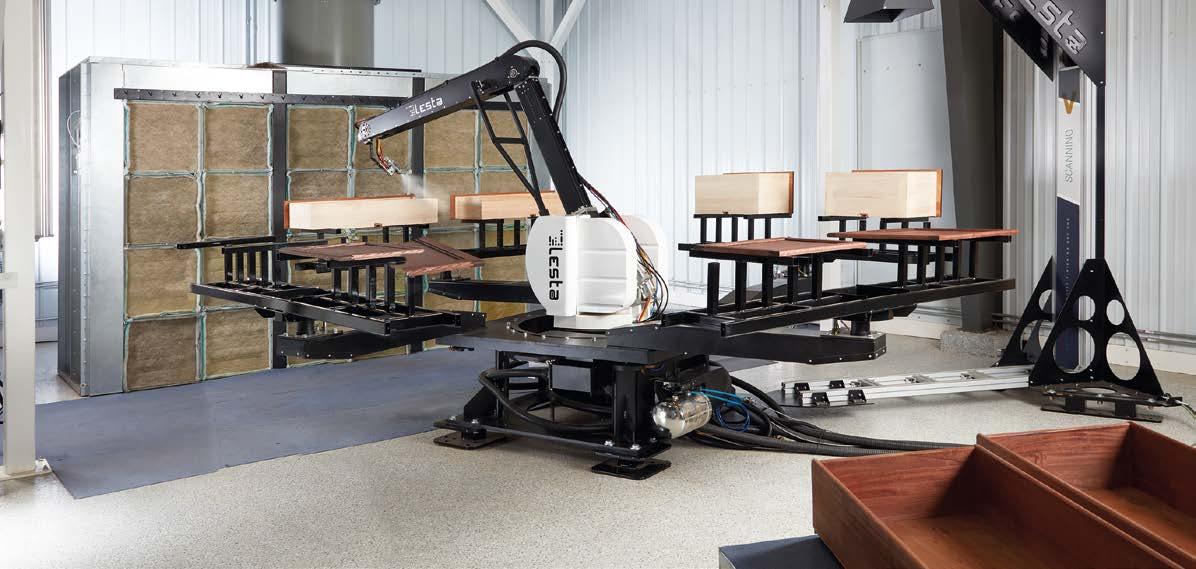
15 minute read
BRAND NEW
© Lesta
LestaUSA Announced New Distribution Partnerships
LestaUSA, the North American integrator, manufacturer and technical support for mechanical and software of Lesta robots for industrial painting applications, has announced that it has reached a new distribution partnership. The company will collaborate with Sames Kremlin and Wagner/C.A. Technologies to deliver automated finishing solutions to wood industry manufacturers. “We’ve really come a long way since we debuted to the wood industry at the AWFS Fair in 2021. Today, we’re working in partnership with the best in the industry to leverage our technologies that will continue to push the boundaries of what’s possible in finishing,” has stated Derek DeGeest, the president of LestaUSA. “The success we’ve had has resulted in an opportunity to go deeper with our Equipment Partners. For the first time ever, our partners are bringing our automation solutions into their product lines. This allows us to collaborate on bringing our technologies together to offer an even more robust system along with service to our mutual customers.” “We are excited to bring more automation solutions to the Wood Industry in addition to flat lines. We can now look to combine the two proven technologies. This automation push in wood is essential to growth in today’s market and economy,” has commented Kevin Higgins, the vice-president of Sales/Distribution at Sames Kremlin. “We have equipment in their test lab and they have their robots in ours. Manufacturers can bring this automated solution into their operation knowing that it works and will be supported by Wagner, our distributors, and LestaUSA. That’s the peace of mind Wagner customers come to expect from us,” has added JR Rogers, Wagner Engineered Systems National Sales Manager.
Users were able to experience the automated finishing solutions of LestaUSA during the International Woodworking Fair (IWF) – that took place from 23rd to 26th August 2022 in Atlanta (U.S.A.) – at the booths of Sames Kremlin and Wagner/C.A. Technologies.
For further information: www.lestausa.com
MKS Instruments Announced the Closing of Atotech Acquisition
MKS Instruments, Inc. has announced that it has completed the previously announced acquisition of Atotech Limited for approximately $4.4 billion in cash and MKS common stock. “The acquisition of Atotech positions MKS to accelerate roadmaps for future generations of advanced electronics devices. By combining leading capabilities in lasers, optics, motion and now process chemistry, MKS is set to be a leader in the next frontier for miniaturization and complexity: optimizing the InterconnectSM, a significant enabling point of next-generation advanced electronics. Atotech’s leadership in functional and decorative surface finishing will also extend MKS’ product offering for industrial applications and grow our market reach. I could not be more excited to welcome the Atotech team to the MKS family,” has declared John Lee, the President and CEO of MKS. The combination of MKS and Atotech creates a company with pro forma revenue of $4.5 billion for the twelve months ended June 30, 2022. As a result of higher interest rates on debt financing compared to the time the transaction was originally announced in July 2021, as well as the impact of the current macroeconomic and inflationary environment on the business of the company, MKS currently anticipates the acquisition will be accretive to Non-GAAP diluted net earnings per share for the full fiscal year 2024.
For further information: www.mks.com and www.atotech.com
WASTE WATER TREATMENT PLANTS
FOR METAL FINISHING LINES
Our potential customers
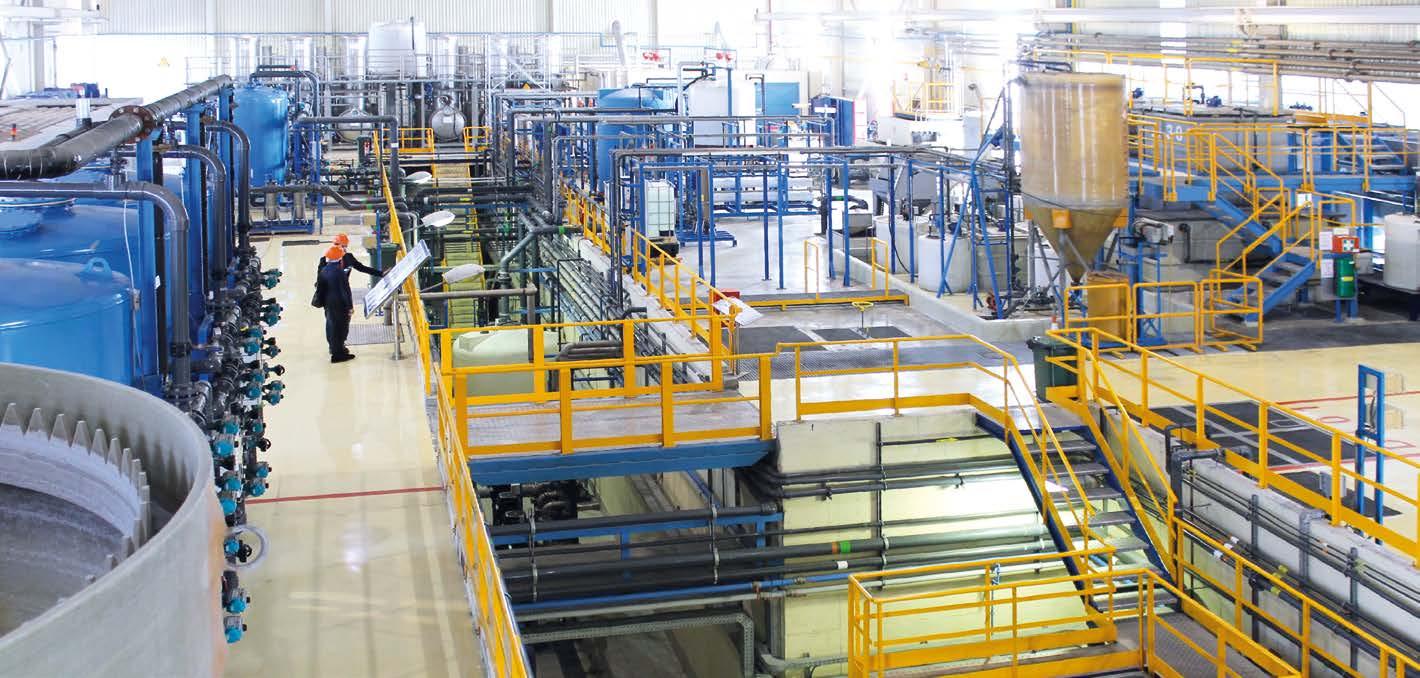

© AdobeStock
Edited by BYK-Chemie GmbH
Wesel, Germany
More Sustainable Additives for a Better Future
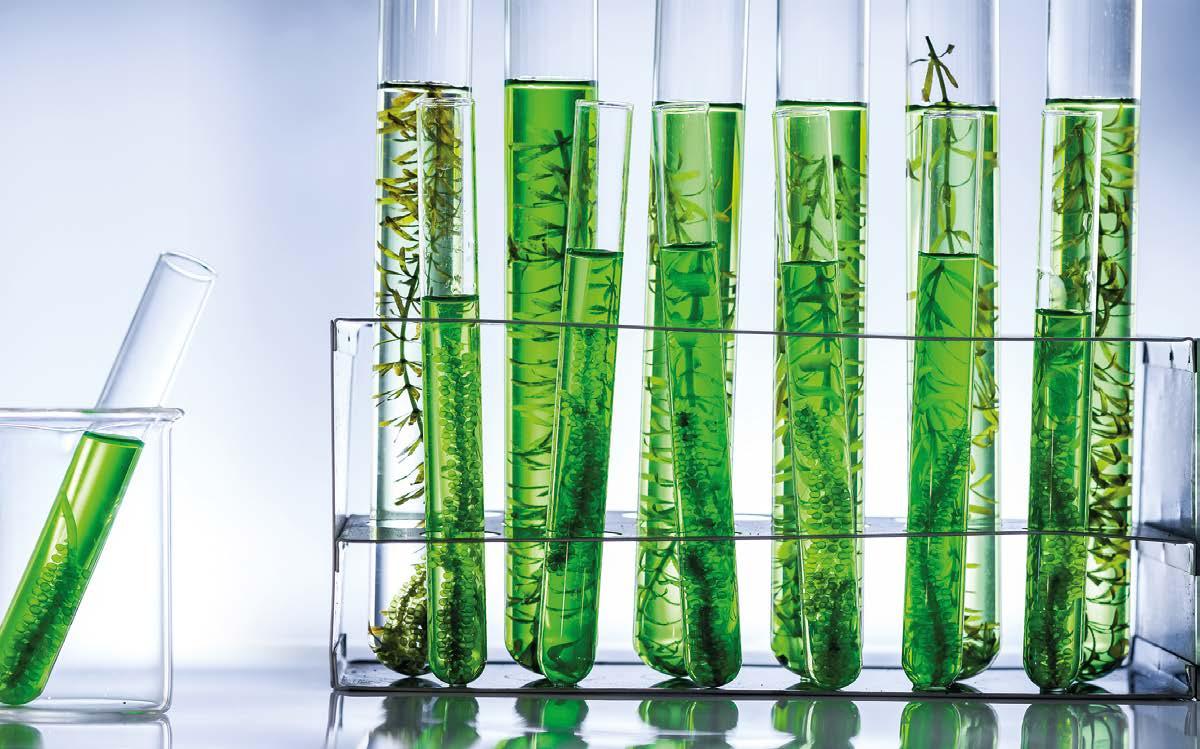
Sustainability is an important aspect in the development of new products. In addition to the product’s direct properties and effects, questions regarding environmental impact, chemical basis, and energy consumption often play a significant role too.
Many wax-based additives on the market comprise raw materials won from crude oil or gas, ranging from traditional (high-density) polyethylene waxes for increasing matting properties or improving scratch resistance to polypropylene waxes or PTFE for surface slip adjustment in coatings. They exhibit a fairly good performance and have a beneficial factor, which is why they are designated in their applications. Nevertheless, considering aspects of sustainability, e.g., the use of bio-based raw materials, all these waxes must be reviewed critically. Why there is a need for change
One obvious and major factor is: crude oil is a finite raw material. This means its availability over the next centuries is decreasing and there is a great need to discover, test and finally use new alternative raw materials. Another major factor is climate change. Climate change is still ongoing, and it is significantly influenced by our actions. Saving every ton of CO2 possible will help to comply with the Paris Agreement of 2015 to keep global warming below 1.5 °C. Governments are aware of the topic and are undertaking measures to
combat climate change, which in turn impact on the use of fossil raw materials. Exemplary measures are the levying of taxes on carbon dioxide (CO2) emissions or the purchase of certificates that allow the buyer to emit a certain amount of CO2. But the economic effect is just one side of the story. The ecological effect is much more important for a reduction in the use of crude-oil-based products. Other aspects of sustainability deal with the endof-life options of products. In our daily life, we are surrounded by plastic and cause a lot of plastic waste. This plastic waste needs a lot of time to be degraded in the environment: in the case of PE plastic bags, it is around 500 years. Thus end-of-life options like biodegradability, where the plastic is degraded by microorganisms such as bacteria and fungi in shorter time frames, are becoming more and more important. But plastic is not always so obvious in our lives as in the case of plastic bags. Many wax additives are based on synthetic raw materials, so these are, like plastics, affected by the issue of biodegradability. Therefore, an increasing amount of biodegradable material can help to pave the way to a more sustainable future.
BYK’s approach for a more sustainable future
CERAFLOUR 1000 is one excellent example of an additive with improved sustainability, launched in 2011. It has specific properties of traditional additives manufactured using either natural or synthetic waxes, but is based on a bio-based polymer and is also fully biodegradable. In 2021, BYK expanded its portfolio by two new additives based on the same raw material, but with different particle size distributions: CERAFLOUR 1001 and CERAFLOUR 1002. All three additives have a bio-based content of > 97% and are fully biodegradable. Moreover, bio-based polymers make a positive contribution to the ongoing microplastic discussion and conserve aquatic life (Fig. 1). The polymers of the CERAFLOUR 1000 series are produced with the help of microorganisms. These organisms are fed with carbohydrates and produce the bio-based polymer in a fermentation process. In additional steps, the polymer is separated from the microorganism and purified. The last step of micronization leads to polymers which can be used for different coatings applications. With CERAFLOUR 1001, BYK offers an additive with even finer particle size distribution than CERAFLOUR 1000 to achieve the utmost in transparency while simultaneously intensely reducing gloss. On the other hand, with CERAFLOUR 1002, BYK has introduced an additive with a larger particle size to create a surface texture with high transparency that, at the same time, produces the best matting performance. The spherical structure of the polymers, which form agglomerates, can be seen on the SEM (scanning electron microscope) images. The particle size of CERAFLOUR 1000 lies between that of the other two products (Fig. 2).
Broad field of application
The additives were very intensively tested in different kinds of applications. Starting with water-based systems, in 100% UV coatings, but also in traditional
© BYK
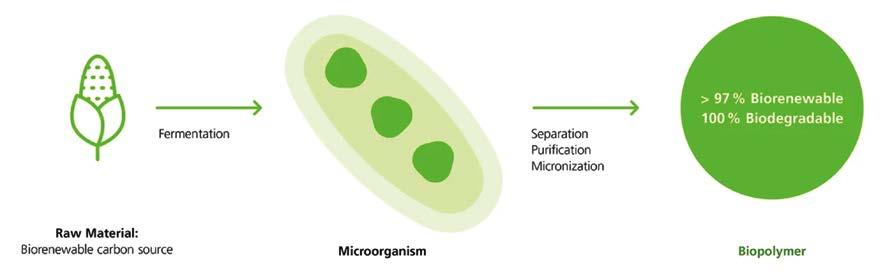
Figure 1: Overview of the extraction of the raw material for polymers in the CERAFLOUR 1000 series.
Figure 2: SEM images of CERAFLOUR 1001 and CERAFLOUR 1002 in comparison.

© BYK
© BYK
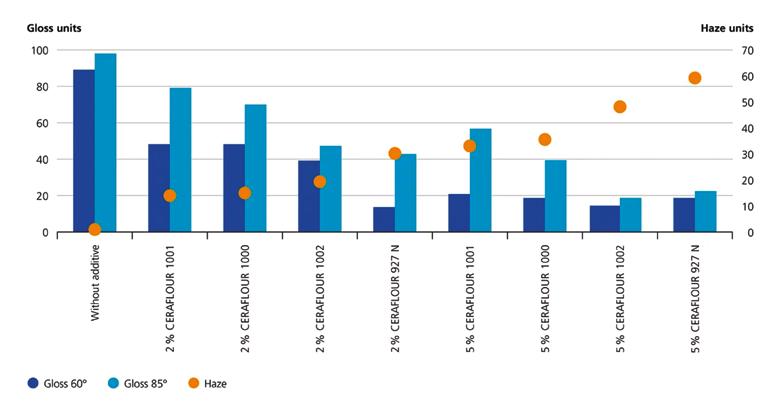
Figure 3: Gloss and haze values of polymers in the CERAFLOUR 1000 series in comparison to an HD PE wax additive in a water-based pure acrylic wood coating system.
Figure 4: Improvement of anti-burnishing in comparison to an HD PE wax additive (CERAFLOUR 927 N).
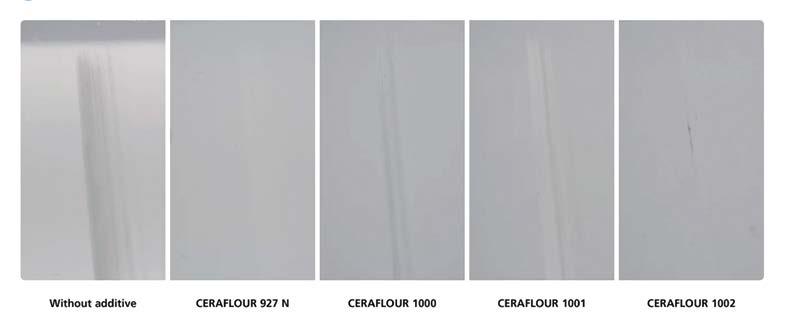
© BYK solvent-borne coating systems, the additives show excellent compatibility and performance. Their usage in wood and furniture coatings, printing inks, and general industrial coatings is highly recommended. CERAFLOUR 1001 shows the lowest haze with good matting properties at the same time. Especially at higher dosages, CERAFLOUR 1001 shows low haze values compared to other PE waxes (Fig. 3). In laboratory tests, the polymers show synergistic effects with common PE waxes to improve the scratch resistance and abrasion resistance of a coating’s formulation. Only a small addition (0.5% on total formulation) of these is sufficient to create good scratch resistance of the coating’s surface. Furthermore, all three products show synergistic effects with silica-based matting agents (Fig. 4). On top, all three products provide excellent haptic properties and provide a “soft feel” effect of the surface. This is particularly true for the smaller particle sizes. What is more, adding polymers of the CERAFLOUR 1000 series help to increase the amount of renewable carbon of a formulation to fulfil the requirements of the market for finding more sustainable solutions.
Looking to the future – there is a need for change
Sustainability is a complex topic and there are many aspects to consider. It is not only the raw material source which can be exchanged for an environmentally friendly solution. Lower film formation temperatures, a smaller number of solvents or coalescents, faster curing speed, or better degradability – there are many opportunities to reduce CO2. The CERAFLOUR 1000 series is yet another excellent step towards BYK’s goal of becoming more sustainable across the complete supply chain and providing sustainable solutions to customers.
SATA Presented the Special Edition SATAjet X 5500 FUTURE Spray Guns
The gravity flow cup guns will reflect SATA’s efforts towards a more sustainable and connected future.
© SATA
© SATA
SATA GmbH & Co. KG, a German manufacturer of coatings technologies and equipment, has recently presented SATAjet X 5500 FUTURE, a limited edition version of its gravity flow cup spray guns. The special edition was exclusively available from SATA dealers starting from 13th September 2022 until sold out. Resembling the company motto “Green is more than just a colour to us”, the new green spray guns are then not only a reference to nature, but also a symbol for harmony, hope and a more sustainable and connected future. The globe-shaped circuits on the spray gun represent the technology which is connecting people and thus enables the globalised world of the future. The radiant green colour with the black components not only looks harmonious, it stands for aligning the actions of the company with sustainability and the preservation of nature. The special edition SATAjet X 5500 FUTURE is available in the following nozzle sizes, as HVLP and RP and in standard or digital versions: • SATAjet X 5500 HVLP 1,3 I • SATAjet X 5500 HVLP 1,3 O • SATAjet X 5500 HVLP 1,4 I • SATAjet X 5500 HVLP 1,4 O • SATAjet X 5500 RP 1,3 I • SATAjet X 5500 RP 1,3 O • SATAjet X 5500 RP 1,1 I • SATAjet X 5500 RP 1,1 O • SATAjet X 5500 RP 1,2 I • SATAjet X 5500 RP 1,2 O.
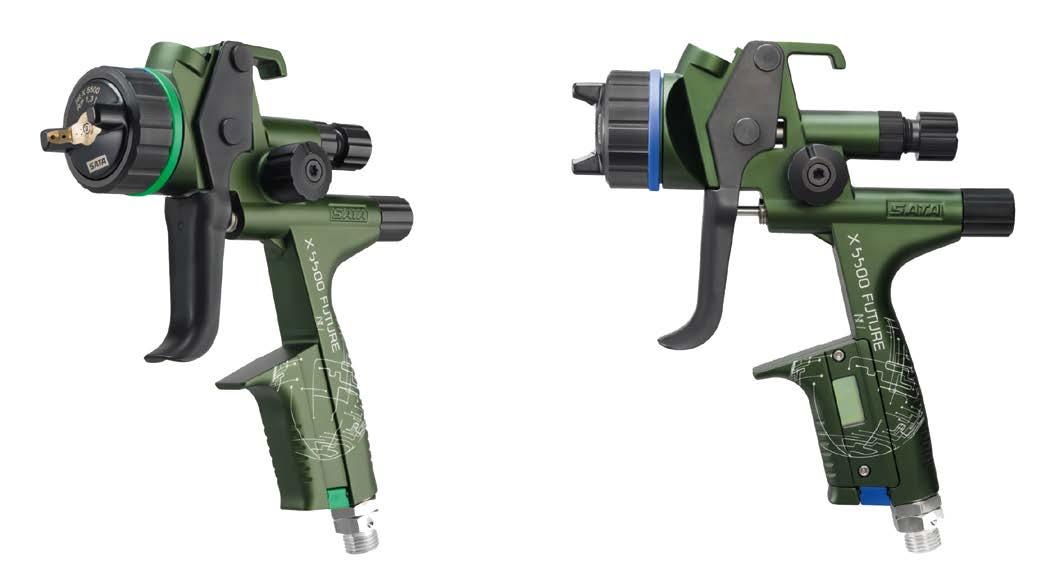
Visitors of the Automechanika trade fair, that took place from 13th to 17th September 2022 in Frankfurt (Germany), were able to test the SATAjet X 5500 FUTURE spray guns at the booth of the company.
For further information: www.sata.com
KANSAI HELIOS Completed the Acquisition of wefa
The acquisition will strengthen KANSAI HELIOS’ position in the railway and ace coatings sectors.

The KANSAI HELIOS Group has recently announced that it has completed the acquisition of Westdeutsche Farben GmbH (“wefa”), a German coatings manufacturer. The acquisition realised by their newly set-up group company, KANSAI HELIOS Wefa, based in Essen, includes all assets, business activities, brands and employees. “This acquisition is an important step in the growth strategy of the KANSAI HELIOS Group, which will strengthen its presence in Germany. The group will serve the market as a system supplier with the combined strength of two production units, each specialized in their respective areas: KANSAI HELIOS Germany GmbH in Buchholz-Mendt and the new company in Essen,” has declared Dietmar Jost, the executive director of the KANSAI HELIOS Group. The acquisition will allow the company to strengthen its position within the European railway and ACE industry and other industrial coatings segments as well, thanks to wefa’s decades of experience with water-based coatings. Robert Scramm, the owner of wefa, will also be one of the managing directors of KANSAI HELIOS Wefa: “This step is a milestone in wefa´s almost 100-year history. Founded as a family company, the brand has now made it into the ranks of the top European coating brands. As a new member of KANSAI HELIOS, we will benefit from additional experience and know-how within the group. This is a win for wefa and vice versa as our specialized coating formulations complete the new owner’s product range and ensure the highest product quality for a wide range of applications, especially for the railway industry.”
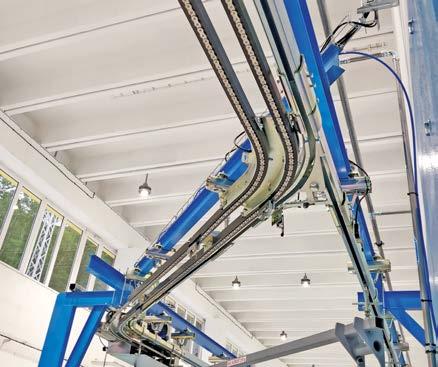
For further information: www.kansaihelios-wefa.de
© KANSAI HELIOS Wefa
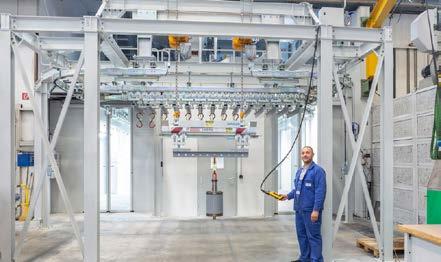
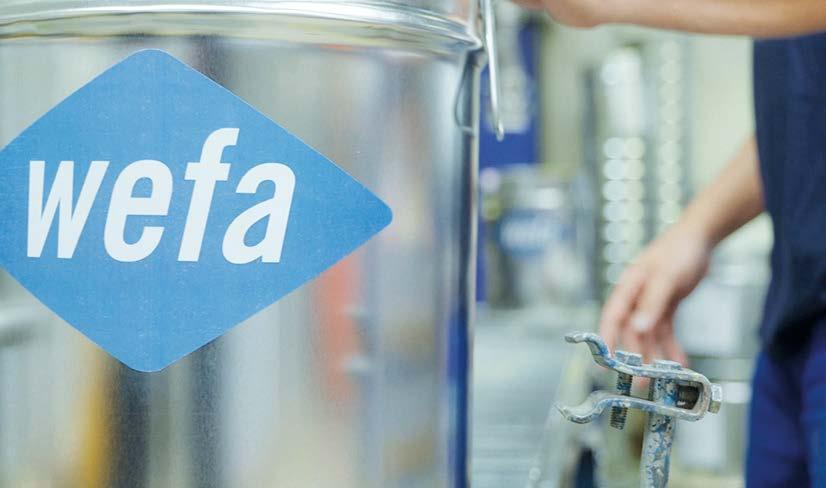
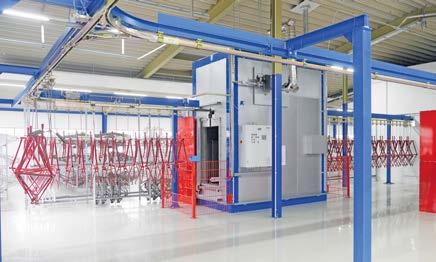
The “Ask an Expert” Column
Kevin Biller
kbiller@chemquest.com
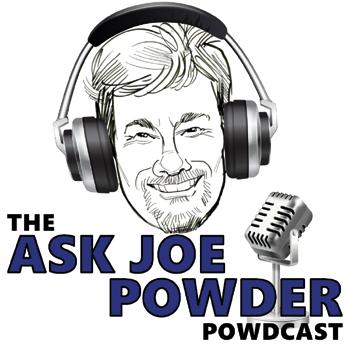
Joe Powder comes back again on this issue to answer questions about the everyday challenges of coaters around the world.
Dear Sir, Can you tell me please in corona charging gun how powder will charge? Is it charged with electrode? I mean flat jet nozzle or round jet nozzle? Thx, Shahroz Khan Pakistan
Greetings Shahroz, How are things in Pakistan? Your question is a good one. Basically, the electrostatic charge in a corona type powder spray gun is created by ionizing air. The high voltage at the gun tip electrode pulls electrons off air molecules (N2, O2, etc.) which results in a field of negative charge. This electric field converges on the earthed target. The deposition of powder is accomplished by passing a cloud of particles through the electric field. The particles pick up electrons as they traverse through the field.
© Kevin Biller
Interior corners of box shaped parts can be a challenge to penetrate with charged powder. A good earth is important for best transfer efficiency.
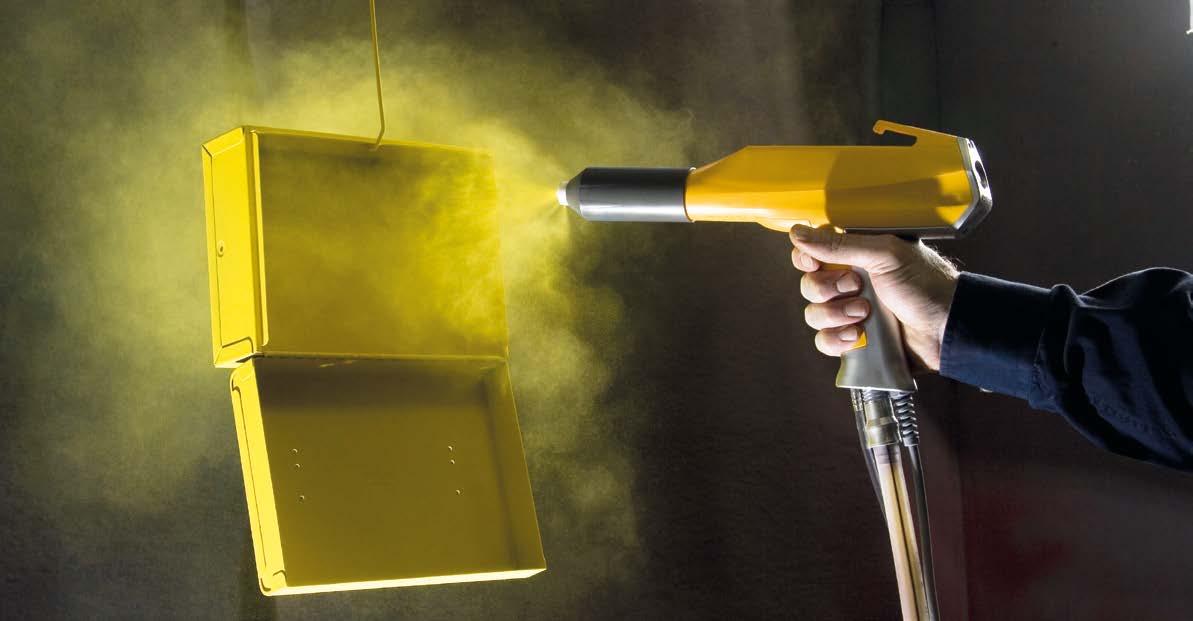
These negatively charged particles are attracted to the conductive surface if it is adequately connected to earth. As the negatively charged particles accumulate on the surface of the substrate negative charge leaves the substrate to earth. The loss of negative charge at the surface creates a net positive charge at the interface. This positive face charge secures the negatively charged powder to the surface. The nozzle type affects the manner in which the powder cloud exits the spray gun. It has only minimal effect, if any, on the charging characteristics of the powder. I hope this helps answer your question. Best regards, Joe
Dear Joe, Hope you are fine. What is your recommendation to guarantee an adhesion of powder paint for surface “hotdip zinc coating’’? Best regards Ozlem Ekinci BPC, Turkey
Dear Ozlem, Life is good for me lately. We are enjoying the fall with many celebrations with family and friends. Lots of wonderful cooking and some pleasant drinks as well. I hope life is good for you also. As for your question - this is a difficult one. One of the biggest issues is the variability in the quality of the hot dipped galvanized (HDG). It can be very inconsistent not only from batch to batch of HDG but also on different sections of the same part coated with HDG. What I recommend is first careful cleaning of the surface. This can be an alkaline cleaner followed by a good quality rinse. You may also want to consider media blasting as well, however this adds cost to the process. As for adhesion - some powder coatings work better than others. A good quality epoxy will adhere better to HDG than a polyester powder. Hybrids (epoxypolyester) fall somewhere in between. If this is for an outdoor durable application you need to either use a zinc phosphate pre-treatment with the polyester or the combination of an epoxy primer followed by the polyester topcoat. Also it is important to de-gas the HDG prior to applying the powder coating. Otherwise, you may observe pinholes in the coating. De-gassing involves preheating the HDG and applying the powder to the warm substrate. Preheating to 150 to 175°C usually suffices. I hope that this helps answer your question. Kind regards, Joe
Hi Joe, I am James the Quality Technician from a finishing house in Northern Ireland. I am currently in the process of doing some R and D with powder coating on top of chilled iron grit blasted material and we are currently experiencing problems. I thought you might have a good knowledge of the subject after reading your Q&A’s with other powder coaters. The system we have in place is the SA 2.5 grit blasting then coated with APP120 (a zinc-rich primer) and cured at 180° C for 30 minutes. However, after this stage the top coat refuses to adhere to the primed substrate and when it does it generally “stars up” during spraying. I have tried spraying it hot (metal temp greater than 150°C), changing cure times for the primer (shorter bakes at higher temps), lowering gun kV’s and changing the base primer but none of it gets satisfactory results.
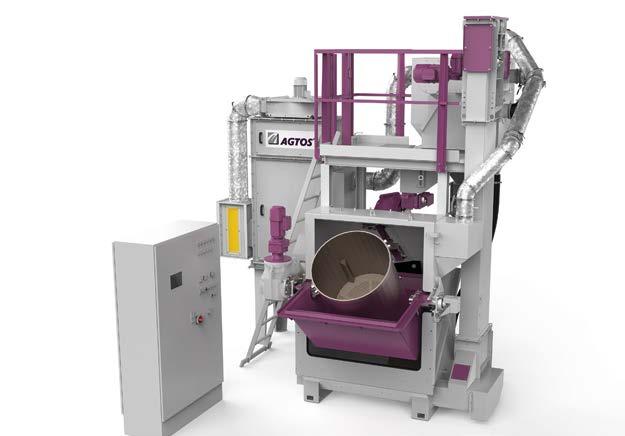
20 years
Competence in Shot Blast Technology
As a full-range supplier, we design and manufacture shot blasting machines including filter and transport technology. ➜ New shot blast machines ➜ Second hand machines ➜ Service and spare parts ➜ Reparation & maintenance ➜ Inspection & consulting ➜ Performance improvement AGTOS | GmbH | D-48282 Emsdetten info@agtos.de | www.agtos.com
352-10/21-4c-GB