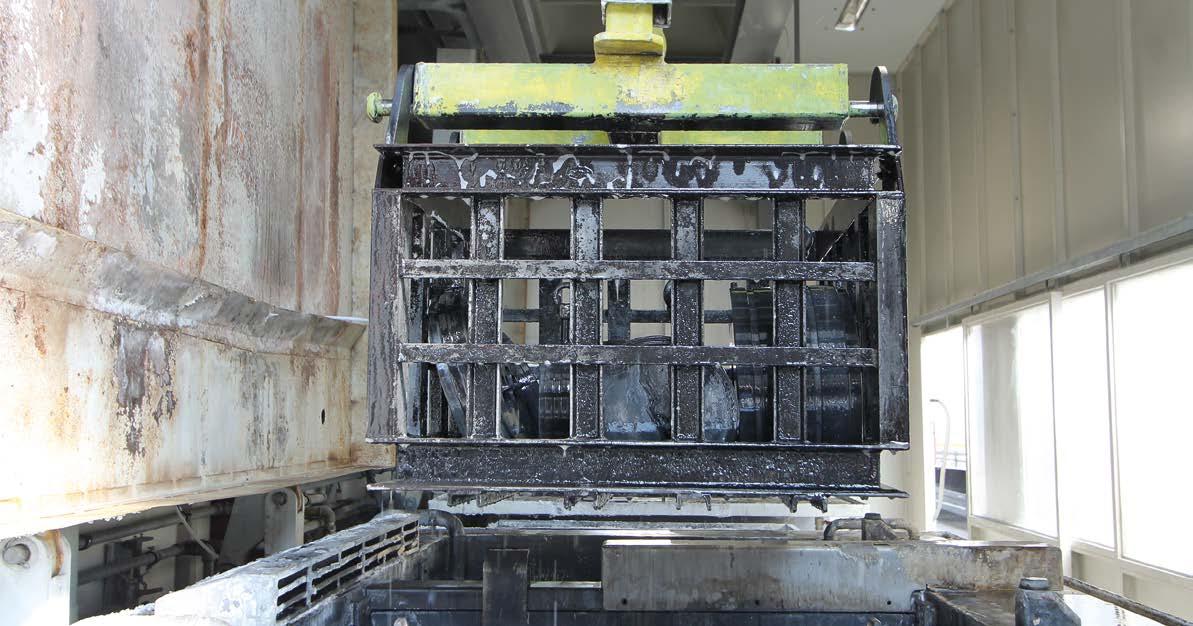
18 minute read
INNOVATIONS:PRESENT&FUTURE
Improving Extrusion Dies Cleanliness with Claris 9346 MB
Claudio Burato
Alit Technologies, San Bonifacio (Verona) - Italy claudio.burato@alit-tech.com
Every manufacturer of aluminium profiles for door and window frames, shower cubicles, automotive components, and many more products use extrusion presses to transform aluminium billets into profiles with the most diverse sections, optimised for their intended use. The dies of the extrusion presses are “templates” that give shape to the profiles. After each use, these have traces of solidified aluminium that must be completely removed before storing the dies until they are mounted on the press again. ALIT Technologies developed an innovative product that reduces the cost and time of cleaning extrusion dies for and in partnership with Alumec (Rudiano, Brescia, Italy).
In the aluminium industry, the extrusion dies are regularly cleaned by heating caustic soda baths and the aluminium scraps trapped into the die body are brought into solution through an exothermic reaction. This process involves the consumption of significant amounts of soda ash, which must be dismissed of at the end of the cleaning bath’s life cycle. The corrosiveness of soda ash combined with high operating temperatures close or above to 100 °C generate corrosive and dangerous fumes and, furthermore, the formation of sodium aluminate fouling implies continuous maintenance work, which is complicated by the corrosiveness of the liquid solution. In this scenario, it is crystal clear that the optimisation and cost savings for this process is strongly desired by all those companies operating in the field of aluminium profile extrusion. ALIT’s answer to this need is the additive Claris 9346 MB, entirely developed in our laboratories.
© ipcm
The treatment system for cleaning the extrusion dies.
Claris 9346 MB is an additive developed for the extrusion die cleaning systems for aluminium profiles; the liquid state easily allows automated dosing. Claris 9346 MB enables a more efficient die cleaning process by improving the following aspects: • It improves the general cleanliness of the extrusion die, facilitating the dissolution of aluminium residues that often gather in the most inaccessible points of the die. • It considerably increases the service life of the bath. • If appropriately dosed, it maintains the working temperature of the die-cleaning bath at around 90 °C, thus reducing fumes emissions and evaporation consumption. Maintaining the temperature in the process tank means an average energy savings of 20%. • It does not enhance the sludge formation.
How to use the product
The extrusion die cleaning bath should typically be loaded with soda ash diluted to 30% w/w. At this point, a certain quantity of Claris 9346 MB varying between 3% and 4% by weight on volume should be added to the bath. For every 1,000 litres of solution, approximately 35 kg of Claris 9346 MB should be added. Next, the product can be mixed, the bath heated, and the typical matrix cleaning cycle started.
Product analysis
The correct amount of soda ash and the maximum aluminium content dissolved in the matrix cleaning bath can be accurately determined by simple chemical analysis, easily performed by process operators. If necessary, the amount of Claris 934 6MB can also be determined by following the analysis instructions in the product data sheet. The possibility to detect these values, along with the improved thermal stability of the bath after addition of Claris 9346 MB, will make the entire process easier to manage by the operator.
Case Study
Claris 9346 MB has been implemented and co-developed by a major aluminium profile extrusion Italian company, Alumec (Rudiano, Brescia), which owns more than 11,000 proprietary dies. This company is already know to ipcm® readers, as it was the protagonist of a report1 on its efforts to make production more and more environmentally sustainable through a paint stripping process also developed by ALIT Technologies. Since the issue of that magazine, Alumec has made even more significant strides to become ever greener: from installing photovoltaic panels on all the factory’s available surfaces to replacing its pre-treatment products with chrome-free and nanotechnology ones, up to recently upgrading its extrusion die cleaning process. This company was using heated solutions of 30% soda ash for die cleaning. Under these conditions, the soda baths had a lifetime of only three working days, considering three shifts per day. The customer complained about the high soda consumption, shallow cleaning of the dies, and continuous fouling of the die cleaning system. After the addition of Claris 9346 MB in the matrix cleaning tank, at a rate of 3.5% w/w, the following benefits immediately occurred: • Product lifetime improving from 3 days to 6 or 7 days. • Improved overall level of the matrix cleanliness. • Temperature stability of bath within a 90-95 °C range, and less production of fumes. • Adsence of sludge at the end of the cleaning cycle.
The use of Claris 9346 MB generated different benefits such as the saving of large quantities of caustic soda, reduction of energy consumption and improved extrusion dies cleanliness. Compared with the previous management process without Claris 9346 MB, the customer is now fully satisfied. “Our collaboration with ALIT has been greatly strengthened since the publication of your article about the out-of-line stripping system for our vertical plant’s hanging hooks,” explains Manolo Brunotti, coating plant manager at Alumec.

1 Alessia Venturi, Improving Efficiency, Productivity, and Environmental Friendliness with Chemical Paint Stripping: Alumec’s Experience in ipcm® no. 68, Vol. XII, March-April 2021, pp. 56-62
© ipcm
The cleaning phase of the extrusion dies.
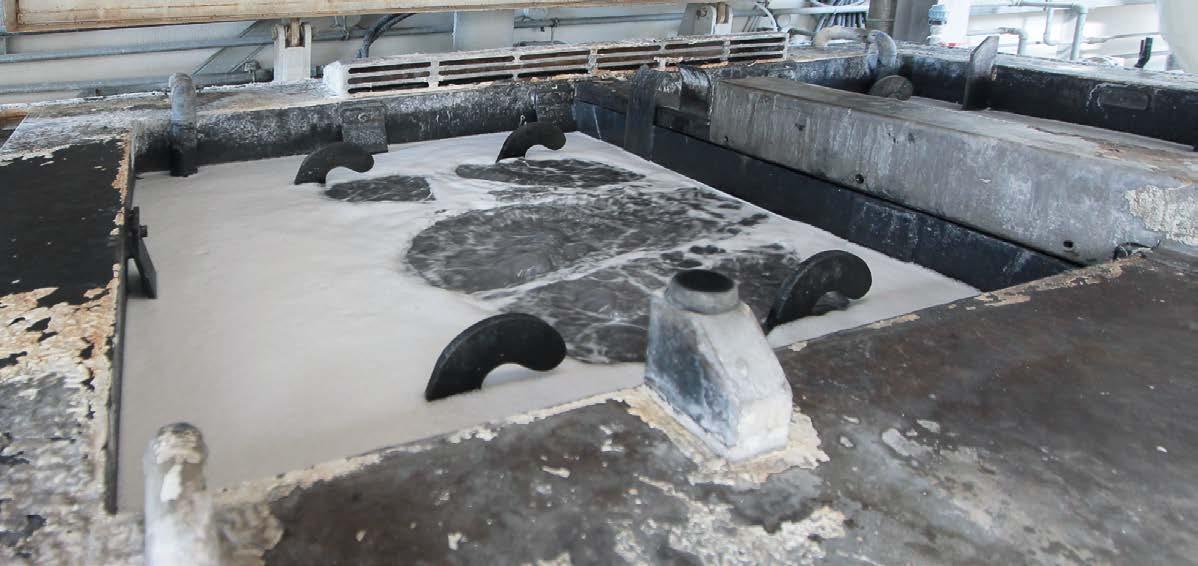
“After attending the technical course organised by ipcm® Academy and obtaining the international certificate of the Industrial Surface Finishing Process Technologist, I realised that we could further optimise our painting process to save time and money and, above all, respect the environment as much as possible. After fine-tuning our paint stripping system, we therefore continued the collaboration with ALIT up to replacing our entire pre-treatment process with its products,” indicates Brunotti. “I specifically asked to create a product that would meet our needs and, together with ALIT, we started to develop an innovative product for cleaning the dies we use on our extrusion presses. We mainly needed to speed up the cleaning process and extend the life of the bath. We invested a lot of time with ALIT in researching and testing the optimal formulation and the result was a product that definitely improved this significant operation in many respects. An important achievement is related to the consumption of methane gas: the bath containing soda must be kept at a temperature close to 100 °C and, therefore, our burners had to be lit 24/7. With the addition of Claris 9346 MB, the burners are switched off once the solution reaches a temperature of 80 °C and, due to the endothermic effect, the bath maintains a constant temperature, thus requiring the burners to be restarted only when the baskets containing the dies to be cleaned are immersed and then removed.” Brunotti adds: “Another important advantage has been reducing our disposal costs as well as soda ash consumption by over 50%. Considering that we have also sped out our cleaning process by 20%, I think we can be quite pleased. I personally thank ALIT also for the given name: MB 9346 are the initials of my name”.
The official launch of this new product will take place at the Aluminium 2022 trade fair in Düsseldorf (Germany) from 27-29 September 2022, where ALIT Technology .will present this and other innovations to its stand’s visitors.
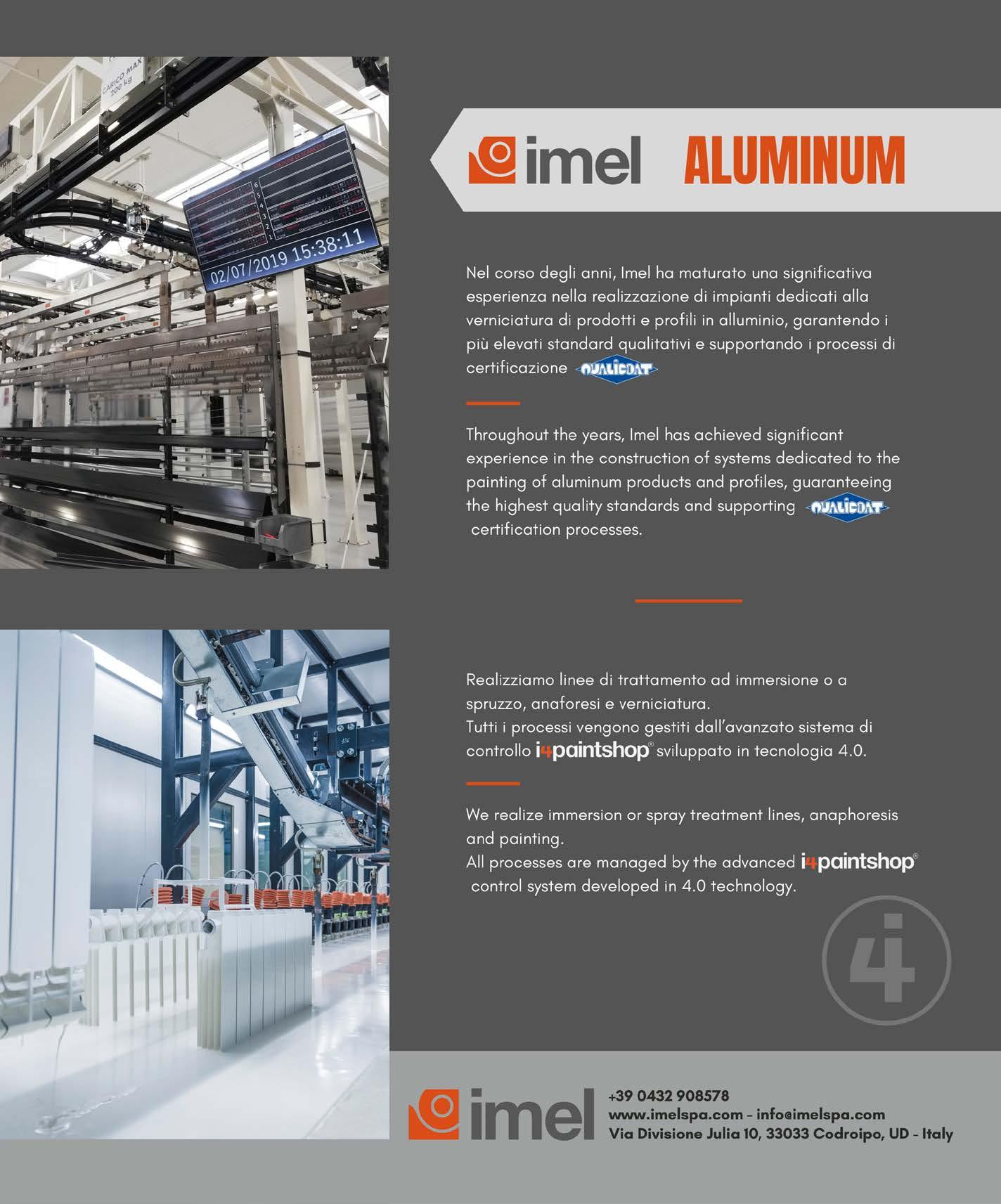
FOCUS ON TECHNOLOGY
Pracal Consolidates Partnership with Its Coil Paint Supplier and Guarantees Finishes Beyond Quality Standards on Its Roller Shutters
Monica Fumagalli, ipcm®
A company specialising in the production of roller shutters, Pracal has made a name for itself in one of the most complex areas in terms of economic development thanks to the nonconformist choices and entrepreneurial skills of its owner and of the partners, such as its paint supplier Condoroil Chemical, that have helped it develop eCOILS, the new company specializing in the continuous-flow pre-coating of aluminium and steel coils.
© Pracal
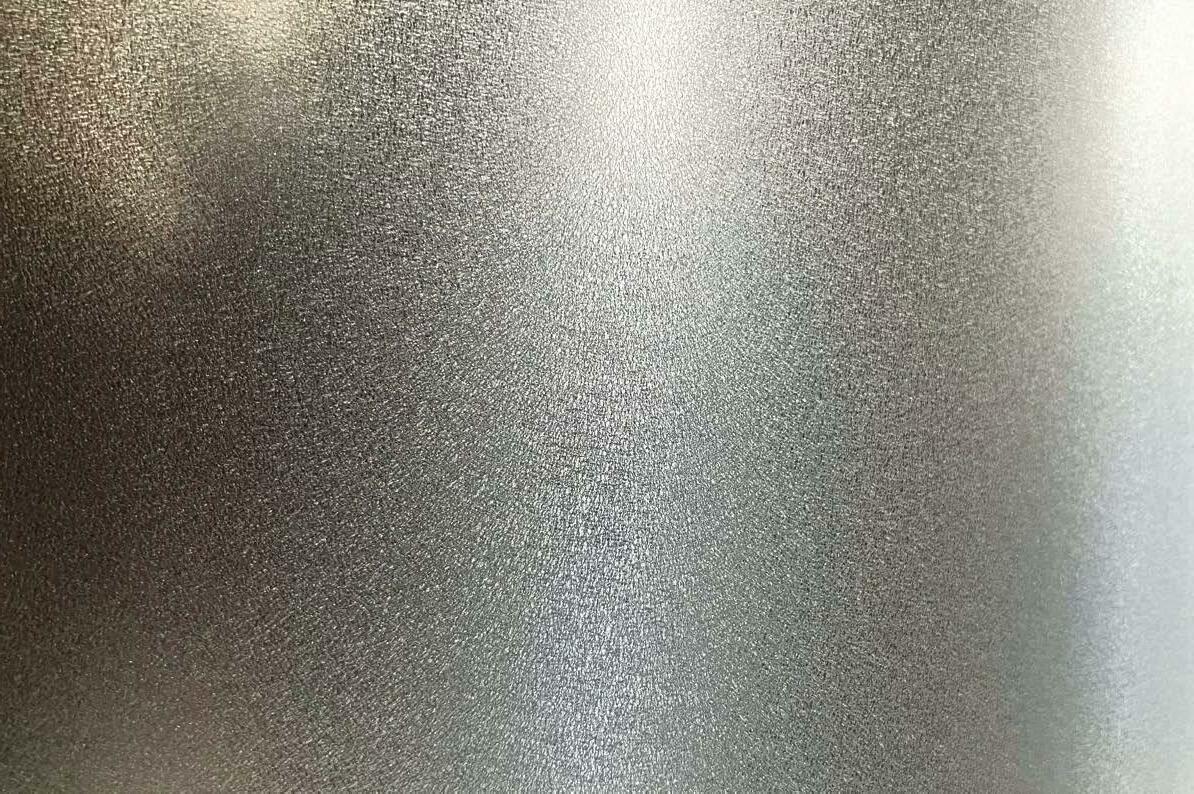
The new eSKIN finish by eCOILS, a branch of Pracal, which guarantees excellent performance in the bending phase and UV resistance.
One of the most technically and operationally complex processes is the continuous-flow pre-coating of coils made of various metal substrates, especially aluminium and steel, for use in construction (façades, roofs, and roller shutters), transport (walls and interiors of RVs and trains), and the industry (packaging and household appliances). It consists of several “sub-processes” that must be perfectly synchronised in order to achieve optimum quality results, from roller paint application to the curing of the paint product, be it liquid or powder, which must take place within seconds, to the post-coating phases such as, for example, coil profiling, stamping, bending, and drawing or chemical treatments such as off-set printing or sublimation. Precisely due to this peculiar characteristic, i.e. painting done before forming, the coil coating process must be carried out with extreme care and attention in every operational, handling, and storage phase, since the finish coming out of the coil coating line is the one the end user will see, because no further surface treatments are foreseen. Achieving the technical knowledge needed to run a coil coating line and provide its customers with a product that exceeds quality standards was the biggest challenge for Pracal Srl, a manufacturer of profiles for roller shutters based in Polla (Salerno, Italy). “We are now a national and international benchmark in the coil coating sector, as well as for roller shutters, thanks to the expertise acquired in the field,” explains Vittorio
© ipcm Iacullo, manager of eCOILS, a Pracal’s branch, “to our partnerships with companies specialising in the production of coil paints, such as Condoroil Chemical (Casale Litta, Varese, Italy), and to the quality of our workers, motivated and ready to face new challenges”.
A pioneering vision and extreme problem solving skills: Pracal’s trump cards
“Pracal (an acronym that stands for “steel aluminium profiles”) is the latest expression of a long-standing company founded in the second half of the 1980s for the assembly of PVC roller shutters, thanks to the far-sighted and pioneering vision of our current president, Francesco Pinto, who founded the firm,” says CEO Maria Massaro. “As early as the 1990s, our company started implementing plastics extrusion and became a leader in Southern Italy for the production of PVC roller shutters, to which it soon added customised slats, retractable doors, and shower enclosures. After 2000, it also specialised in aluminium and steel profiling. Pracal was thus born: it has established itself on the market thanks to its professionalism, its ability to find quick solutions to customer needs, and its fast and impeccable service from order to delivery.” The decision to insource the surface treatment of metal profiles is also the brainchild of owner Francesco Pinto and his son Raffaele, who since
The continuous-flow pre-coating department of Pracal Srl.

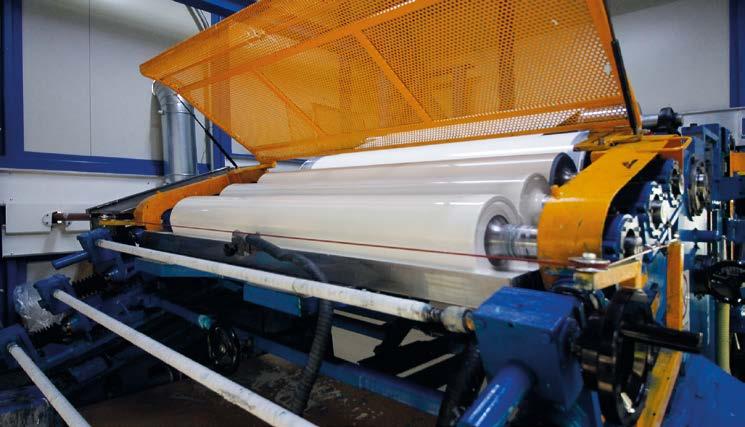
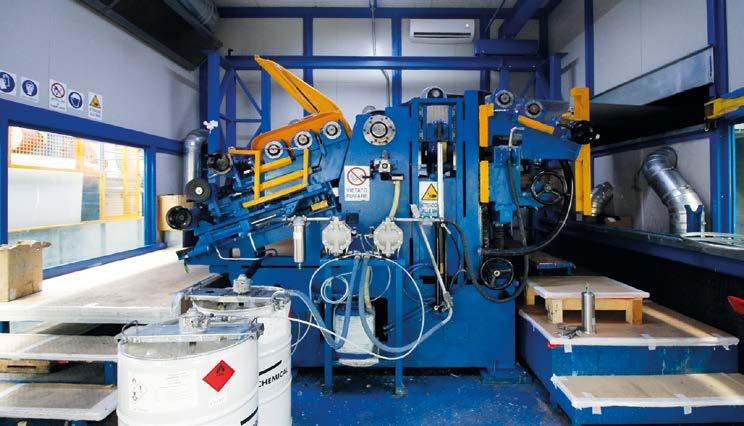
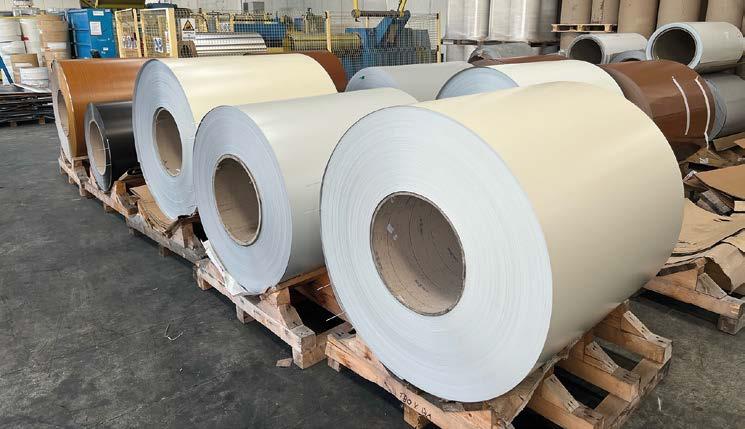
© Pracal
© ipcm joining the company has poured an incredible energy. “The idea started to take shape in 2009, when the need to respond just-in-time to customer demands no longer matched our availability in stock, because the contractors we relied on were unable to keep pace with our intensive production. We therefore started to paint our coils with a small plant, but colour repeatability was not up to our quality standards. However, the tools and procedures that we have to develop in order to solve the issues that arose from time to time, proved to be useful to achieve the skills that now allow us to manage the new continuous-flow coating system we installed to place alongside the previous one, which has soon become the flagship of our production.”
eCOILS: the coil coating at the beginning of the company’s production flow
The Pracal headquarters is located in an industrial area which is perfectly connected to the nearby motorway. The company has managed to develop an efficient and resilient organization that has resulted in constant growth, despite facing unfavourable economic conditions in the latest 2 years, and a penalizing geographical position compared to its competitors. The last two years have been characterised by steady growth; moreover, the company recently decided to launch a new brand, eCOILS, which started as a brand of Pracal but which may soon be developed as a stand-alone company to manufacture and sell prepainted coils, as is already happening in sectors other than the roller shutters ones.
© ipcm
From top to bottom:
Coils treated by Pracal.
The first coating booth for primer and back coat application.
The coating heads for the application of the top coat.
“Our new coil coating plant,” notes quality manager Sabatino Di Domenico, “enabled us to take a productive leap and establish ourselves in this sector. Today, we liquid-coat coils with a thickness of 0.2 to 1.8 mm and a maximum width of 1500 mm, with different types of paints, including polyester, polyamide, polyurethane, and PVDF, and we rely also on the Condoroil Chemical team to supply us with back coats and top coats.” “The continuous-flow coating process,” explains Di Domenico while describing this operation’s phases, “starts with the loading of aluminium or thin steel coil blanks onto two decoilers. Prior to pre-treatment and coating, the coils are joined by means of a splicer so that they can be treated with a continuous flow; indeed, our coil storage tower allows splicing two coils without ever stopping the plant. Speed and temperature are the two parameters that must always be kept constant.” Pre-treatment includes alkaline degreasing in the first tunnel with high-pressure spray bars and mechanical brushes to remove any traces of oil, grease, and oxides from coils; a second spray tunnel carries out a rinse with mains water and completes this phase with a second rinse; and a third tunnel performs passivation by fluozirconation. “The recovered waste water is then taken to the purification plant, which we are upgrading with a further filter system to cope with production peaks and thus improve water recycling: this is one of our main goals. The coils then reach a drying system that was developed by Pracal’s mechanical department to achieve perfect drying of the surface of coils with a thickness of more than 10 tenths of a millimetre, in order to offer the perfect pre-painted item, not only to roller shutters’ manufacturers, but also to tinsmiths, facade builders, roofers and panel manufacturers used in various sectors, from construction to naval industries”.
The continuous-flow coating process
After drying, the coils enter the first of the three coating booths, which is equipped with two coaters capable of applying a primer and a back coat in one pass. This is followed by oven polymerisation, air cooling, and water cooling. “One of the advantages of liquid coatings,” indicates Di Domenico, “is their very short polymerisation time, during which the pigment colours remain stable. The coils’ dwell time in the oven ranges from 6 to 60 seconds depending on their characteristics, while the temperature ranges between 210 and 250 °C. Once a coil has entered the oven, it gradually reaches a temperature close to that of the oven itself. Upon exiting, it is cooled by jets of cold air and demineralised water. “The second booth applies the top coat and any special effects such as metallic, wood-effect, antiqued or weathering steel-effect finishes. The third one is pre-arranged for clear coat application. The overall
towards the future
SOLUZIONI ROBOTIZZATE DI
ROBOTIC PAINTING SOLUTIONS VERNICIATURA


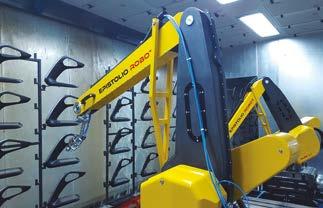
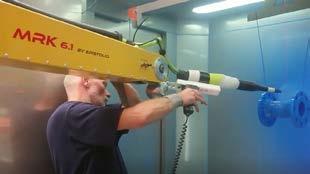
Epistolio Srl.
Via Piemonte 120 21100 Varese (VA) ITALY Ph: +39 0332 212692 Fax: +39 0332 223666 info@epistolio.com www.epistolio.it


© eCOILS
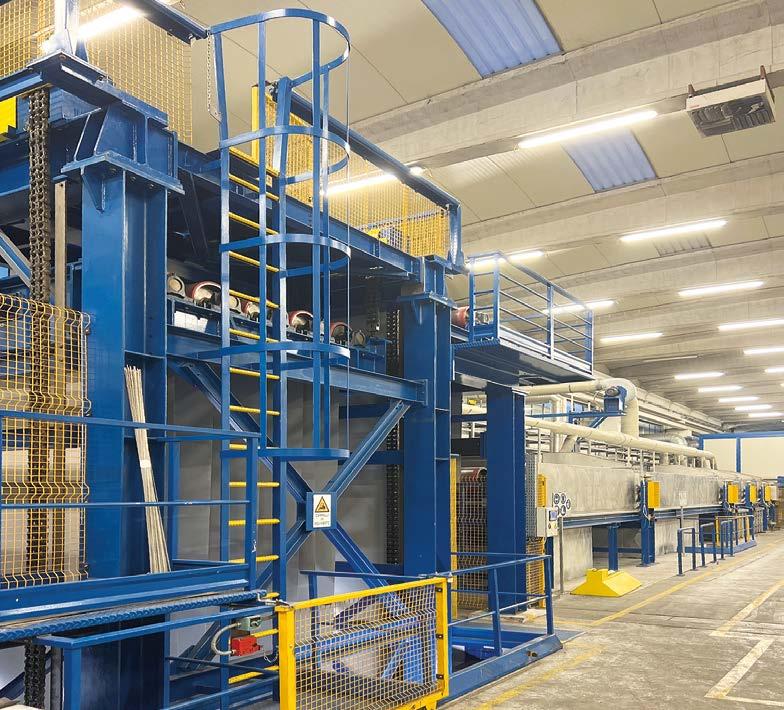

© ipcm © ipcm
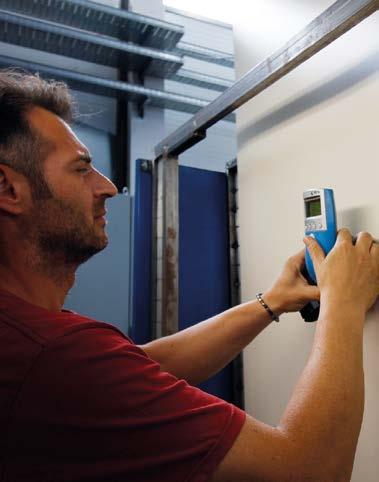
- The cooling tower.
- The first inspection after coating is performed with manual instruments by Antonio Salviati.
- Cross-hatch test being carried out on a painted plate.
thickness of the coating on a finished product is generally between 5 and 15 microns for the primer and 15-30 microns for the second layer. The coils then re-enter the air and water cooling oven and reach a storage buffer, where they are cut, and finally the recoiler at the plant’s exit.” Each station is equipped with a control PLC for data collection and analysis, coil tracking, and overall management of the coating line. “The innovative management of all data coming from PLC devices,” says Di Domenico, “was part of the investment we made last year to structure our factory according to the parameters of Industry 4.0. With this system, we are able to better manage our entire production cycle, which is very strict: since painting is the first phase and not the last, as is the case in traditional coating lines, all surface treatment operations must be carried out in time compatible with the subsequent processes, such as coil cutting and roller shutters profiling, guaranteeing short delivery times, never at the expense of quality.”
eCOILS and Condoroil Chemical working together for quality control
On leaving the coil coating line, the coils undergo an initial visual check. More in-depth checks are then carried out with manual and automatic measuring instruments, such as thickness gauges and micrometres, in the analysis laboratory. “We carry out all possible controls to deliver products with a quality level beyond the prescribed standards, from Machu to impact and cross-hatch tests. As for salt spray tests, we rely on Condoroil Chemical’s test laboratory, which not only supplies us with the paints to be used in our coil coating line, but also provides us with support and advice on the finishing results obtained. We are also in constant contact with them for the optimisation of paint formulations,” states Antonio Salviati, technician of the company’s internal lab. “Once they pass the quality tests, the coils are ready for packaging and delivering to our customers both in Italy and
abroad” – Iacullo continues. “Our particular finishes are highly appreciated for their aesthetic and qualitative value which makes the eCOILS brand recognizable on the market. In particular, we have received great satisfaction from our new eSKIN finish which guarantees excellent performance in the bending phase and UV resistance. In addition, we pursue an increasingly green policy, aiming to achieve the zero plastic waste goal: this is why 90% of the coated coil currently in our company is free of any PVC protective film. We are also trying to replace some typical packaging elements such as film or bubble wraps, but currently they are the only waterproof solution.”
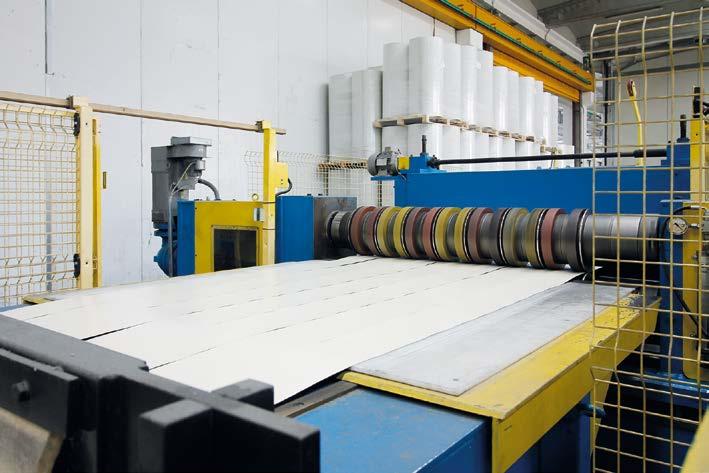
A supplier guaranteeing timely deliveries
“With a raw material supply chain made unpredictable by the situation we all know, delivering our products in a timely manner is crucial,” indicates Iacullo.
© ipcm
Cutting a coil after coating.
SMART SOLUTION FOR POWDER COATING - NOW EVEN MORE POWERFUL.

E-Line Plus
• Economical entry into automatic coating • Optimized powder recovery with Energy Efficiency Package (EEP) • Easy and fast color change • Combination with PXM powder center:
Automatic fresh powder supply and integrated system control via 15.6 inch touchscreen

© ipcm
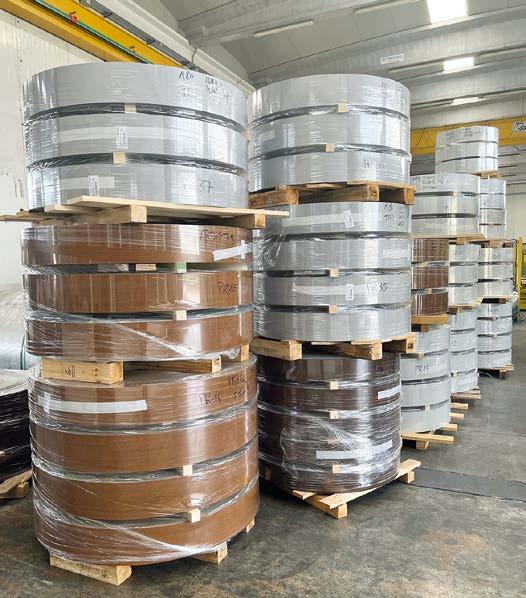
© Pracal
- Packaged coils ready for shipment.
- A pre-painted coil in RAL 1013 ivory.

- From left to right: Paola Zavattoni and Sara Ponti, the owner and laboratory manager of Condoroil Chemical respectively, Michele Langone, Vittorio Iacullo and Sabatino Di Domenico from Pracal Srl.
© ipcm
“In order to do so in such a dynamic sector, however, one needs to have partnered up with the right suppliers. Consistency and reliability in fulfilling all orders are also of the essence. Condoroil Chemical meets all these requirements: their supply of polyamide and polyurethane paints for roller shutters and blackout systems and of polyester paints for outdoor products has always been precise and punctual, even with new colours formulated on request.” “The paints we supply Pracal with,” says Sara Ponti, the head of Condoroil’s laboratory, “can be standard or customised with any tint required by its customers, but they all have the right surface hardness, flexibility, and adhesion characteristics to facilitate the subsequent profiling and bending operations.” “Collaboration with this supplier,” points out Iacullo to conclude, “will continue in the future, probably even more intensively since we want to establish ourselves in the market with our new eCOILS brand. We believe that the energy, technical and environmental solutions that aluminium can give us are the best; not only because aluminium is a 100% and infinitely recyclable metal, but also for its physico-chemical properties improved and enhanced by our coils surface treatments. Despite the considerable emigration rate that has distinguished Southern Italy for centuries, we are able to attract and train high-profile professionals and operators for which the security of a relationship with a supplier that can support us at every stage of the process, from R&D to quality control of coated products, is key to us. This is yet another reason why we appreciate Condoroil Chemical. Those who work in eCOILS and in the Pracal group in general, believe in the corporate vision of Francesco and Raffaele Pinto and are determined to contribute to the development of a modern industry, in authentic Italian style, which has its heart here: in the heart of Southern Italy”.
Innovation and Technology for Three Generations
