
23 minute read
FOCUS ON TECHNOLOGY
VAFE Celebrates 60 Years in Business with a New Horizontal Coating Line for Architectural Profiles, Sheets, and Accessories. Productivity is Improved Through Smart Conveyor and Plant Design
Alessia Venturi, ipcm®
Any contractor worthy of its name has one mission: meeting all customer requirements without ever stopping its production line. This is all the more imperative for coating contractors, especially those operating in a market requiring quality excellence, namely that of architecture. VAFE has found the technological tool to live up to this mission in a horizontal coating plant designed by Omsa, Futura Convogliatori Aerei and Gema. Thanks to independent transport circuits with different chain speeds, automation 4.0, a cellular pre-treatment tunnel, and two curing ovens (one for each booth), this line guarantees high productivity without ever stopping, extreme flexibility in terms of both treatment and part type, and high coating quality.
“We know who we are and what we can offer.” These few words from Giampiero Gritti encapsulate the key to the success of VAFE Srl, a contract coating company based in Grassobbio (Bergamo, Italy) specialising in the painting of special and non-standard metal sheets and profiles for metal architecture. “Our finishes remain on the surface, but our expertise goes deeper” is the motto of this firm, which over the years has gradually implemented a wide range of treatment and coating cycles capable of meeting any requirement of the architectural sector, as well as gaining all the necessary certifications, qualifications, and approvals to work in this demanding, multifaceted, and sometimes whimsical sector. VAFE turned 60 years old in 2022: founded by the grandfather of the current generation (the third one) at the helm of the company, it has been operating in the field of industrial metal pre-treatment and coating in Italy and Europe since 1962. From its original site in a “chicken coop” in the Upper Town of Bergamo, as Gritti put is, VAFE soon moved to Grassobbio, where it is still based today, implementing powder coating technologies right from their first appearance on the industrial finishing market. Today, VAFE offers high-tech treatments giving unrivalled aesthetic qualities and durability to structures, profiles, and components made of extruded, die-cast, and rolled aluminium, but also iron, Sendzimir iron, and galvanised steel. Over the years, it has gained all the qualifications and certifications needed to work for an international clientele: Qualicoat and Qualicoat Seaside for aluminium – it is the only company in Italy and among the few in Europe to have this certification for profiles up to 13 metres –, Qualisteelcoat for iron and galvanised steel up to corrosion class C5, and the approvals of all major Italian customers in the architecture and infrastructure sector. Taking over from his father at the reins of VAFE, Giampiero boosted the company’s development by conquering a niche of excellence within the metal architecture market, which is that of the finishing of special and non-standard profiles (up to 13 m in length and 8-10 kg/m2 in weight), cladding sheets for curtain walls, accessories, and square tubes for awnings, and even entering the design, lighting, automotive, and transport sectors. All industries in which finishing quality is held in very high regard, not only for aesthetic reasons but also with a view to functionality and resistance to weathering, ageing, and corrosion. Recently, Giampiero has handed the company over to his sons, Matteo and Francesco Gritti and his nephew Stefano Algeri, the third generation of the family, who are continuing to grow the business. They are the ones who, on the occasion of the 60th anniversary celebrations in July, explained to us the reasons behind VAFE’s most recent investment, the replacement of one of the existing coating plants for bars up to 8 metres long with a new state-of-the-art line designed by Omsa (Besana in Brianza, Monza e Brianza, Italy), Futura Convogliatori Aerei (Robecco Pavese, Pavia, Italy) and Gema Europe (Trezzano sul Naviglio, Milan).
© ipcm © ipcm
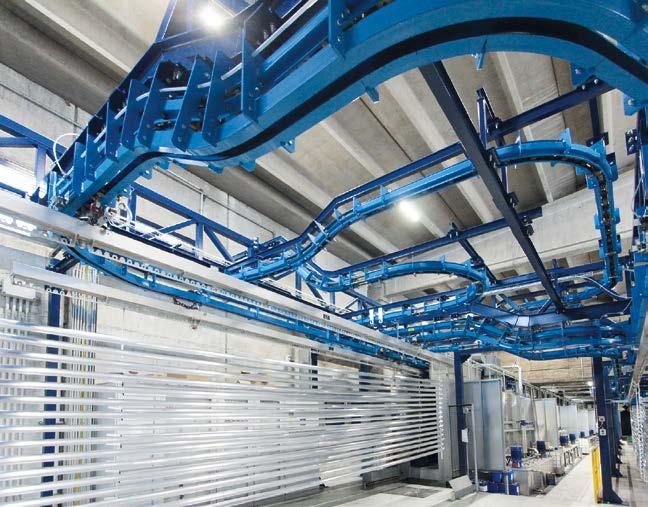
VAFE celebrated its 60th anniversary with an event involving partners and employees with their families, suppliers, and customers. Load bars entering the pre-treatment tunnel. The fast circuit independent of the main chain that takes the profiles along the pre-treatment tunnel is clearly visible.
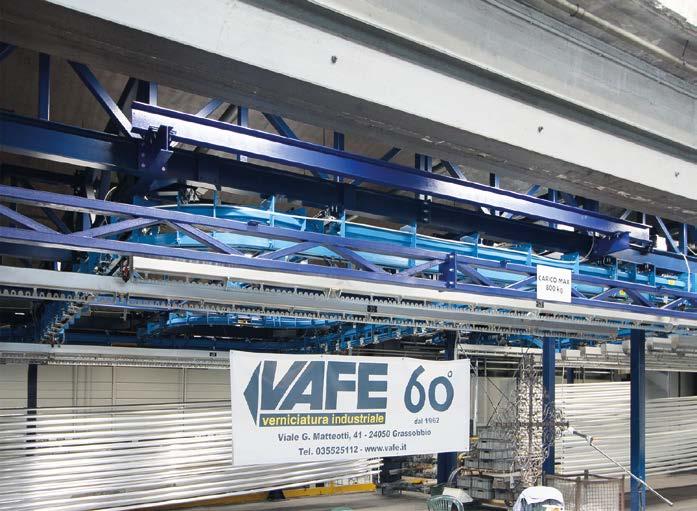
Opening photo: Coated profiles approaching the unloading bay of the new system installed by VAFE and designed by OMSA with a Futura conveyor.
© ipcm © ipcm
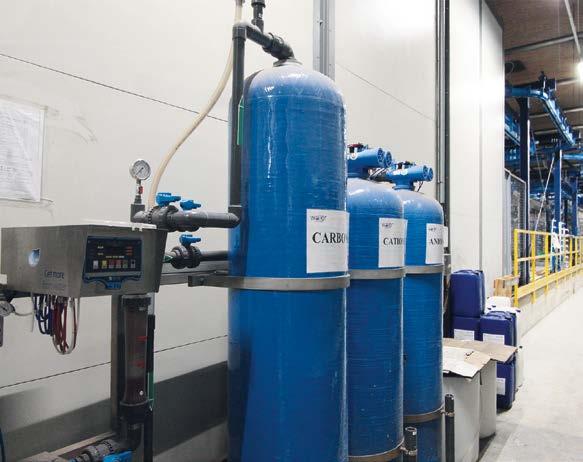
The pre-treatment tunnel and the demineraliser provided by WaterEnergy.

This fully automatic line is able to guarantee a very high productivity and such a flexibility degree that VAFE can meet any customer need and demand without ever stopping the plant, thus reaching excellence in contract coating. Let us see how.
Three coating plants for customised operations
With its three last generation plants, VAFE offers a wide range of treatment cycles that guarantee high-quality and durable results even for the most complex projects.
Horizontal coating plant for materials up to 13 metres
• maximum length > 13,000 mm • maximum height > 3,000 mm • maximum width > 1,500 mm • maximum load capacity > 3,000 kg
Horizontal coating plant for materials up to 8 metres
• maximum length > 8,000 mm • maximum height > 2,000 mm • maximum width > 450 mm • maximum load capacity > 800 kg
Vertical coating plant for materials up to 3 metres
• maximum length > 1,200 mm • maximum height > 3,000 mm • maximum width > 600 mm • maximum load capacity > 120 kg. The new plant created by the technical departments of OMSA and Futura replaced the existing line for treating materials up to 8 metres, which after thirty years of full use it was necessary to change with the new technologies on the market. “The project for this plant started about five years ago. My uncle Giampiero had realised that in order to differentiate itself within a market as varied as the contract coating one, in which there are companies of very different natures and with very different skills, VAFE had to stand out by offering a highly specific service with premium quality and flexibility levels. It was therefore strictly necessary to upgrade our ‘medium-sized’ plant handling materials up to 8 metres and devote it exclusively to architectural applications”. “This new plant has enabled us to improve productivity and quality – not only in terms of product quality, but also of work quality. The fact that it is structured in stages over several circuits independent of each other enables us to stop individual chains in the event of delays or changed needs at certain stages of treatment. Its design and automation characteristics optimise the time required by each process step, minimise the error rate because the operators do not have to ‘run after’ production, make the line speed constant, and ensure consistently high finishing quality,” adds Stefano Algieri.
Design features of the two-rail conveyor
“We have equipped this plant with a power&free conveyor with a maximum load capacity of 1 tonne (800 kg + the weight of the load bar) and several independent transport circuits,” says Stefano Gerletti, sales manager at Futura Convogliatori Aerei. “Design-wise, the most complicated aspect proved to be the need to fit a conveyor with such a
capacity and with 1 km of chain into a very small space within the VAFE factory. There are two loading bays, a main one for standard batches with a pre-load area (which allows the plant to be loaded at the end of the working day and given automatic one-hour operational autonomy for the following day, even unmanned) and a second, smaller one for out-of-standard parts, special products, and smaller volumes”. “In order to reach the maximum productivity allowed for this type of operations, we have equipped the conveyor with separate circuits with independent chains,” adds Gerletti. “In addition, we have mounted a 400 mm oscillator on each load bar to optimise drainage between one stage and another: the system unhooks the load bars from the fast chain and the oscillator comes into operation.” “The ingenuity of this plant’s design lies in the fact that, thanks to the various circuits with which its conveyor is equipped, the booths can work independently and the
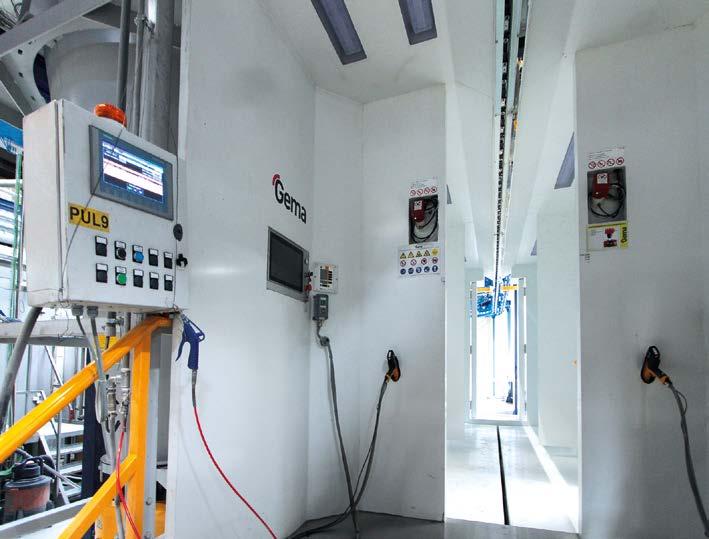
© ipcm
The MagicCompact EquiFlow BA04 booth.
SIMPLY STRIKING –powerful blue from every angle
Get to know the world’s first effect pigment with such a strong, highly chromatic dark blue. Thanks to ECKART’s patented anti-fading technology, EDELSTEIN Sapphire Blue retains this powerful color from any viewing angle.
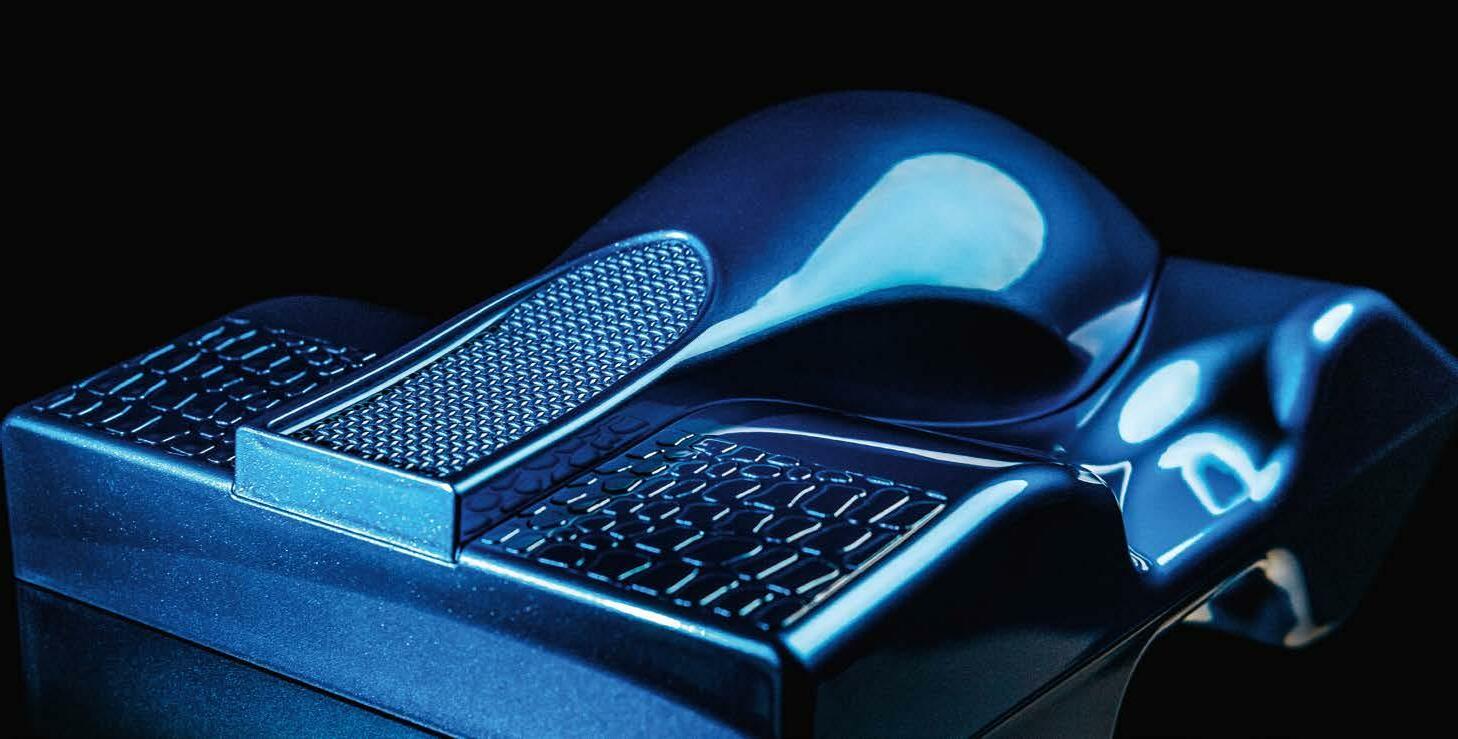
Contact us for more information:
ECKART GmbH · Guentersthal 4 · 91235 Hartenstein · Germany Phone +49 9152 77-0 · info.eckart@altana.com · www.eckart.net
© ipcm
© ipcm
The OC06 All-In-One powder centre.
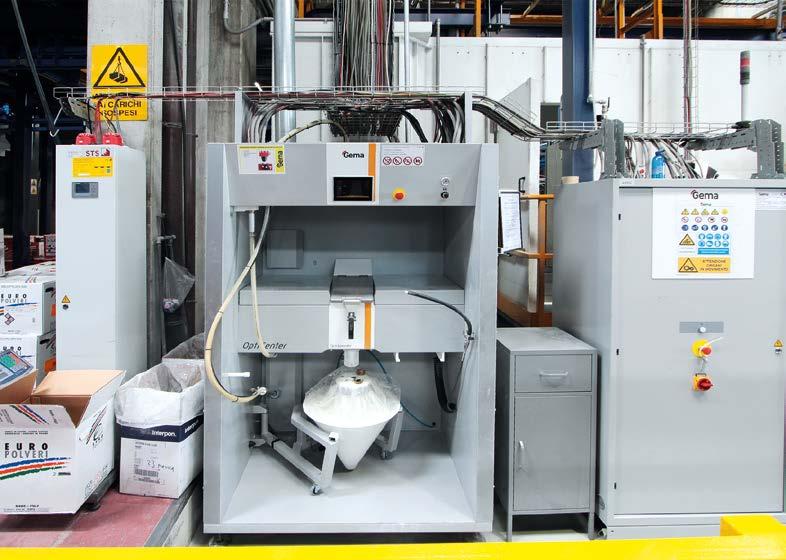
Perspective view of the conveyor switch system after the coating booths.
load bars can be recirculated in the same booth,” notes Stefano Algieri. “Each booth is equipped with its own storage buffer that allows two-coat systems to be applied without losing productivity. The same applies to colour change operations: the storage buffers created along the conveyor path, combined with smart production scheduling, give us extreme flexibility. This enables us to meet any customer requirement without ever reducing our productivity or stopping the line.”
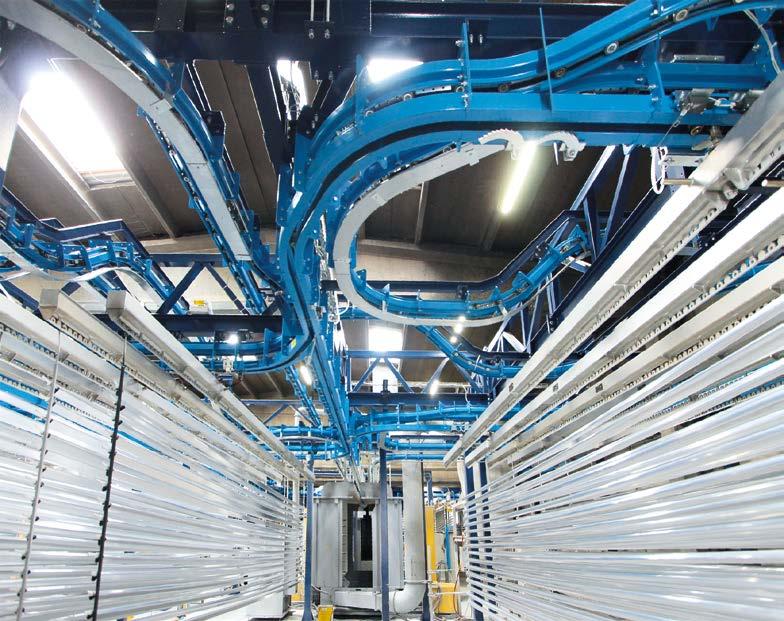
General characteristics of the line
The plant consists of a 7-stage pass-through spray pre-treatment tunnel with four cells (of which two, i.e. the rinse cells, are double), performing a final stage of norinse passivating product atomising. The cycle is both Qualicoat and Qualisteelcoat certified as all active baths (alkaline phosphodegreasing, acid deoxidation, and final conversion) can use different chemicals depending on whether the material being treated is aluminium or iron/galvanised metal. “The plant management software package performs a product switch according to the recipe selected during loading,” explains Gilberto Riva from Omsa’s technical sales department. “The line continues with a drying oven with an air vein exchanger, two automatic powder application booths, and a gelling oven and a curing oven, both with an indirect heat exchanger. Each of the two ovens is assigned to a spray booth; in particular, the gelling oven is used to gel primers in the case of two-coat finishing cycles (and thus prevent the part to pass through the booth twice) and small colour batches. Booths and ovens can work simultaneously.” The coating booths use conventional Venturi application technology on the reciprocators and dense phase technology on the manual touch-up units.
© ipcm
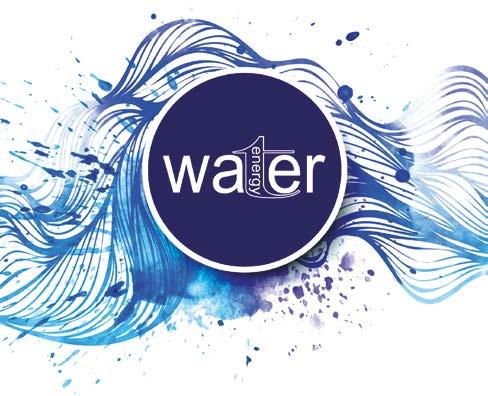
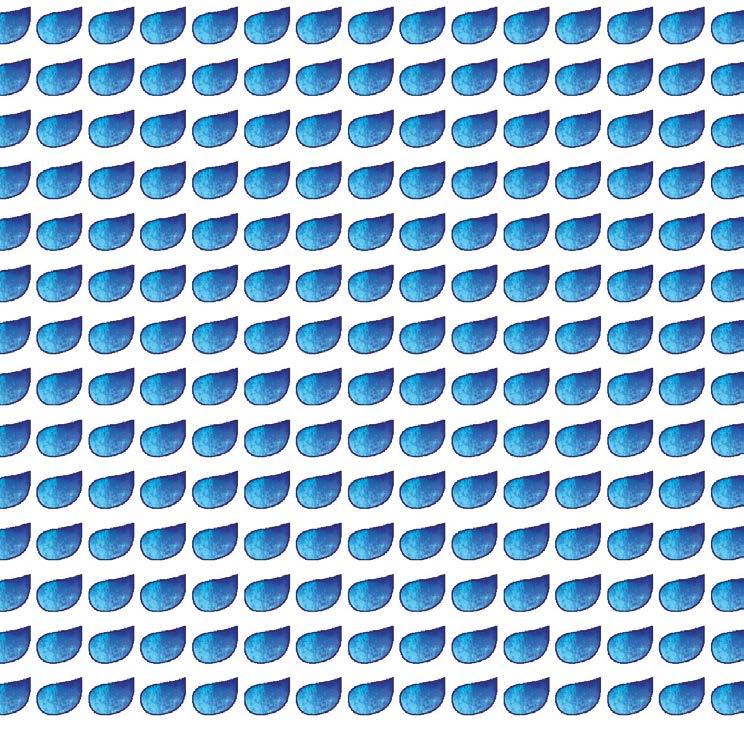
The storage buffers located by Futura along the two-rail conveyor.

“We have two booths: one was revamped with Gema’s Venturi equipment and the second is a new MagicCompact Equiflow booth also supplied by Gema and linked to the latest OptiCenter OC06 All-In-One powder centre,” explains Francesco Gritti. “We decided to adapt the application technology of the new booth, and we chose the updated All-in-One device, based on the Venturi system, which guarantees higher performance and application speed. Indeed, after various comparative tests that I have personally carried out, I found that the dense phase with the OptiSpray AP01 application pumps was crucial in eliminating the Faraday Cage effect in manual touchup operations, resulting decisive for some particularly complex products”.
Industry 4.0
Futura and Omsa co-developed the management software package 4.0 for VAFE’s line. “All orders are uploaded into the management system and each of them is assigned a code containing the type of paint, the treatment cycle, and the curing time,” explains Stefano Gerletti from Futura. “The loading and unloading stations are equipped with two panels where the operators can enter the load bar’s code either with a bar code gun or manually and select the required process from the PC. The load bar enters the line and, from then on, it is subjected to the entire process flow matching with the information assigned to it. Human error is reduced to a minimum, as the operator can only make a mistake in selecting the process, a detail that is however
Get more from water
Turn key solutions for industrial wastewater treatment Design and manufacturing of plants and chemicals for industrial wastewater treatment Chemical-physical plants Sludge treatment and compactor systems Ion exchange demineralization systems and reverse osmosis systems Oil separators Filtering systems Batch type systems Flotation units Chemicals and spare parts for water treatment Technical service, support and maintenance of wastewater treatment plants
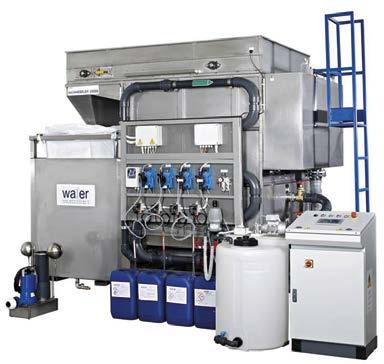
Beware of imitations, buy the original!
© ipcm
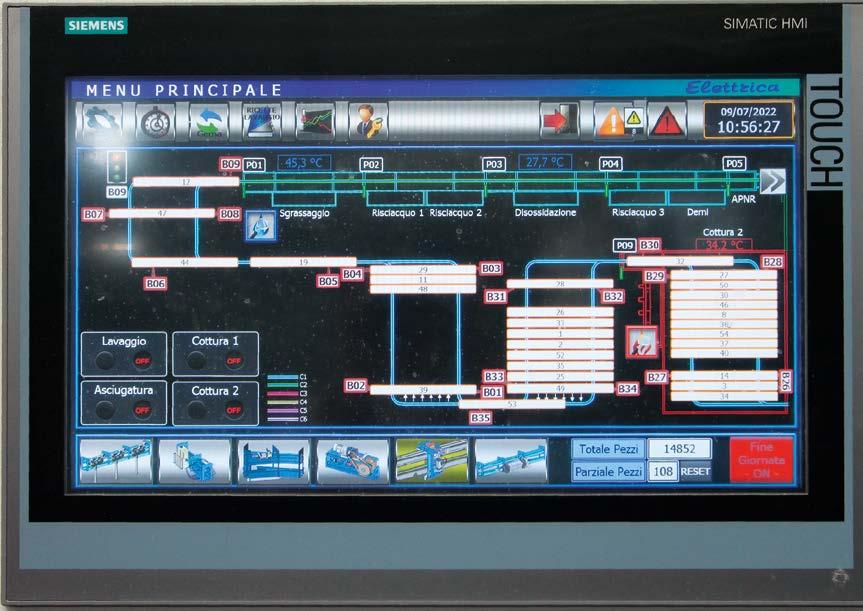
The plant’s control panel.
checked repeatedly during the whole workflow. In front of the pretreatment tunnel, the Futura software programme ‘hands over’ the code to the OMSA programme, which continues to process the part based on the information assigned to it. The same happens in front of the curing ovens. It is possible to follow the position of each load bar on the touch panel through the shift register (the virtual tracking system). Clicking on an individual load bar opens a further window containing all information related to it.”
A much-needed investment
“Thanks to the investment in this plant, not only have we increased our production capacity and achieved a high level of flexibility, but we can also investigate and correct, in real time, any problems that arise during treatment,” states Matteo Gritti. “Flexibility is the aspect that has pleased us the most because we are heavily focussing on two-coat painting cycles,” indicates Stefano Algieri. “We apply numerous two-coat systems on products made in outdoor iron and Sendzimir iron, which consists in pre-galvanised sheets that have no real edge protection. However, we also recommend their use on aluminium, for example for products intended to be installed on the seafront: where the budget allows, we prefer to combine Qualicoat Seaside-level protection with primer application.” “We can therefore be very satisfied with this investment. It was just what we needed to further develop VAFE’s market,” summarises Francesco Gritti. “We are also pleased with the work of our suppliers, in terms not only of technologies installed but also of the level of the service offered and the way they support us.”
© BT Group
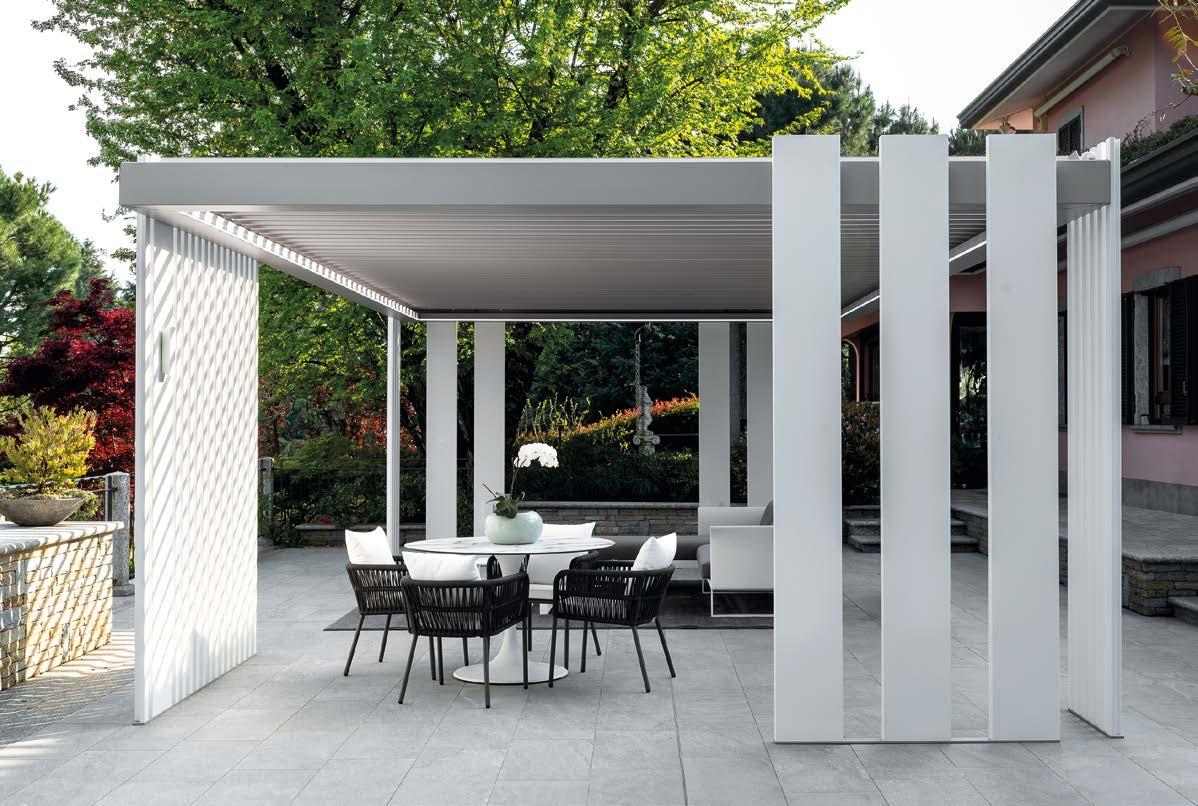
A pergola from the CODE range entirely built and coated by BT group.
FOCUS ON TECHNOLOGY
SPECIAL ISSUE ON ALUMINIUM
Total Customisation of Aluminium Outdoor Structures for Sun Protection: BT Group’s Challenge
Gabriele Lazzari, ipcm®
BT Group has become a market protagonist in the Italian and international pergola and awning sector thanks to the flexibility of its production and the high customisation degree of its offer. The increase in demand that the sun protection industry has seen in recent years has enabled it to expand its operations with a new automatic powder coating plant designed, built, and installed by Silvi in collaboration with Futura, Chemetall, and Wagner.
©ipcm
The two standard colour palettes offered by BT Group.

After closing 2018 with a turnover of 1,244 million Euros, Pambianco, a consulting company operating in the luxury sector, reported that the Italian awning and pergola industry saw an increase in turnover and profit margins in the following years as well1 . Federlegno Arredo also disclosed that demand further increased immediately after the lockdown periods, as confirmed by BT Group, a multinational group based in Lesmo (Monza e Brianza, Italy) and active in the production of outdoor domestic sunscreen structures. This firm was founded in 1954 by Ambrogio Radaelli in Monza, whose province is firmly rooted in traditional craftsmanship. Over the years, it has expanded its production, the types of solutions, and the degree of customisation offered to its customers, managing to serve not only the Italian but also the international market. “BT Group has become a market protagonist in the sun protection industry thanks to its production flexibility. Our awnings, pergolas, and bioclimatic awnings are in fact the ideal extension of any home’s interior and they must therefore be able to meet all kinds of needs: customisation does not only concern colours and finishes, but also dimensions, shapes, movement mechanisms, and accessories,” states BT Group CEO Andrea Radaelli. “The COVID-19 pandemic has dramatically increased demand, as the general public has realised that our products are a great solution for living outdoors without leaving the comfort and security of one’s own house.”
1https://design.pambianconews.com/fatturati-in-aumento-per-i-big-dei-sistemi-diprotezione-solare/ In order to cope with such an increase in orders, the company turned to Silvi Srl (Peregallo di Lesmo, Monza e Brianza) for the design, construction, and installation of a new coating system that would allow it to speed up production without sacrificing product quality.
Fully customised production and finishing
BT Group deals in-house with the whole design phase, always remaining in close contact with customers to offer the highest possible level of customisation. The raw extruded aluminium profiles and all the other components used to build the structures of the company are acquired by Italian suppliers. “We still use some plastic components but, since the market is shifting towards more environmentally friendly solutions, we are trying to replace them with aluminium parts that are die cast. This new trend is an advantage for us, as our group includes the foundry Form, specialising in the moulding of aluminium and zamak,” indicates sales manager Alessandro Citterio. “Profiles are acquired raw and then cut to the required size and subjected to machining using state-of-the-art CNC systems in our light metalwork department. The parts are finally sent to our finishing department.” “The coating process is the most important phase of our entire production cycle,” says plant manager Luca Grazzi. “In addition to often being the first aspect that customers notice, finishes are also the
©ipcm
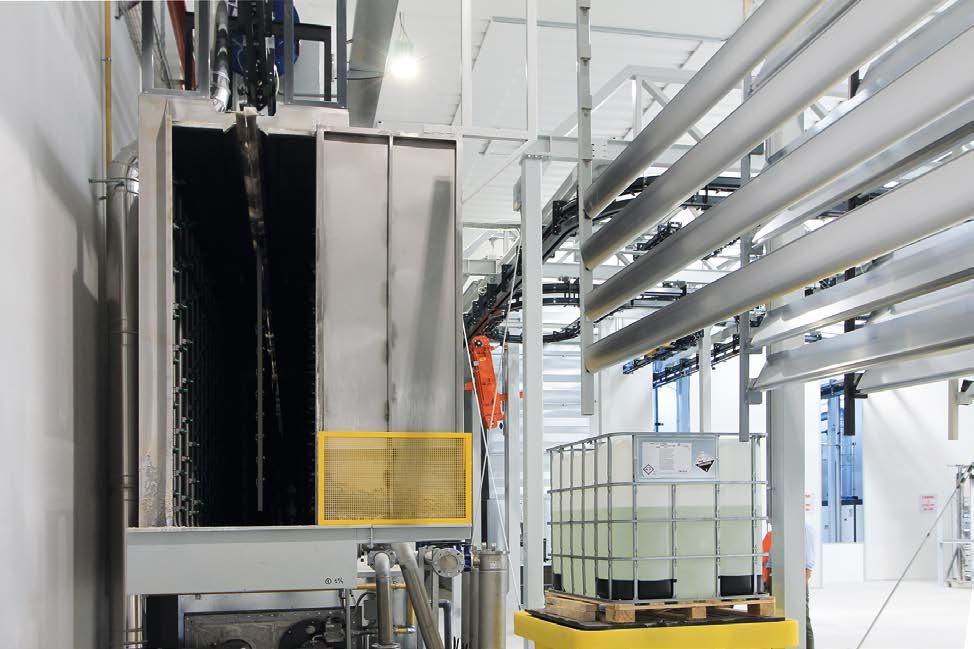
The entrance to the pre-treatment tunnel performing the process developed by Chemetall.
element about which we may receive the most quality complaints, due to constant handling, transport, and assembly operations on site.” BT Group offers its customers numerous tints from two different colour palettes: one includes matte RAL colours with a slightly textured finish, whereas the other includes several metallic colours. “The most popular shades are white, which accounts for 40% of our production, and grey and brown shades with a textured finish, which create a beautiful aesthetic effect. However, in the awning sector glossy shades are still highly requested, especially white, ivory, and 7035 grey,” explains Citterio. “As already mentioned, flexibility is our main strength. Therefore, we can also utilise powder coatings personally selected by our customers, provided they meet all our quality requirements. Our products are certainly going to be exposed outdoors, but in the case of some orders, we do not know in depth the environmental characteristics of the place where they will be installed and the degree of corrosion to which they will be subjected. This is why we always comply with the quality standards of the QUALICOAT class 2 certification and we apply polyester powder coatings, as they guarantee greater resistance and better penetration even on complex-shaped parts,” notes Grazzi. The need for a new powder coating plant
BT Group already owned a coating plant installed at the beginning of the century in its long-standing factory in Lesmo. Intended for coating bars, die-cast parts, and iron frames, it was subsequently upgraded by Silvi itself. However, as demand increased, soon the company was once more no longer able to cope with the new production volumes. It initially turned to a few coating contractors, but even they could not guarantee that the required delivery time would be met. BT Group therefore decided to invest in a new coating line. “We were, and still are completely satisfied with the performance of the system revamped by Silvi. In addition, we visited the plants of other coaters to better understand the advantages and disadvantages of other painting technologies. This is why, after an initial analysis phase, we decided to once again entrust Silvi with the design of the new plant. At the same time, we acquired a plot of land on which to build the new paint shop and a warehouse to store our bars,” adds Citterio.
The pre-treatment cycle
The new plant installed by the company has a large loading area, the starting point of a power&free conveyor built by Futura Convogliatori.
©ipcm
The inside of the spray pre-treatment tunnel.

Made entirely of stainless steel, the spray tunnel is configured in stations separated by doors to guarantee a more efficient process and avoid contamination among baths. All spraying bars are equipped with special filters, typical of cataphoresis tanks, to improve the application of the treatment solutions. The tunnel is completed by two 3,000-litre recirculation demineralisers for the production of demineralised water, which is then sent to a storage tank, and a 12,000-litre vacuum evaporator to treat waste water. These make the line a “zero liquid discharge” plant. “During the design phase of the new plant,” says Andrea Monti, the technical coordinator of the Surface Treatment global business unit of BASF’s Coatings division, operating under the Chemetall brand, “we analysed BT Group’s requirements and, together with them, we chose a pre-treatment cycle with the Oxsilan® thin-film hybrid nanotechnology solution, which combines the corrosion-
©ipcm
©ipcm
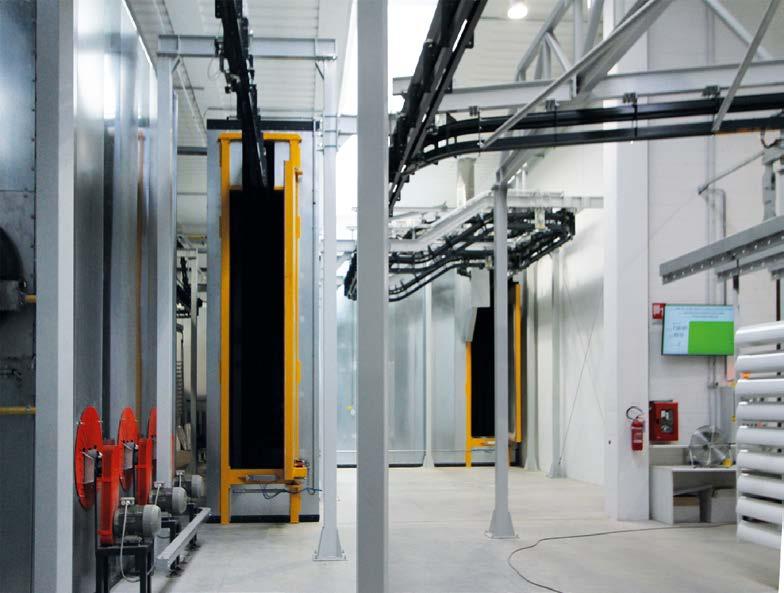
The conveyor entering the drying oven (above) and the storage buffer with the Futura conveyor.
inhibiting properties of inorganic metals such as zirconium with the flexibility provided by silanes. It is the same solution used in the first plant ever since it was revamped to replace the hexavalent chromium-based process. While it is true that some QUALICOAT Class 2 paints presented adhesion problems in the past, the inorganic polymer elements of Chemetall’s technologies help solve them. In this way, the profiles’ surfaces are prepared for the application of the several different coatings used by BT Group.” The pre-treatment cycle consists of ten stages. It starts with strong alkaline pickling to degrease and deoxidise the profiles in order to eliminate the “deformation layer” formed during extrusion and eliminate any organic contaminants. After two rinses with mains water, a multimetal acid degreasing stage is carried out to complete dissolution of the alloying elements resurfaced due to the removal of the “deformation layer”, which could cause filiform corrosion. This is followed by a further rinse with mains water to remove the metal residues detached by the previous steps and one with demineralised water, which eliminates the metals contained in the mains water and prepares the profiles to enter the nanotechnology conversion chamber. Finally, after a second rinse with demineralised water, the conveyor’s tilting system returns the load bars to the horizontal axis and takes them to the drying oven with an indirect flame heater operating at 120-140 °C.
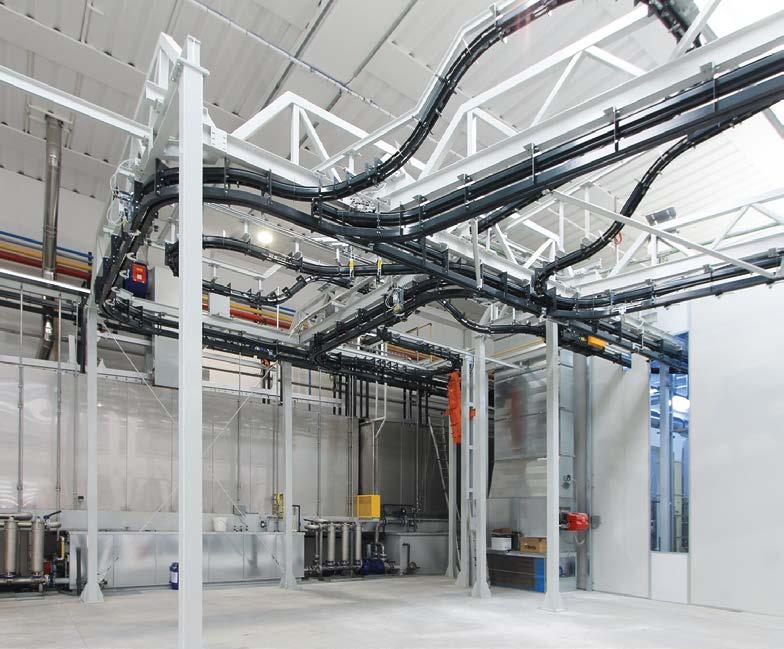
High-quality coating with 15 colour change operations per shift
On leaving the drying oven, the overhead conveyor directs the load bars towards one the two automatic coating booths supplied by J. Wagner GmbH, one applying light colours and the other dark colours, both placed in a pressurised and air-conditioned clean room with a constant temperature of 25 °C in order to prevent contamination. Each booth is equipped with two opposing
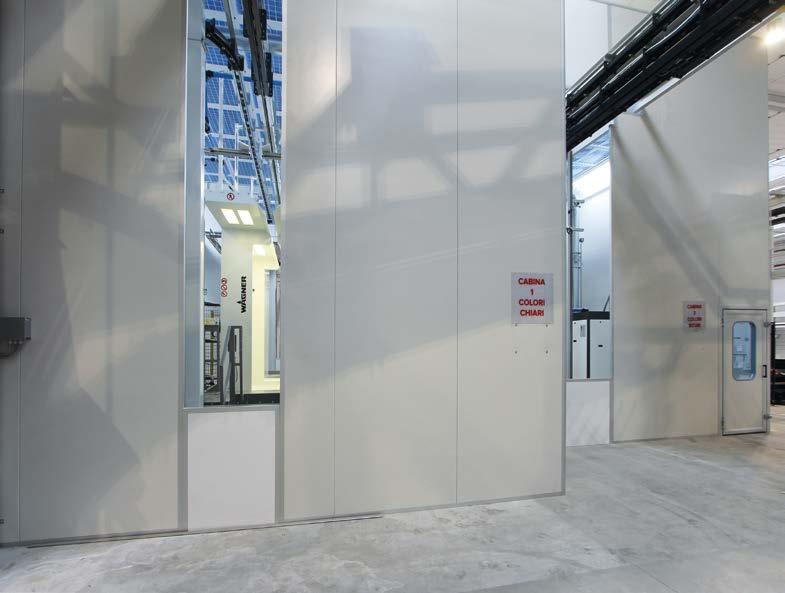
reciprocators, two manual pre- and postfinishing stations, and twelve automatic guns with traditional Venturi feeding technology, which move closer to or further away from the profiles to favour optimal adhesion and penetration of the powder coating, thanks to an optical sensor located at the entrance of the booth that detects the size and geometry of workpieces. “We also specifically requested the SuperCenter EVO powder center, thanks to which we have the possibility of sifting and mixing virgin and recovery powder - thus keeping the application quality constant - and which is able to dictate and automatically perform the colour change phases, regardless of the operator’s experience. Indeed, because we perform as many as fifteen per shift, we wanted our colour change operations to be managed independently and as efficiently as possible. Currently a colour change takes from four to thirteen minutes (with an average of eight) depending on the duration of the batch and the type of powders used”, says Grazzi. “We prefer to make sure our results’ quality level is high. This is why we also experimented with different arrangements of the profiles on the load bars, to try and further optimise our coating process. At the end of the cycle, moreover, our operators carefully check the quality degree of each individual profile.” After leaving the two coating booths, the components are taken to a gelling prechamber to prevent colour dispersion and then to the curing oven. Finally, they dwell in a storage buffer to cool down before being unloaded and immediately packaged, in order to avoid any excessive handling or damage during transport.
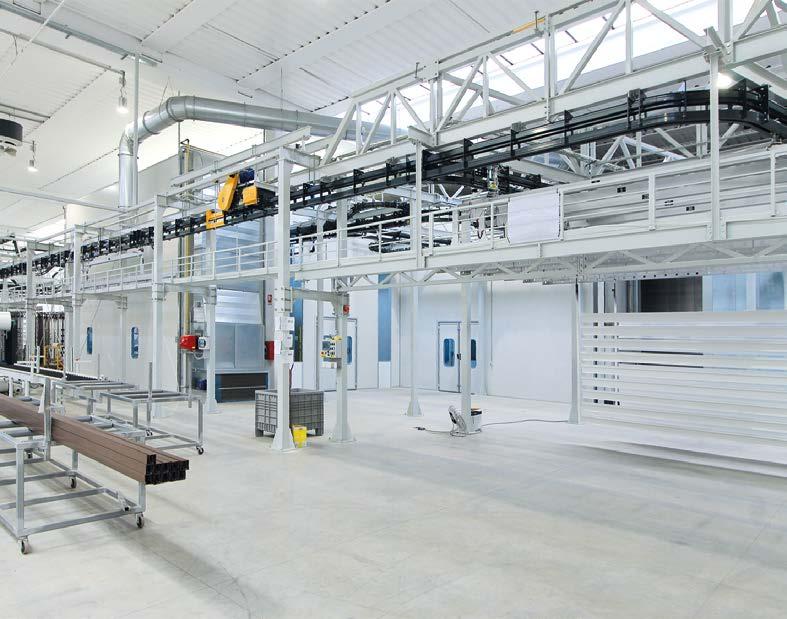
The role of Silvi and the importance of collaboration
“This plant has enabled us to exceed a salt spray resistance value of one thousand hours. It is extremely efficient and we are completely pleased with it. It has been in operation for over five months, but we have never
©ipcm
©ipcm
A detail of the power&free overhead conveyor (above) and the exterior of the clean room with the two booths applying light and dark colours, respectively.
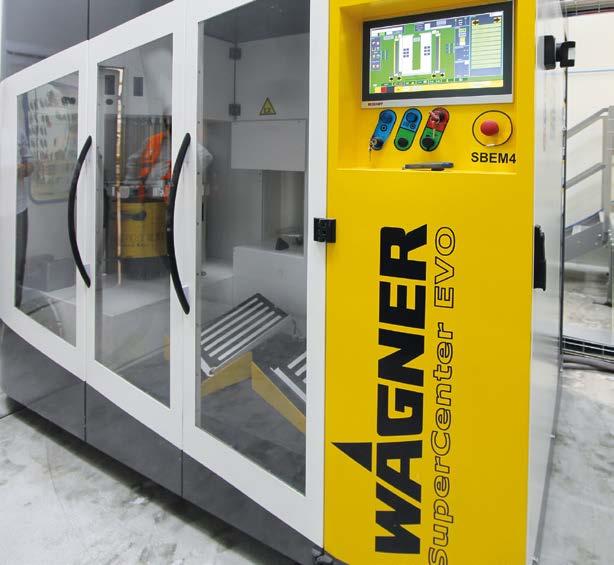
©ipcm
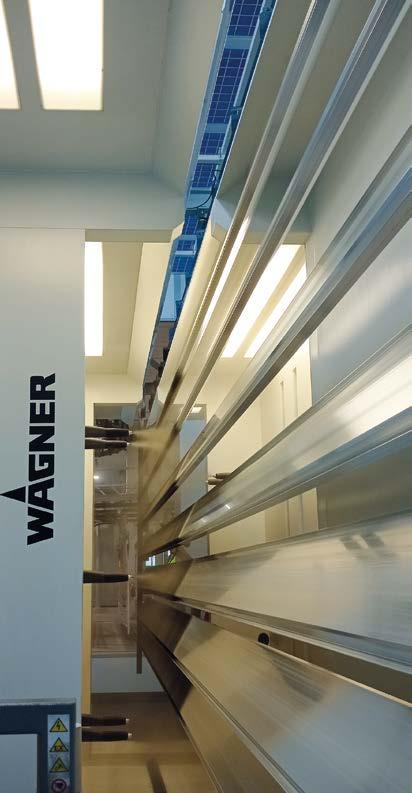
©ipcm
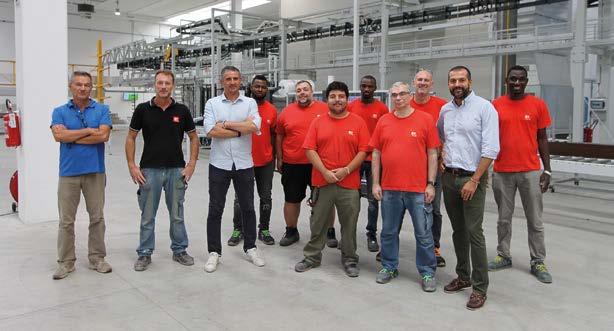
Aluminium profiles coated with the Wagner automatic booths.
The powder center.
BT Group’s team in front of the new plant.
©ipcm
encountered any difficulties or problems so far. This is also thanks to BT Group, which interacted with all the partners involved with the aim of providing the most suitable solutions for our individual needs,” states Citterio. “Our first step was to create a working group that included us from Silvi, the technical management of BT Group, Futura, Chemetall, and Wagner. We listened to the customer’s requests and we each supplied a key element to solve a specific issue. Then, we also worked with the provider in charge of BT Group’s management system, in order to interconnect the new Industry 4.0-oriented plant with the company’s management software package from the outset. Thanks to the flexibility shown by all the parties involved, we were able to install and test the entire plant on time, despite the problems caused by the shortage of raw materials,” says a satisfied Daniele Fumagalli, the General Manager of Silvi. “The choice of relying on Silvi once again proved to be a winning one. It brought us both quantitative benefits, because we were able to increase production, and qualitative advantages. We did not think that the development and implementation of the project could proceed so quickly. We are also happy to have involved all of our operators from the very beginning, as they were able to learn all of the system’s functions and make it highly efficient. In fact, we will soon start working on two shifts,” concludes Grazzi.