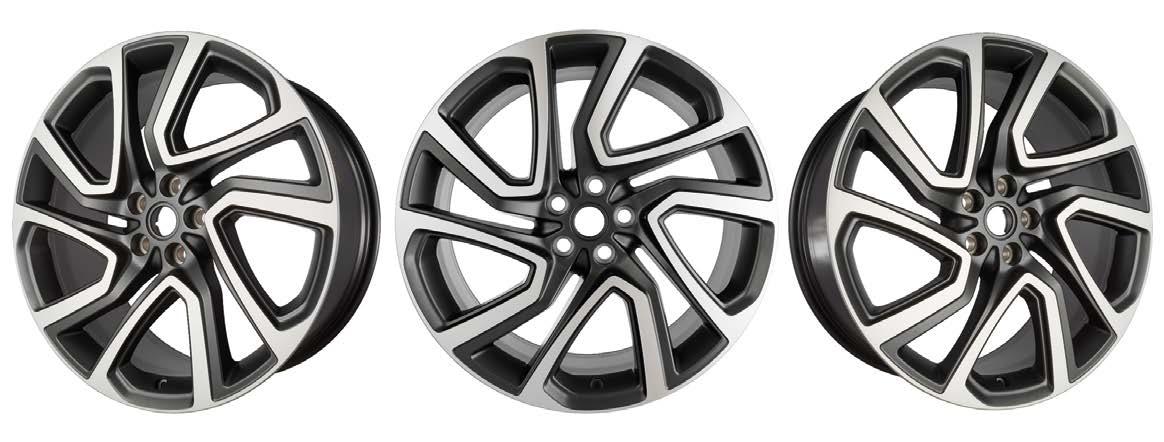
4 minute read
SPECIALIZED TRAINING
Alloy wheels manufactured by Maxion Wheels.
SPECIAL ISSUE ON AUTOMOTIVE
Investing in Training and Finishing Technologies with a View to Sustainability. Maxion Wheels Group’s Painting Training Course
Luca Armellin Maxion Wheels Italia Srl , Alessandro Soba and Andrea Minelli, Consultant New Business INP & Wheels Verind S.p.A.
© Maxion Wheels
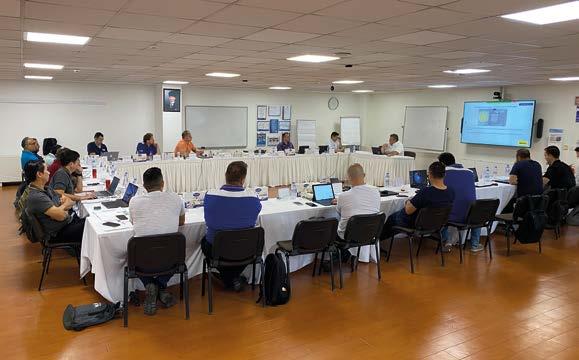
A Painting Training theoretical session in the classroom.
An industrial process can be analysed in terms of energy, efficiency, and environmental friendliness with a technological approach aimed at minimising raw material consumption while improving overall energy balance and thus waste and costs. Wheel painting, in particular, is a surface treatment operation that demands aesthetic excellence and the high chemical/physical quality of the applied coating. It is the final stage in the production process of an alloy wheel and it impacts the environment in terms of emissions, creation of special waste, and water pollution. Moreover, it is one of the most energy-intensive stages of the overall production process. Reducing energy consumption is actually a driver of economic development: technological innovation and sustainability are two key elements in every development plan. With this in mind, innovative engineering choices are now being made more and more often for
highly productive and environmentally friendly coating lines, with the aim as follows: • Reducing the energy consumption of individual processes • Reducing consumption of products and raw materials used • Reducing liquid and gaseous discharges • Increasing efficiency and quality • Reducing global CO2 emissions • Optimising the cost per unit produced • Integrating automation and digitisation • Increasing efficiency through flexibility.
In an increasingly competitive context, reducing one’s environmental impact and achieving ever more energy-efficient processes are therefore the biggest challenges of our time. Combined with OEM customers’ expectations for ever higher levels of finishing quality, the advent of Industry 4.0 calls for constantly higher sophistication of production processes, with a particular focus on coating systems. This also means that process engineers are required to have everincreasing levels of expertise and the ability to master topics and technologies that span more and more differentiated fields.
Painting Training for excellence in wheel finishing
Maxion Wheels, a division of IOCHPE-MAXION, is a world leader in the production of aluminium and steel wheels with production facilities worldwide. Having always firmly believed in training its technical staff, it brought together twenty of its best engineers and paint technicians from all over the world for an all-round training event at its plant in Turkey, in June. Using the different coating process phases as a common thread, from wheel inspection before loading to the final check to ensure compliance with customer requirements, thirty-five specific training sessions alternated with seven practical sessions held on the host plant’s painting systems. Over two whole weeks, speeches were given by Maxion specialists, paint and chemical suppliers, and top industry partners with whom the Group has been long collaborating. Each presentation brought up new products, solutions, developments, and technologies to give Maxion’s process engineers and technicians the opportunity to see all the latest possibilities and solutions available on the market. The event was also an excellent opportunity to focus on the pursuit of two important goals: continuous improvement of coating plants’ efficiency and reduction of waste and environmental impact, an issue on which Maxion places great emphasis.
Innovative ecotechnologies and digitalisation in the wheel finishing process
VERIND, belonging to the international Dürr Group, is one of the


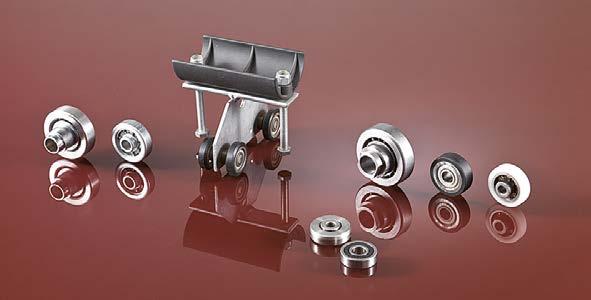
© Maxion Wheels
© Verind
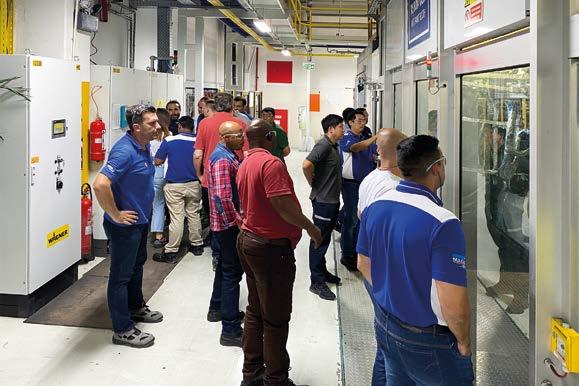
© Verind industrial partners that actively participated in Maxion’s Painting Training course. Through innovation and applied research, the Dürr Group has been developing important technologies for the automotive sector and the wheel market, which were presented and explained during the training sessions in Turkey.
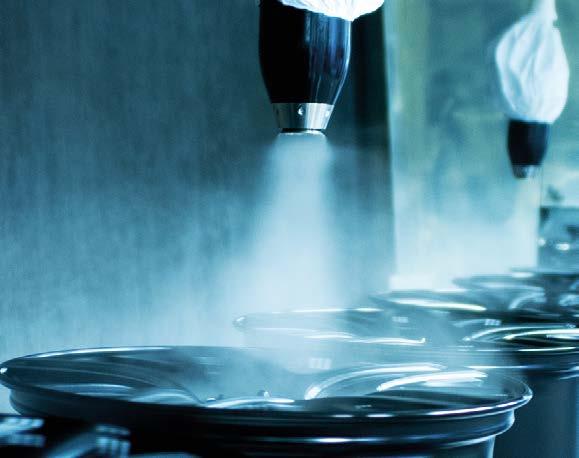
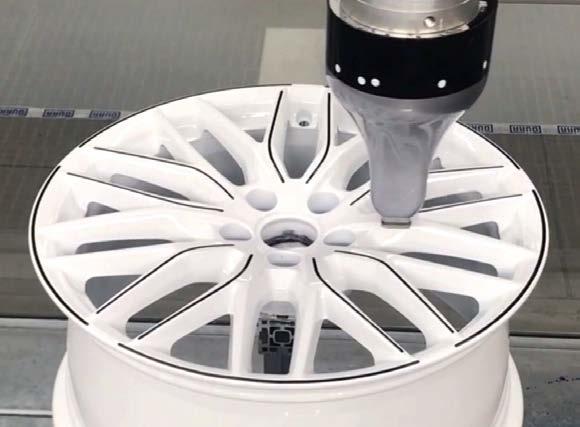
EcoBell electrostatic technology It allows saving paint in high-quality and high-productivity processes thanks to the electrostatic effect, which ensures high transfer efficiency values.
EcoSupply P technology It allows saving paint and cleaning products in production lines where frequent colour changes are required. Unused paint in the pipes is recovered in the paint drum and reused.
EcoPaint Jet - OFA (Overspray Free Application) technology It allows saving paint in production lines devoted, for example, to two-tone surfaces. It eliminates overspray and the need for masking operations and it reduces process energy consumption.
Digitalisation of the coating process with DXQ The goal is to apply efficiency measures at all phases of the coating process to systematically increase productivity, reduce unit costs while maintaining the highest quality, and improve sustainability. Integrating expertise in information technology and factory mechanical engineering enables to develop digital solutions for highly optimised industrial production processes. DXQ is a powerful industrial tool offering solutions for the operation, analysis, and control of modern industrial plants. It allows large volumes of data to be processed and analysed to streamline operations, thus guaranteeing optimised energy consumption, higher production rates, and smart spare parts ordering to minimise the impact of preventive maintenance. In a word, it allows operators and maintenance technicians to interact efficiently with the paint shop’s equipment.
From top to bottom:
Engineers and process technicians during a practical demonstration session.
Two of the Dürr technologies demonstrated by Verind during the Painting Training course: the EcoBell atomiser and the EcoPaint Jet-OFA system.
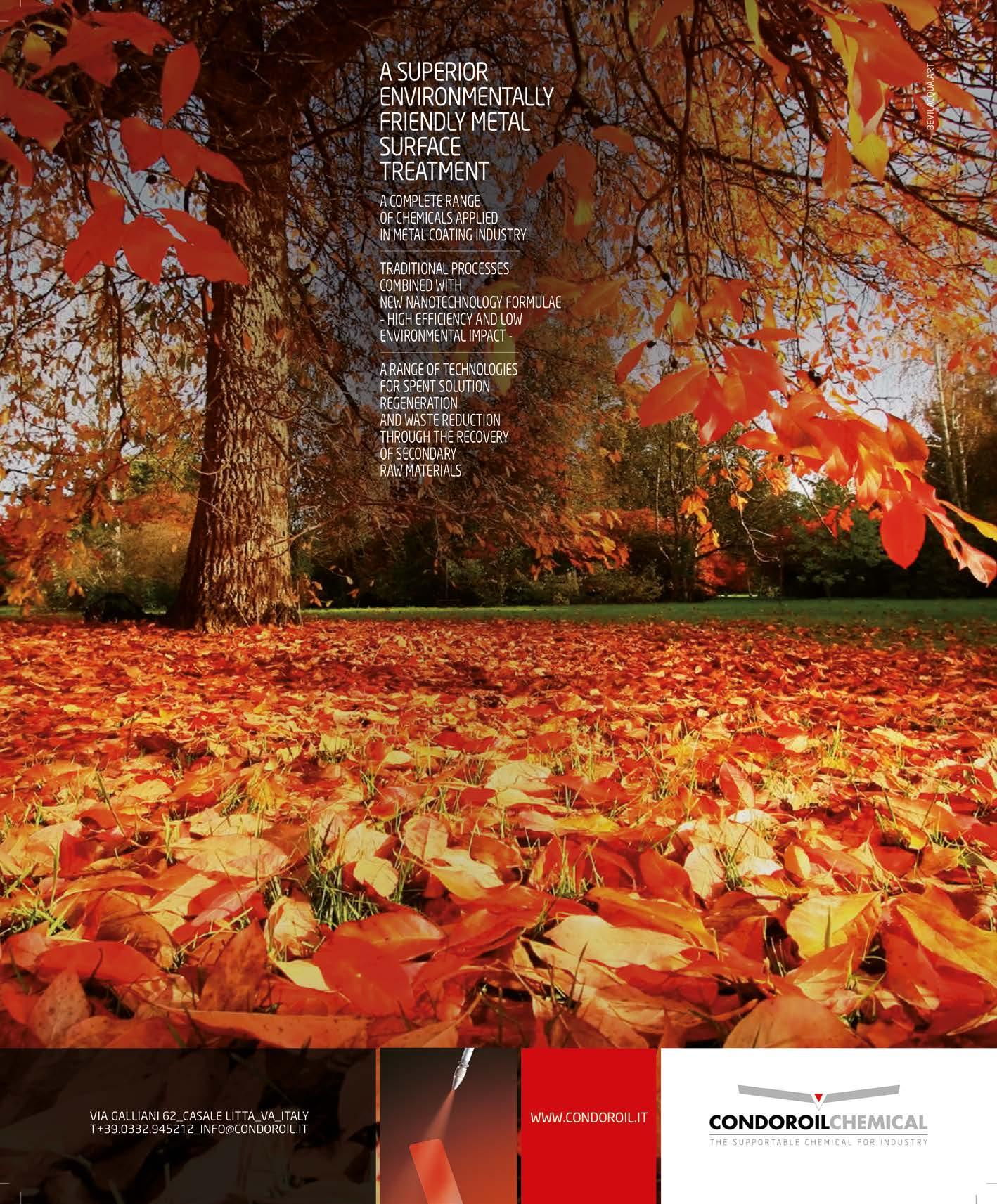