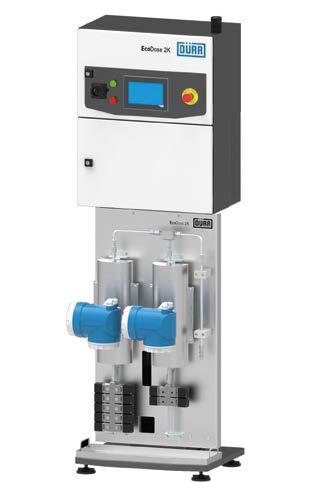
7 minute read
HIGHLIGHT OF THE MONTH
SPECIAL ISSUE ON AUTOMOTIVE
EcoDose2k for Automated Colour Matching of Bodywork Paints
To achieve greater accuracy, repeatability and speed in its Milan laboratory’s colour matching activities for the refinish industry and to provide customers with high-quality coatings formulations for body parts, in line with its standards, PPG has opted for the Verind-Dürr EcoDose2k dosing and mixing technology which, thanks to specific colour change cycles, has also made it possible to optimize the environmental impact by reducing the consumption of solvents by 400kg per year.
With the global refinish paint market expected to reach a value of $12.29 billion by 20281, manufacturers are investing in cutting-edge technology to offer the industry new coatings that not only are of high quality and environmentally friendly, but can also be applied to car bodies to faithfully replicate the colour and characteristics of OEM paints. One of them is PPG, American multinational company that has been developing paints, coatings and special materials for several market segments for 140 years. In 2021 it invested more than $463 million (around 3% of its annual net sales) in the R&D departments and with over 3,500 engineers in more than 75 countries it studies solutions to optimise its products and internal processes in order to satisfy the needs of the customers.
1 https://www.reportsanddata.com/report-detail/automotive-refinish-coatings-market In February, PPG installed an EcoDose2k device in its fully automated colour matching laboratory in Milan (Italy). This new electronic system for dosing and mixing water-based and solvent-based paints was supplied by Verind SpA (Rodano, Milan), a company belonging to the international group Dürr AG that specialises in designing innovative technological solutions by integrating know-how, industrial systems engineering, equipment, and ecotechnologies specific to painting, coating, and water treatment processes.
Expertise and automation at the service of customers
PPG’s Milan colour matching laboratory for the automotive refinish industry was upgraded in 2016 with the installation of two closed-loop automatic systems supporting the faithfully reproduction process of paint formulation for any vehicle brand submitted to PPG technicians. “Our activity requires specialised skills, previous experience, and
© ipcm

The metal plates coated with PPG paints created with the automatic dosing and mixing technology from Verind-Dürr and EcoDose2k, Verind-Dürr’s automatic dosing and mixing equipment.
© Verind
The offices of the colour matching laboratory for the refinish sector of PPG in Milan.
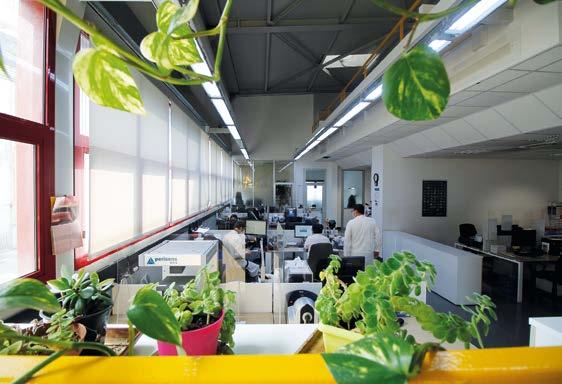
© ipcm
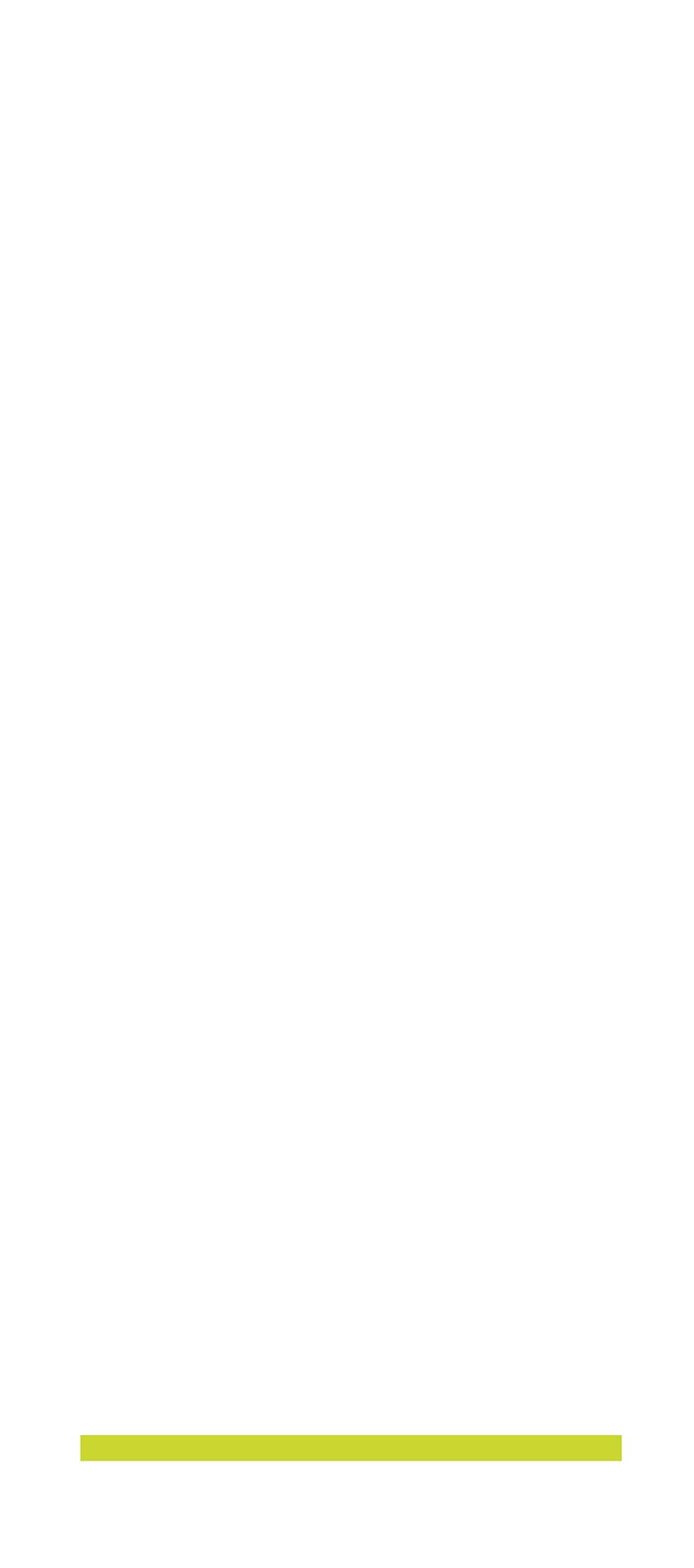
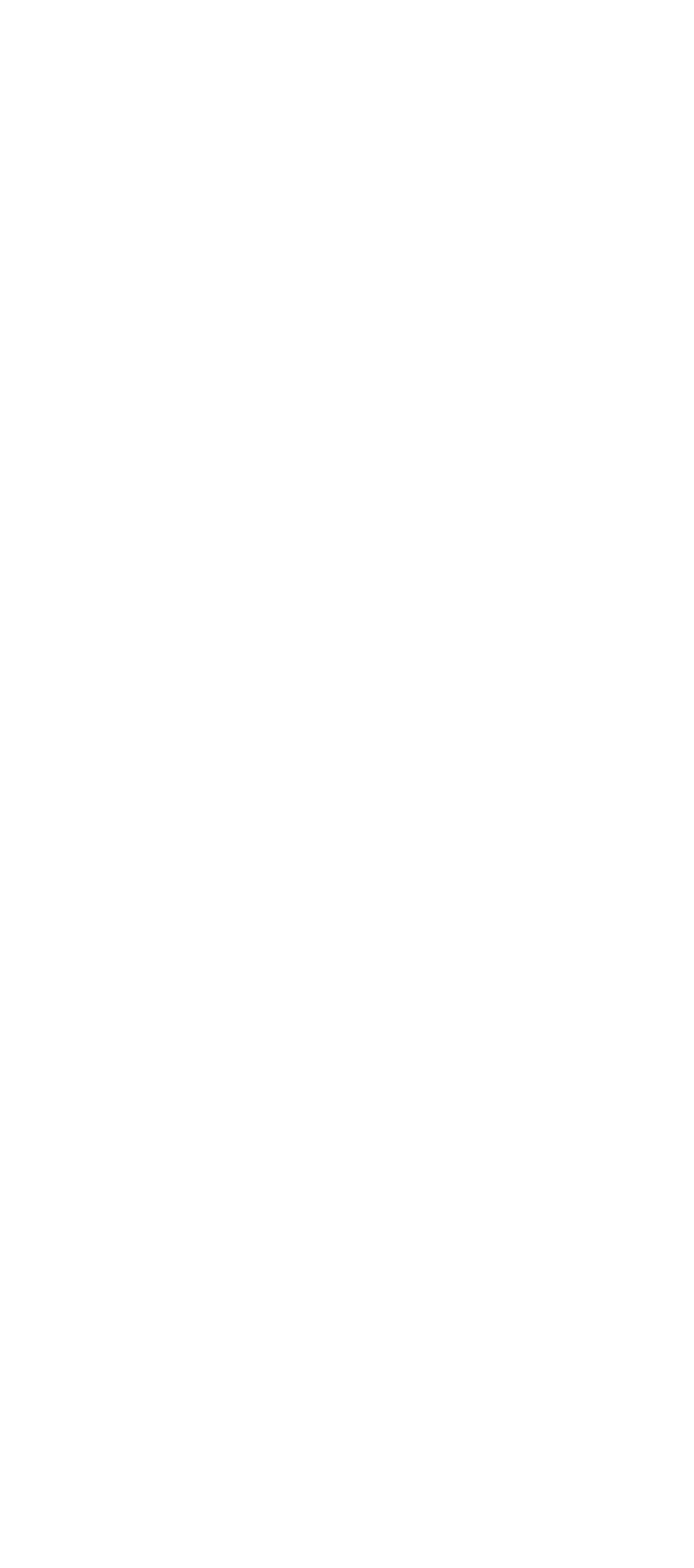

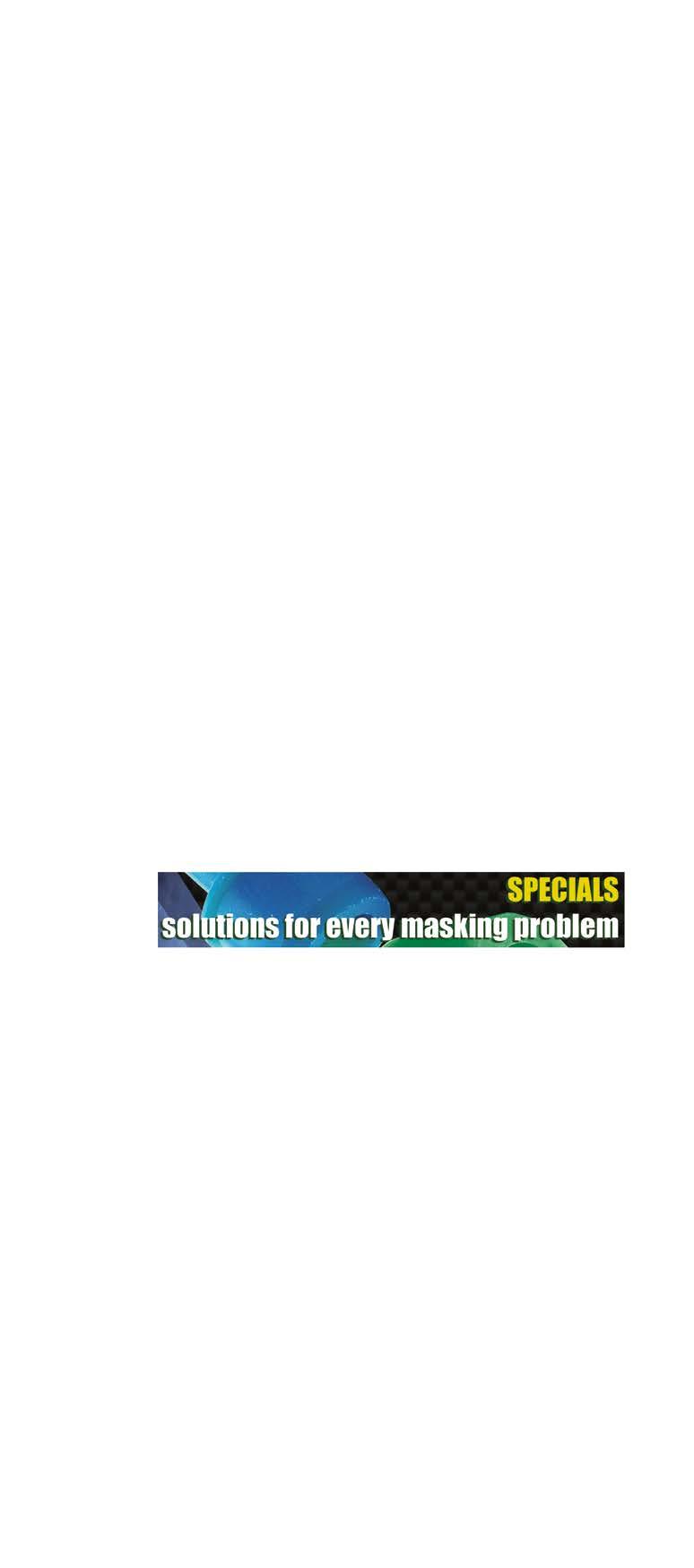
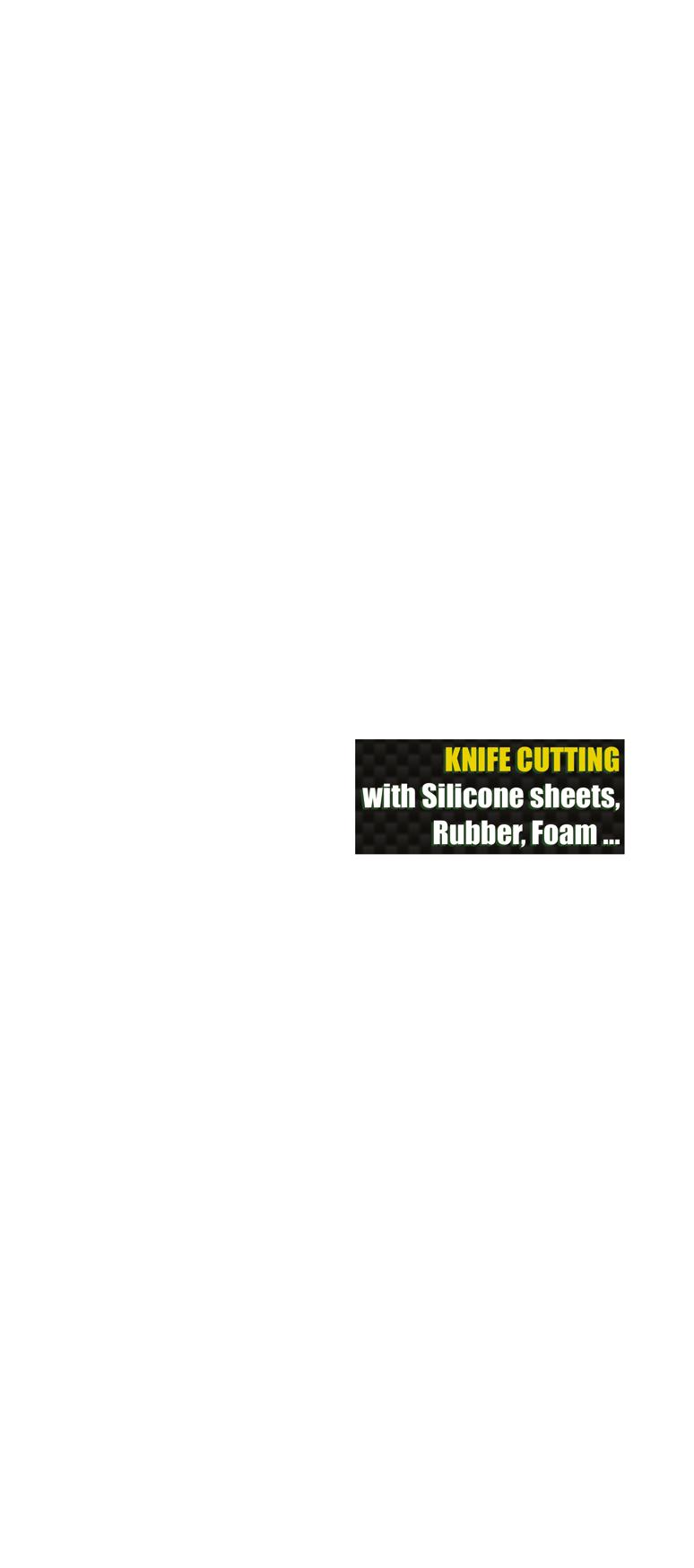
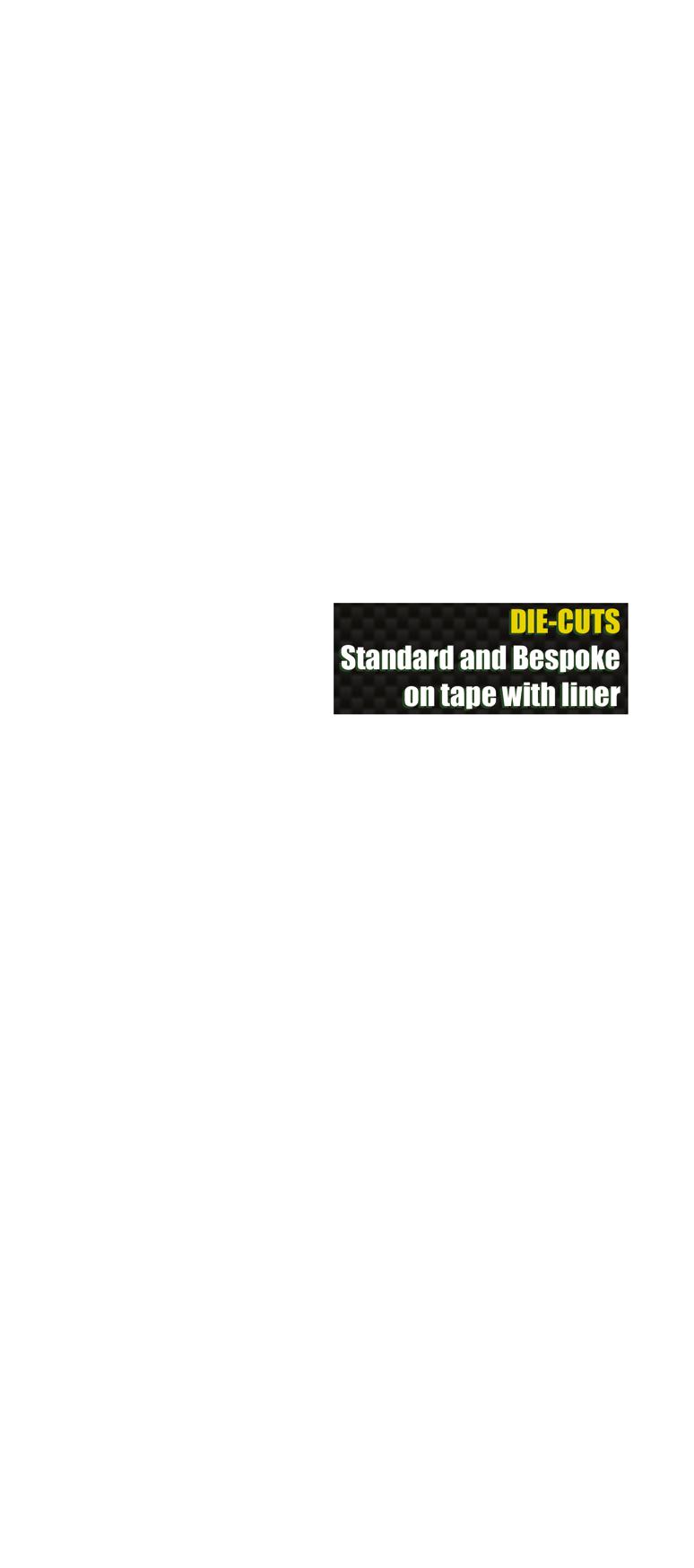
continuous training. The quality and matching degree of the formulations we produce in our lab must meet very high standards, so that our customers use them for the application on car bodies on which OEM paint is already present,” explains Rita Di Leo, Colour Application Engineering Manager at PPG Italia. This company is therefore able to apply both 1K and 2K paints in any shade, as well as transparent gloss finishes, in order to faithfully replicate their related bodywork painting processes, and therefore their results. When PPG’s colourists receive a sample containing a particular tint, they analyse it and enter the relevant data into the plant’s panel, which then doses the paint, mixes it, applies it on metal plates, and dries it according to the customer’s oven specifications. The colourists finally check the metal plates and, if the result does not match the sample supplied, the process is repeated until an exact match is found. “Our technicians use microscopes and spectrophotometers to identify the characteristics of each colour and paint, because we have no information about the pigments used, the dosage, or the type of coating applied, as it may well have been made by other manufacturers. Strong creativity, in-depth knowledge of the PPG products to be used to recreate the formulation, and willingness to experiment are also required. In fact, an exact copy is rarely achieved after just one attempt. It usually takes three or four attempts to replicate a pastel shade, whereas for metallic effects, which are more complicated, it sometimes takes up to ten attempts before finding the matching formulation. Therefore, production rates must be high in order to deliver paints to refinishers in the shortest possible time.” This is why the laboratory collaborated with Verind to find a solution that would optimise its colour matching process while decreasing product consumption due to colour changes and improving the environmental impact of PPG’s operations. MOULDED PRODUCTS SILICONE and EPDM made TAPES in PET, Vinyl, PI, Creped Paper, Aluminium ... HOOKS for painting and weld STEEL and IRON made DIE-CUTS Standard and Bespoke on tape with liner KNIFE CUTTING with Silicone sheets, Rubber, Foam ... SPECIALS solutions for every masking problem
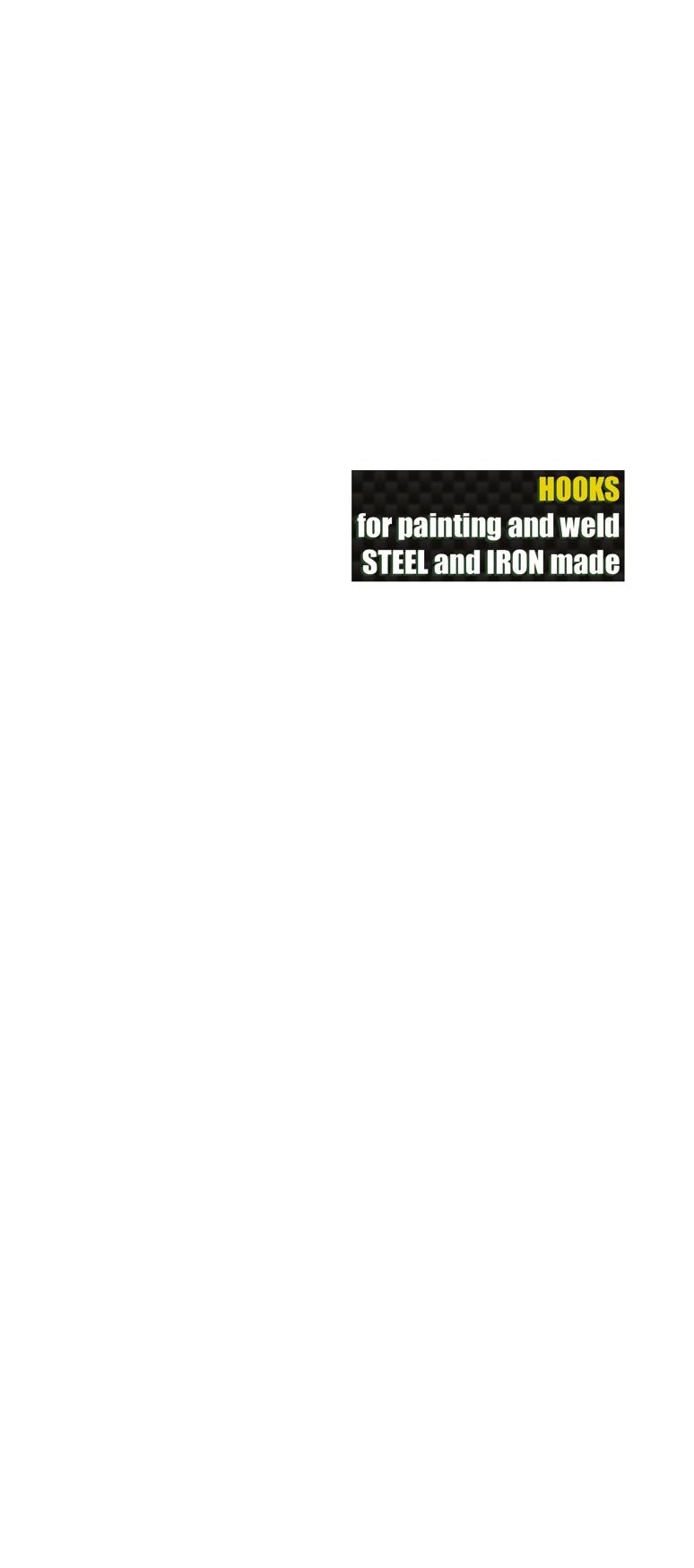
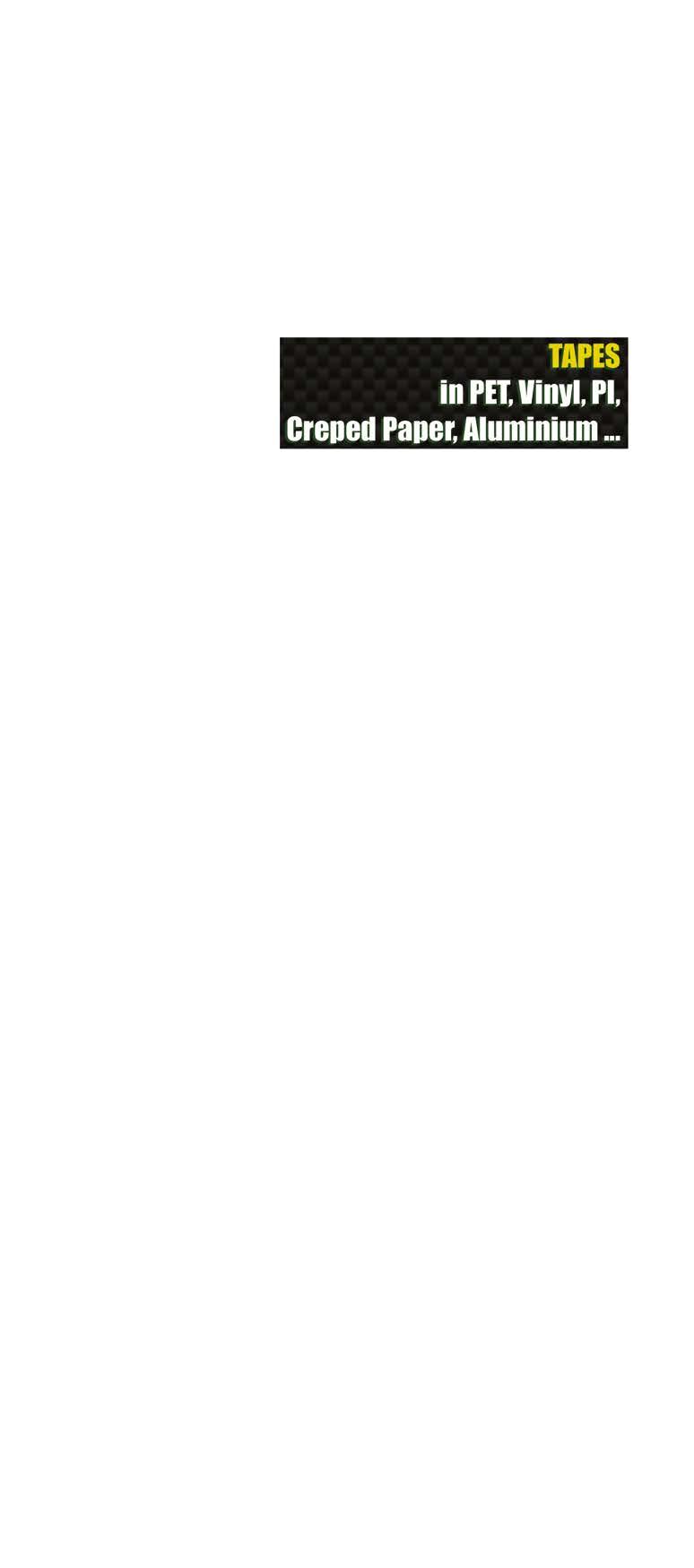
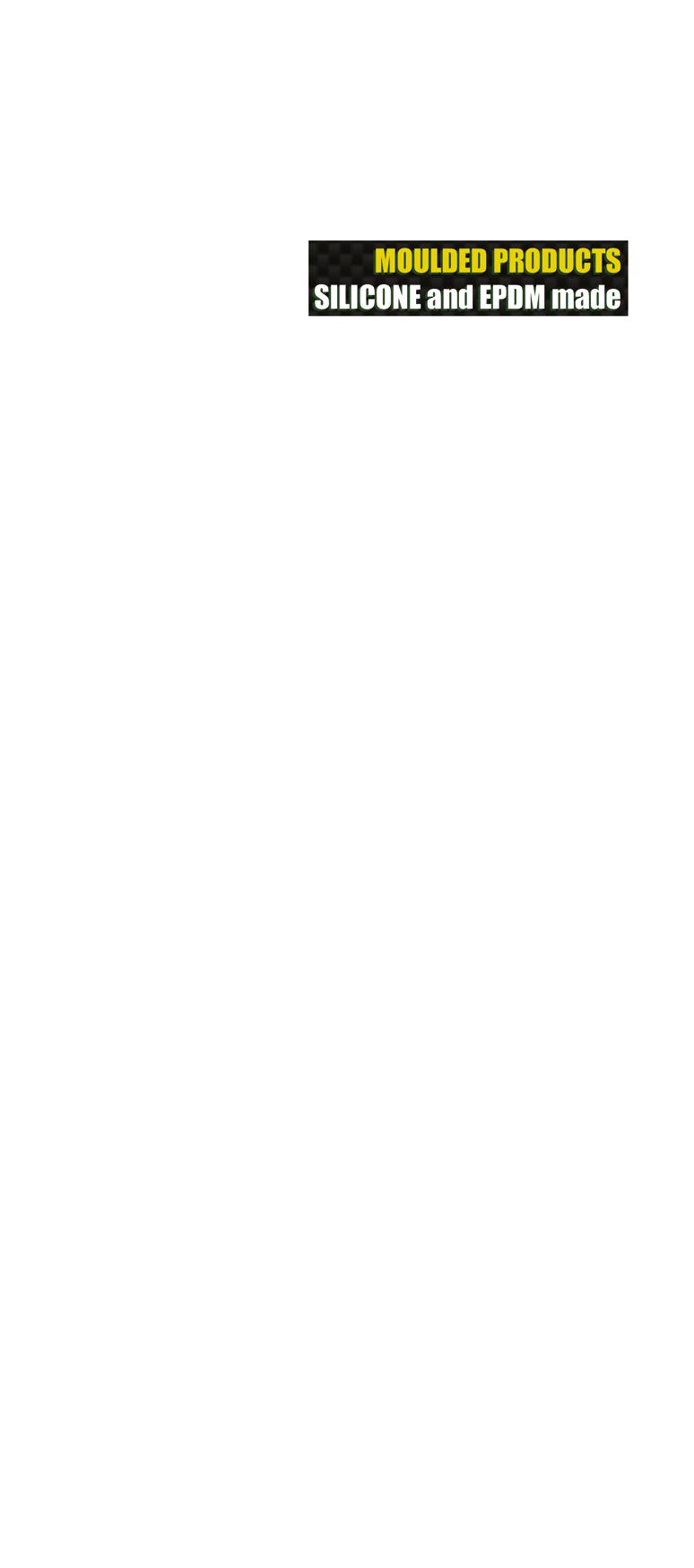
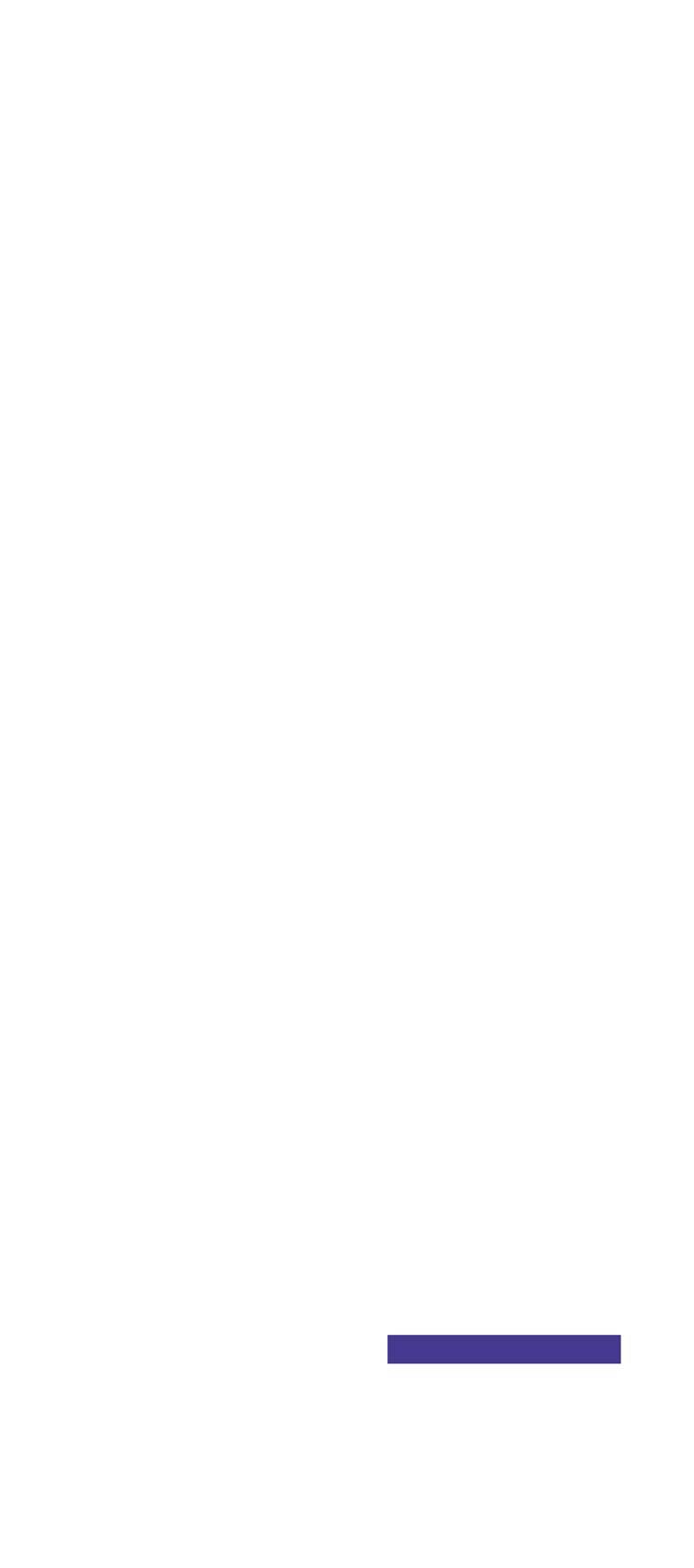
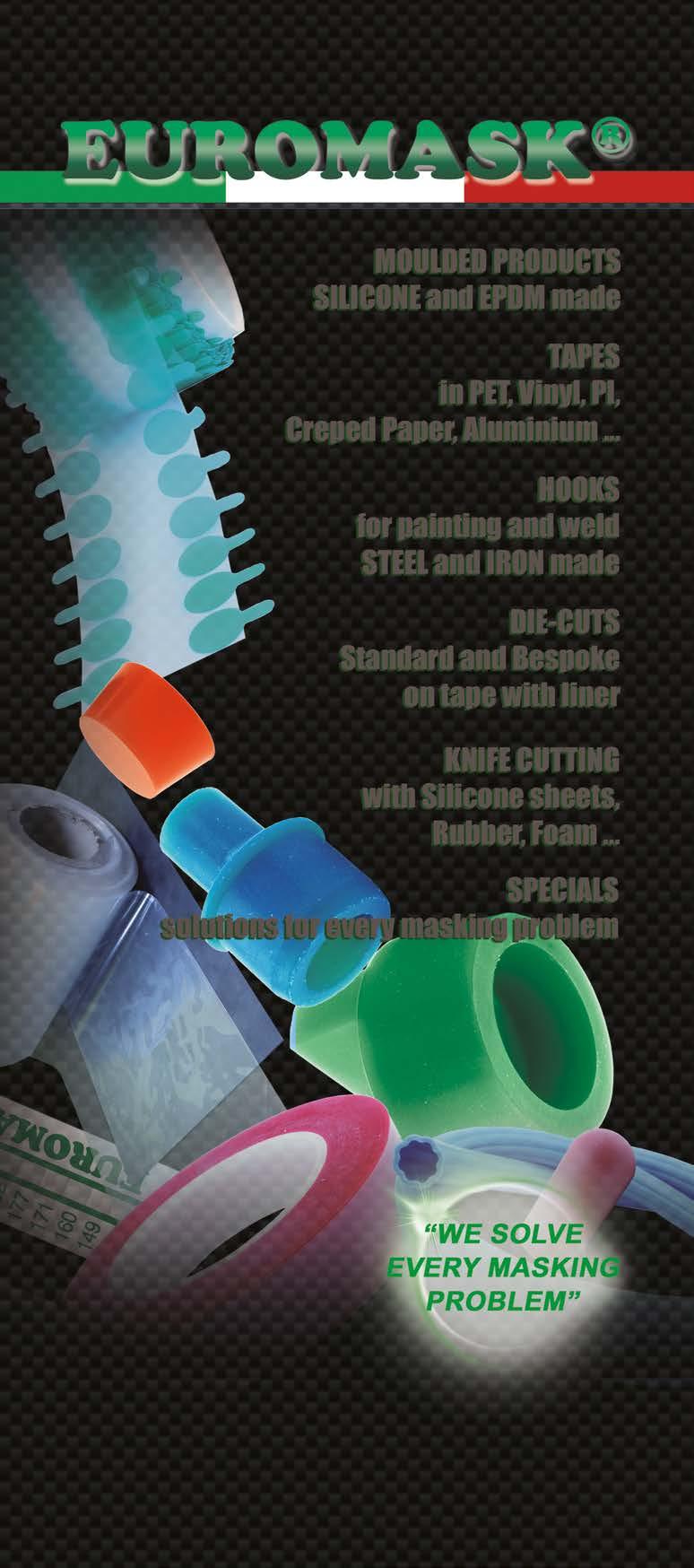
FINISHING GROUP srl
v.le A.DeGasperi, 31 - 20045 Lainate - Milano tel. +39 02 9678 0055 - fax +39 02 9678 2993 www.e i n f o @ e uro u r o maskm a s k s s ho h o p p .com . c o m
© PPG © ipcm
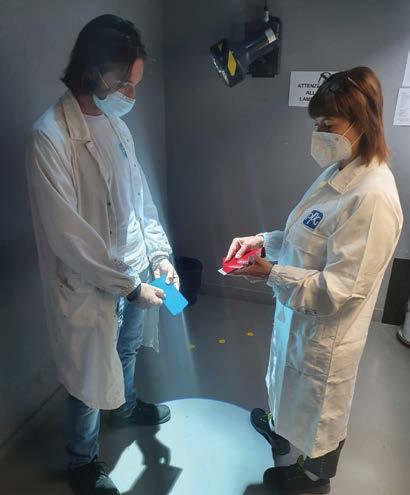
A PPG colourist analysing a sample provided by the customer. One of the control phases of the metal plates obtained with EcoDose2k.

EcoDose2k and the importance of monitoring the dosing and application process
EcoDose2k is a flexible, modular electronic system for stoichiometric dosing and mixing of 2K/3K solvent-based, water-based, and HS coatings; it is also suitable for the DTM technology. The technical data provided by Marco Assorgia of Verind confirm that “EcoDose2k has a stoichiometric catalysis ratio of 1:1 to 30:1, it can store 1,024 working recipes, and it is equipped with Direct Injection Technology (DIT) for dosage capable of meeting dosing tolerances of less than 1%, with two channels (A and B, with density and temperature measurements for each individual channel) and separate cleaning circuits. Finally, it also provides a functional and safety interface with the Master system line via Ethernet UDP communication protocol”. “We provided a solution to combine an application system with an automatic dosing and mixing one featuring Coriolis technology. Installed on the existing coating line, this machine also allows monitoring the entire process,” explains Alessandro Soba, the sales manager of Verind. “Information on productivity and alarms related to the pot life of products and to any deviations from the pre-set quality standards are immediately available on the user interface of the industrial PLC, which also allows advanced management of consumption records for the application station. This makes it possible to take corrective action even remotely. Finally, the software package provides a predictive maintenance service on all components.” “The applied films must have uniform thicknesses and present no orange peel effects, because even a small variation in the amount of paint applied alters the results obtained on the plates. Therefore, constant control of process parameters and component relations is essential in order to also keep coating quality constant and provide our customers with the exact formulation of the samples they submit to us,” notes Di Leo.
The modular, expandable automatic colour change system for paints and catalysts, the high process reliability, stability, and repeatability over time, and the absence of stress on paint products have speeded up and optimised PPG’s operations. The company, which in addition to perfect colour matching also wanted to reduce its consumption levels, is very satisfied: “Environmental sustainability and process optimisation through state-of-the-art technology are the pillars of PPG’s philosophy. Our new equipment has enabled us to optimise the amount of paint products and solvents we utilise and ultimately to reduce resource consumption. Verind’s equipment is very easy to use and its interface displays user-friendly graphs showing the actual flow rate and partial consumption of each programme, as well as information on the VOCs generated. We estimate that we will be able to use 400 kg less solvent per year, which is an excellent achievement with a view to reducing PPG’s environmental impact,” says Di Leo. “Indeed, in June we installed a second EcoDose2k device on our second, identical plant, with the aim of increasing the performance level of our entire colour matching laboratory and making our technological choices greener and greener.”