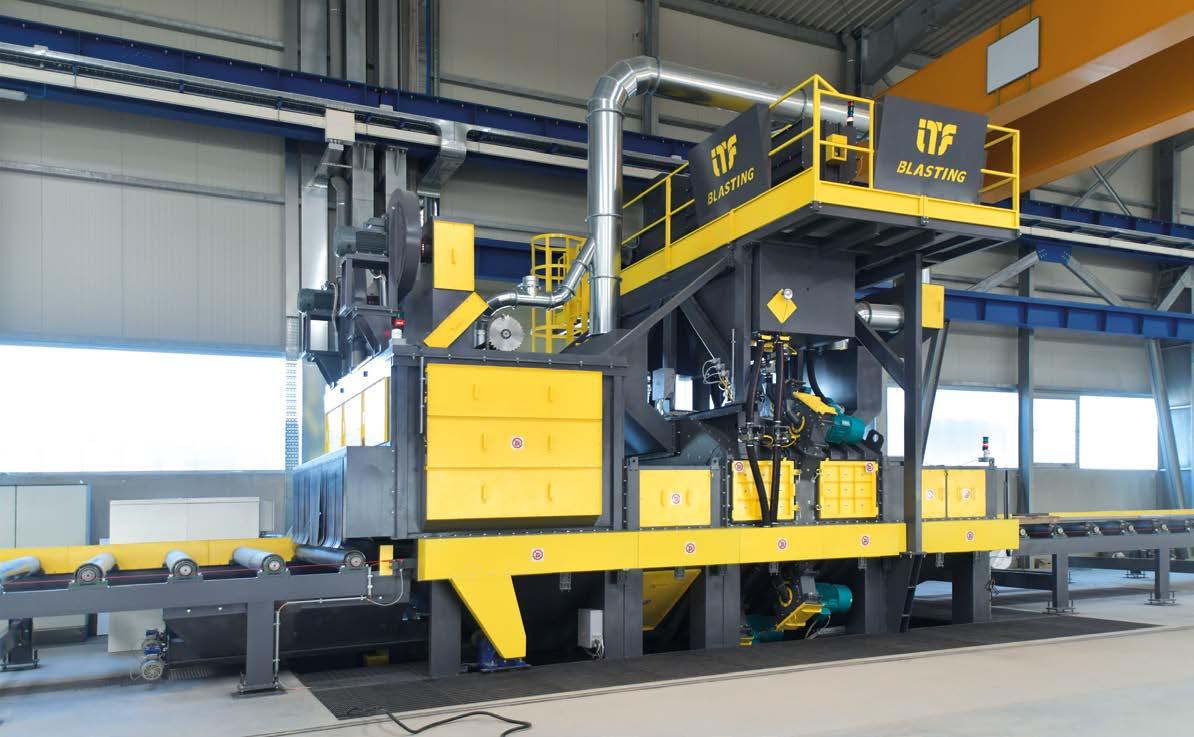
6 minute read
FOCUS ON TECHNOLOGY
The shot blasting machine installed at the customer’s premises.
The Importance of “Zero Shot” Blasting Operations to Allow Sheets to be Handled Correctly through an Overhead Crane with a Magnetic Lifter
Gabriele Lazzari ipcm®
I.T.F. has built a fully automated shot blasting plant for large-sized components in order to meet the complex requirements of a manufacturer of sheets that are over 3 metres wide and weighing up to 15,000 kg. As well as allowing the recovery and replacement of abrasives even during processing, the machine is equipped with three blowers that guarantee “zero shot” operation and the safe handling of sheets through an overhead crane with a magnetic lifter.
The optimisation of processing times is often achieved with automated production and handling equipment. However, when pre-treating and finishing metal sheets and other large structures, special attention should also be paid to the quality of surfaces after treatment, in order to avoid compromising their handling operations and creating a dangerous situation. This is why, for a major manufacturer of sheet metal and steel products, I.T.F. has designed and installed an automatic shot blasting machine with a roller conveyor and a blower system that achieves the “zero shot” result, i.e. it eliminates any residual shot from the parts’ surfaces to ensure the correct and safe handling of sheets by means of an overhead crane with a magnetic lifter.
Speed and automation as basic requirements
This nationally recognised company located in north Italy, specialises in the processing and marketing of hot-rolled coils or individually rolled sheets and other large steel products for various markets such as automotive, industrial vehicles, agricultural and earth moving machinery, shipbuilding, and railway. Previously, it used a machine with manual positioning adjustment. However, wanting to increase its production rates, it needed a fully automated shot blasting plant guaranteeing “zero shot” operation, so that the sheets could be handled by an overhead crane with a magnetic lifter to speed up production. Therefore, it turned to I.T.F. - Impianti Trattamenti Finiture (Mesero, Milan, Italy), specialising in the design, manufacture, and installation of finishing equipment, for a shot blasting machine with a roller conveyor. In January 2021, I.T.F. supplied it with the GLPX 3205-8 pass-through plant that met all requirements, also allowing to optimise resources and reduce the process’ environmental impact.
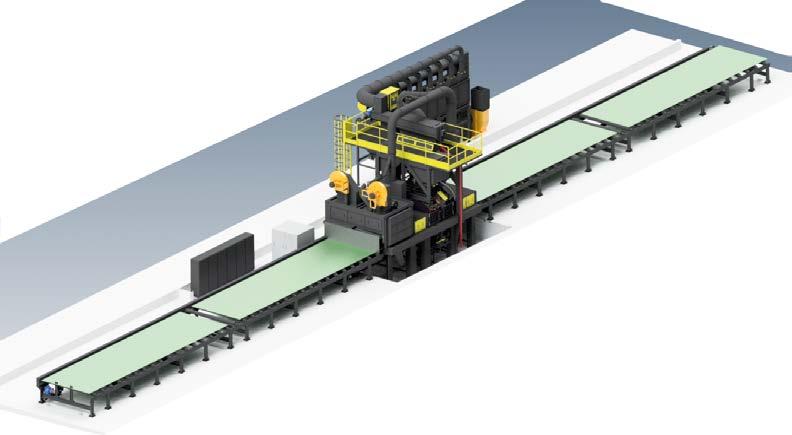
The GLPX pass-through shot blasting system that adapts to any sheet dimensions
I.T.F. has developed a GLPX pass-through plant suitable for sheets, profiles, and structures with dimensions of up to 3,200 millimetres in width and 500 millimetres in height. For ease of transport and installation, this shot blasting machine equipped with a roller conveyor was built in modules with very thick materials and strengthened with metal profiles in order to support structures weighing up to 15,000 kilograms (each roller supports a weight of 3,000 kilograms). Thanks to its size, the machine can even handle several sheets at the same time: it features a 26-metre long inlet and outlet roller conveyors divided into two equally long sections that are independent of each other, as they are equipped with their own self-
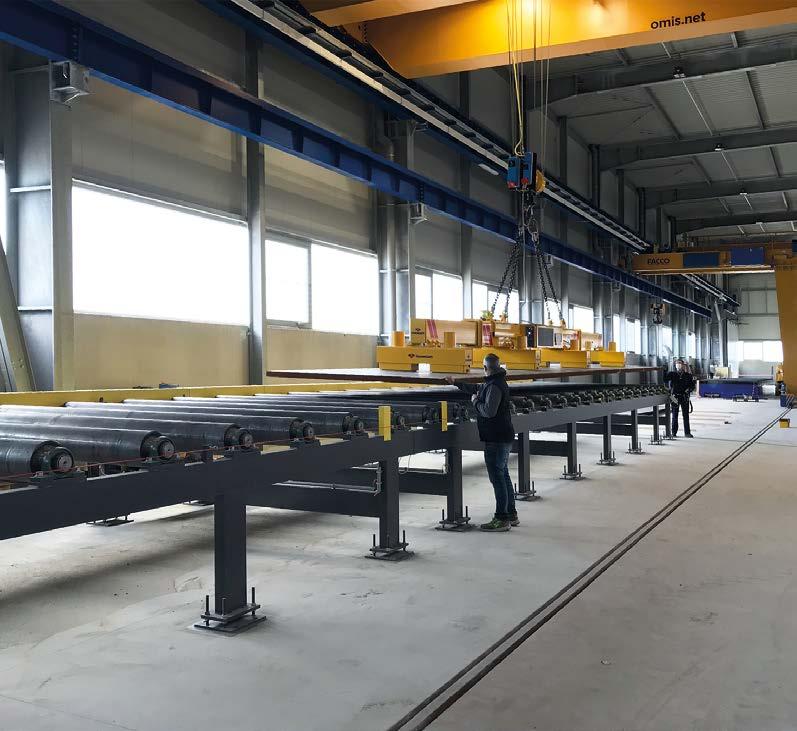
The rendering of the I.T.F. shot blasting machine.
The magnetic overhead crane that releases the sheet metal on the inlet roller conveyor of the shot blasting machine.
© I.T.F.
© I.T.F.
© I.T.F. © I.T.F.
A sheet entering the plant.
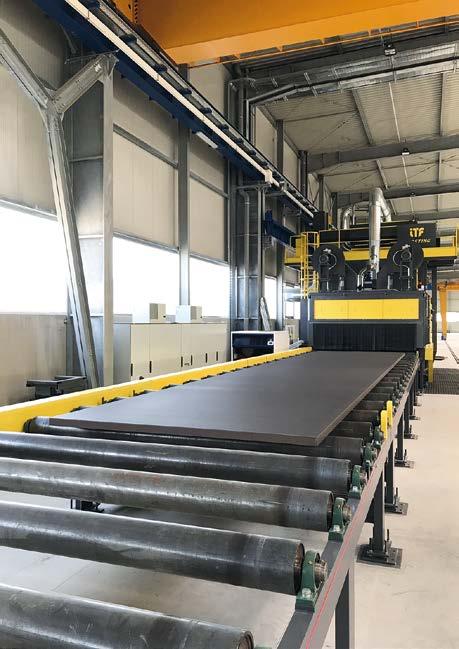
ventilated drive controlled by an inverter, allowing to place two 12-metre long sheets. This has enabled the creation of a buffer for the storage and continuous automatic handling of sheets, which further speeds up production. When the metal sheets are loaded onto the conveyor rollers of one of the two sections (all rollers are equipped with a safety rope), the operator selects the start option, and initiates the sheet’s sideshift. At the entrance to the pre-vestibule of the shot blasting chamber, there are photocells for the recognition of the product geometries, in order to adapt the shot blasting process accordingly. An automatic timer set by the photocells allows the opening of the abrasive dosing valves (a combination of spherical and angular steel) at the exact moment in which the sheet is positioned near the first of the eight turbines with motors of 22 kilowatts each, thus avoiding that shot blasting takes place without the piece in front, optimising resources. The turbines, made entirely in I.T.F.’s own workshop with heat-treated steel and with manganese wear plates, are arranged equally above and below the roller conveyor and tilted, so as to guarantee even treatment. The plant has a series of doors that allow easy access and inspection of the shot blasting chamber and the vestibules, as well as a raised metal platform complete with a ladder for accessing the adjustment and maintenance areas of the “upper” part of the plant, the pneumatic separator, the upper auger with a screen basket, and the elevator head for tensioning the conveyor belt.
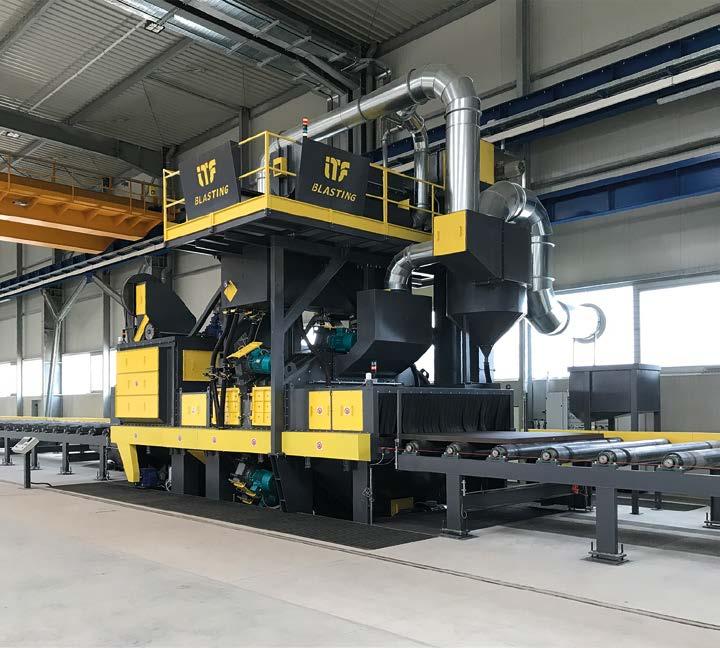
A sheet exiting the plant.
Then, the sheets reach the station devoted to removing the shots projected by the turbines and deposited on the plant’s floor. Here, there is a mobile system called a “brush carriage” that, depending on the workpiece thickness detected by the photocells at the machine inlet, positions itself at a pre-set height. A ploughshare evens out the thickness, then the rotating brush removes the shot from the part’s surface, sending it to an auger that conveys it laterally back into the abrasive cycle. Finally, a blow-off nozzle system removes the residual shot, guaranteeing the “zero shot” result required by the customer. “The additional blow-off phase proved essential to meet the customers’ requirements. Any shot residue on the surfaces of the treated sheets could compromise the magnetic lifter’s handling operations, delaying production and creating a dangerous situation of all operators,” explains the technical personnel of I.T.F. “Most blowers in this field do not allow the “zero shot” result to be achieved. So, I.T.F. has installed two ultra-
high-pressure blade blowers, and a nozzle blower with a dedicated compressor to completely eliminate any dust and shot residues.”
Further application details
In addition to process automation and cleaning quality, the plant also stands out for its special shot-control devices that optimise the use of resources. Instead of conventional abrasive valves, shot dosage is managed by a special magnetic valve with automatic adjustment of the shot’s flow rate, managed by the PLC according to the current absorbed by the turbine motors: the valve acts on the pass-through section by means of a magnetic field, regulating the opening and closing the shot’s jet and preventing it from flowing out when not needed. Finally, the plant is also equipped with an automatic shot refilling system for the highcapacity main storage tank (loaded with 1500-kg big bags). ‹
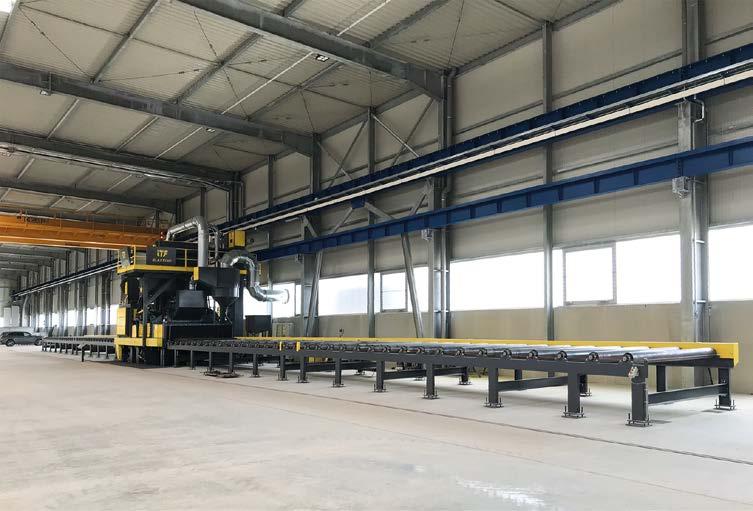
© I.T.F.
I.T.F.’s shot blast machine is over 60 metres in length.
Colorful Protection
Let Nature (and Colorstream®) inspire you and experience the changing faces of nature in surprising new ways of formulating imaginative surfaces for natural and exciting looks.
BE CURIOUS!
www.merckgroup.com/en/s/colorstream-in-nature.html
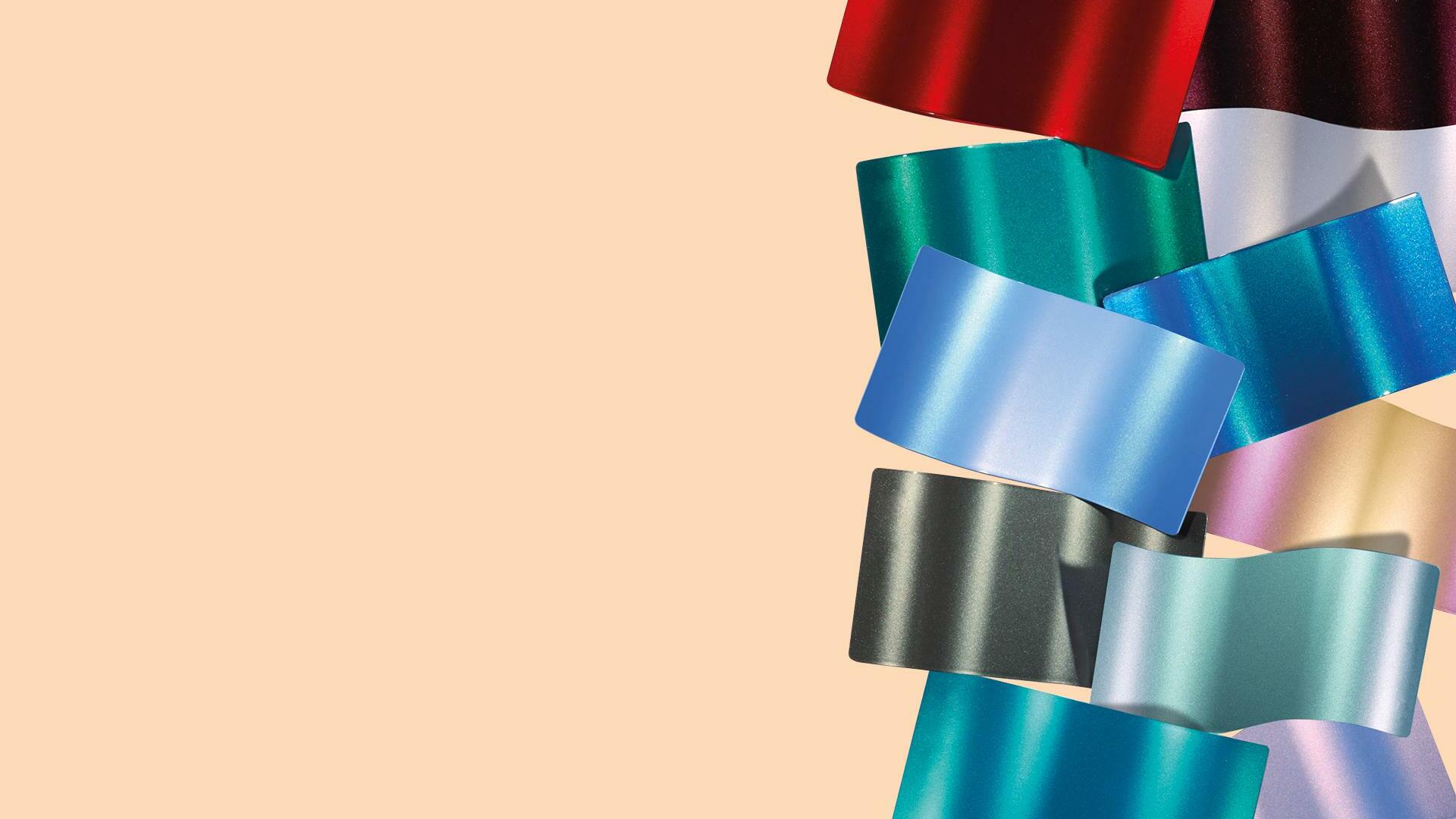
Merck Srl
Electronics Surface Solutions
Via Monte Rosa 93 20149 Milano MI | Italia