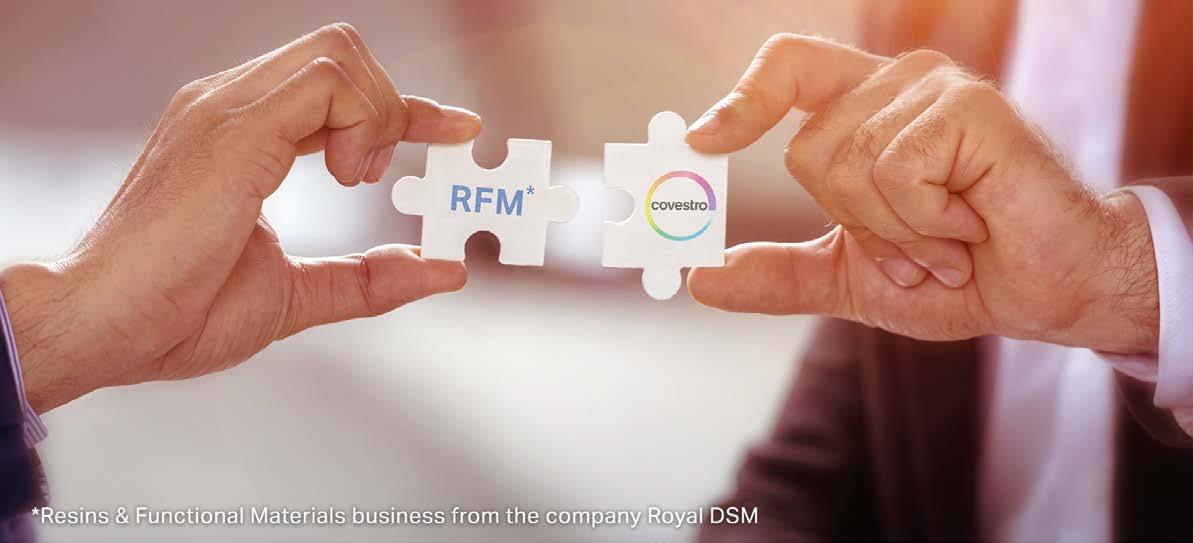
7 minute read
BRAND NEW
Covestro Completes Acquisition of Resins & Functional Materials Business from DSM
Covestro succesfully completed the acquisition of the Resins & Functional Materials business (RFM) from the Dutch company Royal DSM.
With the aim of becoming one of the the leading global suppliers for sustainable coating resins and further expanding its portfolio, Covestro acquired DSM’s Resins & Functional Materials business. The transaction received regulatory approval after Covestro and DSM signed an acquisition agreement in late September 2020. The integration of RFM will expand the Group’s revenues by around EUR 1 billion and will add more than 20 sites to its global production network. “The acquisition of RFM significantly contributes to the implementation of our new Group strategy. With this transaction, we are taking another important step towards sustainability, while at the same time generating sustainable growth,” said Dr. Markus Steilemann, CEO of Covestro. “We are looking forward to meeting our new colleagues and warmly welcoming them to Covestro.” Through the acquisition of RFM, Covestro is adding to its portfolio a complete range of water-based polyacrylate resins, as well as strong brands in terms of sustainability such as Niaga®, solutions for additive manufacturing, and an advanced solar coatings business. In addition, Covestro is enhancing its technology portfolio to include water-based hybrid technologies, powder coating resins as well as radiation curing resins. “With this transaction, we are strengthening our extensive portfolio with further innovative products and technologies that will enable us to meet our customers’ needs in optimal fashion. Now our focus is on integrating the teams, leveraging talent and providing the best possible support for our new and existing customers”, adds Sucheta Govil, Chief Commercial Officer at Covestro. Following a comprehensive analysis, Covestro expects permanent (“run-rate”) synergy effects to build-up to about EUR 120 million per annum from full integration by 2025. These consist of approximately two-thirds of cost and one-third of revenue synergies.
For further information: www.covestro.com and www.dsm.com
© Covestro
SAT Presents the C-Expert Powder Coating Booth
The new C-Expert booth is designed for powder coating of profiles with complex geometries and is perfectly integrated with the new SAT VISI-1 vision system for automatic powder coating.
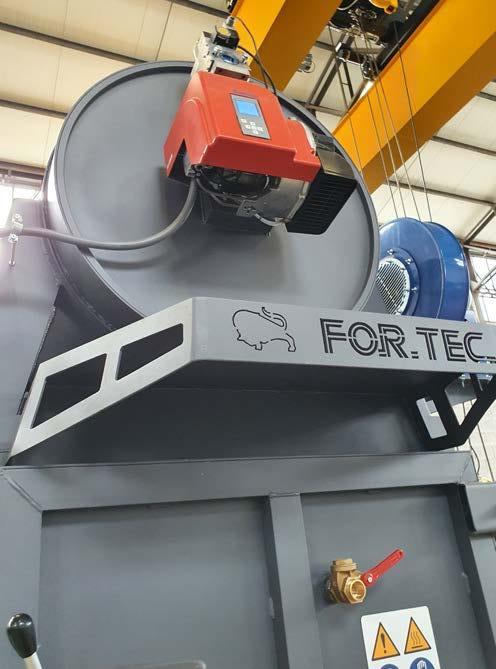
SAT has launched the new C-Expert powder coating booth specifically designed to efficiently and uniformly coat profiles with complex geometries, even at high speeds. Due to the increasing average weight of profiles and the complexity of geometry in the architecture sector, companies are often forced to vary the speed of the conveyor on the vertical line. The new booth, on the other hand, allows to maintain a constant speed. This implies a greater production capacity and a significant reduction in waste. C-Expert is also perfectly integrated with the new SAT VISI-1 vision system for automatic powder coating, allowing repeatability of results and coating efficiency. “We are convinced this booth is a game-changer for high-end and demanding markets. It’s the best vertical booth SAT has ever designed”, said Andrea Trevisan, CEO of SAT.
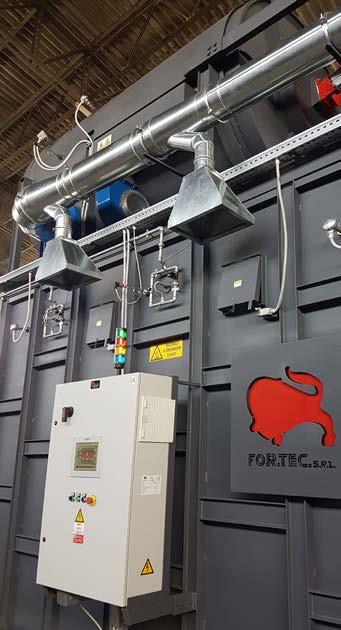
For further information: https://c-expert.com and www.sataluminium.com
© SAT
FOR . .TEC SRL
Senza titolo-5 1 22/01/2014 12:08:51

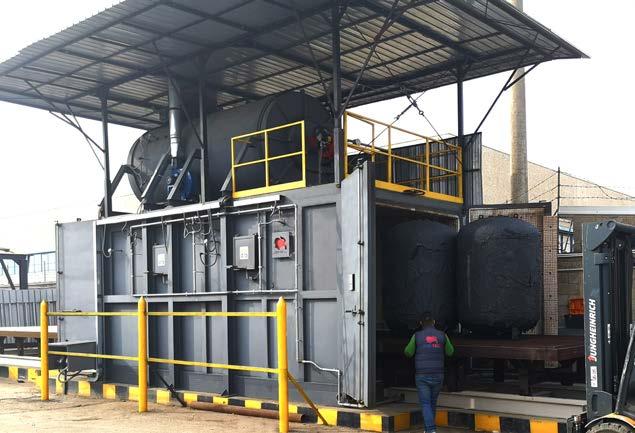
PAINT STRIPPING OVENS
Forni pirolitici per termosverniciatura e...
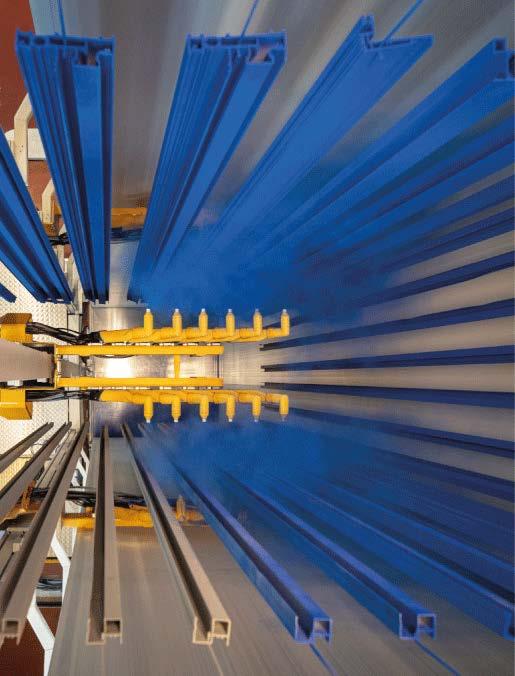
Sverniciatura bilancelle
Hooks paint stripping
Sverniciatura serbatoi gas Gas tanks paint stripping Rigenerazione motori elettrici
Electric motors regeneration Pulizia estrusori
Extruders cleaning Restauro carrozzerie
Body work restoration
Seeing Beyond the Ordinary: Exclusive, Increasingly Customised Finishes for Raleri’s Eyewear
Interview with Francesco Rambaldi, CEO of Raleri Srl
From motorsports to sunglasses and eyeglasses, Raleri’s products constantly evolve through the development of more and more original and customised solutions, obtained through 3D printing and the use of innovative finishing technologies.
Raleri established itself in the eyewear sector by developing a very specific product: tinted visors for motorcyclists. Can you briefly describe how did you start this project and how your company has evolved to gain its current technological expertise?
The idea came from my passion for motorbikes, combined with my work experience in the technology and IT sector in particular. Already in the early 1990s, the design studio which I founded had been recognised for its skills in the 3D modelling of turbines for some Italian energy companies of international standing. At that time, I had the idea of wearing a helmet with an automatic electrodimming visor, which would make riding his motorbike much safer and much more pleasant. Several trips abroad, aimed at seeking out manufacturers and suppliers of LCDs and electronic components to match this project, have led me to gain experience in countries such as Japan and the USA, which are known to be at the cutting edge of technology. At the same time, an analysis of the optics sector, targeted at creating the best product on the market, has led me to acquire in-depth knowledge, in order to begin producing topquality items such as lenses for sports goggles or spectacles, as well as lens supporting structures.
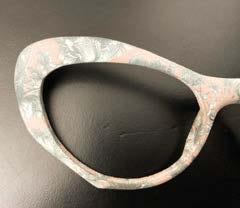
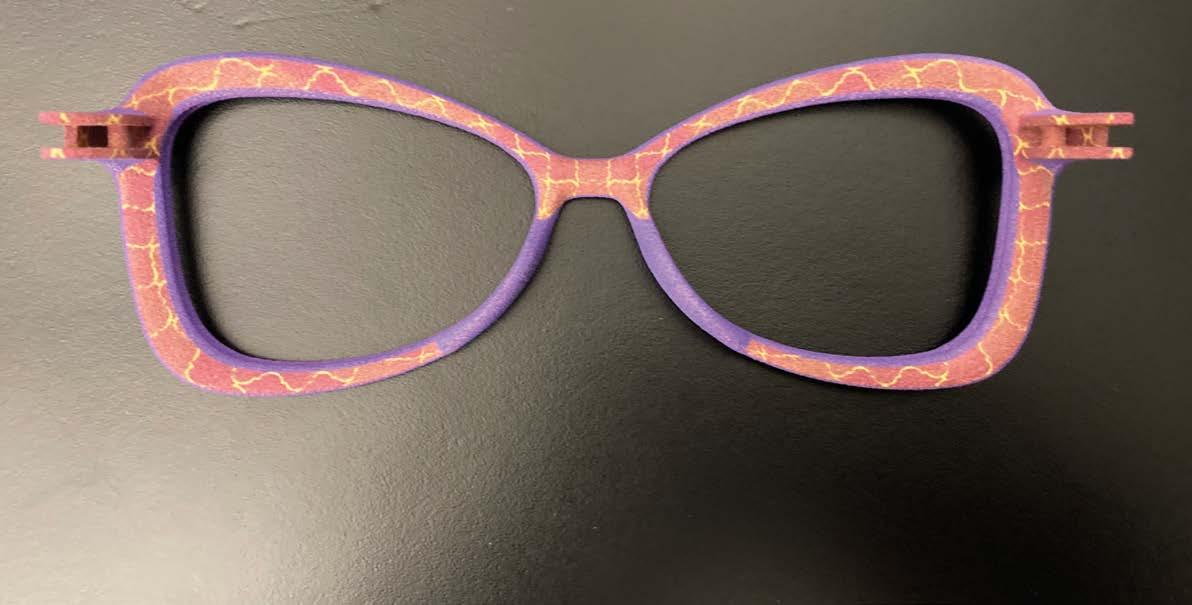
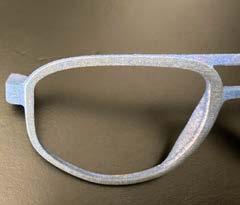
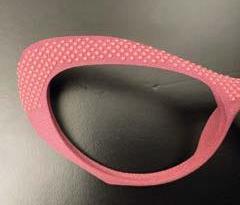
© Raleri
Raleri’s range currently includes products for different sectors, from sport to fashion. Could you describe their standard production cycle?
Raleri employs several people with verticallyintegrated expertise and skills ranging from 3D design to IT and from marketing to product development, all united by the passion for extreme sports such as mountaineering, parachuting, and obviously motorsports. Here, we can personally test our products, which are then either sold under the Raleri brand or made with private labels for different industry brands. Regardless of whether the project is based on a customer briefing or on our own idea, we always entrust different professionals with the various aspects of the production cycle, including design, 3D modelling, prototyping for approval of the final product, and actual industrialisation, which can be carried out in our production facilities in Italy or at the customer’s premises. Raleri takes care of the entire production cycle up to the delivery of the end product or the fine-tuning of production in the end customer’s plant.
How important is the surface treatment of your products, from cleaning to finishing?
With 3D printed objects, surface treatments such as cleaning and finishing are very delicate, but essential steps in order to be able to offer superior quality products with highly customised finishes. To date, we believe we can implement a few unique processing stages on our products, such as ultrasonic cleaning or microblasting, deep coating to obtain a different colour effect from the one offered by the printer, and vibro finishing and semi-gloss finishing to achieve unique results on the treated surfaces with aged wood, volcanic pumice stone, or soft touch effects.
You have recently implemented a new technology for manufacturing glasses with complex finishes: 3D printing. What was the reason for this integration?
Its infinite potential for creating unique, customisable pieces was the basic reason that prompted us to use 3D printing for spectacle frames as well. The finishes we use have been specially designed for this kind of product to make it even more distinctive and unique.
In contrast to commonly used 3D printing processes, Raleri prints its glasses directly in colour. Can you explain in detail how this works and what subsequent surface treatments are required?
We use the brand new HP MJF 580 printer that allows printing directly in full colour, thus making the process much faster. It is all about creating the right print job to give the final product optimum performance in terms of resistance. We can then apply different physical and chemical treatments depending on the effect we want to achieve.
What future do you think this new printing technology will have and how will your products’ surface treatment evolve in relation to it?
There is no doubt that 3D printing is the future, when it comes to manufacturing personalised products. In particular, the needs of customers requiring products made from digitally produced models are changing. The impact of professional 3D printing is evident on the production processes implemented for prototyping, but also on integrated logistics processes, because it enables to manufacture a few parts in a very short time and at an acceptable cost, compared with other options on the industrial market. 3D printing can therefore bring clear advantages over conventional production methods for everyone, as it enables an idea to be transformed into a finished product starting from a drawing made on a home or office computer.
For further information: www.raleri.com
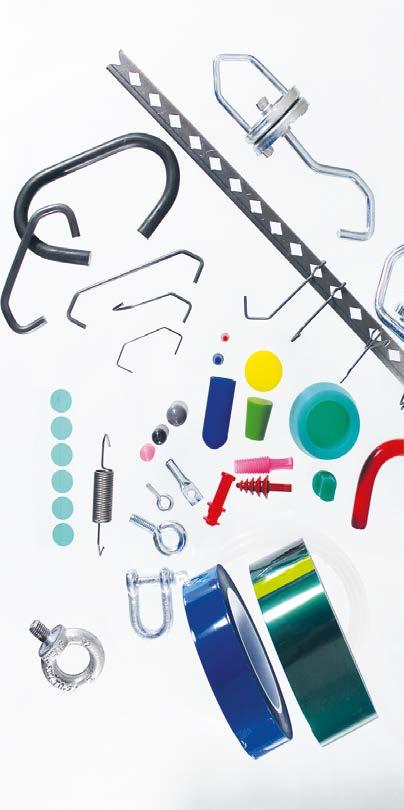