
10 minute read
FOCUS ON TECHNOLOGY
© ipcm
Poles powder coated by Pinturas Marcelino González (Valladolid, Spain).
A Winning Choice: Pinturas Marcelino González Focused on Powder Coating Quality and Durability for Large Workpieces
Alessia Venturi ipcm®
When staking everything on an industrial challenge, in addition to a dose of luck, the key to winning it is to rely on high profile, reliable, solid, and technically skilled partners. This is what has happened to Pinturas Marcelino González, which is now the most important powder and liquid coating contractor for large manufactured parts in central Spain also thanks to its close relationship and technical exchange with AkzoNobel Coatings S.L.U., supplying it with a wide range of Interpon-branded primers, intermediate finishes, and top coats.
In the contract coating sector, there tend to be two approaches to customer service: some companies lack an industrial culture of specialisation and quality and prefer to compete on costs, whereas others offer very high quality coating processes and clearly understand the importance of guaranteeing the durability of the coatings applied. The latter often work for international groups, extending their market beyond national borders –a rare accomplishment for contractors, 90% of which tend to work for local businesses. However, these companies’ coating know-how is such that their reputation goes beyond their country’s borders, attracting customers from neighbouring nations. Pinturas Marcelino González (Valladolid, Spain) belongs to this second group of businesses. It is one of the largest and most flexible industrial coating contractors in its country, and above all one of the few in the nation and the only one in central Spain to offer liquid, powder, or mixed coating processes capable of meeting both very high aesthetic requirements and corrosion resistance standards up to C5M High, the highest in the classification of the ISO 12944 regulation, on large, highmass parts. Marcelino González can carry out painting projects both on site and in its workshop, ranging from the decorative and industrial sectors, with a focus on anti-corrosive applications, to maintenance and industrial flooring. That is an incredible amount of skills and experience
accumulated since 1973, the year it was founded by Marcelino González, the father of its current managers. Over the years, this has been greatly enhanced through the implementation of the powder coating technology in 2007 and through the beginning of a continuous, profitable, and constructive collaboration with AkzoNobel Coatings S.L.U. (Vallirana, Barcelona), which is now Pinturas Marcelino González’ main supplier of powder coatings. The range of AkzoNobel products used by the company is very wide, ranging from the complete Redox primer portfolio to industrial and architectural finishes, such as those from the Futura and Textura collections.
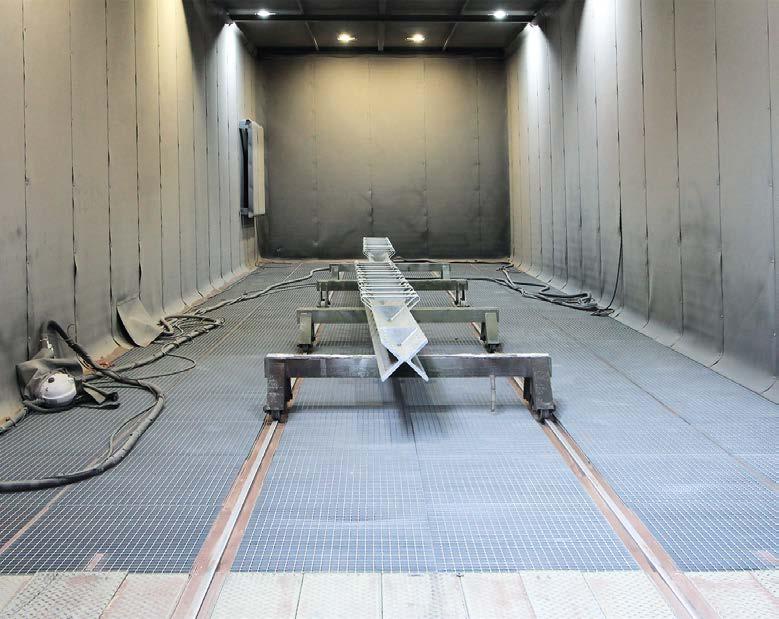
The history of a long-standing enterprise
Pinturas Marcelino González SL started to operate in 1973 with the aim of filling a major gap in this sector and becoming able to serve all types of customers, from private individuals wanting to paint their own house to companies with complex industrial projects requiring both liquid and powder coatings. After about ten years of carrying out small orders from private customers for the renovation and conservation of façades, the firm installed its first industrial wood treatment plant in 1986. The next evolution step was beginning to serve the industrial sector with a metal surface treatment plant. Today, Pinturas Marcelino González covers an area of more than 6000 m2 in the San Cristobal Industrial Park in Valladolid and it is equipped with one of the largest and most modern powder coating lines in Spain, complemented by a large shot blasting plant, liquid coating booths for large parts, and highly qualified personnel to carry out work both on site and in its workshop. “80% of the overhead contact lines and electrification towers for the Spanish high-speed AVE railway line came out of our factory, which we have recently doubled,” says Carlos González Valdivieso, the plant director of Pinturas Marcelino González. “We specialise in the application of anti-corrosion systems
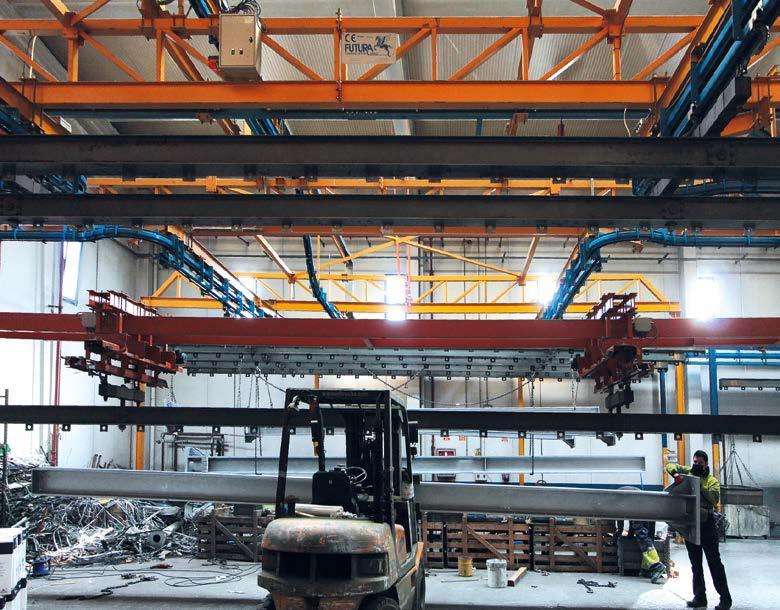
© ipcm
The inside of the corundum shot blasting machine and the lowerator in the loading/unloading area.
© ipcm
© ipcm © ipcm
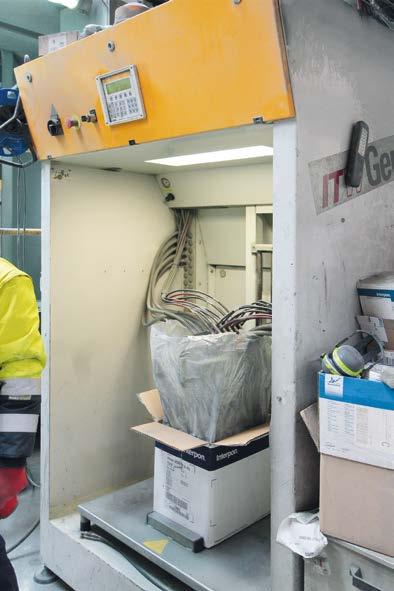
Manual application of powder paint in the coating booth. The powder centre.
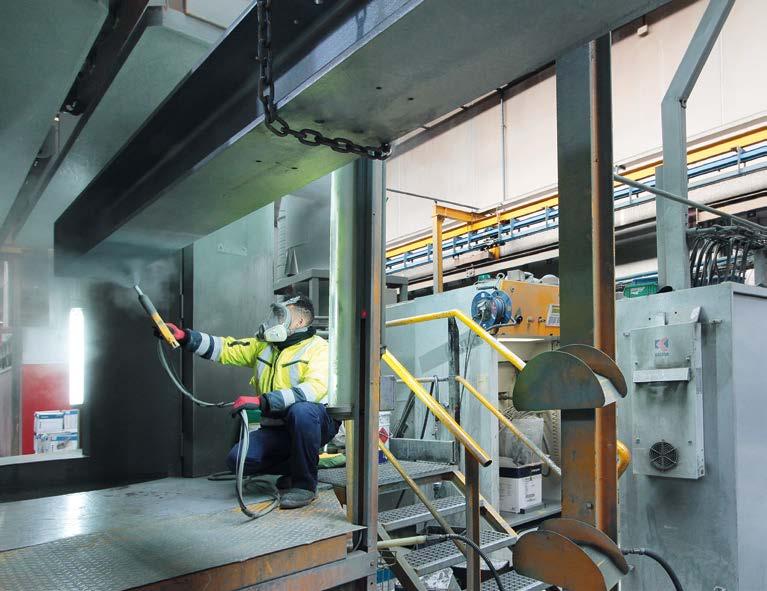
on large-sized, high-volume parts, with the possibility of achieving the C5M High resistance class, i.e. 1440 hours of salt spray resistance with a three-coat powder system (galvanising primer, epoxy intermediate layer, and polyester top coat) applied after shot blasting and chemical pretreatment.” “We started out as a coating contractor for the Indal group, which specialised in outdoor lighting (later transformed into Philips and then Signify) and which decided to rely on our company, thus introducing us to the painting of iron, particularly for light poles. This first experience in the coating world paved the way for the implementation of further different metal surface treatment processes, always performed both in our workshop and on site. On that occasion, we were introduced to powder coating and we also initiated our collaboration with AkzoNobel, which was Indal’s specified powder supplier: it was already using powder products for its street lighting equipment and all its contractors had to adapt. Thanks to the consultancy and continuous coaching of our operators by AkzoNobel’s technicians and through the research activity carried out by both parties, we soon realised that powder coating offers a higher industrial quality level and far greater durability than liquid coating. In 2007, Pinturas Marcelino González decided to invest on powder coatings for its future.” This was certainly a winning choice, given the reputation gained by this contractor all over Spain and with all the foreign groups it supplies through partnerships with Spanish companies. “We soon realised that our coating plants were inadequate to meet the needs of a group like Indal. Therefore, in 2007, we invested in a new line that could treat parts up to 12.5 metres in length, including a metal shot blasting booth, two liquid coating booths (a large one and a smaller one for high quality finishes), and an automatic powder coating booth. Now, we are able to reliably carry out any type of coating project and anticorrosion treatment up to C5M class, even on large-sized, high-volume parts. Finally, in 2020, we doubled our paint shop by installing a line with a corundum shot blasting plant and two large liquid coating booths in a new building.”
Full use of AkzoNobel’s Interpon product portfolio
“With our powder coating system, we are able to carry out a traditional cycle including phosphodegreasing and zirconium-based nanotechnology passivation + 1 coat of powder, achieving a salt spray resistance of 400 hours, or an anti-corrosion cycle including shot blasting and chemical pre-treatment as above + 2 or 3 layers of powder, achieving the C5M High class in compliance with ISO 12944,” explains Carlos González Valdivieso. “As a result, we are highly specialised in the use of powder primers, which we change depending on the material to be coated. AkzoNobel’s Interpon Redox line is a fantastic tool for us, as it is the most comprehensive range of multi-layer powder primers on the market.”
“AkzoNobel has always supported the professionalisation of applicators and provided companies with technical assistance, helping them choose (and test) the right products for their quality and durability requirements and developing the most appropriate systems with them. In fact, this is the most exciting part of our job as agents,” says Juan José Sánchez Maqueda, AkzoNobel’s sales representative. “Together with Pinturas Marcelino González, we normally choose the most suitable primers for the type of materials to be painted from the Interpon Redox range. For instance, when treating carbon steel, we select a zinc-rich primer such as Redox PZ, which offers long-lasting cathodic protection enhanced by a barrier effect, or a primer from the Redox Active epoxy range, which contains pigments that activate a passivation process to protect the substrate. When dealing with porous materials such as galvanised steel or die cast aluminium, we prefer a primer with a degassing additive; indeed, these materials have gases trapped beneath their surfaces: the Interpon Redox Plus FL151F degassing primer prevents them from surfacing during application and curing of the polyester top coat, thus avoiding pinhole defects.” “We paint such a wide range of different substrates, from steel and galvanised steel to aluminium, that having a complete portfolio of products applicable in multi-layer systems is the only way to meet any aesthetic and/or functional specification,” states Carlos González Valdivieso. “AkzoNobel also supplies us with Qualicoat class 1 and 2 polyester finishes. We also choose some finishes from the Futura D2525 (super durable) collection and textured finishes from the D1036 Textura or D2525 Structura series, depending on customer requirements and the intended use of products. We use the full range of colours offered by the Interpon finishes, including metallic and brilliant shades. “We also paint aluminium: therefore, our chemical pre-treatment process is a multi-metal, step-by-step operation, a must for treating parts up to 12.5 metres in length. Only this system enables us to avoid dragging water and chemical solutions from one pre-treatment stage to another. Its cycle includes fluoride-based degreasing, one rinse with mains water, one rinse with demineralised water, and a zirconium-based no-rinse nanotechnology passivation phase. The chemicals used are provided by Proquimia; for the nanotechnology passivation phase, we use the ProSpray atomisation system developed by Proquimia itself, which mixes and applies ever-fresh product without any waste or bath contamination.”
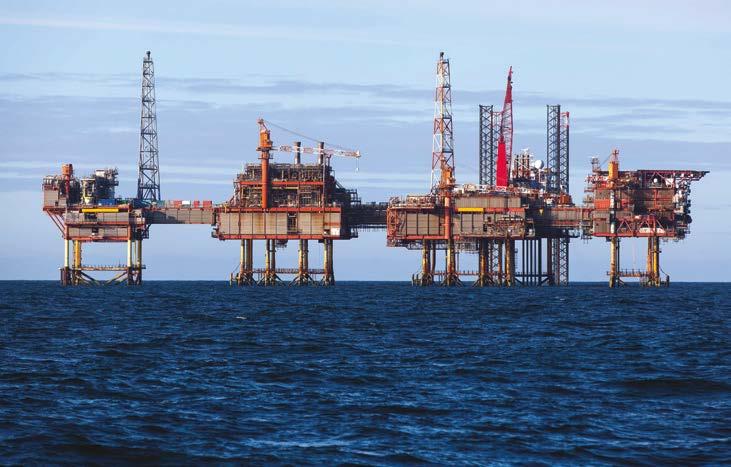
Relying on market leaders to win this industrial challenge
“Since we were totally unfamiliar with powder coating, we chose to rely on the leaders in the field, not only for the powders themselves, with AkzoNobel, but also for the system: the conveyor was designed by Futura Convogliatori Aerei for heavy and special loads, including
Micro-Corrosion Inhibiting Coatings Solve A Wide Variety Of Corrosion Problems!
Powered by Nano VpCI® from Cortec® Corporation
VpCI® Coatings protect a multitude of metal products. Applying VpCI® Coatings provides fast and economical protection for exterior and interior surfaces.
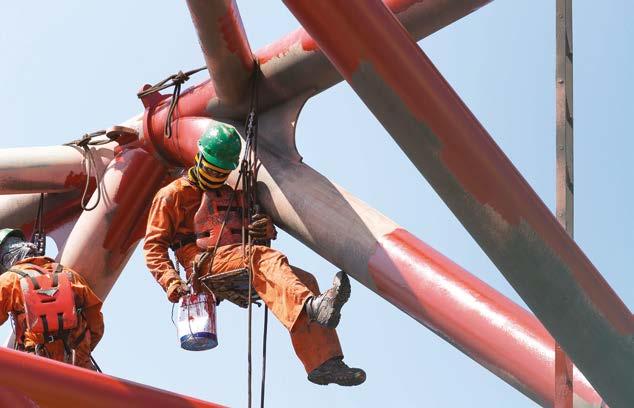
Our technical staff can help you decide which product you need for long lasting and complete protection of your corrosion sensitive products.
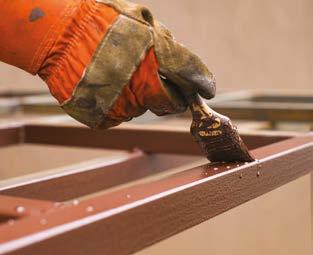
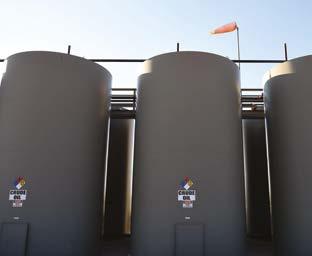
FIRST CROATIAN BIOPLASTICS PLANT
© ipcm
© ipcm
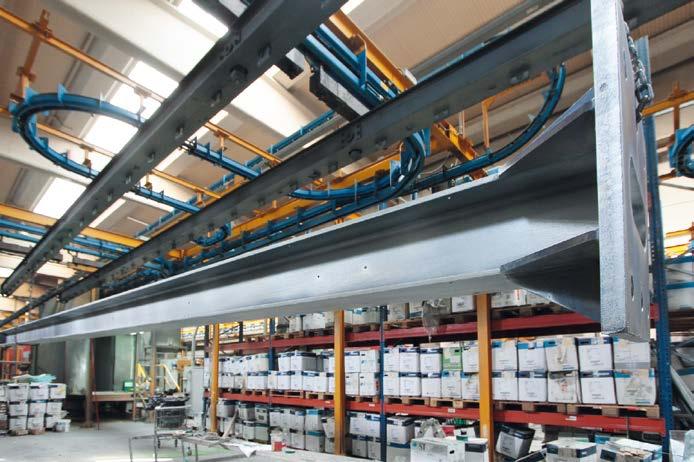
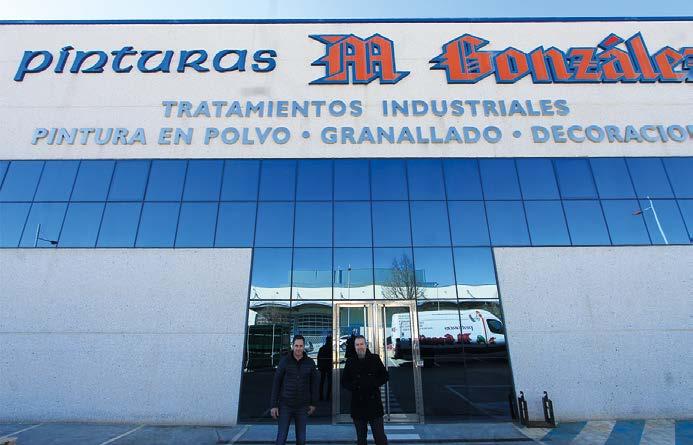
© ipcm a lowerator. Geinsa designed the pre-treatment tunnel and the ovens. Gema designed the powder coating booth. After the building crisis of 2008-2009, most outdoor lighting manufacturers have disappeared. If we had not had such a high-performance plant that was also so flexible in terms of type of workpieces to be powder coated, we would not have been able to overcome that crisis quickly and unscathed. In fact, the versatility of the system and of the powder products we have learned to use allows us to paint everything from light poles, train tracks, railway station arbours, and electrification towers to furniture and design components that require an automotive-degree aesthetic quality. Powder coating has opened up a market we did not even think existed.” “We were actually lucky to “inherit” AkzoNobel as a supplier from Indal, because their technical assistance has helped us learn and master a technology that was unknown to us, providing us with hours of support to ensure that everything worked at its best. Our relationship has been going on for fifteen years and it has been very positive at all times,” indicates Carlos González Valdivieso. “For AkzoNobel Coatings, Pinturas Marcelino González is an important customer not only (or not so much) because of the volumes of powder it consumes, but because of its extreme specialisation, which enables us to use it as an industrial laboratory to test our powder products before putting them on the market. It has accumulated such a great deal of expertise in both liquid and powder coating. It also works for German customers, passing very strict audits and even suggesting improvements to the specified systems, if any,” explains Juanjo Sanchez Maqueda from AkzoNobel. “We are currently launching some super durable powders from the Interpon D3020 series (an alternative to PVDF) and here at Pinturas Marcelino González we can test the products before releasing them in the market. Thanks to its application culture, it help us to understand if we are doing well, not only at the laboratory but also at the industrial level.” This is what a true partnership between a supplier and a customer looks like. ‹
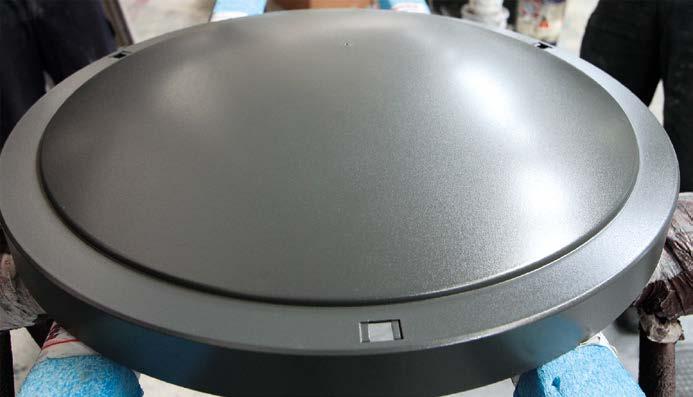
A large workpiece transported by the Futura Power & Free conveyor.
A powder coated part.
Carlos González (left) with Juanjo Sánchez from AkzoNobel.