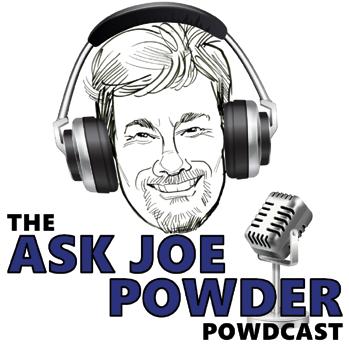
4 minute read
ASK JOE POWDER
The “Ask an Expert” Column
Kevin Biller
kbiller@chemquest.com
Our powder coating expert is back to answer increasingly challenging questions from readers.
Hey Joe, My name is Richard Stange and I’m a Mechanical Engineer at major fabricator in California. I just read your 2017 article, “Technology Interchange: Choosing an Outdoor Durable Powder Coating”. I found your article very informative and feel like I have a better understanding on the subject. Our company designs and manufactures irrigation equipment, which includes metal chassis and pedestals that get powder coated for the outdoor environment, which is sold all over the world. We have multiple sheet metal vendors who use different powder coaters. We recently discovered that the different powder coaters don’t all use the same chemistry type. Some use a polyurethane-based chemistry, where others use a polyester-HAA based chemistry. From your article, it looks like the Industrial and HighPerformance chemistries are what we are looking for in our product for UV durability resistance. My question is this – Is the UV resistance in powder coating based solely on the polyesterHAA or polyurethane, or is an additional “UV inhibitor” added to the chemistry? I’m trying to determine how to best call out UV resistance for the powder coating in my drawings. Appreciate your help and look forward to hearing from you. Best regards, Richard Stange San Marcos, California
Hey Richard, Thanks for reading my article and I am glad that it helped. UV durability is mainly influenced by the primary resin in the powder coating formulation. Both polyester-HAA and polyurethane chemistries rely on a polyester polymer as the main binder component. Polyester polymers can be standard outdoor grade (1-2 years Florida durability) or “superdurable” grade (about 5 years Florida durability). For your products, you’ll want to specify the superdurable grade. Even better yet, require an AAMA 2604 (American Architectural Manufacturers Association) grade (or Qualicoat Class 2) powder. The 2604 spec requires 5 years Florida durability and the Qualicoat Class 2 requires 3 years Florida durability. I have attached copies of these specifications. As for formulators using special additives to enhance outdoor durability, the inherent performance is based on two things - using only UV durable ingredients (raw materials) in the powder formula and not incorporating any weak links or bad actors (e.g., waxes or fillers). Special additives don’t make a big difference especially in pigmented powder coatings. The ole adage, “You can’t make a silk purse out of a sow’s ear”. I hope that this helps. Please let me know if you have any other questions. Kind regards, Joe
Hi Joe, We have been developing new polymers for powder coatings. One of the most critical properties is impact resistance. Our test results have been inconsistent and vary significantly depending on substrate used. In some cases the coating passes 160 inchlbs. and with other conditions only gets 80 inch-lbs. What could be the cause of this variation? And how can we eliminate these variations? Thank you! Rebekah Philadelphia
Hi Rebekah, First of all, kudos to you and your colleagues for developing new polymers. Most advancements in powder coating technology are based on new and improved polymer chemistry. It’s tough for us formulators to create new coatings without innovative polymers. The most common impact resistance test method is described in ASTM D-2794 Standard Test Method for the Rapid Deformation of Organic Coatings (Impact). The ISO-6272-1 standard covers the same test method. The values typically quoted in impact resistance are inchpounds (the metric centric folks use Newton-meters) and refer to the
weight times the distance (height) of the impact. Another parameter is the radius of the “ball” or hemisphere that impacts the surface of the coating. North America typically uses a 5/8-inch (15.9 mm) diameter ball although some specifications call for a ½-inch (12.7 mm) one. The smaller the diameter, the greater the deformation and hence lower impact resistance. Aside from the coating’s inherent flexibility, substrate has the most significant influence on film performance. Adhesion is affected by the type of metal, the surface profile, cleanliness, and pretreatment. Correspondingly impact resistance is affected by adhesion so poorly pre-treated substrate will cause unexpected impact failure. On the other hand, well pre-treated metal will enhance impact resistance by providing a strong bond of the powder to the substrate. In addition to metal preparation, the gauge and type of substrate significantly influences impact resistance because of the degree of deformation to the substrate. Hence 80 inch-lbs. on a ductile grade of aluminium will have different deformation than carbon steel. And certainly, the gauge or thickness of the metal will also influence deformation and therefore impact resistance. Thicker gauge metal will deform less and therefore the coating experiences less stress. Coating parameters to control are mainly film thickness and degree of cure. Thinner films tend to exhibit higher impact resistance whereas thicker ones are more brittle. Complete cure is highly recommended as under-cured powders will usually exhibit lower impact resistance. Make sure your coating receives the time at temperature specified by the coating supplier. When characterizing a coating for impact resistance the challenge is to use substrate(s) that are relevant to the target market(s). For general industrial end uses, cold rolled steel is common whereas the architectural market typically uses various grades of aluminium depending upon the fabrication and performance requirements. In addition, pre-treatment type is important. Cold rolled steel is usually pre-treated with a phosphate (iron or zinc) or in newer installations a zirconium-based product. Aluminium is typically pretreated with chromate, zirconium or sometimes zinc phosphate. For polymer development I suggest that you obtain your substrate from a reputable test panel supplier. A list of them can be found on the PCI website (www.powdercoating.org) under “Members”. Good luck with your polymer chemistry efforts, the industry needs you. Warm regards, Joe
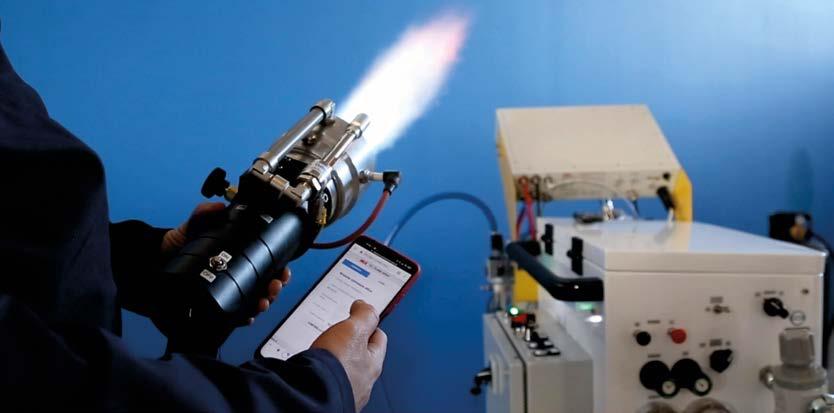