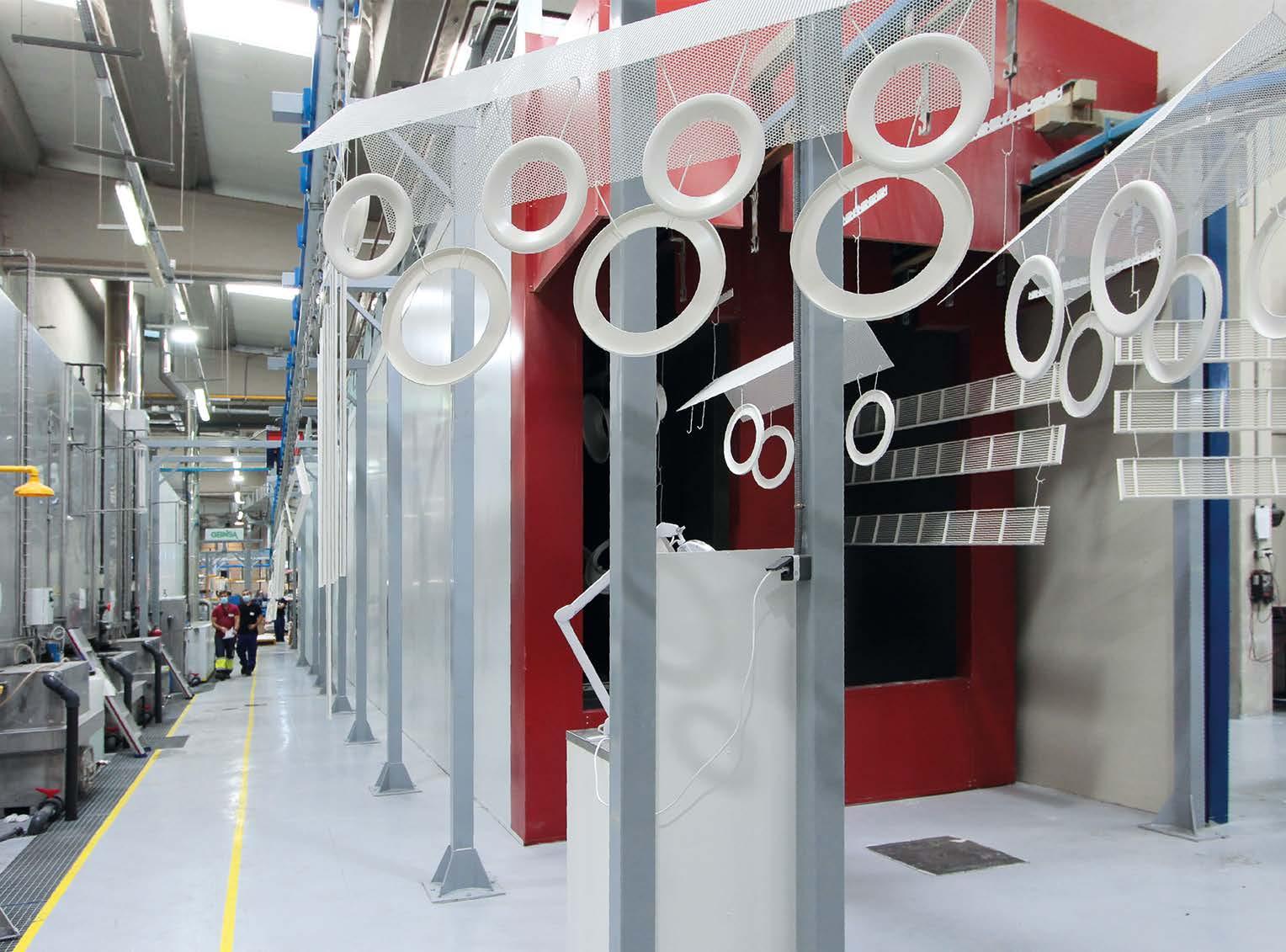
18 minute read
APUESTA POR LA TECNOLOGÍA FOCO NA TECNOLOGIA
Difusores de diferentes geometrias colgados a la linea automática de pintura en polvo instalada por Koolair en su planta de Móstoles.
Difusores com geometrias diversas pendurados na linha de pintura a pó automática instalada pela Koolair em sua fábrica de Móstoles.
Invertir en una línea de cambio rápido de color para el acabado de componentes para sistemas de climatización. El caso de éxito de Koolair.
El acabado superficial es fundamental para los componentes de sistemas de acondicionamento del aire. Además de tener una función estética, el recubrimiento en polvo permite proteger el soporte metálico de la oxidación y personalizar los productos. Por eso Koolair invirtió en una línea de pintura con cabina de cambio rápido de color de Gema.
© ipcm
Investir em uma linha com mudança rápida de cores para o acabamento de componentes para sistemas de ar condicionado. A história do sucesso da Koolair.
O acabamento superficial é fundamental para os componentes para sistemas de ar condicionado. Além de apresentar um papel estético, o revestimento em pó permite proteger o suporte metálico contra a oxidação e personalizar os produtos. Por esta razão a Koolair investiu em uma linha de pintura com uma cabine de mudança rápida de cores fornecida pela Gema.
Componentes de sistemas de acondicionamento del aire proceden del túnel de pre-tratamiento al horno de secado.
Os componentes dos sistemas de ar condicionado passam do túnel de pré-tratamento para o forno de secagem.
© ipcm
“Desde finales de 2018 la empresa Koolair, especializada en productos de distribución de aire, pertenece a una multinacional sueca, el grupo Systemair. En 2019 este grupo tomó el control de la empresa y desde entonces ha apoyado fuertemente la inversión en tecnologías de producción en la planta de Móstoles” empieza Teodoro Rueda Cabrero, Director de Operaciones Industriales de Koolair. “Invertimos primero en una línea automática de punzonado compuesta por dos punzonadoras eléctricas en paralelo y alimentadas permanentemente por una línea de 6 bobinas de metal de 6 Tn de diferentes espesores; luego, en 2020, en una línea de pintura en polvo automática con cabina de cambio rápido de color; finalmente en 2021 invertiremos en otra línea automática de mecanizado. En tres años, y en el medio de una pandemia, Koolair ha completamente revolucionado sus tecnologías productivas”. “La mayoría de nuestros productos están pintados en sus partes externas y visibles. La materia prima utilizada para la fabricación de los difusores es aluminio, chapa galvanizada y chapa sin tratamiento superficial. El 90% de productos fabricados en chapa se fabrica a partir de chapa galvanizada. La porción de difusores, principalmente para edificios industriales, que van totalmente en galvanizado o en aluminio anodizado, es decir sin pintura, es muy pequeña. “Desde o final de 2018, a empresa Koolair, especializada em produtos para distribuição de ar, faz parte do grupo multinacional sueco Systemair. Em 2019 este grupo assumiu o controle da empresa e, desde então, vem incentivando os investimentos em tecnologias de produção na fábrica de Móstoles”, diz Teodoro Rueda Cabrero, diretor de processos industriais da Koolair. “No começo, investimos em uma linha automática de puncionamento composta por duas puncionadeiras elétricas em paralelo e alimentadas em modo permanente por uma linha de 6 bobinas metálicas de 6 toneladas com várias espessuras. Depois, em 2020, investimos em uma linha de pintura automática a pó, com mudança rápida de cores. Enfim, em 2021, investiremos em outra linha de produção automática. Em 3 anos, em plena pandemia, a Koolair revolucionou completamente suas tecnologias de produção”. “A maior parte dos nossos produtos é pintada nas partes externas e visíveis. A matéria-prima utilizada na fabricação dos difusores são alumínio, chapas galvanizadas e chapas sem tratamento de superfície. Dos produtos de chapa de metal, 90% são processados com chapa galvanizada. A quantidade de difusores, principalmente destinados a edifícios industriais, fabricados totalmente com alumínio galvanizado ou anodizado e, portanto, não pintados, é muito pequena. Todos os nossos difusores de ar de alumínio podem ser pintados ou

© ipcm © ipcm
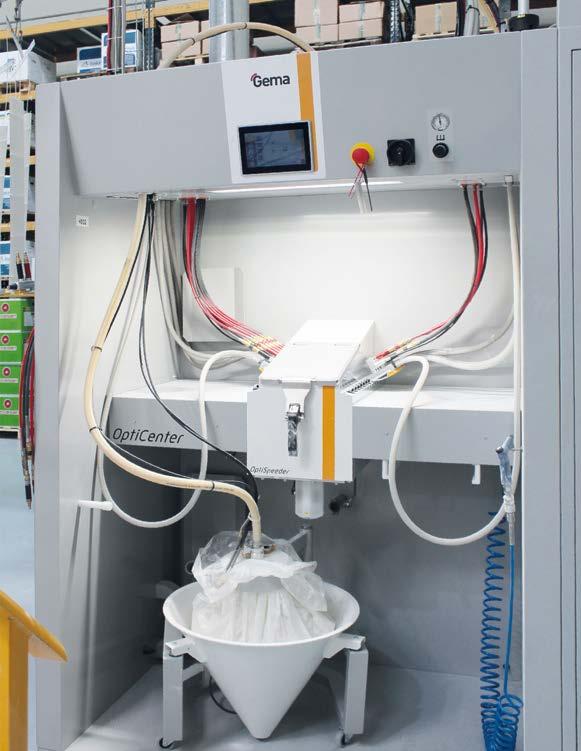
Aplicación de polvo poliester en la cabina Gema EquiFlow BA04 que tiene dos salas de retoque manual, antes y después de la aplicación automática. A la derecha: la central de polvo OptiCenter® OC08 que proporciona una gestión del polvo eficiente en circuito cerrado.
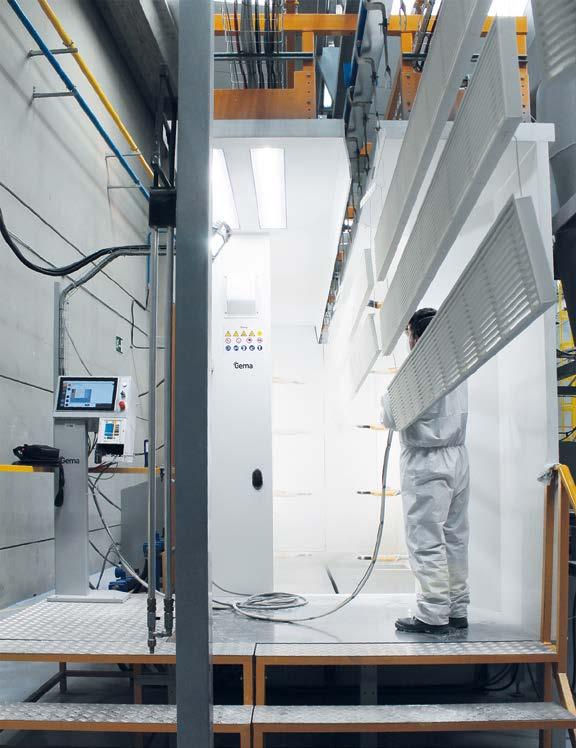
Aplicação de pós de poliéster na cabine EquiFlow BA04, da Gema, equipada com duas estações de retoque manual, antes e depois da aplicação automática. A direita: a central de pó OptiCenter® OC08 que permite uma gestão eficiente de pó em circuito fechado.
Todos nuestros difusores de aire en aluminio tienen la posibilidad de ser pintados o anodizados. El acabado superficial es fundamental para los productos Koolair, tanto para los fabricados a partir de chapa como los fabricados a partir de aluminio, y la inversión en una línea de pintura con cabina de cambio rápido de color ha sido estratégica”. Fundamental en el proceso de elección de la tecnología, en la fase de pruebas industriales y de servicio técnico fue la colaboración con System Pulver S.L. de Sant Just Desvern, Barcelona, distribuidor oficial y exclusivo de las tecnologías Gema, con el proveedor de la instalación, Geinsa de Bilbao y del proceso y las automaciones de pretratamiento, Proquimia de Vic.
Sobre la empresa
El Grupo Koolair, perteneciente al grupo Systemair, es líder especializado en la fabricación de productos de difusión y distribución anodizados. O acabamento superficial é fundamental para os produtos Koolair, tanto para os produtos processados em chapa metálica, quanto para os processados em alumínio, e o investimento em uma linha de pintura com mudança rápida de cores foi estratégico”. Um fator fundamental durante a escolha da tecnologia e na fase dos testes e assistência técnica, foi a colaboração com a System Pulver S.L., de Sant Just Desvern (Barcelona), distribuidor exclusivo oficial das tecnologias Gema, com a Geinsa de Bilbao, fornecedora do equipamento, e a Proquimia, de Vic, fornecedora do processo de prétratamento e automação.
Sobre a empresa O grupo Koolair, parte do grupo Systemair, é uma empresa líder especializada na fabricação de produtos de difusão e distribuição de
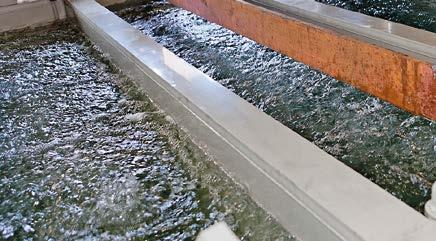
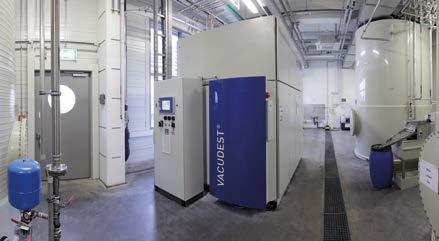
de aire y destaca por el desarrollo, diseño e innovación de sus productos ensayados en su propio laboratorio de I+D+i, uno de los más modernos y avanzados en difusión de aire y acústica. Rejillas, difusores de diferentes geometrías, además de productos para la protección contra incendios, sistemas aire/agua, VAV/VAC, componentes para salas limpias y hospitales, sistemas de control de temperatura por zonas para instalaciones de aire acondicionado forman la gama muy amplia de productos de Koolair, que se distribuyen habitualmente en toda Europa y en otros países del área mediterránea y Sudamérica. Pertenece al grupo Koolair la empresa Safeair S.L., creada en enero de 2001 y que fabrica equipos de protección contra incendios, como compuertas cortafuegos circulares y cuadradas, además de compuertas de evacuación de humos. El Grupo Koolair tiene 3 centros de producción: el más grande se encuentra en Móstoles, cerca de Madrid, los otros dos en la provincia de Toledo, el ya mencionado Safeair y Metalistería Medular. “El Grupo emplea en torno a 400 personas y genera 33 millones de euros de facturación” explica Teodoro Rueda. “Aproximadamente el 50% de las ventas se producen fuera de España. Koolair posee una red comercial propia en algunos países y en otros vende a través de la red comercial de Systemair. Los principales mercados son España, Portugal, Inglaterra, Francia, Países Bajos, Italia, Alemania, y centro de Europa. Tenemos también red comercial en el norte de África”.
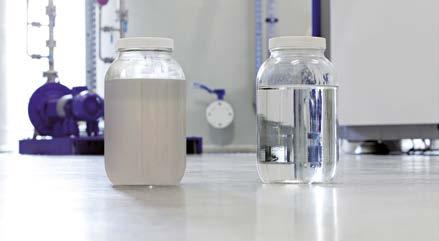
Estética y funcionalidad del recubrimiento
“El recubrimiento de nuestros productos tiene un papel estético y funcional: aunque son productos que van al interior, donde los requerimientos de durabilidad no son muy exigentes como para los componentes que van al exterior, el acabado es fundamental para evitar la oxidación del soporte metálico. Por este motivo utilizamos polvos poliésteres para exterior para dar a todos nuestros productos una calidad superior con una resistencia de aproximadamente 700 horas hasta las 1000 horas en niebla salina. Nuestro objetivo siempre es fabricar un producto de altas prestaciones. Incluso el proceso de pretratamiento de 5 etapas fue ar e se destaca pelo desenvolvimento, projeto e inovação de produtos testados em seu laboratório de P,D&I, um dos mais modernos e avançados em difusão de ar e em acústica. As grelhas, os difusores de várias geometrias, além de produtos para proteção contra incêndio, os sistemas de ar/água, VAV/AVAC, os componentes para salas limpas e hospitais, os sistemas de termo-regulação por zona para sistemas de ar condicionado fazem parte da vastíssima gama de produtos Koolair, regularmente distribuídos em toda a Europa e outros países na área do Mediterrâneo e na América do Sul. A Safeair S.L., fundada em janeiro de 2001, fabricante de dispositivos de combate a incêndio, como dampers corta fogo circulares e quadrados, além de dampers para evacuação de fumaça, pertence ao grupo Koolair. O grupo Koolair possui três fábricas: a maior se encontra em Móstoles, perto de Madrid, as outras duas, Safeair e Metalistería Medularna, na província de Toledo. “O grupo emprega cerca de 400 pessoas, com um volume de negócios de 33 milhões de euros”, explica Teodoro Rueda. “Cerca de 50% das vendas são realizadas fora da Espanha. A Koolair tem sua própria rede comercial em alguns países, enquanto, em outros, vende por meio da rede comercial da Systemair. Os principais mercados são: Espanha, Portugal, Inglaterra, França, Holanda, Itália, Alemanha e Europa Central, mas também temos uma rede comercial no norte da África”.
Estética e funcionalidade do revestimento “O revestimento dos nossos produtos desempenha um papel estético e funcional: embora tratem-se de produtos para uso interno, onde os requisitos de durabilidade não são tão rígidos quanto os dos componentes para uso externo, o acabamento é fundamental para evitar a oxidação do suporte de metal. Por isso, usamos pós de poliéster para uso externo, para dar a todos os nossos produtos uma qualidade superior com uma resistência de cerca de 700 - 1000 horas em névoa salina. Nosso objetivo é sempre criar um produto com alto desempenho. O processo de pré-tratamento com cinco estágios
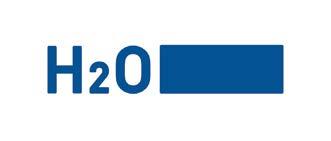
Los Expertos en Vertido Cero de Aguas Residuales.
Tratamiento de Aguas Residuales Industriales
Un Principio Fácil
Resultados Efectivos
Empresas lideres cuentan con sistemas de destilación al vacío para el tratamiento sostenible de aguas residuales industriales.
Usted también quiere beneficiarse de una producción libre de aguas residuales con el VACUDEST?
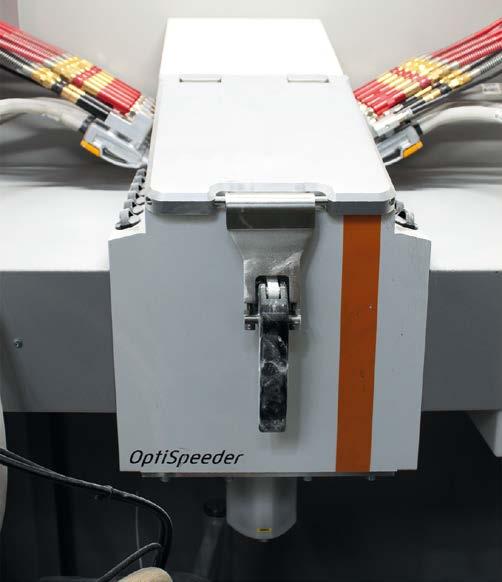
© ipcm © ipcm
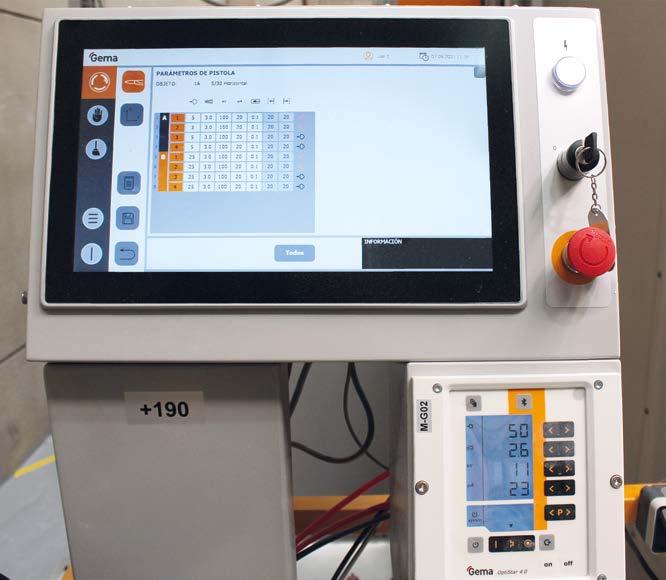
Los inyectores son de la línea OptiFlow IG07-PA de nueva generación que garantizan un flujo de polvo constante, un cambio de color optimizado y costes de operación económicos. A la derecha: el sistema MagicControl 4.0 garantiza una conexión inteligente entre todos los componentes de la aplicación. A nova geração de injetores da linha OptiFlow IG07-PA que garantem um fluxo constante de pó, mudança de cor otimizada e baixos custos operacionais. A direita: o sistema MagicControl 4.0 garante uma conexão inteligente entre todos os componentes da aplicação.
elegido por este motivo: porque nos garantiza una calidad superior y sobre todo una protección y una durabilidad muy altas” afirma Teodoro Rueda. “El 80% de nuestra producción está pintado en blanco: tenemos 3 blancos cuyo uso es más habitual. Sin embargo, tenemos una gran cantidad de colores para lotes pequeños porque pintamos a requerimiento del cliente, ya que toda la producción es bajo pedido. Nuestro objetivo es satisfacer las necesidades de los clientes y por lo tanto ofrecemos prácticamente toda la carta RAL a nuestros clientes. “Las ventajas de pintar internamente nuestra propia producción son evidentes” sigue Rueda. “El hecho de poder controlar el proceso de pintura es una ventaja competitiva muy importante a la hora de ofrecer un excelente servicio al cliente y una garantía de calidad. Lógicamente hay también un interés económico: cuando estudiamos el proyecto, vimos que la inversión podría ser amortizada en un tiempo razonable”.
El proceso y la instalación de pintura
La línea de pintura instalada en la planta de Koolair en Móstoles pinta la producción de las tres fábricas al ser la única instalación de pintura dentro del grupo Koolair. Con un promedio de 4/5 cambio de colores cada turno, Koolair ha elegido la tecnología Gema de última generación também foi escolhido por este motivo: porque nos garante qualidade superior e, sobretudo, proteção e durabilidade muito elevadas”, diz Teodoro Rueda. “De toda a nossa produção, 80% é pintada de branco: temos três brancos cuja aplicação é a mais comum. No entanto, temos uma grande quantidade de cores para pequenos lotes, a pedido do cliente, já que toda a produção é feita por encomenda. Nosso objetivo é atender às necessidades dos clientes e por isso oferecemos o catálogo completo de cores RAL”. “As vantagens de pintar nossa produção internamente são óbvias”, explica Rueda. “Poder controlar o processo de pintura é uma vantagem competitiva muito importante para oferecer um excelente atendimento ao cliente e garantia de qualidade. Obviamente há também um interesse econômico: quando estudamos o projeto, calculamos que o investimento poderia ser amortizado em um prazo razoável”.
O processo e o sistema de pintura A linha de pintura instalada na fábrica da Koolair em Móstoles pinta os produtos das três empresas, por tratar-se do único sistema de pintura do grupo Koolair. Com uma média de 4/5 mudanças de cor por turno, a Koolair escolheu a tecnologia Gema de última geração para obter
con el fin de conseguir cambios rápidos de color, alta calidad en la aplicación y la mayor eficiencia en el consumo de polvo. “La cabina de aplicación, suministrada por Gema es la EquiFlow BA04, diseñada especialmente para aplicaciones que requieren cambios de color frecuentes. El uso de materiales no conductores en combinación con la tecnología EquiFlow (una tecnología patentada de distribución precisa del aire de aspiración) junto a la central de polvo OptiCenter OC08 garantizan una limpieza de la cabina más rápida y una mejor calidad de recubrimiento. La cabina de Koolair tiene dos salas de retoque manual (antes y después las pistolas automáticas), que se utilizan también para pintar en manual lotes muy pequeños de colores diferentes”, explica David Serrano, comercial de System Pulver. “Las piezas vienen del túnel de secado: antes de la entrada a la cabina de aplicación tenemos una barrera de reconocimiento que lee la silueta y el tamaño de las piezas para ajustar distancia y carrera de los reciprocadores, que están equipados con 4 pistolas por lado”. “La central del polvo, donde gestionamos toda la recuperación, el suministro del polvo virgen y del polvo recuperado, es el OptiCenter® OC08 que proporciona una gestión del polvo eficiente en circuito cerrado. Los inyectores son modelo OptiFlow IG07-PA de nueva generación que garantizan un flujo de polvo constante, un cambio de color optimizado y costes de operación económicos. Cabina, mudanças rápidas de cores, alta qualidade de aplicação e máxima eficiência no consumo de pó. “A cabine de aplicação fornecida pela Gema é a EquiFlow BA04, especialmente projetada para aplicações que requerem mudanças frequentes de cor. A utilização de materiais não condutores, combinada com a tecnologia EquiFlow (tecnologia patenteada para distribuição precisa do ar de aspiração) em conjunto com a central de pó OptiCenter OC08, garantem a limpeza mais rápida da cabine e melhor qualidade do revestimento. A cabine da Koolair possui duas estações de retoque manual (antes e depois das pistolas automáticas), que também são utilizadas para pintar manualmente pequenos lotes de cores diferentes”, explica David Serrano, técnico comercial da System Pulver. “As peças chegam do túnel de secagem: antes do ingresso na cabine de aplicação temos uma barreira de reconhecimento que detecta a forma e as dimensões das peças para definir a distância e o percurso dos reciprocadores, equipados com 4 pistolas por lado”. “A central de pó, onde gerenciamos todo o recupero, a alimentação do pó virgem e do pó recuperado, é OptiCenter® OC08, que permite a gestão eficiente do pó em circuito fechado. Os injetores são modelo OptiFlow IG07-PA de última geração e garantem um fluxo de pó constante, mudança de cor otimizada e baixos custos operacionais. A cabine, a central de pó e os dispositivos automáticos são controlados
El sistema de control automático de los parametros operativos del proceso de pretratamiento instalado por Proquimia. O sistema de controle automático dos parâmetros operacionais do processo de pré-tratamento instalado pela Proquimia.
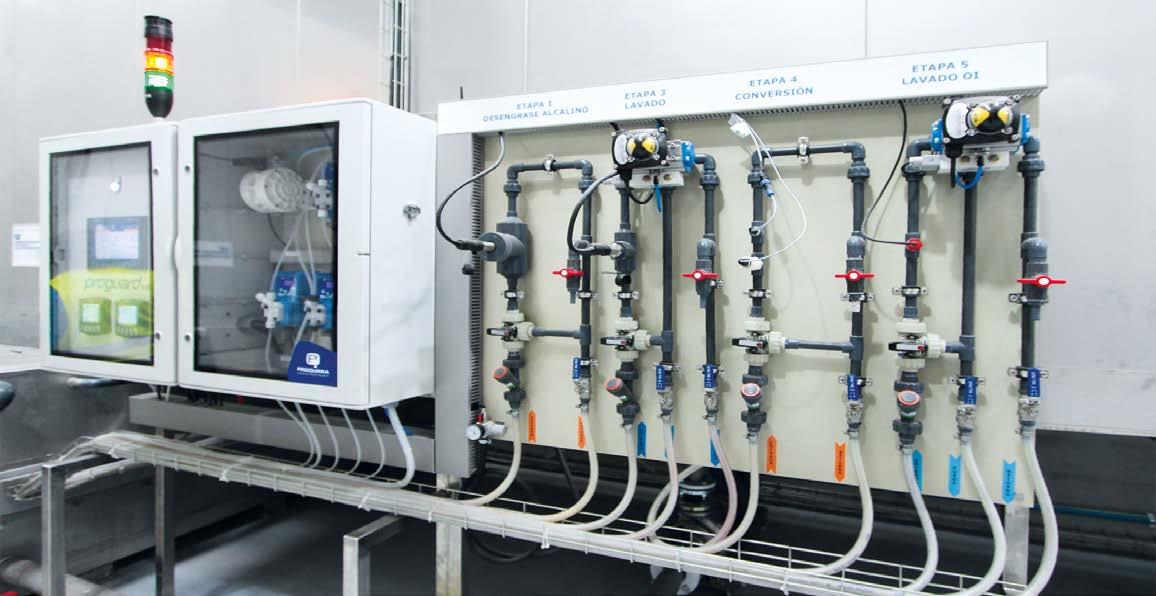
© ipcm
Vista general de la instalación diseñada y suministrada por Geinsa.
Vista panorâmica do sistema projetado e fornecido pela Geinsa.
© ipcm
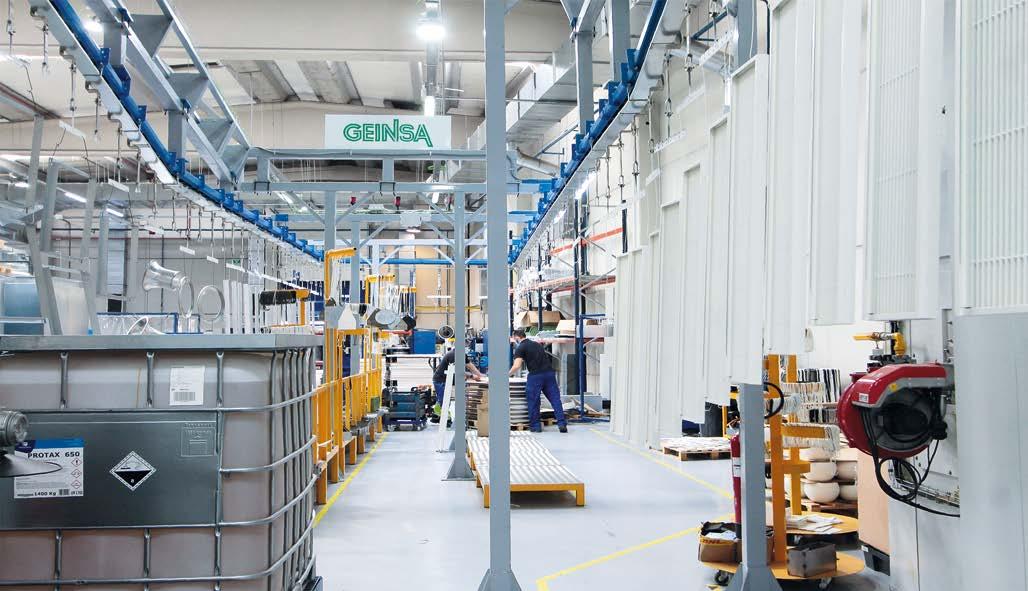
central del polvo y equipos automáticos se controlan con el sistema MagicControl 4.0 (CM40), que garantiza una conexión inteligente entre todos los componentes de la aplicación, y que proporciona toda la información estadística de la línea con el fin de controlar y conocer el proceso detalladamente” prosigue Serrano. “Con la central de polvo OptiCenter® OC08 y el sistema de control CM40 es posible programar automáticamente el tiempo y las modalidades de limpieza, eligiendo entre una forma del limpieza “sencilla” y una “profunda” para cambios de color muy radicales, o bien una personalizada según las necesidades del cliente. Además, hemos suministrado a Koolair una cabina de aplicación manual fuera de la línea con pistolas manuales para pintar lotes muy pequeños, muestras o piezas recuperadas. Esta cabina trabaja a polvo perdido con su propio filtro, como un equipo de pintura independiente”. Además del sistema innovador de aplicación y control de la pintura en polvo, en la línea de Koolair destaca el proceso de petratamiento, que disfruta de la tecnología a cascada inversa y que se compone de 5 etapas: • Desengrase • Primer lavado • Segundo lavado • Conversión con nanotecnología • Lavado final con agua osmotizada de alta calidad. El ciclo de pretratamiento, diseñado por Proquimia, tiene un sistema para el control telemático constante y continuo de los parámetros operativos del túnel. pelo sistema MagicControl 4.0 (CM40), que garante uma conexão inteligente entre todos os componentes da aplicação e fornece todas as informações estatísticas da linha com o objetivo de controlar e conhecer o processo em detalhe” diz Serrano. “Com a central de pó OptiCenter® OC08 e o sistema de controle CM40 é possível programar automaticamente os tempos e os métodos de limpeza, escolhendo entre um método de limpeza “simples” ou “profundo” para mudanças de cor muito radicais, ou um personalizado, dependendo da necessidade do cliente. Além disso, fornecemos à Koolair uma cabine de aplicação manual fora da linha, com pistolas manuais, para pintar lotes muito pequenos, amostras ou peças recuperadas. Essa cabine trabalha com pó descartável com filtro próprio, como uma oficina de pintura independente”. Além do novo sistema de aplicação e o controle de pintura a pó, na linha Koolair se destaca o processo de pré-tratamento que utiliza a tecnologia de cascata reversa e que consiste em 5 estágios: • Desengorduramento • Primeira lavagem • Segunda lavagem • Conversão nanotecnológica • Lavagem final com água osmótica de alta qualidade. O ciclo de pré-tratamento, elaborado pela Proquimia, é equipado com um sistema de controle telemático constante e contínuo dos parâmetros de funcionamento do túnel.
Un alto nivel de satisfacción: un trabajo en equipo
“Para cada una de las 3 partes del proyecto, o sea aplicación, ingeniería y parte química elegimos a las tres empresas que a nuestro criterio son la referencia del sector” concluye Teodoro Rueda. “El factor confianza y cercanía fue fundamental a la hora de elegir los partners. Para mí es fundamental que los partner estén presentes y colaboren con nosotros: Gema, Geinsa y Proquimia me trasmitieron confianza. Gema fue nuestro primer contacto cuando decidimos abordar esta inversión, y nos ayudó a entender el proceso y la tecnología requerida: fueron muy cercanos a nosotros durante este proyecto y nos siguen brindando una asistencia muy profesional cuando son requeridos. Lógicamente han jugado un papel importante los factores económicos y técnicos, pero los factores servicio y confianza fueron fundamentales, sobre todo porque Koolair nunca había tenido experiencia con una instalación de pintura. Hasta ahora estamos muy satisfechos con la elección de este equipo de proveedores. Desde que se instaló la línea a que se puso en marcha ha pasado muy poco tiempo y nunca hemos tenido problemas técnicos”. Alto nível de satisfação: um trabalho de equipe “Para cada uma das três partes do projeto, ou seja, aplicação, projeto e química, escolhemos as três empresas que, a nosso ver, são as referências do setor”, conclui Teodoro Rueda. “Os fatores confiança e proximidade foram fundamentais na escolha dos parceiros. Para mim, é essencial que os parceiros estejam presentes e colaborem conosco: Gema, Geinsa e Proquimia me inspiraram confiança. A Gema foi nosso primeiro contato, quando decidimos enfrentar este investimento, e nos ajudou a entender o processo e a tecnologia necessária: eles nos acompanharam de perto durante este projeto e continuam a nos fornecer uma assistência muito profissional quando necessário. Claro, os fatores econômicos e técnicos desempenharam um papel importante, mas os fatores de serviço e confiança foram fundamentais, especialmente porque a Koolair nunca tinha tido experiência com um sistema de pintura. Até hoje estamos muito satisfeitos com a escolha desta equipe de fornecedores. Desde a instalação da linha até a sua entrada em operação, passou pouquíssimo tempo e nunca tivemos problemas técnicos ”.
¡Descubre el WOW en el know-how!
¡Nuevo eLearning HUMECTANTES DE SUBSTRATO disponible! COATINO® Campus — El nuevo estándar para la transferencia de conocimientos en la industria de recubrimientos y tintas.
Obtenga acceso a información que simplifica su trabajo de formulación, ahorra tiempo y conduce a un mejor rendimiento del recubrimiento y la tinta. ¡Su última plataforma de aprendizaje está a solo un clic de distancia.
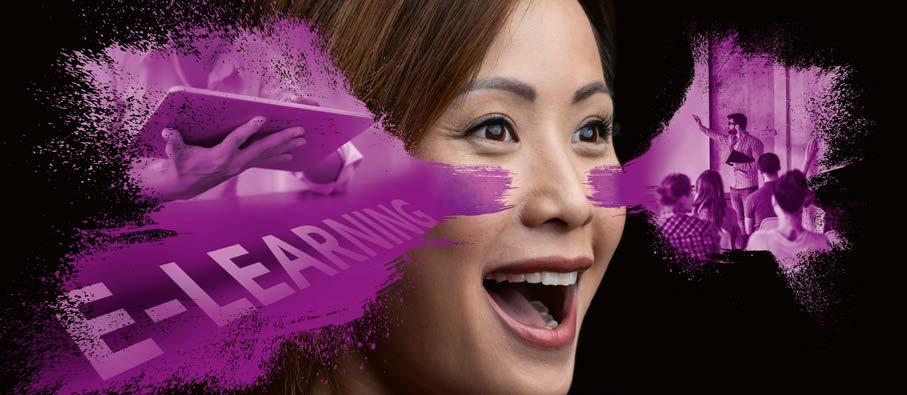