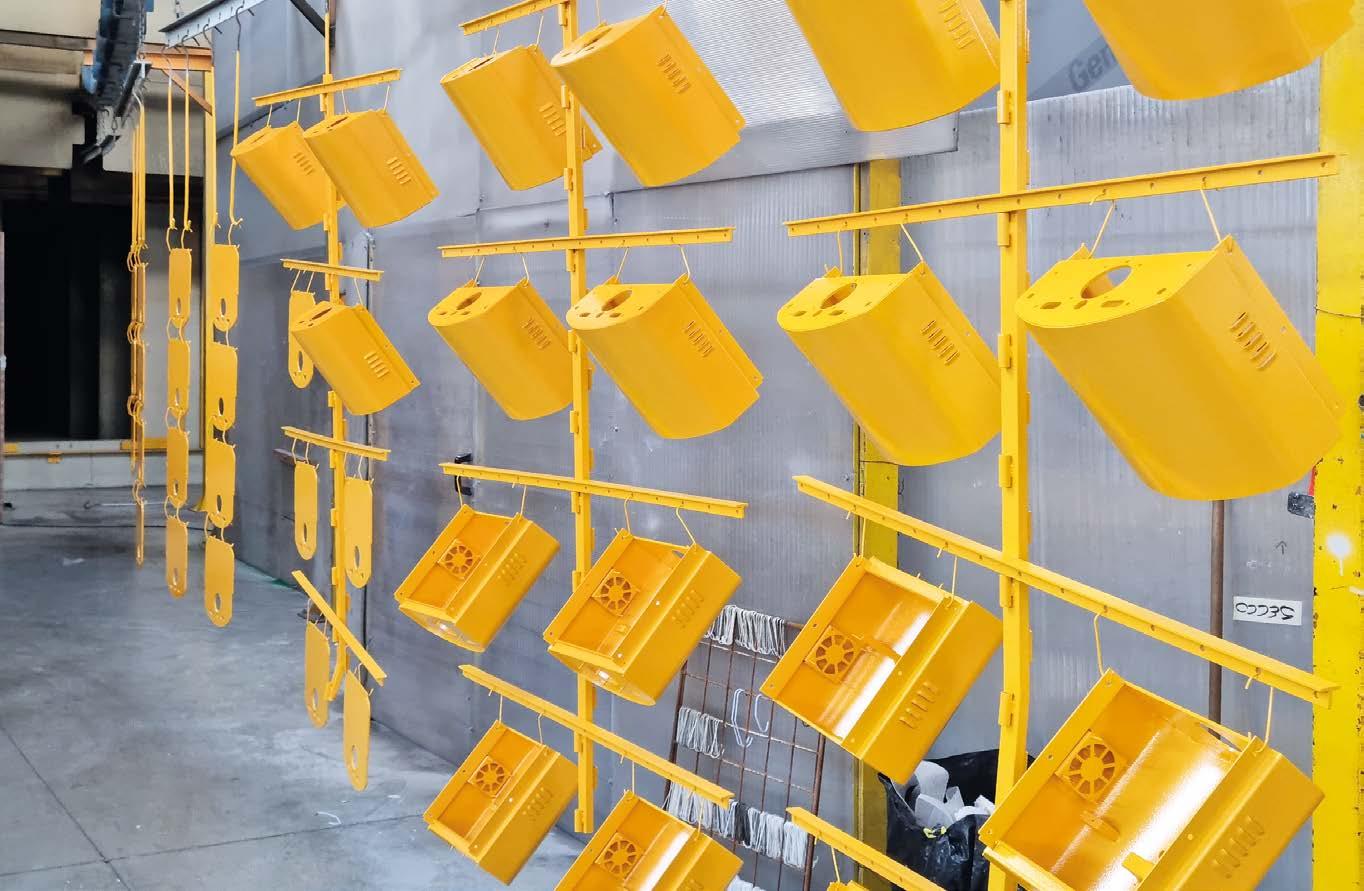
9 minute read
FOCUS ON TECHNOLOGY
New Color’s Environmentally Friendly, High Quality Finishes Achieved by Recovering Pre-Treatment Water and Controlling Every Stage of the Coating Process
Gabriele Lazzari ipcm®
While keeping the flexibility of coating processes as the cornerstone of its production, New Color wanted to optimise and reduce the environmental impact of its operations. The control system for all process phases implemented by Avin and the physical-chemical water treatment process developed by NoksorSokemGroup have thus enabled the company to offer its customers environmentally sustainable, high-quality finishes while reducing consumption.
© ipcm
The pre-treatment tunnel.
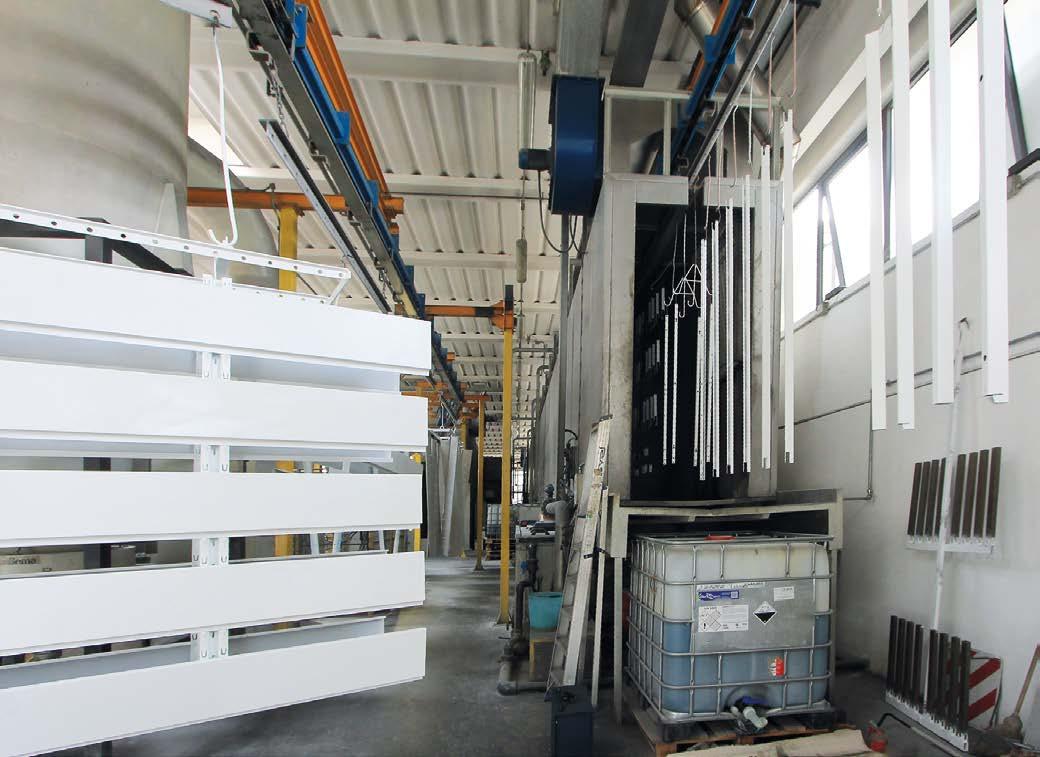
News about climate change is unfortunately the order of the day. Northern Italy, for example, is experiencing its driest period since 1952 and many municipalities are rationing water use1 . Sustainable behaviours are therefore increasingly indispensable both in the lives of individuals and in production processes. In particular, climate change has further affected the water crisis and, therefore, also the technological interventions made by companies to mitigate it. New Color (San Donà di Piave, Venice, Italy), a company specialising in the coating of street furniture, lighting, and home furniture components and metalwork fabrications, is at the forefront of the transition to greener production. “Our company’s mission has always been to provide our customers with finishes that are not only of high quality but also environmentally sustainable,” states Massimo De Gianni, the CEO of New Color. “This is a contract coating firm, so we deal with many different types of parts:
1 https://www.theguardian.com/world/2022/jun/17/italy-drought-po-river-climate-crisis customers turn to us because they know we can adapt our processes to their requirements, but also because they are aware of the efforts we make to limit the consumption of energy resources and waste materials during processing.” Needing to maintain the flexibility of its painting processes, but at the same time wanting to optimise production times and further reduce the environmental impact of its operations, New Color collaborated with NoxorSokem Group Srl (Cusano di Zoppola, Pordenone, Italy) and Avin (San Martino al Tagliamento, Pordenone) to upgrade its existing coating plant. Its synergic cooperation with these two companies has had two main results: implementing an Industry 4.0-oriented digital control system of all phases of the coating process, supplied by Avin, which allowed New Color to improve production times and finishing quality by constantly monitoring each stage, and installing a zero-discharge physical-chemical treatment plant for rinse water and concentrates coming from the pre-treatment line, developed by NoxorSokem.
The in-line coating plant.
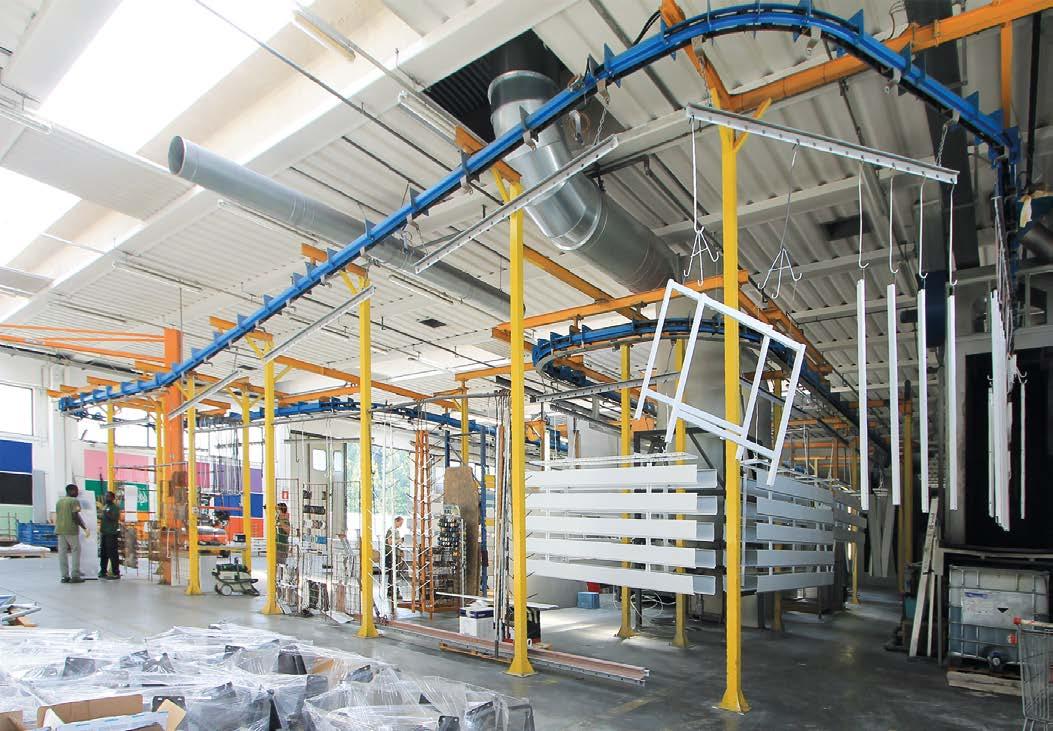
© ipcm
So, the company will be able to add a related section on its website that will allow clients to check all the information about their orders: they will be able to monitor the status, the amount of powder used and the environmental data such as the quantity of water that has been saved compared to processing without a purifier.
Environmental sustainability and quality control
New Color was founded in 1995 with only six employees and a powder application booth. “Thanks to the thirty years of experience of the founding partners, which has been passed on to new employees and heirs, the company has grown steadily, until it acquired a new factory in 2002 and assumed a more prominent role within its market. When we decided to expand our offer to treat outdoor and street furniture components, we turned to some expert companies to develop together with us the most suitable pre-treatment process for our requirements. This allowed us to gain further knowledge, and now we are no longer just a contractor, but we can also carry out consultancy work to help our customers identify the most suitable coating solution for their needs. The technological investments and innovative solutions we have implemented have allowed us to gradually expand and update our coating plant, so as to adapt it to emerging market demands and, at the same time, meet all the environmental sustainability requirements we have imposed on ourselves,” continues De Gianni. “Another important element of our production is the focus on quality and control of every process stage. In fact, we intend to obtain the Qualisteelcoat certification, so that we can offer our customers products made with processes certified by independent institutions,” adds Walter Donà, technical manager at New Color. This is why, to reduce the environmental impact of its production and monitor the quality of its coating process, in the summer of 2021 the company equipped itself with a new water purification and recycling plant designed and installed by Avin together with Noxor, which also takes care of its control, maintenance, and technical support.
A flexible coating plant
New Color uses a static powder coating line for treating steel, galvanised steel, and aluminium components with maximum dimensions of 12 x 2.60 metres and a maximum weight of 1,500 kg and a second automatic plant with a one-rail overhead conveyor to paint parts with maximum dimensions of 5 x 2.4 metres. “This flexible plant enables us to adapt our coating cycle to individual customer needs, by activating or deactivating certain pre-treatment stages even during a single shift. Moreover, our technicians are always available to analyse the needs of individual parts and decide together with the customer the best pre-treatment, coating, and curing recipe,” explains Francesco Bellè, technical manager at New Color. The multi-stage spray pre-treatment process involves the alternative use of phospho-pickling or multi-metal phosphodegreasing depending on the materials to be treated, both performed with a degreasing additive, followed by two rinses with purified water and one with osmotic water. The final stage is no-rinse nanotechnological passivation. Afterwards, the parts are dried in the oven at 150 °C for 15 minutes. This process gives New Color the flexibility to always identify, with the support of the supplier, the most suitable pre-treatment operation for each incoming substrate (ORS, EG, HDI, stainless steel, Al). The parts then go through a Gema automatic booth, where two reciprocators with twelve guns (six on each side) apply the powder coating. There are also two pre- and post-finishing stations, “which, however, are only used for the undercuts and the shielded parts, because the paint’s spread rate is high, consistent, and uniform with most geometries. Furthermore, as the guns are equipped with a Super Corona ring that neutralises excess free ions, overspray is avoided and the orange peel effect is limited,” notes Bellè. Finally, the components are polymerised in an oven at 180 °C for an average of 40 minutes and subjected to a coating quality control phase before being packed and shipped to customers. “An independent test performed by the University of Trento has certified that our painting process achieves uniform and durable finishes that are resistant to thermal and mechanical stress, corrosion, weathering, and chemicals. In fact, our treated parts’ salt spray resistance value exceeds
© ipcm
The water treatment plant built by Avin and NoxorSokem.
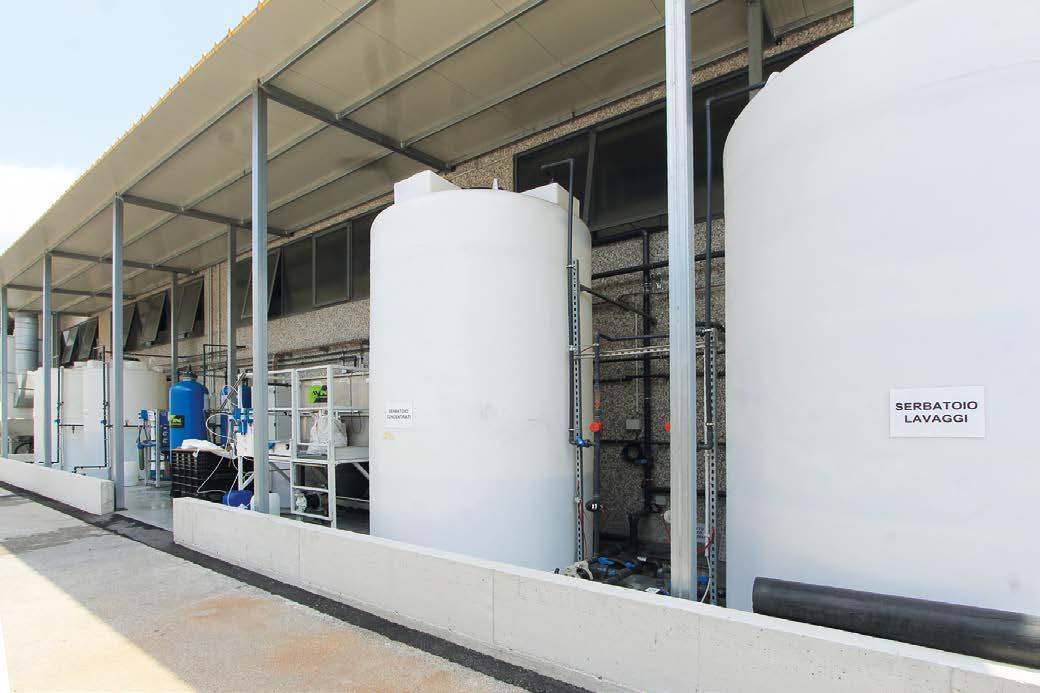
© ipcm
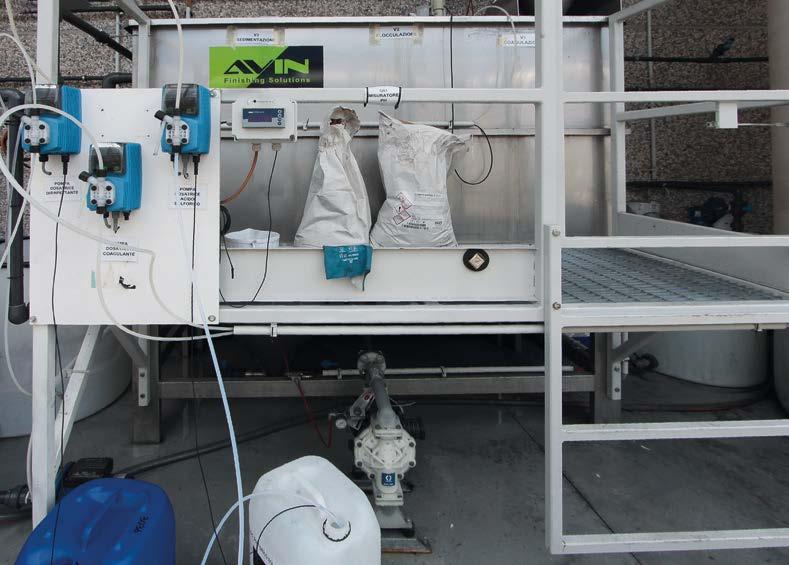
Treatment vessels and dosing pumps.
© ipcm

The reverse osmosis module.
1,000 hours. Consistency of results is indeed essential to meet our customers’ demands. This is why we turned to Avin for a tracking and control system that would enable us to monitor all stages of our coating process and to Noxor for an effective water treatment process that would recover the water used in pre-treatment and recirculate it while maintaining a high-quality degree,” explains Donà.
Avin’s control system
New Color wanted to track its production flow and monitor its quality. Therefore, it turned to Avin to upgrade the electronic and IT aspects of its plant, including a system that would allow controlling values such as temperature, pH in the active pre-treatment baths, water conductivity, and curing conditions for each coating cycle. Using the touch-screen panel, it is also possible to display a summary of the operating parameters set and their status via a user-friendly colour scheme, so that quick action can be taken in the event of an error in programme selection. “We kept the switchboard, but replaced the software package and the PLC, creating a new computer system that allows remote operation. The operator can use the PLC to select the programme to which the different processing parameters are associated, such as the type of pre-treatment process and curing temperature, identified by simple numbers. Once the starting and ending load bars have been selected, the plant performs the entire coating cycle automatically,” indicates Morgan Infanti, Avin’s General Manager. “As we have no standardised customer requirements, our coating cycle has to be adapted to individual orders. In addition, the new system allows monitoring consumption: we can check the quality of water in the pre-treatment phase, the amount of powder used and the corresponding paint tin, and the energy and water consumption of the entire plant,” says Donà.
© ipcm
Eluate collected in big bags.
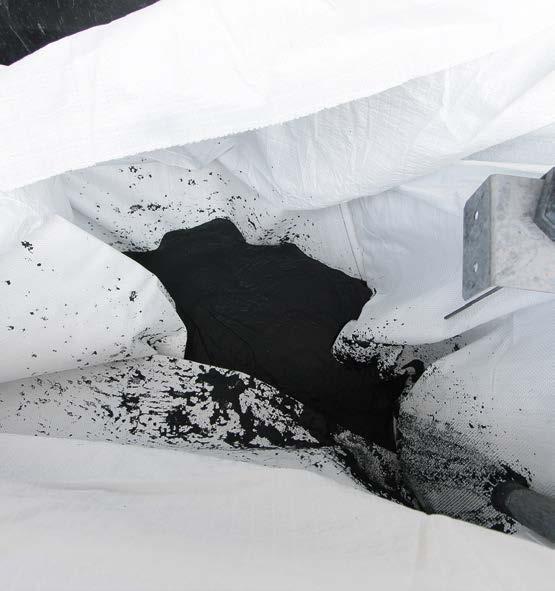
New Color also relied on NoxorSokem and Avin for conceiving a zero-discharge chemical-physical water treatment process that would allow water to be reused during the pre-treatment phase prior to coating. “The system includes a storage tank for rinsing water, which is continuously refreshed, and a tank for storing concentrates. Water and concentrates are dosed inside a three-vessel system equipped with sulphuric acid, coagulant, and disinfectant dosing pumps for the coagulation, flocculation, neutralisation, and sedimentation phases. Water is then filtered with quartzite (to remove any components that do not settle, such as sand) and activated carbon (to remove any organic compounds, such as COD and BOD). Finally, the resulting purified water is subjected to osmotic filtration, while a big bag collects the sludge for external disposal,” explains Fulvio Truant, technical manager at NoxorSorkem. “When New Color approached Avin for this plant, we studied together the best suited physical-chemical process through treatment tests carried out in our laboratory and subsequent analyses to determine the degree of pollutants reduction. We then collaborated with Avin for its integration with the existing pre-treatment process. Furthermore, from the start-up phase, we
© ipcm
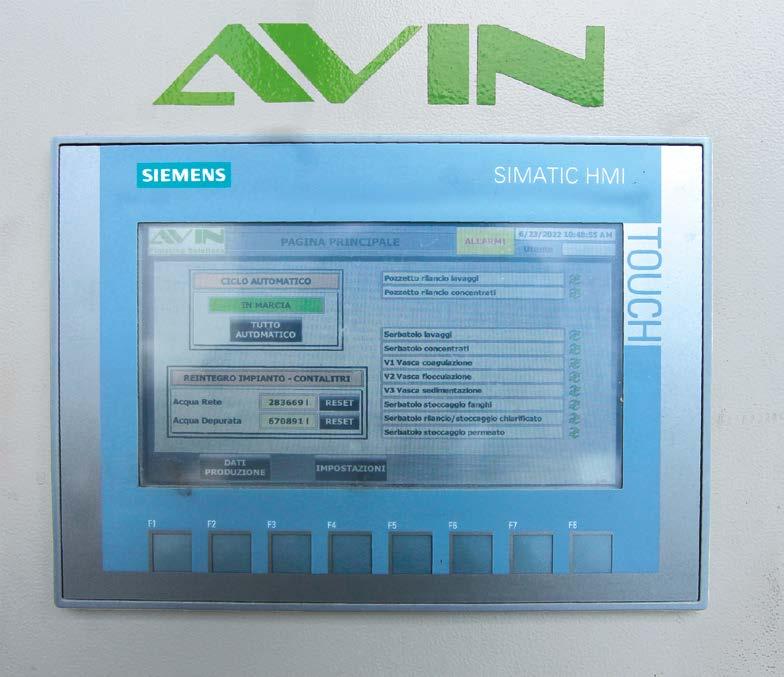
© ipcm take care of scheduled assistance to ensure that the plant always operates in the best conditions, providing also technical support and coaching, as well as a periodic analysis of the wastewater before and after the purification phase,” indicates Sergio Gava from NoxorSokem.
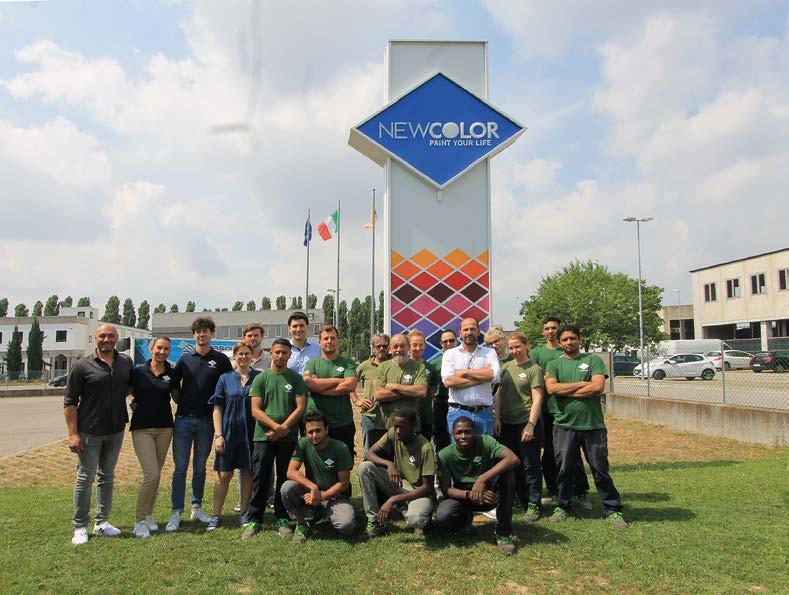
Reduced consumption and improved quality
One year after these systems’ installation, New Color has dramatically decreased its resource consumption and improved the finishing quality level offered to its customers. “The two investments were made simultaneously, with a view to both improving the quality of our coating process and reducing consumption. The water treatment plant enables us to optimise production, because overnight it purifies the water that we will use for pre-treatment the next day. At the same time, it has considerably reduced our consumption rates: in the past, we had to change water every two days, whereas now we have been using the same water for months, with stable conductivity values. So, the quality of our rinsing phase increased and, consequently, the improvement in the consistency and quality degree of our parts. Finally, Avin’s software is not only a great tool for increasing the production rates of our coating plant while maintaining its flexibility: is also able to analyse the quality of recirculated water and provide us with daily reports. We are fully pleased with the results of the synergy between NoxorSokem and Avin,” states Massimo De Gianni.