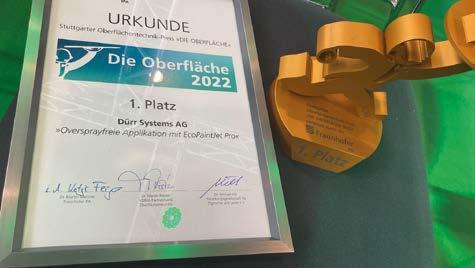
5 minute read
BRAND NEW
EcoPaintJet Pro by Dürr Wins Surface Technology Award 2022
Dürr’s EcoPaintJet Pro application technology won the innovation award “DIE OBERFLÄCHE” organized by the Fraunhofer Institute for Manufacturing Engineering and Automation.
EcoPaintJet Pro by Dürr, which can automatically paint complex car body surfaces without overspray and applying individual design elements without the need for masking, won the innovation award „DIE OBERFLÄCHE“ organized by the Fraunhofer Institute for Manufacturing Engineering and Automation since 2012, which was presented at SurfaceTechnology GERMANY trade fair. EcoPaintJet Pro can also lower production costs while improving the sustainability of individual paint shops. An initial measurement of the DXQ3D.onsite software detects and compensates for any inaccuracies in the conveyor system or the body shop. A second sensor mounted on the robot measures the deviation of the car body to be painted from the reference pattern. The robot controller adjusts the painting paths in real time. The speed and tilt angle of the applicator are also controlled so that the paint is always applied evenly and there is no overspray and no need for masking. In a standard production line that paints 110,000 car bodies per year, this saves more than 1.5 million square meters of film and 2.2 million meters of masking tape every year plus a lot of manual work. Another advantage is that the new process requires up to 30% less energy than the conventional method. “We at Dürr are very proud of the almost 20-strong team, which has been putting great effort and dedication into this invention since 2008. The innovative strength of our employees is the basis for our company’s success,” says Dr. Jochen Weyrauch, CEO of Dürr AG. “The EcoPaintJet Pro reflects a key focus in our development work: sustainability.” The EcoPaintJet Pro has already won the German Innovation Award and was recently a finalist for the European Inventor Award, which is organized by the European Patent Office.
For further information: www.durr.com/en/
© Dürr
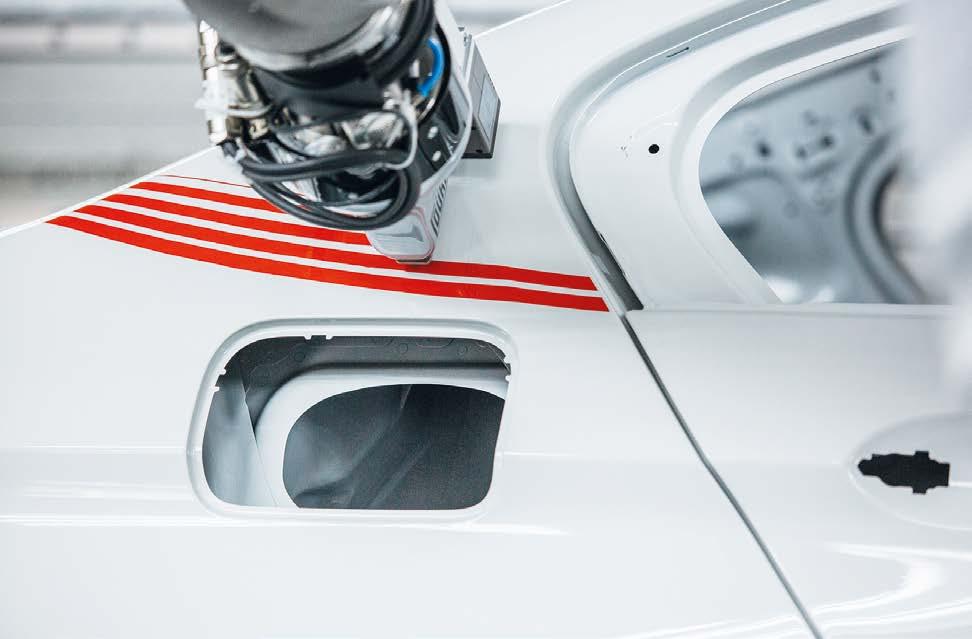
© Dürr
© Nouryon
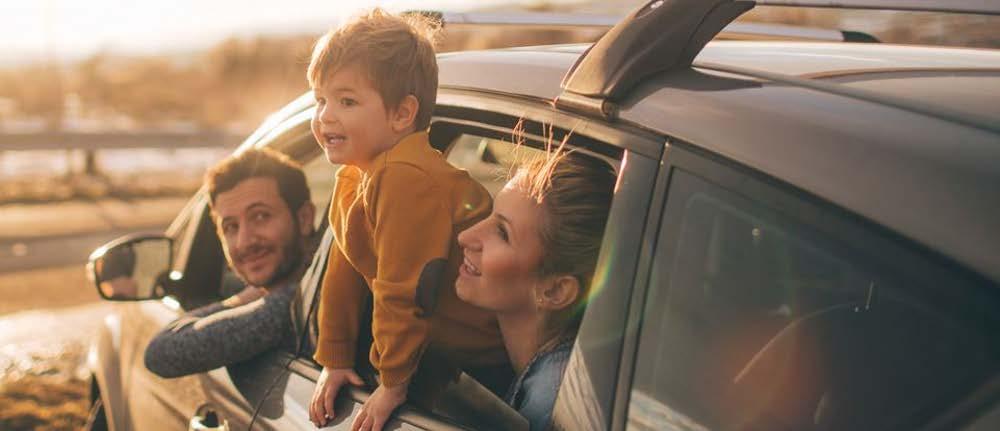
Nouryon Launched Expancel® HP92 Microspheres for the Automotive Industry
The new microspheres developed by Nouryon reduce weight and withstand high pressure in underbody coatings and sealants.
Nouryon has launched the Expancel® HP92 thermoplastic microspheres fillers, specifically developed to reduce the weight of underbody coatings and sealants and withstand high-pressure. When heated, the gas encapsulated in the polymer shell of the microspheres expands, allowing the Expancel microspheres to be used as a lightweight filler and blowing agent to make end products lighter and obtain different surface effects. In addition to requiring less raw material and reducing weight, the new product developed by Nouryon ensures reduced costs and environmental impact. Automotive manufacturers are increasingly needing lightweight materials, in order to meet the stricter emission regulations and the strong consumer interest in fuel-efficient vehicles that do not compromise on performance or passenger comfort. “The ability to produce lightweight solutions for our key markets presents tremendous growth opportunities for Nouryon as our customers increasingly focus on implementing more sustainable solutions. Our customers in the transportation industry are looking for innovations that address several technical requirements in one product and we are proud to support them with a solution that not only improves fuel efficiency, enhances acoustics and seals for harsh weather conditions but also supports the reduction of carbon dioxide emissions,” stated Johan Landfors, Executive Vice President and President of Technology Solutions and Europe at Nouryon. “When used in underbody coatings and sealants, Expancel® HP92 microspheres allow our customers in the automotive industry to use high-pressure application processes on surfaces with up to four times better volume recovery to its original shape after pressurization compared to an older grade of thermoplastic microsphere,” added Sylvia Winkel Pettersson, Vice President of Engineered Polymers at Nouryon. “Our technology is aimed at combining and optimizing the pressure resistance associated with glass microsphere grades with the light weight of thermoplastic microspheres fillers in one refined solution.”
For further information: www.nouryon.com

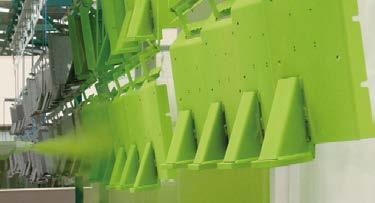
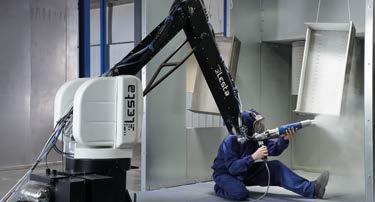
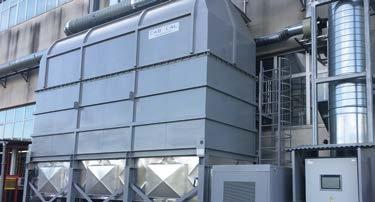
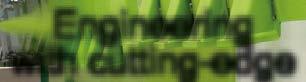
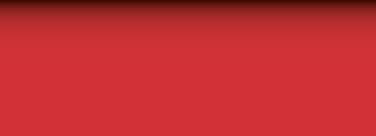
© BMW GROUP
The BMW Group Employs BASF Paints Certified According to The Biomass Balance Approach
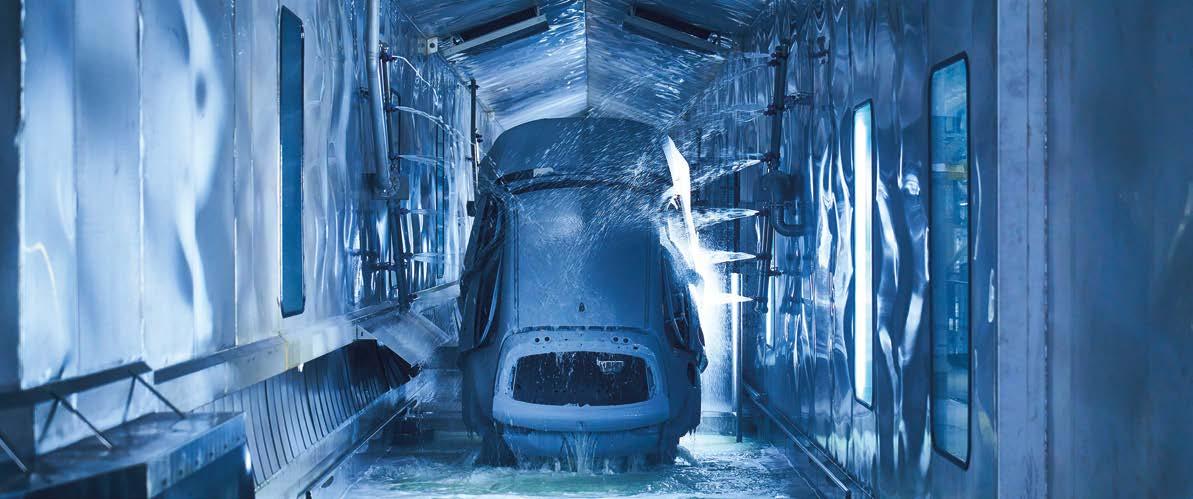
The BMW Group is the first carmaker to place its trust in more sustainable automotive OEM coatings certified according to BASF’s biomass balance approach.
The BMW Group has chosen to use BASF Coatings’ CathoGuard 800 ReSource e-coat at its plants in Leipzig, Germany, and Rosslyn, South Africa, and the iGloss matt ReSource clearcoat throughout Europe, thus investing in the use of more sustainable raw materials. These products enable CO2 avoidance of around 40% per coating layer, which will reduce the amount of CO2 emitted in the plants by more than 15,000 metric tons by 2030. The BMW Group produces an average of around 250,000 vehicles every year at its Leipzig and Rosslyn plants. “As the largest provider of chemical products to the automotive industry, we are aware of our responsibility to support our customers with innovative, eco-efficient solutions. The biomass balance approach allows us to make our coatings solutions even more sustainable while retaining the same quality. We are delighted that the BMW Group has chosen to play a pioneering role in the automotive industry and that our products play a key part in helping it achieve its ambitious sustainability goals,” said Dr. Markus Kamieth, Member of the Board of Executive Directors of BASF SE. “By reducing our use of fossil raw materials, we can conserve natural resources and lower CO2 emissions at the same time. To achieve this, we are increasingly relying on sustainability innovations in our supplier network,” said Joachim Post, member of the Board of Management of BMW AG, responsible for Purchasing and Supplier Network. “Innovative paints based on renewable raw materials are an important step in this direction.” The development of more sustainable versions of its products, falls within BASF’s biomass balance approach: renewable raw materials like bio-based naphtha and biomethane from organic waste are used as raw materials when manufacturing primary chemical products and are fed into the production in Verbund. The proportion of bio-based raw materials is then arithmetically assigned to certain sales products according to a certified method. This attribution model is comparable with the principle of green electricity. An independent certification confirms that BASF has replaced the quantities of fossil resources required for the biomass-balanced product sold with renewable raw materials.