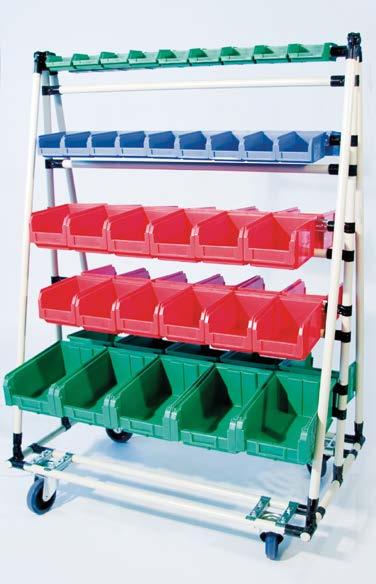
6 minute read
ANALYSIS
SPECIAL ISSUE ON AUTOMOTIVE
Lean Manufacturing: How to Translate it from a Concept into Reality with the Right Logistics, Production, and Storage Structures
Mirko Migliorini
FlexLogik Srl, Galliate (Novara, Italy) mirko.migliorini@flexlogik.it
Maximising value by reducing waste. This summarises the industrial approach that Toyota developed in 1950 to become more competitive against US companies. It involved the introduction of a new production system (afterwards known as the “Toyota Production System” but also as “Toyotism”) based on a simple yet powerful idea: do more with less. Translated into industrial terms, this means using as few resources as possible, as productively as possible, while eliminating any kind of waste. Waste is anything that does not add value to the product or service in the eyes of the customer. This gives rise to a corporate culture that ensures that each individual employee sees their processes through the eyes of the customer, with a view to the creation of value and therefore on the prioritisation of what such value is for the company and what the value stream is. The TPS was then studied, westernised, and translated into what we now know as “lean manufacturing”. This is a mindset, a working philosophy that encompasses various methods that realise it, with the aim of achieving a value-added result for the customer. It includes organisational models, technologies, and technical solutions for improving the functioning of the company while reducing any waste of time, space, and materials. FlexLogik understands the concept of lean manufacturing in a very practical way: saving even just five minutes every time you make, move, or store something quickly translates into thousands of Euros in savings. By eliminating even half of the waste hidden in the folds of industrial production, it is possible to gain in efficiency, yield, satisfaction, market position, and company strength.
© FlexLogik
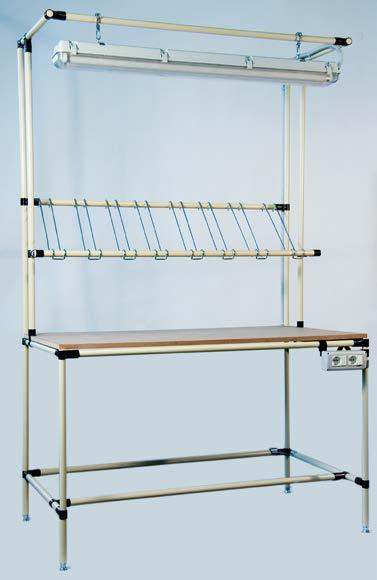
A lean workstation (on the left) and a lean special trolley (on the right) for lean manufacturing within the FlexLogik range of products.
© FlexLogik From theory to practice
How can this approach be implemented? By using highly efficient, robust, logical, and flexible handling, storage, and production systems. FlexLogik’s design department ingeniously exploits space and gravity, studies and optimises routes, and simplifies procurement operations to offer solutions capable as follows: • Increasing usable space by 10 to 60%; • Increasing productivity by 15 to 100%; • Decreasing working hours by 15 to 60%; Decreasing the distance travelled by each batch by 20 to 95%.1
1 Statistical data from the field before and after the implementation of FlexLogik systems.
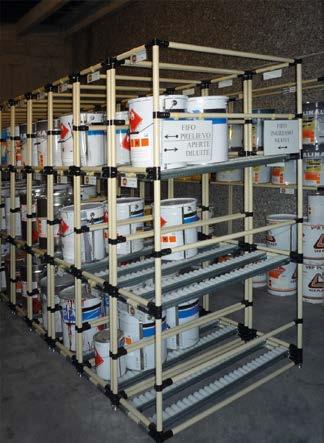
© FlexLogik © FlexLogik
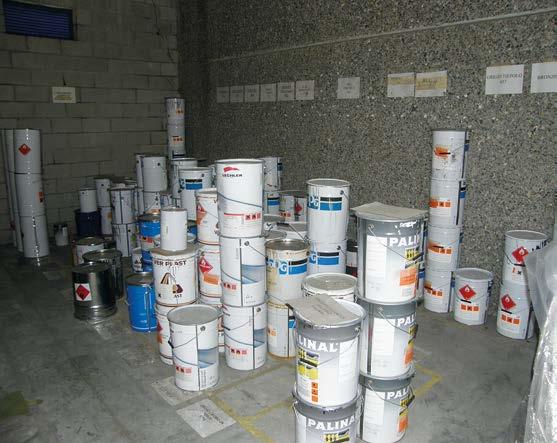
Paint warehouse reorganisation – before and after.
The FlexLogik solutions are manufactured in Italy with quality materials. They can be assembled, modified, and transformed several times. Every component can be built with an Allen key and a pipe cutter. They are flexible, as they integrate seamlessly with existing structures and adapt easily to production changes. Finally, they are made from standard components. The FlexLogik range includes structures for three production macro-areas: • lean solutions for handling, such as gravity roller conveyors and flat roller conveyors for manual or automatic handling of components, semi-finished products, goods, and materials to achieve efficient logistics; • lean solutions for storage, including fixed and mobile structures for dynamic warehouses and FIFO gravity racking for light and heavy loads; • lean solutions for assembly and production, such as line feeding and supply units or equipped trolleys for transporting all types of material.
Lean manufacturing in the automotive sector: where it all began
The concept of lean production originated in the automotive sector, since it originated from Toyota’s successful idea in the 1950s, and it is equally true that this industry is still the one that benefits the most from such approach. If the in-house manufacturing and especially assembly processes of a vehicle are carried out extremely efficiently and without generating any waste, the throughput time of each product is as short as possible, with a positive effect on the end customer’s waiting times. FlexLogik offers numerous solutions for the automotive sector. Here below, we present two case studies with very beneficial outcomes in terms of efficiency, productivity, and waste reduction.
Case study no. 1 - Paint warehouse reorganisation
Paint warehouse containing 80 automotive colours. Drums of different sizes were placed on the floor or on pallets. Each paint drum was placed on top of the previous one with the same colour. Pictured is a partial view of the condition of the premises.
Critical issues Paint display was not clear, but rather difficult to understand, resulting in long pick up times. FIFO (First In First Out) logic was not followed, resulting in the expiry of products. The time needed to carry out the inventory was long and with a high risk of error. Disorganisation prevailed.
After implementing a FlexLogik system The paint warehouse was reinvented with the FlexLogik system, using shelves with gently sloping roller tracks. 14 shelves with 2-storey rollers and 14
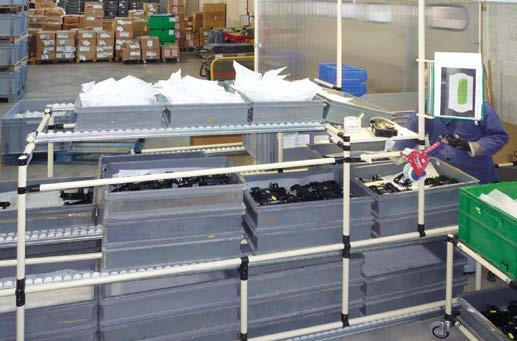
© FlexLogik
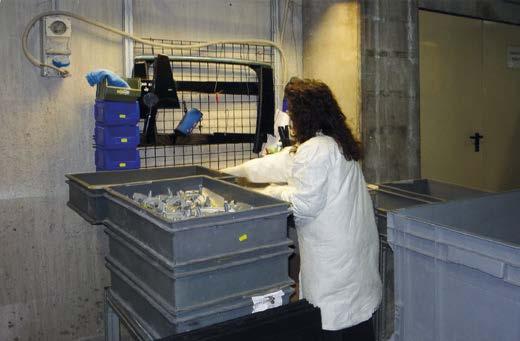
Assembly of handles – before and after.
© FlexLogik
with 3-storey rollers were built. Paint drums are now loaded on one side and unloaded on the other. They slide on the rollers, thus facilitating handling. They are sorted by colour and they are easily distinguishable through their labels. Static shelves containing the paints used in lower volumes were built against the wall. The warehouse respects the FIFO order, i.e. the first incoming drum is the first one to be picked up for use.
Advantages • Increase in the number of colours stocked in the same space from 80 to 150 and 85% space saved; • Average inventory time reduced from 40 to 20 minutes; • FIFO order respected with no possibility of error, thanks to the slight slope of the roller tracks; • Order and cleanliness restored.

Case study no. 2 - Assembly of handles
The line operator took two boxes and an empty container from a pallet and brought them close to their workbench. The empty container was placed behind the operator, whereas the boxes were placed to their side. The operator took the two parts to be assembled from their respective boxes. The two parts were checked and, if they were not defective, they were assembled and packaged. Finally, the assembled handle was placed in the container.
Critical issues The operator lost a lot of time handling the boxes containing the parts.
After implementing a FlexLogik system An assembly system consisting of two modules was built. The first module consists of two roller tracks for the boxes with fixed and mobile handles, a track for plastic bags, and two tracks for the return of empty boxes. The second module consists of a roller for the empty containers and an upper one for the assembled handles. The rollers’ gentle slope allows constant feeding.
Advantages • Previous production: 190 handles/hour; • Current production: 280 handles/hour; • Productivity: + 47%.
About FlexLogik
“Born and raised in production, we prefer deeds to words.” This is how FlexLogik (Galliate, Novara, Italy), a company specialising in the design and supply of highly efficient and flexible lean solutions for more than ten years, presents itself. Lean and flexible itself, this company designs its products in Italy but it has five distribution centres worldwide to serve the Americas and Northern, Southern, Eastern, and Western Europe. Another important feature is the speed of its service: more than 1 million parts ready in stock allow a quick response to any request for efficiency and savings. Prior to purchase, FlexLogik provides customers with a detailed presentation of a tailor-made solution that can be reassembled and modified whenever needed. The project is designed free of charge and without obligation. Upon confirmation, the structures can be assembled and ready in just a few days.

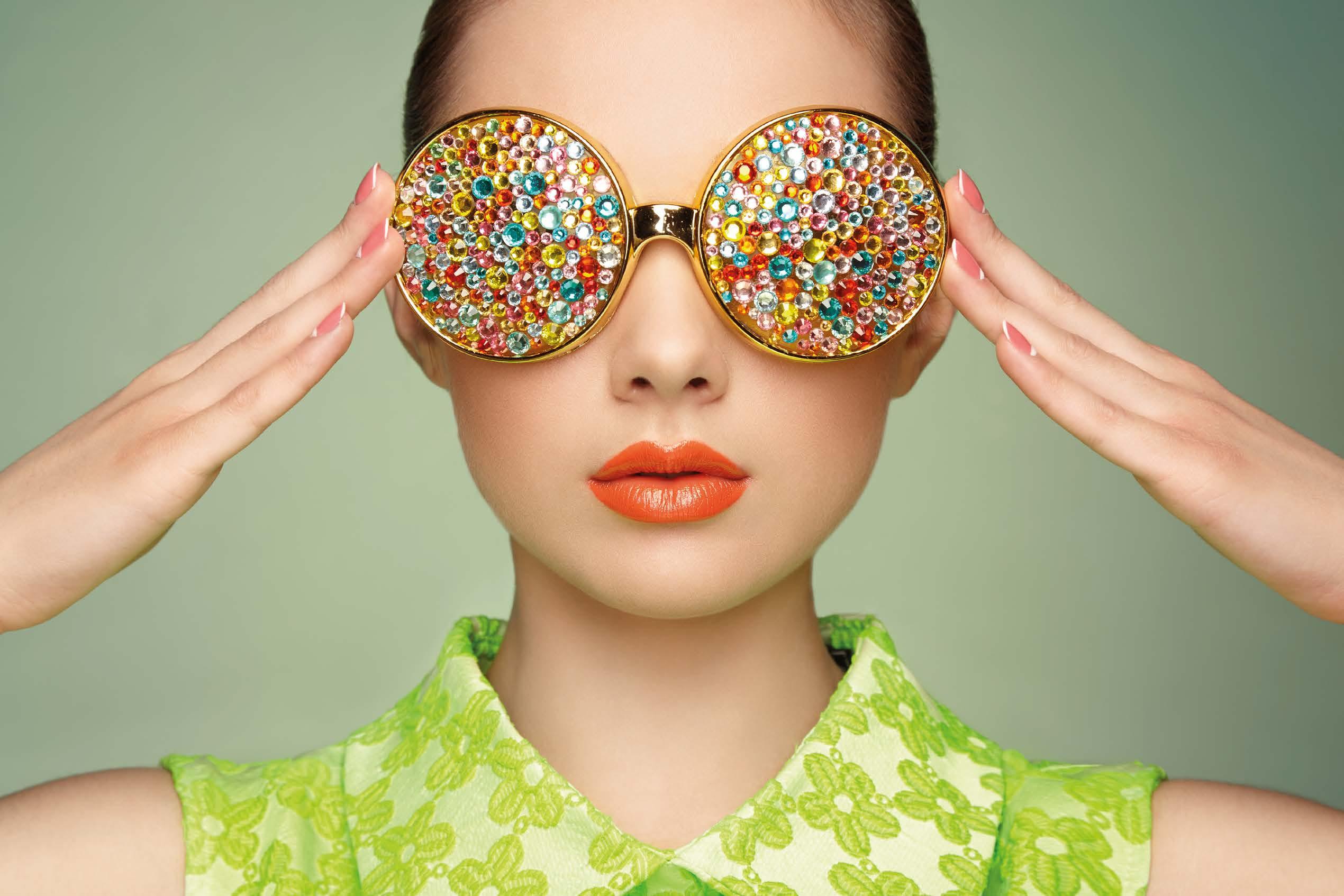