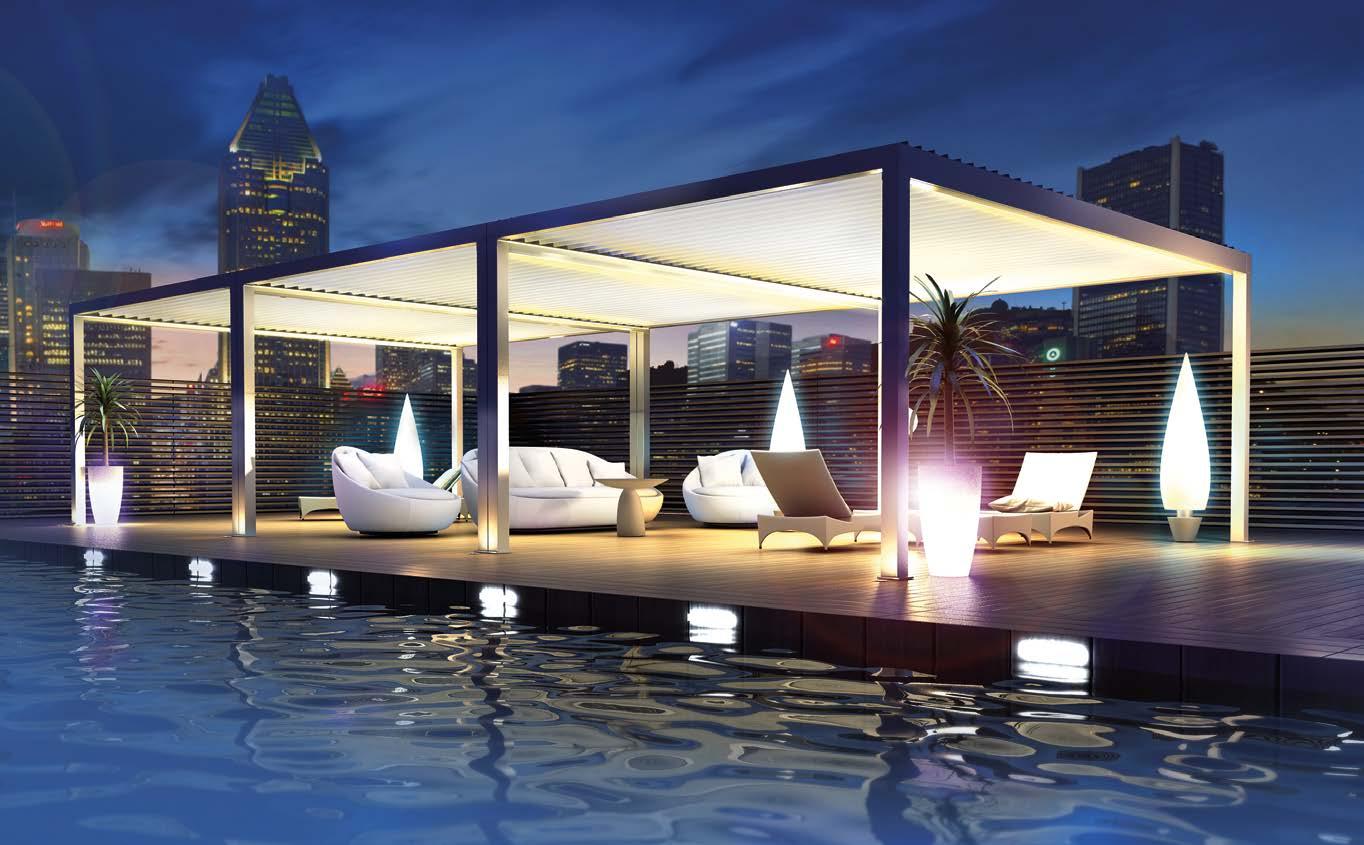
24 minute read
APUESTA POR LA TECNOLOGÍA
Aumento de la producción de hasta el 80% y de la eficiencia energética extrema gracias a una instalación vertical de última generación. El caso de éxito de Proylac, Protecciones y Lacados
Con 40 años de experiencia en el sector de perfilería de aluminio las empresas Aluminios Galisur – Proylac conocen muy bien las necesidades de este sector. La compañía lleva 4 años reformando completamente la logística de la fábrica en Sevilla e invirtiendo en maquinaria y líneas de producción nuevas y mucho más eficientes. Este proceso ha llevado a la empresa Proylac a instalar una nueva línea vertical de lacado de perfiles suministrada por Euroimpianti España, lo que ha aumentado más del doble la productividad y ha reducido a la mitad los consumos de recursos naturales.
Até 80% de aumento da produção e extrema eficiência energética, graças a um sistema vertical de última geração: a história bem sucedida da Proylac, Protecciones y Lacados
Com 40 anos de experiência no setor de perfis de alumínio, as empresas Aluminios Galisur - Proylac conhecem muito bem as necessidades do setor. É por isso que a empresa passou 4 anos revolucionando completamente a logística de produção da fábrica de Sevilha e investindo em máquinas e linhas de produção novas e muito mais eficientes. Este processo levou a empresa Proylac a instalar uma nova linha vertical de pintura de perfis fornecida pela Euroimpianti Espanha, que mais que dobrou a produtividade da antiga linha e reduziu à metade o consumo de recursos naturais.

© ipcm © ipcm

Una de las prensas de extrusión y el almacén de matrices. Uma das prensas de extrusão e o depósito das matrizes.
Con los costes de energía en continua subida y sin ver el final de este interminable encarecimiento de gas y electricidad, realizar inversiones que se enfoquen en la eficiencia energética y en el ahorro de recursos y materiales es imperativo.
En algunos casos esta exigencia se relaciona estrechamente con la necesidad de revolucionar completamente la organización productiva de una empresa, por ejemplo para mejorar el flujo de producción, reducir al mínimo la logística y la manipulación de materiales o dar orden a las diferentes fases productivas. Esto ocurre sobre todo cuando hay un relevo generacional – deseado o forzado – a la cabeza de una empresa. Situación que ocurrió en Protecciones y Lacados
S.L., empresa de extrusión, lacado y anodizado de perfiles en aluminio para arquitectura e industria situada en Alcalá de Guadaíra, Sevilla, que forma junto con Aluminios Galisur S.L. el grupo de empresas de la familia López Conde, hoy dirigido por Don Jesús López Conde, hijo del fundador. Un programa de inversión muy amplio de varios millones de euros que dio comienzo hace 4 años ha revolucionado totalmente la organización productiva, no solamente desde el punto de vista de la eficiencia sino también de la productividad. De hecho, gracias a la inversión de dos instalaciones de lacado de
Euroimpianti España – una carrusel en 2019 y una en vertical de nueva concepción a finales de 2021, que ha sustituido la planta antigua – Proylac ha logrado aumentar el 80% el lacado de perfiles en vertical y hasta el 50% el lacado de chapa y pequeños lotes de color en la horizontal; así como reducir a la mitad el consumo de recursos energéticos y automatizar completamente todas las fases productivas.
“En la época de mi padre el concepto de desarrollo industrial era ir a la máxima productividad, tal vez invirtiendo en maquinaria e instalaciones sobredimensionadas, incluso desde el punto de vista del consumo y de Com os custos do gás e da eletricidade aumentando continuamente em uma corrida sem fim, fazer investimentos visando a eficiência energética e a economia de recursos e materiais é essencial.
Em alguns casos, essa exigência está intimamente relacionada à necessidade mais ampla de revolucionar completamente a organização produtiva de uma empresa, por exemplo, melhorar seu fluxo de produção, minimizar a logística e a manipulação dos materiais o organizar as várias fases de produção. Isto acontece principalmente quando há uma mudança geracional – desejada ou forçada – no comando de uma empresa. E foi exatamente isso que aconteceu com a
Protecciones y Lacados S.L., empresa de extrusão, pintura e anodização de perfis de alumínio para arquitetura e a indústria de Alcalá de Guadaíra, Sevilha, que, com a Aluminios Galisur S.L., constitui o grupo de empresas da família López Conde, hoje liderada por Jesús López
Conde, filho do fundador. Um vastíssimo programa de investimentos de vários milhões de euros que começou há 4 anos e revolucionou completamente a organização da produção, não só do ponto de vista da eficiência, mas também da produtividade. Na verdade, graças ao investimento em dois sistemas de pintura da
Euroimpianti Espanha (um a carrossel, em 2019, e outro vertical, com nova concepção, no final de 2021, que substituiu o antigo sistema), a Proylac obteve: um aumento de 80% na pintura vertical de perfis e até 50% na pintura horizontal das chapas e pequenos lotes de cor; quase metade do consumo de recursos energéticos e a automatização completa de todas as fases de produção. “Na época do meu pai, o conceito de desenvolvimento industrial correspondia ao máximo de produtividade, talvez investindo em máquinas e equipamentos superdimensionados, também do ponto
la potencia energética”, comenta Jesús López Conde. “Sin embargo, hoy Proylac ha buscado invertir en unas plantas que fuesen eficientes energéticamente y que pudieran aprovechar la energía proporcionada por las placas solares que cubren el techo de la fábrica”.
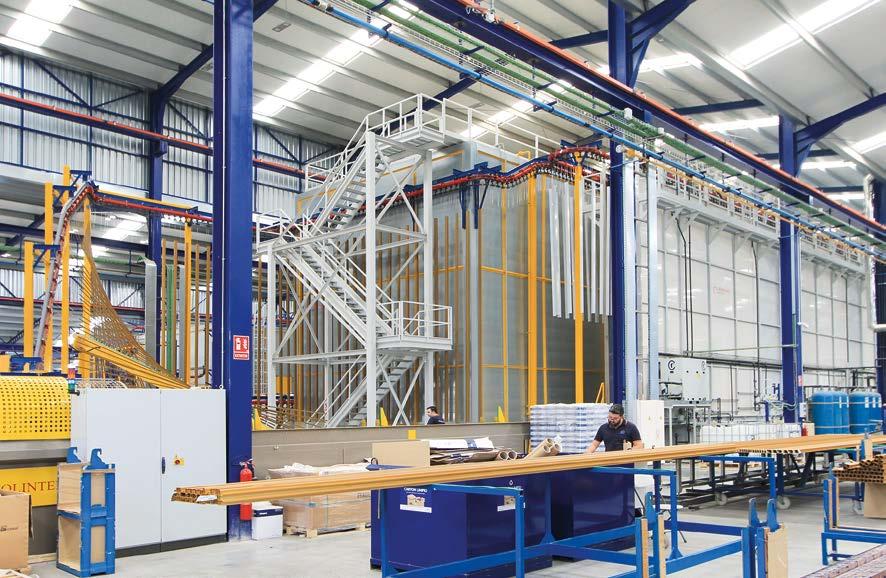
Más de 40 años en perfilería de aluminio
Aluminios Galisur S.L comienza su andadura en 1978 con sede social en Sevilla y con la premisa de dar el servicio de distribución de perfiles de aluminio y accesorios destinados al sector de la carpintería de aluminio. Incidiendo así en la zona sur de España, hasta aquel entonces poco industrializada. “Mi padre comenzó trabajando como comercial en una empresa de aluminio que se llamaba la Viuda del Tornante, en Alicante. Él llevaba la zona de Sevilla, Cádiz y Badajoz. En poco tiempo se convirtió en el comercial que más aluminio vendía de esa empresa”, nos cuenta Jesús López Conde. “En 1978 decidió montar su almacén en solitario en Sevilla: nace Aluminios Galisur, en una nave de 150 m2, para distribuir aluminio de Enespan, la industria estatal de aluminio. La empresa se fue desarrollando muy bien y a comienzos de los años 80 decidió trasladarse a Alcalá de Guadaíra, comprando una empresa de lacado, Protecciones y Lacado (Proylac) que existía allí: así empieza la andadura industrial de Aluminios Galisur”. “Aquella época representó un boom para España ya que fue el periodo de transición de la dictadura a la democracia y de la entrada, en 1986, en la Unión Europea. Se construyó mucho en aquellos años y el
© ipcm
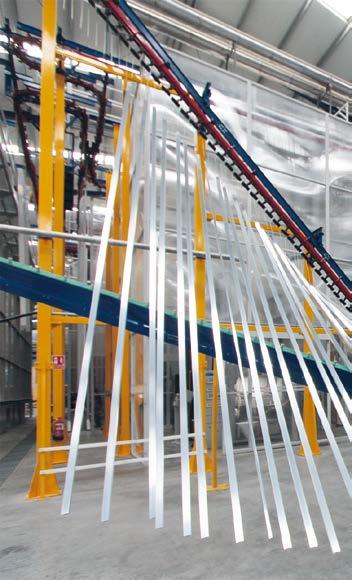
de vista de consumo e potência energética”, diz Jesús López Conde. “No entanto, hoje a Proylac procurou investir em sistemas que fossem eficientes do ponto de vista energético e que poderiam aproveitar a energia fornecida pelos painéis solares que cobrem o telhado da fábrica.”
Mais de 40 anos no setor de perfis de alumínio A Aluminios Galisur S.L iniciou a sua atividade em 1978 em Sevilha para a distribuição de perfis de alumínio e acessórios para o setor da carpintaria de alumínio. Assim, entrou no sul da Espanha, que até então ainda era pouco industrializado. “Meu pai começou a trabalhar como comerciante em uma empresa de vendas de alumínio chamada ‘La Viuda del Tornante’, em Alicante. Foi responsável pela área de Sevilha, Cádiz e Badajoz. Em pouco tempo tornou-se o vendedor que mais vendia alumínio daquela empresa”, conta Jesús López Conde. “Em 1978 decidiu abrir sozinho um depósito em Sevilha: nasceu a Aluminios Galisur, em um galpão de 150 m², para distribuir o alumínio da Enespan, a indústria estatal do alumínio. A empresa estava crescendo muito bem e no início da década de 1980 decidiu se mudar para Alcalá de Guadaíra, adquirindo uma empresa de pintura, Protecciones y Lacado (Proylac), que tinha sede ali: foi assim que começou a atividade industrial da Alumínios Galisur". "Esse período foi um boom para a Espanha porque foi o momento da transição da ditadura para a democracia e a entrada, em 1986, na União Europeia. Muito foi construído naqueles anos e o setor de arquitetura e alumínio passou por um crescimento muito rápido.
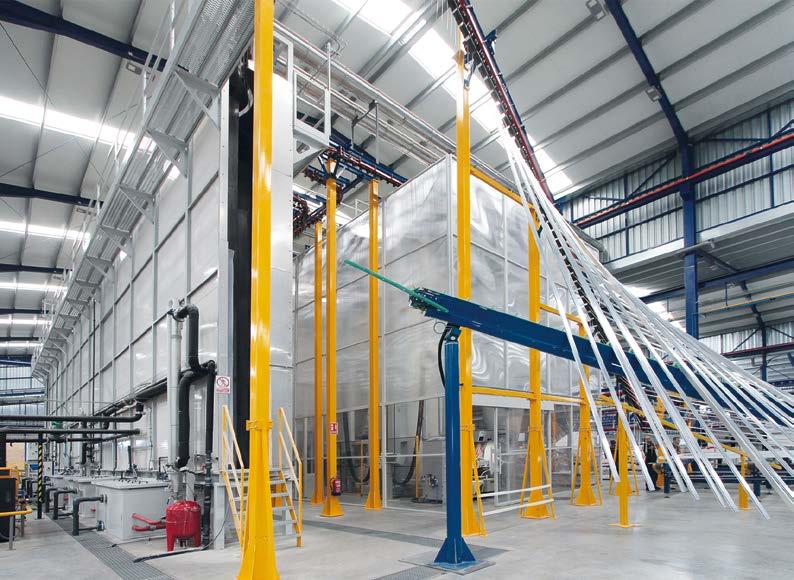
© ipcm
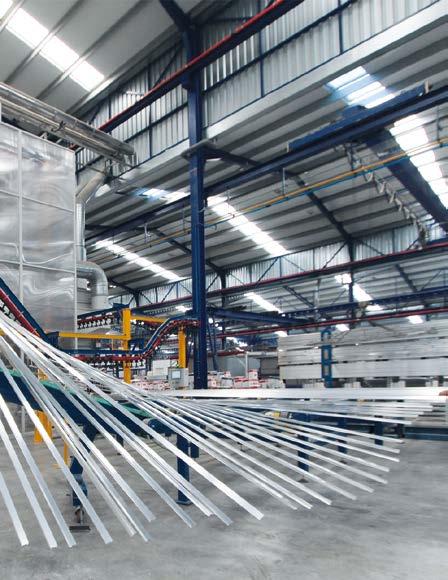
sector de la arquitectura y del aluminio experimentó un crecimiento muy acelerado. Por eso mi padre, con su socio de entonces, decidió introducir sus propios sistemas de aluminio para arquitectura y ampliar la producción de Proylac – cuyo primer cliente era, y todavía es, Aluminios Galisur – con la extrusión con sus propias matrices. En 1984 se compró la primera prensa de extrusión y una inversión tras otra, en el año 2000 la fábrica ya estaba completa, con 3 prensas de extrusión y una planta vertical de lacado. Fue entonces cuando los dos socios decidieron separarse. Mi familia se quedó con ambas marcas, Protecciones y Lacados y Aluminios Galisur”. “Mi padre falleció por una enfermedad repentina en 2016 y yo me hice cargo de la empresa. Veníamos de la época de la crisis de 2008 que fue bastante grave y duró hasta principio del 2014, cuando empezamos a notar una mejora en el mercado. La fábrica estaba saneada económicamente pero llevábamos 8 o 9 años sin hacer inversiones tecnológicas. Para ser competitivos en un mercado global teníamos que invertir en tecnología y reorganizar el flujo productivo de manera más eficiente. La empresa Proylac había crecido comprando naves y el almacén de Galisur estaba justo en el centro de la fábrica: la producción no tenía la logística que debía tener y había demasiada manipulación de material entre las diferentes fases productivas”.
Vista general de la instalación de recubrimiento vertical, de 7 metros de altura, diseñada y montada por Euroimpianti.
El abanico de carga de la instalación vertical.
© ipcm
Por isso meu pai, com seu sócio na época, resolveu introduzir seus próprios sistemas de alumínio para arquitetura e assim ampliar a produção da Proylac - cujo primeiro cliente foi, e ainda é, a Aluminios Galisur – com extrusão com matrizes próprias. Em 1984 foi adquirida a primeira prensa extrusora e, um investimento atrás do outro, em 2000 o sistema já estava completo, com 3 prensas extrusoras e um sistema de pintura vertical. Foi então que os dois sócios decidiram se separar; a minha família manteve as duas marcas, Protecciones y Lacado e Alluminios Galisur”. “Meu pai morreu de uma doença repentina em 2016 e eu passei a chefe da empresa. Vínhamos do período de crise de 2008, que foi muito grave e durou até o início de 2014, quando começamos a notar uma melhora no mercado. A empresa era economicamente sólida, mas não fazia investimentos tecnológicos há 8 ou 9 anos. Para sermos competitivos em um mercado globalizado, tivemos que investir em tecnologia e reorganizar o fluxo de produção com mais eficiência. A empresa Proylac tinha crescido com a aquisição de galpões e o depósito da Galisur situava-se bem no centro da fábrica: a produção não tinha a lógistica que deveria ter e havia excesso de movimentação de materiais entre os departamentos de produção".
Visão geral do sistema vertical que pinta perfis de 7 metros de altura, projetado e instalado pela Euroimpianti.
Leque de carregamento do sistema vertical.
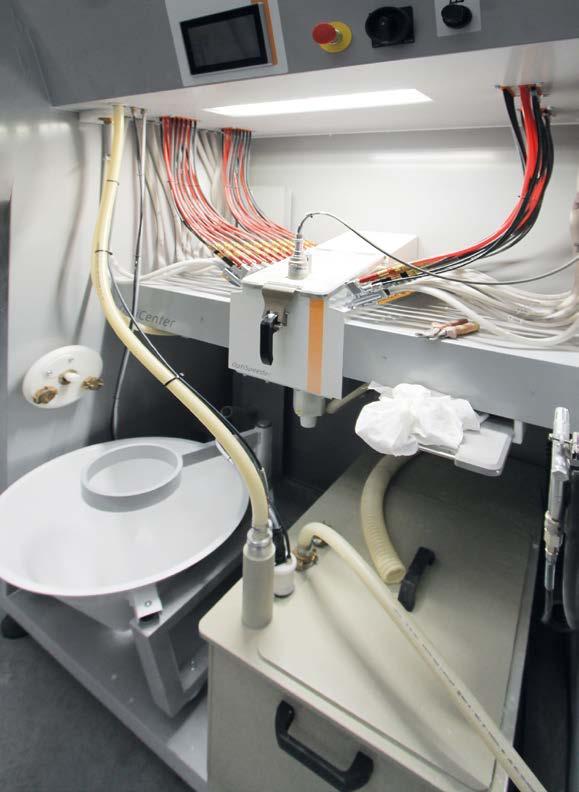
© ipcm
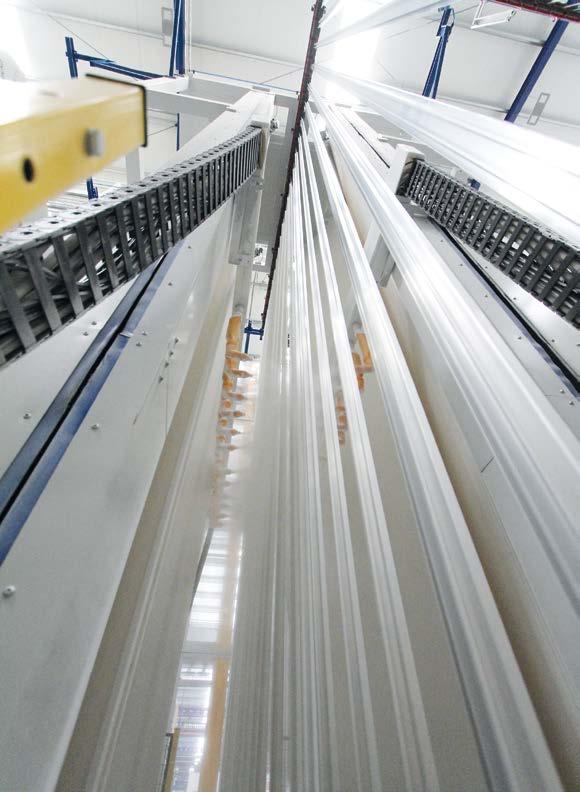
Cada una de las cabinas con forma de diamante está equipada con 24 aplicadores Gema. El centro de alimentación de polvo con inyector Venturi de una de las dos cabinas de la instalación vertical.
As cabines em forma de diamante são equipadas com 24 dispensadores Gema cada uma. Central de pó com injetores Venturi de uma das duas cabines do sistema vertical.
© ipcm
“Decidimos hacer una permuta de nave, así que Galisur se quedó con 5000 m2 donde se ha centralizado el almacén y Proylac se quedó con 12000 m2 productivos (hoy en día son 20.000) donde conseguimos tener un orden logístico de la producción en línea y donde hemos traído la maquinaria de una fábrica que teníamos en Murcia (Extrusionados Levante)”.
Una revolución productiva en 4 años
Actualmente la estructura productiva de GP Grupo (Galisur-Proylac) está así organizada: • un departamento de extrusión con dos prensas de 7 pulgadas cada una: una de ellas cuenta con un sistema de enfriamiento con agua y está preparada para perfiles de mayor peso y aleaciones que requieran mayor enfriamiento. "Decidimos fazer uma troca entre os galpões, ficando a Galisur com 5.000 m² mantendo o depósito em posição central, e a Proylac com 12.000 m² de produção (que hoje são 20.000): aqui conseguimos obter uma ordem lógistica de produção em linha e trouxemos s as máquinas de uma fábrica que tínhamos em Múrcia (Extrusionados Levante) ”.
Uma revolução na produção em 4 anos Atualmente a estrutura produtiva do grupo GP (Galisur-Proylac) está organizada da seguinte forma: • um departamento de extrusão com duas prensas de 7 polegadas cada uma: uma equipada com sistema de refrigeração a água e projetada para perfis mais pesados e ligas que requerem mais resfriamento;
• un reparto de matriceria para la preparación y rectificado de las matrices de extrusión; • un almacén de matrices que cuenta con 5000 referencias en activo tanto nuevas como de propiedad del cliente; • un reparto de nitruración con dos hornos, granallado y limpieza de matrices; • un reparto de lacado con dos líneas Euroimpianti; • un reparto de anodización (ver artículo siguiente); • un departamento de sublimación; • un reparto de rotura de puente térmico y ensamblaje; • un departamento de corte de precisión y mecanizado de perfiles.
“Llevamos 4 años reformando toda la estructura de la empresa, comprando maquinaria nueva y actualizando la maquinaria que ya teníamos”, comenta Manuel Contreras, responsable de calidad de Proylac”. “Lo que ha primado en esta inversión de varios millones de euros ha sido buscar soluciones más eficientes a nivel energético, empezando desde el techo de la nave que está cubierto con paneles solares para conseguir el auto-abastecimiento de la planta. Las prensas tienen un sistema de calentamiento de tocho que aprovecha del calor POLIFLUID_23X14_Layout 1 04/08/2022 14:18 Pagina 1residual para calentar la primera tapa del horno con lo cual se obtiene • um departamento de matrizes, para a preparação e retífica dos moldes de extrusão; • um depósito de matrizes com 5.000 referências ativas, tanto originais, quanto de propriedade dos clientes; • um departamento de nitretação com dois fornos, jateamento e lavagem dos moldes; • um departamento de pintura com duas linhas Euroimpianti; • um departamento de anodização (veja o próximo artigo); • um departamento de sublimação; • um departamento de quebra da ponte térmica e montagem; • um departamento de corte de precisão e maquinagem de perfis.
“Há 4 anos estamos revolucionando toda a estrutura da empresa, adquirindo novos maquinários e atualizando os que já tínhamos”, diz Manuel Contreras, responsável pela qualidade da Proylac. “O que prevaleceu neste investimento de vários milhões de euros foi a busca de soluções mais eficientes em termos energéticos, começando pelo telhado do galpão, que é coberto com painéis solares para obter o auto-abastecimento do prédio. As prensas possuem um sistema de aquecimento dos tarugos que aproveita o calor residual para aquecer a primeira câmara do forno, obtendo assim uma economia significativa
Piazzale Thailandia, 6 58100 Grosseto - Italy ph. +39 0564 425117 Fax +39 0564 418833 info@eurosider.com
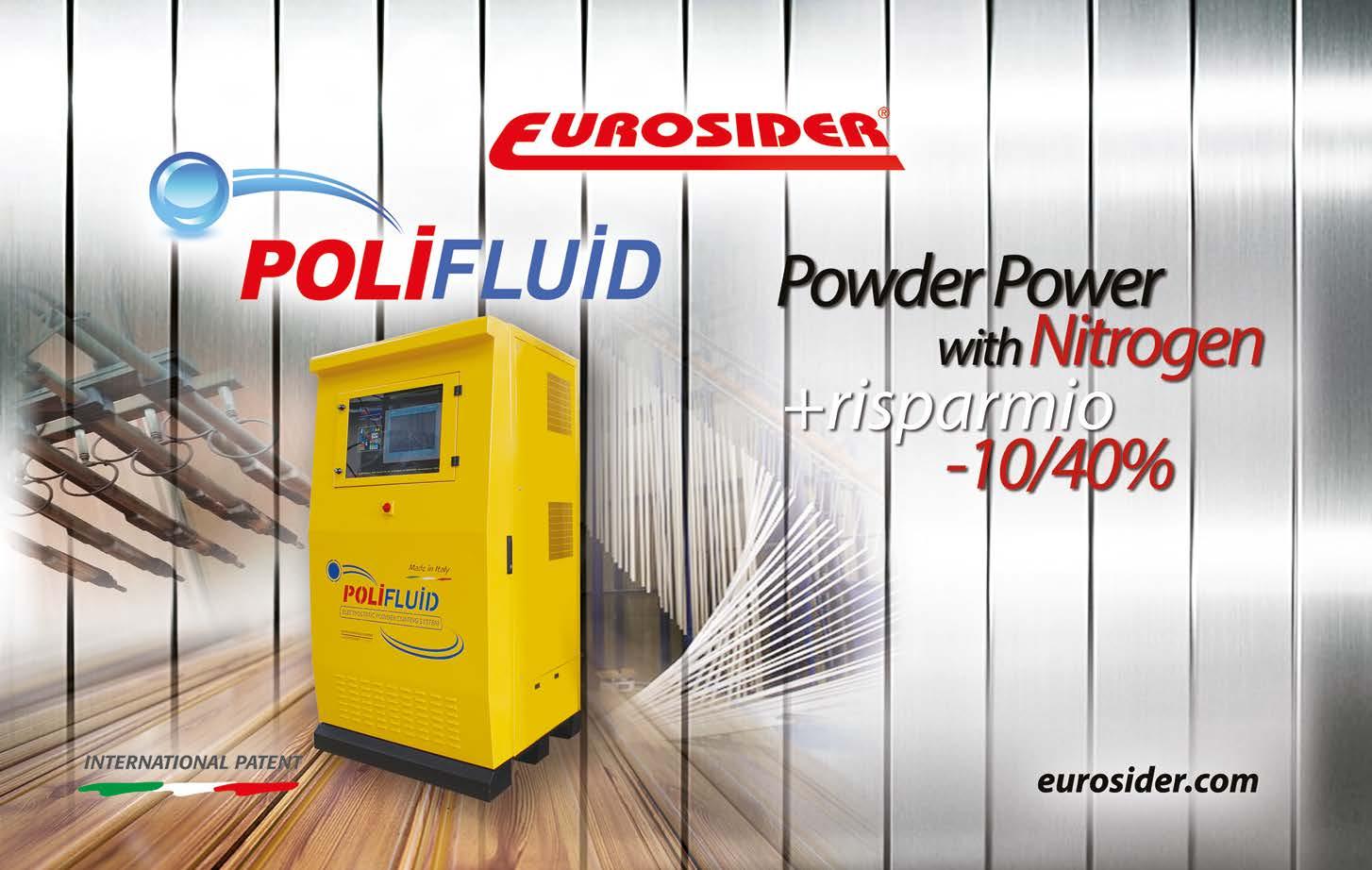
un ahorro importante de energía. A la hora de elegir el proveedor de las instalaciones de lacado, elegimos a Euroimpianti porque era la ingeniería que nos convencía más por el tema de eficiencia energética, o sea por el uso muy bueno de la energía en sus proyectos”. “Vimos varias plantas de Euroimianti y nos gustó la producción que daban y el diseño que tenían” añade López Conde. “Tanto la carrusel como la vertical tienen principalmente consumo eléctrico y esto nos permite disfrutar la energía producida por nuestras placas solares. El horno de polimerización que funciona a gas tiene un sistema que recupera el calor residual para alimentar el horno de secado. Los enjuagues en cascada y un uso muy ahorrativo del agua nos ha permitido disminuir su consumo casi a la mitad. Otro punto muy importante es que la instalación vertical de Euroimpianti, que incorpora todas las últimas tecnologías de la marca, ha duplicado la producción que teníamos con la planta antigua. Hoy estamos haciendo una media de 400-500 perfiles a la hora, con una velocidad de línea de 1,7 m/min, es decir la velocidad que hemos exigido a Euroimpianti”.
Características de la línea vertical de lacado
“Una vez que el perfil extruido sale de la mesa de enfriamiento se corta a la medida del pedido del cliente y se pasa a los hornos de maduración a través de un sistema de apilado automático. Después de la maduración, las tiradas largas del mismo color, todos los pedidos de blanco y las bases para el efecto madera se pintan en la línea vertical, mientras que pedidos cortos o urgentes del cliente se pintan en la horizontal”, explica Manuel Contreras. “Podemos lacar perfiles de hasta 7 metros de longitud en ambas plantas. La instalación vertical ha de energia. Na escolha do fornecedor dos sistemas de pintura, optamos pela Euroimpianti porque foi a engenharia que mais nos convenceu em termos de eficiência energética, pelo excelente aproveitamento de energia em seus projetos”. “Vimos vários sistemas da Euroimpianti e gostamos de sua produtividade e design”, acrescenta López Conde. “Tanto o sistema a carrossel, quanto o vertical consomem principalmente eletricidade e isso nos permite explorar a energia produzida pelos nossos painéis solares. O forno de polimerização, que funciona a gás, é equipado com um sistema que recupera o calor residual para alimentar o forno de secagem. O enxágue a cascata e um uso muito econômico da água nos permitiram reduzir o consumo quase pela metade. Outro ponto muito importante é que o sistema vertical da Euroimpianti, que integra todas as tecnologias mais recentes da marca, mais que dobrou a produção que tínhamos com o sistema antigo. Hoje estamos produzindo uma média de 400-500 perfis por hora, com velocidade de linha de 1,7 m/min, que é a velocidade que pedimos à Euroimpianti”.
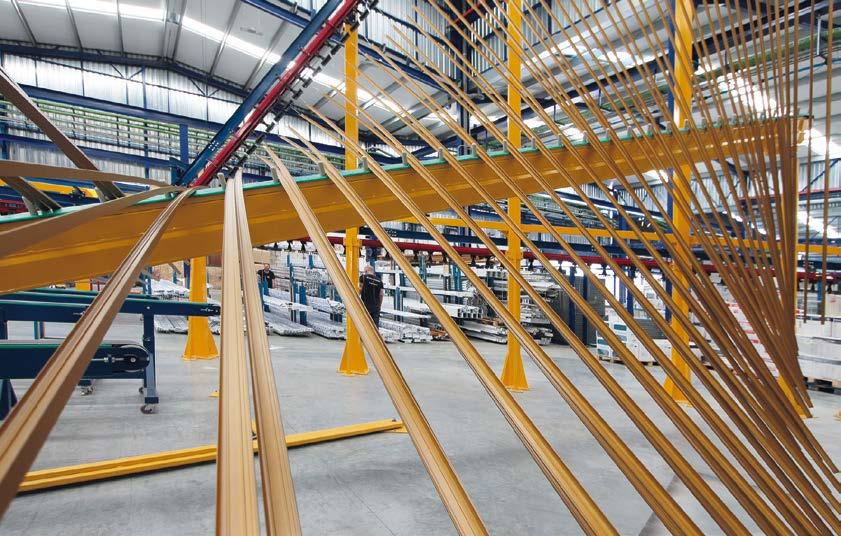
Características da linha de pintura vertical “Depois que o perfil extrudado sai da mesa de resfriamento, ele é cortado sob medida, conforme a solicitação do cliente e conduzido aos fornos de envelhecimento por meio de um sistema de empilhamento automático. Depois do envelhecimento, os lotes grandes da mesma cor, todos os lotes brancos e as bases para o efeito madeira são pintados no sistema vertical, enquanto os lotes curtos ou urgentes são pintados no horizontal”, explica Manuel Contreras. “Podemos pintar perfis de até 7 metros de comprimento em ambos os sistemas. O sistema vertical
© ipcm

sustituido una planta antigua que estaba muy limitada por el tipo de cuelgue que tenía. Proylac buscaba más productividad y más eficiencia: los encontramos en la tecnología Euroimpianti”. La línea vertical diseñada por Euroimpianti tiene un sistema automático de alimentación de material para evitar demasiada manipulación de perfiles. Desde que sale de las prensas, el material se distribuye de manera automática a cada departamento productivo. El puente grúa automático llega hasta la planta de lacado, sitúa los perfiles en la mesa de carga donde los operadores lo taladran y lo pasan por el elevador de donde procede hacia los baños de pre-tratamiento. El ciclo de pre-tratamiento consiste en un primer ataque alcalino (de 1 hasta 2gr/m2 de ataque), doble enjuague con agua osmotizada, ataque ácido neutralizado (de 1 hasta 2 gr/m2), doble enjuague con agua osmotizada, un enjuague de agua desmineralizada y un pasivado libre de cromo. Los productos químicos son de Alsan – Alvarez Schaer. “Todas las fases de pre-tratamiento son en cascada pero el sistema tiene un anillo de aspersión para limpiar el material entre las diferentes etapas, así que no hay contaminación entre las mismas”, explica Manuel Contreras.
La zona de descarga.
La instalación horizontal de carrusel diseñada por Euroimpianti para el acabado de pequeños lotes y de chapa.
En la instalación de carrusel, la cabina, el centro de alimentación de polvo, los módulos de mando de las pistolas y los filtros están montados sobre una plataforma móvil.
substituiu um sistema antigo que tinha uma produtividade muito limitada devido ao tipo de penduramento que havia. A Proylac buscava maior produtividade e eficiência: encontramos as duas na tecnologia Euroimpianti”. A linha vertical projetada pela Euroimpianti é equipada com um sistema automático de carregamento de material para evitar a manipulação excessiva dos perfis. Assim que saem das prensas, são distribuídos automaticamente para cada departamento de produção. A ponte rolante automática chega ao sistema de pintura, deposita os perfis no banco de carga, onde os operadores os furam e os carregam no elevador de onde vão para os banhos de pré-tratamento. O ciclo de pré-tratamento consiste em um ataque alcalino inicial (de 1 a 2 gr/m² de ataque), duplo enxágue com água osmotizada, ataque ácido neutro (de 1 a 2 gr/m²), duplo enxágue com água osmotizada, enxágue com água desmineralizada a uma passivação sem cromo. Os produtos químicos são da Alsan - Alvarez Schaer. “Todas as fases de pré-tratamento são em cascata, mas o sistema é equipado com um anel de nebulização para limpar o material entre as diferentes etapas e separá-los, para que não haja contaminação
Área de descarga.
O sistema horizontal a carrossel projetado pela Euroimpianti para o acabamento de pequenos lotes e das chapas.
No sistema a carrossel, a cabine, a central de pó, os módulos de controle das pistolas e os filtros são montados em uma plataforma móvel.
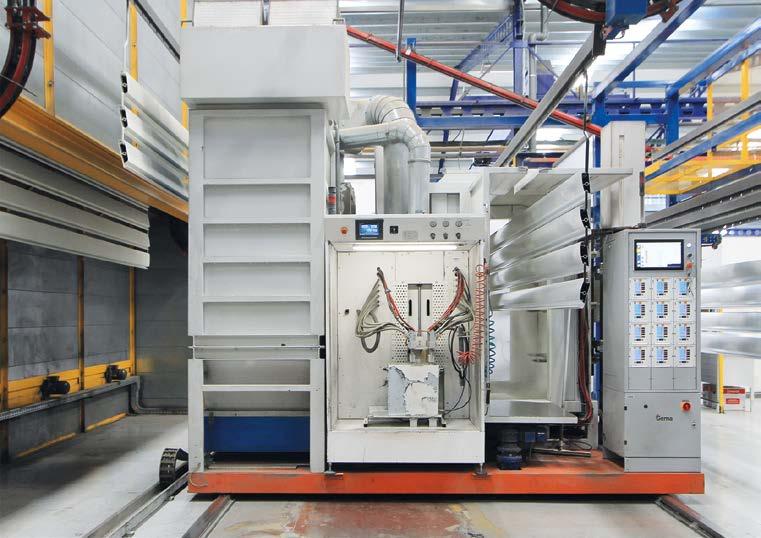
© ipcm © ipcm

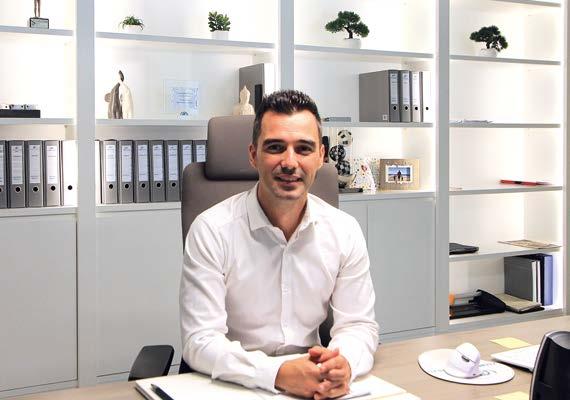
© ipcm
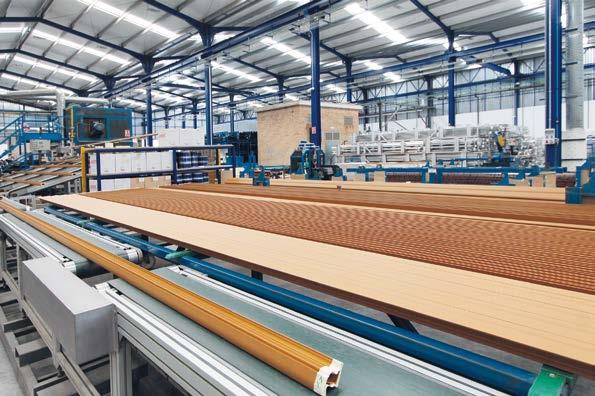
La instalación de sublimación. O sistema de sublimação.
“Además el anillo de aspersión sirve de aporte automático de agua para limpiar a las cubas. Gracias a estos detalles técnicos el consumo de agua se ha reducido de 4 m3 a 1,8 m3 a la hora. Las cubas tiene un sistema de purga automático del aluminio que mantienen los baños de ataque y conversión lo más estable posible”. Después del pre-tratamiento los perfiles se secan usando el calor residual del horno de polimerizado en el horno de secado: el sistema nuevo de Euroimpianti aprovecha el calor residual del horno de polimerizado para alimentar el horno de secado con lo cual se consigue un ahorro energético importante. Para la aplicación de polvo, la línea tiene dos cabinas automáticas en forma de “diamante”, con las pistolas posicionadas en forma curva. Ambas cabinas están equipadas para cambio de color rápido y pueden funcionar en paralelo. A pesar de esto, una cabina pinta solo blanco, que representa el 70% de la producción de Proylac, la segunda cabina pinta cualquier otro color. Cada cabina tiene 24 pistolas y un sistema de detención en automático para regular la altura de las pistolas en función de la longitud de la barra. La alimentación de polvo es con inyectores tradicionales Venturi y cada cabina tiene un sistema de dosificación de polvo por saco de 500 kg, en lugar de big bag. “Una ventaja de esta línea vertical es la posibilidad de lacar perfiles muy pequeños gracias al nuevo sistema de hilo de Euroimpianti, que permite juntar los perfiles más finos para que no se peguen uno con otro y se mantengan tensos. Este sistema automático añade en la punta de abajo del perfil un hilo que cuando termina el proceso se rompe, dejando una marca muy pequeña en la parte inferior del perfil”, concluye Manuel Contreras. “La instalación se completa con el sistema de decapado de gancho por láser de Euroimpianti, otra opción que hemos preferido al decapado químico, porque el láser se alimenta con las placas solares”.
© ipcm
Don Jesús López Conde. Don Jesús López Conde.
dos banhos ativos”, explica Manuel Contreras. “Além disso, o anel de nebulização atua como um alimentador automático de água limpa para os tanques. Graças a estas medidas técnicas, o consumo de água foi reduzido de 4 para 1,8 m³ por hora. Os tanques possuem um sistema automático de purga do alumínio que mantém os banhos de ataque e conversão o mais estáveis possível”. Após o pré-tratamento, a umidade residual é eliminada dos perfis no forno polimerização no forno de secagem: o novo sistema da Euroimpianti aproveita o calor residual do forno de polimerização para alimentar o forno de secagem, obtendo assim uma economia significativa de energia. Para a aplicação do pó, a linha conta com duas cabines automáticas “a diamante”, com as pistolas posicionadas em curva. Ambas as cabines são equipadas para troca rápida de cor e podem trabalhar em paralelo: uma cabine pinta apenas branco, o que representa 70% da produção da Proylac, a segunda cabine pinta as outras cores. Cada cabine possui 24 pistolas e um sistema de detecção automática para ajustar a altura das pistolas, de acordo com o comprimento da barra. O pó é alimentado com injetores tradicionais Venturi e cada cabine é equipada com um sistema de dosagem de pó para sacos de 500 kg, ao invés do big bag. “Uma vantagem desta linha vertical é a possibilidade de pintar perfis bem pequenos, graças ao novo sistema com fio da Euroimpianti, que permite unir os perfis mais finos para que não se choquem e fiquem esticados. Este sistema automático insere na extremidade inferior do perfil, um fio que se rompe no final do processo, deixando uma marca muito pequena na parte inferior do perfil”, explica Manuel Contreras. “O sistema se completa com o equipamento de decapagem a laser dos ganchos, da Euroimpianti, outra opção que preferimos à decapagem química, porque o laser também é alimentado por painéis solares”.
La misión de Proylac: dar servicio a sus clientes
“En Proylac tenemos en cuenta las necesidades de los clientes: plazos de entrega muy cortos y un alto nivel de calidad del acabado de nuestros perfiles son fundamentales para proporcionar un buen servicio” declara Jesús López Conde. “Por eso decidimos invertir en una segunda línea de lacado, una horizontal que funciona desde hace un par de años y que inicialmente acompañaba a la planta vertical antigua. Euroimpianti nos ha suministrado una carrusel para lacar chapas y pedidos de pocas barras, menos de 100, que no sería productivo ni eficiente hacerlo en la planta vertical”. Por el mismo motivo, es decir, dar un servicio puntero al cliente, decidimos invertir en una planta de anodizado, a pesar de que mi padre siempre había estado en contra de incorporar el anodizado en nuestra fábrica. Sin embargo, cuando Alsan, que ya era nuestro proveedor de los productos químicos de pretratamiento, nos enseñó la planta Anodikit® ZONE, su concepto tan avanzando de instalación compacta de anodizado, hizo que no tuviéramos dudas: el anodizado iba a ser nuestra próxima inversión!”. A missão da Proylac: oferecer um serviço aos seus clientes “Na Proylac levamos muito a sério as necessidades dos clientes: prazos de entrega super curtos e um alto nível de qualidade no acabamento de nossos perfis são essenciais para fornecer um bom serviço”, diz Jesús López Conde. “Por isso decidimos investir em outra linha de pintura, desta vez horizontal, que funciona há alguns anos e que inicialmente trabalhava junto com o antigo sistema vertical. A Euroimpianti nos forneceu um sistema a carrossel para pintar chapas e lotes de poucas barras, inferior a 100, o que não seria produtivo nem eficiente para realizar no sistema vertical”. Pelo mesmo motivo, ou seja, para oferecer um atendimento de vanguardia aos clientes, decidimos investir em um sistema de anodização, embora meu pai sempre tenha sido contra a incorporação de anodização na nossa fábrica. No entanto, quando a Alsan, que já era nosso fornecedor de produtos químicos de pré-tratamento, nos mostrou o Anodikit® ZONE, seu conceito muito avançado de uma instalação de anodização compacta não nos deixou dúvidas: a anodização seria nosso próximo investimento!”.
Lea el artículo siguiente para conocer los detalles del proyecto Anodikit® ZONE en Proylac.
EXPERIENCE EXCELLENCE
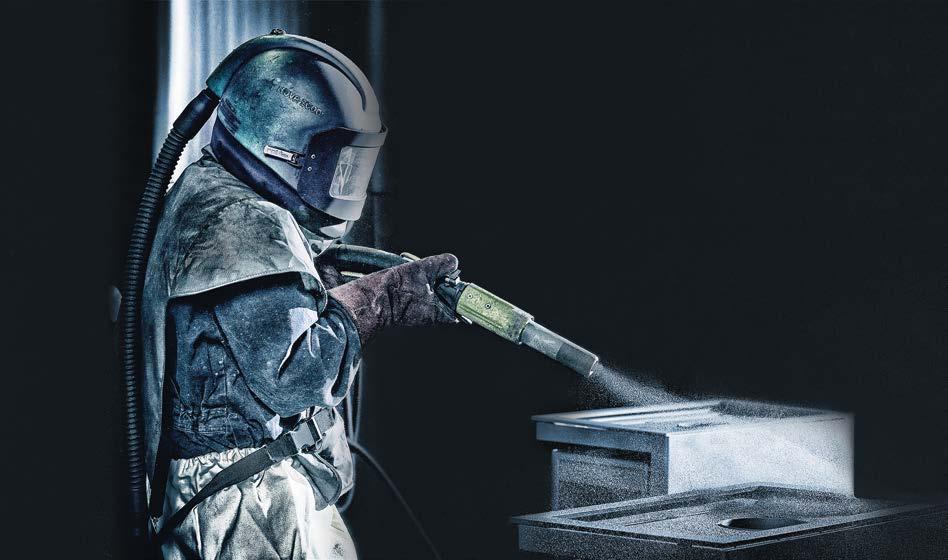
OUR PRODUCTS
Leia o artigo a seguir para conhecer os detalhes do projeto Anodikit® ZONE na Proylac.