficiale e di laminazione e includerà il Surface Pavilion e la Surface & Design Lounge. Infine, la hall 6 sarà dedicata alla fusione e ai trattamenti termici, alla costruzione dei forni, alla produzione primaria e al riciclo. Qui i visitatori troveranno non solo il padiglione delle materie prime e della fonderia, ma anche il Foundry Community Café, il luogo ideale per fare networking e scambiare idee. Un altro highlight sarà il rilancio della Media & Education Lounge nella Hall 6. Questo spazio offre non solo un’area di ristoro con abbondante materiale informativo, ma anche preziosi approfondimenti e nozioni utili sulle caratteristiche dell’alluminio. Saranno inoltre disponibili informazioni sulle opportunità di formazione e sulla carenza di manodopera qualificata ed è previsto un programma speciale per studenti e tirocinanti. Ai visitatori ALUMINUM non presenterà solo le soluzioni attuali e uno
sguardo sul futuro. L’ampio programma dell’ALUMINIUM Conference e dello Speakers Corner offrirà anche argomenti approfonditi: la conferenza, organizzata da Aluminium Deutschland e considerata un evento centrale per il trasferimento di conoscenze e lo scambio di esperienze in fiera, fornisce elementi preziosi sulle tematiche attuali, mentre la The Innovation Plaza “Sustainability & Recycling” anche quest’anno avrà come focus la trasformazione sostenibile dell’industria dell’alluminio.
Inoltre, l’edizione di quest’anno presenterà il 9 ottobre i “Women with Metal – ALUMINIUM Awards” per promuovere l’uguaglianza di genere e la diversità nell’industria dell’alluminio, riconoscendo i risultati ottenuti dalle donne, affrontando la carenza di manodopera qualificata e incoraggiando più donne a intraprendere una carriera in questo settore.
La fiera ALUMINIUM si aprirà l’8 ottobre con un dialogo di settore tra Aluminium Deutschland, IG Metall e IG BCE sulla trasformazione socioeconomica. Questo dialogo mira a promuovere discussioni essenziali con i referenti politici, con relatori come Mona Neubauer, Ministro degli Affari Economici per il Nord Reno-Westfalia.
Per maggiori informazioni: www.aluminium-exhibition.com
Eos Mktg&Communication srl www.eosmarketing.it - info@eosmarketing.it www.myipcm.com - info@ipcm.it
Redazione - Sede Legale: Via Pietro Mascagni, 8 - 20811 - Cesano Maderno (MB) - Italy Tel. +39.0362.503215 - Fax. +39.0362.1794768
Prof. Massimiliano Bestetti: Department of Chemistry, Material and Chemical Engineering, Politecnico of Milan –Section of Applied Chemistry and Physics
Prof. Stefano Rossi: Material Engineering and Industrial Technologies, University of Trento - Product Design
EDITOR IN CHIEF / DIRETTORE RESPONSABILE
ALESSIA VENTURI venturi@ipcm.it
EDITORIAL DIRECTOR / DIRETTORE EDITORIALE
FRANCESCO STUCCHI stucchi@ipcm.it
EDITORIAL OFFICE / REDAZIONE
PAOLA GIRALDO giraldo@ipcm.it
MONICA FUMAGALLI fumagalli@ipcm.it
NICOLE KRAUS kraus@ipcm.it
MATTEO SOTTI sotti@ipcm.it
ILARIA PAOLOMELO paolomelo@ipcm.it
GABRIELE LAZZARI redazione@ipcm.it
FEDERICO MELIDEO melideo@ipcm.it
GIULIA GENTILE gentile@eosmarketing.it
EDITORIAL OFFICE AND GRAPHICS
ELISABETTA VENTURI grafico@ipcm.it
MEDIA SALES
FRANCESCO STUCCHI stucchi@ipcm.it
ILARIA PAOLOMELO paolomelo@ipcm.it
NICOLE KRAUS kraus@ipcm.it
LAYOUT/ IMPAGINAZIONE
ELISABETTA VENTURI grafico@ipcm.it
Dr. Fulvio Zocco: Environment and quality
Prof. Paolo Gronchi: Department of Chemistry, Material and Chemical Engineering, Politecnico of Milan –Chemical Engineering Section
Kevin Biller: ChemQuest Powder Coating Research
SUBSCRIPTION SERVICE - SERVIZIO ABBONAMENTI:
Sale only on subscription - Vendita solo su abbonamento E.mail info@ipcm.it
Subscription Rates 2024 - Tariffe Abbonamento 2024:
Annual subscription print + digital:
EMEA 110,00 € (postage included)
Rest of world 350,00 € (fast airmail shipping included)
Abbonamento annuale cartaceo + digitale:
EMEA 110,00 € (spese postali incluse)
Resto del mondo 350,00 € (spedizione via aerea inclusa)
Single copy: 15,00 € EMEA (postage included) - Rest of world (postage excluded)
Back issues: 30,00 € EMEA (postage included) - Rest of world (postage excluded)
Fascicolo singolo: 15,00 € EMEA (spese postali incluse) - resto del mondo (spese postali escluse)
Arretrati: 30,00 € EMEA (spese postali incluse) - resto del mondo (spese postali escluse)
The smart journal for surface treatments
This magazine is wrapped with a biodegradable and compostable film. Questa rivista è confezionata con un film biodegradabile e compostabile.
PRINT/ STAMPA
SEBEGRAF SRL info@sebegraf.eu
Subscriptions can be made via payment online at: www.myipcm.com
Subscription and the sale of individual issues are exempt from VAT under Italian law: Article 74.1, letter C of DPR 633/72, DM 29/12/1989.
Gli abbonamenti possono essere sottoscritti con carta di credito sul sito: www.myipcm.com L’Iva sugli abbonamenti, nonchè sulla vendita di singole copie è assolta ai sensi dell’art.74 comma 1 lett. C DPR 633/72, DM 29/12/1989.
Registrazione al Tribunale di Monza N° 1970 del 10 Dicembre 2009Eos Mktg&Communication srl è iscritta nel Registro degli Operatori di Comunicazione con il numero 19244
POSTE ITALIANE S.P.A. – SPEDIZIONE IN ABBONAMENTO POSTALE –D.L. 353/2003 (CONV. IN L. 27/02/2004 N.46) ART. 1, COMMA 1 LOM/MI/4351
It is forbidden to reproduce articles and illustrations of “ipcm®” without authorization and without mentioning the source. The ideas expressed by the authors do not commit nor magazine nor eos Mktg&Communication S.r.l and responsibility for what is published is the authors themselves.
È vietata la riproduzione di articoli e illustrazioni di “ipcm®” senza autorizzazione e senza citarne la fonte. Le idee espresse dagli autori non impegnano nè la rivista nè eos Mktg&Communication S.r.l e la responsabilità di quanto viene pubblicato rimane degli autori stessi.
There’s no single answer to sustainability, but small changes to the products you use and the way that you use them can make a big difference in the long run. Like choosing Interpon D2525 Low-E, a low energy powder coating. It’s a superdurable powder coating that achieves an industry first in being able to cure at temperatures as low as 150ºC while still being Qualicoat Class 2 certified. Whether you cure at a lower temperature, or at a faster line speed, either way you win by reducing the total energy consumed, lowering carbon emissions, and enhancing production line efficiencies. Interpon D2525 Low-E is easy to apply, provides excellent edge coverage and comes in a wide range of colors and textures, which means more right-first-time results requiring less re-working and near zero rejection rates.