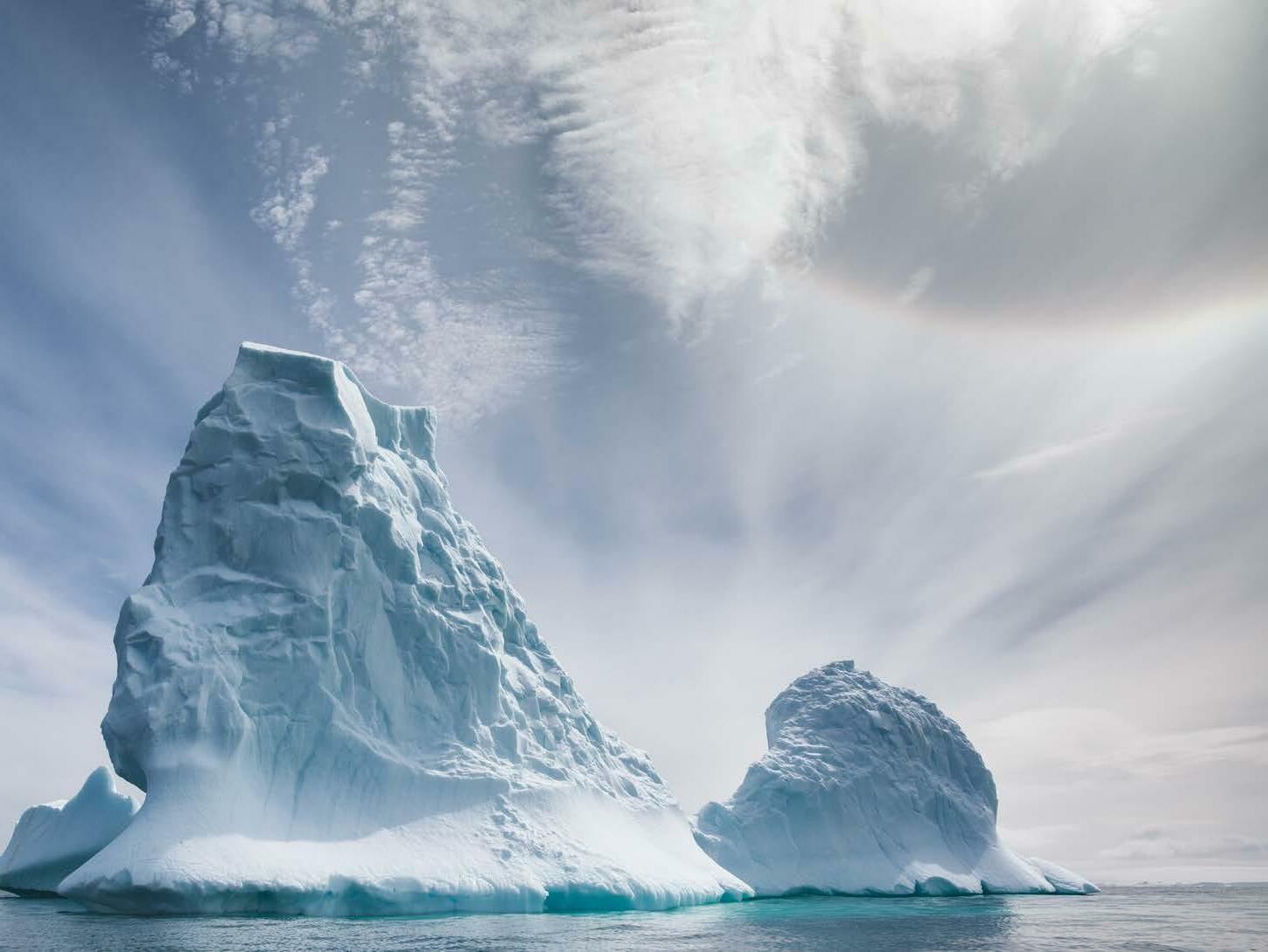

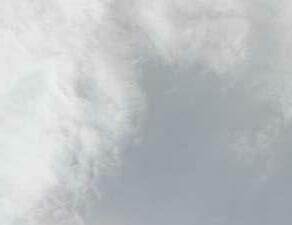
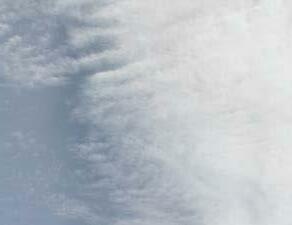
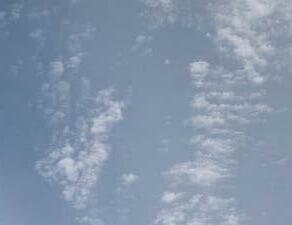




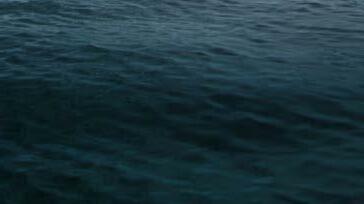

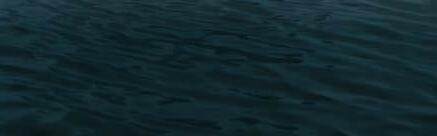
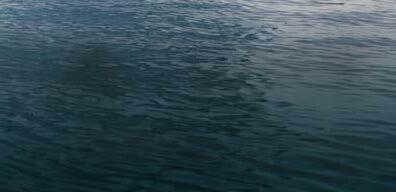
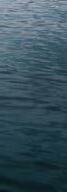
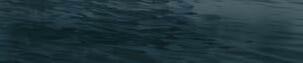






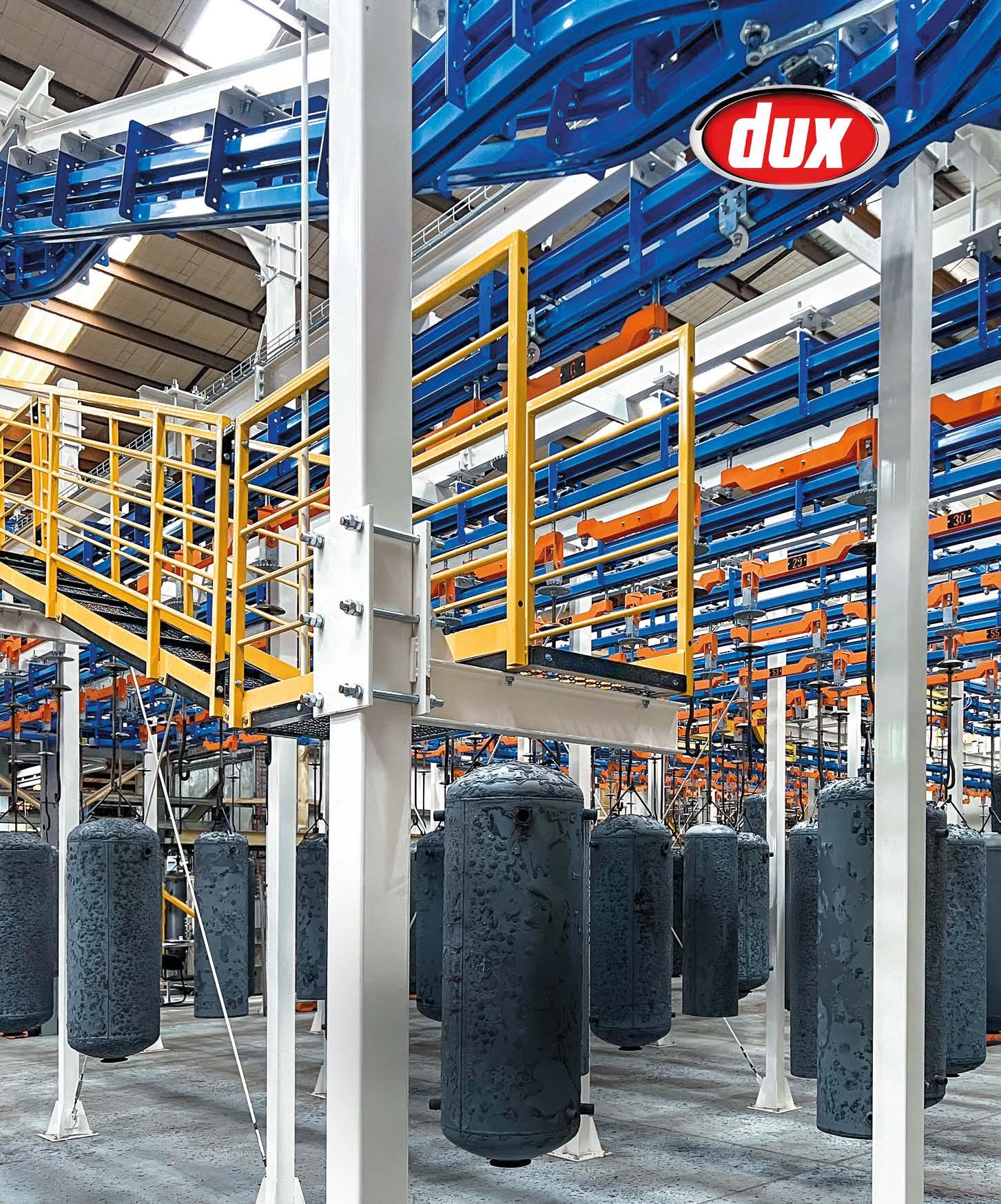


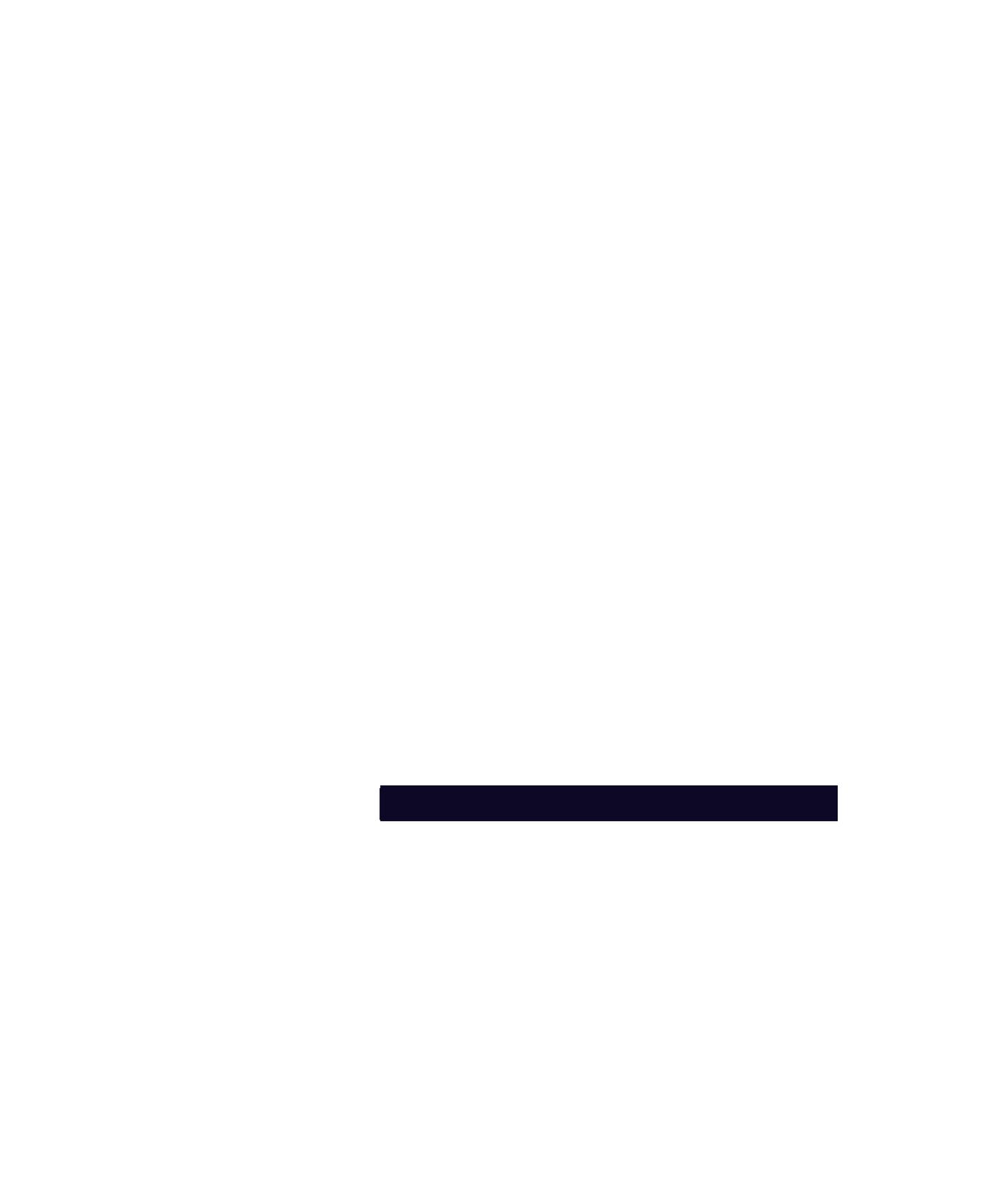
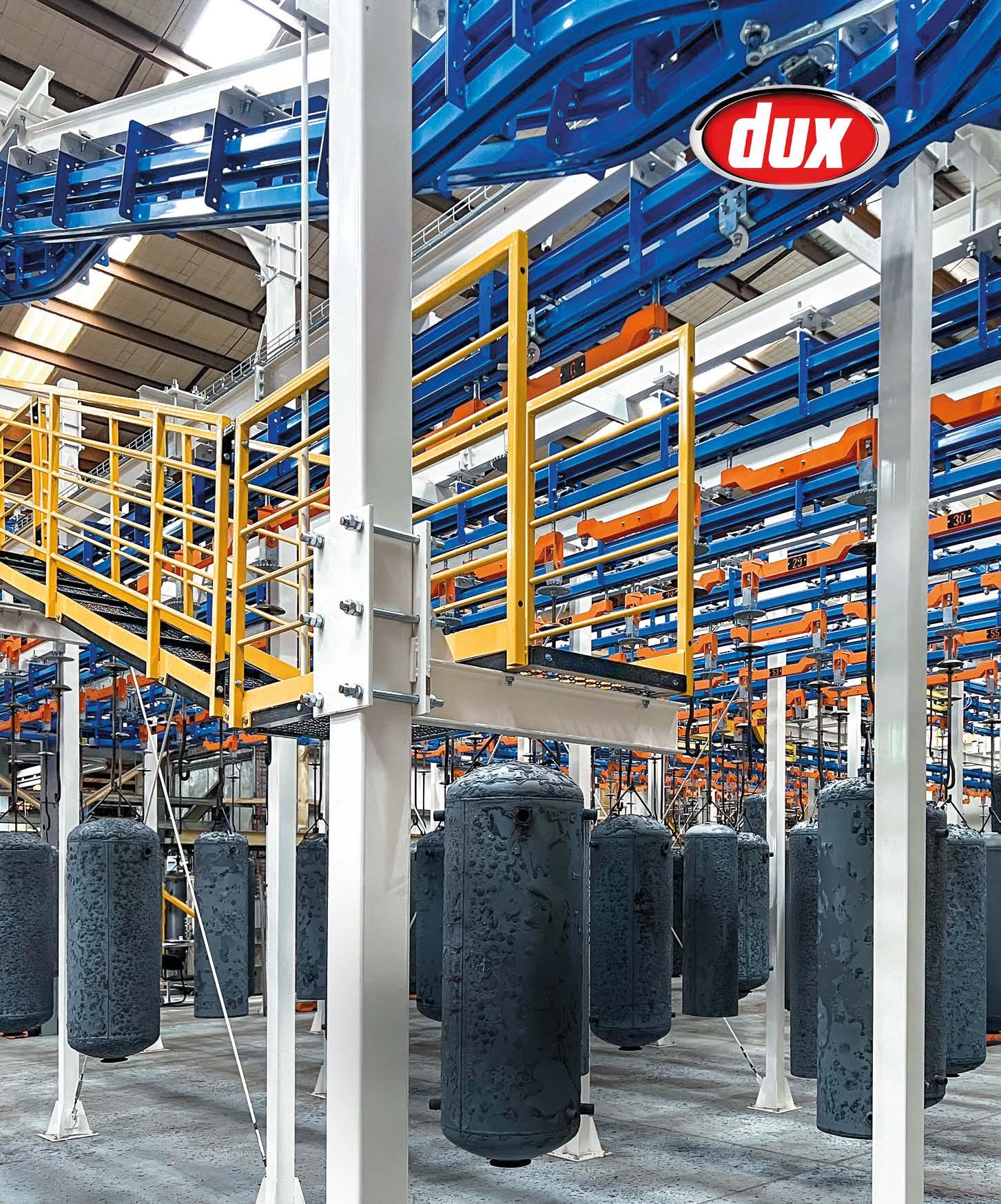
Inspiration and business. Building the future.
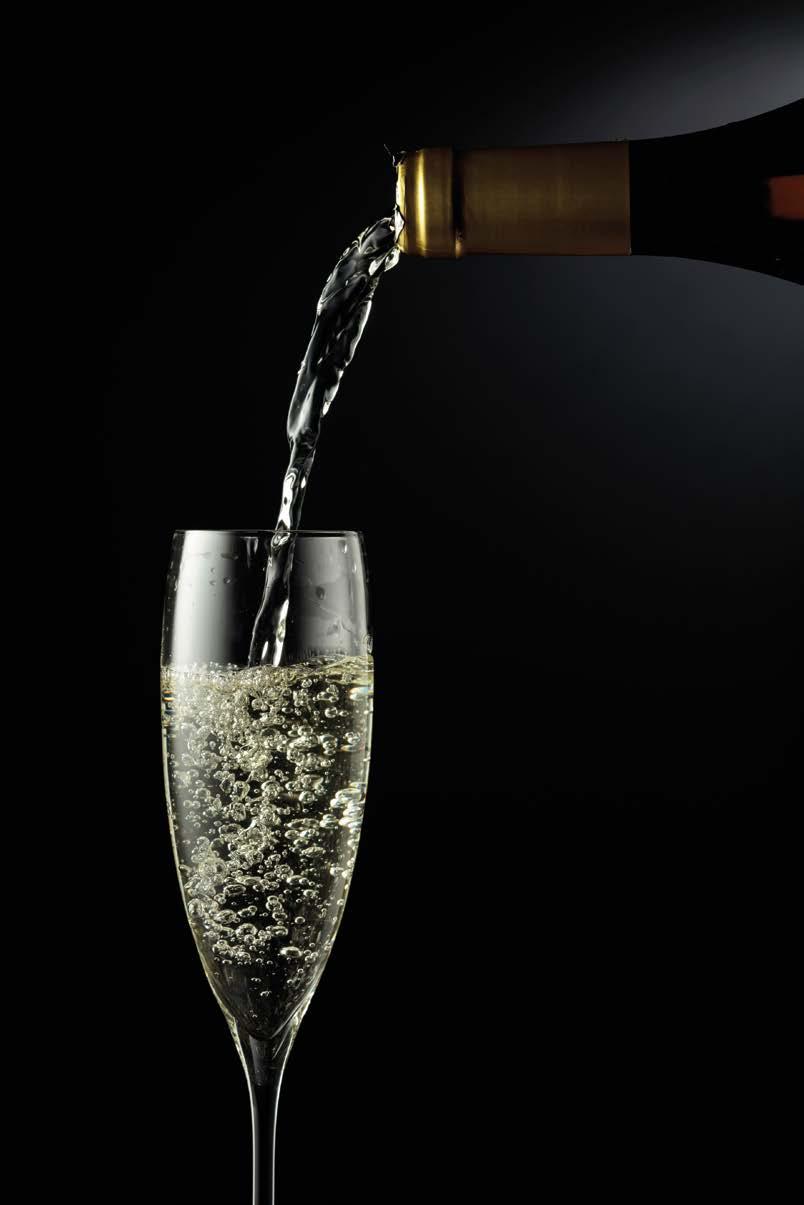
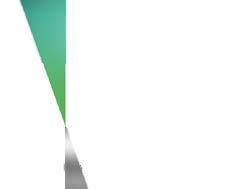
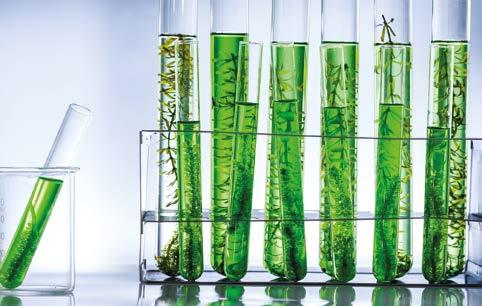
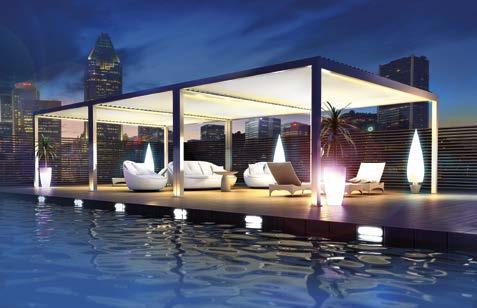

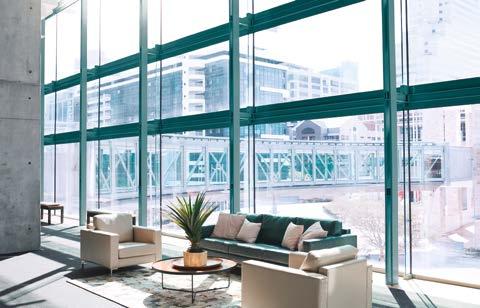
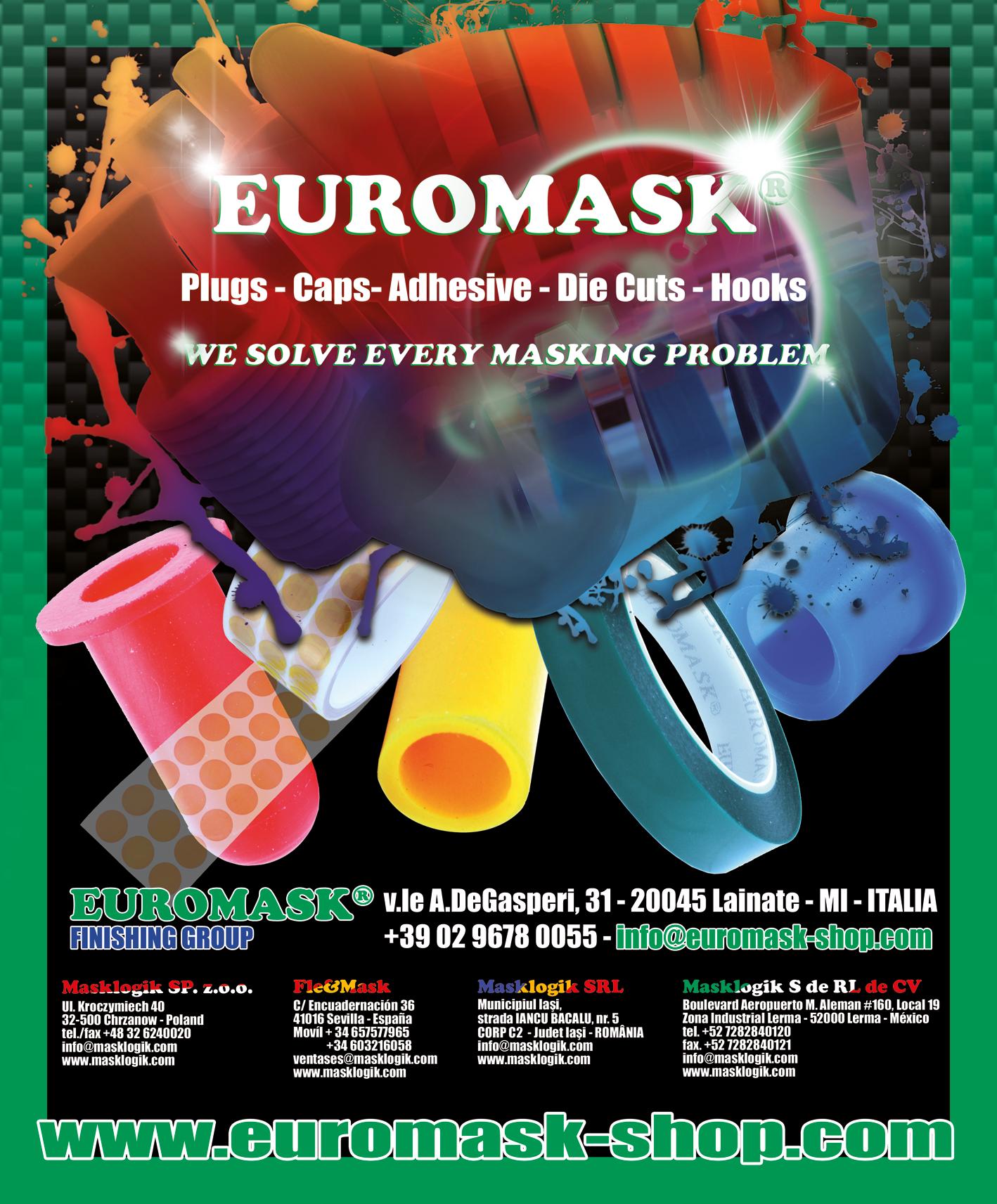
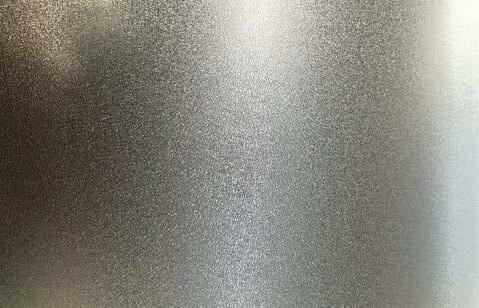
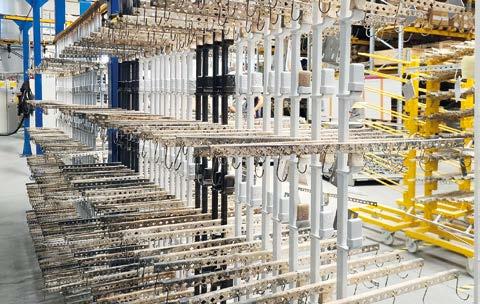
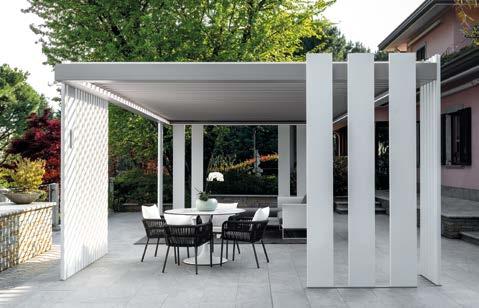
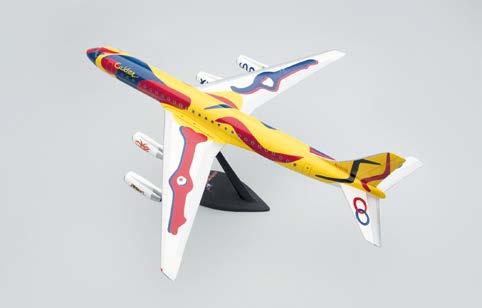
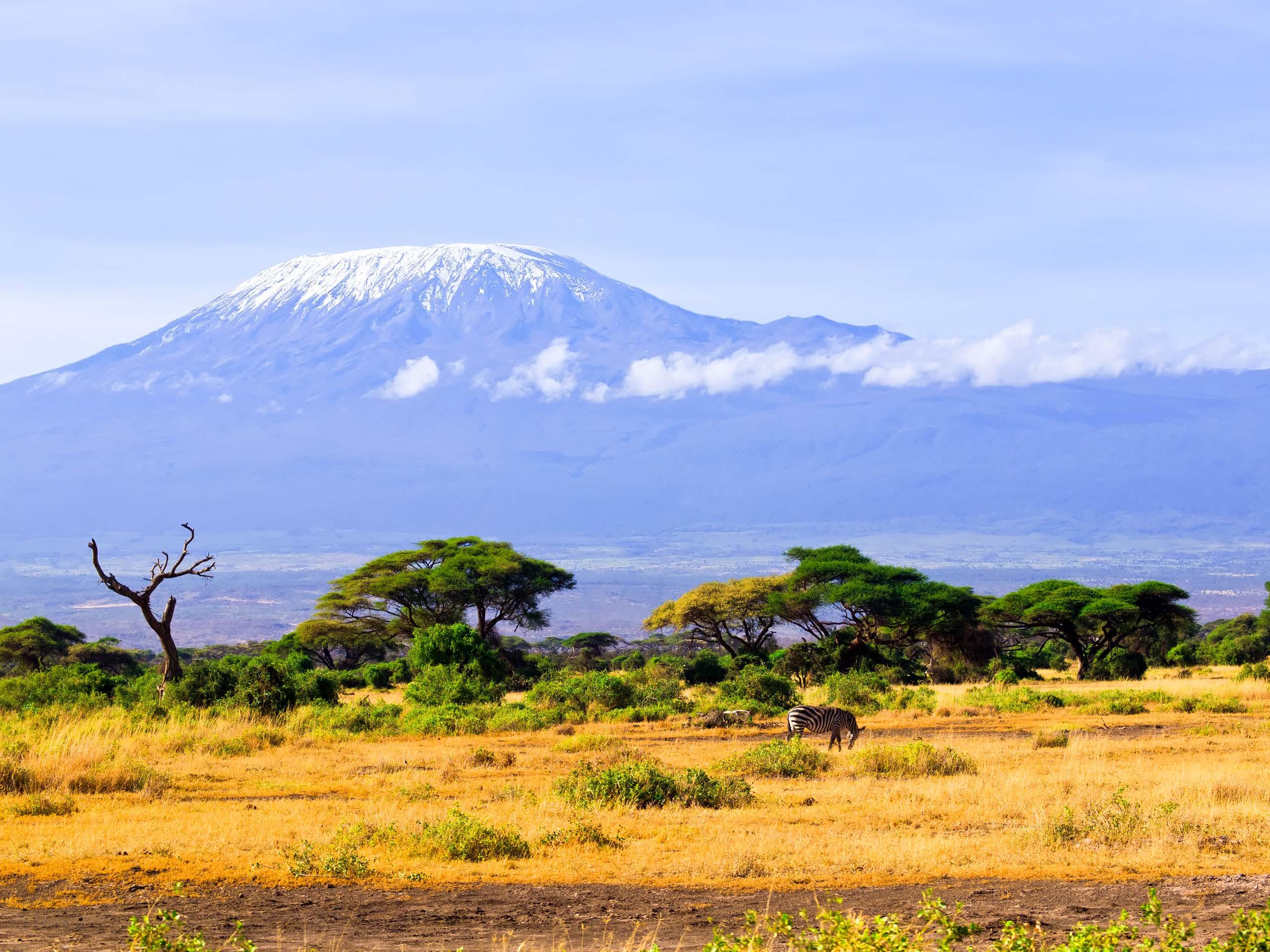






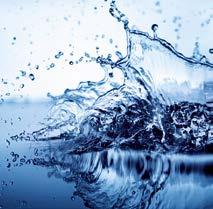


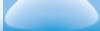




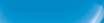
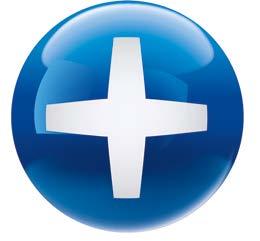
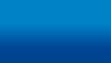





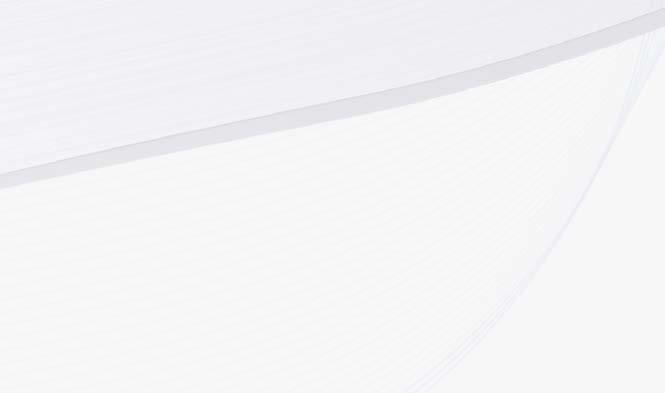
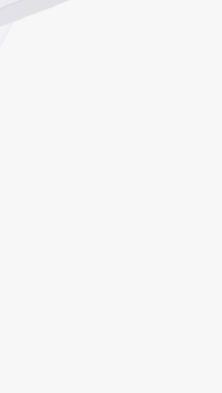

Inspiration and business. Building the future.
these lines while attending IMTS 2022 in Chicago, probably the largest trade fair in the USA for the mechanical industry: a truly huge event, crowded with visitors from all over the world and interested in any innovation related to energy saving. Yes, even here in the US.
After the increases in raw material costs that overshadowed the European industry’s recovery in 2021, 2022 is sure to be the year of the serious consequences of the steep rise in gas prices – not only on households, which have benefited from government aid that has mitigated the impact of such increases, but above all on industrial companies. It is only when we read the order of magnitude of the changes in the bills paid by these firms between 2021 and 2022, that we realise how gas price increases are a more than real danger to economic recovery, consumption, production, and the very survival of many businesses.
Glassworks firms, ceramics and paper manufacturers, and other factories where plants operate at temperatures above 1000 °C have received energy bills of hundreds of thousands of Euros compared with a few tens of thousands last year. The cost of gas has increased by 450% compared with last year, making industrial costs unsustainable, even though order trends for the vast majority of companies are clearly positive. Demand is high, recovery is strong, but this upward race in gas prices is unstoppable, especially as it is going hand in hand with a general rise in the prices of raw materials, noble gases such as oxygen, logistics, and packaging.
Wondering to what extent these increases are the result of the tail end of the pandemic combined with the war in Ukraine and the resulting sanctions on Russia, tensions between the US and China, and market imbalances, or rather the result of speculation that favours only a few people is legitimate, and everyone can seek their own answers.
On the other hand, everything that is technologically feasible to reduce dependence on gas, save energy, reduce natural resources consumption, and approach the circular economy in the field of surface treatments, you will find it in the following pages, with a special focus on the production and finishing of aluminium for architecture and the industry.
It is well known that the finishing industry is one of the most energy-intensive ones, even more so when it comes to aluminium, which requires high-temperature processes to be cast, extruded, tempered, and aged, but also coated, oxidised, sublimated.
Inverters, waste heat recovery units, compact plants sized exactly to meet requirements without excess power or productivity, systems for the parsimonious use and recovery of water are just a few of the technologies – some of which are truly revolutionary, patented innovations – that you will find in this issue of ipcm®. Also featuring a large section dedicated to the surface treatment and finishing of aluminium for architectural and non-architectural applications, it will be the protagonist of the most important international event for this sector: Aluminium 2022, to be held from 27 to 29 September in Düsseldorf, Germany.
After two years with a remote focus, Aluminium is going to return with a rich edition covering all segments of the industry, from foundry to coils to finishing. ipcm® is a media partner of the event and it is going to be present with a stand (1A07) to closely follow developments, research results, and trends in this market, but also the launch of some innovative products by companies that have been collaborating with our magazine for many
Youyears.will get a taste of this in the next few pages (watch out for the advertisements!) and especially in real time on our social channels during the course of the trade fair.
If you really want to stay up-to-date on the global dynamics of the finishing world, keep following us.
Richiedi la versione in italiano a info@ipcm.it
The ChemQuest Technology Institute has entered a three-year agreement to support the development of Universal Matter’s graphene technology based on sustainable feedstocks.
announced that it will explore the benefits of Universal Matter’s pioneering graphene technology in applications for paints and coatings. This high performing, economical graphene technology is based on a range of carbon materials, including coal, cokes, biomass and recycled rubber and plastics, which reduces its environmental footprint versus graphene based on traditional feedstocks.
“In this collaboration, Universal Matter seeks to leverage ChemQuest’s 40-plus years of industry expertise and technology development
experience and to validate performance and value creation benefits in the target applications that will ultimately accelerate the industry transformation,” said John van Leeuwen, CEO of Universal Matter.
“Our team is excited to continue working with this unique and valuable material. Not only is Universal Matter’s graphene technology sustainable thanks to raw materials based on biological and circular sources – it is also economical, scalable and extremely high performing. This is because of its innovative and novel production process,” said Daniel Murad, CEO of The ChemQuest Group.
Universal Matter produces its graphene using rapid, flash-fired bursts of electrical energy.
The process enables the bonding of carbon into few layers of turbostratic graphene, as opposed to AB-stacked (Bernal) graphene, resulting in performance benefits in the target
Theapplications.flashprocess is modularized into compact manufacturing units and can be scaled by adding more modules of identical configuration. Many different carbon-based feedstocks can be transformed into high purity turbostratic graphene using this flash Earlierprocess.collaboration between Universal Matter and ChemQuest demonstrated the effectiveness of the technology in formulations for specific applications. Proven performance improvements included compressive strength, tensile strength, barrier properties, rheological enhancement and flow characteristics. The current initiative will focus on developing knowledge for a broader range of applications in paints and coatings.
“There is an inherent need and significant business opportunity to improve the performance and sustainability of products in these markets via the upcycling of carbon into ‘green’ graphene, thus improving the mechanical properties of these industrial materials and creating stronger, longer lasting coatings, which also significantly reduce our carbon footprint and greenhouse gas emissions”, according to van Leeuwen.
“We look forward to building on our collaboration with Universal Matter and helping them to create higher performing, more sustainable formulated products,” Murad said. “We recently invested in the expansion of our R&D facilities. Our expanded resources will enable us to independently qualify and quantify the benefits of the technology in a diverse range of market applications, identify the most valuable opportunities and help to expedite their commercial feasibility and market entrance.”
For further www.chemquest.cominformation:and www.universalmatter.com
the North American integrator, manufacturer and technical support for mechanical and software of Lesta robots for industrial painting applications, has announced that it has reached a new distribution partnership. The company will collaborate with Sames Kremlin and Wagner/C.A. Technologies to deliver automated finishing solutions to wood industry manufacturers.
“We’ve really come a long way since we debuted to the wood industry at the AWFS Fair in 2021. Today, we’re working in partnership with the best in the industry to leverage our technologies that will continue to push the boundaries of what’s possible in finishing,” has stated Derek DeGeest, the president of LestaUSA. “The success we’ve had has resulted in an opportunity to go deeper with our Equipment Partners.
For the first time ever, our partners are bringing our automation solutions into their product lines. This allows us to collaborate on bringing our technologies together to offer an even more robust system along with service to our mutual customers.”
“We are excited to bring more automation solutions to the Wood
Industry in addition to flat lines. We can now look to combine the two proven technologies. This automation push in wood is essential to growth in today’s market and economy,” has commented Kevin Higgins, the vice-president of Sales/Distribution at Sames Kremlin.
“We have equipment in their test lab and they have their robots in ours. Manufacturers can bring this automated solution into their operation knowing that it works and will be supported by Wagner, our distributors, and LestaUSA. That’s the peace of mind Wagner customers come to expect from us,” has added JR Rogers, Wagner Engineered Systems National Sales Manager.
Users were able to experience the automated finishing solutions of LestaUSA during the International Woodworking Fair (IWF) – that took place from 23rd to 26th August 2022 in Atlanta (U.S.A.) – at the booths of Sames Kremlin and Wagner/C.A. Technologies.
For further information: www.lestausa.com
LestaUSA will collaborate with Sames Kremlin and Wagner/C.A. Technologies to deliver automated finishing solutions for the wood industry.Instruments, Inc. has announced that it has completed the previously announced acquisition of Atotech Limited for approximately $4.4 billion in cash and MKS common stock. “The acquisition of Atotech positions MKS to accelerate roadmaps for future generations of advanced electronics devices. By combining leading capabilities in lasers, optics, motion and now process chemistry, MKS is set to be a leader in the next frontier for miniaturization and complexity: optimizing the InterconnectSM, a significant enabling point of next-generation advanced electronics. Atotech’s leadership in functional and decorative surface finishing will also extend MKS’ product offering for industrial applications and grow our market reach. I could not be more excited to welcome the Atotech
With over 50 ZLD plants installed all over the world, CIE is a leader company in Zero Liquid Discharge for metal finishing industry www.cieeng.com - info@cieeng.com
team to the MKS family,” has declared John Lee, the President and CEO of TheMKS.combination of MKS and Atotech creates a company with pro forma revenue of $4.5 billion for the twelve months ended June 30, 2022. As a result of higher interest rates on debt financing compared to the time the transaction was originally announced in July 2021, as well as the impact of the current macroeconomic and inflationary environment on the business of the company, MKS currently anticipates the acquisition will be accretive to Non-GAAP diluted net earnings per share for the full fiscal year 2024.
For further information: www.mks.com and www.atotech.com
Sustainability is an important aspect in the development of new products. In addition to the product’s direct properties and effects, questions regarding environmental impact, chemical basis, and energy consumption often play a significant role too.
Manywax-based additives on the market comprise raw materials won from crude oil or gas, ranging from traditional (high-density) polyethylene waxes for increasing matting properties or improving scratch resistance to polypropylene waxes or PTFE for surface slip adjustment in coatings. They exhibit a fairly good performance and have a beneficial factor, which is why they are designated in their applications. Nevertheless, considering aspects of sustainability, e.g., the use of bio-based raw materials, all these waxes must be reviewed critically.
One obvious and major factor is: crude oil is a finite raw material. This means its availability over the next centuries is decreasing and there is a great need to discover, test and finally use new alternative raw materials. Another major factor is climate change. Climate change is still ongoing, and it is significantly influenced by our actions. Saving every ton of CO2 possible will help to comply with the Paris Agreement of 2015 to keep global warming below 1.5 °C. Governments are aware of the topic and are undertaking measures to
combat climate change, which in turn impact on the use of fossil raw materials. Exemplary measures are the levying of taxes on carbon dioxide (CO2) emissions or the purchase of certificates that allow the buyer to emit a certain amount of CO2. But the economic effect is just one side of the story. The ecological effect is much more important for a reduction in the use of crude-oil-based products.
Other aspects of sustainability deal with the endof-life options of products. In our daily life, we are surrounded by plastic and cause a lot of plastic waste. This plastic waste needs a lot of time to be degraded in the environment: in the case of PE plastic bags, it is around 500 years. Thus end-of-life options like biodegradability, where the plastic is degraded by microorganisms such as bacteria and fungi in shorter time frames, are becoming more and more important. But plastic is not always so obvious in our lives as in the case of plastic bags. Many wax additives are based on synthetic raw materials, so these are, like plastics, affected by the issue of biodegradability. Therefore, an increasing amount of biodegradable material can help to pave the way to a more sustainable future.
CERAFLOUR 1000 is one excellent example of an additive with improved sustainability, launched in 2011. It has specific properties of traditional additives manufactured using either natural or synthetic waxes, but is based on a bio-based polymer and is also fully biodegradable. In 2021, BYK expanded its portfolio by two new additives
based on the same raw material, but with different particle size
AllCERAFLOUR 1002. distributions: CERAFLOUR 1001 andthreeadditiveshaveabio-basedcontentof> 97%
and are fully biodegradable. Moreover, bio-based polymers make a positive contribution to the ongoing microplastic discussion and conserve aquatic life (Fig. 1). The polymers of the CERAFLOUR 1000 series are produced with the help of microorganisms. These organisms are fed with carbohydrates and produce the bio-based polymer in a fermentation process. In additional steps, the polymer is separated from the microorganism and purified. The last step of micronization leads to polymers which can be used for different coatings applications.
With CERAFLOUR 1001, BYK offers an additive with even finer particle size distribution than CERAFLOUR 1000 to achieve the utmost in transparency while simultaneously intensely reducing gloss. On the other hand, with CERAFLOUR 1002, BYK has introduced an additive with a larger particle size to create a surface texture with high transparency that, at the same time, produces the best matting performance. The spherical structure of the polymers, which form agglomerates, can be seen on the SEM (scanning electron microscope) images.
The particle size of CERAFLOUR 1000 lies between that of the other two products (Fig. 2).
The additives were very intensively tested in different kinds of applications. Starting with water-based systems, in 100% UV coatings, but also in traditional
Figure 1: Overview of the extraction of the raw material for polymers in the CERAFLOUR 1000 series.solvent-borne coating systems, the additives show excellent compatibility and performance. Their usage in wood and furniture coatings, printing inks, and general industrial coatings is highly recommended.
CERAFLOUR 1001 shows the lowest haze with good matting properties at the same time. Especially at higher dosages, CERAFLOUR 1001 shows low haze values compared to other PE waxes (Fig. 3).
In laboratory tests, the polymers show synergistic effects with common PE waxes to improve the scratch resistance and abrasion resistance of a coating’s formulation. Only a small addition (0.5% on total formulation) of these is sufficient to create good scratch resistance of the coating’s surface. Furthermore, all three products show synergistic effects with silica-based matting agents (Fig. 4).
On top, all three products provide excellent haptic properties and provide a “soft feel” effect of the surface. This is particularly true for the smaller particle sizes. What is more, adding polymers of the CERAFLOUR 1000 series help to increase the amount of renewable carbon of a formulation to fulfil the requirements of the market for finding more sustainable solutions.
Looking to the future – there is a need for change
Sustainability is a complex topic and there are many aspects to consider. It is not only the raw material source which can be exchanged for an environmentally friendly solution. Lower film formation temperatures, a smaller number of solvents or coalescents, faster curing speed, or better degradability – there are many opportunities to reduce CO2
The CERAFLOUR 1000 series is yet another excellent step towards BYK’s goal of becoming more sustainable across the complete supply chain and providing sustainable solutions to customers.
The gravity flow cup guns will reflect SATA’s efforts towards a more sustainable and connected future.
GmbH & Co. KG, a German manufacturer of coatings technologies and equipment, has recently presented SATAjet X 5500 FUTURE, a limited edition version of its gravity flow cup spray guns. The special edition was exclusively available from SATA dealers starting from 13th September 2022 until sold out. Resembling the company motto “Green is more than just a colour to us”, the new green spray guns are then not only a reference to nature, but also a symbol for harmony, hope and a more sustainable and connected future. The globe-shaped circuits on the spray gun represent the technology which is connecting people and thus enables the globalised world of the future. The radiant green colour with the black components not only looks harmonious, it stands for aligning the actions of the company with sustainability and the preservation of nature. The special edition SATAjet X 5500 FUTURE is available in the following nozzle sizes, as HVLP and RP and in standard or digital versions:
• SATAjet X 5500 HVLP 1,3 I
• SATAjet X 5500 HVLP 1,3 O
• SATAjet X 5500 HVLP 1,4 I
• SATAjet X 5500 HVLP 1,4 O
• SATAjet X 5500 RP 1,3 I
• SATAjet X 5500 RP 1,3 O
• SATAjet X 5500 RP 1,1 I
• SATAjet X 5500 RP 1,1 O
• SATAjet X 5500 RP 1,2 I
• SATAjet X 5500 RP 1,2 O.
Visitors of the Automechanika trade fair, that took place from 13th to 17th September 2022 in Frankfurt (Germany), were able to test the SATAjet X 5500 FUTURE spray guns at the booth of the company.
For further information: www.sata.com
The acquisition will strengthen KANSAI HELIOS’ position in the railway and ace coatings sectors.
TheKANSAI HELIOS Group has recently announced that it has completed the acquisition of Westdeutsche Farben GmbH (“wefa”), a German coatings manufacturer. The acquisition realised by their newly set-up group company, KANSAI HELIOS Wefa, based in Essen, includes all assets, business activities, brands and employees. “This acquisition is an important step in the growth strategy of the KANSAI HELIOS Group, which will strengthen its presence in Germany. The group will serve the market as a system supplier with the combined strength of two production units, each specialized in their respective areas: KANSAI HELIOS Germany GmbH in Buchholz-Mendt and the new company in Essen,” has declared Dietmar Jost, the executive director of the KANSAI HELIOS Group. The acquisition will allow the company to strengthen its position within the European railway and ACE industry
and other industrial coatings segments as well, thanks to wefa’s decades of experience with water-based Robertcoatings.Scramm, the owner of wefa, will also be one of the managing directors of KANSAI HELIOS Wefa: “This step is a milestone in wefa´s almost 100-year history.
Founded as a family company, the brand has now made it into the ranks of the top European coating brands. As a new member of KANSAI HELIOS, we will benefit from additional experience and know-how within the group. This is a win for wefa and vice versa as our specialized coating formulations complete the new owner’s product range and ensure the highest product quality for a wide range of applications, especially for the railway industry.”
For further www.kansaihelios-wefa.deinformation:
Joe Powder comes back again on this issue to answer questions about the everyday challenges of coaters around the world.
Dear Sir, Can you tell me please in corona charging gun how powder will charge? Is it charged with electrode? I mean flat jet nozzle or round jet nozzle?
Greetings Shahroz, How are things in Pakistan? Your question is a good one. Basically, the electrostatic charge in a corona type powder spray gun is created by ionizing air. The high voltage at the gun tip electrode pulls electrons off air molecules (N2, O2, etc.) which results in a field of negative charge. This electric field converges on the earthed target. The deposition of powder is accomplished by passing a cloud of particles through the electric field. The particles pick up electrons as they traverse through the field.
Interior corners of box shaped parts can be a challenge to penetrate with charged powder. A good earth is important for best transfer efficiency.These negatively charged particles are attracted to the conductive surface if it is adequately connected to earth. As the negatively charged particles accumulate on the surface of the substrate negative charge leaves the substrate to earth. The loss of negative charge at the surface creates a net positive charge at the interface. This positive face charge secures the negatively charged powder to the surface. The nozzle type affects the manner in which the powder cloud exits the spray gun. It has only minimal effect, if any, on the charging characteristics of the powder.
I hope this helps answer your question.
Best regards, Joe
Dear Joe, Hope you are fine. What is your recommendation to guarantee an adhesion of powder paint for surface “hotdip zinc coating’’?
Best BPC,OzlemregardsEkinciTurkey
Dear Ozlem,
Life is good for me lately. We are enjoying the fall with many celebrations with family and friends. Lots of wonderful cooking and some pleasant drinks as well. I hope life is good for you also.
As for your question - this is a difficult one. One of the biggest issues is the variability in the quality of the hot dipped galvanized (HDG). It can be very inconsistent not only from batch to batch of HDG but also on different sections of the same part coated with HDG. What I recommend is first careful cleaning of the surface. This can be an alkaline cleaner followed by a good quality rinse. You may also want to consider media blasting as well, however this adds cost to the process. As for adhesion - some powder coatings work better than others. A good quality epoxy will adhere better to HDG than a polyester powder. Hybrids (epoxypolyester) fall somewhere in between. If this is for an outdoor durable application you need to either use a zinc phosphate pre-treatment with the polyester or the combination of an epoxy primer followed by the polyester topcoat. Also it is important to de-gas the HDG prior to applying the powder coating. Otherwise, you may observe pinholes in the coating. De-gassing involves preheating the HDG and applying the powder to the warm substrate. Preheating to 150 to 175°C usually suffices.
I hope that this helps answer your question. Kind regards, Joe
Hi Joe,
I am James the Quality Technician from a finishing house in Northern Ireland. I am currently in the process of doing some R and D with powder coating on top of chilled iron grit blasted material and we are currently experiencing problems. I thought you might have a good knowledge of the subject after reading your Q&A’s with other powder coaters.
The system we have in place is the SA 2.5 grit blasting then coated with APP120 (a zinc-rich primer) and cured at 180° C for 30 minutes. However, after this stage the top coat refuses to adhere to the primed substrate and when it does it generally “stars up” during spraying. I have tried spraying it hot (metal temp greater than 150°C), changing cure times for the primer (shorter bakes at higher temps), lowering gun kV’s and changing the base primer but none of it gets satisfactory results.
As a full-range supplier, we design and manufacture shot blasting machines including filter and transport technology. shot blast machines Second
I was just wondering if there was anything basic that I could be missing or a variable that I have overlooked in order to give better results. I understand if you aren’t willing to divulge such information and if you have any questions for me, please do not hesitate to ask.
Kind Jamesregards,Breen, BSc Bio Med Quality Technician - Northern Ireland
your question and it’s great to hear from Northern Ireland. I hope all is well in Newtownabbey. It sounds like you’re getting rather frustrated in getting good parts off your finishing line. You are wise to select the materials and process you are trying to make work. Blasting the metal is a good idea and the dual coat approach gives a very durable finish. To make this work, the devil is in the details.
The biggest problem seems to be getting a good second coat on these primed parts. The first place to investigate is “are you getting a good earth to your parts?” If you are seeing starring and poor film build, you probably have poor electrical continuity to the earth. Checking for earth requires a megohmmeter which not only measures resistance but also provides up to 500VDC which helps define resistance more accurately. You want to have 1 megohm or less resistance. If it is greater than 1 megohm start looking for poor contact points including hooks, hangers, racks and conveyors.
Regarding the powders I would stick with the original powders and work on the application process. It is wise to undercure (or “gel”) the primer prior to applying the second coat then fully bake the two coats. This provides the best inter-coat adhesion.
I hope this helps. Please let me know if you have any further questions. Warm regards, Joe Powder
world is marked by sudden and unpredictable changes and moving at a rapid pace towards an increasingly digital ecosystem. This led us to rethink our annual Trade Show Calendar, listing the main events to be held in the surface treatment industry. We chose to better meet the sector’s need by approaching our calendar in a new way and transforming what was previously a digital and printed brochure into a web app accessible from any device: myFAIR.
A web app is a versatile tool that can be accessed from both desktop and mobile devices, which does not require downloading from the store. Nevertheless, it is possible to create a shortcut directly in the smartphone menu, making access to the app quick and easy.
myFAIR is therefore a free, up-to-date, and highly interactive tool at the service of professionals in the surface treatment industry (and beyond) for the organisation of their trade fair agenda, both as exhibitors and visitors. Through the myFAIR web app, users can browse, filter, add to favourites, trigger alerts, and get up-to-date information on the world’s most important events happening in the industrial finishing sector.
The Exhibitions section shows all trade fairs in alphabetical order. The list can be filtered by country and category. It is also possible to type the name of an exhibition directly into the search bar for even faster access to information on a particular event. Tapping on the name of a trade fair takes the user to the specific tab
The ipcm® team is pleased to present myFAIR, a new web app to stay up-to-date with all major events happening in the surface treatment industry.The Exhibitions section with the (filterable) list of all trade fairs in the app and the trade fair tab with detailed and up-to-date information on each event. The Schedule section, showing all trade fairs divided by month.
for that event, with up-to-date information on dates, location, focus, and website. From here, it is also possible to get directions to the event location directly on Google Maps and add the trade fair to favourites, in order to receive alerts in case of new updates. There is also a list of related trade fairs by sector.
The Schedule section allows filtering the trade fairs by month and year. This is an easy way to organise one’s schedule on a monthly basis and check which exhibitions are going to be held in a particular month with a few Here,touches.too,itis possible to apply additional country and product category filters.
The Suppliers section presents a list of suppliers of various services that revolve around the world of trade fairs: from catering to stand construction, from translations to hostess and steward services, from communication to digital printing, from gadget creation to logistics. Companies can be filtered according to the services offered and a simple tap takes the user to a detailed tab with the main contact information.
myFAIR it is not only a useful tool for organising ones’ own trade fair calendar. It also offers an interesting opportunity for companies to promote themselves to a highly specialised target group, under the aegis of the prestigious ipcm® brand.
The providers of services for exhibitors have a dedicated section where they can upload their company profile and contact information. Exhibitors, visitors, and trade fair organisations can rely on three display advertising options to promote their business.
For further information: sales@ipcm.it
The Suppliers section is dedicated to all companies that offer services revolving around the world of trade fairs, such as stand construction or gadget creation.
Dürrhas launched the latest software tool from the DXQanalyze product family: DXQplant.analytics, which helps paint shop operators to improve production quality and effectiveness by detecting – through AI algorithms and data-driven machine learning –systematic fault patterns and their causes early.
The basis of DXQplant.analytics is quality information recorded digitally for each workpiece during the surface inspection. In addition, process parameters, alarms, and anomalies from the individual processing steps supplement the workpiece-related data records. This creates a digital file for each body that models the entire production and life cycle, including any faults found. Machine learning can help identify patterns and
correlations in data records. If there are frequent contaminants in the paint, the software will detect this and immediately assign information about the underlying cause to the fault pattern.
With the Advanced Analytics module, the first market-ready AI application for paint shops, DXQplant.analytics has access to a wealth of data for fault analysis.
The software can then detect whether the fault is a one-time or systematic issue, making it possible to analyze systematic production quality deficiencies and quickly identify and fix their causes. Simplified detection and cause analysis make it possible to avoid the fault in the future.
DXQplant.analytics also provides graphics and automatically generated reports to share with colleagues, workers, and management. Integrated documentation functions allow the DXQplant.analytics user to save and manage defined optimization measures and track their impact on quality. Therefore, DXQplant. analytics helps the paint shop operator increase the first-run rate in a targeted way, thus boosting overall equipment effectiveness.
To use and maintain these digital solutions, Dürr also offers DXQsupport, a comprehensive service package to provide support for the entire software life cycle, thus increasing availability, performance and quality.
In addition to regular updates, Dürr offers a team of experts who constantly monitor live production activity to react quickly in the event of failures or irregularities. These services are complemented by a comprehensive modular training catalog, allowing operators to leverage the full potential of their digital portfolio.
For further information: www.durr.com
TheCoating Additives business line of Evonik has launched COATINO® Defect Detection (CDD), a new tool for the digital analysis of coated test samples that precisely and objectively detects and evaluates coating defects, delivering quantifiable results within few seconds.
Usually, when developing a new formulation, laboratory personnel used to rely on samples which had to be carefully compared and evaluated visually. This routine work was then very time-consuming, especially for larger test series.
The COATINO Defect Detection allows laboratory experts to save a lot of time by using a camera connected to the computer to photograph the coated samples. Within seconds the tool assesses them, using innovative image recognition methods.
“COATINO Defect Detection simplifies our customers’ daily laboratory routine and frees them up for other important tasks. In addition, our digital solution delivers objectively reproducible results. This means that the evaluation of test samples no longer depends on the subjective assessment of laboratory
personnel,” has stated Oliver Kröhl, the head of Strategic Business Development at Evonik Coating Additives.
The new tool developed by Evonik, which is part of the COATINO formulation network, evaluates coating defects to an accuracy of a tenth of a percent. The application is browserbased, so there is no need to install the software on the lab computers. The test series are documented in the system and can be retrieved at any time. In addition, an integrated help centre provides detailed answers to all questions regarding the required hardware or individual application steps.
“For example, you can immediately see what percentage of the surface is affected by foam. Reference formulations or blank samples can also be added to more clearly highlight the performance of the tested formulations. Based on the data, you can select the best formulation for the specific application,” clarifies Philipp Isken, head of COATINO Product Development.
The digital analysis tool was initially developed for pigmented systems in the architectural sector. The Coating Additives business line of Evonik plans to add more industries and defect types to it and, in the next stage of development, the CDD will also independently suggest new formulations.
For further www.coatino.cominformation:
Since the merger of Malvern and Panalytical in 2017, the analytical instruments company that prides itself on a customer centric approach, has been consolidating its solutions portfolio to deepen ties to the paints and coatings industry.
“Every customer has a slightly different requirement” say Robert van der Meer, director of physical and thermal products. “That is why our analytical systems are provided in deep technical consultation with customers and that’s why we have the greatest range in sample handling options. Our customers might want to measure particle size in a slurry
or a dispersion, a spray, or a powder. In addition to the market leading Mastersizer 3000 for particle sizing using laser diffraction, we have a wide range of systems for measuring micro and nano-particle sizes and shapes. A wide portfolio gives the customer choice in how to satisfy their analytical needs at each stage of their product development and manufacture”. The merger has brought multiple analytical technologies under one roof and, nearly every Malvern Panalytical system has a role to play in the analytical value chain for paints and coatings. X-ray diffraction (XRD) solutions enable a deeper understanding of pigment mineral phases, amorphous to crystalline ratio and the ratios of polymorphs (e.g., rutile to anatase in TiO2). X-ray fluorescence (XRF) is used for elemental analysis which can also screen for mineral composition and the presence of ppm quantities of toxins such as lead. Both X-ray technologies offer numerous measurements for thin films and coatings.
Says segment marketing manager Patricia Kidd: “We are all now aligning our personal and corporate aims to be more sustainable in the way we operate. End customer choice and our sustainability aims drive innovation, and our customers are busy implementing sustainability into their products. Changing any components in a complex formulation is a risk, and requires rigorous pre-test and analysis. If you think you need help with something, talk to us!”.
For further information: www.malvernpanalytical.com
Paint wastes are often ‘sticky’ or ‘tacky’ and are very difficult to remove or separate from water streams that are often used to catch the over-spray. Atotech presents its KleerAid® EZ Treat 2.0 technology which improves the handling of existing over-spray and the detackification process.
Paintoverspray treatment is frequently a challenge for wet paint applicators. The procedure typically involves excessive cleaning due to incomplete detackification of solvent-based paints. When water-based paints are mixed into the same system it often results in unpleasant odour, excessive foam generation, and sludge with high water content. These burdens impact cleaning and maintenance operations and can be a source of increased paint defect rates when water circulation systems are no longer able to carry out their dust control function.
The easiest way to high-performance paint overspray treatment
KleerAid® EZ Treat 2.0 is a sustainable, efficient, and cost-effective paint-overspray treatment process that addresses common challenges associated with paint detackification: it reduces the stickiness of paint sludge, generates a lower quantity of waste, improves the overall system cleanliness, and reduces foam generation.
The robust KleerAid® EZ Treat 2.0 solution is highly versatile and suitable for the most demanding configurations and is therefore the
Flocculated paint accumulating during the paint overspray treatment process.ideal solution for automotive OEM and Tier 1 paint applicators. The process, designed to efficiently treat waterborne, solvent-borne, and mixed paint systems, contains only two products, a coagulant and a detackifier. KleerAid® EZ Treat 2.0 ensures easy water parameter control and consistent paint sludge quality.
Cost-effective and environmentally sound paint overspray treatment
Compared to conventional products, KleerAid® EZ Treat 2.0 provides improved water properties and sludge quality by eliminating paint stickiness even for high solid paints. It substantially reduces the chemical oxygen demand (COD) and stabilizes parameters such as total suspended solids, sludge water content, and dissolved oxygen. The collected paint sludge’s low water content reduces waste disposal costs and decreases environmental impact. KleerAid® EZ Treat 2.0 technology also addresses odour issues and eliminates the need for biocides and other toxic and hazardous products.
Superior detackification provided by the process prevents sludge accumulation in the paint booths and sluiceways, which reduces the service and maintenance requirement for equipment cleaning and improves water clarity. The process streamlines the dosing procedure and reduces chemical consumption by up to 60%.
It allows for greater treatment flexibility and
reduces the need for extra additives. Thus, KleerAid® EZ Treat 2.0 simplifies the treatment significantly, leading to significant savings in the paint-overspray process.
In addition, KleerAid® EZ Treat 2.0 is an easy and effective way to save on labour and maintenance while improving sustainability and reducing costs by minimizing water consumption and waste generation resulting in a reduced environmental footprint.
• Easy to use two component solution
• Suitable for waterborne, solvent-borne, and mixed paint systems
• Sustainable process decreasing waste disposal
• Eliminates use of biocides and other toxic products
• Improves sludge quality, resulting in reduced sludge quantity and associated disposal costs
• Eliminates associated unpleasant odours
• Reduces chemistry consumption by up to 60%
• Cost-effective, efficient, low service requirements, low maintenance.
North America’s Largest Metal Forming, Fabricating, Welding and Finishing Event
Discover innovative solutions, gain insights on opportunities and trends transforming the industry, and make connections that count. From interactive demos on the show floor to impromptu conversations with colleagues, there’s nothing quite like the FABTECH experience.
KleerAid ® EZ Treat 2.0 is designed to provide the most efficient, powerful, and consistent paint detackification in the market today. The high-performing and cost-effective process is environmentally sound and efficiently treats waterborne, solvent-borne and mixed paint systems. The process improves paint sludge quality by eliminating stickiness and increasing flotation rate, even with high solid paint.
KleerAid ® EZ Treat 2.0 provides consistent water parameters (pH, TSS, COD) while reducing maintenance and equipment cleaning requirements. It also addresses typical odor issues without using biocides, toxic or hazardous products. towards
CORTIZO Enriches its Coating Plant Equipment with a High-Productivity Vertical System Installed in a Fully productivity which includes all the latest developed by brusher, made of a better resistance to - the vision system that coating booth, automatic these are, in summary, the characteristics of the by in Padrón, which brings to 7 the vertical lines installed the
It is pronounced CORTIZO, but it means CORTIZOALUMINIUM.ispositioned as the first manufacturer and distributor of exclusive aluminium and PVC systems for architecture and the industry in the Iberian Peninsula and as a benchmark at the European level. This Spanish company based in Padrón (Galicia, Spain) is one of the undisputed leaders of the aluminium industry, in which it stands out from competitors thanks to its ability to directly handle its entire production cycle: casting, extrusion, coating, oxidation, polishing, machining, packaging, storage, and distribution. This makes CORTIZO’s presence also very strong throughout Europe, where exports are growing steadily, with the American market now also opening up.
With 9 production centres and 31 delegations all over Europe, a presence in 60 countries, and almost 3900 employees, the Spanish company’s production capacity reaches 150,000 T/year, of which 74,000 are produced in its headquarters in Padrón, in the verdant region that is home to the famous city Santiago de Compostela. The headquarters, in particular, is currently equipped with 1 foundry, 9 extrusion presses, 5 vertical and horizontal powder coating lines, 2 anodising plants, 2 chemical polishing plants, countless plants for profile machining, 2 smart automatic warehouses, a technology centre, and a logistics area. In its three-year strategic plan 2017-2020, CORTIZO had earmarked an investment of 87 million Euros to increase its production and logistics capacity. Of these, 17 million Euros were destined for the main factory in Padrón where, over the course of five years, 2 new extrusion presses were put into operation, of which one has a power of 2500 tonnes and is fully automated and capable of producing up to 6000 tonnes/year of profiles and the second is a 4500-tonne system for the production of large profiles, both housed in a newly built plant.
The plan also included the installation of 1 new vertical coating line and 1 new chemical polishing one. In 2021, the company further expanded the production capacity of the Padrón factory by adding 2 more presses, 1 vertical and 1 horizontal coating line, and packaging, assembly, and plasticisation lines in a newly built plant with a covered area of around 23,000 m2. Here, the mentioned production lines are totally connected to each other by a complex automatic logistics system with overhead cranes and storage buffers, which eliminates any unnecessary human handling of profiles.
The vertical coating system installed in this plant, in particular, is a high flexibility vertical line supplied by SAT (Verona, Italy). Developed to meet the need for maximum painting flexibility, SAT’s line is a smart system that optimises the aluminium finishing process in order to meet the growing requirements for repeatability and high productivity in the coating industry, thanks to its advanced technological components.
“The plant where we installed our SAT line houses a closed-loop, self-sufficient, and fully interconnected production process, starting with extrusion and ending with plasticisation and assembly of the thermal bridge break,” says Alberto Freire Nande, the communication manager of CORTIZO. “This 20 million Euros investment was started about a year ago, when the previous five-year development plan came to an end.
The fan-shaped loading area. The only manual operation is the insertion of the hanging hooks into the profiles to be Thepainted.brushing machine at work.
“The profiles come from the 2 new extrusion presses: the “cages”, or trays, containing them automatically reach the heat-treatment ovens for material hardening, and then an intermediate warehouse that takes care of the distribution of the profiles towards the subsequent production lines, that is, coating, assembly, packaging, and plasticisation, via overhead cranes. In addition to the 2 new presses, this investment included the installation of a vertical coating line to which 2 more are going to be added: a horizontal one for nonstandard profiles and a new vertical one to be also supplied by SAT. Finally, this part of our factory includes 3 automatic warehouses for powder coatings.”
The vertical profile coating line’s cycle “The logistics system connecting one production stage to the other consists of overhead cranes that handle the material arranged on the trays. After extrusion, the profiles are stored in a vertical warehouse. When an order is entered into our management software programme, the system picks up the tray containing the matching profiles and takes it to the paint shop’s feed roller conveyor, where the profiles are unloaded by rows and hung onto the line by the operators. Indeed, the only operation in this entire logistical process that requires human intervention is the insertion of hanging hooks,” says José Labandeira, the production manager of this new CORTIZO plant. “The line paints profiles up to 7.5 metres and it integrates all of SAT’s most important technological innovations. The first one is the automatic brushing machine, which performs a mechanical pre-treatment process prior to the traditional chemical one, in order to remove any extrusion defects from profiles and thus produce higher quality surfaces. We have been the first SAT customer to integrate a brushing machine, first at our Slovakian, French and Manzanares (Ciudad Real) sites, then at our Spanish plants in Canarias, Cervera and in Poland, now here in
“ThePadrón.”chemical pre-treatment phase includes an acid stage with its rinse, an alkaline stage with its rinse, a pickling stage with its rinse, and a final conversion stage with its rinse using demineralised water,” indicates José Labandeira. “This is the first line provided with a pretreatment tunnel entirely made of polypropylene, a material which guarantees many advantages: resistance to aggressive chemicals, thermal isolation, an improved aspiration system. Each stage is double, in order to achieve better pre-treatment quality. After drying, the profiles proceed to the two C-Expert spray booths, one for dark colours and the other for light colours, which incorporate another SAT’s technological innovation: the VISICOAT profile vision system. A picture of the incoming profile appears on the booth’s control panel: automatically, the booth and its application equipment set the correct coating parameters, i.e. speed, amount of powder dispensed, distance of the guns from the profiles, tension applied, and so on. Of
course, we previously entered data for each type of profile we produce, so that the vision system can compare the incoming part to the database “Applicationinformation.”is
done through OptiSpray 01 pumps with Gema SmartInLine – Technology. This is the first time CORTIZO uses dense phase feeding equipment,” notes José Labandeira. “All the other coating plants we own here in Padrón and in our other eight production centres use Venturi injector technology. Based on our first application experiences, I must say that the result is much better. We still have to check whether maintenance is really so minimal as to justify such a significantly higher SAT’sinvestment.”planthas an impressive capacity at full three-shift operation: 50 tonnes per day. At the moment, 7-8 colour change operations are performed per day, which is a higher number than what will be the average for the plant once full capacity is reached. The plant was designed for very large batches and very high productivity levels.
At the end of the coating cycle and after curing, the profiles reach the unloading platform, featuring SAT’s fourth innovation, i.e. the automatic profile offload system. After unloading and placing the profiles on the transport trays, the factory’s logistics system separates the coated
material into three different storage buffers that feed the assembly, plasticisation, and packaging lines respectively.
The trays are always called up automatically to proceed to the next processing step. “Storage buffers are crucial because the coating line has a much higher productivity than the three systems that follow it, so they prevent the trays destined for the different lines from mixing up,” explains José Labandeira
Analysis of the innovative elements integrated in CORTIZO’s plant VISICOAT
The unique Vision Recognition System developed specifically for vertical coating lines introduces the AI to control the aluminium profile coating process. Thanks to close collaboration between SAT and Gema, VISICOAT is able to recognise the cross section of the profiles, and perform the coating process autonomously through a sophisticated AI solution.
It is a cutting-edge technology able to manage profiles of any shape, weight and length in an easier and more efficient way. It uses five
Profiles exiting the pre-treatment tunnel. Coated profiles exiting the polimerization oven.helical belts or conveyors to transit the aluminium extrusions from the vertical to the horizontal position for the unloading. Once the aluminium profiles reach the horizontal position, they are moved to the motorised unloading table for handling. This five belts unloading system is designed to process extruded aluminium profiles between 2 meters and 8 meters length. The Automated Unloader allows the customer to offload extrusions from their vertical powder coating system without adjusting the position of the unload system. The Automated Unloader is able to eliminate the gaps between the extrusions on the line and to minimise marring and bending of the parts as they move along the vertical curve of the conveyor.
The new Vertical Brushing Machine is placed in-line prior to the entrance of the chemical pre-treatment tunnel. The aim of THE BRUSHER is to operate a mechanical pre-treatment of profiles surface. There are three main advantages guaranteed by a mechanical treatment before the chemical one:
• THE BRUSHER removes a relevant part of the aluminium particles (chips) or dirtiness coming from the extrusion process or from a nonideal storage, drastically reducing the incidence of surface defects.
• THE BRUSHER permits to scratch the profile surface, increasing the overall surface of the profile and allowing a more thorough chemical attack. This means the possibility of reducing the chemical concentration inside the tank or reducing the time of contact: in any case, it reduces the consumption of chemicals into the pre-treatment tunnel.
• THE BRUSHER increases the grip of powder on the aluminium surface, guaranteeing outstanding adherence performances.
Thanks to the 3 pairs of brushes, the mechanical action intensity can be adjusted according to the desired result (varying the Round Per Minute of the brushes and their vertical speed).
It is the new Vertical Powder Booth. Its main characteristics are:
• Complete integration with GEMA CM 4.0
• Enhanced coating penetration in difficult recesses, also at a high conveyor speed
• Developed specifically to work with Visi1 Vision System
• Quick colour change
• Openable cyclone (optional).
Cortizo: historic sales record in 2021
In 2021, the group founded by Manuel Cortizo Soñora reached a 47% higher turnover than before the Covid pandemic. Internationalisation
certainly played a key role in this success, since exports to Europe account for almost 60% of the Group’s sales and exports to Americas for a small further percentage.
The mammoth investments made over the past six years have also certainly driven this growth. Currently, the CORTIZO Group owns 17 coating lines, including 2 horizontal systems installed in Padrón, 1 in Romania, 1 in Portugal, 1 in Poland and 1 in Slovakia, and 8 vertical ones. SAT supplied 7 of these, no less.
“SAT is able to provide cutting-edge technology in line with our philosophy: for all our factories, we look for suppliers that share our approach to automation, digitisation, Industry 4.0, and of course sustainability,” states Alberto Freire.
Operating in the construction market since 1988 as a leader in the design and manufacture of false ceilings and metal cladding for the architectural market, Atena is a multi-market, multi-product, and multi-channel company whose business model focuses on three strengths: flexibility, diversification, and autonomy. In the context of a wide-ranging investment programme launched in 2021, it implemented a series of Industry 4.0-oriented upgrades, including the purchase of state-of-the-art metalworking machinery and the installation of a latestgeneration plant for recovery, filtration, and recirculation of the waste water generated by the coating process. This was supplied by Avin (San Martino al Tagliamento, Pordenone, Italy) and uses chemicals developed by NoxorSokem (Cusano di Zoppola, Pordenone).
Atena’s plant in Gruaro (Venice, Italy) is a state-of-the-art production site, home to four business units specialising in the design and production of metal ceilings, architectural façade cladding, naval fittings, and drywall systems. All its production processes take place here, from coil and sheet metal cutting to metal finishing.
The Jesolo Museum, the headquarters of Ote (a leading German telecommunications company), Apple in Israel, Samsung in Slovakia, the Tel Aviv metro station, Balenciaga’s stores in Italy, Holland, Morocco, and Spain, and the Tenerife Airport were among its most recent customers, as well as Duka in Bressanone, Sanofi in Panama, and Hotel Monaco and
After two years of pandemic, its turnover in 2021 increased by 44% to over 44 million Euros. Such a growth was confirmed by turnover and order book trends in the first half of 2022. One of the keys to this company’s success is the sound and consistent investment programme that president and owner Mauro Barbuio has carried out over the years to upgrade plants, equipment, and production sites in order to make Atena independent in terms of both design and production. Every process is indeed performed at the Gruaro plant, the company’s headquarters housing all staff activities. Fast, in-house design and quality control processes as well as a very short production chain are also important competitive factors, because they guarantee the company’s autonomy from the markets and encourage innovation through the input and contamination it receives from the different segments in which it operates.
This was the background to the investment plan launched in 2021, which included measures to improve Atena’s production system and reduce both the cost and the environmental impact of its processes. The jewel in the crown of this development programme was the construction of a new industrial building adjacent to the Gruaro production site. The plant occupies an area of about 14,000 m2, of which 3,000 are covered. It is an autonomous production, storage, and distribution centre
powered by a photovoltaic plant, totally interconnected and automated with remote control and monitoring systems for all processes, including even the photovoltaic plant and transformer room. The ambitious Industry 4.0 programme involved, among other measures, the purchase of a series of metalworking machinery and the installation of a new generation plant for the recovery, filtration, and recirculation of coating waste water.
For the latter project, Atena relied on the expertise of two Italian companies specialising in surface treatments, Avin and NoxorSokem. Avin developed the plant engineering aspects and NoxorSokem stepped in for the chemical ones, working together to implement a zero liquid discharge physical-chemical treatment process allowing recovered water to be reused in the pre-treatment station. Indeed, the combination of these two firm’s expertise guarantees the creation of water treatment systems that are highly digitised and tailored to the specific needs of the customer, the characteristics of the processes carried out, and the performance of the existing pre-treatment plants.
The waste water treatment plant developed by Avin and NoxorSokem can work with a total continuous flow rate of up to 800 L/h. The system includes a storage tank for rinsing water, which is kept ever fresh through a continuous-flow operation, and a tank for storing concentrates. Through a physical-chemical process, the water to be treated is conveyed to the first storage section through a pumping system, where it decants before reaching the deoiling stage. The deoiled water is fed into the third station, where it is biologically purified before reaching the accumulation and pumping tank. It is then sent to the final clarification section to remove any impurities remained after sedimentation. Backwashing of the clarification column and activated carbon is then carried out with filtered water. Afterwards, the recovered water is recirculated into the system for cleaning the parts to be coated, thus avoiding disposal costs and the continuous formation of waste water. In other words, this high-performance system helps reduce waste and optimise the economic impact of water disposal, while protecting the environment against the release of harmful “Togetherelements.withAvin and NoxorSokem,” explains Monica Jogna Prat, Atena’s Facility Manager and Quality and Certification Manager, “we identified the physical-chemical process best suited to our needs. Specifically, in order to determine the degree of pollutant abatement, we performed a number treatment tests at the Noxor laboratory, followed by a series of technical analyses. Avin then took care of the
process’ integration with our existing pre-treatment phase and of the digital management and monitoring of operating parameters. From the start-up phase onwards, NoxorSokem also offered us a scheduled assistance service aimed at guaranteeing the best conditions for plant operation, through dedicated technical support and periodic analyses of waste water before and after purification.”
“Atena’s pre-treatment system,” says Avin CEO Morgan Infanti, “had a significant matter with the degreasing product being dragged into the subsequent processing tanks. This was especially due to the properties of the treated parts, which have wide surfaces characterised by the presence of micro holes. In some cases, this caused peeling of the products’ metal surfaces. The installation of the new water treatment system, with the chemicals developed by NoxorSokem to be suitable for an alkaline-bath process such as the one in use at Atena, has stabilised the coating quality degree, in terms of both adhesion and salt spray resistance. The active bath is constantly renewed, discharge is controlled, and an alarm system enables deviating parameters to be corrected in real time before generating any production scrap.”
For the finishing of its metal surfaces, Atena uses a variety of decorative techniques such as laser cutting, moulding, artistic drilling, nanotechnology coating, sublimation, and state-of-the-art digital printing, which enable it to faithful reproduce images and imitate natural materials such as wood, marble, weathering steel, and aged
The WWT system’s control panel and the pre-treatment tunnel.metal. “We perform all our processing operations in our Italian plant,” indicates Monica Jogna Prat, “which also houses our ever-evolving coating department, where we only use VOC-free inks and substances and operate with ultra-high resolution images and precise control metrics.
For the coating of metal surfaces, we utilise Qualicoat 1 and 2 certified paints, NCS-compliant powders, sample colours, and products with special functions, such as antibacterial or textured finishes. The performance level of our sublimation, digital printing, and coating processes has also been certified for the marine sector, where excellent technical quality, fire and corrosion resistance, and durability are required. For both powder coatings and printing inks, therefore, the choice of supplier depends on every specific project’s requirements.”
Aiming at running an increasingly sustainable business, Atena manufactures all its products using energy from renewable sources and recycled and recyclable materials with a high durability degree. At the end of their life cycle, Atena’s products become non-hazardous waste and they can be subjected to selective demolition, recycling, or reuse. Mapped in compliance with the new Leed V4.1 protocol, they comply with C.A.M. requirements and they have earned Type III Environmental Product Declarations (EPDs). Atena’s headquarters is totally powered by renewable sources, through both the purchase of certified energy and the photovoltaic plant’s production, now reaching 1 GWh.
“The objectives we set ourselves,” states Mauro Barbuio, “are the result of a pragmatic vision closely linked to the dynamics of an ever-changing market. Like everyone else, we operate within macroeconomic scenarios that are increasingly complex and characterised by accelerating disruption throughout the supply chain, which calls for flexibility and speed of adaptation – but we are ready to cope with these new dynamics.”
Some Atena’s department.
The booth.
Alessia
With forty years of experience in the aluminium profile sector, the Aluminios Galisur – Proylac companies are very familiar with the requirements of the industry. That is why they spent four years completely revolutionising the production logistics of their Seville factory and investing in new, much more efficient machinery and production lines. This led Proylac to install a new vertical profile coating line supplied by Euroimpianti, which more than doubled productivity and halved natural resources consumption.
SPECIAL ISSUE ON ALUMINIUM A pergola built with Proylac’s aluminium profiles.Withthe energy costs for gas and electricity continually rising in a race that seems to have no end, making investments that focus on energy efficiency and the saving of resources and materials is simply crucial. In some cases, this requirement is closely related to the need to completely revolutionise the production organisation of a company, for instance with the aim of improving its production flow, minimising logistics and material handling, and bringing order to the various manufacturing stages. This is especially the case when there is a (wanted or forced) generational change at the helm of a company. That is exactly what happened to Protecciones y Lacados S.L. (Alcalá de Guadaíra, Seville, Spain), a company specialising in the extrusion, coating, and anodising of aluminium profiles for architecture and the industry that, together with Aluminios Galisur S.L., constitutes the López Conde family’s group of companies, now led by Jesús López Conde, the founder’s son.
Indeed, a multi-million Euro investment programme that started four years ago has totally revolutionised its production organisation, in terms of not only efficiency but also productivity. In particular, by investing in two coating systems supplied by Euroimpianti – a carousel plant in 2019 and a newly developed vertical plant at the end of 2021, which replaced the old one – Proylac achieved an 80% improvement in the vertical painting of profiles and an improvement of up to 50% in the horizontal painting of sheet metal and small colour batches, while almost halving consumption of energy resources and completely automating all production steps. “In my father’s time, the concept of industrial development was related to maximising productivity, perhaps by investing in machinery that was oversized also in terms of energy consumption and power,” says Jesús López Conde. “However, at Proylac, we have strived to invest in plants that were energy efficient and
electrically powered wherever possible, in order to utilise the energy provided by the solar panels covering the roof of our factory.”
Over forty years in the aluminium profile industry Aluminios Galisur S.L. began its activity in 1978 in Seville, distributing aluminium profiles and accessories for the aluminium metalwork sector. It thus penetrated the southern part of Spain, which was still not very industrialised back then. “My father started working as a salesman in an aluminium sales company called La Viuda del Tornante, in Alicante. He was responsible for the area of Seville, Cadiz, and Badajoz. In a short time, he became the employee who sold the most aluminium,” recalls Jesús López Conde. “In 1978, he decided to open his own warehouse in Seville: Aluminios Galisur was established in a 150 m2 building to distribute aluminium for Enespan, the state-owned aluminium industry. The company grew very well and, in the early 1980s, he decided to move to Alcalá de Guadaíra and acquire a coating company, called Protecciones y Lacados (Proylac), which was based there: this is how the industrial activity of Aluminios Galisur began.
“That was a period of economic boom in Spain, thanks to the transition from dictatorship to democracy and the entry into the European Union in 1986. Much was built in those years and the architecture and aluminium sector grew very rapidly. That is why my father and his business partner at the time decided to launch their own aluminium systems for architecture and thus expand the production of Proylac –whose first customer was, and still is, Aluminios Galisur – with extrusion operations using proprietary dies. In 1984, they purchased their first extrusion press and, one investment after another, by 2000 the plant was already complete, with three extrusion presses and a vertical coating plant. It was then that the two partners decided to separate;
One of the extrusion presses and the dies warehouse.my family kept both brands, Protecciones y Lacados and Aluminios Galisur.”
“My father died of a sudden illness in 2016 and I took over as head of the company. The crisis period of 2008 had been quite severe and lasted until early 2014, when we started to see an improvement in the market. The company was still financially healthy, but it had not invested in technologies for eight or nine years. In order to be competitive in the global market, we had to invest in technology and reorganise the production flow more efficiently. Proylac had grown by acquiring different buildings and Galisur’s warehouse was right in the middle of the factory: production did not have the right logistics flow and there was excessive handling of materials among production departments. We therefore decided to make a switch: Galisur was assigned a 5,000 m2-wide area and kept the warehouse in a central location, whereas Proylac was assigned a 12,000 m2-wide (now 20,000) production area, where we were able to organise in-line operations logically and transferred some machinery from a factory we had in Murcia (Extrusionados Levante).”
Currently, the production structure of the GP (Galisur-Proylac) Group is organised as follows:
• an extrusion department with two 7-inch presses, one of which is equipped with a water-cooling system and is designed for heavier profiles and alloys requiring more cooling;
• a die department for the preparation and grinding of extrusion dies;
• a die warehouse with 5,000 active product codes, both proprietary and customer-owned;
• a nitriding department with two ovens, a shot blasting machine, and a die cleaning system;
• a coating department with two Euroimpianti lines;
• an anodising department (see next article);
• a sublimation department;
• a thermal bridge breaking and assembly department;
• a department for precision cutting and machining of profiles.
“For the past four years, we have been revolutionising the entire company structure, acquiring new machinery and upgrading old one,” states Manuel Contreras, the quality manager of Proylac.
“The focus of this multi-million Euro investment was the search for more energy-efficient solutions, starting with the factory’s roof, now covered with solar panels to self-power the factory. The presses have a billet heating system that uses residual heat to raise the temperature of the first oven chamber, thus achieving significant energy savings. When choosing the supplier of the coating systems, we selected Euroimpianti because its project was the most convincing one in terms of energy efficiency and, in general, of the excellent use of energy.”
“We saw several Euroimpianti systems and liked their productivity and design levels,” notes López Conde. “Both our carousel and vertical system have a predominantly electrical consumption, which enables us to utilise the energy produced by our solar panels. The
Bringing your surface to perfection. Dürr offers painting solutions from manual to automatic application, high-quality and easy to integrate. www.verind.it
The pre-treatment tunnel.gas-powered curing oven is equipped with a system that recovers residual heat to feed the drying oven. Cascade rinses and very sparing use of water enabled us to reduce water consumption by almost half. Another very important aspect is that Euroimpianti’s vertical plant, which incorporates all this supplier’s latest technologies, has more than doubled the output we achieved with the old system. Today we produce an average of 400-500 profiles per hour with a line speed of 1.7 m/min, which is the value we had requested from Euroimpianti.”
The main features of the vertical coating line “When an extruded profile leaves the cooling table, it is cut to size according to customer requests and sent to the ageing ovens via an automatic stacking system. Afterward, large batches with the same colour, all white batches, and those requiring wood-effect base coats are painted in the vertical system, whereas small and urgent batches are painted in the horizontal one,” explains Manuel Contreras. “We can paint profiles up to 7 metres long with both systems. The vertical plant replaced an old machine that had very limited productivity due to its type of hanging system. Proylac was looking for greater productivity and
efficiency: we found them in Euroimpianti’s technology.”
The vertical line designed by Euroimpianti is equipped with an automatic loading system to prevent excessive profile handling. As soon as it leaves the presses, the material is automatically distributed among the different production departments. The automatic overhead crane reaches the coating plant and lays the profiles on the loading platform where the operators drill them and load them onto the elevator taking them to the pre-treatment baths.
The pre-treatment cycle includes alkaline attack (1 to 2 g/m2 attack), two rinses with osmotic water, neutral acid attack (1 to 2 g/m2 attack), two further rinses with osmotic water, one rinse with demineralised water, and chrome-free passivation. The chemicals used are provided by Alsan – Alvarez Schaer. “All pre-treatment stages are cascaded, but the system is equipped with an atomising ring to clean the material between one stage and another and separate them, so that there is no contamination among them,” explains Manuel Contreras. “In addition, the atomising ring acts as an automatic feeder of clean water to the tanks. Thanks to these technical measures, water consumption has been reduced from 4 to 1.8 m3 per hour. The tanks have an automatic aluminium purging
system that keeps the attack and conversion baths as stable as possible.” After pre-treatment, the profiles are dried using the residual heat recovered from the curing oven: in other words, Euroimpianti’s new system uses the curing oven’s residual heat to power the drying oven, thus achieving significant energy Forsavings.powder
application, the line has two automatic diamondshaped booths, with the guns arranged along a curve. Both booths are equipped for quick colour change operations and they can run simultaneously: one booth applies only white, which accounts for 70% of Proylac’s production, and the other applies all other colours. Each booth has 24 guns and an automatic detection system to adjust the guns’ height according to the bar’s length. Powder is fed with traditional Venturi injectors and each booth is equipped with a powder dosing system for 500 kg bags instead of big bags.
“An advantage of this vertical line is the possibility of coating very small profiles thanks to Euroimpianti’s new thread technology, which allows thinner profiles to be joined so that
The unloading area.
they do not hit each other and remain taut. This automatic system inserts a thread into the lower end of the profile, which breaks at the end of the process thus leaving a very small mark at the bottom of the profile itself,” indicates Manuel Contreras. “The system is completed with a Euroimpianti laser paint stripping system for hooks, an option we preferred to chemical stripping because the laser is also powered by solar panels.”
“At Proylac, we take our customers’ needs into great consideration: very short delivery times and high finishing quality are essential to provide a top service,” states Jesús López Conde. “This is why we decided to invest in a second coating line, this time a horizontal one, which has been in operation for a couple of years now and which initially worked alongside the old vertical plant. Euroimpianti provided us with a carousel system to paint sheet metal and batches of a few bars, i.e. less than 100, which would not be productive or efficient to treat in the vertical plant.
“For the same reason, that is, with the aim of providing our customers with a state-of-the-art service, we decided to invest in an anodising plant, even though my father had always been against its implementation. However, when Alsan, which was already our pre-treatment chemical supplier, introduced us to Anodikit® ZONE, their highly advanced compact anodising plant concept, we had no doubts: that would be our next investment!
Check out the next article to learn more about Proylac’s Anodikit® ZONE project.
The horizontal carousel plant designed by Euroimpianti for finishing small batches and metal sheets.
The carousel system’s booth, powder centre, gun control modules, and filters are mounted on a mobile Donplatform.Jesús López Conde.
Throughout the history of aluminium, many difficulties have prevented the industry’s professionals from entering the world of anodising. The need for high investment, large physical spaces for plants, and qualified personnel, among other factors, have deterred many entrepreneurs from implementing one of the safest and highest quality processes available for protecting and decorating aluminium. In 2020, Alsan – Alvarez Schaer patented ANODIKIT® Zone, a new compact and automatic anodising line allowing this process to be carried out safely while also meeting all Qualanod quality requirements. In this way, Alsan has offered an affordable solution to all those companies reluctant to install a traditional anodising line in their factories.
(Alcalá de Guadaíra, Seville, Spain), which extrudes, paints, and anodises aluminium profiles for architecture and the industry and which is part of the López Conde family’s GP group together with its main customer, Aluminios Galisur, was among such hesitant
Althoughcompanies.ithadmany doubts about the feasibility of running an anodising process in-house, Proylac managed to include this technology among its services precisely thanks to Alsan’s revolutionary ANODIKIT® Zone, as part of a very extensive investment programme of several million Euros developed over four years (see the previous article, Ed.).
“With an investment that is about three times less than that of a standard anodising plant, Proylac has managed to add a very important service to its offer. We can now guarantee very short delivery times and meet all the demands of the aluminium market,” states Don Jesús López Conde, the owner of Proylac and Galisur.
“The installed line only requires 250 m2 in our factory, it switches on and off at the touch of a button, it does not require an integrated environmental authorisation because the volumes of water used
are much smaller than a conventional line, and it needs very little maintenance as it is made of plastic and glass fibre.”
Galisur and Proylac: leaders in the aluminium sector
“Aluminios Galisur offers a wide range of aluminium systems, combining advanced technology and design to offer the most innovative solutions to the architectural sector,” explains Jesús López Conde.
“Galisur is the most important customer of Proylac, which is the “executive arm” of the group, although the two companies act independently in the market. In particular, the industrial and automotive sectors account for 75% of Proylac’s turnover. Even before 2016, when my father was still at the helm of the companies, the idea of supplementing our service range with an anodising plant did not convince us. We saw the operation of an anodising line as something complicated, polluting, and above all energy intensive. In addition, we knew that the line had to remain active at all times, even during holidays, as well as requiring very frequent maintenance. This is why, when we started to revolutionise our production structure, focussing on more energy-efficient and less resource-consuming machinery
Overview of Alsan’s ANODIKIT® Zone compact anodising plant, which occupies a space of approximately 250 m2.and systems, we decided not to implement “Whenanodising.”Alsan, which was already our supplier of pre-treatment chemicals for our coating lines, showed us this new plant concept, we realised that it was something totally different from what we had always seen. I pictured an anodising plant as a mega structure occupying an entire building, always dirty and corroded. However, Alsan’s system looked like a 200-250 m2 cube, made entirely of plastic, with low maintenance and consumption,” adds Jesús López Conde. “Starting out in the anodising sector with Alsan’s plant would bring us a big advantage: until then, we had been outsourcing this service. I knew that the demand that we would face would not be sufficient to cover one shift of a plant, even a small one, but the investment would be already justified by the reduction of our delivery time, which, with an external supplier, was up to 45 days and therefore too long for specific customer requirements. The ANODIKIT® Zone line was commissioned in January 2022 and we are now very happy with its performance, productivity, and ease of handling.”
This compact, automated line concept, which does not require a lot of space or personnel, is designed to provide high service quality and cope with production rhythms that are not very high, such as order changes, small colour runs, or overnight orders. It has a maximum capacity of 100 tonnes per month for class 10 and 75 tonnes for class 15. The lines’ construction elements are completely different from those used in conventional plants: there is no iron or stainless steel and everything is made of plastic, including the gangways, the structure where the line is positioned, and the frames for loading and unloading, or reinforced fibreglass (the support pillars). Therefore, maintenance is minimal and installation is very clean. ANODIKIT® Zone
works with only two operators per shift, who load and unload the profiles to be processed.
“The concept for this compact anodising plant, unique in the world and patented in 2020, was created to make anodising services accessible to customers that do not require very high production capacities, cannot make too high an investment, or do not have enough space in their facilities,” says Elia Schaer, the CEO of Alsan.
“The plant is designed as a cube that can be assembled in a space of 200 to 250 m2, depending on the process steps required. It is arranged on two levels: on the lower one, there are the tanks for chemical baths and rinses plus the pumps and hydraulic circuits; on the upper one, there are the process tanks. Within this compact cubic form, the location of the machinery can be adapted to the available space according to each project.
“ANODIKIT® Zone is available in three versions:
• A version for natural anodised finishes (the smallest one, with four tanks);
• A version for coloured finishes (including an electrocolouring tank);
• A version for Qualanod-certified finishes (including an ageing bath). “All these systems can be operated manually or automatically. The plant we have installed at Proylac’s premises is top of the range. It is set up to perform natural finishes and electrocolouring (the full range of stainless steel and bronze effects from the lightest to the darkest and black) and it has a final tank for the ageing step required to obtain the Qualanod certification,” indicates Elia Schaer while describing Proylac’s plant in “Thedetail.key element that differentiates this line from traditional ones is that surface finishing is done by spraying. In fact, this is what makes it
possible to “compact” the process and reduce the space required for the line, that is, the number of tanks required as well as their volume.”
• The steps preceding the anodising process are all carried out in a multi-process spray tank: degreasing and rinsing, satin finishing and rinsing, neutralising and rinsing; this means that the ANODIKIT® Zone concept saves a minimum of six tanks. In this tank, the profiles rotate so that the treatment is complete and uniform on all faces within the same batch. At the end of the degreasing process, the liquid used is automatically collected and poured into the lower tank below the degreasing one, and rinsing begins. The same occurs with the satin finishing and neutralising stages. During each process, the loaded batch does not move from the relevant tank.
• The second stage is natural anodising, which is carried out in a standard immersion tank. Concentration values and working parameters are exactly the same as any other anodising plant. After anodising, the parts undergo an immersion rinsing step. In the case of the basic plant version, which only performs natural anodising, this is the last step before sealing.
• The third (optional) stage is electrocolouring by immersion operation.
• The last stage is cold spray sealing. Like the first one, this is a multiprocess tank where all steps are carried out automatically by spraying: pre-rinsing, sealing, and rinsing. Likewise, the process liquids are collected in the corresponding tanks at the lower level of the plant.
• The most complete plant version includes an ageing bath at 60 °C, which is necessary to obtain the Qualanod certification. The line has one area for both loading and unloading. One of the key differences with traditional lines, and also one of Alsan’s patented elements, is the type of frame used. The loading system is completely different from that of a traditional anodising system, because the finishing product is sprayed during almost the entire process: in order to achieve the same finishing quality as a standard plant, it is very important to have a moving frame, so that all profile faces can receive a homogenous application throughout the different treatment stages. With a fixed frame, the inner faces of profiles would show stains, different degrees of gloss, and other surface defects.
“The key step in the development of the ANODIKIT® Zone line was to design and patent a customised frame,” says Elia Schaer. “It is a wheel that rotates in the assembly area and on which the operator can
arrange the profiles. The type of wheel varies depending on the type of profile to be treated. Wheels of different sizes are available, the larger ones being for door and window frame profiles and the smaller ones for beads. We provide three or four different types that fit the vast majority of the profiles our customers work with, whereas we custom-design those required for more specific profiles.
“Another advantage of this line is environmental: in Spain, we have quite strict waste requirements and an anodising plant requires an integrated environmental authorisation for the high volumes of liquids coming from each bath. ANODIKIT® Zone does not need it because the process volumes are much smaller: we are talking about a degreasing tank of, for example, 2 m3 compared to the 30 m3 or more required for the same tank in a traditional line. This also translates into a lower impact in terms of waste water treatment.”
Line automation is controlled by AluZone software, which continuously and automatically collects more than 200 variables, controlling temperature, conductivity, water supply, dosing system, and other essential operating parameters.
“The general screen displays the different baths with their temperature and conductivity values. Each bath can be managed differently: by conductivity, by analytical test, or by load number,” notes Manuel García from Alsan. “In the central part of the screen, one can monitor the process: by accessing each tank, one can see the different recipes with all the corresponding step-by-step times and the total step time. In this way, when they load the material, the operators already know how long it will take for each process stage.”
“The work of the Alsan team, combining chemical and engineering know-how, was very important in the development of this line,” explains Elia Schaer. “The spraying systems are not standard; their flow rates and application angles were specifically designed for this type of frame and frame rotation. We knew the difficulties we would encounter when applying a degreaser, satin finish, or neutraliser by spraying, and we had to adapt all our chemical formulations to ensure perfect decorative finishes on aluminium surfaces even with such operation. By reformulating all our products, we were able to create a completely new range, optimised for working in the ZONE plant.”
“This investment entailed a shared risk between Alsan and Proylac, because it was the first ANODIKIT® Zone line to be installed in the world, if we do not count the prototype that Alsan built in its Paterna factory. Today, after about six months of operation, we can say that we are very satisfied with this investment. We are able to provide our customers with a state-of-the-art service and also cope with small requests, while having a compact and fully automated plant that requires little staff to operate and is managed very easily in terms of process, baths, and waste water,” summarises Jesús López Conde.
From an interview with Gian Luca Falleti Nanoprom Chemicals (Sant’Antonino di Casalgrande, Reggio Emilia) gianluca@nanoprom.it Ivan Bonvini - LEBA 1974 (San Genesio ed Uniti, Pavia) ivanbonvini@leba.it
As a company specialising in finishing treatments for aluminium and light alloys, LEBA 1974 developed its new Nalucoat treatment with the Polysil nanocoating patented by Nanoprom Chemicals, an environmentally friendly alternative to traditional surface treatments.
According to the European Chemicals Agency (ECHA), nanomaterials are “chemicals or materials composed of particles with at least one dimension between 1 and 100 nanometres”. However, not everyone agrees with this definition because, in many cases, their peculiarity lies in the innovative functions that these materials take on thanks to the presence of nanoparticles rather than in their size.
The development of nanotechnology applied to surface coatings has characterised the work and success of Nanoprom Chemicals (Sant’Antonio di Casalgrande, Reggio Emilia, Italy) and recently led it to develop a new application called Nalucoat in partnership with LEBA 1974, a start-up from San Genesio e Uniti (Pavia, Italy) founded to channel over fifty years’ experience in the field of aluminium and light alloy surface treatment with a view to sustainability. “In the late 1990s,” explains Nanoprom CEO Gian Luca Falleti, “our company started developing silicon-based nanomaterials applied to all surfaces needing to be protected: polymer-based structures, metals, alloys, and glass. The quality leap came with the industrialisation by a famous multinational packaging company of Polysil, a product that we developed and that it still uses for protecting its steel, aluminium, and glassmade production plants around the world.”
Nanoprom Chemicals has been developing silicon-based nanomaterials to be applied to all surfaces since the late 1990s © Nanoprom ChemicalsFrom submarines to satellites: nanotechnology appreciated in all fields
“Polysil has the same qualities as glass,” says Falleti. “Therefore, all surfaces, be they made of gelcoat, fibreglass, metal, or other substrates, can be recovered or preserved from wear in the same way as the material on which it is deposited, ensuring excellent corrosion resistance and high hardness. In addition, due to reduced surface tension, surfaces become resilient to dirt.”
The application potential of this nanotechnology coating is almost endless. “From submarines to satellites, from water to air, this technology can be applied by dipping or spraying, with traditional or latest-generation devices, on any type of product and it can perform different functions depending on customer requirements.” Thanks to Polysil’s flexibility, throughout its history Nanoprom has been awarded in various sectors, including naval, aeronautics, automotive, food, military, cosmetic packaging, and above all Formula One, to name but a few.
“Based on the experience gained from the various applications of Polysil and with the collaboration of LEBA 1974, we have recently patented a nanocoating
application for treating and functionalising aluminium. It is an environmentally sustainable alternative to conventional surface treatments such as electroplating and anodising and it guarantees 100% recyclability of coated parts. It consists of a streamlined, waste-free, 3-stage coating cycle including pre-coating, application, and curing.”
“As experts in sustainable surface treatments for aluminium and light alloys,” says LEBA 1974 CEO Ivan Bonvini, “we were looking for a coating that would maintain the tactile characteristics of this particular metal, but at the same time be environmentally friendly in terms of both energy consumption and waste. We did not found any other process that guaranteed the same component sustainability and recyclability degree as Nanoprom’s nanotechnology coating. Therefore, we adopted this aestheticfunctional permanent finishing treatment with very low thicknesses, based on a nanocomposite coating whose main element is silicon dioxide from quartz sand, abundantly present in nature, which allows producing completely recyclable and recoverable
Leading companies rely on vacuum distillation systems for the sustainable and effective treatment of industrial wastewater. Do you want to benefit from a Zero Liquid Discharge production with VACUDEST aswell? Contact us!Gian Luca Falleti, CEO of Nanoprom Chemicals. Ivan Bonvini, CEO of LEBA 1974.
components.” “One of the advantages of this new process,” explains Falleti, “is that a Nalucoat-coated component can be immediately returned to the melting crucible for recycling and metal recovery, without requiring any further surface treatment.” Indeed, as Falleti adds, “Silicon dioxide (SiO2), of which our product is composed, does not affect the remelted primary alloy as it only negligibly varies the titration of silicon. It is not overcoatable, but it can be supplied in any colour required. We collaborate with leading pigment manufacturers to meet the most complex requirements and develop new innovative effects. After pre-treatment, our product can be applied in one coat at room temperature by spraying or dipping, just like conventional paints; it is cured with 20% humidity and it is dust-free in 10 minutes, even at 20 °C. The tests we have carried out guarantee a salt spray resistance value of up to 700 hours.”
Not only its ability to develop a new technology in the field of nanomaterials, but also its business model have determined Nanoprom’s success. “We have a presence in many sectors,” states Falleti, “but not everyone knows us, because our main objective is to develop technologies to be then promoted and disseminated by our customers. It is only in the military, aerospace, and Formula One fields that we intervene directly and, in general, we do so to solve the innumerable difficulties generated by surface treatments with our nanocoating. We have paved the way for previously unimaginable developments, finding innovative solutions for manufacturers in a wide variety of industries with a constantly updated method that our customers can adapt from time to time. So far, we have accepted and won every challenge presented to us and we are ready to be put to the test every day in future as well.”
PPG announced that its 2023 Colour of the Year, Vining Ivy, is expected to shape the styling direction of industrial and consumer products, including cookware, consumer electronics and office furniture. PPG also announced a collection of three coordinating colour palettes called Reflection.
PPG’s 2023 Colour of the Year, Vining Ivy, is expected to shape the styling direction of industrial and consumer products. Vining Ivy reflects the continued global dominance of green around the world. It is the second consecutive year that PPG selected a shade of green and the third in the past five years.
During their annual colour forecasting workshop, PPG colour stylists arrived at Vining Ivy after a comprehensive review of top trends from industries that include automotive, electronics, architectural building applications and fashion across 10 global regions.
“We are seeing green on a broader range of product applications than ever before,” said Vanessa Peterson, PPG global colour styling leader, Industrial Coatings. “We felt compelled to recognize its ongoing influence with the 2023 selection because it has infiltrated the market in such a strong and powerful way.”
PPG’s colour stylists believe that the dominance of the hue is reflective of the continued interest in biophilic design, which is a trend that incorporates nature into everyday lives and spaces.
“Green has a calming yet modern aesthetic and symbolizes prosperity, freshness and progress,” said Peterson. “It perfectly reflects our current Comparedclimate.”toPPG’s
2022 Colour of the Year, Olive Sprig, which is a desaturated soft green, Vining Ivy is a deeper, more saturated tone that lands between a woodsy forest green and a blue-green teal.
PPG has unveiled its 2023 Colour of the Year: the “bluish, greenish” Vining Ivy.It provides product designers with a versatile and luxurious shade that lends itself to a broad array of product applications.
“For furniture, the use of green can be calming in the workplace and help employees feel nurtured,” Peterson said. “When used in consumer electronics, green feels safe and helps people engage with technology. For kitchenware, Vining Ivy complements various food colours and coordinates well with stainless steel, bringing a touch of luxury to PPG’skitchens.”global team of colour stylists also have curated a palette of 45 coordinating hues for a Reflection-themed colour collection, which is inspired by the shared – and growing – appreciation for minimalism, quiet design, biophilia and solace. The compilation is organized into three unique colour stories: Serenity, Origin and Duality. A gentle palette of milky pastels, watery tones and warm neutrals, Serenity reflects the desire for calm and solitude in a chaotic world and inspires a sense of renewal and peace. By capturing the authentic beauty of nature, Origin cultivates a sense of wonder with a bio-palette curated with
organic hues. Lending itself to both traditional and contemporary styles, Duality leans into contrasts and is a means of self-expression through bold and bright shades, clean pastels and strong neutrals. PPG’s industrial coatings business has produced a stylized short video that tells the Reflection story through the experiences of a young woman embarking on a journey of growth and self-discovery.
GSB will show visitors how the companies adhere to the GSB Quality Regulations at the booth 7AA07 during the next ALUMINIUM exhibition.
Qualityassurance can be found everywhere. When a product is purchased or a service is contracted, customers assume that the promised quality level will be met. In order for suppliers to deliver this level of quality, an appropriate quality assurance system must be utilised. While these systems obviously differ depending on the product or service, they have one thing in common. Most of the time, customers are familiar with the standards, certificates and regulations, but few really get a direct insight into quality assurance. For example, one rarely has the opportunity to attend an audit or test.
The GSB is taking up this challenge by making GSB Quality Assurance as transparent as possible for everyone and showing why coatings according to GSB Quality Regulations are considered to be the highest standard in the field of outdoor applications in architecture and industry. In the end, it is not without reason that coatings according to GSB are requested when aluminium, steel or galvanised steel needs to be coated, because the GSB ensures the quality of the entire coating process chain - from pre-treatment through coating powders or liquid paints to the coating companies.
At the ALUMINIUM 2022, everyone interested is very welcome to get an insight into the quality assurance of the GSBbooth:7AA07. There will be the possibility to have a look at sample sets from different tests. Of course, due to sheer logistical reasons, it is difficult to show all processes at a trade fair. Therefore, member companies have carried out a joint video project that makes it possible to look behind the scenes - a novelty in the industry! Last but not least, there will be live coating at the fair - a miniature coating plant makes it possible.
For further https://gsb-international.de/en/information:
Converting outdoors into a space to live. This is what Corradi, the Italian leading manufacturer of structures intended for sun protection of outdoor spaces, aims to achieve. Coating plays a key role in conveying this concept. This is why the company has relied on Gema’s application technologies to provide its aluminium profiles with an unrivalled aesthetic and functional level.
SPECIAL ISSUE ON ALUMINIUM An aluminium structure for sun protection of outdoor spaces manufactured by Corradi.“Decoratingis not about making stage sets, it’s not about making pretty pictures for the magazines, it’s really about creating a quality of life, a beauty that nourishes the soul.” Corradi Srl’s showroom in Castel Maggiore (Bologna, Italy) welcomes us with a quote by American interior designer and decorator Albert Hadley. The core value of this producer of outdoor furniture solutions is creating living spaces that combine functional and aesthetic quality, strength and elegance, Italian-made design, and life style. Colours and finishes, therefore, play a key role.
“Every Corradi structure is tailor-made to customer needs, as we wish to blend the finish of our structures with the house project and the surrounding environment they will be part of. In addition to some standard models, we are also at the designer’s disposal to evaluate and apply the most suitable colour; most requests involve textured white, matte white, anthracite grey, or spring green, but we have also had to interact directly with paint manufacturers in order to devise a specific product,” states Raf Segers, Corradi’s CEO. Customising finishes is thus the main competitive advantage of the company, but it has required significant investments in processes
and technologies to enable it to retain its production flexibility while achieving repeatability and quality of operations. The last action taken was the installation of an automatic powder coating booth MagicCompact EquiFlow BA04 supplied by Gema, integrated within a pre-existing line, which enabled Corradi to make colour change operations faster and improve paint adhesion.
The company was founded in 1978 by brothers Alberto and Raffaele as a workshop for sun awnings. On-going innovation and search for new styles and design solutions enabled the the company to patent in 1998 Pergotenda®, a wooden sun protection load-bearing system with a retractable awning cover. Corradi later focused on additional structures for open spaces, also introducing into its product range its Sun Sails sun-shading sails and bioclimatic pergolas – provided with about 20-centimetre-large orientable aluminium blades letting light and air filter into the space, while effectively protecting from sun “Weexposure.initially manufactured wooden structures and Pergotenda®
accounted for 90% of our production. However, we decided to also develop some aluminium systems, as our company’s founders considered aluminium as a material with huge potentialities: it is cost-effective, it is more recyclable, and it facilitates maintenance by end users. Such a choice turned to be crucial, as we could further expand the styles offered by our product range and implement solutions suitable to different contexts and needs. Today aluminium bioclimatic pergolas account for three quarters of our production and are marketed everywhere in the world,” says Davide Faccini, Head of Operations
Nowadays,Department.Corradi is an independent company belonging to international group Renson Outdoor based in Belgium, and can reach customers throughout Europe. Its Bologna headquarters also include the production plant mainly supplying the Italian, Spanish, French, Swiss, Austrian, German, Romanian, Russian, and Ukrainian markets.
The group includes also the renewed production branch of Corradi U.S.A., located in Dallas. “The distribution of our products on the global market has very long transport and storage times. Their finishes must therefore be of top quality and able to withstand different climates, even the most aggressive and exotic ones,” explains Faccini.
From top to bottom:
The pre-treatment tunnel entirely made of plastic material.
The pre-finishing station of the new booth and the OptiCenter OC07 powder management unit.
The Gema OptiSpray AP01 pumps with Smart Inline Technology.
The company receives raw materials, i.e. aluminium extruded profiles, from several Italian and European producers and stores them in its warehouse before carrying out machining processes and a manual smoothing, milling, and boring operation on each aluminium profile, in order to fix possible damages resulting from wrongful handling. The components are later subjected to coating and finally assembled to other elements such as pillars, beams, and electric circuits. At the same time, Corradi also produces the textiles for its Pergotenda® and Screens (perimeter closing awnings) models in its tailoring department as well as plastic materials to be used by the installers on-site.
“All these processes are crucial to guarantee the quality of our products, create structures suitable to fulfil the designers’ requests, and establish an emotional relation with users. However, it is the coating department to be the core of our factory,” indicates Luigi Lorenzano, the head of the coating department. “Corradi creates customised and tailor-made solutions. Finishes and colours are not only used to enhance our products’ structure, but also to create a place in harmony with the surrounding environment. Our experts
cooperate with designers and architects to identify the most suitable coating solution for every requirement: for instance, a restaurant in the city centre of a Northern Europe small town will need different tints and finishes than a farmhouse in the Tuscany hills,” explains Faccini. “Coating is not only crucial to provide the aesthetic features required by customers, but also to comply with all mechanical, thermal, and corrosion resistance requirements”, Faccini adds. “We carry out all the procedures required by the QUALICOAT Class 2 standard and we have developed a production culture focused on quality control. In fact, following the curing oven, there is a line to backlit examine our products and find any defects caused by improper extrusion or non-optimised coating. The MagicCompact EquiFlow BA04 booth supplied by Gema, in any case, has sensibly reduced the latter occurrence.”
Corradi’s coating plant consists of a 7-stage pre-treatment tunnel entirely made of plastic, a drying oven, two powder coating booths, an infrared oven for paint gelling, and a curing oven served by a two-rail overhead conveyor by Railtechniek B.V, the Dutch company that acted as the prime contractor during the implementation and installation of this line in 2018. The profiles are arranged on the load bars and taken into the pre-treatment tunnel, where they undergo a process engineered and developed by ALIT Technologies. The workpieces are treated in a double-step with the degreasing acid Alfideox 82/3, that removes the residues from previous processing and strengthens the aluminium surfaces. Then, a final conversion step with Alficoat 748/3 provides corrosion protection and improves paint adhesion. After oven drying, the conveyor takes the aluminium parts to the two coating booths.
Then, the profiles are taken through Infragas Srl’ oven with infrared panels and they are finally cured for 20 minutes at 180 °C.
“Our horizontal plant is the result of a cooperation among several partners, which examined our needs and provided each a key element to our coating process’ success. Although the system was installed envisaging the presence of two coating booths, we firstly incorporated only one. In the meantime, however, production rhythms increased enormously and we could not fulfil the demand even working on three shifts. This is why, in December 2021, we turned to Gema to find out a solution,” Lorenzano notes.
The Italian headquarter of Gema has provided the company with a rectangular MagicCompact EquiFlow BA04 booth equipped with six OptiGun GA03 automatic guns on each side and OptiSpray AP01 feed pumps with Smart Inline Technology, which can apply the several tints required in just a few minutes, thanks to the quick colour change system that is managed autonomously by the OptiCenter OC07 powder centre. This technology was specifically chosen as it can ensure quick colour changes and automatic cleaning of the circuits, the float, the dispensing hose, and the spraying guns.
The twelve automatic guns and the manual pre- and postfinishing workstations were designed to offer high transfer efficiency, uniform application of polyester powder paints, and deep penetration with any workpiece geometry. In addition, using a single channel circuit (hence the definition Smart Inline Technology), the OptiSpray AP 01 feed pumps with ensure a homogeneous powder flow and better jet management, thus making it possible to spray a precise amount of powder, which varies according to the application requirements, while keeping the flow constant.
The plastic non-conductive material which makes up the booth, along with the EquiFlow suction technology, prevents powder from depositing at the bottom or on the walls, thus speeding up internal cleaning operations and improving the healthiness of the workstations, while its H-shaped layout improves air distribution and suction: the three slits at the bottom of the booth ensure excellent powder containment and optimal ventilation in the manual application area. A homogeneous airflow is thus generated making it possible to easily control the application process and obtain excellent coating results.
The parent company Renson had already cooperated with Gema to test some powder coating solutions for painting large-size products and implement more than twenty colour change operations per shift. Corradi’s requirements are different, as it needs to coat components with a maximum length of 7 metres and a maximum BOOTHS WATER SLUDGE REMOVAL DEMINERALIZATION OF CONTAMINATED SYSTEMS a complete
width of 40 centimetres, “but the results of tests carried out in Belgium were very satisfactory and showed that this solution could guarantee significantly greater powder savings than similar alternatives using traditional feeding technology with Venturi injectors. Therefore, we decided to rely on Gema. This choice turned out to be a winning one: we were very pleased with the professionalism, helpful attitude, and flexibility of their technicians and sales network and, although we have only been using the BA04 booth for six months now, we have already seen a significant quality improvement. The Smart Inline Technology keeps the powder distribution homogeneous and consistent over time, as the lack of transport air makes it possible to better adjust the paint jet and envelope the workpiece while ensuring a considerable saving in the coating product. By contrast, the technologies using Venturi
injectors are more likely to wear and they need more maintenance and the frequent replacement of sleeves in order not to jeopardise feeding stability,” adds Lorenzano.
“Our production processes and times have also improved. The MagicControl 4.0 panel, that allows to manage the entire booth, is user-friendly and our operators were able to perfectly use it since the very beginning. We feared that a few weeks would be necessary to get used to the new system, leading to delays in our deliveries, but no production slowdown occurred. Even those few times we had to resort to the Italian technicians of Gema to understand how to optimise some booth settings, the response was quick and thorough. We succeeded in increasing productivity while reducing our work shifts from three to two and we could not be more pleased with the investment,” Faccini concludes.
The infrared tunnel for paint gelling before the curing oven’s entrance. From left to right: Luigi Lorenzano from Corradi, Claudio Sergenti from Gema Europe, and Davide Faccini from Corradi. ©ipcm ©ipcmEvery manufacturer of aluminium profiles for door and window frames, shower cubicles, automotive components, and many more products use extrusion presses to transform aluminium billets into profiles with the most diverse sections, optimised for their intended use. The dies of the extrusion presses are “templates” that give shape to the profiles. After each use, these have traces of solidified aluminium that must be completely removed before storing the dies until they are mounted on the press again. ALIT Technologies developed an innovative product that reduces the cost and time of cleaning extrusion dies for and in partnership with Alumec (Rudiano, Brescia, Italy).
Inthe aluminium industry, the extrusion dies are regularly cleaned by heating caustic soda baths and the aluminium scraps trapped into the die body are brought into solution through an exothermic reaction. This process involves the consumption of significant amounts of soda ash, which must be dismissed of at the end of the cleaning bath’s life cycle. The corrosiveness of soda ash combined with high operating temperatures close or above to 100 °C generate corrosive
and dangerous fumes and, furthermore, the formation of sodium aluminate fouling implies continuous maintenance work, which is complicated by the corrosiveness of the liquid solution. In this scenario, it is crystal clear that the optimisation and cost savings for this process is strongly desired by all those companies operating in the field of aluminium profile extrusion. ALIT’s answer to this need is the additive Claris 9346 MB, entirely developed in our laboratories
Claris 9346 MB is an additive developed for the extrusion die cleaning systems for aluminium profiles; the liquid state easily allows automated dosing.
Claris 9346 MB enables a more efficient die cleaning process by improving the following aspects:
• It improves the general cleanliness of the extrusion die, facilitating the dissolution of aluminium residues that often gather in the most inaccessible points of the die.
• It considerably increases the service life of the bath.
• If appropriately dosed, it maintains the working temperature of the die-cleaning bath at around 90 °C, thus reducing fumes emissions and evaporation consumption. Maintaining the temperature in the process tank means an average energy savings of 20%.
• It does not enhance the sludge formation.
The extrusion die cleaning bath should typically be loaded with soda ash diluted to 30% w/w. At this point, a certain quantity of Claris 9346 MB varying between 3% and 4% by weight on volume should be added to the bath. For every 1,000 litres of solution, approximately 35 kg of Claris 9346 MB should be added. Next, the product can be mixed, the bath heated, and the typical matrix cleaning cycle started.
The correct amount of soda ash and the maximum aluminium content dissolved in the matrix cleaning bath can be accurately determined by simple chemical analysis, easily performed by process operators. If necessary, the amount of Claris 934 6MB can also be determined by following the analysis instructions in the product data sheet. The possibility to detect these values, along with the improved thermal stability of the bath after addition of Claris 9346 MB, will make the entire process easier to manage by the operator.
Claris 9346 MB has been implemented and co-developed by a major aluminium profile extrusion Italian company, Alumec (Rudiano, Brescia), which owns more than 11,000 proprietary dies. This
company is already know to ipcm® readers, as it was the protagonist of a report1 on its efforts to make production more and more environmentally sustainable through a paint stripping process also developed by ALIT Technologies. Since the issue of that magazine, Alumec has made even more significant strides to become ever greener: from installing photovoltaic panels on all the factory’s available surfaces to replacing its pre-treatment products with chrome-free and nanotechnology ones, up to recently upgrading its extrusion die cleaning process.
This company was using heated solutions of 30% soda ash for die cleaning. Under these conditions, the soda baths had a lifetime of only three working days, considering three shifts per day. The customer complained about the high soda consumption, shallow cleaning of the dies, and continuous fouling of the die cleaning system. After the addition of Claris 9346 MB in the matrix cleaning tank, at a rate of 3.5% w/w, the following benefits immediately occurred:
• Product lifetime improving from 3 days to 6 or 7 days.
• Improved overall level of the matrix cleanliness.
• Temperature stability of bath within a 90-95 °C range, and less production of fumes.
• Adsence of sludge at the end of the cleaning cycle.
The use of Claris 9346 MB generated different benefits such as the saving of large quantities of caustic soda, reduction of energy consumption and improved extrusion dies cleanliness.
Compared with the previous management process without Claris 9346 MB, the customer is now fully “Oursatisfied.collaboration with ALIT has been greatly strengthened since the publication of your article about the out-of-line stripping system for our vertical plant’s hanging hooks,” explains Manolo Brunotti, coating plant manager at Alumec.
1 Alessia Venturi, Improving Efficiency, Productivity, and Envi ronmental Friendliness with Chemical Paint Stripping: Alumec’s Experience in ipcm® no. 68, Vol. XII, March-April 2021, pp. 56-62
The cleaning phase of the extrusion dies.
“After attending the technical course organised by ipcm® Academy and obtaining the international certificate of the Industrial Surface Finishing Process Technologist, I realised that we could further optimise our painting process to save time and money and, above all, respect the environment as much as possible. After fine-tuning our paint stripping system, we therefore continued the collaboration with ALIT up to replacing our entire pre-treatment process with its products,” indicates “IBrunotti.specifically
asked to create a product that would meet our needs and, together with ALIT, we started to develop an innovative product for cleaning the dies we use on our extrusion presses. We mainly needed to speed up the cleaning process and extend the life of the bath. We invested a lot of time with ALIT in researching and testing the optimal formulation and the result was a product that definitely improved this significant operation in many respects. An important achievement is related to the consumption of methane gas: the bath containing soda
must be kept at a temperature close to 100 °C and, therefore, our burners had to be lit 24/7. With the addition of Claris 9346 MB, the burners are switched off once the solution reaches a temperature of 80 °C and, due to the endothermic effect, the bath maintains a constant temperature, thus requiring the burners to be restarted only when the baskets containing the dies to be cleaned are immersed and then removed.” Brunotti adds: “Another important advantage has been reducing our disposal costs as well as soda ash consumption by over 50%. Considering that we have also sped out our cleaning process by 20%, I think we can be quite pleased. I personally thank ALIT also for the given name: MB 9346 are the initials of my name”.
The official launch of this new product will take place at the Aluminium 2022 trade fair in Düsseldorf (Germany) from 27-29 September 2022, where ALIT Technology .will present this and other innovations to its stand’s visitors.
A company specialising in the production of roller shutters, Pracal has made a name for itself in one of the most complex areas in terms of economic development thanks to the nonconformist choices and entrepreneurial skills of its owner and of the partners, such as its paint supplier Condoroil Chemical, that have helped it develop eCOILS, the new company specializing in the continuous-flow pre-coating of aluminium and steel coils.
Oneof the most technically and operationally complex processes is the continuous-flow pre-coating of coils made of various metal substrates, especially aluminium and steel, for use in construction (façades, roofs, and roller shutters), transport (walls and interiors of RVs and trains), and the industry (packaging and household appliances). It consists of several “sub-processes” that must be perfectly synchronised in order to achieve optimum quality results, from roller paint application to the curing of the paint product, be it liquid or powder, which must take place within seconds, to the post-coating phases such as, for example, coil profiling, stamping, bending, and drawing or chemical treatments such as off-set printing or sublimation. Precisely due to this peculiar characteristic, i.e. painting done before forming, the coil coating process must be carried out with extreme care and attention in every operational, handling, and storage phase, since the finish coming out of the coil coating line is the one the end user will see, because no further surface treatments are foreseen. Achieving the technical knowledge needed to run a coil coating line and provide its customers with a product that exceeds quality standards was the biggest challenge for Pracal Srl, a manufacturer of profiles for roller shutters based in Polla (Salerno, Italy). “We are now a national and international benchmark in the coil coating sector, as well as for roller shutters, thanks to the expertise acquired in the field,” explains Vittorio
Iacullo, manager of eCOILS, a Pracal’s branch, “to our partnerships with companies specialising in the production of coil paints, such as Condoroil Chemical (Casale Litta, Varese, Italy), and to the quality of our workers, motivated and ready to face new challenges”.
A pioneering vision and extreme problem solving skills: Pracal’s trump cards
“Pracal (an acronym that stands for “steel aluminium profiles”) is the latest expression of a long-standing company founded in the second half of the 1980s for the assembly of PVC roller shutters, thanks to the far-sighted and pioneering vision of our current president, Francesco Pinto, who founded the firm,” says CEO Maria Massaro. “As early as the 1990s, our company started implementing plastics extrusion and became a leader in Southern Italy for the production of PVC roller shutters, to which it soon added customised slats, retractable doors, and shower enclosures. After 2000, it also specialised in aluminium and steel profiling. Pracal was thus born: it has established itself on the market thanks to its professionalism, its ability to find quick solutions to customer needs, and its fast and impeccable service from order to Thedelivery.”decision to insource the surface treatment of metal profiles is also the brainchild of owner Francesco Pinto and his son Raffaele, who since © ipcm
The continuous-flow pre-coating department of Pracal Srl.joining the company has poured an incredible energy. “The idea started to take shape in 2009, when the need to respond just-in-time to customer demands no longer matched our availability in stock, because the contractors we relied on were unable to keep pace with our intensive production. We therefore started to paint our coils with a small plant, but colour repeatability was not up to our quality standards. However, the tools and procedures that we have to develop in order to solve the issues that arose from time to time, proved to be useful to achieve the skills that now allow us to manage the new continuous-flow coating system we installed to place alongside the previous one, which has soon become the flagship of our production.”
The Pracal headquarters is located in an industrial area which is perfectly connected to the nearby motorway. The company has managed to develop an efficient and resilient organization that has resulted in constant growth, despite facing unfavourable economic conditions in the latest 2 years, and a penalizing geographical position compared to its competitors. The last two years have been characterised by steady growth; moreover, the company recently decided to launch a new brand, eCOILS, which started as a brand of Pracal but which may soon be developed as a stand-alone company to manufacture and sell prepainted coils, as is already happening in sectors other than the roller shutters ones.
From top to bottom:
Coils treated by Pracal.
The first coating booth for primer and back coat application.
The coating heads for the application of the top coat.
“Our new coil coating plant,” notes quality manager Sabatino Di Domenico, “enabled us to take a productive leap and establish ourselves in this sector. Today, we liquid-coat coils with a thickness of 0.2 to 1.8 mm and a maximum width of 1500 mm, with different types of paints, including polyester, polyamide, polyurethane, and PVDF, and we rely also on the Condoroil Chemical team to supply us with back coats and top coats.”
“The continuous-flow coating process,” explains Di Domenico while describing this operation’s phases, “starts with the loading of aluminium or thin steel coil blanks onto two decoilers. Prior to pre-treatment and coating, the coils are joined by means of a splicer so that they can be treated with a continuous flow; indeed, our coil storage tower allows splicing two coils without ever stopping the plant. Speed and temperature are the two parameters that must always be kept constant.”
Pre-treatment includes alkaline degreasing in the first tunnel with high-pressure spray bars and mechanical brushes to remove any traces of oil, grease, and oxides from coils; a second spray tunnel carries out a rinse with mains water and completes this phase with a second rinse; and a third tunnel performs passivation by “Thefluozirconation.recovered waste water is then taken to the purification plant, which we are upgrading with a further filter system to cope with production peaks and thus improve water recycling: this is one of our main goals. The coils then reach a drying system that was developed by Pracal’s mechanical department to achieve perfect drying of the surface of coils with a thickness of more than 10 tenths of a millimetre, in order to offer the perfect pre-painted item, not only to roller shutters’ manufacturers, but also to tinsmiths, facade builders, roofers and panel manufacturers used in various sectors, from construction to naval industries”.
After drying, the coils enter the first of the three coating booths, which is equipped with two coaters capable of applying a primer and a back coat in one pass. This is followed by oven polymerisation, air cooling, and water cooling. “One of the advantages of liquid coatings,” indicates Di Domenico, “is their very short polymerisation time, during which the pigment colours remain stable. The coils’ dwell time in the oven ranges from 6 to 60 seconds depending on their characteristics, while the temperature ranges between 210 and 250 °C. Once a coil has entered the oven, it gradually reaches a temperature close to that of the oven itself. Upon exiting, it is cooled by jets of cold air and demineralised water.
“The second booth applies the top coat and any special effects such as metallic, wood-effect, antiqued or weathering steel-effect finishes. The third one is pre-arranged for clear coat application. The overall
thickness of the coating on a finished product is generally between 5 and 15 microns for the primer and 15-30 microns for the second layer. The coils then re-enter the air and water cooling oven and reach a storage buffer, where they are cut, and finally the recoiler at the plant’s exit.”
Each station is equipped with a control PLC for data collection and analysis, coil tracking, and overall management of the coating line. “The innovative management of all data coming from PLC devices,” says Di Domenico, “was part of the investment we made last year to structure our factory according to the parameters of Industry 4.0. With this system, we are able to better manage our entire production cycle, which is very strict: since painting is the first phase and not the last, as is the case in traditional coating lines, all surface treatment operations must be carried out in time compatible with the subsequent processes, such as coil cutting and roller shutters profiling, guaranteeing short delivery times, never at the expense of quality.”
On leaving the coil coating line, the coils undergo an initial visual check. More in-depth checks are then carried out with manual and automatic measuring instruments, such as thickness gauges and micrometres, in the analysis laboratory. “We carry out all possible controls to deliver products with a quality level beyond the prescribed standards, from Machu to impact and cross-hatch tests. As for salt spray tests, we rely on Condoroil Chemical’s test laboratory, which not only supplies us with the paints to be used in our coil coating line, but also provides us with support and advice on the finishing results obtained. We are also in constant contact with them for the optimisation of paint formulations,” states Antonio Salviati, technician of the company’s internal lab. “Once they pass the quality tests, the coils are ready for packaging and delivering to our customers both in Italy and by Antonio Salviati.
abroad” – Iacullo continues.
“Our particular finishes are highly appreciated for their aesthetic and qualitative value which makes the eCOILS brand recognizable on the market. In particular, we have received great satisfaction from our new eSKIN finish which guarantees excellent performance in the bending phase and UV resistance. In addition, we pursue an increasingly green policy, aiming to achieve the zero plastic waste goal: this is why 90% of the coated coil currently in our company is free of any PVC protective film. We are also trying to replace some typical packaging elements such as film or bubble wraps, but currently they are the only waterproof solution.”
A supplier guaranteeing timely deliveries
“With a raw material supply chain made unpredictable by the situation we all know, delivering our products in a timely manner is crucial,” indicates Iacullo.
• Economical entry into automatic coating
• Optimized powder recovery with Energy Efficiency Package (EEP)
• Easy and fast color change
• Combination with PXM powder center: Automatic fresh powder supply and integrated system control via 15.6 inch touchscreen
“In order to do so in such a dynamic sector, however, one needs to have partnered up with the right suppliers. Consistency and reliability in fulfilling all orders are also of the essence. Condoroil Chemical meets all these requirements: their supply of polyamide and polyurethane paints for roller shutters and blackout systems and of polyester paints for outdoor products has always been precise and punctual, even with new colours formulated on request.”
“The paints we supply Pracal with,” says Sara Ponti, the head of Condoroil’s laboratory, “can be standard or customised with any tint required by its customers, but they all have the right surface hardness, flexibility, and adhesion characteristics to facilitate the subsequent profiling and bending operations.” “Collaboration with this supplier,” points out Iacullo to conclude, “will continue in the future, probably even more intensively since we want to establish ourselves in the market
with our new eCOILS brand. We believe that the energy, technical and environmental solutions that aluminium can give us are the best; not only because aluminium is a 100% and infinitely recyclable metal, but also for its physico-chemical properties improved and enhanced by our coils surface treatments. Despite the considerable emigration rate that has distinguished Southern Italy for centuries, we are able to attract and train high-profile professionals and operators for which the security of a relationship with a supplier that can support us at every stage of the process, from R&D to quality control of coated products, is key to us. This is yet another reason why we appreciate Condoroil Chemical. Those who work in eCOILS and in the Pracal group in general, believe in the corporate vision of Francesco and Raffaele Pinto and are determined to contribute to the development of a modern industry, in authentic Italian style, which has its heart here: in the heart of Southern Italy”.
From an interview with Prof.Dr.-Ing Dimosthenis Trimis Karlsruhe Institute of Technology Heiko Schneider - GoGaS Ing. Massimiliano Fontana - Tecno Group
Within the framework of the project ECCO, twelve partners have joined forces to build an innovative coil coating plant with the aim of not only increasing the compactness of the system, but also optimizing production flexibility thanks to a modular and energetically self-sustainable process, which can provide an energy surplus to be used in other parts of the coil coating process.
is not always an easy task, especially when a process is tried and tested. However, there are really no fields or processes that do not have at least some room for improvement. If anything, this is exactly how true innovation comes to be: when people with the right intuition and skills meet and decide to put their minds to the Whentask.
it comes to innovation in the coil coating sector, on the pages of our magazine, we have already presented an example of one of the most advanced coil coating plants
for the powder coatings application, which employs catalytic IR technology to speed up the process without over-expanding the plant1 Today, we introduce you to another gamechanging innovation, that of ECCO: a research project conducted by a consortium of twelve partners (four universities, two private research centres, three SMEs and three large enterprises) and founded by the European
1 M. Fumagalli, “AluCoating Chose Catalytic IR Technol ogy to Speed Up Powder Coating on Aluminium Coils”, ipcm® International Paint&Coating Magazine n. 75, pp. 52-56.
Community’s Framework Programme for Research and Innovation Horizon 2020, aimed at developing a more energy efficient coils liquid coating process by using new materials and implementing an advanced plant setup.
How ECCO started “Ten years ago, we had the idea to create a new coil coating process able to drastically reduce the energy demand of the curing process. To achieve this, we needed to dismiss the convective dryers, which require an enormous amount of pre-heated air so that the solvent concentration in the air is below the low flammability limit (≤ 1% of solvent concentration). In fact, with standard coil coating processes, if you want to save energy, you have to recuperate the heat and have a dedicated thermal oxidizer to eliminate the solvent”, explains Prof.Dr.-Ing Dimosthenis Trimis, Head of Institute, Division of Combustion Technology of the Karlsruhe Institute of Technology. “So, we asked ourselves, is there another way to operate a more energy-efficient coil coating plant? We found that the answer to this question was yes, but in order to do it we had to build a plant able to operate above the upper flammability limit while avoiding the risk of
Thisexplosion.means having an atmosphere in the oven full of organic solvent but with not enough air
The coater.to lead to a possible explosion. To achieve this, we figured we had to heat indirectly and not convectively and that radiant heating was the answer to the “Toproblem”.exploit
radiant heating, you need to have the radiators within the curing oven section. However, if the radiators are based on combustion, like in our case, they need to be physically separated from the oven through an infrared transmissive interface that still allows the infrared radiation to pass and thus heating the curing oven”.
“This was the principle at the base of our idea.
Ten years ago, we started a proof of concept to understand if we could find a type of transparent infrared window that would allow this kind of operation. In addition, we also wanted to investigate whether the burners could be operated with the evaporated solvents of the curing oven. This would have allowed us to optimize energy consumption in two ways: one, we would not have needed to pre-heat huge amounts of air anymore and then recuperate it; two, we would not have needed to use natural gas by employing instead the solvents already in the process”.
This project was conducted by the Karlsruhe Institute
of Technology and GoGaS, a company specializing in construction and manufacturing of drying plants for different industrial branches.
“The first exploratory project was successful: we demonstrated that we could operate the radiant burners with the solvents and that we could also have transparent infrared windows that could withstand these harsh conditions of high infrared radiation and heating”, says Heiko Schneider, Managing Director of GoGaS.
“Once we proved the feasibility of the project we moved to the next step, which needed to take into consideration the overall complexity of such system.
To achieve this, we assembled a consortium of twelve partners, including companies, universities and research centres, each with a specific task based on their field of expertise”, recounts professor Trimis.
There were two main research areas. One was aimed at improving the radiant burners themselves.
“The radiant burners are porous ceramic burners and combustion takes place in the porous cavities. They are radiating at around 1400°C – very high temperatures for normal radiant burners, which
From left to right:
The complete setup of the curing oven and the burners sections.
The post-inertization chamber.
The cooling tunnel.
© ipcm
usually operate around 1000/1100°C. Therefore, we needed high temperature ceramics that could resist thermal shocks and oxidation. In fact, the ceramics that are usually employed in this kind of application are based on silicone carbide, which can oxidise with time and is subjected to degradation. So, one research team was at work to improve these materials, by applying, for example, protective layers to create an oxidation barrier or by doping them with further compounds. Partners that participated in this research were Scuola Universitaria Professionale della Svizzera Italiana (SUPSI) and EngiCer Sa, a manufacturer of high temperature ceramic structures. Politecnico di Torino took charge of analysing the materials with very sophisticated Theinstrumentations”.secondresearch group focused on the “Whenwindows.itcame to the glass window separating the burners and the oven section, there were two main challenges to face. The first one was that the windows had to withstand the thermal shock while being, at the same time,
infrared transmissive. When we talk about infrared transmissivity, for the temperatures we are achieving, we have to go up to 6 micrometres of transmissivity. Normal glasses block the transmission at 1.5/2 micrometres. Quartz glass may go up to 3 micrometres, if specially treated. So, the challenge was to have a material that would allow us to reach a high wavelength range but robust enough to withstand the thermal stress. The second problem was posed by possible pyrolytic reactions. In fact, in the curing section, there is an atmosphere very rich in evaporated solvents at a temperature of 250-300°C. So, pyrolytic reactions could produce deposits that block the windows and, consequently, the transmissivity. To tackle this challenge, we applied a catalytic transparent coating on the windows, which supported the oxidation of carbon deposits during operation. This research was conducted by Colorobbia, which is specialized in glass materials, and another research group of the Politecnico di Torino, specialized in the development of catalytic systems”.
In addition to improving the materials employed, the consortium had to also simulate the overall operation.
“The plant features a burner section and the oven section, which are separated by transparent window tiles. So, we needed a dedicated flow in order to avoid convective heating of the window tiles, that is, a direct contact of the exhaust gases of the burners with the tiles. We also needed to recirculate the atmosphere of the curing oven both to homogenize it and to exploit a part of the recirculation loop as fuel for the burners. Finally, we needed to have inertization chambers at the entrance and at the exit of the oven to avoid air from the environment to come into the system or solvent vapours to go out. We developed a concept to achieve all this but to actually create it we needed detailed numerical simulations of all these flows in real 3D geometries and in high resolution. This was done by our Portuguese colleagues of the Instituto Superior Técnico of Lisbon. This research actually brought a lot of changes in the design”, explains professor Trimis.
“All the partners are having a specific role, each within their own field of expertise, but there is a lot of cooperation and dependency on each other’s work”, states Heiko Schneider.
The Karlsruhe Institute of Technology coordinated the entire work and researched how to design the burners: how should the porous structure be, how to combine the materials to achieve process stability etc. It was also in charge of the simulation of the overall process.
The pilot plant is currently located at Tecno Group srl Officine Meccaniche, an Italian company specialized in the construction and assembly of special machines, including those for the handling and coating of coils.
“We have been involved in the project by our customer Globus Srl, an engineering company specialized in the design, construction and commissioning of coil coating plants and to which we usually supply the machines necessary to the process. For this special project, we have made our factory available to assemble the complete line and carry out
the operational tests”, says Ing. Massimiliano Fontana, owner of Tecno Group.
ThyssenKrupp Steel Europe, a major player in coil coating, was also involved in the project to define process quality.
“From the very beginning, we kept in contact with ThyssenKrupp, who showed interested in the possibility to transfer this process to the coil coating lines they are operating. In particular, the ThyssenKrupp team helped us evaluating the energy consumption compared to standard plants.
They are also evaluating the benefits in terms of the size of the installation. In fact, the oven is much smaller than conventional ones and, since we are burning the solvents in the burners, heating the oven, there is no need for a separate thermal treatment afterwards. This makes the overall installation significantly smaller. ThyssenKrupp played a major role also in defining the quality tests to be carried out: on which coils and materials, if these are to be pre-treated or not; with which speed we should conduct the tests and the evaluation parameters of the samples. They
are also supplying all the coils and they are doing all the pre-treatments that are needed, depending on the tests we have to carry out”, explains Trimis.
“We have supplied forty coils, which are being treated and analysed to control the quality level, comparing it with our own production. In my opinion, this is the beginning of a new era for the coating and curing of coils, in terms of cost efficiency, maintenance and optimization of space”, adds Joseph Schneider, process engineer of ThyssenKrupp.
AkzoNobel was the supplier of the paints employed to coat the coils.
“The company also provided some sensitive information on the composition of the solvents and is currently modifying the paint formulations according to our needs. For instance, they are creating for us batches of white paint with a tailored, higher absorption rate of the infrared radiation”, explains professor Trimis.
“We also needed to evaluate the process under an environmental point of view and conduct a life cycle analysis, comparing it with
benchmark cases of the current technologies. However, since the process is new, we also needed to develop new corresponding KPIs. The National Technical University of Athens is taking care of this aspect. It is truly a project with a lot of interrelations: when they are defining a KPI, we need to create the corresponding sensors to gather data so that they can build this indicator”.
“The project started with the development of the single components and the simulation of their integration. This first phase was followed by an engineering stage, during which all these newly developed components had to be thoroughly analysed to pinpoint possible bottlenecks and problems. This is when the numerical simulations played a major role. Then we started the building phase, procuring the necessary components and fabricating the ovens from scratch. Then we had to evaluate the safety measures with accredited bodies. This is taking some time because there is no standard, it’s something new, which requires new evaluations. We are now in the commissioning stage, testing both the components and the complete process. Once
this is completed and after the evaluation of the accredited bodies, we will start the demo phase”, says Trimis.
“This is the first plant we ever built with this setup, which aims at reducing energy consumptions below the current state of the art, reducing the size of the installation, and consequently gain more process flexibility. Globus and GoGaS are planning to commercialize this plant after the demo on this pilot plant, which is already semiindustrial. Even if it is not equipped as an industrial plant, with an integrated pretreatment and the possibility to apply both the primer and the top coat, it is still a proof of concept on a very relevant scale”, adds Heiko Schneider.
“The process starts with the unrolling of the coil. Then, the coil goes through the coater. Right now, we decide which kind of coating to apply (primer or top coat) and its thickness. After the coating stage, the coil enters the furnace, which is 6 meters long. The furnace has two separate areas: one is the curing oven section and the other hosts the radiant burners. In between these two areas there
are the transparent windows. At the entrance and at the exit of the furnace there are the inertization chambers, divided in turn in two separate areas: in one area, the injection of the exhaust gas from the burners takes place, in order to build a barrier against the outside air. The second area is dedicated to the extraction of both the exhaust gas and the air from the outside. Afterwards, there’s a cooling down phase with sprayed water. Then the coil is rolled again”, explains professor Trimis. “The different streams of the plant need to be pre-heated or cooled, so the plant features also a network of heat exchangers that adjust the temperatures levels of the different streams. For instance, the exhaust gas of the burners is not simply injected into the inertization chamber but it is first cooled down. While this happens, the gas is also used to pre-heat the air for the burners or for the recirculation of the solvents to have a constant temperature in the room. There’s also a network of air and gas supply with the corresponding valves. This external part of the plant is as big as the process area, but still very compact compared to standard systems”.
“Having demonstrated that this pilot plant works, the barriers to install a standard production setup are now lower. So, the goal is to build an industrial coil coating line and to start penetrating the market with this technology, which has the potential to change the game. Our duty now is to answer the possible concerns about the novelty and reliability of the plant and to demonstrate its great potential”, concludes Heiko Schneider.
Any contractor worthy of its name has one mission: meeting all customer requirements without ever stopping its production line. This is all the more imperative for coating contractors, especially those operating in a market requiring quality excellence, namely that of architecture. VAFE has found the technological tool to live up to this mission in a horizontal coating plant designed by Omsa, Futura Convogliatori Aerei and Gema. Thanks to independent transport circuits with different chain speeds, automation 4.0, a cellular pre-treatment tunnel, and two curing ovens (one for each booth), this line guarantees high productivity without ever stopping, extreme flexibility in terms of both treatment and part type, and high coating quality. Alessia Venturi, ipcm®
“Weknow who we are and what we can offer.” These few words from Giampiero Gritti encapsulate the key to the success of VAFE Srl, a contract coating company based in Grassobbio (Bergamo, Italy) specialising in the painting of special and non-standard metal sheets and profiles for metal architecture. “Our finishes remain on the surface, but our expertise goes deeper” is the motto of this firm, which over the years has gradually implemented a wide range of treatment and coating cycles capable of meeting any requirement of the architectural sector, as well as gaining all the necessary certifications, qualifications, and approvals to work in this demanding, multifaceted, and sometimes whimsical sector. VAFE turned 60 years old in 2022: founded by the grandfather of the current generation (the third one) at the helm of the company, it has been operating in the field of industrial metal pre-treatment and coating in Italy and Europe since 1962. From its original site in a “chicken coop” in the Upper Town of Bergamo, as Gritti put is, VAFE soon moved to Grassobbio, where it is still based today, implementing powder coating technologies right from their first appearance on the industrial finishing market. Today, VAFE offers high-tech treatments giving unrivalled aesthetic qualities and durability to structures, profiles, and components made of extruded, die-cast, and rolled aluminium, but also iron, Sendzimir iron, and galvanised steel. Over the years, it has gained all the qualifications and certifications needed to work for an international
clientele: Qualicoat and Qualicoat Seaside for aluminium – it is the only company in Italy and among the few in Europe to have this certification for profiles up to 13 metres –, Qualisteelcoat for iron and galvanised steel up to corrosion class C5, and the approvals of all major Italian customers in the architecture and infrastructure sector.
Taking over from his father at the reins of VAFE, Giampiero boosted the company’s development by conquering a niche of excellence within the metal architecture market, which is that of the finishing of special and non-standard profiles (up to 13 m in length and 8-10 kg/m2 in weight), cladding sheets for curtain walls, accessories, and square tubes for awnings, and even entering the design, lighting, automotive, and transport sectors. All industries in which finishing quality is held in very high regard, not only for aesthetic reasons but also with a view to functionality and resistance to weathering, ageing, and corrosion.
Recently, Giampiero has handed the company over to his sons, Matteo and Francesco Gritti and his nephew Stefano Algeri, the third generation of the family, who are continuing to grow the business. They are the ones who, on the occasion of the 60th anniversary celebrations in July, explained to us the reasons behind VAFE’s most recent investment, the replacement of one of the existing coating plants for bars up to 8 metres long with a new state-of-the-art line designed by Omsa (Besana in Brianza, Monza e Brianza, Italy), Futura Convogliatori Aerei (Robecco Pavese, Pavia, Italy) and Gema Europe (Trezzano sul Naviglio, Milan).
This fully automatic line is able to guarantee a very high productivity and such a flexibility degree that VAFE can meet any customer need and demand without ever stopping the plant, thus reaching excellence in contract coating. Let us see how.
With its three last generation plants, VAFE offers a wide range of treatment cycles that guarantee high-quality and durable results even for the most complex projects.
Horizontal coating plant for materials up to 13 metres
• maximum length > 13,000 mm
• maximum height > 3,000 mm
• maximum width > 1,500 mm
• maximum load capacity > 3,000 kg
Horizontal coating plant for materials up to 8 metres
• maximum length > 8,000 mm
• maximum height > 2,000 mm
• maximum width > 450 mm
• maximum load capacity > 800 kg
Vertical coating plant for materials up to 3 metres
• maximum length > 1,200 mm
• maximum height > 3,000 mm
• maximum width > 600 mm
• maximum load capacity > 120 kg.
The new plant created by the technical departments of OMSA and Futura replaced the existing line for treating materials up to 8 metres, which after thirty years of full use it was necessary to change with the new technologies on the market. “The project for this plant started about five years ago. My uncle Giampiero had realised that in order to differentiate itself within a market as varied as the contract coating one, in which there are companies of very different natures and with very different skills, VAFE had to stand out by offering a highly specific service with premium quality and flexibility levels. It was therefore strictly necessary to upgrade our ‘medium-sized’ plant handling materials up to 8 metres and devote it exclusively to architectural “Thisapplications”.newplant has enabled us to improve productivity and quality – not only in terms of product quality, but also of work quality. The fact that it is structured in stages over several circuits independent of each other enables us to stop individual chains in the event of delays or changed needs at certain stages of treatment. Its design and automation characteristics optimise the time required by each process step, minimise the error rate because the operators do not have to ‘run after’ production, make the line speed constant, and ensure consistently high finishing quality,” adds Stefano Algieri.
“We have equipped this plant with a power&free conveyor with a maximum load capacity of 1 tonne (800 kg + the weight of the load bar) and several independent transport circuits,” says Stefano Gerletti, sales manager at Futura Convogliatori Aerei. “Design-wise, the most complicated aspect proved to be the need to fit a conveyor with such a
capacity and with 1 km of chain into a very small space within the VAFE factory. There are two loading bays, a main one for standard batches with a pre-load area (which allows the plant to be loaded at the end of the working day and given automatic one-hour operational autonomy for the following day, even unmanned) and a second, smaller one for out-of-standard parts, special products, and smaller volumes”.
“In order to reach the maximum productivity allowed for this type of operations, we have equipped the conveyor with separate circuits with independent chains,” adds Gerletti. “In addition, we have mounted a 400 mm oscillator on each load bar to optimise drainage between one stage and another: the system unhooks the load bars from the fast chain and the oscillator comes into operation.”
“The ingenuity of this plant’s design lies in the fact that, thanks to the various circuits with which its conveyor is equipped, the booths can work independently and the
Get to know the world’s first effect pigment with such a strong, highly chromatic dark blue. Thanks to ECKART’s patented anti-fading technology, EDELSTEIN Sapphire Blue retains this powerful color from any viewing angle.
Contact us for more information: ECKART GmbH · Guentersthal 4 · 91235 Hartenstein · Germany Phone +49 9152 77-0 · info.eckart@altana.com · www.eckart.net
The MagicCompact EquiFlow BA04 booth.load bars can be recirculated in the same booth,” notes Stefano Algieri.
“Each booth is equipped with its own storage buffer that allows two-coat systems to be applied without losing productivity. The same applies to colour change operations: the storage buffers created along the conveyor path, combined with smart production scheduling, give us extreme flexibility. This enables us to meet any customer requirement without ever reducing our productivity or stopping the line.”
The plant consists of a 7-stage pass-through spray pre-treatment tunnel with four cells (of which two, i.e. the rinse cells, are double), performing a final stage of norinse passivating product atomising. The cycle is both Qualicoat and Qualisteelcoat certified as all active baths (alkaline phosphodegreasing, acid deoxidation, and final conversion) can use different chemicals depending on whether the material being treated is aluminium or iron/galvanised
“Themetal.plant management software package performs a product switch according to the recipe selected during loading,” explains Gilberto Riva from Omsa’s technical sales department. “The line continues with a drying oven with an air vein exchanger, two automatic powder application booths, and a gelling oven and a curing oven, both with an indirect heat exchanger. Each of the two ovens is assigned to a spray booth; in particular, the gelling oven is used to gel primers in the case of two-coat finishing cycles (and thus prevent the part to pass through the booth twice) and small colour batches. Booths and ovens can work simultaneously.”
The coating booths use conventional Venturi application technology on the reciprocators and dense phase technology on the manual touch-up units.
“We have two booths: one was revamped with Gema’s Venturi equipment and the second is a new MagicCompact Equiflow booth also supplied by Gema and linked to the latest OptiCenter OC06 All-In-One powder centre,” explains Francesco Gritti. “We decided to adapt the application technology of the new booth, and we chose the updated All-in-One device, based on the Venturi system, which guarantees higher performance and application speed. Indeed, after various comparative tests that I have personally carried out, I found that the dense phase with the OptiSpray AP01 application pumps was crucial in eliminating the Faraday Cage effect in manual touchup operations, resulting decisive for some particularly complex products”.
Futura and Omsa co-developed the management software package 4.0 for VAFE’s line. “All orders are uploaded into the management system and each of them is assigned a code containing the type of paint, the treatment cycle, and the curing time,” explains Stefano Gerletti from Futura.
“The loading and unloading stations are equipped with two panels where the operators can enter the load bar’s code either with a bar code gun or manually and select the required process from the PC. The load bar enters the line and, from then on, it is subjected to the entire process flow matching with the information assigned to it. Human error is reduced to a minimum, as the operator can only make a mistake in selecting the process, a detail that is however
checked repeatedly during the whole workflow. In front of the pretreatment tunnel, the Futura software programme ‘hands over’ the code to the OMSA programme, which continues to process the part based on the information assigned to it. The same happens in front of the curing ovens. It is possible to follow the position of each load bar on the touch panel through the shift register (the virtual tracking system). Clicking on an individual load bar opens a further window containing all information related to it.”
“Thanks to the investment in this plant, not only have we increased our production capacity and achieved a high level of flexibility, but we can also investigate and correct, in real time, any problems that arise during treatment,” states Matteo Gritti.
“Flexibility is the aspect that has pleased us the most because we are heavily focussing on two-coat painting cycles,” indicates Stefano Algieri. “We apply numerous two-coat systems on products made in outdoor iron and Sendzimir iron, which consists in pre-galvanised sheets that have no real edge protection. However, we also recommend their use on aluminium, for example for products intended to be installed on the seafront: where the budget allows, we prefer to combine Qualicoat Seaside-level protection with primer application.”
“We can therefore be very satisfied with this investment. It was just what we needed to further develop VAFE’s market,” summarises Francesco Gritti. “We are also pleased with the work of our suppliers, in terms not only of technologies installed but also of the level of the service offered and the way they support us.”
The plant’s control panel.Syntha Pulvin® - the premier Architectural Powder Coatings brand in Europe, setting the industry standard in terms of innovation, quality, and service. Our wide range of Architectural Powder Coatings are formulated to decorate and protect architectural aluminum and galvanized steel exposed to extreme weather and ultraviolet conditions.
Contact us today on gi.emeai.marketing@sherwin.com to receive your colour card from one of our collections: Fine Texture, Anodite, Vision 2020, Echelon.
Visit: industrial.sherwin.eu | www.synthapulvin.com
Gabriele Lazzari, ipcm®
BT Group has become a market protagonist in the Italian and international pergola and awning sector thanks to the flexibility of its production and the high customisation degree of its offer. The increase in demand that the sun protection industry has seen in recent years has enabled it to expand its operations with a new automatic powder coating plant designed, built, and installed by Silvi in collaboration with Futura, Chemetall, and Wagner.
1
Afterclosing 2018 with a turnover of 1,244 million Euros, Pambianco, a consulting company operating in the luxury sector, reported that the Italian awning and pergola industry saw an increase in turnover and profit margins in the following years as well1 Federlegno Arredo also disclosed that demand further increased immediately after the lockdown periods, as confirmed by BT Group, a multinational group based in Lesmo (Monza e Brianza, Italy) and active in the production of outdoor domestic sunscreen structures. This firm was founded in 1954 by Ambrogio Radaelli in Monza, whose province is firmly rooted in traditional craftsmanship. Over the years, it has expanded its production, the types of solutions, and the degree of customisation offered to its customers, managing to serve not only the Italian but also the international market.
“BT Group has become a market protagonist in the sun protection industry thanks to its production flexibility. Our awnings, pergolas, and bioclimatic awnings are in fact the ideal extension of any home’s interior and they must therefore be able to meet all kinds of needs: customisation does not only concern colours and finishes, but also dimensions, shapes, movement mechanisms, and accessories,” states BT Group CEO Andrea Radaelli. “The COVID-19 pandemic has dramatically increased demand, as the general public has realised that our products are a great solution for living outdoors without leaving the comfort and security of one’s own house.”
In order to cope with such an increase in orders, the company turned to Silvi Srl (Peregallo di Lesmo, Monza e Brianza) for the design, construction, and installation of a new coating system that would allow it to speed up production without sacrificing product quality.
Fully customised production and finishing BT Group deals in-house with the whole design phase, always remaining in close contact with customers to offer the highest possible level of customisation. The raw extruded aluminium profiles and all the other components used to build the structures of the company are acquired by Italian suppliers.
“We still use some plastic components but, since the market is shifting towards more environmentally friendly solutions, we are trying to replace them with aluminium parts that are die cast. This new trend is an advantage for us, as our group includes the foundry Form, specialising in the moulding of aluminium and zamak,” indicates sales manager Alessandro Citterio. “Profiles are acquired raw and then cut to the required size and subjected to machining using state-of-the-art CNC systems in our light metalwork department. The parts are finally sent to our finishing department.”
“The coating process is the most important phase of our entire production cycle,” says plant manager Luca Grazzi. “In addition to often being the first aspect that customers notice, finishes are also the
The two standard colour palettes offered by BT Group.element about which we may receive the most quality complaints, due to constant handling, transport, and assembly operations on site.” BT Group offers its customers numerous tints from two different colour palettes: one includes matte RAL colours with a slightly textured finish, whereas the other includes several metallic colours. “The most popular shades are white, which accounts for 40% of our production, and grey and brown shades with a textured finish, which create a beautiful aesthetic effect. However, in the awning sector glossy shades are still highly requested, especially white, ivory, and 7035 grey,” explains
“AsCitterio.already mentioned, flexibility is our main strength. Therefore, we can also utilise powder coatings personally selected by our customers, provided they meet all our quality requirements. Our products are certainly going to be exposed outdoors, but in the case of some orders, we do not know in depth the environmental characteristics of the place where they will be installed and the degree of corrosion to which they will be subjected. This is why we always comply with the quality standards of the QUALICOAT class 2 certification and we apply polyester powder coatings, as they guarantee greater resistance and better penetration even on complex-shaped parts,” notes Grazzi.
BT Group already owned a coating plant installed at the beginning of the century in its long-standing factory in Lesmo. Intended for coating bars, die-cast parts, and iron frames, it was subsequently upgraded by Silvi itself. However, as demand increased, soon the company was once more no longer able to cope with the new production volumes. It initially turned to a few coating contractors, but even they could not guarantee that the required delivery time would be met. BT Group therefore decided to invest in a new coating line.
“We were, and still are completely satisfied with the performance of the system revamped by Silvi. In addition, we visited the plants of other coaters to better understand the advantages and disadvantages of other painting technologies. This is why, after an initial analysis phase, we decided to once again entrust Silvi with the design of the new plant. At the same time, we acquired a plot of land on which to build the new paint shop and a warehouse to store our bars,” adds Citterio.
The new plant installed by the company has a large loading area, the starting point of a power&free conveyor built by Futura Convogliatori.
The entrance to the pre-treatment tunnel performing the process developed by Chemetall.Made entirely of stainless steel, the spray tunnel is configured in stations separated by doors to guarantee a more efficient process and avoid contamination among baths. All spraying bars are equipped with special filters, typical of cataphoresis tanks, to improve the application of the treatment solutions. The tunnel is completed by two 3,000-litre recirculation demineralisers for the production of demineralised water, which is then sent to a storage tank, and a 12,000-litre vacuum evaporator to treat waste water. These make the line a “zero liquid discharge” plant.
“During the design phase of the new plant,” says Andrea Monti, the technical coordinator of the Surface Treatment global business unit of BASF’s Coatings division, operating under the Chemetall brand, “we analysed BT Group’s requirements and, together with them, we chose a pre-treatment cycle with the Oxsilan® thin-film hybrid nanotechnology solution, which combines the corrosion-
inhibiting properties of inorganic metals such as zirconium with the flexibility provided by silanes. It is the same solution used in the first plant ever since it was revamped to replace the hexavalent chromium-based process. While it is true that some QUALICOAT Class 2 paints presented adhesion problems in the past, the inorganic polymer elements of Chemetall’s technologies help solve them. In this way, the profiles’ surfaces are prepared for the application of the several different coatings used by BT Group.”
The pre-treatment cycle consists of ten stages. It starts with strong alkaline pickling to degrease and deoxidise the profiles in order to eliminate the “deformation layer” formed during extrusion and eliminate any organic
Aftercontaminants.tworinses
with mains water, a multimetal acid degreasing stage is carried out to complete dissolution of the alloying elements resurfaced due to the removal of the “deformation layer”, which could cause filiform corrosion. This is followed by a further rinse with mains water to remove the metal residues detached by the previous steps and one with demineralised water, which eliminates the metals contained in the mains water and prepares the profiles to enter the nanotechnology conversion chamber.
Finally, after a second rinse with demineralised water, the conveyor’s tilting system returns the load bars to the horizontal axis and takes them to the drying oven with an indirect flame heater operating at 120-140 °C.
On leaving the drying oven, the overhead conveyor directs the load bars towards one the two automatic coating booths supplied by J. Wagner GmbH, one applying light colours and the other dark colours, both placed in a pressurised and air-conditioned clean room with a constant temperature of 25 °C in order to prevent contamination. Each booth is equipped with two opposing
reciprocators, two manual pre- and postfinishing stations, and twelve automatic guns with traditional Venturi feeding technology, which move closer to or further away from the profiles to favour optimal adhesion and penetration of the powder coating, thanks to an optical sensor located at the entrance of the booth that detects the size and geometry of “Weworkpieces.alsospecifically requested the SuperCenter EVO powder center, thanks to which we have the possibility of sifting and mixing virgin and recovery powder - thus keeping the application quality constant - and which is able to dictate and automatically perform the colour change phases, regardless of the operator’s experience. Indeed, because we perform as many as fifteen per shift, we wanted our colour change operations to be managed independently and as efficiently as possible. Currently a colour change takes from four to thirteen minutes (with an average of eight) depending on the duration of the batch and the type of powders used”, says Grazzi.
“We prefer to make sure our results’ quality level is high. This is why we also experimented with different arrangements of the profiles on the load bars, to try and further optimise our coating process. At the end of the cycle, moreover, our operators carefully check the quality degree of each individual profile.”
After leaving the two coating booths, the components are taken to a gelling prechamber to prevent colour dispersion and then to the curing oven. Finally, they dwell in a storage buffer to cool down before being unloaded and immediately packaged, in order to avoid any excessive handling or damage during transport.
“This plant has enabled us to exceed a salt spray resistance value of one thousand hours. It is extremely efficient and we are completely pleased with it. It has been in operation for over five months, but we have never
A detail of the power&free overhead conveyor (above) and the exterior of the clean room with the two booths applying light and dark colours, respectively.encountered any difficulties or problems so far. This is also thanks to BT Group, which interacted with all the partners involved with the aim of providing the most suitable solutions for our individual needs,” states “OurCitterio.first step was to create a working group that included us from Silvi, the technical management of BT Group, Futura, Chemetall, and Wagner. We listened to the customer’s requests and we each supplied a key element to solve a specific issue. Then, we also worked with the provider in charge of BT Group’s management system, in order to interconnect the new Industry 4.0-oriented plant with the company’s management software package from the outset. Thanks to the flexibility shown by all
the parties involved, we were able to install and test the entire plant on time, despite the problems caused by the shortage of raw materials,” says a satisfied Daniele Fumagalli, the General Manager of Silvi. “The choice of relying on Silvi once again proved to be a winning one. It brought us both quantitative benefits, because we were able to increase production, and qualitative advantages. We did not think that the development and implementation of the project could proceed so quickly. We are also happy to have involved all of our operators from the very beginning, as they were able to learn all of the system’s functions and make it highly efficient. In fact, we will soon start working on two shifts,” concludes Grazzi.
has recently launched SYNAQUA® 9511, a new performance waterborne binder specifically designed for the formulation of industrial paints with reduced VOC levels (<150 g/l). The new binder developed by Arkema is a waterborne acrylic polyol emulsion with hydroxyl groups (3% OH) specifically designed for challenging industrial applications. SYNAQUA 9511 is then suitable for both top-coat and mono-coat applications on several substrates such as metal, plastic, glass, wood and concrete flooring.
“SYNAQUA® 9511 acrylic polyol emulsion offers significantly lower VOC capabilities and performs well in 2K or 1K stoving systems. Our goal was to help industrial paint formulators more easily meet their sustainability goals by achieving lower VOC levels with a high-performance waterborne solution,” has stated Claire Reynier, the global marketing and business development manager at Arkema Coating Solutions. So, the coatings produced with the company’s new product help manufacturers to meet key performance target of durability, gloss,
adhesion and chemical resistance. Specific benefits include:
• On Metal (2K PU Topcoat): low VOC capability (86 g/l), chemical resistance, durability and good mechanical properties;
• On Metal (1K Stoving Topcoat): low VOC capability (100g/l), good hardness, chemical resistance and low yellowing;
• On Plastic (2K PU Topcoat): low VOC capability (85 g/l), good adhesion, high hardness, chemical resistance and durability;
• On Glass (1K Stoving Monocoat): Low VOC capability (100 g/l), high hardness, good adhesion, water resistance and chemical resistance. “Sustainability is a core component of everything we do, from research, new product development, to manufacturing, to how we ship and handle our products. We are continually looking for new ways to help our customers meet current and emerging sustainability challenges in this industry,” has concluded Reynier.
For further information: www.coatingresins-arkema.com
Arkema has introduced SYNAQUA® 9511, a new acrylic polyol emulsion specifically developed for challenging industrial applications. ArkemaSun Chemical has launched Paliocrom® Satin Gold EH 3600, a mid-shade golden aluminium-based effect pigment developed for automotive and high-performance industrial coatings.
allows for the thin film thickness of automotive basecoats due to the small particle size of the passivated, iron oxide coated, aluminium flake Paliocromsubstrate.
aluminium effect pigments are the ideal choice for modern automotive and high-performance industrial coatings. They provide excellent coverage and extreme saturation, suitable in thin film applications for yellow-to-red premium colours.
“We are thrilled to be introducing Satin Gold as part of our Paliocrom family of products,” said Michael Venturini, Marketing Director, Color Materials, Sun Chemical. “Paliocrom pigments are the industry standard and Satin Gold will provide another superior travel and hiding colour option for automotive and industrial coatings applications.”
SunChemical has introduced Paliocrom® Satin Gold EH 3600 (L 2131), a medium-toned golden aluminium-based effect pigment. The new pigment has a distinct satin character, high chroma as well as an extremely smooth appearance. Satin Gold offers a unique colour travel, excellent gloss levels and experience in finishing
For further information: https://bit.ly/3qd4ENw
Group specialises in the design and manufacture of components for outdoor awnings. The company, founded in 1983 in the province of Venice, is one of the main world players in the sector of components and accessories for outdoor blinds and sun screens, with branches not only in Europe (Spain, France, and Sweden), but also overseas, in the United States. With over thirty-five years of experience in the field, this industrial group also owns the successful brand KE, with commercial and production offices in Italy, Spain, France, and the United States.
BATBAT’s product range is divided into two macro-categories: parts and systems for various types of awnings and for vertical drop-down blinds. Its component portfolio is among the widest and most complete on the market: it includes not only standard systems but also customised solutions that are made to measure according to customer needs. Diversification and product quality have in fact allowed this company to establish itself on the market; however, they are also one of the aspects that make its production cycle more complex and the coating stage (which plays a strategic role) more difficult to manage. Rostirolla
Rostirolla developed and supplied BAT Group, an international leading manufacturer of components for outdoor awnings, with a more flexible, efficient, and durable hanging system making operators more autonomous in the management of the material to be loaded on the coating line. The new hanging concept for awning components supplied by Rostirolla to BAT Group.This is the reason why BAT asked Rostirolla Srl, a manufacturer of hanging and masking systems, to provide it with the most suitable tools to make its coating line more efficient.
The entire production cycle takes place in-house and starts with the creation of a mould in the mechanical department after the design and preliminary engineering phases carried out by the technical team, who use a polymer 3D printer for part prototyping and checking before production start-up. After moulding, the parts move on to shot blasting in order to remove burrs, tumbling in order to eliminate small surface imperfections, and sanding by means of two robots equipped with cameras for constant monitoring. The parts to be precision-machined and those made in extruded aluminium are then taken to the machining department, equipped with machining centres (horizontal milling plants), sliding-head lathes for making small workpieces, and presses for moulding Afterwards,plastics.theresulting components are taken to the coating department, where they are pre-treated in an 8-stage pre-treatment system. The degreasing, deoxidisation, and protective treatments carried out prior to painting ensure perfect adhesion of the polyester powder to be applied and, therefore, increased durability of components, which
must withstand even the harshest environmental conditions generated by sun, wind, and water. This is also why the products are subjected to salt spray tests in compliance with the standard ISO9227, confirming the quality and consistency of BAT’s processes.
The last production phase takes place in the kit assembly and arm assembly departments. The former is equipped with independent workbenches, whereas the latter has four production lines for the manufacture (assembly, precharge, fastening) of all types of extendable arms. The line ends with a control, cleaning, and packaging station.
One of the main bottlenecks in this production cycle was the hanging of parts onto the conveyor’s frames in the coating department. Pierluigi Rostirolla, the owner of the eponymous company together with his brother Simone, explains: “Being able to manage the hanging of each workpiece to be coated in the best possible way and, above all, autonomously is essential, because it leads to greater efficiency of the entire painting cycle and, consequently, to considerable energy savings. Therefore, we designed a hanging system that could be adapted to BAT’s diversified production and that includes our P25 series welded columns and combs, GNW series combs, and their related stripping boxes. The combination of these elements enables BAT to coat most of its components with one system, by simply adjusting the distance Rostirolla
between one hook and another in both width and height. Furthermore, the harmonic steel in which they are made allows supporting heavy weights even with a small diameter (e.g. Ø2).” The combination of the recently-launched GNW interlocking system and the P20/P25 columns further speeds up the loading of components by utilising the available space in the paintshop in the most efficient way.
Rostirolla also supplies BAT with special P25 series combs, designed specifically for a limited number of components. “It often happens that a standard hook does not allow a workpiece to be hung correctly, either because it would not remain in the required position or because it cannot be hung by the only place where a mark can be left: in these cases, special frames are normally built. BAT has been using our P25 columns for a few years now, which enable it to create a customised comb structure. Thanks to the flexible characteristics of the P25 system,” points out Pierluigi, “mounting the final structure is so simple and intuitive that it can be even carried out quickly and directly on the chain.” Finally, BAT uses the boxes supplied by Rostirolla for comb paint stripping: “When the coating layer deposited on the combs is too thick,
they are placed on small trolleys and sent to the paint stripping plant. This prevents the comb hooks from jamming together during transport and paint stripping, so that afterwards they are immediately ready for a new coating cycle. In any case, the hooks can be replaced and fitted in a different position, depending on customer needs.”
Optimising part hanging has proved to be strategic for improving and speeding up BAT Group’s production flow. For a company like this, which strives for maximum customisation of its awning systems and components, equipping itself with the right tools to make production smoother and more flexible is a must – and the new hanging concept developed by Rostirolla allows doing so by becoming even more autonomous in part loading management prior to coating. Rostirolla thus proved to be a supplier able to immediately understand the problems of a paintshop and offer the perfect system for a rapid solution.
For further information: www.rostirolla.it
Rostirolla supplied BAT with special P25 series combs, designed specifically for a limited number of components. A hanging system designed in this way makes the operator more autonomous in handling the material to be loaded onto the line.Gema©
The new powder coating technology developed by Gema allows the automatic coating of tricky areas.
an international manufacturer of powder coating technologies and equipment, has recently presented the multigun axis UA05-x. The new solution developed by the company has been specifically designed for applications where top or underside coating with multiple guns are required. The multi-gun axis UA05-x employs a single positioning axis for the horizontal alignment of up to three automatic guns during the coating of complex components and XXL parts. In combination with the vertical Z-axis, it then unfolds its full strength to solve complex challenges allowing new application solutions such as fixed gun positioning, horizontal oscillation across the work piece and applications where
vertical gun positioning or top and/or bottom product tracking are UA05required.isavailable
in two different versions: UA05-2 with two automatic guns and UA05-3 with the automatic guns. The compact design allows the guns to be arranged in a single row in a grid dimension of only 87 mm, ensuring the automatic coating of tricky areas and offering a flexible approach for top-, underside- and deep contour coating. In addition, the new Gema technology is also expandable with angled nozzles and extensions to further increase the application range.
For further information: www.gemapowdercoating.com/en/
ECKART launched the new ProFlake Zn 3000 zinc flake pigment which is optimized for sustainable corrosion protective paint systems.
Following the revision of norms and regulations that now allow a more flexible use of zinc flake pigments for the formulation of performance-based corrosion protective paints, ECKART has developed ProFlake Zn 3000 zinc flake pigment which allows for significantly lower zinc content in formulations. This makes more sustainable corrosion protective formulations for heavy duty and a reduced CO2 footprint compared to currently applied corrosion protective paints, possible. The percolation between these zinc flakes as well as their additional barrier layer formation ensures ideal corrosion protection, providing a clear advantage over existing zinc systems. ProFlake Zn 3000 zinc flake-based paints are also simple to handle and apply, and provide limited settlement properties. The new 31 µm (D50) product is ideally suited for use in marine, ship or bridge construction coatings, among others.
Custom-built painting installations
Shot blasting booths
Washing tunnels
Liquid painting installations
Powder painting booths verniciatura
Curing ovens
Eurotherm S.p.A.
T +39 011 98 23 500 | M info@eurotherm.eu
Eurotherm Oberflächentechnik GmbH
T +49-7571-92795-10 | M
Eurotherm France S.A.S.
T +33 (0) 4 90 55 |
In 1962, Ravarini Castoldi & C. Srl launched TURBODYN®, the first fully Italian-made electrostatic gun. The company has since expanded its range with a variety of electrostatic powder and liquid coating equipment, such as the recently launched TURBODYN® 50K high-speed automatic rotary bell atomiser.
Castoldi & C. Srl is a long-standing Italian company founded in Milan in 1867 by Carlo Ravarini, the grandfather of current sole director Luigi. Although it initially produced walking sticks, its operations evolved over the years to include the manufacture of electrostatic industrial coating equipment under the brand name
ELETTROSPRAY®Thisincludes,inparticular, TURBODYN®, the first fully Italian-made electrostatic gun launched on the market in 1962. Over the course of the last sixty years, the TURBODYN® range has been modified, updated, and expanded, but always reflecting the company’s constant evolution and its goal of providing customers with state-of-the-art technologies that guarantee high-quality coating results. “Our first gun was obviously a completely different device compared with the current solutions offered by the ELETTROSPRAY® brand, but it marked the beginning of a great adventure that continues to this day,” fondly says Carlo Ravarini, the son of current sole director Luigi, a true protagonist of the painting industry’s history. “It was a manual electrostatic rotary bell system. Over time, of course, we have further expanded and renewed our range with
automatic technologies, such as our flagship product TURBODYN® 50 K and its recently introduced TURBODYN® 50K-W version, a multi-purpose solution suitable for all sectors utilising electrostatically charged waterbased paints.”
TURBODYN® 50 K
TURBODYN® 50 K is a high-speed electrostatic rotary bell atomising unit that can be mounted on both reciprocators and coating robots. Suitable for metal, wood, and plastic substrates, this technology can be used at a speed between 5,000 and 50,000 rpm. The electronic automatic adjustment device allows the rotation speed to be kept constant within a tolerance of +/- 1.5% under all working conditions. All information is transferred to the control panel in real time via a fibre optic cable, enabling the operator to monitor the parameters, modify them according to coating requirements, and quickly intervene in the event of an
“Thiserror.isone of the few technologies capable of controlling revolutions through fibre optics with an accuracy of +/- 1.5%. We noticed that
Ravarini Castoldi & C.’s history. The entrance to the Painting Test Room.some customers found it difficult to keep speed constant, because the paint product can heat up during operations, decreasing viscosity and consequently increasing the flow rate and jeopardising the paint layer’s uniformity. With TURBODYN 50® K, however, revolutions remain constant. Therefore, compressed air consumption is also significantly reduced: a constant speed value of 25,000 rpm requires only 1 bar,” explains Luigi Ravarini.
The unit’s head is equipped with three integrated pneumatically controlled valves, reducing the pipelines between the paint valve and the bell, between the paint valve and the recirculation valve, and between the cleaning diluent valve and the bell. This reduces both the time needed for colour change operations and diluent consumption. TURBODYN® 50 K can also be customised with additional equipment. An electrostatic ring reflector can be mounted on the unit’s head, acting as a counter-electrode to direct the electrostatic field towards the workpieces to be coated. Alternatively, a ring blower can be fitted, which, in addition to acting as a reflector, allows the cloud of diluent to be blown towards the booth’s floor during colour change and bell cleaning operations. “We wanted to create a technology that was compact but
at the same time enabled users to reach every area, in order to simplify cleaning and maintenance. Moreover, the turbine and its bearings are protected against accidental paint or solvent pouring by a labyrinth and permanent pressurisation of the entire casing.”
TURBODYN® 50K-W
TURBODYN® 50K-W is the latest high-speed automatic electrostatic rotary bell atomiser developed by Ravarini Castoldi, conceived specifically for the application of water-based coatings without requiring insulation of paint feeders. The bell’s end is equipped with eight protruding electrodes that give the sprayed paint an electrostatic charge, while the bell remains grounded. “We have developed this technology to enable coaters to use conventional paint feeders, such as permanently grounded piston or gear pumps, as is the norm with TURBODYN® 50 K and other solvent-based paint products,” indicates Ravarini. “Installing it is therefore simpler and more economical, while the atomising unit itself is easy to use and requires less maintenance even if several feeders are used for different colours, all permanently grounded.”
The inside of the Painting Test Room with its equipment. The TURBODYN® 50 K automatic electrostatic atomiser.Like the solvent-based liquid paint version, the TURBODYN® 50K-W is equipped with electronic rotation speed control to ensure maximum application uniformity. However, this automatic electrostatic atomiser differs from other technologies in its insulation casing. “This simplifies the device’s use, because customers no longer have to insulate the different tanks with the various colours and their related pumps: for companies requiring a solution for efficiently applying water-soluble paints, we always recommend TURBODYN® 50 K-W,” states Ravarini. The other technologies offered by Ravarini Castoldi & C.
Over the last sixty years, in addition to designing industrial coating equipment, Ravarini Castoldi has developed many other technologies for the application of water- and solvent-based powder and liquid paints for different markets, such as the mechanical, aluminium, wood, plastic, and agro-food industries. In its factory in Cesano Boscone (Milan, Italy), an entire wing is also dedicated to the manufacture of special equipment for electrostatic steel and aluminium coil oiling for the automotive, food, and household appliance sectors.
In 1986, Ravarini Castoldi manufactured its first electrostatic blade oiler
at the specific request of a customer for use on one of its pickling lines. “That first experience was a success: its excellent performance level and ease of maintenance convinced us to invest in this technology as well. Today, we can supply high voltage electrostatic oilers for cold and hot rolling mills and many other machining lines, including pickling, rolling, recoiling, cutting, and inspection lines.”
The importance of cooperating with customers
“Ravarini Castoldi’s distinguishing feature, however, does not only lie in our equipment, but also in the relationship we establish with our customers,” notes Carlo Ravarini. “In order to meet all their needs, it is essential for us to carry out multiple tests in our factory, in order to understand the performance level achieved by our technologies with the substrates and paint products they use. We have a test room dedicated exclusively to this activity: when a customer turns to us, we ask them to bring some of their parts and the coatings they would like to apply. We then carry out a series of tests to choose, in close collaboration with them, the technology best suited to their specific needs, so as to provide them with the most suitable equipment.”
The TURBODYN® 50K-W atomising unit. One of the electrostatic oilers manufactured by Ravarini Castoldi.Coating plastics with powders to a high standard has always been challenging. FreiLacke’s new conductive primer UR1967 makes the treated surfaces conductive with a special pigmentation to allow them to be painted with the same material as metals, for example. The UR1967 product is therefore the perfect addition to the company’s coatings family.
are lightweight materials with very good static properties. This is why they are widely used to manufacture components in numerous industries, such as automotive, mechanical engineering, furnishing, or sanitary. Their main disadvantage, on the other hand, is they are only suitable for powder coating to a limited extent, as they generally cannot withstand high curing temperatures. Indeed, the problem arises when a customer wants to have a machine’s components coated with the same look and the same surface structure as its metal ones: how can one achieve a coherent overall look?
FreiLacke’s horizontal coating systems offer a solution to this problem. They are so well matched to each other for different substrates that the coated components match perfectly in terms of colour tone, gloss, and structure and can be mounted next to each other without any visual issue.
As a rule, plastics do not have highly conductive surfaces: therefore, direct paint application with electrostatic processes is not possible. This is where the new FreiLacke EFDEDUR conductive primer UR1967 comes into play: thanks to its special pigmentation, it makes the plastic surfaces electrically conductive and thus prepares them optimally for the electrostatic application of the top coat.
“The primer can be applied on non-conductive substrates using conventional pneumatic technology. Thanks to its stable bonding agents, the UR1967 product withstands the curing process very well and it does not become brittle,” explains Andreas Morlock, FreiLacke’s Industrial Coatings Development and Application Technology Group Manager. This ensures excellent, permanent adhesion to the substrates.
Thanks to FreiLacke’s new conductive primer, plastic parts can now also be powder coated. Even when aluminium and plastic are used within the same workpiece, the end result is homogeneous.This results in the possibility to prepare plastic components with the conductive primer UR1967M so that they can be subsequently coated with the same powder as the other parts to be painted. In some cases, they can even be assembled before top coat application, with the great advantage that it is not necessary to paint each individual component separately. Another benefit is that less overspray is produced than with individual part coating.
“All these measures guarantee uniform, consistent surfaces that are identical in terms of colour tone, structure, and gloss degree on every component, which in turn results in a significantly improved finishing quality level,” indicates Andreas Hepting from FreiLacke’s industry sales Ofdepartment.course,the prerequisite for the successful use of this primer is the correct match between the paint system and the plastic material. The plastic as well as the conductive primer must withstand the thermal load in the oven. Finally, the primer layer must be applied evenly over the
entire surface, as a non-compact primer layer can lead to disturbances in the electrostatic field and thus jeopardise the top coat application process.
The EFDEDUR conductive primer UR1967 is a solvent-based, twocomponent polyurethane product containing isocyanate-crosslinking acrylate resin.
It is suitable for plastic substrates such as polycarbonate (PC), Acrylonitrile-Butadiene-Styrene copolymer (ABS), and others. This matte conductive primer has an application viscosity of 35-45 sec/4 mm; its maximum workability time is of 2 h at 20 °C.
Oven drying is possible up to 80 °C; when air-drying, it is dust dry after 10 min (drying degree 1 / ISO 9117-5), touch dry after 1.5 h (drying degree 4 / ISO 9117-5), and completely dry after 7 days (pendulum damping test / ISO 1522). Different colour shades are available on request.
FreiLacke has been synonymous with innovative paints and coatings since 1926. This family-owned company is now in its third generation and, with 600 employees at its headquarters in Döggingen (Germany), in the Black Forest, it develops customised solutions for customers in the wheel, car, mechanical engineering, contract coating, railway, wind power, functional furniture, storage, construction, and sanitary sectors.
As a modern family-run business in its third generation, its headquarters’ ties with the territory are just as important as worldwide sales and proximity to customers through subsidiaries and partners abroad.
Its product range of leading paint systems at the European level covers the entire spectrum from industrial coatings, powder coatings, and electrodeposition coatings to solutions for composites.
A global network of subsidiaries and partners worldwide handles international sales.
Environmental protection has always been a key issue for FreiLacke. That is why it strives to develop environmentally friendly products, reduce emissions, packaging materials, and waste, and use resources sparingly.
In 2019, FreiLacke was named one of the top 100 employers in Germany in the “Great Place to Work Competition” and it places a high value on the topic of training, with a ratio of 10%.
Florida International University – Miami (FL), United States
This 23, 2022, republished courtesy of the author.
Humanityis heading back to the moon, this time to stay. An innovation from the FIU College of Engineering and Computing could be key to the quest’s success.
NASA’s Artemis Program1 plans to build the first-ever base camp on the lunar surface. The agency seeks to generate scientific discoveries, economic benefits and inspiration for a new generation of explorers. Artemis’ success will depend in large part on protecting technology like rovers and excavation tools from the harsh elements of space. To help,
FIU’s Plasma Forming Laboratory2 has developed an innovative coating material to shield structures at their movement and pivot points-the chinks in their armour. This fall, a sample of the coating is heading to the International Space Station, where it will be mounted to a platform outside the facility far exposure to space. The coating will then be analysed for its resistance to radiation. Radiation can interrupt signal processing in electronics and shorten the service lite of structures.
“By attaching the material to the International Space Station, we can get close to simulating the real radiation that structures will face on the moon,” says Professor Arvind Agarwal, chair of the department of the
1 https://www.nasa.gov/specials/artemis/
2 https://pfl.fiu.edu/
mechanical and materials engineering department and director of the Plasma Forming Lab. FIU’s sample coating will be placed on the side of the International Space Station that directly faces the Sun. After six months, a crew of astronauts will take the material back to Earth far analysis. “Our team selected direct exposure to the sun because we want to be very harsh on our coatings,” says Sara Rengifo, a materials engineer at NASA who is working with Agarwal on the research.
FIU and NASA scientists will be watching closely for how the coating changes temperature as the space station orbits Earth. Meanwhile, back at FIU and NASA laboratories, the material will be tested for its durability against lunar dust, tiny shards of rock found in abundance on the moon’s surface.
NASA expects the test’s findings to benefit future missions. The resulting data could help the agency reduce service and repair needs. The research may also yield commercial implications in industries where materials face harsh conditions, such as in nuclear waste containment and hypersonic vehicles production. The research is a collaboration between public and private entities. Six Panthers are working on the project, including four interns. FIU is the principal academic partner.
A FIU - Florida International University’s lab has developed a new coating to protect machinery for use on the lunar surface - think rovers and excavators - against radiation levels up to 1,000 times greater than on Earth.
Through the use of particular shapes, colours and shadows, Alexander Calder has been able to convey a sense of uninterrupted motion to his art installations. From small wooden and metal sculptures to cars and even an airplane, the American artist has created an impressive collection of artworks that have been showcased during the exhibition “Modern from the Start”.
up in a family of classically trained artists, the American sculpture Alexander Calder has instead decided to revolutionise the concept of movement and space with his abstract colourful installations. He reimagined the concept of sculpture as an experiment of uninterrupted motion, upending centuries-old notions that claimed it should be static, grounded and dense by making artworks that often move freely and interact with their surroundings. “Calder’s objects are like the sea: always beginning over again, always new,” wrote the French philosopher Jean-Paul Sartre. This is clearly visible in “Modern from the Start”, an immersive art exhibition of 70 artworks from the American sculptor hosted by the Museum of Modern Art (MoMA) in Manhattan, New York. During his career, Calder developed a new method of sculpting: by
bending and twisting metal wire, he was basically capable of drawing three-dimensional figures in empty spaces. Bringing together painted stainless-steel sheets and other metal sculptures, iron rods and pipes, steel wires and wooden inserts, works on paper, jewellery and mobiles, the exhibition takes a deep dive into the full breadth of the artist’s career and inventiveness.
The compositions seem to keep themselves in balance while dancing. Despite being static, the sculptures suggest the idea of movement thanks to numerous wires and the lights reflected on the colourful Assculptures.amatter
of fact, Calder has always considered paints as another tool to convey a senso of movement, as also demonstrated by the DC8-62 plane and the BMW 3.0 CSL painted by the artist himself.
The DC-8-62 plane painted by Alexander Calder.
the required quality results), but also of opening up our field to professionals coming from different working environments, perhaps more related to conventional coating, but wishing to study these issues in greater depth.
In my years of experience in this sector, I have noticed that there is a lack of an intermediate professional role fitting in between more operational and more theoretical roles. I therefore enthusiastically embraced this new adventure and I am convinced that the course organised by the Academy will help us train exactly these rare professionals. On the other hand, we must ensure the continuity of the sector by training new generations of coil coating experts coming from both universities and technical institutes.
Theautumn session of the courses organised by ipcm® Academy, the training division of ipcm®, will begin in November with a day devoted to the in-depth study of the continuous coil coating process. We interviewed one of the lecturers, Sergio Bianchi, who has been working in the field of liquid and powder pre-coated aluminium for over twenty years and has already gained training experience at the university level.
What are the training needs of a complex sector such as coil coating?
Continuous-flow coil pre-coating, known as “coil coating”, is an advanced surface finishing process used for various metal substrates, with a total output of several million square metres per year. This is a niche sector, whose technology is not as well known as traditional painting: this is also why it is not easy to find specialised operators. This, in turn, is the reason why I personally believe that training is fundamental not only in terms of teaching the technical concepts needed to deal with this process (made complex by the sub-processes that characterise it and that must be perfectly synchronised to achieve
A coil coating plant treats between 10 and 15 metres per second: this already hints at one of its main challenges, namely the speed of the line, which is achieved through perfect integration of mechanics, thermodynamics, electronics, pre-treatment chemicals, and coating chemicals. The ability to manage all these aspects in a system that treats an average of 1000 metres of coil per cycle with a continuous flow is certainly the result of sound knowledge, but above all of experience. This is why I believe that training in this field is crucial, as well as why we will take our trainees to see how this treatment takes place in a longstanding company in the sector, Novelis, headquartered in Bresso, in the province of Milan.
During the first part of the day, I will present the process in all its details: the definition of the product in terms of metal quality, pre-treatment, and type of paint and the components of a continuous-flow liquid or powder coating line.
Then, we will visit the company’s coating department and control laboratory to see how this very special process takes place and experience first-hand the qualities of the paints used and the different types of finished products developed.
Stefano Prada, an expert in liquid coil coatings, and Emanuele
Magistrelli, a specialist in pre-treatment products, will also speak during the session. I will form a team with them, which will then be supported by our operators during the plant visit.
What goals do you intend to achieve with this new course?
This course is a challenge for me: the variety of expertise levels and backgrounds of the trainees call for clear explanations from me that take nothing for granted.
The aim is to train professionals who will then able to deal decisively and quickly with the problems that a coil coating process raises every day. Perhaps more so than in a traditional paint shop, reaction times are tight and action must be taken promptly. With this course, we aim at filling the training gap that characterises the coil pre-coating sector. I personally find that, rather than a specialised course in this field, a structured course such as the one offered by ipcm® Academy is more suited to the purpose, because it is set in a broader coating training context: with these skills, trainees can delve deeper into the subject of coil coating and then continue in that field if they consider it interesting enough. I would like to conclude by saying that, in my opinion, this type of training course will also allow our sector to open up to the wider world of coating more than ever before.
Knowing the customer journey is essential to push the right communication levers and send the right message at the right time. In today’s article we explain in detail what the customer journey is and how to implement the 5-stage model.
online, there are several versions of the customer journey, otherwise known as a buyer’s journey or marketing funnel or sales funnel. All these names refer to the journey that our buyer personas make to get to the purchase of our products and services. And, once the transaction is concluded, the factors that ensure their loyalty to our brand. Preparing a strategy based on a marketing funnel can help us not only to better visualize the different stages that make up the journey of our potential customers but also to identify and leverage the contents and channels most suitable for the stage in which they are, thus creating a more targeted communication strategy. But let’s start with a definition.
The term customer journey refers to the relationship that exists between a consumer and a brand, and identifies the itinerary that the consumer travels, from the first stage of searching for a product/service to satisfy a certain need up to the purchase phase.
In truth, the buyer’s journey does not end at the purchase stage, but continues afterwards, with a stage dedicated to brand loyalty. Now let’s see in detail the 5 stages that make up the customer journey and the most suitable communication levers for each phase.
In the awareness stage, the consumer is actively looking for solutions to solve a particular problem or need. Intercepting the need of our potential customers and presenting our solution to them is essential to ensure that they enter our sales funnel. Therefore, let’s try to garner their attention through blog articles, insights, social posts, advertising. In short, we must be active on all the channels that we believe will be consulted by our potential customer.
In the consideration stage, the prospect has come into contact with our brand but does not yet know us well enough to make a decision. It is also likely that they are considering our competitors, as well. Our task at this stage is to ensure that our brand is memorized by the prospect and associated with certain values, qualities, benefits and
is important to provide in-depth information and, above all, to underline what sets us apart from our competitors. Let’s leverage our channels to provide demonstrations or lead magnets such as white papers, eBooks, checklists, exclusive training sessions that can make the client understand our authority and our skills in the field.
In the conversion stage, our buyer personas have probably figured out which solution is right for them, they follow our pages and are subscribed to our newsletters. They only need to clear out any possible remaining doubt. In these cases, bearing the testimonials of other people who use and know our products or services, such as ambassadors, can help us tip the balance in our favour. This is also the stage in which to provide discounts and special offers.
At this stage, the consumer purchases our products or services. Often, many funnels stop here. However, the purchase is not the last stage of the customer journey, especially if we want our customer to continue to be so in the future.
In the retention phase, we must keep the customers engaged, understand if they are satisfied with the purchase, support them in case of need and then encourage them to buy again and activate word of mouth. A good re-marketing strategy, with tailored communications and offers, as well as a good after-sales service and customer support are the necessary ingredients to ensure that the customer is loyal to our brand and remains in the sales funnel.
Scan or click the QR code to read this article on our blog, and leave your comment on it
UCIF – Italian Surface Treatment Equipment Manufacturers’ Association Milan, Italy info@ucif.net
On 17 May, the Decree Law No. 50/2022 was published in the Italian Official Gazette, containing “Urgent measures on national energy policies, business productivity, and investment attraction, as well as on social policies and the Ukrainian crisis” (Aid Decree). This is a substantial measure (59 articles) allocating resources amounting to 16.7 billion Euros, an important initiative that was not put aside by the end of Draghi’s government. It involves three main areas: containing energy and fuel costs and simplifying the use of renewable energy sources; fostering economic
recovery and giving liquidity support to companies; and supporting workers against inflation. The decree’s design and development suffered from the particular economic situation. Indeed, it lacks structural measures, although it does outline a strategic direction in terms of the much-needed energy diversification. On the energy front, the measures to simplify authorisation procedures for renewable energy plants are valuable and aimed towards a structural change; the broadening of the credit assignment regulations is also commendable. The previous government emphasised three
priorities in this field: filling gas storage in anticipation of the 2022/2023 winter; completing the campaign to diversify gas supplies from other countries to replace the 29 billion cubic metres of gas imported from Russia by expanding sources; and strengthening the decarbonisation process thus accelerating the development of renewable sources and energy efficiency.
Whereas the enhancement of tax credits for the purchase of electricity and gas in support of both energy and gas-intensive and non-energy and gas-intensive businesses is welcome, these measures are still limited to the short term.
In addition, a review of the anchoring of credit standards to the de minimis regime would be called for, introduced by a parliamentary amendment. In order to foster the economic recovery, it would also be important to strengthen tax credits for intangible assets and
training 4.0 for 2022, as well as to implement measures to support internationalisation and the refinancing of the IPCEI fund. The labour and liquidity issues are also addressed in the decree, albeit still with a short-term perspective.
Finally, the section related to exceptional transports is valuable, aimed at including the so-called “super exceptional transports” in the regulations in force as of 9 November 2021 and at postponing the adoption of the decree that is to contain the guidelines for exceptional transport services by the Ministry of Infrastructure and Sustainable Mobility.
Together with the Institutional Relations Area of ANIMA Confindustria, UCIF is keeping a close eye on the application of this decree, which is going to have an impact not only on Italy’s industry but also on its economy in general.
Topics CARLTON,
Making its return to the Toronto Congress Centre for the first time since 2018, FABTECH Canada 2022 demonstrated the upcoming years’ advancements and solutions in metal fabrication and welding from June 14 – 16. The event represented an eagerness to return to business drawing over 5,500 attendees from Ontario and across Canada.
“The feedback has been overwhelmingly positive,” said John Catalano, SME senior director, FABTECH. “The show remains the best place for attendees to explore the latest technology advancements, connect with peers, network, and gain a competitive business edge. Exhibitors were enthusiastic about the high-quality of leads they collected and the sales inquiries generated during the show.”
Close to 60 new products were on display at the three-day event on the Congress Centre’s 80,000 square foot show floor, with features from over 200 world-class companies in metal fabrication, metal forming, welding and laser cutting equipment.
AMADA CANADA, BLM Group, Bystronic Canada, FANUC Canada, Heraeus Noblelight America, Hypertherm Inc, KUKA Robotics Canada, Lincoln Electric, Mitsubishi Laser, Sames Kremlin Inc, TRUMPF Inc, and Westway Machinery were among the top-rated exhibiting companies participating, providing hands-on displays and live product demonstrations in several dozen technology focus areas that included cutting, lasers, press brakes, robotics, and welding machines.
“Westway Machinery had a great experience at this year’s FABTECH Canada,” said Matt Walter. “After four years without a local fabricating
trade show, because of the pandemic, it was great to be back. There was a lot of excitement and interest to see what was new at our booth. Overall, we were very pleased with the amount of activity this year!” FABTECH Canada also partnered this year with the CWB Group, an industry-supported private sector organization providing welding certification, management systems registration and training services, to further provide connectivity and networking opportunities for Canada’s welding industry. The CWB Group held its CanWeld 2022 Conference in conjunction with FABTECH Canada on June 15-16, educating attendees on the latest welding technologies, and current issues affecting the welding industry.
Adding to the 50+ conference sessions and workshops was a series of insightful, educational keynote presentations and leadership discussion panels from NGen CEO Dr. Jayson Myers, CWB Association Director Max Ceron, and former NHL captain Doug Gilmour. The presentation’s topics covered a wide range including the growth of manufacturing, risks and solutions in cybersecurity, the modern landscape of hiring and skills evaluation, the positive shifts in women-to-men work ratios in the automotive industry, and the new strategies and opportunities for
Themanufacturers.returnofCanada’s
largest metal forming, fabricating, welding and finishing event is planned for June 11-13, 2024.
For further information: https://canada.fabtechexpo.com
FABTECH Canada welcomed over 5,500 attendees from more than 2,000 companies located across Canada.
environmental commitment and industrial design.
The companies participating in VETECO 2022, an event once again promoted by the Spanish Association of Light Façades and Windows (ASEFAVE in Spanish) will again display the newest ranges of windows, structural glass, light façades, roofs and skylights, glass, solar protection and control, automatic doors, home automation and machinery.
The Fair will set up VETECO GLASS, a space dedicated to the glass industry, which includes glass manufacturers and glass processing companies, which, in turn, are the suppliers of window manufacturers, façade producers, glaziers, etc. It will also host a large number of manufacturers and distributors of equipment (machinery, tools, fittings and accessories, sealants, micro-profiles, etc.).
Theevent will be held 15 to 18 November this year, under the umbrella of ePower&Building, which once again brings together the building industry. A gathering which includes, in addition to VETECO, the International Exhibition of Materials, Techniques and Building Solutions, CONSTRUTEC; the International Exhibition of Stone Architecture, ARCHISTONE; the third leading European trade fair for BIM services, networking, knowledge and solutions, BIMEXPO; the 20th International Exhibition for Solutions for the Electricity Industry and Electronics, MATELEC; MATELEC LIGHTING, and the third edition of the International Exhibition of Industry and Smart Factory Solutions, MATELEC INDUSTRY. In this way, ePower&Building is once again confirmed to be the largest commercial and business platform in southern Europe in this important economic sector. There are high expectations for this exhibition which will again focus on its important international dimension, with the implementation of an ambitious programme of guest foreign buyers, from the main markets of interest for the sector. In this way VETECO 2022 will once again be confirmed to be the most comprehensive trade show for the building industry in Spain. On this occasion, the exhibition will place special emphasis on sustainability, efficient refurbishment, energy efficiency,
VETECO SOLAR will once again be the best trade show for firms dedicated to blinds, awnings, fabrics, automatic systems, bioclimatic pergolas and structural solar control. A space especially aimed at attending to the prescription and architecture channel, construction and refurbishment companies, as well as professionals, manufacturers, workshops and awning installers in order to prepare for the next
Thecampaign.tradeexhibition
will be topped off with an interesting agenda of professional meetings, in which high level experts will tackle the most pressing issues for the sector.
Within this programme is the 14th edition of the VETECO - ASEFAVE awards, aimed at recognising the best windows, light façades, solar protection solutions and the Best End of Degree Project which includes a light façade. The awards will be handed out on the 17 November, during the celebration of 30 years of VETECO, organised by IFEMA MADRID at its showground, on the 15 - 18 November 2022, within the ePower&Building community (an umbrella which also includes the CONSTRUTEC, ARCHISTONE, BIMEXPO AND MATELEC events).
The awards aim to distinguish the windows, light façades and solar protection products which are committed to quality, design, energy efficiency, sustainability and respect for the environment.
For further information: www.ifema.es/en/veteco
IFEMA MADRID will host at its showground the 17th edition of the International Exhibition of Windows, Façades and Solar Protection - the only specialised event for this industry in Spain and with a prominent international dimension.Eos Mktg&Communication srl
www.eosmarketing.it - info@eosmarketing.it www.myipcm.com - info@ipcm.it
Redazione - Sede Legale: Via Pietro Mascagni, 8 - 20811 - Cesano Maderno (MB) - Italy Tel. +39.0362.503215 - Fax. +39.0362.1794768
EDITOR IN CHIEF / DIRETTORE RESPONSABILE
ALESSIA VENTURI venturi@ipcm.it
EDITORIAL DIRECTOR / DIRETTORE EDITORIALE FRANCESCO STUCCHI stucchi@ipcm.it
EDITORIAL OFFICE / REDAZIONE
PAOLA GIRALDO giraldo@ipcm.it
MONICA FUMAGALLI fumagalli@ipcm.it NICOLE KRAUS kraus@ipcm.it
MATTEO SOTTI sotti@ipcm.it BARBARA PENNATI pennati@ipcm.it
ILARIA PAOLOMELO paolomelo@ipcm.it GABRIELE LAZZARI redazione@ipcm.it
EDITORIAL OFFICE AND GRAPHICS
ELISABETTA VENTURI grafico@ipcm.it
MEDIA SALES
FRANCESCO STUCCHI stucchi@ipcm.it
BARBARA PENNATI pennati@ipcm.it NICOLE KRAUS kraus@ipcm.it SVEN KRAUS sven.kraus@ipcm.it CLAUS GÖRLICH goerlich@ipcm.it
Prof. Massimiliano Bestetti: Department of Chemistry, Material and Chemical Engineering, Politecnico of Milan –Section of Applied Chemistry and Physics
Dr. Franco Busato: European environmental legislation and new technologies
Prof. Paolo Gronchi: Department of Chemistry, Material and Chemical Engineering, Politecnico of Milan –Chemical Engineering Section
Kevin Biller: The Powder Coating Research Group
Prof. Stefano Rossi: Material Engineering and Industrial Technologies, University of Trento - Product Design
Dr. Fulvio Zocco: Environment and quality
ELISABETTA VENTURI grafico@ipcm.it
This magazine is wrapped with a biodegradable and compostable film. Questa rivista è confezionata con un film biodegradabile e compostabile.
SUBSCRIPTION SERVICE - SERVIZIO ABBONAMENTI: Sale only on subscription - Vendita solo su abbonamento E.mail info@ipcm.it Subscription Rates 2023 - Tariffe Abbonamento 2023:
Annual subscription print + digital:
EMEA 100,00 € (postage included)
Rest of world 300,00 € (fast airmail shipping included)
Abbonamento annuale cartaceo + digitale: EMEA 100,00 € (spese postali incluse)
Resto del mondo 300,00 € (spedizione via aerea inclusa)
Single copy: 15,00 € EMEA (postage included) - Rest of world (postage excluded)
Back issues: 30,00 € EMEA (postage included) - Rest of world (postage excluded)
Fascicolo singolo: 15,00 € EMEA (spese postali incluse) - resto del mondo (spese postali escluse)
Arretrati: 30,00 € EMEA (spese postali incluse) - resto del mondo (spese postali escluse)
Subscriptions can be made by bank transfer to the following account: Eos Mktg&Communication Srl IBAN IT97F0844033270000000084801 - SWIFT CODE CRCBIT22 or via payment online at: www.myipcm.com
Gli abbonamenti possono essere sottoscritti versando il relativo importo a mezzo b/b IBAN IT97F0844033270000000084801 intestato a eos Mktg&Communication Srl oppure con carta di credito direttamente dal sito www.myipcm.com L’Iva sugli abbonamenti, nonchè sulla vendita di singole copie è assolta ai sensi dell’art.74 comma 1 lett. C DPR 633/72, DM 29/12/1989.
Registrazione al Tribunale di Monza N° 1970 del 10 Dicembre 2009Eos Mktg&Communication srl è iscritta nel Registro degli Operatori di Comunicazione con il numero 19244
POSTE ITALIANE S.P.A. – SPEDIZIONE IN ABBONAMENTO POSTALE –D.L. 353/2003 (CONV. IN L. 27/02/2004 N.46) ART. 1, COMMA 1 LOM/MI/4351
PRINT/ STAMPA ROTOLITO SPA info@rotolito.com
It is forbidden to reproduce articles and illustrations of “ipcm®” without authorization and without mentioning the source. The ideas expressed by the authors do not commit nor magazine nor eos Mktg&Communication S.r.l and responsibility for what is published is the authors themselves.
È vietata la riproduzione di articoli e illustrazioni di “ipcm®” senza autorizzazione e senza citarne la fonte. Le idee espresse dagli autori non impegnano nè la rivista nè eos Mktg&Communication S.r.l e la responsabilità di quanto viene pubblicato rimane degli autori stessi.
I n a n e v e r c h a n g i n g w o r l d , S a l c h i r e m a i n s a t y o u r s i d e t o h e l p y o u b e c o m e a r e a l m a r k e t d i f f e r e n t i a t o r . w w w . s a l c h i m e t a l c o a t . c o m