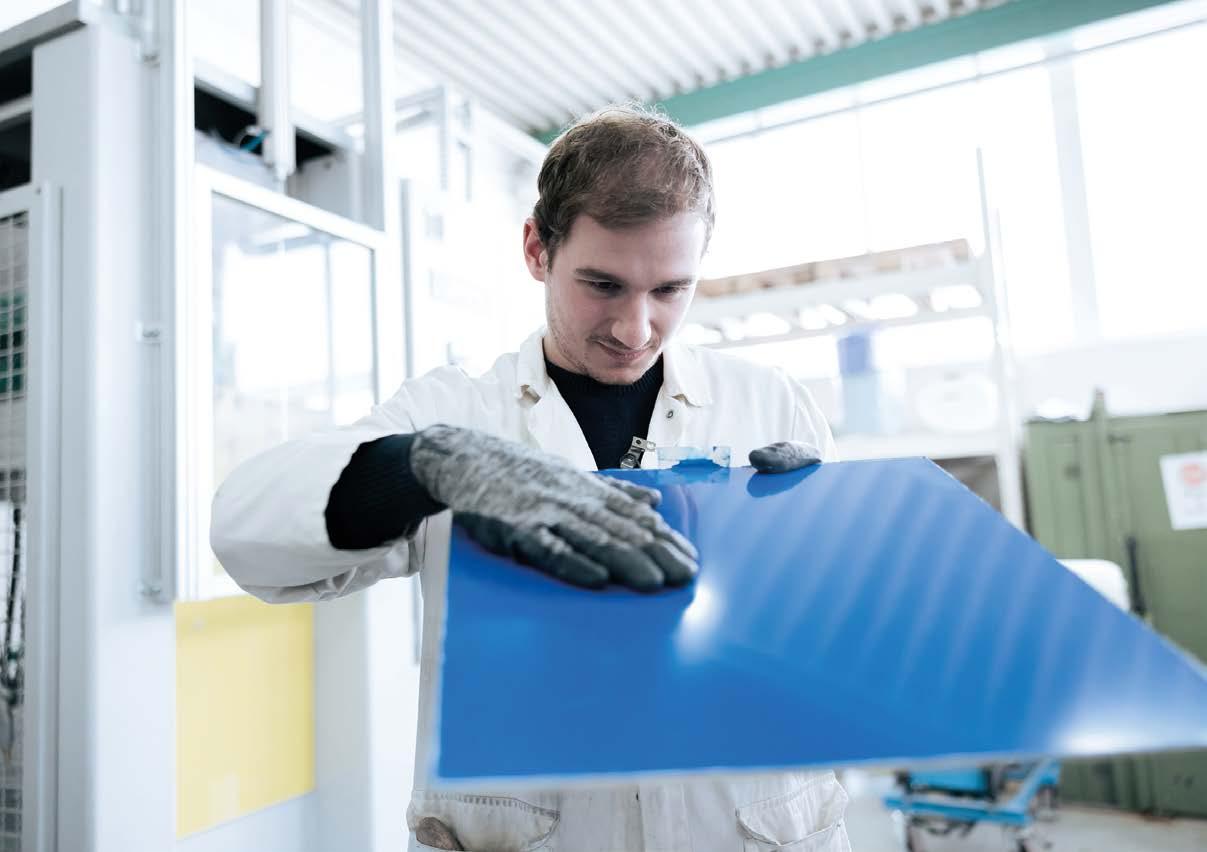
4 minute read
INNOVATIONS:PRESENT&FUTURE
© FreiLacke
Powder Coating: Making Plastics Conductive
Oliver Zanner
FreiLacke - Emil Frei GmbH & Co. KG, Bräunlingen-Döggingen (Germany) o.zanner@freilacke.de
Coating plastics with powders to a high standard has always been challenging. FreiLacke’s new conductive primer UR1967 makes the treated surfaces conductive with a special pigmentation to allow them to be painted with the same material as metals, for example. The UR1967 product is therefore the perfect addition to the company’s coatings family.
© FreiLacke © FreiLacke
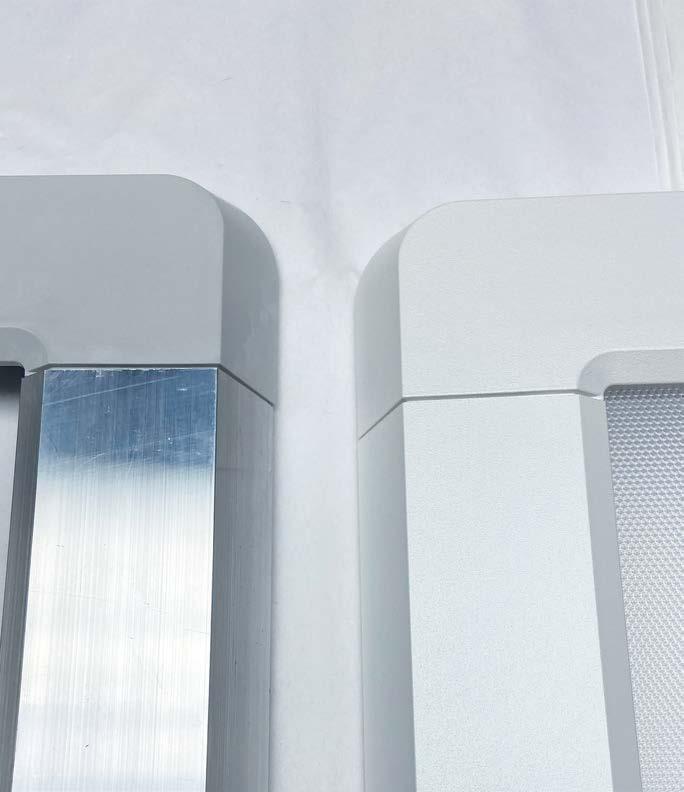
Thanks to FreiLacke’s new conductive primer, plastic parts can now also be powder coated. Even when aluminium and plastic are used within the same workpiece, the end result is homogeneous.
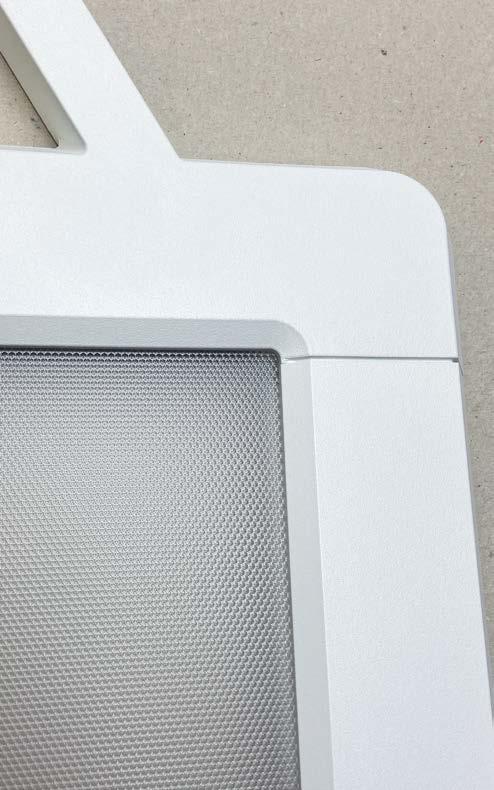
Plastics are lightweight materials with very good static properties. This is why they are widely used to manufacture components in numerous industries, such as automotive, mechanical engineering, furnishing, or sanitary. Their main disadvantage, on the other hand, is they are only suitable for powder coating to a limited extent, as they generally cannot withstand high curing temperatures. Indeed, the problem arises when a customer wants to have a machine’s components coated with the same look and the same surface structure as its metal ones: how can one achieve a coherent overall look? FreiLacke’s horizontal coating systems offer a solution to this problem. They are so well matched to each other for different substrates that the coated components match perfectly in terms of colour tone, gloss, and structure and can be mounted next to each other without any visual issue. Special pigmentation
As a rule, plastics do not have highly conductive surfaces: therefore, direct paint application with electrostatic processes is not possible. This is where the new FreiLacke EFDEDUR conductive primer UR1967 comes into play: thanks to its special pigmentation, it makes the plastic surfaces electrically conductive and thus prepares them optimally for the electrostatic application of the top coat. “The primer can be applied on non-conductive substrates using conventional pneumatic technology. Thanks to its stable bonding agents, the UR1967 product withstands the curing process very well and it does not become brittle,” explains Andreas Morlock, FreiLacke’s Industrial Coatings Development and Application Technology Group Manager. This ensures excellent, permanent adhesion to the substrates.
Effectively avoiding overspray
This results in the possibility to prepare plastic components with the conductive primer UR1967M so that they can be subsequently coated with the same powder as the other parts to be painted. In some cases, they can even be assembled before top coat application, with the great advantage that it is not necessary to paint each individual component separately. Another benefit is that less overspray is produced than with individual part coating. “All these measures guarantee uniform, consistent surfaces that are identical in terms of colour tone, structure, and gloss degree on every component, which in turn results in a significantly improved finishing quality level,” indicates Andreas Hepting from FreiLacke’s industry sales department. Of course, the prerequisite for the successful use of this primer is the correct match between the paint system and the plastic material. The plastic as well as the conductive primer must withstand the thermal load in the oven. Finally, the primer layer must be applied evenly over the entire surface, as a non-compact primer layer can lead to disturbances in the electrostatic field and thus jeopardise the top coat application process.
EFDEDUR conductive primer UR1967
The EFDEDUR conductive primer UR1967 is a solvent-based, twocomponent polyurethane product containing isocyanate-crosslinking acrylate resin. It is suitable for plastic substrates such as polycarbonate (PC), Acrylonitrile-Butadiene-Styrene copolymer (ABS), and others. This matte conductive primer has an application viscosity of 35-45 sec/4 mm; its maximum workability time is of 2 h at 20 °C. Oven drying is possible up to 80 °C; when air-drying, it is dust dry after 10 min (drying degree 1 / ISO 9117-5), touch dry after 1.5 h (drying degree 4 / ISO 9117-5), and completely dry after 7 days (pendulum damping test / ISO 1522). Different colour shades are available on request.
About FreiLacke
Coating systems & application solutions
FreiLacke has been synonymous with innovative paints and coatings since 1926. This family-owned company is now in its third generation and, with 600 employees at its headquarters in Döggingen (Germany), in the Black Forest, it develops customised solutions for customers in the wheel, car, mechanical engineering, contract coating, railway, wind power, functional furniture, storage, construction, and sanitary sectors. As a modern family-run business in its third generation, its headquarters’ ties with the territory are just as important as worldwide sales and proximity to customers through subsidiaries and partners abroad. Its product range of leading paint systems at the European level covers the entire spectrum from industrial coatings, powder coatings, and electrodeposition coatings to solutions for composites. A global network of subsidiaries and partners worldwide handles international sales. Environmental protection has always been a key issue for FreiLacke. That is why it strives to develop environmentally friendly products, reduce emissions, packaging materials, and waste, and use resources sparingly. In 2019, FreiLacke was named one of the top 100 employers in Germany in the “Great Place to Work Competition” and it places a high value on the topic of training, with a ratio of 10%.