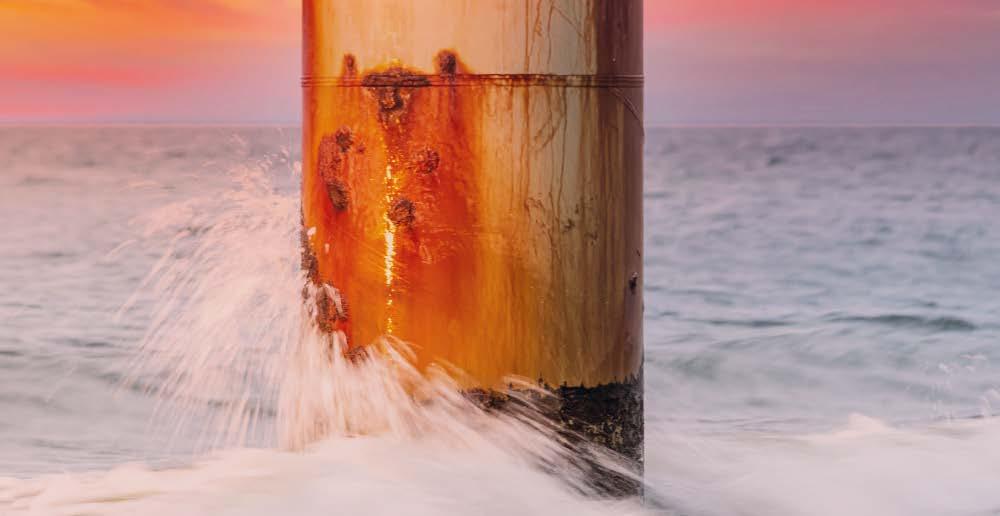
16 minute read
BRAND NEW
© AGM
AGM has launched its own range of graphene-enhanced anti-corrosion paints alongside another high-performance non-metal additive.
Applied Graphene Materials (AGM) has introduced two new product developments in quick succession, continuing to demonstrate its commitment to innovation. Following exceptional results achieved through extensive internal research and testing, AGM has launched a range of industrial anticorrosion paints incorporating its own Genable graphene additives. The two epoxy-based prototype primer systems represent an easy way for those considering the adoption of graphene to quickly test and evaluate its potential benefits. The Genable Epoxy primer is a C3-classified hybrid product that contains graphene and a zinc phosphate additive to allow the end user to benefit from the synergies offered by both systems in standard applications, such as urban and industrial environments. The Genable CX primer is a high-performance hybrid system based on graphene and aluminium chemistries which allows to protect surfaces against corrosion even in harsh environments, such as offshore and marine applications. Additionally, AGM has also introduced a range of non-metal, active anticorrosion graphene to extend its Genable 3000 dispersion series. Using a combination of graphene with traditional sacrificial additives, the new hybrid range, which is free of metals and VOC, maximizes synergies between complementary systems to offer the paint and coatings industry excellent corrosion protection. The new graphene additives are based on the company’s established Genable technology, which improves performance such as chemical resistance, barrier properties and anticorrosion properties. Genable 3100 and Genable 3105 are optimized formulation-ready dispersions that are easy to formulate, safe to incorporate and stabilized in a standard epoxy resin; Genable 3120 offers a more sustainable option in an environmentally friendly bio-based epoxy resin to increase anticorrosion performance while contributing to environmental goals. Adrian Potts, Chief Executive Officer for AGM, said: “We are pleased to be able to launch these new Genable products, which we anticipate will help further accelerate the adoption of graphene nanoplatelet technology in the industry. Our technology development programmes have focused on extensive testing and evaluation for a range of applications, and this experience is valuable to guide customers in the use of our products.”
The second cooperation event with practical presentations on corrosion protection with zinc flake systems will take place on May 17-18 in Markdorf (Germany).
On May 17th and 18th, 2022, the cooperation event “Corrosion protection with zinc flake systems in the spraying process” will take place in the Wagner’s headquarters in Markdorf on Lake Constance (Germany). After a successful first cooperation event in 2021, the companies coatmaster, Dörken, Fanuc, Sidasa, Vulkan Inox and Wagner have joined forces again and organized a joint event. As in the previous year, the latest developments as well as current knowledge and trends in the field of spray application will be presented and discussed during this meeting. What is special about this is that thanks to the cooperation between the companies, participants will gain insights into different points in the process and value chain - practically and individually. Here they can benefit from the combined know-how of the experts. The topics of the practical presentations are: • Corrosion protection with in-process coating thickness measurement - Andor Bariska (coatmaster) • Manual coating: the easiest way of application - Stefan Baum (Wagner) Full and partial automation of coating systems – Lars Hayen (Sidasa) • Surface preparation by shot blasting - Christian Hoffmann (Vulkan Inox) • Edge sharp application of rotationally symmetrical parts - Alexander Vonbach, Michael Hense, Matthias Mandal (Wagner) • Zinc flake systems as solution for various applications - Markus Nowak (Dörken Coatings) • Efficient rack coating with robots - Christian Eising (Wagner) • Industrial robots of today: intuitive and easy to program - Marc Wischnewski (Fanuc). Another highlight is the joint evening event on the first day, which will offer plenty of opportunities to network and exchange ideas. The event is limited to 32 participants and the registration is available until May 2nd .
For further information: https://bit.ly/3Jp9izb
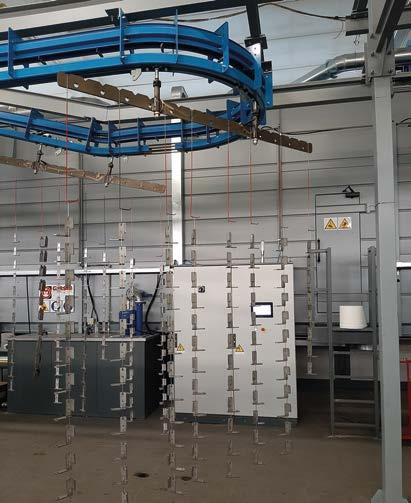
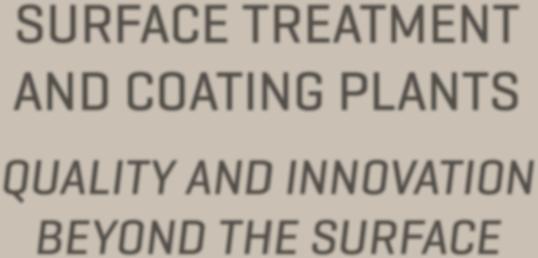
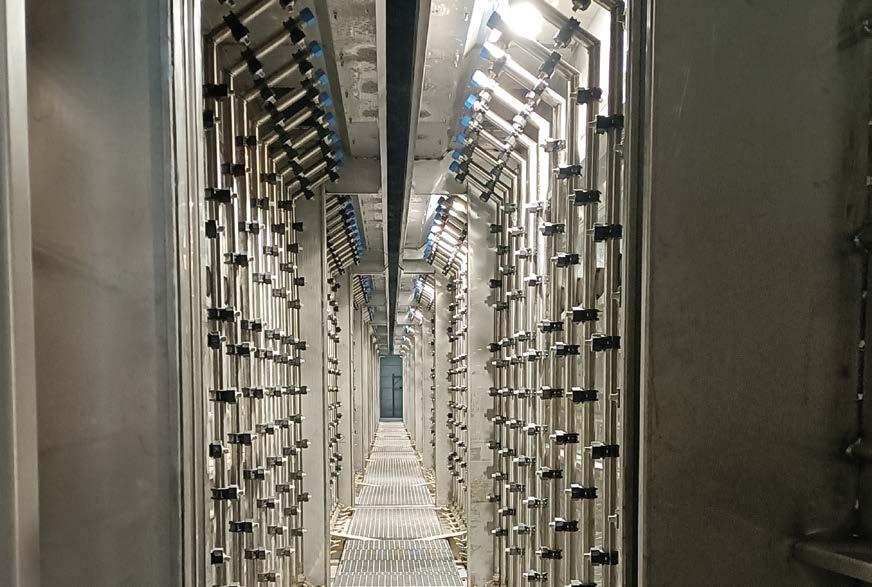

© AGTOS
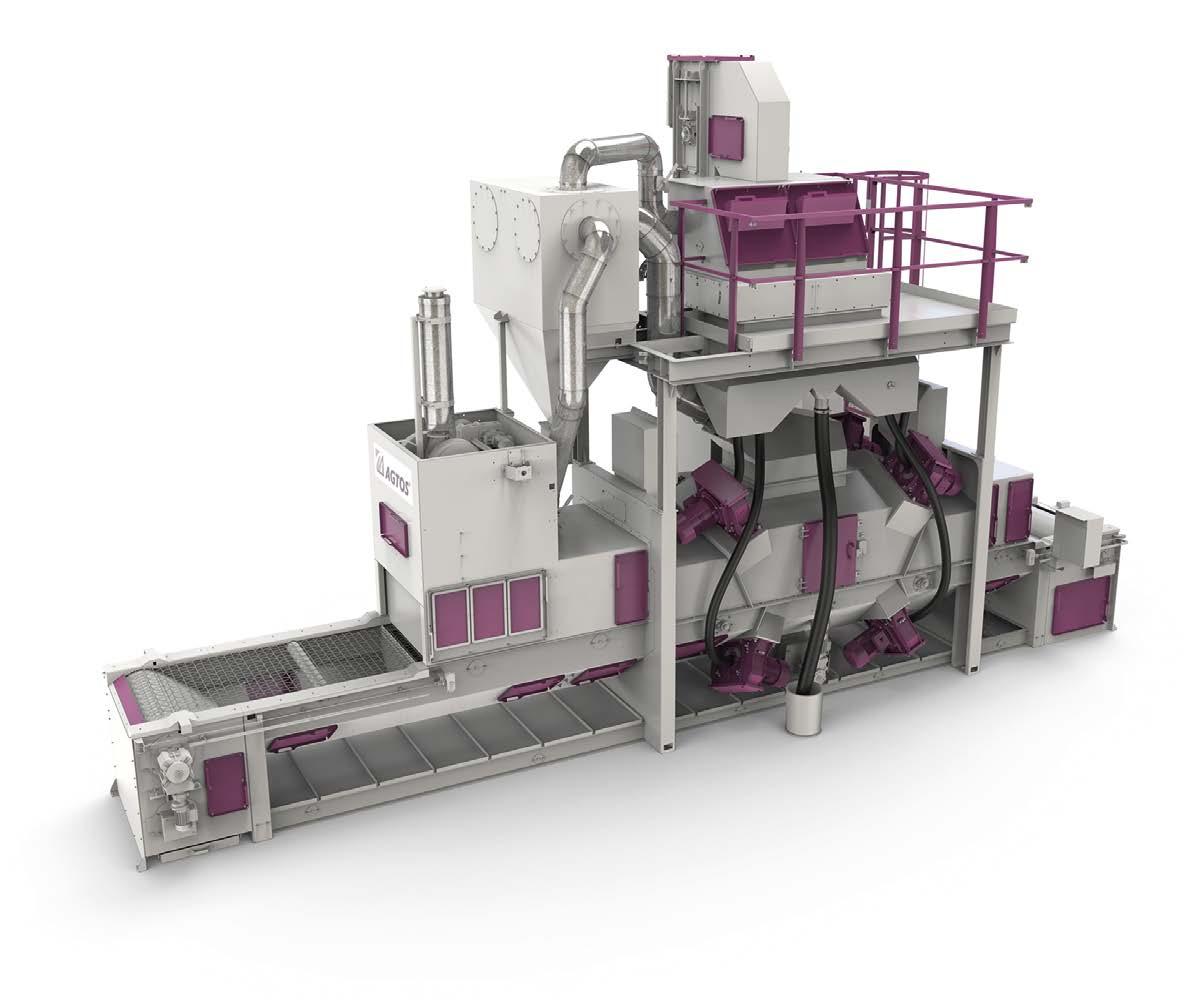
AGTOS Has Confirmed Its Participation at EUROGUSS
At the trade fair EUROGUSS, AGTOS will present the latest developments in shot blasting technology.
AGTOS has recently announced that it will take part in the next edition of EUROGUSS, the trade fair dedicated to die casting that will take place from 08th to 10th June 2022 in Nuremberg (Germany), to present its latest innovations in the shot blasting technology field. The requests for the surface treatment of complex cast workpieces made from aluminium or magnesium are becoming more and more sophisticated, so the reproducibility of the shot blasting process for mass-produced parts is extremely important. AGTOS has then designed and developed special shot blasting systems for coherently treating lightweight parts and aluminium and magnesium castings. The company will present its latest innovations and provide visitors with useful insights on how to increase the power of existing shot blasting machines, so that turbines specially designed for this purpose work more gently and the abrasive consumption is reduced. In addition, it will also showcase the new AGTOS Service APP, via which service technicians can provide instruction in the case of maintenance and repair work and share supplementary documents such as drawings, illustrations and photos. AGTOS will exhibit in hall 9, stand 9-300.
For further information: www.agtos.de
Cortec has launched EcoClean Scale and Rust Remover HP with the aim of achieving fast-acting scale removal on a safer level.
Cortec has introduced EcoClean® Scale and Rust Remover HP, which can clear away scale buildup on all water-contacting equipment surfaces in a variety of industrial systems, such as, heat exchangers, chillers, condensers, cooling towers and pipes. Scale removal is an important maintenance activity, as over time, calcium carbonate from hard water builds up on the surfaces of pipes and heat exchangers, reducing water flow and heat-transfer efficiency. EcoClean Scale and Rust Remover HP also removes corrosion on multiple metal types and contains powerful corrosion inhibitors to counteract the aggressiveness of acids on metals.
A safer and more sustainable alternative
EcoClean Scale and Rust Remover HP is a safer alternative to harsh minerals and organic acids like muriatic acid. Classified as only a mild skin irritant according to the OECD Principles of GLP (Good Laboratory Practice), EcoClean Scale and Rust Remover HP is drastically safer than muriatic acid, even if it is still considerably fast-acting and effective. While proper precautions should be taken, including the use of PPE, EcoClean Scale and Rust Remover HP is a much better route to scale removal in terms of worker safety. Since EcoClean Scale Remover HP is classified as non-corrosive to mildsteel, it is non-regulated for ground shipments per US DOT, a great advantage for those distributing the product. EcoClean Scale and Rust Remover HP is phosphate free and also considered a biodegradable industrial descaler according to product components and is a low contributor to BOD/COD in effluents.
How to use EcoClean Scale and Rust Remover HP
Immersion in the product produces the best results for most substrates and often works within five minutes to an hour, depending on the amount of scale and corrosion. Light abrasion helps speed up penetration and removal of corrosion products. Application should be followed with a neutralizing cleaner for further protection. EcoClean Scale and Rust Remover HP can be used multiple times if filtered and monitored for pH after use.
For further information: www.cortecvci.com
© Cortec
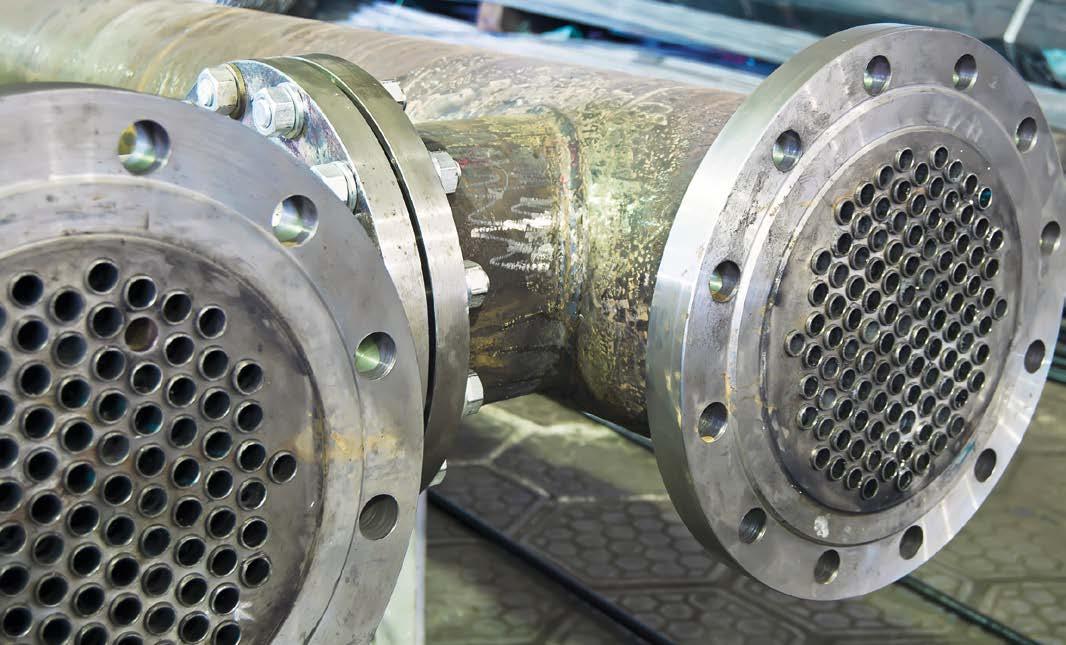
Belzona Launched the Solvent-Free Containment Grade Coating Belzona 5815
The new coating with enhanced flexibility developed by Belzona allows to protect secondary containment areas.
© Belzona
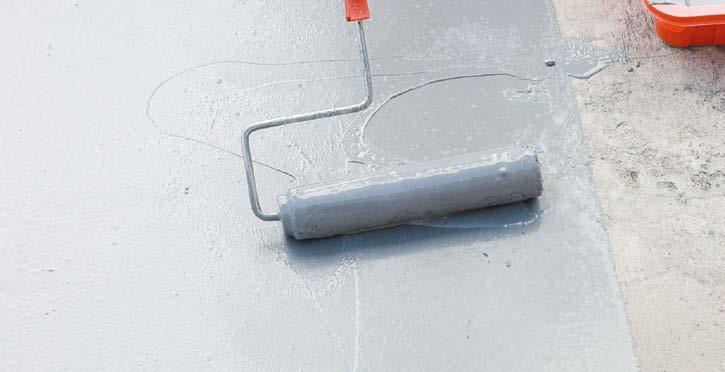
© Belzona The manufacturer of polymer repair composites and industrial protective coatings Belzona has recently launched Belzona 5815, a new solvent-free containment grade coating with enhanced flexibility specifically developed for the protection of secondary containment areas. Concrete is commonly used to build secondary chemical containment areas and bunds that need to retain spilled chemicals and facilitate product recovery. However, it is susceptible to physical and chemical damage due to its porosity and other damages caused by cracking and reinforcing bar corrosion. Belzona 5815 allows to solve these issues, as it has high tensile and flexural strength and can resist pressure up to 2,430 psi, allowing to bridge cracks. In addition to this, the newly developed coating is able to endure temperatures ranging from -40 °C up to 160 °C and it is particularly easy to mix and apply by brush, roller, squeegee or airless spray system, since it does not require surface conditioner. “Belzona 5815 is an economical solution to secondary containment areas holding non-aggressive chemicals. It has undergone testing to prove that the product can resist a range of dilute acids, alkalis, fuels, and oils. Moreover, it can bridge cracks in concrete up to an extent and has great adhesion to non-metallic and metallic substrates”, stated Osmay Oharriz, the Technical Manager of Belzona.
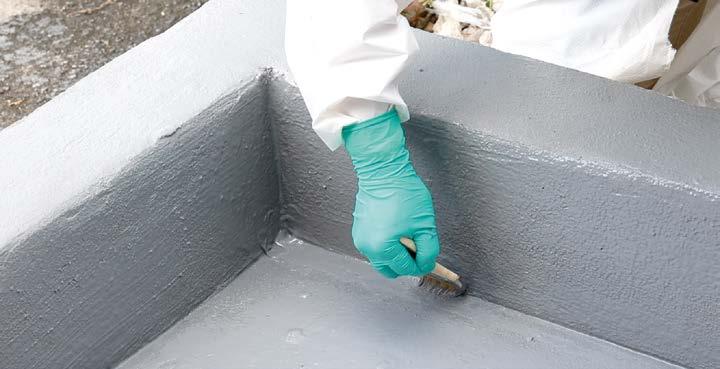
For further information: www.belzona.com
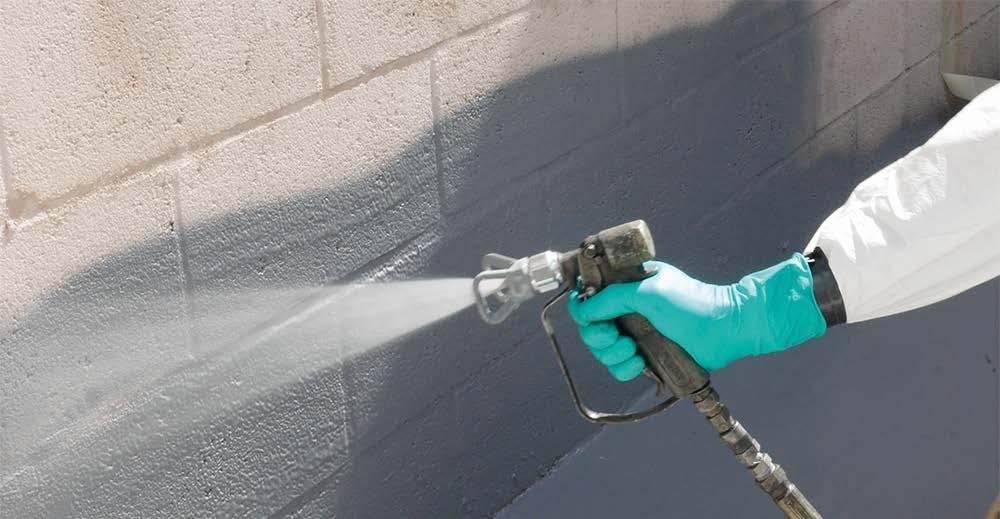
© Belzona
Graco Expands the Reactor® Proportioner Family with the Reactor 3 Spray Foam Proportioner Systems
Graco has developed a new fully connected system for spray foam and polyurea applications.
Graco Inc. has expanded its family of Reactor® proportioner with the Reactor 3™ spray foam proportioner systems to allow contractors to maximise material yield, productivity and profitability. The systems are available in the three product tiers Standard, Pro and Elite – that have been designed to meet the current contractor’s needs while allowing future upgrades if needed. “The Reactor 3 proportioner project took a fresh look at the entire system. All components were updated from drum to gun to improve performance and increase reliability. Each system component plays an important role in the final product being dispensed. So, we wanted a system that could self-monitor and automatically adjust to environmental changes. Its communication system ensures peak performance and makes it easier for contractors to complete their jobs on time and with quality results,” stated Nick Pagano, Graco Global Product Marketing Manager for Foam and Polyurea Equipment. The improved performance and reliability are ensured by the new Core™ transfer pumps, that communicate directly with the proportioner, and the independently temperature-controlled and internally heated Xcelerator™ hoses that provide quicker heat-up times, increased flexibility and optimised yield. In addition, the Reactor 3 system includes a new advanced touchscreen control, the active ISO lube pump system, larger and easier to maintain inlet filters and advanced software features, including the Smart Control® pressure management system, the Auto Pressure Balancing and the automatic cellular software updates. Finally, the Reactor 3 system also features the exclusive Katalyst™ software that brings a high level of intelligence and allows to optimise spray, eliminate ratio issues and improve yield.
For further information: www.graco.com
© Graco
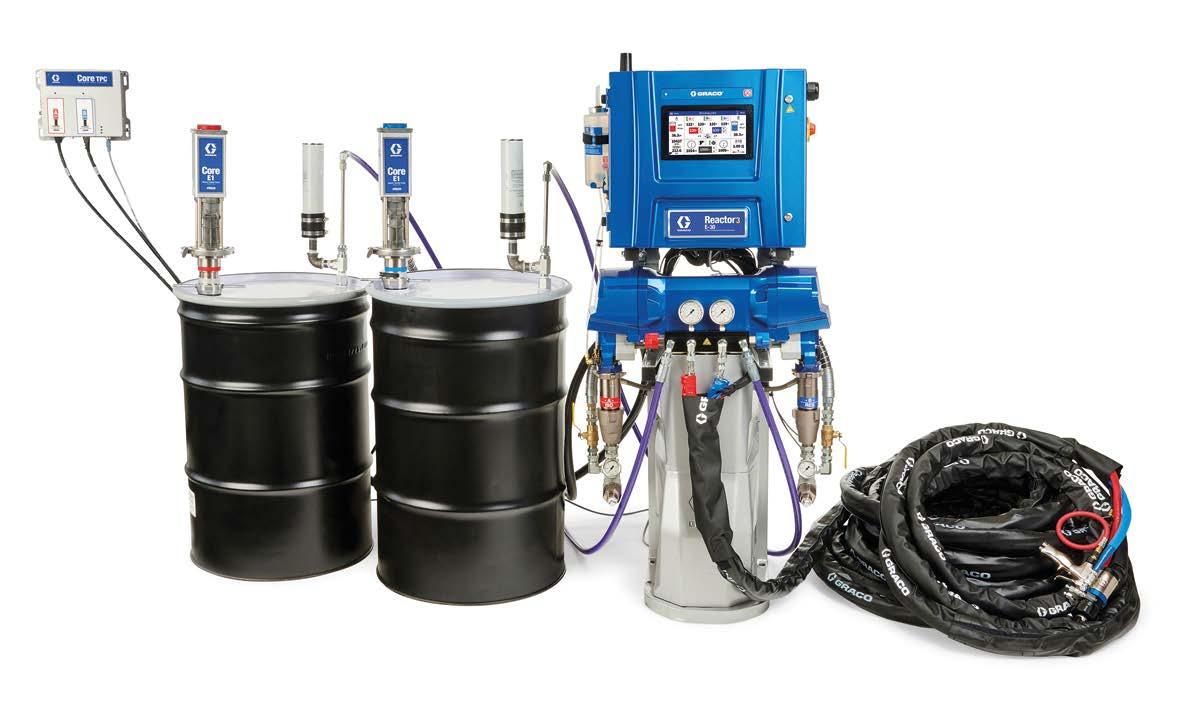
Hexigone Has Received a New UK Patent
The patent for Improved Corrosion Inhibition Incorporating Phosphates was granted to Hexigone Inhibitors.
Hexigone Inhibitors Limited has announced that in January 2022 it has received the UK Patent No: GB2588924 for Improved Corrosion Inhibition Incorporating Phosphates for the Intelli-ion® solution. The product developed by Hexigone provides corrosion protection both as a single replacement and as a synergistic inhibitor, as it improves the performance of phosphate-based inhibitors and lowers the amount of anti-corrosive additives required in the coating, allowing in this way to reduce the costs related to raw materials. Meeting the strict global environmental standards and requirements, Intelli-ion® is used to protect metal assets in several sectors, such as the marine and aerospace industry. “We are extremely pleased to see the hard work and dedication of the Hexigone Team resulting in this new patent being granted. This patent further enhances the company’s patent portfolio and demonstrates the company’s novel and solid chemistry,” stated Dr. Patrick Dodds, the CEO of Hexigone. “We are working globally to provide the coatings industry with safer and smarter solutions when it comes to corrosion protection. This patent demonstrates the high performance of the Intelli-ion® product range as a stand-alone inhibitor, or when used in synergy with other commercially available chromate free inhibitors. We look forward to our products and synergistic materials removing the previous reliance on chromium-6 corrosion inhibitors. Hexigone’s technical, manufacturing and commercial teams are driving the company forward as we undertake further collaborations with our customers.”
For further information: www.hexigone.com
© Hexigone
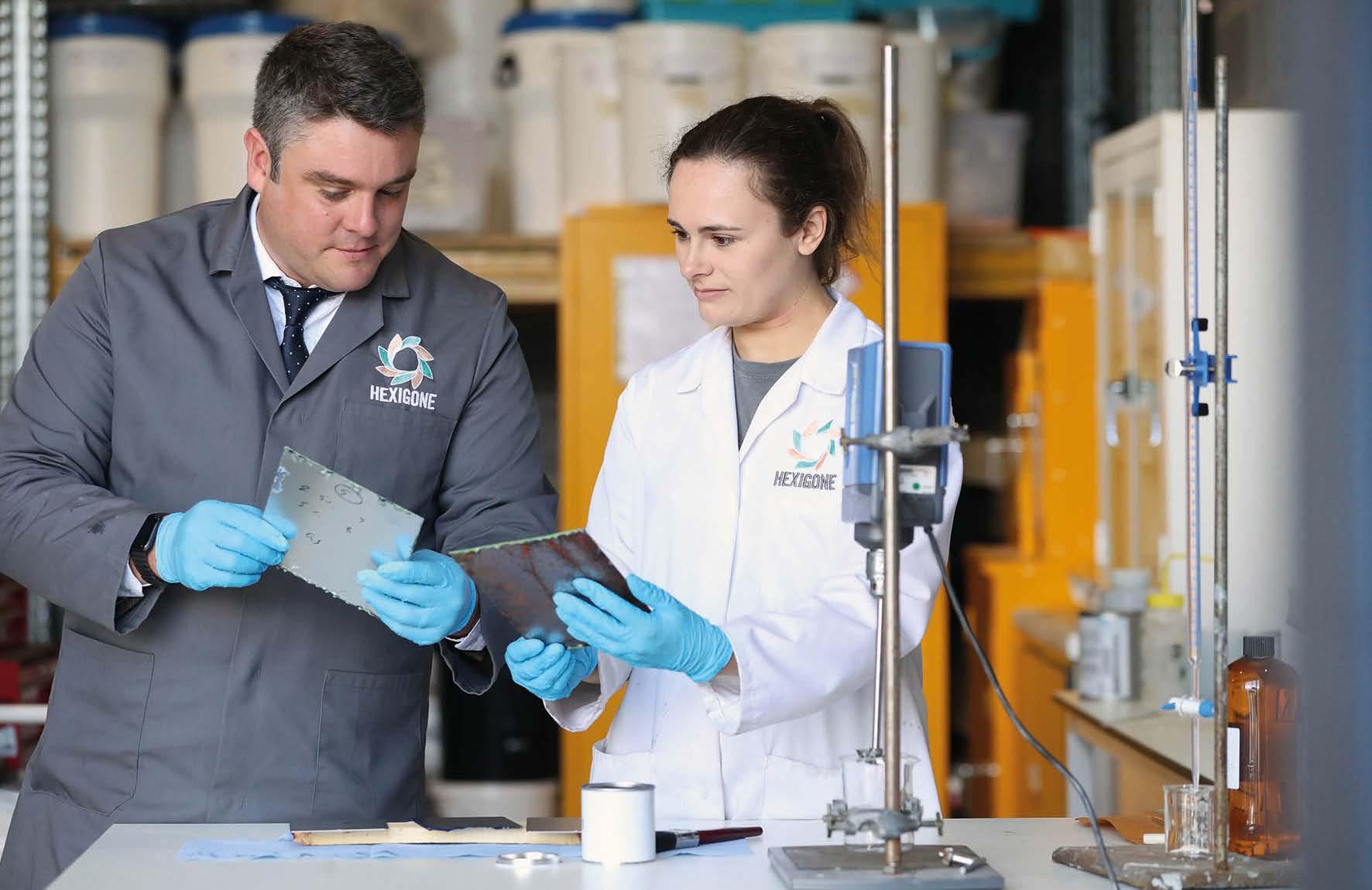
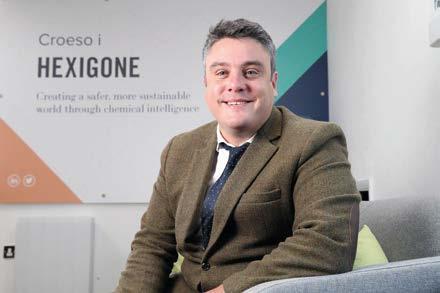
Dr. Patrick Dodds, the CEO of Hexigone.
A team from the University of Southern Queensland (Australia), led by Professor Pingan Song, has developed a lava-like non-toxic, fire extinguishing coating.
The researchers from the University of Southern Queensland (Australia) have announced the development of a new nontoxic fire extinguishing coating that could prevent buildings from being engulfed in flames. The study, led by the chemical engineer Pingan Song, was inspired by lava, one of the hottest substances that could be found on the surface of Earth. As lava, the new hybrid coating would in fact melt and then gradually form a flowing but non-combustible ceramic layer when exposed to extreme heat. “Melton lava is like a viscous flowing liquid but non-flammable. Once cooled, it solidifies to become a ceramic layer that does not support fire. Inspired by this interesting phenomenon, we designed a fire retardant coating that can create a non-combustible ceramic layer which can offer fire protections for the underlying substrates, just like a fire shield,” stated professor Pingan Song. The flame retardant is composed by a mixture of several metal oxide powders (including oxides of aluminium, silicon, calcium and sodium) that starts to melt at around 350°C (below the temperature of most flames), forming a glasslike sheet. The researchers added then tiny flakes of boron nitride, which flow easily and help fill any spaces between the metal oxides as the glass forms. Finally, they added a fire-retardant polymer that acts as a binder to glue the rest of the mixture. Spraying this new coating on building materials – such as thermal insulation foam, timber and steel structures – during the construction process could prevent disasters like the 2017 Grenfell Tower blaze in London, where 72 people lost their lives. Besides building, the lava-like flame retardant can be applied also in other different settings, for example wooden furniture, mining, tunnels and transportations. “Polymer foams were identified as the main cause of recent catastrophic disasters, particularly the Grenfell Tower fire. Solid wood materials, also widely used in buildings but extremely combustible, can also trigger fires, like the Notre-Dame de Paris blaze in 2019. Our fire retardant coating produces a very robust and thermally stable ceramic layer, compared to existing coatings, which usually produce a protective layer that is fragile and degrades at high temperatures,” continued Song.
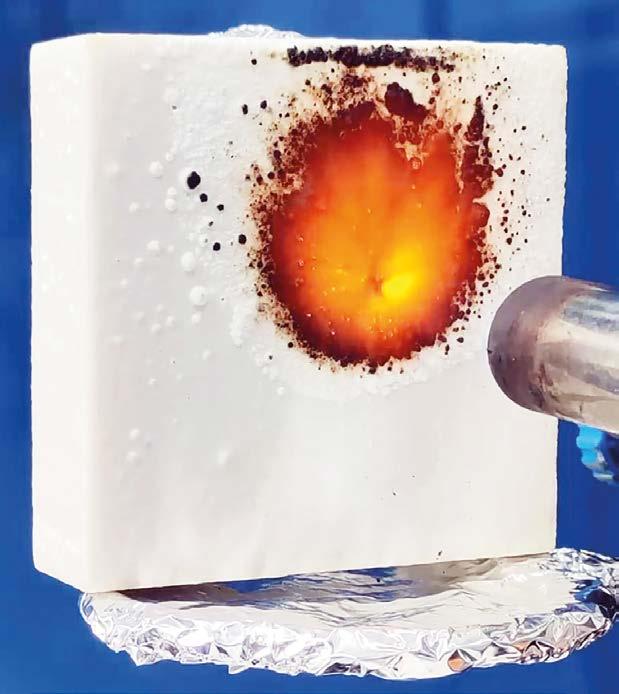
© USQ
The fire-retardant coating still needs to undergo further testing and refinement before its launch on the market, that is expected to take place within the next three years. The research, which was financially supported by an Australian Research Council Future Fellowship, was published in the journal Matter1 .
For further information: shorturl.at/gBR46
1 https://www.sciencedirect.com/science/article/abs/pii/S2590238521006342?via%3Dihub
COSCO’s Fleet to Be Coated with Nippon Paint Marine’s FASTAR® Antifouling
Nippon Paint Marine will apply its new antifouling system FASTAR® to COSCO’s fleet to provide high performance and improve drydock efficiency.
COSCO Shipping has recently announced that it will have its entire VLCCs fleet coated with FASTAR®, the new antifouling system developed by Nippon Paint Marine, once initial applications have been evaluated. FASTAR is a self-polishing, antifouling paint that includes a nano-domain resin structure designed to minimise the effects of seawater temperatures and vessel speeds on the performance of the coatings. FASTAR will be applied also to the passenger ferry COSCO Star and the 56,000dwt bulk carrier Xin Liu Lin Hai: COSCO Star will dock at the COSCO Shanghai Dockyard in February for a FASTAR® XI application while the bulker is currently scheduled to be coated with FASTAR® I in May at the COSCO Guangzhou Dockyard. “COSCO Shipping has a long history of applying Nippon Paint Marine antifouling to the hulls of its vessels as a way of improving propulsion efficiency and reducing emissions. Once the shipowner has verified the precise, predictable performance of FASTAR® on these two vessels, more vessels are expected to take advantage of this revolutionary coating system,” stated Jun Ye, the M & R Sales Director for Nippon Paint Marine in China. “With the current high freight rates, shipowners want to keep their vessels trading for as long as possible. FASTAR® antifouling not only provides next level performance but improves drydock efficiency, reducing significantly the time required in drydock for paint work.” The shipowner has chosen the newly introduced antifouling to allow its vessels to meet the Energy Efficiency Existing Ship Index (EEXI) requirements. “We were keen to evaluate and assess the feasibility of Nippon Paint’s next generation antifouling for possible VLCC application. The coating’s potential to reduce fuel consumption and carbon emissions by up to 8% is attractive and seen as a viable way towards meeting EEXI requirements. We also anticipate reduced paint volumes and quick drying time will result in cost savings,” commented from COSCO Shipping.
© COSCO Shipping
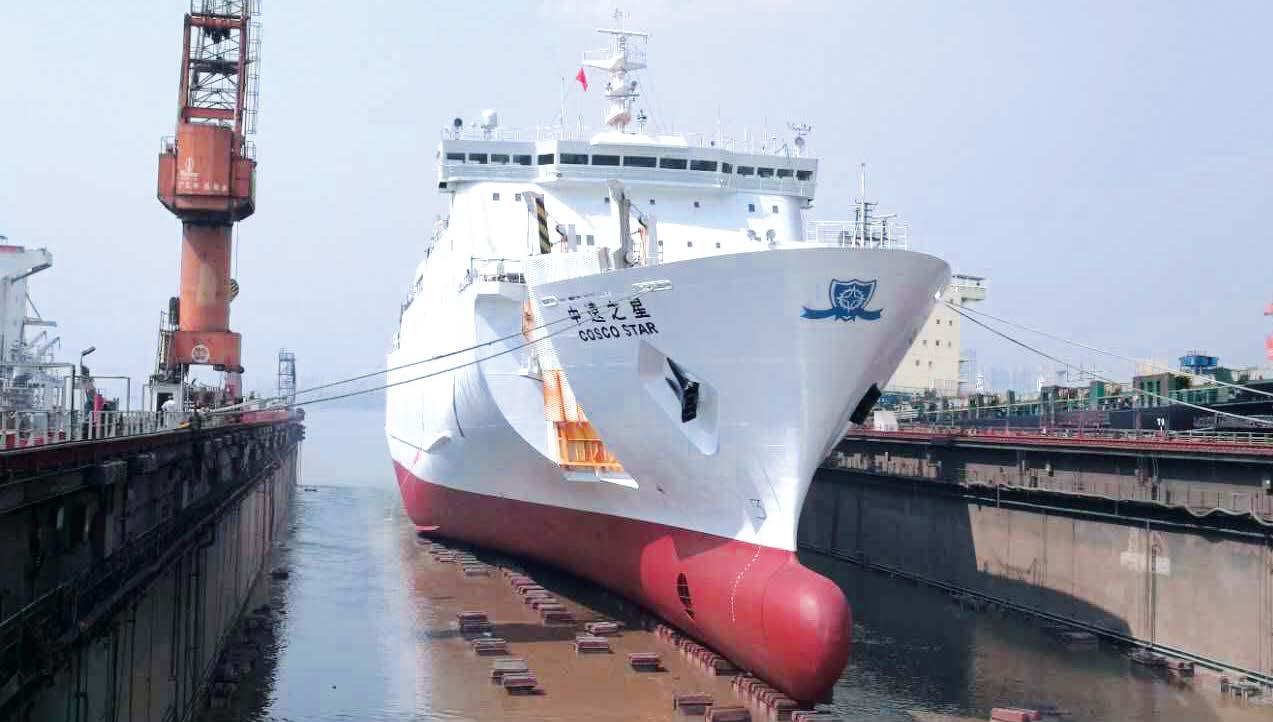
PPG Launched PPG PHENGUARD 985 Phenolic Epoxy Tank Coating
The new tank lining developed by PPG offers two or three coat flexibility and increases the resistance against fatty acids.
PPG has recently announced the launch of PPG PHENGUARD® 985, a phenolic epoxy tank lining specifically developed to provide temperature and chemical resistance against a wide range of aggressive chemicals that contain fatty acids. “The latest addition to our PPG Phenguard range, PPG Phenguard 985 tank lining features a patentpending formulation that can be applied in two or three coats instead of the traditional three coats without compromising chemical resistance. This gives asset owners and contractors flexibility to apply their preferred coating system build-up while having full confidence in the end result,” stated Bart Martens, PPG global product manager, chemical protection, Protective and Marine Coatings. Fatty acids are highly aggressive chemicals that could cause several problems for operators within the marine and tank storage industry, as the temperature window required for their storage is narrow and difficult to manage. Since temperature overshoots might jeopardize the efficacy of the tank lining, leading to additional expense, PPG
Phenguard 985 has been specifically designed to accommodate an extended temperature window. “In an increasingly competitive operating environment for asset owners, PPG Phenguard 985 creates the opportunity to reduce tank lining application and servicing costs while also maximizing cargo opportunities. As well as the initial application cost savings from moving from three to two coats, the liner’s higher thickness tolerance reduces the need for costly rework in case of overapplication,” concluded Martens.
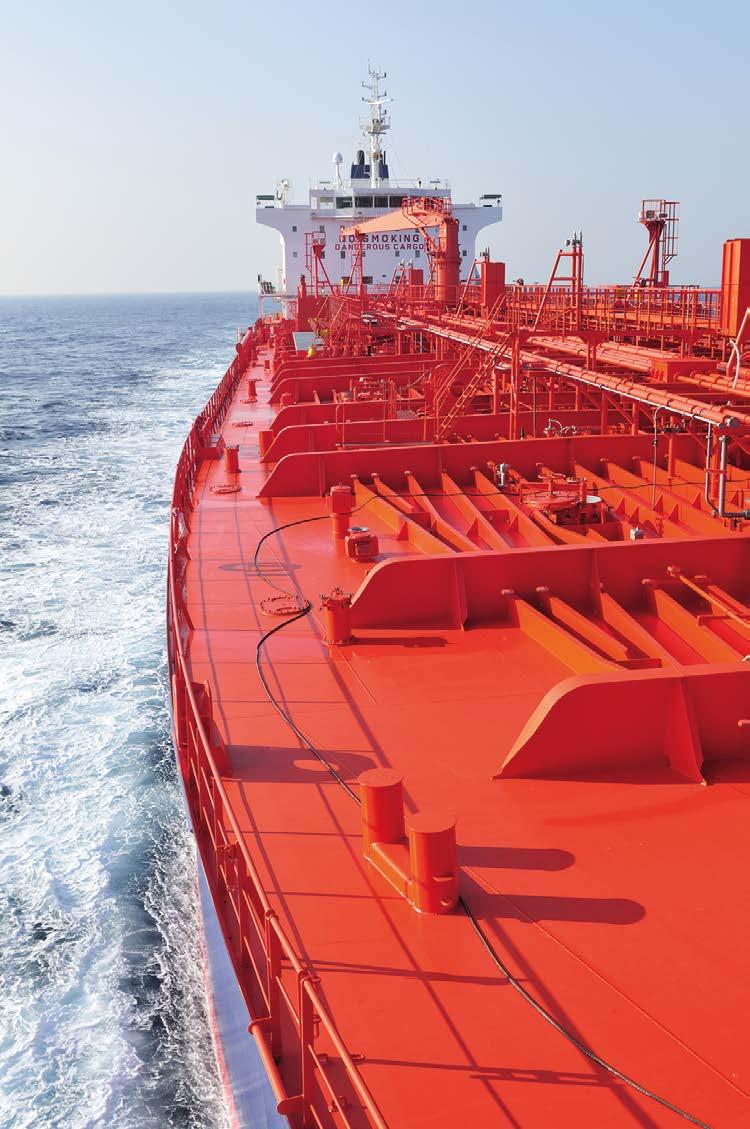
For further information: www.ppgpmc.com
© Oleksandr Kalinichenko-Shutterstock