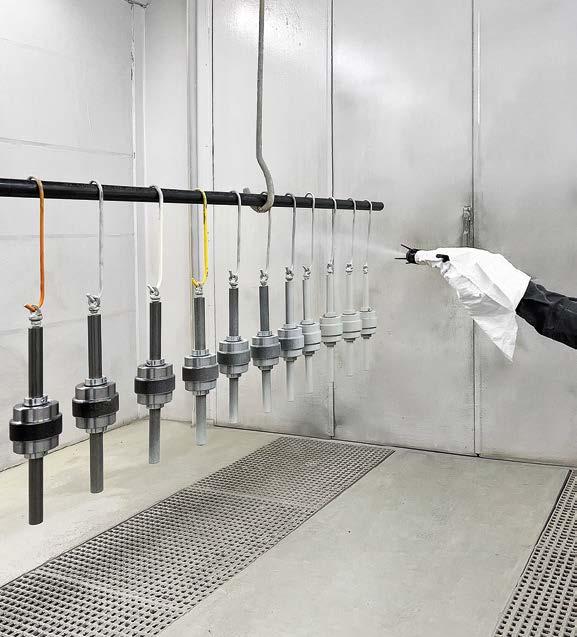
16 minute read
SUCCESS STORIES
30% Material Savings in Silo Coating: Oltrogge’s Electrostatic Application System at Awila Anlagenbau
When coating large surface areas or particularly complex-shaped parts, it is often difficult to achieve even film thickness. This is especially true for large industrial structures such as silos for animal feed, grain, or biomass pellets. Long-established service provider Oltrogge GmbH & Co. KG (Bielefeld, Germany) has installed an electrostatic coating system at the premises of Awila Anlagenbau GmbH, which can now achieve uniform thicknesses on all components while reducing material consumption and saving costs.
Tailor-made solutions for customer-specific requirements
In many industrial sectors, there are raw, semi-finished, or end products that have to be transported, dosed, or stored in the form of powder or bulk goods, including food and animal feed but also colour pigments, pharmaceutical substances, cement, or coal. Silos of the appropriate size are ideal for storing these products. For more than one hundred years, Awila Anlagenbau GmbH (Lastrup, Lower Saxony, Germany) has been designing and building structures of this kind and assembling them in 57 countries worldwide. Its core business includes small to large turnkey and, on request, modular animal feed and grain handling systems, developed for customers mainly operating in the animal feed, plastics, and food industries. Depending on customer needs, as well as on regional conditions and requirements, Awila can create both comprehensive overall solutions and individual components.
© Oltrogge © Oltrogge
Awila builds silos, plants, and individual components for a wide range of industries. A special challenge for its staff lies in the coating of very large-sized structures.
Traditionally, Awila had been using proven airless painting technology. During a product demonstration by long-established service provider Oltrogge, however, it got to know the electrostatic coating process.
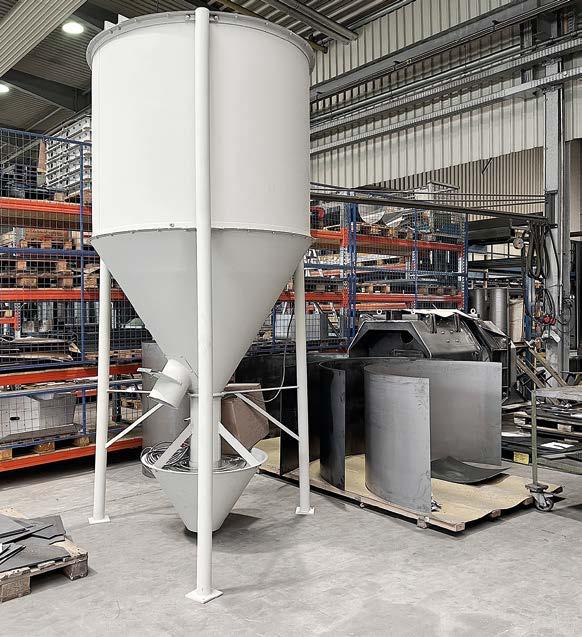

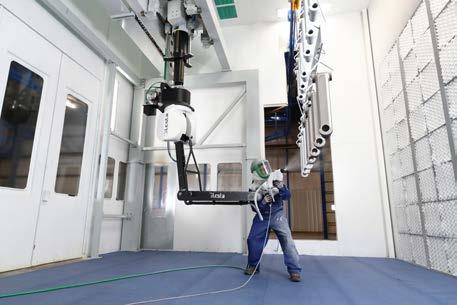
Tomas Schulze, Head of Production and Manufacturing at Awila, puts the company’s mission in a nutshell: “Our ultimate goal is to multiply our customers’ successes. We are always on the lookout for innovative solutions to effectively support them in turning raw materials into high-quality products.” Among other things, this firm’s employees boast in-depth know-how in mechanical and thermal process engineering with regard to conveying, cleaning, sorting, grinding, mixing, dosing, hygienising, drying, and forming raw products.
From airless to electrostatic coating
As a reliable technology partner, therefore, Awila develops and builds silos, plants, and individual components for a wide range of industries. A special challenge for its staff lies in the coating of very largesized structures. Traditionally, Awila had been using proven airless technology for this. This process consists of feeding paint to an airless spray gun via a hose with the aid of a high-pressure pump: thanks to such high pressure, the material is finely atomised and effectively applied to surfaces.
© Oltrogge
Increase your productivity
WITH SELF-LEARNING ROBOT FOR FINISHING
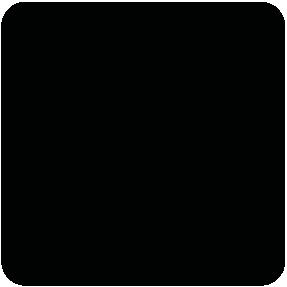
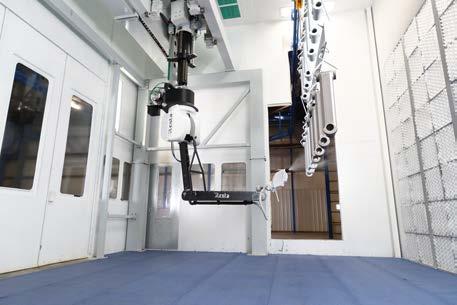
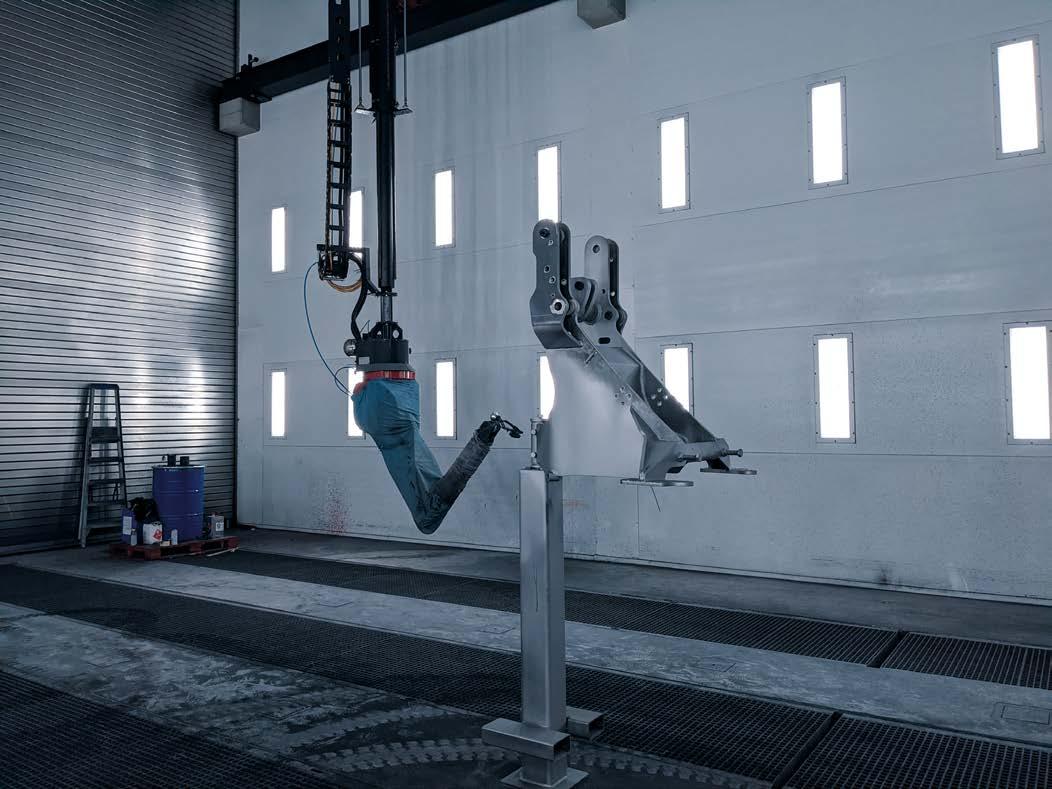
A practical test convinced the company to install a new system.
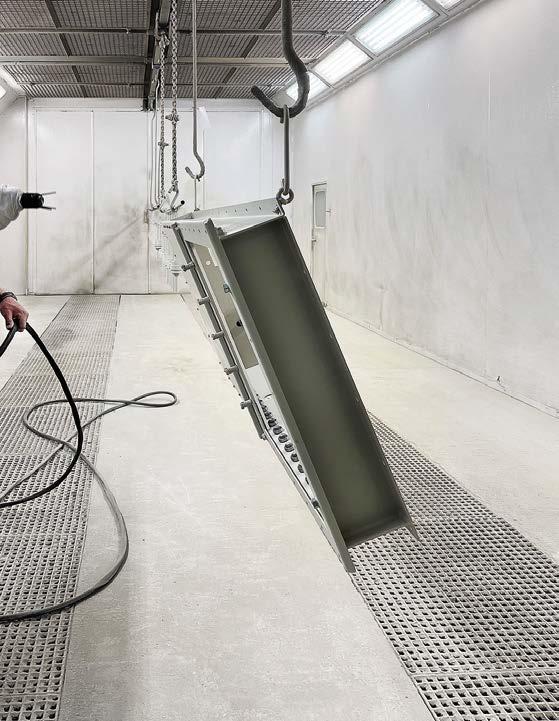
Metal, plastic, carbon parts
SELF-LEARNING
ROBOT
1 OPERATOR
REQUIRED
EUROPEAN
ASSISTANCE
info@Lesta.it
www.Lesta.it
During a product demonstration by long-established service provider Oltrogge in Bielefeld (Germany), however, Awila got to know another type of coating process, as Marco Dahlkötter, area sales manager at Oltrogge, recalls: “We were able to get Awila interested in electrostatic coating during a product demonstration and to provide it with our system for a few days, thus enabling it to directly compare both painting processes in its actual production conditions.” This practical test completely convinced Awila: it bought Oltrogge’s system and had it fully installed at its Lastrup site just a few days later.
High-quality products offered by Oltrogge-Partner Wagner
Awila is now using Oltrogge-Partner Wagner’s electrostatic coating system, consisting of an electrostatic handgun of the latest generation and a control unit. In addition to their robustness and comfortable, ergonomic handling, the GM 5000 handguns guarantee a soft and homogeneous spray jet for high coating quality and very high application efficiency. “The smart control unit allows adjusting all coating parameters in real time,” explains Reiner Feldkamp, application engineer at Oltrogge. “This ensures that the gun delivers optimum performance under any condition.” For example, setting the voltage and current depending on material properties, ambient conditions, and workpiece requirements can prove essential. The control unit also guarantees maximum safety during the electrostatic coating process and monitors the gun’s earthing: if this is not connected, the high voltage switches off automatically.
Awila’s switch from airless to electrostatic painting has paid off. “Especially with large surface areas, we now achieve perfect film thickness: thanks to this new technology, the coating spreads optimally and homogeneously at all times,” notes Tomas Schulze. “On small or complex-shaped parts, we also obtain a significant material saving of 30 to 50% compared with our previous coating process.” This process’ operating principle, based on the attraction of the earthed workpieces to the charged paint droplets, depending on the paint, part geometry, and set parameters, also ensures significantly less overspray and thus higher application efficiency and more sustainable and cost-effective use of materials. Paint savings, lower disposal costs, and lower VOC emissions guarantee the rapid amortisation of the system and provide yet another proof that Awila’s investment in electrostatic coating was absolutely the right decision.
For further information: www.oltrogge.de
© Oltrogge
Awila is now using Oltrogge-Partner Wagner’s electrostatic coating system, consisting of an electrostatic handgun of the latest generation and a control unit. The robust spray gun offers comfortable, ergonomic handling and it provides a soft and homogeneous spray jet for high coating quality and application efficiency.
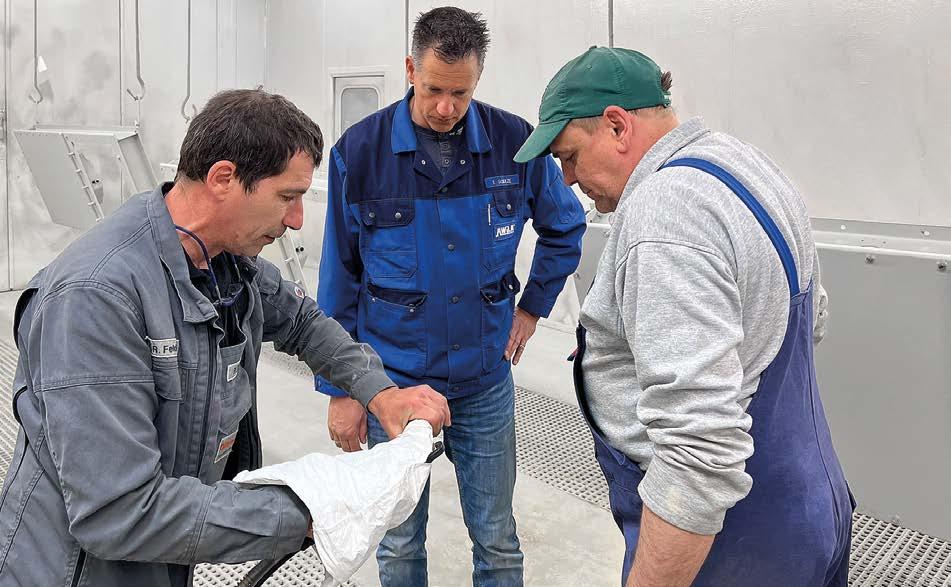
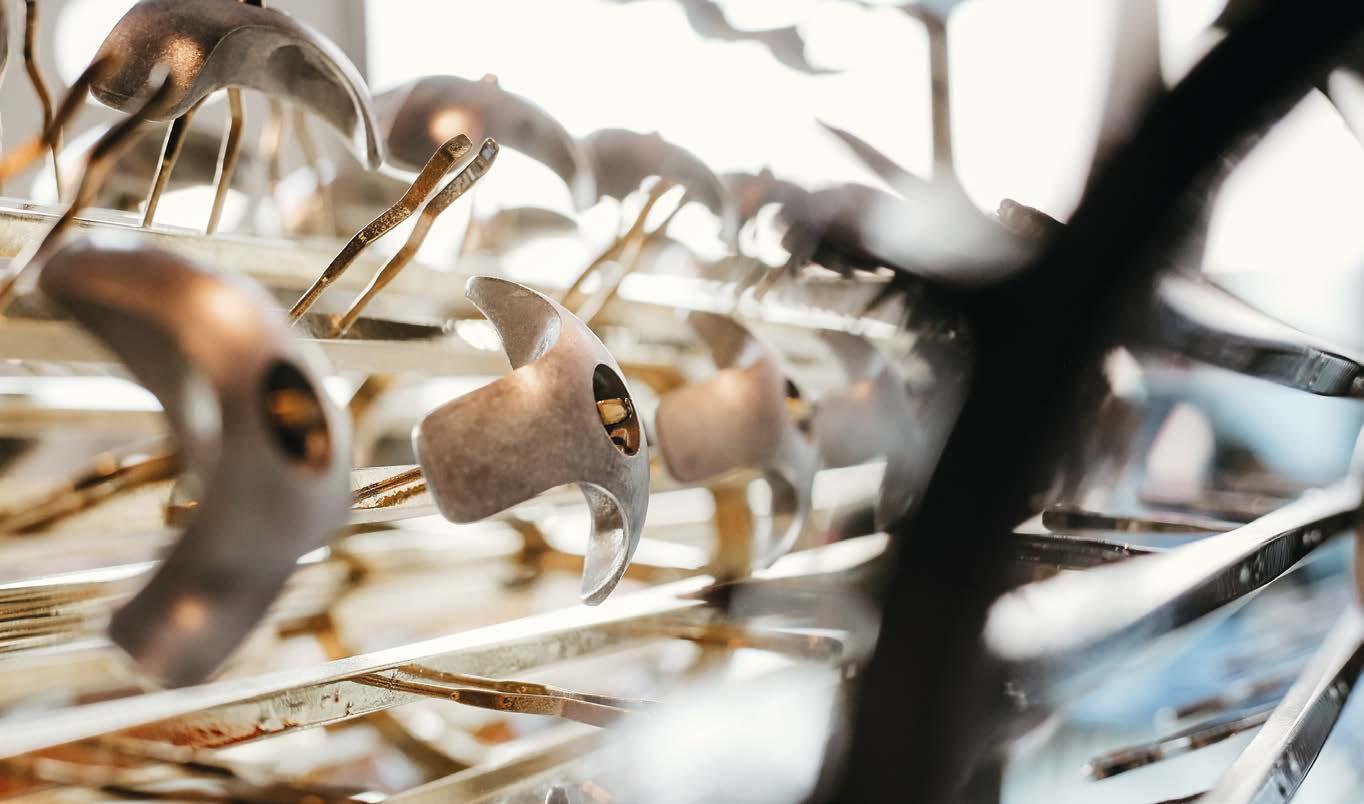
Eurogalvano coats metal, plastic, glass, and crystal components while also applying special, customised effects.
FOCUS ON TECHNOLOGY
Eurogalvano Found the Ideal Solution for its Flexible Coating Cycle in Cooperating with Multiple Partners
Gabriele Lazzari ipcm®
To overcome the coating issues it was facing and speed up production, surface treatment specialist Eurogalvano started a joint project for a liquid painting plant. Thanks to Daphne Impianti’s system with CM Automazione’s conveyor, Epistolio’s self-learning coating robot, and Sames Kremlin’s paint management unit, the company is now equipped with a flexible solution adapted to its application needs.
Automation and self-learning robots are two elements that are becoming increasingly common within the manufacturing industry, as they allow optimising and speeding up production while improving the precision and quality of machining operations. The Italian Association of Robotics and Automation (SIRI) estimated a 22.6% increase in domestic purchases in 20211 .
1 http://www.imprese-lavoro.com/2022/05/19/la-robotica-in-italia-forte-incremento-della-domanda-nel-2021/
However, some doubts may still arise as to the usefulness of such systems with production cycles that require flexibility and adaptability, as in the case of Eurogalvano S.r.l (Lodrino, Brescia, Italy). “We offer a very high number of different surface treatments and we select the most suitable cycle for each requirement together with every customer. As we produce components that will be subjected to mechanical stress, high temperatures, and corrosive environments, coating for us is a means of providing a high degree of protection and aesthetic value. With the recent increase in customer requests, however, we also needed to speed up our painting process. We considered installing a self-learning robot, but we were concerned that it would not be a flexible solution capable of adapting to the different types and quantities of workpieces we treat,” says Matteo Anfuso, production manager at Eurogalvano. “However, a partnership with four renowned Italian companies made us change our mind.” Indeed, Eurogalvano identified the right solution in cooperating with Daphne Impianti S.r.l. (Casella (Pesaro Urbino), CM Automazione S.r.l. (Giussano, Monza e Brianza), Epistolio Srl (Casciago, Varese), and Sames Kremlin Srl (Pioltello, Milan). The resulting liquid coating system with a self-learning application robot has in fact enabled the company to improve paint consistency, reduce consumption, and optimise production by being able to quickly alternate between automatic and manual processes.
Innovation on a two-year basis
Eurogalvano began operations in 1993 as a contractor in the field of cleaning, sandblasting, tumbling, decorative electroplating, and Teflon coating of aluminium, iron, and steel for furniture components and weapons. Always attentive to changing market demands, it has since been expanding or upgrading its equipment on a two-year basis. To differentiate its target markets, it first updated its systems to be able to process rocker arms for Ducati gearboxes and pistons for Brembo brakes. Then, in order to also expand the types of surface treatments on offer, it had a new department built with an electroplating plant specifically devoted to hard chrome plating, intending to meet new market demands and guarantee better technical properties even for products made from less noble materials. It later implemented new treatments such as (polished or thick) brass plating and bronzing and it began machining all types of alloys, even the most delicate ones such as aluminium and stainless steel, in order to expand its range of decorative
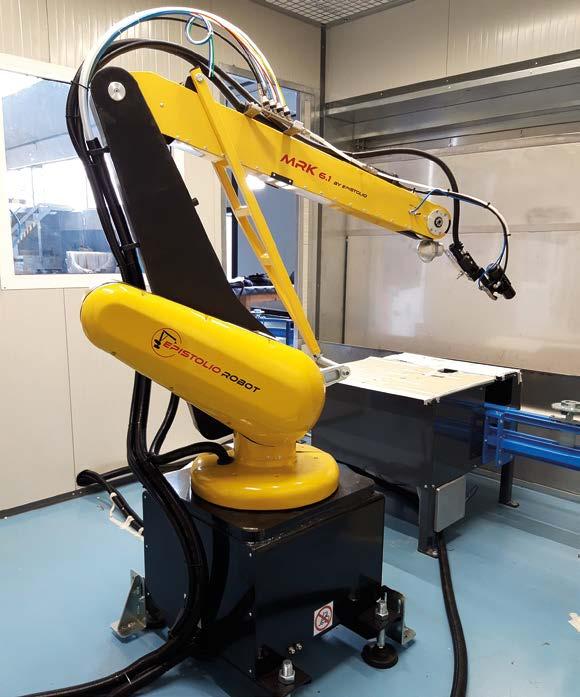
© ipcm
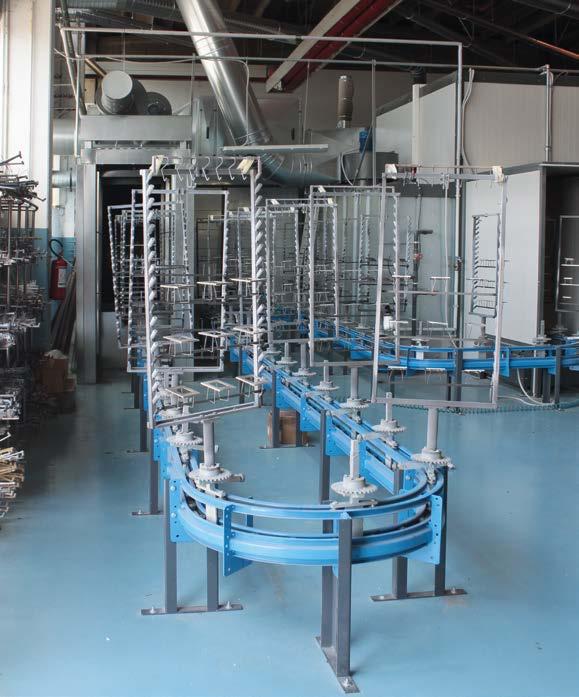
The X37R inverted conveyor supplied by CM Automazione.
© Epistolio
The MRK self-learning coating robot supplied by Epistolio.
© ipcm © Epistolio

Coating some home automation components with the Sames Kremlin TRP gun mounted on the robot’s mechanical arm and the paint management unit supplied by Sames Kremlin.
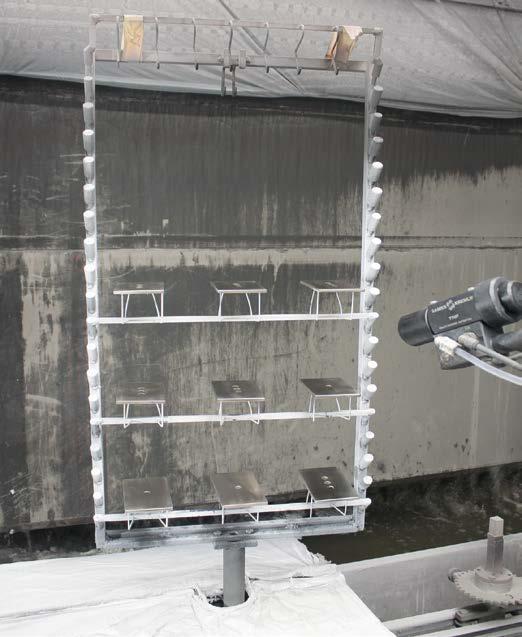
treatments. Subsequently, it implemented a zero-impact sputtering process that enabled the vaporisation and deposition of noble metals in a vacuum. “We carefully observe the market and take action to improve our equipment and provide new services to our customers, which have grown exponentially over the years and now cover a variety of sectors: automotive, marine, home and industrial furniture, home automation, doors and windows, and small parts. We also have an in-house chemical laboratory, which has proved indispensable in controlling the quality of our treatments. Every day, we carry out chemical analyses on our plating baths, salt spray resistance tests, thermal shock tests, and destructive thickness tests,” states Anfuso. The acquisition of new plants, machinery, and equipment has therefore enabled Eurogalvano to expand the treatments it offers, its target markets, and its expertise. This is why, in addition to contract machining, the company built another factory for the own-brand production of over 200 types of modular joints, tubes, and accessories for civil, business, and industrial furniture.
A flexible, customisable production cycle
Eurogalvano is therefore now able to coat metal, plastic, glass, and crystal components while also applying special, customised effects. It has also obtained the ISO 9001:2015 certification for its quality management system. “The characteristic that has allowed us to grow is our flexibility. We process 40,000 parts per day and have 230 customers. We are able to provide a complete, tailor-made service from the design of a component to the formulation of its finish, including moulding and all intermediate surface treatments,” explains Anfuso. Indeed, the company puts its research and development department and technicians at the service of each customer, in order to identify together the properties and configuration of the required workpiece. It then realises a design, creates a prototype in plastic or metal using 3D printing technology, scans it, and finally mass produces it. Of course, it also carries out the most suitable surface treatments to meet the aesthetic and technical requirements of every part: Eurogalvano can perform different types of pre-treatment by deburring with abrasive belts, polishing with cotton wheels and heated abrasive pastes, solventfree ultrasonic cleaning, phosphating, or shot blasting. Afterwards, the parts undergo the required finishing processes.
The importance of coating
“More than half of our products is destined for foreign countries, so we make sure that our treatments generate high-quality surfaces that can withstand high temperatures and corrosive environments. Coating plays a very important role here, both because it enables us to offer finishes
with a high aesthetic value and because it is a valid alternative to the use of hexavalent chromium. We can apply transparent, matte, glossy, and pigmented protective finishes on workpieces with very different dimensions and shapes. We are equipped with eighty tanks for electroplating processes, a manual powder coating booth, and a water transfer printing tank. In 2019, we also added a new liquid coating plant with an Epistolio MRK articulated robot with a self-learning module, in order to achieve greater flexibility in production, better uniformity in application, and a significant reduction in lead times. This investment also enabled us to offer an additional service to our customers, the coating of plastics, thus further expanding the range of surfaces we are able to paint,” notes Anfuso. “Finally, in 2021, we also installed a colour mixing system to create unique finishes. We make them in-house, test them, and apply them. Finally, we provide the recipes to our customers so that they can replicate them.”
The new liquid coating plant
The flexibility that characterises its liquid coating plant enables Eurogalvano to handle large batch quantities as well as smaller, customised orders. “During a work shift, we have to be able to handle very different components. For example, we might have to paint 500 plates for hotel domotics, then 100 small fittings for furniture, and finally 10 components for 1.5-metre long coat hangers. Consequently, we needed a solution that would allow us to quickly switch between automatic and manual operation,” indicates Anfuso. The plant is composed of five stations: a loading and unloading area, a liquid paint booth, a flash-off tunnel, a drying oven, and a cooling area.
Features of the X37R inverted conveyor
The coating line is linked to an X37R inverted conveyor with a maximum distributed load of 3,000 daN, characterised by a step-by-step or continuousflow operation with a speed of 3 m/min at 50 Hz and controlled through the line’s general switchboard. The attachments to the chain, which can be rotated and are equipped with a locking lever, are moved together with the parts to be processed along the entire line, up to the discharge area. There are 116 frames with a maximum load capacity of 20 daN per attachment and a 600-mm pitch. One of the special features of the conveyor is the presence in the motorised rotation device of a pneumatic cam for releasing the lever that blocks the rotation of the chain’s hooks in the segment passing through the coating station: a movable casing allows the device to be closed while the parts are being painted, in order to protect the conveyor’s gears and reduce cleaning and maintenance work. The drying booth is equipped with a second rotation device with the same characteristics as the one located in the coating booth.
The MRK self-learning coating robot
The pressurised liquid painting booth is equipped with an Epistolio MRK six-axis articulated robot, on which a Sames Kremlin TRP 501 electrostatic gun is mounted. “The robot allows parts with complex and very different shapes and geometries to be coated precisely, applying a uniform finish to each surface while avoiding the Faraday cage effect and reducing paint consumption. Outside the booth, the touchscreen control panel with multilingual software includes a module for managing and customising production, as well as offering statistics and data on robot utilisation,” indicates Epistolio sales manager Luca Venturini. The MRK coating robot has a self-learning function: by means of an ergonomic, removable joystick with programmable buttons, one operator can set the manual movement of the robot and guide it in spraying a workpiece. “Once the start button is pressed, the software programme stores all movements, saving them when the operator confirms that the painting cycle has been successfully completed. In this way, all subsequent parts can be treated automatically. It is also possible to modify existing programmes, should an alternative cycle be identified or any subsections be added or changed. The robot is in fact equipped with proportional valves through which paint quantities, atomisation, fan opening, and kilovolt range can be adjusted to customise even individual sections of each coating programme according to the requirements of parts,” says Venturini. “For example, if we find any difficulties in coating, we can change the parameters and avoid or reduce Faraday cage issues at critical surface areas. In
© Eurogalvano © Eurogalvano
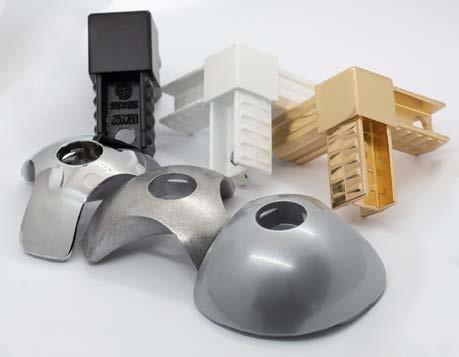
Products treated with a satin chrome plating process and other components manufactured by Eurogalvano.
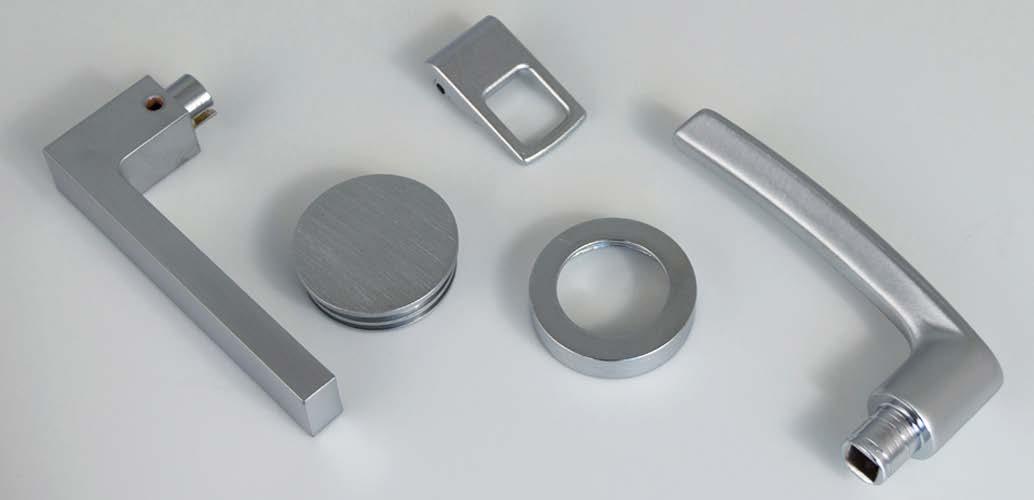
addition, the robot’s pneumatically balanced arms are made of very robust yet lightweight materials, so manoeuvrability during programming and manual painting is comfortable and quick. As mentioned, we need to be very flexible and able to coat even just a dozen components. Selflearning is very useful, but so is the ability to quickly configure the robot arm for manual operation. In this way, for example, we can paint a frame with components that require a high degree of customisation and, after a few minutes, resume the automated coating of other batches. Finally, in order to ensure the safety of all personnel, Epistolio’s articulated robot is also equipped with appropriate safety systems that immediately stop arm movements if they perceive the presence of an operator,” explains Anfuso.
The paint management unit
Sames Kremlin’s mixing system and control unit automatically manage two tanks containing hardeners and five tanks with other paint components, the feed pumps, and the cleaning and quick colour change operations, the latter of which takes two minutes. Paint products can thus be created, mixed with hardeners, and fed to the robot directly the moment they are to be applied. Based on customer requirements, Eurogalvano applies primers, base coats, and customised twocomponent top coats even on small batches. In addition, should it be necessary to paint many components in sequence, the automatic mixing system integrated with the product and catalyst tanks allows production to be quickly alternated. “One of the advantages of having our different suppliers cooperate with each other is that we can manage the Sames Kremlin’s unit directly from Epistolio software. We are therefore able to optimise paint application, configure the transition from manual to semi-automatic application, and adjust the oven’s parameters, the conveyor’s frame rotations, and the amounts of dispensed paint in order to minimise material consumption and improve finishing quality,” notes Anfuso.
The added value of cooperation
The plant went into operation in 2019 and Eurogalvano is completely satisfied with the investment. “We visited Epistolio’s premises to see an MRK robot in operation, test the ergonomics of its mechanical arm and its self-learning function, and see if it was the most suitable solution for our flexibility requirements. The robot immediately proved to be very useful and easy to handle, so we decided to make this investment. We discussed with Epistolio, Daphne Impianti, CM Automazione, and Sames Kremlin, we identified together the potential problems we would face, and we studied how to solve them.” “Synergy was our trump card for this project. For example, an Epistolio motor interpolated with the robot’s 6 axes is mounted on CM Automazione conveyor’s workpiece rotation unit to manage the workpiece rotation in terms of angle and speed, thus further optimising the coating process. This was made possible by working with several qualified and reliable partners. All the companies that took part in the project discussed the best solution, each providing their technologies best suited to the needs of Eurogalvano,” points out Venturini. “We encountered maximum willingness on everyone’s part. Now, our system is perfectly configured and optimised. It has provided us with benefits in terms of coating speed and quality, but also of production process management. The operator teaches the articulated robot the best coating cycle, then takes over personally to paint smaller batches when we have specific requests, and finally lets the robot resume normal production,” states Anfuso.