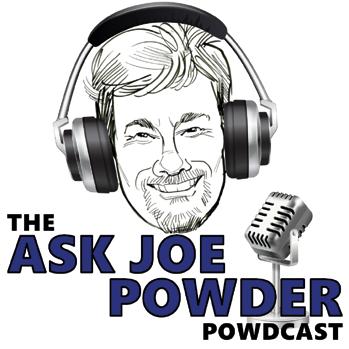
5 minute read
ASK JOE POWDER
La rubrica “Chiedi a un esperto”
Kevin Biller
kbiller@chemquest.com
Il nostro esperto di verniciatura a polvere è tornato per rispondere alle domande sempre più impegnative dei lettori.
Ciao Joe, Mi chiamo Richard Stange e lavoro come ingegnere meccanico presso un importante costruttore in California. Ho appena letto il tuo articolo pubblicato nel 2017, “Cambiamento tecnologico: scegliere una vernice in polvere durabile per esterni”. Ho trovato il tuo articolo molto istruttivo e sento di avere una migliore comprensione dell’argomento. La nostra azienda progetta e produce apparecchiature per l’irrigazione, che includono telai e piedistalli in metallo rivestiti con vernici in polvere per esterni, venduti in tutto il mondo. Abbiamo più fornitori di lamiere che si affidano a diverse aziende di verniciatura a polvere conto terzi. Di recente abbiamo scoperto che quest’ultimi non utilizzano la stessa chimica. Alcuni usano una formulazione a base di poliuretano, mentre altri usano una formulazione a base di poliestere-HAA. Dal tuo articolo, sembra che le chimiche industriali e ad alte prestazioni siano ciò che stiamo cercando per il nostro prodotto per conferire resistenza ai raggi UV. La mia domanda è la seguente: la resistenza ai raggi UV nelle vernici in polvere è data soltanto dalla presenza di poliestere-HAA o di poliuretano, oppure viene aggiunto un ulteriore “inibitore UV” nella formulazione? Sto cercando di determinare come specificare al meglio la resistenza ai raggi UV per la verniciatura in polvere nei miei progetti. Ti ringrazio per l’aiuto e attendo un tuo riscontro. Cordialmente, Richard Stange San Marcos, California
Ciao Richard, Grazie per aver letto il mio articolo e sono felice che ti sia stato di aiuto. La durabilità ai raggi UV è principalmente influenzata dalla resina primaria contenuta nella formulazione del rivestimento in polvere. Sia la chimica poliestere-HAA sia quella poliuretanica hanno un polimero di poliestere come componente principale del legante. I polimeri di poliestere possono essere di qualità per esterni standard (durabilità in Florida di 1-2 anni) o di qualità “superdurabile” (durabilità in Florida di circa 5 anni). Per i tuoi prodotti, ti consiglio di richiedere la qualità “superdurabile”. Sarebbe ancora meglio richiedere una polvere di qualità AAMA 2604 (American Architectural Manufacturers Association) o Qualicoat Classe 2. La specifica 2604 richiede 5 anni di durabilità in Florida e la Qualicoat Class 2 richiede 3 anni di durabilità in Florida. Ho allegato copie di queste specifiche. Per quanto riguarda i formulatori che utilizzano additivi speciali per migliorare la durabilità all’esterno, le prestazioni intrinseche si basano su due fattori: utilizzare nella formulazione della vernice in polvere solo ingredienti (materie prime) resistenti ai raggi UV e non incorporare alcun anello debole della catena o agenti dannosi (tra cui cere o riempitivi). Gli additivi speciali non fanno una grande differenza, specialmente nelle vernici in polvere pigmentate. Spero di esserti stato di aiuto. Fammi sapere se hai altre domande. Cordiali saluti, Joe
Ciao Joe, Abbiamo sviluppato nuovi polimeri per vernici in polvere. Una delle proprietà essenziali è la resistenza agli urti. I risultati dei nostri test sono stati contraddittori e variano in modo significativo a seconda del substrato utilizzato. In alcuni casi il rivestimento supera i 160 pollici-libbre (18.0776 Nm) e con altre condizioni ottiene solo 80 pollici-libbre (9.038 Nm). Quale potrebbe essere la causa di questa variazione? E come possiamo eliminare questi cambiamenti? Grazie! Rebekah Philadelphia
Ciao Rebekah, Innanzitutto complimenti a te e ai tuoi colleghi per lo sviluppo di nuovi polimeri. La maggior parte dei progressi nella tecnologia delle vernici in polvere si basa su polimeri nuovi e migliorati. È difficile per noi formulatori creare nuovi rivestimenti senza polimeri innovativi. Il metodo di prova di resistenza all’urto più comune è descritto nell’ASTM D-2794 Standard Test Method per la deformazione rapida dei rivestimenti organici (impatto). Lo standard ISO-6272-1 copre lo stesso
metodo di prova. I valori tipicamente citati nella resistenza all’impatto sono in pollici-libbre (Newton-metri per coloro che utilizzano il sistema metrico) e si riferiscono al peso moltiplicato per la distanza (altezza) dell’impatto. Un altro parametro è il raggio della sfera che colpisce la superficie del rivestimento. Il Nord America utilizza in genere una sfera di 5/8 pollici (15,9 mm) di diametro, sebbene alcune specifiche richiedano una sfera da ½ pollici (12,7 mm). Minore è il diametro, maggiore è la deformazione e quindi minore resistenza agli urti. A parte la flessibilità intrinseca del rivestimento, il substrato ha l’influenza più significativa sulle prestazioni del film. L’adesione è influenzata dal tipo di metallo, dal profilo della superficie, dalla pulizia e dal pretrattamento. Conseguentemente la resistenza all’impatto è influenzata dall’adesione, quindi un substrato scarsamente pretrattato causerà un cedimento imprevisto. D’altra parte, un metallo ben pretrattato migliorerà la resistenza agli urti creando un legame solido tra la polvere e il substrato. Oltre alla preparazione del metallo, lo spessore e il tipo di substrato influenzano notevolmente la resistenza agli urti a causa del grado di deformazione del substrato. Quindi 80 pollici-libbre su un grado duttile di alluminio avranno una deformazione diversa rispetto all’acciaio al carbonio. E certamente, anche lo spessore del metallo influenzerà la deformazione e quindi la resistenza agli urti. Il metallo con uno spessore maggiore si deformerà meno e quindi il rivestimento subirà meno sollecitazioni. I parametri del rivestimento da controllare sono principalmente lo spessore del film e il grado di polimerizzazione. I film più sottili tendono a mostrare una maggiore resistenza agli urti mentre quelli più spessi sono più fragili. La polimerizzazione completa è altamente raccomandata poiché le polveri poco polimerizzate di solito mostrano una minore resistenza agli urti. Assicurati che il tuo rivestimento riceva il tempo a temperatura specificata dal fornitore del rivestimento. Quando si formula un rivestimento per la resistenza agli urti, la sfida consiste nell’utilizzare substrati rilevanti per il mercato di destinazione. Per usi finali industriali generici, l’acciaio laminato a freddo è comune, mentre il settore architettonico utilizza solitamente varie tipologie di alluminio a seconda della fabbricazione e dei requisiti di prestazione. Inoltre, il tipo di pretrattamento è importante. L’acciaio laminato a freddo viene solitamente pretrattato con un fosfato (ferro o zinco) o nelle installazioni più recenti con un prodotto a base di zirconio. L’alluminio è tipicamente pretrattato con cromo, zirconio o talvolta fosfato di zinco. Per lo sviluppo del polimero ti suggerisco di procurarti il tuo substrato da un fornitore affidabile di pannelli di prova. Un elenco di essi è disponibile sul sito web PCI (www.powdercoating.org) sotto “Members”. Buona fortuna per i tuoi sforzi nella chimica dei polimeri, l’industria ha bisogno di te. Cordiali saluti, Joe
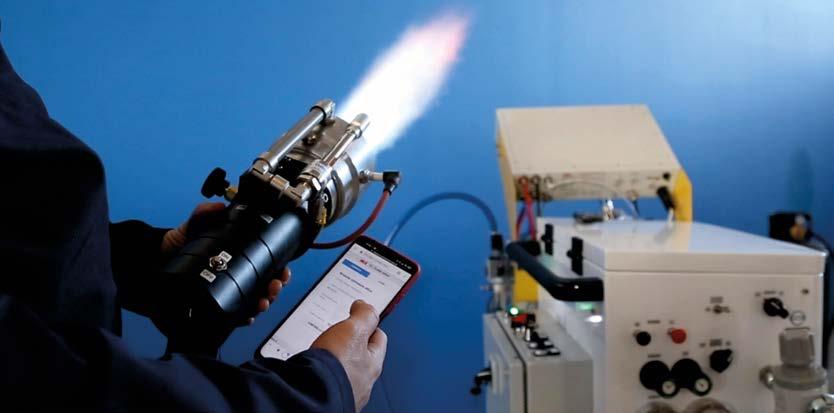